零件质量的自动化检测系统设计
基于机器视觉的电子元器件检测系统设计

基于机器视觉的电子元器件检测系统设计一、引言随着电子行业的迅速发展,电子元器件的质量和可靠性对产品的性能和寿命至关重要。
为了提高电子元器件的生产质量和效率,设计一种基于机器视觉的电子元器件检测系统非常必要。
本文旨在探讨基于机器视觉的电子元器件检测系统的设计原理、关键技术和实现方法,以及该系统在电子元器件生产过程中的应用和优势。
二、设计原理基于机器视觉的电子元器件检测系统主要通过获取电子元器件的图像数据,利用图像处理和分析的方法,对元器件的质量进行检测和评估。
具体设计原理如下:1. 图像采集通过相机等设备对电子元器件进行图像采集,将元器件的外观和内部细节转化为数字图像数据。
这些图像数据将作为后续图像处理和分析的基础。
2. 图像预处理对采集到的图像数据进行预处理,包括灰度化、滤波、去噪等操作,以提高后续处理的准确性和效率。
3. 特征提取与分析通过图像处理和计算机视觉算法,对元器件图像中的特征进行提取和分析。
这些特征可能包括元器件的形状、尺寸、颜色、缺陷等,通过与标准样本进行比对,判断元器件的质量。
4. 判定与分类根据提取的特征和分析结果,对元器件进行判定和分类。
合格的元器件将被送往下一工序,不合格的元器件将被剔除或进一步分析。
三、关键技术基于机器视觉的电子元器件检测系统设计涉及到多个关键技术,下面重点介绍其中几个关键技术:1. 特征提取算法特征提取是实现元器件质量检测的基础,需要采用适合的算法对元器件图像进行特征提取。
常用的特征提取算法包括边缘检测、角点检测、轮廓提取等。
2. 图像分类模型通过对元器件图像进行特征提取和学习,建立图像分类模型,用于对元器件进行判定和分类。
常用的图像分类模型有支持向量机(SVM)、卷积神经网络(CNN)等。
3. 实时性处理对于电子元器件生产过程中的在线检测,系统需要具备快速的实时处理能力。
为了提高系统的实时性,可以采用并行处理、GPU加速等技术手段。
四、系统应用和优势基于机器视觉的电子元器件检测系统在电子元器件生产过程中具有广泛的应用和重要的优势:1. 自动化检测相比传统的人工检测方式,机器视觉系统能够实现电子元器件的自动化检测,提高生产效率和减少人力成本。
基于图像处理与分析的自动化质检系统设计与优化

基于图像处理与分析的自动化质检系统设计与优化图像质检在现代制造业中扮演着重要的角色,其通过使用图像处理和分析技术,可以自动检测并判断产品的外观质量。
本文将讨论基于图像处理与分析的自动化质检系统的设计与优化,旨在改进质检过程的效率和准确性。
首先,设计一个基于图像处理与分析的自动化质检系统需要考虑以下几个关键因素。
首先是图像采集设备的选择,这是确保所获得的图像质量和分辨率足够高的重要因素。
合适的图像采集设备应能够捕捉产品表面的细节和纹理,并产生高质量的数字图像。
常用的图像采集设备包括高分辨率相机和光学镜头,通过选择适当的设备,可以保证图像质检系统的准确性和可靠性。
其次,图像处理算法的选择也是自动化质检系统设计的关键。
图像处理算法可以用来预处理图像数据,并从中提取有用的特征。
例如,通过应用滤波算法可以降噪图像,提高图像质量;边缘检测算法可以用来识别产品的边界;形状检测算法可以帮助系统检测产品的形状和大小等。
根据不同的质检要求,选择合适的图像处理算法可以提高系统的准确性和效率。
除了图像处理算法,图像分析算法也是自动化质检系统中的重要一环。
通过应用图像分析算法,可以从图像中识别和分析产品的缺陷或不合格之处。
例如,借助机器学习算法,系统可以学习并识别产品的常见缺陷,如破损、污渍、异物等。
此外,还可以利用深度学习算法来进行产品质量评估和分类。
通过使用合适的图像分析算法,可以有效提高质检的精度和速度。
在设计自动化质检系统时,还应考虑到系统的实时性和可靠性。
一个优秀的质检系统应具备快速、准确、稳定的特性。
为了实现这些目标,可以采用并行计算和分布式处理的技术,以充分利用计算资源。
此外,还可以采用硬件加速技术,如GPU加速,以提高图像处理和分析的速度。
通过优化系统的并行性和计算效率,可以减少质检时间,提高系统的实时性。
此外,自动化质检系统的设计还需要考虑到系统的可扩展性和适应性。
随着制造业的发展和变化,质检需求也会不断变化。
基于机器视觉的自动化检测系统设计与实现

基于机器视觉的自动化检测系统设计与实现机器视觉技术的发展在工业制造等领域中起到了至关重要的作用。
基于机器视觉的自动化检测系统利用计算机视觉技术,通过对图像或视频的处理分析,实现对物体进行自动化检测和判断。
本文将介绍基于机器视觉的自动化检测系统的设计与实现。
一、引言随着工业生产的快速发展,传统的人工检测方式已经无法满足生产效率和质量要求。
基于机器视觉的自动化检测系统应运而生。
该系统可以准确、快速地对产品进行检测,大大提高了检测精度和效率。
二、系统设计1. 硬件设计基于机器视觉的自动化检测系统的核心设备是计算机和视觉检测设备。
计算机负责图像处理和算法运算,视觉检测设备负责图像采集和输入。
此外,根据具体需求,系统还可配备其他硬件设备,如运动控制系统、光照控制系统等。
2. 软件设计软件设计是基于机器视觉的自动化检测系统的关键部分。
在软件设计过程中,需要考虑图像处理算法的选择和优化,以及系统界面的设计等方面。
首先,根据实际需求选择合适的图像处理算法,如边缘检测、形状匹配、颜色识别等。
根据不同的应用场景,可能需要集成多种算法,以实现更精确的检测和判定。
其次,设计系统界面,使之简洁明了、易于操作。
用户可以通过界面设置检测参数,查看检测结果等。
三、系统实现1. 数据采集系统实现时,首先需要进行图像或视频的采集。
根据实际应用场景,可以选择合适的图像采集设备,如摄像头、工业相机等。
通过采集设备,将待检测的物体图像输入到计算机中。
2. 图像处理与特征提取采集到的图像需要进行预处理,并提取出适用于检测的特征。
预处理包括图像去噪、图像增强等操作,以提高后续处理的效果。
特征提取是基于机器视觉的自动化检测系统的核心步骤,通过选择合适的算法和参数,从图像中提取出目标物体的特征信息。
3. 检测与判断通过对特征提取的结果进行分析和处理,系统可以对目标物体进行自动化检测和判断。
根据具体需求,可以设置不同的检测标准和判定规则,以实现对不同缺陷或问题的检测和判断。
计算机自动检测零件直线度误差控制系统设计

(PS — O ER M1 ¨ 防 电 EII POE(I A 爆 机 X,O R F  ̄C ( ON E H
长度, 并装在测量座_ , 景座每移动 一 L 个节距 , 在两 删量头_ 分别读出蕊个数值 二 A D转换 器在程序控制下把连续变化的模拟 / 量转 变成 数字量 , 后传 送到计 算 机逆 行处理 然
维普资讯
防爆 电机
( X L SO E P O I N—P O F E E T I AC IE R O L C R C M HN )
20 年第 1 ( 02 - 期 总第 l 期 ) 1 0
20 02年 3月 3 1日 出 版
计算 机 自动 检 测零 件 直线 度误 差控 制 系统 设 计
张建成 王 禹
佳 木斯纸 业集 团 , 黑龙 江住 木斯 (50 5  ̄4 0 )
摘
偿。
要
简述直线度 自动检涮系统的硬 件组 成和软件设 计 , 并进行 了双删头 量 丰的误 差补 自动检删 直 线度 误差
关键词
De in o sg fCo to l g Sy tm f rLie rt f n r l n se i o n a iy o P r sAu o a ia l tc e y usn mp t r a t t m t ly De e t d b i g Co u e c
②
用C 语言编写 , 主要用于数据采集和数据 处理 , 次性完成对被删量件合格与否的判断
3 1 系统 功能 范 围 . 适 用于 0~60rn不 同长 30m
位置 1 时 位置 i 时
度和不同节距的直线度误差测量 , 可打印 出采样 点的采样 值 , 分析 使用 供 32 数据采集 采集时通过平均值滤波 舍弃粗 , 大误差, 以消除干扰 影响 , 由计数 器控制采集间 隔, 对采集至 的数据自动显示和存贮。 I 33 数 据标定 设 置 对两 个 传 感 器 分别 进 行标 .
《基于机器视觉的工件识别与定位系统的设计与实现》
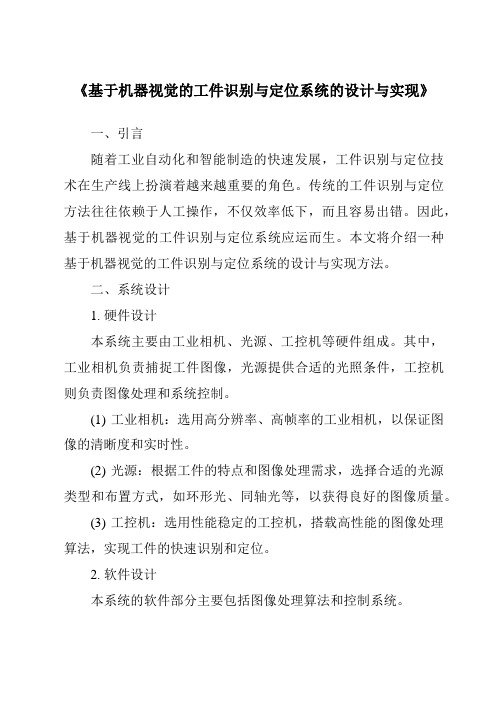
《基于机器视觉的工件识别与定位系统的设计与实现》一、引言随着工业自动化和智能制造的快速发展,工件识别与定位技术在生产线上扮演着越来越重要的角色。
传统的工件识别与定位方法往往依赖于人工操作,不仅效率低下,而且容易出错。
因此,基于机器视觉的工件识别与定位系统应运而生。
本文将介绍一种基于机器视觉的工件识别与定位系统的设计与实现方法。
二、系统设计1. 硬件设计本系统主要由工业相机、光源、工控机等硬件组成。
其中,工业相机负责捕捉工件图像,光源提供合适的光照条件,工控机则负责图像处理和系统控制。
(1) 工业相机:选用高分辨率、高帧率的工业相机,以保证图像的清晰度和实时性。
(2) 光源:根据工件的特点和图像处理需求,选择合适的光源类型和布置方式,如环形光、同轴光等,以获得良好的图像质量。
(3) 工控机:选用性能稳定的工控机,搭载高性能的图像处理算法,实现工件的快速识别和定位。
2. 软件设计本系统的软件部分主要包括图像处理算法和控制系统。
(1) 图像处理算法:采用机器视觉算法对图像进行处理,包括图像预处理、特征提取、模式匹配等步骤。
其中,特征提取是关键环节,通过提取工件的形状、颜色、纹理等特征,实现工件的准确识别。
(2) 控制系统:控制系统负责协调各个硬件设备的工作,包括相机的触发、光源的开关、工件的抓取等。
同时,控制系统还需要与上位机进行通信,接收上位机的指令并反馈系统状态。
三、算法实现1. 图像预处理图像预处理是机器视觉系统的重要环节,主要包括图像滤波、二值化、边缘检测等步骤。
通过对图像进行预处理,可以消除噪声、提高信噪比,为后续的特征提取和模式匹配做好准备。
2. 特征提取特征提取是工件识别的关键环节。
本系统采用基于深度学习的特征提取方法,通过训练神经网络模型,自动学习工件的形状、颜色、纹理等特征。
在提取特征时,需要选择合适的特征描述符和特征匹配算法,以实现工件的准确识别。
3. 模式匹配模式匹配是工件定位的关键步骤。
基于PLC控制的物料自动检测与分拣系统设计

基于PLC控制的物料自动检测与分拣系统设计摘要:随着工业自动化的不断发展,物料自动检测与分拣系统在生产线上的应用越来越广泛。
本文基于PLC控制技术,设计了一种物料自动检测与分拣系统,实现了快速、准确、高效的物料检测和分拣过程。
该系统具备自动化、智能化、灵活性强等特点,可以广泛应用于各类生产线。
1. 引言物料自动检测与分拣系统是工业生产线上的关键设备之一,它能够实现对物料进行准确的检测和分拣,提高生产效率和产品质量。
PLC控制技术是目前广泛应用于物料自动检测与分拣系统中的一种先进技术,具有稳定性好、可靠性高等优点。
本文将对基于PLC控制的物料自动检测与分拣系统进行详细设计和论述。
2. 系统设计方案2.1 硬件设备设计系统硬件设备主要包括传感器、执行机构、PLC控制器和人机界面等。
传感器用于采集物料的各种参数,如尺寸、重量等;执行机构用于完成分拣工作;PLC控制器则负责接收传感器数据、控制执行机构和人机界面的交互等。
人机界面通过图像显示和按键输入等方式,实现对系统的监控和操作。
2.2 系统软件设计系统软件主要包括PLC程序设计和人机界面程序设计两部分。
PLC程序设计主要负责处理传感器数据,通过逻辑运算和控制算法,判断物料的合格与否,并控制执行机构进行分拣。
人机界面程序设计则实现了人机交互,包括传感器数据显示、设定系统参数、状态监控等功能。
3. 系统工作原理3.1 检测过程物料通过传送带进入物料自动检测与分拣系统,由传感器进行检测。
传感器采集物料的尺寸、重量等参数,并将数据传输给PLC控制器。
PLC控制器根据预设的检测标准,对传感器数据进行处理和判断,得出物料是否合格的结果。
3.2 分拣过程在检测完成后,PLC控制器根据检测结果,控制执行机构进行分拣。
执行机构根据物料的不同属性,将合格物料和不合格物料分别放置在不同的位置上。
4. 系统优势4.1 自动化程度高物料自动检测与分拣系统基于PLC控制技术,可以实现自动化操作,减少人工干预,提高生产效率。
汽车零部件自动化装配线防错设计

一般情况下,防错的频次根据产品的批量可设定 为每班次或者每换型进行防错的验证。防错方法根据 防错的类型采用缺陷件进行防错的验证,比如针对漏 装的防错,采用位移传感器进行检测,用一个漏装零 件的缺陷件在设备上进行检测,若设备能够识别是漏 装零件的缺陷件,说明防错有效。
4.带有检测值的采用传感器作为防错机构的防 错
结语
通过系统的梳理,定义了汽车零部件自动化装配 线的方措施设计,包括防错的来源、防错项目清单、 防错方法、验证方法、防错件的制作以及指导书和记 录。系统化的防错设计符合PDCA质量环原则,符合质 量体系要求,为产品质量提升保驾护航。
微信号 auto1950 / 2021年 第 7 期
9
防错项目的来源一般情况下有两个:产品的潜在 失效模式与影响分析(PFMEA),类似产品失效的问 题横展。因此,在一个新产品开发过程当中进行潜在 失效模式与影响分析,梳理出需要防错的项目并建立 防错清单,即哪些项目需要进行防错。防错项目具体
图1o1950
特别策划 | Special Plan
石飞飞
汽车零部件装配行业防错设计的系统性与完整性尤为重要。主要介绍了一个全新的产品在质量规划初期 如何完成完整有效的防错设计流程,确保交付至客户端的产品质量,提升客户满意度,降低公司质量损失,同 时对于功能件而言提升产品的安全性。
产品质量检测系统的设计与实现

产品质量检测系统的设计与实现随着现代化工业的不断发展,各种各样的产品被大量生产出来,这些产品的使用对人们的生活起到了极大的便利作用,但同时也给人们的健康和安全带来许多潜在的危险。
因此,如何保证产品的质量,成为一个无比重要的问题。
产品质量检测系统正是针对这一问题而设计的,本文将介绍产品质量检测系统的设计与实现。
一、产品质量检测系统的概述产品质量检测系统是一种将计算机技术、传感器技术、自动控制技术等集成在一起的全自动检测系统。
该系统具有高精度、高速度、高可靠性等优点,能够自动完成对产品的检测、测试、控制等过程,充分保证了产品的品质。
二、产品质量检测系统概念及分类1. 检测概念检测是指对产品进行的实验、测量、观察等手段的应用,以发现和评价产品存在的问题。
2. 检测方法产品的检测方法分为物理检测和化学检测两种,物理检测以物理学理论为基础,对产品的物理性质进行定性和定量分析,如质量、温度、电流等;化学检测则以化学反应为基础,对产品的化学性质进行分析,如PH值、浓度等。
3. 检测分类产品的检测分类有三种:第一种是根据产品类型的不同而进行的检测,如电子产品检测、食品检测等;第二种是根据检测的目的而进行的分类,如安全检测、质量检测等;第三种是根据检测的过程而进行的分类,如全过程自动检测和部分检测。
三、产品质量检测系统的设计产品质量检测系统存在四个主要部分,分别是传感器模块、信号处理模块、控制模块和显示模块。
1. 传感器模块传感器模块的主要作用是采集产品的特征信息,如压力、温度、湿度,然后将采集到的信号传输到信号处理模块进行处理。
2. 信号处理模块信号处理模块的主要作用是对传感器模块采集到的信号进行滤波、放大、处理等操作,使其成为可供监测的数值信号。
3. 控制模块控制模块的主要作用是接收信号处理模块的处理结果,然后根据预设的控制程序,自动控制产品的质量,如调整生产线的速度等。
4. 显示模块显示模块的主要作用是将产品的质量信息,如产品的编号、质量等级等,显示出来,使操作员能够随时了解产品的质量状况。
- 1、下载文档前请自行甄别文档内容的完整性,平台不提供额外的编辑、内容补充、找答案等附加服务。
- 2、"仅部分预览"的文档,不可在线预览部分如存在完整性等问题,可反馈申请退款(可完整预览的文档不适用该条件!)。
- 3、如文档侵犯您的权益,请联系客服反馈,我们会尽快为您处理(人工客服工作时间:9:00-18:30)。
哈尔滨工业大学
制造系统自动化技术作业
题目:零件质量的自动化检测系统设计班号:
学号:
姓名:
3PS
作业三 零件质量的自动化检测系统设计
一、零件结构图
二、自动检测项目
(1)孔是否已加工?
如图1所示,利用光电传感器来检测孔是否已加工。
1PS 、2PS 、3PS 三个光电
传感器接受光信号,其中1PS 和3PS 检测从凸台两侧反射回来的光信号,2PS 检测从凸台中心线出反射回来的光信号。
当孔已加工则所测得的波形如图3中2PS 所示,若孔还没有加工
则2PS 所测得的波形和1PS 、3PS 所测得的波形相同,故可以通过波形来确认孔是否已加工。
图3 检测波形图
PG
2
(2)面A和B是否已加工?
图4为检测A,B面是否加工的检测原理图,光电传感器发射装置发射脉冲,若两个面均已经加工,则接收装置可以在工件经过时候接收到光电脉冲。
若A,B 面没有加工,则在工件经过时检测不到光电脉冲。
图4 工件检测图
(3)孔φ15±0.01精度是否满足要求?
方向设计一个类似于塞规的测定杆,在测定杆的圆周上沿半径方向放置三只电感式位移传感器。
测量原理如图所示。
假设由于测定杆轴安装误差,移动轴位置误差以及热位移等误差等导致测定杆中心与镗孔中心O存在偏心e,则可通
过镗孔内径上的三个被测点W1,W2,W3测出平均圆直径。
在测定杆处相隔,角装上三个电感式位移传感器,用该检测器可测量出间隙量,,。
已知测定杆半径r,则可求出。
根据三点式平均直径测量原理,平均圆直径=,公式中a,b为常数,由传感器配置角决
定,该测量杆最佳配置角度取,取a=b=0.8717。
偏心e的影响完全被消除,具有以测定杆自身的主机算环为基准值测量孔径的功能,可消除室温变化引起的误差,确保的测量精度。
图5 孔径测定原理图
(4)凸台外径φ40±0.012精度是否满足要求?
测量凸台外径φ40±0.012精度时可以用CCD图像传感技术,其示意图如图6所示。
图6 凸台外径尺寸检测系统结构图
该系统主要有照明装置、图像采集装置及处理系统三部分组成。
主要工作原理:通过光学成像系统将工件外径图像成在CCD的像敏面上,像敏面将罩在每个像敏单元上的图像信号通过光电效应,将物体的反射光线按亮度强弱转变,变成相应数目的载流子。
在某一个时钟周期内,CCD 器件在转移脉冲的作用下将门极上收集到的电子量转移到CCD 的移位寄存器中,在图像采集卡作中,通过放大电路对信号进行放大,再经过 A /D 转换将模拟信号的一系列有目的性的处理转变成为数字信号。
数字信号保存到计算机或者其他处理器进行图像或图形的处理,从而获取工件外径尺寸的相关信息,进而转化为具体的尺寸值,以判断外径尺寸是否满足其精度要求。
(5)零件质量20±0.01kg是否满足要求?
在测力传感器中,把电阻应变片贴在专门设计的传感部件(弹性元件上),
当被测力作用在弹性体上时,弹性体因受力而产生应力和应变,粘贴在变形部位的电阻应变片的阻值发生改变。
当贴片部位受拉应力作用时,应变片的电阻丝被拉长而使阻值变大,当贴片部位受压应力作用时,应变片得电阻丝被压缩而使阻值减小,通过分压电路或者电桥测量应变片阻值变化大小,即可测量出被测力的大小。
将受拉应力和压应力的应变片构成如图所示的电桥,在电桥的一个对角上施加一定的电压,另一个对角作为信号输出。
当被测力为零时,,电桥处于平衡状态,所以=0;被测力不为零时,贴在弹性体上的应变片的阻值改变,,电桥失去平衡,此时
公式中-应变片的泊松比,一般为0.25
K-应变片的灵敏系数,可以查表取得。
E-弹性材料的弹性模量,采用钢时为2.1N/
L-变形梁的长度,m
b-变形筋的宽度,m
W-额定载荷重力,N
-输入电压,V
-输出电压,V
(6)产品标签(白色)是否帖正或漏帖?
如图7所示,利用四个圆柱式反射型传感器来检测标牌是否正确安装。
当标牌在正确位置时候,四个传感器收到相同强度的反射光,系统工作正常,让产品通过。
当标牌位置不正确时或者漏钉标牌时,反射光变化,经逻辑电路启动机械推杆,剔出线外纠正。
(光电开关)
图7标签检测图
(7)如果不合格将其剔除到次品箱;
如图8所示,在每个检测台上安装一台废品剔除装置,当检测得到该产品不合格时立即给此装置一个信号,电磁阀动作使液压缸中的活塞杆向前推进,将不合格产品推到次品箱中。
图8 剔除废品装置
(8)对合格产品和不合格产品进行计数。
在第一道工序开始出和最后一道工序结束出分别安装一组光电计数器,分别统计加工产品的总数总N 和加工合格的产品数合N ,然后通过计算机记录数据,并计算出不合格产品数不总合=-N N N 。
三、自动检测流程图。