哈工大数控技术课大作业
哈工大数控技术大作业二 DDA法椭圆插补
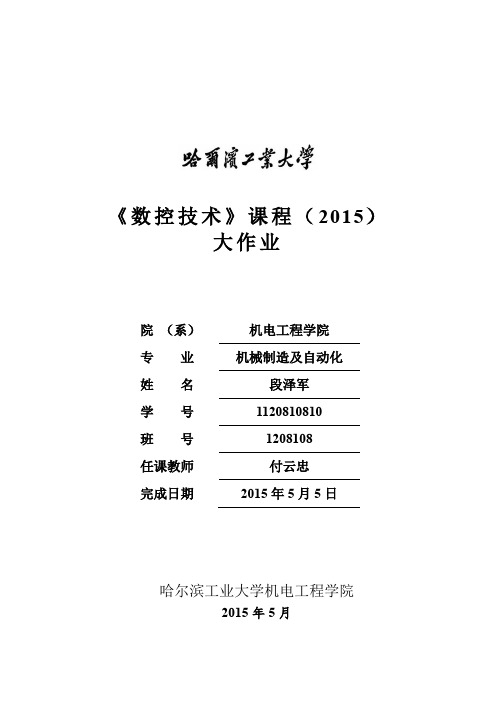
三,插补器的结构框图
dɵ
X
b/adyຫໍສະໝຸດ Y -1a/bdx
图 2.2 插补器的结构框图
四,DDA 法椭圆插补的终点判别
每次累加后,用 ������、 ������与椭圆终点坐标值作比较,当某个坐标轴到终点,该 轴不会有脉冲发出,当两个坐标轴都到达终点时,插补结束。
4
数控技术(双语)课程作业——题目 3
五,DDA 法椭圆插补实例
设已知椭圆方程为25 + 26 = 1,插补起点 A(5,0),插补终点 B(0,4),逆时针加 工,用 DDA 法插补此段圆弧。 根据上述插补方法,设寄存器整数部分占 4 位,小数部分占 4 位,共 8 位, 慢 8 溢出,则插补过程如表 2.1。
数控技术(双语)课程作业要求
目的:
数字积分插补方法是实现数控插补功能的重要方法之一。除平面直线和圆弧 外,数字积分法法也可以实现多坐标插补联动以及描绘如二次曲线甚至高次曲线 等各种函数曲线,精度也能满足要求,在一些专用数控机床和高档数控系统中得 到了广泛的应用。因此,深入理解数字积分插补方法是掌握数控加工知识的重要 内容之一。
������ =
0
������ ������
������������������ =
1 2������
������ =1 ������
������ =1
3
数控技术(双语)课程作业——题目 3
二,椭圆插补的步骤
1,插补运算开始,x 轴、y 轴的被积函数分别存放其初值(分别为������ ������、������ ������) , 总步长分别为 ������������ − ������������ 、 ������������ − ������������ ; 2,x 轴累加器得到的溢出脉冲发向-x 方向,y 轴累加器得到的溢出脉冲发送 到+y 方向; 3,某一轴发出一个进给脉冲后,须将该轴被积函数的坐标轴修正,即当 x 轴 方向发出进给脉冲时 y 轴的被积函数的 x 值减 1 后乘以������ ,当 y 轴方向发出进给脉 冲时 x 轴的被积函数的 y 值加 1 后乘以 。
哈工大——CADCAM技术基础大作业

CAD/CAM技术基础大作业题目: CAD/CAM技术应用及发展趋势学院:机电工程学院班号:姓名:学号:成绩:指导教师:日期:2014年05月28日CAD/CAM 技术现状及其发展趋势摘要:对CAD/CAM在企业中的应用现状进行分析,进一步指出了CAD/CAM技术的发展方向及在企业中的应用前景。
并结合汽车工业中的CAD/CAM技术的应用具体说明一些先进技术的应用前景与趋势,并分析国内外在CAD/CAM技术的发展上的差别。
关键词:CAD/CAM 应用现状发展趋势汽车工业1. CAD/CAM 技术概述计算机辅助设计和计算机辅助制造(CAD/CAM)技术是设计人员和组织产品制造的工艺技术人员在计算机的辅助之下,根据产品的设计和制造程序进行设计和制造的一项新技术,是传统技术与计算机技术相结合的产物。
设计人员通过人机交互操作方式进行产品设计构思和论证,产品总体设计、技术设计、零部件设计,完成有关零件的强度、刚度、热、电、磁的分析计算和零件加工信息(工程图纸或数控加工信息等)的输出,以及技术文档和有关技术报告的编制。
而工艺设计人员则可以利用CAD 过程提供的信息和CAM 系统的功能,进行零部件加工工艺路线的控制和加工状况的预显,并生成控制零件加工过程的信息。
目前,CAD/CAM 的工作内容主要有以下几个方面:(1 )产品设计数据库;(2)加工工艺库;(3)基础图形库;(4)应用程序库;(5)产品计算机辅助设计;(6)产品计算机辅助制造;(7)产品数理等。
CAD用于产品结构的表示,其作用是形成数字化产品。
也就是说顾客需要什么产品,那么设计者就根据顾客的需求,利用电脑做出它的模样。
当然从创作上讲,首先它有艺术创作的意义。
不过作为工厂加工时,它就应该遵循工厂加工条件。
狭隘的理解,所谓产品结构其实就是以前工程师的工程制图。
只是现在把制图工作计算机化。
当然,CAD 实现的不仅仅是平面工程图的绘制,它也能给出复杂的三维造型。
哈工大机械精度大作业参考资料

机械零件的精度设计1内容提要1. 机械零件精度设计的内容及选用;2. 圆柱齿轮精度设计的内容及选用:(1)单个齿轮的精度设计内容及选用;(2)齿轮坯的精度设计内容及选用;(3) 齿轮副的精度设计内容及选用。
3. 轴的精度设计内容及选用;4. 齿轮减速器箱体的精度设计内容及选用;5. 装配图上标注的尺寸和配合代号。
计算齿轮圆周线速度,确定其平稳性精度。
运动精度要求不高,故也选8级;载荷分布均匀性精度一般不低于平稳性精度,我们选7级。
2008)8 2008)2008)= 0.155mm。
用插入法得jbnminr0.1450.1151.26IT926.1r =×==b 1.10r =F 得由表15根据E sns =-0.110、E sni =-0.223和F r=0.056代入式(10.8),可得公法线长度上、下偏差为sin 72.0cos n n sns bns αα−=E Esin 72.0cos n n sni bni αα+=E E 按计算结果,在图样上的标注为117.0196.0551.87−−=k W 117.020sin 056.072.020cos 110.0 00−=×−−=196.020sin 056.072.020cos 223.000−=×+−=即Φ58H7 =E E03.00 58+φ072.039.2458h 39.245 −==φφa d 即20(3) 基准端面的圆跳动公差由式(10.14)得基准端面对基准孔轴线的圆跳动公差为()/2.0βd i F b D t ×=5. 确定齿轮副精度(1)齿轮副中心距极限偏差由表10.8查得f a =±0.0315则在图样上标注为0315.0150±=a ()016.0021.0232/600.2=×=21(2)轴线平行度偏差由式(10.11)得垂直平面上的平行度偏差最大值为()/βF b L f =∑δ由式(10.10)得轴线平面上的平行度偏差最大值为()/5.0βF b L f =∑β()035.0021.060/100=×=()018.0021.060/1005.0=×=表4.16齿面表面粗糙度为Ra≤1.25μmRa的上限值为1.25~2.5μm 取2 μm。
哈工大数控大作业完美版
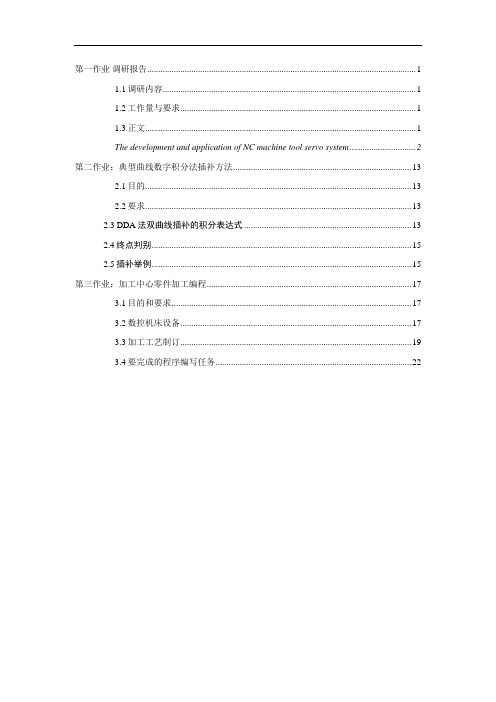
第一作业调研报告 (1)1.1调研内容 (1)1.2工作量与要求 (1)1.3正文 (1)The development and application of NC machine tool servo system (2)第二作业:典型曲线数字积分法插补方法 (13)2.1目的 (13)2.2要求 (13)2.3 DDA法双曲线插补的积分表达式 (13)2.4终点判别 (15)2.5插补举例 (15)第三作业:加工中心零件加工编程 (17)3.1目的和要求 (17)3.2数控机床设备 (17)3.3加工工艺制订 (19)3.4要完成的程序编写任务 (22)《数控技术》课程(2015)大作业院(系)专业姓名学号班号任课教师完成日期哈尔滨工业大学机电工程学院2015年5月数控大作业第一作业调研报告1.1调研内容请以课堂所学习的知识为基础,自主选择课程中所涉及的任一知识点进行调研。
可以调研知识点的发展脉络,也可以重点介绍该知识点的发展现状、争议与未来发展趋势。
请提交交独一无二的报告1.2工作量与要求1. 报告需用英文撰写,可计算机打印,也可手写,但最后封面需手工签名。
2. 格式请参照本科生毕业论文要求(见教务处网站),总字数不少于2000字。
3.在调研报告的最后,请列出参考的主要文献(英文学术刊物上正式发表的文献不少于5篇)或网址,并在正文中标注引用。
4. 如果出现雷同,两位同学均无成绩。
1.3正文The development and application of NC machine tool servo system Since the invention of NC machine tool in 1950s, servo system has been the indispensable component of the NC machine tool. With the rapid development of new materials, electronic power and controlling system, the servo system has evolved from the step-by-step system to DC system and then to AC system. As the blossom of AC servo technology, AC servo system will replace the DC system wholly and take up the dominant position in the family of servo system.With the electronic power conversion unit as actuator and controller as c ore , Servo system which contains the servo driver and servo motor const itutes the main part of the electric-driving and automatic control system . When working, firstly the servo system willreceive the signal from NC devices, and then drive the motion of machine tool as well as ensure the accuracy and speediness of movement under the guidance of pulse command . Usually, precision and speed of t he NC machine tool and other technical indicatorsmainly depend on the servo system itself1.The improvement and assortment of NC servo systemAt present, engineers tend to assess the quality by reference to several im portant indicators, such as precision, speed and so on. Therefore, a NC se rvo system must meet these requirements.High precisionUnlike the traditional manufacturing which can be manually handled to r egulate and compensate errors, the NC servo system has a high demand o n positioning accuracy and repeated positioning accuracyQuick repose characteristicQuick response is one of important indicators of servo system’s dynamic quality which requires the servo system following the command signal with minimum error as well as quick repose and high stability. Once receiving the instruction of manipulator, the working machine can restore the original state of equilibrium quickly after a short regulation or a disturbance from outer space.Wide speed rangeDue to the difference in work piece materials, cutting tool and process requirements, servo system must have wide speed range, so as to ensure that the CNC machine in any circumstances can get the optimal cutting condition. Thus the machine tool can satisfy the requirement of high speed machining as well as the requirement of low speed feed.The speed range is generally larger than 1 to 10000. when the machine is working in a low cutting speed which ask for a larger stable torqueoutput, NC servo system must maintain a good reliability.Good reliabilitythe usage of machine tool is frequent, usually with 24 hours' continuous work, so the servo system must have good working reliability. Servo system of NC machine tool can be divided into open loop control system and closed loop control system according to the presence of feedback test components. Drive control Unit transforms feeding instructions to perform signal needed by actuator, and then actuator convert this signal into mechanical displacement.In Open loop control system, there is no feedback detecting components and comparing control links. On the contrary, these are essential part of a closed-loop control system.The composition of servo systemServo system can be classified into the feed drive system and the spindle drive system on the basis of function and usage. Besides,the NC servo system can also be sorted into open loop control system and the closed loop control system in light of the presence of feedback detecting element.In addition, according to the difference of actuators, servo system can be divided into stepping servo system, dc servo system and ac servo system.Stepping servo systemBefore the 1960 s,the stepping servo system is based on step motor driven hydraulic servo motor or characterized by power steppingmotor as direct drive,and servo system uses open-loop control. Stepping servo system works with the pulse signal, and its speed and turning Angle depends on the frequency or the number ofInstruction pulses.Because there is no testing and feedback loop, the precision of the stepper motor step depends on the step angle, the accuracy of the gear transmission clearance and so on, its accuracy is low. stepping motor is easy to appear vibration phenomenon when working in the low frequency,and its output torque decreases with increment of speed. Because the stepping servo system is the open loop control, step motor in the start of machine with the over-high frequency or large load shows"lost" or "blocked" phenomenon and prone to appear phenomenon of high speed overshoot in the braking of the machine tool. At the same time, step motor speed accelerating from 0 to working speed requires longer time and slower speed response. But because of its simple structure, easy adjustment, and good working reliability and the low prices, the stepping system is a good choice in many many occasions of low occasions.Dc servo systemAfter 60 and 70 s, most of numerical control system adopts dc servo system. Dc servo motor has a good wide range speed performance, large output torque, and strong overload capacity. servo system also has evolved from open loop control into closed-loop control, thus in the industry as well as its related fields gains the more extensive or aboard application. However, with the rapid development of modern industry, the corresponding equivalents such as precision CNC machine tools, industrial robots make higher and higher requirements to the electrical servo system, especially the precision, reliability and other performance.The traditional dc motor uses a mechanical commutator, faced up with many problems in the application process, such as brush and commutator wear easily, maintenance work is heavy and the cost of it is high. Commutator reversing would produce sparks, the maximum speed of the motor and the application environment is limited;Dc motor has a more complex structure, higher cost,and prone to interfere other devices'work.Ac servo systemThe existence of these problems, limiting the dc servo system in high precision, high performance requires the application of servo driveoccasion.Because hard-overcoming weakness of dc motor, people have been seeking the development of ac servo motor to replace the dc motor whose advantage is limited by mechanical commutor and brush to satisfy the needs of various application fields, especially in the field of high precision and high-performance servo drive .But because the ac motor has strong coupling, nonlinear characteristics, so control is very complete and the high-performance application has been limited. Since the 1980 s, with the boom of the new technology such as electronic electricity, the modern control theory, and the breakthrough in the field of vector control algorithm, the original problems of AC motor which has bothered so many engineers has been solved, and ac servo development faster and faster.The characteristics of the ac servo systemIn addition to good stability, good rapidity,and high precision,servo motor system has a series of other advantages.with out the limitation of commutator circumferential speed and armature reactance potential numerical element, the speed limit ofAC motor can be design higher than DC motor in the same given motor. with a wide range of speed regulation, the most ac servo motor speed ratio can reach 1:50000,and high-performance servo motor speed ratio can even amount to ver 100000. Meet the numerical control machine tooldrive, wide speed range and small static rate request.good torque speed characteristicAC motor as the constant torque output, i.e. within its rated speed output rated torque, in for a constant power output above the rated speed.And torque overload capacity, can overcome the inertia moment of inertia load moment at start-up.Meet the machine tool servo system, large output torque, good dynamic accordingly, high positioning accuracy demands.The research status of domestic ac servoAc servo system consists of the ac servo system based on asynchronous motor and the ac servo system on the base of synchronous motor.At present machine mainly adopts a permanent magnet synchronous ac servo system.In the field of ac servo research, the Japan, the United States and Europe are in the forefront.In the mid 1980s, Japan yaskawa company has successfully developed the world's first ac servo drive.Then F ANUC, Mitsubishi, Panasonic and other companies have launched their own ac servo system. Most of these products from aboard companies are based on the asynchronous motor. However,domestic institutes has set up late in ac servo system with asynchronous motor,and so far there are still no products available. Many domestic researchers put much importance on the research of permanent magnet synchronous motor servo system. Huazhong university of science and technology, Beijing machine toolresearch institute, xi 'an micro motor research institute, shenyang institute of automation of Chinese academy of sciences, lanzhou electric factory etc have started out in the research of AC servo system and are expected to launch their own products. DA98 all-digital ac servo drive unit from guangzhou NC manufacturing company has already knock at the door of high-precision servo driver industry in our country, broken the monopoly of foreign countries , and initiated a new era belonging to our national brands.Ac servo signal and numerical control system interface have three different modes, which can also divided into three stages.Domestically, Guangzhou CNC DA98 which belongs to the first generation and is also a epoch-making servo drive, at the same time, it is first all-digital domestic ac servo drive unit, pulse command it accept direction. The second generation is EDB series delegated by Aston, it can not only accept pulse command signal, but also receive the signal from the speed control and torque control analog input.The third generation is networked ac servo worked servo system is the organic combination of industrial field-bus technology and full digital ac servo,which enables users to adjust the parameters according to load conditions and saves some unstable factors such as drift produced by analog circuits. Based on field bus network control technology,the servosystem the microprocessor and field bus interface in all type ac motor servo drive, form independent of intelligent digital servo control unit, it directly connected to the industrial field bus, it formed a new type of network control system based on field-bus.Reduced the number of hardware and the attachment, the structure of intelligent units on independent, to the outside world and realize data sharing between each other, but also can use other field control equipment, easy to extend.So far, the network communication server product in domestic has not yet mature.Robotics institute of Beijing university of aeronautics and astronautics development design a network based on DSP + FPGA + ASIPM ac servo control system, the principle prototype has been got preliminary validation of the three-dimensional carving machine. currently, the most server drive adopt high-speed DSP processors,which promote the movement of all kinds of advanced control algorithms in the use of new type of drive. Mostly, suppliers of servo system employ the structure of DSP + CPLD (FPGA) on the hardware. Because the DSP and CPLD (FPGA) can repeat programming,they are easy to realize modular re-configurable of the ac servo system.As long as the software for corresponding different system configurations, including the control algorithm can control and asynchronous motor, permanent magnet synchronous servo motor, brush-less dc motor, and through the reconfiguration of FPGA can also drive dc motor and three phaseinduction of stepping motor.It's for NC machine tool upgrade and innovation has left a lot of space.The development tendency of ac servoWith the constant improvement of productive forces, the ac servo system will be sophisticated in the direction of the integration, intelligent and network .integrationBy using a single and multi-function control unit, the servo system can achieve position control and speed control function through the setting of software and constitute a half closed loop feedback unit configuration or full closed loop control system of high accuracy through the external interface composition.intelligentServer intelligent control mode, such as internal programming can achieve a certain trajectory in advance and control the surrounding IO port as well as the adjustment of master-slave's following with electronic CAM, etc.networkServer implementation is distributed by network.The server's modulation could be reconstructed with low cost .conclusionThe modern NC machine tool is developing rapidly in the direction ofhigh speed and high precision.As the essential component of the NC machine tool,servo system has gradually equated to ac servo system which has several incomparable advantages compared with other servo systems. With the progress of the ac servo technology, it will gradually replace dc servo system overall.[参考文献][1]Tryling, David P.Simple servo uses.ProQuest Journal,2009.[2]J. Cao ;Z.W. Li ;Z.X. Meng.Development Of A Nc Servo System Based On Fuzzy Adaptive Control.Key engineering materials,2009.[3]Fusaomi&Nagata.Development of CAM system based on industrial robotic servo controller without using robot languag.Robotics andComputer Integrated Manufacturing,2013.[4]Mulan Wang Kaiyun Xu Chuan He Lei Zhou.Research on Servo System for CNC Machine Tool Driven by Permanent Magnet Synchronous Torque Motor.Materials Engineering and Automatic Control,2012[5]Xu, Kaiyun Li, Ning Lin, Jian He, Chuan.Development of linear servo control system for CNC machine tool based on DSP.International Conference on Mechatronic Science, Electric Engineering and Computer,2011第二作业:典型曲线数字积分法插补方法2.1目的数字积分插补方法是实现数控插补功能的重要方法之一。
哈工大2002及 2003学数控技术

哈工大 2003学年秋季学期数控技术 试题一、名词解释(10分) 1. 1.插补2.2.点位控制3.3.轮廓控制4.4.分辨率5.5.模态代码二、简答(30分)1.1.画出数控机床的组成框图,简要说明各部分作用。
2.简述CNC 装置是如何工作的。
3.简要说明CNC 装置的软件结构及特点。
4.简述光电脉冲编码器的各部结构及作用。
5.列举数控机床的位置检测装置有哪些?三、(20分)1.数控机床是如何通过“数据密化”控制刀具进行轮廓加工的?2.已知:第一象限直线OA ,起点O 在原点,终点A (4,2)注意行为规范,遵守考试纪律!要求:用DDA 直线插补加工OA ,其过程用表格说明,并画出插补加工轨迹。
1.用钻削固定循环加工图中两孔,要求编写程序并注释,使用刀具长度补偿,H02=-4mm 。
起刀点x=0、y=0、z=0;初始平面在z=150mm 处,参考平面和钻孔结束点如图所示。
其它参数合理自定。
y2 1 02.编写车削加工程序,加工ABCDEFGHI 部位的外轮廓,使用刀尖圆弧半径补偿(与铣削刀具半径补偿一样),直径设定。
加工尺寸如图,其它参数合理自定。
各程序段要求注释。
五、数控直流进给运动和交流进给运动的速度控制各用什么伺服电机?调速原理是什么?如何进行调速的?(20分)哈工大 2002 学年 数控技术 试题一、名词解释(10分) 6. 1.插补7.2.C 刀补注意行为规范,遵守8.3.轮廓控制9.4.分辨率10.5.模态G代码二、简答(30分)2.1.简要说明数控机床的组成及各部分作用。
2.简述CNC装置是如何工作的3.简要说明CNC装置的软件结构及特点。
4.基准脉冲插补和数据采样插补的特点?5.列举数控机床的六种位置检测装置?三、(25分)1. 已知:第一象限直线OA,起点O在原点,终点A(2,4)要求:用DDA直线插补加工OA,其过程用表格说明,并画出x2.简述光电脉冲编码器的工作原理,各部结构及作用。
数控加工工艺编程大作业

数控加工工艺编程大作业一、判断题(题末括号内1为正确,0为错误)1. 用设计基准作为定位基准,可以避免基准不重合引起的误差。
(1)2. 开机后,只要机床运动,其运动位置即可由相对位置显示出来,并可随时清零。
(1)3. G72是复合型车削固定循的端面粗车循环,它的循环走刀是与X轴平行运动的,所以在设置P(NS)起点定位值时,必须是Z方向值。
(1)4. 加工程序中有某些重复出现的部分,可作为子程序、由主程序直接调用和多次重复调用。
(1)5. 加工工艺的主要内容有:a、制定工序、工步及走刀路线等加工方案b、确定切削用量(包括主轴转速S、进给速度F、吃刀量等)C、制定补偿方案。
(1)6. 在GSK980系统中,U、W数值代表绝对坐标的径向尺寸和长度方向尺寸数值。
(0)7. GSK980系统中G92 X(U)__Z(W)__F_:代表英制螺纹切削循环。
(0)8. 加工中心和数控车床因能自动换刀,在其加工程序中可以编入几把刀具,而数控铣床因不能自动换刀,其加工程序只能编入一把刀具。
(1)9. 数控机床上可用公制螺纹指令加工英制螺纹,也可用英制螺纹指令加工公制螺纹。
(0)10. 在同一个程序里,既可以用绝对值编程又可以用增量值编程。
(1)11. 参考点是机床上的一个固定点,与加工程序无关。
(1)12. 对于任何曲线,既可以按实际轮廓编程,应用刀具补偿加工出所需要的廓形,也可以按刀具中心轨道编程加工出所需要的廓形。
(1)13. 尺寸链封闭环的基本尺寸是其它各组成环基本尺寸的代数差。
(0)14. 所谓前刀面磨损就是形成月牙洼的磨损,一般在切削速度较高,切削厚度较大的情况下,加工塑性金属材料时引起的。
(1)15. 工件以其已加工平面,在夹具的四个支承块上定位,属于四点定位。
(0)16. 逆时针圆弧插补指令是G02。
(0)17. 车削脆性材料时,车刀应选择较大的前角。
(0)18. 伺服系统由伺服驱动和伺服执行两个部分组成。
哈工大机械制造技术基础大作业

哈工大机械制造技术基础大作业一、零件加工图样在CA6140机床中,拨叉在变速箱中起到控制齿轮组的移动,改变啮合齿轮对,从而改变传动比实现变速功能。
零件材料采用200HT 灰铸铁,生产工艺简单、可铸性高,但材料脆性大不易磨削。
需要加工的部分及加工要求如下:1、0.0210Φ22+孔,还有与其相连的8M 螺纹孔和Φ8锥销孔;2、小孔的上端面,大孔的上下两端面;3、大头的半圆孔0.40Φ55+;4、Φ40上端面,表面粗5、糙度为 3.2Ra ,该面和Φ20孔中心线垂直度误差为0.05mm ;5、0.50Φ73+半圆形上下端面与Φ22孔中心线垂直度误差为0.07mm 。
二、零件加工工艺设计(一)确定毛坯的制造形式零件材料为HT200。
考虑到零件在机床运行时过程中所受冲击不大,零件结构又比较简单,生产类型为大批生产,故选择铸件毛坯。
选用铸件尺寸公差等级CT9级。
(二)工艺初步安排零件的加工批量以大批量为主,用通用机床加工,工序适当集中,减少工件装夹次数以缩短生产周期、保证其位置精度。
(三)选择基准基准的选择是工艺规程设计中的重要工作之一。
基准选择得正确合理,可以使加工质量得到保证,生产效率得以提高。
(1)粗基准的选择:以零件的底面为主要的定位粗基准,以两个小头孔外圆表面为辅助粗基准。
这样就能限制工件的五个自由度,再加上垂直的一个机械加紧,就可达到完全定位。
(2)精基准的选择:考虑到要保证零件的加工精度和装夹准确方便,依据“基准重合”原则和“基准统一”原则,以粗加工后的底面为主要定位基准,以两个小孔头内圆柱表面为辅助的定位精基准。
(四)制定工艺路线1.工艺方案分析此零件加工工艺大致可分为两个:方案一是先加工完与Φ22mm 的孔有垂直度要求的面再加工孔。
而方案二恰恰相反,先加工Φ22mm的孔,再以孔的中心线来定位加工完与之有垂直度要求的三个面。
方案一装夹次数较少,但在加工Φ22mm的时候最多只能保证一个面与定位面之间的垂直度要求。
哈尔滨工业大学 cad cam 大作业

CAD/CAM技术基础大作业题目:CAD/CAM软件在机械制造业中的作用及展方向学院:班号:姓名:学号:成绩:指导教师:日期:2014年06月03日CAD/CAM软件在机械制造业中的作用及发展方向摘要:随着计算机技术和信息技术的发展,CAD/CAM技术在全球迅速普及开来。
对制造业来说,CAD/CAM是提高产品设计品质和制造品质、缩短产品开发周期,降低产品开发成本的强有力手段,已成为企业赢得市场的制胜法宝。
因此,研究我国机械行业CAD/CAM技术应用现状、作用,探讨其发展前景,对加快我国机械行业CAD/CAM技术推广应用步伐,提高我国机械制造业的国际竞争力具有深远意义。
本文对我国机械行业CAD /CAM技术应用现状进行了综合分析,分析其作用,进一步指出了我国CAD /CAM技术的发展方向。
关键词:CAD/CAM;机械行业;作用;发展方向- 2 -引言现代机械制造业从设计到成型再到大批量生产,是一个十分复杂的过程,它需要产品设计师、加工工艺师、熟练的操作工人以及生产线的管理人员等协同努力来完成。
传统的手工设计、制造已越来越难以满足市场激烈竞争的需要,CAD/CAM技术的运用,取得了显著的经济效益。
CAD/CAM(计算机辅助设计与制造)技术产生于20世纪50年代后期发达国家的航空和军事工业中。
随着计算机技术和信息技术的发展,CAD/CAM技术在全球迅速普及开来。
对制造业来说,CAD/CAM是提高产品质量、缩短产品开发周期,降低产品开发成本的有力手段。
因此,研究我国机械行业CAD/CAM技术应用现状,探讨其发展前景,对加快我国机械行业CAD/CAM技术推广应用步伐,提高我国机械制造业的国际竞争力具有深远意义。
1.我国机械行业CAD/CAM技术应用现状1.1功能单一,经济效益并不明显CAD/CAM技术在企业中的应用仅是单一功能技术的应用,只是从企业生产的各个侧面来提高效率,推进自动化。
采用单一功能的CAD/CAM技术其效果是相当有限的,只有将CAD、CAPP、CAM等技术集成在一起,综合应用在设计与制造过程中,才能产生显著经济效益。
- 1、下载文档前请自行甄别文档内容的完整性,平台不提供额外的编辑、内容补充、找答案等附加服务。
- 2、"仅部分预览"的文档,不可在线预览部分如存在完整性等问题,可反馈申请退款(可完整预览的文档不适用该条件!)。
- 3、如文档侵犯您的权益,请联系客服反馈,我们会尽快为您处理(人工客服工作时间:9:00-18:30)。
《数控技术》课程大作业院(系)机电工程学院专业机械制造及其自动化姓名学号班号完成日期哈尔滨工业大学机电工程学院第一作业:加工中心零件加工编程一、目的和要求本作业通过给定一台数控机床具体技术参数和零件加工工艺卡,使学生对数控机床具体参数、加工能力和加工工艺流程有直观了解和认识。
同时,锻炼学生解决实际加工问题的能力。
1.了解加工中心的具体技术参数,加工范围和加工能力;2.了解实际加工中,从零件图纸分析到制定零件加工工艺过程;3.按照加工工艺编写指定的工序的零件数控加工程序。
二、数控机床设备(1)机床结构主要由床身、铣头、横进给、升降台、冷却、润滑及电气等部分组成。
XKJ325-1数控铣床配用GSK928型数控系统,对主轴和工作台纵横向进行控制,用户按照加工零件的尺寸及工艺要求,先编成零件的加工程控,最后完成各种几何形状的加工。
(2)机床的用途和加工特点本机床适用于多品种中、小批量生产的零件,对各种复杂曲线的凸轮、孔、样板弧形糟等零件的加工效能尤为显著;该机床高速性能好,工作稳定可靠,定位精度和重复精度较高,不需要模具就能确保零件的加工精度,减少辅助时间,提高劳动生产率。
(3)加工中心的主要技术参数数控机床的技术参数,反映了机床的性能及加工范围。
进给切削进行速度mm/min 1-4000快速移动速度m/min 15/10刀库刀库容量把20(24)刀具尺寸/重量mm/kg ∅80×300/8换刀时间s 气液动7S凸轮3S加工能力钻孔能力mm ∅32 镗孔能力mm ∅80 攻丝能力mm M24 铣削能力Cm3/min 100位置精度定位精度mm ±0.005 重复定位精度mm ±0.003其它气源气压L/min,bay250 5-7机床重量(净重/毛重) T 7.5/8.5机床外型尺寸mm 2756×2696×3000包装箱尺寸mm 3840×2545×3080三、加工工艺制订(一)加工零件加工图1零件,材料HT200,毛坯尺寸长*宽*高为170×110×50mm,试分析该零件的数控铣削加工工艺、如零件图分析、装夹方案、加工顺序、刀具卡、工艺卡等,编写加工程序和主要操作步骤。
图1 加工零件图(二)工艺分析(1)零件图工艺分析。
该零件主要由平面,孔及外轮廓组成,平面与外轮廓的表面粗糙度要求Ra6.3,可采用铣粗—精铣方案。
(2)确定装夹方案。
根据零件的特点,加工上表面,¢60外圆及其台阶面和孔系时选用平口虎钳夹紧;铣削外轮廓时,采用一面两孔的定位方式,即以底面,¢40H和¢13孔定位。
(3)确定加工顺序。
按照基面先行,先面后孔,先粗后精的原则确定加工顺序,即粗加工定位基准面(底面)——¢60外圆及其台阶面——孔系加工——外轮廓铣削——精加工底面并保证尺寸40。
(4)刀具的选用加工中心刀具通常由刃具和刀柄两部分组成,刃具有面加工用的各种铣刀和孔加工用的各种钻头、扩孔钻、镗刀、铰刀及丝锥等,刀柄要满足机床主轴自动松开和夹紧定位,并能准确地安装各种刃具和适应换刀机械手的夹持等要求。
主要是刀具的长度和直径的选择,如加工孔依据其深度和孔径选择。
表2 刀具选择(5)切削用量的选择该材料,铣削平面、¢60外圆及其台阶面和外轮廓时可留0.5MM 的精加余量,其余一次走完粗铣。
确定主轴转速时,可先查确削用量手册,硬质合金铣刀加工铸铁(190~260HB)时的速度为45~90m/min,取Vc=70m/min,根据铣刀直径和公式计算主轴转速,并填入工序卡片中。
确定进给速度时,根据铣刀齿数、主轴转速、和切削用量手册中给出的每齿进给量,计算进给速度并填入工序卡片中。
拟订数控铣削加工工序卡片如表3。
把零件加工顺序,采用的刀具和切削用量等参数编入数控加工工序卡片中,以指导编程加工操作。
表3 数控加工工序卡片四、要完成的程序编写任务坐标原点:¢40圆的圆心处为工件编程X、Y轴原点坐标,Z轴原点坐标在精铣后的工件上表面。
刀具补偿:刀具补偿号自定。
作业中画出加工工件和坐标系。
(1)编写精铣¢60外圆工序(仅工序5中¢60外圆,台阶不管)加工程序;(2)编写工序6~10加工程序;(3)编写工序12精铣外轮廓加工程序。
五、加工工件和坐标系六、所编写的程序(一).精铣Φ60外圆工序加工程序N5 G92 X0 Y0 Z50;设定工件坐标系N10 G90 G00 Z250 T02 M06;绝对坐标编程,快速运动到换刀点换T02端面立铣刀N15 G43 Z3 H02;快速运动到参考平面进行刀具长度补偿N20 G42 X30.0 Y0 D02;快速运动到外圆轮廓上方进行刀具半径补偿N25 S600 M03;主轴正转N30 G01 Z-18 F100; 进给速度运动到外圆底部N35 G03 X30 Y0 R-30 F100;铣外圆N40 G00 Z50 G40 G49 M05;快速返回初始平面N45 X0;快速返回起始点N50 M30;程序结束(二).工序6~10加工程序N5 G92 X0 Y0 Z50;设定工件坐标系N10 G90 G00 Z250 T03 M06;绝对坐标编程,快速运动到换刀点换T03Φ38钻头N15 G43 Z50 H03;快速运动到初始平面进行刀具长度补偿N20 S400 M03;主轴正转N25 G98 G81 X0 Y0 Z-43 R3 F50;定位钻Φ40底孔返回初始平面N30 M05;主轴停N35 G00 G49 Z250 T04 M06;快速运动到换刀点,取消刀具长度补偿,换T04镗孔刀N40 G43 Z50 H04;快速运动到初始平面进行刀具长度补偿N45 S400 M03;主轴正转N50 G99 G85 X0 Y0 Z-43 R3 F100;粗镗Φ40底孔返回R平面N55 S900; 主轴速度变为900N60 G98 G76 X0 Y0 Z-43 R3 F100;精镗Φ40底孔返回初始平面N65 M05; 主轴停N70 G00 G49 Z250 T05 M06; 快速运动到换刀点,取消刀具长度补偿,换T05Φ13钻头N75 G43 Z50 H05;快速运动到初始平面进行刀具长度补偿N80 S500 M03;主轴正转N85 G98 G81 X60 Y0 Z-43 R-15 F50;定位钻右侧Φ13孔返回初始平面N90 X-60; 定位钻左侧Φ13孔返回初始平面N95 G00 X0 M05;快速返回初始点,主轴停N100 G49 Z250 T06 M06;快速运动到换刀点,取消刀具长度补偿,换T06Φ22锪钻N105 G43 Z50 H06; 快速运动到初始平面进行刀具长度补偿N110 S350 M03;主轴正转N115 G98 G82 X60 Y0 Z-30 R-15 P300 F200; 定位锪右侧Φ22孔返回初始平面N120 X-60; 定位锪左侧Φ22孔返回初始平面N125 G00 X0 M05;快速返回初始点,主轴停N130 G49;取消刀具长度补偿N135 M30;程序结束(三).工序12精铣外轮廓加工程序N5 G92 X0 Y0 Z50.0;设定工件坐标系N10 G90 G00 Z250.0 T7 M06;绝对坐标编程,快速运动到换刀点换T07铣刀N15 G43 Z50 H07;快速运动到初始平面进行刀具长度补偿N20 G42 X67.858 Y18.392 D07;快速运动到加工起始点上方进行刀具半径补偿N25 Z-15;快速运动到Z-15N30 S1200 M03;主轴正转N35 G01 Z-43 F100;进给速度运动到外轮廓底部N40 X11.786 Y47.588;铣右上方直线段N45 G03 X-11.786 R30;逆时针铣上方圆弧N50 G01 X-67.858 Y18.392;铣左上方直线段N55 G03 Y-18.392 R20;逆时针铣左侧圆弧N60 G01 X-11.786 Y-47.588; 铣左下方直线段N65 G03 X11.786 R30; 逆时针铣下方圆弧N70 G01 X67.858 Y18.392;铣右下方直线段N75 G03 Y-18.392 R20; 逆时针铣右侧圆弧N80 G00 Z50.0 M05;快速返回初始平面,主轴停N85 G40 G49 X0 Y0; 快速返回起始点取消刀具半径长度补偿N90 M30; 程序结束第二作业调研报告——数控系统的国内外发展及应用现状一、目的数控系统是数字控制系统简称,英文名称为Numerical Control System,是数控机床的关键技术所在。
早期是由硬件电路构成的称为硬件数控(Hard NC),1970年代以后,硬件电路元件逐步由专用的计算机代替称为计算机数控系统。
计算机数控(Computerized numerical control,简称CNC)系统是用计算机控制加工功能,实现数值控制的系统。
CNC 系统是根据计算机存储器中存储的控制程序,执行部分或全部数值控制功能,并配有接口电路和伺服驱动装置的专用计算机系统。
CNC系统由数控程序输入装置、输出装置、计算机数控装置(CNC装置)、可编程逻辑控制器(PLC)、主轴驱动装置和进给(伺服)驱动装置(包括检测装置)等组成。
CNC系统的核心是CNC装置。
请以课堂所学习的知识为基础,对数控系统的国内外发展及应用现状进行调研,并提交调研报告。
二.工作量与要求1. 对数控系统的发展过程和趋势进行总结;2. 分别对国外和国内各至少两种数控系统进行功能介绍与应用分析;3. 对国内数控系统与国外知名数控系统进行比较,并总结存在的差距;4. 报告需用计算机打印,手工签名,格式请参照本科生毕业论文要求(见教务处网站),总字数不少于5000字。
调研报告——数控系统的国内外发展及应用现状机电工程学院:王新春学号:1110810907摘要:本文对数控系统的发展过程和趋势进行总结;分别对国外和国内的几种数控系统进行功能介绍与应用分析;对国内数控系统与国外知名的数控系统进行比较,并总结存在的差距。
关键词:数控系统,发展过程,应用现状,国内外对比一、引言数控系统是数字控制系统简称,英文名称为Numerical Control System,是数控机床的关键技术所在。
CNC系统是根据计算机存储器中存储的控制程序,执行部分或全部数值控制功能,并配有接口电路和伺服驱动装置的专用计算机系统。
数控机床,简单的说,就是采用了数控技术的机床。
即将机床的各种动作、工件的形状、尺寸以及机床的其他功能用一些数字代码表示,把这些数字代码通过信息载体输入给数控系统,数控系统经过译码、运算以及处理,发出相应的动作指令,自动地控制机床的刀具与工件的相对运动,从而加工出所需要的工件。