流水线设计例子概要
企业流水线生产的组织设计概述

设备升级:对流水线上的设备进行升级改造,提高设备的自动化程度和生产效率,减少人工操作失误。
人员培训:对流水线上的员工进行培训,提高员工的技能水平和操作规范意识,确保生产顺利进行。
05
避免生产瓶颈
建立应急处理机制确保设Fra bibliotek维护和保养优化生产流程和操作方法
合理规划生产线布局
保持生产平衡
定义:确保流水线各工序的生产能力相匹配,避免生产瓶颈和浪费
优化生产流程:减少生产过程中的浪费和不必要的环节,提高生产效率
提高设备利用率:通过定期维护和保养设备,确保设备处于良好状态,提高设备利用率
降低原材料成本:通过与供应商建立长期合作关系,争取更优惠的价格和更好的质量保证
06
案例一:某汽车制造企业的流水线生产组织设计
案例背景:某电子产品制造企业面临生产效率低下、产品质量不稳定等问题,需要进行流水线生产组织设计。组织设计目标:提高生产效率、降低成本、提高产品质量和客户满意度。流水线生产流程设计:根据产品特点和生产需求,设计合理的流水线生产流程,包括原材料采购、加工、装配、检测等环节。人员配置和培训:根据生产流程和设备需求,合理配置操作人员和设备维护人员,并进行相关培训,提高员工技能和素质。设备选型和布局:根据产品特性和生产需求,选择合适的生产设备和工艺,并进行合理的布局,提高生产效率和产品质量。信息化管理:采用先进的生产管理系统,实现生产过程的信息化管理和监控,提高生产效率和产品质量。案例总结:通过流水线生产组织设计,某电子产品制造企业实现了生产效率的提高、成本的降低、产品质量的稳定和客户满意度的提升。
流水线的组织设计
确定生产节拍:根据市场需求和生产能力,确定每个生产环节的时间间隔
制定工艺流程:根据产品特点和生产要求,确定各工序的先后顺序和衔接方式
流水线设计的思想介绍与设计实例

流水线设计的思想介绍与设计实例
流水线设计
流水线概述
如下图为工厂流水线,工厂流水线就是将一个工作(比如生产一个产品)分成多个细分工作,在生产流水线上由多个不同的人分步完成。
这个待完成的产品在流水线上一级一级往下传递。
图片来自网络
比如完成一个产品,需要8道工序,每道工序需要10s,那么流水线启动后,不间断工作的话,第一个产品虽然要80s才完成,但是接下来每10s就能产出一个产品。
使得速度大大提高。
当然这也增加了人员等资源的付出。
对于电路的流水线设计思想与上述思想异曲同工,也是以付出增加资源消耗为代价,去提高电路运算速度。
流水线设计实例
这里以一个简单的8位无符号数全加器的设计为实例来进行讲解,实现
assign {c_out,data_out [7:0]} = a[7:0] + b[7:0] +c_in
c_out 为进位位。
(源码链接:https://pan.baidu/s/1-imO5A51dJ_pfWpRfOYcHg 提取码:dx0k )
如果有数字电路常识的人都知道,利用一块组合逻辑电路去做8位的加法,其速度肯定比做2位的加法慢。
因此这里可以采用4级流水线设计,每一级只做两位的加法操作,当流水线一启动后,除第一个加法运算之外,后面每经过一个2位加法器的延时,就会得到一个结果。
整体结构如下,每一级通过in_valid,o_valid信号交互,分别代表每一级的输入输出有效信号。
工程设备流水线设计方案

工程设备流水线设计方案一、前言随着科技的不断发展和工业生产的提高,工程设备流水线的应用越来越广泛。
流水线可以有效提高生产效率和降低生产成本,因此在各种工业领域得到了广泛的应用。
本文将针对工程设备流水线的设计方案进行详细的介绍和分析。
二、流水线设计的重要性1. 提高生产效率:流水线可以实现生产自动化,减少人工操作,提高生产效率。
2. 降低生产成本:流水线可以降低生产过程中的能耗和材料损耗,实现生产成本的降低。
3. 优化生产流程:通过流水线的设计,可以优化生产流程,减少生产浪费,提高生产质量。
因此,流水线的设计对于提高生产效率、降低生产成本和优化生产流程具有重要的意义。
三、工程设备流水线设计方案1. 设备选型首先需要根据生产需求和产品特性,选择合适的设备进行流水线的设计。
设备选型应考虑到设备的生产能力、适用范围、稳定性、易维护性等因素。
例如,对于生产装配线,需要选择高性能的机械手臂和传动设备;对于生产包装线,需要选择高速包装机和自动封箱机等设备。
2. 设备布局设备布局是流水线设计的重要环节。
合理的设备布局可以确保生产流程的顺畅进行,减少设备之间的交叉影响,提高生产效率。
设备布局应考虑设备之间的连线、通道宽度、作业空间、设备维修等因素。
通过合理的设备布局,可以实现生产过程的自动化、高效化。
3. 输送方式流水线的输送方式包括链式输送、辊道输送、皮带输送、气浮输送等多种方式。
输送方式的选择应根据产品特性、生产速度、生产场地等因素进行综合考虑。
例如,对于重型产品的生产线,可以选择链式输送方式;对于高速生产线,可以选择辊道输送方式。
通过合理的输送方式的选择,可以保证产品的顺畅流动,提高生产效率。
4. 安全设施在流水线设计中,安全设施是不可忽视的重要环节。
流水线设计应该设置应急停车系统、防护罩、警示标识等安全设施,确保生产过程中人员和设备的安全。
5. 自动化控制流水线的自动化控制是提高生产效率的关键。
通过PLC控制系统、传感器检测系统、计量系统等自动化控制设备,可以实现生产过程的智能化管理,提高生产效率。
流水线生产的组织设计

生产线布局优化:合理规划生产线布局,减少生产过程中的物流距离和时间,提高生产效率
设备配置优化:根据生产需求和设备性能,合理配置设备数量和类型,提高设备利用率和生产效率
人员培训和管理:加强员工技能培训和管理,提高员工操作水平和生产效率,降低人为因素对生产的影响
提高生产效率和产品质量
优化生产流程:减少生产过程中的浪费和延误,提高生产效率
பைடு நூலகம்
感谢您的观看
流水线生产的应用范围
03
工艺流程原则
添加标题
确定生产工艺流程:根据产品特性和生产需求,确定合理的工艺流程,确保生产过程高效、稳定。
添加标题
优化工艺流程:对现有工艺流程进行分析,找出瓶颈和问题,通过改进工艺、提高设备精度等方式优化工艺流程,提高生产效率。
添加标题
标准化操作:制定标准化的操作规程,确保生产过程中的各个环节都有明确的操作要求和标准,提高生产的一致性和稳定性。
制定生产计划:根据生产目标,制定详细的月度、周度、日度生产计划。
调度方案:根据生产计划,合理安排生产设备、人员、物料等资源,确保生产顺利进行。
调整与优化:根据实际生产情况,及时调整生产计划和调度方案,提高生产效率和质量。
05
优化生产线布局和设备配置
设备维护和保养:建立完善的设备维护和保养制度,确保设备正常运行,减少故障停机时间
智能化和自动化:未来流水线生产将更加智能化和自动化,提高生产效率和产品质量。
柔性制造:未来流水线生产将更加注重柔性制造,能够快速适应市场需求的变化。
绿色环保:未来流水线生产将更加注重绿色环保,采用环保材料和工艺,降低对环境的影响。
定制化生产:未来流水线生产将更加注重定制化生产,满足消费者个性化需求。
生产流水线设计范文
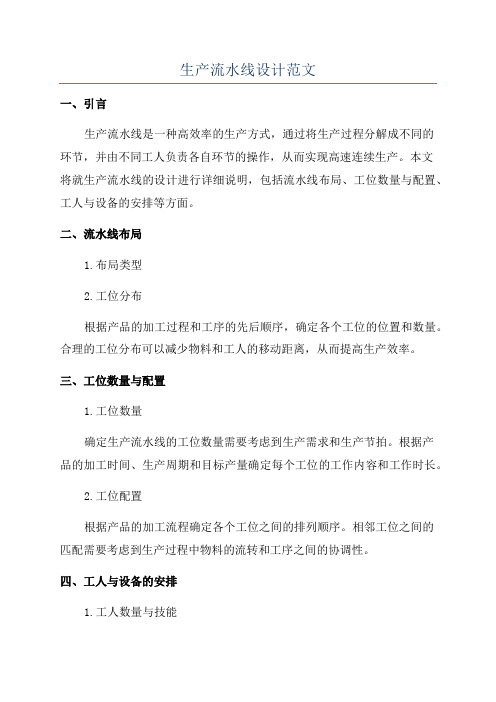
生产流水线设计范文一、引言生产流水线是一种高效率的生产方式,通过将生产过程分解成不同的环节,并由不同工人负责各自环节的操作,从而实现高速连续生产。
本文将就生产流水线的设计进行详细说明,包括流水线布局、工位数量与配置、工人与设备的安排等方面。
二、流水线布局1.布局类型2.工位分布根据产品的加工过程和工序的先后顺序,确定各个工位的位置和数量。
合理的工位分布可以减少物料和工人的移动距离,从而提高生产效率。
三、工位数量与配置1.工位数量确定生产流水线的工位数量需要考虑到生产需求和生产节拍。
根据产品的加工时间、生产周期和目标产量确定每个工位的工作内容和工作时长。
2.工位配置根据产品的加工流程确定各个工位之间的排列顺序。
相邻工位之间的匹配需要考虑到生产过程中物料的流转和工序之间的协调性。
四、工人与设备的安排1.工人数量与技能根据生产流水线的设计,确定所需的工人数量和技能水平。
根据各个工位的工作内容和难易程度,确定不同工人在不同工位的分配比例。
2.设备选择与安装根据生产流水线的要求,选择合适的设备。
设备的性能和质量对整个流水线的效率和稳定性有重要影响。
严格按照设备的安装要求进行安装和调试。
五、生产效率的提高与控制1.定时维护与保养定期对设备进行维护和保养,确保设备的正常运转。
定期更换磨损严重的零部件,避免设备故障对生产造成影响。
2.生产过程的监督与管理建立严格的生产管理制度,监督生产过程中各个环节的运行情况。
对生产情况进行及时记录和分析,及时发现问题并采取措施进行调整和优化。
六、风险与安全措施在设计生产流水线的过程中,需要考虑到生产过程中可能出现的风险和安全隐患,并采取相应的安全措施,确保工作人员的身体健康和生产环境的安全。
七、总结本文介绍了生产流水线的设计要点,包括流水线布局、工位数量与配置、工人与设备的安排等方面。
通过合理的设计和管理,生产流水线可以提高生产效率,降低生产成本,提高产品质量。
同时,需要注意安全风险和工人健康的保障,确保生产过程的可持续发展。
学习生活中的流水线例子
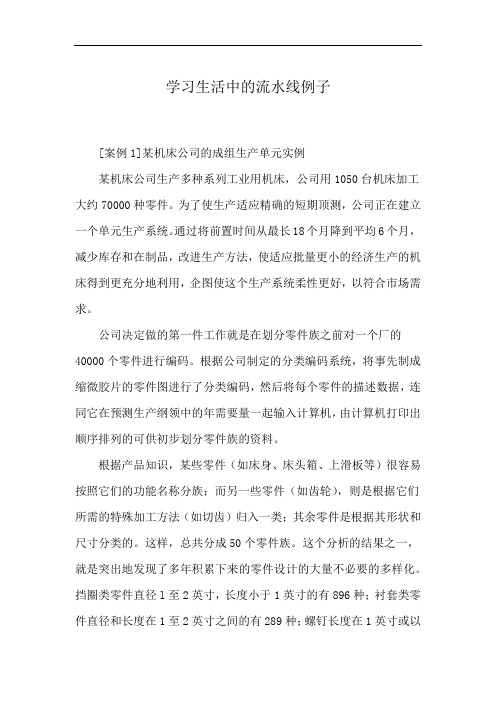
学习生活中的流水线例子[案例1]某机床公司的成组生产单元实例某机床公司生产多种系列工业用机床,公司用1050台机床加工大约70000种零件。
为了使生产适应精确的短期顶测,公司正在建立一个单元生产系统。
通过将前置时间从最长18个月降到平均6个月,减少库存和在制品,改进生产方法,使适应批量更小的经济生产的机床得到更充分地利用,企图使这个生产系统柔性更好,以符合市场需求。
公司决定做的第一件工作就是在划分零件族之前对一个厂的40000个零件进行编码。
根据公司制定的分类编码系统,将事先制成缩微胶片的零件图进行了分类编码,然后将每个零件的描述数据,连同它在预测生产纲领中的年需要量一起输入计算机,由计算机打印出顺序排列的可供初步划分零件族的资料。
根据产品知识,某些零件(如床身、床头箱、上滑板等)很容易按照它们的功能名称分族;而另一些零件(如齿轮),则是根据它们所需的特殊加工方法(如切齿)归入一类;其余零件是根据其形状和尺寸分类的。
这样,总共分成50个零件族。
这个分析的结果之一,就是突出地发现了多年积累下来的零件设计的大量不必要的多样化。
挡圈类零件直径l至2英寸,长度小于1英寸的有896种;衬套类零件直径和长度在1至2英寸之间的有289种;螺钉长度在1英寸或以下的有347种;盖板类零件10英寸见方1英寸厚或以下的有74种,这些盖板每种都要求不同的木模和钻模。
于是,公司进行了零件标准化的工作。
建立了推荐的尺寸和公差,设计了标准的钻模、夹具和刀具装置。
据估计,使零件多样化减少25%,就可以使通过生产单元的零件批数减少,批量增大,从而增加生产10%。
例如,有15种盖板可以立即用5种代替,这五种盖板只需用5个木模和4个钻模。
接下来,公司制定了一个计算机程序利用现有生产数据来分析各个初步划分的零件族中每个零件的工艺流程,打印出矩阵表,表示出每个零件的工艺流程、所用机床以及每台机床的年负荷量。
打印出来的资料表明:公司多年来设计了大量多种多样的工艺过程。
3生产线案例
流水生产线规划[案例1]福特的汽车装配生产线亨利·福特(1863—1974)于1903年创建福特汽车公司。
20世纪初,福特的工厂创造了工业革命以来最先进的生产技术,他的T型汽车创造了每分钟出产6辆的历史最高纪录。
福特创立的流水线生产方法称为大规模工业化生产的基本模式,推动了工业革命的进程。
20世纪初,美国汽车行业的做法是面向较为富有的阶层,汽车因为价格昂贵成为了只供富人消费的奢侈品。
当时福特汽车公司推出的新型汽车也都是“奢华型”产品:车体笨重,多为定制,价格昂贵,非一般人财力可以企及。
在这种社会环境中,福特萌发了一个愿望。
他希望让美国所有的普通家庭都能买得起他的汽车。
福特意识到,为了实现他的理想,必须最大限度地降低产品的生产成本和价格。
而要降低成本,就要大幅度提高汽车的产量。
1906年7月,福特宣布公司的发展战略,他说:“本公司致力于生产标准化、规格同意、价格低廉、质量优越、能为广大公众接受的产品。
大家的眼睛不要光盯着富人的口袋,全美国的富人本来就少,况且有多少汽车商都在打富人的主意。
我们想要生存,要获得大的发展,只有另辟蹊径,在社会公众中寻找市场,在中等收入阶层找到我们的市场。
”福特强调标准化的意义,他说:“生产一种设计标准化的汽车是我们今后的主要任务。
”福特的发展战略赢得了公司董事们的一致赞同。
福特公司的这一举措立竿见影。
1906年下半年到1907年年底,在美国经济开始滑入低谷的情况下,福特汽车公司却取得了惊人的业绩,盈利达125万美元,其产品在市场上供不应求。
公司的销售业绩证明,产品价格越低,利润反而越大。
因此,福特公司当时生产统一规格、价格低廉、能为普通大众接受的汽车是明智之举。
在这种背景下,1908年3月19日,福特汽车公司的新产品:T型汽车投产。
该产品很快就收到了普通大众的广泛欢迎。
当时T型车的市场销售价格为每辆3200美元,价格仍然处于很高的水平。
但福特不断对其汽车生产过程进行革新,连续化、专业化的生产方式渐渐从部件供应线的应用转移向最后的组装。
月饼制作流水线分析设计
1 流水线背景图 2 月饼制作流程图 3 原始流水线 4 5W1H分析 5 改善后流水线
目录
背景介绍
月饼制作流程图
• 本车间月饼制作过程采用传统的粗 略节拍流水线,各工序的加工时间 与节拍相差很大,为充分地利用人 力、物力,只要求流水线每经过一 个合理的时间间隔,生产等量的制 品,而每道工序并不按节拍进行生 产。
减少等待时间
加工 团面、捏合、称重三道工序是否可以合并
搬运
团馅、团面是否可以更换顺序以减少搬运距 离
检查 是否能提高工人技术减少称重次数
储存
是否可以增加散热器以减少晾晒时间,缩短 储存时间
改善方案
• 通过研究分析: 1、改变了工厂的布局; 2、改变流水线的形状为U型,增加一条流水
线; 3、合并了捏合、称重两道工序; 4、增加一台烤箱,以减少等待时间。
改善后流水线各工序时间(车)
• 进行工序的改进之后,再分析工序3、4、5、6、7、8、9 的节拍。
• 一条流水线的计划日产量为10车,一班制工作,每班10小 时,计划废品率为3%,时间有效利用系数为90%。
• 1、流水线的节拍为: r=FK/N=10*60*90%/[10/(1-3%)]=52.38(mi水线的负荷系数: • K3=S3/Se3=0.095 • K4=S4/Se4=0.478 • K5=S5/Se5=0.351 • K6=S6/Se6=0.153 • K7=S7/Se7=0.086 • K8=S8/Se8=0.057 • 则整个流水线的负荷系数为:
流水线设计例子
,因此决定采用方案2-2。
5
方案3-1组合(③,⑧),
6
10
7
5 9
Te31 5 3 8
1
5
5
Sk31 3 46 10 8 8/10 5
2
3
11
方案3-2组合(⑦),
6
3
5
8
8
10
Te32 6
4
Sk32 3 46 10 8 6/10 6
Si ti R
各工序设备负荷系数计算公式为:
Ki Si Sei
总设备负荷系数计算公式为:
K Si Sei 4.6/ 5 0.92
I
II
III
设备数Si
1
0.7
1
实际设备数Sei
1
1
1
IV
V
1
0.9
1
1
设备利用率
1
0.7
1
1
0.9
2020/3/2
15
4.安排合适员工人数
在流水生产线上安排员工时主要考虑以下几方面 因素:每个岗位工作时同时所需要人数、工作班次、 检验人员数、管理人员和辅助人员数,整条流水生 产线的员工人数是所有岗位员工人数之和。
2020/3/2
17
6.流水生产线的平面布置
流水生产线的平面布置应当有利于员工操作,制品运输路线 最短,生产空间充分利用。同时,要考虑流水生产线之间的相互 衔接,从而使所有流水生产线的布置符合产品生产过程的流程。
2020/3/2
18
• 练习
– 一装配线计划每小时装配50件产品,每小时用于生 产的时间是53分钟。
生产流水线设计方案
生产流水线设计方案1. 引言生产流水线是一种高效的生产工艺,它可以将一个复杂的制造过程分解为多个简单的工序,并通过流水线的传送带使得产品在各个工序之间连续流动,从而大大提高生产效率和产品质量。
本文将介绍一个生产流水线的设计方案,包括流程规划、设备选择、工序安排等内容。
2. 流程规划在设计生产流水线之前,我们首先需要对生产过程进行流程规划。
这包括确定产品的生产步骤、每个工序的工作内容和先后顺序等。
2.1 产品生产步骤我们以汽车生产为例,假设汽车的生产步骤包括:车身焊接、油漆喷涂、总装等。
2.2 工序工作内容在每个工序中,我们需要确定具体的工作内容,以便后续进行设备选择和工序安排。
例如,在车身焊接工序中,需要确定焊接接缝的位置、焊接方法等。
2.3 工序先后顺序确定各个工序之间的先后顺序是非常重要的,以确保整个生产过程的顺畅进行。
例如,在汽车生产中,车身焊接应该在油漆喷涂之前进行,以避免焊接对油漆的影响。
3. 设备选择在生产流水线中,设备的选择对整个生产过程的效率和质量有着重要的影响。
在选择设备时,我们需要考虑以下几个方面:3.1 自动化程度自动化程度高的设备可以减少人工操作,提高生产效率,并减少人为错误的发生。
在汽车生产的例子中,可以选择自动化的焊接机器人来代替人工焊接。
3.2 设备的稳定性和可靠性稳定性和可靠性是设备选择的重要考虑因素。
不稳定的设备容易导致生产出现中断,而不可靠的设备可能需要大量的维修和维护,增加生产成本。
因此,在选择设备时,我们需要对设备的质量和性能进行充分的评估。
3.3 设备的适用性设备的适用性是指设备是否能够满足具体的生产需求。
在选择设备时,我们需要考虑生产的规模、产品的特点以及工艺的要求等因素。
4. 工序安排在确定了流程规划和设备选择之后,我们需要对各个工序进行合理的安排,以便实现高效的生产。
4.1 平衡生产速度在生产流水线中,不同工序的处理速度可能存在差异。
为了避免生产过程中的积压或拖延,我们需要对生产速度进行平衡。
- 1、下载文档前请自行甄别文档内容的完整性,平台不提供额外的编辑、内容补充、找答案等附加服务。
- 2、"仅部分预览"的文档,不可在线预览部分如存在完整性等问题,可反馈申请退款(可完整预览的文档不适用该条件!)。
- 3、如文档侵犯您的权益,请联系客服反馈,我们会尽快为您处理(人工客服工作时间:9:00-18:30)。
第一步:计算重新组合安排第1个工序 方案1-1 组合(①,②,⑤), Te11 6 2 1 9 方案1-2 组合(①,②,⑥),
S k11 1 46 9 / 10 5
S k12 1 46 10 / 10 5
Te12 6 2 2 10
5
9 5 8 3 11 5 10
7
最小工序数超过5,说 明此时继续走下去不是 很合适。需要尝试新途 径。
8 4 5
8
2018/11/21
7
方案2-1组合(③,⑤)
Te21 5 1 6
Sk 21 2 46 10 6 / 10 5
6 10 1 2 6 7 5 3 7 4 1 5
T 有效时间 300 2 8 0.95 60 273600
(分钟)
计划期节拍为:
2018/11/21
R
T有效时间 Q
273600 7.3 (分/件) 36000
1
R
2.工序同期化
工序同期化是通过技术组织措施调整流水线各工序时间, 使各工序时间与节拍相等或成倍数。它是组织连续流水线的必 要条件。 具体装配线平衡处理步骤如下:首先确定装配流水线节拍 R , 再者计算装配线上需要的最少工作地数Sm,最后重新组织安排 工序;在对工步进行重新组合安排工序时应按以下规则进行分 配:①保证个工步之间的先后顺序。②每个工序分配到的工步 作业时间不能大于节拍。③各工序的作业时间应尽量接近或等 于节拍。④应使工序数目 S尽量少。⑤在相同工序数时以新安 排工序时间越接近节拍为优先选择。⑥全部工步合理组合划分 为工序,且各工序的时间损失最少和比较均匀。
2018/11/21
,因此决定采用方案2-2。
5
方案3-1组合(③,⑧),
Te31 5 3 8
6 10 1 2 6 8 4 5 7 5 3 3 8
5
9 5 11 5 10
S k 31 3 46 10 8 8 / 10 5
方案3-2组合(⑦),
Te32 6
例题4-2 某流水线计划年产某产品 36000件,该流水线 每天工作两班,每班 8小时,全年工作天数为 300 天, 每天工作时间有效利用系数为 0.95。(1)试计算该流 水生产线的节拍。(2)若在加工工艺上尚存在某些质 量问题,目前在生产过程中仍有一定的废品发生;如 果把废品率定为 5.0%,则该流水生产线的节拍应是多 少? 解:①计划期内有效的工作时间为:
2018/11/21 2
现通过举例来说明处理过程。 【例】节拍为10分/件,各工步之间的关系见图4-10;试 开展工序同期化处理。
2018/11/21
3
解:
T t i 6 2 5 7 1 2 6 3 5 5 4 46
i 1
11
T 46 S 最少工序数为: min R 10 4.6 5
6
5
8
5
7
③,⑧
⑦
③,⑨
④
5
8
6
6
5
10
④,⑧
6
7
5
⑩,⑾
10
5
2018/11/21
9
12
工序同期化小结:
(1)计算处理工序同期化安排的最少工序数为: 式中,方括号T R 为大于等于T / R 最小整数 (2)通过采用公式4-3计算预期工序数,并与最少工序数 Smin 比较:
5
9 5 11 3 8 5 10
方案2-2组合(④,⑤),
Te22 7 1 8
S k 22 2 46 10 8 / 10 5
方案2-3组合(⑤,⑦),
Te23 6 1 7
Sk 23 2 46 10 7 / 10 5
尝试采用方案2-3。
S k 32 3 46 10 8 6 / 10 6
由于
S k 31 < S k 32
,因此决定采用方案3-1。
2018/11/21
6
6
方案4-1组合(⑦),
Te41 6
Sk 41 4 46 10 8 8 6 / 10 6
10 1 2 6
Te22 7 1 8
S k 22 2 46 10 8 / 10 5
方案2-3组合(⑤,⑦),
Te23 6 1 7
Sk 23 2 46 10 7 / 10 5
Sk 21 Sk 22 Sk 23 Te21 Te23 Te22
由于 S k 31 = S k 32
7 4
Te 32 < Te 31,因此决定采用方案3-1。
2018/11/21
9
7
方案4-1组合(④,⑧),
7 10 1 2 6 5 5 10 3 9 7 4 11 3 8 5 10
Te 41 7 3 10
S k 41 4 46 10 7 10 10 / 10 5
2018/11/21 8
7
方案3-1组合(③,⑨),
Te31 5 5 10
S k 31 3 46 10 7 10 / 10 5
7 10 1 2 6 5 5 3 5 9 3 8 5 10
5 11
方案3-2组合(④),
Te32 7
S k 32 3 46 10 7 7 / 10 5
2018/11/21
10
7
7 方案5-1由 第10工步和第11工步组合而成,计算
Te5 为9和 S k 5 为5。
10 1 2 6
5 10 3 9 10 4 8 5 10
4 11
以上整个解决问题的过程都可以用以下图来表示:
2018/11/21
11
全部工步
①②⑤
①②⑥
5
9
③,⑤
5
④,⑤
10
⑤,⑦
5
Sk11 Sk12
2018/11/21
Te11 Te12
因此决定采用方案1-2。
4
方案2-1组合(③,⑤)
Te21 5 1 6
Sk 21 2 46 10 6 / 10 5
6 10 1 2 6 7 5 3 7 4 1 5
5
9 5 11 3 8 5 10源自方案2-2组合(④,⑤),