LCD不良品分析数据统计表
LCD不良品图示识别一览表

不良名称 框胶气泡 不良名称 牛顿环异常
NG
OK
不良名称 粉碎彩虹 不良名称 银点彩虹
OK
NG
不良名称 崩 脚 不良名称 切割披锋 不良名称 切割多边 不良名称 电极斜边
不良名称 玻璃表划 不良名称 未印银点不良名称 贴片气泡 不良名称 液晶气泡
不良名称 灌晶冲刷纹 不良名称 液晶气泡 不良名称 边框彩虹 不良名称 夹缝不干净
不良名称 ITO腐蚀 不良名称 封口污染 不良名称 封口点彩 不良名称 封口口漏
不良名称 磨边不良 不良名称 进胶不良 OK NG NG OK
不良名称 封口偏大/小 不良名称 盒内内污
NG OK
不良名称 定向不良1 不良名称 定向不良2 不良名称 欠 扭 不良名称 边框点彩
不良名称 无规则内划 不良名称 有规则内划
不良名称 外丝印偏位 不良名称 丝印线异常
不良名称 喷码不良 不良名称 偏光片漏光 OK NG
不良名称 PIN脚多/少 不良名称 包装盒破损 多 OK 少 不良名称 包装不良 不良名称 框设计不良
不良名称 排骨彩虹 不良名称 外丝印不准
OK
NG
不良名称 污物彩虹 不良名称 摩擦斜纹 不良名称 显示字朦 不良名称 反黑/反白
不良名称 视 角 反 不良名称 显示多画 不良名称 电极划伤 不良名称 缺 划
不良名称 电压异常 不良名称 上下短路
NG
OK
不良名称 IC位线细 不良名称 保护膜翘起
不良名称 图形连线 不良名称 图形断线 不良名称 显影不足 不良名称 ITO划伤
不良名称 APR版不良 不良名称 IC标覆盖
不良名称
铬版错误
NG
OK
不良名称 酸刻过度 OK
LCD常见不良品解析ppt

手指印 抽插篮划伤
四、定向不良
指摩擦异常导致的不良,常见的摩擦不良有以下几种情况: ①摩擦条纹不良(常见于VA及负显产品,正显产品条纹基本可流程) ②单面摩擦(两面玻璃其中一面未摩擦) ③摩擦视角反(电测显示部分字体模糊不清或者视角方向与图纸不符合) ④摩擦时绒布上有杂质导致划伤PI层
单面摩擦框不良 ⑥CS不良 ⑦网印不良 ⑧组合歪不良 ⑨静电击伤 ⑩原破及粉压碎不良
制盒组不良
一、内污不良
产生原因:LCD盒内有异物不良,目测台观察多为白色异物。
导致内污不良的几大原因:①杂质 ②纤维毛线 ③漏边框、银点料 ④溶剂 ⑤粉团、粉压碎 ⑥摩擦绒布毛线 ⑦PI脏点
产生原因:①显影液或酸刻液浓度过高 ②显影液或酸刻液温度过高 ③显影或酸刻时间过长 ④曝光光强过度(引起显影过度)
上图均为蚀刻不足导致的“白点”短路
显影不足
显
影
过
度
①PI印刷不均匀
PI组不良
②PI印刷偏位
③PI点及PI脏点不良
④PI层印刷过厚或过薄
一、PI印刷不均匀
产生原因:①PI凸版或者网版异常 ②设备异常(匀胶轮自身有缺陷) ③PI房温湿度异常 ④PI个体特性
LCD常见不良及原因分析
制作:李波 日期:2017-3-1
光刻组不良
①短路、多划 ②断路、缺亮 ③显影不足、显影过度 ④蚀刻不足、蚀刻过度
一、短路
定义:同一面上本不应该连在一起的的ITO走线却发生了连接导通
不良表现:电测机在分显扫描时连续2声或3声报警,并且扫描电流大。 短路不良装模组后表现为某些笔段显示淡或者不显示。
三、PI点及PI脏点不良 PI点:目测表现为单独点状异常(点的颜色与玻璃底色差异大),贴片后呈黑色小点。 电测表现为显示时字体内有黑、白点异常 PI脏点:主要为目测时的内污不良及电测黑白点不良
LCD常见不良品解析

CS不良电测现象
盒内金属物质
七、网印不良
产生原因:丝印刮刀压力过大,导致网布压伤PI层。
不良现象:在目测时可见网布印痕,常见的有圆圈状、条状、封口附近八字 型冲刷网印及大面积网印压痕。部分网印形状、位置、模号一样,则是网板本身 异常导致(网板上有杂质或者网版制作有缺陷)
封口附近八字型冲刷网印
条状网印 点状网印
八、组合歪不良
产生原因及电测现象:两片玻璃在贴合时位置不正,导致全显时走线外露 或者字体形变。 在显微镜下观察贴合标记,一般可见圆环已相交。
贴合标记已相交
走线外露 字体形变
九、静电击伤不良
产生原因:摩擦或者喷粉过程中静电强度大而未篮划伤
四、定向不良
指摩擦异常导致的不良,常见的摩擦不良有以下几种情况: ①摩擦条纹不良(常见于VA及负显产品,正显产品条纹基本可流程) ②单面摩擦(两面玻璃其中一面未摩擦) ③摩擦视角反(电测显示部分字体模糊不清或者视角方向与图纸不符合) ④摩擦时绒布上有杂质导致划伤PI层
单面摩擦 摩擦视角混乱
摩擦绒布划伤PI层 VA产品摩擦条纹
五、边框不良
常见边框不良类型:①框虚不良 ②框肥不良 ③框断及框细(边框丝印下料不好导致) ④边框彩虹(热压时边框未下去)
框肥不良
框虚不良 显微镜下状况
边框彩虹
六、CS不良
产生原因:盒内金属物质将上下片走线相连,形成上下短路(也称为层间短路) 常见金属物质有铁屑、银点料、ITO来料锡点等。
产生原因:①曝光过程中有杂质粘附在菲林版表面 ②显影不足 ③蚀刻不足
规律性短路产生原因: ①曝光过程中有杂质粘附在菲林版表面 ②菲林砸伤导致线条错乱,不该相连的线路连接在了一起 ③菲林来料异常:菲林本身存在油墨点短路或其他制作原因。
不良品分析统计表

256
0
不良率 0.00%
良率=产品总数/抽检数*抽检不良品总数/产品总数
100
90
#DIV/0!
80
#DIV/0!
70
#DIV/0!
60
#DIV/0!
50
#DIV/0! #DIV/0! #DIV/0! #DIV/0! #DIV/0!
40
30
20
10
0
0
0
0
0
0
0
0
0
0
#DIV/0!
可接受
B类-可接受
全天总产品不良率
抽检数
抽检不良品总数
256
0
不良率 0.00%
抽检数
抽检不良品总数
椭圆
水纹
不良品
0
备注:
压盖不良数量分类统计
盖体毛边 缺料 压坏
0
0
0
0
0
0
0
0
0
0
0
0
0
0
产品不良项目 变形 黑点 色差 椭圆
水纹
不良品合计
0 0 0 0 0 0 0
不良率 (%)
0.00% 0.00% #DIV/0! #DIV/0! #DIV/0! #DIV/0! 0.00%
数量
柏拉图分析
不良率%
盖口毛边
0
盖体毛边
0
缺料
0
压坏
0
变形
0
3:50 黑 点
色差
椭圆 水纹
不良品
0
时间
23:40 3:50 0:00 0:00 0:00 0:00 总计
样品 数 盖口毛边
128
不良品统计表图表
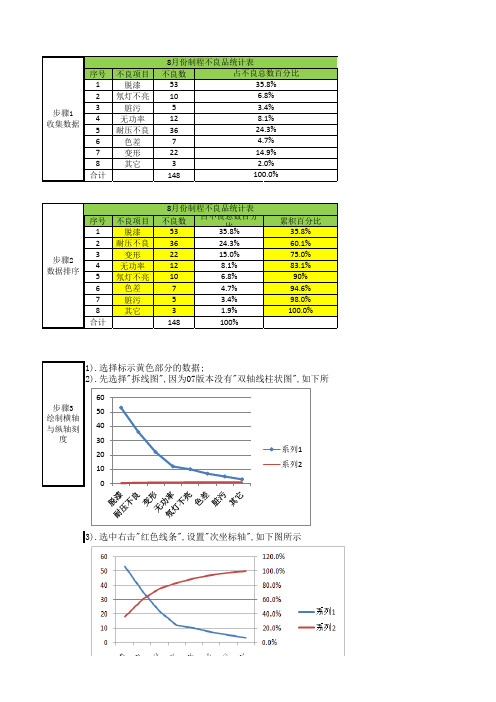
序号不良项目不良数1脱漆532氖灯不亮103脏污54
无功率125
耐压不良366
色差77
变形228
其它3合计148
序号不良项目不良数占不良总数百分比累积百分比1脱漆5335.8%35.8%2耐压不良3624.3%60.1%3变形2215.0%75.0%4
无功率128.1%83.1%5
氖灯不亮10 6.8%90%6
色差7 4.7%94.6%7
脏污5 3.4%98.0%8
其它3 1.9%100.0%合计148100%
步骤1
收集数据步骤2
数据排序步骤3
绘制横轴
与纵轴刻
度3).选中右击"红色线条",设置"次坐标轴",如下图所示
100.0%8月份制程不良品统计表1).选择标示黄色部分的数据;
2).先选择"拆线图",因为07版本没有"双轴线柱状图",如下所8.1%24.3%4.7%14.9%2.0%8月份制程不良品统计表占不良总数百分比35.8%6.8%3.4%010
20
30
405060
系列1系列2
5).再选中右击蓝色线条,更改图表类型为柱状图,如下所示6).再选中右击红色线条,更改"数据系列格式",如下图所示4).选中更改左右和下面轴线的格式,如下图所示
35.8%
60.1%75.0%83.1%90%94.6%98.0%0%10%20%30%40%50%60%70%80%90%100%0102030405060708090100110120130140系列1系列2。
LCD常见不良品解析

短路不良图片
上图为曝光杂质引起的短路 菲林杂质引起的多划不良(走线与填充块连接)
二、断路
定义:ITO走线被划伤断开,导致该显示的图案不显示。
不良表现:电测全显状态时图案缺失,装机表现也是图案缺失。
产生原因: ①涂胶针孔及杂质 ②光刻胶脱落 ③胶面划伤 ④菲林砸伤 ⑤“刀砍”不良 ⑥显影过度及蚀刻过度 ⑦曝光效果差
“刀砍”不良
光刻胶脱落
胶面划伤
涂胶针孔
曝光效果差显影后线条变细或脱落
三、显影不足与酸刻不足
不良现象:使玻璃产生短路、多划或导致走线外露。
产生原因:①显影液或酸刻液浓度不够 ②显影液或酸刻液温度不够 ③显影或酸刻时间不足 ④曝光光强不足(引起显影不足)
四、显影过度与蚀刻过度
不良现象:使玻璃产生大面积缺划或影响电极端子导通
摩擦绒布划伤PI层 VA产品摩擦条纹
五、边框不良
常见边框不良类型:①框虚不良 ②框肥不良 ③框断及框细(边框丝印下料不好导致) ④边框彩虹(热压时边框未下去)
框肥不良
框虚不良 显微镜下状况
边框彩虹
六、CS不良
产生原因:盒内金属物质将上下片走线相连,形成上下短路(也称为层间短路 常见金属物质有铁屑、银点料、ITO来料锡点等。
三、PI点及PI脏点不良 PI点:目测表现为单独点状异常(点的颜色与玻璃底色差异大),贴片后呈黑色小点。 电测表现为显示时字体内有黑、白点异常 PI脏点:主要为目测时的内污不良及电测黑白点不良
四、PI印刷过厚或过薄 导致产品贴片后显底影(即8字外露)
上图为PI点不良在目测台下现象 上图为PI点不良在显微镜下现象
封口附近八字型冲刷网印
条状网印 点状网印
八、组合歪不良
不良品分析报告表格

不良品分析报告表格篇一:产品不良报告格式篇二:不良分析报告导光板不良品分析报告一、数据收集123、二、主要不良原因分析1、导光板来料不良因为厂家在1000级净化房生产,10000级贴保护膜,导致导光板来料存在大量毛尘、杂质,来料不良率在30%左右,其中揭膜残留在显示区域不良占来料不良总数的20%,直接造(转载于: 小龙文档网:不良品分析报告表格)成半成品不良在6%左右2、存储与来料检验(参考实验1)来料IQC检验、库房拆包点数量等环境不符合要求会导致大量杂质、毛尘吸附到产品保护膜表面,贴合时揭膜又吸附到产品表面,因为IQC、库房不是每包都拆,所以当产线用到拆过包装的产品时不良会上升到15%左右,占总不良2%左右3、车间生产环境车间环境无尘室等级在10W级别,贴合机里动态能到1000,边缘治具旁边在1W级,我们上线前需要在10W级裁切导光板四周保护膜,停留几分钟再进行入1W经左右的治具上揭膜,这个过程中也会产生毛尘,一般的显示产品都是在1000级房生产,所以我们的制程过程洁净度也不符合业界做法,从产线一些数据可以看出此问题,平常生产不良15%左右,如果有几个外来人员在无尘室工操作,不良能达到25%,空调不开,拆包拿出来烘烤等也会产生不良,总共5%-10%左右4、标准问题成品标准:1、周边区域(距四周边1cm范围内)直径小于0.25,数量小于3个,间距大于3cm;2、中心区域直径小于0.15,数量小于2个,间距大于5cm 因为杂质、毛尘点组成成品后打光会形成亮点,会扩大0.5-1.5倍左右成品0.25MM的点来料需控制在0.12-0.15左右,成品0.15MM的点来料控制在0.05-0.10左右,所以也有存在1%左右的误判产品三、改善措施及建议1、导光板来料不良联系厂家处理,退货或返工,要求厂家立即改善厂家品质经理回复将他们库存进行复检,将保护膜贴合移到1000级洁净房生产,并收到不良品三天内回复8D报告2、存储与来料检验后续拆包产品必须在无尘车间从新进行清洁方可上线使用,用气枪吹去表面毛尘IQC检验环境需进行改善建议后续在无尘室检验。
不良_分析报告_LCD(经典)

Confidential
JIG Cross check
现
Line, Dot
现 /电 认
画 /电
工
N/D,,MTP N/D,,MTP
[ 须 认项 ]
检查项 : 观 认 设 设备 : SMT显 镜 SMT显 检查项 : - CONN'检查, FPC 观检查, FPC补 CONN'检查, 观检查, FPC补 - IC 观检查, PANEL PAD 检查 观检查, 检查项 : FOG 压贴 认 设备 : 光学显 镜 见 项 : FOG压贴 , FOG压贴 FOG压贴 FOG压贴 Line 检查项 : COG 压贴 认 设备 : 光学显 镜 检查项 : COG压贴 检查, IC Crack检查 COG压贴 检查, Crack检查 Dot 检查项 : CELL / 线 认 备 : 光学显 镜 检查项 - CELL E/T PAD 压,Scratch检查 ,Scratch检查 - Pattern Scratch, Panel 细 Crack - 静电 护 Damage检查(AMOLED Damage检查(AMOLED 关) MTP进 MTP进 (MTP , 当 电 N/D) 工 SWAP TEST ( Swap test ) SWAP 高时交 技术 Repair 实 (具 问题,参 系) 认 检查 ( 发)
■Line Tracing ① ②
Line 异
认 顺 Line Crack, 蚀等 认.
异 时 揭开Pol
检查
异 .
■ Gate/Data
线状态
Crack
异
short
PAD Crack时 隔 条线 Open 现 多发
Pad Crack (TFT 12/19 线 态)