压铸模类外文翻译——压塑和压铸工艺
压铸模具与成型专业名词(中英文版)
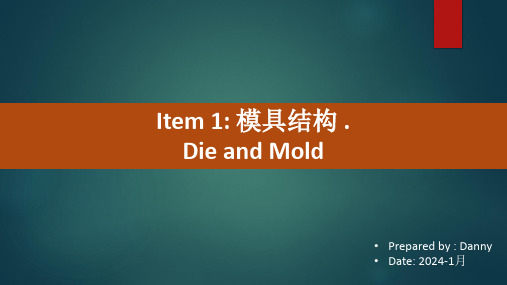
常用软件推荐(Common software recommendation)
Flow 3D / Pro cast Software(US)-目前国内小压铸厂比较多用,因为是免费软件。 Small die casting plant is more commonly used, because it is a free software. Magma-software(Germany)-汽配件大型压铸厂信赖的软件。 This software trusted by large automobile parts company for die casting. Any-casting (Korea)-国内小型压铸厂用的多些。 It was made in Korea, it was more used in the small die casting plant in China.
氮 碳 共 渗 是 在 含 有 活 性 碳 、 氮 原 子 的 介 质 中 同 时 渗 入 氮 和 碳 , 并 以 渗 氮 为 主 的 低 温 氮 碳 共 渗 工 艺 ( 530℃580℃)。氮碳共渗的渗层脆性小,共渗时间比渗氮时间大为缩短。压铸模经氮碳共渗后,可显著提高其热疲劳性 能。
电镀涂层- Electroplating Coating
Item 1: 模具结构 . Die and Mold
• Prepared by : Danny • Date: 2024-1月
压铸模具零件结构-Mold components.
✓ 前模固定板 Cavity Fixing Plate/ A Plate
✓ 料套 Sprue Bush
模具安装在压铸机上。 Tooling fixed in the die casting machine.
压铸模具专业英语
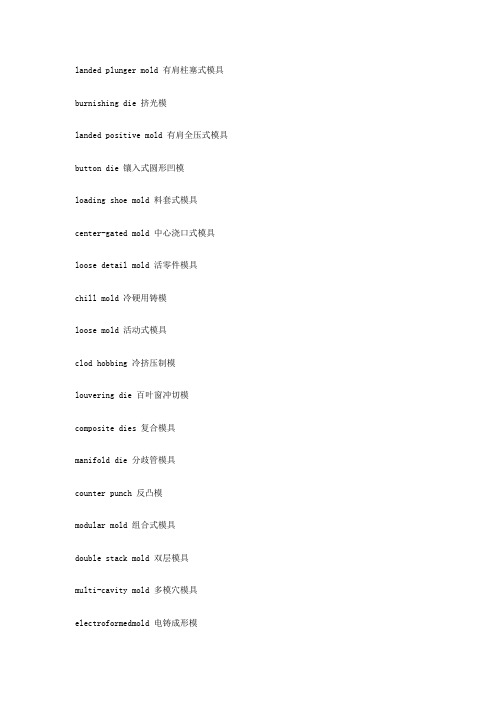
landed plunger mold 有肩柱塞式模具burnishing die 挤光模landed positive mold 有肩全压式模具button die 镶入式圆形凹模loading shoe mold 料套式模具center-gated mold 中心浇口式模具loose detail mold 活零件模具chill mold 冷硬用铸模loose mold 活动式模具clod hobbing 冷挤压制模louvering die 百叶窗冲切模composite dies 复合模具manifold die 分歧管模具counter punch 反凸模modular mold 组合式模具double stack mold 双层模具multi-cavity mold 多模穴模具electroformedmold 电铸成形模multi-gate mold 复式浇口模具expander die 扩径模offswt bending die 双折冷弯模具extrusion die 挤出模palletizing die 叠层模family mold 反套制品模具plaster mold 石膏模blank through dies 漏件式落料模porous mold 通气性模具duplicated cavity plate 复板模positive mold 全压式模具fantail die 扇尾形模具pressure die 压紧模fishtail die 鱼尾形模具profile die 轮廓模flash mold 溢料式模具progressive die 顺序模gypsum mold 石膏铸模protable mold 手提式模具hot-runner mold 热流道模具prototype mold 雏形试验模具ingot mold 钢锭模punching die 落料模lancing die 切口模raising(embossing) 压花起伏成形re-entrant mold 倒角式模具sectional die 拼合模runless injection mold 无流道冷料模具sectional die 对合模具segment mold 组合模semi-positive mold 半全压式模具shaper 定型模套single cavity mold 单腔模具solid forging die 整体锻模split forging die 拼合锻模split mold 双并式模具sprueless mold 无注道残料模具squeezing die 挤压模stretch form die 拉伸成形模sweeping mold 平刮铸模swing die 振动模具three plates mold 三片式模具trimming die 切边模unit mold 单元式模具universal mold 通用模具unscrewing mold 退扣式模具yoke type die 轭型模。
模具名词三语对照表
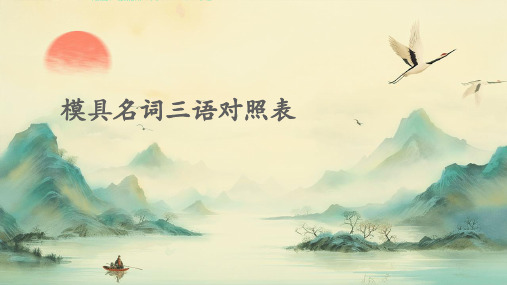
排气系统设计
排气系统
排气系统是指模具中用于排除型腔内 气体的通道和机构。
排气系统的作用
排气系统的作用是排除型腔内的气体, 避免产品出现气孔、鼓包等问题,提 高产品质量。
排气系统的设计原则
排气系统的设计应遵循结构简单、易 于维护、不影响产品外观等原则。
排气系统的类型
根据产品结构和模具结构,排气系统 可分为自然排气和强制排气两种类型。
分模面设计
01
02
03
04
分模面
模具设计中的分模面是指将模 具分成动模和定模两个部分的
面。
分模面设计原则
分模面设计应遵循便于模具加 工、降低模具复杂度、保证产
品精度等原则。
分模面的类型
根据产品结构和模具结构,分 模面可分为水平分模面、垂直 分模面、倾斜分模面等类型。
分模面的选择
选择合适的分模面可以简化模 具结构,提高模具强度和寿命 ,同时保证产品顺利脱模。
模具名词三语对照表
• 模具类型 • 模具部件 • 模具材料 • 模具设计
01
模具类型
注塑模具
注塑模具:注射成型模,德文:Spritzgussform
英文:Injection Mould
注塑模具主要用于热塑性塑料制品的成型,也可用于热固性塑料制品的 成型,而结构上又具备可调镶件、斜导柱、顶针、司筒、分流器、定位 环、冷却水道等结构。
冲压模具主要用于金属薄板零件的成型,如汽 车覆盖件、家电零件等。冲压模具的结构包括 凹模、凸模、压边圈、定位销等部分。
挤出模具
挤出模具:挤出成型模,德文:Extrusionform
英文:Extrusion Mould 挤出模具主要用于塑料制品的连续成型,如塑料管材、塑料薄膜等。挤出 模具的结构包括机头、口模、芯棒、加热系统等部分。
压铸工艺英文描述
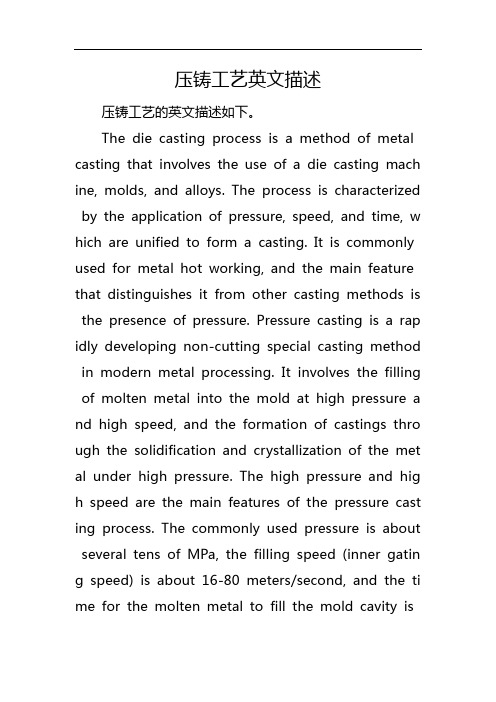
压铸工艺英文描述压铸工艺的英文描述如下。
The die casting process is a method of metal casting that involves the use of a die casting mach ine, molds, and alloys. The process is characterized by the application of pressure, speed, and time, w hich are unified to form a casting. It is commonly used for metal hot working, and the main feature that distinguishes it from other casting methods is the presence of pressure. Pressure casting is a rap idly developing non-cutting special casting method in modern metal processing. It involves the filling of molten metal into the mold at high pressure a nd high speed, and the formation of castings thro ugh the solidification and crystallization of the met al under high pressure. The high pressure and hig h speed are the main features of the pressure cast ing process. The commonly used pressure is about several tens of MPa, the filling speed (inner gatin g speed) is about 16-80 meters/second, and the ti me for the molten metal to fill the mold cavity isvery short, about 0.01-0.2 seconds.。
压铸模具设计外文文献译文

半固态压铸件ADC12铝合金的可行性1。
采矿和材料工程专业,工程学院,大学Songkla王子2。
工业工程专业,工程学院, 科技大学Rajamangala Srivijaya3。
机械工程学系,工程学院,大学Songkla王子2010年5月13日至2010年6月25日文摘:研究半固态压铸件ADC12铝合金的可行性。
已经确定活塞速度受壁厚和固态粒度浆缺陷的影响。
研究表明缺陷是由缩松引起的。
在实验中,采用的是半固态浆料制备半固态gas-induced(GISS)的技术。
然后,液态金属被转移到压铸模具之中,模具和套筒温度分别保持在180 C和250 C 结果表明,GISS制作的压铸模具松孔较小没有气泡和均匀的微观结构。
实验结果表明可以推论,GISS是可行的,适用于ADC12铝压铸过程。
另外GISS可以改进性能比如减少孔隙度和增加组织均匀性。
关键词:ADC12铝合金;半固态压铸;气体引起的半固态(GISS);流变铸造第1章在电子、航天、和建筑领域。
多年来一直使用铝制部件这些部件通常使用高压压铸过程大量生产压铸过程的优点在于实现了如生产效率高和生产小且复杂的工件压铸过程包括将铝液在高压下注入到一个模具型腔中。
金属液灌到模具型腔中,导致金属反应和铸造的过程中产生气孔。
因此,最终的结构部分充满气泡和氧化物夹杂。
此外,压铸件通常不能进行加工,由于这些缺陷的产生要进行阳极氧化、焊接、热处理,[1 4]。
来提高的压铸过程质量和性能因此在这里介绍了半固态金属技术。
大量的半固态压铸的研究报道,使用半固态压铸有助于改善产品性能和提高质量的压铸零件[5 7]。
半固态金属加工过程使用流变路线可以提供更高粘度的液体与更高的粘度, 能够获得更少的湍流流动,这有助于减少空气孔隙度和氧化物夹杂在模具填充[5 7]。
此外,流变过程可以很容易被应用于传统的压铸模具的生产过程,只需要少量修改便可使效率提高[8]。
许多研究显示成功的半固态压铸与流变过程[7 12]。
【2017年整理】压铸模具术语
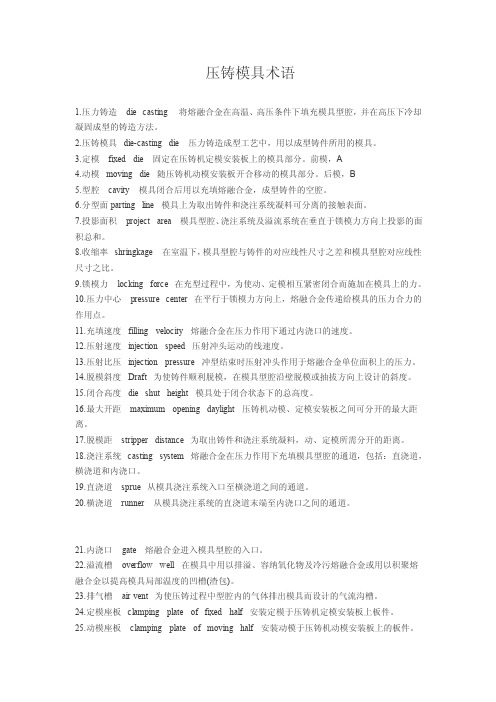
压铸模具术语1.压力铸造die casting 将熔融合金在高温、高压条件下填充模具型腔,并在高压下冷却凝固成型的铸造方法。
2.压铸模具die-casting die 压力铸造成型工艺中,用以成型铸件所用的模具。
3.定模fixed die 固定在压铸机定模安装板上的模具部分。
前模,A4.动模moving die 随压铸机动模安装板开合移动的模具部分。
后模,B5.型腔cavity 模具闭合后用以充填熔融合金,成型铸件的空腔。
6.分型面parting line 模具上为取出铸件和浇注系统凝料可分离的接触表面。
7.投影面积project area 模具型腔、浇注系统及溢流系统在垂直于锁模力方向上投影的面积总和。
8.收缩率shringkage 在室温下,模具型腔与铸件的对应线性尺寸之差和模具型腔对应线性尺寸之比。
9.锁模力locking force 在充型过程中,为使动、定模相互紧密闭合而施加在模具上的力。
10.压力中心pressure center 在平行于锁模力方向上,熔融合金传递给模具的压力合力的作用点。
11.充填速度filling velocity 熔融合金在压力作用下通过内浇口的速度。
12.压射速度injection speed 压射冲头运动的线速度。
13.压射比压injection pressure 冲型结束时压射冲头作用于熔融合金单位面积上的压力。
14.脱模斜度Draft 为使铸件顺利脱模,在模具型腔沿壁脱模或抽拔方向上设计的斜度。
15.闭合高度die shut height 模具处于闭合状态下的总高度。
16.最大开距maximum opening daylight 压铸机动模、定模安装板之间可分开的最大距离。
17.脱模距stripper distance 为取出铸件和浇注系统凝料,动、定模所需分开的距离。
18.浇注系统casting system 熔融合金在压力作用下充填模具型腔的通道,包括:直浇道,横浇道和内浇口。
压铸的工艺流程英文版
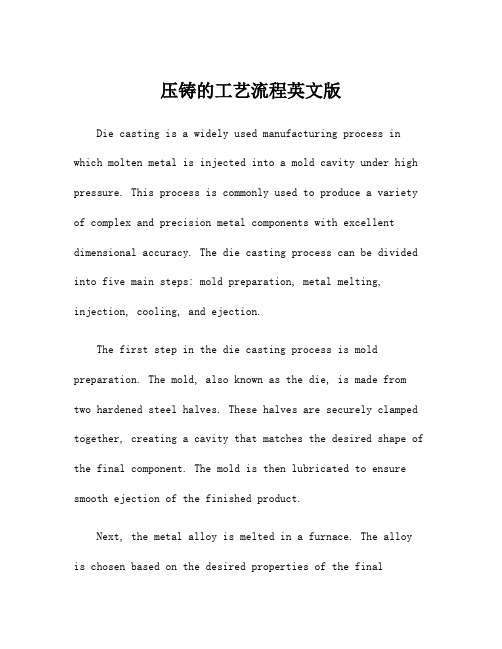
压铸的工艺流程英文版Die casting is a widely used manufacturing process in which molten metal is injected into a mold cavity under high pressure. This process is commonly used to produce a variety of complex and precision metal components with excellent dimensional accuracy. The die casting process can be divided into five main steps: mold preparation, metal melting, injection, cooling, and ejection.The first step in the die casting process is mold preparation. The mold, also known as the die, is made from two hardened steel halves. These halves are securely clamped together, creating a cavity that matches the desired shape of the final component. The mold is then lubricated to ensure smooth ejection of the finished product.Next, the metal alloy is melted in a furnace. The alloy is chosen based on the desired properties of the finalcomponent, such as strength, durability, and heat resistance. Once the metal reaches the desired temperature, it is transferred to a holding furnace, where it is kept at a consistent temperature to ensure proper flow and fill of the mold cavity.The third step is the injection phase. The mold halves are closed, and the molten metal is injected into the mold cavity at high pressure using a piston or plunger. The pressure forces the metal to fill all the intricacies of the mold, ensuring the replication of complex details. The injection process is carefully controlled to prevent any air or gas entrapment.After the mold cavity is completely filled, the fourth step begins, which is the cooling phase. The metal starts to solidify as it comes into contact with the cool surfaces of the mold. Cooling channels within the mold help to extract heat from the metal and hasten solidification. This stagerequires careful timing to ensure proper solidification of the component.Once the metal is completely solidified, the final stepis ejection. The mold halves are opened, and the finished component, also known as the casting, is ejected from the mold cavity. Any excess material, known as the flash, is trimmed off. The casting goes through further processing, such as heat treatment, surface finishing, and quality inspections, to meet the desired specifications.In conclusion, die casting is a multi-step process that involves mold preparation, metal melting, injection, cooling, and ejection. It enables the production of complex and precise metal components with superior dimensional accuracy. This versatile manufacturing process finds extensive applications in industries such as automotive, aerospace, and electronics.。
压铸的工艺流程英文手册

压铸的工艺流程英文手册Die casting is a metal casting process that involves forcing molten metal into a mold cavity under high pressure. 压铸是一种金属铸造工艺,其过程涉及将熔化金属在高压下注入模腔。
This process is commonly used for manufacturing complex parts with high accuracy and consistency. 这种过程通常用于制造具有高准确性和一致性的复杂零件。
Die casting is known for its ability to produce parts with excellent surface finish and dimensional accuracy. 压铸以生产具有出色表面光洁度和尺寸精度的零件而闻名。
The die casting process begins with the preparation of the mold, which is usually made of steel. 压铸过程始于模具的准备,通常是由钢制成。
The mold is then closed and molten metal is injected into the cavity at high pressure. 然后封闭模具,将熔化金属以高压注入腔体内。
The metal solidifies within the mold cavity and the part is ejected once it has cooled. 金属在模腔内固化,一旦冷却便可以取出零件。
This process can be repeated hundreds or thousands of times to produce large quantities of parts. 这个过程可以被重复数百次甚至数千次,以生产大量零件。
- 1、下载文档前请自行甄别文档内容的完整性,平台不提供额外的编辑、内容补充、找答案等附加服务。
- 2、"仅部分预览"的文档,不可在线预览部分如存在完整性等问题,可反馈申请退款(可完整预览的文档不适用该条件!)。
- 3、如文档侵犯您的权益,请联系客服反馈,我们会尽快为您处理(人工客服工作时间:9:00-18:30)。
压塑和压铸工艺近年,压塑工艺应用于热固性掺混料,如脲醛塑料、酚醛树脂、环氧树脂、蜜胺树脂和橡胶中。
尽管有一些材料可注射成型,但采用压塑工艺仍非常普遍。
压铸用材料较压塑用材料要求可塑性更软。
许多热固性材料具有高抗冲级(1.0ft一lb)和良好缺口冲击强度的保持性,只有在极限压力下才会流动。
压塑热固性材料的压塑成型的明显优点是系统简单。
将材料置入一加热型腔,保压至所要求团化时间。
因工艺过程简单,费用少。
添加剂和增强剂无规则,并能得到较好强度。
由于无浇口和流道,不浪费材料,模具几乎也不用维修。
零件的统一性好,无铸口和流痕,减少了修饰成本。
根据制品结构和所用的塑料应用特点,可采用全压式模具、半压式模具和闭模(可参见有关压塑模具方面的文章)。
设备:简单也是压塑设备的主要特点。
两半压板结合在一起,加温,加压,将材料制成预定形状。
多数压塑过程采用液压操作;也有采用气动操作的。
上下两压板在压力之下在4个角柱上上下移动。
根据压塑设备的大小,压力一般为20—1000吨。
压板的大小一般为8英寸2到5英尺2.在加料和固化以后的脱模方面存在不同自动化程度,常用最现代的液压机进行。
以前的简单系统有温度控制、压力控制、停压控制和时间控制。
现代设备采用更高级的微处理机控制。
对于较薄的制品,在板中可用加热筒或带式加热器。
对较深的制件,需要用筒形电加热器、蒸汽加热或热油系统加热。
有数种用于压塑中的加热体系:用蒸汽加热模温均匀,但加热温度限在350°F以下;套筒加热或其它加热(加热盘管、加热带等)比较干净,易于保养,用得比较普及;热油加热,由于加热介质循环稳定,所以加热均匀。
现在又有许多新加热方法,热水加热,类似于热油加热,加热介质一水一气体燃烧连续循环,可提供更高的压塑温度。
增强改性高分子材料工业发展迅速,要求压塑工业有新改进。
模塑增强塑料用两个模具:阳模(模塞)和阴模(模腔)。
当模具充满增强材料时,对模的两半热模具闭合,然后加热、加压固化得到产品。
相配合的模具复杂性变化很大,可用铝、塑料或钢制做。
轻质材料制做起来比较便宜,一般用于短期生产如“冷模塑”。
冷模塑用室温固化树脂,但仍使用模具和压塑液压机。
长期生产用硬化钢模具比较合算,对截坯口可提供较好的剪切性能和优良的光洁度。
这些压塑钢模采用机械上适配的截坯口,通常面对合模区。
用这种对模的金属模具,其制品表面均匀,光洁度好。
闭模工艺用于压塑成型、压铸成型、注射成型及一些可冲压的增强复合材料。
一些热塑材塑料可压塑模塑,但一般还是用预掺混的热固性树脂如BMC(预制整体模塑料)、SMC(片料成型模塑料)、TMC(厚模塑料)、毡片成型等。
毡片成型有时叫湿成型复合材料,在液压机的作用下将增强材料和树脂结合在一起。
经常在模中放置毡片,将树脂倾倒在加强材料上。
在加压过程中树脂充满模腔时加强材料固定不动。
若制件有严重的异形或斜度,有必要进行预成型。
多数毡片和预成型制州在投影面积上需要加150—200磅/英寸2的模压力。
预掺混料,如SMC,预浸树脂,填料、催化剂和增强料切割成一定大小队片状,再加入热的模具中(一般300—400°F),在1000~2000磅/英寸2压力下模塑。
用于SMC的较新的压塑设备的总循环周期可少于一分钟(从头到尾)。
已经发展了用特殊的液压装置推回压塑机中料筒,自动控制压板的水平度。
增强塑料,如SMC,用金属对模压塑光洁度好,这对制件的表面很重要。
在加工时有时出现纤维状的收缩。
用内模涂层的方法可改进表面光洁度。
BMC的压塑过程是最老的预掺混后的模塑过程之一。
填料(木屑、矿物料、纤维素等)的掺混混合是在叶片形的混合器中进行的。
将一批料装入300~400°F的模具中.在500磅/英寸2压力下模塑。
因用料廉价,所以原料成本低。
不过由于在模塑过程中纤维的定向性降低了机械强度。
高速压塑,即增强热塑性塑料片材的冲压,用途广泛。
玻璃毡片和聚丙烯相配合用于可冲压的塑料,其循环周期低于40秒。
生坯送至对流炉中加热。
加热以后,毛坯放入压塑模具中,这一过程用新的压塑机速度可达1400英寸/分钟。
以75英寸/分钟(比SMC的压塑过程快约3倍)加压进料。
根据市场的要求,有些新的可冲压塑料,表面光洁度好,并且具有可涂布性。
模塑压力一般1吨/英寸2。
传统的压塑工艺近几年一直呈增长的趋势。
在空间技术和国防方面的应用正在使这种工艺向其难点冲击。
在SMC、BMC、TMC、热塑性片材的冲压、增强材料的掺混和压塑机械方面的发展迅速增长,以适应工业的新要求。
一些先进的掺混料的压塑主要是在空间技术和国防应用方面发展迅速。
工具和模具的新概念及高温(达1200°F)模塑机,使石墨一碳纤维复合材料得以发展,代替了现有的金属铸件。
高温硅树脂正用作高压介质。
复合材料做的片层用于压塑模中。
现在,材料和生产成本已使该工艺更加适于空间技术市场,这类硅树脂也很快转向汽车领域。
压铸在压铸工艺中,热固性树脂料加入一单独的料腔,常叫料槽,然后强制送入一个或多个闭模中进行聚合(固化)。
料道,也叫注道和流道,使物料从料槽流向模腔,进入模腔之前经过限流器或浇口。
很多模腔具有单一料槽。
料腔中的空气被进来的物料所置换,并通过一特别放置的排气口排出。
当物料置入料槽中时,在一紧凑的测量装置中测料量,然后预热到接近聚合温度。
一次只加入足够一次的注塑量。
将预热的原料送出料槽的力再将其送往一注料器,该注料器紧接装在料槽上,以防止从活塞和料槽边之间的缝隙中漏料。
通常将密封套卡进注料器以进一步防漏。
料槽、注料器、浇口、流道和模腔的表面维持可使原料迅速固化的一定温度,根据物料性质、模具的设计和制件的几何形状该温度为280~380°F。
在压铸物达到固化期的终点时,将该次完整的压铸物进行脱模,包括脱除浇口、流道、注道和料槽中形成固化料垫(叫做残料)。
在压铸中,物料的预热很重要。
冷料流动缓慢,先进入模腔的料尚未到其终点,即可能聚合。
若发生上述情况,产品质量低劣,不仅是外观,也体现于机械性能。
有些例外,如一次注射量很少,或一些低粘度的物料。
可用加热灯或炉子加热,但有效而常用的方法是用专为塑料模塑制做的介电加热器。
Plastic and pressure die casting processIn recent years, the pressure technique used in thermosetting plastic material mixing ,such as urea-formaldehyde plastics, phenolic resin, epoxy rsin, melamine resin and rubber. In spite of some of the material can be injection moiding, but the use of plastic pressure process is still very common. More pressure die casting material used plastic materials require more malleable soft. Many thermosetting materials with high impact level (1.0ft-1b) and good impact strength of maintaining the gap, only under ertreme pressure will flow.Thermosetting plastic molding material pressure of the obvious advantages of the system is simple. Materials will be placed in a heating cavity, the pressure required by the Mission to time. As a result of the process simple, cost less. Enhancer and additive-free rules, and be able to get a better strength. As the gate and no runner ,not a waste of materials, die almost no maintenance. Parts of unity, and I cast no trace flow and reduce the cost of the modification. According to the structure and products used in the application of the characteristics of can be full-pressure die ,and die-pressure semi-closed mode (can be found in the plastic, plastic mold pressure related articles).Equipment: The pressure is a simple plastic deices the main features . platen combination of the two and a half , heating, pressure, the shape of the target material. Most of the process of plastic used hydraulic pressure to operate; also used pneumatic operation .Tow board up and down under pressure in the 4 corner posts on moving up and down. According to the plastic device the size of the pressure, the pressure is generally 20-1000 tons. The general board for the 8-inch size 2-5 feet 2.In addition, and after curing the release of different aspects of the degree of automation, the most commonly used modern hydraulic machine. Theprevious system , there is a simple temperature control, pressure control, pressure control and stop-time control. The use of modern equipment, advanced microprocessor control. For thinner products, in the board can be used in heating tube or belt heater. To the deeper parts, the need to use tube-shaped electric heater , heating steam or hot oil heating system. There are several types of plastic used in pressure in the heating system: uniform temperature steam heating mode, but the heating temperature is limited to below 350F;sleeve heating or other heating (heating coil, heating,ect.) relatively clean and easy maintenance, A more universal; thermal heating oil, heating due to the stability of the media cycle, the heat evenly. Now there are many new methods of heating ,hot water heating ,similar to the hot oil heating , water heating a medium for a gas combustion cycle , provides a greater degree of pressure temperature plastic.Polymer modified to enhance rapid industrial development requires a new pressure to improve the plastic industry . Enhanced by two molded plastic mold: mold-yang (side mode) and the negative mold (cavity). When the mold is full of reinforcements, the mode of the hot mold closed two and a half, and then heated, pressurized product to be cured. Along the lines of big changes in the complexity of the mold can be used aluminum, plastic or steel do.Light-weight materials making them less expensive, generally used for the production of short-term such as “cold-molding”.Coll at room temperature with molded resin, but the use of plastic mold and hydraulic pressure. The production of long-term use of hardened steel molds relatively cost-effective, the cut-off billet I can provide better performance and excellent cut finish. These steel pressure module on the use of machinery on the cut-off billet adapter I usually die together in the face area. This mode f metal molds, the products of its uniform surface, a good finish. Closed-mode technology used to pressure plastic molding,die-casting molding, injection and stamping some of the reinforced composites.Some of the thermoplastic plastic materials can be molded plasticpressure, but in general or with pre-mixing of thermosetting resins such as BMC (prefabricated molding as a whole),SMC(film forming material molding),TMC(thick molding),film forming, such as carpet.Carpet wet film forming sometimes called composite molding, in the hydraulic press will strengthen the role of materials and combined with resin. Often placed in the mold in carpet film will be dumped in to strengthen the resin material. Pressure in the process of cavity filled with resin to strengthen the material when fixed.If there are serious parts of the alien or gradient, it is necessary to carry out pre-forming. Most of the film and felt pre-forming system in the projected area of the state’s need to 150-200 pounds/2 inch of mold pressure. Pre-mixing materials, such as SMC, prepreg resin, filler, and the catalyst size enhance the material cut into a certain team sheet, and then adding the hot mold (in general 300-400 F), 1000-2000 1b/2 inch pressure Under the molding.SMC for the relatively new plastic devices the pressure of the total cycle may be less than one minute (from start to finish). Has developed a special hydraulic device back in the bowl pressure machine, automatic control of the board level degrees.Reinforced plastics, such as SMC, with a metal finish on molded plastic, tjis is very important parts of the surface. Sometimes occur in the processing of fibrous contraction.Model with coating method could improve the surface finish. BMC pressure of the process of plastic is the oldest pre-mixing after one of the molding process. Filling materials (wood, mineral materials, such as celluiose) are mixed in mixing the leaves in the shap of the mixer. Will feed into a group of 300~400 F in the mold. In the 500-pound/2 inches under the pressure of molding. As a result of the use of materials for low-cost, the cost of raw materials. However, as in the molding process, the orientation of fiber reduces the mechanical strength.Plastic high-speed pressure, that is, enhanced thermoplastic stampingthe sheet, a wide range of uses. Felt piece of glass and polypropylene can be used to match the plastic stamping, the cycle less than 40 seconds. Green sent to the convection heating furnace. Heating, rough pressure into plastic molds, in the process with new pressure machine machine speed up to 1400 inches/minute. To 75 inches/minute (SMC than the pressure of plastic process about 3 times as fast) feed pressure. According to the requirements of the market, some of the new stamping plastics, surface finish, and can be coated with nature. I metric ton of pressure on the general molding/2 inch. Traditional plastic pressure technology in recent years has been on the rise. In the space technology for national defense and the application of this technology is difficult to shock.In the SMC, BMC, TMC, the thermoplastic sheet stamping, reinforcement of the Blending plastic mechanical pressure and the development of the rapid growth of industry in order to meet the new requirements.A number of advanced materials mixing plastic pressure mainly in space technology and applications in the rapid development of national defense. Tools and dies and the new concept of high-temperature (up to 1200 F) molding machine to make a graphite carbon fiber composite materials can be developed to replace the existing metal castings.High temperature silicone is used as a high-pressure media. The composite sheet for the pressure in the mold. Now ,materials and production costs have made the process more suitable for space technology market, this type of silicone is also soon to the area of automobile.In the die-casting process, thermosetting resin material is expected to join a separate chamber, often called trough, and then forced into one or more closed modules for polymerization(curing).Liu, also known as Notes and the road runner, so that the flow of materials from the through cavity into the mold cavity before or after limiting gate. Many cavity with a single through. The air chamber is expected to be the replacement materials come in through a special place of the exhaust emissions.When the materials placed in the trough, in a compact measuring device detected charge, and then warm-up to close to the polymerization temperature. Only by adding a sufficient amount of time the injection.Preheat the raw materials will be sent trough of force and then a note sent to the feeder, the feeder note immediately installed in the trough, so as to prevent the pistons from the trough and gap between the edge of missing material. Taoka is usually closed to inject into the feeder to further leak-proof.Trough, the note feeder, gate, runner and mold cavity on the surface of the material can maintain the rapid solidification of a certain temperature,according to the nature of the materials, mold design and parts of the temperature of 280~380 F.In the die-casting material to reach the end of the curing period, the second-casting for a complete release, including the removal gate, runner and injecting Road in trough and the formation of curing pad material (called salvage).In the die-casting, the warm-up material is very important. Cold expected to sloe the flow, first into the cavity of the material to its destination yet, that is likely to polymerization. If it happens, poor product quality, not just the appearance, but also in mechanical properties. Some exceptions, such as injecting a small amount, or some of the low viscosity of the material. Available light or heating stove heating, but an effective and commonly used method is used for making molded plastic dielectric heater.。