论述塑料橡胶纤维的加工成型方法
2020年(塑料橡胶材料)橡胶制品的基本生产工艺过程

(塑料橡胶材料)橡胶制品的基本生产工艺过程橡胶制品的基本生产工艺过程4.1基本工艺流程伴随现代工业尤其是化学工业的迅猛发展,橡胶制品种类繁多,但其生产工艺过程,却基本相同。
以壹般固体橡胶(生胶)为原料的制品,它的生产工艺过程主要包括:原材料准备→塑炼→混炼→成型→硫化→休整→检验4.2原材料准备橡胶制品的主要材料有生胶、配合剂、纤维材料和金属材料。
其中生胶为基本材料;配合剂是为了改善橡胶制品的某些性能而加入的辅助材料;纤维材料(棉、麻、毛及各种人造纤维、合成纤维)和金属材料(钢丝、铜丝)是作为橡胶制品的骨架材料,以增强机械强度、限制制品变型。
在原材料准备过程中,配料必须按照配方称量准确。
为了使生胶和配合剂能相互均匀混合,需要对某些材料进行加工:生胶要在60--70℃烘房内烘软后,再切胶、破胶成小块;块状配合剂如石蜡、硬脂酸、松香等要粉碎;粉状配合剂若含有机械杂质或粗粒时需要筛选除去;液态配合剂(松焦油、古马隆)需要加热、熔化、蒸发水分、过滤杂质;配合剂要进行干燥,不然容易结块、混炼时旧不能分散均匀,硫化时产生气泡,从而影响产品质量;4.3塑炼生胶富有弹性,缺乏加工时的必需性能(可塑性),因此不便于加工。
为了提高其可塑性,所以要对生胶进行塑炼;这样,在混炼时配合剂就容易均匀分散在生胶中;同时,在压延、成型过程中也有助于提高胶料的渗透性(渗入纤维织品内)和成型流动性。
将生胶的长链分子降解,形成可塑性的过程叫做塑炼。
生胶塑炼的方法有机械塑炼和热塑炼俩种。
机械塑炼是在不太高的温度下,通过塑炼机的机械挤压和摩擦力的作用,使长链橡胶分子降解变短,由高弹性状态转变为可塑状态。
热塑炼是向生胶中通入灼热的压缩空气,在热和氧的作用下,使长链分子降解变短,从而获得可塑性。
4.4混炼为了适应各种不同的使用条件、获得各种不同的性能,也为了提高橡胶制品的性能和降低成本,必须在生胶中加入不同的配合剂。
混炼就是将塑炼后的生胶和配合剂混合、放在炼胶机中,通过机械拌合作用,使配合剂完全、均匀地分散在生胶中的壹种过程。
橡胶的成型方法

橡胶的成型方法
橡胶的成型方法有多种,具体选择的方法取决于橡胶制品的形状、尺寸、用途和生产要求。
以下是几种常见的橡胶成型方法:
1.压缩成型:压缩成型是最常见的橡胶成型方法之一。
将橡
胶原料放入加热的模具中,然后使用压缩机将模具封闭并
施加压力。
在加热和压力的作用下,橡胶原料会充分填充
模具,并在冷却后形成所需形状的橡胶制品。
2.注塑成型:注塑成型是通过将预热的橡胶原料注入到预先
设计好的模具中,然后使其冷却和固化形成所需的橡胶制
品。
注塑成型通常适用于生产大批量且相对简单的橡胶制
品,如密封件、垫圈等。
3.挤出成型:挤出成型适用于生产长条状、管状或其他截面
形状规则的橡胶制品。
通过加热和软化橡胶原料,将其推
入挤出机中的螺杆,并经过模具挤出,从而形成所需形状
的橡胶制品。
4.发泡成型:发泡成型是在橡胶中加入发泡剂,使其在成型
后产生气泡和孔隙,从而形成轻盈、柔软的橡胶发泡制品。
这种成型方式通常用于制作汽车座椅垫、鞋垫等。
除了上述成型方法,还有一些其他的橡胶成型方法,如真空成型、涂料成型等。
不同的成型方法在生产效率、成品质量、复杂度和适用范围等方面会有所差异。
在选择具体的成型方法时,需要综合考虑产品的要求、生产设备和生产环境等因素来确定
最合适的方法。
橡胶成形工艺技术

橡胶成形工艺技术橡胶成形是一种常见的制造橡胶制品的工艺技术,广泛应用于汽车、电子、机械等行业。
下面,我们将介绍橡胶成形的工艺流程和常见的成形方法。
橡胶成形的工艺流程一般包括原料准备、混炼、模具制造、成形、烧结和检验等步骤。
首先,根据产品要求选择或配制合适的橡胶原料,包括天然橡胶、合成橡胶和添加剂等。
然后,将原料进行混炼,通过加热、搅拌和塑化等工艺,使橡胶材料达到适宜的流动性和可塑性。
混炼后,根据产品设计要求制作模具,可以采用压缩模具、注塑模具、挤出模具等不同的制造方法。
在成形过程中,首先将混炼好的橡胶材料放入模具中,然后运用压力和温度等因素,使橡胶材料在模具中形成所需的形状。
其中,压缩成形方法是将橡胶材料放入模具中,然后通过加热和压力,使橡胶材料在模具中被压缩成形。
注塑成形方法是将橡胶材料加热熔化后注入模具中,并通过压力将橡胶材料填充到模具的每一个细小空间,然后冷却固化形成所需的形状。
挤出成形方法是将橡胶材料放入挤出机中,在高温和高压的作用下,通过挤出模具的形状,将橡胶材料挤出成形。
成形完成后,需要进行烧结处理,即将成型的橡胶制品进行加热,使橡胶材料中的化学反应发生,使橡胶制品达到适宜的硬度和强度。
最后,对成型的橡胶制品进行检验,包括外观检查、尺寸测量、性能测试等,确保橡胶制品的质量符合标准。
橡胶成形工艺技术的发展也在不断提升。
如今,随着3D打印技术的发展,橡胶成形也应用到了快速成型的工艺中。
通过设计和制作3D打印的模具,可以实现更加复杂和精细的橡胶成形。
此外,还有热流道技术和射出成形技术等也为橡胶成形带来了更大的改进和提高。
总之,橡胶成形工艺技术是一种成熟且广泛应用的制造技术。
通过科学的工艺流程和不断创新的成形方法,可以生产出高质量的橡胶制品,满足不同行业的需求。
随着技术的不断进步,相信橡胶成形工艺技术将在未来发展得更加完善和先进。
橡胶生产工艺介绍

橡胶生产工艺介绍橡胶生产工艺介绍1综述橡胶制品的主要原料是生胶、各种配合剂、以及作为骨架材料的纤维和金属材料,橡胶制品的基本生产工艺过程包括塑炼、混炼、压延、压出、成型、硫化6个基本工序。
橡胶的加工工艺过程主要是解决塑性和弹性矛盾的过程,通过各种加工手段,使得弹性的橡胶变成具有塑性的塑炼胶,在加入各种配合剂制成半成品,然后通过硫化是具有塑性的半成品又变成弹性高、物理机械性能好的橡胶制品。
2橡胶加工工艺2.1塑炼工艺生胶塑炼是通过机械应力、热、氧或加入某些化学试剂等方法,使生胶由强韧的弹性状态转变为柔软、便于加工的塑性状态的过程。
生胶塑炼的目的是降低它的弹性,增加可塑性,并获得适当的流动性,以满足混炼、亚衍、压出、成型、硫化以及胶浆制造、海绵胶制造等各种加工工艺过程的要求。
掌握好适当的塑炼可塑度,对橡胶制品的加工和成品质量是至关重要的。
在满足加工工艺要求的前提下应尽可能降低可塑度。
随着恒粘度橡胶、低粘度橡胶的出现,有的橡胶已经不需要塑炼而直接进行混炼。
在橡胶工业中,最常用的塑炼方法有机械塑炼法和化学塑炼法。
机械塑炼法所用的主要设备是开放式炼胶机、密闭式炼胶机和螺杆塑炼机。
化学塑炼法是在机械塑炼过程中加入化学药品来提高塑炼效果的方法。
开炼机塑炼时温度一般在80℃以下,属于低温机械混炼方法。
密炼机和螺杆混炼机的排胶温度在120℃以上,甚至高达160-180℃,属于高温机械混炼。
生胶在混炼之前需要预先经过烘胶、切胶、选胶和破胶等处理才能塑炼。
几种胶的塑炼特性:天然橡胶用开炼机塑炼时,辊筒温度为30-40℃,时间约为15-20min;采用密炼机塑炼当温度达到120℃以上时,时间约为3-5min。
丁苯橡胶的门尼粘度多在35-60之间,因此,丁苯橡胶也可不用塑炼,但是经过塑炼后可以提高配合机的分散性顺丁橡胶具有冷流性,缺乏塑炼效果。
顺丁胶的门尼粘度较低,可不用塑炼。
氯丁橡胶得塑性大,塑炼前可薄通3-5次,薄通温度在30-40℃。
高分子材料成型工艺

高分子材料成型工艺高分子材料是一种具有高分子量、由许多重复单元组成的材料,如塑料、橡胶和纤维等。
高分子材料的成型工艺是指将原料经过一系列加工工艺,使其具备特定形状和性能的过程。
本文将就高分子材料的成型工艺进行探讨,包括热塑性塑料和热固性塑料的成型工艺、注塑成型、挤出成型、吹塑成型、压延成型等内容进行详细介绍。
首先,热塑性塑料的成型工艺是指在一定温度范围内具有可塑性的塑料。
在加热软化后,通过模具加压成型,冷却后即可得到所需形状的制品。
而热固性塑料的成型工艺则是在一定温度范围内,通过热固化反应形成三维网络结构,使其成型后不再软化。
这两种成型工艺在实际生产中有着各自的特点和应用领域,需要根据具体情况选择合适的工艺。
其次,注塑成型是一种常见的高分子材料成型工艺,它是将熔融状态的塑料通过注射机注入模具中,经过一定的压力和温度条件下,塑料在模具中冷却凝固,最终得到所需的制品。
挤出成型是将塑料颗粒或粉末加热至熔融状态后,通过挤出机的螺杆推动,使塑料通过模具的特定截面形成连续的断面,冷却后得到所需的制品。
吹塑成型是将热塑性塑料加热软化后,通过气压吹塑成型。
压延成型是将热塑性塑料加热软化后,通过压延机的辊轧压成型。
这些成型工艺在高分子材料加工中起着至关重要的作用,不同的工艺适用于不同的产品类型和生产要求。
总的来说,高分子材料成型工艺是高分子材料加工中至关重要的一环,它直接影响着制品的质量和性能。
因此,在实际生产中,需要根据具体的材料特性、产品要求和生产条件选择合适的成型工艺,以确保生产出符合要求的制品。
同时,随着科技的不断进步和工艺的不断创新,高分子材料成型工艺也在不断发展和完善,为高分子材料的应用提供了更广阔的空间。
在实际生产中,需要根据具体的材料特性、产品要求和生产条件选择合适的成型工艺,以确保生产出符合要求的制品。
同时,随着科技的不断进步和工艺的不断创新,高分子材料成型工艺也在不断发展和完善,为高分子材料的应用提供了更广阔的空间。
橡胶件生产工艺

橡胶件生产工艺橡胶件是一种广泛应用于各个行业的重要零部件,它具有优良的耐磨性、耐腐蚀性和弹性等特点,广泛应用于汽车、航空、机械、电子等领域。
橡胶件的生产工艺对于产品的质量和性能有着至关重要的影响。
在本文中,将介绍橡胶件的常见生产工艺,以及每种工艺的特点和应用范围。
首先,常见的橡胶件生产工艺包括压制法、注塑法、挤出法和涂胶法等。
这些工艺在不同的应用领域和产品要求下具有各自的优势和适用性。
压制法是橡胶件生产中最常见的一种工艺。
它通过将橡胶材料放置在加热的模具中,施加压力使其充分热塑变形,然后冷却固化成型。
这种工艺适用于大批量生产,能够生产出具有一致性和精度的橡胶件。
然而,压制法对于橡胶材料的流动性要求较高,且模具成本较高。
注塑法是另一种常见的橡胶件生产工艺。
它与塑料件的注塑工艺类似,将橡胶材料加热熔化后注入模具中,经过冷却固化成型。
注塑法适用于生产精度要求较高的橡胶件,能够生产出形状复杂的产品。
但注塑法对于橡胶材料的流动性和热稳定性要求较高。
挤出法是将橡胶材料加热熔化后通过挤出机挤出成型的工艺。
这种工艺适用于生产长条状或管状的橡胶件,如密封条、管道等。
挤出法具有生产效率高、成本低的优势,但对于形状复杂的橡胶件不太适用。
涂胶法是将橡胶材料涂覆在另一种材料表面的工艺。
这种工艺适用于生产复合材料橡胶件,可以将橡胶材料与其他材料结合在一起,提高产品的性能和功能。
涂胶法可以应用于各种形状的橡胶件生产,但对于橡胶与其他材料的粘接性要求较高。
除了上述常见的生产工艺,橡胶件的生产还涉及到材料的选择和成型工艺的优化。
橡胶材料的选择对于产品的性能和寿命有着重要的影响,需要根据产品的使用环境和要求选择合适的材料。
成型工艺的优化可以提高产品的生产效率和质量,减少生产成本。
例如,采用先进的模具设计和制造技术,可以提高成型的精度和一致性;采用自动化生产线可以提高生产效率和减少人工成本。
综上所述,橡胶件生产工艺的选择应根据产品的要求和应用环境来确定。
纤维注塑工艺
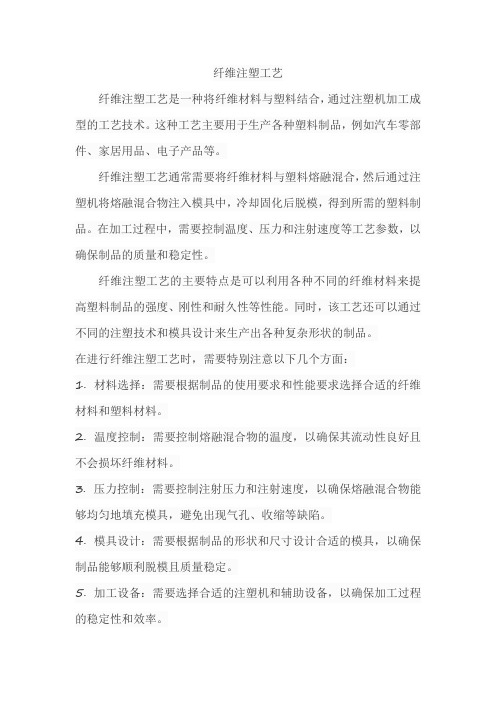
纤维注塑工艺
纤维注塑工艺是一种将纤维材料与塑料结合,通过注塑机加工成型的工艺技术。
这种工艺主要用于生产各种塑料制品,例如汽车零部件、家居用品、电子产品等。
纤维注塑工艺通常需要将纤维材料与塑料熔融混合,然后通过注塑机将熔融混合物注入模具中,冷却固化后脱模,得到所需的塑料制品。
在加工过程中,需要控制温度、压力和注射速度等工艺参数,以确保制品的质量和稳定性。
纤维注塑工艺的主要特点是可以利用各种不同的纤维材料来提高塑料制品的强度、刚性和耐久性等性能。
同时,该工艺还可以通过不同的注塑技术和模具设计来生产出各种复杂形状的制品。
在进行纤维注塑工艺时,需要特别注意以下几个方面:
1. 材料选择:需要根据制品的使用要求和性能要求选择合适的纤维材料和塑料材料。
2. 温度控制:需要控制熔融混合物的温度,以确保其流动性良好且不会损坏纤维材料。
3. 压力控制:需要控制注射压力和注射速度,以确保熔融混合物能够均匀地填充模具,避免出现气孔、收缩等缺陷。
4. 模具设计:需要根据制品的形状和尺寸设计合适的模具,以确保制品能够顺利脱模且质量稳定。
5. 加工设备:需要选择合适的注塑机和辅助设备,以确保加工过程的稳定性和效率。
总之,纤维注塑工艺是一种高效、灵活、可定制的工艺技术,可以广泛应用于各种塑料制品的生产中。
(完整版)高分子材料成型加工四种成型加工方法优缺点

1.压制成型:应用于热固塑料和橡胶制品的成型加工压制成型方法对于热固性塑料、橡胶制品和增强复合材料而言,都是将原料加入模具加压得到制品,成型过程都是一个物理—化学变化过程。
不同的是橡胶制品的成型中要对原料进行硫化。
橡胶通过硫化获得了必需的物理机械性能和化学性能。
而在复合材料压制成型过程中,还用到了层压成型(在压力和温度的作用下将多层相同或不同材料的片状物通过树脂的粘结和熔合,压制成层压塑料的成型方法)和手糊成型(以玻璃纤维布作为增强材料,均匀涂布作为黏合剂的不饱和聚酯树脂或环氧树脂的复合材料)。
2.挤出成型:适用于所有高分子材料,广泛用于制造轮胎胎面、内胎、胎管及各种断面形状复杂或空心、实心的半成品,也用于包胶操作。
挤出成型挤出成型对于高分子三大合成材料所用的设备和加工原理基本上是相同的。
有区别的是橡胶挤出是在压出机中对混炼胶加热与塑化,通过螺杆的旋转,使胶料在螺杆和料筒筒壁之间受到强大的挤压作用,不断向前推进,并借助于口型(口模)压出具有一定断面形状的橡胶半成品。
而合成纤维的挤出纺丝过程,采用三种基本方法:熔融纺丝、干法纺丝、湿法纺丝。
一般采用熔融纺丝(在熔融纺丝机中将高聚物加热熔融制成溶体,通过纺丝泵打入喷丝头,并由喷丝头喷成细流,再经冷凝而成纤维)。
3.注射成型:应用十分广泛,几乎所有的热塑性塑料及多种热固性塑料都可用此法成型,也可以成型橡胶制品。
注射成型高分子三大合成材料的注射成型过程中所用设备和工艺原理比较相似,但是从基本过程和要求看热固性塑料注射和热塑性塑料注射有很多不同之处。
热固性塑料的注射成型要求成型物料首先在温度相对较低的料筒内预塑化到半熔融状态,然后在随后的注射充模过程中进一步塑化,避免其因发生化学反应而使黏度升高,甚至交联硬化为固体。
塑料注射成型原料是粒状或粉状的塑料,而橡胶注射成型原料则是条状或块粒状的混炼胶,且混炼胶在注压入模后须停留在加热的模具中一段时间,使橡胶进行硫化反应。
- 1、下载文档前请自行甄别文档内容的完整性,平台不提供额外的编辑、内容补充、找答案等附加服务。
- 2、"仅部分预览"的文档,不可在线预览部分如存在完整性等问题,可反馈申请退款(可完整预览的文档不适用该条件!)。
- 3、如文档侵犯您的权益,请联系客服反馈,我们会尽快为您处理(人工客服工作时间:9:00-18:30)。
论述塑料橡胶纤维的加工成型方法
塑料橡胶纤维是一种常见的合成纤维材料,其加工成型方法主要包括以下几种:
1. 纺丝法:将塑料橡胶颗粒加热至熔化状态,通过纺丝机将熔融的塑料橡胶挤出成连续的纤维。
这种方法适用于生产连续纤维,如涤纶、尼龙等。
2. 拉伸法:将塑料橡胶加热至柔软状态,然后通过拉伸和扩展的方式将其形成纤维状。
这种方法适用于生产短纤维,如纺织用弹性纤维。
3. 旋转纺丝法:将塑料橡胶颗粒放置在旋转的模具中,通过离心力将熔融的塑料橡胶喷射到模具内壁上,在模具内壁上形成纤维状。
这种方法适用于生产具有特殊结构的纤维,如中空纤维。
4. 涂覆法:将塑料橡胶溶解在有机溶剂中,然后通过涂布或喷涂的方式将溶解的塑料橡胶均匀地涂覆在基材上,最后通过干燥将溶剂蒸发,形成纤维状。
这种方法适用于生产涂层纤维,如涂层织物和涂层线。
以上是几种常见的塑料橡胶纤维加工成型方法,每种方法都有其适用的场景和特点,具体选择哪种方法取决于产品的要求和工艺的要求。