炼钢厂30T电弧炉电气自动化控制技术文件综述
电气自动化技术在钢铁制造业中的应用分析

电气自动化技术在钢铁制造业中的应用分析电气自动化技术在钢铁制造业中的应用已经成为现代化钢铁生产过程中的重要组成部分。
这种技术的应用极大地提高了钢铁生产的效率和质量,并且使得整个生产过程更加安全和可靠。
下面将对电气自动化技术在钢铁制造业中的应用进行一些分析。
电气自动化技术在钢铁冶炼过程中起到了重要的作用。
在冶炼过程中,电气自动化控制系统可以对温度、压力和化学成分等参数进行实时监控和调节,从而确保冶炼过程的稳定性和一致性。
电气自动化技术还可以实现自动化的添加合金和燃料等操作,提高生产效率和冶炼质量。
在钢铁制造过程中的连铸工艺中,电气自动化技术也发挥着重要的作用。
连铸是将熔化的钢液连续注入到铸坯机中,通过水冷而凝固成坯料的工艺。
电气自动化技术可以对连铸工艺中的各个环节进行自动化控制,实现连铸速度、冷却水流速率等参数的精确调控,从而保证铸坯的质量和尺寸的准确性。
电气自动化技术在钢铁制造过程中的轧制工艺中也得到了广泛应用。
轧制是将铸坯经过一系列连续轧制机组进行压制和拉伸,最终形成所需要的板材或型材的工艺。
电气自动化技术可以对轧制过程中的轧机参数、卷取张力等进行自动化控制,实现轧制过程的精确调控,提高产品的质量和生产效率。
电气自动化技术还可以在钢铁制造过程中的能源管理和环境保护方面发挥重要作用。
通过对能源消耗的实时监测和控制,电气自动化技术可以有效地提高能源利用率,降低能源消耗,减少钢铁生产对环境的影响。
电气自动化技术在钢铁制造业中的应用对提高生产效率、质量和安全性具有重要意义。
通过对冶炼、连铸、轧制和能源管理等环节的自动化控制,可以实现钢铁生产过程的智能化和数字化,提高钢铁企业的竞争力和可持续发展能力。
小议钢铁厂电气自动化控制技术
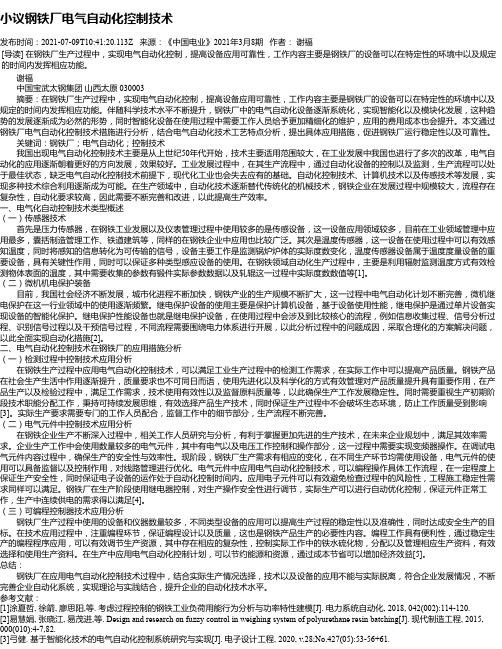
小议钢铁厂电气自动化控制技术发布时间:2021-07-09T10:41:20.113Z 来源:《中国电业》2021年3月8期作者:谢福[导读] 在钢铁厂生产过程中,实现电气自动化控制,提高设备应用可靠性,工作内容主要是钢铁厂的设备可以在特定性的环境中以及规定的时间内发挥相应功能。
谢福中国宝武太钢集团山西太原 030003摘要:在钢铁厂生产过程中,实现电气自动化控制,提高设备应用可靠性,工作内容主要是钢铁厂的设备可以在特定性的环境中以及规定的时间内发挥相应功能。
伴随科学技术水平不断提升,钢铁厂中的电气自动化设备逐渐系统化,实现智能化以及模块化发展,这种趋势的发展逐渐成为必然的形势,同时智能化设备在使用过程中需要工作人员给予更加精细化的维护,应用的费用成本也会提升。
本文通过钢铁厂电气自动化控制技术措施进行分析,结合电气自动化技术工艺特点分析,提出具体应用措施,促进钢铁厂运行稳定性以及可靠性。
关键词:钢铁厂;电气自动化;控制技术我国出现电气自动化控制技术主要是从上世纪50年代开始,技术主要适用范围较大,在工业发展中我国也进行了多次的改革,电气自动化的应用逐渐朝着更好的方向发展,效果较好。
工业发展过程中,在其生产流程中,通过自动化设备的控制以及监测,生产流程可以处于最佳状态,缺乏电气自动化控制技术前提下,现代化工业也会失去应有的基础。
自动化控制技术、计算机技术以及传感技术等发展,实现多种技术综合利用逐渐成为可能。
在生产领域中,自动化技术逐渐替代传统化的机械技术,钢铁企业在发展过程中规模较大,流程存在复杂性,自动化要求较高,因此需要不断完善和改进,以此提高生产效率。
一、电气化自动控制技术类型概述(一)传感器技术首先是压力传感器,在钢铁工业发展以及仪表管理过程中使用较多的是传感设备,这一设备应用领域较多,目前在工业领域管理中应用最多,囊括制造管理工作、铁道建筑等,同样的在钢铁企业中应用也比较广泛。
其次是温度传感器,这一设备在使用过程中可以有效感知温度,同时将感知的信息转化为可传输的信号,设备主要工作是监测锅炉炉体的实际度数变化,温度传感器设备属于温度度量设备的重要设备,具有关键性作用,同时可以保证多种类型感应设备的使用。
钢铁厂的电气自动化控制技术分析

77C omputer automation计算机自动化钢铁厂的电气自动化控制技术分析谭雄军(湖南华菱涟钢炼铁厂原料场,湖南 娄底 417009)摘 要:伴随着市场经济的不断发展和进步,电气自动化控制技术的应用范围也在不断扩大,为了发挥技术优势,满足时代发展需求,就要整合技术要点,应用在相应的行业领域中,从而有效提升钢铁厂常规化工作的综合水平,为生产力的提升奠定坚实基础。
本文分析了钢铁厂运行电气自动化技术体系的意义,并从设备可靠性测试、可编程逻辑控制器技术以及电气元件处理等方面分析了具体的技术应用内容,仅供参考。
关键词:钢铁厂;电气自动化控制;意义;内容中图分类号:TF089 文献标识码:A 文章编号:11-5004(2020)12-0077-2收稿日期:2020-06作者简介:谭雄军,男,生于1984年,汉族,湖南娄底人,本科,助理工程师,研究方向:电气控制维修。
近几年,科学技术呈现出全面转型发展的趋势,钢铁企业作为传统工业也要紧跟时代发展的步伐,从技术层面提高行业的市场竞争力,优化技术管理效果的同时,在科学技术支持下实现生产效率的进步目标,提高产品的整体质量和产量,满足社会的发展需求。
1 钢铁厂运行电气自动化技术体系的意义我国应用电气自动化控制技术的研究较多,并且应用时间也较长,为了满足发展和变革的要求,就要在整合技术应用模式的同时,契合行业的发展特点。
将电气自动化控制技术融合到钢铁厂常规化管控体系内,能为企业带来较大的经济效益,在贴合社会生产力需求的基础上,确保生产效率也能得以优化。
需要注意的是,工业生产流程中,整体体系的运行质量决定了工作运行的合理性,要在维系生产质量的同时打造安全生产的环境,而借助自动化控制模式能有效减少人力、物力资源的浪费,提高实际控制和检修工作的质量,在降低劳动强度的基础上,满足新时代对行业的科技发展目标[1]。
另外,钢铁厂在应用电气自动化技术的过程中,还能将企业的具体工作流程和项目环节结合到产品质量管控模式中,从而满足生产质量和效率的整体要求,为钢铁厂实现全面可持续健康发展奠定坚实基础。
钢铁冶炼设备的自动化控制技术

钢铁冶炼设备的自动化控制技术随着科技的不断发展,钢铁冶炼设备的自动化控制技术也在不断进步。
自动化控制技术的发展极大地提高了钢铁冶炼设备的生产效率和质量,同时也降低了人工成本,为钢铁行业的发展做出了重要的贡献。
钢铁冶炼设备的自动化控制技术可以实现多个方面的控制,例如温度、压力、流量、浓度等。
通过对这些参数的精确控制,可以在不额外增加工人的情况下,提高生产效率和品质,降低设备的运行成本和维护费用。
钢铁冶炼设备的自动化控制技术包括了多个方面,其中最重要的就是控制系统。
控制系统是实现钢铁生产自动化控制的核心,它可以确保各种控制模式的实现,例如PID控制。
PID控制即比例+积分+微分的控制方式,它可以根据设定的目标温度来进行控制,并对设备进行调整。
另一个重要的组成部分是自动化设备,例如PLC、SCADA等。
这些设备可以自动执行指定的任务,并将实时数据传输到控制系统中,在控制系统的支配下实现自动化生产。
通过优化PLC和SCADA系统的使用,不仅可以提高生产效率,还可以确保环境和设备的安全性。
除了控制系统和自动化设备,自动控制技术还需要不断的进行不断的优化和更新。
这些更新可能包括控制算法的优化、设备的升级以及数据处理技术的改进等等。
通过不断地进行更新,可以确保控制系统的最优化运作,及时对设备出现的问题做出反应,以确保生产效率和生产质量。
总的来说,控制系统、自动化设备以及更新和优化技术是自动化控制技术的三个主要方面。
钢铁冶炼设备的自动化控制技术不断的优化和更新,为设备的实际运作带来了巨大的提高,使钢铁行业不断发展壮大,更好地满足了市场需求。
电气自动化技术在钢铁制造业中的应用分析

电气自动化技术在钢铁制造业中的应用分析
随着现代科技的不断进步和电气自动化技术的不断发展,钢铁制造业也不断吸收和应
用这些新技术,以提高生产效率、降低成本、提高产品质量和品牌形象。
本文将简单地分
析电气自动化技术在钢铁制造业中的应用。
首先,电气自动化技术在钢铁制造业中的最大应用就是钢铁生产中的自动化控制。
钢
铁制造过程中有很多环节需要自动化控制,例如高炉的自动化控制、连铸机的自动化控制、轧机的控制等等。
这些自动化控制系统能够实时监测生产情况,实现无人值守,提高生产
效率和生产质量,减少了生产中的人为错误和事故。
其次,电气自动化技术在生产设备的控制方面也得到了大量的应用。
目前,钢铁生产
设备大多采用电气控制系统,例如各类变频器、PLC控制器等系统。
这些控制系统能够实
现对生产设备的自动控制和监测,从而提高设备利用率和生产效率,减少生产成本和人为
工作量。
再次,电气自动化技术在产品检测和质量控制方面也得到了广泛应用。
通过搭建自动
化检测系统,能够实现对生产过程中的各项参数,如温度、压力、流量等的自动测量和监测。
同时,电气自动化技术支持产品重复性检测和优化,以保证产品质量和一致性。
最后,基于大数据和云计算平台,电气自动化技术也在钢铁制造业中应用广泛。
通过
采集和分析生产过程中的数据,钢铁制造厂商能够更好地掌握生产流程,制定更加合理的
生产计划。
通过云存储和计算,能够将产生的大量数据进行处理,并实现远程监测和管理,更好地为生产提供保障。
钢铁厂电气自动化控制技术探讨
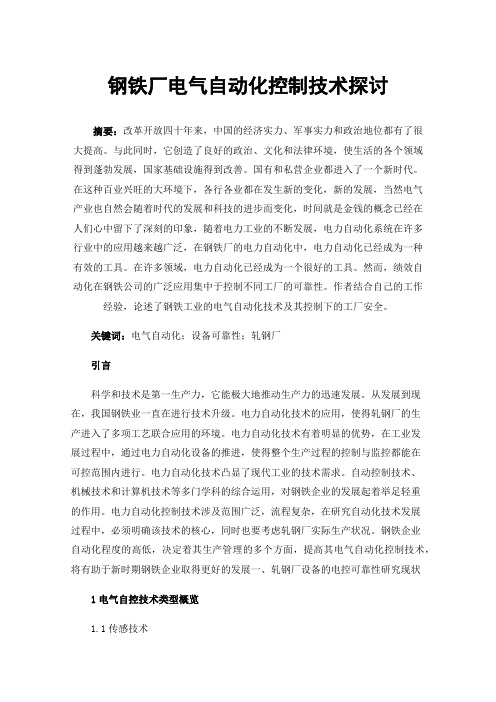
钢铁厂电气自动化控制技术探讨摘要:改革开放四十年来,中国的经济实力、军事实力和政治地位都有了很大提高。
与此同时,它创造了良好的政治、文化和法律环境,使生活的各个领域得到蓬勃发展,国家基础设施得到改善。
国有和私营企业都进入了一个新时代。
在这种百业兴旺的大环境下,各行各业都在发生新的变化,新的发展,当然电气产业也自然会随着时代的发展和科技的进步而变化,时间就是金钱的概念已经在人们心中留下了深刻的印象,随着电力工业的不断发展,电力自动化系统在许多行业中的应用越来越广泛,在钢铁厂的电力自动化中,电力自动化已经成为一种有效的工具。
在许多领域,电力自动化已经成为一个很好的工具。
然而,绩效自动化在钢铁公司的广泛应用集中于控制不同工厂的可靠性。
作者结合自己的工作经验,论述了钢铁工业的电气自动化技术及其控制下的工厂安全。
关键词:电气自动化;设备可靠性;轧钢厂引言科学和技术是第一生产力,它能极大地推动生产力的迅速发展。
从发展到现在,我国钢铁业一直在进行技术升级。
电力自动化技术的应用,使得轧钢厂的生产进入了多项工艺联合应用的环境。
电力自动化技术有着明显的优势,在工业发展过程中,通过电力自动化设备的推进,使得整个生产过程的控制与监控都能在可控范围内进行。
电力自动化技术凸显了现代工业的技术需求。
自动控制技术、机械技术和计算机技术等多门学科的综合运用,对钢铁企业的发展起着举足轻重的作用。
电力自动化控制技术涉及范围广泛,流程复杂,在研究自动化技术发展过程中,必须明确该技术的核心,同时也要考虑轧钢厂实际生产状况。
钢铁企业自动化程度的高低,决定着其生产管理的多个方面,提高其电气自动化控制技术,将有助于新时期钢铁企业取得更好的发展一、轧钢厂设备的电控可靠性研究现状1电气自控技术类型概览1.1传感技术第一种是压力传感器,在钢铁行业发展和仪表管理过程中,用得较多的是感应设备,这一设备应用范围很大,目前在工业领域管理中,主要用于生产管理、铁路建筑等同样,在钢铁企业中应用也很广泛。
30t高功率电弧炉技术参数及设备清单
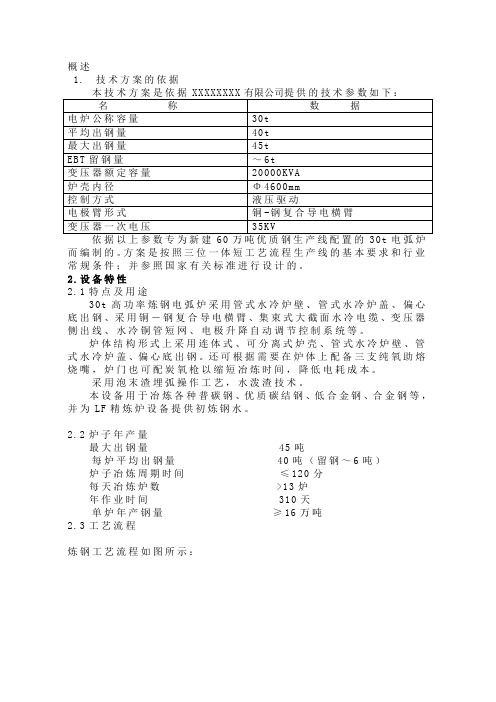
概述1.技术方案的依据而编制的。
方案是按照三位一体短工艺流程生产线的基本要求和行业常规条件;并参照国家有关标准进行设计的。
2.设备特性2.1特点及用途30t高功率炼钢电弧炉采用管式水冷炉壁、管式水冷炉盖、偏心底出钢、采用铜-钢复合导电横臂、集束式大截面水冷电缆、变压器侧出线、水冷铜管短网、电极升降自动调节控制系统等。
炉体结构形式上采用连体式、可分离式炉壳、管式水冷炉壁、管式水冷炉盖、偏心底出钢。
还可根据需要在炉体上配备三支纯氧助熔烧嘴,炉门也可配炭氧枪以缩短冶炼时间,降低电耗成本。
采用泡末渣埋弧操作工艺,水泼渣技术。
本设备用于冶炼各种普碳钢、优质碳结钢、低合金钢、合金钢等,并为LF精炼炉设备提供初炼钢水。
2.2炉子年产量最大出钢量45吨每炉平均出钢量40吨(留钢~6吨)炉子冶炼周期时间≤120分每天冶炼炉数>13炉年作业时间310天单炉年产钢量≥16万吨2.3工艺流程炼钢工艺流程如图所示:附件一主要技术参数及设备说明一、30t高功率电弧炉主要技术参数序号名称单位数值附注1.1电炉容量公称容量t 30平均出钢量t 40 每炉留钢5-7t1.2平均冶炼周期min ≤1101.3单炉年产钢量万吨≥161.4年作业率% 85 310天1.5日冶炼炉数炉>131.6摇架导轨中心距mm 5100 高架式1.7出渣方式水泼渣操作1.8炉体装置炉壳内径mm Ø4600熔池直径mm Ø3700熔池深mm 830 含渣层厚100-150mm 熔池容积m3 7.65炉底耐材厚mm 650钢液容积m3 5.7钢液质量t 38(新炉衬)比重7t/m3炉内总容积m3 31.75炉壳总高度mm 3500水冷炉壁面积m2 20.5 管式炉门尺寸(宽×高)mm 1000×760EBT出钢口直径 mm Ø130EBT出钢启动方式液压及手动水冷炉壁型式水冷密排管式炉壳更换方式可分体吊装上炉壳尺寸、重量下炉壳尺寸、重量、含耐材总重1.9 炉盖炉盖提升高度mm 400电极心圆直径mm 1150±10炉盖提升时间s <60炉盖旋开角度(°)-75旋开速度(°)/s ≤1.5传动控制方式PLC-液压炉盖水冷面积m2 17 水冷密排管式1.10 短网电参数相电抗绝对值mΩ/相 2.46三相电抗不平衡≤ 5%1.11 电炉变压器额定容量KVA 20000 可长期超载20%一次电压KV 35二次电压V 500-380-260二次额定电流 A 30388调压方式有载电动调压进出线方式顶进,侧出,三角形内封口1.12 电极升降装置电极升降行程mm 3100电极直径mm Ø450 国产高功率电极上升最大速度m/min 6下降最大速度m/min 4控制方式PLC-电液比例阀电极调节器响应时间s ≤0.31.13 炉体倾动装置出钢最大倾角(°)20 正常出钢12°-15°出渣最大倾角(°)15出钢(出渣)倾炉速度(°)/s 1 出钢快速回倾速度≥3 控制方式PLC-比例阀1.14 冷却水装置进水压力MPa 0.25-0.3(表压)带显示进水温度℃<35 带显示出水温度℃<55 有报警冷却水耗量m3/h炉盖160 工业水炉壁200 工业水变压器50 工业水其它m3/h 110 工业水合计520水质要求PH 7-8.5总硬度dH 10 以现有水质为准悬浮物mg/l ≤45 以现有水质为准导电率µs/min ≤500 以现有水质为准1.15 液压系统工作压力MPa 10-12泵流量l/min 117×3工作介质水一乙二醇(甲方自备)柱塞恒压变量泵型号ATV55DR额定压力/最大压力bar 350/400排量Ml/r 117配用电机Y225M-6 30kW数量台 3生产厂美国派克电液比例阀型号4WRGE16E200额定压力bar 315流量L/min 200数量台 3型号4WR225E325额定压力bar 315流量L/min 325数量台炉体倾动一个生产厂美国派克高压罐(皮囊储能器组)数量 1 组8个容积m3 0.8 (事故状态可将电极提起)集液箱容积m3 4.5材质不锈钢1.16 压缩空气系统耗量Nm3/h 4 不含炭枪用气压力MPa ≥0.41.17 耐火材料重量t -601.18 炉体吊装重量t -801.19 金属结构重量t -190 不含液压及电气设备重量二、机械设备说明30t高功率电弧炉为炉盖旋开顶装料式(操作形式:左操作),其机械部分由倾动装置、炉体装配、水冷炉盖、炉盖提升及旋转装置、电极升降装置、大电流线路、冷却水系统、液压系统、气动系统等组成。
电弧炉炼钢工艺简介与控制技术

保护和信号回路
检测计量显示回路
电极升降自动调节回路
电弧炉机械设备供电线路
(电磁电弧搅炉炼拌钢线工艺路简介)和控制技术
高压电源
隔离开关
断路器 变压器一次侧 炉用变压器 变压器二次侧母线
变压器二次侧
测量仪表用变压器 电炉控制盘 电极自动调节器
电弧炉
电极升降机构
主电路接线图 电弧炉炼钢工艺简介和控制技术
穿井期 d极→炉底
主熔化期 熔末升温期
炉底→电 弧暴露
电弧暴露 →全熔
必要条件 保护炉顶 保护炉底 快速熔化 保护炉壁
办
较低电压 较低电流 较大电压 较大电流 最高电压 最大电流 低电压 大电流
法 炉顶布 轻废钢 石灰垫
底
水冷+ 泡沫渣
电弧炉炼钢工艺简介和控制技术
典型的供电曲线
电弧炉炼钢工艺简介和控制技术
还原期→出钢(浇铸成钢锭或钢坯) 优点: 氧化期用加矿或吹氧进行脱C和脱P,使熔池沸腾,可以去除
钢中气体和杂质。 还原期可以脱O、脱S及调整成分和温度。 可得到含P、气体和夹杂物都很低的钢。 可用廉价废钢为原料,适合冶炼[P]高、锈多、[C]较高
的钢铁料,应用最广泛。 缺点: 若炉料中有合金返回料,则其中合金元素氧化烧损较大。
按废钢预热方式
运输机上料 半连续废钢预热 分批熔炼
Comelt Consteel(连续加料) Fuchs(指条式竖炉) ConArc、 ContiArc IHI式双电极直流
运输机上料 连续废钢预热 Mid-shaft EAF 竖炉(竖井在炉顶中央) 连续电弧熔炉炼炼钢工艺简介和控制技术
6.1 电弧炉炼钢技术概述
出钢槽 轨梁 基础
电极夹持器 电极 悬臂式平台 炉盖 炉体 炉门
- 1、下载文档前请自行甄别文档内容的完整性,平台不提供额外的编辑、内容补充、找答案等附加服务。
- 2、"仅部分预览"的文档,不可在线预览部分如存在完整性等问题,可反馈申请退款(可完整预览的文档不适用该条件!)。
- 3、如文档侵犯您的权益,请联系客服反馈,我们会尽快为您处理(人工客服工作时间:9:00-18:30)。
天远炼钢有限公30T电弧炉电气控制系统改造技术文件供方:XXXXXXX需方:天远炼钢有限公1.总则电弧炉电气控制系统主要完成三相电极升降及自动功率控制功能,要求技术先进、性能可靠,操作方便。
2.系统构成及说明2.1 硬件:操作台(上位机:17‘液晶显示,256M/40XCD/80G,PLC:S7-300,CPU314系列)2.2 软件:西门子最新授权的相关软件STEP7,上位机组态软件KINGVIEW2.3 系统功能说明如下:2.3.1 上位机具有管理、参数显示功能。
能够显示三相冶炼电流、电压、给定电流数值,具有棒图显示。
同时还可以通过上位机控制三相电极手动升降速度。
2.3.2P LC采用西门子最新产品(S7-300,CPU314,模拟量为光隔12BIT,开关量为16BIT,备用I/O点为10%)2.3.3操作台仪表显示三相冶炼电压、电流;档位显示;高压分、合闸显示;炉变故障显示;液压站控制等2.3.4设定电流采用电位器给定,电流调节采用最优模糊控制方法,三相冶炼功率平衡,自动设定非灵敏区,控制支臂升降,有手动/自动两种方式。
2.3.5自动起弧,穿井快速跟踪。
2.3.6低压电器元件采用国内名牌产品以上技术要求可在技术交流中具体明确1概述电弧炉以及精炼炉在运行过程中其产生的高次谐波及强电磁场所形成的强大干扰,是严重威胁控制和通讯系统安全运行的主要原因。
50吨炼钢电弧炉的电炉变压器额定容量为31500KVA,二次额定电流可达到42KA以上,其冲击和短路电流有时可达到和超过100KA。
强电磁场和电弧的弧光放电引起的宽带噪声干扰及高次谐波分量与闪变(电压波动),成为计算机及通讯网络,电子设备稳定和安全运行的主要问题。
在方案设计和系统设计及PLC选型以及制造工艺设计时,都必须充分考虑和关注到系统所处的恶劣运行现场工业环境的抗扰问题。
在为太钢集团公司第一炼钢厂设计的50吨炼钢电弧炉及60吨钢包精炼炉控制系统中?穴50吨电弧炉和60吨钢包精炼炉的系统总结构图略,可向作者索取?雪,两台电炉的控制系统全部采用SIEMENS公司的S7-300系列PLC及其通讯技术。
经过现场调试和运行结果证明该系统运行状态良好,性能可靠稳定。
2系统的总体设计2.1硬件结构的设计整个系统采用4台SIEMENSS7-315-2DPPLC主站分别完成对电弧炉炉体控制、电弧炉电极调节,钢包精炼炉炉体控制和钢包精炼炉电极调节。
在四台PLC主站之间采用SIEMENS公司的CP-342通讯模块构成PROFIBUS-S7通讯网完成各主站间的数据通讯。
电弧炉炉体和钢包精炼炉炉体控制PLC主站共下设6个ET200远程从站,通过SIEMENS公司工业现场总线PROFIBUS-DP完成主——从通讯。
系统设计使用一台工程师站,两台操作员站。
三台工业计算机中分别采用SIEMENS公司CP5412网卡通过PROFIBUS-S7数据通讯网络完成计算机与各PLC主站之间的数据通讯。
操作员站的画面组态软件选用SIEMENS公司的WINCC完成用户二次软件的开发。
炼钢电弧炉炉体控制PLC主站主要完成对35KV高压系统的合分闸操作及高压系统事故分闸的控制,对31500KVA电炉变压器及变压器油水冷却系统运行状态的监控和保护,并完成电炉水冷炉盖、水冷炉壁等水冷系统23个测温点水温变化情况的模拟量实时数据采集以及冷却水系统压力、流量等的实时数据采集监视和越限及事故报警。
同时通过PROFIBUS-S7网向操作员站进行实时数据的传输,由人机界面完成监控数据的记录、显示和故障报警。
炼钢电弧炉的各ET200远程从站分别设置在炉前操作室、炉后操作室、液压泵站和液压阀站以及炉门碳氧喷枪的操作站内。
分别构成炉前的炉盖和炉体动作操作和控制炉前倾炉操作,三相立柱锁定和炉前电极升降操作及炉门钢水测温I/O。
炉后倾炉及EBT出钢操作、出钢钢包车操作和修理平台的旋转操作I/O。
液压泵站主、辅液压泵的切换和运行控制,对高压液罐和气罐的液位和压力控制、空气压缩机的控制、主液箱和回液箱的液位自动控制及液压介质自动温度控制的I/O,液压阀台的I/O及炉门碳氧喷枪三维动作的操作及控制I/O。
钢包精炼炉炉体控制PLC主站的作用同炼钢电弧炉相似,ET200远程从站仅设置在钢包精炼炉的液压站内。
用于控制炉内电弧功率的炼钢电弧炉和钢包精炼炉电极调节系统设计各采用一台SIEMENSS7-315-2DPPLC主站。
主要承担输入炉内的三相电弧功率的实时自动控制,根据不同冶炼工艺和冶炼期自动修正功率配电曲线和控制参数,以满足冶炼工艺要求。
设计采用独立设置的两套PLC主站作为电炉和精炼炉电极调节系统可以减轻电炉和精炼炉炉体控制PLC主站CPU的负担,缩短程序扫描周期,有利于提高实时系统相应的响应速度和调节精度。
2.2控制软件的设计四台PLC主站的用户程序是在基于SIEMENS公司的SIMATICSTEP7BasisV5.0软件平台上完成硬件组态、地址和站址的分配以及电弧炉和钢包精炼炉用户程序的设计开发的,在主程序(OB1)中将各种控制功能和各PLC站点间的通讯数据分别编写在不同的子程序(功能块FB、DB、FC)中,其中35KV高压合分闸、事故高压分闸,模拟量信号的输入均充分考虑了现场工业运行环境的强干扰问题,在软件设计中采用了抗干扰措施。
人机界面的画面组态采用SIEMENS公司的SIMATICWINCC作为二次用户程序开发的软件平台,在工程师站安装WINCC-RC用于开发,操作员站安装WINCC-RT用于运行,WINCC运行于WindowsNTV4.0操作系统平台之上,以增加系统运行安全和稳定性,并给用户将来建立工厂管理网带来方便。
现场操作人员通过分别设置在电炉和精炼炉操作员站的人机界面监视整个系统各个主要参数的运行情况;这些参数包括:输入炉内的三相电弧电流,三相电弧电压,三相电弧功率,电能耗的实时显示和历史趋势显示。
冷却水系统温度监测点的水温监测以及流量及压力的监测和超温越限报警。
35KV高压系统过流、欠压监测。
电炉变压器的各种故障报警信号监测和报警,变压器低压侧过电流和高压跳闸信号的监测。
炉体状态显示及液压系统的工作状态监测。
同时,在不同冶炼阶段炉内三相电弧工作电流的给定值、冶炼时间、35KV高压通电时间,钢水温度的显示以及各种报警参数的历史记录和打印报表的生成。
2.3通讯网络的组态网络组态采用SIEMENS公司的SIMATICNET,NCMS7PROFIBUS组态软件完成PROFIBUSS7通讯网的网络组态。
在工程师站、操作员站分别设计安装CP5412网卡,在四台PLC主站安装CP342-5通讯模块,通过SIEMENS公司的PROFIBUSS7通讯电缆完成工程师站、操作员站和分别分布在电弧炉及钢包精炼炉主控制室的四台PLC主站之间的通讯网络硬件组态。
3抗干扰措施的设计和实施在电弧炉炼钢的工业环境中,切实有效的硬件和软件抗干扰措施的实施成为系统设计和工厂设计及设备制造和安装过程中必须谨慎考虑的非常主要的环节。
根据现场运行实践证明,电炉变压器在高压合闸瞬间所产生的浪涌,大电流运行时变压器所产生的强磁场,炉内电弧以及大电流线路在电弧短路时所产生的强电磁场,电网的谐波分量等诸因素综合起来的干扰源可视为一个从低频到甚高频的宽带噪声源,其所产生的各种干扰都将严重威胁系统运行及通讯网络的安全和稳定。
故而在设计中针对各种干扰的存在考虑了以下的抗干扰措施:3.1隔离电源PLC主站和远程从站的工作电源均通过带屏蔽的隔离变压器完成对PLC电源供电,使PLC与大功率电气设备的电位隔离开来,以避免供电线路带来的噪扰。
3.2电源滤波器隔离变压器的二次侧采用电源滤波器以滤除和衰减以共模和串模形态出现的工频干扰。
共模形态出现的干扰将沿地线被滤除,串模干扰则被旁路。
3.3有源隔离端子现场引入的模拟量输入信号和输出信号采用有源隔离端子将由地环路引起的噪声隔离,切断通过现场引入的模拟量信号地环路中的噪声通道。
3.4模拟量输入通道的滤波三相电弧电流、电弧电压等主要电气参数的模拟量采样信号输入通道在进入PLC模拟量通道前在经过有源隔离后再由有源滤波器抑制模拟量通道中的串模干扰,在保证有用信号不被衰减的情况下最大限度地将高频噪声衰减,提高通道的信噪比。
有源滤波能确保通道信号的增益。
3.5模拟量通道的屏蔽模拟量通道的输入信号传输导线设计采用耐高温的有屏蔽的双绞线电缆以降低辐射干扰和电磁耦合性干扰。
3.6数字量输入通道的隔离PLC的数字量输入通道采用光电隔离模块,从强电场现场环境(如高压开关室的真空断路器柜)引入的数字量信号在其触点和模块间加设中间继电器对通道进行双重隔离,防在真空断路器合闸操作同时强干扰串入而引起真空断路器误分闸动作。
3.7数字量输出通道的隔离PLC的数字量输出通道主要驱动交流和直流感性负载,大电流负载采用中间继电器过渡,所有通道均设计采用浪涌吸收和RC组件做为保护。
3.8电磁屏蔽工程师站和操作员站采用钢壳机箱的工控机,系统中的电子设备亦采用屏蔽外壳,再置入控制柜台内形成与柜台外壳间绝缘的双重电磁屏蔽。
PLC采用悬浮安置方式将金属安装底版与柜壳绝缘隔离。
所有电子设备均采用独立引出的专用地线接地,柜台的外壳则接保护地。
3.9电子设备的浮地供电电子设备的直流供电电源采用浮地供电,输入和输出通道直流供电电源各自独立。
计算机采用在线式UPS电源供电,电子设备采用线性电源供电,其它直流负载采用开关电源供电。
3.10通讯电缆的敷设两个物理层的通讯电缆采用SIEMENS公司的PROFIBUS通讯电缆(buscablesolid)?熏在敷设时单独金属穿管。
电缆的屏蔽层通过电缆插头的金属外壳经PLC的通讯模块CP和DP的接口接入独立引出的专用地线接地。
同时在电缆走向上注意避免与动力电缆平行,并尽可能远离电炉炉体和大电流线路。
3.11地线电弧炉炉体外壳采用相对独立的接地线引出接地。
电气设备的保护接地进入工厂接地网。
计算机、PLC和通讯网络及电子设备的接地则进入独立的专用地线。
浮地处理的电子设备的地线各自独立。
3.12电气设备制造工艺的保证电气设备柜内的布局,柜内各种电缆和导线(动力、信号、通讯以及接地)的走向,屏蔽和接地的合理布置也是须在设计和设备制造过程中加以认真考虑的。
3.13软件设计中的抗干扰处理合理设置PLC的硬件看门狗时间及采样中断时间。
在程序设计中对数字量输入信号采用脉宽甄别、锁存、指令复执技术。
在对缓变的模拟量信号进行运算处理之前采用滑动均值滤波等数字滤波技术措施。
在PID调节过程中对干扰比较敏感的一是当偏差e较小时,易受影响,二是微分项易引起较大变动。
前者用一阶及一阶滞后滤波处理,后者则用不完全微分型PID算法。