主要窑型比较
各种先进石灰窑的对比
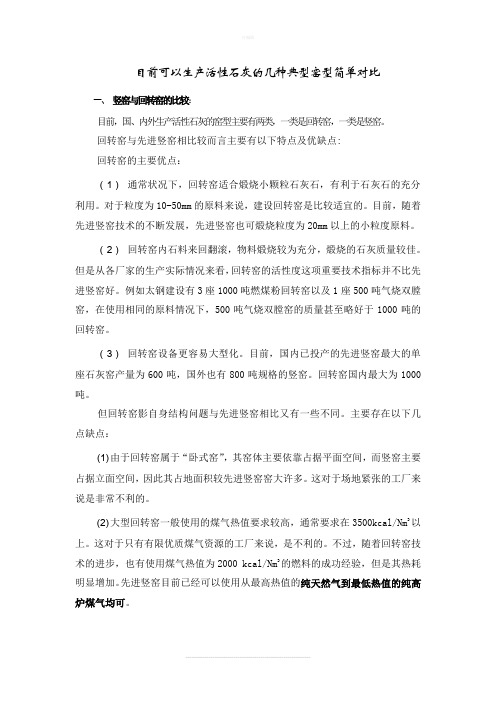
目前可以生产活性石灰的几种典型窑型简单对比一、竖窑与回转窑的比较:目前,国、内外生产活性石灰的窑型主要有两类,一类是回转窑,一类是竖窑。
回转窑与先进竖窑相比较而言主要有以下特点及优缺点:回转窑的主要优点:(1)通常状况下,回转窑适合煅烧小颗粒石灰石,有利于石灰石的充分利用。
对于粒度为10-50mm的原料来说,建设回转窑是比较适宜的。
目前,随着先进竖窑技术的不断发展,先进竖窑也可煅烧粒度为20mm以上的小粒度原料。
(2)回转窑内石料来回翻滚,物料煅烧较为充分,煅烧的石灰质量较佳。
但是从各厂家的生产实际情况来看,回转窑的活性度这项重要技术指标并不比先进竖窑好。
例如太钢建设有3座1000吨燃煤粉回转窑以及1座500吨气烧双膛窑,在使用相同的原料情况下,500吨气烧双膛窑的质量甚至略好于1000吨的回转窑。
(3)回转窑设备更容易大型化。
目前,国内已投产的先进竖窑最大的单座石灰窑产量为600吨,国外也有800吨规格的竖窑。
回转窑国内最大为1000吨。
但回转窑影自身结构问题与先进竖窑相比又有一些不同。
主要存在以下几点缺点:(1)由于回转窑属于“卧式窑”,其窑体主要依靠占据平面空间,而竖窑主要占据立面空间,因此其占地面积较先进竖窑窑大许多。
这对于场地紧张的工厂来说是非常不利的。
(2)大型回转窑一般使用的煤气热值要求较高,通常要求在3500kcal/Nm3以上。
这对于只有有限优质煤气资源的工厂来说,是不利的。
不过,随着回转窑技术的进步,也有使用煤气热值为2000 kcal/Nm3的燃料的成功经验,但是其热耗明显增加。
先进竖窑目前已经可以使用从最高热值的纯天然气到最低热值的纯高炉煤气均可。
(3)由于回转窑的设备体积庞大,设备复杂,因此其投资通常要较先进竖窑高出约20%。
(4)回转窑的热耗较先进竖窑高出约40%,因此,其生产成本较活性竖窑约高20%以上(对于600吨/天的石灰窑,回转窑每年煤气多用1000万人民币)。
回转窑设计方案手册

回转窑的设计一、窑型和长径比1.窑型所谓窑型是指筒体各段直径的变化。
按筒体形状有以下几种窑型:(1)直筒型:制造安装方便,物料在窑内移动速度较均匀一致,操作控制较易掌握,同时窑体砌造及维护较方便;(2)热端扩大型:加大单位时间内燃烧的燃料量及传热量,在原窑直径偏小的情况下,扩大热端将相应提高产量,适用于烧成温度高的物料;(3)冷端扩大型:便于安装热交换器,增大干燥受热面,加速料浆水分蒸发,降低热耗及细尘飞损,适用于处理蒸发量大、烘干困难的物料;(4)两端扩大型(哑铃型):中间的填充系数提高,使物料流动的机会减少,还可以节约部分钢材;还有单独扩大烧成带或分解带的“大肚窑”,这种窑型易挂窑皮,在干燥带及烧成带能力足够时,可以显著提高产量。
但这种窑型操作不便。
总之,不论扩大哪一带,必须保持预烧能力和烧结能力趋于平衡。
只有在生产窑上,经过生产实践和充分调查研究(包括必要的热工测定和计算),发现某一带确为热工上的薄弱环节,在这种特定条件下将该带扩大,才会得出较明显的效果。
目前国内外发展趋势仍以直筒型窑为主,而且尺寸向大型方面发展。
其他有色金属工业用回转窑(还原、挥发、硫化精矿焙烧、氯化焙烧、离析、烧结转化等)多采用较短的直筒窑。
2.长径比要得长径比有两种表示方法:一是筒体长度L与筒体公称直径D之比;另一是筒体长度L与窑的平均有效直径D均之比。
L/D便于计算,L/D均反映要的热工特点更加确切,为了区别起见,称L/D均为有效长径比。
窑的长径比是根据窑的用途、喂料方式及加热方法来确定的。
根据我国生产实践的不完全统计,各类窑的长径比示于表1中。
长径比太大,窑尾废气温度低,蒸发预热能力降低,对干燥不利;长径比太小,则窑尾温度高,热效率低。
同类窑的长径比与窑的规格有关,小窑取下限,大窑取上限。
表1各类窑的长径比窑的名称公称长径比有效长径比氧化铝熟料窑(喷入法)20~2522~27氧化铝焙烧窑20~2321.5~24碳素煅烧窑13.5~1917~24干法和半干法水泥窑11~15——湿法水泥窑30~42——单筒冷却机8~12——铅锌挥发窑14~1716.7~18.3铜离析窑——15~16氯化焙烧窑——12~17.7二、回转窑的生产率回转窑生产是一个综合热工过程,其生产率受多方面因素影响。
套筒窑、弗卡斯窑、双膛窑、回转窑等石灰窑型的对比
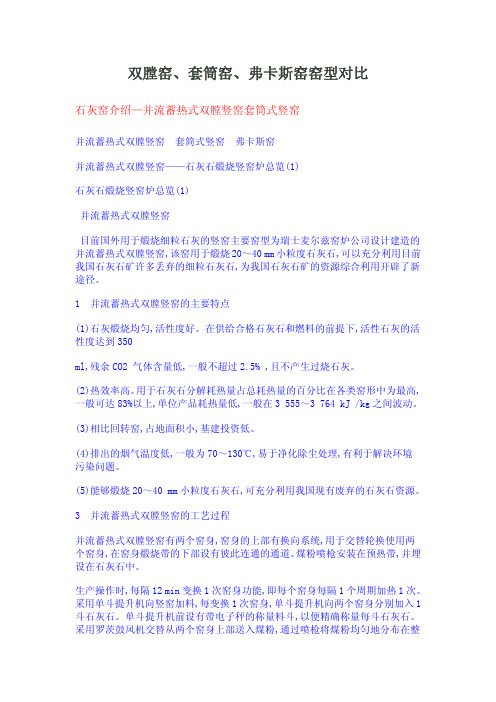
双膛窑、套筒窑、弗卡斯窑窑型对比石灰窑介绍—并流蓄热式双膛竖窑套筒式竖窑并流蓄热式双膛竖窑 套筒式竖窑 弗卡斯窑并流蓄热式双膛竖窑——石灰石煅烧竖窑炉总览(1)石灰石煅烧竖窑炉总览(1)并流蓄热式双膛竖窑目前国外用于煅烧细粒石灰的竖窑主要窑型为瑞士麦尔兹窑炉公司设计建造的并流蓄热式双膛竖窑,该窑用于煅烧20~40 mm小粒度石灰石,可以充分利用目前我国石灰石矿许多丢弃的细粒石灰石,为我国石灰石矿的资源综合利用开辟了新途径。
1 并流蓄热式双膛竖窑的主要特点(1)石灰煅烧均匀,活性度好。
在供给合格石灰石和燃料的前提下,活性石灰的活性度达到350ml,残余CO2 气体含量低,一般不超过2.5% ,且不产生过烧石灰。
(2)热效率高。
用于石灰石分解耗热量占总耗热量的百分比在各类窑形中为最高,一般可达83%以上,单位产品耗热量低,一般在3 555~3 764 kJ /kg之间波动。
(3)相比回转窑,占地面积小,基建投资低。
(4)排出的烟气温度低,一般为70~130℃,易于净化除尘处理,有利于解决环境污染问题。
(5)能够煅烧20~40 mm小粒度石灰石,可充分利用我国现有废弃的石灰石资源。
3 并流蓄热式双膛竖窑的工艺过程并流蓄热式双膛竖窑有两个窑身,窑身的上部有换向系统,用于交替轮换使用两个窑身,在窑身煅烧带的下部设有彼此连通的通道。
煤粉喷枪安装在预热带,并埋设在石灰石中。
生产操作时,每隔12 min变换1次窑身功能,即每个窑身每隔1个周期加热1次。
采用单斗提升机向竖窑加料,每变换1次窑身,单斗提升机向两个窑身分别加入1斗石灰石。
单斗提升机前设有带电子秤的称量料斗,以便精确称量每斗石灰石。
采用罗茨鼓风机交替从两个窑身上部送入煤粉,通过喷枪将煤粉均匀地分布在整个窑的断面上。
采用罗茨鼓风机将燃烧用的空气从竖窑顶部送入窑内,经预热带进入煅烧带与煤粉混合,使煤粉在煅烧带内燃烧,火焰与物料并流使物料得以煅烧。
在煅烧带将石灰石煅烧后产生的废气,通过两个窑身的连接通道进入另一个窑身,与装入的石灰石料流相反向上流动,预热了另一个窑身内的石灰石。
双膛窑与回转窑的比较
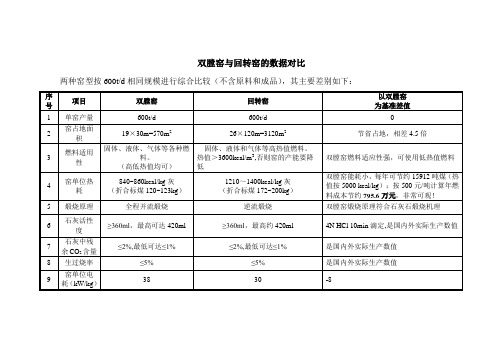
双膛窑与回转窑的数据对比
两种窑型按600t/d相同规模进行综合比较(不含原料和成品),其主要差别如下:
通过差别比较可以看出,600T/D的回转窑仅在原料最小粒度和耐材异型砖种类上有些优势。
双膛窑竖窑在单位产品热耗、电耗、自动化水平、原料粒度适用性、耐材寿命、燃料适用性等方面双膛窑都明显优越于回转窑。
在投资新建窑炉上选择何种形式的窑炉及其配套使用的燃料及其重要,优先考虑的是矿山原料的综合利用,其次还要考虑运行成本、维护成本、施工难易程度、自动化控制水平高低等各种因素。
综上所述,使用煤粉为燃料煅烧高质量石灰应优先选用双膛窑技术。
柴窑-煤窑-气窑的差别

柴窑-煤窑-气窑的差别近年来,很多瓷器作品都会提到柴窑一词,似乎瓷器只要一粘上柴窑就身价倍增。
但柴窑烧制与现在的烧制方法有什么区别?为什么会有区别?却一直没有人能说明白。
在网上收集了一些资料,以备大家参考,共同学习!柴窑烧制难在何处?一是政府明令禁烧柴窑,没有松柴供应,二是一窑下来,烧掉近2000斤松柴,成本相当高,三是烧一次窑要有一整套经验丰富班子集体协作,特别是把桩师傅,没几十年成功经验是不行的,决不是凑合几个人就行的,如果没有专门的资金保证和目的,谁也不敢轻易动火。
柴窑烧制与现代烧制方式的内在差别:景德镇柴窑因烧松柴得名,也称镇窑.在过去,砌造技术完全由家族行帮垄断,师傅言传身教,密不外传.每次烧窑前,必须请"挛窑户"专门检修,外人无法操作.一座窑使用60-80次必须重建.每烧1公斤瓷器需松柴2-3公斤,大的蛋型窑一次可烧10-15吨日用瓷器,需松柴25-40吨,小窑烧松柴的比例要高一些,当然成本就更高了.不是什么人随便砌个炉子就可以用几根木头烧瓷器的为保护森林资源,景德镇在50年代末期改烧煤、油时候,发现祖祖辈辈使用的配釉已经不适应了,高温下粘度降低很快,烧出来的釉面阴黄、沉碳、烟熏。
,注意一下上面话里的两个关键词,一个是粘度,一个是釉面阴黄,其实这揭示燃料改进后温度曲线和窑内物质元素已经发生变化。
古老的石灰釉已经不能用了,后来改革成长石釉,又叫5311釉。
古代釉水里面的天然着色氧化物含量高,在部分胎釉接合处产生一线窑红的现象,这是一种特征。
在古代老柴窑的烧制环境中,那些着色氧化物是不用担心的,老柴窑可以灭掉它的危害,甚至在灭掉危害性的同时造出釉面白里泛青的玉质效果,巧夺天工。
煤窑、气窑、电窑呢?做不到。
现代那些做高仿的,如果按古代配釉技术配釉,他必须得拿柴去烧,用其他燃料他烧不出来,哪怕用计算机控制窑内温度的变化也最多解决个“粘度”问题。
另外一种方法就是搞假釉面,即用适合现代气窑烧造的釉水做点手脚,加点东西,模拟一下,然后还用气窑烧,这种并不算高仿。
回转窑与其他窑型工艺比选

回转窑与其他窑型工艺比选我呀,在这窑炉的世界里也算是混了好些年了。
今天就和大家唠唠回转窑和其他窑型工艺的那些事儿。
咱先来说说这回转窑。
回转窑就像是一个巨大的旋转着的热管道,一直在那儿慢悠悠地转着,可别小瞧了它这慢悠悠的劲儿,这里面可大有学问呢。
它的结构相对比较简单,就是一个长长的筒体,架在托轮上不停地转动。
这就好比一个人在不停地原地转圈,但是这个圈转得可有用了。
在生产过程中,物料从窑的一端进去,随着窑体的转动,就像坐过山车一样,慢慢地向另一端移动。
在这个过程中,物料被加热到很高的温度,发生各种物理和化学变化。
就拿水泥生产来说吧,石灰石等原料在回转窑里被烧得红红的,就像在太上老君的炼丹炉里一样,最后变成了我们熟悉的水泥熟料。
而且回转窑的操作比较灵活,可以根据不同的生产需求调整转速、温度等参数。
这就像是一个善变的魔术师,能根据观众的要求变出不同的花样来。
再看看其他窑型,比如说立窑。
立窑就像一个直挺挺的大烟囱,物料是从顶部加入,然后在窑内自上而下地进行反应。
立窑的占地面积比较小,这就像住在小房子里,虽然空间有限,但是也有它自己的优势。
可是呢,它也有不少麻烦事儿。
立窑内部的物料受热不太均匀,就像烤蛋糕的时候,有的地方烤焦了,有的地方还没熟呢。
这就导致产品的质量不太稳定,有时候好,有时候坏,可把生产的人急得直跺脚。
还有隧道窑,这隧道窑就像一条长长的地下通道。
它是把物料放在窑车上,然后窑车沿着隧道慢慢地走,就像一列小火车在轨道上行驶。
隧道窑的热效率比较高,因为它可以把热量充分利用起来,就像一个精打细算的家庭主妇,一点也不浪费。
但是呢,隧道窑的建设成本可不小,就像盖一座豪华的大房子,得花不少钱呢。
而且一旦隧道窑的某个环节出了问题,就像火车脱轨了一样,整个生产过程都会受到影响,维修起来也比较麻烦。
我有个朋友,以前在一个立窑的工厂工作。
他就老是跟我抱怨,说那立窑生产出来的产品质量参差不齐,搞得他们老是被客户投诉。
双梁窑、双膛窑、套筒窑比较
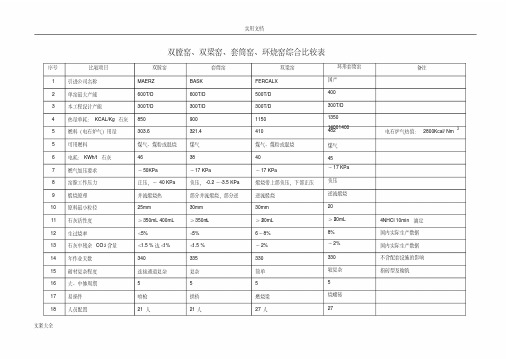
实用文档
文案大全双膛窑、双梁窑、套筒窑、环烧窑综合比较表
序号比较项目双膛窑套筒窑双梁窑环形套筒窑备注
1 引进公司名称MAERZ BASK FERCALX 国产
2 单窑最大产能600T/D 600T/D 500T/D 400
3 本工程设计产能300T/D 300T/D 300T/D 300T/D
4 热量单耗:KCAL/Kg石灰850 900 1150 1350
14001400
5 燃料(电石炉气)用量303.
6 321.4 410 482 电石炉气热值:2800Kcal/ Nm3
5 可用燃料煤气、煤粉或混烧煤气煤气、煤粉或混烧煤气
6 电耗:KWh/t 石灰46 38 40 45
7 燃气加压要求~50KPa ~17 KPa ~17 KPa
~17 KPa
8 窑膛工作压力正压,~40 KPa 负压,-0.2~-3.5 KPa 煅烧带上部负压,下部正压负压
9 煅烧原理并流煅烧热部分并流煅烧,部分逆逆流煅烧逆流煅烧
10 原料最小粒径25mm 30mm 30mm 20
11 石灰活性度≥350mL 400mL≥350m L ≥320mL ≥320mL 4NHCl 10min滴定
12 生过烧率≤5% ≤5% 6~8% 8% 国内实际生产数据
13 石灰中残余CO2含量≤1.5 %达≤1% ≤1.5 % ~2% ~2% 国内实际生产数据
14 年作业天数340 335 330 330 不含配套设施的影响
15 耐材复杂程度连接通道复杂复杂简单较复杂指砖型及砌筑
16 大、中修周期 5 5 5 5
17 易损件喷枪拱桥燃烧梁
烧嘴砖
18 人员配置21人21人27人27。
立窑和回转窑的区别

立窑和回转窑的区别1、回转窑的产量高。
非常适合大型活性石灰生产线,现在世界上已有日产2200吨的石灰回转窑投入生产;国内外已建成很多日产150~300吨石灰回转窑,运行状况很好,也适合中、小型石灰企业的应用。
2、回转窑属敞开式煅烧,窑体结构简单,气流畅通,含硫烟气可及时排出,燃料中的硫份不易附着,因而产品含硫量低,符合炼钢的要求。
同时因物料在窑内均匀滚动前进,受热均匀,产品质量稳定,生、过烧率很低,可以煅烧高活性度的炼钢用石灰。
在同等条件下,回转窑生产的石灰其活性度高于气烧竖窑,平均高30ml以上,活性度一般为340~380ml,甚至高达400ml。
3、回转窑可以直接煅烧10~50mm的细粒级石灰石,一般石灰石矿山产品0~30mm细粒级石灰石约占总产量的30~40%,这部分石灰石其他窑型不能利用。
且随着钢铁原料的“精料化”,烧结逐渐以生石灰代替石灰石,细粒级石灰石得不到综合利用。
建设回转窑生产线不但能充分利用优质石灰石矿山资源,且符合石灰工业的可持续发展方针。
4、在窑尾配置竖立预热器可充分利用回转窑内煅烧产生的高温烟气,将石灰石从常温预热到初始分解温度状态。
这不仅能大大提高回转窑的产量,还能降低单位产品热耗;5、窑头处配置竖立冷却器不仅可使高温石灰骤冷,提高产品活性度,也便于运输、储存。
同时还能得到较高温度的入窑二次风。
能有效地提高窑内烧成温度,降低燃料消耗。
6、经窑尾竖式预热器排出的烟气温度低,在280~350℃之间,含尘量低,约为20g/Nm3,使后续烟气处理设备的配置简捷有效,可顺利的达到环保要求。
7、回转窑石灰质量稳定是其最大的优点。
从总的发展趋势看来,我国活性石灰生产设备应立足于国内。
不论从生产能力的适应性,能生产满足炼钢要求的高活性、低硫份、质量稳定的活性石灰、还是能充分利用优质石灰石矿山资源等方面,回转窑均具有很好的发展前景。
- 1、下载文档前请自行甄别文档内容的完整性,平台不提供额外的编辑、内容补充、找答案等附加服务。
- 2、"仅部分预览"的文档,不可在线预览部分如存在完整性等问题,可反馈申请退款(可完整预览的文档不适用该条件!)。
- 3、如文档侵犯您的权益,请联系客服反馈,我们会尽快为您处理(人工客服工作时间:9:00-18:30)。
窑型情况介绍
根据我公司业绩及了解情况,对比目前国内主要窑型基本介绍如下。
双膛窑与套筒窑、回转窑的主要指标如下:
说明:主要参数竖窑参照主流的600TPD窑型作说明;不同厂家操作情况不同,部分数据有差别。
一、双膛竖窑
1.基本介绍
式活性双膛竖窑由于其具有合理的煅烧石灰的热工特性,因此可以生产出高质量的石灰制品;由于燃烧采用蓄热式技术原理,其能耗指标是所有窑型中最低的。
并流蓄热式活性双膛竖窑自动化水平高,可保证石灰窑长期安全稳定高效运行,并减少操作工人成本。
燃料可使用气体和固体燃料,也可使用液体燃料,且可以使用低热值燃料,热值最低要求1250Kcal即可。
2. 原理
双膛窑是先进的石灰煅烧设备,它有两个竖直的窑膛,在窑体中下部有通道将两窑膛连通。
双膛窑煅烧工艺有两大特点:并流和蓄热。
所谓并流就是在石灰石煅烧时,燃烧产物和石灰石一起向下流动,这
样利于煅烧出高质量的活性石灰。
所谓蓄热就是在窑膛A煅烧时,煅烧的产物——高温烟气通过窑膛中下部的通道进入窑膛B。
进入窑膛B后,高温烟气向上流动,将预热带的石灰石预热到较高温度,这一过程相当于把烟气的热量在窑膛B的预热带储蓄起来。
经过窑膛B 的烟气下降到一个很低的温度后排出窑膛。
这种工作原理充分地利用了烟气余热,保证了该种窑具有很高的热效率。
3.窑主要技术特点
1)并流煅烧:这是双膛竖窑的首要技术特点,由于最高温的火焰接
触石灰石,使热交换率很高,相对较低的热气体接触快烧好的物料,避免了过烧和欠烧。
2)在石灰石及燃料的质量满足要求的前提下,煅烧的石灰质量好,
活性度≥360ml (用4N-HCl,10min滴定值),残余CO2含量一般不超过2%,硫含量较低。
3)热利用率高:高温废气从预热窑膛排出,经过较长时间的热交换
后将热量传给石灰石,使石灰石温度升高,废气温度降低,有效地利用了热能,从而达到了节能的目的。
双膛石灰窑每公斤石灰能耗为880kal(以燃气为燃料)。
如果采用高热值燃气,可进一步降低热能消耗。
4)供热均匀:2×33根喷枪在窑膛内均匀分布,每根喷枪的供热覆
盖范围相同,使窑膛断面上的热量供应均匀,利于石灰的均匀稳定煅烧。
5)环保效果好,双膛竖窑排出的废气温度和粉尘含量较低,易于采
取废气净化处理措施,有利于减轻环境污染。
6)质检方便:窑下设有质量检查门,通过检查各部位的产品质量可
以调节相应喷枪的燃料供给量来最终保证质量。
7)设备可靠:竖窑上的大部分设备都采用液压操作,运行稳定可靠。
这些设备有:空气/废气换向闸板、烟气换向闸板、窑膛关闭闸板、加料料斗闸板、出料装置、出料料斗密封闸板及石灰石料位指示
器等。
一般双膛窑大修期在5年以上。
8)窑体隔热性能好:表面温度低,即保护了环境又节省了能源。
9)自动化程度高:该窑采用PLC控制和LED显示,按生产工艺流程
进行集中监视和自动控制,对生产过程中所用的操作参数进行记录,并可随时打印。
可实现智能化操作,当窑产量改变时,仅需修改几个参数即可。
二、套筒竖窑
1.基本原理
窑前料仓的石灰石原料由胶带输送机送至称量斗,经称量斗称量后装入料车内运至窑顶,经给料斗进入环形套筒内。
环形套筒是由石灰窑窑壳的耐火材料内衬和与窑外壳同心布置的下内筒和上内筒组成。
石灰石穿过预热带进入煅烧带。
煅烧带布置上、下两层烧嘴,每层的每个燃烧室都固定在环形套筒内,等分布置。
上、下两层烧嘴将煅烧带分割成逆流运行的上部煅烧带和并流运行的下部煅烧带。
从预热带出来并汇集在环形烟道的废气,与来自热交换器的废气汇合,由废气风机排入布袋除尘器。
进入废气引风机的废气温度一般在180~250 ℃左右。
2.窑型特点
套筒窑的主要特点是:
1) 运行非常稳定,属于无故障窑型;
2) 活性石灰的质量非常高,一般情况下,活性度在350-400ml,10分钟所消耗的4当量浓度的盐酸,活性石灰中CO2残余量在2%以内,甚至可控制在1%以下。
生/过烧率在3%以内;
3)消耗低,特别是电耗,每吨活性石灰只有32kwh,比双膛窑低;热耗比双膛窑高些,每公斤活性石灰是980kcal;
4)由于是负压生产,非常有利于环保和安全生产;
5)由于是负压生产,对石灰石和燃料条件要求不象双膛窑那样苛刻,对生产过程中石灰石和燃料理化指标的波动不象双膛窑那样敏感,
不会轻易出现结瘤粘窑现象;
6)备件消耗极低;
7)由于是单筒竖窑,占地面积小于双膛窑和回转窑。
3.我公司技术特点
中冶南方武钢设计院可以为业主提供耐火材料行业从原料制备到成品产出全流程工艺生产线设计以及设备成套和工程总承包等一条龙服务。
在冶金灰方面,我公司除配套武钢回转窑外还建设了套筒窑。
2007年承担武钢耐火材料厂新建3#活性石灰套筒窑工程总体设计,该窑是世界首座日产600吨环型套筒窑,主体技术及关键设备引进,创造了工期最短、日产量最高、自动化程度最高三项世界第一,目前该套筒窑运作正常。
在套筒窑的前期建设以及后期使用中,逐步掌握了关于套筒窑的核心技术,具备了各种套筒窑的开发、施工、使用、维护以及工程技术的输出能力。
2013年承担武钢耐火公司4#套筒窑总包工程,为武钢耐火公司建成第二座日产600吨套筒窑,该窑的设计及建设全部国产化,2013年7月投产,至今运行状态良好。
以上两座石灰竖窑目前均运转良好,产品质量、产量、能耗、环保要求等均满足设计及国标要求。
我公司在实施以上工程的国产中,对现有技术进行了转化吸收,并做了一定改进工作。
套筒石灰竖窑的拱桥是整个窑体的关键部分之一,国内部分套筒窑存在掉砖、拱桥垮塌等问题,我公司在实施第二座套筒石灰竖窑的国产中对拱桥砖型、砌筑技术等方面做了部分改进,应用情况良好。
套筒窑在国内运行多年,在高温区的燃烧室与窑体夹角处容易出现温度高,甚至窑壳发红的情况。
通过改进材质及施工方案,使用喷
涂料喷涂,可以有效改善上述情况。
原套筒窑设计采用旋转式布料器,在实际使用过程中出现磨损现象,且需耗能。
现改进为固定式布料器,也可以达到布料均匀的效果。
煤气环管由两根改为一根,每个烧嘴的煤气控制调节阀由手动改为自动,并接入PLC控制系统,可以实现全自动控制,减少操作人员数量及巡检强度。
窑体耐材部分的改进,如上内筒顶部、上内筒中部、上下内筒底部、拱桥、燃烧室顶部等部位的耐火材料易出现掉砖、耐材剥落等现象。
我公司通过改进设计,优化施工方案,重新制定烘炉方案,有效避免出现以上问题。
三、回转窑
1.基本介绍
回转窑是一种传统窑型,因其产品质量好,目前仍在大面积使用。
回转窑的产量高,回转窑属敞开式煅烧方式,窑体结构简单,气流畅通,含硫烟气可及时排出,燃料中的硫成份不易附着,因而产品含硫量低,符合炼钢的要求。
回转窑生产的活性石灰质量稳定是其最大的优点。
但回转窑煅烧系统设备重量大,投资高,占地面积大。
2.主要原理
进入石灰石仓的石灰石由布料器均匀的布入竖式预热器中,经预热的石灰喂入石灰窑本体。
回转窑由筒体、支撑装置、传动装置、前后挡轮装置、窑尾及窑头密封、窑头罩组成。
物料从窑尾(筒体的高端)进入窑内煅烧。
由于筒体的倾斜和缓慢的回转作用,物料既沿圆周方向翻滚又沿轴向(从高端向低端)移动,继续完成其工艺过程,燃料自热端喷入,在空气助燃下燃烧放热并产生高温烟气,热气在风机的驱动下,自热端向次端流动,而物料和烟气在逆向运动的过程中进行热量交换,使石灰石烧成石灰。
转窑托轮传动为两档形式,轴承为水冷式油勺润滑滑动轴承,并
有球面瓦能自动调心。
在靠近大齿圈处还配有前后液压挡轮。
主传动系统采用交流变频调速电机驱动窑体,并设有辅助电动机驱动窑体。
窑头窑尾采用密封装置及冷却风机。
大齿圈设计自润滑功能。
3. 回转窑主要技术特点
1)回转窑的产量高,非常适合大型活性石灰生产线,现在世界上已
有日产2200吨的石灰回转窑投入生产;运行状况良好,也适合中小石灰企业的应用。
2)回转窑属敞开式煅烧,窑体结构简单,气流畅通,含硫烟气可以
及时排出,燃料中的硫份不易附着,因而产品含硫量低,符合炼钢要求。
3)回转窑可以直接煅烧10-50mm的细粒级石灰石,一般矿山产品
0-30mm细粒级石灰石约占总产量的30-40%,这部分石灰石其它窑型不能利用。
4)在窑尾配置竖式预热器可充分利用回转窑内煅烧产生的高温烟
气,将石灰石从常温预热到初始分解状态。
这不仅能大大提高回转窑的产量,还能充分降低单位产品热耗;
5)窑头处配置竖式冷却器不仅可使高温石灰骤冷,提高产品活性度,
也变于输送、储存。
同时还能得到较高温度的入窑二次风。
能有效提高窑内烧成温度,降低燃料消耗。
6)经窑尾竖式预热器排出的烟气温度在280-350℃之间,使后续
烟气处理的配置简捷有效,可顺利达到环保要求。