华菱涟钢2250生产线工艺介绍
年产280万吨2250热轧带钢生产线设计毕业论文
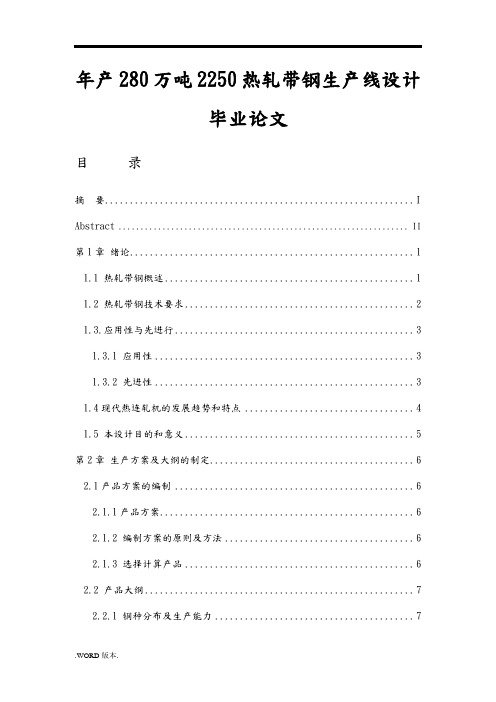
年产280万吨2250热轧带钢生产线设计毕业论文目录摘要 (I)Abstract (II)第1章绪论 (1)1.1 热轧带钢概述 (1)1.2 热轧带钢技术要求 (2)1.3.应用性与先进行 (3)1.3.1 应用性 (3)1.3.2 先进性 (3)1.4现代热连轧机的发展趋势和特点 (4)1.5 本设计目的和意义 (5)第2章生产方案及大纲的制定 (6)2.1产品方案的编制 (6)2.1.1产品方案 (6)2.1.2 编制方案的原则及方法 (6)2.1.3 选择计算产品 (6)2.2 产品大纲 (7)2.2.1 钢种分布及生产能力 (7)2.2.2原料及产品规格 (7)2.3 生产方案 (8)2.3.1 选择生产方案依据 (9)2.3.2 制定生产方案 (9)第3章设计方案 (10)3.1 工艺方案的选择 (10)3.2 主机型式的选择 (12)3.3 轧机数量及相关设备的选择 (13)3.3.1 粗轧机组设备选择 (13)3.3.2 侧压设备的选择 (14)3.3.3精轧机组设备选择 (15)3.4加热炉的选择 (19)第4章生产设备及参数 (21)4.1工艺装备 (21)4.2 主要设备形式及主要技术参数 (22)4.2.1 加热炉 (22)4.2.2粗轧区设备 (22)4.2.3 精轧区设备 (28)4.2.4 卷取机区主要设备 (31)第5章生产工艺流程 (34)5.1生产工艺流程 (34)5.2 生产工艺流程框图 (36)5.3.1 坯料管理制度 (37)5.3.2 加热制度 (37)5.3.3 轧制制度 (39)5.3.4 冷却制度 (40)5.3.5卷曲制度 (41)5.4 车间自动化 (42)第6章轧制工艺参数设计 (45)6.1制定轧制制度的原则和要求 (45)6.1.1在保证设备能力允许的条件下尽量提高产量 (45)6.1.2 在保证操作稳便的条件下提高质量 (46)6.1.3 道次选择确定 (47)6.2 粗轧压下规程 (47)6.2.1 粗轧压下制度 (47)6.2.2粗轧速度制度 (48)6.2.3 粗轧温度制度 (50)6.3 精轧压下规程 (51)6.3.1 精轧压下制度 (51)6.3.2 精轧速度制度 (52)6.3.3 精轧轧制时间和周期的确定 (53)6.3.4 精轧温度制度 (55)6.4 轧制图表 (56)6.6 各道次变形抗力 (57)6.7 计算各道的传动力矩 (59)6.8 轧辊辊缝和转速的设定 (61)第7章电机轧辊的强度校核 (63)7.1静负荷图 (63)7.2 等效力矩计算及电动机的校核 (64)7.3 电动机功率的计算 (65)7.4 轧辊强度校核 (66)7.4.1 支承辊弯曲强度校核 (66)7.4.2 工作辊的扭转强度校核 (68)第8章轧钢机产量计算 (70)8.1 轧机小时产量计算 (70)8.2 轧机平均小时产量计算 (71)8.3.轧钢车间年产量计算 (71)第9章厚度控制方式 (73)9.1 预控AGC系统 (74)9.2间接测厚反馈闭环控制系统 (75)第10章辊型与板形控制 (76)10.1 板型控制理论 (76)10.2 板形设定模型 (78)10.3 影响辊缝形状的因素 (80)10.3.1 轧辊热膨胀对辊缝的影响 (80)10.3.2 轧辊的磨损对辊缝的影响 (81)10.3.3 原始辊型对辊缝的影响 (81)10.3.4 入口板凸度对辊缝的影响 (81)10.4 轧辊凸度计算 (82)10.5 轧辊的磨损的确定 (85)10.6 初始加工辊型确定 (86)10.7 静态凸度计算 (86)10.8 轧辊辊型设计 (87)10.9 弯辊装置 (87)10.9.1 弯曲工作辊 (87)10.9.2 弯曲支撑辊 (88)第11章车间平面设计 (89)11.1平面布置的原则 (89)11.2 金属流程线的确定 (89)11.3仓库面积的确定 (90)11.3.1确定仓库面积的原则 (90)11.3.2原料仓库面积的确定 (90)11.3.3成品仓库面积的确定 (90)第12章环境保护 (92)12.1环境保护概述 (92)12.2环境保护的容与对策 (92)12.2.1绿化 (92)12.2.2水质处理 (92)12.2.3噪音防治 (93)12.2.4大气污染的防治 (93)12.2.5有害废弃物的处理 (93)12.2.6车间的综合利用 (93)结论 (95)参考文献 (96)谢辞 (98)第1章绪论1.1 热轧带钢概述热轧宽带钢是国民经济的重要物资,是制造其他薄板类钢铁产品的重要原料, 主要作为冷轧板、焊管、冷弯或焊接型钢的原料或直接用于制作各种结构件、容器、汽车、造船、集装箱等。
2250产线知识

●高炉炼铁高炉生产时从炉顶装入铁矿石、焦炭、造渣用熔剂(石灰石),从位于炉子下部沿炉周的风口吹入经预热的空气。
在高温下焦炭(有的高炉也喷吹煤粉、重油、天然气等辅助燃料)中的碳同鼓入空气中的氧燃烧生成的一氧化碳和氢气,在炉内上升过程中除去铁矿石中的氧,从而还原得到铁。
炼出的铁水从铁口放出。
铁矿石中未还原的杂质和石灰石等熔剂结合生成炉渣,从渣口排出。
产生的煤气从炉顶排出,经除尘后,作为热风炉、加热炉、焦炉、锅炉等的燃料。
高炉冶炼的主要产品是生铁,还有副产高炉渣和高炉煤气。
●转炉炼钢转炉炼钢(converter steelmaking)是以铁水、废钢、铁合金为主要原料,不借助外加能源,靠铁液本身的物理热和铁液组分间化学反应产生热量而在转炉中完成炼钢过程。
转炉按耐火材料分为酸性和碱性,按气体吹入炉内的部位有顶吹、底吹和侧吹;按气体种类为分空气转炉和氧气转炉。
碱性氧气顶吹和顶底复吹转炉由于其生产速度快、产量大,单炉产量高、成本低、投资少,为目前使用最普遍的炼钢设备。
转炉主要用于生产碳钢、合金钢及铜和镍的冶炼。
●炼铁2座4150 m3高炉,高炉利用系数2.2 t/m3.d卡鲁金顶燃式热风炉系统无钟炉顶装料系统【高炉利用系数是衡量高炉炼铁生产率的一项重要技术经济指标。
利用系数值越高,表示高炉生产率越高。
在中国以每立方米高炉有效容积1昼夜的合格生铁产量表示,计算式如下:利用系数=高炉日产量/高炉容积ηV=P/V式中ηV为高炉利用系数,t/(m3·d);P为高炉1昼夜生铁产量,t;V为高炉有效容积,m 。
d为1天】●铁水预处理3 套KR法脱硫装置[S ]含量≤50 ppm (ppm是浓度单位(百万分之一))如果ppm换算成百分号“%”为:1ppm=0.0001%【KR法最早是由日本1965年开发的,它是将浇注耐火材料并经过烘烤的十字形搅拌头,浸入铁水包熔池一定深度,利用在大型搅拌器激烈搅拌作用下产生的漩涡,使氧化钙或碳化钙基脱硫粉剂与铁水充分接触反应,达到脱硫目的。
涟钢炼钢、轧制生产工艺流程

四辊粗轧机
用途:与E立辊轧机一起经 5-7道次轧制。 型式:四辊可逆。 轧制压力:55000 KN 主电机功率:11000KW 轧制速度:0-3.25-6.5 m/s 最大压下量:50 mm 压下速度:0-40 mm/s 压下方式:电动APC+液压 HGC 工作辊尺寸: Ф1250/Ф1150×2250 mm 工作辊材质:高鉻钢 工作辊磨辊:可带箱磨辊
●钢板(或板带钢)按轧制温度分为热轧钢板和冷轧钢板;
按用途分为桥梁板、锅炉板、造船板、汽车板、电工板 ●钢板是应用最为广泛的钢材之一,用厚×宽来表示。
0.2~3mm的钢板称为薄板,热轧薄板(包括带钢)在工 业发达国家中已占钢板总量的80%左右,占钢材总产量 的50%以上,因而在现代轧钢生产中占有重要地位。
6、板材认证
序号 1 认证产品 管线钢 牌号 认证机构
X80及X80以下 国家质检总局 HP295 HP325 LGNS1
2 3
气瓶钢 耐硫酸露点腐蚀钢
国家质检总局 中国烟草总公司
4
船板用钢
A、B级
CCS
5
火车车厢板
09CuPCrNiA Q450NQR1
■ 型钢可分为大型材、中型材和小型材等。 接和镀层等钢材; 低合金钢等等;
■ 根据加工方式分为热轧材、冷轧、冷拔、 锻压、焊
■ 根据钢的材质或性能分为:优质钢、普通钢、合金钢、
■ 根据钢材的用途分为:造船板、锅炉板、油井管、油
气输送管、电工用钢等等。
三) 轧制的基本概念 ●轧钢是利用金属的塑性使金属在两个旋转的轧辊之间 受到压缩产生塑性变形,从而得到具有一定形状、尺寸和 性能的钢材的加工过程。 ●被轧制的金属叫轧件;使轧件实现塑性变形的机械设 备叫轧钢机;轧制后的成品叫钢材。 ●经加工变形后的金属中,随着温度的增加,其晶体组 织有出现重新改组为新晶粒的现象,称为金属的再结晶。 ●金属进行再结晶的最低温度称为金属的再结晶温度。 T再=(0.35-0.40)TM TM:金属的熔点,以绝对温度K表示。
热处理双炉生产回火板的生产实践

涟钢科技与管理 2018年第1期·9·热处理双炉生产回火板的生产实践刘鹏晗(涟钢2250热轧板厂)摘 要 针对热处理现有产能不能满足市场需求的状况,本文从目前现有设备条件出发,在不增加投入的情况下,通过工艺优化、设备改进,实现了淬火炉改为回火炉,与现有的回火炉进行双炉生产回火板,大幅度提高了热处理线产能。
关键词 热处理 回火板 产能 工艺优化从2017年初起国内工程机械行业逐渐呈现爆发式的增长,公司接到的热处理产品订单也随之激增。
作为公司一条重要的高品质钢铁材料生产线,热处理产品订单的按期交付不仅是创造效益最大化的需要,更是关系着后续客户的合作。
本文在现有生产条件基础上,提出利用淬火炉改为回火炉进行回火生产,实现两座热处理炉同时进行回火的工艺,大幅度提高了热处理线产能,为国内主流工程机械制造商客户的产品需求提供了强有力的保障,也为进一步提高工程机械用钢市场占有率打下坚实的基础。
1 热处理线现有工艺条件涟钢2250热轧板板厂横切热处理车间热处理线目前有两座热处理炉。
1#热处理生产线为辐射管加热辊底式热处理炉+淬火机处理线,负责钢板的淬火、正火处理;2#热处理生产线为明火加热辊底式热处理炉处理线,负责钢板的回火处理。
2座热处理炉的工艺参数见表1、表2,工艺流程见图1。
表1 1#热处理炉参数入炉温度 淬火温度/℃ 正火处理温度/℃ 最高炉温/℃常温冷装800~980890~9201000表2 2#热处理炉参数入炉温度 回火处理温度/℃最高炉温/℃常温冷装150~7308002 工艺实践原设计两座热处理炉共用一条炉后收集线,且1#炉只能用于钢板的淬火、正火热处理,在生产高强钢回火板时1#炉停炉,只用2#炉进行生产。
新工艺采用同一母卷的原料钢板两座热处理炉交替入炉,出炉后交替汇合进入2#冷床,再经冷矫、取样、喷印、堆垛、打包、下线。
图1 热处理生产工艺流程图2.1 存在的主要问题a. 工序耗时不匹配。
涟钢炼钢、轧制生产工艺流程

涟钢炼钢、轧制生产工艺流程
七机架精轧机组具有 自动宽度控制、自动厚 度控制、自动平直度控 制、凸度控制技术,辊 缝润滑系统,可使带钢 尺寸精度达到国际先进 水平。
涟钢炼钢、轧制生产工艺流程
冷轧辊
涟钢炼钢、轧制生产工艺流程
五、涟钢概况与主要产品
一)、涟钢概况
中南地区重要精 品板材基地。
1、在华菱的布局
涟钢
湘钢
以专用板为主导的宽厚板。 以工业加工用材为主导的 线、棒材。
衡钢
涟钢炼钢、轧制生产工艺流程
系全球大型无缝钢管 生产企业,中国第二 大专业化无缝钢管生 产企业。
涟钢炼钢、轧制生产工艺流程
层流冷却
用途: 控制冷却速度,保证卷取
温度以确保产品质量和性能。
冷却带钢厚度: 1.2~25.4 mm
冷却带钢宽度:900~2130 mm
终轧温度: 870~900℃
卷取温度: 200~800℃
冷却水温度:
35℃
冷却段长度:超快冷段:9.12m
常规段:94.62 mm
冷却组数:
T403- 2超
HMD4-2 T404-2超 T405-2超
1 2 3 4 5 6 7 8 9 10 11 12 13 14 15
16 17 18
:超超超超超超
:超超超超超超 :超超超超超超
:超超超超超超超超超超 :超超超超 :超超
:超超超超 :超超超
图 1 轧后冷却系统设备布置图
涟钢炼钢、轧制生产工艺流程
2250线热轧酸洗板质量问题及解决措施
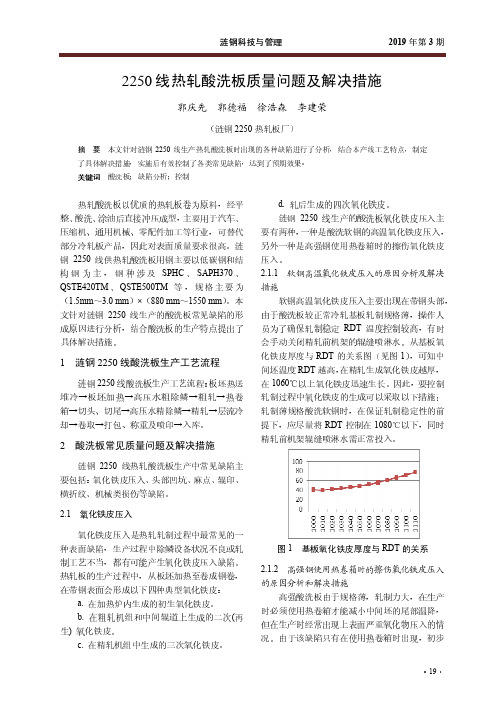
高强酸洗板由于规格薄,轧制力大,在生产 时必须使用热卷箱才能减小中间坯的尾部温降, 但在生产时经常出现上表面严重氧化物压入的情 况。由于该缺陷只有在使用热卷箱时出现 ,初步
··
2019 年第 3 期
氧化铁皮压入是热轧轧制过程中最常见的一 种表面缺陷,生产过程中除鳞设备状况不良或轧 制工艺不当,都有可能产生氧化铁皮压入缺陷。 热轧板的生产过程中,从板坯加热至卷成钢卷, 在带钢表面会形成以下四种典型氧化铁皮:
a. 在加热炉内生成的初生氧化铁皮。 b. 在粗轧机组和中间辊道上生成的二次(再 生) 氧化铁皮。 c. 在精轧机组中生成的三次氧化铁皮。
LYS Science-Technology& Management
判断该缺陷是中间坯在热卷箱卷取过程中带钢表 压入带钢表面所致。选取有凹坑缺陷的试样进行
面与辊道或花架等接触,辊子表面磨损或粘钢后 扫描电镜观察(见图3),另选取机架框架上的结垢
压印到中间坯表面,精除鳞无法去除,经精轧机 物进行能谱分析(见图4),发现凹坑中成分(见表
轧制形成这种擦伤性氧化铁皮压入的缺陷。现场 1)与机架上的结垢物成分(见表2)一致。
检查也发现热卷箱弯曲辊辊面状况较差,确实存 措施 2.2.2
在粘钢情况。
a. 加强机架间的清理工作,一般在生产酸洗
为减少这种擦伤氧化铁皮压入造成的缺陷, 板前或者利用检修停机时间进行轧机机架的清理,
在每次生产前应检查弯曲辊辊面情况,若有异常 彻底去除机架框架上的氧化铁皮结垢。
动导致粘接在设备上的积灰或氧化物结垢掉落到 带钢表面,经轧制后压入带钢表面产生的。反查 表检系统可以发现大多数异物压入位置在带头 20 m左右,严重的还有周期性,周期在2.4m左右, 因此判定头部凹坑是精轧后机架上的异物掉落后
涟钢横切热处理线工艺及设备简介

上辊采用弯辊装置以补偿机械变形和改善板材的中 浪和边浪。
根据板厚和材料强度,下辊可以单独调整以改变辊 缝间隙。
技术参数:
矫直辊数量:
11个
矫直力:
24000KN
(7)冲印机
技术参数: 字符: 字符模式:
可自选 字符高度: 字符宽度: 行数: 字符个数: 冲孔深度:
点径: 冲头硬度:
英文(A~Z)、阿拉伯数字(0~9)及特殊符号 7x5点阵和9x7点阵,使用中
涟钢横切热处理线工艺 及设备简介
2011年5月
主要内容
一、横切线工艺及其设备简介 1、横切线产品概述 2、横切线工艺流程概述 3、横切线主要设备简介 二、热处理线工艺及其设备简介 1、热处理线产品概述 2、热处理线工艺流程 3、热处理线主要设备简介 三、热处理基本原理
一、横切线工艺及其设备简介
1、横切线产品概述
•
横切生产线为涟钢2250热轧板厂的一条产品
深加工生产线,其作用是将2250热轧板厂的成品
钢卷加工成板材,设计生产规模为年产50万吨横
切板。
1.1生产钢种
生产品种主要有碳素结构钢、优质碳素结构钢 、低合金结构钢、高强度结构钢、工程机械用钢 、耐磨钢、建筑结构用钢、汽车大梁用钢、桥梁 用结构钢、压力容器及锅炉用钢、船体用结构钢 等。
7) 飞剪剪切
用飞剪前的夹送辊装置将带钢喂入飞剪,正常剪切时飞剪 先切除带钢头部进行零位记忆,再以生产速度连续将带钢 切成定尺成品板。
8) 精矫直
飞剪剪成的定尺钢板用精矫直机进行矫直,根据矫直机出 口摄像头监视的板形情况调节矫直机辊缝或弯辊。
9) 喷印、冲印及检查
对常规钢板进行喷印,对特殊要求的钢板(如船板、压力 容器板等)进行喷印+冲印。在检查台处对更换矫直辊后 的首卷、同一炉号或单个轧制计划的首卷进行表面检查。 根据检查情况判定当前钢板的物流去向并在机旁进行物流 去向操作。
2250工艺知识简介(轧线-郁盛富)

涟钢2250mm热轧项目介绍
粗轧区域成本相关
时间成本计算方法:10s*2*本月增加道次板坯数*1.5(加权系数)*每秒吨钢产 量*100元/吨利润*有效作业率=24* 0.1583*67.7%*本月增加道次板坯数=75*本 月增加道次板坯数 电耗成本计算方法:10s*2*本月增加道次板坯数*1.5(加权系数)*每秒吨钢 产量*56.65元/吨=30* 0.1583*56.65*本月增加道次板坯数=269.2468*本月增 加道次板坯数
涟钢2250mm热轧项目介绍
平直度仪
我厂平直度仪采用 IRM公司产品,测量臂上共 有9条测量线(3条固定在 中央区域,其他6条分为两 组,每组各三条,其位臵 可随板带的宽度设定调整) 非常快速的(0.3秒)边部 跟踪,能够自动实现辊道 横向上的激光三角形,对 应产品宽度变化调整位臵。
摄像头
射线
涟钢2250mm热轧项目介绍
涟钢2250mm热轧项目介绍
工作辊窜辊和弯 辊装置 高精度液压活套 入出口导卫 上止推块和下阶 梯垫 可分段控制工作 辊冷却水 辊缝喷淋水、烟 尘抑制水 带钢侧喷水、机 架间冷却水
辊缝润滑系统
涟钢2250mm热轧项目介绍
多功能仪
在精轧机F7出口, 安装有多功能仪,它能 即时和连续地测量中心 线、横截面厚度、温度、 剖面、宽度、 边缘降 和热轧出口时的板型。 从测量得到的一系列过 程控制和质量保证数据 有 助于操作者提高操 作质量,从而提高轧 机的生产效率。
热轧钢卷库
直发卷 平整分卷线 热剪 热处理 横切线 至冷轧
外发
涟钢2250mm热轧项目介绍
主线介绍
涟钢2250mm热轧项目介绍
蓄热式步进炉
2250MM热轧建设的2 座蓄热式加热炉主要参 数如下:有效长 度:59000 MM;炉膛内 宽:11700 MM;单炉 冷坯加热能力390T/H (热坯425T/H);装 出料辊道中心距: 66000MM
- 1、下载文档前请自行甄别文档内容的完整性,平台不提供额外的编辑、内容补充、找答案等附加服务。
- 2、"仅部分预览"的文档,不可在线预览部分如存在完整性等问题,可反馈申请退款(可完整预览的文档不适用该条件!)。
- 3、如文档侵犯您的权益,请联系客服反馈,我们会尽快为您处理(人工客服工作时间:9:00-18:30)。
HSM工艺技术与装备
立辊轧机E
•轧辊尺寸: Ф1200/Ф1100 mm×650 mm •最大单面侧压量:50 mm •轧制压力: 6000 KN •主传动电机:AC 2×1500 Kw •电机转速: 0~160~400 r/min •速比: 3.865 •设有自动宽度控制系统(长行程
粗除鳞机 •喷嘴前水压:≥20 MPa •上下方均设有除鳞喷嘴,共 二组
HSM工艺技术与装备
精轧机组
•F1~F7机架设全液压AGC控制带钢全长的厚度精度 • 精轧机组设有带工作辊弯辊的板形控制系统和工作辊 窜辊装置。 • 精轧机机架间采用液压活套进行速度和张力控制 • 设置轧制工艺润滑系统,以降低轧制压力、延长轧辊 寿命、提高带钢表面质量 •采用塑烧板式除尘
HSM工艺技术与装备
2250热轧板生产线 工艺介绍
2010年11月
2250热轧板厂位于涟钢西北部, 建于原棒材一厂厂址 厂区占地面积29.3万m2 总建筑面积16.16万m2
2250热轧板厂工厂效果图
HSM工艺技术与装备
工艺平面布置图
HSM产品大纲
生产规模
钢卷年产量 441万吨 板坯年需量 450万吨 横切中板50 万吨 热处理中板 15万吨 热轧综合成 材率98%
产品品种
碳素结构钢 低合金高强钢 IF钢 高耐候结构钢 管线用钢 热轧双相钢 中高牌号无取 向硅钢、取向硅 钢
HSM产品大纲
年产量品种分配图(×10000t)
压力容器及锅炉用 钢, 13 热轧多相钢DP, 9 船用钢, 18 桥梁用结构钢, 18 焊接气瓶用钢, 18 耐候钢, 18 高耐候结构钢, 18 汽车大梁用钢, 18 中高牌号无取向硅 钢, 20 管线钢, 29 低合金结构钢, 57 超低碳钢IF, 62 优碳结构钢, 88
HSM工艺技术与装备
加热炉 •空气蓄热煤气预热步进梁式加热炉 •加热炉有效炉长为58.9m,炉膛内 宽11.7m •采用高、焦、转混合煤气,煤气热 值为6500~8500kJ/Nm3 , •采用最佳化燃烧控制模型 •板坯加热温度1100~ 1250℃ •小时加热能力370 ~ 400t/h(冷坯) •单位燃耗 290×4.18 kJ/kg •降低燃耗,减少NOx生成
剪切带坯断面:50×2130mm (X70) 剪切温度:≥ 900℃ 剪切力:14700KN 剪切带坯速度:0.5~2.2 m/s 剪刃布置型式:双剪刃90º ,直 剪刃 转鼓中心距:1280 mm 切头长度:≤500 mm 主传动减速机速比:1ห้องสมุดไป่ตู้.56 主传动电机:AC2 x 1600 Kw 600 r/min 具有优化剪切功能
卷板
带钢厚度: 带钢宽度: 钢卷内径: 钢卷外径: 钢卷质量: 单位宽度质量: 1.2~25.4mm 900~2130 mm 762 mm max.2100mm max.38t max.22kg/mm
4.0~25.4 mm 850~2130 mm 2000~16000 mm
min.1200mm
精轧除鳞机 喷嘴前水压: ≥20MPa 前后带夹送辊设有二 组除鳞喷嘴
HSM工艺技术与装备
精轧机组
•型式: 四辊不可逆式HCW轧机 •最大轧制力:F1━F4:50000 KN, F5━F7: 40000 KN •最大开口度:70 mm (最大辊径时) •工作辊直径:F1━F4:Ф850/Ф760 mm,F5━F7:Ф700/Ф630 mm •工作辊辊身长度:F1━F4:2550 mm,F5━F7:2550 mm •支承辊直径: Ф1600/Ф1450 mm •支承辊辊身长度:2250 mm •压下液压缸(HGC)行程:100mm •弯辊力(单侧) :F1━F4:2000 KN,F5━F7:1500 KN •弯辊缸行程:上辊165 mm,下辊85 mm •窜辊行程:320 mm •主传动电机:F1━F5:AC10000 Kw 150/450 r/min, •F6 ━F7:AC10000 Kw 200/600 r/min •I1 4.217,i2 3.26,i3 2.52,i4 1.75,i5 i6 i7 1 •F7出口速度: 22 m/s,最高轧制速度:18 m/s
HSM工艺技术与装备
工艺流程
7机架精轧机组 层流冷却 精轧前除鳞机 卷取机 热卷箱 四辊粗轧机 粗轧除鳞机 蓄热式步进炉 快速冷却装置 夹送辊 精轧前立轧机 切头飞剪 预留保温罩 立辊轧机 预留硅钢炉
HSM工艺技术与装备
板坯库
•与连铸相邻布 置,采用辊道输 送直接热装 (DHCR) 约 占 40% 板坯入 炉温度≥700℃, 实现工艺节能。 •布置具有加热 功能的保温坑, 满足硅钢生产要 求。
碳结钢, 57
HSM产品大纲
横切线产品品种分配
钢种 碳素结构钢 优质碳素结构钢 低合金结构钢 低合金高强度结构钢板 工程机械用钢板 耐磨钢板 建筑结构用钢板 汽车大梁用钢 桥梁用结构钢 压力容器及锅炉用钢 船体用结构钢 管线钢 总计 Q195 Q275 08、08Al、10~45、65Mn Q345 Q460 Q500D/E、Q550D/E、Q620D/E、Q690D/E A681、StE460、HITEN540SA~780LE等 NM360、NM400等 Q460GJ C/D/E 16MnL、16MnReL、10TiL、LG510L Q235q、Q345q 16Mng、20Mng、20g、09MnNiDR13、 12MnNiVR、15CrMoR、12CrMoVg、15CrMog A、B、D、A32、A36 S290~S555 代表钢号 年产量(104t/a) 5 5 12 9 6 1 0.8 3 1 1.2 5 1 50
AWC)和短行程控制(SSC)功能
HSM工艺技术与装备
四辊可逆粗轧机R
•工作辊:Ф1250/1150×2250 mm •支撑辊:Ф 1650/1500×2230 mm •压下系统:电动压下,配置上置式液压HGC •轧制压力:50000 KN (max) •中间坯厚度:35~60 mm •轧制速度: 0~3.25~6.5m/s •传动电机功率:AC2×11000 Kw •电机转速:0~50~100 r/min •R粗轧前测宽,R粗轧后测宽测厚 •与立辊采用微张力控制 •设辊缝仪、测压仪 •前后设除鳞装置
HSM工艺技术与装备
卷取机
•型式:固定式三助卷辊踏 步控制的全液压卷取机 •卷取带钢厚度:1.2~25.4 mm •卷取带钢宽度:900~2130 mm •卷取带钢温度:max800℃ Min200℃ •卷筒传动电机:AC1350 Kw 230/600 r/min
HSM电气系统
主传动
采用交-直-交变频调速系统,全数字矢量控制,实现高精度、高速度控制功能
自动化控制
采用四级系统实现生产自动化和企业管理的全流程控制。 1)基础自动化系统(L1级) 主要完成设备的顺序控制、自动位置控制、速度控制、液压控制、板/卷的温度、 厚度、宽度、板形控制,加热炉热工参数控制,各种操作界面和数据采集等任务。 2)过程自动化系统(L2级) 主要完成材料跟踪,过程控制参数设定计算、自适应控制、质量数据收集与分析, 以及操作指导等任务。 3)生产制造执行系统(MES) 主要完成全厂物料跟踪、三库(板坯库、钢卷库和成品库)管理、质量管理、发 货管理、磨辊管理、轧制计划的编制、调整和发行,生产实绩数据的收集、处理, 以及统计分析报告等任务。 4)企业资源计划管理系统(ERP) 主要完成经营决策、采购管理、销售管理、财务管理、人力资源管理、生产计划 编制协调、材料申请、将作业计划下发给L3级、并收集L3级的生产实绩,跟踪生产 和质量情况,以及组织成品出厂发货等任务。
宽度,mm
HSM产品大纲
产品厚度分配表 产量,万吨
120 100 80 60 40 20 0
1.2- 2.1- 2.4- 3.1- 3.6- 4.1- 5.1- 7.1- 12.7- 16.02.0 2.3 3.0 3.5 4.0 5.0 7.0 12.7 16.0 25.4
92.61
103.64 70.56
HSM产品大纲
热处理线产品品种
重要品种包括: 工程机械用钢板 低合金高强度结构钢板 耐磨板 压力容器及锅炉板 碳素结构钢板 优质碳素结构钢 桥梁板及高层建筑结构钢板 等
热处理工艺包括: 调质钢板:3万t 正火钢板:8万t 回火钢板:3万t 正火+回火钢板:1万t 合计:15万t
HSM产品大纲
产品规格
HSM工艺技术与装备
F1E立辊轧机
•型式: 吸附型、上传动式 (不可逆) •轧制压力:Max 1500 KN •单侧压下量:Max 5 mm (坯 厚60 mm时) •辊身直径:Ф630/Ф570 mm •辊身长度:350 mm •开口度: 880 ~2250 mm •主传动电机:AC370 Kw 200/500 r/min 2台 •与水平辊采用微张力控制 •左、右主传动电器同步,左、 右侧压下液压同步
39.69 13.23
46.31 37.49 19.85 11.03 6.62
厚度,mm
HSM工艺技术与装备
涟钢2250mm热轧项目采用自主设计、自主集成 建设模式,由国内技术总负责,只引进国内部分 关键技术和关键设备,其它均由国内配套。具有 装备先进、节省投资、缩短工期、满足较高产品 质量要求的特点。 设计单位:中冶赛迪 主轧设备制造商:中国一重 电气设备供应商:TMEIC 加热炉制造商:赛迪工业炉 层轧后冷却系统:东北大学RAL 横切机组及热处理:正在技术谈判中
Sensor symbols Load cell Pyrometer
PT
Pressure Transducer
X P
- Thickness gage - Profile gage - Width gage
F
- Flatness meter
•F7轧机后及卷取机前分别设上下表面质量质量检测仪