混流式水轮机设计实例-叶片设计
混流式水轮机转轮叶片三维造型的研究

三维 模 型 , 由于 软件 的本 身 缺 陷 可 能 造 成 叶 片 模 型 的 不正 常 凹 凸现 象 , 能 提供 精 确有 效 的三 维 模 型 。 不
图 1 木模 截面图直接生成 的 3 D图形
1 混 流 式 转 轮 叶 片 三 维 造 型 的原 理
木 模截 面 图 直 接 生 成 的 3 图形 , 图 1所 示 。 D 如
G m i中生 成 三 维 模 型 。 先 找 出 叶 片 的几 组 轴 面 截 a bt
线; 在此基础 上用 一元 理论 绘制 出水 流过 叶片工 作
面 和背 面 的类 流线 ; 类流 线 组成 叶 片工 作 面和 背 面 , 用
收 稿 日期 : 2 0 0 7—1 0一l 6
生成面域以 .a 文件输 出。打开 G m i直接读人从 s t ab t
要精确的三维数字化模 型 ; 以前 的电站大多数都只 而 有 木模 图 , 而 基 于 木 模 图 的三 维 造 型 是 很 有 意 义 因
的。 因混 流式 机 组 应用 广 泛 , 本 文 以混 流 式 水 轮 机 故
转轮 叶片 为例 进 行 三维 造 型分 析 。
如 果直 接 利 用 木 模 图 的 二 维 线 条 为 边 界 来 生 成
维普资讯
20 0 8年 7月
农 机 化 研 究
第 7期
混 流 式 水 轮 机 转 轮 叶 片 三 维 造 型 的 研 究
曾永 忠 ,陈 波, 陈 果 ,黄 煌
( 华 大 学 能 源与 环 境 学 院 ,成 都 西
60 3 ) 10 9
摘
要 : 传 统 的水轮 机 转 轮设 计包 括 流体 动 力学 设计 和 几 何设 计 , 几 何 设 计 中采 用 二维 木 模 图来 表 示 叶 片 , 在 无
基于MATLAB-UG的混流式水轮机叶片三维建模
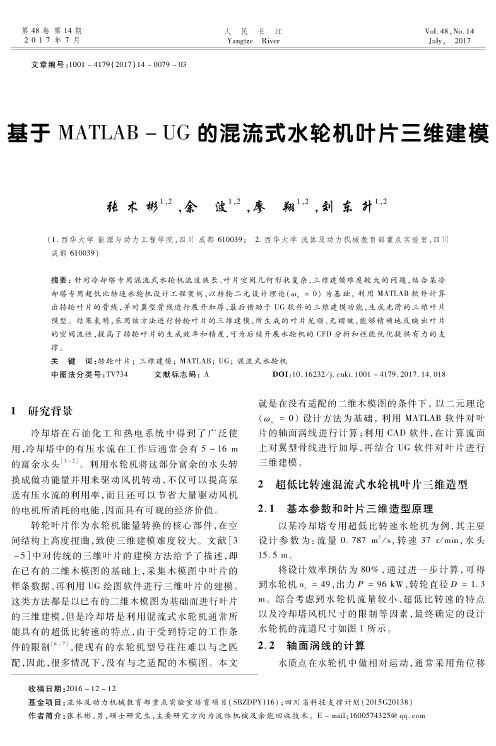
第48卷第14期2 0 1 7年7月人民长江Yangtze RiverVol.48,No. 14July,2017文章编号:1001 -4179(2017) 14 -0079-03基于MATLAB- U G的混流式水轮机叶片三维建模祐术彬,会波“2,参靭“2,釗i計1,2(1.西华大学能源与动力工程学院,四川成都610039; 2.西华大学流体及动力机械教育部重点实验室,四川成都 610039)摘要:针对冷却塔专用混流式水轮机流道狭长、叶片空间几何形状复杂,三维建模难度较大的问题,结合某冷却塔专用超低比转速水轮机设计工程案例,以转轮二元设计理论(〇>…= 0)为基础,利用MATLAB软件计算出转轮叶片的骨线,并对翼型骨线进行展开加厚,最后借助于UG软件的三维建模功能,生成光滑的三维叶片模型。
结果表明,采用该方法进行转轮叶片的三维建模,所生成的叶片光顺、无稽皱,能够精确地反映出叶片的空间流性,提高了转轮叶片的生成效率和精度,可为后续开展水轮机的C FD分析和性能优化提供有力的支撑。
关键词:转轮叶片;三维建模;MATLAB; U G;混流式水轮机中图法分类号:TV734 文献标志码:A D O I:10. 16232/j. cnki. 1001 -4179. 2017. 14. 018i研究背景冷却塔在石油化工和热电系统中得到了广泛使 用,冷却塔中的有压水流在工作后通常会有5 ~ 16 m 的富余水头[1_2]。
利用水轮机将这部分富余的水头转 换成做功能量并用来驱动风机转动,不仅可以提高栗 送有压水流的利用率,而且还可以节省大量驱动风机 的电机所消耗的电能,因而具有可观的经济价值。
转轮叶片作为水轮机能量转换的核心部件,在空 间结构上高度扭曲,致使三维建模难度较大。
文献[3 -5]中对传统的三维叶片的建模方法给予了描述,即在已有的二维木模图的基础上,采集木模图中叶片的 样条数据,再利用U G绘图软件进行三维叶片的建模。
带副叶片的混流式水轮机转轮流场的计算
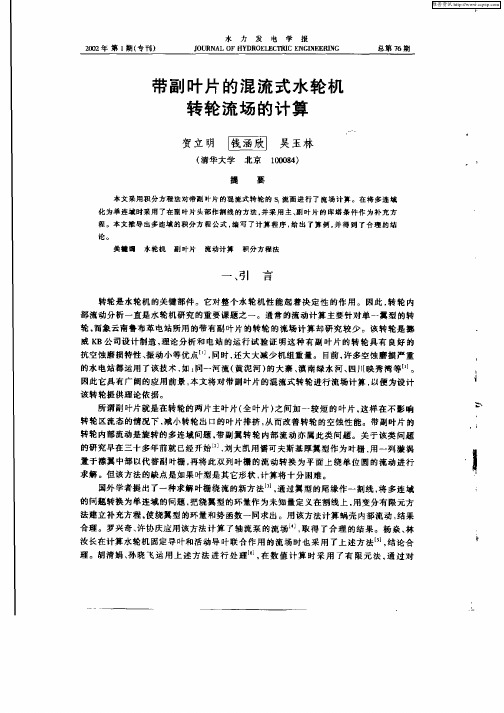
二、 计算 数学 模 型
对水 轮机 内部流动 进行数 值计算 , 设 水流 是 非粘 性 的不 可 压定 常 流 。取 与转 轮一 假
起旋 转 的正 交 曲线坐 标 , 图 1 其 中 口 =cnt 通过 转轮 轴线 的平 面 ,: os是 s 如 , os是 q =cnt
=;Ⅳ= 1 :
= () h1 q.巩= 毒
式 中 h 为 所取基 准点处 的半径 , ( ) r O 为所取基 准点 处的 流层 厚度 , h为流层 的相 对 厚度 。
S 流面基本 方程 的连续 方程 和运动无 旋方 程表 述如下 :
杀( 15( = J ) ̄H o - ) q
和 q, 映射平 面上 的连续方 程和无 旋方 程 : 得
杀 0 ∽ l
( 1 )
把沿 回转 面的流 动保角 映射 为沿 x—Y平 面 的流 动 , 分别 对应 于正 交 曲线 坐标 轴 口 ,
妻:。 3 } 一x。 o I
引入流 函数 , 得映射 平 面上 的流 函数 方程 :
维普资讯
贺 立 明萼 : 副 叶 片 的混 流式 承 轮 机 转 轮 流 场 的 计 算 带
13 6
A5 5 7转轮 ( 验转 轮 ) 试 计算 , 与试验 数据进 行 比较 , 并 二者 比较吻合 。
本文 的主要 工作 在于 : 用 在半 叶片头部作 割线 的方 法将多 连域化 为 单连域 , 采 推导 出 多 连域的积 分方 程公式 , 并采 用 Gus 分法进 行离 散 求解 。 同传 统的有 限元 法相 比, as积 该
水轮机叶片毕业设计

一、工程背景及水轮机叶片简介图 1、为某型水轮机叶片的CAD模型。
在发电工作工程中水流由进水口流向出水口,叶片承受水流的冲刷从而开始运动,这种运动通过传动轴传递到发电机,从而带动发电机工作发电。
但是水轮机在工作仅仅一年多时间以后,就有数片叶片发生了疲劳断裂事故,使得水轮机不能正常工作发电,造成了一定的经济损失,同时也说明水轮机叶片在结构的设计方面确实存在不完善之处。
然而,由于水轮机在水下进行工作,很难通过测量得方法获得叶片上应力和位移的分布情况,也就无法知道叶片为何会断裂,无法有效的改善叶片的几何结构。
在这种情况下,长江水利委员会陆水枢纽局的委托我们对LS591水轮机叶片的进行Ansys有限元模拟计算,获得叶片的应力场和位移场的分布,从而为叶片断裂事故分析提供技术支持,并对叶片结构的改进提供具体方案。
传动轴进水口出水口图1、CAD模型二、ANSYS简介及解题步骤1、ANSYS简介对于大多数工程技术问题,由于物体的几何结构比较复杂或则问题的某些特征是非线性的,我们很难求得其解析解。
这类问题的解决通常具有两种途径:一是引入简化假设,但这种方法只是在有限的情况下是可行的。
也正是因为这样,有限元数值模拟的技术产生了。
有限元方法通过计算机程序在工程中得到了广泛的应用。
到80年代初期,国际上较大型的面向工程的有限元通用软件达到了几百种,其中著名的有:ANSYS,NASTRAN,ASKA, ADINA,SAP等。
其中,以ANSYS为代表的工程数值模拟软件,即有限元分析软件,不断的吸取计算方法和计算机技术的最新进展,将有限元分析、计算机图形学和优化技术相结合,已成为解决现代工程问题必不可少的有力工具。
尤其是在某些环境中,样机试验是不方便的或者不可能的,而利用ANSYS软件,对这个问题有了很好的解决。
本文中水轮机叶片是在水下的环境进行工作,测量很难进行,利用有限元软件ANSYS这个问题得到了很好的解决。
2、ANSYS分析步骤ANSYS分析可以分为三个步骤:a、创建有限元模型(1)创建或读入几何模型根据实体模型按照给定的尺寸建立模型或者直接导入已经生成的几何模型,并对其进行一定程度的修复、简化等。
混流式水轮机活动导叶CFD计算分析
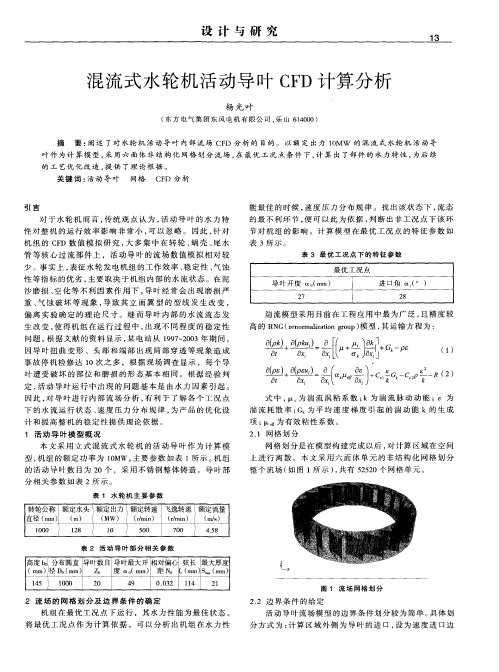
表 1 水 轮 机 主 要 参 数
网 格划 分 是在 模 型 构 建完 成 以后 , 对计 算 区域在 空 间
上 进 行 离 散 。本 文采 用 六 面 体 单 元 的 非 结构 化 网格 划 分 整 个 流场 ( 如 图 1所示 ) , 共有 5 2 5 2 0个 网格单 元 。
少 。事 实 上 , 表 征 水轮 发 电机组 的工 作效 率 、 稳定性 、 气 蚀 性 等 指标 的优 劣 , 主 要取 决 于 机 组 内部 的水 流状 态 。在 泥 沙磨损 、 空 化 等 不 利 因 素作 用 下 , 导 叶 经 常 会 出 现 磨 损 严
重、 气蚀破坏等现象 , 导 致 其 立 面 翼 型 的 型线 发 生 改 变 ,
=
=
㈩ ¨
定, 活 动 导 叶运 行 中 出现 的 问题 基 本 是 由水 力 因 素 引起 。
因此 , 对 导 叶进 行 内部 流 场 分 析 , 有 利 于 了 解 各 个 工 况 点
嘉 簧
譬 2
式中 , 为湍流涡粘系数 ; k为 湍 流 脉 动 动 能 ; e 为 湍流耗散率 ; G 为 平 均 速 度 梯 度 引起 的 湍 动 能 k的 生 成 项; 为 有 效粘 性 系数 。
表 2 活 动 导 叶部 分 相 关 参数
高度 b 。 1 分布圆直 【 导叶数 目 导 叶最大开 相对偏心 弦长 最大厚度 ( m m ) J 径I ) 0 ( m m) J Z 0 度o / 0 ( m m) 距 M L( m m) s n ( m s )
r
转轮公 称 额定水头 额定出力 额定转速 飞逸转速 I 额定流量
直径 ( mi l 1 )
混流式水轮机叶片自由曲面的延展
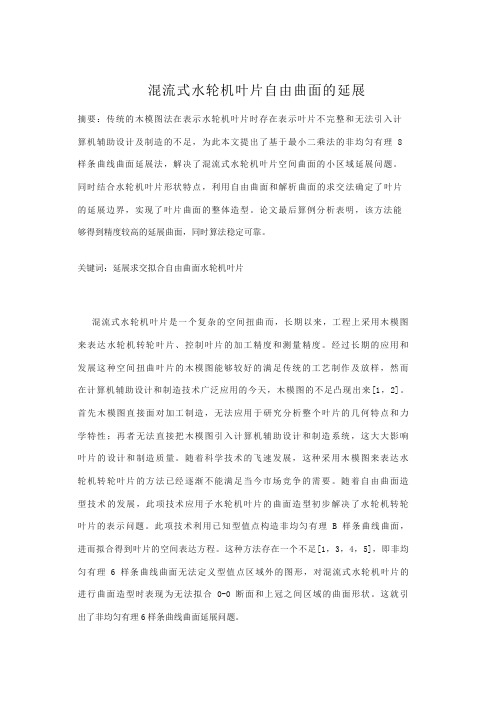
混流式水轮机叶片自由曲面的延展摘要:传统的木模图法在表示水轮机叶片时存在表示叶片不完整和无法引入计算机辅助设计及制造的不足,为此本文提出了基于最小二乘法的非均匀有理8 样条曲线曲面延展法,解决了混流式水轮机叶片空间曲面的小区域延展问题。
同时结合水轮机叶片形状特点,利用自由曲面和解析曲面的求交法确定了叶片的延展边界,实现了叶片曲面的整体造型。
论文最后算例分析表明,该方法能够得到精度较高的延展曲面,同时算法稳定可靠。
关键词:延展求交拟合自由曲面水轮机叶片混流式水轮机叶片是一个复杂的空间扭曲而,长期以来,工程上采用木模图来表达水轮机转轮叶片、控制叶片的加工精度和测量精度。
经过长期的应用和发展这种空间扭曲叶片的木模图能够较好的满足传统的工艺制作及放样,然而在计算机辅助设计和制造技术广泛应用的今天,木模图的不足凸现出来[1,2]。
首先木模图直接面对加工制造,无法应用于研究分析整个叶片的几何特点和力学特性;再者无法直接把木模图引入计算机辅助设计和制造系统,这大大影响叶片的设计和制造质量。
随着科学技术的飞速发展,这种采用木模图来表达水轮机转轮叶片的方法已经逐渐不能满足当今市场竞争的需要。
随着自由曲面造型技术的发展,此项技术应用子水轮机叶片的曲面造型初步解决了水轮机转轮叶片的表示问题。
此项技术利用已知型值点构造非均匀有理B样条曲线曲面,进而拟合得到叶片的空间表达方程。
这种方法存在一个不足[1,3,4,5],即非均匀有理6样条曲线曲面无法定义型值点区域外的图形,对混流式水轮机叶片的进行曲面造型时表现为无法拟合0-0断面和上冠之间区域的曲面形状。
这就引出了非均匀有理6样条曲线曲面延展问题。
1基于最小二乘法的非均匀有理B样条曲线曲而延展法1.1延展问题的已知条件现在通用的木模阁在表示水轮机叶片时一般给出等2而的0^)数椐。
如图1所示,由图可以看出,在0-0断而以上只有一个已知型值点,即进水边与上冠的交点,有时甚至还没有表示出这个点;同样在16-16断而以下也只有一个已知型值点,即出水边与下环的交点,有时甚至还没有表示出这个点。
混流式水轮机设计实例-叶片设计
1e
同理,
u
2
9.63m / s
V
o
m2
f ( L 2) 4.45m / s
2
arctan V m 2 24.8
对于其他流线同理可得到以下数据:
u
2e
26.8
0
2
进出口速度三角形的计算结果
流线 L1 r1 528 r2 276 u1 18.43 Vu1 17.13 Vω1 1.3 Vm1 4.1 β1(º) β1e(º) 72.41 74.41 u2 9.63 Vm2 4.45 β2(º) β2e(º) 24.8 26.8
2
1
根据已知,为便于计算取 (V uR)
2
0
r
1
528mm, r 2 276mm, u 1
2 r 1n 60
2 528 333.3 10 60
3
18.43m / s
2 n 2 333.3 34.89 60 60
V
m1
f ( L1) 4.1m / s
在方格纸上绘出V f ( L) 曲线图,L为等势线与流线交点到流 线进口端点的弧线长度。
m
16
Vm(m/s)
15
14
13 12 11
10
9 8 7 6
5
L1 L2 L3 L4 L5
4 3 2
1
0 0 50 100 150 200 250 300 350 400 450 500 550 600 650 700 L(mm)
A
R
n
式中 R----流道出口断面外半径 n----出口断面的圆环个数。 出口断面CD上各轴面分点位置可 用半径rk表示。 K r n R
混流式水轮机转轮叶片技术要求
混流式水轮机转轮叶片技术要求=13。
1.叶片数Z12.水轮机旋转方向:俯视顺时针。
3.叶片材质为VOD精练ZG00Cr13Ni4Mo不锈钢。
4.叶片铸件应符合JB/DQ1554-89《中小型水轮机铸钢件技术条件》。
5.铸件不得有裂纹、气孔、夹渣等铸造缺陷。
6.铸件须退火处理。
7.叶片采用三坐标数控工艺进行加工。
加工精度应满足GB/T10969-1996《水轮机通流部件技术条件》的规定。
8.叶片正、背面型线坐标允许偏差为±0.5mm。
9.叶片头部形状用样板检验。
共检验断面2、3和4等三个断面,头部形状的允许偏差为±1.0mm。
头部样板采用厚度为1.0mm的钢板制作。
10.叶片出水边厚度允许偏差为-0.5~+1.0mm。
11.叶片与上冠相贯面应留3mm的焊接收缩裕量。
本木模图中给出的上冠相贯面尺寸不含收缩裕量。
叶片与下环相贯面按图纸尺寸加工到位。
焊接坡口待与转轮组焊厂家协商后确定。
12.叶片进水边头部修圆后,各断面的最大高度值按图纸要求,允许偏差为±1.5mm。
13.叶片正、背面局部存在的波浪度应低于2/100,叶片背面易遭空蚀部位的波浪度应小于1/100。
14.叶片表面粗糙度不低于1.6~3.2μm。
15.单个叶片理论净重为52kg。
单个叶片重量允许偏差为-3~+5%,叶片平均重量允许偏差为-1~+3%。
叶片出厂时标记实际重量。
16.成品叶片出厂时,须提供下列质量检验报告和其他有关资料各两份。
(1)叶片材质化学成分和机械性能检验报告;(2)叶片制造精度检验报告,内容包括:叶片各断面型线坐标偏差、叶片头部形状偏差、叶片出口边缘厚度偏差、叶片表面波浪度、叶片表面粗糙度、叶片上冠相贯面偏差、叶片下环相贯面偏差、叶片进水边各断面高度偏差、叶片重量等;(3)叶片超声波和磁粉探伤报告;(4)转轮叶片正常检修补焊和打磨防变形有关工艺资料。
17.成品叶片出厂时,须提供2块同材质的标准试块。
混流泵叶片优化设计
混流泵叶片优化设计方案对提高混流泵性能、降低混流泵运行时产生的噪音与振动和提高机组的安全稳定运行提供理论支撑,为今后混流泵的优化设计奠定了一定基础和为企业提供了一套完整的混流泵的优化设计理论和方法。
1.叶轮参数化造型叶片参数化在自动优化中是极其重要的一步。
自动优化中可以选择参数化叶片中的各自有参数进行优化,并以初始参数化叶片为模板进行叶片几何造型、网格划分、流场计算等。
一般在优化设计中,叶片参数化拟合需要一个初始叶片为模板进行拟合,所以首先要根据已有参数设计出一个叶片,然后对叶片用参数化方法去表达,通过对端壁型线、流面控制线、堆叠规律和翼型型线的控制来参数化叶片。
在旋转机械中,可以将叶片角作为可变自由参数,前缘到尾缘的叶片角能很TP唐健.TIF;%30%30;Z5mm,YTS(JZHT7.H图1TS)大程度上影响泵的性能。
之前的研究表明叶片的厚度对泵的水力效率影响不大,所以在本文的参数化拟合中,初始叶片的厚度设置为不变,同样轮缘和轮毂的子午面和出口直径也保持不变。
本文所研究的叶片参数化造型拟合分为两步完成,分别是初始参数化拟合和二次参数化拟合。
参数化后模型如图1所示。
2.性能分析2.1网格划分。
为了提高数值模拟的计算速度和优化过程中有效样本的数量,首先在划分网格时,就采用了多重网格技术。
多重网格方法是提高计算效率、加快收敛方面的一个非常有效的方法。
确定叶轮转速为490r/min、叶片数为6、叶片展向节点数为43和边界层网格单元大小,完成网格的制作,划分得到的叶片网格数为607469。
2.2边界条件设定。
边界条件是指流体在运动或静止的边界条件上给予的确定性条件,所以边界条件的参数直接影响了求解过程和得到的结果。
对导叶式混流泵进行数值模拟,流体介质为清水,密度为997kg/m3,边界条件设置如下:(1)进口边界条件:静态温度为293K,湍流粘度为1e-6m2/s,叶轮进口采用速度进口,速度方向垂直于叶轮进口。
混流式水轮机
/trade/pay_success.htm?biz_order_id=213979720000462&out_trade_no=T200P213979720000462&dealing=T第一节混流式水轮机结构一、概述混流式水轮机是反击式水轮机的一种,其应用水头范围很广,从20~700m水头均可使用。
它结构简单,制造安装方便,运行可靠,且有较高的效率和较低的空蚀系数。
现以图2-1所示的混流式水轮机为例来介绍这种水轮机结构。
水轮机的进水部件是具有钢板里衬的蜗壳,座环支柱也称固定导叶1,在转轮四周布置着导水机构导叶2。
座环支柱具有坚固的上环a和下环b,蜗壳和上下环焊接在一起。
导叶轴颈用衬套(钢或尼龙材料)支承在底环3和固定于顶盖4的套筒5上。
底环固定于座环的下环上面。
顶盖用螺钉6与座环的上环连接。
导水的传动机构是由安置在导水叶上轴颈的转臂12,连杆13和控制环14组成。
导叶的开度0a(从导叶出口边端到相邻导叶背部的最短距离)的改变是通过导水机构的两个接力器16和控制环连接的推拉杆15传动控制环来实现的。
图2-1 HL200-LJ-550水轮机剖面图(高度单位:m,尺寸单位:mm)1—固定导叶;2—导叶;3—底环;4—顶盖;5—套筒;6—螺钉;7—主轴法兰;8—主轴;9—上冠;10—下环;11—叶片;12—转臂;13—连杆;14—控制环;15—推拉杆;16—接力器;17—导轴承;18—泄水锥;a19,b19—上,下迷宫环;a—坐环上环;b—坐环下环;20—连接螺栓由于混流式水轮机应用水头较高,导叶承受的弯曲载荷大,因此导叶的相对高度0b与轴流式水轮机比较起来做得短一些,以减小跨度。
此外,随着水头增高,相同功率下水轮机的过流量减小,这样有可能减小流道的过流载面。
0b一般随水头增加而减小。
导叶和水轮机顶盖4及底环3之间的间隙及相邻导叶在关机时的接合面都会有漏水现象。
一般采用橡胶的或金属制成的密封件,可使导水机构关闭时的漏水量最小。
- 1、下载文档前请自行甄别文档内容的完整性,平台不提供额外的编辑、内容补充、找答案等附加服务。
- 2、"仅部分预览"的文档,不可在线预览部分如存在完整性等问题,可反馈申请退款(可完整预览的文档不适用该条件!)。
- 3、如文档侵犯您的权益,请联系客服反馈,我们会尽快为您处理(人工客服工作时间:9:00-18:30)。
方法二:(也是本次设计所采 用的设计方法) 直接按附录中给定的数据点在 图纸上绘制流道进口在左上方 的流道图。 附录其实就是各条流线的坐标 点,把各个坐标点绘在图纸上 并光滑连接就会得到流道图和 五条流线。
2.检查过水断面面积
在转轮流道内做内切于转轮上冠和转 轮下环的公切圆,如图。自该圆心o 向切点A、B做连线,过点A、B做圆 弧切于OA和OB,用t表示圆弧AB长 度,则母线长度为 2 t (s ) 3 式中 s---弦线AB长度 ρ---内切圆半径 母线AB的形心位于图中D点, 1 1 CD OC h 3 3 则轴面液流过水断面面积为
1e
同理,
u
2
9.63m / s
V
o
m2
f ( L 2) 4.45m / s
2
arctan V m 2 24.8
对于其他流线同理可得到以下数据:
u
2e
26.8
0
2
进出口速度三角形的计算结果
流线 L1 r1 528 r2 276 u1 18.43 Vu1 17.13 Vω1 1.3 Vm1 4.1 β1(º) β1e(º) 72.41 74.41 u2 9.63 Vm2 4.45 β2(º) β2e(º) 24.8 26.8
m pj
r
m
用各自的 b' 校正轴面流线位置。 由此得到第二次近似流线,以此 为基准重新修正过水断面。直至 rm Δb与平均值偏差小于5%时即可。
4.检查流网准确性
1)计算时可以原有等势线为中 线,在其两侧各作一相近的 等势线,如图实线为原等势 线,两边虚线为相近等势 线。
2)由同一组相邻等势线和各轴面 流线组成的各段的
混流式水轮机叶片设计
叶片是水轮机乃至所有流体机械最重要的部 件,它的设计要求也较高,对整个机械的性 能影响较大。同时,叶片的设计工作量较大, 设计步骤较为繁琐,个别步骤需要反复修改。 因此,在设计时应认真对待。下面以设计实例 进行说明。
一. 设计参数:
Hmin=20m Hav=35m Hmax=48m Nr=3692.71Kw 转速n=333.3r/mim Qr=11.95m/s D1=1.34m Hs=1.9m 海拔高程:79m
ΔL(mm)
14.3 13.3 11.7 10.1 13.3 10.4 9.2 8
R/ΔL
29.89 32.48 37.52 44.15 25.789 35.12 41.68 49.56
Δb(mm)
60 56 49.5 43 80 59 48 42
RΔb/ΔL
1793.70 1818.94 1857.30 1898.81 2063.15 2072.37 2000.87 2081.62
t(mm) 842 842 908.3
A=2πrt(mm2) 10.538 7.835 7.022
做出轴面液流过水断面面积沿Lm的变化曲线
A
Lm(m) 2
因扩散形流道易产生脱流而导致较大水力损失, 所以轴面流道过水面积沿Lm应是逐渐减小的。 实际设计中应反复检查修改直到面积变化规律满 足要求。
3.按轴面流速为均匀分布绘制轴面流线
(RΔb/Δl)av Δ(Δb) Δ(Δb)/Δb
-1.62 -0.71 1842.19 0.40 1.28 0.33 0.50 2054.50 -1.28 0.54 -0.027 -0.012 0.008 0.029 0.004 0.008 -0.026 0.013
ςa
L3 L4 L5 L1 L2
ςb
L3
L4 L5
5.计算轴面流速
当流网修正满足要求后,按下 表计算轴面流速Vm
Q V m 2 4L
ΔL---流线上两边等势线之间 的长度
等势线 流线 L1 L2 ΔL(mm) 15 14 Vm(m/s) 4.30 4.60
ςa
L3 L4
L5
12.5 11
9
5.16 5.86
7.16
这里只计算了一条等势线,7 条等势线按同样的方法得到。
A
R
n
式中 R----流道出口断面外半径 n----出口断面的圆环个数。 出口断面CD上各轴面分点位置可 用半径rk表示。 K r n R
2 k
K---由上冠至下环的轴面流线的序 号,K=0、1、2、3、4 用rk确定出口流线分点0、1、2·· ·
3)轴面流线的起点和终点确定 后,就可做出第一次近似的轴 面流线,一般规律为近下环处 流线较密集,在近上冠处流线 较稀疏。根据过水断面与流线 相互垂直的原则,作线垂直于 各轴面流线,并以该线为母线 绕水轮机轴线旋转得到的回转 面就是过水断面。
二.设计步骤 • 1.确定流道几何形状。(比例:1:2)
方法一: 1)根据设计参数可确定比转速,单位参数。按我国水轮机 型谱推荐的额定水头与比转速关系,水轮机的比转速为 2000 2000 20 20 318(m kw) ns H 35 因此,选择比转速在318左右的为宜,选择HL310, D1=1.34m。 2)参照教材或《水轮机设计手册》的转轮流道尺寸确定导 叶相对高度、上冠处曲率半径、下环处曲率半径等参数。 3)按比例换算,并在图纸上绘出流道图。
• 根据计算得到的不同 轴面上的叶片进出口 角度,在baldegen的 Angel View中设计进 出口角度,并给出适 当的包角。
• 利用NACA翼 型给定叶片的 厚度,并进行 调整。 • 给定三个截面 的叶片厚度。
最终调整并得到叶片形状
木模图绘制——1.输出叶片
在UG中做出木模截面,并求出木模截线
混流式水轮机转轮轴面流速沿各流线的分布
6. 进出口三角形计算及绘制
1) 参照《水轮机设计手册》的转轮流道尺寸确定叶片进出口 位置。
2)确定叶片进出口速度矩分布
首先,取定进出口速度矩的比值,一般取 (V uR) (0.02 ~ 0.05)(V uR) (对不同流线可取不同的值)。然后,通过基本方程 (V uR)1(V uR) 2 gH ,计算进出口速度矩并按每根流线在叶 片进出口点的半径计算Vu,按上一步得到的曲线图V m f ( L), 插值得轴面速度Vm,计算进出口角。
7.2
8.5 8.8 8.8
28.5
26.5 23.2 20.3
30.5
28.5 25.2 22.3
绘制每条流线上进出口速度三角形(这里只画出L1的进出口速度三 角形,其它同理)
β1
β2
7. 根据初步的轴面图生成初始叶片
• 调整轴面图,同 时调整轴面流线
• 可以通过求点的方 式来对应bladegen 中的点
在方格纸上绘出V f ( L) 曲线图,L为等势线与流线交点到流 线进口端点的弧线长度。
m
16
Vm(m/s)
15
14
13 12 11
10
9 8 7 6
5
L1 L2 L3 L4 L5
4 3 2
1
0 0 50 100 150 200 250 300 350 400 450 500 550 600 650 700 L(mm)
R b const L
Δb---相邻二轴面流线间等势中 线长度 R---Δb的平均半径 ΔL---各段中间轴面流线长度,如 图。
b 3)若同一组等势线上各段的 R L 不等于常数,则应该校正轴 面流线位置,可计算其平均值。
b R L
则Δb的修正值为
pj
b b R R L i L pj R L pj
1)确定进口的n+1个起点。 图中AB直线为母线,轴面流 线按相邻流面间流量相等绘 制,因过水断面上轴面流速 均匀分布,等分母线AB就可 得到起始断面上轴面流线的 分点。若取n+1条轴面流线, 则二轴面流线的间距为b0/n。 本设计为5条流线,所以n=4。
2)确定出口的n+1个终点 因要求二相邻流面间流量相等,当 轴面流线均匀分布时,轴面流线将 轴面出口断面分为若干个面积相等 的圆环。每个圆环面积为A, 2
4)校正流线
若所绘轴面流线的位置符合要求, 则 r mb const Δb---相邻二流线间母线长度 rm---- Δb的平均半径 若每一过水断面上被二相邻流线 所分各段的rm Δb值不等。需要对 轴面流线进行校正,为此计算过 水断面上rm Δb的断面平均值 (r b) 用平均值校正,b' (r mb) pj
2
1
根据已知,为便于计算取 (V uR)
2
0
r
1
528mm, r 2 276mm, u 1
2 r 1n 60
2 528 333.3 10 60
3
18.43m / s
2 n 2 333.3 34.89 60 60
V
m1
f ( L1) 4.1m / s
输出:dxf
在AUTOCAD中打开
选择俯视图
调整至正常木模图位置
画出木模图
t
A 2 rt
r---母线AB形心至水轮机轴线的距离。
计算各断面面积(这里只计算前三个圆)
lm (mm) 0 510.8 816
12 10 8 6 4 2 0 0 0.5 1 1.5
内切圆 o1 o2 o3
S(mm) 842 842 903
ρ(mm) 421 421 459.5
r(mm) 1992 1481 1230.4
按照修正值校正轴面流线位置及其相应的等势线,从而得到 第二次近似轴面流网,重复上述计算直至符合要求为止。对 各等势线组分别检查轴面流线位置的正确性。一般要求偏差 不大于3~4%。下表为最终计算结果。