音箱旋钮注射模的设计
旋钮的塑料模具设计

旋纽模具的设计一、塑件的工艺性分析1、塑件的原材料分析塑件的材料采用聚甲基丙烯酸甲酯,属热塑性塑料,该塑料具有如下的成型特性:●无定形料、吸湿性大、不易分解。
●质脆、表面硬度低。
●流动性中等,溢边值0.03mm左右,易发生填充不良、缩孔、凹痕、熔接痕等缺陷。
●宜取高压注射,在不出现缺陷的条件下宜取高料温、模温,可增加流动性,降低内应力、方向性,改善透明度及强度。
●模具浇注系统应对料流阻力小,脱模斜度应大,顶出均匀,表面粗糙度应好,注意排气。
●质透明,要注意防止出现气泡、银丝、熔接痕及滞料分解、混入杂质。
2、塑件的结构和尺寸精度及表面质量分析1)塑件的结构分析该零件的总体形状为圆形,结构比较简单。
2)塑件尺寸精度的分析该零件的重要尺寸,如,30.9±0.09mm的尺寸精度为3级,次重要尺寸3.75±0.07mm的尺寸精度为4级,其它尺寸均无公差要求,一般可采用8级精度。
由以上的分析可见,该零件的尺寸精度属中等偏上,对应模具相关零件尺寸的加工可保证。
从塑件的壁厚上来看,壁厚最大处为4.5mm,最小处为2.25mm,壁厚差为2.25mm,较为均匀。
3)表面质量的分析该零件的表面要求无凹坑等缺陷外,表面无其它特别的要求,故比较容易实现。
综上分析可以看出,注射时在工艺参数控制得较好的情况下,零件的成型要求可以得到保证。
3、塑件的体积重量计算塑件的重量是为了选用注射机及确定模具型腔数。
计算得塑件的体积:V=9132mm3计算塑件的质量:公式为W=Vρ根据设计手册查得聚甲基丙烯酸甲酯的密度为ρ=1.18kg/dm3,故塑件的重量为:W=Vρ=9132×1.18×10-3=10.776g根据注射所需的压力和塑件的重量以及其它情况,可初步选用的注射机为:SZ-60/40型注塑成型机,该注塑机的各参数如下表所示:4、塑件的注射工艺参数的确定根据情况,聚甲基丙烯酸甲酯的成型工艺参数可作如下选择,在试模时可根据实际情况作适当的调整。
智能音箱注塑模具加工装置的研究及应用

智能音箱注塑模具加工装置的研究及应用摘要:智能音箱市场近年来呈现了持续快速增长的趋势,随着人工智能和物联网技术的不断进步,智能音箱作为智能家居和人工智能技术的重要组成部分,在现代生活中扮演着越来越重要的角色,其广泛应用涵盖了诸多领域。
本文旨在剖析智能音箱注塑模具加工装置的研究及应用,期望可以进一步凸显对智能音箱注塑模具加工装置优化的需求,以确保生产的高效性和产品质量的稳定性,为智能音箱行业持续发展提供有力支持。
关键词:智能音箱注塑模具;加工装置;研究;应用前言注塑模具在制造业中扮演着至关重要的角色,尤其是在智能音箱的生产过程中,作为塑料制品生产的关键工艺装备,注塑模具直接影响着产品的质量、成本和生产效率。
因此,注塑模具质量的稳定与优化直接影响着智能音箱产品的制造质量和企业的市场竞争力,保证注塑模具清洁与良好维护对于提高模具的使用寿命、保证产品质量和生产效率具有重要意义。
1智能音箱的广泛应用和重要性智能音箱市场近年来呈现了持续快速增长的趋势,随着人工智能和物联网技术的不断进步,智能音箱作为智能家居和人工智能技术的重要组成部分,在现代生活中扮演着越来越重要的角色,其广泛应用涵盖了诸多领域。
智能音箱作为智能家居系统的中枢,能够通过语音指令控制家居设备,如灯光、温度调节、安防系统等,为用户带来便捷与舒适。
智能音箱不仅可以播放音乐、广播电台,还能通过互联网提供丰富的信息服务,如新闻、天气、股票等实时资讯,满足用户多样化的需求。
通过人工智能技术,智能音箱能够执行诸多任务,如提醒日程安排、制定购物清单、查询食谱、翻译语言等,有效提升用户的生活效率和便利性。
智能音箱利用先进的语音识别与自然语言处理技术,能够与用户进行自然、智能的语音交互,为用户提供更加智能化、便捷化的服务体验。
这些应用领域的不断拓展与智能音箱市场的迅速增长,彰显了智能音箱在提升生活品质、促进智能家居发展以及推动人工智能技术创新方面的重要作用。
这也进一步凸显了对智能音箱注塑模具加工装置优化的需求,以确保生产的高效性和产品质量的稳定性,为智能音箱行业持续发展提供有力支持。
毕业设计——旋钮的注塑模设计

毕业设计——旋钮的注塑模设计旋钮的注塑模设计【摘要】本篇论文为关于旋钮注塑模的设计,以生产产品的数量及工艺等要求来确定用注射成型的方法来生产。
因为旋钮需要生产的数量太多,所以要求再设计时应注意要有较高的注射率,同时使用的系统要有自动脱模的功能,而且对塑件的表面要求很高,不能有损伤,如果塑件的表面要求不是很高的话可以采用侧浇口,同时要有自动脱模的功能。
对于模具的型腔我们可以考虑采用一模两腔平衡的装置,并采用侧浇口浇注结构,对于模具的推出结构采用四推丝杆的推出机构。
模具的设计中应具有冷却系统,这样可以保证塑件的工艺性能。
【关键词】:成型工艺分析;注射机的选择;模具设计目录未找到目录项。
(七)模架的选择 (6)四、模具的总装图 (7)总结 (9)参考文献 (10)谢辞 (11)引言旋钮在现代生活中有着广泛的应用,它在家庭生活以及工业加工等方面起着不可忽视的作用,方便了人们的生活同时提高了人们的生活效率。
由于旋钮在生活中人们每天都离不开,所以得保证它所使用的材料对人体无害,采用材料为PMMA。
同时它的设计应该让人们使用方便,根据市场的需要一般它的外表也要设计的合理美观赏心悦目。
其一般都是用注塑模来制造的,因为注射模制造能够提高经济效益提高工作效率。
用塑料来作为旋钮的材料也使得材料使用相对于其它材料来说更为轻便。
对于从生产方的角度来说,它们不仅要考虑到市场以及消费人员的利益,同时也得考虑到自己的生产成本,再从产品设计、材料到生产需要全面考虑以生产出经济适用的产品。
一、旋钮塑件的工艺分析(一)塑件成型工艺分析零件图纸:如图1-1图1-1产品名称:旋钮产品材料:聚丙烯材料特性:该产品具有无毒、无味、强度和刚度均优等特点,同时还具有很高的抗疲劳的特点,聚丙烯在高温的情况下还具有电性能和绝缘性,同时也不受温度的影响,它适合用于耐腐蚀和绝缘的零件。
一般常见的腐蚀溶剂对其基本不起作用,且还可以用与制作餐具。
材料成型性能:聚丙烯因其是结晶料,吸湿性也比较小,所以它容易发生融体的破裂,聚丙烯也不能长时间的与热金属接触,否则会致使聚丙烯发生分解。
旋钮外壳注射模具设计说明书

旋钮外壳注射模具设计说明书设计人:指导教师:刘海初设计时间:2011年12月一、塑件图材料:ABS生产批量:10万件塑件具体尺寸见三维图。
塑件为旋钮盖子,要求下端能放入杯体即可。
由于盖子本身具有一定柔性,故对上盖精度要求不高,对密封性无要求。
二、工艺性分析材料性能取收缩率为0.5%2、塑件分析(1)形状特性体积 =3824.757361687 mm^3面积 =7848.654803147mm^2质量 = 0.030091264 kg塑件形状较为规则,易于成型。
(2)厚度分析塑件平均壁厚0.95,最大壁厚1.02,塑件局部壁厚均匀。
ABS极限流动长度与塑件厚度的比值为250:1,塑件最大流程与壁厚大约在54:1.25,流程中无尖锐拐角,故注塑时流动性较好。
(3)拔模分析塑件外表面侧壁拔模角为3度,内表面侧壁拔模角为3度,满足脱模要求。
(4)塑件精度塑件为日常用品,精度要求不高,从加工经济性考虑,选用7级精度等级。
三、成型方案为提高生产率,初步确定模具采用三板式大水口模具成型,一出二,推件板推出,其简图如下:模具温度40度,熔体温度98度。
四、注塑机选用选用SZ250/1250卧式注射机,其参数如下:1、最大注射量每次注射两个塑件,重量为60g,浇注系统凝料为 1.830g,总注射量约为61.83g,选用注射机最大注射量为270g,为理论注射量的23%。
五.型芯型腔设计、分型面选在塑件最大轮廓处。
1、型腔设计型腔为圆柱形凸缘式结构,如图,材料采用P20。
型腔壁厚的计算(1)按刚度计算侧壁11443310361.15() 1.15()16[]2100000.03ph s E δ⨯≥=⨯=⨯㎜ 底板11443310360.56()0.56()7.76[]2100000.03ph h E δ⨯≥==⨯㎜(2)按强度计算公式侧壁1122[]400[()1]23[()1]0.6[]2400210s r p σσ≥-=-=--⨯11222220230.87()0.87() 4.47[]400pr h σ⨯≥==型腔压力p=10Mpa 塑件高度h=36㎜ 弹性模量E=210000 Mpa 允许变形量[]δ=0.03㎜ 塑件半径r=23㎜材料许用应力[]σ=400 Mpa因按强度计算结果远小于按刚度计算结果,故型腔壁厚按满足刚度要求取侧壁厚20㎜,底部厚8㎜。
家用迷你音响外壳的注射模设计

优秀设计毕业设计题目家用迷你音响外壳的注射模设计系别专业班级姓名学号指导教师日期设计任务书设计题目:家用迷你音响外壳的注射模设计设计要求:1.确定合理工艺方案2.设计合理的模具结构3.在模具的设计中最好有创新4.设计要全面介绍模具的工作原理5.内容丰富、文字精练、讲述详细、实用价值高6.模具的设计有效地体现出实用的特色设计进度要求:1. 11月28日——12月 3 日搜集模具相关资料及前期准备工作2. 12月 4 日——12月13日模具基本类型与工作部分零件尺寸计算3. 12月14日——12月20日模具整体及其零件的设计和绘制结构尺寸图4. 12月21日——12月26日毕业论文的校核、修改、定稿及打印装订指导教师(签名):摘要 (4)前言 (5)1 家用迷你音响外壳塑件的工艺分析 (7)1.1成形工艺分析 (7)1.2塑件的成形工艺参数确定 (8)2 模具基本结构设计及模架选择 (10)2.1确定成形方法 (10)2.2型腔布置 (10)2.4浇注系统设计 (12)2.5脱模机构设计 (17)2.6导向机构的设计 (17)2.7 选择模架 (19)3 选择成形设备 (21)3.1注塑机的选择 (21)3.2工艺参数的校核 (22)4 模具结构尺寸的设计计算 (25)4.1型腔尺寸计算 (26)4.2型芯的尺寸计算 (27)5 模具总装图及模具的装配、试模 (31)5.1模具总装图及模具的装配 (31)5.2模具的安装试模 (31)结束语 (34)致谢 (35)参考文献 (36)本次的毕业设计是家用小音响外壳注塑模的设计,小巧、轻便、美观且实用性强,是家用电器的一种,是良好的播放器工具。
塑料制品具有原料来源丰富,价格低廉,性能优良等特点。
它在电脑、手机、汽车、电子、汽车、电机、电器、仪器仪表、家电和通讯产品制造中具有不可替代的作用,应用极其广泛。
注射成形是成形热塑件的主要方法,因此应用范围很广。
注射成形是把塑料原料放入料筒中经过加热熔化,使之成为高黏度的流体,用柱塞或螺杆作为加压工具,使熔体通过喷嘴以较高压力注入模具的型腔中,经过冷却、凝固阶段,而后从模具中脱出,成为塑料制品。
音响外壳注塑模具设计说明书
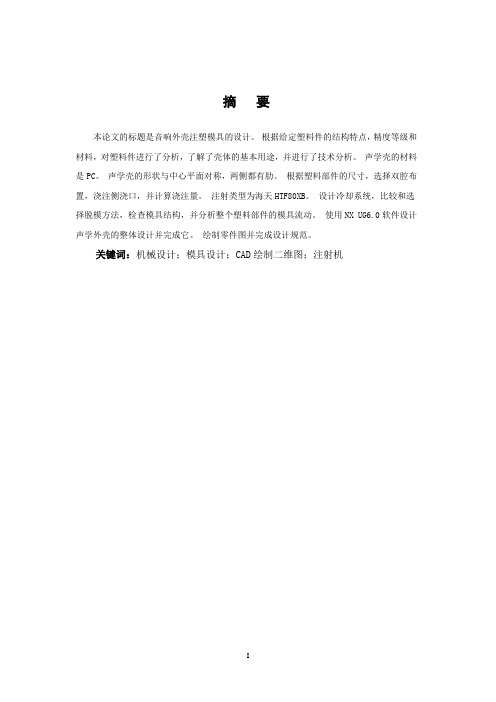
摘要本论文的标题是音响外壳注塑模具的设计。
根据给定塑料件的结构特点,精度等级和材料,对塑料件进行了分析,了解了壳体的基本用途,并进行了技术分析。
声学壳的材料是PC。
声学壳的形状与中心平面对称,两侧都有肋。
根据塑料部件的尺寸,选择双腔布置,浇注侧浇口,并计算浇注量。
注射类型为海天HTF80XB。
设计冷却系统,比较和选择脱模方法,检查模具结构,并分析整个塑料部件的模具流动。
使用NX UG6.0软件设计声学外壳的整体设计并完成它。
绘制零件图并完成设计规范。
关键词:机械设计;模具设计;CAD绘制二维图;注射机ABStractThe topic of this paper for the juicer filter injection mold design, according to the given the structure characteristics of the plastic parts, precision grade and the qualitative analysis of plastic parts, understand the basic purposes, juicer filter manufacturability analysis, juicer filter is made of PC, the appearance of wall covered with center face said, both sides have stiffened plate, choose according to the size of the plastic parts of one module and one cavity arrangement, side pouring gate, the pouring amount calculated, injection model USES the Haitian HTF80XB, to design of cooling system, compares the demoulding mode choice, and to check the mould structure, and to the whole plastic mold flow analysis, using NX UG6.0 software for the integral design of the mould of juicer filter and complete detail drawings of rendering, and finish the preparation of the design specification.Key words: mechanical design; die design; CAD drawingtwo-dimensional map; injection machine目录摘要 (I)第1章绪论 (1)第2章塑料材料分析 (4)2.1 塑料材料的基本特性 (4)2.2 塑件材料成型性能 (4)第3章塑件的工艺分析 (5)3.1 塑件的结构设计 (6)3.2 塑件尺寸及精度 (7)3.3 塑件表面粗糙度 (7)3.4 塑件的体积和质量 (7)第4章注射成型工艺及模具结构确定 (8)4.1、注射成型工艺过程分析[5] (8)4.2 浇口种类的确定 (8)4.3 型腔数目的确定 (9)4.4 注射机的选择和校核 (9)4.4.1 注射量的校核 (10)4.4.2 锁模力的校核 (11)4.4.3 模具与注射机安装校核 (11)第5章注射模具结构设计 (13)5.1 分型面的设计 (13)5.2 型腔的布局 (13)5.3 浇注系统的设计 (14)5.3.1 浇注系统组成 (15)5.3.2 确定浇注系统的原则 (15)5.3.3 主流道的设计 (15)5.3.4 分流道的设计 (17)5.3.5 浇口的设计 (18)5.4 注射模成型零部件的设计[7] (18)5.4.1 成型零部件结构设计 (18)(1)、凹模宽度尺寸的计算 (19)(2)、凹模长度尺寸的计算 (20)(3)、凹模高度尺寸的计算 (20)(4)、凸模宽度尺寸的计算 (20)(5)、凸模长度的计算 (20)(6)、凸模高度尺寸的计算 (20)5.4.2 成型零部件计算 (22)5.5 排气结构设计 (22)5.7 脱模机构的设计 (22)5.7.1 脱模机构的选用原则 (22)5.7.2 脱模机构类型的选择 (23)5.7.3 推杆机构具体设计 (23)5.8 注射模温度调节系统 (23)5.8.1 温度对塑件的影响 (24)5.8.2 冷却系统之设计规则 (24)5.9 模架及标准件的选用 (25)5.9.1 模架的选用 (25)第6章模具材料的选用 (26)6.1 成型零件材料选用 (26)6.2 注射模用钢种 (26)总结 (27)致谢 (31)参考文献 (32)。
一体式音箱壳体注射模设计

2
模具设计
根据塑件的形状特点及具体要求,模具设计中主
要考虑以下几点。
2.1
分型面的选择
根据塑件结构特点,分型面选在顶部和底部的
状及尺寸如图 1 所示。该塑件形状为圆柱体,主要外
中心位置,这样有利于简化侧斜抽芯机构,顶部的
为喇叭安装孔,背面为电池安装凹槽,顶部按键凹
3.支撑柱
11.滑块 T 块
26.斜顶杆
4.复位杆
12.动模挤紧块
19.浇口板
6.锁滑块垫板螺丝
13.分段滑块座
20.定模座板
27、28、38.顶杆
36.动模型芯
图 5 模具结构
5.动模板
30.滑块
15.定模板
22.浇口套
31.楔紧块
8.锁油缸垫板螺丝
16.分段滑块
23.模具圆垫脚
32.滑块镶件
17.
唐志玉,李德群,徐佩弦. 塑料模具设计师指南[M]. 北京:
国防工业出版社,
1999.
杨丽萍,华丽霞.模内贴标成型工艺及其塑件设计[J].塑
料工业,
2007,
(10)
第一作者简介:王波群,男,1983 年生,江西上饶
人,在职博士,讲师/技师,主要从事模具设计与制造
图 12 改进后压板与吸塑模具配合结构
塑件成型。该模具经过 50 多万次的生产验证,模具设计结构合理,工作可靠,生产出的塑
件能满足功能要求,对左右是通孔且前后都是凹槽的特殊复杂壳体的注射模设计有一定
的参考作用。
关键词:
音箱壳体;油缸深抽芯滑块;斜滑块;抽芯机构
中图分类号:
TQ320.66
音响外壳注塑模具设计
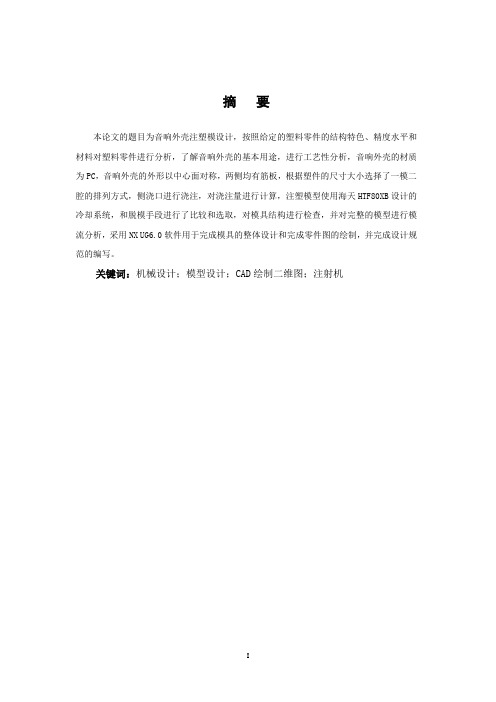
摘要本论文的题目为音响外壳注塑模设计,按照给定的塑料零件的结构特色、精度水平和材料对塑料零件进行分析,了解音响外壳的基本用途,进行工艺性分析,音响外壳的材质为PC,音响外壳的外形以中心面对称,两侧均有筋板,根据塑件的尺寸大小选择了一模二腔的排列方式,侧浇口进行浇注,对浇注量进行计算,注塑模型使用海天HTF80XB设计的冷却系统,和脱模手段进行了比较和选取,对模具结构进行检查,并对完整的模型进行模流分析,采用NX UG6.0软件用于完成模具的整体设计和完成零件图的绘制,并完成设计规范的编写。
关键词:机械设计;模型设计;CAD绘制二维图;注射机ABStractThe topic of this thesis is the design of injection molding mold for acoustic shell. According to the structural characteristics, accuracy level and materials of a given plastic part, the plastic part is analyzed, the basic purpose of the acoustic shell is understood, and the process analysis is carried out. The material of the acoustic shell is PC. The shape of the acoustic shell is symmetrical in the center, with ribs on both sides. According to the size of the plastic part, a mode of arrangement with two cavities is selected. The side gate is poured, the pouring amount is calculated, and the injection model is used. The cooling system designed by Haitian HTF 80XB, Compared and selected with the demoulding method, the die structure was checked, and the complete model was modeled. The NXUG6 .0 software was used to complete the overall design of the mold and complete the drawing of the part diagram, and the design specification was completed.Key words: mechanical design; die design; CAD drawingtwo-dimensional map; injection machine目录摘要 (I)第1章绪论 (1)第2章塑料材料分析 (4)2.1 塑料材料的基本特性 (4)2.2 塑件材料成型性能 (4)第3章塑件的工艺分析 (6)3.1 塑件的结构设计 (6)3.2 塑件尺寸及精度 (7)3.3 塑件表面粗糙度 (7)3.4 塑件的体积和质量 (7)第4章注射成型工艺及模具结构确定 (8)4.1、注射成型工艺过程分析[5] (8)4.2 浇口种类的确定 (8)4.3 型腔数目的确定 (9)4.4 注射机的选择和校核 (9)4.4.1 注射量的校核 (11)4.4.2 锁模力的校核 (12)4.4.3模具与注射机安装校核 (12)第5章注射模具结构设计 (14)5.1 分型面的设计 (14)5.2 型腔的布局 (14)5.3 浇注系统的设计 (15)5.3.1 浇注系统组成 (16)5.3.2 确定浇注系统的原则 (16)5.3.3 主流道的设计 (16)5.3.4 分流道的设计 (18)5.3.5 浇口的设计 (19)5.4 注射模成型零部件的设计[7] (19)5.4.1 成型零部件结构设计 (19)(1)、凹模宽度尺寸的计算 (20)(2)、凹模长度尺寸的计算 (21)(3)、凹模高度尺寸的计算 (21)(4)、凸模宽度尺寸的计算 (21)(5)、凸模长度的计算 (21)(6)、凸模高度尺寸的计算 (22)5.4.2 成型零部件计算 (24)5.5 排气结构设计 (24)5.7 脱模机构的设计 (24)5.7.1 脱模机构的选用原则 (24)5.7.2 脱模机构类型的选择 (24)5.7.3 推杆机构具体设计 (24)5.8 注射模温度调节系统 (25)5.8.1 温度对塑件的影响 (25)5.8.2 冷却系统之设计规则 (26)5.9 模架及标准件的选用 (26)5.9.1 模架的选用 (26)第6章模具材料的选用 (28)6.1 成型零件材料选用 (28)6.2 注射模用钢种 (28)总结 (29)致谢 (33)参考文献 (34)第1章绪论1.1 塑料简介塑料是高分子聚合物材料,核心的化学成分是树脂,是有机的聚合物,它的特色是可以在一定的温度和压力下流动,可以任意地形成不同形状和大小的结构,塑料零件形成之后,形状不会发生改变。
- 1、下载文档前请自行甄别文档内容的完整性,平台不提供额外的编辑、内容补充、找答案等附加服务。
- 2、"仅部分预览"的文档,不可在线预览部分如存在完整性等问题,可反馈申请退款(可完整预览的文档不适用该条件!)。
- 3、如文档侵犯您的权益,请联系客服反馈,我们会尽快为您处理(人工客服工作时间:9:00-18:30)。
课题任务书系:专业:附表五毕业设计(论文)开题报告任务书系:专业:答辩资格审查表注:此表中内容综述由学生填写,资格审查项目由指导教师填写。
摘要注射模具是生产各种工业产品的重要工艺装备,是现代生产制造行业的核心,在大多数国家,注射模具设计与制造技术已经成为衡量一个国家生产制造技术先进与否的关键。
本设计通过对音箱旋钮的工艺、材料分析,选用适当的注射机,并拟定合理的注射成型工艺方案。
在模具设计中,采用一模两腔式的布局。
并通过对分型面、浇注系统、成型零部件、顶出脱模机构、冷却系统的设计,选用合适的标准模架及标准件,完成对音箱旋钮的一套完整的模具设计方案。
关键词:音箱旋钮;注射;模具设计ABSTRACTInjection mold is an important tooling for industry products,it is the core of the modern manufacturing industry and in most countries injection mold design and manufacturing technology have become the keywords of measuring it is production technology.This design through analysed the process and material of chemical instrument cover,choosed the proper injection machine,and roughcast reasonable injection mold design scheme.In the design process,it used the configuration of two cavityin one plate.And through designing the parting line,running gate system,modeling parts,ejection stripping mechanism,cooling system,choosing adaptive standard mould base and standard parts,it finised the whole mold design scheme for the chemical instrument cover.Keywords:Speaker knob;injection;mold design目录摘要ABSTRACT前言 (1)1、塑件的工艺性分析 (4)1.1、塑件的原材料分析 (4)1.2、塑件的结构和尺寸精度及表面质量分析 (7)1.3、塑件的体积重量 (9)1.4、塑件的注射工艺参数的确定 (12)1.5、注塑成型的准备 (12)2、型腔数的确定及浇注系统的设计 (14)2.1、塑料配方说明 (14)2.2、分型面的选择 (15)2.3、型腔数的确定 (16)2.4、确定型腔的排列方式172.5、浇注系统的设计 (17)2.6、剪切速率的校核 (20)2.7、模具材料的选择 (21)3、排气、冷却系统的设计与计算 (22)3.1、排气系统的设计 (22)3.2、冷却系统的设计与计算 (23)4、模具工作零件的设计与计算 (25)4.1、凸凹模的设计 (25)4.2、型腔侧壁厚度和底板厚度的计算 (26)4.3、模架的选用 (27)4.4、导向与定位机构 (28)5、脱模机构的设计与计算 (30)5.1、顶出系统设计 (30)5.2、推件板的厚度 (31)5.3、顶杆直径的计算 (32)6、注射机与模具各参数的校核 (35)6.1、工艺参数的校核 (35)6.2、安装参数的校核 (36)参考文献 (37)致谢 (43)前言自20世纪80年代以来,我国的经济逐渐起飞,也为模具产业的发展提供了巨大的动力。
20世纪90年代以后,大陆的工业发展十分迅速,模具工业的总产值在1990年仅60亿元人民币,1994年增长到130亿元人民币,1999年已达到245亿元人民币,2000年增至260~270亿元人民币。
今后预计每年仍会以10℅~15℅的速度快速增长。
目前,我国17000多个模具生产厂点,从业人数五十多万。
除了国有的专业模具厂外,其他所有制形式的模具厂家,包括集体企业,合资企业,独资企业和私营企业等,都得到了快速发展。
其中,集体和私营的模具企业在广东和浙江等省发展得最为迅速。
例如,浙江宁波和黄岩地区,从事模具制造的集体企业和私营企业多达数千家,成为我国国内知名的“模具之乡”和最具发展活力的地区之一。
在广东,一些大集团公司和迅速崛起的乡镇企业,为了提高其产品的市场竞争能力,纷纷加入了对模具制造的投入。
例如,科龙,美的,康佳和威力等知名集团都建立了自己的模具制造中心。
中外合资和外商独资的模具企业则多集中于沿海工业发达地区,现已有几千家。
在模具工业的总产值中,企业自产自用的约占三分之二,作为商品销售的约占三分之一。
其中,冲压模具约占50℅(中国台湾:40℅),塑料模具约占33℅(中国台湾:48℅),压铸模具约占6℅(中国台湾:5℅),其他各类模具约占11(中国台湾:7℅)。
中国台湾模具产业的成长,分为萌芽期(1961——1981),成长期(1981——1991),成熟期(1991——2001)三个阶段。
萌芽期,工业产品生产设备与技术的不断改进。
由于纺织,电子,电气,电机和机械业等产品外销表现畅旺,连带使得模具制造,维修业者和周边厂商(如热处理产业等)逐年增加。
在此阶段的模具包括:一般民生用品模具,铸造用模具,锻造用模具,木模,玻璃,陶瓷用模具,以及橡胶模具等。
1981年——1991年是台湾模具产业发展最为迅速且高度成长的时期。
有鉴于模具产业对工业发展的重要性日益彰显,自1982年起,台湾地区就将模具产业纳入“策略性工业适用范围”,大力推动模具工业的发展,以配合相关工业产品的外销策略,全力发展整体经济。
随着民生工业,机械五金业,汽机车及家电业发展,冲压模具与塑料模具,逐渐形成台湾模具工业两大主流。
从1985年起,模具产业已在推行计算机辅助模具设计和制造等CAD/CAM技术,所以台湾模具业接触CAD/CAM/CAE/CAT技术的时间相当早。
成熟期,在国际化,自由化和国际分工的潮流下,1994年,1998年,由台湾地区政府委托金属中心执行“工业用模具技术研究与发展五年计划”与“工业用模具技术应用与发展计划”,以协助业界突破发展瓶颈,并支持产业升级,朝向开发高附加值与进口依赖高的模具。
1997年11月间台湾凭借模具产业的实力,获得世界模具协会(ISTMA)认同获准入会,正式成为世界模具协会会员,。
整体而言,台湾模具产业在这一阶段的发展,随着机械性能,加工技术,检测能力的提升,以及计算机辅助设计,台湾模具厂商供应对象已由传统的民用家电,五金业和汽机车运输工具业,提升到计算机与电子,通信与光电等精密模具,并发展出汽机车用大型钣金冲压,大型塑料射出及精密锻造等模具。
模具主要类型有:冲模,锻摸,塑料模,压铸模,粉末冶金模,玻璃模,橡胶模,陶瓷模等。
除部分冲模以外的的上述各种模具都属于腔型模,因为他们一般都是依靠三维的模具形腔是材料成型。
(1)冲模:冲模是对金属板材进行冲压加工获得合格产品的工具。
冲模占模具总数的50%以上。
按工艺性质的不同,冲模可分为落料模,冲孔模,切口模,切边模,弯曲模,卷边模,拉深模,校平模,翻孔模,翻边模,缩口模,压印模,胀形模。
按组合工序不同,冲模分为单工序模,复合模,连续模。
(2)锻模:锻模是金属在热态或冷态下进行体积成型是所用模具的总称。
按锻压设备不同,锻模分为锤用锻模,螺旋压力机锻模,热模锻压力锻模,平锻机用锻模,水压机用锻模,高速锤用锻模,摆动碾压机用锻模,辊锻机用锻模,楔横轧机用锻模等。
按工艺用途不同,锻模可分为预锻模具,挤压模具,精锻模具,等温模具,超塑性模具等。
(3)塑料模:塑料模是塑料成型的工艺装备。
塑料模约占模具总数的35%,而且有继续上升的趋势。
塑料模主要包括压塑模,挤塑模,注射模,此外还有挤出成型模,泡沫塑料的发泡成型模,低发泡注射成型模,吹塑模等。
(4)压铸模:压铸模是压力铸造工艺装备,压力铸造是使液态金属在高温和高速下充填铸型,在高压下成型和结晶的一种特殊制造方法。
压铸模约占模具总数的6%。
(5)粉末冶金模:粉末冶金模用于粉末成型,按成型工艺分类粉末冶金模有:压模,精整模,复压模,热压模,粉浆浇注模,松装烧结模等。
模具所涉及的工艺繁多,包括机械设计制造,塑料,橡胶加工,金属材料,铸造(凝固理论),塑性加工,玻璃等诸多学科和行业,是一个多学科的综合,其复杂程度显而易见。
20世纪80年代开始,发达工业国家的模具工业已从机床工业中分离出来,并发展成为独立的工业部门,其产值已超过机床工业的产值。
改革开放以来,我国的模具工业发展也十分迅速。
近年来,每年都以15%的增长速度快速发展。
许多模具企业十分重视技术发展。
加大了用于技术进步的投入力度,将技术进步作为企业发展的重要动力。
此外,许多科研机构和大专院校也开展了模具技术的研究与开发。
模具行业的快速发展是使我国成为世界超级制造大国的重要原因。
今后,我国要发展成为世界制造强国,仍将依赖于模具工业的快速发展,成为模具制造强国。
中国塑料模工业从起步到现在,历经了半个多世纪,有了很大发展,模具水平有了较大提高。
在大型模具方面已能生产48"(约122CM)大屏幕彩电塑壳注射模具,6.5KG 大容量洗衣机全套塑料模具以及汽车保险杠和整体仪表板等塑料模具,精密塑料模方面,以能生产照相机塑料件模具,多形腔小模数齿轮模具及塑封模具。
经过多年的努力,在模具CAD/CAE/CAM技术,模具的电加工和数控加工技术,快速成型与快速制模技术,新型模具材料等方面取得了显著进步;在提高模具质量和缩短模具设计制造周期等方面作出了贡献。
尽管我国模具工业有了长足的进步,部分模具已达到国际先进水平,但无论是数量还是质量仍满足不了国内市场的需要,每年仍需进口10多亿美元的各类大型,精密,复杂模具。
与发达国家的模具工业相比,在模具技术上仍有不小的差距。
今后,我国模具行业应在以下几方面进行不断的技术创新,以缩小与国际先进水平的距离。
(1)注重开发大型,精密,复杂模具;随着我国轿车,家电等工业的快速发展,成型零件的大型化和精密化要求越来越高,模具也将日趋大型化和精密化。
(2)加强模具标准件的应用;使用模具标准件不但能缩短模具制造周期,降低模具制造成本而且能提高模具的制造质量。