APQP的作用
APQP作业指导书
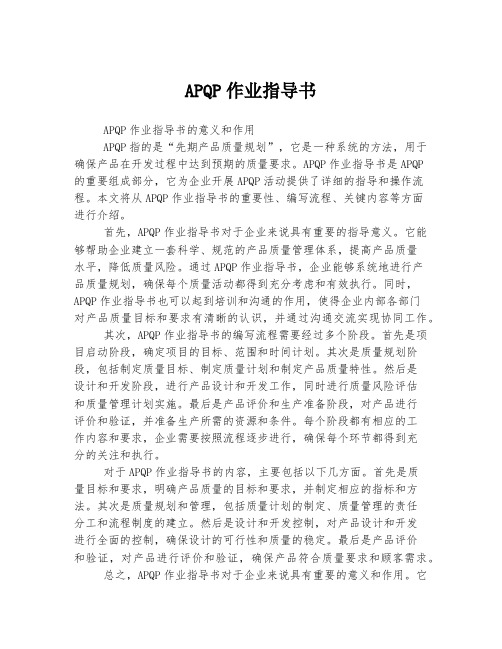
APQP作业指导书APQP作业指导书的意义和作用APQP指的是“先期产品质量规划”,它是一种系统的方法,用于确保产品在开发过程中达到预期的质量要求。
APQP作业指导书是APQP的重要组成部分,它为企业开展APQP活动提供了详细的指导和操作流程。
本文将从APQP作业指导书的重要性、编写流程、关键内容等方面进行介绍。
首先,APQP作业指导书对于企业来说具有重要的指导意义。
它能够帮助企业建立一套科学、规范的产品质量管理体系,提高产品质量水平,降低质量风险。
通过APQP作业指导书,企业能够系统地进行产品质量规划,确保每个质量活动都得到充分考虑和有效执行。
同时,APQP作业指导书也可以起到培训和沟通的作用,使得企业内部各部门对产品质量目标和要求有清晰的认识,并通过沟通交流实现协同工作。
其次,APQP作业指导书的编写流程需要经过多个阶段。
首先是项目启动阶段,确定项目的目标、范围和时间计划。
其次是质量规划阶段,包括制定质量目标、制定质量计划和制定产品质量特性。
然后是设计和开发阶段,进行产品设计和开发工作,同时进行质量风险评估和质量管理计划实施。
最后是产品评价和生产准备阶段,对产品进行评价和验证,并准备生产所需的资源和条件。
每个阶段都有相应的工作内容和要求,企业需要按照流程逐步进行,确保每个环节都得到充分的关注和执行。
对于APQP作业指导书的内容,主要包括以下几方面。
首先是质量目标和要求,明确产品质量的目标和要求,并制定相应的指标和方法。
其次是质量规划和管理,包括质量计划的制定、质量管理的责任分工和流程制度的建立。
然后是设计和开发控制,对产品设计和开发进行全面的控制,确保设计的可行性和质量的稳定。
最后是产品评价和验证,对产品进行评价和验证,确保产品符合质量要求和顾客需求。
总之,APQP作业指导书对于企业来说具有重要的意义和作用。
它能够帮助企业建立科学规范的质量管理体系,提高产品质量水平,降低质量风险。
通过按照APQP作业指导书的要求进行工作,企业能够实现协同工作,提高工作效率,更好地满足客户需求。
五大工具手册APQP、PPAP、SPC、MSA、FMEA

五大工具手册APQP、PPAP、SPC、MSA、FMEA1.产品质量先期策划(APQP)、2.测量系统分析(MSA)、3.统计过程控制(SPC)、4.生产件批准(PPAP)5.潜在失效模式与后果分析(FMEA)一、APQP(Advanced Product Quality Planning)即产品质量先期策划,是一种结构化的方法,用来确定和制定确保某产品使顾客满意所需的步骤。
产品质量策划的目标是促进与所涉及的每一个人的联系,以确保所要求的步骤按时完成。
有效的产品质量策划依赖于公司高层管理者对努力达到使顾客满意这一宗旨的承诺。
产品质量策划有如下的益处:◆引导资源,使顾客满意;◆促进对所需更改的早期识别;◆避免晚期更改;◆以最低的成本及时提供优质产品二、PPAP:生产件批准程序(Production part approval process)ppap生产件提交保证书:主要有生产件尺寸检验报告,外观检验报告,功能检验报告,材料检验报告;外加一些零件控制方法和供应商控制方法;主要是制造形企业要求供应商在提交产品时做ppap文件及首件,只有当ppap文件全部合格后才能提交;当工程变更后还须提交报告。
ppap是对生产件的控制程序,也是对质量的一种管理方法。
三、SPC(Statistical Process Control)即统计过程控制,主要是指应用统计分析技术对生产过程进行适时监控,科学区分出生产过程中产品质量的随机波动与异常波动,从而对生产过程的异常趋势提出预警,以便生产管理人员及时采取措施,消除异常,恢复过程的稳定从而达到提高和控制质量的目的。
SPC非常适用于重复性的生产过程,它能够帮助组织对过程作出可靠的评估,确定过程的统计控制界限判断过程是否失控和过程是否有能力;为过程提供一个早期报警系统,及时监控过程的情况,以防止废品的产生,减少对常规检验的依赖性,定时以观察以及系统的测量方法替代大量检测和验证工作。
产品建议书-APQP

产品建议书-APQP引言概述:APQP(Advanced Product Quality Planning,先进产品质量规划)是一种用于确保产品质量的方法论,它能够在产品开发过程中提前预防和解决潜在问题,从而确保产品的质量和可靠性。
本文将从五个方面阐述APQP的重要性和应用。
一、需求分析与规划1.1 确定产品需求:通过与客户沟通和了解,明确产品的功能需求、性能要求、外观要求等。
1.2 制定产品规划:根据产品需求,制定产品的开发计划、时间表和资源分配,确保项目能够按时完成。
1.3 评估风险和可行性:对产品开发过程中可能出现的风险进行评估,确定解决方案并评估其可行性,以降低项目失败的风险。
二、设计与开发2.1 进行设计评审:在产品设计过程中,进行多轮设计评审,确保产品的设计满足需求,并与客户进行沟通和确认。
2.2 制定质量目标:根据产品的特性和市场需求,制定产品的质量目标,包括可靠性、性能、寿命等指标。
2.3 进行设计验证:通过模拟测试、原型验证等方式,验证产品设计的可行性和符合性,及时发现和解决设计上的问题。
三、过程评估与改进3.1 制定过程控制计划:根据产品的特性和制造过程的要求,制定过程控制计划,包括工艺流程、检验标准、设备要求等。
3.2 进行过程评估:对制造过程进行评估,包括工艺能力评估、设备能力评估、操作员能力评估等,确保过程的稳定性和可控性。
3.3 持续改进:根据过程评估的结果,制定改进计划并落实,通过持续改进,提高产品的质量和可靠性。
四、供应商管理4.1 供应商评估与选择:对潜在供应商进行评估,包括其质量管理体系、生产能力、技术实力等,选择合适的供应商。
4.2 建立合作关系:与供应商建立长期合作关系,共同制定质量目标和要求,并进行定期的沟通和协作。
4.3 监控供应商质量:对供应商进行质量监控,包括对原材料的检验、对供应商生产过程的监控等,确保供应链的质量和可靠性。
五、产品验证与批准5.1 进行样品验证:在产品开发的最后阶段,制作样品进行验证,确保产品的设计和制造满足客户的需求和要求。
质量管理体系五大工具培训
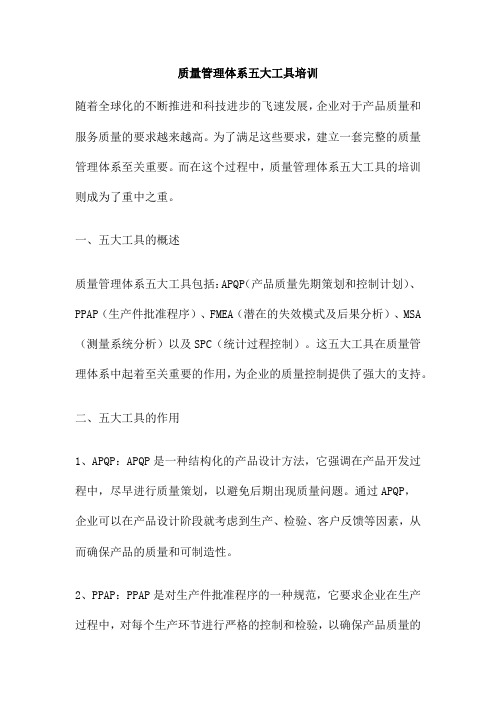
质量管理体系五大工具培训随着全球化的不断推进和科技进步的飞速发展,企业对于产品质量和服务质量的要求越来越高。
为了满足这些要求,建立一套完整的质量管理体系至关重要。
而在这个过程中,质量管理体系五大工具的培训则成为了重中之重。
一、五大工具的概述质量管理体系五大工具包括:APQP(产品质量先期策划和控制计划)、PPAP(生产件批准程序)、FMEA(潜在的失效模式及后果分析)、MSA (测量系统分析)以及SPC(统计过程控制)。
这五大工具在质量管理体系中起着至关重要的作用,为企业的质量控制提供了强大的支持。
二、五大工具的作用1、APQP:APQP是一种结构化的产品设计方法,它强调在产品开发过程中,尽早进行质量策划,以避免后期出现质量问题。
通过APQP,企业可以在产品设计阶段就考虑到生产、检验、客户反馈等因素,从而确保产品的质量和可制造性。
2、PPAP:PPAP是对生产件批准程序的一种规范,它要求企业在生产过程中,对每个生产环节进行严格的控制和检验,以确保产品质量的一致性和稳定性。
3、FMEA:FMEA是一种预防性的质量控制工具,它通过对产品潜在的失效模式进行分析,提前找出可能存在的问题,并采取相应的措施加以预防。
4、MSA:MSA是一种测量系统的分析方法,它通过对测量系统的误差进行分析,确保测量结果的准确性和可靠性。
5、SPC:SPC是一种实时监控生产过程的质量控制工具,它通过对生产过程中的数据进行统计分析,及时发现异常,并采取相应的措施加以纠正。
三、培训的重要性质量管理体系五大工具的培训对于企业来说至关重要。
通过培训,企业可以了解到五大工具的使用方法和应用场景,从而在实际工作中更好地运用这些工具。
同时,培训还可以提高员工的质量意识和技能水平,增强企业的整体竞争力。
四、培训的实施1、制定培训计划:根据企业实际情况和员工需求,制定合理的培训计划。
培训计划应该包括培训内容、时间、地点和人员等详细信息。
2、组织培训:组织相关人员进行培训,确保培训的顺利进行。
质量管理体系中APQP和CP培训教案
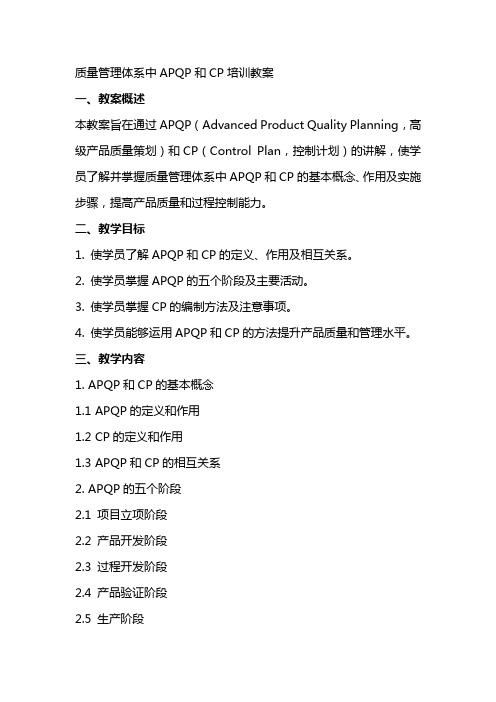
质量管理体系中APQP和CP培训教案一、教案概述本教案旨在通过APQP(Advanced Product Quality Planning,高级产品质量策划)和CP(Control Plan,控制计划)的讲解,使学员了解并掌握质量管理体系中APQP和CP的基本概念、作用及实施步骤,提高产品质量和过程控制能力。
二、教学目标1. 使学员了解APQP和CP的定义、作用及相互关系。
2. 使学员掌握APQP的五个阶段及主要活动。
3. 使学员掌握CP的编制方法及注意事项。
4. 使学员能够运用APQP和CP的方法提升产品质量和管理水平。
三、教学内容1. APQP和CP的基本概念1.1 APQP的定义和作用1.2 CP的定义和作用1.3 APQP和CP的相互关系2. APQP的五个阶段2.1 项目立项阶段2.2 产品开发阶段2.3 过程开发阶段2.4 产品验证阶段2.5 生产阶段3. CP的编制方法3.1 CP的基本结构3.2 CP的编制步骤3.3 CP的注意事项4. APQP和CP在实际应用中的案例分析四、教学方法1. 讲授:讲解APQP和CP的基本概念、作用、实施步骤及注意事项。
2. 案例分析:分析实际应用中的案例,使学员更好地理解APQP和CP的实施过程。
3. 小组讨论:分组讨论CP的编制方法和注意事项,提高学员的实践能力。
五、教学时间共计16学时,其中:1. APQP和CP的基本概念:2学时2. APQP的五个阶段:4学时3. CP的编制方法:4学时4. 案例分析:4学时5. 小组讨论:2学时六、APQP的五个阶段详解6.1 项目立项阶段在这个阶段,需要确定产品或项目的方向,明确市场需求,对可能的风险进行评估,并制定项目计划。
6.2 产品开发阶段在这个阶段,需要对产品的设计进行规划,包括制定设计目标,进行概念设计,详细设计,并对设计进行验证。
6.3 过程开发阶段在这个阶段,需要对生产过程进行规划,包括选择合适的制造过程,工艺流程,并对过程进行验证。
APQP cop(Advanced Product Quality Planning and Control Plan)

如要求,获得负责的工程批准。
21
三.控制计划方法论
3.控制计划栏目说明
13)顾客质量批准日期
如要求,获得负责的供方质量代表批准。
14)其他批准日期
如要求,获得其他同意的批准。
15)零件/过程编号
该项编号通常参照与过程流程图,如果有多零件编号存 在(组件),那么相应地列出单个零件编号和它们的过 程编号。
排放、噪声、无线电干扰等等 的产品要求(尺寸、规
范、试验)或过程参数
专用术语 安全/符合<S/C>
关键特性-CC
盾形-<S>
符号
▽
9
与COP有关的特殊特性符号 标注 COP
10
APQP 流程
开始
阶段1.0 输出
顾客呼声
业务计划 营销策略
基准确定
产品/过程 设想
可靠性 研究
顾客输
设计目标
可靠性/质量 目标
产品质量先期策划和控制计划 (APQP)
1
一.概述
1.什么是APQP?
APQP 英 文 全 文 是g and Control Plan。
APQP是用来确定和制定确保某产品使顾客满意所需步 骤的一种结构化方法。
2
2.APQP的输入和输出
风
设计记录
险
FMEA
防错
控制计划 作业指导书
PPAP
APQP进程
7
二.APQP实施
设计目标 满足法规和实施规则的要求
8
附录C 特殊特性符号
定义
通用汽车公司北美部
福特汽车公司
克莱斯勒汽车公司
非主要特 指这种产品特性:在可预料的 不采用
APQP 第二版培训教材

●遇到困难,推荐使用规程化的问题解决方 式。
●可行时应当使用附录B里的分析技术。
三、APQP的第一阶段
(第一章 策划和定义项目-13)
1.1 顾客的呼声
1.1.1 市场调研 1.1.2 历史保Hale Waihona Puke 记录和质量信息 1.1.3 小组经验
1.2 业务计划和市场策略 1.3 产品/过程标杆数据 1.4 产品/过程设想
特殊特性
ISO/TS16949:2002标准7.3.2.3 组织应确定特殊特性,并且: 在控制计划中包括所有的特殊特性 与顾客规定的定义和符号相符合 对过程控制文件,包括图样、FMEAs、控 制计划及作业指导书,用顾客的特殊特性符 号或组织的等效符号或说明来加以标识,以 包括对特殊特性有影响的那些过程步骤 注:特殊特性可包括产品特性和过程参数
共49项
二、APQP基础知识介绍
(2、五个阶段的解释)
● 阶段一:立项阶段 ● 阶段二:样件阶段-原型/工装 ● 阶段三:试生产前的准备阶段 ● 阶段四:试生产阶段 ● 阶段五:量产阶段
二、APQP基础知识介绍
(3、APQP的实施方式)
● 由跨职能小组完成 ● 跨职能小组也称多方论证小组或跨部
门小组或项目小组 ● 跨职能小组一般包括工程,制造﹑材
产品质量先期策划/控制计划 ( Advanced Product Quality Planning and Control Plan )
第一版 1992年3月生效 第二版 2008年11月生效,除非顾客有特别规
定 版权由戴姆勒克莱斯勒公司、福特汽车公司和
通用汽车公司所有
一、APQP的作用
(APQP的目的)
五大工具手册APQP、PPAP、SPC、MSA、FMEA

五大工具手册APQP、PPAP、SPC、MSA、FMEA1.产品质量先期策划(APQP)、2.测量系统分析(MSA)、3.统计过程控制(SPC)、4.生产件批准(PPAP)5.潜在失效模式与后果分析(FMEA)一、APQP(Advanced Product Quality Planning)即产品质量先期策划,是一种结构化的方法,用来确定和制定确保某产品使顾客满意所需的步骤。
产品质量策划的目标是促进与所涉及的每一个人的联系,以确保所要求的步骤按时完成。
有效的产品质量策划依赖于公司高层管理者对努力达到使顾客满意这一宗旨的承诺。
产品质量策划有如下的益处:◆引导资源,使顾客满意;◆促进对所需更改的早期识别;◆避免晚期更改;◆以最低的成本及时提供优质产品二、PPAP:生产件批准程序(Production part approval process)ppap生产件提交保证书:主要有生产件尺寸检验报告,外观检验报告,功能检验报告,材料检验报告;外加一些零件控制方法和供应商控制方法;主要是制造形企业要求供应商在提交产品时做ppap文件及首件,只有当ppap文件全部合格后才能提交;当工程变更后还须提交报告。
ppap是对生产件的控制程序,也是对质量的一种管理方法。
三、SPC(Statistical Process Control)即统计过程控制,主要是指应用统计分析技术对生产过程进行适时监控,科学区分出生产过程中产品质量的随机波动与异常波动,从而对生产过程的异常趋势提出预警,以便生产管理人员及时采取措施,消除异常,恢复过程的稳定从而达到提高和控制质量的目的。
SPC非常适用于重复性的生产过程,它能够帮助组织对过程作出可靠的评估,确定过程的统计控制界限判断过程是否失控和过程是否有能力;为过程提供一个早期报警系统,及时监控过程的情况,以防止废品的产生,减少对常规检验的依赖性,定时以观察以及系统的测量方法替代大量检测和验证工作。
- 1、下载文档前请自行甄别文档内容的完整性,平台不提供额外的编辑、内容补充、找答案等附加服务。
- 2、"仅部分预览"的文档,不可在线预览部分如存在完整性等问题,可反馈申请退款(可完整预览的文档不适用该条件!)。
- 3、如文档侵犯您的权益,请联系客服反馈,我们会尽快为您处理(人工客服工作时间:9:00-18:30)。
日本标准是日本工业标准调查会(JISC)负责制订的。
日本工业标准调查会(JISC)是根据日本工业标准化法建立的全国性标准化管理机构。
成立于1946年2月。
1921年 4月,成立工业品规格统一调查会(JESC),开始有组织、有计划地制定和发布日本国家标准。
1929年该会代表日本参加国家标准化协会国际联合会(ISA)。
1946年 2月工业品规格统一调查会解散,并同时成立工业标准调查会。
1949年7月 1日日本开始实施《工业标准化法》,根据该法设立日本
工业标准调查会。
1952年 9月日本工业标准调查会代表日本参加国际标准化组织(ISO),1953年参加国际电工委员会(IEC)。
日本工业标准调查会的主要任务是组织制定和审议日本工业标准(JIS);调查和审议 JIS标志指定产品和技术项目。
它是通商产业省主管大臣以及厚生、农林、运输、建设、文部、邮政、劳动和自治等省的主管大臣在工业标准化方面的咨询机构,就促进工业标准化问题答复有关大臣的询问和提出的建议,经调查会审议的JIS标准和JIS标志,由主管大臣代表国家批准公布。
调查会由 240名以内的委员组成。
委员由有关大臣从有经验的生产者、消费者、销售商和第三方的专家和政府职员中推荐,经通产省大臣任命,任期2年。
正、副会长由委员中遴选产生。
另设 258名专门委员,负责调查专门事项,根据会长提议,由通产省大臣任命。
遇有必要调查审议特别事项时,设临时委员,该事项调查审议结束,临时委员即行退任。
调查会由总会、标准会议、部会和专门委员会组成。
标准会议是它的最高权力机构,负责管理调查会的全部业务,制定综合规划,审议重大问题;审查部会的设置与撤销,以及规定专门委员会的比例,协调部会之间的工作。
标准会议按审议工作范围设立土木、建筑、钢铁、有色金属、能源等29个部会。
各部会由会长指定的委员组成,负责审查专门委员会的设置与撤销,协调专门委员会之间的工作,对专门委员会通过的JIS标准草案进行终审。
专门委员会是每项技术专题设置一个,由生产、使用、销售等各方面的代表按比例选举产生,负责审查JIS标准的实质性内容。
调查会共设有2 000多个专门委员会,有委员 2万名左右。
调查会隶属于通商产业省工业技术院。
工业技术院标准部是调查会的办事机构,负责调查会的日常工作,实际上是具体制定日本工业标准化方针、计划和落实计划的管理机构。
标准部下设标准、材料规格、纺织和化学规格、机械规格和电气规格 5个课。
日本工业标准(JIS)是日本国家级标准中最重要、最权威的标准。
根据日本工业标准化法的规定,JIS标准对象除药品、农药、化学肥料、蚕丝、食品以及其他农林产品另制定有专门的标准或技术规格外,涉及到各个工业领域。
其内容包括:产品标准(产品形状、尺寸、质量、性能等)、方法标准(试验、分析、检路与测量方法和操作标准等)、基础标准(术语、符号、单位、优先数等)。
专业包括:建筑、机械、电气、冶金、运输、化工、采矿、纺织、造纸、医疗设备、陶瓷及日用品、信息技术等。
1990年以来,JIS标准总数一直保持在8 200个左右。
其中:产品标准约4 000个,方法标准1 600个,基础标准2 800个。
截至 1999年 3月底,共有现行JIS标准8 428个。
德国粉末冶金材料标准 DIN 30910 Teil4。