橡胶类产品母料加工工艺
橡胶产品的工艺流程

橡胶产品的工艺流程
《橡胶产品的工艺流程》
橡胶产品是一种常见的工业原料,广泛应用于汽车、电子、建筑等各个领域。
而橡胶制品的生产过程则包括以下几个关键的工艺流程。
首先是原料的准备。
橡胶制品生产的原料主要包括天然橡胶和合成橡胶。
而原料的准备主要包括混炼、粉碎和过筛等工艺。
在混炼的过程中,将橡胶和其他添加剂进行混合,以确保橡胶的成形性能。
接下来是成型工艺。
成型工艺主要包括挤出、压延和压制等。
在挤出工艺中,橡胶混炼胶料被挤压成具有一定截面形状的半成品。
而在压制工艺中,则是通过模具将橡胶混炼胶料进行成型。
然后是硫化工艺。
硫化是橡胶产品生产中的重要工艺环节。
传统的硫化工艺主要包括热硫化和冷硫化两种方式。
在硫化的过程中,通过加热或加压等方式,使橡胶材料的分子链发生交联,从而提高其物理性能。
最后是检验和包装。
在橡胶产品的生产流程中,检验和包装是至关重要的环节。
通过对成品进行质量检验,可以确保产品的质量合格,并进行相应的包装和标识,以便于运输和销售。
总的来说,橡胶产品的生产过程是一个复杂而严谨的工艺流程。
只有严格控制每一个细节,才能保证生产出质量上乘的橡胶制品。
橡胶产品生产工艺流程

橡胶产品生产工艺流程
橡胶产品的生产工艺流程包括橡胶原料的准备、混炼、造型、硫化、整形和检测等几个主要步骤。
首先是橡胶原料的准备。
橡胶原料一般包括天然橡胶和合成橡胶。
天然橡胶是从橡胶树中取得的橡胶乳,合成橡胶则是通过化学合成的方式制得。
将橡胶原料根据所需成品的性质、用途和制造方法选择合适的橡胶种类,并进行称量和破碎处理。
接下来是混炼。
将橡胶原料加入混炼机中进行混炼。
混炼的目的是将橡胶原料中的各种添加剂和助剂充分分散均匀,使其具有良好的加工性能和物理性能。
然后是造型。
将混炼好的橡胶料送入造型机中,通过模具的加工和挤压,将橡胶形成所需的产品形状。
制造橡胶制品的方法有很多种,如压制、挤出、注塑、涂覆等。
接下来是硫化。
将造型好的橡胶制品放入硫化炉中进行硫化处理。
硫化是将橡胶中的硫元素和硫化剂在高温下发生化学反应,使橡胶中的链结成弹性体的工艺,使橡胶制品具有弹性和耐久性。
然后是整形。
硫化后的橡胶制品需要进行裁剪、修整、打磨等整形工艺,使其外观完美和尺寸标准。
最后是检测。
对橡胶制品进行质量检验,通过检测其物理性能、化学性能、外观等,判断产品是否符合要求。
总而言之,橡胶产品的生产工艺流程主要包括橡胶原料的准备、混炼、造型、硫化、整形和检测等几个主要步骤。
不同类型的橡胶制品可能会有些差异,但总体来说,这个流程较为基本和普遍。
通过这些工艺步骤,能够确保橡胶制品的质量和性能。
橡胶产品的工艺流程
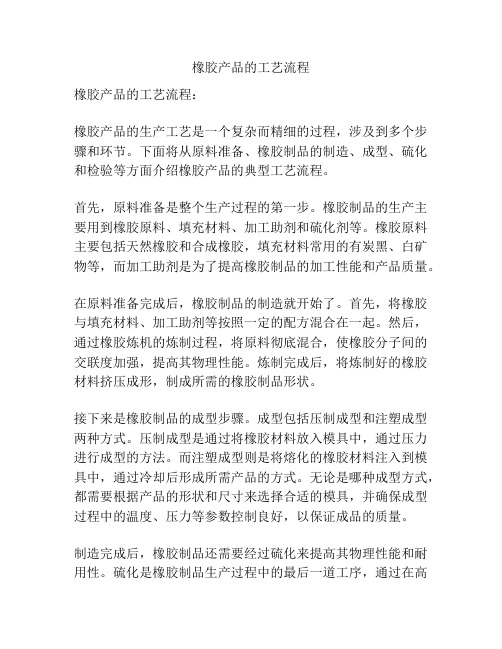
橡胶产品的工艺流程橡胶产品的工艺流程:橡胶产品的生产工艺是一个复杂而精细的过程,涉及到多个步骤和环节。
下面将从原料准备、橡胶制品的制造、成型、硫化和检验等方面介绍橡胶产品的典型工艺流程。
首先,原料准备是整个生产过程的第一步。
橡胶制品的生产主要用到橡胶原料、填充材料、加工助剂和硫化剂等。
橡胶原料主要包括天然橡胶和合成橡胶,填充材料常用的有炭黑、白矿物等,而加工助剂是为了提高橡胶制品的加工性能和产品质量。
在原料准备完成后,橡胶制品的制造就开始了。
首先,将橡胶与填充材料、加工助剂等按照一定的配方混合在一起。
然后,通过橡胶炼机的炼制过程,将原料彻底混合,使橡胶分子间的交联度加强,提高其物理性能。
炼制完成后,将炼制好的橡胶材料挤压成形,制成所需的橡胶制品形状。
接下来是橡胶制品的成型步骤。
成型包括压制成型和注塑成型两种方式。
压制成型是通过将橡胶材料放入模具中,通过压力进行成型的方法。
而注塑成型则是将熔化的橡胶材料注入到模具中,通过冷却后形成所需产品的方式。
无论是哪种成型方式,都需要根据产品的形状和尺寸来选择合适的模具,并确保成型过程中的温度、压力等参数控制良好,以保证成品的质量。
制造完成后,橡胶制品还需要经过硫化来提高其物理性能和耐用性。
硫化是橡胶制品生产过程中的最后一道工序,通过在高温和压力下进行硫化反应,将橡胶材料中的硫原子与橡胶分子进行交联,从而使制品变得更加稳定和耐用。
硫化过程中还要控制硫化时间、温度和压力等因素,以确保制品硫化均匀。
最后,橡胶制品的生产过程还需要进行质量检验。
检验包括外观检验、尺寸检验、物性测试等多个环节,以确保产品符合设计要求和质量标准。
橡胶制品的生产工艺流程非常庞杂,每个环节都需要精细控制和严格把关。
只有通过科学合理的工艺流程和质量控制,才能生产出优质、可靠的橡胶制品。
这些橡胶制品广泛应用于汽车、机械、建筑、电子、医疗等行业,对于推动现代工业的发展起到了重要的作用。
橡胶制品的基本生产工艺过程

橡胶制品的基本生产工艺过程橡胶制品的生产工艺是一个包含多个步骤的复杂过程。
以下是橡胶制品的基本生产工艺过程:1. 原材料准备:橡胶制品的主要原材料是天然橡胶和合成橡胶。
原材料需要进一步加工,以便在后续的工艺过程中使用。
这包括清洗、切割和破碎等步骤。
2. 配方调配:根据产品要求,制定合适的橡胶配方。
不同类型的橡胶制品需要不同的橡胶配方,以确保产品具有所需的物理性能和特性。
在配方中,可能需要添加硫化剂、防老化剂、增塑剂和填充剂等助剂。
3. 混炼:将橡胶原料和各种助剂混合在一起,形成混炼胶料。
这个过程可以使用混炼机完成,混炼机能够把原料均匀地混合在一起,并产生适当的热量以促进反应。
4. 成型:将混炼好的胶料放入模具中,并通过压力或挤压等方式进行成型。
成型过程根据产品的不同可以使用不同的技术,例如压延、注射、挤出和压痕等。
成型完成后,需要进行烘干或固化以确保产品的硬度和形状。
5. 处理和整理:对成型后的产品进行修整和整理,以确保产品的质量和外观。
这包括去除多余的边角料、刷洗和打磨等处理过程。
6. 检测和检验:对制造完成的橡胶制品进行检测和检验,以确保产品符合预定的标准和要求。
这可以包括物理性能、化学性质、外观和尺寸等方面的测试。
不合格的产品将进行返工或退货。
7. 包装和储存:将合格的产品进行包装,并标明产品的规格、批次和生产日期等信息。
然后将产品储存到仓库或发往销售渠道。
总的来说,橡胶制品的生产工艺包含了原料准备、配方调配、混炼、成型、处理和整理、检测和检验,以及最后的包装和储存。
其中每个步骤都需要精确的操作和控制,以确保最终产品的质量和效果。
橡胶制品的生产工艺是一个精细而复杂的过程,需要严格的控制和技术实力。
接下来将继续介绍橡胶制品的详细生产工艺过程以及一些常见的应用。
8. 二次加工:某些橡胶制品需要进行二次加工,以达到特定的要求和功能。
例如,橡胶密封件可能需要进行模切和槽口切割,橡胶管道可能需要进行穿刺和加强带的固定等。
橡胶加工工艺及配方
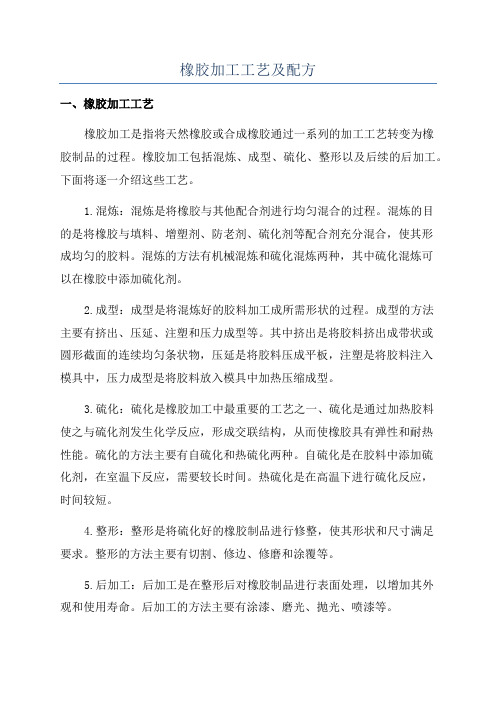
橡胶加工工艺及配方一、橡胶加工工艺橡胶加工是指将天然橡胶或合成橡胶通过一系列的加工工艺转变为橡胶制品的过程。
橡胶加工包括混炼、成型、硫化、整形以及后续的后加工。
下面将逐一介绍这些工艺。
1.混炼:混炼是将橡胶与其他配合剂进行均匀混合的过程。
混炼的目的是将橡胶与填料、增塑剂、防老剂、硫化剂等配合剂充分混合,使其形成均匀的胶料。
混炼的方法有机械混炼和硫化混炼两种,其中硫化混炼可以在橡胶中添加硫化剂。
2.成型:成型是将混炼好的胶料加工成所需形状的过程。
成型的方法主要有挤出、压延、注塑和压力成型等。
其中挤出是将胶料挤出成带状或圆形截面的连续均匀条状物,压延是将胶料压成平板,注塑是将胶料注入模具中,压力成型是将胶料放入模具中加热压缩成型。
3.硫化:硫化是橡胶加工中最重要的工艺之一、硫化是通过加热胶料使之与硫化剂发生化学反应,形成交联结构,从而使橡胶具有弹性和耐热性能。
硫化的方法主要有自硫化和热硫化两种。
自硫化是在胶料中添加硫化剂,在室温下反应,需要较长时间。
热硫化是在高温下进行硫化反应,时间较短。
4.整形:整形是将硫化好的橡胶制品进行修整,使其形状和尺寸满足要求。
整形的方法主要有切割、修边、修磨和涂覆等。
5.后加工:后加工是在整形后对橡胶制品进行表面处理,以增加其外观和使用寿命。
后加工的方法主要有涂漆、磨光、抛光、喷漆等。
二、橡胶配方橡胶配方是指将橡胶与各种配合剂按一定比例混合,形成胶料的配方。
橡胶配方的配料包括橡胶本体、填充剂、增塑剂、硬化剂、防老剂、防护剂、促进剂等。
下面将介绍常用的橡胶配方。
1.橡胶本体:橡胶本体是指原料橡胶,可以是天然橡胶或合成橡胶。
常用的橡胶有天然橡胶、丁苯橡胶、丁腈橡胶、氯丁橡胶、丁基橡胶等。
2.填充剂:填充剂是指填充到橡胶中的无机或有机物质,可以改变橡胶的物理和机械性能。
常用的填充剂有炭黑、白炭黑、沉香末、沥青等。
3.增塑剂:增塑剂是指能增加橡胶柔软性和延展性的物质。
常用的增塑剂有塑化油、脂肪酸酯、酸酐和酯类增塑剂等。
橡胶制品的基本生产工艺过程

橡胶制品的基本生产工艺过程橡胶制品的基本生产工艺过程橡胶制品是一种重要的工业原材料,广泛应用于轮胎、密封件、管道、胶带、鞋子等各行各业。
其生产工艺涉及多个环节,包括橡胶原料的选配、加工、模压、硫化等过程。
本文将详细介绍橡胶制品的基本生产工艺过程。
1. 原材料选配橡胶制品的生产需要选用优质橡胶原料,包括天然橡胶和合成橡胶两种。
天然橡胶主要产自南美洲、非洲和东南亚等地区,由橡胶树采集而得。
合成橡胶是一种人工合成的高分子合成材料,通常由石油化工产品进行加工合成。
原材料的选配要根据生产目的、使用环境和成本等因素进行考虑。
2. 橡胶加工橡胶加工是将橡胶原料进行分散、混合、塑化等过程,使其具有可塑性和可成型性。
这个过程中需要用到橡胶加工机械,包括橡胶混炼机、单螺杆挤出机、双螺杆挤出机、压延机等。
其中,橡胶混炼机是橡胶制品加工过程中最关键的设备之一,其作用是将原料加工成橡胶糊,以便后续的模压工艺。
3. 模压模压是将橡胶加工成需要的形状和尺寸的工艺过程。
首先,将加工好的橡胶糊均匀地塑造成所需的形状,然后放入模具中进行加压成形。
模具的选用要根据所需产品的尺寸、形状和数量进行考虑,常见的模具包括单腔模和多腔模等。
4. 硫化硫化是将模压成形的橡胶制品进行加热处理的工艺过程。
加热的目的是要将橡胶糊中的硫化剂激活,使其与橡胶分子进行交联,从而形成强度高、耐磨性好的橡胶制品。
硫化的温度、时间和压力等参数要根据所用硫化剂和橡胶制品的种类和尺寸进行合理设置。
5. 后处理生产出的橡胶制品需要进行后处理,使其具有所需要的使用性能和外观效果。
后处理的工艺包括去模、除油、喷漆、涂胶等,根据所需产品的用途和外观要求进行选择。
总之,橡胶制品的生产工艺过程包括原材料选配、橡胶加工、模压、硫化和后处理等多个环节。
这些环节中的每一个都至关重要,只有合理选择和组合各个环节,才能制造出品质优良的橡胶制品。
橡胶制品的基本生产工艺过程
橡胶制品的基本生产工艺过程
橡胶制品是一种应用广泛的材料,用于生产各种产品,从汽车轮胎到家具配件都有橡胶制品的身影。
本文将介绍橡胶制品的基本生产工艺过程,包括原料准备、混炼、挤压、成型、硫化等环节。
1. 原料准备
橡胶制品的生产过程首先需要准备橡胶原料。
橡胶通常是从橡胶树上采集的,经过处理后变成橡胶块或橡胶粉。
除了橡胶外,生产橡胶制品还需要添加助剂,如硫化剂、促进剂、抗氧化剂等。
2. 混炼
将橡胶块或橡胶粉与助剂混合均匀是橡胶制品生产的第一步。
混炼的目的是在原料中均匀分布各种成分,并提高橡胶的韧性和弹性。
混炼通常需要使用橡胶混炼机来完成。
3. 挤压
混炼后的橡胶原料经过挤压成型,成为一定形状的橡胶带或橡胶管。
挤压是通过挤压机完成的,橡胶原料被挤压出来后,在传送带上进行输送。
4. 成型
橡胶带或橡胶管经过挤压后还需要进行成型。
根据产品设计要求,将橡胶原料切割、压制成所需的形状。
常见的成型方式包括模具压制、注射成型等。
5. 硫化
硫化是橡胶制品生产中至关重要的一步。
通过加热橡胶制品并加入硫化剂,使橡胶原料交联,提高橡胶的硬度和耐磨性。
硫化过程可以通过热压硫化、热风硫化等方式完成。
结语
橡胶制品的生产工艺包括原料准备、混炼、挤压、成型和硫化等环节。
每个环节都至关重要,影响着成品的品质和性能。
只有严格按照标准操作,才能生产出高质量的橡胶制品。
橡胶促进剂母胶粒的工艺
橡胶促进剂母胶粒的工艺橡胶促进剂母胶粒的工艺可以分为以下几个步骤:第一步:原材料的准备橡胶促进剂(也称为橡胶助剂)主要包括硫化剂、活性剂、抗老化剂、防裂剂等。
在制备橡胶促进剂母胶粒之前,需要准备好这些原材料,并进行精确的配比。
第二步:混合橡胶和促进剂将预先准备好的橡胶原料和橡胶促进剂按照一定的配比混合在一起。
混合的方法有物理混合和化学混合两种。
物理混合主要是通过机械设备将橡胶和促进剂进行充分的摩擦、挤压、翻滚等,达到均匀混合的效果;化学混合则是将橡胶和促进剂通过化学反应使它们结合在一起。
第三步:加入其他辅助剂在混合好的橡胶与促进剂的基础上,可以根据需要添加一些辅助剂,如增塑剂、填充剂、助剂等。
这些辅助剂的添加可以改善橡胶的物理性能、加工性能以及抗老化能力。
第四步:加工成粒状将混合好的橡胶促进剂母胶通过挤出、切割、出料等工艺加工成颗粒状。
挤出是指将橡胶母胶通过挤出机进行挤压,形成一定规格的橡胶带状物;切割是将橡胶带状物通过切割机进行切割,形成一定长度的橡胶颗粒;出料是将切割好的橡胶颗粒通过输送带或者其他方式进行收集和包装。
第五步:配方设计与调整根据具体的应用要求和产品性能要求,可以根据实际情况对橡胶促进剂母胶粒的配方进行设计和调整。
配方设计的关键是根据产品的使用环境、使用寿命和使用温度等因素,合理选择和调整不同的橡胶促进剂,以达到最佳的使用效果。
第六步:质量检测橡胶促进剂母胶粒制备完成后,需要进行质量检测。
常见的检测项目包括橡胶拉伸强度、硬度、断裂伸长率等物理性能,以及抗老化性能、耐磨性能等。
合格的橡胶促进剂母胶粒可以进入下一道生产工序,否则需要进行调整或者重新制备。
总结:橡胶促进剂母胶粒的制备工艺包括原材料准备、混合橡胶和促进剂、加入其他辅助剂、加工成粒状、配方设计与调整以及质量检测等步骤。
通过精确的配比和合理的工艺控制,可以制备出符合要求的橡胶促进剂母胶粒,为橡胶制品的生产提供优质原材料。
橡胶加工工艺流程
橡胶加工工艺流程
橡胶加工工艺是指将橡胶原料经过一系列的加工步骤,最终制成各种橡胶制品的过程。
下面是橡胶加工工艺的一般流程:
1. 橡胶混炼:首先将橡胶原料放入混炼机中进行混炼,目的是将橡胶与其他添加剂充分混合并使其成为一个均匀的胶料。
2. 压延:将混炼好的橡胶胶料放入压延机中进行压延,使其成为一定厚度的橡胶带.
3. 制模:将橡胶带放入模具中,通过压力和温度的作用,使其成型并固化。
制模的方式有多种,常见的有压热压缩法、注塑法等。
4. 硫化:将制好的橡胶制品放入硫化箱中进行硫化处理。
硫化是橡胶加工中非常重要的一步,通过加热和硫化剂的作用,使橡胶分子互相交联,增强其强度和抗老化性能。
5. 切割和修整:硫化后的橡胶制品经过切割和修整,使其形状更加精确。
6. 检验和测试:对制好的橡胶制品进行检验和测试,以确保其质量和性能符合要求。
主要包括外观检查、尺寸测量、物理性能测试等。
7. 包装和存储:将合格的橡胶制品进行包装,通常采用塑料袋或纸盒包装。
然后存放在干燥、通风的库房中。
以上是橡胶加工工艺的一般流程,不同的橡胶制品可能会有一些特殊的工艺步骤。
橡胶加工的过程中,需注意橡胶原料的质量、混炼工艺参数、硫化条件等。
只有严格控制每一个环节,才能制备出质量稳定、性能优越的橡胶制品。
橡胶配料工序
橡胶配料工序是橡胶制品生产过程中的重要环节,其主要包括以下步骤:
1. 原材料加工:生胶需要切碎并烘干,同时配合剂需要进行粉碎、筛选、溶化、过滤和蒸发等过程。
在这一过程中,生胶和配合剂的烘干温度不得超过70°C,以避免引起燃烧。
2. 配料:将各种生胶、配合剂按配方逐项称量,并存放于容器内,以备混炼。
配料应尽量采用密闭自动称量,以减少粉尘飞扬。
人工配料时,必须轻拿轻放,同时应穿戴好个人防护用品,室内应有吸尘装置,并保持通风良好,以减少各种粉尘对人体的危害。
在完成配料后,就可以进行混炼工序,即将橡胶与其他配合剂进行均匀混合,形成均匀的胶料。
混炼的方法有机械混炼和硫化混炼两种,其中硫化混炼可以在橡胶中添加硫化剂。
完成混炼后,就可以进行成型工序,即将混炼好的胶料加工成所需形状。
成型的方法主要有挤出、压延、注塑和压力成型等。
以上是橡胶配料工序的基本步骤,供您参考,建议咨询专业人士获取更准确的信息。
- 1、下载文档前请自行甄别文档内容的完整性,平台不提供额外的编辑、内容补充、找答案等附加服务。
- 2、"仅部分预览"的文档,不可在线预览部分如存在完整性等问题,可反馈申请退款(可完整预览的文档不适用该条件!)。
- 3、如文档侵犯您的权益,请联系客服反馈,我们会尽快为您处理(人工客服工作时间:9:00-18:30)。
1 丁苯橡胶 2 顺丁橡胶 3 异戊橡胶 4 乙丙橡胶 5 丁基橡胶
6 氯丁橡胶
特 种 合 成 橡 胶
凡是具有特殊性能,专门用于制作耐热、耐寒、 耐化学物质腐蚀、耐溶剂、耐辐射等特种橡 胶制品橡胶称为特种合成橡胶。
)。容量过大或过小,都影响生胶获得良好的塑炼效果。容量
过小,生胶会在密炼室中打滚,不能获得有效塑炼;容量过 大会使生胶塑炼不均匀,排胶温度升高,设备因超负荷运转 而易于损坏。装胶容量应根据密炼室壁和转子突棱磨损后的 缝隙大小,通过实验确定。通常,装胶容量为密炼室容量的 55%~75%(即填充系数为0.55~0.75)。
1 丁腈橡胶 2 硅橡胶 3 氟橡胶 4 聚氨酯橡胶 5 丙烯酸酯橡胶 6 氯磺化聚乙烯
2.橡胶的配合剂
橡胶配合剂
硫化剂
硫化剂是一类使橡胶由线形长链分子转变为
网状大分子的物质,这种转变称为硫化。
硫化剂:硫磺、一氯化硫、硒、碲及其氯化
物、硝基化物、有机过氧化物以及某些金属氧化
物。
橡胶配合剂
硫化促进剂
无氧(氮气保护)存在时,断
链所形成的自由基可发生偶合或 支化反应,此时则得不到塑炼效 果。
温度的作用
低温塑炼:分子链断裂
的主要原因是由于机械力的作
高 温 塑 炼
用。随着温度的升高,生胶粘 度的降低,分子滑动性增加,
低温塑炼
塑炼时遭受机械力的作用降低。
因此,在低温塑炼时要注意降 温,防止随着炼胶时间的增加,
光、机械力等)的作用,而逐步失去其原有的优良性能,以 至最后丧失了使用价值。 添加防老剂的目的:抑制橡胶的老化现象。 • 物理防老剂:石蜡
• 化学防老剂:热稳定剂、抗氧剂、紫外吸收剂、光屏蔽剂
橡胶配合剂
填充剂
补强填充剂提高硫化橡胶的强力,撕裂强度, 定伸强度,耐磨性等物理机械性能。
炭黑、白炭黑、活性陶土、超细活性碳酸钙。
螺杆机塑炼的特点是高温下连续进行。在螺杆机中, 生胶一方面受到螺杆的强烈机械搅拌作用,另一方面 由于生胶受螺杆与机身间的摩擦而产生大量热,温度 可高达150-180℃,从而加速氧化裂解,获得塑炼效
果。
螺杆机塑炼的主要影响因素: 机温、胶温、填胶速度、出胶空隙
螺杆机塑炼
C、螺杆机塑炼 螺杆机塑炼具有连续化、自动化程度高,生产能 力大,劳动强度低等优点。最适用于生胶品种少、耗 胶量大的大规模工业生产。 但从目前国内使用螺杆机塑炼来看,还存在一些如 排胶温度高、塑炼胶热可塑性大、可塑性不均匀(夹 生现象)和较低等缺陷,因此在应用上受到一定限制。
硫化促进剂可促进橡胶的硫化作用,降低硫化 所需温度,缩短硫化时间,并改善硫化胶的物理 机械性能。 硫化促进剂的种类很多。无机类硫化促进剂 (如氧化铅,氧化镁等)硫化效果较差,已被淘汰。 目前主要使用有机类硫化促进剂。
橡胶配合剂
防老剂
橡胶的老化:橡胶在加工、贮存和使用过程中,由于受
到各种外界因素(如热、氧、臭氧、金属离子、电离辐射、
橡胶分子链断裂,降低大分子长度。 橡胶的分子链很长,分子间吸引力大且线性分子之间
存在大量缠结点,大大阻碍了长链分子的位移运动。要增加
橡胶的可塑性或塑性变形,必须使橡胶分子易于发生大分子 链的位移运动,所以减少橡胶分子链的长度(降低分子量), 是降低分子间作用力、增大橡胶分子的塑性变形的最有效方 法。 一般门尼粘度在60以下的均可不经过塑炼而直接混炼。
塑炼方法
机械塑炼法:采用开炼机、密炼机、螺杆塑炼机
等的机械作用切断分子链而获得生胶可塑性。 化学塑炼法:在化学药品的作用下,使橡胶大分 子链解聚而达到塑化的目的。
塑炼的机器
A、开炼机
•
•
优点:比较机动灵活、投资小、适用于变化较多的场合。
缺点:劳动强度大、生产效率低、操作条件差。
开炼机的两个滚筒的速比:前比后(1:1.15-1.27) 操作方法:
薄通塑炼法、包辊塑炼、分段塑炼法、化学塑解剂法。
开炼机
开炼机塑炼的主要影 响因素: 辊温 辊距 辊速 时间 容量
开炼机
辊温:
开炼机塑炼为低温塑炼,为提高塑炼效果,应加强辊
筒的冷却,严格控制辊温。 生产中,由于辊筒冷却受到各种条件的限制,如辊筒 导热性差和冷却水温度不易降低等,使辊温不易达到理想 要求。因此,采用冷却胶片的方法是提高塑炼效果的有效
橡胶类产品母料加工工艺
长园电子研发部 王华东
内容
1 2 3 4 橡胶的基本概念 橡胶的配合剂 橡胶母料的加工工艺 我司用胶介绍
1.橡胶的基本概念
定义和用途
橡胶:具有可逆形变的高弹性聚合物材料。其伸长率可达100%~
1000%,除去外力后能恢复原状。橡胶属于完全无定型聚合物,它的玻璃
化转变温度(Tg)低,其分子量一般都在10万以上,有的甚至达到100万 以上。
机械力的作用
当温度一定时,随着施 加于橡胶上的总机械功的增 大(如增加塑炼机械的转速、 增加薄通次数等),分子链 降解程度就愈大。 塑炼的结果:使橡胶的 分子量变小,分子量分布变 窄。
氧的作用
在低温塑炼时,橡胶大分子 受机械力的作用,分子链被切断 而形成自由基,这种自由基能迅 速地与氧产生化学反应,从而使 断链后异丁腈
高低温通用型塑解剂:硫醇及其二硫化物类、二邻苯甲酰胺二苯基二
硫化物
低温塑解剂起自由基受体的作用,使断链的橡胶自由基稳定,从而生
成较短的分子。 高温塑解剂在高温时分解成极不稳定的自由基,促使橡胶分子生产自
由基,进而氧化断链,起引发剂的作用。
而高低温通用型的塑解剂兼有上述两项功能。
增长而不断地增大。但到后期 ,可塑度增长放缓,可根据实 际情况确定塑炼时间。
密炼机
转子转速: 一定温度条件下,塑炼胶可塑度随转子转速的增加而增
大。但是,转子转速不宜过快,否则会使生胶温度过高,致
使橡胶分子剧烈氧化裂解,或引起支化交联而产生凝胶。
密炼机
装胶容量: 密炼机塑炼时,必须首先合理确定装胶容量(称工作容量
措施,如使用胶片循环爬架装置以及采用薄通塑炼和分段
塑炼等均属于这类措施。
注:合成橡胶的塑炼温度一般为:30~45℃。当添加了化学塑解剂后,为了使化学 塑解剂产生最佳效果,炼胶温度一般以70~75℃为宜。
开炼机
辊距: 辊筒的速度恒定时,辊距减小会使生胶通过辊缝时所受 的摩擦、剪切力、挤压力增大,同时胶片变薄易于冷却。 辊速: 塑炼时,辊筒转速快,即单位时间内生胶通过辊缝次 数多,所受机械力的作用大,塑炼效果好。但辊筒速度过
密炼机
上顶栓压力: 上顶栓压力的大小,对塑炼效果影响很大。实验表明,
适当增加上顶栓压力,提高对胶料的剪切力作用,是缩短塑
炼时间的有效方法。当压力不足时,上顶栓被塑炼胶推动产 生上、下浮动,不能使胶料压紧,减小对胶料的剪切力作用 。但压力太大,上顶栓对胶料阻力增大,使设备负荷增大。
螺杆机塑炼
C、螺杆机塑炼
惰性填充剂增加胶料体积,节约成本,改善加
工性能。
云母粉、滑石粉、沉淀碳酸钙、硫酸钡。
橡胶配合剂
软化剂和增塑剂
目的:改善橡胶的加工和成型性能,增加橡胶的塑 性。
物理增塑剂:使橡胶溶胀,增大橡胶分子间的距
离,降低分子间的作用力,从而使胶料的塑性增
加。
化学增塑剂:加速橡胶分子在塑炼时的断链作用, 并使已断链的橡胶分子趋于稳定
橡胶分子链断裂的主要影响因素
由于橡胶在塑炼时,遭受到氧、热,机械力和增塑
剂等因素的作用,所以塑炼机理与这些因素密切相关。
机械力的作用 氧的作用 温度的作用
增塑剂的作用
机械力的作用
生胶在塑炼机械剧烈的拉伸、挤压和剪切应力的反复
作用下,长链分子产生局部应力集中,致使分子链断裂,然
后断链的活性自由基为氧或其他自由基受体所俘获而稳定, 变成较短的分子而增加了可塑性。 机械断链一般只对一定长度的橡胶分子链有效,当橡 胶分子量小到一到一定程度后,因内聚力小,链段相对运动 容易,机械力作用产生的切应力小,则不足以使其断裂。
胶料温度升高。
高温塑炼:主要是氧化使分子链断裂。适当的高温有利于胶料 的热氧断链,但要注意:温度过高,胶料降解严重,会影响物理机械 性能。
增塑剂的作用
使用化学塑解剂能提高塑炼效果。它在塑炼中的作用与氧相似。不同 塑解剂的作用机理也各不相同。根据他们的使用温度,可分为: • 低温塑解剂:苯醌和偶氮苯
橡胶是高弹性的高分子材料,由于橡胶具有其他材料所没有的高弹
性,因而也称作弹性体。 橡胶经过硫化可将线型高分子交联成三维网状高分子量聚合物。这 种已硫化交联的橡胶称作硫化橡胶,俗称熟橡胶。未硫化的橡胶俗称生胶 或生橡胶。 用途:广泛用于制造轮胎、胶管、胶带、电缆及其他各种橡胶制品。
橡胶的共性
具有橡胶状弹性。 具有粘弹性。
快,塑炼胶升温快,反而会使塑炼效果下降,同时操作也
不安全。
开炼机
时间: 生胶塑炼效果与时间有一
定关系。在一定的时间范围内
,塑炼时间越长,塑炼效果越 好。超过这个时间范围后,可 塑性趋于平稳。 在用开炼机作包辊塑炼时,般塑炼时间不宜超过20min。
密炼机 B、密炼机
密炼机主要部件包括密炼室、转子、上顶栓、下顶栓、 冷却系统、润滑系统、密封装置和传动装置。
会无效地消耗在橡胶的可逆变形上。为此,需将生胶经过机 械加工、热处理或加入某些化学助剂,使其由强韧的弹性状
态转变为柔软而便于加工的塑性状态。
塑炼结果:
使生胶获得一定的可塑性,适合于混炼等后段工序。
使生胶的可塑性均匀化,使胶料的质量均匀。 改善胶料的流动性,便于压延、压出操作。
塑 炼
塑炼机理:橡胶经塑炼以增加其可塑性,其实质乃是使