不锈钢生产流程详解
不锈钢的生产工艺
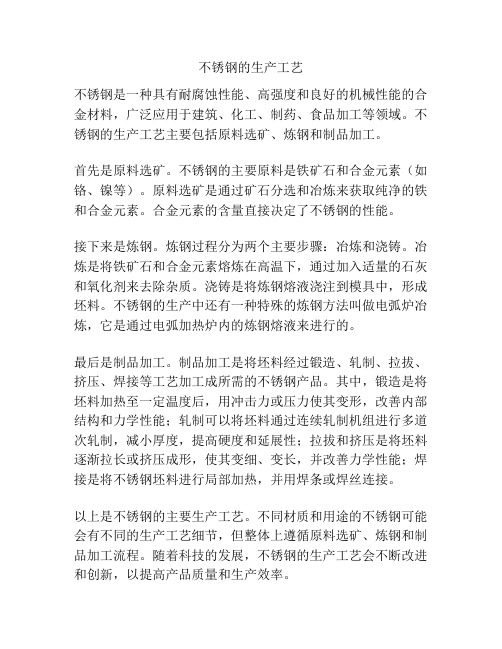
不锈钢的生产工艺
不锈钢是一种具有耐腐蚀性能、高强度和良好的机械性能的合金材料,广泛应用于建筑、化工、制药、食品加工等领域。
不锈钢的生产工艺主要包括原料选矿、炼钢和制品加工。
首先是原料选矿。
不锈钢的主要原料是铁矿石和合金元素(如铬、镍等)。
原料选矿是通过矿石分选和冶炼来获取纯净的铁和合金元素。
合金元素的含量直接决定了不锈钢的性能。
接下来是炼钢。
炼钢过程分为两个主要步骤:冶炼和浇铸。
冶炼是将铁矿石和合金元素熔炼在高温下,通过加入适量的石灰和氧化剂来去除杂质。
浇铸是将炼钢熔液浇注到模具中,形成坯料。
不锈钢的生产中还有一种特殊的炼钢方法叫做电弧炉冶炼,它是通过电弧加热炉内的炼钢熔液来进行的。
最后是制品加工。
制品加工是将坯料经过锻造、轧制、拉拔、挤压、焊接等工艺加工成所需的不锈钢产品。
其中,锻造是将坯料加热至一定温度后,用冲击力或压力使其变形,改善内部结构和力学性能;轧制可以将坯料通过连续轧制机组进行多道次轧制,减小厚度,提高硬度和延展性;拉拔和挤压是将坯料逐渐拉长或挤压成形,使其变细、变长,并改善力学性能;焊接是将不锈钢坯料进行局部加热,并用焊条或焊丝连接。
以上是不锈钢的主要生产工艺。
不同材质和用途的不锈钢可能会有不同的生产工艺细节,但整体上遵循原料选矿、炼钢和制品加工流程。
随着科技的发展,不锈钢的生产工艺会不断改进和创新,以提高产品质量和生产效率。
不锈钢304的生产工序
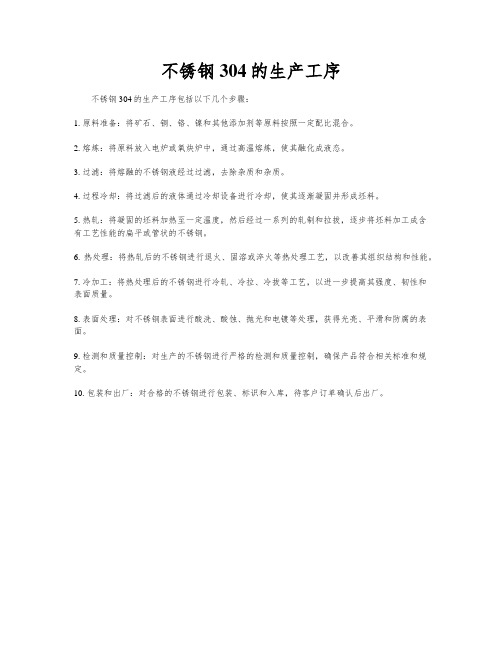
不锈钢304的生产工序
不锈钢304的生产工序包括以下几个步骤:
1. 原料准备:将矿石、铜、铬、镍和其他添加剂等原料按照一定配比混合。
2. 熔炼:将原料放入电炉或氧炔炉中,通过高温熔炼,使其融化成液态。
3. 过滤:将熔融的不锈钢液经过过滤,去除杂质和杂质。
4. 过程冷却:将过滤后的液体通过冷却设备进行冷却,使其逐渐凝固并形成坯料。
5. 热轧:将凝固的坯料加热至一定温度,然后经过一系列的轧制和拉拔,逐步将坯料加工成含
有工艺性能的扁平或管状的不锈钢。
6. 热处理:将热轧后的不锈钢进行退火、固溶或淬火等热处理工艺,以改善其组织结构和性能。
7. 冷加工:将热处理后的不锈钢进行冷轧、冷拉、冷拔等工艺,以进一步提高其强度、韧性和
表面质量。
8. 表面处理:对不锈钢表面进行酸洗、酸蚀、抛光和电镀等处理,获得光亮、平滑和防腐的表面。
9. 检测和质量控制:对生产的不锈钢进行严格的检测和质量控制,确保产品符合相关标准和规定。
10. 包装和出厂:对合格的不锈钢进行包装、标识和入库,待客户订单确认后出厂。
不锈钢制作工艺流程

不锈钢制作工艺流程主要包括以下几个步骤:
1. 炼钢:制造不锈钢的第一步是炼钢,通常是通过冶炼生铁和废钢的混合物来实现。
原材料首先被放入一个炉子中加热至高温,并混合搅拌以消除杂质。
随后,钢液被熔融并注入模具,最终形成钢坯。
2. 压制和热处理:钢坯随后被送入一个轧机中,通过压制和轧制的过程将其转变成所需的形状和尺寸。
一旦钢材被切割成所需的尺寸,将进行热处理,即加热至高温并冷却,以增强其强度和耐腐蚀性能。
3. 加工和表面处理:不锈钢经过热处理并获得所需的形状和尺寸后,将进一步加工,例如焊接、冲压、抛光和钻孔等。
这些加工步骤可根据所需的应用程序和最终产品的形状和大小来选择。
4. 洗涤和包装:最后,制造的不锈钢产品需要进行清洗以去除表面的污垢和杂质,并进行包装以确保在运输和存储过程中不受损坏。
此外,不锈钢的制作工艺需要对不锈钢的特点有深入了解,以确保其在制作过程中不失去其耐腐蚀性能、高温稳定性等特点。
如需了解更多关于不锈钢制作工艺的信息,建议咨询材料学专家或查阅相关文献资料。
不锈钢制造过程

不锈钢制造过程
不锈钢是一种耐腐蚀性能极佳的合金材料,广泛应用于制作各种产品。
以下是不锈钢的制造过程:
1. 原料准备:不锈钢材料的制造通常采用高品质钢铁材料,如304、316等。
这些材料会经过精密的筛选和评估,确保质量符合制造要求。
2. 熔化:将原料放入电弧炉中,加热至高温状态,使材料熔化并达到预定的成分。
3. 铸造:将熔化的材料倒入预定的注模中。
在冷却期间,不锈钢材料会逐渐凝固,形成原始型材或坯料。
4. 拉制或轧制:通过拉伸或轧制原始型材或坯料进一步加工成不同形状和尺寸的不锈钢管、板、线等产品。
5. 热处理:将不锈钢制品加热至一定温度,然后快速冷却,以提高其硬度和强度。
6. 表面处理:在不锈钢制品表面覆盖上一层保护膜,以增强其耐腐蚀性能。
7. 检测和质量控制:对制造的不锈钢产品进行严格的检测,确保产品符合制造和质量要求。
以上便是不锈钢的制造过程,每一个步骤都非常重要。
一流的材料、科学的工艺、先进的检测技术和严格的质量控制,是确保不锈钢产品质量的关键。
不锈钢的制作工艺流程

不锈钢的制作工艺流程
《不锈钢的制作工艺流程》
不锈钢是一种耐腐蚀、不易生锈的金属材料,广泛应用于制造业中。
不锈钢的制作工艺流程经过多道工序,包括原料准备、熔炼、浇铸、轧制、淬火、退火等过程。
首先,原料准备是不锈钢制作的第一步。
通常使用铁矿石和铬矿石等原料,经过选矿、破碎、磨矿等工艺处理,得到原料粉末。
接下来是熔炼工序,将原料粉末投入高温熔炉中熔化,经过一系列的炼钢工艺处理,使其成为符合要求的不锈钢液态金属。
然后是浇铸工序,将熔化的不锈钢金属倒入模具中,通过冷却凝固成型,制成不同形状的不锈钢坯料。
接着是轧制工序,将不锈钢坯料进行热轧或冷轧,调整其厚度和尺寸,使其满足不同工业领域的需要。
淬火和退火是不锈钢制作中的重要工序,淬火可以增加材料的硬度和强度,退火则可以使材料中的应力得以释放和结构得到改善。
最后,经过抛光、清洗、包装等工序,成品不锈钢材料得以完全制作完成,可以投入市场应用。
总的来说,不锈钢的制作工艺流程经过多道工序,需要严格的控制和操作,以确保最终产品的质量和性能。
不锈钢材料因其高耐腐蚀性、美观性和可塑性等特点,广泛应用于航空航天、汽车、建筑、化工等领域,对其制作工艺的要求也越来越高。
不锈钢生产流程
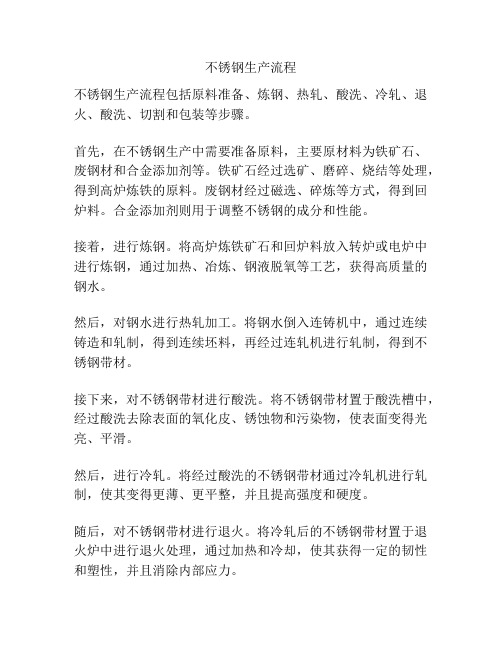
不锈钢生产流程
不锈钢生产流程包括原料准备、炼钢、热轧、酸洗、冷轧、退火、酸洗、切割和包装等步骤。
首先,在不锈钢生产中需要准备原料,主要原材料为铁矿石、废钢材和合金添加剂等。
铁矿石经过选矿、磨碎、烧结等处理,得到高炉炼铁的原料。
废钢材经过磁选、碎炼等方式,得到回炉料。
合金添加剂则用于调整不锈钢的成分和性能。
接着,进行炼钢。
将高炉炼铁矿石和回炉料放入转炉或电炉中进行炼钢,通过加热、冶炼、钢液脱氧等工艺,获得高质量的钢水。
然后,对钢水进行热轧加工。
将钢水倒入连铸机中,通过连续铸造和轧制,得到连续坯料,再经过连轧机进行轧制,得到不锈钢带材。
接下来,对不锈钢带材进行酸洗。
将不锈钢带材置于酸洗槽中,经过酸洗去除表面的氧化皮、锈蚀物和污染物,使表面变得光亮、平滑。
然后,进行冷轧。
将经过酸洗的不锈钢带材通过冷轧机进行轧制,使其变得更薄、更平整,并且提高强度和硬度。
随后,对不锈钢带材进行退火。
将冷轧后的不锈钢带材置于退火炉中进行退火处理,通过加热和冷却,使其获得一定的韧性和塑性,并且消除内部应力。
然后,再次进行酸洗。
将退火后的不锈钢带材放入酸洗槽中进行酸洗,去除退火过程中产生的氧化皮和锈蚀物。
最后,对不锈钢带材进行切割和包装。
将不锈钢带材根据需求进行切割成特定尺寸的板材或卷材,然后进行包装,以便运输和使用。
以上即为不锈钢生产的主要流程,通过这些步骤可以得到质量优良的不锈钢产品。
不锈钢因其耐腐蚀性和美观性,广泛应用于建筑、机械、化工等领域。
不锈钢的制作工艺流程
不锈钢的制作工艺流程不锈钢是一种常用的金属材料,具有防腐蚀、高强度、耐磨损等特点,广泛应用于家具、建筑、机械等领域。
不锈钢的制作工艺流程主要包括选材、熔炼、制坯、热轧、酸洗、冷轧、退火、切割、抛光和再加工等环节。
首先,不锈钢的制作需要选材。
不锈钢可以分为多种牌号,根据不同的使用要求选择合适的牌号。
选材时需要考虑机械性能、耐腐蚀性能以及价格因素,确保选用的材料能够满足产品要求。
接下来是熔炼阶段。
将选好的不锈钢材料放入熔炼炉中进行熔化,熔炼过程需要精确控制温度和材料成分,确保熔化后的合金成分符合要求。
制坯是制作不锈钢的重要环节。
熔炼后的不锈钢通过连铸或铸造等工艺制成坯料,坯料的形状和尺寸根据产品要求进行设计和加工。
热轧是将坯料经过加热和塑性变形,通过压力进行成形的过程。
这个过程主要是通过轧机将坯料加热至适当的温度后,通过轧制机器将其压制成所需要的形状和尺寸。
热轧之后是酸洗。
酸洗是为了去除表面的氧化皮和杂质,提高亮度和清洁度。
酸洗使用强酸溶液将不锈钢表面进行处理。
冷轧是将经过热轧和酸洗的不锈钢坯料通过冷轧机进行再次压制成所需要的形状和尺寸。
冷轧可以提高产品的机械性能,使其表面更加光滑。
退火是对冷轧后的不锈钢进行热处理的过程。
通过加热和冷却的方法,将材料的晶粒重新排列,消除内部应力,提高材料的塑性和韧性。
切割是将不锈钢材料切割成所需要的尺寸和形状。
常见的切割方法有剪切、焊割和激光切割等。
抛光是对不锈钢表面进行处理,使其更加光滑亮丽。
抛光可以通过机械抛光、电解抛光和化学抛光等方法进行。
最后是再加工。
根据产品的要求,对不锈钢进行加工,如焊接、折弯、冲孔等步骤,使其成为最终的成品。
总之,不锈钢的制作工艺流程包括选材、熔炼、制坯、热轧、酸洗、冷轧、退火、切割、抛光和再加工等多个环节。
每个环节都需要严格的控制和操作,确保最终的产品质量符合要求。
不锈钢生产流程
不锈钢生产流程
不锈钢是一种具有抗腐蚀性能的金属材料,广泛应用于建筑、
化工、医疗器械等领域。
其生产过程包括原料准备、熔炼、铸造、
轧制、热处理、表面处理等多个环节。
下面将详细介绍不锈钢的生
产流程。
首先,不锈钢的生产需要准备原料,主要包括铁矿石、铬、镍、锰等金属原料,以及石灰石、煤炭等辅助原料。
这些原料经过严格
的筛选和配比后,送入高炉进行冶炼。
在高炉中,原料经过熔融反应,产生生铁和炼钢渣。
生铁中含
有较高的碳和其他杂质,需要通过转炉或电弧炉进一步精炼,去除
杂质,调整合金成分,得到合格的钢水。
接下来是铸造环节,将熔化的钢水注入铸造模具中,经过凝固
后得到不锈钢铸件。
铸件经过去除气孔、修整表面等工艺处理后,
可以进入下一步的加工工艺。
轧制是不锈钢生产中非常重要的一环,通过轧制工艺可以将铸
件加工成不同规格和形状的半成品。
这个过程中需要经过粗轧、精
轧、酸洗、冷拔等多道工序,最终得到符合要求的卷材或板材。
热处理是不锈钢的重要工艺之一,通过加热和冷却的方式,改变不锈钢的组织结构和性能,使其具有更好的力学性能和耐腐蚀性能。
最后,不锈钢需要进行表面处理,包括酸洗、抛光、喷丸等工艺,以提高不锈钢的表面光洁度和耐腐蚀性能。
总的来说,不锈钢的生产流程经过原料准备、熔炼、铸造、轧制、热处理、表面处理等多个环节,每个环节都需要严格控制工艺参数,确保不锈钢的质量和性能达到要求。
随着工艺技术的不断进步,不锈钢的生产流程也在不断优化,以满足市场对高品质不锈钢的需求。
不锈钢加工流程
不锈钢加工流程不锈钢是一种具有耐腐蚀性、耐高温性和美观性的金属材料,因此在工业制造中得到了广泛的应用。
不锈钢加工流程是指将不锈钢原材料进行切割、成型、焊接、抛光等一系列工艺,最终制成各种不锈钢制品的过程。
下面将详细介绍不锈钢加工的流程及注意事项。
1. 材料准备。
不锈钢加工的第一步是材料的准备。
通常情况下,我们会选择不同规格和型号的不锈钢板材、管材或型材作为加工的原材料。
在进行加工之前,需要对原材料进行检验,确保材料的质量符合加工要求。
2. 切割。
切割是不锈钢加工的关键步骤之一。
根据加工需要,可以选择激光切割、等离子切割、剪切或锯切等不同的切割方式。
在进行切割时,需要根据加工图纸和要求,精确控制切割尺寸和形状,确保切割后的材料能够满足后续加工的需要。
3. 成型。
成型是将切割好的不锈钢原材料进行弯曲、冲压、拉伸等工艺,使其成为所需的形状和结构的过程。
成型过程中需要注意控制加工参数,避免材料变形或出现裂纹,保证加工后的产品质量。
4. 焊接。
在不锈钢加工中,焊接是常见的工艺之一。
通过焊接,可以将不锈钢材料连接成各种结构,如焊接成型、角焊接、对接焊接等。
在进行焊接时,需要选择合适的焊接方法和焊接材料,控制好焊接参数,确保焊接接头的质量和牢固度。
5. 抛光。
抛光是不锈钢加工中的重要环节之一,也是提升不锈钢制品外观质量的关键步骤。
通过抛光,可以使不锈钢表面光滑、亮丽,提升其装饰效果。
在抛光过程中,需要选择合适的抛光工艺和抛光材料,控制好抛光时间和力度,确保不锈钢表面的光洁度和平整度。
6. 检验和包装。
在完成不锈钢加工后,需要对加工好的产品进行检验,确保产品的质量符合要求。
检验包括外观检查、尺寸检测、材质分析等内容。
通过严格的检验,可以排除不合格品,保证产品质量。
最后,对合格的产品进行包装,以防止在运输和使用过程中受到损坏。
综上所述,不锈钢加工流程包括材料准备、切割、成型、焊接、抛光、检验和包装等多个环节。
在每个环节中,都需要严格控制加工参数,保证加工质量,最终生产出符合要求的不锈钢制品。
不锈钢生产流程详解
不锈钢生产流程详解不锈钢是一种具有耐腐蚀性、耐高温性、美观性等优点的金属材料,广泛应用于建筑、化工、医疗、航空航天等领域。
那么,不锈钢是如何生产的呢?下面就为大家详细介绍不锈钢生产流程。
1. 原材料准备:不锈钢的主要原材料是铁、铬、镍、钼等金属,以及一些合金元素。
这些原材料需要经过筛选、清洗、烘干等处理,以确保其质量符合要求。
2. 熔炼:将原材料放入高温炉中进行熔炼,使其融化成液态金属。
在熔炼过程中,需要控制温度、氧化还原条件等因素,以确保金属成分的准确性和均匀性。
3. 钢水处理:将熔炼好的钢水进行处理,去除其中的杂质和气泡。
这一步通常采用真空处理、氧化还原处理等技术。
4. 连铸:将处理好的钢水倒入连铸机中,通过冷却和拉伸等过程,将其变成长条状的钢坯。
这一步需要控制冷却速度和拉伸力度,以确保钢坯的质量。
5. 热轧:将钢坯放入热轧机中进行加热和轧制,使其变成所需的板材、棒材等形状。
这一步需要控制温度、轧制力度等因素,以确保产品的尺寸和表面质量。
6. 冷轧:将热轧好的钢材放入冷轧机中进行冷轧,使其表面更加光滑、尺寸更加精确。
这一步需要控制冷却速度和轧制力度等因素。
7. 退火:将冷轧好的钢材放入退火炉中进行退火处理,使其恢复原有的晶粒结构和性能。
这一步需要控制温度和时间等因素。
8. 表面处理:将退火好的钢材进行表面处理,如抛光、酸洗、电镀等,以提高其表面光洁度和耐腐蚀性。
9. 检验和包装:对生产好的不锈钢产品进行检验,如化学成分分析、机械性能测试等,以确保其质量符合要求。
然后进行包装和标识,以便运输和使用。
以上就是不锈钢生产的主要流程。
不锈钢生产过程中需要控制多个因素,以确保产品的质量和性能。
随着科技的不断进步,不锈钢生产技术也在不断创新和改进,使得不锈钢产品的质量和应用范围不断提高。
- 1、下载文档前请自行甄别文档内容的完整性,平台不提供额外的编辑、内容补充、找答案等附加服务。
- 2、"仅部分预览"的文档,不可在线预览部分如存在完整性等问题,可反馈申请退款(可完整预览的文档不适用该条件!)。
- 3、如文档侵犯您的权益,请联系客服反馈,我们会尽快为您处理(人工客服工作时间:9:00-18:30)。
不锈钢丝生产流程不锈钢是20世纪重要发明之一,经过近百年的研制和开发已形成一个有300多个牌号的系列化的钢种。
在特殊钢体系中不锈钢性能独特,应用范围广,起其它特殊钢无法代替的作用。
而不锈钢几乎可以涵盖其它任何一种特殊钢。
不锈钢合金含量高,价格比较高,但使用寿命远远高于其他钢种,维护费用少,是使用成本最低的钢种。
不锈钢回收利用率高,对环境污染少,是改善环境,美化生活的绿色环保材料。
不锈钢的生产和使用在一定程度上反映出一个国家或地区经济发展水平和人民生活水平。
不锈钢的发展几乎不受某个特定行业发展的影响,而与国家和地区GDP(国民生产总值)的增长密切相关。
我国是一个发展中国家,近年来GDP值以每年7%~8%的速度稳步上升,国内不锈钢表观消费量一直以每年15%左右速度递增,2001年中国不锈钢表观消费量已达225万吨。
预计未来几年这种增长势头将有增无减,不锈钢市场前景一片光明。
不锈钢丝是不锈钢产品系列中一个重要品种,主要用作制造业的原材料。
我国经济目前以制造业为支柱,所以我国不锈钢丝消费量在不锈钢总消费量中所占比重要高于发达国家。
世界钢丝在不锈钢总量中所占比例大约为4.5%,我国2001年钢丝所占比例已达4.9%,预计未来几年将上升到5.0%~5.5%的水平。
根据2001年调查资料全国不锈钢丝表观消费量为11万吨,品种结构为铆螺占40.1%,气阀占22.7%,筛网和焊丝分别占9.1%,精密轴占4.5%,医疗器械占2.7%,滚动体占1.8%,弹簧和制绳分别占0.9%,其它占8.2%。
如果按钢的组织结构来划分,我国奥氏体不锈钢丝:铁素体不锈钢丝:马氏体不锈钢丝消费比例为65:10:25,而日本三者比例为70:18:12,由此看出消费水平尚有一定差距。
相对于其他品种,不锈钢丝属于投资少,见效快的产业。
近年来国内不锈钢丝生产企业如雨后春笋般的发展起来,尽管如此生产增长仍赶不上消费的增长,每年不锈钢丝的进口量一直维持在2万吨左右。
发展不锈钢丝生产,提高不锈钢丝产品质量水平是制品行业面临的一项重要而迫切的任务。
1. 不锈钢的特性、用途及品种不锈钢是指一些在空气、水、酸性溶液及其它腐蚀介质中具有较高化学稳定性,在高温下具有抗氧化性的钢。
不锈钢的耐腐蚀性能和抗氧化性与其化学成分密切相关。
1.1、化学成分对不锈钢的组织和性能的影响1.1.1 铬是决定不锈钢耐腐蚀性能的主要元素为什么铬能决定不锈钢的耐腐蚀性能?是不是含铬的钢都是不锈钢?回答这个问题必须从金属腐蚀说起。
金属腐蚀可分为化学腐蚀和电化学腐蚀两种。
在高温下金属直接与空气中的氧反应,生成氧化物,是一种化学腐蚀。
在常温下这种腐蚀进行得很缓慢,金属的腐蚀主要是电化学腐蚀。
电化学腐蚀的本质是金属在介质中离子化。
以铁为例,电化学腐蚀过程可表示为:Fe-e=Fe++一种金属耐电化学腐蚀的能力,决定于本身的电极电位。
电极电位越负,越易失去电子,发生离子化。
电极电位越正,越不易失去电子,不易离子化。
常见金属的标准电极电位如表1-1。
表1-1 常见金属的标准电极电位1/8、2/8、3/8……原子比时,铁-铬合金钢的电极电位呈跳跃式的提高,这种变化规律叫n/8定律,如图1-1所示。
当铁-铬固溶体中铬的原子含量达到12.5%(1/8)第一个突变值时,基体在FeSO4溶液中的电极电位由-0.56V跳增至+0.2V,通常把12.5%的原子含量作为不锈钢的最低含铬量,换算成重量百分比则为:12.5%×(铬原子量/铁原子量)=12.5%×52/55.8=11.65% 含铬低于11.65%的钢,一般不叫不锈钢。
铬提高钢的耐蚀性能的第二个原因是铁-铬合金钢在氧化性介质中极易形成一层致密的钝化膜(FeO.Cr2O3),这层钝化膜稳定、完整,与基体金属结合牢固,将基体与介质完全隔开,从而有效地防止钢进一步氧化或腐蚀。
但在还原性介质中,这层膜有破裂的倾向。
一般说来,不锈钢的耐蚀性能和抗氧化性能是随铬含量的增加而增加的。
从表1-2可以看出,铁-铬合金钢在海洋大气中的腐蚀随铬含量的增加而减少。
图1-2显示铁-铬合金钢在1000℃时,氧化失重与铬含量的关系。
碳是不锈钢中仅次于铬的第二号常用元素,不锈钢的组织和性能在很大程度上取决于碳含量及其分布状态。
碳是稳定奥氏体元素,它对奥氏体的稳定作用很强烈,约为镍的30倍。
图1-3显示碳对不锈钢奥氏体区的影响。
在高温下处于α或α+γ相区的铬钢是不能或很难通过淬火得到马氏体组织的。
以含铬13%的钢为例,碳含量小于0.08%时为铁素体钢,碳含量0.08%~0.15%时为半马氏钢,碳含量大于0.15%时为马氏体钢。
碳能显著提高不锈钢的强度,从2Cr13、3Cr13、4Cr13到9Cr18,钢的强度随碳含量增加逐级提高。
在奥氏体钢中碳也是最有效的固溶强化元素。
表1-3显示奥氏体钢抗拉强度和屈服强度随碳含量增加而上升。
由于碳和铬的亲和力很大,它能与铬形成一系列复杂的碳化物,碳化物的类型因钢中铬含量的不同而异。
含铬小于10%的钢,主要为渗碳体型碳化物(Fe.Cr)3C,高铬钢中的碳化物为复杂碳化物Cr7C3和Cr23C6。
碳化物中的铬可以被置换,以(Fe.Cr)7C3和(Fe.Cr)23C6的的形式存在。
不锈钢中的碳化物主要以(Fe.Cr)23C6形式存在。
碳与铬形成碳化物时要占用不锈钢中的一部分铬,以Cr23C6为例计算:Cr23C6:(铬原子量×23)/(碳原子量×6)=(52×23)/(12×6)≈17不锈钢中的碳要与17倍的铬结合,生成碳化物,固溶体中的铬含量必然要减少,钢的耐腐蚀性能就要降低。
如果形成碳化物后固溶体中的铬含量低于11.65%,就不能称其为不锈钢,模具钢Cr12和Cr12MoV就是一例。
0Cr13~4Cr13五个牌号标准中规定含铬量为12.0~14.0%,就是考虑到碳要与铬形成碳化物确定的。
因为碳对耐腐蚀性能有不利的影响,奥氏体和铁素体钢很少采用碳来强化,其含碳量多在0.15%以下。
马氏体钢的含碳量大多在0.10%~0.40%范围内。
1.1.3 镍是稳定奥氏体元素镍是不锈钢中第三号常用元素,它在钢中起扩大奥氏体区、稳定奥氏体组织的作用。
铬不锈钢中加入一定量的镍后,组织和性能都发生明显变化。
如1Cr17为铁素体钢,热处理后抗拉强度在500N/mm2左右,加入2.0%的镍,变为1Cr17Ni2马氏体钢,淬火后抗拉强度达1100N/mm2以上。
图1-4显示了含碳0.10%的钢,在不同铬含量下得到稳定奥氏体组织所需的镍含量。
当铬为18%时,只需要8%的镍,常温下就能得到奥氏体组织,这就是18-8型不锈钢的来由。
镍能显著地提高铬钢的耐腐蚀性能和高温抗氧化性能,铬-镍奥氏体钢比铬含量相同的铁素体和马氏体钢有更好的耐腐蚀性能。
铬含量在20%以下时,钢的抗氧化性能随镍量的增加不断改善。
对于高铬钢,最佳镍含量在10%~20%之间,Cr20Ni10和Cr25Ni20就是两个典型的耐热钢。
镍能有效地降低铁素体钢的脆性,改善其焊接性能,但对抗应力腐蚀性能有不利的影响,对于奥氏体钢,镍能降低钢的冷加工硬化趋势,改善冷加工性能,使钢在常温和低温下均具有很高塑性和韧性。
1.1.4锰和氮可以代替镍锰是奥氏体形成元素,它能抑制奥氏体的分解,使高温形成的奥氏体组织保持到室温。
锰稳定奥氏体的作用为镍的二分之一,2%的锰可以代替1%的镍。
铬-锰钢要在常温下得到完全奥氏体组织,与钢中的碳和铬含量密切相关,当碳低于0.2%、铬大于14%~15%时,不论向钢中加入多少锰都不能得到纯奥氏体组织。
要得到奥氏体组织必须增加碳含量或降低铬含量,这两种作法都会降低钢的耐蚀性能,所以锰不能代替全部镍。
含锰钢具有冷加工强化效应显著,耐磨性高的优点。
缺点是对晶间腐蚀很敏感,并且不能通过加钛和铌来消除晶间腐蚀。
氮也是稳定奥氏体元素,氮与锰结合能取代比较贵的镍。
氮稳定奥氏体的作用比镍大,与碳相当。
氮代镍的比例约为0.025∶1,一般认为氮可取代2.5%~6.5%的镍。
在奥氏体中氮也是最有效的固溶强化元素之一。
氮与铬的亲和力要比碳与铬的亲和力小,奥氏体钢很少见到Cr2N的析出。
因此氮能在不降低耐蚀性能的基础上,提高不锈钢强度,研制含氮不锈钢是近年来不锈钢工业的趋势。
氮在钢中的溶解度有限(<0.15%),加入铬和锰能提高其溶解度,加入镍和碳能减少其溶解度。
在大气冶炼条件下,氮以Cr-N或Mn-N合金形式加入钢中,很难准确控制回收率。
一般认为氮含量超过0.2%对冶炼操作极为不利。
氩-氧精炼,加压电渣熔炼,平衡压力浇铸等技术的发展和应用,能准确控制钢中氮含量,用氮来控制钢中的组织成为现实。
近期研究成果表明,适当调整不锈钢成分,特别是铬与锰的配比,能将钢中的氮含量稳定在0.4%左右,如美国的205(17Cr-1.25Ni-15Mn-0.15C-0.35N)氮含量为0.30%~0.40%。
1.1.5 钛和铌可以防止晶间腐蚀铬-镍奥氏体不锈钢在450~800℃温度区加热,常发生沿晶界的腐蚀破坏,称为晶间腐蚀。
一般认为,晶间腐蚀是碳从饱和的奥氏体以Cr23C6形态析出。
造成晶界处奥氏体贫铬所致。
防止晶界贫铬是防止晶间腐蚀的有效方法。
如将各种元素按与碳的亲和力大小排列,顺序为:Ti、Zr、V、Nb、W、Mo、Cr、Mn。
钛和铌与碳的亲和力都比铬大,把它们加入钢中后,碳优先与它们结合生成碳化钛(TiC)和碳化铌(NbC),这样就避免了析出碳化铬而造成晶界贫铬,从而有效防止晶间腐蚀。
另外,钛和铌与氮可结合生成氮化钛和氮化铌,钛与氧可结合生成二氧化钛,奥氏体中还能溶解一部分铌(约0.1%)。
考虑这些因素,实际生产中为防止晶间腐蚀,钛和铌加入量一般按下式计算:Ti=(C-0.02)×5~0.8%Nb≥10×C%含钛和铌的钢固溶处理后得到单相奥氏体组织,这种组织处于不稳定状态,当温度升高到450℃以上时,固溶体中的碳逐步以碳化物形态析出,650℃是Cr23C6形成温度,900℃是TiC 形成温度,920℃是NbC形成温度。
要防止晶间腐蚀就要减少Cr23C6含量,使碳化物全部以TiC和NbC形态存在。
由于钛和铌的碳化物比铬的碳化物稳定,钢加热到700℃以上时,铬的碳化物就开始向钛和铌的碳化物转化。
稳定化处理是将钢加热到850~930℃之间,保温1h,此时铬的碳化物全部分解,形成稳定的TiC和NbC,钢的抗晶间腐蚀性能得到改善。
不锈钢中加入钛和铌,在一定条件下弥散析出Fe2Ti和Fe3Nb2金属间化合物,钢的高温强度有所提高。
由于铌的价格昂贵(是钛的70倍),广泛采用的是加钛不锈钢。
含钛钢存在一些缺点,如:TiO2和TiN以夹杂物存在,含量高且分布不均,降低钢的纯净度;铸锭表面质量差,增加工序修磨量,极易造成大批废品;成品抛光性能不好,很难得到高精度表面等。