开题报告+自动加料机控制系统.doc
PLC与组态软件的饲料加工自动控制系统的设计开题报告
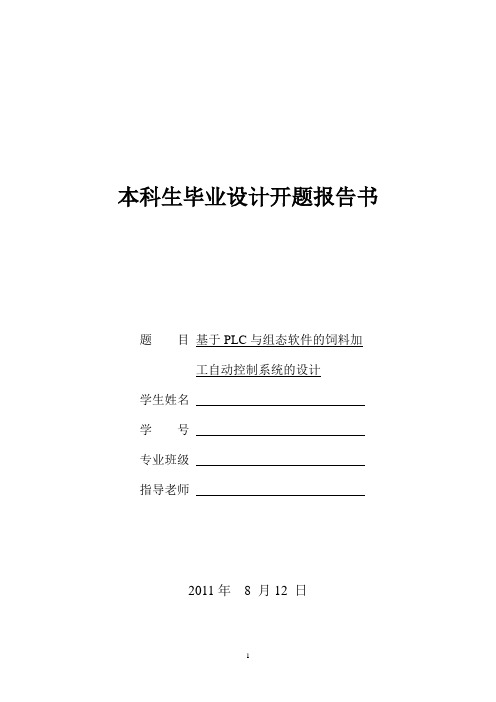
本科生毕业设计开题报告书题目基于PLC与组态软件的饲料加工自动控制系统的设计学生姓名学号专业班级指导老师2011年8 月12 日论文(设计)题目基于PLC与组态软件的饲料加工自动控制系统的设计课题目的、意义及相关研究动态:饲料工业是畜牧养殖业的基础。
我国饲料工业从上世纪70年代中后期,经过近四十年的发展,我国饲料业已完成了从手工作坊式的生产到世界第二大饲料生产国的飞越,成为我国重要的支柱产业之一。
但是饲料厂的配套自动控制系统和高精度配料控制系统还相对滞后,因此实现安全可靠的自动控制系统和高精度配料系统就显得十分迫切和必要。
饲料厂自动控制系统的发展经历了人工手动控制、机械电气控制、单片机控制、工业计算机集中控制等几个阶段。
第一阶段:饲料加工技术比较简单,各机械之间没有逻辑联系,现场操作人员一般只负责一到两个设备的操作与监控,并手工记录各项数据,产品质量人为因素很大。
第二阶段:继电器手工控制在很大程度上降低了工人的劳动强度,但大量的中间继电器和时间继电器组成的电控系统非常复杂,可靠性极低,特别是调试和改造时难度很大。
第三阶段:随着大规模集成芯片技术的的成熟,单片机控制系统应运而生。
单片机配料系统较之前两种系统设计电路复杂程度降低,可靠性大大提高,但其抗干扰能力比较差也局限了它的应用。
第四阶段:随着计算机技术的迅猛发展和广泛应用,基于工控机的饲料厂自控系统也开始出现,这种系统大多采用集中控制方式。
计算机除具有工艺流程控制、工况实时显示、提供数据存储、报表打印等功能等功能外,还要完成对各象的直接控制和数据采集任务。
在经济不断发展,科技日新月异的今天,科学技术越来越多的应用于饲料工业中,特别是现场总线和计算机技术的迅猛发展,饲料工业的自动化控制水平也在相应提高。
美国及欧洲的一些国家的饲料厂从进料到成品散装出料,全部为计算机自动控制,整厂单班操作人员只需要两人。
饲料厂的管理和控制全部通过计算机进行操作,管理系统采用先进的模块化结构,可根据各部门职能选择不同的系统模块。
开题报告自动控制供料系统设计.doc
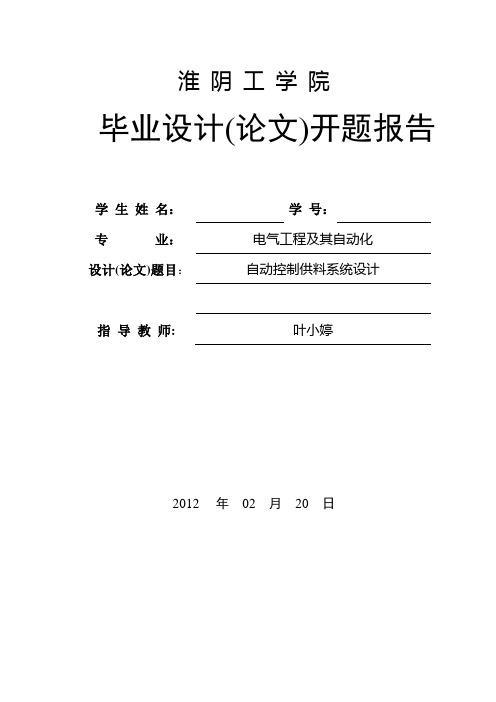
淮阴工学院毕业设计(论文)开题报告学生姓名:学号:专业:电气工程及其自动化设计(论文)题目:自动控制供料系统设计指导教师: 叶小婷2012 年02 月20 日1.结合毕业设计(论文)课题情况,根据所查阅的文献资料,每人撰写2000字左右的文献综述文献综述1.1设计背景和研究意义在我国的乡镇企业、私营企业,由于受资金管理等方面的限制,一般送料绝大多数采用人工手送料,且缺乏保护装置,造成劳动强度大,效率低,事故发生大等特点。
随着科技信息科技的迅猛,市场经济的高速发展,国内、国际市场竞争日益激烈,产品更新更快,尤其是随着高新科技的日新月异产品的类型、工艺外形越来越复杂,精度越来越高,再加上企业经营与发展必会面对劳工的短越、人工成本上要节省化、合理化与自动化的发展趋向,传统的手工送料已经不能满足要求,这时自动送料机就应运而生,在今天现代的科学领域中送料机就是用于专门粒料,粉料,片状料等材料的自动化,数控化,精确化的输送系统,是无论是轻工业还是重工业都不可缺少的设备。
近年来,由于单片机控制技术、检测技术及电子技术的飞速发展,作为辅助装置的送料系统自动化水平也需要越来越高。
提高自动化的水平不仅可以提高效率、产品的质量同时也能保证人工的身体安全。
而单片机就是实现控制的重要关节,单片机是一种集成在电路芯片,是采用超大规模集成电路技术把具有数据处理能力的中央处理器CPU 随机存储器RAM、只读存储器ROM、多种I/O口和中断系统、定时器/计时器等功能,可能还包括显示驱动电路、脉宽调制电路、模拟多路转换器、A/D转换器等电路,集成到一块硅片上构成的一个小而完善的计算机系统。
综上所述,在本着节约资本、降低成本、提高生产效率,保证人员身体安全的科学人性化管理的方针下对送料进行自动化管理。
采用单片机为核心的自动控制技术来实现,这样就可以在不购买新设备的基础上对旧设备进行自动化改良,这不仅提高了工作的效率,使整个过程又快又节约资本。
自动配料控制系统设计开题报告书

自动配料控制系统设计开题报告书一、设计背景和意义目前,在食品加工行业中,配料控制是一个关键的环节,对于产品的质量和稳定性有着重要的影响。
传统的配料控制方式依赖于人工操作,容易受到人为因素的影响,存在一定的不稳定性和误差。
为了提高配料的准确性和稳定性,自动配料控制系统应运而生。
自动配料控制系统能够在加工过程中根据需要自动添加正确的配料,并实时监测和调整配料的量,从而保证产品的品质和稳定性。
该系统具有速度快、准确度高、可靠性强等优点,能够大幅度提高配料的效率和准确度,减少人工操作的错误和疏忽。
二、设计目标和内容本设计的目标是设计一个高效、智能的自动配料控制系统,通过对原料的实时监测和分析,自动调整配料的含量,保证产品的质量和稳定性。
具体的设计内容包括以下几个方面:1.原料检测和分析:通过传感器对原料进行实时监测和分析,获取原料的含量和质量数据。
2.配方管理:设计一个配方管理系统,根据产品的要求和配料的特性,确定合适的配方,并将其存储在系统中。
3.自动配料控制:根据产品的配方要求和原料的质量数据,自动计算和调整配料的含量。
4.过程监控和调整:实时监测配料过程中的关键参数,如温度、压力等,并根据需求进行调整。
5.故障处理和报警系统:设计一个故障处理和报警系统,及时发现和处理系统故障,确保系统的稳定运行。
三、设计方法和技术1.传感器技术:利用先进的传感器技术对原料进行实时监测和分析,获取原料的质量和含量数据。
2.控制算法:设计合适的控制算法,根据产品的配方要求和原料的质量数据,计算和调整配料的含量。
3.数据处理和分析:将传感器获取的数据进行处理和分析,得出配料的准确含量,并进行合理的调整。
4.人机界面:设计一个友好的人机界面,方便操作员进行参数的设定和监控。
5.故障处理和报警系统:设计一个故障处理和报警系统,及时发现和处理系统故障,保证系统的正常运行。
四、设计计划和预期成果本设计计划分为以下几个阶段进行:1.需求调研和分析:对于自动配料控制系统的需求进行调研和分析,确定系统的功能和性能要求。
工厂配料控制系统开题报告

工厂配料控制系统开题报告1. 项目背景随着工业化和自动化的发展,越来越多的工厂需要进行配料控制,以确保产品质量的稳定性和生产效率的提高。
传统的手动配料控制已经无法满足大规模生产的需求,因此有必要开发一套工厂配料控制系统来实现自动化和精确化的配料过程。
2. 项目目标本项目旨在设计和开发一套工厂配料控制系统,实现以下目标:•实时监控原料库存情况,并根据生产计划进行配料计算;•控制配料设备,按照配料方案自动完成配料过程;•提供用户界面,方便操作人员监控和调整配料过程;•可以与其他工厂管理系统进行集成,实现信息共享和数据交互。
3. 项目计划为了顺利完成本项目,我们将按照以下计划进行开发:•需求分析阶段:明确项目需求和功能要求,制定详细的功能规格说明书;•概要设计阶段:根据需求分析结果,设计系统的整体结构和模块划分,确定技术选型;•详细设计阶段:对每个模块进行详细设计,包括数据库设计、接口设计等;•编码阶段:根据详细设计进行编码实现,并进行单元测试;•集成测试阶段:将各模块进行集成测试,并进行系统测试和性能测试;•部署阶段:将系统部署到实际生产环境中,并进行功能验收;•运维支持阶段:对系统进行运维和支持,修复漏洞和提供功能更新。
4. 技术选型根据项目需求和技术要求,我们选择以下技术进行开发:•后端开发语言:Python,具有丰富的库和框架支持,适合快速开发和扩展;•前端开发语言:JavaScript,使用React框架进行开发,可以实现交互性较强的用户界面;•数据库:采用关系型数据库MySQL,可以满足系统的数据存储和查询需求;•通信协议:使用TCP/IP协议进行设备间的通信,保证数据传输的可靠性和稳定性。
5. 预期成果通过本项目的开发,预期可以获得以下成果:•一套完整的工厂配料控制系统,可以实现自动化和精确化的配料过程;•可视化的用户界面,方便操作人员进行配料监控和调整;•数据库中存储的历史数据和统计报表,方便管理人员进行数据分析和决策;•可以与其他工厂管理系统进行集成,实现信息共享和数据交互;6. 风险分析在项目开发过程中,可能会面临以下风险:•技术风险:开发过程中可能会遇到技术难题,需要解决相关技术挑战;•人力风险:项目所需的开发人员和测试人员需要具备一定的技术和经验;•进度风险:项目开发过程中可能会遇到一些延误和调整,需要合理控制进度;•成本风险:项目开发过程需要一定的成本投入,需要合理控制成本。
自动送料开题报告

⾃动送料开题报告⾃动送料开题报告 随着当今社会科学技术的发展,各类物料输送的⽣产线对⾃动化程度的要求越来越⾼,原有的⽣产送装料设备已经远远的不能满⾜当前⾼度⾃动化的需要。
基于PLC的⾃动送料控制系统篇⼀: 摘要:可编程序控制器(Programmable controller)简称PLC,由于PLC的可靠性⾼、环境适应性强、灵活通⽤、使⽤⽅便、维护简单,所以PLC的应⽤领域在迅速扩⼤。
本⽂对送料⼩车系统中的控制系统进⾏研究和设计。
并针对送料⼩车应达到的控制要求利⽤PLC进⾏了⼩车控制的具体程序设计。
关键词:PLC,送料⼩车,控制,程序设计 1 ⽂献综述 1.1PLC研究现状、应⽤及前景 随着社会迅速的发展,各机械产品层出不穷。
控制系统的发展已经很成熟,应⽤范围涉及各个领域,例如:机械、化⼯、汽车制造、交通、军事、民⽤等。
长期以来,计算机控制和PLC控制⼀直是⼯业控制领域的两种主要控制⽅法[1]。
PLC⾃1969年问世以来,以其功能强、可靠性⾼、使⽤⽅便、体积⼩等优点在⼯化领域得到迅速推⼴,成为⼯业⾃动化领域中极具竞争⼒的控制⼯具。
⽽对当今的PLC⼏乎可以说凡是需要控制系统存在的地⽅就需要PLC。
尤其是近⼏年来,PLC的成本下降,功能⼜不段增强,所以⽬前PLC在国内外已被⼴泛应⽤于各个⾏业。
20世纪末期,可编程控制器的发展特点是更加适应于现代⼯业的需要。
随着系统能⼒的提⾼,PLC提供系统通信的能⼒,构成了可编程控制系统,⼈机界⾯逐步完善,具有离散量和模拟量数据采集系统的监控能⼒[2、3]。
从控制规模上来说,这个时期发展了⼤型机和超⼩型机;从控制能⼒上来说,诞⽣了各种各样的特殊功能单元,⽤于压⼒、温度、转速、位移等各式各样的控制场合;从产品的配套能⼒来说,⽣产了各种⼈机界⾯单元、通信单元,使应⽤可编程控制器的⼯业控制设备的配套更加容易[4、5、6]。
⽬前,可编程控制器在机械制造、⽯油化⼯、冶⾦钢铁、汽车、轻⼯业等领域的应⽤都得到了长⾜的发展。
(完整版)自动配料系统开题报告与任务书
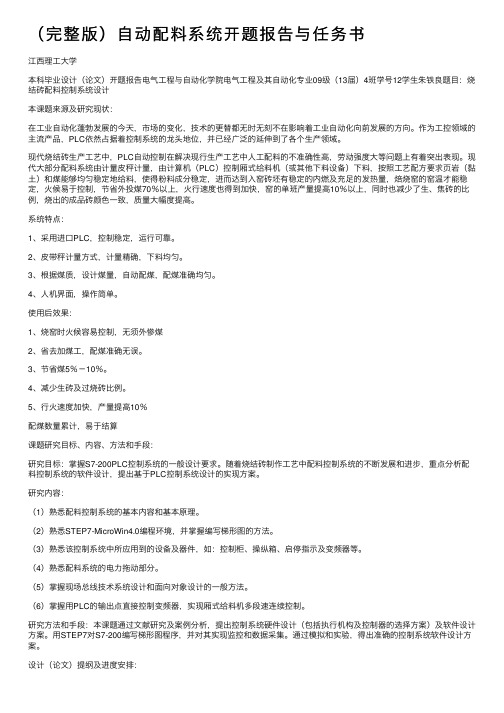
(完整版)⾃动配料系统开题报告与任务书江西理⼯⼤学本科毕业设计(论⽂)开题报告电⽓⼯程与⾃动化学院电⽓⼯程及其⾃动化专业09级(13届)4班学号12学⽣朱铁良题⽬:烧结砖配料控制系统设计本课题来源及研究现状:在⼯业⾃动化蓬勃发展的今天,市场的变化,技术的更替都⽆时⽆刻不在影响着⼯业⾃动化向前发展的⽅向。
作为⼯控领域的主流产品,PLC依然占据着控制系统的龙头地位,并已经⼴泛的延伸到了各个⽣产领域。
现代烧结砖⽣产⼯艺中,PLC⾃动控制在解决现⾏⽣产⼯艺中⼈⼯配料的不准确性⾼,劳动强度⼤等问题上有着突出表现。
现代⼤部分配料系统由计量⽪秤计量,由计算机(PLC)控制厢式给料机(或其他下料设备)下料,按照⼯艺配⽅要求页岩(黏⼟)和煤能够均匀稳定地给料,使得粉料成分稳定,进⽽达到⼊窑砖坯有稳定的内燃及充⾜的发热量,焙烧窑的窑温才能稳定,⽕候易于控制,节省外投煤70%以上,⽕⾏速度也得到加快,窑的单班产量提⾼10%以上,同时也减少了⽣、焦砖的⽐例,烧出的成品砖颜⾊⼀致,质量⼤幅度提⾼。
系统特点:1、采⽤进⼝PLC,控制稳定,运⾏可靠。
2、⽪带秤计量⽅式,计量精确,下料均匀。
3、根据煤质,设计煤量,⾃动配煤,配煤准确均匀。
4、⼈机界⾯,操作简单。
使⽤后效果:1、烧窑时⽕候容易控制,⽆须外惨煤2、省去加煤⼯,配煤准确⽆误。
3、节省煤5%-10%。
4、减少⽣砖及过烧砖⽐例。
5、⾏⽕速度加快,产量提⾼10%配煤数量累计,易于结算课题研究⽬标、内容、⽅法和⼿段:研究⽬标:掌握S7-200PLC控制系统的⼀般设计要求。
随着烧结砖制作⼯艺中配料控制系统的不断发展和进步,重点分析配料控制系统的软件设计,提出基于PLC控制系统设计的实现⽅案。
研究内容:(1)熟悉配料控制系统的基本内容和基本原理。
(2)熟悉STEP7-MicroWin4.0编程环境,并掌握编写梯形图的⽅法。
(3)熟悉该控制系统中所应⽤到的设备及器件,如:控制柜、操纵箱、启停指⽰及变频器等。
自动配料装车系统开题报告

自动配料装车系统开题报告自动配料装车系统开题报告一、引言自动配料装车系统是一种应用于物流行业的先进技术,通过自动化设备和智能控制系统,实现了物料的自动配料和装车,提高了生产效率和减少了人力成本。
本文将对自动配料装车系统进行深入研究,探讨其原理、优势和应用前景。
二、系统原理自动配料装车系统主要由配料设备、输送设备、控制系统和装车设备组成。
首先,通过配料设备将不同种类的物料按照一定比例混合,然后通过输送设备将混合物料输送至装车设备,最后由控制系统自动将物料装载至车辆中。
整个过程中,控制系统根据预设的配料方案和装车要求,自动控制设备的运行和物料的配送,实现了高效、准确的装车操作。
三、系统优势1. 提高生产效率:自动配料装车系统能够实现物料的快速、准确配料和装车,大大缩短了生产周期,提高了生产效率。
相比传统的人工配料和装车方式,自动化系统能够减少人力投入,降低了人力成本。
2. 降低错误率:自动配料装车系统通过智能控制系统,能够准确按照预设的配料方案进行操作,避免了人为因素导致的错误。
系统能够精确计量物料的重量和比例,保证了产品质量的稳定性。
3. 提高安全性:自动配料装车系统采用了先进的安全措施,如防爆装置、防滑装置等,有效保障了操作人员和设备的安全。
系统还能够实时监测设备运行状态,及时发现并处理异常情况,避免了事故的发生。
四、应用前景自动配料装车系统在物流行业中有着广阔的应用前景。
首先,该系统能够适用于各种物料的配料和装车,包括粉状物料、液体物料和固体物料等,适用范围广泛。
其次,自动化系统能够根据生产需求进行灵活调整,实现多品种、小批量的生产,满足个性化需求。
此外,随着物流行业的发展和技术的进步,自动配料装车系统将不断优化和升级,提高系统的智能化和自动化水平,进一步提升生产效率和产品质量。
五、结论自动配料装车系统作为一种先进的物流技术,具有很高的应用价值和发展潜力。
通过自动化设备和智能控制系统,该系统能够实现物料的自动配料和装车,提高生产效率、降低错误率,并提高安全性。
开题报告
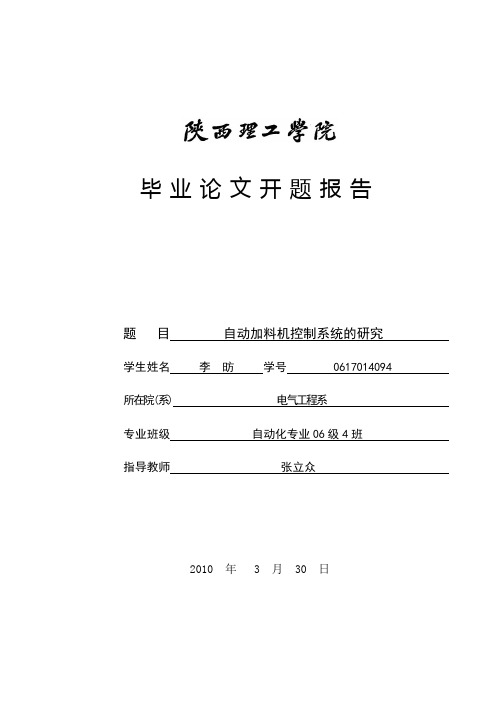
控制系统的控制器有单片机89C51和扩展电路组成,单片机控制继电器,继电器控制交流接触器,又由接触器控制电机等执行机构的运动。本控制系统可以根据送料工艺的需要,设置两条生产线的输送、排料、满料、空料等参数值,也可装载系统前次工艺参数值。
毕业论文开题报告
题目自动加料机控制系统的研究
学生姓名李昉学号**********
所在院(系)电气工程系
专业班级自动化专业06级4班
指导教师张立众
2010年3月30日
题目
自动加料机控制系统
一、选题的目的及研究意义
在现代科学技术的许多领域中,自动控制技术起这愈来愈重要的作用,并且,随着生产和科学技术的发展,自动化水平也越来越高。自动控制利用控制装置使被控对象的某个参数自动的按照预定的规律运行。本设计的自动加料机控制系统就是采用自动控制技术来实现功能的,这样就大大提高了工作的效率,整个过程又快又稳。本设计的由单片机控制的自动加料系统是与料斗式干燥机配套的加料系统。根据加料工艺要求,其工作原理是:先将真空管关闭,启动电机,用低真空气流将塑料树脂粒子送入真空管,电机停转,再将粒子排入料斗,如此循环。
5、在连接键盘电路采用8255A为扩展并行口时,要在中间加一个74LS373,它可以作为单片机外部一个扩展输入口。
6、2864A与AT89C51连接时,需要在单片机外部增加地址锁存器。
四、检索与本课题有关参考文献资料的简要说明
- 1、下载文档前请自行甄别文档内容的完整性,平台不提供额外的编辑、内容补充、找答案等附加服务。
- 2、"仅部分预览"的文档,不可在线预览部分如存在完整性等问题,可反馈申请退款(可完整预览的文档不适用该条件!)。
- 3、如文档侵犯您的权益,请联系客服反馈,我们会尽快为您处理(人工客服工作时间:9:00-18:30)。
毕业设计开题报告
自动加料机控制系统
院别:电子工程学院
班级:通信0501班
学生姓名:罗勇
指导教师:张骥祥
2008年12月2日
开题报告填写要求
1.开题报告作为毕业设计答辩委员会对学生答辩资格审查的依据材料之一,应在指导教师指导下,由学生在毕业设计工作前期完成,经指导教师签署意见、专家组及系主任审查后生效;
2.开题报告必须用黑墨水笔工整书写或按教务处统一设计的电子文档标准格式(可从教务处网页上下载)打印,禁止打印在其它纸上后剪贴;
3.毕业设计的开题报告应包括以下内容:
(1)主要技术指标;
(2)工作思路;
(3)课题的准备情况及进度计划;
(4)参考文献。
4.开题报告的撰写应符合科技文献规范,且不少于2000字;参考文献应不少于15篇,包括中外文科技期刊、教科书、专著等。
5.开题报告正文字体采用宋体小四号,1.5倍行距。
附页为A4纸型,左边距3cm,右边距2cm,上下边距为2.5cm,字体采用宋体小四号,1.5倍行距。
6.“课题性质”一栏:
理工类:A.理论研究B.应用研究C工程设计D.软件开发E.其它
经管文教类:A.理论研究 B.应用研究 C.实证研究 D.艺术创作E.其它
“课题来源”一栏:
A.科研立项
B.社会生产实践
C.教师自拟
D.学生自选
“成果形式”一栏:
A.论文
B.设计说明书
C.实物
D.软件
E.作品
毕业设计开题报告
附页:
我的毕业设计是运用单片机AT89S52来实现自动加料控制系统。
在现代科学技术的许多领域中,自动控制技术起这愈来愈重要的作用,并且,随着生产和科学技术的发展,自动化水平也越来越高。
自动控制利用控制装置使被控对象的某个参数自动的按照预定的规律运行。
本设计的自动加料机控制系统就是采用自动控制技术来实现功能的,这样就大大提高了工作的效率,整个过程又快又稳。
(一)主要技术指标
(1)采用AT89S52单片机作为控制器控制步进电机。
(2)用数码管进行显示,用按键进行调整。
(3)使用反射式红外传感器进行工件计数。
(4)可实现步进电机平滑调速、对工件进行计数。
(5)分手动和自动两种工作模式。
(6)自动状态壳实现定时开关,定量开关。
(7)使用L298N电机驱动器对步进电机进行驱动。
AT89S52是一种低功耗、高性能CMOS8位微控制器,具有 8K 在系统可编程Flash 存储器。
使用Atmel 公司高密度非易失性存储器技术制造,与工业80C51 产品指令和引脚完全兼容。
片上Flash允许程序存储器在系统可编程,亦适于常规编程器。
在单芯片上,拥有灵巧的8 位CPU 和在系统可编程Flash,使得AT89S52为众多嵌入式控制应用系统提供高灵活、超有效的解决方案。
AT89S52具有以下标准功能: 8k 字节Flash,256字节RAM, 32 位I/O 口线,看门狗定时器,2 个数据指针,三个16 位定时器/计数器,一个6向量2级中断结构,全双工串行口,片内晶振及时钟电路。
另外,AT89S52 可降至0Hz 静态逻辑操作,支持2种软件可选择节电模式。
空闲模式下,CPU 停止工作,允许RAM、定时器/计数器、串口、中断继续工作。
掉电保护方式下,RAM内容被保存,振荡器被冻结,单片机一切工作停止,直到下一个中断或硬件复位为止.
(二)工作思路
本设计的由单片机控制的自动加料系统是根据加料工艺要求,其工作原理是:对传送带中的工件进行计数,可以定时启动电机或停止电机。
可以设定产量,使其自动停止。
可以改变传送带的传动速度以提高生产效率。
使用反射式红外传感器对工件进行计数,一对单位时间内生产产量进行计算。
用单片机来实现生产中的自动加料,须外接电机驱动器,我的设计采用市场上性能稳定驱动能力强的电机专用驱动芯片L298N,这样充分提高了电机的使用效率。
更提高了控制电机的能力,减小误差较,减少软件编程的复杂度.按照系统设计功能的要求,初步确定设计系统由主控模块、传感器模块、存储模块、键盘接口模块、显示模块和电机驱动模块共6个模块组成。
1.主控模块:以AT89S52单片机为核心。
2.传感器模块:采用反射式传感器JX-359-403W
3.存储模块:采用 AT24C02。
AT24C02是美国ATMEL公司的低功耗CMOS串行EEPROM,它
是内含256×8位存储空间,具有工作电压宽(2.5~5.5V)、擦写次数多(大于10000次)、写入速度快(小于10ms)等特点。
4.键盘接口模块:本设计共采用按键6个,分别与单片机的六个I/O管脚相连,功能分
别为手动/自动切换、启动/停止、加速、减速、定时启动停止、定产量停止。
5.显示模块:显示部分是由6个数码管显示4个一组显示生产数量。
两个一组显示定时
时间。
6.电机驱动模块:使用电机驱动器L298N并使用TP521光电耦合器进行抗干扰隔离。
原理图
(三)课题的准备情况及进度计划
进度计划:
(四)参考文献
[1] 李广弟单片机基础北京航空航天大学出版社 2006.
[2] 孙涵芳 MCS-51/96系列单片机原理及应用北京航空航天大学出版社 2006.
[3] 王福瑞单片微机测控系统设计大全北京航空航天大学出版社 2003.
[4] 余永权 89系列FLASH单片机原理与应用电子工业出版社 2000.
[5] 楼然苗、李光飞 51系列单片机设计实例北京航空航天出版社 2003.
[6] 何立民单片机高级教程-应用与设计北京航空航天大学出版社 2001.
[7] 蔡美琴 MCS-51单片机系统及其应用高等教育出版社 1999.
[8] 李华单片机原理与接口技术清华大学出版社 1999.
[9] 公茂法单片机人机接口实例集北京航空航天大学出版社 1998.
[10] 刘光潭中外集成电路简明速察手册电子工业出版社 2001.
[12] 李宏,张家田液晶显示器件应用技术机械工业出版社 2004 .
[13] 刘利液晶显示原理电子工业出版社 2002.
[14] 一九九九年产品目录(第一期)武汉力源股份有限公司 1999.
[15] MAXIM.NEW RELEASES DATA BOOK (VOLUME V),AMERICA,1998.。