污水处理的英文文献中英文翻译
污水处理的重要性英语作文
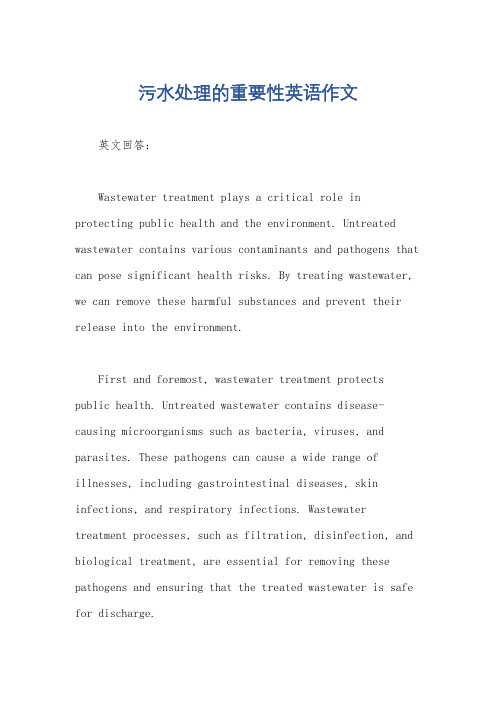
污水处理的重要性英语作文英文回答:Wastewater treatment plays a critical role inprotecting public health and the environment. Untreated wastewater contains various contaminants and pathogens that can pose significant health risks. By treating wastewater, we can remove these harmful substances and prevent their release into the environment.First and foremost, wastewater treatment protects public health. Untreated wastewater contains disease-causing microorganisms such as bacteria, viruses, and parasites. These pathogens can cause a wide range of illnesses, including gastrointestinal diseases, skin infections, and respiratory infections. Wastewater treatment processes, such as filtration, disinfection, and biological treatment, are essential for removing these pathogens and ensuring that the treated wastewater is safe for discharge.Moreover, wastewater treatment helps preserve the environment. Untreated wastewater can damage aquatic ecosystems. It can cause algal blooms, deplete oxygen levels, and harm wildlife. Additionally, it can contaminate groundwater resources and contribute to soil pollution. Wastewater treatment plants remove pollutants like heavy metals, organic matter, and nutrients, which help protect both freshwater and marine environments.Wastewater treatment also plays a significant role in resource recovery. Advanced treatment technologies allow us to extract valuable resources from wastewater, such as energy, nutrients, and water. By doing so, we can reduce our reliance on fossil fuels, conserve water resources, and promote a circular economy.Furthermore, wastewater treatment contributes to economic development. It creates jobs in the environmental sector and supports industries that rely on treated wastewater, such as agriculture and tourism. By investing in wastewater treatment infrastructure, communities canimprove their overall quality of life and economic prosperity.In conclusion, wastewater treatment is essential for protecting public health, preserving the environment, recovering resources, and promoting economic development. It is a vital component of a sustainable and healthy society.中文回答:污水处理对于保护公众健康和环境至关重要。
污水处理工业废水回用中英文对照外文翻译文献

污水处理工业废水回用中英文对照外文翻译文献XXX and resource recovery in us industries。
and they are of significant XXX-catalysis has been well established for water recovery and reuse。
chemo-catalysis is only starting to make an XXX-catalytic processes for water reuse。
XXX。
XXX.2.Chemo-XXX reuseChemo-XXX。
including XXX。
One of the most promising ns of chemo-XXX。
XXX。
This process has been shown to be effective in removing COD (chemical oxygen demand) XXX.3.XXX COD removalXXX treatment。
The process involves the use of a XXX can be a metal oxide or a metal complex。
and the oxidizing agent can be hydrogen peroxide。
ozone。
or XXX mild ns。
and the process is XXX.4.XXXXXX (AOPs) such as XXX。
photo-Fenton n。
and electro-XXX include the use of anic frameworks (MOFs) XXX.5.nIn n。
chemo-catalytic processes。
XXX。
XXX。
such as AOPs。
MOFs。
and nanomaterials。
污水处理厂 外文文献

ENVIRONMENTAL BIOTECHNOLOGYOne-stage partial nitritation/anammox at15°Con pretreated sewage:feasibility demonstration at lab-scale Haydée De Clippeleir&Siegfried E.Vlaeminck&Fabian De Wilde&Katrien Daeninck&Mariela Mosquera&Pascal Boeckx&Willy Verstraete&Nico BoonReceived:26November2012/Revised:28January2013/Accepted:30January2013#Springer-Verlag Berlin Heidelberg2013Abstract Energy-positive sewage treatment can beachieved by implementation of oxygen-limited autotrophicnitrification/denitrification(OLAND)in the main water line,as the latter does not require organic carbon and thereforeallows maximum energy recovery through anaerobic diges-tion of organics.To test the feasibility of mainstreamOLAND,the effect of a gradual temperature decrease from29to15°C and a chemical oxygen demand(COD)/Nincrease from0to2was tested in an OLAND rotatingbiological contactor operating at55–60mg NH4+–NL−1 and a hydraulic retention time of1h.Moreover,the effectof the operational conditions and feeding strategies on thereactor cycle balances,including NO and N2O emissionswere studied in detail.This study showed for the first timethat total nitrogen removal rates of0.5g NL−1day−1can bemaintained when decreasing the temperature from29to15°Cand when low nitrogen concentration and moderate CODlevels are treated.Nitrite accumulation together with elevatedNO and N2O emissions(5%of N load)were needed to favoranammox compared with nitratation at low free ammonia(<0.25mg NL−1),low free nitrous acid(<0.9μg NL−1),and higher DO levels(3–4mg O2L−1).Although the total nitrogen removal rates showed potential,the accumulation of nitrite and nitrate resulted in lower nitrogen removal efficiencies (around40%),which should be improved in the future. Moreover,a balance should be found in the future between the increased NO and N2O emissions and a decreased energy consumption to justify OLAND mainstream treatment. Keywords Energyself-sufficient.Nitrospira.Nitricoxide. Nitrous oxide.DeammonificationIntroductionCurrently,around40full-scale one-stage partial nitrita-tion/anammox plants are implemented to treat highly loaded nitrogen streams devoid in carbon(Vlaeminck et al.2012). This process,known under the acronyms oxygen-limited autotrophic nitrification/denitrification(OLAND)(Kuai and Verstraete1998),deammonification(Wett2006),com-pletely autotrophic nitrogen removal over nitrite(Third et al. 2001),etc.,showed highly efficient and stable performance when treating digestates from sewage sludge treatment plants and industrial wastewaters(Wett2006;Abma et al. 2010;Jeanningros et al.2010).For clarity,one-stage partial nitritiation/anammox processes will be referred to as OLAND in this work.From an energy point of view,the implementation of the OLAND process for the treatment of sewage sludge digestate decreased the net energy consump-tion of a municipal wastewater treatment plant(WWTP)by 50%,with a combination of a lower aeration cost in the side stream and the opportunity to recover more organics from the mainstream(Siegrist et al.2008).Moreover,when co-digestion of kitchen waste was applied,an energyneutral Electronic supplementary material The online version of this article(doi:10.1007/s00253-013-4744-x)contains supplementary material,which is available to authorized users.H.De Clippeleir:S.E.Vlaeminck:F.De Wilde:K.Daeninck:M.Mosquera:W.Verstraete:N.Boon(*)Laboratory for Microbial Ecology and Technology(LabMET),Ghent University,Coupure Links653,9000Gent,Belgiume-mail:Nico.Boon@UGent.beP.BoeckxLaboratory of Applied Physical Chemistry(ISOFYS),Ghent University,Coupure Links653,9000Gent,BelgiumAppl Microbiol BiotechnolDOI10.1007/s00253-013-4744-xWWTP was achieved(Wett et al.2007).To fully recover the potential energy present in wastewater,a first idea of a new sustainable wastewater treatment concept was reported (Jetten et al.1997).Recently,a“ZeroWasteWater”concept was proposed which replaces the conventional activated sludge system by a highly loaded activated sludge step (A-step),bringing as much as organic carbon(chemical oxygen demand(COD))as possible to the solid fraction, and a second biological step(B-step)removing the residual nitrogen and COD with a minimal energy demand (Verstraete and Vlaeminck2011).Subsequently,energy is recovered via anaerobic digestion of the primary and sec-ondary sludge.For the B-step in the main line,OLAND would potentially be the best choice as this process can work at a low COD/N ratio,allowing maximum recovery of COD in the A-step.Moreover,it was calculated that if OLAND is implemented in the main water treatment line and a maximum COD recovery takes place in the A-step,a net energy gain of the WWTP of10Wh inhabitant equivalent (IE)−1day−1is feasible(De Clippeleir et al.2013).To allow this energy-positive sewage treatment,OLAND has to face some challenges compared with the treatment of highly loaded nitrogen streams(>250mg NL−1).A first difference is the lower nitrogen concentration to be removed by OLAND.Domestic wastewater after advanced concen-tration will still contain around30–100mg NL−1and113–300mg CODL−1(Metcalf and Eddy2003;Tchobanoglous et al.2003;Henze et al.2008).High nitrogen conversion rates(around400mg NL−1day−1)by the OLAND process can be obtained at nitrogen concentrations of30–60mg N L−1and at low hydraulic retention times(HRT)of1–2h(De Clippeleir et al.2011).A second challenge is the low tem-perature at which OLAND should be operated(10–15°C compared with34°C).Several studies already described the effect of temperature on the activity of the separate micro-bial groups(Dosta et al.2008;Guo et al.2010;Hendrickx et al.2012).Only a few studies showed the long-term effect of a temperature decrease below20°C on the microbial bal-ances of anoxic and aerobic ammonium-oxidizing bacteria (AnAOB and AerAOB)and nitrite-oxidizing bacteria (NOB)at nitrogen concentrations above100mg NL−1 (Vazquez-Padin et al.2011;Winkler et al.2011).However, the combination of low temperature and low nitrogen con-centration was never tested on a co-culture of AerAOB, AnAOB,and NOB before.At temperatures around15°C, maintaining the balance between NOB and AnAOB and the balance between NOB and AerAOB will get more challeng-ing since the growth rate of NOB will become higher than the growth rate of AerAOB(Hellinga et al.1998). Therefore,it will not be possible to wash out NOB based on overall or even selective sludge retention.The third and main challenge in this application will therefore be the suppression of NOB at temperature ranges of10–20°C and at nitrogen concentration ranges of30–60mg NL−1 (low free ammonia and low nitrous acid),which was not shown before.A final fourth challenge will include the higher input of organics at moderate levels of90–240mg biodegradable CODL−1in the wastewater.Depending on the raw sewage strength,COD/N ratios between2and3are expected after the concentration step,which is on the edge of the described limit for successful OLAND(Lackner et al. 2008).The presence of organics could result in an extra competition of heterotrophic denitrifiers with AerAOB for oxygen or with AnAOB for nitrite or organics,since certain AnAOB can denitrify consuming organic acids (Kartal et al.2007).In this study,the challenges2to4,were evaluated in an OLAND rotating biological contactor(RBC).This reactor at 29°C was gradually adapted over24,22,and17to15°C under synthetic wastewater conditions(60mg N L−1, COD/N of0).Additionally,the COD/N ratio of the influent was increased to2by supplementing NH4+to diluted sewage to simulate pretreated sewage.The effect of the operational conditions and feeding strategies on the reactor cycle balan-ces,including gas emissions and microbial activities were studied in detail.An alternative strategy to inhibit NOB activity and as a consequence increase AnAOB activity at low temperatures based on NO production was proposed. Materials and methodsOLAND RBCThe lab-scale RBC described by De Clippeleir et al.(2011) was further optimized at29°C by an increase in the influent nitrogen concentration from30to60mg NL−1and a limitation of the oxygen input through the atmosphere by covering the reactor before this test was started.The reactor was based on an air washer LW14(Venta,Weingarten, Germany)with a rotor consisting of40discs interspaced at 3mm,resulting in a disc contact surface of1.32m2.The reactor had a liquid volume of2.5L,immersing the discs for 55%.The latter was varied over the time of the experiment. The reactor was placed in a temperature-controlled room. The DO concentration was not directly controlled.In this work,continuous rotation was applied at a constant rotation speed of3rpm,which allowed mixing of the water phase. RBC operationThe RBC was fed with synthetic wastewater during phases I to VII.From phase VIII onwards,the COD/N was gradually increased(phases VIII–X)to2(phases XI–XIII).The syn-thetic influent of an OLAND RBC,consisted of(NH4)2SO4 (55–60mg NL−1),NaHCO3(16mg NaHCO3mg−1N),andAppl Microbiol BiotechnolKH2PO4(10mg PL−1).Pretreated sewage was simulated by diluting raw sewage of the communal WWTP of Gent, Belgium(Aquafin).The raw wastewater after storage at 4°C and settlement contained23–46mg NH4+–NL−1, 0.2–0.4mg NO2−–NL−1,0.4–2.7mg NO3−–NL−1,23–46mgKjeldahl–NL−1,3.8–3.9mg PO43−–PL-1,26–27mg SO42−–S L−1,141–303mg COD tot L−1,and74–145mg COD sol L−1.The raw sewage was diluted by factors2–3to obtain COD values around110mg COD tot L−1and by addition of(NH4)2SO4to obtain final COD/N values around2.The reactor was fed in a semi-continuous mode:two periods of around10min/h for phases I–XI and one period of20min/h for phases XII and XIII.The influent flow range varied from47to65Lday−1and the reactor volume from3.7to2.5L(during78and55% submersion,respectively).Corresponding HRTare displayed in Tables1and2.Reactor pH,DO,and temperature were daily monitored and influent and effluent samples were taken at least thrice a week for ammonium,nitrite,nitrate,and COD analyses. Detection of AerAOB,NOB,and AnAOB with FISHand qPCRFor NOB and AnAOB,a first genus screening among the most commonly present organisms was performed by fluo-rescent in-situ hybridization(FISH)on biomass of days1 (high temperature)and435(low temperature and COD presence).A paraformaldehyde(4%)solution was used for biofilm fixation,and FISH was performed according to Amann et al.(1990).The Sca1309and Amx820probes were used for the detection of Cand.Scalindua and Cand. Kuenenia&Brocadia,respectively,and the NIT3and Ntspa662probes and their competitors for Nitrobacter and Nitrospira,respectively(Loy et al.2003).This showed the absence of Nitrobacter and Scalindua(Table S1in the Electronic supplementary material(ESM)).Biomass sam-ples(approximately5g)for nucleic acid analysis were taken from the OLAND RBC at days1,60,174,202,306,385, 399,and413of the operation.DNA was extracted using FastDNA®SPIN Kit for Soil(MP Biomedicals,LLC), according to the manufacturer’s instructions.The obtained DNA was purified with the Wizard®DNA Clean-up System (Promega,USA)and its final concentration was measured spectrophotometrically using a NanoDrop ND-1000spec-trophotometer(Nanodrop Technologies).The SYBR Green assay(Power SyBr Green,Applied Biosystems)was used to quantify the16S rRNA of AnAOB and Nitrospira sp.and the functional amoA gene for AerAOB.The primers for quantitative polymerase chain reactions(qPCR)for detection of AerAOB,NOB,and AnAOB were amoA-1F–amoA-2R (Rotthauwe et al.1997),NSR1113f–NSR1264r(Dionisi et al. 2002),and Amx818f–Amx1066r(Tsushima et al.2007),re-spectively.For bacterial amoA gene,PCR conditions were: 40cycles of94°C for1min,55°C for1min,and60°C for 2min.For the amplification of Nitrospira sp.16S rRNA gene, 40cycles of95°C for1min,50°C for1min,and60°C for 1min were used while for AnAOB16S rRNA the PCR temperature program was performed by40cycles of15s at 94°C and1min at60°C.Plasmid DNAs carrying NitrospiraTable1Effect of temperature decrease on the operational conditions and performance of OLAND RBC reactorPhase I II III IV V VI VIIPeriod(days)1–2122–3536–6162–210210–263263–274275–306 Immersion level(%)78787878557855 Temperature(°C)29±224±122±0.617±1.216±0.915±0.814±0.4 Operational conditionsDO(mg O2L−1) 1.1±0.2 1.3±0.2 1.4±0.1 1.7±0.3 2.8±0.4 2.4±0.2 3.1±0.2 pH(−)7.5±0.17.5±0.17.5±0.17.6±0.17.7±0.17.7±0.17.8±0.1 HRT(h) 1.85±0.04 1.84±0.09 1.73±0.04 1.86±0.11 1.09±0.02 1.57±0.02 1.09±0.02 FA(mg NL−1)0.35±0.180.36±0.180.34±0.140.36±0.130.25±0.160.33±0.170.13±0.04 FNA(μg NL−1)0.3±0.10.3±0.20.4±0.20.4±0.10.9±0.40.6±0.10.9±0.2 PerformanceTotal N removal efficiency(%)54±552±549±934±936±936±942±4 Relative NO3−prod(%of NH4+cons a)7±17±17±114±618±916±321±4 Relative NO2−accum(%of NH4+cons)2±43±45±515±530±826±631±5 AerAOB activity(mg NH4+–NL−1day−1)267±38267±49260±52260±53811±229460±44986±71 NOB activity(mg NO2–NL−1day−1)0±00±00±09±1260±9420±585±25 AnAOB activity(mg N tot L−1day−1)412±38403±37368±76248±67448±117305±74529±75DO dissolved oxygen,HRT hydraulic retention time,F A free ammonia,FNA free nitrous acid,cons consumption,prod production,accum accumulation,tot totala NH4+consumption is corrected for nitrite accumulationAppl Microbiol Biotechnoland AnAOB16S rRNA gene and AerAOB functional AmoA gene,respectively,were used as standards for qPCR.All the amplification reactions had a high correlation coefficient (R2>0.98)and slopes between−3.0and−3.3.Detailed reactor cycle balancesFor the measurements of the total nitrogen balance,including the NO and N2O emissions,the OLAND RBC was placed in a vessel(34L)which had a small opening at the top(5cm2).In this vessel,a constant upward air flow(around1ms−1or0.5L s-1)was generated to allow calculations of emission rates.On the top of the vessel(air outlet),the NO and N2O concentra-tion was measured,off-and online,respectively.NH3emis-sions were negligible in a RBC operated at about2mg NH3–NL−1(Pynaert et al.2003).Since FA levels in the currentstudy are about ten times lower,NH3emissions were not included.In the water phase,ammonium,nitrite,nitrate,hy-droxylamine(NH2OH),N2O,and COD concentrations were measured.Moreover,DO concentration and pH values were monitored.The air flow was measured with Testo425hand probe(Testo,Ternat,Belgium).Chemical analysesAmmonium(Nessler method)was determined according to standard methods(Greenberg et al.1992).Nitrite and nitrate were determined on a761compact ion chromatograph equipped with a conductivity detector(Metrohm,Zofingen, Switzerland).Hydroxylamine was measured spectrophoto-metrically(Frear and Burrell1955).The COD was determined with NANOCOLOR®COD1500en NANOCOLOR®COD 160kits(Macherey-Nagel,Düren,Germany).The volumetric nitrogen conversion rates by AerAOB,NOB,and AnAOB were calculated based on the measured influent and effluent compositions and the described stoichiometries,underestimat-ing the activity of AnAOB by assuming that all COD removed was anoxically converted with nitrate to nitrogen gas (Vlaeminck et al.2012).DO and pH were measured with respectively,a HQ30d DO meter(Hach Lange,Düsseldorf, Germany)and an electrode installed on a C833meter (Consort,Turnhout,Belgium).Gaseous N2O concentrations were measured online at a time interval of3min with a photo-acoustic infrared multi-gas monitor(Brüel&Kjær, Model1302,Nærem,Denmark).Gas grab samples were taken during the detailed cycle balance tests for NO detec-tion using Eco Physics CLD77AM(Eco Physics AG, Duernten,Switzerland),which is based on the principle of chemiluminescence.For dissolved N2O measurements,a1-mL filtered(0.45μm)sample was brought into a7-mL vacutainer(−900hPa)and measured afterwards by pressure adjustment with He and immediate injection at21°C in a gas chromatograph equipped with an electron capture detector (Shimadzu GC-14B,Japan).Table2Effect of COD/N increase on the operational conditions and performance of OLAND RBC reactorPhase VIII IX X XI XII XIIIPeriod(days)355–361362–369370–374375–406407–421422–435 Immersion level(%)555555555555COD/N(-)0.51 1.5222 Feeding regime(pulsesh−1)222211 Operational conditionsDO(mg O2L−1) 2.9±0.3 2.5±0.6 2.4±0.3 3.0±0.7 3.6±0.3 3.2±0.3 pH(−)7.8±0.027.7±0.17.6±0.027.6±0.17.6±0.27.6±0.1 HRT(h) 1.06±0.11 1.03±0.020.92±0.020.94±0.05 1.10±0.05 1.06±0.2 FA(mg NL−1)0.10±0.050.04±0.050.15±0.050.21±0.100.23±0.120.04±0.02 FNA(μg NL−1)0.4±0.10.2±0.20.2±0.010.3±0.10.2±0.10.6±0.2 PerformanceTotal N removal efficiency(%)36±545±1823±328±623±1342±3 Relative NO3−prod(%of NH4+cons a)42±543±1263±250±662±1846±6 Relative NO2−accum(%of NH4+cons)20±410±105±18±37±413±6 AerAOB activity(mg NH4+–NL−1day−1)592±15446±31238±28352±73289±138600±204 NOB activity(mg NO2−–NL−1day−1)257±19294±81465±60352±84427±115394±76 AnAOB activity(mg N tot L−1day−1)385±86452±205262±39355±73281±159481±73COD removal rates were negligible in all phasesDO dissolved oxygen,HRT hydraulic retention time,F A free ammonia,FNA free nitrous acid,cons consumption,prod production,accum accumulation,tot totala NH4+consumption is corrected for nitrite accumulationAppl Microbiol BiotechnolResultsEffect of temperature decreaseDuring the reference period (29°C),a well-balanced OLAND performance (Fig.1;Table 1)was reached with minimal nitrite accumulation (2%)and minimal nitrate production (7%).This was reflected in an AerAOB/AnAOB activity ratio of 0.6(Table 1,phase I).The total nitrogen removal rate was on average 470mg N L −1day −1or 1314mg Nm −2day −1,and the total nitrogen removal efficiency was 54%.Decreasing the temperature from 29to 24°C and further to 22°C over the following 40days,did not result in anysignificant changes of the operational conditions (Table 1;phases I –III),performance of the reactor (Fig.1)or abun-dance of the bacterial groups (qPCR;Fig.S1in the ESM ).However at 17°C,a decrease in total nitrogen removal efficiency was observed (Table 1;phase IV).An imbalance between the AerAOB and the AnAOB was apparent from a stable AerAOB activity yet a declining AnAOB activity.Moreover,NOB activity was for the first time detected in spite of free ammonia (FA)and free nitrous acid (FNA)con-centrations did not change (Table 1;phase IV).Moreover,no significant differences in abundance of NOB,AerAOB,and AnAOB could be detected with qPCR (Fig.S1in the ESM ).However,DO concentrations started to increase during that period from 1.4to 1.7mg O 2L −1.As the availabilityofFig.1Phases I –VII:effect of temperature decrease on the volumetric rates (top )and nitrogen concentrations (bottom )Appl Microbiol Biotechnoloxygen through the liquid phase did not seem to be satisfac-tory to counteract the decrease in ammonium removal effi-ciency,the immersion level was lowered to55%to increase the availability of oxygen through more air-biofilm contact surface.Consequently,the volumetric loading rate increased (factor1.7)due to the decrease in reactor volume(day210, Fig.1).This action allowed higher ammonium removal effi-ciencies due to higher AerAOB activities(factor3).AnAOB activity increased with a similar factor as the volumetric loading rate(1.8compared with1.7)consequently resulting in an increased imbalance between these two groups of bac-teria(Table1;phase V).Moreover,although the FNA in-creased with a factor2,the NOB activity increased with a factor7,resulting in a relative nitrate production of30% (Table1;phase V).As NOB activity prevented good total nitrogen removal efficiencies,the immersion level was in-creased again to78%(day263;Fig.1).This resulted indeed in a lower NOB activity(Table1;phase VI).However,also the AerAOB activity decreased with the same factor,due to the lower availability of atmospheric oxygen.Therefore,the reactor was subsequently operated again at the lower immer-sion level(55%)to allow sufficient aerobic ammonium conversion.The latter allowed a stable removal efficiency of 42%.The AnAOB activity gradually increased to a stable anoxic ammonium conversion rate of529mg NL−1day−1. During the synthetic phase,no changes in AerAOB, AnAOB,and NOB abundance were measured with qPCR (Fig.S1in the ESM).The effluent quality was however not optimal as still high nitrite(around15mg NL−1)and nitrate (around13mg NL−1)levels were detected.Effect of COD/N increaseThe synthetic feed was gradually changed into pretreated sewage by diluting raw sewage and adding additional nitro-gen to obtain a certain COD/N ratio.During the first3weeks of this period(Fig.2),the COD/N ratio was gradually increased from0.5to2.Due to the short adaptation periods (1week per COD/N regime),the performance was unstable (Fig.2;Table2,phases VIII–XI).Compared with the end of the synthetic period(phase VII),operation at a COD/N ratio of2(phase XI)resulted in a sharp decrease in nitrite accu-mulation(Fig.2)and an increase in the ammonium and nitrate levels.This indicated increased NOB activity(factor 4),decreased AerAOB(factor3)and decreased AnAOB (factor2)activity(Tables1and2).To allow higher nitrogen removal rates,the HRT was increased from0.94to1.1h,by decreasing the influent flow rate.Moreover,the feeding regime was changed from two pulses of10min in1h to one period of20min/h.These actions did not significantly decrease the effluent nitrogen concentration(Fig.2)and did not influence the microbial activities(Table2,phase XII). Therefore the loading rate was again increased to the levels before phase XII.However,the single-pulse feeding wasmaintained.This resulted in high ammonium removal effi-ciencies and therefore low ammonium effluent concentra-tion around dischargeable level(4±1mg NH4+–NL−1; Fig.2).Nitrate and nitrite accumulation were not counter-acted by denitrification as only0.02mg CODL−1day−1wasremoved.Therefore,nitrite and nitrate levels were still toohigh to allow effluent discharge.The total nitrogen removalefficiency(42%)and rate(549±83mg NL−1day−1or1,098±106mgNm−2day−1)at COD/N ratios of2wassimilar as during the synthetic period(phase VII).Comparedwith the reference period at29°C,the total nitrogen removalrate did not changed significantly(470±43versus549±83mgNL−1day−1at high and low temperatures,respectively).The22%lowered removal efficiency was merely due to anincreased nitrogen loading rate.Nitratation and NO/N2O emissionsAt the end of the synthetic phase(phase VII)and the end ofthe experiment(phase XIII),the total nitrogen balance of thereactor was measured.A total nitrogen balance was obtainedby measuring all nitrogen species(NH4+,NO2−,NO3−,NH2OH,and N2O)in the liquid phase and N2O and NO inthe gas phase.A constant air flow,diluting the emitted N2Oand NO concentrations was created over the reactor tomeasure gas fluxes over time.The effect of the loading rate,feeding pattern,and concentration of nitrite and ammoniumon the total nitrogen balance in the reactor were tested(Table3).NH2OH measurements showed low concentra-tions(<0.2mg NL−1)in all tests,making it difficult to linkthe profiles with the N2O emission.Lowering the loading rate by increasing the HRT(Table3,test B)increased the DO values and allowed higherDO fluctuations over time at synthetic conditions.Moreover,NOB activity increased significantly resultingin lower total nitrogen removal efficiencies and high levelsof nitrate in the effluent(Table3,test B).The relative N2Oemissions did not change and were relatively high(6%of Nload).However,the concentration of N2O in the liquid andin the gas phase decreased with a factor2(Table3).When pretreated sewage was fed to the reactor,theOLAND RBC was operated at lower nitrite concentration,while similar ammonium and nitrate concentrations wereobtained(Table3,test C).The lower nitrite concentrationshowever did not result in lower N2O emission rates.Whenthe feeding regime was changed to a more continuous-likeoperation(4pulses/h),the N2O emission increased signifi-cantly,while NO emission remained constant(Table3,testD).Due to the lower ammonium removal efficiency(65compared with81%),but similar relative nitrite and nitrateaccumulation rate,the total nitrogen removal efficiencydecreased.Appl Microbiol BiotechnolWhen a nitrite pulse was added just after feeding,about 20mg NO 2−–NL −1was obtained in the reactor.This did increase the NO and N 2O emissions significantly (p <0.05)compared with the same feeding pattern (Table 3,tests C –E).Although similar constant total nitrogen removal efficien-cies were obtained during this operation,a significant (p <0.05)decrease in the relative nitrate production was observed.The latter was mainly caused by a global increase in AnAOB activity.In the last test (F),the influent ammo-nium concentration was doubled,leading to higher ammo-nium and also FA concentrations (1±0.4mg N L −1compared with 0.1±0.4mg NL −1).Due to overloading of the system,the total nitrogen removal efficiency decreased.However,at these conditions a lower relative nitrate pro-duction was obtained;due to a decrease in NOB and in-crease in AnAOB activity (Table 3,test F).Together with this,increased NO and N 2O emissions were observed.As the influence of the nitrogen loading and DO concentration could be considered minor in this test range (Fig.S2in the ESM ),these tests show a relation between increased NO emissions and decreased relative nitrate productions (Table 3).When the activity during the feeding cycle was studied in more detail,it could be concluded that the highest nitrogen conversion rates took place during the feeding period,which was characterized by a high substrate availability and high turbulence (Fig.3).As the HRT is only 1h,the reactor volume is exchanged in 20min.During this phase,ammo-nium increased,while nitrite and nitrate concentrations de-creased due to dilution (Figs.S3,S4,and S5in the ESM ).The NOB/AnAOB ratio was around 1,which means that NOB were able to take twice as much nitrite thanAnAOBFig.2Phases VIII –XIII:effect of COD/N increase on the volumetric rates (top )and nitrogen concentrations (bottom ).Data during the N balance tests (days 424–431)were not incorporated in the figure but are shown in Table 3Appl Microbiol BiotechnolTable 3Operational parameters and nitrogen conversion rates during the six different RBC operations which differ from feeding composition and feeding regime (volume at 2.5L and 50%immersion of the discs,days 307–309for synthetic feed,and days 424–431)Reactor phaseVII (synthetic)XIII (pretreated sewage)Test A a B C a D E -F Additive––––NO 2−NH 4+Feeding regime (pulses/h)221411Total N loading rate (mg NL −1day −1)1,1695851,3401,5541,7372,718Temperature water (°C)15±0.316±0.2*14±0.415±0.1*16±0.1*15±0.4DO (mg O 2L −1) 2.9±0.1 3.7±0.6* 4.0±0.1 3.2±0.1* 3.3±0.1* 3.2±0.1*pH (-)7.6±0.067.6±0.057.6±0.047.6±0.017.6±0.027.8±0.02*Ammonium out (mg NL −1)9±1 1.4±1*11±319±3*12±158±4*Nitrite out (mg NL −1)14±213±16±16±0.418±2*9±0.3*Nitrate out (mg NL −1)17±337±6*18±216±1*18±0.420±0.4NH 4+oxidation rate (mg NL −1day −1)895±22509±2*1,051±73957±891,053±161,285±93*Relative nitrite accumulation (%)25±320±1*14±315±18±4*15±1Relative nitrate production (%)36±876±6*48±147±342±2*34±3*Total efficiency (%)38±417±4*35±328±4*32±227±4*AerAOB activity (mg NH 4+–NL −1day −1)658±88469±17*827±44781±57795±30938±46*NOB activity (mg NO 2−–NL −1day −1)174±59299±28*375±38342±24*362±13277±18*AnAOB activity (mg N tot L −1day −1)205±3849±13*234±20218±29263±15*354±49*N 2O in liquid (μg NL −1)64±4630±22*78±12104±29*61±1374±4NO emission (mg Nday −1)0.53±0.03n.d.0.66±0.060.74±0.08 1.65±0.18*0.82±0.1*N 2O emission (mg Nday −1)151±2893±23*170±19179±6*274±37*202±18*%N 2O emission on loading5.1±1.06.4±1.6*5.0±0.64.5±0.2*6.2±0.8*3.0±0.3*aReference period for synthetic and pretreated sewage*p <0.05,significant differences compared with referenceperiod Fig.3Detailed NO/N 2Omonitoring during the reference test (Table 3,test C)and when nitrite was pulsed (Table 3,test E)and effect on AerAOB,AnAOB,and NOB activity during the different phases of the feeding cycle.Significant differences in AerAOB,AnAOB,NOB,and NO/N 2O concentration compared with the reference period areindicated with asterisks ,circles ,double quotation mark ,and plus sign ,respectivelyAppl Microbiol Biotechnol。
污水处理英文文献英语

Oxidize the ditch craft in dirty water handle of application and developmentCaiZhi一jun(Foshan City Shunde District Environmental EngineeringBranch Foshan Guangdong 528000)【Abstract 】Setanaerobic, naoxic section Carrous oxidation ditch with biologicla nitrogen and phosphoru sremoval capabilitie, is curren dythe mainstream of city life process of sewage treatme nt, This article descirbes the structure of Carrousel oxidation ditch, porcess and design problems d uring the oper-ation and the corresponding solutions.【Keywords】Carrousel;Oxidationditch;Phosphorusnadnitrogenremoval;Structure;Mechanism1. ForewordOxidize the ditch( oxidation ditch) again a continuous circulation spirit pond( Continuous loop r eactor), is a live and dirty mire method a kind of to transform.Oxidizing the dirty water in ditch ha ndles the craft be researched to manufacture by the hygiene engineering graduateschool of Hollan d in the 50'sof20centuriessuccess.Since in 1954 at Dutch throw in the usage for the velY first nme .secause its a water fluid matter good, circulate the stability and manage convenience etc. techniqu e characteristics, already at domestic and international and extensive application in live the dirty w ater to is dirty to manage aquecustv with the industy[1].Current application than oxidize extensively the ditch type include:The ( Pasveer) oxidizes the ditch, the (Carrousel) oxidizes the ditch, ( Orbal) oxidizes the ditch, the type of T oxidizes the ditc h( three ditch types oxidize the ditch), the type of DE oxidizes the ditch to turn to oxidize the ditch with the Integral whore.these oxidize the ditch because of the difference of esse in construction wi th circulating, therefore each characteristics[2].This text will introduce construction, mechanism, e xistent problem and its latest developments that Carrousel oxidize ditches primarily.2. The Carrousel oxidizes the construction of the ditchThe Carrousel Oxidize the ditch to be researched to manufacture by Dutch DHV company deve lopment in 1967.0xidize the last the companyofDHVinfou ndationoftheditchin theoriginal Carrous el to permited specially the company EIMCO to invent again with its patent in the United States C arrousel 2000 system realizes the living creature of the higher request takes off the nitrogen with d ividedbythefunctionof.Therehasbeen in the world up to now more than 850 Carrousels oxidize the ditch with the Carrousel 2000 system are circulating From diagram therefore[3].The Carrousel oxidizes the ditch the usage the spirit of that definite direction control with shak e up the device, face to mix with the liquid deliver the level speed, from but make drive the liquid of admixture that shake up is in oxidize ditch shut match outlet circulate nowrnererore oxidize the ditch have the special hydraulics flows the ,current complete mix with the characteristics of the ty pe reactor, have the characteristics that push the flow type reactor again, the ditch inside exsrts obviously of deliquescence oxygen density steps degree.Oxidizing the ditch cross section is rectangle or trapezoids, the fiat surface shape is many for oval, the ditch internal water is deep general for2.5 -4 .5 m , the breadth is deep compare for 2:1, also have the deep wate r amount to 7 ms of, ditch inside average speed in water current is 0.3 mS/ s.ostorze ditch spirit admixture equipments cont ain surface spirit machine, the spirit of turn to brush or turn the dish and shoot to flow the spirit m achine, pipe type spirit machine with promote take care of type spirit machine etc., match with in r ecent years usage still contain underwater push machine[4~6].3. The Carrousel oxidizes the mechanism of the ditch3.1 The Carrousel oxidizes the ditch handles dirty and aqueous principleThe at the beginning common Carrousel oxidizes the dirty water In inside In craft of the ditch di rect with dirty mire In reflux together enteroxidize theditch system.The surface spiritmachinemake sfuse In the liquid of admixture the density of the oxygen DO increases about 2 the 3 mgsl t.uncer this kind of well the term of the oxygen, the microorganism gets the enough deliquescence oxygen comes and go to divided by the BOD;At the same time, the ammonia were too oxidized nitrate wi th second nitrate, this time, mix with the liquid be placed in the oxygen appearance.In the spirit ma chine downstream, after water current be become by the swift flow appearance of the spirit Distric t oP even flow the appearance, the water current maintainsin theminim umcurrentvelocity,guarante eingthe liveand dirty mire be placed in the floats the appearance.( average current vercctvs-o.a msl s)Oxldlze microbially the process consumed to fuse theoxygenin thewater,until thevalueofDOdecl inesforzero, mixing with the liquid report the anoxia appearance.versa nitric that turn the function through anoxia area, mix with the liquid enter to have the oxygen area, completing once circulatin g.That system inside, the BOD declines the solution is a continuous process, the nitric turns the fu nction to turn with the versa nitric ~e function ta ke place in same pond.Because of structural restri ct, this kind of oxidize the ditch although can then valid whereabouts BOD,divided by the phosph orus take off the nitrogenous ability ltmrtedt".3.2 The Carrousel oxidizes the ditch divideds by the phosphorus takes off the nitrogenous inf luence factor.Affecting the Carrousel oxidizes the ditch divideds by the phosphoric factor is dirty mire, nitrat e density and quality densities primarily.The research expresses, being total and dirty mire as 11% that a hour biggest phosphorus 4% with deal is its fuck dirty mire deal within live and dirty mire, k eep for the the germ physical endowment measures, but when dirty mire over 15 d hour dirty mire the Inside is biggesttocontain theobviousdescentindealIn phosphorus,canning not reach the biggest divideding by the result of phosphorus on the contrary.Therefore, prolong persistently the dirty mi re (for example 20ds,25ds,30ds) is to have no necessary, proper choose to use within the scope of 8~ 15 d.At the same time, high nitrate density with low quality density disadvantage in divided by the process of phosphorus .4. The Carrousel oxidizes problem and solution methods of the ditch esse.Though the Carrousel oxidizes the ditch has a water fluid matter good, the anti-pounds at the b urthen ability strong, divided by the phosphorus take off the nitrogen efficiency. But, in physically of movement process, still exstts a series of problem.4.1 Dirty mire inflation problemWhen discard the aquatic carbohydrate more, the N, P contains the unbalance of deal, the pH value is low, oxidizing the dirty mire in inside in ditch carries high, fuse the oxygen density the shor tage, line up the mire not etc. causes easily dirty mire ingerm in form in silk inflatlon;Not the dirty mire in germ in form in silk inflation takes place primarily at the waste water water temperature is lower but the dirty mire carries higher hour.The microbial burthen is high, the germs absorbed the large quantity nourishment material, is low because of the temperature, metabolism the speed is sl ower, accumulating the rises large quantity is high to glue sexual and many sugar materials, makin g the surface of the live and dirty mire adhere to the water to increase consumedly, SVI the value i s very high, becoming the dirty mire inflation.Cause that aim at the dirty mire inflation, can adopt the different counterplan:From the anoxia, water temperature high result in of, can enlargement tolerance or lower into the water measures to alleviate burthen, or the adequacy lowers the MLSS( control dirty mire reflux measure), making n eed the oxygen measures decrease.It the dirty mirecarrieshigh, can increaseMLSS, toadjusttheburt hen, necessity4.2 Foam problemBecauseentering totakethe greaseoflarge quantityinthewater, handling system can't completely and availably its obviation, parts of greases enriches to gather in in the dirty mire, through turn to brush the oxygen agitation, creation large quantity foam;The mire is partial to long, the dirty mire is aging, and also easy creation toam.Sprav topourthewaterordivided bywiththesurfacetheof do aw ay with the foam, in common use divided by the an organism oil, kerosene, the oil of stncon, thro w deal as 0.5~ 1.5 mgsl L.Pass to increase dirty mire in pond in spirit in density or adequacies let up the tolerance of ,also can control the foam creation effectively.When contain the live materia! i n surface in the waste water more, separate with the foam easily and in advance method or other m ethods do away with.Also can consider to increase to establish a set of dlvideding by the oil device moreover.But enhance most importantly the headwaters manage, reducing to contain the oil over t he high waste water and other poisonous waste water of into[llJ.4.3 Float the problem on the dirty mireWhen contain in the waste water the oil measures big, whole system mire quality become light , can't like to control very much in operate process its at two sink the pond stop over time, resultin g in the anoxia easily, producing the corrupt and dirty mire ascend to float;When spirit time over l ong, take place in pond the high degree nitric turn the function, making nitrate density high, at two sink the versa nitric in easy occurrence in pond turn the function, creation nitrogen spirit, make di rty mire ascend f1oat;Moreover, contain the oil in the waste water?Take place thedirtymire ascendafterfloating should pauseenter water, broke off or dirty mire in clearance, judge the clear reason, adjust the operation.The dirty mire sinks to decline the sex bad, can throw to add of oagulate or sloth materials, the improvement precipitates the sex;Suchas entert he watercarries big let upintothe water measures or the enlargement reflux measures.Sucn as the di rty mire grain small lower the spirit machine turn soon.If discovers versanitricturning,shouldletup thetolerance,enlarge the reflux or row the mire measures;1f discover the dirty mire is corrupt, shou ld enlargement tolerance, the clearance accumulates the mire, and try the ameliorative pond intern al water dint term!':"4.4 Current velocity is not all and the dirty mire sinks to accumulate the problemIn Carrousel oxidize ditch, for acquiring its special admixture with handles result, mix with liq uid must with certain current velocity is in ditch circulate flow.Think generally, the lowest current velocity should should attain for an average current velocity for, doing not take place sinking acccmutetmq 0.3~0.5 msl s.The spirit equipments that oxidize the ditch is general to turn to brush for t he spirit of to turn the dish with the spirit of , turning to brush of immerse to have no depth for 25 0 ~300 mms, turn the dish immerse to have no depth for 480"'530 mms.With oxidize the ditch wat er the deep(3.0~3.6 ms) comparing, turn to brush occupied the deep 1 / 1 0~ in water 1/12, turned t he dish to also occupy the 1/6'" only 1/7, therefore result in to oxidize the ditch upper part current velocity bigger{ roughly 0.8"'1.2 ms, even larger}, but the bottom current velocity is very small( e specially at the water is deep 2/3 or 3/4 below, mix with the liquid has no current velocity almost), causing ditch bottom large quantity accumulate the mire( sometimes accumulate the mire thicknes s amount to a 1.0 ms), the valid capacity that reduced to oxidize the ditch consumedly, lowered to handle result, affected a water fluid matter[13].Moreover, pass in the spirit on board swim to establish the underwater push machine can also t urn to the spirit of the liquid of admixture that brush the bottom low speed area circulates to flow t o rise positive push function, from but the solution oxidizes the problem that low and dirty mire in current velocity in bottom in ditch sink accumulates,Establish the underwater push machine useds for exclusivelythe push mixs withtheliquidcan make movementmethod that oxidize the ditch much more vivid, this for economy energy, lift the high-efficiency having the very important meaning[14].5. The Carrousel oxidizes the development of the ditchBecause the dirty water handles standard inside to divided by the phosphorus take off the nitro genous request more and more strict, the development that Carrousel further oxidized the ditch to also get.Current, the research and application includes morely below two category type:Tiny bore spirit type Carrousel 2000 systems, Carrousel 3000 system.5.1 TIny bore spirit type Carrousel 2000 systemTiny bore spirit type Carrousel 2000 tiny bore in adoption in system spirit( provide oxygen equi pments as the drum breeze machine), the tiny bore spirit machine can produce the diameter of larg e quantity as a surface for or so and small spirit steeping, this consumedly increases spirit bubble a ccumulates, undering the certain circumstance in capacity in pond make the oxygen transfer the gr oss measures aggrandizement.( if deep increment in pond, its spread the quality efficiency will be higher)Produce the technique ability of the factory house according to the current drum breeze ma chine, the valid waterof thepond is deepbiggestamountingtoa8 ms, therefore can select by examina tions according to the different craft request the fit water is deep.The tradition oxidizes the ditch p ushes to flow is to make use of to turn to brush, turn a disc or pour the umbrella type form machin e realizes of, its equipments utilization is low, the motive consumes big.TIny bore spirit type Carro usel 2000 systems then adopted the underwater pushes the way that flow, rises to dive the propelle r the leaf the motivation that round creation the direct function namely in the of water, at push to fl ow the function to can keep dirty mire from sinking to decline effectively again at the same time.A s a result, the adoption dives the propeller since lower the motive consume, making mire water got again to mixs with adequately.5.2 Carrousel 3000 systemCarrousel 3000 systems are in the Carrousel 2000 systems are ex-to plus a living creature the c hoice the area.That living creature choice area is a craft to make use of high organism carries to sie ve germ grow, repress silk form germ increase, increase each pollutant do away with the rate, after ward principle together Carrousel 2000 syste m.Carrousel 3000 system of bigger increases to express at:An is to increased the pond deep, can a mount to 7.5"'8 ms, united at heart circle type, the pond wall uses totally, reducing to cover the are a, lowering to build the price to increases to bear the low temperature ability at the same time;( ca n amount to 7 'C )Two is the liquid of admixture that spirit equipments that skillful design, the for m machine descends to install to lead to flow ,the anoxia of take out, adopt the underwater propell er solution current velocity problem;Three is to used the advanced spirit controller QUTE.( it adop t the much aer kind of changing the deal control mode)f our is to adopt the integral whole turn the design, starting from the center, Including below wreath form consecuuon craft unu.eoter the well of waterwiththecent watermachine thatused for the liveand dirty mire in reflux;Difference from fo ur-part the choice pond that cent constitute with !X oxygen pond.This outside is a Carrousel to hav e three spirit machine with a prepare versa nitric turn the pond 2000 system.( such as figure 2 sho w)Five is tube line that the design that the circular integral whole turn to make oxidize the ditch do not need additionally, can immediately realize dirty mire in reflux allotment in different craft unit[ [17].6. ConclusionThe Carrousel oxidizes the ditch because of having the good a phosphorus takes off the nitroge n ability, anti-pounds at the burthen ability with circulate to manage the convenience etc. the adva ntage, having got the extensive application.But because of technological development with social advance, that craft is necessarily will exaltation getting further.The author thinks:The carrousel oxi dizes the future research direction of the ditch will now of main below several aspects.1 Combination living creature method, research with develop the living creature model carrouse l oxidize the e this can not only increases the microorganism gross of the unit reactor meas ures, from but increases the organism carries, but also living creature oneself the inside that have p laces the AI the system of 0 enhances to take off the nitrogen result[[18].2 Increases continuously the Carrousel oxidize the microbial activity in Inside in crtcn.scr exa mple throw to add the EM in oxidize ditch with single mind the germ grow, throws in that the salt of Iron make the microorganism tame the live char in iron, devotion in living creature to become t he torrnation to strengthen the germ gumregiment and increases to bear the toxicity pound at etc..3 Increasing the Carrousel oxidizes the ditch equtpments function with supervise and control the technique.Function that increases form machine, underwater propeller, reduce to maintain the w orkload; Making use of DO, etc. of ORP many targets supervises and control the technique and ch anges the technique of is from now on the carrouseloxidizes ditchsciencecirculatenecessarilyfromi troad.4 Increasing the Carrousel oxidizes the ditch resistant to cold and bear toxicity can, reduce to co ver the area to build the price with the engineering.Theoretical application, deep pond in water po wer term with the research of the craft function is to lowers the engineering builds the price and in creases resistant to cold bear the toxicity can wait to provide the possible direction. 【References】[1] Xia Shibin, Liu Junxin. An innovative integrated oxidation ditch with vertical circle for domestic wastewater treatment. Process Biochemistry, 2004, 39(4):1117[2] X, Hao; Doddema, H. J.; van Groenestijn, J. W. Use of contact tank to enhance denitrification in oxidation ditches. Water Science and Technology, 1996, 34(1-2):195~202.1~1117.[3] 汪大,雷乐成。
污水处理工业废水回用中英文对照外文翻译文献

(文档含英文原文和中文翻译)中英文资料对照外文翻译Catalytic strategies for industrial water re-useAbstractThe use of catalytic processes in pollution abatement and resource recovery is widespread and of significant economic importance [R.J. Farrauto, C.H. Bartholomew, Fundamentals of Industrial Catalytic Processes, Blackie Academic and Professional,1997.]. For water recovery and re-use chemo-catalysis is only just starting to make an impact although bio-catalysis is well established [J.N. Horan, BiologicalWastewater Treatment Systems; Theory and Operation, Chichester, Wiley,1990.]. This paper will discuss some of the principles behind developing chemo-catalytic processes for water re-use. Within this context oxidative catalytic chemistry has many opportunities to underpin the development of successful processes and many emerging technologies based on this chemistry can be considered .Keywords: COD removal; Catalytic oxidation; Industrial water treatment1.IntroductionIndustrial water re-use in Europe has not yet started on the large scale. However, with potential long term changes in European weather and the need for more water abstraction from boreholes and rivers, the availability of water at low prices will become increasingly rare. As water prices rise there will come a point when technologies that exist now (or are being developed) will make water recycle and re-use a viable commercial operation. As that future approaches, it is worth stating the most important fact about wastewater improvement–avoid it completely if at all possible! It is best to consider water not as a naturally available cheap solvent but rather, difficult to purify, easily contaminated material that if allowed into the environment will permeate all parts of the biosphere. A pollutant is just a material in the wrong place and therefore design your process to keep the material where it should be –contained and safe. Avoidance and then minimisation are the two first steps in looking at any pollutant removal problem. Of course avoidance may not be an option on an existing plant where any changes may have large consequences for plant items if major flowsheet revision were required. Also avoidance may mean simply transferring the issue from the aqueous phase to the gas phase. There are advantages and disadvantages to both water and gas pollutant abatement. However, it must be remembered that gas phase organic pollutant removal (VOC combustion etc.,) is much more advanced than the equivalent water COD removal and therefore worth consideration [1]. Because these aspects cannot be over-emphasised,a third step would be to visit the first two steps again. Clean-up is expensive, recycle and re-use even if you have a cost effective process is still more capital equipment that will lower your return on assets and make the process less financially attractive. At present the best technology for water recycle is membrane based. This is the only technology that will produce a sufficiently clean permeate for chemical process use. However, the technology cannot be used in isolation and in many (all) cases will require filtration upstream and a technique for handling the downstream retentate containing the pollutants. Thus, hybrid technologies are required that together can handle the all aspects of the water improvement process[6,7,8].Hence the general rules for wastewater improvement are:1. Avoid if possible, consider all possible ways to minimise.2. Keep contaminated streams separate.3. Treat each stream at source for maximum concentration and minimum flow.4. Measure and identify contaminants over complete process cycle. Look for peaks, which will prove costly to manage and attempt to run the process as close to typical values as possible. This paper will consider the industries that are affected by wastewater issues and the technologies that are available to dispose of the retentate which will contain the pollutants from the wastewater effluent. The paper will describe some of the problems to be overcome and how the technologies solve these problems to varying degrees. It will also discuss how the cost driver should influence developers of future technologies.2. The industriesThe process industries that have a significant wastewater effluent are shown in Fig. 1. These process industries can be involved in wastewater treatment in many areas and some illustrations of this are outlined below.Fig. 1. Process industries with wastewater issues.2.1. RefineriesThe process of bringing oil to the refinery will often produce contaminated water. Oil pipelines from offshore rigs are cleaned with water; oil ships ballast with water and the result can be significant water improvement issues.2.2. ChemicalsThe synthesis of intermediate and speciality chemicals often involve the use of a water wash step to remove impurities or wash out residual flammable solvents before drying.2.3. PetrochemicalsEthylene plants need to remove acid gases (CO2, H2S) formed in the manufacture process. This situation can be exacerbated by the need to add sulphur compounds before the pyrolysis stage to improve the process selectivity. Caustic scrubbing is the usual method and this produces a significant water effluent disposal problem.2.4. Pharmaceuticals and agrochemicalsThese industries can have water wash steps in synthesis but in addition they are often formulated with water-based surfactants or wetting agents.2.5. Foods and beveragesClearly use water in processing and COD and BOD issues will be the end result.2.6. Pulp and paperThis industry uses very large quantities of water for processing –aqueous peroxide and enzymes for bleaching in addition to the standard Kraft type processing of the pulp. It is important to realise how much human society contributes tocontaminated water and an investigation of the flow rates through municipal treatment plants soon shows the significance of non-process industry derived wastewater.3. The technologiesThe technologies for recalcitrant COD and toxic pollutants in aqueous effluent are shown in Fig. 2. These examples of technologies [2,6,8] available or in development can be categorised according to the general principle underlying the mechanism of action. If in addition the adsorption (absorption) processes are ignored for this catalysis discussion then the categories are:1. Biocatalysis2. Air/oxygen based catalytic (or non-catalytic).3. Chemical oxidation1. Without catalysis using chemical oxidants2. With catalysis using either the generation of _OH or active oxygen transfer. Biocatalysis is an excellent technology for Municipal wastewater treatment providing a very cost-effective route for the removal of organics from water. It is capable of much development via the use of different types of bacteria to increase the overall flexibility of the technology. One issue remains –what to do with all the activated sludge even after mass reduction by de-watering. The quantities involved mean that this is not an easy problem to solve and re-use as a fertilizer can only use so much. The sludge can be toxic via absorption of heavy metals, recalcitrant toxic COD. In this case incineration and safe disposal of the ash to acceptable landfill may be required. Air based oxidation [6,7] is very attractive because providing purer grades of oxygen are not required if the oxidant is free. Unfortunately, it is only slightly soluble in water, rather unreactive at low temperatures and, therefore, needs heat and pressure to deliver reasonable rates of reaction. These plants become capital intensive as pressures (from _10 to 100 bar) are used. Therefore, although the running costs maybe low the initial capital outlay on the plant has a very significant effect on the costs of the process. Catalysis improves the rates of reaction and hence lowers the temperature and pressure but is not able to avoid them and hence does not offer a complete solution. The catalysts used are generally Group VIII metals such as cobalt or copper. The leaching of these metals into the aqueous phase is a difficulty that inhibits the general use of heterogeneous catalysts [7]. Chemical oxidation with cheap oxidants has been well practised on integrated chemical plants. The usual example is waste sodium hypochlorite generated in chlor-alkali units that can be utilised to oxidise COD streams from other plants within the complex. Hydrogen peroxide, chlorine dioxide, potassium permanganate are all possible oxidants in this type of process. The choice is primarily determined by which is the cheapest at the point of use. A secondary consideration is how effective is the oxidant. Possibly the mostresearched catalytic area is the generation and use of _OH as a very active oxidant (advanced oxidation processes) [8]. There are a variety of ways of doing this but the most usual is with photons and a photocatalyst. The photocatalyst is normally TiO2 but other materials with a suitable band gap can be used [9,10]. The processes can be very active however the engineering difficulties of getting light, a catalyst and the effluent efficiently contacted is not easy. In fact the poor efficiency of light usage by the catalyst (either through contacting problems or inherent to the catalyst) make this process only suitable for light from solar sources. Photons derived from electrical power that comes from fossil fuels are not acceptable because the carbon dioxide emission this implies far outweighs and COD abatement. Hydroelectric power (and nuclear power) are possible sources but the basic inefficiency is not being avoided. Hydrogen peroxide and ozone have been used with photocatalysis but they can be used separately or together with catalysts to effect COD oxidation. For ozone there is the problem of the manufacturing route, corona discharge, which is a capital intensive process often limits its application and better route to ozone would be very useful. It is important to note at this point that the oxidants discussed do not have sufficient inherent reactivity to be use without promotion. Thus, catalysis is central to their effective use against both simple organics (often solvents) or complex recalcitrant COD. Hence, the use of Fenton’s catalyst (Fe) for hydrogen peroxide [11]. In terms of catalysis these oxidants together with hypochlorite form a set of materials that can act has ‘active oxygen transfer (AOT) oxidants’ in the presence of a suitable catalyst. If the AOT oxidant is hypochlorite or hydrogen peroxide then three phase reactions are avoided which greatly simplifies the flowsheet. Cheap, catalytically promoted oxidants with environmentally acceptable products of oxidation that do not require complex chemical engineering and can be produced efficiently would appear to offer one of the best solutions to the general difficulties often observed.3.1. Redox catalysis and active oxygen transferThe mechanism of catalytically promoted oxidation with hydrogen peroxide or sodium hypochlorite cannot be encompassed within one concept, however there are general similarities between the two oxidants that allows one to write a series of reactions for both (Fig. 3) [5]. This type of mechanism could be used to describe a broad range of reactions for either oxidant from catalytic epoxidation to COD oxidation. The inherent usefulness of the reactions is that;1. The reactions take place in a two-phase system.2. High pressure and temperature are not required.3. The catalytic surface can act as an adsorbent of the COD to be oxidised effectively increasing the concentration and hence the rate of oxidation.The simple mechanism shows the selectivity issue with this type of processes. The oxidant can simply be decomposed by the catalyst to oxygen gas – this reaction must be avoided because dioxygen will play no role in COD removal. Its formation is an expensive waste of reagent with oxygen gas ($20/Te) compared to the oxidant ($400–600/Te). To be cost competitive with alternative processes redox catalysis needs excellent selectivity.3.2. Technology mappingThe technologies so far described can be mapped [12] for their applicability with effluent COD concentration (measured as TOC) and effluent flow rate (m3 h-1). The map is shown in Fig. 4. The map outlines the areas where technologies are most effective. The boundaries, although drawn, are in fact fuzzier and should be only used as a guide. Only well into each shape will a technology start to dominate. The underlying cost model behind the map is based on simple assertions – at high COD mass flows only air/oxygen will be able to keep costs down because of the relatively low variable cost of the oxidant. At high COD concentrations and high flows only biological treatment plants have proved themselves viable –of course if done at source recovery becomes an option. At low flows and low COD levels redox AOT catalysis is an important technology – the Synetix Accent 1 process being an example of this type of process (see Fig. 5 for a simplified flowsheet). The catalyst operates under very controlled conditions at pH > 9 and hence metal leaching can be avoided (<5 ppb). The activity and selectivity aspects of the catalyst displayed in Fig. 3 can be further elaborated to look at the potential surface species. This simple view has been extended by a significant amount of research [3,4,5]. Now the mechanism of such a catalyst can be described in Fig. 6. The key step is to avoid recombination of NiO holes to give peroxy species and this can be contrasted with the hydrogen peroxide situation where the step may be characterized as oxygen vacancy filled. From both recombination will be facilitated by electronic and spatial factors. The range of application of the process is outlined below. From laboratory data some general types of chemical have been found suitable –sulphides, amines, alcohols, ketones, aldehydes, phenols, carboxylic acids, olefins and aromatic hydrocarbons. From industrial trials recalcitrant COD (nonbiodegradable) and sulphur compounds have been successfully demonstrated and a plant oxidising sulphur species has been installed and is operational.4. ConclusionsWastewater treatment processes are in the early stages of development. The key parameters at present are effectiveness and long term reliability. Many processes operating are in this stage, including the redox Accent TM is a trademark of the ICIGroup of Companies. catalysis systems. However,once proven, redox catalysis offers many advantages for COD removal from wastewater:1. The low capital cost of installation.2. Simple operation that can be automated.3. Flexible nature of the process – can be easily modified to meet changing demands of legislation.Hence it will be expected to develop into an important technology in wastewater improvement.AcknowledgementsThe author is grateful to Jane Butcher and Keith Kelly of Synetix for discussions on this paper. References[1] R.J. Farrauto, C.H. Bartholomew, Fundamentals of Industrial Catalytic Processes, Blackie Academic and Professional, 1997. F.E. Hancock / Catalysis Today 53 (1999) 3–9 9[2] J.N. Horan, Biological Wastewater Treatment Systems; Theory and Operation, Chichester, Wiley, 1990.[3] F.E. Hancock et al., Catalysis Today 40 (1998) 289.[4] F. King, F.E. Hancock, Catal. Today 27 (1996) 203.[5] J. Hollingworth et al., J. Electron Spectrosc., in press.[6] F. Luck, Environmental Catalysis, in: G. Centi et al. (Eds.), EFCE Publishers, Series 112, p. 125.[7] D. Mantzavinos et al., in: V ogelpohl and Geissen (Eds.), in: Proceedings of the Conference on Water Science and Technology, Clausthal-Zellerfeld, Germany, May 1996, J. Int. Assoc. Water Quality, Pergamon, 1997.[8] R. Venkatadri, R.W. Peters, Hazardous Waste Hazardous Mater. 10 (1993) 107.[9] A.M. Braun, E. Oliveros, Water Sci. Tech. 35 (1997) 17.[10] D. Bahnemann et al., Aquatic and surface photochemistry, Am. Chem. Soc. Symp. Ser. (1994) 261.[11] J. Prousek, Chem. Lisy 89 (1995) 11.工业废水回用的接触反应策略摘要:无论从控制污染还是资源恢复的角度,接触反应都是被广泛应用并极具经济效益的。
污水处理工业废水回用中英文对照外文翻译文献

中英文资料对照外文翻译Catalytic strategies for industrial water re-useAbstractThe use of catalytic processes in pollution abatement and resource recovery is widespread and of significant economic importance [R.J. Farrauto, C.H. Bartholomew, Fundamentals of Industrial Catalytic Processes, Blackie Academic and Professional,1997.]. For water recovery and re-use chemo-catalysis is only just starting to make an impact although bio-catalysis is well established [J.N. Horan, BiologicalWastewater Treatment Systems; Theory and Operation, Chichester, Wiley, 1990.]. This paper will discuss some of the principles behind developing chemo-catalytic processes for water re-use. Within this context oxidative catalytic chemistry has many opportunities to underpin the development of successful processes and many emerging technologies based on this chemistry can be considered .Keywords: COD removal; Catalytic oxidation; Industrial water treatment1.IntroductionIndustrial water re-use in Europe has not yet started on the large scale. However, with potential long term changes in European weather and the need for more water abstraction from boreholes and rivers, the availability of water at low prices will become increasingly rare. As water prices rise there will come a point when technologies that exist now (or are being developed) will make water recycle and re-use a viable commercial operation. As that future approaches, it is worth stating the most important fact about wastewater improvement–avoid it completely if at all possible! It is best to consider water not as a naturally available cheap solvent but rather, difficult to purify, easily contaminated material that if allowed into the environment will permeate all parts of the biosphere. A pollutant is just a material in the wrong place and therefore design your process to keep the material where it should be –contained and safe. Avoidance and then minimisation are the two first steps in looking at any pollutant removal problem. Of course avoidance may not be anoption on an existing plant where any changes may have large consequences for plant items if major flowsheet revision were required. Also avoidance may mean simply transferring the issue from the aqueous phase to the gas phase. There are advantages and disadvantages to both water and gas pollutant abatement. However, it must be remembered that gas phase organic pollutant removal (VOC combustion etc.,) is much more advanced than the equivalent water COD removal and therefore worth consideration [1]. Because these aspects cannot be over-emphasised,a third step would be to visit the first two steps again. Clean-up is expensive, recycle and re-use even if you have a cost effective process is still more capital equipment that will lower your return on assets and make the process less financially attractive. At present the best technology for water recycle is membrane based. This is the only technology that will produce a sufficiently clean permeate for chemical process use. However, the technology cannot be used in isolation and in many (all) cases will require filtration upstream and a technique for handling the downstream retentate containing the pollutants. Thus, hybrid technologies are required that together can handle the all aspects of the water improvement process[6,7,8].Hence the general rules for wastewater improvement are:1. Avoid if possible, consider all possible ways to minimise.2. Keep contaminated streams separate.3. Treat each stream at source for maximum concentration and minimum flow.4. Measure and identify contaminants over complete process cycle. Look for peaks, which will prove costly to manage and attempt to run the process as close to typical values as possible. This paper will consider the industries that are affected by wastewater issues and the technologies that are available to dispose of the retentate which will contain the pollutants from the wastewater effluent. The paper will describe some of the problems to be overcome and how the technologies solve these problems to varying degrees. It will also discuss how the cost driver should influence developers of future technologies.2. The industriesThe process industries that have a significant wastewater effluent are shown in Fig. 1. These process industries can be involved in wastewater treatment in many areas and some illustrations of this are outlined below.Fig. 1. Process industries with wastewater issues.2.1. RefineriesThe process of bringing oil to the refinery will often produce contaminated water. Oil pipelines from offshore rigs are cleaned with water; oil ships ballast with water and the result can be significant water improvement issues.2.2. ChemicalsThe synthesis of intermediate and speciality chemicals often involve the use of a water wash step to remove impurities or wash out residual flammable solvents before drying.2.3. PetrochemicalsEthylene plants need to remove acid gases (CO2, H2S) formed in the manufacture process. This situation can be exacerbated by the need to add sulphur compounds before the pyrolysis stage to improve the process selectivity. Caustic scrubbing is the usual method and this produces a significant water effluent disposal problem.2.4. Pharmaceuticals and agrochemicalsThese industries can have water wash steps in synthesis but in addition they are often formulated with water-based surfactants or wetting agents.2.5. Foods and beveragesClearly use water in processing and COD and BOD issues will be the end result.2.6. Pulp and paperThis industry uses very large quantities of water for processing –aqueous peroxide and enzymes for bleaching in addition to the standard Kraft type processing of the pulp. It is important to realise how much human society contributes to contaminated water and an investigation of the flow rates through municipal treatment plants soon shows the significance of non-process industry derived wastewater.3. The technologiesThe technologies for recalcitrant COD and toxic pollutants in aqueous effluent are shown in Fig. 2. These examples of technologies [2,6,8] available or in development can be categorised according to the general principle underlying the mechanism of action. If in addition the adsorption (absorption) processes are ignored for this catalysis discussion then the categories are:1. Biocatalysis2. Air/oxygen based catalytic (or non-catalytic).3. Chemical oxidation1. Without catalysis using chemical oxidants2. With catalysis using either the generation of _OH or active oxygen transfer. Biocatalysis is an excellent technology for Municipal wastewater treatment providing a very cost-effective route for the removal of organics from water. It is capable of much development via the use of different types of bacteria to increase the overall flexibility of the technology. One issue remains –what to do with all the activated sludge even after mass reduction by de-watering. The quantities involved mean that this is not an easy problem to solve and re-use as a fertilizer can only use so much. The sludge can be toxic via absorption of heavy metals, recalcitrant toxic COD. Inthis case incineration and safe disposal of the ash to acceptable landfill may be required. Air based oxidation [6,7] is very attractive because providing purer grades of oxygen are not required if the oxidant is free. Unfortunately, it is only slightly soluble in water, rather unreactive at low temperatures and, therefore, needs heat and pressure to deliver reasonable rates of reaction. These plants become capital intensive as pressures (from _10 to 100 bar) are used. Therefore, although the running costs maybe low the initial capital outlay on the plant has a very significant effect on the costs of the process. Catalysis improves the rates of reaction and hence lowers the temperature and pressure but is not able to avoid them and hence does not offer a complete solution. The catalysts used are generally Group VIII metals such as cobalt or copper. The leaching of these metals into the aqueous phase is a difficulty that inhibits the general use of heterogeneous catalysts [7]. Chemical oxidation with cheap oxidants has been well practised on integrated chemical plants. The usual example is waste sodium hypochlorite generated in chlor-alkali units that can be utilised to oxidise COD streams from other plants within the complex. Hydrogen peroxide, chlorine dioxide, potassium permanganate are all possible oxidants in this type of process. The choice is primarily determined by which is the cheapest at the point of use. A secondary consideration is how effective is the oxidant. Possibly the most researched catalytic area is the generation and use of _OH as a very active oxidant (advanced oxidation processes) [8]. There are a variety of ways of doing this but the most usual is with photons and a photocatalyst. The photocatalyst is normally TiO2 but other materials with a suitable band gap can be used [9,10]. The processes can be very active however the engineering difficulties of getting light, a catalyst and the effluent efficiently contacted is not easy. In fact the poor efficiency of light usage by the catalyst (either through contacting problems or inherent to the catalyst) make this process only suitable for light from solar sources. Photons derived from electrical power that comes from fossil fuels are not acceptable because the carbon dioxide emission this implies far outweighs and COD abatement. Hydroelectric power (and nuclear power) are possible sources but the basic inefficiency is not being avoided. Hydrogen peroxide and ozone have been used with photocatalysis but they can be used separately or together with catalysts to effect COD oxidation. For ozone there is the problem of the manufacturing route, corona discharge, which is a capital intensive process often limits its application and better route to ozone would be very useful. It is important to note at this point that the oxidants discussed do not have sufficient inherent reactivity to be use without promotion. Thus, catalysis is central to their effective use against both simple organics (often solvents) or complex recalcitrant COD. Hence, the use of Fenton’s catalyst (Fe) for hydrogen peroxide [11]. In terms of catalysis these oxidants together with hypochlorite form a set of materials that can acthas ‘active oxygen transfer (AOT) oxidants’ in the presence of a suitable catalyst. If the AOT oxidant is hypochlorite or hydrogen peroxide then three phase reactions are avoided which greatly simplifies the flowsheet. Cheap, catalytically promoted oxidants with environmentally acceptable products of oxidation that do not require complex chemical engineering and can be produced efficiently would appear to offer one of the best solutions to the general difficulties often observed.3.1. Redox catalysis and active oxygen transferThe mechanism of catalytically promoted oxidation with hydrogen peroxide or sodium hypochlorite cannot be encompassed within one concept, however there are general similarities between the two oxidants that allows one to write a series of reactions for both (Fig. 3) [5]. This type of mechanism could be used to describe a broad range of reactions for either oxidant from catalytic epoxidation to COD oxidation. The inherent usefulness of the reactions is that;1. The reactions take place in a two-phase system.2. High pressure and temperature are not required.3. The catalytic surface can act as an adsorbent of the COD to be oxidised effectively increasing the concentration and hence the rate of oxidation.The simple mechanism shows the selectivity issue with this type of processes. The oxidant can simply be decomposed by the catalyst to oxygen gas – this reaction must be avoided because dioxygen will play no role in COD removal. Its formation is an expensive waste of reagent with oxygen gas ($20/Te) compared to the oxidant ($400–600/Te). To be cost competitive with alternative processes redox catalysis needs excellent selectivity.3.2. Technology mappingThe technologies so far described can be mapped [12] for their applicability with effluent COD concentration (measured as TOC) and effluent flow rate (m3 h-1). The map is shown in Fig. 4. The map outlines the areas where technologies are most effective. The boundaries, although drawn, are in fact fuzzier and should be only used as a guide. Only well into each shape will a technology start to dominate. The underlying cost model behind the map is based on simple assertions – at high COD mass flows only air/oxygen will be able to keep costs down because of the relatively low variable cost of the oxidant. At high COD concentrations and high flows only biological treatment plants have proved themselves viable –of course if done at source recovery becomes an option. At low flows and low COD levels redox AOT catalysis is an important technology – the Synetix Accent 1 process being an example of this type of process (see Fig. 5 for a simplified flowsheet). The catalyst operates under very controlled conditions at pH > 9 and hence metal leaching can be avoided (<5 ppb). The activity and selectivity aspects of the catalyst displayed in Fig. 3 can befurther elaborated to look at the potential surface species. This simple view has been extended by a significant amount of research [3,4,5]. Now the mechanism of such a catalyst can be described in Fig. 6. The key step is to avoid recombination of NiO holes to give peroxy species and this can be contrasted with the hydrogen peroxide situation where the step may be characterized as oxygen vacancy filled. From both recombination will be facilitated by electronic and spatial factors. The range of application of the process is outlined below. From laboratory data some general types of chemical have been found suitable –sulphides, amines, alcohols, ketones, aldehydes, phenols, carboxylic acids, olefins and aromatic hydrocarbons. From industrial trials recalcitrant COD (nonbiodegradable) and sulphur compounds have been successfully demonstrated and a plant oxidising sulphur species has been installed and is operational.4. ConclusionsWastewater treatment processes are in the early stages of development. The key parameters at present are effectiveness and long term reliability. Many processes operating are in this stage, including the redox Accent TM is a trademark of the ICI Group of Companies. catalysis systems. However,once proven, redox catalysis offers many advantages for COD removal from wastewater:1. The low capital cost of installation.2. Simple operation that can be automated.3. Flexible nature of the process – can be easily modified to meet changing demands of legislation.Hence it will be expected to develop into an important technology in wastewater improvement.AcknowledgementsThe author is grateful to Jane Butcher and Keith Kelly of Synetix for discussions on this paper. References[1] R.J. Farrauto, C.H. Bartholomew, Fundamentals of Industrial Catalytic Processes, Blackie Academic and Professional, 1997. F.E. Hancock / Catalysis Today 53 (1999) 3–9 9[2] J.N. Horan, Biological Wastewater Treatment Systems; Theory and Operation, Chichester, Wiley, 1990.[3] F.E. Hancock et al., Catalysis Today 40 (1998) 289.[4] F. King, F.E. Hancock, Catal. Today 27 (1996) 203.[5] J. Hollingworth et al., J. Electron Spectrosc., in press.[6] F. Luck, Environmental Catalysis, in: G. Centi et al. (Eds.), EFCE Publishers, Series 112, p. 125.[7] D. Mantzavinos et al., in: V ogelpohl and Geissen (Eds.), in: Proceedings of the Conference on Water Science and Technology, Clausthal-Zellerfeld, Germany, May 1996, J. Int. Assoc. Water Quality, Pergamon, 1997.[8] R. Venkatadri, R.W. Peters, Hazardous Waste Hazardous Mater. 10 (1993) 107.[9] A.M. Braun, E. Oliveros, Water Sci. Tech. 35 (1997) 17.[10] D. Bahnemann et al., Aquatic and surface photochemistry, Am. Chem. Soc. Symp. Ser. (1994) 261.[11] J. Prousek, Chem. Lisy 89 (1995) 11.工业废水回用的接触反应策略摘要:无论从控制污染还是资源恢复的角度,接触反应都是被广泛应用并极具经济效益的。
污水处理的英文文献翻译(1)
Nutrient removal in an A2O-MBR reactor with sludgereductionABSTRACTIn the present study, an advanced sewage treatment process has been developed by incorporating excess sludge reduction and phosphorous recovery in an A2O-MBR process. The A2O-MBR reactor was operated at a flux of 77 LMH over a period of 270 days. The designed flux was increased stepwise over a period of two weeks. The reactor was operated at two different MLSS range. Thermo chemical digestion of sludge was carried out at a fixed pH (11)and temperature (75℃) for 25% COD solubilisation. The released pbospborous was recovered by precipitation process and the organics was sent back to anoxic tank. The sludge digestion did not have any impact on COD and TP removal efficiency of the reactor. During the 270 days of reactor operation, the MBR maintained relatively constant transmembrane pressure. The results based on the study indicated that the proposed process configuration has potential to reduce the excess sludge production as well as it didn't detonated the treated water quality.Keywords: A2O reactor; MBR; Nutrient removal; TMP1. IntroductionExcess sludge reduction and nutrients removal are the two important problems associated with wastewater treatment plant. MBR process has been known as a process with relatively high decay rate and less sludge production due to much longer sludge age in the reactor (Wenet al., 2004). Sludge production in MBR is reduced by 28-68%, depending on the sludge age used (Xia et al.,2008). However, minimizing the sludge production by increasing sludge age is limited due to the potential adverse effect of high MLSS concentrations on membrane (Yoon et al., 2004). This problem can be solved by introducing sludge disintegration technique in MBR (Young et al., 2007). Sludge disintegration techniques have been reported to enhance the biodegradability of excess sludge (Vlyssides and Karlis, 2004). In overall, the basis for sludge reduction processes is effective combination of the methods for sludge disintegration and biodegradation of treated sludge. Advances in sludge disintegration techniques offer a few promising options including ultrasound (Guo et al., 2008), pulse power (Choi et al.,2006), ozone (Weemaes et al., 2000), thermal (Kim et al., 2003), alkaline (Li et al., 2008) acid (Kim et al., 2003) and thermo chemical(Vlyssides and Karlis, 2004). Among the various disintegration techniques, thermo chemical was reported to be simple and cost effective (Weemaes and Verstraete, 1998). In thermal-chemical hydrolysis, alkali sodium hydroxide was found to be the most effective agent in inducing cell lysis (Rocker et al., 1999). Conventionally, the nutrient removal was carried out in an A2O process. It has advantage of achieving, nutrient removal along with organic compound oxidation in a single sludge configuration using linked reactors in series (Tchobanoglous et al., 2003). The phosphoroes removal happens by subjecting phosphorous accumulating organisms (PAO) bacteria under aerobic and anaerobic conditions (Akin and Ugurlu, 2004). These operating procedures enhance predominance PAO, which are able to uptake phosphorous in excess. During the sludge pretreatment processes the bound phosphorous was solubilised and it increases the phosphorousconcentration in the effluent stream (Nishimura, 2001).So, it is necessary to remove the solubilised phosphorus before it enters into main stream. Besides, there is a growing demand for the sustainable phosphorous resources in the industrialized world. In many developed countries, researches are currently underway to recover the phosphoroes bound in the sludge's of enhanced biological phosphorus removal system (EBPR). The released phosphorous can be recovered in usable products using calcium salts precipitation method. Keeping this fact in mind, in the present study, a new advanced wastewater treatment process is developed by integrating three processes, which are: (a) thermo chemical pretreatment in MBR for excess sludge reduction (b) A2O process for biological nutrient removal (c) P recovery through calcium salt precipitation. The experimental data obtained were then used to evaluate the performance of this integrated system.2. Methods2.1. WastewaterThe synthetic domestic wastewater was used as the experimental influent. It was basically composed of a mixed carbon source, macro nutrients (N and P), an alkalinity control (NaHCO3) and a microelement solution. The composition contained (/L) 210 mg glucose, 200 mg NH4C1, 220 mg NaHCO3, 22一34 mg KH2PO4, microelement solution (0.19 mg MnCl2 4H20, 0.0018 mg ZnCl22H2O,0.022 mg CuCl22H2O, 5.6 mg MgSO47H2O, 0.88 mg FeCl36H2O,1.3 mg CaCl2·2H2O). The synthetic wastewater was prepared three times a week with concentrations of 210±1.5 mg/L chemical oxygen demand (COD), 40±1 mg/L total nitrogen (TN) and 5.5 mg/L total phosphorus (TP).2.2. A2O-MBRThe working volume of the A2O-MBR was 83.4 L. A baffle was placed inside the reactor to divide it into anaerobic (8.4 L) anoxic (25 L) and aerobic basin (50 L). The synthetic wastewater was feed into the reactor at a flow rate of 8.4 L/h (Q) using a feed pump. A liquid level sensor, planted in aerobic basin of A2O-MBR controlled the flow of influent. The HRT of anaerobic, anoxic and aerobic basins were 1, 3 and 6 h, respectively. In order to facilitate nutrient removal, the reactor was provided with two internal recycle (1R). IRl (Q= 1)connects anoxic and anaerobic and IR 2 (Q=3) was between aerobic and anoxic. Anaerobic and anoxic basins were provided with low speed mixer to keep the mixed liquid suspended solids (MLSS) in suspension. In the aerobic zone, diffusers were used to generate air bubbles for oxidation of organics and ammonia. Dissolved oxygen (DO) concentration in the aerobic basin was maintained at 3.5 mg/1 and was monitored continuously through online DO meter. The solid liquid separation happens inaerobic basin with the help of five flat sheet membranes having a pore size of 0.23 pm. The area of each membrane was 0.1 m2. They were connected together by a common tube. A peristaltic pumpwas connected in the common tube to generate suction pressure. In the common tube provision was made to accommodate pressure gauge to measure transmembrane pressure (TMP) during suction. The suction pump was operated in sequence of timing, which consists of 10 min switch on, and 2 min switch off.2.3. Thermo chemical digestion of sludgeMixed liquor from aerobic basin of MBR was withdrawn at the ratio of 1.5% of Q/day and subjected to thermo chemical digestion. Thermo chemical digestion was carried out at a fixed pH of 11(NaOH) and temperature of 75℃for 3 h. After thermo chemical digestion the supernatant and sludge were separated. The thermo-chemicallydigested sludge was amenable to further anaerobic bio-degradation (Vlyssides and Karlis, 2004), so it was sent to theanaerobic basin of the MBR2.4. Phosphorus recoveryLime was used as a precipitant to recover the phosphorous in the supernatant. After the recovery of precipitant the content was sent back to anoxic tank as a carbon source and alkalinity supelement for denitrification.2.5. Chemical analysisCOD, MLSS, TP, TN of the raw and treated wastewater were analyzed following methods detailed in (APHA, 2003). The influent and effluent ammonia concentration was measured using an ion-selective electrode (Thereto Orion, Model: 95一12). Nitrate in the sample was analyzed using cadmium reduction method (APHA, 2003).3. Results and discussionFig. 1 presents data of MLSS and yield observed during the operational period of the reactor. One of the advantages of MBR reactor was it can be operated in high MLSS concentration. The reactor was seeded with EBPR sludge from the Kiheung, sewage treatment plant, Korea. The reactor was startup with the MLSS concentration of 5700 mg/L. It starts to increase steadily with increase in period of reactor operation and reached a value of 8100 mg/L on day 38. From then onwards, MLSS concentration was maintained in the range of 7500 mg/L by withdrawing excess sludge produced and called run I. The observed yields (Yobs) for experiments without sludge digestion (run I) and with sludge digestion were calculated and given in Fig. 1. The Yobs for run I was found to be 0.12 gMLSS/g COD. It was comparatively lower than a value of 0.4 gMLSS/g CODreported for the conventional activated sludge processes (Tchoba-noglous et al., 2003). The difference in observed yield of these two systems is attributed to their working MLSS concentration. At high MLSS concentration the yield observed was found to be low (Visva-nathan et al., 2000). As a result of that MBR generated less sludge.The presently used MLSS ranges (7.5一10.5 g/L) are selected on the basis of the recommendation by Rosenberger et al. (2002). In their study, they reported that the general trend of MLSS increase on fouling in municipal applications seems to result in no impact at medium MLSS concentrations (7一12 g/L).It is evident from the data that the COD removal efficiency of A2O system remains unaffected before and after the introduction of sludge digestion practices. A test analysis showed that the differences between the period without sludge digestion (run I) and with sludge digestion (run II and III) are not statistically significant.However, it has been reported that, in wastewater treatment processes including disintegration-induced sludge degradation, the effluent water quality is slightly detonated due to the release of nondegradable substances such as soluble microbial products (Ya-sui and Shibata, 1994; Salcai et al., 1997; Yoon et al., 2004). During the study period, COD concentration in the aerobic basin of MBR was in the range of 18-38 mg/L and corresponding organic concentration in the effluent was varied from 4 to 12 mg/L. From this data it can be concluded that the membrane separation played an important role in providing the excellent and stable effluent quality.Phosphorus is the primary nutrient responsible for algal bloom and it is necessary to reduce the concentration of phosphorus in treated wastewater to prevent the algal bloom. Fortunately its growth can be inhibited at the levels of TP well below 1 mg/L (Mer-vat and Logan, 1996).Fig. 2 depicts TP removal efficiency of the A2O-MBR system during the period of study. It is clearly evident from the figure that the TP removal efficiency of A/O system was remains unaffected after the introduction of sludge reduction. In the present study, the solubilised phosphorous was recovered in the form of calcium phosphate before it enters into main stream. So, the possibility of phosphorus increase in the effluent due to sludge reduction practices has been eliminated. The influent TP concentration was in the range of 5.5 mg/L. During thefirst four weeks of operation the TP removal efficiency of the system was not efficient as the TP concentration in the effluent exceeds over 2.5 mg/L. The lower TP removal efficiency during the initial period was due to the slow growing nature of PAO organisms and other operational factors such as anaerobic condition and internal recycling. After the initial period, the TP removal efficiency in the effluent starts to increase with increase in period of operation. TP removal in A2O process is mainly through PAO organisms. These organisms are slow growing in nature and susceptible to various physicochemical factors (Carlos et al., 2008). During the study period TP removal efficiency of the system remains unaffected and was in the range of 74-82%.。
污水处理 英文文献3 翻译
丹宁改性絮凝剂处理城市污水J.Beltrán-heredia,J.ánche z-Martin埃斯特雷马杜拉大学化学工程系和物理化学系,德埃娃儿,S / N 06071,巴达霍斯,西班牙摘要一种新的以丹宁为主要成分的混凝剂和絮凝剂已经过测试用以处理城市污水。
TANFLOC 证实了其在浊度的去除上的高效性(接近100%,取决于剂量),并且近50%的BOD5和COD 被去除,表明TANFLOC是合适的凝集剂,效力可与明矾相媲美。
混凝絮凝剂过程不依赖于温度,发现最佳搅拌速度和时间为40转/每分钟和30分钟。
多酚含量不显著增加,30%的阴离子表面活性剂被去除。
沉淀过程似乎是一种絮凝分离,所以污泥体积指数和它随絮凝剂剂量的改变可以确定。
证明TANFLOC是相当有效的可用于污水处理的混凝絮凝剂。
关键词: 基于丹宁的絮凝剂城市污水絮凝天然混凝剂1.简介人类活动是废物的来源。
特别是在城市定居点,来自家庭和工业的废水可能是危险有害的产品[ 1 ],需要适当的处理,以避免对环境[ 2 ]和健康的影响[ 3,4 ]。
2006年12月4日联合国大会通过决议宣布2008为国际卫生年。
无效的卫生基础设施促使每年220万人死于腹泻,主要在3岁以下儿童,600万人因沙眼失明,两亿人感染血吸虫病,只是为了给出一些数据[ 5 ]。
显然,他们中的大多数都是在发展中国家,所以谈及城市污水,必须研究适当的技术来拓宽可能的处理技术种类。
在这个意义上,许多类型的水处理被使用。
他们之间的分歧在于经济和技术特点上。
了摆脱危险的污染[ 6 ],一些令人关注的论文已经发表的关于城市污水处理的几种天然的替代方法,包括绿色过滤器、化学初步分离、紫外消毒[ 7 ]和多级程序[ 8 ]。
几个以前的文件指出了城市污水管理[9,10]的重要性。
这种类型的废物已成为社会研究的目标,因为它涉及到几个方面,都与社会结构和社会组织[11 ]相关。
根据这一维度,必须认识到废水管理作为发展中国家的一种社会变化的因素,事关污水处理和生产之间的平衡,是非常重要的,一方面,人类要发展,另一方面,显而易见。
污水处理外文翻译---污水的生物处理过程
污水处理外文翻译---污水的生物处理过程XXX to a level where the discharge of effluent will not harm the XXX only needs to be to a required level。
The degree andtype of treatment for a specific XXX。
The degree of treatment often depends on the XXX so that the DO of the receiving water is not depressed too far。
The amount of BOD that must be XXX.XXX。
let's assume a "XXX: BOD ≤ 15mg/L。
SS ≤ 15mg/L。
and P ≤ 1mg/L.XXX-XXX。
Secondary treatment。
on the other hand。
is a logical process that XXX。
Finally。
XXX of physical。
logical。
and chemical XXX。
While there could have been nal effluent standards established。
we will focus on these three for XXX.The third step in XXX grit and sand。
These substances can cause damage to equipment such as pumps and flow meters。
so itis crucial to remove them。
The most common method for removing grit is through a grit chamber。
关于污水处理的英语作文
关于污水处理的英语作文英文回答:Importance of Wastewater Treatment in Protecting Environmental and Human Health.Wastewater treatment plays a pivotal role in safeguarding both environmental and human well-being. Untreated or inadequately treated wastewater can pose significant threats to human health and the environment, leading to water contamination, disease outbreaks, and ecological degradation.Water Contamination: Wastewater contains a complex mixture of pollutants, including pathogenic microorganisms, organic matter, and toxic chemicals. When released into water bodies, these pollutants can contaminate drinking water sources, making them unsafe for human consumption and leading to waterborne diseases such as cholera, typhoid, and gastroenteritis.Disease Outbreaks: Untreated wastewater can create breeding grounds for disease-carrying organisms such as bacteria, viruses, and parasites. These organisms can transmit diseases to humans through direct contact with contaminated water or indirect exposure via contaminated food or drinking water.Ecological Degradation: Wastewater discharge can disrupt aquatic ecosystems by altering water chemistry, increasing nutrient levels, and introducing harmful pollutants. This can lead to eutrophication, resulting in algal blooms, loss of biodiversity, and declines in fisheries.Economic Impacts: The consequences of wastewater contamination extend beyond health and environmental concerns. It can also have significant economic impacts. Contaminated water supplies can lead to costly treatment and purification efforts, and can also reduce tourism and recreational activities that rely on clean water.Benefits of Wastewater Treatment:Wastewater treatment plays a crucial role in mitigating these risks and ensuring the safety and sustainability of our water resources. By removing pollutants from wastewater, treatment plants help to protect public health, the environment, and the economy.Public Health Protection: Wastewater treatment plants use a combination of physical, chemical, and biological processes to remove contaminants from wastewater. These processes effectively reduce the presence of pathogens, organic matter, and toxic chemicals, making the treated water safe for discharge into water bodies or reuse in irrigation or industrial applications.Environmental Protection: Wastewater treatment helps to preserve the integrity of aquatic ecosystems by reducing nutrient pollution and the discharge of harmful chemicals. This prevents eutrophication, supports biodiversity, and ensures the continued productivity of fisheries.Water Resource Conservation: By treating wastewater to a level suitable for reuse or discharge, wastewater treatment plants conserve valuable water resources. This is particularly important in arid or semi-arid regions where water availability is scarce.Challenges and Innovations:Despite the significant benefits of wastewater treatment, there are also challenges that need to be addressed. These include:Energy Consumption: Wastewater treatment processes can be energy-intensive, especially when using conventional technologies. Innovations in energy-efficient technologies are crucial to minimize the environmental footprint of treatment plants.Emerging Contaminants: Over time, new emerging contaminants such as pharmaceuticals and microplastics have been detected in wastewater streams. These compounds can pose unique challenges for traditional treatment methods,requiring research and development of innovative removal strategies.Climate Change: Climate change is expected to affect wastewater treatment infrastructure, particularly incoastal areas vulnerable to sea level rise and storm surges. Adaptation measures are necessary to ensure the resilienceof treatment plants in the face of changing climate conditions.Conclusion:Wastewater treatment is a vital process for protecting environmental and human health, ensuring the safety of our water resources, and supporting economic development. By investing in wastewater treatment infrastructure and continuing to innovate in more efficient and sustainable technologies, societies can mitigate the risks associated with untreated wastewater and create a healthier and more sustainable future.中文回答:污水处理在保护环境和人类健康中的重要性。