锂电池随使用而最大容量下降的原因
锂电池大内阻故障修复技术研究

锂电池大内阻故障修复技术研究随着电子产品的普及和需求的增加,锂电池作为一种高效、可充电性强的电池,已经成为了广泛应用的能源储存设备。
然而,随着使用时间的增长,锂电池会出现大内阻故障,影响其性能和寿命。
本文旨在研究锂电池大内阻故障的原因、症状以及修复技术。
一、锂电池大内阻故障的原因锂电池大内阻故障一般是由以下几个原因造成的:1.1 高温环境:锂电池在高温环境下容易发生大内阻故障。
高温会使电池内部化学反应速度加快,导致正负极活性物质的损耗,进而增加电池内部电阻。
1.2 过充或过放:长时间的过充或过放会导致电池内的锂离子极化反应不均衡,进而引发大内阻故障。
1.3 阳极结膜:镍氢电池在长时间使用后,阳极表面会产生一层结膜,导致电池内阻增加。
二、锂电池大内阻故障的症状锂电池出现大内阻故障时,常会表现出以下症状:2.1 电池容量下降:由于大内阻故障使得电池内部电阻增加,导致电池容量减少,使用时间明显缩短。
2.2 充电速度变慢:大内阻故障会使得电池内部反应速度变慢,充电速度明显减慢。
2.3 温度升高:电池内阻增加会产生大量的热量,导致电池温度升高。
三、锂电池大内阻故障的修复技术针对锂电池出现大内阻故障的情况,研究人员提出了以下几种修复技术:3.1 电池慢充:将电池放在恒定电流下进行缓慢充电,可以通过化学反应修复一部分大内阻故障。
3.2 极化修复:通过外加电压的方式,在极化阶段进一步激活电池内部的活性物质,促进内部结构的修复。
3.3 温度修复:将电池放在适当的温度环境下进行修复,可以促使锂离子迁移速度增加,减少内阻。
3.4 电池容量回收:通过循环充放电的方式,逐步恢复电池的容量,并降低内阻。
3.5 增加导电剂:在电池内部增加一定比例的导电剂,可以降低内阻。
结论总之,锂电池大内阻故障会严重影响电池的使用寿命和性能。
针对该故障,研究人员提出了多种修复技术,包括电池慢充、极化修复、温度修复、电池容量回收以及增加导电剂等方法。
锂电池大内阻故障与电池寿命的关系

锂电池大内阻故障与电池寿命的关系锂电池是一种常见的可充电电池,广泛应用于移动设备、电动车辆等领域。
然而,锂电池在使用过程中可能会出现内阻增大的情况,这对电池性能和寿命产生重要影响。
本文将探讨锂电池大内阻故障与电池寿命的关系。
一、锂电池大内阻故障的原因1. 过充和过放过充和过放是导致锂电池内阻增大的常见原因之一。
过充会引起正极材料的氧化和结构变化,过放则会增加负极材料的脱锂程度,这些因素对电池内部的化学反应速率和电子传导性能产生负面影响,导致内阻的增加。
2. 高温高温也是引起锂电池内阻增大的主要原因之一。
在高温环境下,电池内部的化学反应速率会增加,同时也会引起电极材料的膨胀和结构变化,进一步增加了内阻。
3. 循环次数锂电池的循环次数也会影响其内阻。
循环次数越多,电池内部的材料和结构可能会发生变化,导致内阻逐渐增加。
二、锂电池大内阻故障对电池寿命的影响1. 容量衰减锂电池内阻增大会导致充电和放电时的能量转化损耗增加,从而引起容量衰减。
电池的实际可用容量会逐渐减少,导致电池寿命缩短。
2. 充电效率下降大内阻故障影响了电池内部的电子传导性能,会导致电池充电效率下降。
电池在充电过程中会产生更多的热量,并且需要更长的充电时间才能完成充电,这进一步增加了电池的能量损耗。
3. 电池温升大内阻故障还容易引起电池的温度升高。
由于内部化学反应速率的增加和电池充电效率的下降,电池在使用过程中会产生更多的热量,如果不能及时散热,可能会导致电池过热,从而进一步缩短电池的寿命。
三、延长锂电池寿命的方法1. 控制充放电水平避免过充和过放是延长锂电池寿命的重要方法之一。
合理控制电池的充电和放电水平,避免超过电池的额定电压和容量范围,可以减缓内阻的增加,延长电池的使用寿命。
2. 温度控制保持适宜的温度对于延长锂电池寿命也非常重要。
尽量避免将电池暴露在高温环境下,避免快速充电和过度充放电,这样可以降低内阻的增大速度,并减轻电池的温升现象。
锂电保护ic
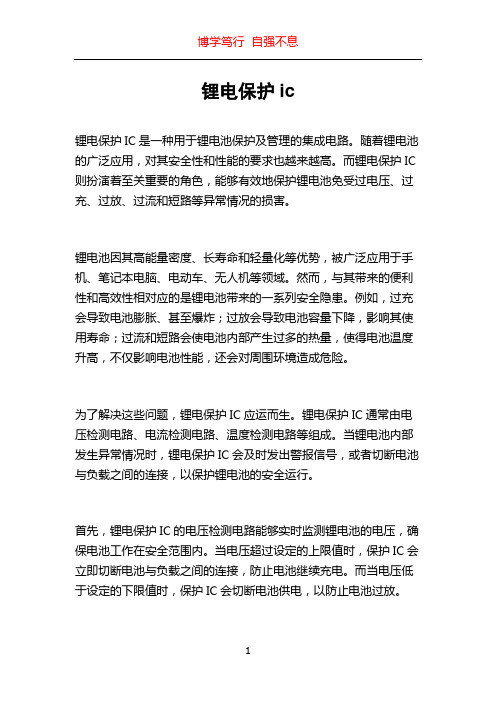
锂电保护ic锂电保护IC是一种用于锂电池保护及管理的集成电路。
随着锂电池的广泛应用,对其安全性和性能的要求也越来越高。
而锂电保护IC 则扮演着至关重要的角色,能够有效地保护锂电池免受过电压、过充、过放、过流和短路等异常情况的损害。
锂电池因其高能量密度、长寿命和轻量化等优势,被广泛应用于手机、笔记本电脑、电动车、无人机等领域。
然而,与其带来的便利性和高效性相对应的是锂电池带来的一系列安全隐患。
例如,过充会导致电池膨胀、甚至爆炸;过放会导致电池容量下降,影响其使用寿命;过流和短路会使电池内部产生过多的热量,使得电池温度升高,不仅影响电池性能,还会对周围环境造成危险。
为了解决这些问题,锂电保护IC应运而生。
锂电保护IC通常由电压检测电路、电流检测电路、温度检测电路等组成。
当锂电池内部发生异常情况时,锂电保护IC会及时发出警报信号,或者切断电池与负载之间的连接,以保护锂电池的安全运行。
首先,锂电保护IC的电压检测电路能够实时监测锂电池的电压,确保电池工作在安全范围内。
当电压超过设定的上限值时,保护IC会立即切断电池与负载之间的连接,防止电池继续充电。
而当电压低于设定的下限值时,保护IC会切断电池供电,以防止电池过放。
其次,锂电保护IC的电流检测电路能够监测电池与负载之间的电流。
当电流超过设定的最大值时,保护IC会切断电池与负载之间的连接,以防止过流产生过多的热量和电池损坏。
此外,锂电保护IC还具备温度检测功能。
当电池温度超过设定的上限值时,保护IC会发出警报,并切断电池与负载之间的连接,以防止过热导致电池内部发生热失控。
除了上述的基本功能外,一些高级的锂电保护IC还具备平衡充电和SOC估算等功能。
平衡充电功能可以确保锂电池各个单体之间的电压平衡,延长电池的寿命。
SOC估算功能可以实时估算锂电池的剩余电量,提供准确的电池使用情况。
总之,锂电保护IC通过监测和控制电池的电压、电流和温度等参数,有效地保护锂电池的安全性和性能,降低了锂电池的使用风险。
锂电池内阻故障与电池寿命的关系

锂电池内阻故障与电池寿命的关系随着科技的快速发展,锂电池已经成为了现代电子设备中不可或缺的能源供应器。
锂电池的内阻故障是导致其性能下降的主要原因之一,而内阻故障与电池寿命之间也存在着密切的关系。
本文将探讨锂电池内阻故障的原因以及与电池寿命之间的关联。
一、锂电池的内阻故障原因1.1 材料老化首先,锂电池内阻故障的主要原因之一是材料老化。
锂电池充放电循环过程中,正极、负极材料以及电解质等都会逐渐老化,导致电池内部的电解质阻抗增加,从而引发内阻故障。
1.2 间隔膜失效其次,间隔膜失效也是引起锂电池内阻故障的常见原因之一。
间隔膜的质量和粘结性能直接影响着锂电池的安全性和寿命。
一旦间隔膜失效,电解液中的金属离子就可能直接接触到正负极之间,导致内部短路并产生较大的内阻。
1.3 极化过程最后,极化过程也可能导致锂电池内阻故障。
在电池的充放电过程中,电流通过正负极之间的界面时,会发生极化现象。
极化过程会降低电极的活性物质的利用率,从而增加电池的内阻。
二、锂电池内阻故障对电池寿命的影响2.1 电池温升锂电池在工作过程中会产生一定的内阻,内阻过大会引起电池发热问题。
当电池温度过高时,不仅会加剧内阻故障,而且还会导致电池的寿命减少。
因此,内阻故障对电池温升速率的影响与电池的寿命密切相关。
2.2 电池容量衰减内阻故障也会导致锂电池容量衰减。
内阻增加会导致电压下降,从而影响电池的放电性能。
而电池的容量衰减则直接影响锂电池的使用时间和电池寿命。
2.3 充放电效率降低内阻故障会引起充放电效率降低。
当内阻增加时,电池在充放电过程中会有更多的能量转化为热能而不是电能,从而导致电池的能量转化效率下降,电池的寿命也会随之减少。
2.4 电池循环寿命减少最后,锂电池内阻故障也会显著减少电池的循环寿命。
内阻增加会导致电池在循环充放电过程中能量损失增加,使得电池无法正常工作。
因此,内阻故障与电池的循环寿命之间存在着直接的关系。
综上所述,锂电池的内阻故障与电池寿命之间存在着紧密的关系。
锂电池的不一致性指的是什么

锂电池的不一致指的是什么?通常经过配对组合的锂电池组在使用一段时间后,有个别的电池出现了充电先充满,放电先放完的情况,导致整个电池组的电性能大大下降,这就是电池组出现短板效应,原因就是电池组内的电池出现了不一致。
这些不一致性主要指那些呢?1.电压不一致主要指开路电压的不一致,电芯在经过化成后,经过同样的充放电制度,静止老化几天,在同样的环境温度下,测试电池的开路电压,这时电芯就出现了开路电压不一样。
同批电池出现这样的情况,采用同批的原材料,这主要跟电芯的工艺及工艺参数相关。
同理,相同开路电压的电芯组装成电池组后,在使用过程中,电芯的不一致也会出现,这不仅跟工艺及工艺参数相关,还跟电芯的使用环境温度,内阻,容量等相关。
2.内阻不一致电芯的内阻,特别是组装成动力电池,内阻的大小显得非常重要。
特别是组成电池组后,随着充放电次数的增加,因为内阻的不一致,导致电芯的不一致会越来越严重。
采用相同原材料的同批电池,内阻的不一致性不仅跟工艺及工艺参数相关,还跟组装工艺及组装材料相关。
即使是同样内阻的电芯,在经过组装工艺后,在后续的充放电过程中也会因为组装工艺的不一致而导致内阻不一致。
3.容量的不一致性电芯的容量一般在组装电池组时,会进行分选。
一般容量不一致性导致的原因很多方面,主要还是在生产电芯的过程中导致的。
所以很多锂电池厂家通过标准化作业来提高生产的不一性,同时不断提高锂电池的智能化生产线的主要原因就是机器比人更好控制工艺过程。
4.寿命的不一致性电芯的寿命只能够通过抽检来大概衡量,无法准确预测,这个测试过程非常长,通常电芯都已经在使用了,抽检数据并未出来,但是寿命通常都是锂电池使用者最为关心的问题。
电芯组装成电池组后,电池组的寿命通常也只能粗略预测,毕竟电池组寿命影响的因素太多了,不仅跟生产工艺相关,还和使用的环境温度,电池的使用条件相关。
5.电池的温升不一性电芯本身制造出来后,内阻都不一样,虽然经过分选,但是在使用过程中,这种不一性会加剧。
锂电池安全问题及失效分析
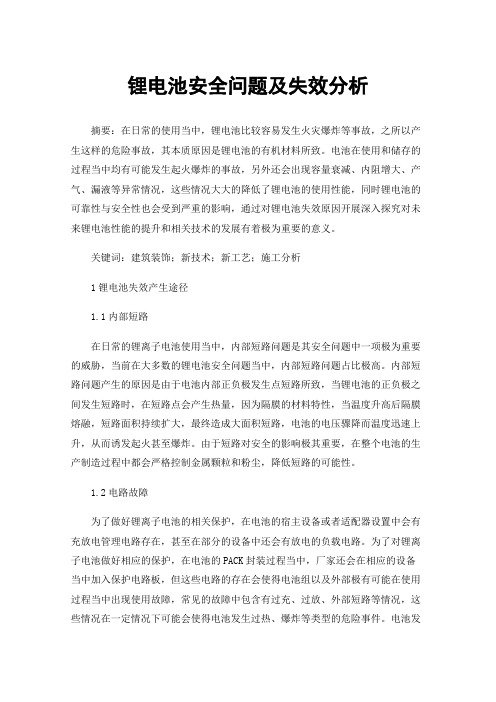
锂电池安全问题及失效分析摘要:在日常的使用当中,锂电池比较容易发生火灾爆炸等事故,之所以产生这样的危险事故,其本质原因是锂电池的有机材料所致。
电池在使用和储存的过程当中均有可能发生起火爆炸的事故,另外还会出现容量衰减、内阻增大、产气、漏液等异常情况,这些情况大大的降低了锂电池的使用性能,同时锂电池的可靠性与安全性也会受到严重的影响,通过对锂电池失效原因开展深入探究对未来锂电池性能的提升和相关技术的发展有着极为重要的意义。
关键词:建筑装饰;新技术;新工艺;施工分析1锂电池失效产生途径1.1内部短路在日常的锂离子电池使用当中,内部短路问题是其安全问题中一项极为重要的威胁,当前在大多数的锂电池安全问题当中,内部短路问题占比极高。
内部短路问题产生的原因是由于电池内部正负极发生点短路所致,当锂电池的正负极之间发生短路时,在短路点会产生热量,因为隔膜的材料特性,当温度升高后隔膜熔融,短路面积持续扩大,最终造成大面积短路,电池的电压骤降而温度迅速上升,从而诱发起火甚至爆炸。
由于短路对安全的影响极其重要,在整个电池的生产制造过程中都会严格控制金属颗粒和粉尘,降低短路的可能性。
1.2电路故障为了做好锂离子电池的相关保护,在电池的宿主设备或者适配器设置中会有充放电管理电路存在,甚至在部分的设备中还会有放电的负载电路。
为了对锂离子电池做好相应的保护,在电池的PACK封装过程当中,厂家还会在相应的设备当中加入保护电路板,但这些电路的存在会使得电池组以及外部极有可能在使用过程当中出现使用故障,常见的故障中包含有过充、过放、外部短路等情况,这些情况在一定情况下可能会使得电池发生过热、爆炸等类型的危险事件。
电池发生在过充后在内部会产生剧烈的化学反应,在一系列的反应发生的同时会伴随有大量的热产生,热量的聚集会导致隔膜失效,从而使得电池内部发生热失控。
过放会使电池的电压出于低于规定的放电截止电压,在低电压情况下,电解液会进一步分解进而形成大量的气体,内压突增,从而使电池外壳膨胀,最终导致漏液情况的发生。
镍钴铝三元锂电池容量“跳水”机理研究

第50 卷第 6 期2023年6 月Vol.50,No.6Jun. 2023湖南大学学报(自然科学版)Journal of Hunan University(Natural Sciences)镍钴铝三元锂电池容量“跳水”机理研究杨小龙†,罗卫,樵燊,高晓琳(湖南大学汽车车身先进设计制造国家重点实验室,湖南长沙 410082)摘要:对一款商用镍钴铝(LiNi0.8Co0.15Al0.05O2, NCA)/石墨锂电池进行固定节点老化实验,结合差分电压分析方法和电化学阻抗谱分析方法辨识出全生命周期内的老化模式,通过观察微观形貌对老化机理进行验证. 分析结果表明,该锂电池容量衰减过程存在2个阶段:第1阶段容量衰减较慢,该阶段的老化模式主要以负极活性材料损失和锂离子损失为主;第2阶段容量衰减剧烈,这是由于负极表面发生了析锂,直接消耗大量可循环锂造成锂离子损失增加,之后金属锂与电解液反应形成钝化层,增加电极在脱嵌锂过程中的机械应力,使得电极活性材料损失增加. 析锂副反应造成了容量“跳水”现象,后续钝化层的形成导致的活性材料损失加剧和析锂副反应的持续发生则是老化第2阶段容量快速衰减的原因.关键词:锂离子电池;衰退;石墨;容量跳水;老化机理中图分类号:TM912.9 文献标志码:AResearch on Capacity Plunge Mechanisms of NCA/GraphiteLithium-ion BatteriesYANG Xiaolong†,LUO Wei,QIAO Shen,GAO Xiaolin(State Key Laboratory of Advanced Design and Manufacturing for Vehicle Body, Hunan University, Changsha 410082, China)Abstract:In this study, the aging mechanism of commercial LiNi0.8Co0.15Al0.05O2/Graphite lithium-ion batteries at fixed nodes was studied experimentally,and the degradation modes in the whole life cycle were identified by differential voltage analysis method and electrochemical impedance spectroscopy analysis method,and verified by microscopic morphology observation. The results show that the capacity degradation of these lithium-ion batteries has two stages. In the first stage,the capacity degradation is slow,and the degradation modes in this stage are mainly composed of loss of anode active material and loss of lithium ions. In the second stage,the capacity degradation is sharp due to the lithium plating on the surface of the anode,which consumes a large number of recycled lithium ions directly,so the loss of lithium ions increases. The metallic lithium then reacts with the electrolyte and forms a dense covering layer, which increases the mechanical stress of the electrode in the process during the Li+intercalation/deintercalation processes,and makes the loss of electrode active material increase. Generally speaking,the lithium plating causes the capacity plunge phenomenon,the formation of the passivation layer aggravates the loss of active material, and the continuous lithium plating causes drastic capacity decay in the∗收稿日期:2022-02-27基金项目:国家自然科学基金资助项目(51775179), National Natural Science Foundation of China(51775179);汽车仿真与控制国家重点实验室基金项目(20201210),Foundation of State Key Laboratory of Automotive Simulation and Control (20201210)作者简介:杨小龙(1973—),男,湖南桃源人,湖南大学副教授,博士† 通信联系人,E-mail:****************文章编号:1674-2974(2023)06-0171-09DOI:10.16339/ki.hdxbzkb.2023305湖南大学学报(自然科学版)2023 年second stage of aging.Key words:lithium-ion batteries;degradation;graphite;capacity plunge;aging mechanism近年来,使用清洁能源的新能源汽车特别是电动汽车得到快速发展,锂电池凭借着高能量密度、高功率密度、无记忆效应、自放电率低以及循环寿命长等优点,成了新能源汽车的首选储能方式[1]. 但是,随着锂电池的使用,伴随容量衰减以及功率下降,严重影响电动汽车的续航里程、加速性能以及安全性,因此,当车用锂电池衰减到初始容量的80%时,为避免安全隐患发生会强制锂电池退役. 退役下来的锂电池由于还有较高的使用价值,往往会被梯次利用,布置在电动工具、储能系统中使用. 然而,锂电池在梯次利用周期中经常出现容量“跳水”现象,容量“跳水”现象指的是锂电池在某个阶段,最大可用容量发生突变,容量衰减速率增大,同时亦伴随着内阻在某个阶段发生突变,内阻增长速率突然增大[2]. 容量“跳水”极大地缩短了锂电池的全生命周期,因此,需要对容量“跳水”机理进行研究,指导电池设计或者使用策略制定,进而避免发生容量“跳水”,增加锂电池的使用价值.NCA/石墨锂电池相比磷酸铁锂电池,具有更高能量密度、更好的低温性能等优点,被广泛使用在电动汽车上[3]. 不少学者研究了NCA/石墨锂电池的循环老化. Wang等[4]研究不同充电模式下的NCA/石墨锂电池的老化性能,相比于恒流恒压充电模式,恒流充电模式能使锂电池快速衰减. Wong等[5]研究不同放电倍率下的NCA/石墨锂电池的老化性能,大倍率放电能够加快锂电池老化,脉冲放电比恒流放电能使锂电池更快老化. Waldmann等[6]研究不同温度下的NCA/石墨锂电池的老化性能,从0到60 ℃,随着温度的升高,锂电池的老化速率逐渐变小. 以上学者研究的都是锂电池容量“跳水”前的老化影响因素以及对应的老化机理,大多数老化实验衰减到80%左右便终止,对于容量“跳水”阶段鲜有涉及.而在实际应用过程中,锂电池梯次利用阶段也十分重要,因此需要对容量“跳水”进行机理分析.锂电池老化机理的表征方法可分为破坏性表征和非破坏性表征. 破坏性表征方法是通过将NCA/石墨锂电池拆解,进行形貌观察、元素测定以及成分分析等工作[7]. Bhattacharya等[8]将循环后的电池拆解,利用透射电子显微镜等工具,观察25 ℃和60 ℃环境下负极表面固体电解质界面层(Solid Electrolyte In⁃terphase, SEI)的生长规律,在60 ℃下,SEI膜生长比较均匀,可以快速地覆盖负极表面,而在25 ℃下SEI 生长存在不一致性,这会消耗大量的循环锂,使得容量相比60 ℃衰减得更快.非破坏性表征方法是通过固定节点老化实验,利用不同节点下的外特性数据分析整个容量衰减周期内的老化模式,常用的非破坏性表征方法有差分电压(Differential Voltage, DV)分析方法和电化学阻抗谱(Electrochemical Imped⁃ance Spectroscopy, EIS)分析方法[9]. Zulke等[10]采用DV分析方法研究不同荷电状态和不同温度下NCA/石墨锂电池在长时间搁置下的老化模式,发现日历老化主要的老化模式是SEI膜生长造成的锂离子损失.杨博健等[11]采用EIS分析方法研究了三元锂电池在不同温度(25 ℃、45 ℃)和不同充电倍率(0.5C、1C)下的老化模式,结果表明,在这4种循环条件下,锂离子损失和活性材料损失在电池老化中占主导地位,电导率损失影响较小.为了探究NCA/石墨锂电池老化后期容量“跳水”现象的老化机理,本研究将非破坏性表征方法和破坏性表征方法相结合. 首先,设计固定节点老化实验,记录每个节点的电池容量、内阻和阻抗谱等外特性数据;接着,通过DV分析方法对锂电池全生命周期的老化模式进行定性分析;然后,基于EIS分析方法和电压“迟豫”效应分析方法辨识“跳水”现象的诱因;最后,通过形貌观察对分析结果进行进一步验证. 对老化后期容量“跳水”现象的内在机理进行研究,可以为指导长寿命锂电池设计提供理论基础.1 实验方法实验采用的是全新松下三元圆柱锂离子电池,型号为NCR18650B,负极材料为石墨,正极材料为NCA,技术参数如表1所示. 首先,在25 ℃下对电池进行参考性能测试(Reference Performance Test,172第 6 期杨小龙等:镍钴铝三元锂电池容量“跳水”机理研究RPT),包括容量标定测试、DV测试、混合脉冲功率特性(Hybrid Pulse Power Characteristic,HPPC)测试、EIS测试以及电压“迟豫”效应测试.具体测试步骤如下:容量标定测试按以下工步循环2次:①将锂电池以0.5C恒流充电直至电压升至4.2 V,接着以4.2 V 恒压充电直至电流降至65 mA;②静置1 h;③将锂电池以0.5C恒流放电直至电压降至2.5 V;④静置1 h. 选取第2次循环的放电容量作为当前节点下的容量. DV测试按以下工步进行:①将锂电池以1/6C恒流充电直至电压升至4.2 V;②静置1 h;③将锂电池以1/2C恒流放电直至电压降为2.5 V;④静置1 h. 将充电段数据进行均值滤波,接着进行差分处理,绘制当前节点的差分电压曲线.HPPC测试按以下工步运行:①将锂电池以0.5C 恒流充电直至电压升至4.2 V,接着以4.2 V恒压充电直至电流降至65 mA;②静置1 h;③将锂电池以0.5C 恒流放电,直至消耗10%的标定容量;④静置1 h;⑤循环工步③~④,直至电压降至2.5 V.EIS测试按以下设置进行:①锂电池荷电状态为100%;②频率范围为0.01~10×103 Hz,幅值为0.002,灵敏度为1.电压迟豫效应测试按以下工步运行:①将锂电池以1C倍率恒流充电直至电压达到4.2 V,接着以4.2V恒压充电直至电流降为65 mA;②静置7 h;③将锂电池以0.5C倍率恒流放电直至电压降为2.5 V;④静置0.5 h. 将充电后静置段的电压数据进行差分分析,绘制当前节点的d V/d t-t曲线.为避免实验的偶然性,根据容量和内阻选取两个一致性较高的电池进行循环老化实验. 将电池置于25 ℃恒温箱中,按照图1所示进行1C倍率循环老化实验,充、放电循环测试步骤如表2所示. 每隔20次循环将电池置于25 ℃下进行RPT,追踪该循环次数下电池的老化状态. 当电池容量出现“跳水”现象,且衰减至50%左右时,结束循环老化实验进行拆解实验.实验所用的设备包括深圳新威生产的高性能电池测试系统(CT-4008-5V50A-NTA)、厦门易仕特生产的可编程式恒温恒湿试验箱(ST-100LB)、上海辰华生产的电化学分析仪(CHI604E)和德国蔡司生产的场发射扫描电子显微镜(ΣIGMA HD/VP).2 实验结果与讨论锂离子电池的健康状态可以用当前最大可用容量或者内阻评价[12],因此,通过容量标定测试结果和HPPC测试结果可以判断容量是否发生“跳水”.2.1 容量标定测试结果图2(a)和图2(b)是2个不同电池在不同循环次数下的充、放电曲线. 由图2(a)和图2(b)可以看出,随着循环次数的增加,锂电池的最大可用容量下降. 根据容量标定数据绘制的电池相对容量衰减曲线,如图2(c)所示,可以观察到,当规定容量损失20%为图1 循环老化实验流程图Fig.1 The flow chart of the cycling aging experiments表2 充、放电循环测试步骤Tab.2 The test steps of the charge and discharge cycle步骤1234状态CC-CV充电静置30 minCC放电静置30 min电流3.25 A (1C)3.25 A (1C)截止条件U≥4.2 V、I≤65 mAt=30 minU≤2.5 Vt=30 min表1 松下NCR18650B锂电池技术参数Tab.1 The technical parameters of Panasonic NCR18650Blithium-ion battery项目额定容量/最小容量充/放电截止电压标准充/放电倍率循环寿命(标准工况下)电芯尺寸电芯质量负极/正极材料技术参数3 250 mAh / 3 200 mAh4.2 V/ 2.5 V0.5C/1C180次循环(衰减到80%)直径18 mm、高度65 mm48.5 gGraphite / NCA173湖南大学学报(自然科学版)2023 年寿命终点时,该电池在25 ℃的1C 充、放电循环寿命分别为100次左右. 在25 ℃条件下,容量衰减曲线分为2个阶段:第1个阶段为0次循环到120次循环,线性衰减;第2个阶段为120次循环到160次循环,也是线性衰减,但衰减速率增大. 因此,可以判断锂电池在120次循环左右出现容量“跳水”现象.2.2 HPPC 测试结果图3为典型的HPPC 测试数据以及内阻的计算方法. 以50% SOC 时的放电片段为例,欧姆内阻R ohm 由放电片段前1 s 的电压差除以放电电流计算得到,极化内阻R polar 由放电片段1~60 s 的电压差除以放电电流得到.根据不同节点下的HPPC 数据,可绘制不同放电阶段下在20%SOC 、50%SOC 和80%SOC 的欧姆内阻和极化内阻曲线. 如图4(a )所示,随着循环次数的增加,欧姆内阻增加存在两个阶段,在老化第1阶段,欧姆内阻增加缓慢;进入老化第2阶段后,增长率变大. 如图4(b )所示,随着循环次数的增加,极化内阻也存在两个阶段,在老化第1阶段,极化内阻缓慢增加;进入老化第2阶段后,增长率变大. 由图4可知,欧姆内阻和极化内阻的两个阶段相重合,与容量衰减曲线的两个阶段相一致,因此,更加确定在120次循环左右时,锂电池出现了“跳水”现象.(a )不同循环次数下的锂电池欧姆内阻变化曲线(b )不同循环次数下的锂电池极化内阻变化曲线图4 HPPC 测试结果Fig.4 The results of HPPC tests(a )1号电池在不同循环次数下的充、放电曲线(b )2号电池在不同循环次数下的充、放电曲线(c )电池相对容量衰减曲线图2 容量标定测试结果Fig.2 The results of capacity calibration tests图3 典型的HPPC 测试数据以及内阻的计算方法Fig.3 Typical data of HPPC tests and calculationmethods of internal resistance174第 6 期杨小龙等:镍钴铝三元锂电池容量“跳水”机理研究3 老化机理研究按照老化机理对锂电池内部的影响,将老化机理归纳成3种老化模式(Degradation Mode, DM),分别是电导率损失(Conductivity Loss, CL)、锂离子损失(Loss of Lithium Ions, LLI)和活性材料损失(Lossof Active Material, LAM)[13]. CL对应的老化机理有集流体腐蚀、黏结剂溶解等;LLI对应的老化机理是SEI 膜生长、电解质分解、金属锂析出等;LAM可分为负极活性材料损失(LAM neg)和正极活性材料损失(LAM pos), LAM neg对应负极活性材料破裂、脱落、孤立等,LAM pos对应正极活性材料中二次颗粒破碎、开裂等.本文首先利用DV分析方法对NCA/石墨锂电池全生命周期内的老化模式进行定性分析,确定锂电池老化的主要老化模式以及老化模式演变规律. 其次结合EIS分析方法和电压“迟豫”效应分析方法确定“跳水”现象的内在机理.根据形貌观察分析方法对锂电池内部的老化机理进行辨识,进一步研究“跳水”现象出现的原因. 最后归纳在25 ℃条件下,镍钴铝三元锂电池全生命周期内衰减的老化机制.3.1 DV分析结果DV分析方法是锂电池非破坏性老化表征的常用方法,DV曲线的横坐标是容量Q,纵坐标是d V/d Q,电压和容量来源于1/6C的恒流充电数据. 由于锂离子在电极的脱嵌过程存在相变,反映到DV曲线上有相应的波峰形成,对于NCA/石墨体系的锂电池,据相关研究[14],DV曲线有3个明显的峰,如图5(a)和图5(b)所示,峰P1、P2由负极决定,峰P3由正极决定,通过观察峰的偏移即可确定锂离子损失以及正、负极活性材料损失,0%SOC与峰P2之间的横坐标差Q1的变化量ΔQ1反映了循环过程中由于负极活性材料损失造成的负极容量损失Q neg,N,峰P3与100%SOC之间的横坐标差Q3的变化量ΔQ3反映了循环过程中正极活性材料损失造成的正极容量损失Q pos,N,而P2和100%SOC之间的横坐标差Q2的变化量ΔQ2反映了锂离子损失造成的电解液容量损失Q ele,N,Q cell的变化量ΔQ cell直接反映了整个电池的容量损失Q cell,N.Q cell,N = ΔQ cell = Q cell,Fresh–Q cell,N(1)Q neg,N = ΔQ1 = Q1,Fresh–Q1,N(2)Q ele,N = ΔQ2 = Q2,Fresh–Q2,N(3)Q pos,N = ΔQ3 = Q3,Fresh–Q3,N(4)式中:N代表循环次数(N=40、80、120、160).如图5(c)和图5(d)所示,在25 ℃环境温度下的(a)1号电池DV曲线(b)2号电池DV曲线(c)1号电池容量损失(d)2号电池容量损失图5 不同循环次数的DV分析结果Fig.5 The DV analysis results at different cycles175湖南大学学报(自然科学版)2023 年1C倍率循环过程中,存在锂离子损失和正负极活性材料损失,其中以负极活性材料损失和锂离子损失为主,两者相互影响,共同导致容量衰减. 在老化第1阶段(0~120次循环),电池容量损失Q cell,N线性增加,同时Q neg,N、Q ele,N和Q pos,N也是线性增长的.在老化第2阶段(120~160次循环),容量发生“跳水”,可以观察到电池容量损失Q cell,N大幅度增加,此时Q neg,N、Q ele,N和Q pos,N也有大幅度增加.但依然以Q neg,N和Q ele,N为主. 综上所述,NCA/石墨锂电池在该条件下循环老化的主要老化模式是负极活性材料损失和锂离子损失,存在少量的正极活性材料损失. 老化后期,负极活性材料损失和锂离子损失会增加,这是容量“跳水”阶段容量快速衰减的内在机理.3.2 EIS分析结果EIS是研究锂电池内部电极界面反应机理和容量衰减机制强有力的工具,能通过等效电路模型拟合得到相关电极过程动力学参数和电池阻抗.图6(a)和图6(b)分别是1、2号电池是在25 ℃不同循环次数下100%SOC状态下的EIS曲线. 由6(a)和图6(b)可以发现,锂电池的EIS曲线由2个半圆和2条斜线构成,高频区域的半圆与锂电池的SEI膜阻抗(R SEI)有关,低频区域的半圆与电池电荷传递阻抗(R ct)有关,高频区域的斜线与锂电池欧姆阻抗(R ohm)有关,低频区域的斜线与离子扩散阻抗(R w)有关. 各个阻抗随循环次数的变化曲线分别如图6(c)和图6(d)所示.为了更好地量化锂电池内部各部分阻抗,通过Zview软件,采用二阶RC等效电路模型对EIS曲线进行最小二乘拟合. 因为老化模式不仅会带来容量的下降,还会带来相应阻抗的增加,因此,可以通过阻抗的增长规律来研究对应老化模式的演变情况. 据相关研究[15],如表3所示,R ohm反映的老化模式是电导率损失,R SEI和R ct反映的老化模式为锂离子损失,而R w反映的老化模式是电极活性材料损失.由于各个阻抗的量级存在差异,因此无法通过阻抗的大小直接确定老化模式的主次,只能通过各个阻抗的增长情况来辨识对应老化模式的增长情况. 据有关研究[7],可以采用如下公式量化各个老化模式的定基增长率(Fixed Base Growth Rate, FBGR).I CL,N=R ohm,N / R ohm,Fresh-1(5)I LLI,N=(R SEI,N+R ct,N)/(R SEI,Fresh+R ct,Fresh)-1(6)I LAM,N=R w,N/R w,Fresh-1(7)式中:I CL,N为电导率损失的定基增长率;I LLI,N为锂离子损失的定基增长率;I LAM,N为活性材料损失的定基增长率;N代表循环次数(N=40、80、120、160).(a)1号电池不同循环次数的EIS曲线(b)2号电池不同循环次数的EIS曲线(c)R SEI 随循环次数的变化曲线(d)R ohm、R ct和R w随循环次数的变化曲线图6 不同循环次数的EIS分析结果Fig.6 The EIS analysis results at different cycles176第 6 期杨小龙等:镍钴铝三元锂电池容量“跳水”机理研究图7为各个老化模式的定基增长率曲线. 由图7可知,随着循环次数的增加,锂离子损失和活性材料损失的定基增长率在老化第2阶段明显增大,说明锂离子损失和活性材料损失在“跳水”之后变得更加剧烈,导致容量衰减更快,这与DV分析结果一致. 而电导率损失的定基增长率几乎不变,说明电导率损失速率在全生命周期内几乎没有变化. 观察SEI膜阻抗的变化曲线[图6(c)],SEI膜阻抗增加存在两个阶段,第1阶段是0~120次循环,SEI膜缓慢增加,通常认为是电解液在负极发生了还原反应,有机碳酸溶剂被还原成二碳酸乙烯锂(Lithium Ethylene De⁃carbonate, LEDC)、氟化锂等物质,形成一层内部致密(以无机固体为主)、外部疏松(以有机固体为主)的SEI膜,SEI膜的缓慢增厚导致SEI膜阻抗的缓慢增加. 在120次循环左右,SEI膜阻抗迅速增加,根据相关文献报道[16],NCA/石墨锂电池中SEI膜主要分布在负极,因此可以推断锂电池负极在120次循环后有新的副反应发生,副反应产物共同构成SEI膜,极大地增加了SEI膜阻抗. 通过对1号电池不同循环次数下的充电后搁置段数据进行差分电压分析,如图8所示,在经历120次循环后,d V/d t-t曲线都存在相应的波谷,据相关文献报道[17],这一现象是负极表面发生析锂副反应后导致的电压“迟豫”效应.综上所述,容量“跳水”现象的内在机理是因为锂离子损失和负极活性材料损失发生了剧烈增加,其中锂离子损失激增是由于在负极表面诱发了析锂副反应,消耗了大量锂离子,同时钝化膜的形成使得SEI膜阻抗也发生了激增. 至于负极活性材料损失的剧烈增加还需要进一步分析.3.3 形貌观察分析结果将1号电池和一新电池在0%SOC状态下进行拆解,肉眼观察到的局部形貌如图9所示. 1号电池负极活性材料脆性较大,易剥落,说明电解液发生了分解,电池内部液相减少. 同时1号电池负极表面有银白色的固体附着,根据有关文献报道[18],银白色固体是析出的金属锂与电解液反应形成的钝化层,这与前面讨论的“跳水”现象诱因相对应. 1号电池正极活性材料与隔膜黏结,亦可反映电解液分解严重. 可以看到1号电池负极表面钝化层以点带状分布,正极与隔膜的黏结也以点带状分布,且两者相对应,说明钝化层的形成增加了电池各个组件之间的应力,使得隔膜易黏结在正极表面.制作包含钝化层的1号电池负极裁片,以及不包含隔膜黏结部分的1号电池正极裁片,同时制作新电池正、负极裁片. 将4个裁片用碳酸乙烯酯(Eth⁃ylene Carbonate, EC)溶剂进行清洗,经烘干后再进行喷金处理,最后进行SEM形貌对比,如图10所示.相比新电池负极,1号电池负极表面覆盖了一层厚实的膜(钝化层),观察不到石墨颗粒的形貌,同时表面膜分布着裂纹. 1号电池正极的一部分二次颗粒发生破碎,破碎的一次颗粒附着在表面. 通过对1号电图8 充电后搁置段的差分电压分析曲线Fig.8 Differential voltage analysis curves of shelving sectionafter charging图7 各个老化模式的FBGR曲线Fig.7 FBGR curves of each degradation modes表3 老化模式、阻抗以及老化机理之间的对应关系Tab.3 The corresponding relationship among degradation modes, impedances and aging mechanisms老化模式CL LLI LAM 对应的阻抗R ohmR SEI和R ctR w对应的老化机理集流体腐蚀、黏结剂分解电解液分解与氧化、析锂、SEI膜生长、Ni-O膜生长电极活性材料分解与剥落、晶体结构无序化、过渡金属溶解与析出177湖南大学学报(自然科学版)2023 年池进行形貌观察,可以推断主要的老化机理是负极活性材料开裂、SEI 膜生长、析锂副反应以及钝化膜的形成、正极二次颗粒破碎等,这与前面的全生命周期内老化模式分析和“跳水”现象机理研究相一致.相关研究认为正极过渡金属(Ni 、Co 、Al )的溶解并迁移到负极,会加速SEI 膜的形成,从而导致SEI 膜阻抗激增[19]. 针对这一可能原因,在进行负极的形貌表征工作的同时,对老化电池的负极也进行了局部能量色散光谱(Energy Dispersive Spectroscopy , EDS )分析,对负极表面局部区域的元素进行定性和定量检测. 老化电池负极的局部EDS 如图11所示,元素分析结果如表4所示. 由图11和表4可知,在负极表面没有发现过渡金属,因此,推断该电池并不是由于正极过渡金属离子的溶解并迁移到负极,导致负极SEI 膜增厚.根据以上分析,可以把NCA/石墨锂电池在25 ℃下进行1C 倍率循环时的全生命周期老化机理进行归纳. 在老化第1阶段,容量损失主要由负极SEI 膜形成造成的锂离子损失和负极活性材料损失主导. 随着负极表面膜的增厚,诱发了析锂副反应,金属锂与电解液反应形成的致密钝化层,增加了电极与隔膜之间的接触应力,导致活性材料损失加剧. 因此,析锂副反应是“跳水”现象的诱因,持续的析锂和钝化膜形成造成的负极活性材料损失加剧是老化第2阶段容量快速衰减的内在原因.(a )新电池负极(b )1号电池负极(c )新电池正极(d )1号电池正极图9 新电池和老化电池的肉眼形貌观察对比Fig.9 The observation and comparison of electrodes betweenfresh cell and aged cell by eyes(a )新电池负极(b )1号电池负极(c )新电池正极(d )1号电池正极图10 新电池和老化电池的SEM 形貌对比Fig.10 The observation and comparison of electrodes betweenfresh cell and aged cell by SEM178第 6 期杨小龙等:镍钴铝三元锂电池容量“跳水”机理研究4 结 论为了研究NCA/石墨锂电池容量“跳水”现象内在的机理,在常温下设计了老化实验并利用DV 分析方法、EIS 分析方法以及形貌观察分析方法进行相应的表征. NCA/石墨锂电池老化存在两个阶段,老化第1阶段衰减较缓,主要的老化模式是负极活性材料损失和锂离子损失;随着循环的继续进行,负极表面发生析锂,消耗了大量可循环锂,后续钝化层的形成使得电极内部应力增加,导致活性材料损失加剧,这些副反应共同导致容量“跳水”现象发生,从而进入容量衰减剧烈的老化第2阶段. 该研究为长寿命电池设计提供了新思路,可以预留电池内部各部件之间的间隙,当钝化膜形成时,电池内部应力较小,不足以增加活性材料损失,从而延长电池使用寿命. 同时该研究确定了全生命周期内的老化机理演变过程,为机理老化模型的建立提供理论基础.参考文献[1]胡兴军,惠政,郭鹏,等.锂离子电池组间接接触液冷散热结构研究[J ].湖南大学学报(自然科学版),2019,46(2):44-50.HU X J ,HUI Z ,GUO P ,et al .Research on the indirect contact liquid cooling heat dissipation structure of lithium-ion battery pack [J ].Journal of Hunan University (Natural Sciences ),2019,46(2):44-50.(in Chinese )[2]李浩强,范茂松,周自强,等.三元锂离子电池的容量跳水机理研究[J ].电源技术,2021,45(2):153-157.LI H Q ,FAN M S ,ZHOU Z Q ,et al .Research on capacity divingmechanism of ternary lithium-ion batteries [J ].Chinese Journalof Power Sources ,2021,45(2):153-157.(in Chinese )[3]LIU C ,QIAN K ,LEI D N ,et al .Deterioration mechanism ofLiNi 0.8Co 0.15Al 0.05O 2/graphite-SiO x power batteries under high temperature and discharge cycling conditions [J ].Journal of Materials Chemistry A ,2018,6(1):65-72.[4]WANG H , FRISCO S , GOTTLIEB E , et al. Capacity degradationin commercial Li-ion cells : the effects of charge protocol and temperature [J ]. Journal of Power Sources , 2019, 426: 67-73.[5]WONG D , SHRESTHA B , WETZ D A , et al. Impact of high ratedischarge on the aging of lithium nickel cobalt aluminum oxide batteries [J ]. Journal of Power Sources , 2015, 280: 363-372.[6]WALDMANN T , KASPER M , WOHLFAHRT-MEHRENS M.Optimization of charging strategy by prevention of lithium deposition on anodes in high-energy lithium-ion batteries-electrochemical experiments [J ]. Electrochimica Acta , 2015, 178: 525-532.[7]WALDMANN T , ITURRONDOBEITIA A , KASPER M , et al.Post-mortem analysis of aged lithium-ion batteries : disassembly methodology and physico-chemical analysis techniques [J ]. Journal of the Electrochemical Society , 2016, 163(10): A2149.[8]BHATTACHARYA S , RIAHI A R , ALPAS A T. Thermal cyclinginduced capacity enhancement of graphite anodes in lithium-ion cells [J ]. Carbon , 2014, 67: 592-606.[9]PASTOR-FERNANDEZ C , YU T F , WIDANAGE W D , et al.Critical review of non-invasive diagnosis techniques for quantification of degradation modes in lithium-ion batteries [J ]. Renewable and Sustainable Energy Reviews , 2019, 109: 138-159.[10]ZULKE A , LI Y , KEIL P , et al. High-energy nickel-cobalt-aluminium oxide (NCA ) cells on idle : anode-versus cathode-driven side reactions [J ]. Batteries & Supercaps , 2021, 4(6):934-947.[11]杨博健,戴海峰.基于交流阻抗谱的锂离子电池老化模式量化方法[J ].武汉大学学报(工学版),2019,52(7):635-641.YANG B J ,DAI H F .Quantification of degradation mode using electrochemical impedance spectroscopy of lithium-ion battery [J ].Engineering Journal of Wuhan University ,2019,52(7):635-641.(in Chinese )[12]FANG R Q , DONG P , GE H , et al. Capacity plunge of lithium-ion batteries induced by electrolyte drying-out : experimental andmodeling study [J ]. Journal of Energy Storage , 2021, 42: 103013.[13]BIRKL C R , ROBERTS M R , MCTURK E , et al. Degradationdiagnostics for lithium ion cells [J ]. Journal of Power Sources , 2017, 341: 373-386.[14]RAJ T , WANG A A , MONROE C W , et al. Investigation of path-dependent degradation in lithium-ion batteries [J ]. Batteries &Supercaps , 2020, 3(12): 1377-1385.[15]PASTOR-FERNANDEZ C , UDDIN K , CHOUCHELAMANE GH , et al. A comparison between electrochemical impedance spectroscopy and incremental capacity-differential voltage as Li-ion diagnostic techniques to identify and quantify the effects of degradation modes within battery management systems [J ]. Journal of Power Sources , 2017, 360: 301-318.[16]WATANABE S , KINOSHITA M , HOSOKAWA T , et al.Capacity fade of LiAl y Ni 1-x -y Co x O 2 cathode for lithium-ion batteries during accelerated calendar and cycle life tests (surface analysis of LiAl y Ni 1-x-y Co x O 2 cathode after cycle tests in restricted depth of discharge ranges )[J ]. Journal of Power Sources , 2014, 258: 210-217.[17]REN D S , SMITH K , GUO D , et al. Investigation of lithiumplating-stripping process in Li-ion batteries at low temperature using an electrochemical model [J ]. Journal of the Electrochemical Society , 2018, 165(10): A2167.[18]SIEG J , STORCH M , FATH J , et al. Local degradation anddifferential voltage analysis of aged lithium-ion pouch cells [J ]. Journal of Energy Storage , 2020, 30: 101582.[19]ZHANG J H ,JIN Y H ,LIU J B ,et al .Recent advances inunderstanding and relieving capacity decay of lithium ion batteries with layered ternary cathodes [J ].Sustainable Energy & Fuels ,2021,5(20):5114-5138.图11 老化电池负极的局部EDSFig.11 Local EDS of the negative electrode of the aging battery表4 老化电池负极的局部EDS 元素分析结果Tab.4 Results of local EDS element analysis of negativeelectrode of aging battery元素CO F P 总量质量分数/%47.0647.494.790.66100.00原子数分数/%54.7241.463.520.30100.00179。
深度剖析NCM811电池寿命衰减原因

深度剖析NCM811电池寿命衰减原因为了满足EV和大规模静态储能市场的需求,锂电池逐渐向着能量密度更大、更便宜、更安全和更长寿命的方向发展。
锂电池的能量密度可以通过提高材料比容量和平均工作电压来提高。
但是,电极材料的结构稳定性和锂电池内部的寄生反应严重影响着锂电池的循环寿命。
那么到底什么才是最主要的原因呢?镍钴锰三元材料是当前动力电池的主要材料之一,三元素对于正极材料具有不同的意义,其中镍元素是为了提高电池容量的,镍含量越高材料比容量越大。
NCM811比容量能达到200mAh/g,放电平台约3.8V,可以做成高能量密度的电池。
但是NCM811电池存在的问题是安全性差及循环寿命衰减较快,影响其循环寿命和安全性的原因是什么,如何解决这个难题呢?下面来深度剖析下:将NCM811做成纽扣电池(NCM811/Li)、软包电池(NCM811/石墨),分别测试其克容量和全电池的容量。
将软包电池分为4组进行单因素实验,参数变量是截止电压,其值分别为4.1V、4.2V、4.3V、4.4V。
首先,将电池以0.05C倍率循环2次,之后以0.2C倍率在30℃下循环。
经过200次循环后,软包电池循环曲线如下图所示:由图中可以看出,在较高截止电压条件下,活物质克容量、电池容量都高,但是电池容量和材料的克容量衰减地也更快。
反而是较低的截止电压(4.2V以下)下,电池容量衰减缓慢,循环寿命更长。
本实验利用等温量热技术研究寄生反应和利用原位、非原位XRD和SEM对正极材料在循环过程中的结构和形态退化进行了研究。
结论如下:一、结构变化并不是电池循环寿命衰减的主要原因非原位XRD和SEM数据结果表明:未循环的电池极片与截止电压分别为4.1V、4.2V、4.3V、4.4V的电池以0.2C倍率循环200次后,在颗粒形貌上和原子结构上无明显区别。
所以,充放电过程中活物质急剧的结构变化并不是电池循环寿命衰减的主要原因。
反而是,在电解液和脱锂状态下高活性活物质颗粒界面间的寄生反应才是4.2V高电压循环下电池寿命缩短的主要原因。
- 1、下载文档前请自行甄别文档内容的完整性,平台不提供额外的编辑、内容补充、找答案等附加服务。
- 2、"仅部分预览"的文档,不可在线预览部分如存在完整性等问题,可反馈申请退款(可完整预览的文档不适用该条件!)。
- 3、如文档侵犯您的权益,请联系客服反馈,我们会尽快为您处理(人工客服工作时间:9:00-18:30)。
锂电池随着使用次数增加而最大容量下降
将分为内因和外因来说:
1.内因
(1)在电极方面,反复充放电使电极活性表面积减少,电流密度提高,极化增大;活性材料的结构发
生变化;活性颗粒的电接触变差,甚至脱落;电极材料(包括集流体)腐蚀;
现阶段常用电池负极为石墨,正极是LiCoO2,LiFePO4以及LiMn2O4等,电池放点初期电解液会在电
极表面形成一层SEI(固态电解质)膜,其成分主要是ROCO2Li(EC和PC环状碳酸酯还原产物)、ROCO2Li和ROLi(DEC和DMC等链状碳酸酯的还原产物)、Li2CO3(残余水和ROCO2Li反应产物),若用LiPF6时,残余的HF会与SEI中ROCO2Li,使SEI中主要是LiF和ROLi。
SEI是Li+导体,脱嵌锂时碳电极体积变化很小,但即使很小,其产生的内应力也会使负极破裂,暴露
出来新的碳表面再与溶剂反应形成新的SEI膜,这样就造成了锂离子和电解液的损耗,同时,正极材料
活性物质膨胀超过一定程度也会形成无法修复的永久性结构触损耗,这样正极和负极的不断损耗造成了
容量的不断衰减;再者,增加的SEI膜会造成界面的电阻层架,使电化学反应极化电位升高,造成电池
性能衰减
在电极中,随着充放电反应的进行,黏结剂的性能也会逐步下降,,黏结强度降低,使电极材料脱落;
铜箔和铝箔是常用的负极和正极集流体,两者都容易发生腐蚀,腐蚀产物聚集在集流体表面成膜,增加
内阻,铜离子还能形成枝晶,穿透隔膜,使电池失效。
(2)在电解质溶液方面,电解液或导电盐分解导致其电导率下降,分解物造成界面钝化;
锂离子电池液体电解质一般由溶质(如LiPF6、LiBF4、LiClO4等锂盐)、溶剂和特种添加剂构成。
电
解质具有良好的离子导电性和电子绝缘性,在正负极之间起着输送离子传导电流的作用。
锂离子电池在
第一次充放电、过充和过放时以及长期循环之后,电解质会发生降解作用,并伴有气体产生,气体的组
成较为复杂,还无法通过某种反应在电池内加以消除。
随着电池充放电次数的增加。
由于电极材料氧化
腐蚀会消耗掉一部分电解液,导致电解液缺乏,极片不能完全清润到电解液,从而电化学反应的不完全,使得电池容量达不到设计要求。
(3)隔膜阻塞或损坏,电池内部短路等
隔膜的作用是将电池正负极分开防止两极直接短路。
在锂离子电池循环过程中,隔膜逐渐干涸失效是电
池早期性能衰退的一个重要原因。
这主要是由于隔膜中电解液变干使溶液电阻增大,隔膜电化学稳定
性和机械性能,以及对电解质浸润性在反复充电过程中变差造成的。
由于隔膜的干涸,电池的欧姆内阻
增大,导致放电不完全,电池反复受到大容量过充,电池容量无法回复到初始状态,大大降低了电池的
放电容量和使用寿命。
2.外因
(1)快速充放电
快速充电时,电流密度过大,负极严重极化,,锂的沉积会更明显,使在铜箔与碳类活性物质边界处的铜
箔脆化,极易产生裂缝。
电芯自发卷绕受到固定空间的限制,铜箔无法自由伸展产生压力,在压力的作
用下,原有的裂缝扩散生长,因扩展空间不够,铜箔发生断裂。
(2)温度
在明显高于室温的情况下,有机电解质的热稳定性成为首先要考虑的问题,这全要包括有机电解质自身
热稳定性以及电极隋机电解质相互作用的热稳定性两个方面。
一般认为,正极/有机电解质的反应对铿
离子电池安全性的影响是主要因素。
因为正极、电解质的反应动力学非常快,故控制着整个电池耐热
性能。
如果电池的环境温度足以引起正极电解质反应,就会导致电池的热失控状态,甚至起火、爆炸。
放电电流的大小直接影响锂离子电池的放电容量,在大电流放电时不仅存在严重的电柳电解质界面极化,还有活性体即嵌入离子及在电极中的扩散极化。
(3)长期深度充放点
放电要转入从内部结构来说,一是会造成电解液过度挥发,二是锂电池的负极过度反应使其介质膜发生
变化造成脱嵌能力下降,形成容量的永久性损失;充电主要从电压稳定性和到深夜电网电压升高,本已
经停止充电的充电器,电压升高后,又会继续充电,造成电池过充电导致正极材料结构变化容量损失,
分解放氧与电解液剧烈氧化反应进而燃烧爆炸;电解液有机溶剂/电解质锂盐分解;负极析锂过放可能导
致负极铜集电极溶解,正极形成铜枝晶。
(4)震动和冲撞
一般是工艺原因,如焊接牢固与否,内部电路是否设计合理等有关。
参考文献
[1]Abraham D P, Knuth J L, DeesD W.Performance degradation of high-power lithium-ion cells-electrochemistry of harvested electrodes[J].Journal of Power Sources,2007,170(2):465 -475.
[2]刘明志.可靠性试验[M].北京:电子工业出版社,2004: 75-80.
[3]贾颖,黎火林.锂离子电池失效率模型的探讨[J].北京航空航天大学学报,2008,34(8):973-985
[4] 周震涛,严燕. 表面处理对锂离子电池胶粘剂性能的影响[J]. 电池. 2000(06)
[5] 覃迎峰,周震涛. 锂离子动力电池过充行为的研究[A]. 电动车及新型电池学术交流会论文集[C]. 2003
[6] 姚晓林,陈春华. 提高锂离子电池安全性的电解液添加剂探索[A]. 第十二届中国固态离子学学术会议论
文集[C]. 2004
[7]黎火林;苏金然;;锂离子电池循环寿命预计模型的研究[J];电源技术;2008年04期等。