循环经济与企业环境成本控制外文文献翻译
企业成本控制外文翻译文献
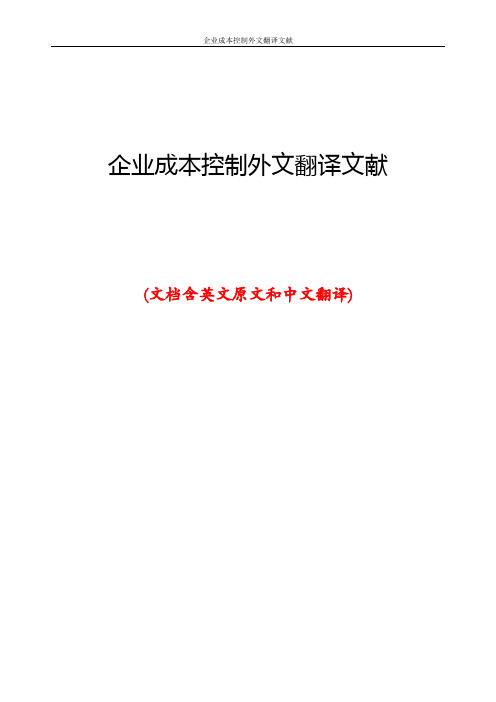
企业成本控制外文翻译文献(文档含英文原文和中文翻译)译文:在价值链的成本控制下减少费用和获得更多的利润摘要:根据基于价值链的成本管理理念和基于价值的重要因素是必要的。
首先,必须有足够的资源,必须创造了有利的价值投资,同时还需要基于客户价值活动链,以确定他们的成本管理优势的价值链。
其次,消耗的资源必须尽量减少,使最小的运营成本价值链和确保成本优势是基于最大商业价值或利润,这是一种成本控制系统内部整个视图的创建和供应的具实践,它也是一种成本控制制度基于价值链,包括足够的控制和必要的资源投资价值的观点,创建和保持消费的资源到合理的水平,具有价值的观点主要对象的第一个因素是构造有利的价值链,从创造顾客价值开始;第二个因素是加强有利的价值链,从供应或生产客户价值开始。
因此它是一个新型的理念,去探索成本控制从整个视图的创建和供应的商品更盈利企业获得可持续的竞争优势。
关键词:成本控制,价值链,收益,支出,收入,成本会计1、介绍根据价值链理论,企业的目的是创造最大的顾客价值;和企业的竞争优势在于尽可能提供尽可能多的价值给他们的客户,作为低成本可能的。
这要求企业必须首先考虑他们是否能为顾客创造价值,和然后考虑在很长一段时间内如何创造它。
然而,竞争一直以“商品”(或“产品”)作为最直接的载体,因此,传统的成本控制方法主要集中在对“产品”和生产流程的过程。
很显然,这不能解决企业的问题,企业是否或如何能为客户创造价值。
换句话说,这至少不能从根本上解决它。
因此,企业必须首先投入足够的资源,以便他们能够创建客户值取向,然后提供它以最少的资源费用。
所以在整个视图中对价值创造和提供整体的观点来控制成本,它可以为客户提供完美的动力和操作运行机制运行成本的控制,也可以从根本上彻底克服了传统的成本控制方法的缺点,解决了无法控制的创造和供应不足的真正价值。
基于此,本文试图从创作的整体观讨论成本控制提供价值并探讨实现良性循环的策略,也就是说,“创造价值投资成本供应价值创造价值”。
一项关于循环经济的环境经济学的介绍性说明【外文翻译】

外文翻译原文An introductory note on the environmental economics of thecircular economyMaterial Source:Sustainability Science(2007)2Author: Mikael Skou Andersen IntroductionThe concept of a circular economy – currently widely promoted in Asia – has its conceptual roots in industrial ecology, which envisions a form of material symbiosis between otherwise very different companies and production processes. Industrial ecology emphasises the benefits of recycling residual waste materials and by-products through, for example, the development of complex interlinkages, such as those in the renowned industrial symbiosis projects (see Jacobsen 2006). However, in more general terms, it promotes resource minimisation and the adoption of cleaner technologies (Andersen 1997, 1999).In industrial ecology, it is implied that a circular economy will be beneficial to society and to the economy as a whole. Benefits will be obtained, not only by minimising use of the environment as a sink for residuals but –perhaps more importantly –by minimising the use of virgin materials for economic activity. Intuitively, the potential benefits seem straightforward, but it is important to stress that the perspective prevailing within the circular economy approach is, in fact, based on physical rather than economic observations.The assumed benefits are based on the fundamental observation that the loss of material residuals, in physical units, is minimised. But how far should society go in the recycling of materials? While the first and most straightforward recycling options provide evident benefits, once the recycling road is embarked upon, the subsequent benefits gradually become more and more difficult to achieve. It has to be acknowledged that at some stage there will be a cut-off point where recyclingwill become too difficult and burdensome to provide a net benefit. A circular economy cannot promote recycling in perpetuity.Many adherents of the circular economy approach are strong proponents, on environmental and ethical premises, of material reuse and recycling. However, in a market economy (and in some planned economies as well), the prices of materials and natural resources will be too low and will mainly reflect the costs associated with mining and short-term values, but not with depletion nor the environmental costs. In such cases, only a limited range of circular options will make sense from the perspective of company managers. It can be argued that if companies are rational and profit-seeking, the recycling and reuse options should already have been realised. In a conventional capitalist economy, recycling will be undertaken only where it is desirable from a private economic viewpoint.Decision-makers responsible for public policy-making need to transcend such narrow perspectives and institute mechanisms that secure that recycling and reuse takes place where it is socially desirable and efficient. As a first step, it is necessary to analyse more carefully from a socio-economic perspective how circular economy principles can provide net benefits. Environmental economics offers an analytical approach that can be of considerable help in identifying which material streams and which recycling options provide the greatest benefits to the economy –if circular rather than open-ended principles are introduced. Environmental economic analysis in public policy-making presumes, in practice, an in-depth understanding and description of the environmental consequences of various choices, thereby making the analysis interdisciplinary in nature. Environmental economics also offers the basis for introducing “externality adders” to market prices in the form of environmental taxes and charges, so that prices can reveal the true situation, thereby allowing market actors to take account of the real costs in their mutual transactions.This paper provides an introduction to the approach of environmental economics and indicates its potential for achieving a sound and efficient circular economy.Sustainable development and sustainable economic welfareBefore examining how values can be attached to the economic services and disservices related to the environment, we need to consider briefly the implications associated with requirements for sustainable development with respect to the choice of economic approach.The UN’s World Commission defines sustainable development as a trajectory where future generations are secured the same level of welfare as present living generations. The implication of this approach, as seen from an economics standpoint, is a requirement for constant consumption or, phrased in a slightly more abstract manner, constant utility. In order to maintain annual yield at a constant level, there will be, in the absence of technological progress, a requirement for the stock of environmental resources to be kept constant. Environmental resources should be managed in such a way that the future yield does not diminish and future generations will not be worse off. In this manner, environmental resources can be viewed as a bank account where the capital (deposited amount) remains constant so as to generate a steady stream of interest to live on.The requirement for constant yield and a constant stock of natural capital is restrictive. It has become customary to distinguish between strong and weak versions of sustainable development. Within the weak form of sustainability, the substitution of natural capital and other types of capital is allowed, such that the depletion of natural capital has to be compensated through savings in other types of capital, such as human capital or physical capital. While often regarded as a relaxation of the sustainability criteria, even this weaker definition of sustainability would be a challenge for many countries which do not have systems in place that are able to account for whether or not the extraction of fossil fuels is compensated through reinvestments in education (human capital) or infrastructure (physical capital). The strong version of sustainable development, which does not allow for substitution, is normally made less rigid so that focus is on the non-substitutability of certain types of critical capital.The economic sustainability definition is usually associated with Hartwick’s savings rule, which suggests that the rents from natural resource extraction should be reinvested in other types of capital and that the government should ensure this by instituting a tax on natural resource extraction so as to guarantee a sustainable levelof savings. In the case of fossil fuels, Hartwick’s savings rule implies tha t income from fossil fuel taxes would be reinvested in other types of capital and that these would yield a level of annual rent in the future similar to the present extraction of fossil fuels.Socio-economic analysis of the circular economyThe externality estimates can be used in the analysis of projects that are considered to improve the circular aspects of the economy. In the case of recycling, the potential benefits are basically comprised of three elements:–the market value of the recycled materials;–reduced burden from waste disposal (incineration orlandfill);–reduced burden due to reductions in extraction of virginmaterials.In the case of the circular economy, companies with residual waste streams may often be some distance from the market where they obtain the value of materials. As such, the waste products do not relate to their main area of activity and the companies may be forced to dump them at unfavourable prices to nearby plants that are willing to accept them. However, if the authorities institute a set of taxes on the key pollutants, any activity that will diminish the net environmental burden will become profitable for both the receiving and the disposing companies. Alternatively, the authorities may require a socio-economic analysis of the benefits of recycling, as outlined above.ConclusionsSignificant advances in the pricing of externalities have been achieved in recent years by means of complex interdisciplinary analyses that attempt to account indetail for the environmental consequences. The monetary estimates reached as a result of such interdisciplinary research are gradually being applied by the authorities to the economic analysis of environmental policy priorities. A prominent example was the assessment that emerge d from the EU’s 6th Envir onmental Action Programme (RIVM,2001). This assessment relied on the results of the ExternE project, and the economic analysis was based on the use of the National Institute for Public Health and the Environment of the Netherlands' (RIVM) expertise and models for the natural scientific basis.The challenge in accounting for external effects is very much related to the necessity to transcend disciplinary orientations and to combine the knowledge and data available in various subfields. That environmental issues are complex has been acknowledged for decades, and the resulting predominance of symbolic politics been deplored by many observers. Whether the insights obtained by combining natural science models with economic principles of accounting for external effects will lead to an environmental policy that is more rational and less sensitive to abuse by vested interests is perhaps to early to say, but we can at least hope that a more confined playing field for the clash of interests can be defined.The establishment of a future trajectory for a circular economy will require that this approach be extended so that the broader issue of sustainability can be addressed more comprehensively. Whereas external effects relate mainly to the present generations, the sustainability issue implies a need to address the future generations as well when the implications of the environmental pressures are quantified. Although the available estimates for external effects provide only a partial and incomplete picture of the environmental costs at stake, they help support and expand on the analysis of the virtues of a more circular economy.译文一项关于循环经济的环境经济学的介绍性说明资料来源: 可持续发展科学(2007)2 作者:迈克尔•斯科•安徒生简介目前循环经济的概念被广泛推广到亚洲。
企业环境成本会计外文翻译word精品文档11页

IMPLEMENTING ENVIRONMENTAL COSTACCOUNTING IN SMALL AND MEDIUM-SIZEDCOMPANIES1.ENVIRONMENTAL COST ACCOUNTING IN SMESSince its inception some 30 years ago, Environmental Cost Accounting (ECA) has reached a stage of development where individual ECA systems are separated from the core accounting system based an assessment of environmental costs with (see Fichter et al., 1997, Letmathe and Wagner , 2002).As environmental costs are commonly assessed as overhead costs, neither the older concepts of full costs accounting nor the relatively recent one of direct costing appear to represent an appropriate basis for the implementation of ECA. Similar to developments in conventional accounting, the theoretical and conceptual sphere of ECA has focused on process-based accounting since the 1990s (see Hallay and Pfriem, 1992, Fischer and Blasius, 1995, BMU/UBA, 1996, Heller et al., 1995, Letmathe, 1998, Spengler and H.hre, 1998).Taking available concepts of ECA into consideration, process-based concepts seem the best option regarding the establishment of ECA (see Heupel and Wendisch , 2002). These concepts, however, have to be continuously revised to ensure that they work well when applied in small and medium-sized companies.Based on the framework for Environmental Management Accounting presented in Burritt et al. (2002), our concept of ECA focuses on two main groups of environmentally related impacts. These are environmentally induced financial effects and company-related effects on environmental systems (see Burritt and Schaltegger, 2000, p.58). Each of these impacts relate to specific categories of financial and environmental information. The environmentally induced financial effects are represented by monetary environmental information and the effects on environmental systems are represented by physical environmental information. Conventionalaccounting deals with both – monetary as well as physical units – but does not focus on environmental impact as such. To arrive at a practical solution to the implementation of ECA in a company’s existing accounting system, and to comply with the problem of distinguishing between monetary and physical aspects, an integrated concept is required. As physical information is often the basis for the monetary information (e.g. kilograms of a raw material are the basis for the monetary valuation of raw material consumption), the integration of this information into the accounting system database is essential. From there, the generation of physical environmental and monetary (environmental) information would in many cases be feasible. For many companies, the priority would be monetary (environmental) information for use in for instance decisions regarding resource consumptions and investments. The use of ECA in small and medium-sized enterprises (SME) is still relatively rare, so practical examples available in the literature are few and far between. One problem is that the definitions of SMEs vary between countries (see Kosmider, 1993 and Reinemann, 1999). In our work the criteria shown in Table 1 are used to describe small and medium-sized enterprises.Table 1. Criteria of small and medium-sized enterprisesNumber of employees TurnoverUp to 500 employees Turnover up to EUR 50m Management Organization- Owner-cum-entrepreneur -Divisional organization is rare- Varies from a patriarchal management -Short flow of information stylein traditional companies and teamwork -Strong personal commitmentin start-up companies -Instruction and controlling with- Top-down planning in old companies direct personal contact- Delegation is rare- Low level of formality- High flexibility Finance Personnel- family company -easy to survey number ofemployees- limited possibilities of financing -wide expertise-high satisfaction of employees Supply chain Innovation-closely involved in local -high potential ofinnovationeconomic cycles in special fields- intense relationship with customersand suppliersKeeping these characteristics in mind, the chosen ECA approach should be easy to apply, should facilitate the handling of complex structures and at the same time be suited to the special needs of SMEs.Despite their size SMEs are increasingly implementing Enterprise Resource Planning (ERP) systems like SAP R/3, Oracle and Peoplesoft. ERP systems support business processes across organizational, temporal and geographical boundaries using one integrated database. The primary use of ERP systems is for planning and controlling production and administration processes of an enterprise. In SMEs however, they are often individually designed and thus not standardized making the integration of for instance software that supports ECA implementation problematic. Examples could be tools like the “eco-efficiency” approach of IMU (2003) or Umberto (2003) because these solutions work with the database of more comprehensive software solutions like SAP, Oracle, Navision or others. Umberto software for example (see Umberto, 2003) would require large investments and great background knowledge of ECA –which is not available in most SMEs.The ECA approach suggested in this chapter is based on an integrative solution – meaning that an individually developed database is used, and the ECA solution adopted draws on the existing cost accounting procedures in the company. In contrast to other ECA approaches, the aim was to create an accounting system that enables the companies to individually obtain the relevant cost information. The aim of the research was thus to find out what cost information is relevant for the company’s decision o n environmental issues and how to obtain it.2.METHOD FOR IMPLEMENTING ECASetting up an ECA system requires a systematic procedure. The project thus developed a method for implementing ECA in the companies that participated in the project; this is shown in Figure 1. During the implementation of the project it proved convenient to form a core team assigned with corresponding tasks drawing on employees in various departments. Such a team should consist of one or two persons from the production department as well as two from accounting and corporate environmental issues, if available. Depending on the stage of the project and kind of inquiry being considered, additional corporate members may be added to the project team to respond to issues such as IT, logistics, warehousing etc.Phase 1: Production Process VisualizationAt the beginning, the project team must be briefed thoroughly on the current corporate situation and on the accounting situation. To this end, the existing corporate accounting structure and the related corporate information transfer should be analyzed thoroughly. Following the concept of an input/output analysis, how materials find their ways into and out of the company is assessed. The next step is to present the flow of material and goods discovered and assessed in a flow model. To ensure the completeness and integrity of such a systematic analysis, any input and output is to be taken into consideration. Only a detailed analysis of material and energy flows from the point they enter the company until theyleave it as products, waste, waste water or emissions enables the company to detect cost-saving potentials that at later stages of the project may involve more efficient material use, advanced process reliability and overview, improved capacity loads, reduced waste disposal costs, better transparency of costs and more reliable assessment of legal issues. As a first approach, simplified corporate flow models, standardized stand-alone models for supplier(s), warehouse and isolated production segments were established and only combined after completion. With such standard elements and prototypes defined, a company can readily develop an integrated flow model with production process(es), production lines or a production process as a whole. From the view of later adoption of the existing corporate accounting to ECA, such visualization helps detect, determine, assess and then separate primary from secondary processes.Phase 2: Modification of AccountingIn addition to the visualization of material and energy flows, modeling principal and peripheral corporate processes helps prevent problems involving too high shares of overhead costs on the net product result. The flow model allows processes to be determined directly or at least partially identified as cost drivers. This allows identifying and separating repetitive processing activity with comparably few options from those with more likely ones for potential improvement.By focusing on principal issues of corporate cost priorities and on those costs that have been assessed and assigned to their causes least appropriately so far, corporate procedures such as preparing bids, setting up production machinery, ordering (raw) material and related process parameters such as order positions, setting up cycles of machinery, and order items can be defined accurately. Putting several partial processes with their isolated costs into context allows principal processes to emerge; these form the basis of process-oriented accounting. Ultimately, the cost drivers of the processes assessed are the actual reference points for assigning and accounting overhead costs. The percentage surchargeson costs such as labor costs are replaced by process parameters measuring efficiency (see Foster and Gupta, 1990).Some corporate processes such as management, controlling and personnel remain inadequately assessed with cost drivers assigned to product-related cost accounting. Therefore, costs of the processes mentioned, irrelevant to the measure of production activity, have to be assessed and surcharged with a conventional percentage.At manufacturing companies participating in the project, computer-integrated manufacturing systems allow a more flexible and scope-oriented production (eco-monies of scope), whereas before only homogenous quantities (of products) could be produced under reasonable economic conditions (economies of scale). ECA inevitably prevents effects of allocation, complexity and digression and becomes a valuable controlling instrument where classical/conventional accounting arrangements systematically fail to facilitate proper decisions.Thus, individually adopted process-based accounting produces potentially valuable information for any kind of decision about internal processing or external sourcing (e.g. make-or-buy decisions).Phase 3: Harmonization of Corporate Data –Compiling and Acquisition On the way to a transparent and systematic information system, it is convenient to check core corporate information systems of procurement and logistics, production planning, and waste disposal with reference to their capability to provide the necessary precise figures for the determined material/energy flow model and for previously identified principal and peripheral processes. During the course of the project, a few modifications within existing information systems were, in most cases, sufficient to comply with these requirements; otherwise, a completely new software module would have had to be installed without prior analysis to satisfy the data requirements.Phase 4: Database conceptsWithin the concept of a transparent accounting system, process-basedaccounting can provide comprehensive and systematic information both on corporate material/ energy flows and so-called overhead costs. To deliver reliable figures over time, it is essential to integrate a permanent integration of the algorithms discussed above into the corporate information system(s). Such permanent integration and its practical use may be achieved by applying one of three software solutions (see Figure 2).For small companies with specific production processes, an integrated concept is best suited, i.e. conventional and environmental/process-oriented accounting merge together in one common system solution.For medium-sized companies, with already existing integrated production/ accounting platforms, an interface solution to such a system might be suitable. ECA, then, is set up as an independent software module outside the existing corporate ERP system and needs to be fed data continuously. By using identical conventions for inventory-data definitions within the ECA software, misinterpretation of data can be avoided.Phase 5: Training and CoachingFor the permanent use of ECA, continuous training of employees on all matters discussed remains essential. To achieve a long-term potential of improved efficiency, the users of ECA applications and systems must be able to continuously detect and integrate corporate process modifications and changes in order to integrate them into ECA and, later, to process them properly.中小企业环境成本会计的实施一、中小企业的环境成本会计自从成立三十年以来,环境成本会计已经发展到一定阶段,环境会计成本体系已经从以环境成本评估为基础的会计制度核心中分离出来(参考Fichter et al., 1997, Letmathe 和 Wagner , 2002)。
制造型企业环境成本控制研究外文文献翻译最新译文

毕业设计附件外文文献翻译:原文+译文文献出处: Markus G. The research of environment cost control in manufacturing enterprise [J]. International Journal of Production Economics, 2016, 2(3): 16-28.原文The research of environment cost control in manufacturing enterpriseMarkus GAbstractAlthough the development of manufacturing industry has brought the economic high growth, but at the same time we must see to the resources and the environment has brought great pressure, will restrict the sustainable development of manufacturing industry. From microscopic view, under the condition of the fierce market competition, manufacturing companies often from their own interests, environmental protection is generally only meet the minimum standards set by the government policy, resulting in a large number of environmental pollution by the society "to pay". However, as the environment problem increasingly prominent, and the increase of environmental protection demands, that the environmental responsibility on to their social situation will not exist. So the cost of manufacturing firms are active in environmental control will become particularly important, enterprise more environmental cost control as soon as possible, the more can meet the requirements of all aspects, to avoid the increasing environmental costs, to obtain competitive advantage, improve the economic benefit.Keywords: Manufacturing enterprise; Environmental cost; Value chain1 Research statusBemons (1971) and Malin (1973) the innovative put forward the concept of pollution of the environment accounting, they think the enterprise caused by the external environmental costs should be internalized. Park and Lee (2003) of environmental cost budget estimation methods are discussed in this paper. Robert and Frank (2005) studied to deal with the economic interests of the environment cost and time and space redistribution system method. Thomas, Robert and Daniel (2007) in financial analysis considering the external environmental costs and economic value added. Barnum (2009) on the basis of DEA analysis method, using the principle of materialbalance estimate input cost of coal, oil, natural gas and carbon dioxide output cost. Adam (2009) thinks the polluter pays principle (PPP) is still dominant in the cost allocation, and waste water treatments by purchasing power parity (PPP) explore the cross-border issues. Tran (2009) use economic model to study the shrimp and the relationship between the environmental costs of production.Yet Jeffrey a. (1994) argues that free trade will have far-reaching effect to the enterprise environment cost control. Julie a. Hewitt and Daniel k. Brown (2000), the study found that the environmental group manager for cost purposes rather than providing services received are marginal effect. Alan e. Rime r, PE, Dee, Black (2000) study found that organization and working process of the key factors is the company's environmental cost driver. John (2004) argues that environmental cost management consulting (ECMC) can help enterprises to evaluate its production cycle, reduce the enterprise environment cost. Hansen and Quintana (2007) discuss how to identify, track and monitor the environmental costs in order to improve enterprise's environmental performance. Robert (2008) design a comprehensive environmental quality management total cost assessment (TQEM - TCA) framework, to evaluate and control the environmental costs of some of the biggest companies in the United States. Gordon (2008) study shows that using the total cost management framework (TCM) can enhance the consistency and comparability of different kinds of environment cost estimation.Michael Porter for the first time put forward the concept of value chain, is to analyze the important tool of enterprise competitive advantage. Shank and Vijay expanded the potter the meaning of value chain; the enterprise's value chain should start the whole process of supplier to the user. Norman R and Ramirez R (1993) proposed the concept of value constellation, enterprises should pay attention to more capable to create value, and not stay to add value. Jeffrey and John (1995) put forward the concept of virtual value chain, the enterprise is present in the material and the virtual world, shall obtain the competitive advantages of the two world., (1996) argue that customer value chain is a unique competitive advantage, enterprises can not only strengthen the company management system, the characteristics of but also can improve the competitive advantage of enterprises. Alexandra j. Campbell (1998) studied the international cooperation's main trading partner on the value chain of influencing factors. Tom and Nick (1999) think that the method of value chain should include material distribution requirements planning, continuousreplenishment program, jointly managed inventory, etc. Stuart (2001) put forward the enterprise is not enough to have the ability to create value, the key is to be able to get what you create value. Merlin and Kevin (2002) in the value chain partners to share customer data is very important, and to explore different methods for sharing data and in commercial applications. Adam (2007) built a biform two-phase game model, the use of the model to quantitative analysis of the value chain of the relationship of value.2 Related theories2.1 Environment cost theory2.1.1 Concepts and characteristicsConsensus has not been formed the current definition of environmental costs, in this paper, with reference to the United Nations international accounting and reporting standards intergovernmental expert working group (ISAR) definition of environmental cost, environmental cost is to show the enterprise in line with those responsible for the environment for the principle, the initiative for environmental pollution control or the cost of what happens to be enforced, and enterprise in the activities of other costs. Environmental cost is an important part of enterprise cost, it has some characteristics different from other enterprise cost, main show is sudden, concealment, and increasing.2.1.2 The content of the environmental cost and classificationPredecessors have made more research on environment cost classification field, think of the content of environmental costs include not only the current after induction enterprise already bear the costs of environmental liability shall also include the enterprise had not, but the future is likely to be borne by the enterprises of the cost. Environmental costs include not only measurable environmental spending, should also include cannot clear measurement of environmental impact. Not only tangible environmental spending, including enterprise environment cost shall also include losing its environmental image of the invisible. From the point of the whole management process, according to enterprise's effects on the environment and environmental cost expenditure, in this paper, the environmental cost is divided into the following four categories:(1)Natural resource depletion costEnterprise will use in the production of economic activity, the consumption of natural resources, which reduce the number of resources value, is the cost of depletion of naturalresources. According to the renewable resources whether, natural resource depletion cost but also the specific classification of non-renewable resource depletion cost and cost of renewable resource depletion.(2) The cost of environmental degradationEnterprise production and operation of emissions than the quantity of the natural environment can carry,, in turn, led to the decrease of the quality of the environment, including the loss of value is the cost of environmental degradation, such as enterprise result in pollution of air, water, etc. Due to accurate verification of actual damage, caused the enterprise did not completely corresponding environmental responsibility.(3) The environment and resources protection costEnterprises in the process of its production and business operation will inevitably impact on environment and resources, in order to protect the environment and resources, to maintain their sustainable development and utilization of enterprises take measures of environmental resource protection, namely, cost. For example: in order to prevent and reduce pollution accidents, enterprise purchase the corresponding facilities extra spending, in order to improve employee knowledge of environmental protection of the training expenses, etc.(4) The environment and resources cost recovery and regenerationWhat we mean by environmental resources mainly include common human breathing air, minerals needed for the industrial production, most of the world's oceans, farming land, human creation of civilization heritage. Environmental resources recovery and regeneration cost is refers to the enterprise has caused damage to the environment resources, in order to restore what had happened to the cost. Such as the cost of industrial sewage purification, repeat use of the costs of waste, etc2.2 Environmental cost control theoryEnvironmental cost control is the enterprise to take corresponding measures will be formed to control the environmental cost of each items, trying to push the environmental cost control in reasonable level, in order to achieve environmental protection while promoting economic efficiency of enterprises. Environmental cost control is not a simple compression on environment cost, through the system control can improve the management level of enterprise environment cost. Enterprise environment cost control should have the following features:(1) ComprehensiveDue to the enterprise of adverse effects on the environment may was not reflected in the current, the internalization of environmental costs, including the enterprise has the burden of costs, shall also include the enterprise is likely to be borne by the enterprises environmental costs in the future. Therefore, the enterprise of the internalization of environment cost control should not only for cost control, for potential, externalized, considering the environmental cost shall remain at the same time, enterprises should also starting from the complete life cycle of a product or service, fully consider the cost of environment, and to control its each link.(2) The sustainabilityEnterprises to actively control the environmental cost will lead to spending, and in the short term, the enterprise environment cost control increased the burden of the enterprise, but in the long run, the enterprise to get higher utilization rate of raw materials, better product quality, lower environmental risks and benefits such as the cost of financing, which will increase the competitiveness of the enterprises, and is helpful to realize the sustainable development of enterprises.2.3 The value chain theoryThe McKinsey, a consultancy, opened up the value chain thought, followed by Michael Porter, Michael e. Porter) in his book the competitive advantage of the system elaborated the concept of value chain, with the continuous development of these years, the value chain is endowed with new meaning, the following lists the representative value chain thought, the traditional value chain refers to the value chain theory proposed by Michael Porter, the enterprise production and management mainly includes the research design, production, sales and support activities, all these activities can be expressed as the value chain. Enterprise value activities can be divided into basic activities and auxiliary activities further these two categories, basic activities can create value for enterprise directly; auxiliary activities just help create value for the basic activity, will not be able to create value directly. Peter, Peter Haynes (Hines) think enterprise value chain should be integrated material transit, the value of its different from the potter profit as the ultimate goal of enterprise value chain theory, thought he is only a by-product of meet customer demand for products. In addition, he wills also raw materials and customers of the two factors into their value system. Jeffrey and virtual value chain, d the carat puts forward the concept of virtual value chain.They think, under the background of information age, the value added in the enterprise value chain activities can be divided into based on some of the material resources and in the market place in the market based on the part of the information resources in the space. Which is based on material resources value-added activities constitute the traditional value chain, and based on the information resource is a virtual value chain, virtual value chain theory is that information is the important source of value?3 Environmental cost control model in real timeReal-time control is the enterprise in the information environment of product environmental cost information, this paper compares and analyzes the information in order to realize the real-time monitoring of environmental cost control. But considering the factors such as information transmission time, any real time delayed, and the real-time control mode is relative.3.1 Environmental cost control based on ERPUsing ERP system to control environmental cost is to use its plan, analysis, and other functions, each activity of the enterprise environment cost accounting. In the ERP environment, the enterprise will be in the business environment each link (inventory materials, production processes, production workshop, suppliers, customers, distributors and other business resources) combining, accurately and in a timely manner to all these aspects of dynamic monitor environmental cost information, so as to realize the effective control of the enterprise environment cost.3.2 Environmental cost control based on ABCEnvironmental cost control based on homework cost method is the homework cost method is used to achieve the goal of environmental cost control, the homework cost method of accounting object is each job, rather than directly to a product, embodied in: first, to confirm the enterprise use resources of all assignments, next to the cost of the consumption of resources allocated to the relevant work, finally put all the homework cost allocation to the product. For enterprise environmental cost occur through homework assigned to products, can reasonable distribution of environmental costs, eventually to achieve the environment of the enterprise cost control.译文制造型企业环境成本控制研究Markus G摘要虽然制造业的发展带来了经济的高增长,但同时我们必须看到给资源与环境带来了巨大的压力,将制约制造业的可持续发展;从微观来看,在激烈的市场竞争条件下,制造型企业通常从自身利益出发,环境保护普遍仅仅满足政府政策的最低要求,导致大量环境污染由社会“买单”。
企业成本控制外文文献翻译作业成本法2014年译文3300多字
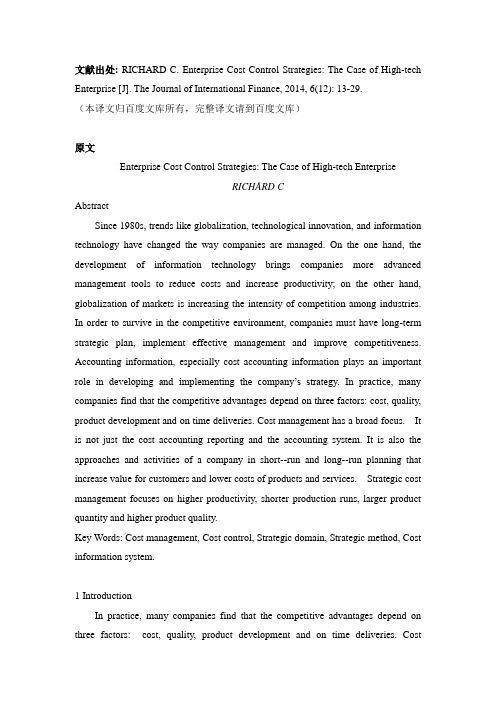
文献出处: RICHARD C. Enterprise Cost Control Strategies: The Case of High-tech Enterprise [J]. The Journal of International Finance, 2014, 6(12): 13-29.(本译文归百度文库所有,完整译文请到百度文库)原文Enterprise Cost Control Strategies: The Case of High-tech EnterpriseRICHARD CAbstractSince 1980s, trends like globalization, technological innovation, and information technology have changed the way companies are managed. On the one hand, the development of information technology brings companies more advanced management tools to reduce costs and increase productivity; on the other hand, globalization of markets is increasing the intensity of competition among industries. In order to survive in the competitive environment, companies must have long-term strategic plan, implement effective management and improve competitiveness. Accounting information, especially cost accounting information plays an important role in developing and implementing the company’s strategy. In practice, many companies find that the competitive advantages depend on three factors: cost, quality, product development and on time deliveries. Cost management has a broad focus. It is not just the cost accounting reporting and the accounting system. It is also the approaches and activities of a company in short--run and long--run planning that increase value for customers and lower costs of products and services. Strategic cost management focuses on higher productivity, shorter production runs, larger product quantity and higher product quality.Key Words: Cost management, Cost control, Strategic domain, Strategic method, Cost information system.1 IntroductionIn practice, many companies find that the competitive advantages depend on three factors: cost, quality, product development and on time deliveries. Costmanagement has a broad focus. It is not just the cost accounting reporting and the accounting system. It is also the approaches and activities of a company in short--run and long--run planning that increase value for customers and lower costs of products and services. Strategic ost management focuses on higher productivity, shorter production runs, larger product quantity and higher product quality. There are distinct differences both on concept and practice between strategic cost management and conventional cost management in high-tech companies. The purpose of this thesis is to do research on the cost management in high-tech companies and find more effective cost control methods that enable high-tech companies to reduce operating risk, improve competitiveness and succeed in competitive business world.2. Research methods and thoughtsIn this thesis, the author uses both theoretical research method and case study method. The author mainly uses typical cases when she employs case study method. For example, by analyzing the 3-year product life cycle income statements and cost reports of A information technology company, the author indicates that cost control in high-tech companies is not limited to production process but also includes product life cycle cost control. Besides, through MeiDi Air Conditioner zero inventory control case, the author concludes that high-tech companies can use Just-in-time production system to reduce procurement costs, increase inventory turnover rate and reduce inventory level so as to control total inventory costs. In addition, the author chooses W company as an example to prove that Activity-based Costing is a useful method for high-tech companies to control costs.Based on the characteristics of high-tech companies, the author concludes that conventional cost management is no longer suitable for the development of high-tech companies. Companies can use strategic cost management to improve competitiveness. In this thesis, the author first clarifies high-tech company’s cost control target. Next the author identifies the keyissues of cost control and points out some practical cost control methods that some high-tech companies currently use. Finally, the uthor believes it is necessary to establish a complete cost control information system to fulfill the cost control goals.3. Structure of the thesisThere are four chapters and about 57,000 words in this thesis. Cost management of high-tech companies. This chapter focuses on characteristics of high-tech company’s cost management and strategic cost management. In this chapter, the author defines the high-tech company, analyzes the characteristics of high-tech company, points out the limitation of conventional cost management, and proves that implementing strategic cost management can help high-tech company to identify competitive and obtain advantages .Identification of key issues in strategic cost control. The author first defines the term of cost control as a broad cost management concept, includes all the efforts to reduce costs. Next, the author analyzes and sets the strategic cost control goal. Then, the author identifies key issues of strategic cost control. These key issues include cost driver analysis, total product life cycle costs control, human capital control and product quality cost control.Application of strategic cost control method in high-tech companies. Cost management is not practiced in isolation. It is an integral part of general management strategies and their implementation. For example, Just-in-time production system is a comprehensive production and inventory management system. Companies can effectively control costs by combining Just-in-time production system and value chain analysis. Meanwhile, in order to control total costs of the product life cycle, company should emphasize the up-stream cost control. And target costing is very useful to control total costs of the product life cycle. Next, by analyzing high-tech company’s production environment and characteristics, the author suggests high-tech company also needs to control operation costs. At last, the author uses bothtraditional costing and ABC methods to compute W high-tech corporation’s operating income, indirect costs and profits. By comparing the difference of the results, the author concludes that ABC method is more accurate for the high-tech company to calculate costs. The operation cost control based on ABC method is more likely to satisfy the need of strategic cost management.4. Strengths of the thesisA new research perspective. The process of traditional research on cost control goes like this: definition of cost control — components of cost control —cost control principles —cost control process and methods. However, the author of this thesis first determines the cost control goals of high-tech companies. Based on the goals, the author clarifies the key issues of cost control and then chooses several practical cost control methods to do research. Finally, the author emphasizes that cost control must be supported by information system.New definition. In this thesis, cost control is same as cost management. It includes all the activities that could reduce product costs, such as product esigning, product producing, and marketing. It is necessary that all the departments coordinate together to conduct effective cost control.Focus on strategic cost management. Cost control is not only to reduce costs, it is also related to competition strategy, technology strategy, human capital management strategy and organization structure design. The company’s long-term goal is to obtain sustainable competitiveness. For high-tech companies, it is necessary to invest more money to produce better and differentiated products. Although the costs may rise with new product development, the companies can achieve their strategic goals by offering superior and unique products or service to customers.译文企业成本控制策略:以高新技术企业为例作者:理查德·科勒摘要20 世纪80 年代,人类开始进入信息社会时期。
成本控制外文文献(Costcontrol,foreignliterature)

成本控制外⽂⽂献(Costcontrol,foreignliterature)成本控制外⽂⽂献(Cost control, foreignliterature)成本控制外⽂⽂献(Cost control, foreign literature) 坎贝尔博⼠,坎贝尔,CPA杂志,在内部控制中增加了重要的价值在社会主义市场经济条件下,为企业⽣产经营取得良好的经济效益为⽬的,不断提⾼企业整体素质,在追求良好的经济效益的过程中,加强成本管理和控制,不断降低产品成本是⼀个重要的⽅法和⼿段。
那么,中⼩企业如何降低产品成本呢,从以下⼏个⽅⾯:1,近年来,原材料价格上涨,能源价格上涨的成本有很⼤的影响。
如何在存在这些不利因素的情况下降低成本,提⾼效率,企业必须树⽴技术改造观念,是通过技术改造降低成本的重要途径,采⽤新技术、新⼯艺、新材料,提⾼产品技术含量,为降低⽣产成本铺平了道路。
⼀是特别注重技术改造,积极采⽤新技术、新⼯艺,节能降耗,从根本上减少原材料的消耗,产品达到质量⽬标的同时,确保实现成本控制⽬标;⼆是技术改造项⽬建设的实施应要注意降低项⽬建设成本,注意到⽤较少的投资更多的回报。
2,深化企业改⾰,不断激发劳动者的劳动热情,提⾼职⼯素质,建⽴适应市场经济的⾼效运⾏机制,也是降低成本的重要环节。
作为企业效率的重要⼯作,每⼀个企业都要深化改⾰。
⾸先,改⾰⼈事制度,打破界限的⼲部职⼯,体现“,主管,⼯作好”的⽤⼈原则,整合招聘和⼈事制度聘任制,优化劳动组合和竞争,优胜劣汰,做“全能,前来认领”,所以为调动员⼯的积极性,提⾼劳动⽣产率,责任感和危机感,增强企业员⼯的⼯作意识,动员全体⼲部职⼯为作者的⼯作效率。
3,然⽽,产品的质量和产品的成本有着⾮常密切的关系。
在竞争条件下竞争激烈,谁的产品质量好,谁有竞争⼒,产品有市场,不会占⽤太多的钱;⾼质量、不合格项或更少的产品,可以直接降低⽣产成本;产品质量⾼,可以根据质量⽅针,在更⾼的价格出售,在销售收⼊中的⽐重相对降低成本;⾼质量的产品,才能赢得更多的客户,增加销售,降低销售成本;产品质量⾼,实际上也节省了能源和原材料;产品质量⾼,可节省⼈⼯和管理费⽤,这肯定会降低成本。
成本会计 外文翻译 外文文献 英文文献 中小企业环境成本会计的实施
成本会计外文翻译外文文献英文文献中小企业环境成本会计的实施IMPLEMENTING ENVIRONMENTAL COSTACCOUNTING IN SMALL AND MEDIUM-SIZEDCOMPANIES1(ENVIRONMENTAL COST ACCOUNTING IN SMESSince its inception some 30 years ago, Environmental Cost Accounting (ECA) has reached a stage of development where individual ECA systemsare separated from the core accounting system based an assessment of environmental costs with (see Fichter et al., 1997, Letmathe and Wagner , 2002).As environmental costs are commonly assessed as overhead costs, neither the older concepts of full costs accounting nor the relatively recent one of direct costing appear to represent an appropriate basisfor the implementation of ECA. Similar to developments in conventional accounting, the theoretical and conceptual sphere of ECA has focused on process-based accounting since the 1990s (see Hallay and Pfriem, 1992, Fischer and Blasius, 1995, BMU/UBA, 1996, Heller et al., 1995, Letmathe, 1998, Spengler and H.hre, 1998).Taking available concepts of ECA into consideration, process-based concepts seem the best option regarding the establishment of ECA (see Heupel and Wendisch , 2002). These concepts, however, have to becontinuously revised to ensure that they work well when applied in small and medium-sized companies.Based on the framework for Environmental Management Accounting presented in Burritt et al. (2002), our concept of ECA focuses on two main groups of environmentally related impacts. These areenvironmentally induced financial effects and company-related effects on environmental systems (see Burritt and Schaltegger, 2000, p.58). Each of these impacts relate to specific categories of financial and environmental information. The environmentally induced financial effects are represented by monetary environmental information and the effects on environmental systems are represented by physical environmental information. Conventional accounting deals with both – monetary as well as physical units – but does notfocus on environmental impact as such. To arrive at a practical solution to the implementation of ECA in a company’s existingaccounting system, and to comply with the problem ofdistinguishing between monetary and physical aspects, an integrated concept is required. As physical information is often the basis for the monetary information (e.g. kilograms of a raw material are the basis for the monetary valuation of raw material consumption), the integration1of this information into the accounting system database is essential. From there, the generation of physical environmental and monetary (environmental) information would in many cases be feasible. For manycompanies, the priority would be monetary (environmental) informationfor use in for instance decisions regarding resource consumptions and investments. The use of ECA in small and medium-sized enterprises (SME) is still relatively rare, so practical examples available in the literature are few and far between. One problem is that the definitions of SMEs vary between countries (see Kosmider, 1993 and Reinemann, 1999). In our work the criteria shown in Table 1 are used to describe small and medium-sized enterprises.Table 1. Criteria of small and medium-sized enterprisesNumber of employees TurnoverUp to 500 employees Turnover up to EUR 50mManagement Organization- Owner-cum-entrepreneur -Divisional organization is rare- Varies from a patriarchal management -Short flow of information stylein traditional companies and teamwork -Strong personal commitment in start-up companies -Instruction and controlling with- Top-down planning in old companies direct personal contact- Delegation is rare- Low level of formality- High flexibilityFinance Personnel- family company -easy to survey number of employees- limited possibilities of financing -wide expertise-high satisfaction of employeesSupply chain Innovation-closely involved in local -high potential of innovationeconomic cycles in special fields- intense relationship with customersand suppliers2Keeping these characteristics in mind, the chosen ECA approachshould be easy to apply, should facilitate the handling of complex structures and at the same time be suited to the special needs of SMEs.Despite their size SMEs are increasingly implementing Enterprise Resource Planning (ERP) systems like SAP R/3, Oracle and Peoplesoft. ERP systems support business processes across organizational, temporal and geographical boundaries using one integrated database. The primary use of ERP systems is for planning and controlling production and administration processes of an enterprise. In SMEs however, they are often individually designed and thus not standardized making the integration of for instance software that supports ECA implementation problematic. Examples could be tools like the “eco-ef ficiency” approach ofIMU (2003) or Umberto (2003) because these solutions work with the database of more comprehensive software solutions like SAP, Oracle, Navision or others. Umberto software for example (see Umberto, 2003)would require large investments and great background knowledge of ECA –which is not available in most SMEs.The ECA approach suggested in this chapter is based on anintegrative solution –meaning that an individually developed database is used, and the ECA solution adopted draws on the existing cost accounting procedures in the company. In contrast to other ECA approaches, the aim was to create an accounting system that enables the companies to individually obtain the relevant cost information. The aim of the research was thus to find out what cost information is relevant for the company’s decision on environmental issues andhow to obtain it.2(METHOD FOR IMPLEMENTING ECASetting up an ECA system requires a systematic procedure. Theproject thus developed a method for implementing ECA in the companiesthat participated in the project; this is shown in Figure 1. During the implementation of the project it proved convenient to form a core team assigned with corresponding tasks drawing on employees in various departments. Such a team should consist of one or two persons from the production department as well as two from accounting and corporate environmental issues, if available. Depending on the stage of theproject and kind of inquiry being considered, additional corporate members may be added to the project team to respond to issues such as IT, logistics, warehousing etc.Phase 1: Production Process Visualization3At the beginning, the project team must be briefed thoroughly on the current corporate situation and on the accounting situation. To this end, the existing corporate accounting structure and the related corporate information transfer should be analyzed thoroughly. Following theconcept of an input/output analysis, how materials find their ways into and out of the company is assessed. The next step is to present the flow of material and goods discovered and assessed in a flow model. To ensure the completeness and integrity of such a systematic analysis, any input and output is to be taken into consideration. Only a detailed analysisof material and energy flows from the point they enter the company until they leave it as products, waste, waste water or emissions enables the company to detect cost-saving potentials that at later stages of the project may involve more efficient material use, advanced process reliability and overview, improved capacity loads, reduced wastedisposal costs, better transparency of costs and more reliable assessment of legal issues. As a first approach, simplified corporate flow models, standardized stand-alone models for supplier(s), warehouse and isolated production segments were established and only combinedafter completion. With such standard elements and prototypes defined, a company can readily develop an integrated flow model with production process(es), production lines or a production process as a whole. From the view of later adoption of the existing corporate accounting to ECA,such visualization helps detect, determine, assess and then separate primary from secondary processes.Phase 2: Modification of AccountingIn addition to the visualization of material and energy flows, modeling principal and peripheral corporate processes helps prevent problems involving too high shares of overhead costs on the net product result. The flow model allows processes to be determined directly or at least partially identified as cost drivers. This allows identifying and separating repetitive processing activity with comparably few options from those with more likely ones for potential improvement.By focusing on principal issues of corporate cost priorities and on those costs that have been assessed and assigned to their causes least appropriately so far, corporate procedures such as preparing bids, setting up production machinery, ordering (raw) material and related process parameters such as order positions, setting up cycles of machinery, and order items can be defined accurately. Putting several partial processes with their isolated costs into4context allows principal processes to emerge; these form the basisof process-oriented accounting. Ultimately, the cost drivers of the processes assessed are the actual reference points for assigning and accounting overhead costs. The percentage surcharges on costs such as labor costs are replaced by process parameters measuring efficiency (see Foster and Gupta, 1990).Some corporate processes such as management, controlling and personnel remain inadequately assessed with cost drivers assigned to product-related cost accounting. Therefore, costs of the processes mentioned, irrelevant to the measure of production activity, have to be assessed and surcharged with a conventional percentage.At manufacturing companies participating in the project, computer-integrated manufacturing systems allow a more flexible and scope-oriented production (eco-monies of scope), whereas before only homogenous quantities (of products) could be produced under reasonable economic conditions (economies of scale). ECA inevitably preventseffects of allocation, complexity and digression and becomes a valuable controlling instrument where classical/conventional accounting arrangements systematically fail to facilitate proper decisions.Thus, individually adopted process-based accounting produces potentially valuable information for any kind of decision about internal processing or external sourcing (e.g. make-or-buy decisions).Phase 3: Harmonization of Corporate Data – Compiling andAcquisitionOn the way to a transparent and systematic information system, it is convenient to check core corporate information systems of procurement and logistics, production planning, and waste disposal with reference to their capability to provide the necessary precise figures for the determined material/energy flow model and for previously identified principal and peripheral processes. During the course of the project, afew modifications within existing information systems were, in most cases, sufficient to comply with these requirements; otherwise, a completely new software module would have had to be installed without prior analysis to satisfy the data requirements.Phase 4: Database conceptsWithin the concept of a transparent accounting system, process-based accounting can provide comprehensive and systematic information both on corporate material/ energy flows5and so-called overhead costs. To deliver reliable figures over time, it is essential to integrate a permanent integration of the algorithms discussed above into the corporate information system(s). Such permanent integration and its practical use may be achieved by applying one of three software solutions (see Figure 2).For small companies with specific production processes, anintegrated concept is best suited, i.e. conventional andenvironmental/process-oriented accounting merge together in one common system solution.For medium-sized companies, with already existing integrated production/ accounting platforms, an interface solution to such a system might be suitable. ECA, then, is set up as an independent software module outside the existing corporate ERP system and needs to be fed data continuously. By using identical conventions for inventory-datadefinitions within the ECA software, misinterpretation of data can be avoided.Phase 5: Training and CoachingFor the permanent use of ECA, continuous training of employees onall matters discussed remains essential. To achieve a long-term potential of improved efficiency, the users of ECA applications and systems must be able to continuously detect and integrate corporate process modifications and changes in order to integrate them into ECA and, later, to process them properly.6中小企业环境成本会计的实施一、中小企业的环境成本会计自从成立三十年以来,环境成本会计已经发展到一定阶段,环境会计成本体系已经从以环境成本评估为基础的会计制度核心中分离出来(参考Fichter et al., 1997, Letmathe和 Wagner , 2002)。
企业环境管理中英文对照外文翻译文献
企业环境管理中英文对照外文翻译文献企业环境管理中英文对照外文翻译文献(文档含英文原文和中文翻译)企业环境管理—基于市场奖励的管理企业保护环境的办法已经从被规章条例驱动的被动模式演变为积极主动的方式,即通过自愿管理做法,将环境问题与传统的管理职能结合起来。
作为公司决策的一种行为模式,通过econometrically假设测试取得影响公司积极进行环境管理的因素。
对这些假设进行测试时,使用的样本是标准普尔500指数公司的调查数据。
分析结果表明,经济因素,如环境负债的威胁和符合预期规定的高成本以及生产最终消费品和拥有大量资本产出率给企业带来的市场压力,都在促使这些企业进行环境保护的过程中发挥了显著作用。
此外,企业外部关于企业转移有毒物质的报道和社会大众对企业内部有毒物质单位排放量的压力都对企业通过创新实现环境管理的实践有重大影响。
导论传统上,美国依赖强制性的指挥和环境控制的规章来保护环境质量。
这种做法虽然保护了环境,但是也导致了政策框架的僵硬和高昂的成本,并且还会降低长远上改进环境质量的效率。
这种认识已经导致越来越多基于市场的手段应用于为企业提供灵活选择用最低成本控制污染的环境保护方式,例如排污许可证制度、存款还款计划和公众的环境信息披露自愿程序。
在这些措施中,信息披露的自愿性程序通过非强制性的措施鼓励企业控制污染。
监管机构向社会提供的关于产品环境属性和公司环境绩效的信息能触发产品和资本市场的反应和社会的行动,建立以市场为基础的激励机制,帮助企业改进其环境绩效。
美国环保局每年向社会公布的有毒物质排放清单就是信息提供的一个例子。
此外,争取让企业在环境自我调节的自愿性项目已经成为美国环保局的一个主要政策工具。
1999年,在联邦级别上,这样的项目已经在短短的三年中由28项增长到54项。
这两种做法已经被很多政策分析家看成是对抗性超越“政府推动”的“下一代环境政策”,其依靠企业自身在环境友好政策上的积极努力和社会公众,例如公民和社区的积极参与,来达到保护环境的目的。
成本控制中英文对照外文翻译文献
成本控制中英文对照外文翻译文献(文档含英文原文和中文翻译)原文:COST CONTROLRoger J. AbiNaderReference for Business,Encyclopedia of Business, 2nd ed.Cost control, also known as cost management or cost containment, is a broad set of cost accountingmethods and management techniques with the common goal of improving business cost-efficiency by reducing costs, or at least restricting their rate of growth. Businesses use cost control methods to monitor, evaluate, and ultimately enhance the efficiency of specific areas, such as departments, divisions, or product lines, within their operations.Control of the business entity , then, is essentially a managerial and supervisory function .Control consiets of those actions necessary to assur e that the entity’s resources and operations are focused on attaining established objectives , goals and plans. Control, exercised continuously, flags potential problems so that crises may be prevented. It also standardizeds the quantity of output , and provides managers with objective information about employee performance . Management compares actual performance to predetermined standards and takes action when necessary to correct variances from the standards.Keywords : Cost control, Applications, Control reports, Standards, Strategic Cost control, also known as cost management or cost containment, is a broad set of cost accountingmethods and management techniques with the common goal of improving business cost-efficiency by reducing costs, or at least restricting their rate of growth. Businesses use cost control methods to monitor, evaluate, and ultimately enhance the efficiency of specific areas, such as departments, divisions, or product lines, within their operations.During the 1990s cost control initiatives received paramount attention from corporate America. Often taking the form of corporate restructuring, divestmentof peripheral activities, mass layoffs,or outsourcing,cost control strategies were seen as necessary to preserve—or boost—corporate profits and to maintain—or gain—a competitive advantage. The objective was often to be the low-cost producer in a given industry, which would typically allow the company to take a greater profit per unit of sales than its competitors at a given price level.Some cost control proponents believe that such strategic cost-cutting must be planned carefully, as not all cost reduction techniques yield the same benefits. In a notable late 1990s example, chief executive Albert J. Dunlap, nicknamed "Chainsaw Al" because of his penchant for deep cost cutting at the companies he headed, failed to restore the ailing small appliance maker Sunbeam Corporation to profitability despite his drastic cost reduction tactics. Dunlap laid off thousands of workers and sold off business units, but made little contribution to Sunbeam's competitive position or share price in his two years as CEO. Consequently, in 1998 Sunbeam's board fired Dunlap, having lost confidence in his "one-trick" approach to management.COST CONTROL APPLICATIONSA complex business requires frequent information about operations in order to plan for the future, to control present activities, and to evaluate the past performance of managers, employees, and related business segments. To be successful, management guides the activities of its people in the operations of the business according to pre-established goal and objectives. Management’s guidance takestwo forms of control: (1) the management and supervision of behuvior , and (2) the evaluation of performance.Behavioral management deals with the attitudes and actions of employees. While employee behavior ultimately impacts on success, behavioral management involves certain issues and assumptions not applicable to accounting's control function. On the other hand, performance evaluation measures outcomes of employee's actions by comparing the actual results of business outcomes to predetermined standards ofsuccess. In this way management identifies the strengths it needs to maximize, and the weaknesses it seeks to rectify. This process of evaluation and remedy is called cost control.Cost control is a continuous process that begins with the proposed annual budget. The budget helps: (1) to organize and coordinate production, and the selling, distribution, service, and administrative functions; and (2) to take maximum advantage of available opportunities. As the fiscal year progresses, management compares actual results with those projected in the budget and incorporates into the new plan the lessons learned from its evaluation of current operations.Control refers to management's effort to influence the actions of individuals who are responsible for performing tasks, incurring costs, and generating revenues. Management is a two-phased process: planningrefers to the way that management plans and wants people to perform, while controlrefers to the procedures employed to determine whether actual performance complies with these plans. Through the budget process and accounting control, management establishes overall company objectives, defines the centers of responsibility, determines specific objectives for each responsibility center, and designs procedures and standards for reporting and evaluation.A budget segments the business into its components or centers where the responsible party initiates and controls action. Responsibility centersrepresent applicable organizational units, functions, departments, and divisions. Generally a single individual heads the responsibility center exercising substantial, if not complete, control over the activities of people or processes within the center and controlling the results of their activity. Cost centersare accountable only for expenses, that is, they do not generate revenue. Examples include accounting departments, human resources departments, and similar areas of the business that provide internal services. Profit centersaccept responsibility for both revenue and expenses. For example, a product line or an autonomous business unit might be considered profit centers. If the profit center has its own assets, it may also be considered an investment center,for which returns on investment can be determined. The use of responsibility centers allows management todesign control reports to pinpoint accountability, thus aiding in profit planning.A budget also sets standards to indicate the level of activity expected from each responsible person or decision unit, and the amount of resources that a responsible party should use in achieving that level of activity. A budget establishes the responsibility center, delegates the concomitant responsibilities, and determines the decision points within an organization.The planning process provides for two types of control mechanisms:Feedforward: providing a basis for control at the point of action (the decision point); andFeedback: providing a basis for measuring the effectiveness of control after implementation.Management's role is to feedforwarda futuristic vision of where the company is going and how it is to get there, and to make clear decisions coordinating and directing employee activities. Management also oversees the development of procedures to collect, record, and evaluate feedback.Therefore, effective management controls results from leading people by force of personality and through persuasion; providing and maintaining proper training, planning, and resources; and improving quality and results through evaluation and feedback.Control reports are informational reports that tell management about an entity's activities. Management requests control reports only for internal use, and, therefore, directs the accounting department to develop tailor-made reporting formats. Accounting provides management with a format designed to detect variations that need investigating. In addition, management also refers to conventional reports such as the income statement and funds statement, and external reports on the general economy and the specific industry.Control reports, then, need to provide an adequate amount of information so that management may determine the reasons for any cost variances from the original budget.A good control report highlights significant information by focusing management's attention on those items in which actual performance significantly differs from thestandard.Because key success factors shift in type and number, accounting revises control reports when necessary. Accounting also varies the control period covered by the control report toencompass a period in which management can take useful remedial action. In addition, accountingdisseminates control reports in a timely fashion to give management adequate time to act before the issuance of the next report.Managers perform effectively when they attain the goals and objectives set by the budget. With respect to profits, managers succeed by the degree to which revenues continually exceed expenses. In applying the following simple formula, managers, especially those in operations, realize that they exercise more control over expenses than they do over revenue.While they cannot predict the timing and volume of actual sales, they can determine the utilization rate of most of their resources, that is, they can influence the cost side. Hence, the evaluation of management's performance and its operations is cost control.For cost control purposes, a budget provides standard costs. As management constructs budgets, it lays out a road map to guide its efforts. It states a number of assumptions about the relationships and interaction among the economy, market dynamics, the abilities of its sales force, and its capacity to provide the proper quantity and quality of products demanded.Accounting plays a key role in all planning and control. It does this in four key areas: (1) data collection, (2) data analysis, (3) budget control and administration, and (4) consolidation and review.The accountants play a key role in designing and securing support for the procedural aspects of the planning process. In addition, they design and distribute forms for the collection and booking of detailed data on all aspects of the business.Although operating managers have the main responsibility of planning, accounting compiles and coordinates the elements. Accountants subject proposed budgets to feasibility and profitability analyses to determine conformity to accepted standards andpractices.Management relies on such accounting data and analysis to choose from several cost control alternatives, or management may direct accounting to prepare reports specifically for evaluating such options. As the Chainsaw Al episode indicated, all costs may not be viable targets for cost-cutting measures. For instance, in mass layoffs, the company may lose a significant share of its human capitalby releasing veteran employees who are experts in their fields, not to mention by creating a Decline in morale among those who remain. Thus management must identify which costs have strategic significance and which do not.To determine the strategic impact of cost-cutting, management has to weigh the net effects of the proposed change on all areas of the business. For example, reducing variable costs related directly to manufacturing a product, such as materials and transportation costs, could be the key to greater incremental profits. However, management must also consider whether saving money on production is jeopardizing other strategic interests like quality or time to market. If a cheaper material or transportation system negatively impacts other strategic variables, the nominal cost savings may not benefit the company in the bigger picture, e.g., it may lose sales. In such scenarios, managers require the discipline not to place short-term savings over long-term interests.One trend in cost control has been toward narrowing the focus of corporate responsibility centers, and thereby shifting some of the cost control function to day-to-day managers who have the most knowledge of and influence over how their areas spend money. This practice is intended to promote bottom-up cost control measures and encourage a widespread consensus over cost management strategies.Control of the business entity, then, is essentially a managerial and supervisory function. Control consists of those actions necessary to assure that the entity's resources and operations are focused on attaining established objectives, goals and plans. Control, exercised continuously, flags potential problems so that crises may be prevented. It also standardizes the quality and quantity of output, and provides managers with objectiveinformation about employee performance. Management compares actual performance to predetermined standards and takes action when necessary to correct variances from the standards.译文:成本控制成本控制成本控制,也被称为遏制成本或管理成本,一个广阔的成本管理技术,它的经济增长目标是降低成本提高企业效率。
精编【财务会计管理】企业环境成本会计外文翻译
【财务会计管理】企业环境成本会计外文翻译xxxx年xx月xx日xxxxxxxx集团企业有限公司Please enter your company's name and contentvIMPLEMENTING ENVIRONMENTAL COSTACCOUNTING IN SMALL AND MEDIUM-SIZEDCOMPANIES1.ENVIRONMENTAL COST ACCOUNTING IN SMESSince its inception some 30 years ago, Environmental Cost Accounting (ECA) has reached a stage of development where individual ECA systems are separated from the core accounting system based an assessment of environmental costs with (see Fichter et al., 1997, Letmathe and Wagner , 2002).As environmental costs are commonly assessed as overhead costs, neither the older concepts of full costs accounting nor the relatively recent one of direct costing appear to represent an appropriate basis for the implementation of ECA. Similar to developments in conventional accounting, the theoretical and conceptual sphere of ECA has focused on process-based accounting since the 1990s (see Hallay and Pfriem, 1992, Fischer and Blasius, 1995, BMU/UBA, 1996, Heller et al., 1995, Letmathe, 1998, Spengler and H.hre, 1998).Taking available concepts of ECA into consideration, process-based concepts seem the best option regarding the establishment of ECA (see Heupel and Wendisch , 2002). These concepts, however, have to be continuously revised to ensure that they work well when applied in small and medium-sized companies.Based on the framework for Environmental Management Accounting presented in Burritt et al. (2002), our concept of ECA focuses on two maingroups of environmentally related impacts. These are environmentally induced financial effects and company-related effects on environmental systems (see Burritt and Schaltegger, 2000, p.58). Each of these impacts relate to specific categories of financial and environmental information. The environmentally induced financial effects are represented by monetary environmental information and the effects on environmental systems are represented by physical environmental information. Conventional accounting deals with both –monetary as well as physical units –but does not focus on environmental impact as such. T o arrive at a practical solution to the implementation of ECA in a company’s existing accounting system, and to comply with the problem of distinguishing between monetary and physical aspects, an integrated concept is required. As physical information is often the basis for the monetary information (e.g. kilograms of a raw material are the basis for the monetary valuation of raw material consumption), the integration of this information into the accounting system database is essential. From there, the generation of physical environmental and monetary (environmental) information would in many cases be feasible. For many companies, the priority would be monetary (environmental) information for use in for instance decisions regarding resource consumptions and investments. The use of ECA in small and medium-sized enterprises (SME) is still relatively rare, so practical examples available in the literature are few and far between. One problem is that the definitions of SMEs vary between countries (see Kosmider, 1993 and Reinemann,1999). In our work the criteria shown in Table 1 are used to describe small and medium-sized enterprises.Table 1. Criteria of small and medium-sized enterprisesNumber of employees TurnoverUp to 500 employees Turnover up to EUR 50mManagement Organization- Owner-cum-entrepreneur -Divisional organization is rare- Varies from a patriarchal management -Short flow of information stylein traditional companies and teamwork -Strong personal commitmentin start-up companies -Instruction and controlling with- Top-down planning in old companies direct personal contact- Delegation is rare- Low level of formality- High flexibilityFinance Personnel- family company -easy to survey number ofemployees- limited possibilities of financing -wide expertise-high satisfaction of employeesSupply chain Innovation-closely involved in local -high potential of innovationeconomic cycles in special fields- intense relationship with customersand suppliersKeeping these characteristics in mind, the chosen ECA approach should be easy to apply, should facilitate the handling of complex structures and at the same time be suited to the special needs of SMEs.Despite their size SMEs are increasingly implementing Enterprise Resource Planning (ERP) systems like SAP R/3, Oracle and Peoplesoft. ERP systems support business processes across organizational, temporal and geographical boundaries using one integrated database. The primary use of ERP systems is for planning and controlling production and administration processes of an enterprise. In SMEs however, they are often individually designed and thus not standardized making the integration of for instance software that supports ECA implementation problematic. Examples could be tools like the “eco-efficiency” approach of IMU (2003) or Umberto (2003) because these solutions work with the database of more comprehensive software solutions like SAP, Oracle, Navision or others. Umberto software for example (see Umberto, 2003) would require large investments and great backgroundknowledge of ECA – which is not available in most SMEs.The ECA approach suggested in this chapter is based on an integrative solution –meaning that an individually developed database is used, and the ECA solution adopted draws on the existing cost accounting procedures in the company. In contrast to other ECA approaches, the aim was to create an accounting system that enables the companies to individually obtain the relevant cost information. The aim of the research was thus to find out what cost information is relevant for the company’s decision on environmental issues and how to obtain it.2.METHOD FOR IMPLEMENTING ECASetting up an ECA system requires a systematic procedure. The project thus developed a method for implementing ECA in the companies that participated in the project; this is shown in Figure 1. During the implementation of the project it proved convenient to form a core team assigned with corresponding tasks drawing on employees in various departments. Such a team should consist of one or two persons from the production department as well as two from accounting and corporate environmental issues, if available. Depending on the stage of the project and kind of inquiry being considered, additional corporate members may be added to the project team to respond to issues such as IT, logistics, warehousing etc.Phase 1: Production Process VisualizationAt the beginning, the project team must be briefed thoroughly on thecurrent corporate situation and on the accounting situation. To this end, the existing corporate accounting structure and the related corporate information transfer should be analyzed thoroughly. Following the concept of an input/output analysis, how materials find their ways into and out of the company is assessed. The next step is to present the flow of material and goods discovered and assessed in a flow model. T o ensure the completeness and integrity of such a systematic analysis, any input and output is to be taken into consideration. Only a detailed analysis of material and energy flows from the point they enter the company until they leave it as products, waste, waste water or emissions enables the company to detect cost-saving potentials that at later stages of the project may involve more efficient material use, advanced process reliability and overview, improved capacity loads, reduced waste disposal costs, better transparency of costs and more reliable assessment of legal issues. As a first approach, simplified corporate flow models, standardized stand-alone models for supplier(s), warehouse and isolated production segments were established and only combined after completion. With such standard elements and prototypes defined, a company can readily develop an integrated flow model with production process(es), production lines or a production process as a whole. From the view of later adoption of the existing corporate accounting to ECA, such visualization helps detect, determine, assess and then separate primary from secondary processes.Phase 2: Modification of AccountingIn addition to the visualization of material and energy flows, modeling principal and peripheral corporate processes helps prevent problems involving too high shares of overhead costs on the net product result. The flow model allows processes to be determined directly or at least partially identified as cost drivers. This allows identifying and separating repetitive processing activity with comparably few options from those with more likely ones for potential improvement.By focusing on principal issues of corporate cost priorities and on those costs that have been assessed and assigned to their causes least appropriately so far, corporate procedures such as preparing bids, setting up production machinery, ordering (raw) material and related process parameters such as order positions, setting up cycles of machinery, and order items can be defined accurately. Putting several partial processes with their isolated costs into context allows principal processes to emerge; these form the basis of process-oriented accounting. Ultimately, the cost drivers of the processes assessed are the actual reference points for assigning and accounting overhead costs. The percentage surcharges on costs such as labor costs are replaced by process parameters measuring efficiency (see Foster and Gupta, 1990).Some corporate processes such as management, controlling and personnel remain inadequately assessed with cost drivers assigned to product-related cost accounting. Therefore, costs of the processes mentioned, irrelevant to the measure of production activity, have to be assessed and surcharged with aconventional percentage.At manufacturing companies participating in the project, computer-integrated manufacturing systems allow a more flexible and scope-oriented production (eco-monies of scope), whereas before only homogenous quantities (of products) could be produced under reasonable economic conditions (economies of scale). ECA inevitably prevents effects of allocation, complexity and digression and becomes a valuable controlling instrument where classical/conventional accounting arrangements systematically fail to facilitate proper decisions.Thus, individually adopted process-based accounting produces potentially valuable information for any kind of decision about internal processing or external sourcing (e.g. make-or-buy decisions).Phase 3: Harmonization of Corporate Data – Compiling and Acquisition On the way to a transparent and systematic information system, it is convenient to check core corporate information systems of procurement and logistics, production planning, and waste disposal with reference to their capability to provide the necessary precise figures for the determined material/energy flow model and for previously identified principal and peripheral processes. During the course of the project, a few modifications within existing information systems were, in most cases, sufficient to comply with these requirements; otherwise, a completely new software module would have had to be installed without prior analysis to satisfy the data requirements.Phase 4: Database conceptsWithin the concept of a transparent accounting system, process-based accounting can provide comprehensive and systematic information both on corporate material/ energy flows and so-called overhead costs. To deliver reliable figures over time, it is essential to integrate a permanent integration of the algorithms discussed above into the corporate information system(s). Such permanent integration and its practical use may be achieved by applying one of three software solutions (see Figure 2).For small companies with specific production processes, an integrated concept is best suited, i.e. conventional and environmental/process-oriented accounting merge together in one common system solution.For medium-sized companies, with already existing integrated production/ accounting platforms, an interface solution to such a system might be suitable. ECA, then, is set up as an independent software module outside the existing corporate ERP system and needs to be fed data continuously. By using identical conventions for inventory-data definitions within the ECA software, misinterpretation of data can be avoided.Phase 5: Training and CoachingFor the permanent use of ECA, continuous training of employees on all matters discussed remains essential. T o achieve a long-term potential of improved efficiency, the users of ECA applications and systems must be able to continuously detect and integrate corporate process modifications andchanges in order to integrate them into ECA and, later, to process them properly.中小企业环境成本会计的实施一、中小企业的环境成本会计自从成立三十年以来,环境成本会计已经发展到一定阶段,环境会计成本体系已经从以环境成本评估为基础的会计制度核心中分离出来(参考Fichter et al., 1997, Letmathe 和Wagner , 2002)。
- 1、下载文档前请自行甄别文档内容的完整性,平台不提供额外的编辑、内容补充、找答案等附加服务。
- 2、"仅部分预览"的文档,不可在线预览部分如存在完整性等问题,可反馈申请退款(可完整预览的文档不适用该条件!)。
- 3、如文档侵犯您的权益,请联系客服反馈,我们会尽快为您处理(人工客服工作时间:9:00-18:30)。
文献出处: Markus A. The research of circular economy and the enterprise environment cost control [J]. Journal of Cleaner Production, 2016, 1(3): 215-227.原文The research of circular economy and the enterprise environment cost controlMarkus AAbstractSince middle period of last century, with the rapid development of economic and social and environmental problems those human beings are facing increasingly serious. Atmospheric pollution, global warming, resource supply tension, biological species loss, serious soil and water loss, noise pollution, waste and environment problems are serious threat to human survival and development. Environmental protection and rational utilization of resources has become a common problem that human beings are facing. According to the environmental protection department statistics, 70% of the world's environmental pollution from the production and business operation activities of enterprise, especially in manufacturing enterprises, they each year about more than 50, one hundred million tones of waste harmless and nearly one billion tons of hazardous waste. Therefore, the research enterprise environment management is very important to solve the problem of the human environment pollution.Keywords: Circular economy; Environmental cost; The cost control1 IntroductionAt present, the economy is growing, but the environmental pollution, ecological imbalance and a series of environmental problems are growing. How to adapt to the current circular economy concept, in promoting enterprise contribute to the sustainable development of the society at the same time, realize the sustainable development of its business, and has become the common focus of attention of the international accounting field. Under this premise, the enterprise environment cost management arises at the historic moment. Environmental cost control is a key link of cost management implementation environment, directly affects the success or failure of environmental cost management. In this paper, from the Angle of view of theconcept of circular economy, in the further study of the scholars of environmental cost control model is established and the related environmental cost management theory, on the basis of reference to the quality cost control ideas, build enterprise dynamic environmental quality cost model, the environmental cost control research is quantified and the model, and from the perspective of circular economy enterprise environment cost control strategy, the last on how to perfect the enterprise environment cost control put forward the corresponding countermeasure and the suggestion, for enterprises to strengthen environmental cost management to provide some theoretical reference and support for the decision of its environmental costs. The traditional development view is to pure economic growth as a measure of the development of the main sign. This development idea to bring to mankind the rapid economic growth, at the same time brought about by the negative effect is obvious, that is the shortage of resources, ecological damage, threats to the sustainable development of the human society. Therefore, in order to deal with this dilemma, the concept of "sustainable development", namely, economic development should be fair and consistent and intergenerational fairness and generation. Since the end of last century to establish sustainable development strategy, taking the path of circular economy and constructing circular society has received universal around the world and become a very important channel for the sustainable development in the developed countries and many countries are in the form of legislation to promote and circular economy in the future a long period of time will become a development trend and trend.2 Literature reviewEnvironmental cost accounting is an important new field, than moons (Beams.F.A), published in the journal of accounting is research on the social cost of pollution control in marine (Marlin. Jet.) And spublished accounting problems of pollution, is recognized to be the beginning of the research on enterprises environmental cost. United Nations conference on international accounting and reporting standard intergovernmental panel research on environment cost also early, once disclosure of environmental cost is conducted in-depth research for a long time. The group in 1998approved the announcement of the position of environmental accounting and reporting is considered to be one of the first international guidelines of environmental accounting and report, the announcement from the Angle of the destruction of the environmental impact for the first time to define the concept of environmental cost, namely enterprise adverse effects on the environment and to prevent the business activities or be forced to take measures of costs and other related costs, enforce environmental standards announcement lists to keep and improve the air quality at the same time, carry out environmental audit and inspection cost, the fines, compensation and other costs related to environment, although is beyond the scope of the concept of environmental cost, but also should be disclosed in a timely manner. It is now accepted that is a definition of science. U.S. Environmental Protection Agency (United States Environmental Protection Agency, hereinafter referred to as U.S.E PA) published in 1995, the enterprise management tools, environment accounting is introduced: key concepts and terminology ", defined the concept of Environmental costs, to the enterprise listed companies the possibility of Environmental cost and the classification. The environmental cost is defined as: environmental loss cost, refers to the expenses and costs caused by pollution their spending. Environmental protection costs, is refers to the enterprise and the pollution sources of the isolation of various costs, such as to prevent the noise pollution and the costs of anti noise equipment purchase. Transaction cost, environment refers to the management environment of information processing cost. To eliminate environmental pollution costs, is to eliminate pollution and related costs, such as governance white pollution and the degradation of expenses, etc. At the same time, the environmental cost is further divided into traditional cost, accidental cost; potential hidden costs associated with the image of four categories, such as part and for the first time because of the environmental load to the irrelevant third party or social loss is caused by the social costs are included. The book because of its strong operability and become the technology of enterprise environment cost management practice guidelines. The Canadian association of chartered accountants (CICA) (1993) the environmental cost is classified as environmental loss cost and environmental cost. Environmental cost isrefers to as a result of damage to the environment and the enterprise bear the compensation, environmental governance costs, damages, fines, etc., countermeasures for environmental cost take countermeasures and environmental protection activities for related expenses.1999 Japanese environment agency audit and passed "the guidance of grasping and disclosure about the cost of environment preservation key point, from the specific content of environment preservation costs on the definition, also expounds the general format of environment preservation cost disclosure. The report will be environmental preservation cost is defined as: in order to reduce the enterprise production activities of the adverse effects on the environment and related costs. Dutch national bureau of statistics (CBS) (2000) definition of environmental costs into the cost of environmental protection, and environmental protection is refers to the "due to prevent adverse effects on the environment caused by the environmental behavior", the definition contains the narrow scope of the environment cost, according to this definition, net financial benefits for the enterprise's activities are not included in the enterprise environment, to protect the surrounding community housing security for the purpose of behavior were excluded.3 The theory foundation of enterprise environment cost3.1 The external economy theoryThe university of Cambridge, Marshall and pious is put forward for the first time in the last century "externalities" this concept, it is to point to when a behavior of economic agents (or individual consumer behavior) to the other main body or person caused by the influence of uncontrollable, there are externalities. Externalities according to the result of its impact on the rest of the body and can be divided into external economy and external economy. Because adverse effect to the outside world is called external diseconomy, he refers to some businesses or individuals neither for other enterprises and individual economic activities adversely affected, nor from the impact of these companies and individuals to get compensation of economic phenomena, such as river upstream paper mill discharge sewage, caused the downstream harvest crops, agricultural production condition. Main aim of the research environment problem of externality is adopted the method of economicmanagement, explore the root causes of environmental problems (external diseconomy), namely the externalities of production and consumption and the influence of it, and put forward the solution to environmental pollution and ecological destruction this external diseconomy problems the feasibility of the scheme.3.2 The sustainable development theoryLed by the Norwegian prime minister, world commission on environment and development in 1987, in "our common future" in the report puts forward the definition of sustainable development. Sustainable development refers to satisfy the need of the current and the contemporary, and will never be a threat to the ability of future generations to meet their needs of development mode. Theory of sustainable development for economy and society, human and the nature coordinated development, slam the door simply will develop as strengthening the manpower, equipment, and natural input output growth process of traditional attitudes. Sustainable development is based on protecting natural resources and environment, to encourage economic development conditions, to improve and enhance the quality of human life as the goal, the use of resources accounting system for the resource pricing, through the innovation of science and technology and social system, promote efficient and clean production, improve the natural resources and ecological sustainability.3.3 The circulation economic theoryIn the 1960 s the famous American economist Kenneth Bohr was first put forward the concept of this new circular economy. He was in the "economics of spacecraft compare the entire earth's economic system to a spaceship, and argues that only by strengthening the earth system itself resources circulation way to realize the sustainable development of the whole earth system. This kind of economic ideas have greatly promoted the international economic research resources and the environment. Proposed to the traditional way depends on the development of resource consumption to promote economic growth to rely on ecological resources circulation mode of economic development. In general, the Circular Economy (Circular pa) is the term for Material closed-loop flow type (Closing Material Cycle) is short for the Economy, is the Material, characteristics, cascade and closed Cycle use for energy performance inthe use of resources and environment for efficient utilization of resources, low pollution emissions, and pollution "zero emissions". In essence, the circular economy is a kind of ecological economy, he asked the integrated use of ecology law to guide the economic activities of human beings, not just based on the traditional mechanistic. Its characteristic is to put the clean production and recycling of waste, its core is the resource recycling and saving, the maximum improve efficiency of resource utilization, so as to realize resource conservation, improve efficiency and reduce pollution.3.4 The clean production theorySince the middle of the last century, began to pay more attention to environmental issues. Each country began to invest huge manpower and increase investment in equipment and technology research and development to the governance of the pollutants in the process of production, although certain achievements have been made but the way of the end is still not ideal. Cleaner production is at the end of the adopted corresponding environmental protection measures and countermeasures have failed to meet expectations of pollution control target under the background of innovative environmental management thoughts. Its focus is on pollution prevention before, through the enterprise production process control, eliminate pollution from the source. It's called also each are not identical in different countries, but they just focus on different aspects of clean production and essentially the same. For example: Japan known as the "pollution-free technology", Germany and France, known as the "no by-product production", north American countries known as the "pollution prevention", in addition to these common appellation, other areas also call it "green production", etc.译文循环经济与企业环境成本控制研究Markus A摘要自上世纪中期以来,随着经济和社会的快速发展,人类面临的环境问题日益严重。