齿轮几何参数设计计算
齿轮几 何尺寸计算

பைடு நூலகம்a=m(z1+z2)/2
5 齿数比: u=z2/z1
举例分析:
已知标准直齿圆柱齿轮的齿数为z=40,测得其齿根圆 直径df=75mm。试求: (1)齿距p; (2)全齿高h; (3)分度圆直径d,齿顶圆直径da。 解:df=m(z-2.5) m=df/(z-2.5)=75/(40-2.5)=2mm (1)p=πm=3.14X2=6.28mm (2)h=2.25m=2.25X2=4.5mm (3)d=mz=2X40=80mm da=m(z+2)=2X(40+2)=84mm
新授知识:
三、外啮合标准直齿圆柱齿轮的几何尺寸计算
1、四圆的直径: d =mz da=m(z+2)
df=m(z-2.5) db=dcos20º
2、三高的计算:
ha=m
hf=1.25m h=ha+hf=2.25m
3、三弧的长度:
p=πm
e=s=p/2
4、一对标准直齿圆柱齿轮的中心距: a=d1/2+d2/2
学生练习:
有一对正常齿制的标准直齿圆柱齿轮,测得大 齿轮的齿根圆直径df2=123.75mm,大齿轮的 齿数z2=52,两轮孔中心距a=112.5mm,试 求新配的小齿轮齿数z1。 解:由df=m(z2-2.5)=123.75 → m=2.5mm a=m(z1+z2)/2=112.5 → z1=38
《机
械
胡 尧
基
础》
复习提问:
1、直齿圆柱齿轮:四圆。 2、直齿圆柱齿轮:三高。 3、直齿圆柱齿轮分度圆上的三个弧长。 4、直齿圆柱齿轮的基本参数。
教学内容:
外啮合标准直齿圆柱齿轮的几何尺寸计算
渐开线标准直齿轮几何尺寸计算公式
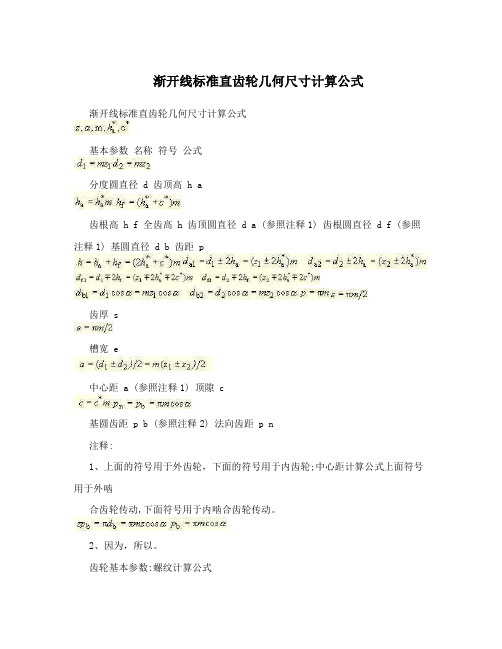
渐开线标准直齿轮几何尺寸计算公式渐开线标准直齿轮几何尺寸计算公式基本参数名称符号公式分度圆直径 d 齿顶高 h a齿根高 h f 全齿高 h 齿顶圆直径 d a (参照注释1) 齿根圆直径 d f (参照注释1) 基圆直径 d b 齿距 p齿厚 s槽宽 e中心距 a (参照注释1) 顶隙 c基圆齿距 p b (参照注释2) 法向齿距 p n注释:1、上面的符号用于外齿轮,下面的符号用于内齿轮;中心距计算公式上面符号用于外啮合齿轮传动,下面符号用于内啮合齿轮传动。
2、因为,所以。
齿轮基本参数:螺纹计算公式1、齿数Z闭式齿轮传动一般转速较高,为了提高传动的平稳性,减小冲击振动,以齿数多一些为好,小一些为好,小齿轮的齿数可取为z1=20~40。
开式(半开式)齿轮传动,由于轮齿主要为磨损失效,为使齿轮不致过小,故小齿轮不亦选用过多的齿数,一般可取z1=17~20。
为使齿轮免于根切,对于α=20o的标准支持圆柱齿轮,应取z1?17。
Z2=u?z1。
2、压力角α rb=rcosα=1/2mzcosα在两齿轮节圆相切点P处,两齿廓曲线的公法线(即齿廓的受力方向)与两节圆的公切线(即P点处的瞬时运动方向)所夹的锐角称为压力角,也称啮合角。
对单个齿轮即为齿形角。
标准齿轮的压力角一般为20”。
在某些场合也有采用α,14.5? 、15? 、22.50?及25?等情况。
3、模数m=p/ π齿轮的分度圆是设计、计算齿轮各部分尺寸的基准,而齿轮分度圆的周长,πd,z p模数m是决定齿轮尺寸的一个基本参数。
齿数相同的齿轮模数大,则其尺寸也大。
4、齿顶高系数和顶隙系数—h*a 、C*两齿轮啮合时,总是一个齿轮的齿顶进入另一个齿轮的齿根,为了防止热膨胀顶死和具有储成润滑油的空间,要求齿根高大于齿顶高。
为次引入了齿顶高系数和顶隙系数。
正常齿:h*a =1; C*=0.25 短齿:h*a =0.8; C*=0.3一般的直齿圆柱齿轮,啮合的条件是:模数相等,压力角相等一、 60?牙型的外螺纹中径计算及公差(国标GB 197/196)a. 中径基本尺寸计算:螺纹中径的基本尺寸=螺纹大径-螺距×系数值公式表示:d/D-P×0.6495例:外螺纹M8螺纹中径的计算8-1.25×0.6495=8-0.8119?7.188b.常用的6h外螺纹中径公差(以螺距为基准)上限值为”0”下限值为P0.8-0.095 P1.00-0.112 P1.25-0.118 P1.5-0.132 P1.75-0.150 P2.0-0.16 P2.5-0.17上限计算公式即基本尺寸,下限值计算公式d2-hes-Td2即中径基本尺寸-偏差-公差M8的6h级中径公差值:上限值7.188 下限值:7.188-0.118=7.07C常用的6g级外螺纹中径基本偏差: (以螺距为基准)P 0.80-0.024 P 1.00-0.026 P1.25-0.028 P1.5-0.032P1.75-0.034 P2-0.038 P2.5-0.042 上限值计算公式d2-ges即基本尺寸-偏差下限值计算公式d2-ges-Td2即基本尺寸-偏差-公差例M8的6g级中径公差值:上限值7.188-0.028=7.16下限值:7.188-0.028-0.118=7.042 注:?以上的螺纹公差是以粗牙为准,对细牙的螺纹公差相应有些变化,但均只是公差变大,所以按此控制不会越出规范界限,故在上述中未一一标出.?螺纹的光杆坯径尺寸在生产实际中根据设计要求的精度和螺纹加工设备的挤压力的不同而相应比设计螺纹中径尺寸加大0.04—0.08之间,为螺纹光杆坯径值,例我们公司的M8外螺纹6g级的螺纹光杆坯径实在7.08—7.13即在此范围.?考虑到生产过程的需要外螺纹在实际生产的未进行热处理和表面处理的中径控制下限应尽量保持在6h级为准二、 60?内螺纹中径计算及公差(GB 197 /196)a. 6H级螺纹中径公差(以螺距为基准)上限值:P0.8+0.125 P1.00+0.150 P1.25+0.16 P1.5+0.180P1.25+0.00 P2.0+0.212 P2.5+0.224 下限值为”0”,上限值计算公式2+TD2即基本尺寸+公差例:M8-6H内螺纹中径为:7.188+0.160=7.348 上限值:7.188为下限值b. 内螺纹的中径基本尺寸计算公式与外螺纹相同即D2=D-P×0.6495即内螺纹中径螺纹大径-螺距×系数值c. 6G级螺纹中径基本偏差E1(以螺距为基准)P0.8+0.024 P1.00+0.026 P1.25+0.028 P1.5+0.032P1.75+0.034 P1.00+0.026 P2.5+0.042例:M8 6G级内螺纹中径上限值:7.188+0.026+0.16=7.374下限值:7.188+0.026=7.214上限值公式2+GE1+TD2即中径基本尺寸+偏差+公差下限值公式2+GE1即中径尺寸+偏差三、外螺纹大径的计算及公差(GB 197/196)a. 外螺纹的6h大径上限值即螺纹直径值例M8为φ8.00上限值公差为”0”b. 外螺纹的6h级大径下限值公差(以螺距为基准)P0.8-0.15 P1.00-0.18 P1.25-0.212 P1.5-0.236 P1.75-0.265P2.0-0.28 P2.5-0.335大径下限计算公式:d-Td 即螺纹大径基本尺寸-公差例:M8外螺纹6h大径尺寸:上限为φ8,下限为φ8-0.212=φ7.788c. 外螺纹6g级大径的计算与公差6g级外螺纹的基准偏差(以螺距为基准)P0.8-0.024 P1.00-0.026 P1.25-0.028 P1.5-0.032 P1.25-0.024 P1.75 –0.034 P2.0-0.038 P2.5-0.042上限计算公式 d-ges 即螺纹大径基本尺寸-基准偏差下限计算公式 d-ges,Td 即螺纹大径基本尺寸-基准偏差-公差例: M8 外螺纹6g级大径上限值φ8-0.028=φ7.972下限值φ8-0.028-0.212=φ7.76注:?螺纹的大径是由螺纹光杆坯径及搓丝板/滚丝轮的牙型磨损程度来决定的,而且其数值在同样毛坯及螺纹加工工具的基础上与螺纹中径成反比出现即中径小则大径大,反之中径大则大径小.?对需进行热处理和表面处理等加工的零件,考虑到加工过程的关系实际生产时应将螺纹大径控制在6h级的下限值加0.04mm以上,如M8的外螺纹在搓(滚)丝的大径应保证在φ7.83以上和7.95以下为宜.四、内螺纹小径的计算与公差a. 内螺纹小径的基本尺寸计算(D1)径基本尺寸=内螺纹基本尺寸-螺距×系数例:内螺纹M8的小径基本尺寸 8-1.25×1.0825=6.646875?6.647b. 内螺纹6H级的小径公差(以螺距为基准)及小径值计算P0.8 +0. 2 P1.0 +0. 236 P1.25 +0.265 P1.5 +0.3 P1.75 +0.335P2.0 +0.375 P2.5 +0.48内螺纹6H级的下限偏差公式D1+HE1即内螺纹小径基本尺寸+偏差注:6H级的下偏值为“0”内螺纹6H级的上限值计算公式=D1+HE1+TD1即内螺纹小径基本尺寸+偏差+公差例:6H级M8内螺纹小径的上限值 6.647+0=6.6476H级M8内螺纹小径的下限值 6.647+0+0.265=6.912c. 内螺纹6G级的小径基本偏差(以螺距为基准)及小径值计算P0.8 +0.024 P1.0 +0.026 P1.25 +0.028 P1.5 +0.032 P1.75 +0.034P2.0 +0.038 P2.5 +0.042内螺纹6G级的小径下限值公式=D1+GE1即内螺纹基本尺寸+偏差例: 6G级M8内螺纹小径的下限值 6.647+0.028=6.6756G级M8内螺纹小径的上限值公式D1+GE1+TD1即内螺纹基本尺寸+偏差+公差例: 6G级M8内螺纹小径的上限值是6.647+0.028+0.265=6.94注:?内螺纹的牙高直接关系到内螺纹的承载力矩的大小,故在毛坯生产中应尽量在其6H级上限值以内?在内螺纹的加工过程中,内螺纹小径越小会给加工具——丝锥的使用效益有所影响.从使用的角度讲是小径越小越好,但综合考虑时一般采用小径的在中限至上限值之间,如果是铸铁或铝件时应采用小径的下限值至中限值之间 ?内螺纹6G级的小径在毛坯生产中可按6H级执行,其精度等级主要考虑螺纹中径的镀层,故只在螺纹加工时考虑丝锥的中径尺寸而不必考虑光孔的小径。
常用齿轮参数计算
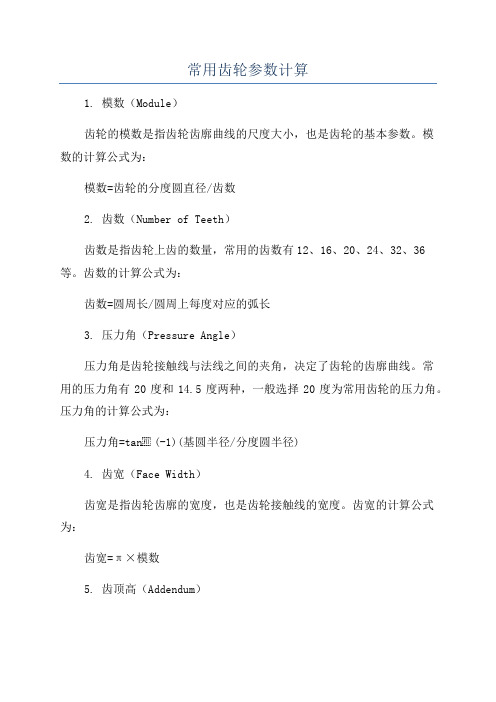
常用齿轮参数计算1. 模数(Module)齿轮的模数是指齿轮齿廓曲线的尺度大小,也是齿轮的基本参数。
模数的计算公式为:模数=齿轮的分度圆直径/齿数2. 齿数(Number of Teeth)齿数是指齿轮上齿的数量,常用的齿数有12、16、20、24、32、36等。
齿数的计算公式为:齿数=圆周长/圆周上每度对应的弧长3. 压力角(Pressure Angle)压力角是齿轮接触线与法线之间的夹角,决定了齿轮的齿廓曲线。
常用的压力角有20度和14.5度两种,一般选择20度为常用齿轮的压力角。
压力角的计算公式为:压力角=tan(-1)(基圆半径/分度圆半径)4. 齿宽(Face Width)齿宽是指齿轮齿廓的宽度,也是齿轮接触线的宽度。
齿宽的计算公式为:齿宽=π×模数5. 齿顶高(Addendum)齿顶高是指齿轮齿顶圆与齿廓的距离,常用的齿顶高为模数的1.25倍。
齿顶高的计算公式为:齿顶高=1.25×模数6. 齿根高(Dedendum)齿根高是指齿轮齿根圆与齿廓的距离,常用的齿根高为模数的1.25倍。
齿根高的计算公式为:齿根高=1.25×模数7. 齿根圆半径(Root Radius)齿根圆半径是指齿轮齿根圆的半径大小,一般取为齿宽的1/2、齿根圆半径的计算公式为:齿根圆半径=齿宽/2以上是常用齿轮参数的计算方法,对于齿轮的设计和选择有着重要的指导意义。
在实际应用中,还需考虑齿轮的强度、传动比、齿轮的重量和制造成本等因素,综合进行综合考虑和优化设计。
齿轮参数的准确计算将为齿轮的性能和使用寿命提供保障。
变位齿轮几何参数计算
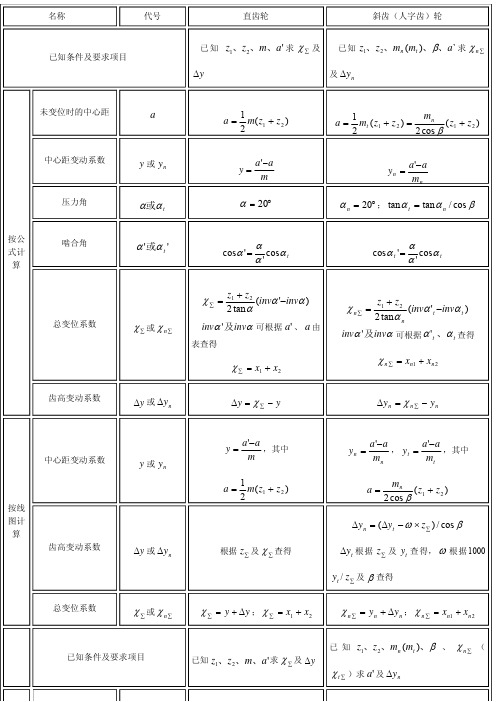
(invα '−invα )
invα '及invα 可根据 a' 、 a 由
表查得
χ ∑ = x1 + x2
χn∑
=
z1 + z2 2 tanα n
(invα 't −invαt )
invα '及invα 可根据 α 't 、α t 查得
χ n ∑ = xn1 + xn2
Δy 或 Δyn
Δy = χ ∑ − y
Δyn = χ n ∑ − yn
按线 图计
算
齿高变动系数 中心距变动系数
Δy 或 Δyn y 或 yn
根据 z∑ 及 χ ∑ 查得 y = χ ∑ − Δy
中心距
α'
α ' = a + ym
注:1.表内公式中的x、xn(xt)本身应带正负号代入;Δy、Δyt永为正号。 2.计算高度变位圆柱齿轮几何尺寸时,公式中的y或yt,Δy或Δyt均为零。
y 或 yn α或α t
y = a'−a m
α = 20°
yn
=
a'−a mn
α n = 20° ; tanα t = tanα n / cos β
按公 式计
算
பைடு நூலகம்
啮合角
α '或α t '
cosα
'
=
α α'
cosα
t
cosα
t
'
=
α α'
cosα
t
总变位系数 齿高变动系数
χ∑或 χn∑
χ∑
=
z1 + z2 2 tanα
齿轮设计计算说明书

齿轮设计计算说明书齿轮设计计算说明书设计背景:齿轮是广泛应用于机械传动系统中的一种重要零件,常用于减速器、变速器、转向器等机械装置中。
在机械设计中,齿轮需要满足一定的强度和耐久性要求,因此需要进行齿轮设计计算。
本说明书将对齿轮设计的相关计算进行详细介绍。
设计计算:1.齿轮参数计算:1.1 齿轮模数(m)的计算公式为:m = K * (√(T_s / (Y * σ))) / (n * z)其中,K为修形系数,取值1.25;T_s为传递的扭矩;Y为齿轮面展向材料的弹性模量;σ为齿轮材料抗弯应力;n为齿轮转速(rpm);z为齿轮的齿数。
1.2 中心距(a)的计算公式为:a = ((z1 + z2) * m) / 2其中,z1和z2分别为两个齿轮的齿数。
1.3 齿轮模数(m)取值范围为0.5mm至50mm。
1.4 中心距(a)的设计范围应满足:1.4.1 当m≤3mm时,a≥2.5m。
1.4.2 当m>3mm时,a≥2.2m。
2.齿轮几何参数计算:2.1 齿高(h)的计算公式为:h = 2.25 * m2.2 齿宽(b)的计算公式为:b = 0.85 * m * z2.3 压力角(α)的计算公式为:α = cos^(-1)((a * sin(β)) / ((z1 + z2) / 2))其中,β为齿轮的压力角。
3.齿轮强度计算:3.1 计算传递的扭矩(T_s):T_s = (P * 60) / (2 * π * n)其中,P为传递的功率(kW);n为齿轮转速(rpm)。
3.2 计算齿轮面弯矩(F)的公式为:F = (T_s * K_f) / (d1 * m)其中,K_f为齿轮面弯曲系数;d1为齿轮1的基圆直径。
3.3 计算转矩系数(K_v):K_v = 1.5 * C_v * (b / m)^(0.25)其中,C_v为转矩载荷系数。
3.4 计算齿轮面张力(F_t)的公式为:F_t = (K_v * F) / b3.5 计算齿轮失效应力(σ_f)的公式为:σ_f = (F_t * K_H) / (b * m)其中,K_H为齿轮荷载分布系数。
斜齿圆柱齿轮的参数及几何尺寸计算
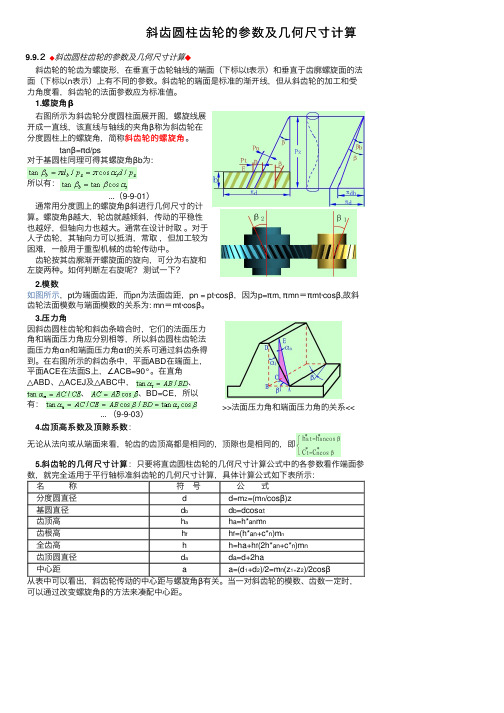
斜齿圆柱齿轮的参数及⼏何尺⼨计算9.9.2 ◆斜齿圆柱齿轮的参数及⼏何尺⼨计算◆ 斜齿轮的轮齿为螺旋形,在垂直于齿轮轴线的端⾯(下标以t 表⽰)和垂直于齿廓螺旋⾯的法⾯(下标以n 表⽰)上有不同的参数。
斜齿轮的端⾯是标准的渐开线,但从斜齿轮的加⼯和受⼒⾓度看,斜齿轮的法⾯参数应为标准值。
1.螺旋⾓β 右图所⽰为斜齿轮分度圆柱⾯展开图,螺旋线展开成⼀直线,该直线与轴线的夹⾓β称为斜齿轮在分度圆柱上的螺旋⾓,简称斜齿轮的螺旋⾓。
tan β=πd/ps对于基圆柱同理可得其螺旋⾓βb 为:所以有: ...(9-9-01) 通常⽤分度圆上的螺旋⾓β斜进⾏⼏何尺⼨的计算。
螺旋⾓β越⼤,轮齿就越倾斜,传动的平稳性也越好,但轴向⼒也越⼤。
通常在设计时取 。
对于⼈⼦齿轮,其轴向⼒可以抵消,常取 ,但加⼯较为困难,⼀般⽤于重型机械的齿轮传动中。
齿轮按其齿廓渐开螺旋⾯的旋向,可分为右旋和左旋两种。
如何判断左右旋呢? 测试⼀下? 2.模数如图所⽰,pt 为端⾯齿距,⽽pn 为法⾯齿距,pn = pt·cos β,因为p=πm, πmn =πmt·cos β,故斜齿轮法⾯模数与端⾯模数的关系为: mn =mt·cos β。
3.压⼒⾓因斜齿圆柱齿轮和斜齿条啮合时,它们的法⾯压⼒⾓和端⾯压⼒⾓应分别相等,所以斜齿圆柱齿轮法⾯压⼒⾓αn 和端⾯压⼒⾓αt 的关系可通过斜齿条得到。
在右图所⽰的斜齿条中,平⾯ABD 在端⾯上,平⾯ACE 在法⾯S 上,∠ACB=90°。
在直⾓△ABD 、△ACEJ 及△ABC 中,、、、BD=CE ,所以有: ... (9-9-03) >>法⾯压⼒⾓和端⾯压⼒⾓的关系<< 4.齿顶⾼系数及顶隙系数齿顶⾼系数及顶隙系数:⽆论从法向或从端⾯来看,轮齿的齿顶⾼都是相同的,顶隙也是相同的,即 5.斜齿轮的⼏何尺⼨计算斜齿轮的⼏何尺⼨计算:只要将直齿圆柱齿轮的⼏何尺⼨计算公式中的各参数看作端⾯参数,就完全适⽤于平⾏轴标准斜齿轮的⼏何尺⼨计算,具体计算公式如下表所⽰: 名 称 符 号 公 式 分度圆直径d d=m z =(m n /cos β)z 基圆直径d b d b =dcos αt 齿顶⾼h a h a =h*an m n 齿根⾼h f h f =(h*an +c*n )m n 全齿⾼h h=ha+h f (2h*an +c*n )m n 齿顶圆直径d a d a =d+2ha 中⼼距a a=(d 1+d 2)/2=m n (z 1+z 2)/2cos β从表中可以看出,斜齿轮传动的中⼼距与螺旋⾓β有关。
变位齿轮几何尺寸计算

变位齿轮几何尺寸计算
变位齿轮是齿轮传动系统中常用的一种齿轮,主要用于传递旋转运动和扭矩。
其特点是在齿轮齿条的侧面具有斜面,能够实现平滑传动和减小齿轮传动时的冲击和噪声。
在设计变位齿轮时,需要进行几何尺寸的计算来保证齿轮的运转性能。
变位齿轮的几何尺寸计算主要包括齿轮的模数、齿数、齿顶高和齿根深等参数。
下面将详细介绍每个参数的计算方法。
1.模数(m)的计算:
模数是齿轮齿条的基本尺寸,它表示齿轮齿条的大小。
模数的计算根据传动所需的扭矩和功率来确定,通常使用公式:
m=K∛(T/P)
其中,m为模数,K为系数(一般取20),T为传动所需扭矩,P为传动功率。
2.齿数(z)的计算:
齿数表示齿轮上的齿的数量。
齿数的计算根据传动比和模数来确定,一般使用公式:
z=m×i
其中,i为传动比。
3.齿顶高(h_a)和齿根深(h_f)的计算:
齿顶高表示齿轮齿条的最高点到齿顶的距离,齿根深表示齿轮齿条的最低点到齿底的距离。
它们的计算可以使用公式:
h_a=1.25×m
h_f=1.35×m
上述是变位齿轮几何尺寸计算的基本方法,但实际设计中还需要考虑齿轮的齿向角、齿轮间的啮合角、齿轮侧隙等因素。
此外,变位齿轮的几何尺寸还需要满足一些额外的要求,如齿轮的强度和刚度等。
关于变位齿轮几何尺寸计算的更详细内容可以参考相关的齿轮设计手册和专业参考书籍。
摆线圆柱齿轮传动的设计计算
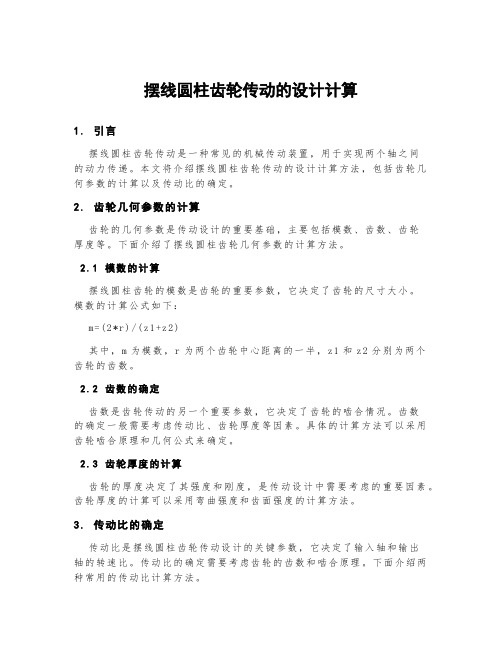
摆线圆柱齿轮传动的设计计算1.引言摆线圆柱齿轮传动是一种常见的机械传动装置,用于实现两个轴之间的动力传递。
本文将介绍摆线圆柱齿轮传动的设计计算方法,包括齿轮几何参数的计算以及传动比的确定。
2.齿轮几何参数的计算齿轮的几何参数是传动设计的重要基础,主要包括模数、齿数、齿轮厚度等。
下面介绍了摆线圆柱齿轮几何参数的计算方法。
2.1模数的计算摆线圆柱齿轮的模数是齿轮的重要参数,它决定了齿轮的尺寸大小。
模数的计算公式如下:m=(2*r)/(z1+z2)其中,m为模数,r为两个齿轮中心距离的一半,z1和z2分别为两个齿轮的齿数。
2.2齿数的确定齿数是齿轮传动的另一个重要参数,它决定了齿轮的啮合情况。
齿数的确定一般需要考虑传动比、齿轮厚度等因素。
具体的计算方法可以采用齿轮啮合原理和几何公式来确定。
2.3齿轮厚度的计算齿轮的厚度决定了其强度和刚度,是传动设计中需要考虑的重要因素。
齿轮厚度的计算可以采用弯曲强度和齿面强度的计算方法。
3.传动比的确定传动比是摆线圆柱齿轮传动设计的关键参数,它决定了输入轴和输出轴的转速比。
传动比的确定需要考虑齿轮的齿数和啮合原理。
下面介绍两种常用的传动比计算方法。
3.1齿数比法齿数比法是一种常用的传动比计算方法,可以用于确定传动时的转速比。
其计算公式如下:i=z2/z1其中,i为传动比,z1和z2分别为输入轴和输出轴的齿数。
3.2速比法速比法是另一种常用的传动比计算方法,它考虑了齿轮的线速度和圆周速度的关系。
其计算公式如下:i=(n2*d2)/(n1*d1)其中,i为传动比,n1和n2分别为输入轴和输出轴的转速,d1和d2分别为输入轴和输出轴的直径。
4.结论摆线圆柱齿轮传动的设计计算是机械传动设计的关键步骤,本文介绍了齿轮几何参数的计算方法以及传动比的确定方法。
通过合理的设计计算,可以确保摆线圆柱齿轮传动的可靠性和高效性。
- 1、下载文档前请自行甄别文档内容的完整性,平台不提供额外的编辑、内容补充、找答案等附加服务。
- 2、"仅部分预览"的文档,不可在线预览部分如存在完整性等问题,可反馈申请退款(可完整预览的文档不适用该条件!)。
- 3、如文档侵犯您的权益,请联系客服反馈,我们会尽快为您处理(人工客服工作时间:9:00-18:30)。
第2章渐开线圆柱齿轮几何参数设计计算2.1 概述渐开线圆柱齿轮设计是齿轮传动设计中最常用、最典型的设计,掌握其设计方法是齿轮设计者必须具备的,对于其它类型的传动也有很大的帮助。
在此重点讨论渐开线圆柱齿轮设计的设计技术。
2.2 齿轮传动类型选择直齿(无轴向力)斜齿(有轴向力,强度高,平稳)双斜齿(无轴向力,强度高,平稳、加工复杂)2.3 齿轮设计的主要步骤多级速比分配单级中心距估算齿轮参数设计齿轮强度校核齿轮几何精度计算2.4 齿轮参数设计原则(1) 模数的选择模数的选择取决于齿轮的弯曲承载能力,一般在满足弯曲强度的条件下,选择较小的模数,对减少齿轮副的滑动率、増大重合度,提高平稳性有好处。
但在制造质量没有保证时,应选择较大的模数,提高可靠性,模数増大对动特性和胶合不利。
模数一般按模数系列标准选取,对动力传动一般不小于2对于平稳载荷:mn=(0.007-0.01)a对于中等冲击:mn=(0.01-0.015)a对于较大冲击:mn=(0.015-0.02)a(2)压力角选择 an=20大压力角(25、27、28、30)的优缺点:优点:齿根厚度和渐开线部分的曲率半径增大,对接触弯曲强度有利。
齿面滑动速度减小,不易发生胶合。
根切的最小齿数减小。
缺点:齿的刚度增大,重合度减小,不利于齿轮的动态特性。
轴承所受的载荷增大。
过渡曲线长度和曲率半径减小,应力集中系数增大。
小压力角(14.5、15、16、17.5、18)的优缺点:优点:齿的刚度减小,重合度增大,有利于齿轮的动态特性。
轴承所受的载荷减小。
缺点:齿根厚度和渐开线部分的曲率半径减小,对接触弯曲强度不利。
齿面滑动速度增大,易发生胶合。
根切的最小齿数增多。
(3)螺旋角选择斜齿轮螺旋角一般应优先选取整:10-13.双斜齿轮螺旋角一般应优先选取:26-33.螺旋角一般优先取整数,高速级取较大,低速级取较小。
考虑加工的可能性。
螺旋角增大的优缺点:齿面综合曲率半径增大,对齿面接触强度有利。
纵向重合度增大,对传动平稳性有利。
齿根的弯曲强度也有所提高(大于15度后变化不大)。
轴承所受的轴向力增大。
齿面温升将增加,对胶合不利。
断面重合度减小。
(4)齿数的选择最小齿数要求(与变位有关)齿数和的要求齿数互质要求大于100齿的质数齿加工可能性问题(滚齿差动机构)高速齿轮齿数齿数要求增速传动的齿数要求(5)齿宽和齿宽系数的选择一般齿轮的齿宽由齿宽系数来确定,φa=b/a φd=b/d1 φm=b/mnφa=(0.2-0.4)齿宽系数φd取值:齿轮对称分布φd最大值1.1-1.4齿轮非对称分布φd最大值0.9-1.1齿轮悬臂结构φd最大值0.6-0.8注意:齿宽系数比较大时注意偏载问题。
齿轮悬臂结构不宜取较大的齿宽系数(6)齿顶高系数 ha=1长齿(1.1、1.2、1.3)的特点:重合度大、接触强度有所提高、对传动平稳性有利。
滑动速度大、齿顶变尖短齿(0.8、0.9)的特点:弯曲强度有所提高、滑动速度小、不易胶合。
重合度小,对振动噪声不利。
(7)顶隙系数(0.25、0.3、0.35、0.4)一般齿轮0.25高精度硬齿面重载齿轮0.35、0.4小模数0.35与刀具有关与齿根圆角有关(8)重合度要求端面重合度EA大于1.15EA+EB大于2.2轴向重合度EB大于1.0(9) 变位系数的选择①变位的目的:可以减小小齿轮的最少齿数,降低结构体积和重量;正变位可避免根切,提高接触和弯曲强度;变位系数合理分配,可降低齿面滑动率;配凑中心距;利用变位可修复磨损的旧齿轮。
②变位选择一般应优先选取XΣ(0.4-1.2)的值.大小轮的最大滑动系数应接近相等。
05变位方法大变位设计问题Xn1+Xn2和越大,强度越大,相啮合率越小Xn1+Xn2和越小,强度越小,相啮合率越大③变位系数的选择特点:Xn1+Xn2=(-0.4 -- -0.8)特殊情况设计(负大变位设计)Xn1+Xn2=(-0.4 -- 0)相啮合率大Xn1+Xn2=(0--0.6)平行较好的齿形Xn1+Xn2=(0.6 – 1.2)齿根与齿面强度较大Xn1+Xn2= (>1.2 特殊情况设计(大变位设计)④变位系数选择的限制条件根切要求齿顶厚要求重合度要求干涉要求等⑤国外一些规范中的变位系数选择方法英国国家规范(BSS NO. 436)中的变位方法:内啮合变位系数选择xn1=0.4(1-z1/z2)xn2=-xn1内啮合变位系数选择xn1=0.4xn2=-0.4德国规范(DINE 3994)中的变位方法:外齿轮:xn=0.5内齿轮:xn=-0.5(10)齿顶厚要求(11)齿面滑动率要求2.5 齿轮基本参数综合优化设计齿轮减速器的优化设计涉及面较广,影响的因素很多,除了要掌握优化设计理论和方法外,更重要的是对齿轮专业知识的深入了解,才能设计出工程上比较合理实用的方案。
国内近20年来在齿轮优化设计方面作了很多研究工作,也取得较大的进展。
但应该认识到齿轮的优化设计不是单单依靠建立优化数学模型就能够完全解决的一个问题。
一个合理实用的工程设计方案是要依靠具有丰富专业知识和工程经验的工程师通过大量的计算、分析、判断、对比等综合确定。
齿轮传动现代设计是一门综合技术,由于齿轮传动是一个很专业的学科,如何运用现代设计技术和手段解决好齿轮设计问题是关键所在。
目前,许多已发表的文章中提出了多种齿轮优化设计方面的建模方法,每种方法各有特点,都说是最佳或最优方案。
但没有一个方法能说明该方法是完美无缺的,这其中主要忽略了一个大前提,那就是在特定的建模条件下寻求最佳方案,这只是一个数学方法问题,与实际工程相差甚远。
齿轮设计是一个集几何、强度、工艺、材料与热处理、使用工况和评价标准等诸多复杂因素组合的综合问题,在一定范围内也是一个系统工程,这样一个问题不是靠简单的数学模型就能加以描述的。
本系列产品的设计方法采用“综合优化”的设计思想,不片面追求理论上的优化值,而是把传统设计方法、现代设计技术和设计者的知识经验有机地结合起来,理论上追求科学合理,应用中力求可靠实用,二者兼顾。
在齿轮减速器优化设计中,一般情况下,多级减速器的优化设计可以分二个步骤进行,即:级间等强度优化设计及单级齿轮优化设计。
2.5.1 中心距和速比优化设计(1)中心距的确定当中心距未定时,一般由接触强度确定,即取值要大于满足接触强度的最小中心距(2) 中心距不定时的速比的分配按各级齿轮体积最小来分配各级速比,由接触强度计算公式可得:231)1(341091.1)1(⎥⎥⎦⎤⎢⎢⎣⎡+=-HPj j j aj j j j j Z u n PK x u a σφη齿轮的体积近似为:最小体积存在的必要条件是:解联立方程可求出各级速比。
(3) 定中心距的速比分配在齿轮减速器的优化设计,给定一个名义总速比,对多级传动有很多种速比排列组合,如何确定比较合理的速比组合,对提高系列减速器的承载能力有着重要的作用。
多级减速器的传动比分配直接影响减速器的承载能力和使用寿命。
一般情况下,传动比的分配应该使各级的承载能力大至相等。
由等接触安全系数相等(即:SH j =SH j+1)可推得:式中2213131112111⎪⎪⎭⎫⎝⎛=⎪⎪⎭⎫ ⎝⎛++⎪⎪⎭⎫ ⎝⎛⎪⎪⎭⎫ ⎝⎛⎪⎪⎭⎫ ⎝⎛⎪⎪⎭⎫ ⎝⎛-------j i j j j j j j j j j j j j j HP HP u u u u a a a a K K Z Z σσφφη21)1(72)1(1091.1⎥⎥⎦⎤⎢⎢⎣⎡+=-H Pjjj j j j j j ijZ u n u PK x B D σηjmj ij j B D u X f v ∑=+==122)1()(0)(=dxx dfK=KaKvKHaKHβZ=ZHZEZεZβU—速比η—传动效率σHP—接触许用应力 (Mpa)j=1.2.3…m (m为传动级数)其中计算系数定义见国家齿轮强度标准《GB/T3480-97》对于m级传动,只有m-1个速比为独立变量,所以,只需求解由上述公式组成的m-1元方程组即可求得各级速比分配。
2.5. 2 齿轮参数综合优化设计在减速器产品齿轮参数优化设计中,如何合理选择齿轮参数是至关重要的。
由于各级中心距组合和名义速比的组合已经给定,而且齿宽与中心距的比值通常也已经确定,那么实际上要设计的变量只有齿数、模数、螺旋角和变位系数。
由于中心距、速比和齿宽已经给定,那么减速器的齿轮接触强度基本上也已确定。
因此,要提高减速器的综合承载能力,主要是提高齿轮的抗弯能力。
也就是说,在保证小轮齿数大于小轮最小齿数Z1min及齿数和(ΣZ1+Z2)大于最小齿数和(Z∑min)的条件下,尽量选取较大的模数,以提高减速器的综合承载能力。
由于齿数、模数、优先螺旋角均为离散变量,所以采用网格枚举法进行齿轮参数的优选。
网格枚举法的设计思路是:按照一定的规则对模数、齿数、螺旋角进行排列组合,对满足条件的方案进行分析对比,筛选出最佳的组合方案。
采用网格枚举法优选齿轮参数的主要设计步骤:1、齿轮设计参数的上下限的确定(1)初步确定小轮齿数Z10根据名义速比u初步确定小轮齿数Z10Z10≥Z1minZ10≥Z∑min/(1+u)式中Z1min —允许最小小轮齿数 Z ∑min--允许最小齿数和 (2) 根据中心距a 、速比u 和小轮齿数Z 10初步确定模数m n0,并确定模数的上下限。
式中β0=(βmin+βmax)/2X ∑0=( X ∑min+ X ∑max)/2 βmin--允许最小螺旋角 βmax --允许最大螺旋角X ∑min--允许最小变位系数和 X ∑max --允许最大变位系数和根据初步确定模数m n0按模数系列确定模数的上下限,即:(mn(i)< mn0<mn(i+1))(3) 根据中心距a 、速比u 、模数m n 等重新确定小轮齿数上下限Z 1L 和Z 1u注意:不同模数对应不同的小轮齿数上下限()()010001cos 2∑++=x Z u a m n β()()()nn Lm u m x a Z +-=∑1cos 2max max 1β()()()nn um u m x a Z +-=∑1cos 2min min 1β2、 可行设计方案的判断及最佳方案选择根据齿轮设计变量的上下界范围,进行排列组合,对所有的组合方案进行可行性判断,既满足各种约束条件要求的方案定为可行方案,在可行方案中根据一定的评价标准最终确定最佳方案。
网格枚举法实际上是一种网格枚举设计法,对于离散变量的设计问题,给出各种参数的组合,对每一种组合根据啮合质量标准的要求,从而获得对应的可行方案,采用模糊数学的综合评判法,给出各项指标的权系数,对各组合进行评价,去劣存优,直到找出最佳设计方案。