橡胶加工图文全过程
橡胶加工工艺流程
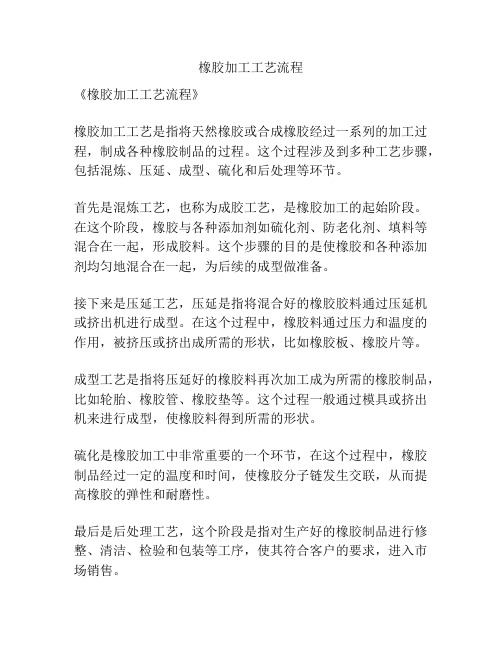
橡胶加工工艺流程
《橡胶加工工艺流程》
橡胶加工工艺是指将天然橡胶或合成橡胶经过一系列的加工过程,制成各种橡胶制品的过程。
这个过程涉及到多种工艺步骤,包括混炼、压延、成型、硫化和后处理等环节。
首先是混炼工艺,也称为成胶工艺,是橡胶加工的起始阶段。
在这个阶段,橡胶与各种添加剂如硫化剂、防老化剂、填料等混合在一起,形成胶料。
这个步骤的目的是使橡胶和各种添加剂均匀地混合在一起,为后续的成型做准备。
接下来是压延工艺,压延是指将混合好的橡胶胶料通过压延机或挤出机进行成型。
在这个过程中,橡胶料通过压力和温度的作用,被挤压或挤出成所需的形状,比如橡胶板、橡胶片等。
成型工艺是指将压延好的橡胶料再次加工成为所需的橡胶制品,比如轮胎、橡胶管、橡胶垫等。
这个过程一般通过模具或挤出机来进行成型,使橡胶料得到所需的形状。
硫化是橡胶加工中非常重要的一个环节,在这个过程中,橡胶制品经过一定的温度和时间,使橡胶分子链发生交联,从而提高橡胶的弹性和耐磨性。
最后是后处理工艺,这个阶段是指对生产好的橡胶制品进行修整、清洁、检验和包装等工序,使其符合客户的要求,进入市场销售。
总体来说,橡胶加工工艺流程是一个复杂而又精细的过程,需要经过多个工艺步骤才能最终制成高质量的橡胶制品。
只有严格执行每一个工艺步骤,才能保证生产出优质的橡胶制品,满足客户的需求。
橡胶的工艺流程

橡胶的工艺流程(精品)2014—10—22橡胶技术网橡胶工艺流程开始1 综述橡胶制品的主要原料是生胶、各种配合剂、以及作为骨架材料的纤维和金属材料,橡胶制品的基本生产工艺过程包括塑炼、混炼、压延、压出、成型、硫化6个基本工序.橡胶的加工工艺过程主要是解决塑性和弹性矛盾的过程,通过各种加工手段,使得弹性的橡胶变成具有塑性的塑炼胶,在加入各种配合剂制成半成品,然后通过硫化是具有塑性的半成品又变成弹性高、物理机械性能好的橡胶制品。
2 橡胶加工工艺2.1塑炼工艺生胶塑炼是通过机械应力、热、氧或加入某些化学试剂等方法,使生胶由强韧的弹性状态转变为柔软、便于加工的塑性状态的过程.生胶塑炼的目的是降低它的弹性,增加可塑性,并获得适当的流动性,以满足混炼、亚衍、压出、成型、硫化以及胶浆制造、海绵胶制造等各种加工工艺过程的要求.掌握好适当的塑炼可塑度,对橡胶制品的加工和成品质量是至关重要的。
在满足加工工艺要求的前提下应尽可能降低可塑度。
随着恒粘度橡胶、低粘度橡胶的出现,有的橡胶已经不需要塑炼而直接进行混炼。
在橡胶工业中,最常用的塑炼方法有机械塑炼法和化学塑炼法。
机械塑炼法所用的主要设备是开放式炼胶机、密闭式炼胶机和螺杆塑炼机。
化学塑炼法是在机械塑炼过程中加入化学药品来提高塑炼效果的方法.开炼机塑炼时温度一般在80℃以下,属于低温机械混炼方法.密炼机和螺杆混炼机的排胶温度在120℃以上,甚至高达160-180℃,属于高温机械混炼。
生胶在混炼之前需要预先经过烘胶、切胶、选胶和破胶等处理才能塑炼.几种胶的塑炼特性:天然橡胶用开炼机塑炼时,辊筒温度为30—40℃,时间约为15—20min;采用密炼机塑炼当温度达到120℃以上时,时间约为3-5min。
丁苯橡胶的门尼粘度多在35—60之间,因此,丁苯橡胶也可不用塑炼,但是经过塑炼后可以提高配合机的分散性顺丁橡胶具有冷流性,缺乏塑炼效果。
顺丁胶的门尼粘度较低,可不用塑炼.氯丁橡胶得塑性大,塑炼前可薄通3-5次,薄通温度在30-40℃。
橡胶产品生产工艺流程

橡胶产品生产工艺流程
橡胶产品的生产工艺流程包括橡胶原料的准备、混炼、造型、硫化、整形和检测等几个主要步骤。
首先是橡胶原料的准备。
橡胶原料一般包括天然橡胶和合成橡胶。
天然橡胶是从橡胶树中取得的橡胶乳,合成橡胶则是通过化学合成的方式制得。
将橡胶原料根据所需成品的性质、用途和制造方法选择合适的橡胶种类,并进行称量和破碎处理。
接下来是混炼。
将橡胶原料加入混炼机中进行混炼。
混炼的目的是将橡胶原料中的各种添加剂和助剂充分分散均匀,使其具有良好的加工性能和物理性能。
然后是造型。
将混炼好的橡胶料送入造型机中,通过模具的加工和挤压,将橡胶形成所需的产品形状。
制造橡胶制品的方法有很多种,如压制、挤出、注塑、涂覆等。
接下来是硫化。
将造型好的橡胶制品放入硫化炉中进行硫化处理。
硫化是将橡胶中的硫元素和硫化剂在高温下发生化学反应,使橡胶中的链结成弹性体的工艺,使橡胶制品具有弹性和耐久性。
然后是整形。
硫化后的橡胶制品需要进行裁剪、修整、打磨等整形工艺,使其外观完美和尺寸标准。
最后是检测。
对橡胶制品进行质量检验,通过检测其物理性能、化学性能、外观等,判断产品是否符合要求。
总而言之,橡胶产品的生产工艺流程主要包括橡胶原料的准备、混炼、造型、硫化、整形和检测等几个主要步骤。
不同类型的橡胶制品可能会有些差异,但总体来说,这个流程较为基本和普遍。
通过这些工艺步骤,能够确保橡胶制品的质量和性能。
橡胶生产工艺流程图

橡胶生产工艺流程图橡胶生产工艺流程图橡胶生产是一个复杂的工艺,涉及到多个步骤和设备。
下面是一个简化的橡胶生产工艺流程图,总共分为六个主要步骤。
步骤一:选择原料橡胶生产的第一步是选择适合制作橡胶产品的原料。
橡胶的主要原料来自于橡胶树的乳液或合成橡胶。
原料选择的好坏直接影响到产品的质量和性能。
步骤二:研磨和混合选好原料之后,需要进行研磨和混合。
这个步骤的目的是将原料研磨成颗粒状,并加入适量的添加剂进行混合。
添加剂可以提供橡胶产品所需要的特殊性能,如耐磨性、耐氧化性等。
步骤三:成型成型是橡胶生产的关键步骤之一。
这个步骤通常使用挤出机、压延机或注塑机进行。
通过将混合物经过加热和加压的处理,使其变得具有可塑性,然后通过模具将其成型成所需的形状,如板材、管材、密封件等。
步骤四:硫化硫化是橡胶生产的另一个关键步骤。
硫化的目的是使橡胶产品具有更好的弹性和耐用性。
硫化过程中,橡胶制品被加热至一定温度,并加入硫化剂。
硫化剂与橡胶反应,形成交联结构,改变橡胶分子链的排列方式,使橡胶产品具有更好的弹性和耐用性。
步骤五:修饰修饰是橡胶生产的后续加工步骤。
这个步骤的目的是对硫化后的橡胶制品进行后续的加工和修饰,以提高产品的外观和性能。
这包括修边、抛光、喷涂和涂覆等工艺。
步骤六:质检和包装最后一步是对成品进行质检和包装。
通过对成品进行检验,确保产品符合相关质量标准和规定。
合格的产品会经过包装,以确保产品在运输和储存过程中不受损坏。
橡胶生产工艺是一个多步骤、多设备的过程。
每个步骤都起着重要的作用,影响着最终产品的质量和性能。
在生产过程中,需要严格控制每一个步骤的参数,确保产品的一致性和稳定性。
只有通过科学合理的工艺流程,才能生产出优质的橡胶制品。
橡胶加工操作规程
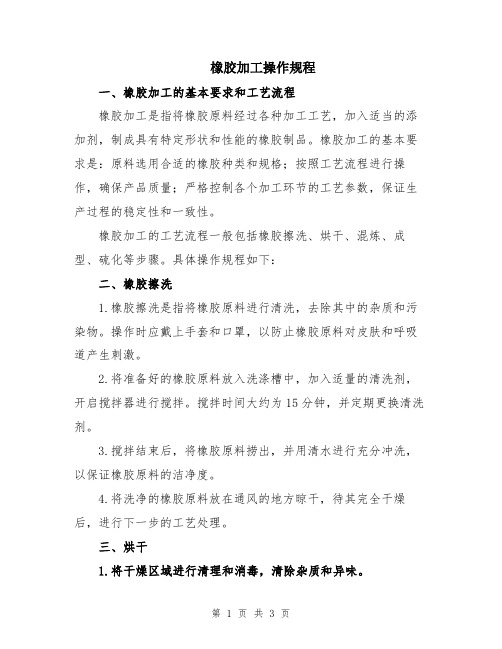
橡胶加工操作规程一、橡胶加工的基本要求和工艺流程橡胶加工是指将橡胶原料经过各种加工工艺,加入适当的添加剂,制成具有特定形状和性能的橡胶制品。
橡胶加工的基本要求是:原料选用合适的橡胶种类和规格;按照工艺流程进行操作,确保产品质量;严格控制各个加工环节的工艺参数,保证生产过程的稳定性和一致性。
橡胶加工的工艺流程一般包括橡胶擦洗、烘干、混炼、成型、硫化等步骤。
具体操作规程如下:二、橡胶擦洗1.橡胶擦洗是指将橡胶原料进行清洗,去除其中的杂质和污染物。
操作时应戴上手套和口罩,以防止橡胶原料对皮肤和呼吸道产生刺激。
2.将准备好的橡胶原料放入洗涤槽中,加入适量的清洗剂,开启搅拌器进行搅拌。
搅拌时间大约为15分钟,并定期更换清洗剂。
3.搅拌结束后,将橡胶原料捞出,并用清水进行充分冲洗,以保证橡胶原料的洁净度。
4.将洗净的橡胶原料放在通风的地方晾干,待其完全干燥后,进行下一步的工艺处理。
三、烘干1.将干燥区域进行清理和消毒,清除杂质和异味。
2.将晾干的橡胶原料放入烘干机中,设置合适的温度和时间进行烘干。
烘干温度一般控制在60-70摄氏度,烘干时间根据橡胶原料的含水量而定,一般为2-4小时。
3.烘干过程中,要定期检查烘干机的温度和风扇的工作状态,确保烘干效果良好。
4.烘干结束后,将烘干的橡胶原料放在凉爽干燥的地方,待其完全冷却后,进行下一步的工艺处理。
四、混炼1.将干燥的橡胶原料放入混炼机中,加入适量的添加剂,如硫化剂、填充剂等。
2.按照橡胶混炼的工艺要求,设置混炼机的温度、旋转速度和混炼时间。
一般来说,混炼温度控制在100-150摄氏度,混炼时间根据橡胶种类和混炼机的规格而定,一般为15-30分钟。
3.混炼过程中,要注意混炼机的工作状态,及时调整温度和旋转速度,保证橡胶原料和添加剂充分混合。
4.混炼结束后,将混炼好的橡胶料放在通风的地方静置,待其自然冷却后,进行下一步的工艺处理。
五、成型1.先将混炼好的橡胶原料切割成合适的大小,放入成型机中。
橡胶制品生产工艺流程

橡胶制品生产工艺流程一、橡胶制品基本工艺流程伴随现代工业尤其是化学工业的迅猛发展,橡胶制品种类繁多,但其生产工艺过程,却基本相同。
以一般固体橡胶 ( 生胶 ) 为原料的制品,它的生产工艺过程主要包括:原材料准备→塑炼→混炼→成型→硫化→休整→检验二、橡胶制品原材料准备橡胶制品的主要材料有生胶、配合剂、纤维材料和金属材料。
其中生胶为基本材料 ; 配合剂是为了改善橡胶制品的某些性能而加入的辅助材料 ; 纤维材料 ( 棉、麻、毛及各种人造纤维、合成纤维 ) 和金属材料 ( 钢丝、铜丝 ) 是作为橡胶制品的骨架材料,以增强机械强度、限制制品变型。
在原材料准备过程中,配料必须按照配方称量准确。
为了使生胶和配合剂能相互均匀混合,需要对某些材料进行加工:生胶要切胶、破胶成小块 ;块状配合剂如石蜡、硬脂酸、松香等要粉碎 ;粉状配合剂若含有机械杂质或粗粒时需要筛选除去 ;液态配合剂 ( 松焦油、古马隆 ) 需要加热、熔化、蒸发水分、过滤杂质;配合剂要进行干燥,不然容易结块、混炼时旧不能分散均匀,硫化时产生气泡,从而影响产品质量;三、橡胶制品的塑炼生胶富有弹性,缺乏加工时的必需性能 ( 可塑性 ) ,因此不便于加工。
为了提高其可塑性,所以要对生胶进行塑炼 ; 这样,在混炼时配合剂就容易均匀分散在生胶中 ; 同时,在压延、成型过程中也有助于提高胶料的渗透性 ( 渗入纤维织品内 ) 和成型流动性。
将生胶的长链分子降解,形成可塑性的过程叫做塑炼。
生胶塑炼的方法有机械塑炼和热塑炼两种。
机械塑炼是在不太高的温度下,通过塑炼机的机械挤压和摩擦力的作用,使长链橡胶分子降解变短,由高弹性状态转变为可塑状态。
热塑炼是向生胶中通入灼热的压缩空气,在热和氧的作用下,使长链分子降解变短,从而获得可塑性。
四、橡胶制品的混炼为了适应各种不同的使用条件、获得各种不同的性能,也为了提高橡胶制品的性能和降低成本,必须在生胶中加入不同的配合剂。
混炼就是将塑炼后的生胶与配合剂混合、放在炼胶机中,通过机械拌合作用,使配合剂完全、均匀地分散在生胶中的一种过程。
橡胶加工工艺
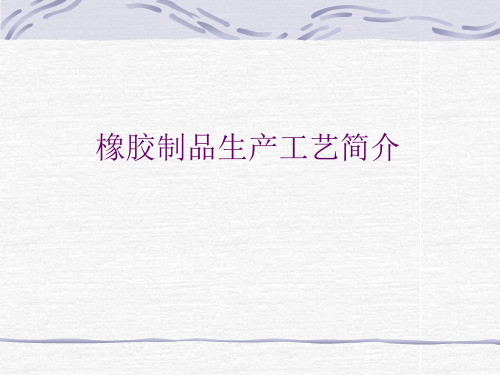
➢ 化学塑解剂:塑解剂的用量,在NR中一般为生胶重量的0.1~0.3%,合 成橡胶则应增大到2~3%。
橡胶制品生产工艺简介-塑炼工艺塑炼工艺
不同胶料开炼机混炼时辊筒温度
胶种
天然胶 丁苯胶 氯丁胶 丁基胶 丁腈胶 顺丁胶 三元乙丙胶 氯磺化聚乙烯 氟橡胶23—27 丙烯酸酯橡胶
橡胶制品生产工艺简介-塑炼工艺塑炼工艺
常用橡胶的塑炼特性
2. SBR ➢ 软SBR的初始门尼粘度一般在54~64之间,不需进行塑炼。 ➢ SBR采用机械塑炼效果不大,比较有效的方法时采用高温
塑炼法,以130~140℃温度最好,温度过高易生成凝胶。 3.BR ➢ BR一般不需要进行塑炼。 4.CR ➢ CR的初始门尼粘度都较低,一般不需要进行塑炼。但在储
➢ 物料在密炼室中主要受到几种作用: 转子间及转子与混炼室内壁间的作用;
转子棱间的搅拌作用;
转子轴向的往复切割作用。
➢ 优点:自动化程度高,生产效率高,节能,劳动强度低
➢ 缺点:温度高,冷却困难,易过炼,出料为无定形状
橡胶制品生产工艺简介-塑炼工艺塑炼工艺
密炼机
橡胶制品生产工艺简介-塑炼工艺塑炼工艺
存过程中其可塑性会下降,因此CR仍需经过塑炼加工,才 能获得所要求的可塑性。 ➢ CR宜采用开炼机进行塑炼,低温薄通塑炼效果最好。
橡胶制品生产工艺简介-塑炼工艺塑炼工艺
常用橡胶的塑炼特性
5.IIR ➢ 门尼粘度在38~75之间的品种一般不需要塑炼。 ➢ IIR采用机械塑炼效果不大,但用密炼机在120℃以上,并
且加入塑解剂进行高温塑炼则可取得较好的塑炼效果。 6.NBR ➢ NBR的塑炼应采用开炼机在低温(40℃以下)、小辊距
橡胶加工工艺介绍PPT课件

1.1.2.4 螺杆机塑炼
• 影响塑炼效果的主要因素是塑炼温度、填胶
速度和生胶温度等。
• (1)塑炼温度
• (2)填胶速度
• (3)生胶温度
1.2 混炼
• 1.2.1 混炼的基本理论
• 1.2.2 混炼方法
• (1)混炼胶是由粒状配合剂分散于生胶中组
成的分散体系,具有胶态分散体系的若干重要 特征。
• (2)配合剂分散在橡胶中,当其每一颗粒完
全被橡胶包围和湿润,方可获得最佳的混炼效 果。
• ()配合剂的表面性质影响橡胶对配合剂的
湿润。
• (4)当混炼时,橡胶分子会结合到活性填料
粒子表面上,成为不溶于橡胶溶液的结合橡胶。
• 1.2.2.2.1 开炼机混炼的影响因素
(1)辊筒的转速和速比 (2)辊距 (3)辊温 (4)混炼时间 (5)容量和堆积胶量 (6)配合剂添加量 (7)加药顺序
1.2.2.3 密炼机混炼
• 1.2.2.3.1 密炼机混炼操作方法
(1)一段混炼法 (2)分段混炼法 (3)逆顺序加料混炼法
1.2.2.3.2 密炼机混炼的影响因素
生胶的可塑性与其分子量有密切的关系。 分子量越小,橡胶的粘度就越低,可塑性也越 大。生胶在塑炼过程中,可塑性的提高是通过 分子量的降低来实现的。
温度对塑炼效果有重要的影响,在不同的 温度范围内,温度对塑炼的作用具有双重性。 低温塑炼,以机械力破坏作用为主;高温塑炼, 则以热氧化为主。
静电是由于橡胶受到强烈的机械捏炼和反 复变形而产生的。静电的作用会使空气中的氧 活化,而促使橡胶分子氧化断键。
• (2)塑炼方法
- 1、下载文档前请自行甄别文档内容的完整性,平台不提供额外的编辑、内容补充、找答案等附加服务。
- 2、"仅部分预览"的文档,不可在线预览部分如存在完整性等问题,可反馈申请退款(可完整预览的文档不适用该条件!)。
- 3、如文档侵犯您的权益,请联系客服反馈,我们会尽快为您处理(人工客服工作时间:9:00-18:30)。
橡胶加工图文全过程Newly compiled on November 23, 2020
橡胶加工图文全过程
1.割胶:
胶乳贮藏在树皮韧皮部的乳管里,把树皮割开,牛奶般的胶乳靠着乳管本身及其周围薄细胞的膨压作用,就会不断地流出来。
割胶一般是凌晨4点左右,这个时候温度比较低,胶树体内水分饱满,细胞的膨压作用是一天中最大的,它排胶就比较流畅,因此清晨割胶产量高。
2.收胶:
不同季节、不同品种,排胶时间的长短有很大差异,当绝大部分胶树已经断滴时便可收胶,必须在太阳升出来前完成收胶工作。
收集碗内的鲜胶乳后树上留下的胶线及胶杯中剩余的凝胶。
它一般可制成l0号、20号标准橡胶,薄褐绉胶片,混合绉胶片和充油橡胶等产品。
3.胶乳净化:
胶乳净化是通过过滤、离心分离(如图)、自然沉降等方法除去胶乳中的杂质。
橡胶中的杂质,会使橡胶制品的性能降低。
如不耐撕裂、不耐磨耗、生热高、轮胎脱层等。
对于标准胶来说,杂质含量是一项主要的指标。
因此,胶乳净化是确保提高橡胶质量的关键措施。
4.胶乳凝固:
在凝固槽中导入净化后的胶乳加酸凝固。
这种加酸凝固工艺目前使用较为普遍,是影响质量的重要环节之一。
胶乳的凝固方法、凝固浓度、凝块熟化时间等会影响制得橡胶的塑性保持率。
橡胶可塑性对橡胶制品生产的工艺操作有着重要意义。
5.压薄、压绉:
把凝固的胶乳通过机械滚压,脱水变为较薄,厚度一致的凝块。
这增加了胶片的表面积,缩短干燥时间。
同时使胶料的强度增加和得到初步造型的目的,有利于保证胶料进一步加工的质量,提高生产效率。
6.造粒:
胶料经锤磨机造粒,所得粒子形状不规则,有孔隙,表面粗糙,使得胶料的后续过程干燥、包装等操作条件得到改善。
通过造粒,使胶料物理性能和堆积比重得到较大提高。
节约运输、储存、包装空间,使加工后橡胶的商品价值和市场竞争力得到提升。
7.干燥:
把湿颗粒胶装入干燥车进行烘干。
颗粒胶加工时的干燥程度会影响制成标准胶的挥发含量。
当橡胶中的挥发物含量越低,在贮存过程中越难长霉,在生产中的应用性也越强,在制品加工过程中焦烧危险性越小,塑炼效果越好,因此容易生产出质量高的橡胶制品。
8.出胶称重:
如果烘好的颗粒胶温度仍很高,出胶时要等热量消散到规定温度才能及时称重包装。
这样橡胶就不容易吸湿返潮造成长霉,有利于长期保存,提高橡胶的使用性能。
目前国内全乳胶的净重为或40kg。
9.压包:
把规定重量的颗粒胶放入打包机加压,颗粒胶会从松散的状态变成一定规格,外形方正的紧密橡胶。
压包结实的橡胶可以更好的运输,堆放及储存。
10.打包:
胶包用聚乙烯薄膜袋和聚丙烯编织袋双层包装,这样有利于保持橡胶的清洁,干燥,防止运输和储存过程中受外来杂质的污染,以及防止橡胶在堆放时互相粘结和沾染灰尘。
11.堆放入库:
胶包的贮存要分种类和级别堆放,堆放高度为4-6层,堆长不限,要求通风良好、干燥、清洁、不漏雨,以免导致橡胶发霉变质。
堆放橡胶的仓库要严禁烟火,周围附近不要存放易燃物品。