数控车床电气控制系统改造
ca6140数控车床plc改造
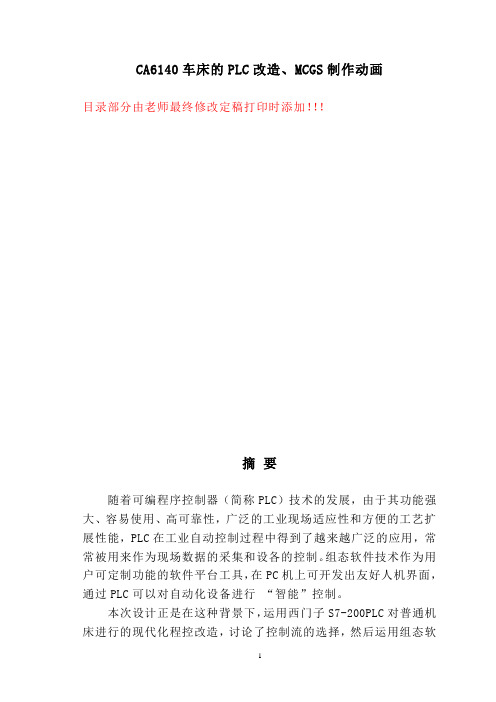
CA6140车床的PLC改造、MCGS制作动画目录部分由老师最终修改定稿打印时添加!!!摘要随着可编程序控制器(简称PLC)技术的发展,由于其功能强大、容易使用、高可靠性,广泛的工业现场适应性和方便的工艺扩展性能,PLC在工业自动控制过程中得到了越来越广泛的应用,常常被用来作为现场数据的采集和设各的控制。
组态软件技术作为用户可定制功能的软件平台工具,在PC机上可开发出友好人机界面,通过PLC可以对自动化设备进行“智能”控制。
本次设计正是在这种背景下,运用西门子S7-200PLC对普通机床进行的现代化程控改造,讨论了控制流的选择,然后运用组态软件对PLC控制系统进行人机界面的监控。
关键词:可编程序控制器,控制流,组态软件ABSTRACTWith the Programmable Logic Controller (PLC) technology, because of its powerful, easy to use, high reliability, wide adaptability and convenience of industrial processes on site scalability, PLC in industrial automation during the process of the Yue and more widely used, often used as a field data collection and set the control. Configuration software technology as a function of user customizable software platform tool, PC, a friendly interface that can bedeveloped through the PLC automation equipment can be "intelligent" control.The design is in this context, using Siemens S7-200PLC modernization of the ordinary program-controlled machine tools for transformation, discussed the control flow of the choice and then use the configuration software on the PLC control system man-machine interface control.KEY WORDS: programmable logic controller, control flow, configuration software目录摘要 (1)前言 (5)第1章绪论 (6)1.1 程控机床的发展前景及意义 (6)1.2 机床改造方案的确定及系统的选择 (7)1.2.1 CA6140车床的概述 (7)1.2.2 对CA6140车床控制系统的选择 (10)第2章控制系统设计 (17)2.1 控制要求 (21)2.2 控制流的选择 (21)2.3 系统的控制过程 (23)第3章系统的硬件设计 (24)3.1 系统的组成 (24)3.2 系统主电路的设计............... 错误!未定义书签。
GS30数控车床电气控制系统改造设计
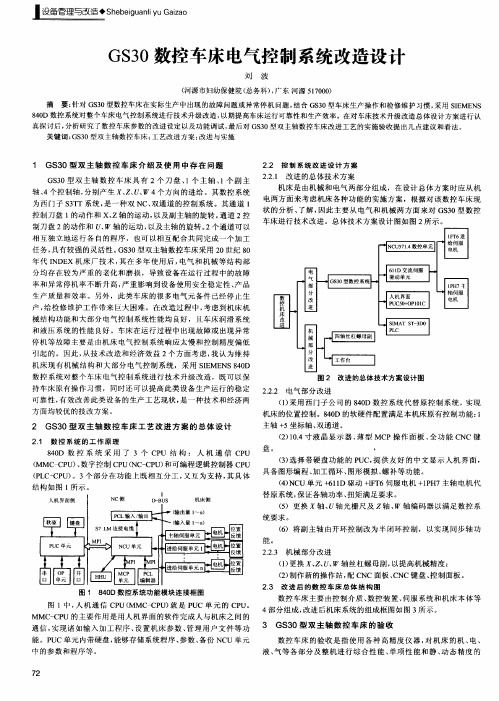
给 伺 服 电机
年代 I E ND X机 床 厂 技 术 , 在 多年 使用 后 , 其 电气 和 机 械 等 结构 部
分 均存 在较 为 严重 的老化 和磨 损 ,导致 设备 在运 行 过程 中 的故 障
率和 异 常 停机 率不 断 升高 , 重 影 响到 设备 使用 安 全稳 定性 、 品 严 产 生 产质 量 和效 率 。另 外 ,此类 车床 的很 多 电气 元 备件 已经 停止 生
停机 等 故 障主 要是 由机 床 电气 控 制系 统 响应 太慢 和 控制 精 度偏 低
电 气 部 分 改进一
一机 械 部 分 改 进
四轴丝杠螺母副
引起 的。 因此 , 技术 改造 和 经济 效益 2 方 面考 虑 , 认 为维 持 从 个 我 机床 现 有 机械 结构 和大 部 分 电气 控 制 系统 ,采 用 SE N 4D IME S80 数摔 系 统对 整 个车 床 电气 控 制系 统进 行 技术 升 级改 造 ,既 可 以保
l
量 sbul _ heay a。 einu z g iGa
GS 0数控车 床 电气控制系统改造设 计 3
刘 波
( 源 市 妇 幼 保健 院 ( 务 科 ) 广 东 河 源 5 7 0 ) 河 总 , 100
摘
要: 针对 GS 0型数控车床在 实际生产中 出现 的故障问题或异 常停机 问题 , 3 结合 GS 0型车床 生产操作和检 修维护 习惯 , 用 SE NS 3 采 IME
工 作 台
图 2 改进的总体技术方 案设 计图
持车 床 原有 操 作 习惯 , 同时还 可 以提 高此 类 设备 生产 运 行 的稳 定 2 . 电气 部分 改进 .2 2 可靠 性 , 效 改善 此类 设备 的生产 工 艺现 状 , 一种 技术 和 经济 两 有 是 () 1 采用 西 门子 公 司 的 8 0 数 控 系统 代 替 原控 制 系 统 , 现 4D 实
数控车床升级改造
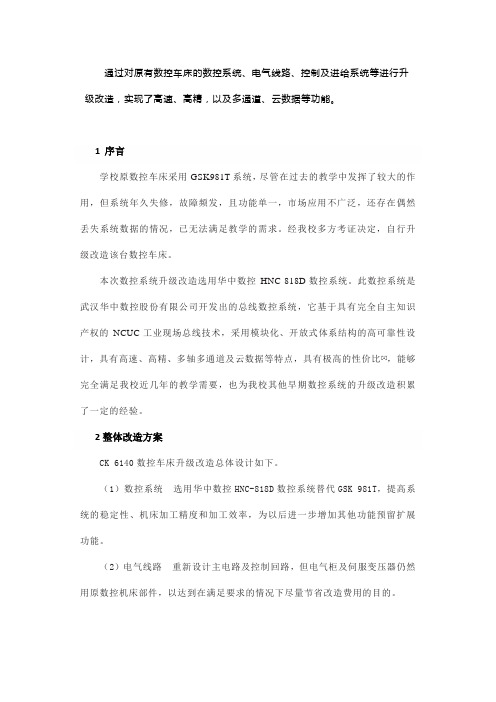
通过对原有数控车床的数控系统、电气线路、控制及进给系统等进行升级改造,实现了高速、高精,以及多通道、云数据等功能。
1 序言学校原数控车床采用GSK981T系统,尽管在过去的教学中发挥了较大的作用,但系统年久失修,故障频发,且功能单一,市场应用不广泛,还存在偶然丢失系统数据的情况,已无法满足教学的需求。
经我校多方考证决定,自行升级改造该台数控车床。
本次数控系统升级改造选用华中数控HNC-818D数控系统。
此数控系统是武汉华中数控股份有限公司开发出的总线数控系统,它基于具有完全自主知识产权的NCUC工业现场总线技术,采用模块化、开放式体系结构的高可靠性设计,具有高速、高精、多轴多通道及云数据等特点,具有极高的性价比[1],能够完全满足我校近几年的教学需要,也为我校其他早期数控系统的升级改造积累了一定的经验。
2 整体改造方案CK 6140数控车床升级改造总体设计如下。
(1)数控系统选用华中数控HNC-818D数控系统替代GSK 981T,提高系统的稳定性、机床加工精度和加工效率,为以后进一步增加其他功能预留扩展功能。
(2)电气线路重新设计主电路及控制回路,但电气柜及伺服变压器仍然用原数控机床部件,以达到在满足要求的情况下尽量节省改造费用的目的。
(3)进给系统将原步进驱动及步进电动机全更换为总线式带绝对位置记忆的伺服驱动器及伺服电动机,提高进给控制精度、运行的稳定性及负载承载能力。
(4)主轴部分保留原变频主轴。
主轴的正转、反转及停止,给定转速及转速的显示均通过外置IO单元实现。
(5)IO输入输出单元将原系统内置的PLC改为外置的IO单元。
考虑改造成本,IO单元采用华中HIO-1200-M1,其总线是IO单元,共有24位输入、16位输出,其上还有DA接口(用于变频主轴)和主轴编码器接口[2],完全能够满足升级改造的需要。
(6)机械部分除操作单元部分由于系统及操作面板的尺寸有变化需重新设计外,其他机械部分仍用原机床部分,只是在选用伺服电动机时,注意在满足驱动要求的前提下,安装接口与机床一致即可。
浅谈普通车床数控化改造的电气控制系统的研究

控车床 , 本文首先 简单 介 绍 7 C 8 0 8 1 型车床 部件 电气控 制系统 的要 求 , 确 定了改 造 的方案 , 并对 P L C 控 制 电路 进行 了详细 的阐述 , 经 改造 后 的
车床 工件 的加 工精 度得 到大 大的提 高。
关键 词 : 普 通车床 ; 电气控制 系统 ; PP E 接地 点只能集中于一点, 接地状 况不好时, 控制变压 器需进行浮地设计, 此时数控 系统 主单元连接 外部电器的电源 ( 3 ) P L C 数字输出所用的2 4 D C 需采用独立 的2 4 V 电源。
( 4 ) 尾座 需夹紧 时, 按下控制开关 接通 电磁 阀, 控制 油路使 应由控制器供 电。
浅谈普通车床数控化改造 的电气控制系统 的研究
屈长衡[ 齐齐哈尔 二机床 ( 集团) 有限 责 任公 司, 黑 龙江 齐齐哈 尔 1 6 1 0 0 5 ]
摘 要 : 本 文 以c 8 0 8 1 型车床 为研 究对 象 , 采用 西门子 P L c 控 制 系统对 c 8 0 8 1 型车床 进行 数控化 改 造 , 成功 的将 c 8 O 8 1 型车床 改造 为c 8 0 8 1 型数
1 C8 0 8 1 车 床部件 电气控 制要 求
先起 动床头箱油泵, 油泵停止工作 时, 不许起动主轴电机 。
设置 回参考点的速度 , 以期精确 的返 回参 考点, 并对 步进
( 1 ) 机床床头箱油泵主要用于润滑主轴, 主轴 电机起 动前应 电机 的转速 进行设定。
4 C 8 0 8 1 车床P L C 控制系统的设计原则
/ O 点数 , 即本控制系统所需的I / O 总数为6 4 个, 选择西门 ( 3 ) 原控 制系统的各元器 件 ( 按钮、 接触器 、 继电器) 功能应 最终的 I 子公司8 0 2 S 型产品, 2 4 V 直流3 2 点输入, 继电器交流3 2 点输出。 与原电气 线路相对应。
探索C6132普通车床电气控制及数控化改造设计
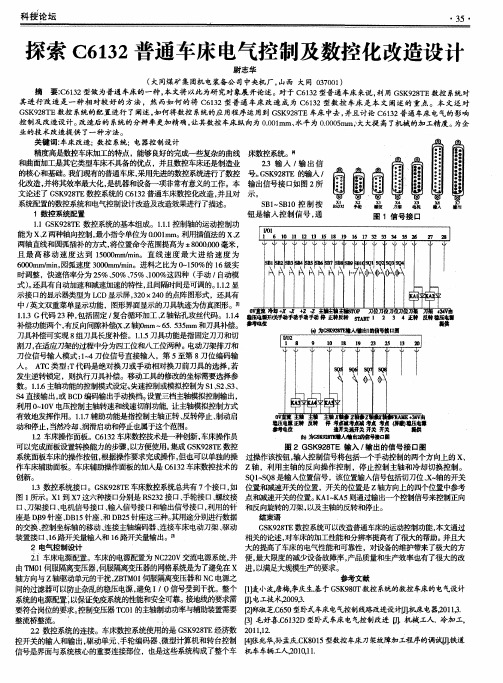
器 龆
端
固
蕊 救
图 1信号接 口
Байду номын сангаас
示接口的显示器类型为 L C D显示屏 , 3 2 0 × 2 4 0 的点阵图形式 ,还具有 中/ 英文双重菜单显示功能,图形界面显示的刀具轨迹为仿真图形。I l l 1 . 1 . 3 G代码 2 3 种, 包括固定 / 复合循环加工、 z轴钻孔攻丝代码。1 . 1 . 4 补偿功能两个, 有反向间隙补偿{ ) ( 、 Z ̄) 0 mm~ 6 5 . 5 3 5 m m和刀具补偿。 刀具补偿可实现 8 组刀具长度补偿 。1 . 1 . 5 刀具功能是指固定刀刀和切 割刀 , 在适应刀架 的过程中分为四工位和八工位两种。电动刀架排刀和 刀位信号输入模式 : 1 ~ 4 刀位信号直接输入 ,第 5 至第 8 刀位编码输 入。 A T C 类型 : T 代码是绝对换刀或手动相对换刀前刀具 的选择 , 若 发生逆转锁定 ,则执行刀具补偿。移动工具的修改的坐标需要选择参 数。1 . 1 . 6 主轴功能的控制模式设定. 失速控制或模拟控制为 s l 、 s 2 、 s 3 、 S 4 直接输出, 或B C D编码输 出手动换档。 设置三档主轴模拟控制输出, 利用 0 ~ 1 0 V电压控制主轴转速和线速切削功能, 让主轴模拟控制方式 有效地发挥作用。1 . 1 . 7 辅助功能是指控制主轴正转 、 反转停止、 制动启 动和停 当然冷却、 润滑启动和停止也属于这个范围。 彻 为G S l 【 5 嘲『 I = l 喇¨J 囊 l 出潮刚馨 呼接口圈 1 . 2车床操作面板。C 6 1 3 2 车床数控技术是一种创新 , 车床操作员 可以完成面板设置转换能力的步骤 , 以方便使用。 集成 G S K 9 2 8 T E 数控 图2 GS K 9 2 8 T E 输入 / 输出的信 号接 口图 系统面板车床的操作按钮 , 根据操作要求完成操作, 但也可以 单独的操 过操作该按钮 , 输人控制信号将包括—个手动控制的两个方 向 上的 x 、 作车床辅助面板。车床辅助操作面板的加入是 C 6 1 3 2 车床数控技术的 z轴 ,利用 主轴 的反 向操作控制 ,停止控制主轴和冷却 切换控制 。 创新。 . S Q I  ̄ S Q 8 是输入位置信号 , 该位置输入信号包括切刀位、 x 轴的开关 1 . 3数控系统接 口。G S K 9 2 8 T E车床数控系统总共有 7 个接 口, 如 位置和减速开关的位置 ,开关 的位置是 z轴方 向上的四个位置中参考 图1 所示。X1 到X 7 这六种接 口分别是 R S 2 3 2 接 口、 手轮接 口、 螺纹接 点和减速开关的位置。 K A 1 一 K A 5 则通过输出—个控制信号来控制正向 口、 刀架接 口、 电机信号接 口、 输入信号接口和输出信号接口, 利用的针 和反向旋转的刀架, 以及主轴的反转和停 止。 座是 D B 9 针座、 D B 1 5 针座、 和D B 2 5 针座这三种。 其用途分别进行数据 结束语 的交换 、 控制坐标轴的移动 、 连接主轴编码器 、 连接车床电动刀架 、 驱动 G S K 9 2 8 T E数控系统可以改造普通车床的运动控制功能, 本文通过 装置接 口、 l 6路开关量输入和 1 6 路开关量输出。 相关的论述 , 对车床的加工J 陛能和分辨率提高有了很大的帮助。 并且大 2电气控制设计 大的提高了车床的电气性能和可靠性 ,对设备的维护带来 了极大的方 2 . 1车床电源配置 。车床的电源配置为 N C 2 2 0 V交流电源系统 , 并 便 , 最大限度的减少设备故障率 , 产品质量和生产效率也有 了 很大的改 由T M O 1 伺服隔离变压器, 伺服隔离变压器的网格系统是为了避免在X 进, 以满足大规模生产的 要求。 轴方向 与z 轴驱动单元的干扰, Z B T M 0 1 伺服隔离变压器和 N C电源之 参 考文献 间的过滤器可以防止杂乱的稳压电源, 避免 I / 0信号受到干扰。整个 『 1 1 麦小波唐 梅 李庆生 基于 G S K 9 8 0 T 数控 系 统的数控车床的电气 设计 电工技 术 , 2 0 0 9 , 3 . 系统的电源配置 以保证免疫系统的性能和安全可靠。 接地线的要求需 要符合岗位的要求 。 控制变压器 T C O 1 的主轴制动功率与辅助装置需要 『 2 ] 郑淑芝. C 6 5 0型卧式车床 电气控制线路改进设计 机床电器, 2 0 1 1 . 3 . 【 3 ] 毛好喜. C 6 1 3 2 D型卧式车 床 电气控制改进 机械工人. 冷加工, 整流 桥整 流 。 . 2 - 2 数控系统的连接。车床数控系统使用的是 G S K 9 2 8 T E经济数 2 01 1 , 1 2 . 4 ] 张兆华, 孙孟庆. C K 8 0 1 5型数控车床 刀架故障加工程序的调试叨. 铁道 控开关的输入和输出, 驱动单元、 手轮编码器、 微型计算机和转台控制 『 信号是界面与系统核心的重要连接部位,也是这些系统构成了整个车 机车车辆工人00 1 0 , 1 1 .
立式车床数控改造电气控制部分安装与调试

立式车床数控改造电气控制部分安装与调试1. 引言立式车床数控改造是一项重要的工程,其中电气控制部分的安装与调试是关键步骤之一。
本文旨在介绍立式车床数控改造电气控制部分的安装与调试过程,并提供相应的操作指南。
2. 安装步骤2.1 准备工作在开始安装之前,需准备以下材料和工具: - 数控控制面板 - 电气控制部件(例如:电气箱、电源等) - 电气连接线 - 扳手、螺丝刀等基本工具 - 电源插座和配电线路2.2 安装电气控制部件2.2.1 电气箱安装1.将车床电源关闭并拔掉电源插头。
2.找到合适的位置安装电气箱,并使用螺丝固定。
3.将电气箱与车床进行电气连接,确保连接牢固可靠。
4.连接电气箱与数控控制面板。
2.2.2 数控控制面板安装1.将数控控制面板固定在车床上,确保安装牢固。
2.连接数控控制面板与电气箱,并用螺丝固定连接。
2.3 连接电气线路1.检查车床的电源插座是否符合电气控制部件的要求,如果不符合,需要进行相应的改造。
2.使用电气连接线将电气控制部件与电源插座进行连接,确保连接牢固、绝缘良好。
3. 调试步骤3.1 软件设置1.打开数控控制面板的电源,并确保数控控制面板上的指示灯亮起。
2.根据数控控制面板的使用手册,进行软件设置,例如选择工作模式、设定加工参数等。
3.2 电气参数调试1.将车床电源接通,并确保车床处于待机状态。
2.使用数控控制面板,逐步进行电气参数调试,例如电机速度、电流等。
3.检查各个电气设备的工作状态是否正常,例如电机是否旋转、传感器是否正常。
3.3 运动调试1.将加工物件放置在车床上,并进行夹紧。
2.根据数控控制面板的指示,使用数控程序进行车床的运动调试,例如进行自动加工、手动操作等。
3.检查车床的运动是否准确、平稳。
4. 安装与调试注意事项1.在进行安装和调试时,务必参考车床和数控控制面板的使用说明书,并按照要求进行操作。
2.在安装和调试过程中,严禁触摸裸露的电线和接触高电压设备,以确保人身安全。
GS30数控车床机电一体化改造研究
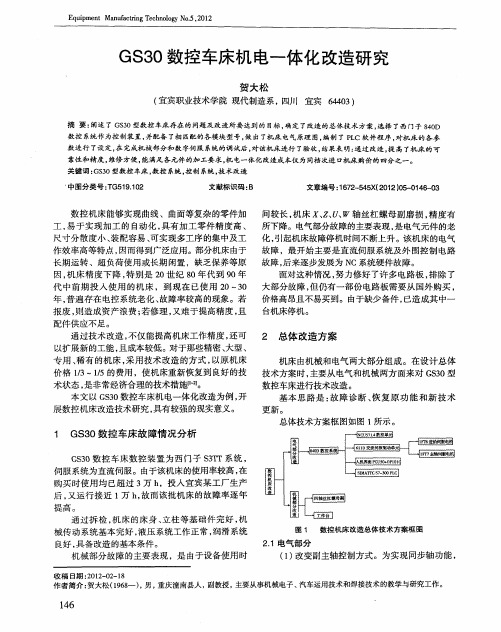
() 6 选择友好 的中文显示人机界面。 为实现图形 编程 、 加工循环 、 图形模拟、 螺距误差补偿等功能 , 选
择 带硬 盘 功能 的 P U3 C t 1 。
图 3 数控机床 的电气控制 系统 图
《 装备制造技术}0 2 2 1 年第 5 期
将 开 环控 制改 为半 闭环控 制 ;
() 2 更新数控系统 。为实现机床的位置控制 , 采
用西 门子公司的 8 0 4 D数控系统代替原数控系统 ; ( ) 换 主轴 电机 系统 。由 Wl 伺 服 电机 + 3更 ' 6 N U单元 + 1D驱动 +1H 代替原主轴电机系统; C 61 P7 ( ) 换 轴 、 轴 光栅尺及 z轴 、 轴 编码 4更 器, 以满足数控系统要求 ; () 5 配置输人输出设备。 全功能 C C N 键盘 , 薄型
2 总体 改造 方案
机床 由机械和电气两大部分组成 。在设计总体
技 术 方案 时 , 主要 从 电气 和机 械 两 方 面来 对 G 3 S 0型
数控车床进行技术改造。 基本 思路是 : 障诊 断 、 故 恢复原 功能 和新 技术 更新。 总体技 术方 案框 图如 图 1 所示 。
图 1 数控机床改造总体技术方案框 图
2 1电气 部分 . 良好 , 具备 改 造 的基本 条件 。 机械部分故 障的主要表现 ,是 由于设备使用时 () 1 改变副主轴控制方式 。为实现同步轴功能 ,
收 稿 日期 :0 2 0 — 8 2 1 — 2 1
作者 简介 : 贺大松( 9 8 ) 男 , 16 一 , 重庆潼南县人 究工作 。 16 4 ’
CA6132车床的进给系统数控化改造(GSK系统)

目录目录 (1)摘要 (2)1 绪论 (3)2 CA6132数控改造总体方案 (5)2.1CA6132概述 (5)2.2拟定总体改造方案 (7)3 进给伺服系统机械改造 (11)3.1进给系统机械结构改造设计 (11)3.2进给伺服系统机械部分的计算与选型 (11)3.3步进电机的选择 (15)4 CA6132车床控制系统设计 (18)4.1CA6132控制要求分析 (18)4.2CA6132车床电气控制设计 (18)总结 (22)参考文献 (23)摘要装备制造业和数控技术是现代工业的基础,随着我国国民经济的的快速发展,国民经济的各个部门对所生产的产品的性能要求越来越高,采用数控机床是实现多品种小批量生产的主要途径。
然而,高速、高精度、高自动化的数控机床价格仍然较为昂贵,且订货周期较长,无法满足生产急需。
采用数控改造技术对原有普通机床进行改造是提高机床的加工范围、加工精度,提高自动化生产水平的重要途径。
数控机床伺服系统是影响数控机床系统加工性能的重要指标,围绕伺服系统动态特性与静态特性的提高,近年来发展了多种伺服驱动技术。
针对把CA6132车床改造为经济型数控车床的目标,对车床的进给系统进行设计。
其设计的思路是根据执行件所受到的载荷,选择并校核其相关的零部件,包括滚珠丝杠螺母副、减速齿轮和电机,本文还对机构的重要零件作了比较详细地介绍。
最后,本文针对改造后的CA6132数控车床的电气控制系统提出了设计方案。
关键字:数控改造;装备制造;进给系统;1 绪论机械装备制造业是国民经济的支柱产业之一,直接影响着国民经济各部门的技术进步,同时反映了国家科学技术发展水平和国民经济的实力。
近年来,结合机电技术、液压技术、气动技术为一体的数控机床在机械装备制造业中广泛应用,已成为不可或缺的加工设备。
帮助人们解决了机械加工制造过程中的许多问题,使结构复杂、批量小、精度高、形状多变的零件的加工变得简单,提高了生产效率和机械自动化程度。
- 1、下载文档前请自行甄别文档内容的完整性,平台不提供额外的编辑、内容补充、找答案等附加服务。
- 2、"仅部分预览"的文档,不可在线预览部分如存在完整性等问题,可反馈申请退款(可完整预览的文档不适用该条件!)。
- 3、如文档侵犯您的权益,请联系客服反馈,我们会尽快为您处理(人工客服工作时间:9:00-18:30)。
齐齐哈尔工程学院论文题目:数控车床电气控制系统改造专业:机械设计制造及其自动化学号: 2013030233学生:王鑫指导教师:陈龙起止日期: 2016.11.21-12.30目录目录摘要 (3)引言 (4)一、概述 (5)1.1 选题的目的和意义 (5)1.2 关于课题的一些介绍和讨论 (5)1.3 电气控制技术的发展 (6)1.4 PLC的发展史及特点 (4)二、镗床的概况 (9)2.1 T6113卧式镗床主要结构及机械运动 (9)2.2 电气控制 (10)2.2.1 卧式镗床电力拖动及控制要求 (10)2.2.2 T6113卧式镗床的电气控制 (10)三、镗床电力拖动电动机的选择 (13)3.1 概述 (13)3.2 镗床用电动机容量的选择 (13)3.2.1 镗床主运动电动机容量的选择 (13)3.2.2 快速移动电动机容量的选择 (13)3.2.3 后立柱电机容量的选择 (13)3.2.4 主轴箱和工作台油泵电动机容量的选择 (13)四 PLC控制系统的设计 (14)4.1 PLC控制系统设计的内容和步骤 (14)4.1.1 PLC控制系统设计的内容 (14)4.1.2 PLC控制系统设计的步骤 (14)4.2 PLC控制系统的硬件配置 (14)4.2.1选择PLC机型 (14)4.2.2开关量I/O模块的选择 (14)4.2.3 PLC的接线电路分析 (14)五、 PLC在T113卧式镗床中的应用 (16)5.1 T6113卧式镗床的PLC控制方案 (16)5.2 T6113控制系统设计 (16)5.2.1 机型的选择及I/O接口的分配 (16)5.2.2 程序编制 (16)结论 (20)参考文献 (21)摘要随着机械工业的发展,作为工作母机的各类机床得到了广泛的应用,而这些机床的自动化和精密程度却有很大差异。
在欧美、日本等国家里,他们的机床数控化程度都相对比较高,但在我国国内的机床大约有90%多还处于老式的继电器控制下。
由于继电器控制的机床有耗材、耗能、故障率高的缺陷,从而浪费了很多的人力、物力和财力。
如果说把这些机床全部都更新换代,那样会需要很大一笔资金,就目前情况上来说是不现实的,所以就有人开始尝试从控制部分的改造方面来下手,将它们的性能提升一个档次,更可以解决它的一些弊端。
基于以上情况,我选择了用PLC来完成T6113卧式镗床的电气控制部分这个题目,目的是使机床能快速响应动作,灵活可靠的完成生产任务,而故障率要相应降低。
PLC以内部的逻辑触点代替了继电器的机械触点,来控制机床的动作,逻辑触点与机械触点相比动作时间大大缩短,连接快而可靠,还有就是它的寿命比机械触点有很大幅度的增长,可达到几百万次到千万次。
经过设计并作了实物的演示,结果证明了设计的成功。
关键词:继电器故障率逻辑触点引言数控车床改造,主要是对原有机床的结构进行创造性的设计,最终使机床达到比较理想的状态。
数控车床是机电一体化的典型代表,其机械结构同普通的机床有诸多相似之处。
然而,现代的数控机床不是简单地将传统机床配备上数控系统即可,也不是在传统机床的基础上,仅对局部加以改进而成(那些受资金等条件限制,而将传统机床改装成建议数控机床的另当别论)。
传统机床存在着一些弱点,如刚性不足、抗振性差、热变形大、滑动面的摩擦阻力大及传动元件之间存在间隙等,难以胜任数控机床对加工精度、表面质量、生产率以及使用寿命等要求。
现代的数控技术,特别是加工中心,无论是其支承部件、主传动系统、进给传动系统、刀具系统、辅助功能等部件结构,还是整体布局、外部造型等都已经发生了很大变化,已经形成了数控机床的独特机械结构。
因此,我们在对普通机床进行数控改造的过程中,应在考虑各种情况下,使普通机床的各项性能指标尽可能地与数控机床相接近。
第1章绪论1.1选题的目的和意义由于现代加工技术的日益提高,对加工机床特别是工作母机的要求也越来越高,由此人们也将注意力集中到机床上来,数控技术是计算机技术、信息技术、现代控制技术等发展的产物,他的出现极大的推动了制造业的进步。
机床的控制系统的优劣与机床的加工精度息息相关,特别是PLC广泛应用于控制领域后,已经显现出它的优越性。
可编程控制器PLC已广泛应用于各行各业的自动控制。
在机械加工领域,机床的控制上更显示出其优点。
由于镗床的运动很多、控制逻辑复杂、相互连锁繁多,采用传统的继电器控制时,需要的继电器多、接线复杂,因此故障多维修困难,费工费时,不仅加大了维修成本,而且影响设备的功效。
采用PLC控制可使接线大为简化,不但安装十分方便而且工作可靠、降低了故障率、减小了维修量、提高了功效。
1.2 关于课题的一些介绍和讨论1.2.1 设计目标、研究内容和拟定解决的关键问题完成对T6113机床的整个控制系统的设计改造,控制核心是PLC,并使其加工精度进一步提高,加工范围扩大,控制更可靠。
研究内容:(1) T6113的电气系统(PLC)硬件电路设计和在机床上的布局。
(2) PLC程序的编制。
解决的关键问题:PLC对机床各个工作部分的可靠控制电气电路的安全问题的解决1.2.2题目的可行性分析虽然目前数控机床以其良好的加工性能得到了人们的肯定,但是其昂贵的价格是一般用户望尘莫及的,所以改造现有的机床以达到使用要求是比较现实的,也是必须的。
经过实践证明这样的改造是可以满足大多数情况下的精度和其他加工要求,并且在实践中已取得的相当好的效益。
1.2.3本项目的创新之处利用PLC作为控制核心,替代传统机床的继电器控制,使得机床的控制更加灵活可靠,减少了很多中间的机械故障的可能。
利用PLC的可编程功能使得变换和改进控制系统成为可能。
1.2.4设计产品的用途和应用领域镗床是一种主要用镗床刀在工件上加工孔的机床。
通常用于加工尺寸较大、精度要求较高的孔。
特别是分布在不同表面上、孔距和位置精度要求较高的孔,如各种箱体,汽车发电机缸体等零件的孔。
一般镗刀的旋转为主运动,镗刀或工件的移动为进给运动。
在镗床上除镗孔外,还可以进行铣削、钻孔、扩孔、铰孔、锪平面等工件。
因此镗床的工作范围较广。
它可以应用于机械加工的各个领域,但因其价格比一般机床贵好多,所以在比较大的加工车间才可见到。
1.3 电气控制技术的发展电气控制技术是随着科学技术的不断发展、生产工艺不断提出新的要求而迅速发展的,从最早的手动控制到自动控制,从简单的控制设备到复杂的控制系统,从有触点的硬接线控制系统到以计算机为中心的存储系统。
现代电气控制技术综合应用了计算机、自动控制、电子技术、精密测量等许多先进的科学技术成果。
作为生产机械的电机拖动,已由最早的采用成组拖动方式,发展到今天无论是自动化功能还是生产安全性方面都相当完善的电气自动化系统。
继电接触式控制系统主要由继电器、接触器、按钮、行程开关等组成,其控制方式是断续的,所以又称为断续控制系统。
由于这种系统具有结构简单、价格低廉、维护容易、抗干扰能力强等优点,至今仍是机床和其他许多机械设备广泛采用的基本电气控制形式,也是学习先进电气控制的基础。
这种控制系统的缺点是采用固定的接线方式,灵活性差,工作频率低,触点易损坏,可靠性差。
从20世纪30年代开始,生产企业为了提高生产率,采用机械化流水作业的生产方式,对不同类型的产品分别组成生产线。
随着产品类型的更新换代,生产线承担的加工对象也随之改变,这就需要改变控制程序,使生产线的机械设备按新的工艺过程运行,而继电接触器控制系统采取固定接线方式,很难适应这个要求。
大型生产线的控制系统使用的继电器的数量很多,这种有触点的电器工作频率很低,在频繁动作的情况下寿命较短,从而造成系统故障,使生产线的运行可靠性降低。
为了解决这个问题,20世纪60年代初期利用电子技术研制出矩阵式顺序控制器和晶体管逻辑控制系统来代替继电接触式控制系统。
对复杂的自动控制系统则采用计算机控制,由于这些控制装置本身存在不足,因此均未能获得广泛应用。
1968年美国最大的汽车制造商通用汽车(GM)公司,为适应汽车型号不断更新,提出把计算机的完备功能以及灵活性、通用性好等优点和继电接触器控制系统的简单易懂、操作方便、价格低等优点结合起来,做成一种能适应工作环境的通用控制装置,并把编程方法输入方法简化。
美国数字设备公司(DEC)于1969年率先研制出第一台可编程控制器(简称PLC),并在通用汽车公司的自动装配线上试用获得成功。
从此以后,许多国家的著名厂商竟相研制,各自成为系列,而且品种更新很快,功能不断增强,从最初的逻辑控制为主发展到能进行模拟量控制,具有数字运算、数据处理和通信联网等多种功能。
PLC另一个突出的优点是可靠性很高,平均无故障运行可达10万小时以上,可以大大减少设备维修费用和停产造成的经济损失。
当前PLC已经成为电气自动化控制系统中应用最广泛的核心控制装置。
电气控制技术的发展始终是伴随着社会生产规模的扩大,生产水平的提高而前进的。
电气控制技术的进步反过来又促进了社会生产力的进一步提高。
同时,电气控制技术又是与微电子技术、电力电子技术、检测传感技术、机械制造技术等紧密联系在一起的。
21世纪电气控制技术必将给人类带来更加繁荣的明天。
1.4 PLC的发展史、优势及特点1.4.1 发展史可编程控制器PLC诞生之前,工业电气控制主要使用低压电器构成的继电接触器电路,它是以接线逻辑实现控制功能的。
这样的控制设备一经生产出来,功能就固定了,若要改变就必须改变控制器内部的硬件接线,使用起来不灵活,也很麻烦。
1968年,美国最大的汽车制造商——通用汽车公司(GM)为了适应生产工艺不断更新的需要,要寻找一种比继电器更可靠,功能更齐全,响应速度更快的新型工业控制器,并从用户角度提出了新一代控制器应具备的十大条件,立即引起了开发热潮。
1969年,美国数字设备公司(DEC)研制出了第一台可编程控制器PDP——14,在美国通用汽车公司的生产线上适用成功,并取得了满意的效果,可编程控制器由此诞生。
可编程控制器自问世以来,发展极为迅速。
1971年,日本开始生产可编程控制器,1973年,欧洲开始生产可编程控制器,到现在,世界各国的一些著名的电器工厂几乎都在生产可编程控制器。
可编程控制器已作为一个独立的工业设备被列入生产中,成为当代电控装置的主导。
早期的可编程控制器主要由分立元件和中小规模集成电路组成,它采用了一些计算机技术,但简化了计算机的内部电路,对工业现场环境适应性较好,指令系统简单,一般只具有逻辑计算的功能。
随着微电子技术和集成电路的发展,特别是微处理器和微计算机的迅速发展,在20世纪70年代中期,美、日、德等国的一些厂家在可编程控制器中开始更多地引入微机技术,微处理器及其他大规模集成电路芯片成为其核心部件,使可编程控制器具有了自诊断功能,可靠性有了大幅提高,性能价格比产生了新的突破。