液压油缸检测报告2-1
液压油缸出厂检验报告

实验、泄漏实验、行程检测、外观检测等出厂实验,实验结果符合要求,质量合格,准予出厂。
备注:“√”为符合产品指标值。
测量时油液温度: 45℃
检验员:
审核:
批准:
1430 21 M22*1.5 螺纹连接
出厂编号
GD20120151-GD20120153
出厂时间
2012.3.20
实验测量值
序号 实验项目
产品指标值
被试产品编号
1
2
3
2012.3.28 检01 3
结果 报告
备注
1 试运行 全行程往复运动数次,完全排除缸内空气。 √
√
√
√
2
起动压力 特性实验
压力逐渐升高,记录下最低起动压力。
2
2
2√Leabharlann 3耐压实验1.5倍的工作压力,保压2min,无渗漏、 变形、松动。
无
无
无
√
低压0.5Mpa(缸径>32mm)或1Mpa (缸径≤32mm)往复3次,停留10s,
各部分无渗漏。(低压泄漏)
无
无
无
√
4 泄漏实验
加压到工作压力,经活塞至未加压腔无 泄漏。(内泄漏)
无
无
无
√
起动、耐压、泄漏实验时,活塞杆密封
********厂
液压油缸出厂检验报告
报告编号:2012032
产品名称
前门油缸 型号规格 GGK1-90/50*1430
检验日期
订货单位
检验员编号
检验根据
GB/T 15622-2005《液压缸实验方法》
检验数量
缸径(mm)
90
杆径(mm)
50
液压油缸压降测试标准
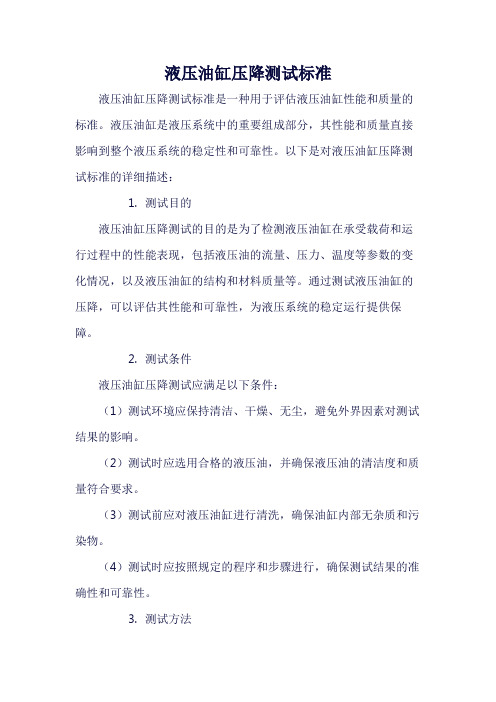
液压油缸压降测试标准液压油缸压降测试标准是一种用于评估液压油缸性能和质量的标准。
液压油缸是液压系统中的重要组成部分,其性能和质量直接影响到整个液压系统的稳定性和可靠性。
以下是对液压油缸压降测试标准的详细描述:1.测试目的液压油缸压降测试的目的是为了检测液压油缸在承受载荷和运行过程中的性能表现,包括液压油的流量、压力、温度等参数的变化情况,以及液压油缸的结构和材料质量等。
通过测试液压油缸的压降,可以评估其性能和可靠性,为液压系统的稳定运行提供保障。
2.测试条件液压油缸压降测试应满足以下条件:(1)测试环境应保持清洁、干燥、无尘,避免外界因素对测试结果的影响。
(2)测试时应选用合格的液压油,并确保液压油的清洁度和质量符合要求。
(3)测试前应对液压油缸进行清洗,确保油缸内部无杂质和污染物。
(4)测试时应按照规定的程序和步骤进行,确保测试结果的准确性和可靠性。
3.测试方法液压油缸压降测试的方法包括以下步骤:(1)将液压油缸安装在测试台上,连接好液压管路和测量仪器。
(2)向液压油缸输入规定的压力和流量,并记录下此时的油压和流量值。
(3)在液压油缸运行一段时间后,逐渐增加负载,并记录下不同负载下的油压和流量值。
(4)在测试过程中,应按照规定的程序和步骤进行,确保测试结果的准确性和可靠性。
4.测试标准液压油缸压降测试的标准包括以下内容:(1)液压油缸的压降值应符合设计要求,不得超过规定值。
(2)在相同负载条件下,液压油缸的压降值应保持稳定,变化幅度不应超过规定范围。
(3)液压油缸在运行过程中,不应出现异常噪声和振动。
(4)液压油缸的结构和材料质量应符合设计要求,不得存在影响性能和安全的质量问题。
5.测试结果分析通过对液压油缸压降测试结果的统计分析,可以得出以下结论:(1)如果液压油缸的压降值符合设计要求,且在相同负载条件下保持稳定,则认为该液压油缸的性能和质量较好,能够满足使用要求。
(2)如果液压油缸的压降值超过规定值,或在不同负载条件下变化幅度较大,则认为该液压油缸的性能和质量存在问题,需要进行检修或更换。
液压实验报告_5
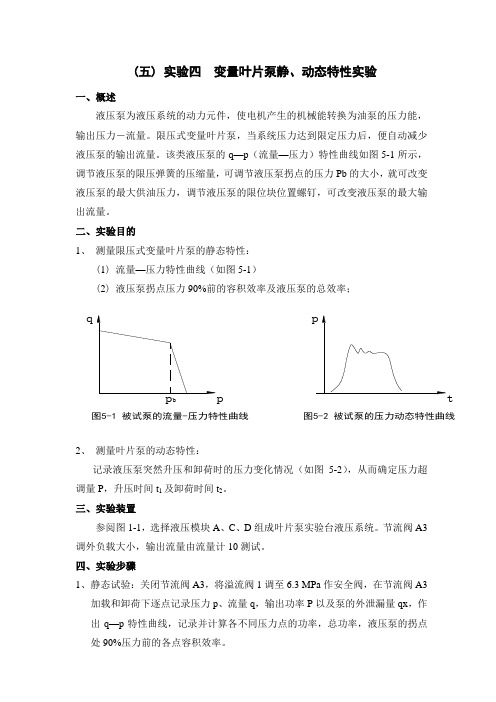
(五) 实验四变量叶片泵静、动态特性实验一、概述液压泵为液压系统的动力元件,使电机产生的机械能转换为油泵的压力能,输出压力-流量。
限压式变量叶片泵,当系统压力达到限定压力后,便自动减少液压泵的输出流量。
该类液压泵的q—p(流量—压力)特性曲线如图5-1所示,调节液压泵的限压弹簧的压缩量,可调节液压泵拐点的压力Pb的大小,就可改变液压泵的最大供油压力,调节液压泵的限位块位置螺钉,可改变液压泵的最大输出流量。
二、实验目的1、测量限压式变量叶片泵的静态特性:(1)流量—压力特性曲线(如图5-1)(2)液压泵拐点压力90%前的容积效率及液压泵的总效率;2、测量叶片泵的动态特性:记录液压泵突然升压和卸荷时的压力变化情况(如图5-2),从而确定压力超调量P,升压时间t1及卸荷时间t2。
三、实验装置参阅图1-1,选择液压模块A、C、D组成叶片泵实验台液压系统。
节流阀A3调外负载大小,输出流量由流量计10测试。
四、实验步骤1、静态试验:关闭节流阀A3,将溢流阀1调至6.3 MPa作安全阀,在节流阀A3加载和卸荷下逐点记录压力p、流量q,输出功率P以及泵的外泄漏量qx,作出q—p特性曲线,记录并计算各不同压力点的功率,总功率,液压泵的拐点处90%压力前的各点容积效率。
2、将实验数据输入计算机相应表格中,由计算机显示及打印流量—压力,功率—压力,液压泵效率—压力特性曲线或将实验数据填入下表通过计算绘制相应的曲线。
3、压力动态响应试验:(1) 将节流阀A3调节到一定的开度与压力;(2) 按电磁铁AD1的得电按钮,使系统突然加载;系统的压力波形由压力传感器5和功率放大等单元转换成电压波形,由计算机记录与绘制动态压力上升响应曲线。
(3) 按AD1复位按钮,使系统突然卸荷,系统的压力波形由压力传感器5和功率放大等单元转换成电压波形,由计算机记录与绘制动态压力卸荷响应曲线。
五、数据测试1、压力P :用压力表P1和压力传感器5测量;2、流量q :采用安置在实验台面板上的椭圆齿轮流量计10和秒表测量(流量计指针每转一圈为10升)或流量数显表读出;3、外泄漏量qx :用秒表测tx 时间内小量杯11的容积(AD3得电);4、输入功率P :用功率表测量电机输入功率P1(安置在实验台面板上)。
液压油缸质量检验规范

液压油缸质量检验规范
前言
本规范用于液压油缸的质量检验,旨在保证液压油缸的质量,提高产品的可靠性和安全性。
检验标准
1. 外观检验
液压油缸的外观应该无裂纹、无变形、无划痕、表面无锈蚀,在装配后应该无泄漏。
2. 尺寸检验
液压油缸的内径、外径、活塞杆直径、活塞杆长度应该符合设计要求。
3. 强度检验
液压油缸在压力测试时,应该承受规定压力2倍的测试压力,无破裂、变形和泄漏等现象。
4. 密封性检验
液压油缸在压力测试时,应该保持规定压力10分钟,没有任何泄漏现象,且在经过密封性试验后活塞杆不会出现损坏。
检验方法
1. 外观检验
使用肉眼或放大镜仔细检查液压油缸表面,如果发现异常,应该进行更加细致的检查。
2. 尺寸检验
使用专业的检测设备,比如游标卡尺、外径千分尺、内景千分尺等,测量液压油缸的相关尺寸。
3. 强度检验
沿对称轴向液压油缸施加试验压力,在压力测试过程中观察液压油缸的变形情况和是否有漏油现象。
4. 密封性检验
涂抹液压油缸需要检验的密封部位,将液压油缸放入水中进行压力测试,观察是否有气泡冒出,检查活塞杆样子并观察密封性。
结论
液压油缸的检验可以保障其质量,减少使用过程中出现的故障,确保液压油缸能够在高压下稳定运行,提高设备的工作效率和安全性。
液压实验报告

一、液压传动认识实验1实验目的(一)理解液压系统的基本组成。
(二)理解液压系统基本元器件的功能。
(三)理解液压传动的基本形式。
2实验要求由实验教师对以简单液压传动系统的结构、工作原理及性能结合实物、剖开的实物、各种阀模型及示教板等进行讲解,充分理解掌握课堂内容和如下内容。
要求同学掌握的内容:理解一般液压系统中传动介质的特点及选用原则;理解一般液压系统中能量转化装置及执行元件的特点;理解液压传动中方向控制、流量控制、压力控制的基本元件及特点理解液压千斤顶的工作原理;理解手动液压钳的工作原理。
3实验内容液压系统的基本组成:一个完整的液压系统由五个部分组成,即动力元件、执行元件、控制元件、辅助元件和液压油。
液压系统基本元器件的功能:1.动力元件动力元件的作用是将原动机的机械能转换成液体的压力能,指液压系统中的油泵,它向整个液压系统提供动力。
液压泵的结构形式一般有齿轮泵、叶片泵和柱塞泵。
2.执行元件执行元件(如液压缸和液压马达)的作用是将液体的压力能转换为机械能,驱动负载作直线往复运动或回转运动。
3.控制元件控制元件(即各种液压阀)在液压系统中控制和调节液体的压力、流量和方向。
根据控制功能的不同,液压阀可分为压力控制阀、流量控制阀和方向控制阀。
压力控制阀又分为益流阀(安全阀)、减压阀、顺序阀、压力继电器等;流量控制阀包括节流阀、调整阀、分流集流阀等;方向控制阀包括单向阀、液控单向阀、梭阀、换向阀等。
根据控制方式不同,液压阀可分为开关式控制阀、定值控制阀和比例控制阀。
4.辅助元件辅助元件包括油箱、滤油器、油管及管接头、密封圈、快换接头、高压球阀、胶管总成、测压接头、压力表、油位油温计等。
5.液压油液压油是液压系统中传递能量的工作介质,有各种矿物油、乳化液和合成型液压油等几大类。
液压千斤顶:1—杠杆手柄2—小油缸3—小活塞4,7—单向阀5—吸油管6,10—管道—大活塞9—大油缸11—截止阀12—油箱图1-1 是液压千斤顶的工作原理图。
油缸出厂检验报告
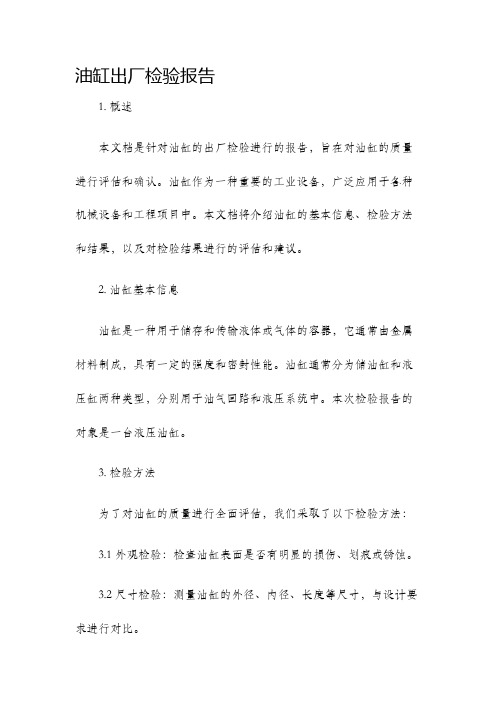
油缸出厂检验报告
1. 概述
本文档是针对油缸的出厂检验进行的报告,旨在对油缸的质量进行评估和确认。
油缸作为一种重要的工业设备,广泛应用于各种机械设备和工程项目中。
本文档将介绍油缸的基本信息、检验方法和结果,以及对检验结果进行的评估和建议。
2. 油缸基本信息
油缸是一种用于储存和传输液体或气体的容器,它通常由金属材料制成,具有一定的强度和密封性能。
油缸通常分为储油缸和液压缸两种类型,分别用于油气回路和液压系统中。
本次检验报告的对象是一台液压油缸。
3. 检验方法
为了对油缸的质量进行全面评估,我们采取了以下检验方法:
3.1 外观检验:检查油缸表面是否有明显的损伤、划痕或锈蚀。
3.2 尺寸检验:测量油缸的外径、内径、长度等尺寸,与设计要求进行对比。
3.3 压力测试:在设定的压力下,对油缸进行静态和动态负荷测试,观察其变形和漏液情况。
3.4 密封性检验:通过注入水或气体,检测油缸的密封性能,观察是否有漏液或漏气现象。
3.5 功能检验:安装油缸到相应设备中,测试其在实际工作环境中的功能和性能。
4. 检验结果
根据以上检验方法,我们对油缸进行了全面的检验,并得出以
下结果:
4.1 外观检验结果:油缸表面无明显损伤、划痕或锈蚀。
4.2 尺寸检验结果:油缸的外径、内径、长度等尺寸符合设计要求。
4.3 压力测试结果:油缸在设定的压力下未出现明显变形和漏液现象。
4.4 密封性检验结果:油缸密封性良好,未出现漏液或漏气现象。
液压油缸泄露实验标准

公称压力×2.5%
2、活塞式单作用油缸最低启动压力不得大于下表:
公称压力
活塞密封形式
活塞杆密封形式
除V型外
V型
≤16MPa
V型
0.5
0.75
除V型外
0.35
0.5
>16MPa
V型
公称压力×3.5%
公称压力×9%
除V型外
公称压力×3.4%
公称压力×6%
3、柱塞式单作用油缸最低启动压力不得大于下表:
液压油缸泄漏实验检测标准
1、双作用油缸最低启动压力不得大于下表:
公称压力
活塞密封形式
活塞杆密封形式
除V型外
V型
≤16MPa
V型
0.5
0.75
O、U、Y、X、组合密封
0.3
0.45
活塞环
0.1
0.15
>16MPa
V型
公称压力×6%
公称压力×9%
O、U、Y、X、组合密封
公称压力×4%
公称压力×6%
活塞环
内泄漏量mL/min
缸内径D mm
内泄漏量mL/min
40
0.03
125
0.28
50
0.05
140
0.30
63
0.08
160
0.50
80
0.13
180
0.63
90
0.15
200
0.70
100
0.20
220
1.00
110
0.22
250
1.10
注:使用组合密封时,允许内泄漏量为规定值的2倍
6、单作用油缸内泄漏量不得大于:
液压站出厂检验报告
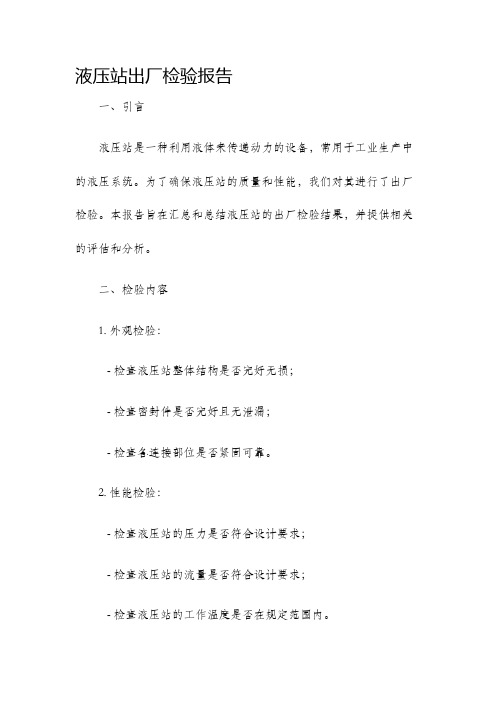
液压站出厂检验报告一、引言液压站是一种利用液体来传递动力的设备,常用于工业生产中的液压系统。
为了确保液压站的质量和性能,我们对其进行了出厂检验。
本报告旨在汇总和总结液压站的出厂检验结果,并提供相关的评估和分析。
二、检验内容1. 外观检验:- 检查液压站整体结构是否完好无损;- 检查密封件是否完好且无泄漏;- 检查各连接部位是否紧固可靠。
2. 性能检验:- 检查液压站的压力是否符合设计要求;- 检查液压站的流量是否符合设计要求;- 检查液压站的工作温度是否在规定范围内。
三、检验结果1. 外观检验结果:根据检验,液压站的外观结构完好无损,密封件完好,各连接部位紧固可靠。
2. 性能检验结果:- 压力检验结果:液压站的压力符合设计要求,平均压力稳定在规定范围内;- 流量检验结果:液压站的流量符合设计要求,并且流量稳定;- 温度检验结果:液压站的工作温度在规定范围内,无异常情况。
四、评估和分析1. 外观检验评估:液压站的外观结构完好无损,密封件完好,各连接部位紧固可靠,表明液压站在运输和安装过程中未受到损坏,各部件安装正确。
2. 性能检验评估:- 压力检验评估:液压站的压力符合设计要求,表明液压站能够产生足够的压力来驱动液压系统;- 流量检验评估:液压站的流量符合设计要求,表明液压站能够提供足够的液压功率;- 温度检验评估:液压站的工作温度在规定范围内,表明液压站能够在正常运行条件下保持稳定的温度。
五、结论通过出厂检验,我们可以得出以下结论:液压站的外观结构完好无损,各部件安装正确,密封件完好,各连接部位紧固可靠。
性能检验结果显示液压站的压力、流量和工作温度符合设计要求,能够提供稳定的液压功率和工作温度。
最后,我们建议购买液压站的用户在安装和使用前仔细阅读并遵守操作手册中的要求,以确保液压站能够稳定、高效地运行,并延长其使用寿命。
如有任何问题或需要进一步咨询,请随时与我们联系。
- 1、下载文档前请自行甄别文档内容的完整性,平台不提供额外的编辑、内容补充、找答案等附加服务。
- 2、"仅部分预览"的文档,不可在线预览部分如存在完整性等问题,可反馈申请退款(可完整预览的文档不适用该条件!)。
- 3、如文档侵犯您的权益,请联系客服反馈,我们会尽快为您处理(人工客服工作时间:9:00-18:30)。
日期:2014年10月21日
液压油缸检测报告
产品名称:工程机械液压缸
规格型号:HSG63/35-80
产品数量:16只
试验项目
试验方法
试验要求
检验结果
备注
试运转
液压缸在空负载工况下全行程往复动作5次以上
运转正常
正常
不正常□
最低启动压力
空载工况下,液压缸无杆腔通入液压油,溢流阀从零开始逐渐升压,观察压力表,记录液压缸活塞杆在启动时的最低启动压力
0.3MPa
正常
不正常□
耐压试验
将液压缸的活塞分别停留在行程两端。调节溢流阀使试验腔的压力为额定压力的1.25倍保压5min
全部零件均不得有破坏或永久变形等异常现象
正常
不正常□
内泄漏
液压缸的活塞分别固定在行程的两端,调节溢流阀,使液压缸的试验腔为额定压力,测量另一腔出油口处泄漏量
1.0~2.2ml/min
正常
不正常□
外渗漏
在检查内泄漏和耐压试验Байду номын сангаас观察活塞杆处及其它结合面渗油情况
在耐久性试验的连续运转中测量活塞杆处外渗漏量
活塞杆处无渗油,缸筒焊接无渗油
有□
无
行程
使液压缸的活塞分别停留在行程的两端位置,测量全行程长度
80±0.5mm
正常
不正常□
经检验,此液压缸各项技术指标均符合国家标准GB/T 15622-2005《中高压液压缸试验方法》的规定,质量合格