产品检验和测量管理程序
测量管理程序文件

测量管理程序文件一、目的为了确保测量工作的准确性、可靠性和一致性,提高产品质量和生产效率,特制定本测量管理程序文件。
二、适用范围本程序适用于公司内所有与测量工作相关的活动,包括但不限于原材料检验、生产过程控制、成品检验、计量器具的管理等。
三、职责分工1、质量部门负责制定和修订测量管理程序文件。
监督测量工作的执行情况,对测量结果进行评估和分析。
组织测量人员的培训和考核。
2、生产部门按照测量要求进行生产过程中的测量工作。
对测量设备进行日常维护和保养。
3、设备管理部门负责测量设备的采购、验收、校准和维修。
建立测量设备的台账和档案。
4、测量人员严格按照测量操作规程进行测量工作。
正确使用和维护测量设备。
如实记录测量数据,并及时上报。
四、测量设备的管理1、采购根据测量工作的需求,由使用部门提出采购申请,经批准后由设备管理部门进行采购。
采购的测量设备应符合国家计量法规和公司的测量要求,具有相应的计量检定证书或校准报告。
2、验收新购置的测量设备到货后,由设备管理部门组织验收。
验收内容包括设备的外观、规格型号、技术参数、附件、计量检定证书或校准报告等。
验收合格的测量设备方可入库或投入使用。
3、校准和检定测量设备应按照规定的周期进行校准或检定。
校准和检定工作应由具有相应资质的计量机构进行。
经校准或检定合格的测量设备应贴上相应的标识,并保存校准或检定记录。
4、标识测量设备应根据其校准或检定结果进行标识,标识分为“合格”、“准用”、“停用”三种。
“合格”标识表示设备经校准或检定合格,可正常使用。
“准用”标识表示设备部分功能或参数不符合要求,但在限定范围内可使用。
“停用”标识表示设备损坏、过期未校准或检定、校准或检定不合格等,禁止使用。
5、使用和维护测量人员应按照操作规程正确使用测量设备,防止因操作不当造成设备损坏或测量结果不准确。
测量设备在使用过程中应注意防潮、防尘、防震,定期进行清洁和保养。
发现测量设备异常时,应立即停止使用,并及时报告设备管理部门进行处理。
产品的监视和测量程序
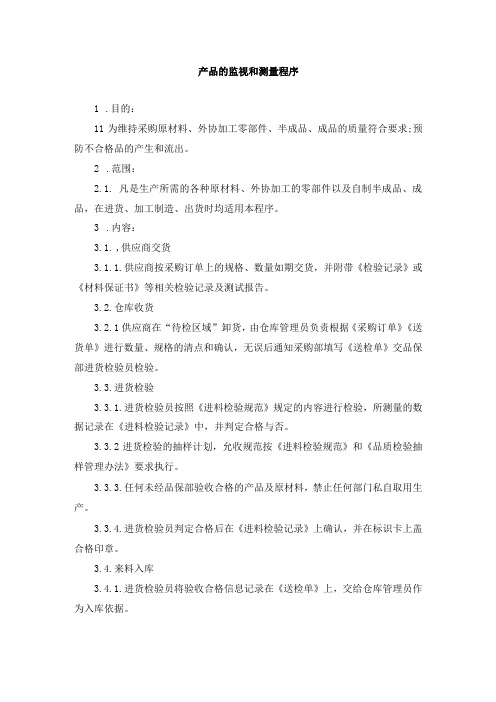
产品的监视和测量程序1.目的:11为维持采购原材料、外协加工零部件、半成品、成品的质量符合要求;预防不合格品的产生和流出。
2.范围:2.1.凡是生产所需的各种原材料、外协加工的零部件以及自制半成品、成品,在进货、加工制造、出货时均适用本程序。
3.内容:3.1.,供应商交货3.1.1.供应商按采购订单上的规格、数量如期交货,并附带《检验记录》或《材料保证书》等相关检验记录及测试报告。
3.2.仓库收货3.2.1供应商在“待检区域”卸货,由仓库管理员负责根据《采购订单》《送货单》进行数量、规格的清点和确认,无误后通知采购部填写《送检单》交品保部进货检验员检验。
3.3.进货检验3.3.1.进货检验员按照《进料检验规范》规定的内容进行检验,所测量的数据记录在《进料检验记录》中,并判定合格与否。
3.3.2进货检验的抽样计划,允收规范按《进料检验规范》和《品质检验抽样管理办法》要求执行。
3.3.3.任何未经品保部验收合格的产品及原材料,禁止任何部门私自取用生产。
3.3.4.进货检验员判定合格后在《进料检验记录》上确认,并在标识卡上盖合格印章。
3.4.来料入库3.4.1.进货检验员将验收合格信息记录在《送检单》上,交给仓库管理员作为入库依据。
3.4.2.仓库管理员根据《搬运、储存、包装、防护和交付控制程序》办理入库手续。
3.5.不合格品处理:3.5.1进货检验员按《进料检验规范》要求进行检测,判定批量不合格,通知供应商质量工程师(以下简称SQE)和采购部,由采购部通知供应商将不合格品领回,并按照《不合格品控制程序》处理。
3.5.2若生产急需,需挑选、返工使用的,则由采购部通知供应商或生产部进行挑选、返工使用。
由生产部挑选、返工时,生产部应做好工时的统计工作,由采购部执行对供应商相应的扣款事宜。
3.6.纠正措施:3.6.1进货检验员判定批量不合格时须按照《纠正与预防措施控制程序》填写《异常改善报告》通知SQE,由SQE要求供应商提出改善措施,并进行跟踪确认。
GJB9001C产品的监视和测量程序

1目的验证产品的特性要求已得到满足,确保对产品特性进行有效的监视和测量。
2适用范围本程序适用于进货检验、生产中半成品(工序)的检验及成品的检验。
3 职责3.1 研发部负责编制产品检验标准(企业标准)。
3.2 研发部负责编制原材料检验规范及过程检验规范。
3.3 品质部负责按照各类检验规范的要求实施原材料进货检验、半成品(工序)检验、成品的检验。
4 程序4.1 进货检验4.1.1采购物料到货后,采购部通知品质部检验员进行检验。
检验员依据“原材料检验规范”要求进行检验,并根据检验规范要求保留供方出具的产品合格证明材料,然后在物料存放区域或其包装上用标识牌或标识签标识检验状态,并填写“原材料入厂验收单”。
4.1.2采购部仓库管理员依据检验员在“原材料入厂验收单”上的检验结论,经检验员加贴合格标签的合格物料,由仓库仓管员办理入库手续。
4.1.3如采购物资出现批量性不合格,应由市场部发出“纠正和预防措施表”,交采购部反馈给供应商。
不合格品执行“不合格品控制程序”。
4.2 半成品(工序)检验4.2.1 根据工艺规程的要求,对于有首检要求的工序,生产出的首件产品应由生产部操作人员实施自检后,交品质部检验员进行首件专检,并填写相应实测数据,检验合格后方可正式生产。
4.2.2品质部检验员对质量控制点按照“工艺文件”的检验要求进行检查,在“随工流程单”中填写相应的检验记录栏目。
对工序完工的产品,由生产车间进行自检、互检,交检验员专检,检验员在“随工流程单”上签字,合格品转入下道工序。
对在工序中发现的质量问题,检验员应该及时通知生产车间有关人员。
4.3 成品检验4.3.1 包装前检验:生产车间将待包装的产品,通知品质部。
品质部检验员按照“产品检验标准”或企业标准要求进行检验,填写“产品出厂检验报告”,产品经品质部检验合格后,方可由包装人员进行包装。
顾客要求参加验收的产品,研发部提交一份“产品提交单”附“产品出厂检验报告”复印件,申请顾客验收,经顾客确认合格,方可包装。
IATF16949产品监视与测量管理程序

文件制修订记录1.目的;对产品特性进行监视和测量,以验证产品要求得以实现,满足顾客要求。
2.范围;适用于对生产所用原材料、零部件、半成品和成品进行监视和测量。
3.权责;3.1资材部仓库:负责对入库产品数量、规格、型号、相关资料的验收以及标识工作;3.2品质部:负责对来料、制程、成品的监视和测量工作;3.3供应商/生产部:负责对不合格品采取纠正以及预防措施;3.4厂长:负责对『紧急放行申请单』进行核准。
3定义:无5.工作程序;5.1品质部负责明确各检验目的、检验范围、检验方式、检验准备及检验项目等,编制检验标准和检验指导书。
5.2对产品执行监视和测量的设备在每次使用前,除要进行日常操作检查外,还要对进行例行检验的测量设备进行运行检查,品质部制定相关监视和测量设备的作业指导书,实施运行检查,并将检查结果填入相关“监视和测量设备点检表”中,如发现设备失准,应采取相应的措施。
必要时,对已检测过的产品重新进行检测。
5.3进料的监视和测量;5.3.1对A类生产购进的物资,由资材部仓管员核对物料的品名、规格、数量等无误、包装无损后,置于待检区,品质部安排人员进行检验,对B类物资由资材部仓管员核对无误后,可直接办理入库。
5.3.2检验员根据《控制计划》、产品检验标准、样品、图纸等执行检验,并填写『进料检验报告』;5.3.3仓管员根据合格的验证记录标识后办理入库手续;5.3.4检验不合格时,仓管员负责进行标识并对不合格品的隔离,并按《不合格品控制程序》进行处理。
5.3.5紧急放行;1)当生产急需来不及验证时,在可追溯的前提下,由品质部填写『紧急放行申请单』,经厂长核准后方可执行放行;2)仓管员根据批准的『紧急放行申请单』,按规定检验数量留取同批样品送检,其余由检验员在『领料单』上注明“紧急放行”字样后放行;生产车间也需在其产品的标识卡上也应注明“紧急放行”;3)在放行的同时,检验员应继续完成该批产品的检验;不合格时,品质部负责对该批紧急放行产品进行追踪处理。
产品监视和测量控制程序

产品监视和测量控制程序1.目的对产品(原料、辅料、与产品接触的材料、半成品、成品)进行监视和测量,确保产品满足规定的要求。
2.适用范围适用于公司产品实现过程中各阶段产品监视和测量的控制。
3.职责和权限3.1川酒研究院负责为产品检验提供相应的技术标准。
3.2各基地质量管理部门负责编制产品检验作业指导书,负责按要求做好各阶段的产品监视和测量工作,是产品监视和测量活动的归口管理部门。
3.3酒体设计单位负责酒处理、水处理及酒体设计用原辅材料的检验。
4.工作程序4.1检验计划的制订4.1.1根据公司产品质量形成的过程,由相关检验单位制订检验计划,明确规定检验项目、依据标准和规范、检查方式、方法和手段、检验地点、人员和频次、检验记录及其传递程序等内容。
酿酒原料、包装材料检验计划经公司主管质量的副总批准后执行,酒处理、水处理及酒体设计用原辅材料的检验计划经酒体设计单位的副总经理批准后执行。
4.1.2质量管理部门根据检验计划制订各项检验规程和检验记录。
规程和记录的编制执行公司《文件控制程序》和《记录控制程序》。
4.1.3质量管理部门根据检验计划设置检验点、配备检验人员和设施设备,宣贯检验标准和规程。
4.2进货监控所有原材料都必须经过进货检验(按采购质量标准进行检验),未经检验或检验不合格,一律不得投产使用。
4.2.1酿酒原辅料由检验人员在入库现场按“采购质量标准”检验,检验员做好现场记录并填写《检验结果通知单》。
4.2.2包装材料验收实行二级检验制,一是由包材检验员在入库现场按包装材料标准逐批检验,作好记录并填写检验结果通知单;二是生产工人在生产中对所用包装材料进行全数筛选,挑出不合格品。
4.2.3酒处理、水处理及酒体设计用原辅材料由酒体设计单位专兼职检验员按检验计划和“采购质量标准”执行,作好记录并填写《检验结果通知单》。
4.2.4酒处理、水处理及酒体设计用的原辅材料,使用部门用感观方法复查进货质量,如有异常,立即通知检验人员进行复检。
IATF16949产品监视和测量程序(含流程表格)
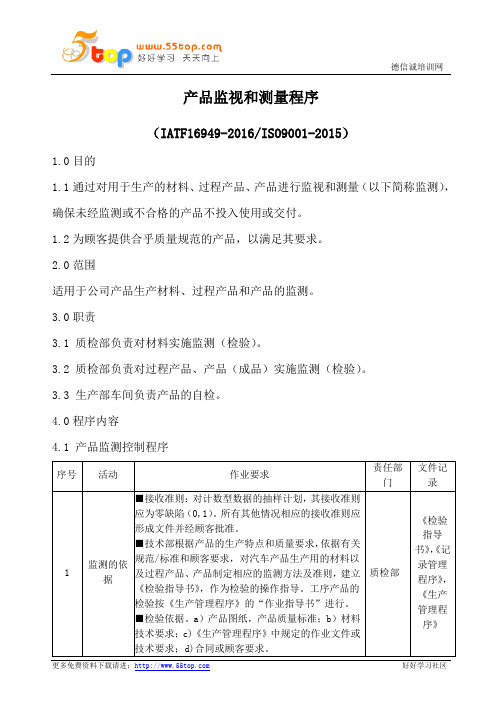
产品监视和测量程序(IATF16949-2016/ISO9001-2015)1.0目的1.1通过对用于生产的材料、过程产品、产品进行监视和测量(以下简称监测),确保未经监测或不合格的产品不投入使用或交付。
1.2为顾客提供合乎质量规范的产品,以满足其要求。
2.0范围适用于公司产品生产材料、过程产品和产品的监测。
3.0职责3.1 质检部负责对材料实施监测(检验)。
3.2 质检部负责对过程产品、产品(成品)实施监测(检验)。
3.3 生产部车间负责产品的自检。
4.0程序内容4.1 产品监测控制程序4.2 其他管理要求4.2.1 对检验中涉及试验时,执行《实验室管理程序》;当委托外部实验室进行试验时,应获得“试验报告单”。
4.2.2 只有在规定的产品监测完成并且符合要求后,产品才可转序或入库,否则不得将产品放行。
除非有相关负责人批准并且有可实现追溯的记录或标识。
4.2.3 过程产品和最终产品检验中发现不合格品时,经质检部组织评审后作返工、返修、让步放行、报废等处置。
具体执行《不合格品管理程序》。
4.2.4 产品审核。
由质检部组织按《内部审核管理程序》策划的安排,至少每半年一次对已入库待发运的产品进行审核。
4.2.5 外观检验。
a)对材料、半成品、成品进行有顾客要求的外观检验项目时,检验场所必须有足够的照明;b)外观检验所需标准样品(极限合格)均应作妥善保管和维护;c)对从事外观检查的质检员应经过适当培训,并由企管部组织进行资格验证,合格后方可上岗。
4.2.6 除非有顾客同意,否则在所有规定活动均已完成之前,不得放行和交付产品。
在有放行的场合下,应考虑:a)此类产品必须符合法律、法规的要求;b)此类放行并不意味着可以不满足顾客的要求。
4.2.7 材料、成品和过程产品监测的记录由质检部负责收集和保存。
5.0相关文件《不合格品管理程序》《采购管理程序》《生产管理程序》《供方管理程序》《记录管理程序》《内部审核管理程序》《监测设备管理程序》《实验室管理程序》《仓库管理程序》《检验指导书》《材料检验单》材料检验记录.d oc《材料验收单》材料验收日报表.xls《首件检验记录》首件产品检验记录表.d oc《自检记录表》自主检验记录表.xls《巡检记录表》I PQ C巡检记录.xl s《质量检验单》产品质量检验表(二).xl s《产品检验记录》产品过程检验记录表.xl s《全尺寸检验/功能测试记录表》铸件全尺寸功能检验报告书.d oc《出厂检验报告》产品出厂检验报告.d oc。
公司质量管理过程和产品的监视和测量控制程序

公司质量管理过程和产品的监视和测量控制程序1. 目的通过对产品实现的必需过程进行监视和测量,以确保满足顾客的要求,对产品特性进行监视和测量,以验证产品符合规定要求。
2.适用范围适用于本公司产品实现过程持续满足预定目标的能力和用于生产的产品进行监视和测量的控制。
3.职责综合部负责对质量管理体系各过程进行监控。
生产部负责产品特性的监控和测量。
4.工作程序4.1过程的监视和测量过程的监视和测量包含对质量管理体系过程活动的监视和测量及对产品实现过程的监视和测量。
4.1.1对质量管理体系过程活动的监视、测量,可采用调查、了解、分析的方法,每年进行一次。
4.1.2对产品实现各过程的监视、测量,根据本公司的实际情况,确定为“焊接、组装、调试”过程进行重点监视和测量。
质检部负责制定焊接、组装、调试的技术规范、测试指标及数据记录等。
4.1.3生产过程的测量和监视a) 生产部门负责使用控制图,对质量形成的关键过程进行测量,对图形数据分布进行趋势分析,明确过程质量和过程实际能力之间的关系,以确定需要采取纠正或预防措施的时机。
b) 当过程产品合格率接近或低于控制下限时,生产部门应及时发出《纠正预防措施实施单》,定出责任部门,对其从人、机、料、法、环等方面分析原因、制定和实施4.2 产品的监视与测量4.2.1综合部编制检验指导书,明确检验点、控制频率、抽样方案、控制项目、监测方法、使用的计量器具设备等。
4.2.2进货验证对购进的材料,仓库管理员核对送货单,确认财产品名、规格数量等无误后,置于待检区或挂上“待检品”牌予以标识和区分。
并填写《送检单》交有关部门检验,具体内容见《采购控制程序》。
4.2.3半成品的监视和测量4.2.3.1对于生产和组装线上的产品,按规定要求设置质量控制点,按规定间隔依检验规程对产品进行监视和测量。
进行检验,经检验合格,在产品上贴上工号标签,对关键过程由检验员进行检验,在产品上贴上检验员工号标签,方可转入下道工序,如不合格则执行《不合格品控制程序》。
检验和测量的控制程序
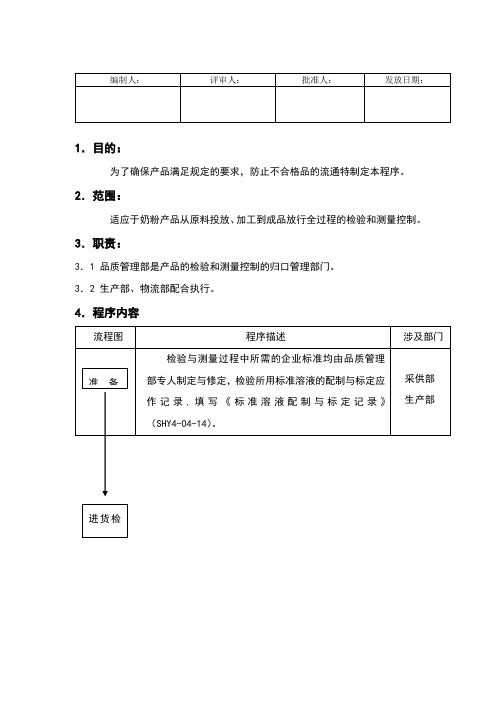
1.目的:
为了确保产品满足规定的要求,防止不合格品的流通特制定本程序。
2.范围:
适应于奶粉产品从原料投放、加工到成品放行全过程的检验和测量控制。
3.职责:
3.1 品质管理部是产品的检验和测量控制的归口管理部门。
3.2 生产部、物流部配合执行。
4.程序内容
5. 参考文件:
《质量手册》
《产品标识和可追溯性控制程序》 SHY(Q)2-10《不合格品的控制程序》 SHY(Q)2-18 《原材料、产品检验执行标准》 SHY3-04-07
6.引用表格:
《奶粉理化检验原始记录(一)、(二)》 SHY4-04-01《奶粉检验报告单》 SHY4-04-02《奶粉卫生检验原始记录》 SHY4-04-03《原材料初检报告单》 SHY4-04-04《部门取样单(原料)》 SHY4-04-12《生产过程控制巡检表》 SHY4-04-10《—班—日奶粉包装质量考核表》 SHY4-04-11《成品检验记录》 SHY4-04-22《成品检验报告单》 SHY4-04-23《部门取样单(成品)》 SHY4-04-16《标准溶液配制与标定记录》 SHY4-04-14《-库房巡检表》 SHY4-04-26。
- 1、下载文档前请自行甄别文档内容的完整性,平台不提供额外的编辑、内容补充、找答案等附加服务。
- 2、"仅部分预览"的文档,不可在线预览部分如存在完整性等问题,可反馈申请退款(可完整预览的文档不适用该条件!)。
- 3、如文档侵犯您的权益,请联系客服反馈,我们会尽快为您处理(人工客服工作时间:9:00-18:30)。
3.成品检验合格后,盖蓝色PASS印章并在【送检单】和【入库单】进行签名确认,通知生产部办理入库。
4.成品检验不合格时,贴红色箭头标或红色不合格标签填写【返工通知单】,通知生产部进行改善。针对返工的产品需重新送检确认合格再进行入库。
1.目的
对本公司收到的材料、半成品、成品通过实施规定的检验、试验来进行有效的控制,确保不合格物品流入下
工序、仓库及客户。
2.范围
适用于本公司原材料、包装材料、外发加工产品及半成品,成品检验的控制。
3.定义
全检:将送检批中的物料或产品100%检验。
4.权责
4.1 品保部:在本文中指的是全面质量管理中心和事业部品保部。
2.针对物料异常同类问题发生超过3次以上,IQC填写【8D报告】,要求供应商进行分析改善。
3.采购部协助QE,必须在3-5个工作日内积极的跟进供应商品质异常处理的结果。
【8D报告】
物流
中心
办理
入库
1.仓库依IQC【进料检验报告】和【实验测试报告】结果及时办理入库。
2.物料出入库时,仓管员均须凭单据及实际收发数量于【物料(成品)进出存卡】上登销帐。
【IPQC巡回检验记录表】
【质量异常报告】
事业部
品保部
内部
检验
品保部依《制程检验规范》对半成品进行全检,不合格品贴不合格标签,放置于不合格区,及时通知车间相关人员进行改善。
不合格标签
事业部
品保部
成品
检验
1.生产组装完成产品,由FQC依CP、FMEA、QCFC、SOP、《制程检验规范》等要求进行检验,填写【FQC检验日报表】。
2.检验合格时,IQC贴绿色合格标签,填写【进料检验报告】,报告经部门主管审核后归档保存。
3.检验不合格时:IQC贴红色不合格标签,填写【进料检验报告】经PMC、采购部、工程部和生产部及其他相关部门共同进行MRB处理。
4.检验完成后,仓管员将货品搬离待检区,按物料所属仓位归位。在检验不合格的,在ERP系统中生成【退货单】或【委外退货单】经采购部确认后退回供应商或加工商。
【进货单】
【委外进货单】
IQC
物料
信息
IQC准备相关检验资料文件,如:样品、图纸、进料检验规范、抽样计划C=0(零缺点)、样品承认书、检测工具等。
《来料检验规范》图纸等
IQC
来料
检验
1.IQC根据《来料检验规范》、抽样计划对来料外观、尺寸、材质、包装、性能、可靠性等项目进行抽样检验和测试,作出品质判定。
【出货检验报告】
【返工通知单】
OQA
成品检验
1.若要出货,仓库部将【销货单】【出货通知单】通知OQA进行出货核对。
2.OQA对包装、外箱等进行核对,合格在【销货单】盖QAPASS章,不合格的,OQA通知相关部门到出货现场进行确认和改善。
【销货单】
【出货通知单】
品保部
全尺寸及功能
针对每一种车灯产品,按控制定期进行全尺寸检验和功能验证,其结果应可供客户评审。
检验结果
相关
部门
不合格品
参照《不合格管理程序》执行。
不合格品处理结果
品保部
记录
参照《记录管理程序》
记录存档
6.参考文件
6.1《进料检验规范》 QSI-016
6.2《制程检验规范》 QSI-004
6.3《成品检验规范》QSI-002
6.4《标识与追溯管理程序》QEP-010
6.5《不合格管理程序》 QEP-011
【物料(成品)进出存卡】
5.2制程检验管理过程
事业部品保部
成品及成品
信息
1.生产条件稳定后,产线制作首件,交品保部进行首件确认填写【首件确认单】。
2.IPQC依照成品检验规范、图纸、BOM、客户订单、ENW、ECN、NPI等对首件的外观、功能、内部结构进行首件确认并填写在【首件确认单】上。
3.对于首件判定不合格,生产部需重新调试再做首件确认,IPQC对合格的首件贴合格标签,将首件放置生产首件放置区。
5.作业内容
5.1 进料检验管理程序
流程图
负责
部门
输入
过程重点提示
输出
文件/表单
物流
中心
待点收物料及送货单
1.收料仓管收到供货商或加工商开立送货单,在ERP系统中核对料号、数量、订单号等与实物无误后,签收送货单并加盖收货专用章。
2.帐务文员凭送货单录入ERP系统中,自动生成【进货单】或【委外进货单】,送IQC检验。
【首件确认单】
事业部
品保部
在制品的检验
1.各工站之作业员进行自检,合格后流入下一个工站。
2.IPQC依CP、FMEA、QCFC、SOP、《制程检验规范》等要求进行巡检,填写【IPQC巡回检验记录表】。
3.IPQC检验不合格贴:红色不合格标签,放置不合格区,及时通知各车间相关人员进行改善。
4.依据《制程检验规范》的要求针对重大异常,IPQC填写【质量异常报告】交PE\QE进行分析改善。
4.2全面质量管理中心(IQC,OQA)
4.2.1负责制定原材料、成品的检验规范。
4.2.2根据检验标准等对进货物料、入库成品和产品出货前的抽查检验和测试。
4.3事业部品保部(IPQC,FQC)
4.3.1负责制定制程半成品的检验规范。
4.3.2负责制程过程中的首检、巡检、定点检验。
4.4事业部生产部:负责生产过程中半成品及成品的自检。
2.IQC无法做实验(盐雾、摇摆),则填写【实验测试申请表】同原料一起提交实验室进行相关实验。实验室依据相关“实验规范”、“实验设备操作指引”对来料进行可靠性实验/试验,并出具【实验测试报告】。
【进料检验报告】
【实验测试报告】
【实验测试申请表】
IQC
物流
中心
采购部
来料
检验
报告
1.针对IQC判定不合格的物料处理,退货及报废时加贴玫瑰红退货标签,在【来料检验报告】、【进货单】或【委外进货单】上注明处理结果,通知仓库处理。
2.FQC检验不合格时贴:红色不格标签,放置不合格区,及时通知各车间相关人员进行改善。
3.FQC发现重大异常时,填写【质量异常报告】交PE\QE进行分析改善。
【FQC检验日报表】
【质量异常报告】
5.3 成品检验管理过程
OQA
成品
检验
1.生产完成后,生产部填写【送检单】和【入库单】通知OQA进行入库检验。
6.6《记录管理程序》QEP-002
7.使用表单(无)
5.参照《不合格管理程序》和《标识与追溯管理程序》。
【进料检验报告】
【退货单】
【委外退货单】
IQC
实验室
来料
检验
1.检验过程中针对原料类别的不同要求,IQC依《进料检验标准》对来料进行可靠性测试,如(高温、酒精、3M、盐雾、拉拔力、粘性、可焊性)。实验合格在【进料检验报告】上填写相关实验项目,且判定合格。