挤出成型工艺参数包括温度(优质借鉴)
挤出成型工艺参数的控制
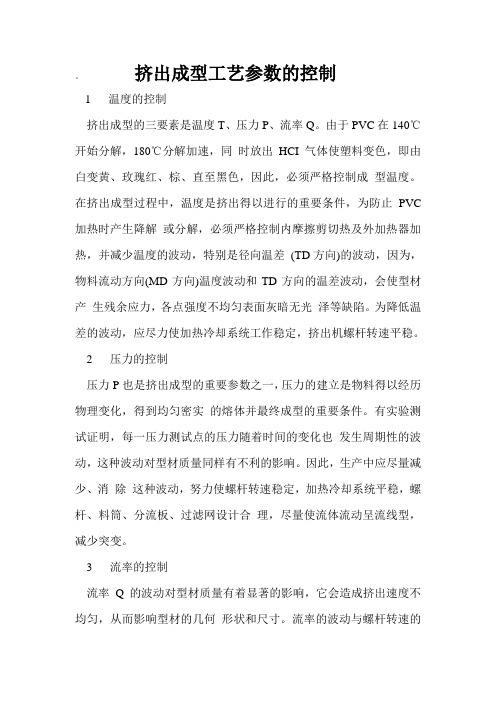
挤出成型工艺参数的控制1 温度的控制挤出成型的三要素是温度T、压力P、流率Q。
由于PVC在140℃开始分解,180℃分解加速,同时放出HCI气体使塑料变色,即由白变黄、玫瑰红、棕、直至黑色,因此,必须严格控制成型温度。
在挤出成型过程中,温度是挤出得以进行的重要条件,为防止PVC 加热时产生降解或分解,必须严格控制内摩擦剪切热及外加热器加热,并减少温度的波动,特别是径向温差(TD方向)的波动,因为,物料流动方向(MD方向)温度波动和TD方向的温差波动,会使型材产生残余应力,各点强度不均匀表面灰暗无光泽等缺陷。
为降低温差的波动,应尽力使加热冷却系统工作稳定,挤出机螺杆转速平稳。
2 压力的控制压力P也是挤出成型的重要参数之一,压力的建立是物料得以经历物理变化,得到均匀密实的熔体并最终成型的重要条件。
有实验测试证明,每一压力测试点的压力随着时间的变化也发生周期性的波动,这种波动对型材质量同样有不利的影响。
因此,生产中应尽量减少、消除这种波动,努力使螺杆转速稳定,加热冷却系统平稳,螺杆、料筒、分流板、过滤网设计合理,尽量使流体流动呈流线型,减少突变。
3 流率的控制流率Q的波动对型材质量有着显著的影响,它会造成挤出速度不均匀,从而影响型材的几何形状和尺寸。
流率的波动与螺杆转速的稳定与否、温控系统的性能、加料情况有密切关系。
对操作者而言,重点应考虑加料的连续性,避免间歇加料。
同时,注意料斗的“架桥”现象发生。
挤出成型中,产量与挤出流率是密切相关的,流率必须与牵引速度相适应,相匹配。
4 牵引速度的控制牵引速度直接影响型材的壁厚和截面尺寸的精确性,它的波动会导致型材截面尺寸的变化,通常牵引速度比挤出速率稍快些。
在调整参数时应参考挤出机特性曲线,使挤出机的挤出处于最佳工作点,追求最佳质量与效益。
如只提高螺杆转速而其它工艺条件不改变,则塑化质量降低,型材内壁粗糙,强度不高。
栾军型材车间2003年1月16日。
peek挤出造粒参数

peek挤出造粒参数
PEEK的挤出造粒参数主要包括以下几点:
1. 温度控制:根据原料和产品的不同,温度设置在230°C\~370°C之间。
2. 螺杆转速:螺杆转速通常在100\~150rpm之间,但具体转速应视产品
要求和设备性能而定。
3. 模头温度:模头温度对产品的成型质量和外观影响较大,一般设置在270°C\~300°C之间。
4. 牵引速度:牵引速度决定了产品的厚度和生产效率,通常在
20\~50m/min之间。
5. 收卷张力:收卷张力决定了产品的致密度和平整度,通常在2\~8kg之间。
6. 添加剂使用:根据需要,可以添加一定比例的增强剂、阻燃剂、抗菌剂等添加剂。
7. 冷却时间:冷却时间对产品的性能和生产效率有影响,一般冷却时间在
10\~30秒之间。
8. 切割长度:根据需要,可以设定不同的切割长度,切割长度一般在
10\~30mm之间。
9. 供料速度:供料速度决定了挤出机的生产效率,供料速度在
30\~120r/min之间。
10. 设备配置:根据生产需要,可以选择不同配置的挤出机、切粒机、干燥机等设备。
请注意,这些参数不是固定的,具体需要根据设备性能、产品要求以及生产环境等因素进行调整。
同时,还需要注意安全操作规程,确保生产过程中的安全。
挤出成型工艺参数包括温度
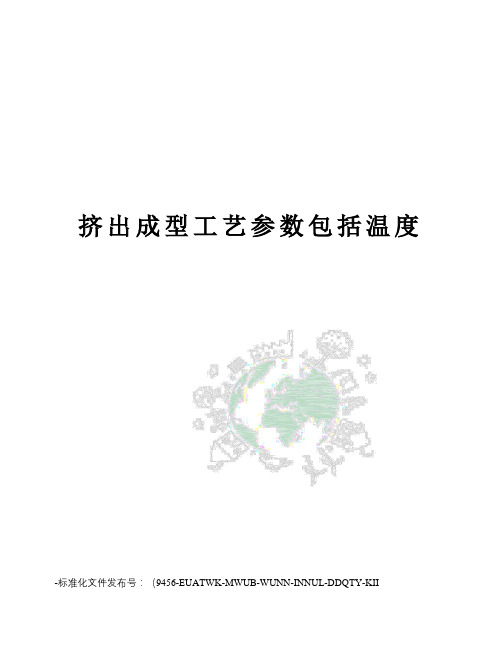
挤出成型工艺参数包括温度-标准化文件发布号:(9456-EUATWK-MWUB-WUNN-INNUL-DDQTY-KII
1.
2. 压力
在挤出过程中,由于料流的阻力,螺杆槽深度的变化,以及过滤网、过滤板增加机头压力可以提高挤出熔体的混合均匀性和稳定性,提高产品致密度,和温度一样,压力随时间的变化也会产生周期性波动,这种波动对塑件质量
3. 挤出速率
挤出速率(亦称挤出速度)是单位时间内挤出机口模挤出的塑料质量(单位kg/h)或长度(单位为m/min)。
挤出速度的大小表征着挤出生产能力的高
影响挤出速度的因素很多,如机头、螺杆和料筒的结构、螺杆转速、加热冷。
高分子材料成型加工中的挤出成型工艺参数优化
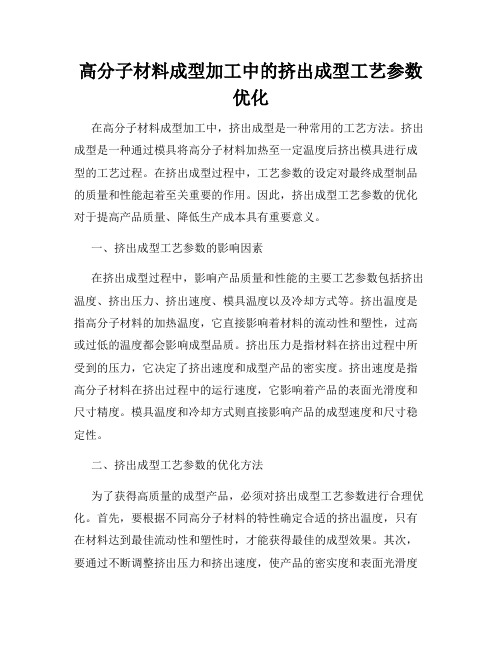
高分子材料成型加工中的挤出成型工艺参数优化在高分子材料成型加工中,挤出成型是一种常用的工艺方法。
挤出成型是一种通过模具将高分子材料加热至一定温度后挤出模具进行成型的工艺过程。
在挤出成型过程中,工艺参数的设定对最终成型制品的质量和性能起着至关重要的作用。
因此,挤出成型工艺参数的优化对于提高产品质量、降低生产成本具有重要意义。
一、挤出成型工艺参数的影响因素在挤出成型过程中,影响产品质量和性能的主要工艺参数包括挤出温度、挤出压力、挤出速度、模具温度以及冷却方式等。
挤出温度是指高分子材料的加热温度,它直接影响着材料的流动性和塑性,过高或过低的温度都会影响成型品质。
挤出压力是指材料在挤出过程中所受到的压力,它决定了挤出速度和成型产品的密实度。
挤出速度是指高分子材料在挤出过程中的运行速度,它影响着产品的表面光滑度和尺寸精度。
模具温度和冷却方式则直接影响产品的成型速度和尺寸稳定性。
二、挤出成型工艺参数的优化方法为了获得高质量的成型产品,必须对挤出成型工艺参数进行合理优化。
首先,要根据不同高分子材料的特性确定合适的挤出温度,只有在材料达到最佳流动性和塑性时,才能获得最佳的成型效果。
其次,要通过不断调整挤出压力和挤出速度,使产品的密实度和表面光滑度达到最佳状态。
同时,要合理控制模具温度和采用适当的冷却方式,保证产品的尺寸稳定性和成型速度。
三、挤出成型工艺参数优化的意义挤出成型工艺参数的优化不仅能够提高产品的质量和性能,还能够降低生产成本,提高生产效率。
合理设定工艺参数可以减少废品率,降低维护成本,增加生产线的稳定性和可靠性。
此外,优化工艺参数还可以提高产品的竞争力,满足市场需求,促进企业的可持续发展。
综上所述,挤出成型工艺参数的优化对于高分子材料成型加工具有重要的意义。
合理设定挤出温度、挤出压力、挤出速度、模具温度和冷却方式等工艺参数,可以获得更高质量的成型产品,降低生产成本,提高生产效率,促进企业的可持续发展。
挤出成型工艺参数包括
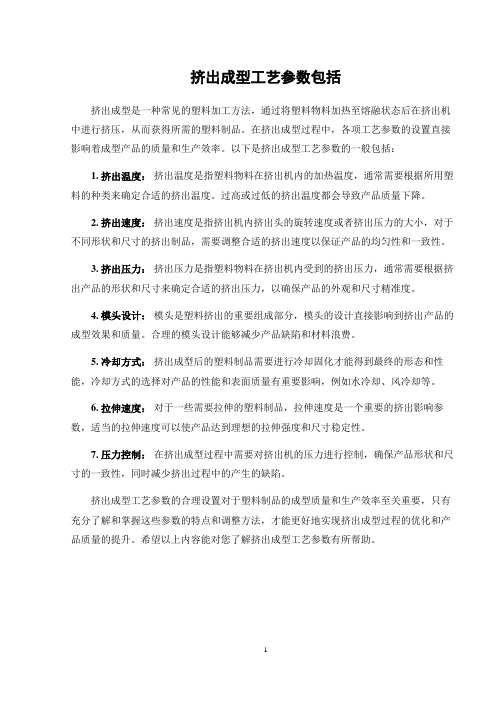
挤出成型工艺参数包括挤出成型是一种常见的塑料加工方法,通过将塑料物料加热至熔融状态后在挤出机中进行挤压,从而获得所需的塑料制品。
在挤出成型过程中,各项工艺参数的设置直接影响着成型产品的质量和生产效率。
以下是挤出成型工艺参数的一般包括:1. 挤出温度:挤出温度是指塑料物料在挤出机内的加热温度,通常需要根据所用塑料的种类来确定合适的挤出温度。
过高或过低的挤出温度都会导致产品质量下降。
2. 挤出速度:挤出速度是指挤出机内挤出头的旋转速度或者挤出压力的大小,对于不同形状和尺寸的挤出制品,需要调整合适的挤出速度以保证产品的均匀性和一致性。
3. 挤出压力:挤出压力是指塑料物料在挤出机内受到的挤出压力,通常需要根据挤出产品的形状和尺寸来确定合适的挤出压力,以确保产品的外观和尺寸精准度。
4. 模头设计:模头是塑料挤出的重要组成部分,模头的设计直接影响到挤出产品的成型效果和质量。
合理的模头设计能够减少产品缺陷和材料浪费。
5. 冷却方式:挤出成型后的塑料制品需要进行冷却固化才能得到最终的形态和性能,冷却方式的选择对产品的性能和表面质量有重要影响,例如水冷却、风冷却等。
6. 拉伸速度:对于一些需要拉伸的塑料制品,拉伸速度是一个重要的挤出影响参数,适当的拉伸速度可以使产品达到理想的拉伸强度和尺寸稳定性。
7. 压力控制:在挤出成型过程中需要对挤出机的压力进行控制,确保产品形状和尺寸的一致性,同时减少挤出过程中的产生的缺陷。
挤出成型工艺参数的合理设置对于塑料制品的成型质量和生产效率至关重要,只有充分了解和掌握这些参数的特点和调整方法,才能更好地实现挤出成型过程的优化和产品质量的提升。
希望以上内容能对您了解挤出成型工艺参数有所帮助。
1。
挤出机常识与工艺(温度、螺杆)教材
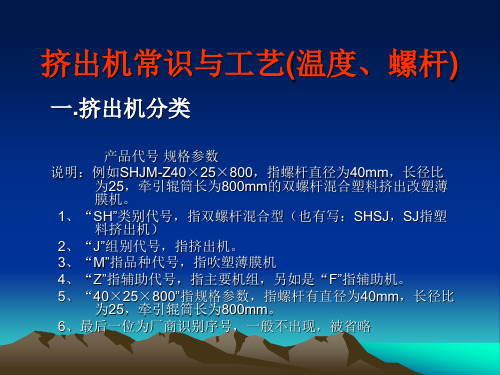
5.均化(料量)段
•
•
A螺杆组合
螺纹块导程渐变小或螺槽渐变小来实现增压,减少背压段长度,同时注意采用单 头螺纹与宽螺棱螺纹来提高排料能力,避免冒料。 B温度设定, 以适当降低温度,但模头高温利于排料。 在熔融段温度基础上,适当降低温度,其原则:根据带光泽降度而定
• • •
五、转速问题:
•
• • • • • • • •
三、螺杆排列及其工艺设定
①螺杆的分段及其功能
• • • • • • • • (1)螺杆一般分:输送段、熔融段、混炼段、排气段、均化段5个段。 1、输送段,输送物料,防止溢料。 2、熔融段,此段通过热传递和摩擦剪切,使物料充分熔融和均化。 3、混炼段,使物料组分尺寸进一步细化与均匀,形成理想的结构, 具分布性与分散性混合功能。 4、排气段,排出水汽、低分子量物质等杂质。 5、均化(计量)段,输送和增压,建立一定压力,使模口处物料有 一定的致密度,同时进一步混合,最终达到顺利挤出造粒的目的。 (2)分布(分配)与分散混合之段别 1、分布混合,使熔体分割与重组,使各组分空间分布均匀,主要通过 分离,拉伸(压缩与膨胀交替产生)、扭曲、流体活动重新取向等应力 作用下置换流动而实现。 2、分散混合,使组分破碎成微粒或使不相容的两组分分散相尺寸达至 要求范围,主靠剪切压力和接伸应力实现。
•
②输送元件,螺纹式的
• 表示法:如“56/56”输送块,前一个”56”指导程为56MM,后一 个”56”指长度为56MM。 • 大导程,指螺距为1.5D~2D • 小导程,指螺距为0.4D左右。 • 其使用规律:随着导程增加,螺杆挤出量增加,物料停留时间减少, 混合效果降低。 • A、选用大导程螺纹的场合,以输送为主的场合,利于提高产量;热 敏性聚合物,缩短停留时间,减少降解;排气处,选用(也有选用浅 槽),增大表面积,利于排气,挥发等。 • B、选用中导程螺纹场合,以混合为主的场合,具不同的工作段逐渐 缩小的组合,用于输送和增压。 • C、选取用小导程螺纹的场合,为一般是组合上逐渐减小,用于输送 段和均化计量段,起到增压,提高熔融;提高混合物化程度及挤出稳 定。
tpe挤出机温度参数

tpe挤出机温度参数TPE挤出机温度参数TPE(热塑性弹性体)挤出机是一种专门用于加工TPE材料的设备。
在TPE挤出过程中,温度参数的设置对产品质量和生产效率都有重要影响。
本文将从挤出机的温度控制、熔体温度、模具温度等方面介绍TPE挤出机的温度参数。
一、温度控制系统TPE挤出机的温度控制系统通常由加热装置、温度传感器和控制器组成。
加热装置通过加热元件对挤出机的加热区域进行加热,温度传感器检测加热区域的温度,并将信号传递给控制器。
控制器根据设定的温度参数,控制加热装置的工作状态,从而实现温度的控制。
二、熔体温度熔体温度是TPE挤出过程中最关键的温度参数之一。
熔体温度的高低直接影响到挤出机的挤出性能和产品的质量。
一般来说,TPE的熔体温度应控制在材料的熔点以上10-20℃的范围内。
如果温度过高,会导致材料热分解、氧化等问题,严重影响产品质量;如果温度过低,会导致材料熔化不彻底,挤出困难,影响生产效率。
三、模具温度模具温度是指TPE在挤出过程中接触到的模具的温度。
模具温度的设置对产品的尺寸精度、表面光洁度和物理性能都有很大影响。
一般来说,模具温度应根据TPE材料的特性和产品要求进行调整。
如果模具温度过高,会导致产品表面融化、变形等问题;如果模具温度过低,会导致产品收缩不均匀,尺寸精度差。
四、升温速率升温速率是指TPE挤出机加热区域温度的升高速率。
升温速率对熔体的熔化和挤出速度有直接影响。
一般来说,升温速率应根据TPE 材料的特性和生产要求进行调整。
如果升温速率过快,会导致熔体熔化不充分,挤出不均匀;如果升温速率过慢,会导致生产效率低下。
五、冷却系统TPE挤出机的冷却系统通常由冷却装置、冷却水管路和风扇等组成。
冷却系统的设置对挤出产品的冷却速度和收缩率有重要影响。
一般来说,冷却系统应根据产品的厚度和尺寸进行调整。
如果冷却不充分,会导致产品收缩不均匀,产生内应力,影响产品的物理性能;如果冷却过度,会导致产品表面出现裂纹、变形等问题。
挤出成型工艺参数有哪些

挤出成型工艺参数有哪些
挤出成型是一种常见的塑料加工工艺,通过加热和压力使塑料颗粒在挤出机中经过螺杆挤出,最终成型为所需的产品。
在挤出成型过程中,需要根据不同的塑料材料和成型要求来调整一系列工艺参数,以确保最终产品的质量和性能。
首先,挤出成型工艺参数中最重要的是挤出温度。
挤出温度是指挤出机不同部位的温度设置,通常包括料筒温度、模头温度和模具温度。
不同类型的塑料材料需要在不同的温度下进行挤出,过高或过低的温度都会影响挤出成型的效果,甚至导致产品质量问题。
其次,挤出速度也是一个至关重要的参数。
挤出速度取决于螺杆的旋转速度以及料筒的进料速度,控制好挤出速度可以有效地控制产品的尺寸和表面光洁度。
过快的挤出速度可能导致产生内部应力过大,从而影响产品的外观和力学性能。
除了温度和速度外,压力也是挤出成型中不可忽视的参数之一。
合理的挤出压力可以保证塑料材料充分填充模腔,避免产生气泡和瑕疵,并且有利于产品的密实性和强度。
同时,压力的大小也要根据产品形状和尺寸的不同做出相应的调整,以求达到最佳的成型效果。
此外,挤出成型还需考虑挤出机的螺杆转速、冷却方式、模具结构等参数。
螺杆转速的选择直接影响塑料材料的挤出速度和均匀性,冷却方式则关系到产品的收缩率和外观质量,模具结构的设计要符合产品的形状和尺寸需求,以确保最终产品达到设计要求。
综上所述,挤出成型工艺参数多种多样,需要综合考虑材料特性、产品要求和设备性能等因素,通过合理的调整和控制来实现挤出成型过程中的稳定性和高效性,从而生产出优质的塑料制品。
1。
- 1、下载文档前请自行甄别文档内容的完整性,平台不提供额外的编辑、内容补充、找答案等附加服务。
- 2、"仅部分预览"的文档,不可在线预览部分如存在完整性等问题,可反馈申请退款(可完整预览的文档不适用该条件!)。
- 3、如文档侵犯您的权益,请联系客服反馈,我们会尽快为您处理(人工客服工作时间:9:00-18:30)。
挤出成型工艺参数包括温度、压力、挤出速率和牵引速度等。
1. 温度
温度是挤出成型得以顺利进行的重要条件之一。
从粉状或粒状的固态物料开始,高温制品从机头中挤出,经历了一个复杂的温度变化过程。
严格来讲,挤出成型温度应指塑料熔体的温度,但该温度却在很大程度上取决于料筒和螺杆的温度,一小部分来自在料筒中混合时产生的摩擦热,所以经常用料筒温度近似表示成型温度。
由于料筒和塑料温度在螺杆各段是有差异的,为了使塑料在料筒中输送、熔融、均化和挤出的过程顺利进行,以便高效率地生产高质量制件,关键问题是控制好料筒各段温度,料筒温度的调节是靠挤出机的加热冷却系统和温度控制系统来实现的。
机头温度必须控制在塑料热分解温度以下,而口模处的温度可比机头温度稍低一些,但应保证塑料熔体具有良好的流动性。
此外,成型过程中温度的波动和温差,将使塑件产生残余应力、各点强度不均匀和表面灰暗无光泽等缺陷。
产生这种波动和温差的因素很多,如加热、冷却系统不稳定,螺杆转速变化等,但以螺杆设计和选用的好坏影响最大。
表9-1是几种塑料挤出成型管材、片材和板材及薄膜等的温度参数。
表9-1 热塑性塑料挤出成型时的温度参数
塑料名称
挤出温度/℃ 原料中水分
控制/% 加料段压缩段均化段机头及口模段
丙烯酸类聚合物室温100~170 ~200 175~210 ≤0.025醋酸纤维素室温110~130 ~150 175~190 <0.5 聚酰胺(PA)室温~90 140~180 ~270 180~270 <0.3 聚乙烯(PE)室温90~140 ~180 160~200 <0.3 硬聚氯乙烯(HPVC)室温~60 120~170 ~180 170~190 <0.2 软聚氯乙烯及氯乙烯共聚
物
室温80~120 ~140 140~190 <0.2 聚苯乙烯(PS)室温~100 130~170 ~220 180~245 <0.1
2. 压力
在挤出过程中,由于料流的阻力,螺杆槽深度的变化,以及过滤网、过滤板和口模等产生阻碍,因而沿料筒轴线方向,在塑料内部产生一定的压力。
这种压力是塑料变为均匀熔体并得到致密塑件的重要条件之一。
增加机头压力可以提高挤出熔体的混合均匀性和稳定性,提高产品致密度,但机头压力过大将影响产量。
和温度一样,压力随时间的变化也会产生周期性波动,这种波动对塑件质量同样有不利影响,螺杆转速的变化,加热、冷却系统的不稳定都是产生压力波动的原因。
为了减少压力波动,应合理控制螺杆转速,保证加热和冷却装置的温度控制精度。
3. 挤出速率
挤出速率(亦称挤出速度)是单位时间内挤出机口模挤出的塑料质量(单位为kg/h)或长度(单位为m/min)。
挤出速度的大小表征着挤出生产能力的高低。
影响挤出速度的因素很多,如机头、螺杆和料筒的结构、螺杆转速、加热冷却系统结构和塑料的特性等。
理论和实践都证明,挤出速率随螺杆直径、螺旋槽深度、均化段长度和螺杆转速的增大而增大,随螺杆末端熔体压力和螺杆与料筒间隙增大而增大。
在挤出机的结构和塑料品种及塑件类型已确定的情况下,挤出速率仅与螺杆转速有关,因此,调整螺杆转速是控制挤出速率的主要措施。
挤出速率在生产过程中也存在波动现象,这将影响塑件的几何形状和尺寸精度。
因此,除了正确确定螺杆结构和尺寸参数之外,还应严格控制螺杆转速,严格控制挤出温度,防止因温度改变而引起挤出压力和熔体粘度变化,从而导致挤出速度的波动。
4. 牵引速度
挤出成型主要生产连续的塑件,因此必须设置牵引装置。
从机头和口模中挤出的塑件,在牵引力作用下将会发生拉伸取向。
拉伸取向程度越高,塑件沿取向方向的拉伸强度也越大,但冷却后长度收缩也大。
通常,牵引速度可与挤出速度相当。
牵引速度与挤出速度的比值称牵引比,其值必须大于1。
表9-2是几种塑料管材的挤出成型工艺参数。
表9-2 几种塑料管材的挤出成型工艺参数
塑料管材工艺参数硬聚氯乙
烯
(HPVC)
软聚氯乙
烯
(LPVC)
低密度
聚乙烯
(LDPE)
ABS
聚酰胺-1010
(PA-1010)
聚碳酸酯
(PC)
管材外径/mm 95 31 24 32.5 31.3 32.8 管材内径/mm 85 25 19 25.5 25 25.5 管材厚度/mm 5 3 2 3 ——
机筒温度/℃ 后段 80 ~ 100 90 ~ 100 90 ~ 100 160 ~ 165 250 ~ 260 200 ~ 240 中段140 ~ 150 120 ~ 130 110 ~ 120 170 ~ 175 260 ~ 270 240 ~ 250 前段160 ~ 170 130 ~ 140 120 ~ 130 175 ~ 180 260 ~ 280 230 ~ 255
机头温度/℃ 160 ~ 170 150 ~ 160 130 ~ 135 175 ~ 180 220 ~ 240 200 ~ 220 口模温度/℃ 160 ~ 180 170 ~ 180 130 ~ 140 190 ~ 195 200 ~ 210 200 ~ 210 螺杆转速/(r/min)12 20 16 10.5 15 10.5 口模内径/mm 90.7 32 24.5 33 44.8 33 芯模外径/mm 79.7 25 19.1 26 38.5 26
稳流定型段长度/mm 120 60 60 50 45 87 牵引比 1.04 1.2 1.1 1.02 1.5 0.97
真空定径套内径/mm 96.5 —25 33 31.7 33 定径套长度/mm 300 —160 250 —250
定径套与口模间距
/mm
———25 20 20。