精益布局管理原则
精益管理五大原则

精益管理五大原则全文共四篇示例,供您参考第一篇示例:精益管理(Lean Management)作为一种高效的管理理念,旨在通过减少浪费、提高效率和质量,实现组织的持续改进。
精益管理的五大原则是其核心理念之一,它们为组织提供了指导方针,帮助其实现更高水平的生产和运营效率。
本文将从各个角度对精益管理的五大原则进行详细介绍,帮助读者深入了解这一管理理念。
第一大原则是价值的识别(Value Identification)。
从顾客的角度出发,理解顾客对产品或服务的真正需求,是企业精益管理的出发点。
意味着企业需要聚焦于生产出顾客愿意购买且愿意支付的产品,而不是盲目地追求规模和产量。
这一原则的核心是通过深入洞察顾客需求、消除无价值的活动,实现价值的最大化。
在实践中,企业需要通过对市场的调研和顾客的反馈,不断优化产品和服务的设计,以确保其能够真正满足市场需求。
第二大原则是价值流的映射(Value Stream Mapping)。
价值流是指将一系列的活动和过程连接起来,产生出顾客信任和愿意支付的产品或服务的全过程。
价值流映射的目的是识别出整个价值流程中的浪费和瓶颈,以便能够全面地优化生产过程。
通过价值流映射,企业能够清晰地了解整个价值流程,识别出影响生产效率和质量的问题,为后续的改进工作提供方向。
第三大原则是流程的拉动(Pull System)。
流程的拉动是指根据实际需求进行生产,而不是依据预测的需求进行批量生产。
这一原则的核心是避免过度生产和库存的积累,通过拉动式生产,使生产与需求之间形成有效的匹配。
通过采用拉动式生产模式,企业能够减少库存积压带来的浪费和成本,保持生产过程的灵活性和高效率。
第四大原则是追求卓越(Pursuit of Perfection)。
追求卓越是精益管理的长期目标和使命。
企业需要不断追求卓越,改善工作流程,提高产品质量,降低成本和交付时间,让企业在竞争中保持优势地位。
这一原则的核心是以不断改进和创新为动力,推动组织朝着更高水平的效率和质量发展。
3.精益布局
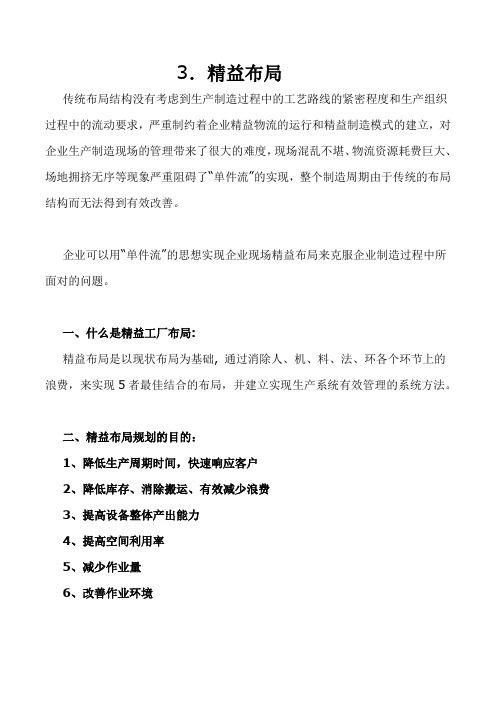
3.精益布局传统布局结构没有考虑到生产制造过程中的工艺路线的紧密程度和生产组织过程中的流动要求,严重制约着企业精益物流的运行和精益制造模式的建立,对企业生产制造现场的管理带来了很大的难度,现场混乱不堪、物流资源耗费巨大、场地拥挤无序等现象严重阻碍了“单件流”的实现,整个制造周期由于传统的布局结构而无法得到有效改善。
企业可以用“单件流”的思想实现企业现场精益布局来克服企业制造过程中所面对的问题。
一、什么是精益工厂布局:精益布局是以现状布局为基础, 通过消除人、机、料、法、环各个环节上的浪费,来实现5者最佳结合的布局,并建立实现生产系统有效管理的系统方法。
二、精益布局规划的目的:1、降低生产周期时间,快速响应客户2、降低库存、消除搬运、有效减少浪费3、提高设备整体产出能力4、提高空间利用率5、减少作业量6、改善作业环境三、未经过精益布局规划的企业工厂布局存在的问题:1、损耗浪费严重据不完全统计,90%以上的企业在新工厂建设时期,由于对企业发展战略和产能规划预想不足,整体物流规划、设备调试和安装、周转期周转量、产线布局及过程设计等因素考虑不完善,有什么摆什么。
因为设计不合理,导致新工厂在投产后出现产距长、设备不足或利用率低、工序不平衡等浪费,企业就这样年复一年,日复一日在这种消耗中生产,这种慢性损耗核算起来,比任何八大浪费都要触目惊心。
2、新厂没有新面貌新工厂,设计者只是关注性能是否符合要求,未考虑和关注设备环境的配色和搭配,建成后灰暗阴沉,毫无生气,员工在里面不要说朝气蓬勃,简直要得抑郁症。
有的工厂就是偏爱蓝色,企业LOGO是蓝色,设备是蓝色,货架和工具柜也是蓝色,好不容易刷个通道吧,因为只有蓝色油漆,也刷成了蓝色!全公司在一片蓝灰里面,冷冷清清,怎么会有温馨明朗的氛围?3、旧厂复制,没有竞争优势很多新工厂只是旧厂的翻版,没有考虑旧厂的一些不合理,采用新的技术或者新的装备去解决问题,效率效益没有提升。
生产精益管理原则及技巧

生产精益管理的原则与技巧建立稳定的流程,运用不断改进的工具以找出导致缺乏效率的根本原因,并采取有效的对策,把最佳实务标准化,以促进学习,而不是在每个新计划及每位新经理人上台后,又重新发明新方法。
一、生产精益管理的原则1、建立无间断流程以使问题浮现。
要求重新设计流程,使流程不仅仅是工作过程的描述。
一定要建立快速输送材料与信息的流程,使流程与员工的行为动作紧密地联结在一起。
要使整个企业文化重视流程,这是促成真正的持续改进流程及员工发展的关键。
2、实施拉式生产制度以避免生产过剩在你生产流程下游的客户有需求的时候,供应给他们正确数量的正确东西。
使在制品及库存减至最少,每项产品只维持少量存货,根据向客户实际交付的数量,经常补充存货。
按客户的需求每天进行调整在制品和存货量,而不是依靠计算机的时间表与系统来追踪已经成为浪费的存货。
3、建立立即暂停以解决问题,从一开始就重视品质管理的文化为顾客提供的品质决定着你的定价。
你要想收益高,首先需要品质好。
为了提高品质,应该使用所有能够确保产品品质的现代方法。
想一想,我们的方法是不是能够确保产品品质?使生产设备具有发现问题及一发现问题就停止生产的能力。
在企业中设立支持快速解决问题的制度和监督检测。
在企业文化中融入发生问题时立即暂停或减缓速度、就地改进质量以提升长期生产力的概念。
4、工作的标准化是持续改进与授权员工的基础在工作场所中的任何地方都使用稳定、可重复的方法,以维持流程的可预测性、规律的运作时间,以及规律的产出。
到一定时间时,应该汲取对流程的累积学习心得,把“现在”的最佳实务进行标准化,让员工对于标准提出有创意的改进意见,把这些见解纳入新标准中。
5、使工作负荷水准稳定(生产均衡化),工作应象龟兔赛跑中的乌龟一样杜绝浪费只是实现精益所必须做的工作的1/3。
避免员工与设备的负荷过重,以避免生产安排的不均匀,也同等重要。
尽量使所有制造与服务流程的工作负荷平均化,以取代大多数公司实行的批量生产方法中经常启动、停止、启动的做法。
精益生产设施布局优化
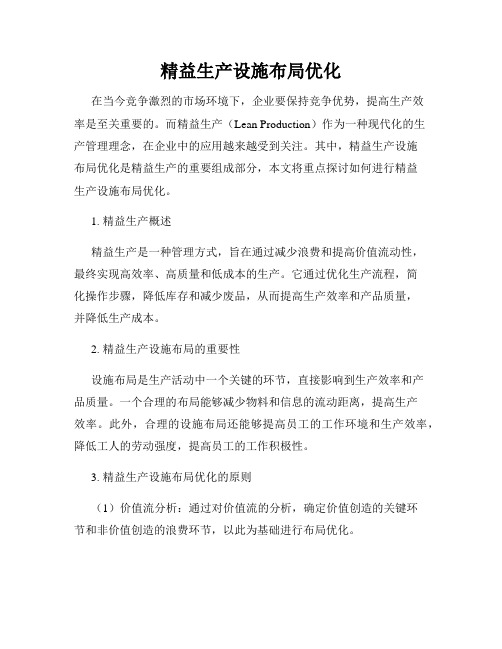
精益生产设施布局优化在当今竞争激烈的市场环境下,企业要保持竞争优势,提高生产效率是至关重要的。
而精益生产(Lean Production)作为一种现代化的生产管理理念,在企业中的应用越来越受到关注。
其中,精益生产设施布局优化是精益生产的重要组成部分,本文将重点探讨如何进行精益生产设施布局优化。
1. 精益生产概述精益生产是一种管理方式,旨在通过减少浪费和提高价值流动性,最终实现高效率、高质量和低成本的生产。
它通过优化生产流程,简化操作步骤,降低库存和减少废品,从而提高生产效率和产品质量,并降低生产成本。
2. 精益生产设施布局的重要性设施布局是生产活动中一个关键的环节,直接影响到生产效率和产品质量。
一个合理的布局能够减少物料和信息的流动距离,提高生产效率。
此外,合理的设施布局还能够提高员工的工作环境和生产效率,降低工人的劳动强度,提高员工的工作积极性。
3. 精益生产设施布局优化的原则(1)价值流分析:通过对价值流的分析,确定价值创造的关键环节和非价值创造的浪费环节,以此为基础进行布局优化。
(2)物料流动性:在布局优化中,要尽量减少物料的运输距离,确保物料流动顺畅,避免过长的等待时间和不必要的运输。
(3)信息流动性:信息在生产过程中起着重要的指导作用,因此在布局优化中要确保信息的流动顺畅,减少信息传递的时间和误差。
(4)工作人员流动性:在布局优化中,要考虑员工的流动性,确保员工能够快速高效地完成各项工作,同时减少员工的劳动强度。
4. 精益生产设施布局优化的关键步骤(1)确定布局目标:根据企业的生产需求和战略目标,明确设施布局的优化目标。
(2)价值流分析:通过对企业生产价值流的分析,确定价值创造和非价值创造的关键环节,为后续优化提供依据。
(3)布局规划:基于价值流分析的结果,进行合理的设施布局规划,确保物料和信息的流动顺畅,降低运输和等待时间。
(4)实施和监控:根据布局规划,逐步实施设施布局优化,同时进行监控和评估,不断改进和优化。
精益管理的核心原则

精益管理的核心原则精益管理是一种追求卓越、追求效率的管理理念和方法,它强调以最小的资源投入,创造出尽可能多的价值,为顾客提供尽可能多的利益。
精益管理的核心原则包括以下几个方面:1.价值原则精益管理的核心思想是消除浪费,创造价值。
在企业管理中,要识别出顾客真正需要的东西,去除那些无用的环节和资源,以最小的投入创造更多的价值。
精益管理强调的是以价值为导向的管理,即通过不断挖掘和提升产品的价值和效益,实现企业价值的最大化。
2.流动原则精益管理的第二个核心原则是流动原则。
在企业中,资源的流动应该是有节奏、有计划、有秩序的,以最小的人力、物力和财力的投入实现高效运转。
精益管理要求企业的各项活动应该像水一样流动起来,形成一个连续的、流畅的生产流程,消除生产中的各种等待、滞留和浪费现象。
3.完美原则精益管理追求完美,它要求企业追求完美的产品品质、完美的服务水平、完美的企业形象。
精益管理强调持续改进、追求卓越,通过不断改善生产流程、优化组织结构、提高员工素质来实现企业的完美化。
精益管理不仅要求企业在产品和服务上做到完美,还要求企业在企业管理、企业文化等方面做到完美。
4.用户驱动原则精益管理的最后一个核心原则是用户驱动原则。
用户是企业生存的基础,精益管理要求企业以用户为中心,以满足用户需求为导向,不断改进产品和服务质量。
精益管理强调与用户的紧密合作,通过与用户的互动和反馈来不断优化产品和服务,提高用户满意度。
除了以上四个核心原则外,精益管理还有许多其他重要的原则和方法,如:5.标准化原则标准化是精益管理的基础,它可以帮助企业规范管理、提高效率、降低成本。
精益管理要求企业建立一套完善的标准化体系,包括生产流程、操作规范、质量标准等,以确保企业各项活动的高效、有序和稳定。
6.持续改进原则持续改进是精益管理的核心理念之一,它要求企业不断寻找和发现存在的问题和不足,通过持续改进来不断提高企业的竞争力和市场占有率。
精益管理鼓励员工提出改进意见和建议,通过不断学习和创新来提高企业的整体素质。
精益生产生产车间现场管理

精益生产车间现场管理:提升效率与品质的关键策略一、现场布局优化,提升空间利用率1. 合理规划生产线布局,减少物料搬运距离。
根据生产流程,将相关工序紧密排列,降低在制品的移动次数,提高生产效率。
2. 采用流线型设计,确保生产流程顺畅。
通过分析生产过程中的瓶颈环节,优化设备布局,使物料流动更加顺畅。
3. 创设整洁、有序的现场环境。
定期清理现场,消除不必要的物品,确保生产空间宽敞,降低安全事故发生的概率。
二、标准化作业,确保生产稳定性1. 制定详细的生产作业指导书,明确各工序操作规程。
让员工按照标准作业,减少人为失误,提高产品质量。
2. 开展技能培训,提高员工操作水平。
针对不同岗位需求,组织专业培训,提升员工技能,降低生产过程中的不良品率。
3. 落实岗位责任制,强化员工责任心。
明确各岗位职责,确保每位员工都能认真负责地完成本职工作。
三、目视化管理,提高现场透明度1. 利用颜色、标识等手段,对现场进行分区、定置。
使员工一目了然,快速找到所需物品,提高工作效率。
2. 设立看板系统,实时展示生产进度、质量状况。
让员工了解生产现状,便于及时调整生产计划。
3. 建立异常反馈机制,鼓励员工发现问题、解决问题。
通过目视化管理,让问题无处藏身,确保生产顺利进行。
四、持续改善,推动现场管理不断提升1. 开展全员参与的质量管理活动,激发员工潜能。
鼓励员工提出合理化建议,不断优化生产流程。
2. 定期组织现场巡查,查找问题根源。
针对发现的问题,制定改进措施,落实整改。
3. 建立持续改善的长效机制,将现场管理纳入日常工作中。
通过持续改进,不断提升车间现场管理水平。
五、库存控制,减少浪费提高响应速度1. 实施准时制生产(JIT),减少在制品和成品库存。
通过精确的需求预测和订单管理,降低库存成本,提高资金周转率。
2. 推行看板管理系统,实现按需生产。
根据生产线的实际消耗情况,动态调整物料供应,避免过量生产。
3. 建立库存预警机制,及时发现潜在问题。
精益布局的原则
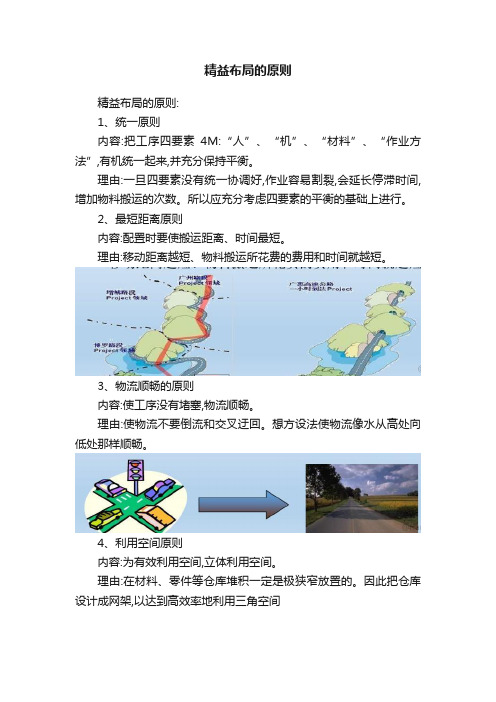
分数四则混合运算(一)一、计算:65+35×54 85-41×(98÷32) (21-61)×53÷5161÷179×(43+32) 1211-41+103÷53 32÷(43-21)×5452+154-52 76×85+83÷67 (117-83)×88 13—48×(121+161)54÷3+32×54 52+21×53+107 1312×73+74×1312+1312二、解方程。
75X - 97 = 913 43X - 31X = 25X + 0.25X = 75三、只列式不必计算。
(1)某仓库的地面是长方形,宽是15米,是长的43。
这个仓库地面面积是多少?列式:(2)一棵龙眼树今年产量是490千克,比去年增产了61,这棵龙眼树去年的产量是多少千克?解:设这棵龙眼数去年的产量是X 千克。
列式:四、列式计算一个数的109是43,这个数是多少? 43减去43与54的积,所得的差除9,商是几?五、解决问题:1、从A 地去B 地,货车需要90分钟,客车需要80分钟。
货车每分钟行35千米,客车每分钟行多少千米?2、一桶油已经用去85后,还剩24千克,这桶油原来有多少千克?3、修一条7500米的水渠,第一期修了全长的31,第二期修了全长的61,两期共修多少米? 4、笑笑利用周末录入一份稿件,已经录了全部稿件的73,如果再继续录入500个字就完成这份稿件的一半,这份稿件共有多少个字?5、服装厂加工1500套校服,前5天加工了这批校服的52,离交货期还有一周的时间,照这样计算,服装厂能按时完成任务吗?分数四则混合运算(二)1、计算 (87-165)×(95+32) 138÷7+71×136 1-(41+83)÷4197÷511+92×115 (61+43-32)×12 2-136÷269-32 99×1009921÷85+41×53 43×52+41÷25 2110×207÷65-41 45×4443(83-41)÷83 83÷(83-41) 65×4-(87+32) 5-87-0.1252、计算下列物体的表面积。
精益布局八大管理要素
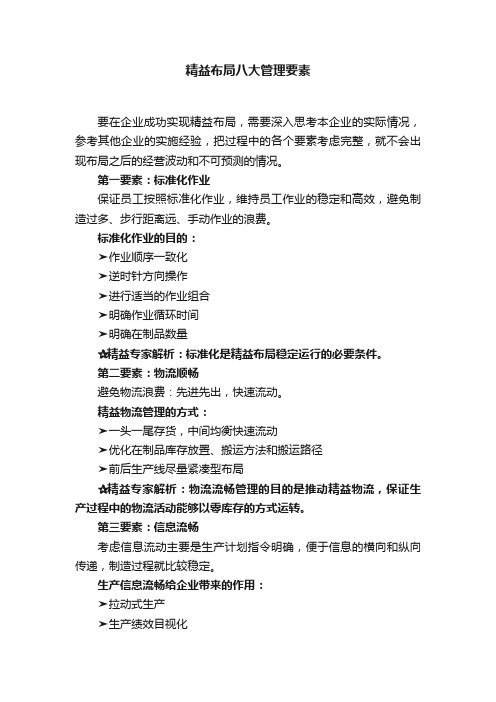
精益布局八大管理要素要在企业成功实现精益布局,需要深入思考本企业的实际情况,参考其他企业的实施经验,把过程中的各个要素考虑完整,就不会出现布局之后的经营波动和不可预测的情况。
第一要素:标准化作业保证员工按照标准化作业,维持员工作业的稳定和高效,避免制造过多、步行距离远、手动作业的浪费。
标准化作业的目的:➤作业顺序一致化➤逆时针方向操作➤进行适当的作业组合➤明确作业循环时间➤明确在制品数量✰精益专家解析:标准化是精益布局稳定运行的必要条件。
第二要素:物流顺畅避免物流浪费:先进先出,快速流动。
精益物流管理的方式:➤一头一尾存货,中间均衡快速流动➤优化在制品库存放置、搬运方法和搬运路径➤前后生产线尽量紧凑型布局✰精益专家解析:物流流畅管理的目的是推动精益物流,保证生产过程中的物流活动能够以零库存的方式运转。
第三要素:信息流畅考虑信息流动主要是生产计划指令明确,便于信息的横向和纵向传递,制造过程就比较稳定。
生产信息流畅给企业带来的作用:➤拉动式生产➤生产绩效目视化➤便于批量处理✰精益专家解析:信息流是精益布局运行的指令中心,是企业制造过程流畅运行的前提。
第四要素:少人化少人化生产是指企业能够弹性生产,按照客户的需求数量和要求,灵活设置人员结构和人员数量,人多人少都能生产。
少人化的建立需要有一定的条件限制:➤U形布置方式➤逆时针摆放➤设备间无阻隔➤人与设备分工:人—装料、卸料、设备—加工➤启动按钮安装方式适当✰精益专家解析:少人化生产不是减员生产,而是能够灵活的应对市场的需求整合不同的人员达到不同需求条件下的生产要求。
第五要素:质量保证确保全数检查,防止不良发生、杜绝不良流出。
我们可以通过如下措施保证产品质量:➤作业人员自主检查➤避免生产与检查相分离➤设备防错功能➤良好的照明➤现场5S✰精益专家解析:精益布局过程必须对设备、生产工装以及模具进行位置的调整,调整之后的硬件要素需要通过工装评审,才能够保证精益布局条件下产品质量的稳定性。
- 1、下载文档前请自行甄别文档内容的完整性,平台不提供额外的编辑、内容补充、找答案等附加服务。
- 2、"仅部分预览"的文档,不可在线预览部分如存在完整性等问题,可反馈申请退款(可完整预览的文档不适用该条件!)。
- 3、如文档侵犯您的权益,请联系客服反馈,我们会尽快为您处理(人工客服工作时间:9:00-18:30)。
4、利用空间原则
5、安全满意原则
❖ 内容:布置得使工作人员既能安全又能轻松作业。 ❖ 理由:确保作业人员的安全和减轻疲劳是非常重要的。材
料的移动、旋转等都会出现不安全状况,抬升、卸下货物 会加剧作业疲劳、应尽量减少。
6、灵活机动原则
❖ 内容:“适应变化,随机应变,采取灵活措施。 ❖ 理由:面对各工序的变化、增减等变化,尽可能随机应变、见机行事。
精益布局管理探讨
企业精益化管理改善路线图
流动化管理的思路
“流动化管理”是:对现有生产线体的结构和功能进行优化,使之实现“一个 流”的状态,生产过程工序与工序之间只有一个生产件(或最小的经济批量) 在各道工序之间流动。
打 破 孤 岛 作 业 建 立 流 动
课程内容简介
一、传统布局模式介绍
二、企业精益布局介绍 三、精益布局的管理原则 四、精益布局实战 五、项目激励制度 六、领导发言—沈总、姜总
10分车行
300米小路
B终点
5.开车麻烦,要考驾照,哪有那么多时间去学,太麻 烦了。
6.有好多档位,最主要骑自行车我是用手刹车的,现 在要用脚踩,不习惯。
44
7.要买保险,要油费,还是骑车好
8………..太多问题了.所以我还是 选择先骑着自行车先。
你看到了什么? 还有呢?
这么大一块空白的面积你们都没看到吗?
1、统一原则 2、最短距离原则 3、物流顺畅原则 4、利用立体空间原则 5、安全满意原则 6、灵活机动原则
1、统一原则
内容: ——把工序四要素“人”、“机”、“材料”、“作业方法”有机统一
起来,并充分保持平衡。
理由: ——一旦四要素没有统一协调好,作业容易割裂,会延长停滞时间,增
加物料搬运的次数。所以应充分考虑四要素的平衡的基础上进行。
锯床员 滚丝员
倒角员 压字员
滚丝员
流水线验收时间:6月3日; 验收合格激励基金: 800元;
陈峰
现场实际问题解决,员工 作业平衡,设备维修,模 具切换等;
现场实际问题解决,员工 作业平衡,设备维修,模 具切换等;
项目沟通机制
目的: 保证项目过程控制,实现既定目标; 监控项目运行状态,及时提供支持加强沟通交流
❖
好的事情马上就会到来,一切都是最 好的安 排。上 午5时2 0分14 秒上午 5时20 分05:2 0:1420 .12.9
❖
每天都是美好的一天,新的一天开启 。20.1 2.920.12.905 :2005:20:14 05:20:14Dec-20
❖
务实,奋斗,成就,成功。2020年1 2月9日 星期三 5时20 分14秒 Wedn esday , December 09, 2020
课程内容简介
一、传统布局模式介绍 二、企业精益布局介绍 三、精益布局的管理原则
四、精益布局实战
五、项目激励制度 六、领导发言—沈总、姜总
精益布局实施步骤
结构 设计
• 流动单元划分 • 整体结构设计 • 流动方式设计 • 流动单元设计
平衡研 究与资 源规划
线体架 设与试 运行
• 动作及时间研究 • 线平衡改善 • 设备规划 • 人力规划 • 员工培训
• 线体架设准备 • 线体架设 • 试运行
产能爬 坡持续 改进
• 产能爬坡改善 • 持续改进
短条产品布局结构设计
拉丝直条区
盘圆拉丝区
1
滚丝车间
2
1.锯床加工的产品直接滚丝,将滚丝机前移到锯床作业区,锯床完后直接滚丝出货; 2.锯床短条作业,加工完成后,后续倒角、刻字、滚丝按照节拍强制流动,形成流水
做一件事情,重要的不是身外之物是否完备,而是有没有决心!有决心了, 拟定目标了,一切都不是问题! 路在自己脚下!每迈出一步,都是一点点收获! 带心上路,一切困难都将解决!
46
课程内容简介
一、传统布局模式介绍 二、企业精益布局介绍 三、精益布局的管理原则 四、精益布局实战方法 五、项目激励制度
六、领导发言—沈总、姜总
2、最短距离原则
内容:配置时要使搬运距离、时间最短。 理由:移动距离越短、物料搬运所花费的费用和时间就越短。
2、最短距离原则
某车间布局现状示意图
运输路径长,员工劳动强度大;
1
5 3
8
7
4
2
6
经过调查统计: 后减产品从车间 1 到成品出门口,共计运输路径约100m;
2、最短距离原则
6 7
布局后----后减产品流程示意图
一、传统布局的基本形式
1、固定式布局(以产品为中心) 2、功能式布局(以设备为中心) 3、流程式布局(以流程为中心) 4、混合式布局(结合前三种布局)
1、固定式布局(以产品为中心)
——固定式布局是:指所生产加工的产品较大时,以产品为中心, 各加工设备,操作平台围绕着产品有序的布局。 (例如:大型机床、飞机、火车、楼层等)。
❖
重于泰山,轻于鸿毛。05:20:1405:2 0:140 5:20W ednes day, December 09, 2020
❖
不可麻痹大意,要防微杜渐。20.12.920.12 .905:2 0:140 5:20:1 4Dece mber 9, 2020
❖
加强自身建设,增强个人的休养。20 20年1 2月9日 上午5 时20分 20.12.920.1 2.9
1 2
3
0.85m 2.5m
1.以1/2-13 规格为例子:布局方式可采用一字布局,利用滑轨连接,形成一个 加工组; 2.生产过程需要按单生产,过程中可能会切换或调整刻字模/滚丝模等; 3.生产过程中需要专门有人统筹管理,来处理人员/设备/物料等问题;
课程内容简介
一、传统布局模式介绍 二、企业精益布局介绍 三、精益布局的管理原则 四、精益布局实战
5
1
3
4
2
5
此处为 滑槽
根据布局计算: 后减产品从车间 1 到成品出门口,共计运输路径约24m;(原布局100米)
3、物流顺畅原则
内容:使工序没有堵塞,物流顺畅。 理由:使物流不要倒流和交叉迂回。要设法使物流像水从高处向低
处那样顺畅。
4、利用空间原则
内容:为有效利用空间,立体利用空间。 理由:在材料仓库、零件仓库等仓库堆积一定是极狭窄放置的。
俗称:混乱式布局
课程内容简介
一、传统布局模式介绍
二、企业精益布局介绍
三、精益布局的管理原则 四、精益布局实战 五、项目激励制度 六、领导发言—沈总、姜总
二、企业精益布局介绍
定义:
——精益布局是以现状布局为基础, 通过消除人、机、料、法、环 各个环节上的浪费,来实现5者最佳结合的布局。
精益布局的目的:
1.提高工序能力 2.消除搬运 3.提高空间使用率 4.减少作业量 5.作业环境改善
企业5种精益布局模式
❖ 串联式布局
❖并联式布局 ❖U型布局 ❖细胞布局 ❖L型布局
企业精益布局模式
串联布局: 并联布局:
U型布局:
V型布局、T型布局、 细胞作业
1、串联式布局(直肠式布局)
串联布局的优点:
• 物流线路清晰 • 方便设备维修 • 设备配置按物流路线直线配置 • 扩大时只需增加列数即可 • 回收材料与垃圾可用皮带传送
2、并联式布局结构
❖ 适合一人操作两台设备 ❖ 步行及搬运距离短 ❖ 可以随时观察设备运作状态
3、U型布局结构
U型布局优点: • 进料和出料口一致 • 一人操作三台以上的设备 • 可以随时观察设备运作状况 • 员工操作步行距离较近
2 1
3
1
3
2
U型布局结构
4、细胞布局结构(CELL)
小单元型
以最短的供应链, 最大的灵活性来 满足客户的需求
E. 团队精神:
班组的劳动成果 显而易见, 得到承认
F. 成本: 降低库存水平
来源: TPS-丰田公司
课程内容简介
一、传统布局模式介绍 二、企业精益布局介绍
三、精益布局的管理原则
四、精益布局实战 五、项目激励制度 六、领导发言—沈总、姜总
三、企业精益布局的原则
五、项目激励制度
六、领导发言—沈总、姜总
项目组织架构及激励制度
负责项目实施过程中的方 向指引,所需人力物力的 资源协调;
副组长 俞美丽
组长 沈总
项目布局实际负责人,项 目管理、过程管控,人员 协调,沟通会议的组织及 总结等;
落地实施总掌控,协助解 决试运行过程中的实际问 题;
吴海祥主任
锯床线长
倒角线长
❖
追求卓越,让自己更好,向上而生。 2020年 12月9 日星期 三上午 5时20 分14秒 05:20:1420.12.9
❖
严格把控质量关,让生产更加有保障 。2020 年12 月上午5 时20 分20.12 .905:2 0Dece mber 9, 2020
❖
重规矩,严要求,少危险。2020年1 2月9日 星期三 5时20 分14秒 05:20:149 December 2020
1
2 ... n
❖ 适合少量多样生产 ❖ 增加了灵活多变性 ❖ 节省人力、空间
❖ 缩短生产周期、减少 库存、提高质量
螺旋型
Hale Waihona Puke cd e fa一个人推车式
Car t 推 车
store parts
一个人一个单元式 短线式
旋转式
5、L型布局结构
❖ L型布局优点: • 一人操作两台以上的设备 • 可以随时观察设备运作状况 • 员工操作步行距离较近 • 操作物料流动方向与原物流路线一致
45
《上路》
一和尚要云游参学。师傅问:“什么时候动身?”“下个星期。路途远,我 托人打了几双草鞋,取货后就动身。” 师父沉吟一会儿,说:“不如这样,我 来请信众捐赠。师父不知道告诉了多少人,当天竟有好几十名信众送来草鞋,堆 满了禅房的一角。隔天一早,又有人带来一把伞要送给和尚。