动臂液压缸铰点位置的优化设计
液压系统的优化设计

液压系统的优化设计随着科技的进步和社会的快速发展,液压系统在各个领域应用越来越广泛,如工业、农业、建筑、航空等。
在这些领域中,液压系统扮演着重要的角色,如汽车制造、飞机制造、船舶制造、建筑机械等需要大量使用液压系统。
因此,液压系统的优化设计显得尤为重要。
一、液压系统的基本原理及构成液压系统是一种利用液体传递能量,并将互不相干的行动组合起来的系统。
液压系统的基本原理是利用液体的压缩性小和容积稳定,通过不同的工作机构来完成某一特定工作的机械装置。
液压系统的构成包括工作部分、执行部分、控制部分和电气部分。
其中,工作部分是指液压泵或发生器、液压马达和液压缸;执行部分是指在液压系统中完成具体工作的机械设备或装置,如液压升降机、液压抓取器等;控制部分是指液压系统中的各种控制装置,如液压阀等;电气部分是指支持液压系统的电气设施,如液压泵电机等。
二、1. 功率密度与效率液压系统的设计中需要考虑功率密度和效率两个方面。
功率密度指的是液压系统单位体积或单位重量所能输出的功率大小。
增加液压系统的功率密度可以提高其工作效率。
效率指的是液压系统的机械工作输出功率与输入功率之比。
在液压系统的设计中应该尽量提高系统的效率,以减少能量损失。
2. 选择合适的组件液压系统的设计中,应该根据不同的工作要求选择合适的组件,如液压泵、液压马达、液压缸和液压阀等。
同时,应注意选择正确的组件配合以确保系统的稳定和可靠性。
例如,液压泵需要与液压马达和液压阀相匹配,才能形成合理的液压系统。
3. 液体选用液压系统液体的选用也是液压系统优化设计的重要因素之一。
液压系统液体应具有压缩性小、稳定粘度、抗氧化性能强、抗腐蚀性好、防爆性能高、热稳定性好等特点,以确保液压系统的可靠性和长寿命。
4. 控制方式确定液压系统的控制方式是液压系统设计中的一个关键问题。
液压系统的控制方式应根据工作条件和要求确定。
例如,对于一些要求精度高、速度快、工作负荷重的工作环境,需要采用闭环控制液压系统,以保证工作的稳定性和可靠性。
凿岩台车伸缩臂油缸铰点设计及注意事项
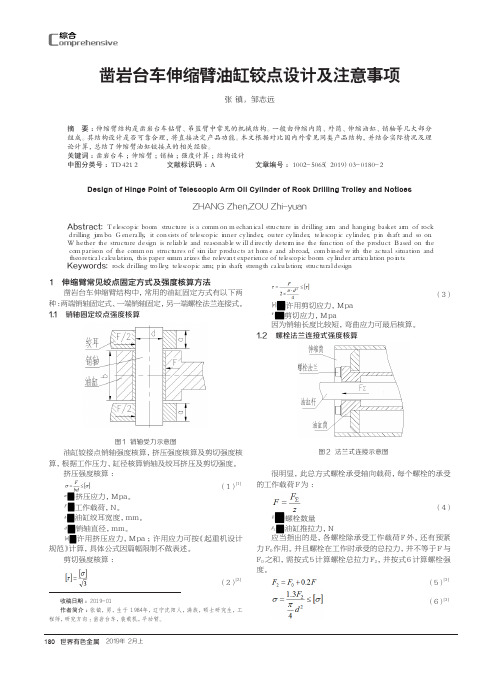
世界有色金属 2019年 2月上180凿岩台车伸缩臂油缸铰点设计及注意事项张 镇,邹志远(辽宁 沈阳 110001)摘 要:伸缩臂结构是凿岩台车钻臂、吊篮臂中常见的机械结构。
一般由伸缩内筒、外筒、伸缩油缸、销轴等几大部分组成。
其结构设计是否可靠合理,将直接决定产品功能。
本文根据对比国内外常见同类产品结构,并结合实际情况及理论计算,总结了伸缩臂油缸铰接点的相关经验。
关键词:凿岩台车;伸缩臂;销轴;强度计算;结构设计 中图分类号:TD421.2 文献标识码:A 文章编号:1002-5065(2019)03-0180-2Design of Hinge Point of Telescopic Arm Oil Cylinder of Rock Drilling Trolley and NoticesZHANG Zhen,ZOU Zhi-yuan(Shenyang 110001,China)Abstract: Telescopic boom structure is a common mechanical structure in drilling arm and hanging basket arm of rock drilling jumbo. Generally, it consists of telescopic inner cylinder, outer cylinder, telescopic cylinder, pin shaft and so on. Whether the structure design is reliable and reasonable will directly determine the function of the product. Based on the comparison of the common structures of similar products at home and abroad, combined with the actual situation and theoretical calculation, this paper summarizes the relevant experience of telescopic boom cylinder articulation points.Keywords: rock drilling trolley; telescopic arm; pin shaft; strength calculation; structural design1 伸缩臂常见绞点固定方式及强度核算方法凿岩台车伸缩臂结构中,常用的油缸固定方式有以下两种:两端销轴固定式、一端销轴固定,另一端螺栓法兰连接式。
剪叉式高空作业平台力学分析与油缸安装铰点位置优化

剪叉式高空作业平台力学分析与油缸安装铰点位置优化剪叉式高空作业平台是用途十分普遍的高空作业设备。
它独特的剪叉机械结构,能使提供给工作人员施工作业的平台始终与地面保持水平,且承载能力强,稳定性较高。
随着剪叉式平台向着节能、提高能量利用率方面发展, 因此对降低油缸工作时的最大推力、减少剪叉机构受力的研究显得尤为关键。
本文研究在液压缸的布置不发生干涉的前提下, 对油缸的铰点安装位置进行优化并进行实物试验验证, 从而减少油缸的最大推力和提高工作平台举升时的上升平稳性。
主要研究内容及成果如下:(1) 通过对剪叉式平台进行运动学分析, 得到了工作平台上升速度的参数表达式, 在驱动液压缸速度为恒速的条件下,掌握了影响平台上升平稳性的相关参数。
对剪叉式平台的油缸进行力学分析, 得到影响油缸推力的油缸位置安装参数;对剪叉机构各铰点位置进行受力分析, 得出各组剪叉杆各铰接孔受力情况。
⑵根据剪叉机构基于AMESin软件建立其仿真模型,得到剪叉机构动态举升过程, 运行仿真后剪叉结构的性能参数以及某些参数的变化曲线, 包括平台的上升速度变化曲线、油缸举升推力曲线等。
(3) 通过理论推导与仿真分析分别在液压油缸不发生干涉的情况下, 以减少油缸最大推力为目标对油缸安装铰点位置进行优化, 得到合理的油缸安装位置参数; 通过液压测试仪测量油缸活塞在优化前后的推力变化曲线,对优化所得曲线进行验证,吻合良好,证明了优化方案的合理性。
⑷采用ANSYS Workbenc软件对优化后的改变油缸安装铰点位置的剪叉臂组进行静力学与疲劳寿命分析, 确定了结构应力集中和最大疲劳损伤的发生区域对剪叉臂的疲劳寿命进行估算, 针对于剪叉臂疲劳寿命薄弱区域进行了结构改进为剪叉臂的设计提供了参考依据以上研究成果已成功取得优化方案的预期效果, 并在实物测试试验进行验证此方案将为结构更复杂的双油缸剪叉式平台优化提供参考依据。
悬臂式液压起重机变幅机构三铰点设计的分析
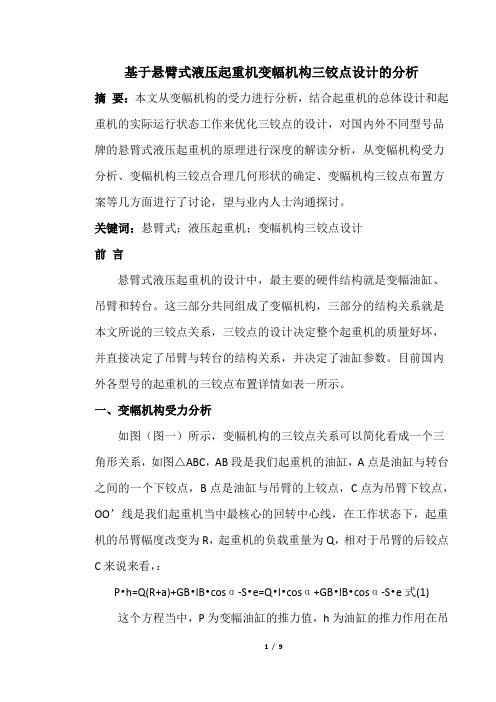
基于悬臂式液压起重机变幅机构三铰点设计的分析摘要:本文从变幅机构的受力进行分析,结合起重机的总体设计和起重机的实际运行状态工作来优化三铰点的设计,对国内外不同型号品牌的悬臂式液压起重机的原理进行深度的解读分析,从变幅机构受力分析、变幅机构三铰点合理几何形状的确定、变幅机构三铰点布置方案等几方面进行了讨论,望与业内人士沟通探讨。
关键词:悬臂式;液压起重机;变幅机构三铰点设计前言悬臂式液压起重机的设计中,最主要的硬件结构就是变幅油缸、吊臂和转台。
这三部分共同组成了变幅机构,三部分的结构关系就是本文所说的三铰点关系,三铰点的设计决定整个起重机的质量好坏,并直接决定了吊臂与转台的结构关系,并决定了油缸参数。
目前国内外各型号的起重机的三铰点布置详情如表一所示。
一、变幅机构受力分析如图(图一)所示,变幅机构的三铰点关系可以简化看成一个三角形关系,如图△ABC,AB段是我们起重机的油缸,A点是油缸与转台之间的一个下铰点,B点是油缸与吊臂的上铰点,C点为吊臂下铰点,OO’线是我们起重机当中最核心的回转中心线,在工作状态下,起重机的吊臂幅度改变为R,起重机的负载重量为Q,相对于吊臂的后铰点C来说来看,:P•h=Q(R+a)+GB•lB•cosα-S•e=Q•l•cosα+GB•lB•cosα-S•e式(1)这个方程当中,P为变幅油缸的推力值,h为油缸的推力作用在吊臂铰点C上距离值,α是吊臂与地面的夹角角度,l是吊臂的长度,GB 是吊臂自身的重量,lB是吊臂的重心和铰点C之间的距离,s是吊臂拉线的拉力值,e是随着α角度的变化S与铰点C之间动态距离数值。
因为S•e<<Q(R+a),式(1)可简化为:P•h=Q•l•cosα+GB•lB•cosα。
式(2)式(2)表明,当起重机的额定载荷Q确定后,油缸推力P是仰角α和力臂h的函数。
仰角α和力臂h是由变幅机构三铰点的几何形状决定的,即△ABC的形状决定油缸推力P。
液压自卸汽车举升机构铰支点位置优化设计
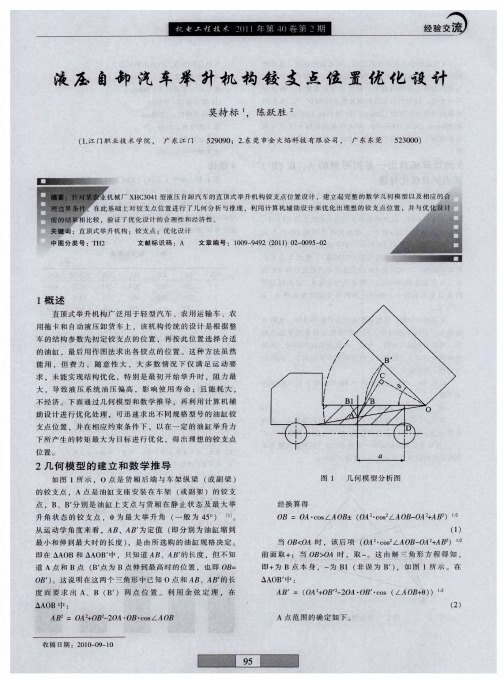
取 8 0r ( 时 O O , 罔 1中 斜 线 区域 为 A 点 可 用 0 tm 此 i A= D) 位 置 范 同 . 点 位 置 只 知 道 在 O 直 线 上 ( 厢 底 中 轴 .B B 货
矩 最 大 . 以后 逐 渐 减 小 , 同 时 在 举 升 过 程 中 如 果 逐 步 卸
序 号 3是 采 用 不 同 的 油 缸 参 数 ( 缸 径 与 序 号 l 但 、2 相 同 )计 算 来 的结 果 .其 动力 臂 比 序号 2更 长 : ( 6 — 8 9 6 4 6 4 1 0 3 % ,举 升 力 比 原 方 案 减 少 3 % ,效 果 4 )/ 4 x 0 %= 5 5 更佳 。
货 , 则 阻 力矩 减 小更 快 ,所 以 ,在 扁 动 油 缸 举 升 时 ,如 果
油 缸 举 升 力动 力 力臂 越 长 , 则 所 需 的 举 升 力 越 小 ,油 缸 压
力 越 省 ,效 果 越 佳 。 延长 A B.过 O 点 作 垂 线 与 A B延 长 线 于 C .O 即 为 C
参考 文 献 :
求出O C的 最 大 值 ( 一。 具 体 就 是 将 前 述 所 求 一 系列 ) C 有 效 点 A,B ( 点 所 对 应 的 O B) A、 0 数 值 代 入 式
() 3 ,用 计 算 机 算 出对 应 的 一 系 列 O C值 ,其 中 最 大 值 为本 例 所 优 化 的 结 果 ( 0 一) 如 图 2所 示 。 即 C 。
科 ,高 级 讲 师 。研 究 领 域 : 内燃 机 构 造 、机 械 制 造 工 艺 学 。 已发 表论文 1 篇。 1
液压系统中的液压缸设计与优化

液压系统中的液压缸设计与优化液压系统是一种常见的动力传输和控制系统,广泛应用于工程和机械领域。
其中,液压缸作为液压系统的重要组成部分,承担着将液压能转化为机械能的关键任务。
本文将探讨液压系统中液压缸的设计与优化。
一、液压缸的基本原理液压缸是一种能够直接转换液压能为机械能的装置。
其基本原理是借助液力传递,通过压力作用使油液推动活塞,从而产生线性运动。
液压缸的组成主要包括气缸筒、活塞、密封元件、传动杆等。
当液压缸接收到液压系统提供的压力油后,压力油进入气缸筒的一侧,将活塞推向另一侧,从而带动传动杆运动。
液压缸的工作过程中,需要满足密封性好、承载能力高、运动平稳等要求。
二、液压缸的设计指标在液压缸的设计过程中,需要考虑以下几个主要指标:1. 力矩和力的要求:液压缸的设计需要满足所需输出力矩和力的要求。
根据工作环境和应用场景的不同,液压缸所需的力矩和力将有所差异。
2. 自重和加载负荷:液压缸在工作时需要克服自重和加载负荷,因此需要根据实际情况确定液压缸的承载能力和稳定性。
3. 运动速度:液压系统中的液压缸的运动速度需要与机械设备的运作速度匹配。
运动速度太快可能导致过载和损坏,而速度太慢可能降低工作效率。
4. 尺寸与重量:液压缸的尺寸和重量直接影响安装和使用的灵活性。
设计过程中需要考虑液压缸的尺寸与重量对机械系统的影响。
三、液压缸的优化设计方法为了满足液压缸的设计指标并提高性能,可以采用以下方法进行优化设计:1. 选择适当的密封结构:密封结构的合理选择对于液压缸的工作性能至关重要。
应选择质量好、密封性能稳定可靠的密封结构,以减小泄漏风险。
2. 优化内部结构:合理设计液压缸内部结构,包括活塞的设计、传动杆的选择和导向装置的设计等。
内部结构的优化可以提高液压缸的工作效率和控制性能。
3. 选用合适的材料:液压缸的工作环境要求其具有良好的抗压、耐腐蚀和磨损性能。
应选择适合的材料,提高液压缸的使用寿命和可靠性。
4. 优化液压缸的控制方式:液压缸的控制方式包括单向控制和双向控制。
液压缸的优化设计

课程(论文)题目:液压缸的优化设计及仿真分析 内容:摘 要对于一种工程中常用的液压缸,提出了有针对性的设计指标,并介绍了这种液压缸结构参数的优化设计方法。
在pro/MECHANICA 5.0平台上,对优化结果给予了仿真分析,得出优化后的参数有一定的可靠性,为油缸设计制造起到了理论指导作用。
一、前言液压缸是重要的液压元件之一,它的类型很多,本文所讨论的是一种带有反柱结构的液压缸,如图1-1,1-2所示。
图1-1 液压缸三维图R 1R 2R 3R 4R 5R 6P p缸体活柱反向柱图1-2 液压缸二维图图中,R1,R1为缸体的内外径,R3,R4为活柱的内外径,R5,R6为反向柱的内外径。
p 为液体的工作压力,P 为液压缸的推力。
这种液压缸有以下特点: (1)在缸径相同的条件下,液压缸的推力大于普通形式的液压缸,即22222452()P R R R p R pππ=+->(2)活柱受到的轴向压力小于普通液压缸,这有利于液压缸的工作稳定性,即2225()R R p Pπ-<(3)在该液压缸的基础上,再增加一个外缸体,即可构成双伸缩液压缸。
这种双伸编写好程序后,直接在MATLAB 里调用程序,并将所得解取整,如表5-2所示:R1/mm R2/mm R3/mm R4/mm R5/mm R6/mm 参数优化优化结果过109.14 91.21 82.65 64.79 51.06 44.55 取整110 90 82 65 50 45表5-2优化后液压缸的结构如下图所示:图5-2这种液压缸的缸径参数较多,用优化设计方法实际是合理有效的。
对以上结果过进行分析,可看到在推力为1400KN时,这种液压缸优化设计结果,使重量减少了5%~10%,外径减少了10%~15%。
本文所提出的优化模型是可行的,对工程设计有一定的参考价值。
在实际工程设计中,可参照前述数学模型,选择不同目标函数形式及个数,并根据具体结构要求增减约束条件及合理地选择必要的结构限制尺寸。
利用ANSYS软件进行动臂(四连杆)优化设计

三.利用ANSYS软件进行动臂(四连杆)优化设计3.1有限元模型建立装载机整机的有限元模型是主要是针对力作用的直接部件进行的,主要包括装载机机身上的转台、主要工作部件铲斗、带动铲斗动作的动臂、动力件油缸、以及运动件连杆和摇臂组成。
在实际建模过程中,通常要求设定材料的性能参数与母材相同,这样做的原因是要对各构件的焊接接头进行连续处理,更为重要的一点是为了在后续精力分析中可以有一个光顺的网格划分,在进行有限元模型的建立中,为了更快捷的进行后续计算,以不至于施加于计算机太多计算负荷,将其中不影响结果数据的螺纹孔、倒角等结构进行了移除。
组件几何模型如图3.1所示。
图3.1 工作装置几何模型根据实际情况定义相应材料的性能,包括:弹性模量e = 2.06×106pa,泊松比μ= 0.3,密度ρ= 7850kg / m3。
每个部件均由solid186单元模拟,接头处的销轴由beam188单元模拟,联接单元由销轴与轴套之间的运动关系模拟,而液压缸则由连杆单元模拟。
通过设置诸如截面积,弹性模量和密度之类的参数来实现对实际液压缸的仿真。
要求将元素尺寸控制在15mm〜20mm之内,并在销轴上局部细化网格,这可以提高计算精度。
最后,为了以危险的姿势获得工作装置的整个有限元模型,需要组装每个部件的有限元模型。
有限元模型包括266783个单元,其中包括266638个实体单元,142个梁单元,3个杆单元和444467个节点。
最后,如果装载机转盘需要完全约束,则应采用边界条件。
通过上述过程计算得出的切向和法向挖掘阻力将作为有限元模型中的外部载荷应用于铲斗尖端,如3.2所示。
图3.2 工作装置有限元模型及边界载荷3.2工作装置静强度分析结果据了解,装载机的材料为 q460c 钢,屈服极限为[ ]=235×106 Pa。
结果表明,工作装置的最大应力为802mpa,该应力发生在提升臂的上吊耳的铰孔和铲斗杆的油缸,远远超过了材料的屈服极限。
- 1、下载文档前请自行甄别文档内容的完整性,平台不提供额外的编辑、内容补充、找答案等附加服务。
- 2、"仅部分预览"的文档,不可在线预览部分如存在完整性等问题,可反馈申请退款(可完整预览的文档不适用该条件!)。
- 3、如文档侵犯您的权益,请联系客服反馈,我们会尽快为您处理(人工客服工作时间:9:00-18:30)。
动臂液压缸铰点位置的优化设计
当今,装载机的动臂液压抽基最低位置时,近水平布置者居多,见图1。
在总体设计中整机及工作装置的基本结构参数和掘起力等主要性能参数,以及液压系统工作压力、流量确定以后,进而可初步确定动臂液压缸的直径。
在此基础上应用微型计算机求动臂液压缸在动臂上的最佳位置坐标,同时确定液压缸的最大行程。
此行程应在满足功能的条件下最小,使动臂提升速度最快。
1.动臂液压缸举升力矩、力臂的计算
装载机工作装置位于地面铲掘状态,工作装置对于动臂下铰点O的最小举升力矩T1:
n
T1=η(ΣG i l i+P1C) (1) i=1
式中:G i——工作装置各部件的重力
l i——工作装置各部件的重心至O点的水平距离
P
1
——铲斗最大掘起力
C——铲斗最大掘起力对O点的力臂
η——安全保险系数(1<η<1.5)
若以整机开始向前倾而失稳和条件,确定力矩T
1
,则
P
=Wa/b (2)
T
1=P
C (3)
式中:P0——作用于P1处使整机前倾和最小力W——整机重力
动臂缸总推力P D及其对O点的力臂R M为:
R
M =T
1
/P
D
(5)
式中: n——动臂缸数
D——动臂缸内径
P——动臂缸工作压力与背压的压差
η
M
——动臂缸的机械效率
铲斗满装位于最大举升高度状态时,工作装置对O点的力矩T
2
: n
T
2=η(ΣG
i
l
i
) (6)
i=1 此时,铲斗的重量及重心位置应将物料计算在内。
动臂缸对O点应具备的最小力臂R
N
为:
R
N =T
2
/P
D
(7)
2.动臂缸铰点位置的约束条件与最优解
图1的动臂结构简图见图2。
以动臂与车体的铰点O为原点,建立直角坐标系。
以O为圆心,R M、R N为半径分别作圆,切线B1P、B2Q的交点为A0。
假如动臂缸和车体的铰点为A,连线AB1AB2就是动臂在最低、最高位置时动臂缸推力的作用线。
若它对O点的力臂为R1、R2,显然A点必须处于∠BA0Q的边线及其夹角之内,否则不能满足R1≥R M、R2≥R N,即动臂缸达不到必要的提升力矩T1、T2。
所以必要的约束条件是:
R1≥R M(8)
R2≥R N(9) A点的位置还必须满足下列两式约束:
AB2=L M=2S+K (11)
式中:LN——动臂缸最小安装尺寸
LM——动臂缸最大安装尺寸
S——动臂缸最大行程
K——动臂缸结构尺寸
在图2中,若B
1、B
2
点的位置不变,则在式(10)、(11)的约束下,A点轨迹为近于圆弧的
曲线,与B
1P的交点为A
1
,显然A
1
点及以下轨迹线上的点均满足式(8)~(11)的约束,即为满足
装载机功能要求的无数组解。
其中A
1
点可使S值(动臂缸)最短,R1=R2,相应的S值是唯一的最优解。
然而,此时R2>R N,表明动臂在最高位置时动臂缸有过大的举升力。
如B1、B2可以在一定范围内变动,则不需要变更臂的基本参数L、M、N,只要改变L B、H B或其中一项数值,都可使OB1(OB1=OB2)长度改变。
规律表明,OB1(OB2)减少,会使A1B2线靠近圆2,A1B1也随之减少,A的轨迹连同A1点将靠向A0点,同时A0点也向A1点靠近。
可以找到唯一的OB1(OB2)长度,使A1点与A0点重合,这样便先后达到:
R1=R M(12)
R2=R N(13)
A0B1=L N=S+K (14)
A0B2=L M=2S+K (15) 由于A0B1是最短的,那么S也是最小的,此时的S值、A0、B1、B2的坐标便是一组最优解。
这是在动臂缸直径确定的情况下,以S值最小为优化目标的最优解。
如果OB1再缩短,A点的轨迹将离开∠B1OQ,而得不到可用解。
动臂设计内径D应符合标准系列缸径值,最大安装长度L M与D的比值j也应有一个恰当的范围(15~22),即:
15≤j= L M/D≤22 (17) 增加D值,可使j减小,同时使最优S值也减小;反之,使S增大。
每次改变D值,则需重新计算最优S值及同组解,最后得出完全符合式(12)~(17)6个约束条件的最优解。
3.计算程序设计
为简要说明计算原理,现将中间计算结果R M、R N视为已知,一些常规运算不再详述。
由图2,首先求出B1(x1y1)、B2(x2y2)的坐标,再算出OB1、OB2及角度ω1、ω2、ω3。
当以任意值赋予S变量后,则L N=S+K ,L M=2S+K也为已知。
设L N从B1开始,沿B1P线布置,且A1B1=L N,则A1点的坐标可以求得,A1B2也可求得。
若
Q=∣L M-A1B2∣≤μ (18) 式中:μ——预设计算精度(0.2)
则认为已满足式(12)~(15)最优条件。
计算中控制L B的变化范围,即可满足式(15)的要求。
最后按式(16)的条件检验缸径D,如需改变D值,则要重复以上计算,多一个循环层次。
4.铰点位置的坐标变换
按以上计算得到的一组最优解S、A0(x0,y0)、B1(L1,H B)。
但A0点在机体上,或B1点在动臂上。
由于结构原因不允许在此位置时,可以适当进行调整。
实施原则是:保持OA、OB1、OB2长度不变,使它们同时顺时针或反时针旋转同样角度,其A0、B2新位置坐标即为所要求的。
这样,原计算机的最优S值、L M、L N发生变化。
5.关于计算点的讨论
本方法以动臂处于最低和最高位置为计算点。
那么,能否保证动臂处于任何位置时驱动力矩总大于阻力矩呢?对此,扼要分析如下:
在装载机装满物料由最低至最高位置的全过程中,以动臂最外伸出时举升阻力矩最大,但一般不超过最低位置举升时的1.4倍。
而我们计算最低位置时的驱动力矩,是按照能产生足够大的掘起力这一要求计算的,其值远大于举升全过程中的最大阻力矩。
而且,动臂由最低位置向上转动时,其驱动力矩还会增大,动臂缸转动α角度时产生最大驱动力矩,而后开始下降,直至动臂转到最外伸出位置时,其驱动力矩总是大于最大阻力矩。
这一规律很好地保证了铲斗高出地面一定距离时,仍具有足够大的掘起力。
显然,动臂处于最高位置点的计算很有必要,且需足够大的安全保险系数。
动臂由最外伸出位置伸到最高点的过程中,阻力矩和驱动力矩都逐渐减小,且变化规律相近,只要这两端的驱动力矩比阻力矩有一定的余量,其中间过程也能保证驱动力矩大于阻力矩。
从以上分析可知,动臂处于最低和最高点位置的计算,可保证动臂处于任何位置时,动臂缸都具有足够的驱动力。
单斗反铲液压挖掘机动臂缸铰点位置的优化设计与装载机类同,其计算点除了动臂处于最低和最高位置外,还应计算向外伸出强力挖掘位置点。