集装箱制造工艺规程工艺守则汇总
集装箱生产工艺流程

集装箱生产工艺流程
1.集装箱制造(ContainerManufacturing):首先将集装箱船的货舱或集装箱船的舱位分割成许多小舱位,将各小舱位按一定的要求进行组装。
2.集装箱制造(ContainerManufacturing):根据集装箱制造计划,在工厂中完成对集装箱的制造、检验和包装等工作。
3.集装箱的安装(ContainerContainerOrganization):把经过工厂组装好的集装箱吊到堆场,将各舱位逐个对中,调整箱内货物位置,使之符合装箱单上所列货物的装载要求。
然后用起重机将各箱位上的集装箱吊起到堆场,待货物落到堆场后再用吊车将各箱位上的集装箱放下。
最后由卡车将各箱位上的集装箱运至仓库或工厂指定的地点。
4.集装箱装箱(ContainerPacking):装箱是一项技术性很强的工作。
要根据所装货物种类,尺寸和质量,选用不同规格的集装箱。
用专用设备将集装箱内货物按一定要求装满,并用封箱胶封好箱口。
—— 1 —1 —。
集装箱制造工艺规程工艺守则汇总

集装箱制造工艺规程工艺守则汇总集装箱作为现代物流运输的重要工具,其制造质量的好坏直接影响到货运的安全和效率。
因此,集装箱的制造工艺规程和工艺守则显得尤为重要。
本文将从集装箱的制造流程、工艺规程和工艺守则三个方面集装箱制造的主要流程和注意事项。
集装箱制造流程集装箱的制造流程主要包括材料选择、板材加工、件装配、焊接、表面处理和检验等阶段,其中每一个阶段都需要严格按照相应的规程和守则操作,这样才能够保证集装箱的质量。
材料选择集装箱的主要材料包括钢板、铝板、不锈钢板等,以钢板为主要材料制造的集装箱主要应用于海运领域。
在进行材料选择时需要根据集装箱的尺寸和负载情况选择合适的材料,并且对所选材料进行质量检测,以确保其符合生产需要。
板材加工板材加工是制造集装箱的重要步骤,主要包括剪板、弯曲、钻孔、切割等操作。
在板材加工过程中需要注意以下几个方面:•切割方向应符合板材奥氏体晶粒的方向。
•确保板材切割边缘平直光滑,无毛刺、无剪切留痕。
•在弯曲板材时要考虑板材的弯曲半径和弯曲角度,以及板材上刻度线的准确性等。
件装配集装箱通常由前、后、左、右、顶、底等六面板件加上门、铰链、紧固件等组成。
在件装配过程中需要注意以下几个方面:•确保板件的平直度、大小、位置和间距符合相应的规程和要求。
•安装门、铰链、紧固件时应确保其位置和功能正确,并且紧固件的拉力应符合规程要求。
焊接焊接是集装箱制造流程中最关键的一环。
焊接不仅直接影响到集装箱的强度和密封性,而且还直接关系到货物运输的安全。
在进行焊接操作时需要注意以下几个方面:•使用合适的焊接工艺及合金焊丝。
•确保焊接的实景无裂纹和疵点,要求间缝均匀,无偏差且朝向同一方向。
•焊接前要对板材和现场进行认真的清理工作,并且进行适当的预热处理等。
表面处理在集装箱制造的最后一步,需要对其表面进行防腐处理和粉末喷涂,以增强集装箱的耐久性和美观度。
在表面处理时需要注意以下几个方面:•确保防腐涂层的厚度和质量符合规定要求。
集装箱制造工艺

集装箱制造工艺1. 概述集装箱制造工艺是指将金属材料转变为可用于运输和存储货物的集装箱的加工过程。
本文档将介绍集装箱制造工艺的主要步骤和关键技术。
2. 材料选择在集装箱制造过程中,常用的材料包括钢铁和铝合金。
这些材料具有良好的强度和耐用性,能够承受运输过程中的振动和外部压力。
3. 制造步骤3.1 设计和规划在制造集装箱之前,需要进行设计和规划。
这包括确定集装箱的尺寸、结构和功能要求,以及制定制造过程中所需的工艺和设备。
3.2 板材加工集装箱的主体结构通常由单一铁板制成。
板材需要经过切割、弯曲、冲压和焊接等加工工序,以形成集装箱的各个部件。
3.3 框架组装板材加工完成后,需要对各个部件进行组装。
这包括焊接框架、连接角部件和安装门、窗等配件。
框架组装需要精确的测量和对齐,以确保集装箱的结构稳固。
3.4 表面处理组装完成后,集装箱需要进行表面处理以防止腐蚀和延长使用寿命。
常用的表面处理方法包括喷涂防锈漆、热浸镀锌和涂覆防腐膜等。
3.5 安装和测试最后,集装箱需要进行安装和测试。
这包括安装门、窗和密封件等配件,并进行密封性、防水性和抗压性等方面的测试,以确保集装箱符合相应的标准和要求。
4. 关键技术在集装箱制造过程中,存在一些关键技术,包括:- 焊接技术:确保焊缝的质量和强度。
- 机械加工技术:用于板材的切割、弯曲和冲压等加工过程。
- 表面处理技术:保护集装箱免受腐蚀和氧化。
- 测试技术:确保集装箱的质量和性能符合标准。
5. 结论集装箱制造工艺是一个复杂的过程,需要专业的设备和技术。
通过合理的设计和规划,并采用适当的材料和工艺,可以制造出高质量和耐用的集装箱。
对于集装箱制造企业来说,合理控制制造成本和提高产品质量是实现可持续发展的关键。
简述集装箱制造工艺流程

简述20’标准钢制干货集装箱制造工艺流程(一)钢材预处理及冲压1.钢板预处理有以下几个步骤:钢卷开卷平板校平一次打砂一次锌粉侧板平板剪断罗拉成形修边冲孔(通风孔)门板,前墙板平板剪断折弯成形修边冲孔(锁杆安装,铭牌孔)底横梁,底侧梁卷板分条(开卷之前分条)罗拉成形(打砂之前)冲缺口(叉槽)其余零件平板剪断裁剪冲缺折弯成形2.型材型材锯断一次打砂一次锌粉所有的零件冲压制作出来后送至焊接车间各对应台位。
(二)部件焊装1.底架(Base assembly)叉槽底横梁与叉槽顶板焊接将底横梁、叉槽、底侧梁组焊,焊接叉槽底板,叉槽加强角钢翻转将底横梁与底侧梁双面满焊焊接固定环,门绳钩运至总装台前待总装2.前端(Front assembly)前底横梁,前底横梁加强板,前底防撞槽钢及封板等焊接成一体前角柱,前端角件,前角柱固定棒焊接成一体前端框架前顶横梁预拱前墙板自焊拼接成一整张前墙板与前端框架焊接3.门端(Rear assembly)后角柱外与后角柱内自动拼焊冷却,校直焊接门铰耳、后角柱固定棒焊铰链销,同时安装门铰链与垫片与后端角件焊接组成后角柱门楣、门楣加强板、门楣板焊接一起组成门楣门楣板做预拱门槛、门槛加强板、门槛防撞槽钢及封板等焊接成一体后角柱、门楣、门槛组成后端框架待后端总装门竖梁封板与门竖梁焊接(后称门竖梁)门竖梁、门横梁、门板组装翻转门板自动焊修整待后端总装将后端框架通过门铰链与两片门叶焊接连接在一起,门楣和门槛上焊接锁座,并在右门中柱焊接一块TIR门挡板,注意控制门叶与门槛,门楣及内角柱槽钢之间的距离。
后端总成修整后堆放待总装。
4. 侧壁(Side assembly )侧壁拼板自动焊将侧板与顶侧梁方管定位点焊波纹焊 焊接顶侧梁固定绳环 修整 待总装 5. 顶板(Roof assembly )顶板拼板 自动焊 修整 待总装(三) 总装1. 将底架放置与总装台上2. 将门端与前端固定于总装台上3. 将两侧壁吊至总装台4. 将底侧梁、底侧梁、门楣、前顶横梁与角件焊接,门楣板、前顶横梁与顶侧梁焊接,侧壁板与底侧梁、顶侧梁点焊定位5. 焊接前后顶角加强板,盖顶板,顶板与顶侧梁点焊定位(四) 总焊(五) 油漆与美妆1. 二次打砂及油漆2. 木地板与美妆。
简述集装箱制造工艺流程(精)
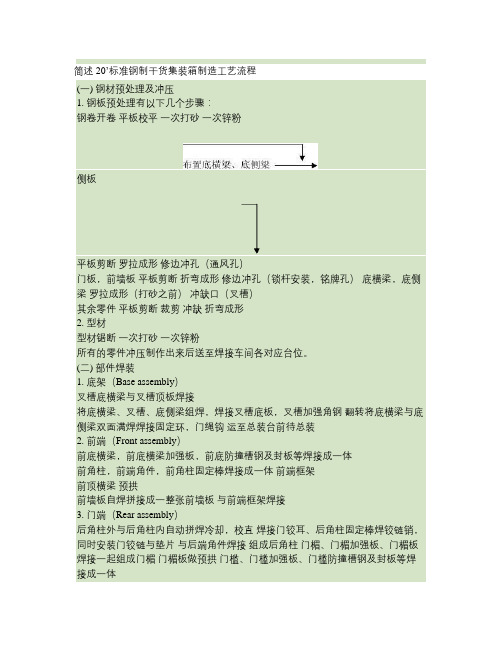
简述20’标准钢制干货集装箱制造工艺流程(一) 钢材预处理及冲压1. 钢板预处理有以下几个步骤:钢卷开卷平板校平一次打砂一次锌粉侧板平板剪断罗拉成形修边冲孔(通风孔)门板,前墙板平板剪断折弯成形修边冲孔(锁杆安装,铭牌孔)底横梁,底侧梁罗拉成形(打砂之前)冲缺口(叉槽)其余零件平板剪断裁剪冲缺折弯成形2. 型材型材锯断一次打砂一次锌粉所有的零件冲压制作出来后送至焊接车间各对应台位。
(二) 部件焊装1. 底架(Base assembly)叉槽底横梁与叉槽顶板焊接将底横梁、叉槽、底侧梁组焊,焊接叉槽底板,叉槽加强角钢翻转将底横梁与底侧梁双面满焊焊接固定环,门绳钩运至总装台前待总装2. 前端(Front assembly)前底横梁,前底横梁加强板,前底防撞槽钢及封板等焊接成一体前角柱,前端角件,前角柱固定棒焊接成一体前端框架前顶横梁预拱前墙板自焊拼接成一整张前墙板与前端框架焊接3. 门端(Rear assembly)后角柱外与后角柱内自动拼焊冷却,校直焊接门铰耳、后角柱固定棒焊铰链销,同时安装门铰链与垫片与后端角件焊接组成后角柱门楣、门楣加强板、门楣板焊接一起组成门楣门楣板做预拱门槛、门槛加强板、门槛防撞槽钢及封板等焊接成一体后角柱、门楣、门槛组成后端框架待后端总装门竖梁、门横梁、门板组装翻转门板自动焊修整待后端总装将后端框架通过门铰链与两片门叶焊接连接在一起,门楣和门槛上焊接锁座,并在右门中柱焊接一块TIR门挡板,注意控制门叶与门槛,门楣及内角柱槽钢之间的距离。
后端总成修整后堆放待总装。
4. 侧壁(Side assembly)侧壁拼板自动焊将侧板与顶侧梁方管定位点焊波纹焊焊接顶侧梁固定绳环修整待总装5. 顶板(Roof assembly)顶板拼板自动焊修整待总装(三) 总装1. 将底架放置与总装台上2. 将门端与前端固定于总装台上3. 将两侧壁吊至总装台4. 将底侧梁、底侧梁、门楣、前顶横梁与角件焊接,门楣板、前顶横梁与顶侧梁焊接,侧壁板与底侧梁、顶侧梁点焊定位5. 焊接前后顶角加强板,盖顶板,顶板与顶侧梁点焊定位(四) 总焊(五) 油漆与美妆1. 二次打砂及油漆2. 木地板与美妆。
集装箱拼板工艺流程及基本要求
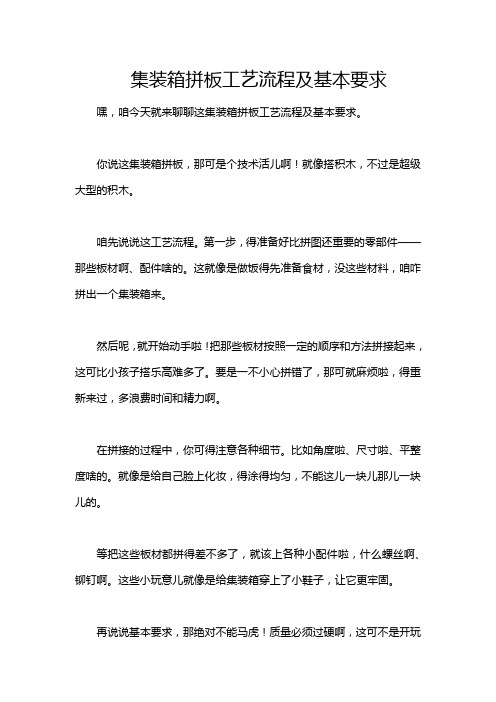
集装箱拼板工艺流程及基本要求嘿,咱今天就来聊聊这集装箱拼板工艺流程及基本要求。
你说这集装箱拼板,那可是个技术活儿啊!就像搭积木,不过是超级大型的积木。
咱先说说这工艺流程。
第一步,得准备好比拼图还重要的零部件——那些板材啊、配件啥的。
这就像是做饭得先准备食材,没这些材料,咱咋拼出一个集装箱来。
然后呢,就开始动手啦!把那些板材按照一定的顺序和方法拼接起来,这可比小孩子搭乐高难多了。
要是一不小心拼错了,那可就麻烦啦,得重新来过,多浪费时间和精力啊。
在拼接的过程中,你可得注意各种细节。
比如角度啦、尺寸啦、平整度啥的。
就像是给自己脸上化妆,得涂得均匀,不能这儿一块儿那儿一块儿的。
等把这些板材都拼得差不多了,就该上各种小配件啦,什么螺丝啊、铆钉啊。
这些小玩意儿就像是给集装箱穿上了小鞋子,让它更牢固。
再说说基本要求,那绝对不能马虎!质量必须过硬啊,这可不是开玩笑的,要是质量不行,那运输途中出点啥问题,那不就悲剧啦。
还得注意环保呢,可不能弄些不环保的材料,咱得为地球妈妈着想啊。
而且,这拼板的师傅也得技术过硬,没个几年的功夫可不行。
不然拼出来的箱子歪七扭八的,谁愿意用啊。
要说在这个过程中我的感受啊,那就是又紧张又兴奋。
每次看到一个完整的集装箱拼出来,就像是自己盖了一栋大楼一样,特有成就感。
但同时呢,也怕自己某个环节出错,那就得推倒重来,那可真是让人头疼。
总之啊,这集装箱拼板工艺流程及基本要求,听起来简单,做起来可不容易。
得细心、耐心、有技术,才能拼出一个个坚固又好用的集装箱。
怎么样,是不是觉得这玩意儿也挺有意思的?下次看到集装箱,你就会想到我今天说的这些啦!哈哈!。
集装箱制造的工艺流程

集装箱制造的工艺流程分为四个初级工序,即:冲压、焊接、喷涂和竣工。
1. 冲压:包括开卷、打砂、下料和成型四个部分。
开卷是用开卷机将钢材卷成平板。
打砂是用一定速度的细钢砂冲击钢材表面,去除数据表面的锈渍,在钢材表面留下凹凸坑(增加油漆附着力)。
下料和成型部分则是通过弯曲、压制、滚压、冲孔剪切、切边等工艺使零件成型。
2. 焊接:将冲压工段加工出来的零件和角件、门铰链等配套零件在焊接工段进行焊接,构成部件和总成。
从胎位来划分,焊接工段可分为:前端、后端、侧板、顶板、底架、总装。
3. 喷涂:箱体内部需要两层油漆,外部需要三层,每层油漆都有严格的膜厚规定,保证盒子油漆3-5年不掉。
因此,喷涂本身的准备也很重要。
4. 竣工:在这一阶段,会对整个集装箱进行检查,确保所有部件都按照设计要求正确地安装并工作。
简述集装箱制造工艺流程(精)
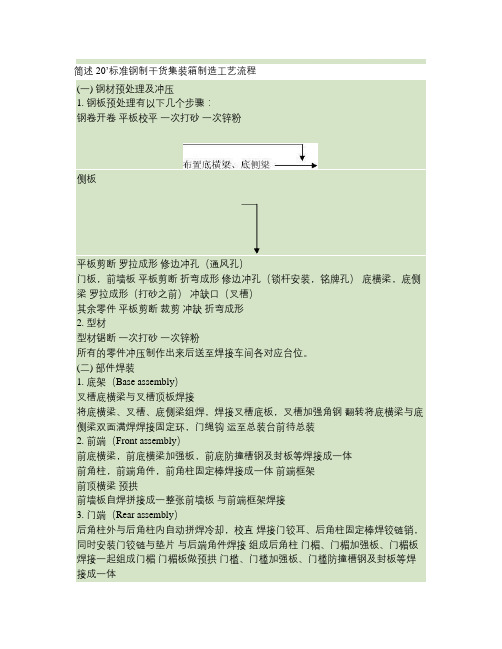
简述20’标准钢制干货集装箱制造工艺流程(一) 钢材预处理及冲压1. 钢板预处理有以下几个步骤:钢卷开卷平板校平一次打砂一次锌粉侧板平板剪断罗拉成形修边冲孔(通风孔)门板,前墙板平板剪断折弯成形修边冲孔(锁杆安装,铭牌孔)底横梁,底侧梁罗拉成形(打砂之前)冲缺口(叉槽)其余零件平板剪断裁剪冲缺折弯成形2. 型材型材锯断一次打砂一次锌粉所有的零件冲压制作出来后送至焊接车间各对应台位。
(二) 部件焊装1. 底架(Base assembly)叉槽底横梁与叉槽顶板焊接将底横梁、叉槽、底侧梁组焊,焊接叉槽底板,叉槽加强角钢翻转将底横梁与底侧梁双面满焊焊接固定环,门绳钩运至总装台前待总装2. 前端(Front assembly)前底横梁,前底横梁加强板,前底防撞槽钢及封板等焊接成一体前角柱,前端角件,前角柱固定棒焊接成一体前端框架前顶横梁预拱前墙板自焊拼接成一整张前墙板与前端框架焊接3. 门端(Rear assembly)后角柱外与后角柱内自动拼焊冷却,校直焊接门铰耳、后角柱固定棒焊铰链销,同时安装门铰链与垫片与后端角件焊接组成后角柱门楣、门楣加强板、门楣板焊接一起组成门楣门楣板做预拱门槛、门槛加强板、门槛防撞槽钢及封板等焊接成一体后角柱、门楣、门槛组成后端框架待后端总装门竖梁、门横梁、门板组装翻转门板自动焊修整待后端总装将后端框架通过门铰链与两片门叶焊接连接在一起,门楣和门槛上焊接锁座,并在右门中柱焊接一块TIR门挡板,注意控制门叶与门槛,门楣及内角柱槽钢之间的距离。
后端总成修整后堆放待总装。
4. 侧壁(Side assembly)侧壁拼板自动焊将侧板与顶侧梁方管定位点焊波纹焊焊接顶侧梁固定绳环修整待总装5. 顶板(Roof assembly)顶板拼板自动焊修整待总装(三) 总装1. 将底架放置与总装台上2. 将门端与前端固定于总装台上3. 将两侧壁吊至总装台4. 将底侧梁、底侧梁、门楣、前顶横梁与角件焊接,门楣板、前顶横梁与顶侧梁焊接,侧壁板与底侧梁、顶侧梁点焊定位5. 焊接前后顶角加强板,盖顶板,顶板与顶侧梁点焊定位(四) 总焊(五) 油漆与美妆1. 二次打砂及油漆2. 木地板与美妆。
- 1、下载文档前请自行甄别文档内容的完整性,平台不提供额外的编辑、内容补充、找答案等附加服务。
- 2、"仅部分预览"的文档,不可在线预览部分如存在完整性等问题,可反馈申请退款(可完整预览的文档不适用该条件!)。
- 3、如文档侵犯您的权益,请联系客服反馈,我们会尽快为您处理(人工客服工作时间:9:00-18:30)。
罐式集装箱制造工艺规程2013-11-20发布2013-12-01实施张家港韩中深冷科技有限公司发布罐式集装箱制造工艺规程1. 总则本工艺规程是对集装箱生产过程的工艺性指导和产品质量控制的法规,除执行相应的国家和行业标准外,应严格按此规程执行。
2. 遵行及引用标准、通用工艺规程GB150《压力容器》JB/T4784-2007《低温液体汽罐式集装箱》TSG R0005-2011《移动式压力容器安全技术监察规程》低温贮罐氧清洁清洗工艺规程氦检漏工艺规程多层绝热缠绕及套装工艺规程抽真空和真空保持检测工艺规程外表面喷砂处理及喷漆工艺规程外部管路、阀门组焊工艺规程3. 内罐的制造(数据以40英尺集装箱为例)3.1 材料:主要受压元件06Cr19Ni10的材料须符合GB/T24511-2009《承压设备用不锈钢钢板及钢带》,复验合格后方可使用。
3.2 内封头:规格按图纸要求,材质 06Cr19Ni10,切边并刨坡口,左封头为外坡口,右封头为内坡口,3.2.1 封头外购,须附质量合格证明书及检验记录,入库时进行各项要求检查,按GB/T25198-2010标准的检查方法检测:(1)直边倾斜度≤1.5mm 。
(2)内直径公差2200±3mm(3)最大最小直径差≤3mm(4)封头总深度 59064+-mm (5)直边高度 4004- mm(6)封头成形后的最小壁厚≥7.2mm 。
(7)封头内外表面应酸洗钝化,并经脱脂处理,表面不得有裂纹,分层,凹坑现象,不合格者不得用于罐箱的制造。
3.3 内筒体:规格按图纸,材质06Cr19Ni103.3.1 划线:将钢板垫平实,按《筒体制造工艺守则》进行划线放样,下料尺寸见下图,并按质量手册有关规定用记号笔进行标记移植。
并划出产品焊接试板500×130两块。
内筒体下料理论展开尺寸按流卡。
(周长按封头实测)3.3.2 切割:用等离子切割下料,并去除熔渣及飞溅,切割后与下料线的偏差:-1mm<△<3mm。
3.3.3 坡口:按下图在刨边机上刨坡口,靠左封头端为外坡口,其余为内坡口。
要求:筒节长度公差≤±1mm,筒节周长公差≤±3mm,对角线公差≤2mm3.3.4 成型:在卷板机上先压头,再卷制成型,并用400mm宽的样板测量,尽量减少卷制来回的次数,以免钢板延伸,周长变长。
3.3.5 组焊:纵缝组焊,严格按照焊接工艺规范操作,不得在筒体上引弧,并将焊接试板组对在纵缝的延伸部位一起焊接。
要求:1 焊缝处成型良好,光滑平整,焊缝条高≤1.5mm。
2 焊缝及热影响区不得有裂纹、咬边、气孔、未熔合及夹渣等缺陷。
3 焊缝表面及两侧的飞测物清理干净。
3.3.6 校圆:将试板和引孤板与纵缝分离。
注意:保持焊缝端部的平齐。
(并将试板送无损检测室进行无损检测)将筒体在卷板机上校园,要求棱角度E≤2.8mm,同一断面上最大最小直径差e≤3mm。
筒节用工装圈撑圆。
3.3.7 无损检测:纵缝100%RT,按JB/T4730.2-2005标准II级合格,合格后转入下道工序。
3.3.8 划线、开孔:左右封头划线经检验确认后开孔,并与管接头组对焊接。
3.3.9 组对:筒节与筒节进行组焊,每条相邻纵缝间距必须大于100mm,罐体纵缝不得布置在筒体横截面中心线以最低点连接半径的左两侧各20°范围内,并注意支撑垫板位置不得与焊缝重叠,筒节并与右封头组焊。
组焊要求:拼接处的棱角E≤2.8mm,错边量b≤2mm。
筒体直线度AL≤3mm3.3.10 焊接按焊接工艺施焊,要求同纵缝质量要求。
3.3.11 无损检测:环缝100%RT,按JB/T4730.2-2005要求II级合格,射线检测技术等级不低于AB级。
3.3.12 划线、开孔:筒体划线,经检验确认后,再用等离子切割,并去渣、打磨坡口。
3.3.13组焊:管接头与筒体组焊,按图采用全焊透结构,并圆弧过度,焊脚高度不得少于图样规定要求。
3.3.14 第一次清洗:内壁按相关通用工艺进行酸洗、钝化,并进行脱脂处理,并用黑灯光检查,无油脂为合格,经检验确认。
3.3.15 组焊:将清洗、脱脂处理好的内件,与筒体右封头组焊,组焊左封头,留小封头一道焊缝不焊。
3.3.16 左封头与筒体的一道合口环缝100%RT符合JB/T4730.2-2005中II合格,射线检测技术等级不低于AB级。
3.3.17第二次清洗:筒体内壁及内件进行第二次清洗,并用白猫洗洁精进行清洗,并采用黑灯光进行检查,方法见通用工艺守则,合格后组焊小封头,焊缝进行100%PT,符合JB/T4730.5-2005中Ⅰ合格。
3.3.18 外部零件组焊:外部管件预先弯制成型,并清洗脱脂处理后再与内胆管接头组焊,外部其它零件与筒体组焊,注意封头套装工艺管在组焊前划好定位线,尽量与封头中心重合,玻璃钢支撑垫板位置公差按图纸要求,并经检验确认。
内筒体外表面去毛刺及焊接飞溅。
3.3.19 气压试验:内胆按图样要求表压作气压试验,按试压通用工艺守则进行无泄漏及异常变形为合格,并作好记录,监检现场确认。
3.3.20 第三次清洗:内胆外表面及管线进行酸洗钝化处理,并进行脱脂处理,按通用工艺规程执行,经检验确认,注意垫板上的螺纹透气孔用螺栓及生料带密封,防止液体渗入。
3.3.21 内胆及管线氦检漏按氦检漏工艺规程执行,并作好相应记录,内筒检查合格后用塑料纸套好待用。
4. 外壳的制造4.1 材料:制造外壳的材料为Q345R,须符合GB713-2008《锅炉压力容器用钢板》,每个炉批号必须有质量合格证明书。
4.2封头:规格按图样要求材质:Q345R 切边并坡外坡口。
4.2.1 封头外购,须附有质量合格证明书及检验记录,入库时进行各项要求检查,按GB/T4746-2002标准的检查方法检测。
(1)直边倾斜度≤1.5 mm。
(2)内直径公差±3mm(3)最大最小直径差≤3mm(4)封头总深度按图样mmmm(5)直边高度404(6)封头成形后的最小壁厚按图样mm(7)封头表面不得有油污、焊渣、裂纹、分层、凹坑现象,不合格者不得用于罐箱的的制作。
4.2.2 左右封头开好孔,在套装前内表面喷砂吸尘干净后用塑料纸封口、待用。
4.3 外筒体:规格按图样材质Q345R4.3.1 划线:将钢板垫平实,按《筒体制造工艺守则》进行划线放样,下料尺寸见下图,并按质量手册有关规定用记号笔进行标记移植。
并划出产品焊接试板550×130两块。
外筒体下料理论展开尺寸按工艺流卡要求(周长按封头实测)4.3.2 切割:用气割下料,并去除熔渣及飞溅,切割后与下料线的偏差:-1mm<△<3mm。
4.3.3 坡口:按下图在刨边机上刨坡口,外坡口,要求:筒节长度公差≤±1mm,筒节周长公差≤±3mm,对角线公差≤2mm4.3.4 成型:在卷板机上卷制成型,并用样板测量,尽量减少卷制来回的次数,以免钢板延伸,周长变长。
4.3.5 组焊:纵缝组焊,严格按照焊接工艺规范操作,不得在筒体上引弧,并将焊接试板组对在纵缝的延伸部位一起焊接。
要求:1 焊缝处成型良好,光滑平整,焊缝条高≤1.5mm。
2 焊缝及热影响区不得有裂纹、咬边、气孔、未熔合及夹渣等缺陷。
3 焊缝表面及两侧的飞测物清理干净。
4.3.6 校圆:将试板和引孤板与纵缝分离。
注意:保持焊缝端部的平齐。
(并将试板送无损检测室进行无损检测)将筒体在卷板机上校园,要求棱角度E≤2.8mm,同一断面上最大最小直径差e≤3mm。
筒节用工装圈撑圆。
4.3.7 无损检测:纵缝20%RT及100%PT,按JB/T4730.2-2005标准III级合格及JB/T4730.5-2005中Ⅰ级合格,射线检测技术等级不低于AB级。
4.3.8 组对:筒节与筒节进行组焊,每条相邻纵缝外圆弧长必须大于200mm,罐体纵缝不得布置在筒体横截面中心线以最低点连接半径的左右两侧各200范围内,筒节并与后封头组焊。
组焊要求:拼接处的棱角E≤2.8mm,错边量b≤2mm。
筒体直线度AL≤3mm 4.3.9 焊接按焊接工艺施焊,要求同纵缝质量要求。
4.3.10无损检测:环缝20%RT及100%PT,按JB/T4730.2-2005标准III级合格及JB/T4730.5-2005中Ⅰ级合格,射线检测技术等级不低于AB级。
4.3.11 组焊:支撑圈与筒体组焊、采用间断焊,双面交错进行,并组焊套装轨道,并用小车做来回滑动试验。
4.3.12 划线开孔,在筒体上划开孔位置线,注意位置公差要求,经检验确认后开孔。
4.3.13 喷砂:套装前8小时内对筒体内表面进行喷砂要求,按喷砂通用工艺执行,并用无油压缩空气,对内表面吹扫,再用吸尘机吸尘,干净后筒体两端用塑料纸封口,待用。
5. 管件的制造5.1 管件的材料为06Cr19Ni10,须符合GB/T14976-2012《流体输送用不透钢无缝钢管》标准的要求,并附质量证明书。
5.2 管件的弯制,应首先制作好弯管模具及检测样板,对形状复杂的可以用φ8mm左右的不锈钢圆钢,制作好模型,弯制时采用定位靠模弯制,弯制R处的波浪形皱折及椭圆度不平度不超过下表的要求:a. 管件弯头的平面不平度按下表规定表一b. 管件弯曲内测表面波浪S应不超过下表规定的数量、波浪间距应大于4倍的管壁厚度。
c. 管件弯曲后对于管径>60mm 的弯头应进行椭圆度检查且符合下表规定:计算公式:a =DN D D min max ×100%5.3 管件弯制后,拼接处应按焊接工艺卡坡口,并用氩弧焊进行焊接,错边量≤0.5mm ,内口应无焊瘤,以免影响流量。
5.4 对接焊缝进行100%RT ,按JB/T4730.2-2005 II 级合格要求,射线检测技术等级低于AB 级。
5.5 管线内外表面进行酸洗、钝化、脱脂处理,并用清水冲洗干净,再用干净无油的干空气吹干净、待用。
6. 玻璃钢支撑6.1 材料:D3848玻璃钢,常温性能参数符合下列要求:a.密度1.65~1.80g/cm 3 b.压缩强度(垂向)≥250MPa c.拉伸强度(垂向)≥200MPa d. 导热系数<0. 40W/m..k6.2 玻璃钢锯切后进行金加工,按图样要求,并加工R 部分,玻璃钢不得有分层、裂纹等缺陷。
6.3 玻璃钢表面不得有油污及灰尘,并用塑料纸封好。
6.4 内容器上的玻璃钢支撑垫板、两端的缠绕支撑垫板,在焊装之前,内容器上被垫板覆盖的部位要求用百叶砂轮抛光并清理干净。
7. 分子筛、氧化钯7.1 低温吸附剂牌号为5A 和13X ,混合的比例为2:1,装填量应符合设计图样,放置于工艺人孔内置封头中,分子筛的要求见下表:7.2 常温吸附剂为高效氧化钯催化剂或Ag400,装填量应符合图样要求,分为两包,分别放置在两端外封头内表面上,氧化钯的钯含量为80%~85%,在650℃空气中4h,活性不变。