电动汽车电池包设计流程
pack电池生产线流程

pack电池生产线流程一、引言pack电池是一种广泛应用于电动汽车、储能系统等领域的重要组件,其生产线流程对于保证产品质量、提高生产效率具有重要意义。
本文将介绍pack电池生产线的整体流程,包括原材料准备、电池模组制造、电池模组测试、装配与封装等环节。
二、原材料准备1. 正极材料准备:包括正极片、集流体等材料的采购、入库,确保其质量符合要求。
2. 负极材料准备:包括负极片、集流体等材料的采购、入库,确保其质量符合要求。
3. 隔膜材料准备:包括隔膜片的采购、入库,确保其质量符合要求。
4. 电解液准备:包括正极材料、负极材料等的混合制备,确保电解液配比准确。
三、电池模组制造1. 正负极片涂布:将正极材料和负极材料分别涂布在集流体上,形成正负极片。
2. 隔膜贴合:将涂布好的正负极片与隔膜片按一定顺序叠压在一起,形成电池模组。
3. 压缩和固化:通过一定的压力和温度条件,使电池模组中的材料紧密结合,提高电池的稳定性和性能。
4. 切割和成品检验:将固化后的电池模组进行切割,形成标准尺寸的电池单体,并进行成品检验,确保电池单体质量合格。
四、电池模组测试1. 电性能测试:对电池模组进行放电和充电测试,检测其电压、电流、容量等参数,以验证其性能是否符合设计要求。
2. 循环寿命测试:对电池模组进行多次充放电循环,模拟实际使用情况,评估其循环寿命和容量衰减情况。
3. 安全性能测试:对电池模组进行过充、过放、短路等安全性能测试,确保其在异常情况下不会发生爆炸或火灾等安全问题。
五、装配与封装1. 电池模组装配:将通过测试的电池模组按照一定的数量和排列方式进行装配,形成pack电池组。
2. 电池组保护:对pack电池组进行保护措施,包括防尘、防水、防震等,确保其在使用过程中能够安全稳定运行。
3. 封装:将装配好的pack电池组进行封装,形成最终的pack电池产品。
4. 成品检验:对封装好的pack电池产品进行成品检验,确保其质量符合要求。
汽车设计-新能源汽车动力电池(PACK)的设计
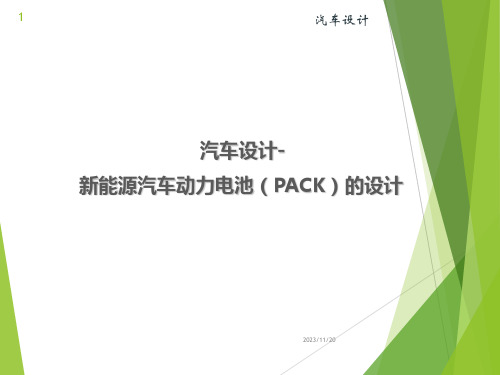
2023/11/20
3
动力电池的组成:
汽车设计
单体动力电池:构成动力电池模块的最小单元。一般由正极、负极、电解质、隔膜、外壳及端子(极 端)等组合而成,可实现电能与化学能之间的直接转换。
电池模组/电池模块:单体电池通过串联和并联在物理结构和电路上连接起来构成动力电池包或最小分 组,可作为一个单元替换。
a)人体触电防护 b)静电防护 c)电磁干扰防护
2023/11/20
20
电气安全设计:
4.电气隔离 (1)电气间隙
定义:在两个导电零部件之间或导电零部件与 设备防护界面之间测得的最短空间距离。即在保 证电气性能稳定和安全的情况下,通过空气能实 现绝缘的最短距离。
汽车设计
(2)爬电距离 定义:在两个导电部分之间沿绝缘材料表面的
(E1、E2、E3、En为各个电池的电动势)
E=nE1(各个电池电势差相同)
汽车设计
4、串联电池组的内阻
R0 R1 R2 R3 Rn
●如果每个电池的内阻相同则
R 0 nR 1
5、串联电池组所供给的电流
串联电池组与负载电阻R构成闭合回路时
I
E1 E2 E3 En R R 1 R 2 R 3 R n
2023/11/20
4
从单体到系统——单体电池:
铝壳包装而成的电 池,采用激光封口 工艺,全密封,铝 壳技术已非常成熟, 且对材料技术,如 气胀率、膨胀率等 指标,要求不高。
汽车设计
软包即软包锂电池,是在液 态锂离子电池套上一层聚合 物外壳的电池,采用铝塑复 合膜包装,软包锂电池的机 械强度不高,在出现安全事 故如内短路等情况下,电池 容易鼓起排气,降低了爆炸 风险。
1
汽车设计
电池PACK生产工艺流程

扫码
测试
测试结果
三、详细工艺
1.8 模组成型 工作内容:将模块、链接铜片、支撑板,利用螺丝组装成模组,并粘贴条码。 设备:无。 工装和工具:气动扳手及套筒 ;扭力扳手及套筒; 工艺要求:扭力符合标准、模块正负极摆放正确。
三、详细工艺
2.预加工段 进行动力电缆加工、螺杆加工、线束加工、铜排加工、BMS检测及组装、高压板
二、工艺流程
三、详细工艺
按照工艺流程图,对每个工段和每个工位的工作内容、设备、人员进行分 解。 1、点焊段
利用分选机对电芯进行分选,分选后的电芯组装成模块、张贴条码,焊接 正负极镀镍钢片,检查焊点,测试模块的电压内阻并扫码记录数据,合格的模 块组装成模组。
三、详细工艺
1.1 电芯分选和模块组装 工作内容:设置分选机的分选参数,对电芯进行扫码、测试内阻、测试电压, 从分选机良品通道里面取出电芯,对于分选机不良品通里面的不合格电芯进行 标识隔离。 设备:分选机。 工装和工具:模块组装工作台。 工艺要求:内阻≤20mΩ,压差≤5mV,需同体系同等级电芯,且电芯无凸起 、凹陷、变形。
2.3热缩管裁切 工作内容:裁切热缩管至要求长度; 设备:热缩管裁切机; 工装和工具:无。
裁切机
三、详细工艺
2.4波纹管裁切 工作内容:裁切波纹管至要求长度; 设备:波纹管裁切机; 工装和工具:无。
波纹管裁切机
三、详细工艺
2.5电缆套管及热缩 工作内容:将裁切好的波纹管和热缩管套到电缆上,并利用热风枪热缩热缩管; 设备:无; 工装和工具:热缩枪 。
三、详细工艺
1.4 等离子清洗
工作内容:等离子清洗是使用等离子设备对组装后模块所有正负极进行清洁, 保证焊接质量。 设备:等离子清洗机。 工装和工具:模块定位夹具。 工艺要求:管控清洗速度及清洗时间,无明显异物。
电池包生产工艺
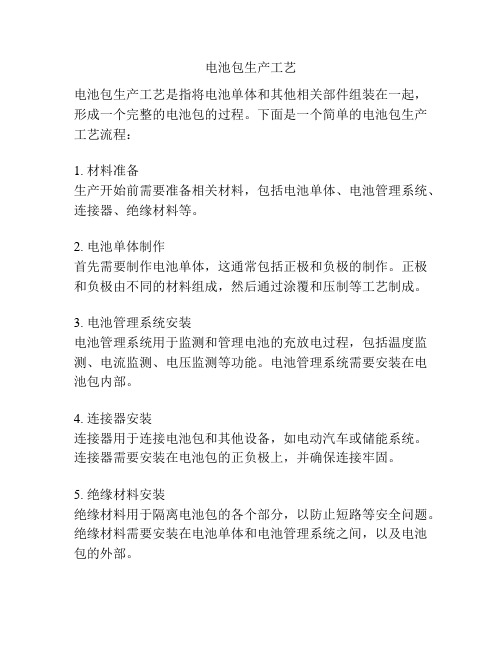
电池包生产工艺电池包生产工艺是指将电池单体和其他相关部件组装在一起,形成一个完整的电池包的过程。
下面是一个简单的电池包生产工艺流程:1. 材料准备生产开始前需要准备相关材料,包括电池单体、电池管理系统、连接器、绝缘材料等。
2. 电池单体制作首先需要制作电池单体,这通常包括正极和负极的制作。
正极和负极由不同的材料组成,然后通过涂覆和压制等工艺制成。
3. 电池管理系统安装电池管理系统用于监测和管理电池的充放电过程,包括温度监测、电流监测、电压监测等功能。
电池管理系统需要安装在电池包内部。
4. 连接器安装连接器用于连接电池包和其他设备,如电动汽车或储能系统。
连接器需要安装在电池包的正负极上,并确保连接牢固。
5. 绝缘材料安装绝缘材料用于隔离电池包的各个部分,以防止短路等安全问题。
绝缘材料需要安装在电池单体和电池管理系统之间,以及电池包的外部。
6. 组装和封装将电池单体、电池管理系统、连接器和绝缘材料等组装在一起,并进行电池包的封装。
封装通常采用胶水、热收缩膜或其他密封材料,以确保电池包的密封性和安全性。
7. 测试和质检完成组装和封装后,需要对电池包进行测试和质检,以确保其性能和质量符合标准要求。
测试包括电池容量测试、循环寿命测试、安全性测试等。
8. 包装和出厂通过包装和标签贴纸等工艺,将电池包包装好,并做好相应的标识。
然后进行入库或出厂销售。
以上是电池包生产的简单工艺流程,实际生产中可能会根据不同的电池类型和生产要求有所差异。
此外,为了确保电池包的质量和安全性,生产过程中需要严格遵守相关安全规定,并进行必要的培训和防护措施。
动力电池pack生产工艺流程
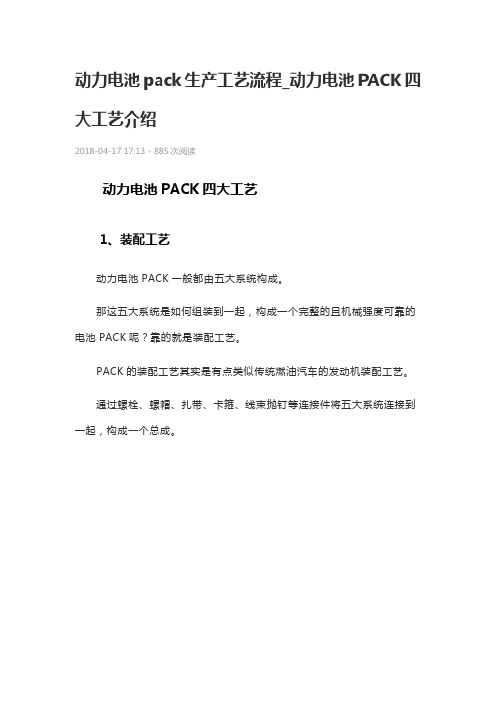
动力电池pack生产工艺流程_动力电池PACK四大工艺介绍2018-04-17 17:13 • 885次阅读动力电池PACK四大工艺1、装配工艺动力电池PACK一般都由五大系统构成。
那这五大系统是如何组装到一起,构成一个完整的且机械强度可靠的电池PACK呢?靠的就是装配工艺。
PACK的装配工艺其实是有点类似传统燃油汽车的发动机装配工艺。
通过螺栓、螺帽、扎带、卡箍、线束抛钉等连接件将五大系统连接到一起,构成一个总成。
2、气密性检测工艺动力电池PACK一般安装在新能源汽车座椅下方或者后备箱下方,直接是与外界接触的。
当高压电一旦与水接触,通过常识你就可以想象事情的后果。
因此当新能源汽车涉水时,就需要电池PACK有很好的密封性。
动力电池PACK制造过程中的气密性检测分为两个环节:1)热管理系统级的气密性检测;2)PACK级的气密性检测;国际电工委员会(IEC)起草的防护等级系统中规定,动力电池PACK 必须要达到IP67等级。
2017年4月份的上海车展,上汽乘用车就秀出了自己牛逼的高等级气密性防护技术。
将充电状态下的整个PACK放到金鱼缸中浸泡7天,金鱼完好无损,且PACK内未进水。
3、软件刷写工艺没有软件的动力电池PACK,是没有灵魂的。
软件刷写也叫软件烧录,或者软件灌装。
软件刷写工艺就是将BMS控制策略以代码的形式刷入到BMS中的CMU和BMU中,以在电池测试和使用过程中将采集的电池状态信息数据,由电子控制单元进行数据处理和分析,然后根据分析结果对系统内的相关功能模块发出控制指令,最终向外界传递信息。
4、电性能检测工艺电性能检测工艺是在上述三个工艺完成后,即产品下线之前必做的检测工艺。
电性能检测分三个环节:1)静态测试:绝缘检测、充电状态检测、快慢充测试等;2)动态测试;通过恒定的大电流实现动力电池容量、能量、电池组一致性等参数的评价。
3)SOC调整;将电池PACK的SOC调整到出厂的SOCSOC:StateOfCharge,通俗的将就是电池的剩余电量。
电池PACK生产工艺流程

三、详细工艺
2.2端子压接 工作内容:扣压电缆线两端端子。 设备:端子压接机; 工装和工具: 压接机配套扣压模具。
三、详细工艺
2.3热缩管裁切 工作内容:裁切热缩管至要求长度; 设备:热缩管裁切机; 工装和工具:无。
裁切机
三、详细工艺
2.4波纹管裁切 工作内容:裁切波纹管至要求长度; 设备:波纹管裁切机; 工装和工具:无。
波纹管裁切机
三、详细工艺
2.5电缆套管及热缩 工作内容:将裁切好的波纹管和热缩管套到电缆上,并利用热风枪热缩热缩管; 设备:无; 工装和工具:热缩枪 。
三、详细工艺
6.1 出货检查
工作内容:检查插接件是否插紧,检查紧固件是否安装牢靠,安装防水垫圈,粘贴铭牌
和高压标识等,在高压连接器上粘贴高温胶带;
设备:铭牌打印机;
工装和工具: 无。
高压标识
高温胶带
防水垫
铭牌
电池包条码
三、详细工艺
6.2 安装箱盖 工作内容:将箱盖安装到箱体上,并用螺栓锁固,利用检漏仪测试箱体气密性; 设备:无; 工装和工具: 风批及批嘴。
三、详细工艺
1.6 焊点检查 工作内容:利用陶瓷起子翘焊点,检查是否有虚焊情况,虚焊的需要返修。 设备:无 工装和工具:陶瓷起子 。 工艺要求:焊接位置正确,无焊穿,炸火,虚焊不良,符合拉来标准≥10kg。
焊点检查
三、详细工艺
1.7 模块测试 工作内容:模块扫码,测试内阻和电压,自动储存到到电脑里面; 设备:无扫码枪,电脑,3562测试仪,测试笔; 工装和工具:无。 工艺要求:电压、内阻符合要求。
电池包生产工艺流程
电池包生产工艺流程1.原材料准备:电池包的主要原材料包括正极材料、负极材料、隔膜材料、电解液和外壳材料。
这些材料需要经过严格的筛选和测试,确保其质量符合要求。
2.正负极制备:首先,正负极材料需要经过混合和烘烤等处理,以达到一定的化学组成和物理性能。
然后,将正负极材料分别涂覆在铜箔和铝箔上,并通过烘烤等步骤使其形成一定的结构和电化学性能。
3.隔膜准备:隔膜材料用于隔离正极和负极,防止短路和其他不良反应的发生。
隔膜材料通常是一种多孔的薄膜,需要经过切割和处理,以适应电池包的尺寸和形状。
4.组装工艺:在组装工艺中,需要将正负极材料和隔膜按照一定的层叠方式叠放在一起,形成电池的结构。
通常情况下,将正负极和隔膜一层层叠加,并通过压力和温度等条件进行固定。
5.注液:在组装好电池结构后,需要通过注液的方式将电解液注入电池包中。
电解液的注入量需要严格控制,以确保电池内部的化学反应正常进行,并且不会发生外泄或其他安全问题。
6.封装和包装:电池包组装完成后,还需要对电池包进行封装和包装。
封装一般通过热融胶或压合等方式进行,以确保电池内部的结构稳定和安全。
同时,还需要对电池包进行标识和包装,以方便运输和使用。
7.产品测试:最后一步是对电池包进行产品测试。
这个过程通常包括外观检验、性能测试和安全测试等。
外观检验主要检查电池包的外观质量是否符合要求;性能测试包括容量、电压、内阻等参数的测试;安全测试主要检查电池包的安全性和稳定性。
总结起来,电池包的生产工艺流程包括原材料准备、正负极制备、隔膜准备、组装工艺、注液、封装和包装以及产品测试等环节。
这些步骤的每个细节都需要严格控制,以确保生产出符合质量标准和安全要求的电池产品。
纯电动汽车电池包设计分析
纯电动汽车电池包设计分析纯电动汽车电池包设计分析纯电动汽车的电池包设计是关键的一步,它直接关系到车辆的性能、续航里程和安全性。
以下是一个分步思考的电池包设计分析:第一步:需求分析在设计电池包之前,我们需要先确定需求。
这包括车辆的预期续航里程、最大充电速度和最大放电功率等。
根据这些需求,我们可以计算出电池包的容量和功率。
第二步:电池选择根据需求,我们需要选择适合的电池类型和规格。
常见的电池类型包括锂离子电池、镍氢电池等。
我们需要考虑电池的能量密度、功率密度、寿命和成本等因素,并选择最合适的电池。
第三步:电池模块设计电池包通常由多个电池模块组成,每个电池模块又由多个电池单体组成。
在设计电池模块时,我们需要考虑到电池单体的连接、散热和安全等问题。
同时,我们还需要设计电池模块的外壳和连接器。
第四步:电池管理系统设计电池管理系统(BMS)是电池包的关键组成部分,它负责监测和控制电池的充放电过程,以确保电池的性能和安全。
BMS需要设计相应的硬件和软件,包括电池监测电路、温度传感器和电池状态估计算法等。
第五步:安全性设计电池包的安全性是非常重要的,特别是在充电和放电过程中。
我们需要设计相应的保护措施,如过流保护、过压保护、过温保护等。
此外,我们还需要考虑电池包的防火和防爆设计。
第六步:结构设计电池包的结构设计需要考虑到电池的布局、散热和机械强度等因素。
我们需要选择适当的材料和结构,以确保电池包的稳定性和安全性。
第七步:系统集成在设计完成后,我们需要将电池包与整车系统进行集成。
这包括电池包与电动机、控制器和充电系统等的连接和优化。
同时,我们还需要进行相应的测试和验证,以确保电池包的性能和安全。
通过以上的分步思考,我们可以设计出性能优良、安全可靠的电池包,为纯电动汽车的发展做出贡献。
电动汽车电池包的机械结构设计与制造
电动汽车电池包的机械结构设计与制造随着环境保护意识的增强和能源危机的日益严重,电动汽车作为一种清洁能源交通工具,受到了越来越多的关注。
而电动汽车的核心部件之一,电池包,对于整个车辆的性能和安全性起着至关重要的作用。
本文将探讨电动汽车电池包的机械结构设计与制造。
一、电动汽车电池包的机械结构设计电动汽车电池包的机械结构设计主要包括外壳设计、冷却系统设计以及固定系统设计。
外壳设计是电池包机械结构设计的重要组成部分。
外壳应具备良好的强度和刚度,能够承受外界的冲击和振动。
同时,外壳还需要具备防水、防尘、防腐蚀等功能,以保护电池包内部的电池单体。
材料的选择和外形的设计都需要考虑到电池包的整体重量、散热性能以及制造成本等因素。
冷却系统设计是为了保证电池包的温度在安全范围内,避免过热引发火灾等安全事故。
冷却系统可以采用空气冷却、液体冷却或者两者的结合。
在设计过程中,需要考虑到冷却效果、冷却介质的选择、冷却系统与电池包的结合方式等因素。
固定系统设计是为了保证电池包在车辆运行过程中的稳定性和安全性。
固定系统需要考虑到电池包的重量、振动、冲击等因素,以确保电池包不会发生脱落或者移位。
同时,固定系统还需要考虑到电池包的拆卸和维修,以方便对电池包进行检修和更换。
二、电动汽车电池包的制造过程电动汽车电池包的制造过程主要包括电池单体的组装、电池包的组装以及测试等环节。
电池单体的组装是电池包制造的第一步。
电池单体的组装需要严格控制工艺参数,确保电池单体的质量和性能。
在组装过程中,需要进行电池单体的连接、固定和绝缘等工作。
同时,还需要进行电池单体的测试,以确保其符合设计要求。
电池包的组装是将多个电池单体组装成一个完整的电池包。
在组装过程中,需要进行电池单体的串联和并联,以满足电动汽车对电池包的电压和容量要求。
同时,还需要进行电池包的外壳安装、冷却系统的连接以及固定系统的安装等工作。
电池包的制造完成后,还需要进行测试以确保其质量和性能。
特斯拉电池包工艺流程
特斯拉电池包工艺流程特斯拉电池包工艺流程是特斯拉公司生产电动汽车电池时所采用的工艺流程。
下面将介绍特斯拉电池包工艺流程的主要步骤。
首先,特斯拉公司在生产电动汽车电池包之前,需要先准备电池单体。
电池单体是由正负极片和电解液组成的,特斯拉采用的是锂离子电池单体。
电池单体的制造包括材料混合、浆料制备、涂敷、干燥等步骤,并通过一系列的质量检测来验证电池单体的质量。
接下来,特斯拉将多个电池单体堆叠在一起,形成电池组。
这个过程称为电池组装。
电池组装包括电池单体间的连接、固定等操作,以确保电池单体在电池组中的位置和连接牢固可靠。
特斯拉采用的是软包电池组装技术,可以提高电池组的能量密度和安全性能。
然后,特斯拉将电池组连接到电池管理系统(BMS)。
电池管理系统是用来监测和控制电池组工作状态的装置。
它可以实时监测电池的电压、电流、温度等参数,并根据需要控制电池的放电和充电过程,以保证电池的安全性和性能。
接着,特斯拉将电池包安装到电动汽车中。
电池包安装包括将电池包固定在汽车底盘上,并与驱动系统和充电系统等部件进行连接。
这个过程需要精确的操作和严格的安全措施,以确保电池包的安全性和可靠性。
最后,特斯拉进行电池包的测试和质量检验。
测试和检验包括容量测试、低温测试、高温测试、充放电循环测试等多项项目,以验证电池包的性能和稳定性。
特斯拉公司注重产品质量,只有通过了严格的测试和检验的电池包才会被使用在特斯拉的电动汽车中。
总结起来,特斯拉电池包工艺流程包括电池单体制备,电池组装,连接到电池管理系统,安装到电动汽车中,以及测试和质量检验等步骤。
通过这些步骤,特斯拉可以生产出高质量、高性能的电动汽车电池包。
特斯拉电池包的工艺流程不仅关注产品的性能和安全性,还注重节能环保和可持续发展。
- 1、下载文档前请自行甄别文档内容的完整性,平台不提供额外的编辑、内容补充、找答案等附加服务。
- 2、"仅部分预览"的文档,不可在线预览部分如存在完整性等问题,可反馈申请退款(可完整预览的文档不适用该条件!)。
- 3、如文档侵犯您的权益,请联系客服反馈,我们会尽快为您处理(人工客服工作时间:9:00-18:30)。
○
注:●必须经历的过程,输出文件必须
热管理设计
根据电池的工作散热情况,确定电池组的最优排列与电池包内散热板的布置。
○
/6
固定结构设计
分析电池包在车身底部安装的最优位置。
●
7
线束设计与布置
确定电池包内单体电池的连接方式,并根据汽车的实际工作情况,确定电池与汽车外电路的连接方式。
线束连接图
●
8
空间校核、结构有限元分析
1、通过有限元分析电池包的安全稳定性
电池包设计流程
编制
审核
批准
日期
XXX新能源公司
设计开发流程图
序号
工作项目
说明
形成文件
责任部门
备注
1
安全性、功能性分析
1、通过文献检索、网络等手段得到国内外典型纯电动汽车、混合动力车型电池包的类型、研究与应用现状。
2、分析电池包工作环境与影响电池包安全性的因素。
3、根据电动汽车所需工作电压,分析电池包功能。
●
2
方案布置
1、根据车辆可布置空间,确定电池包的整体结构及布置位置。
2、根据汽车所需工作额定电压及单体电池的容量,确定电池包的设计方案。
●
3
总体结构设计
根据所需设计的电池容量与车身可布置空间,确定电池的排列,进而确定电池包总体结构。
电池包结构三维图
●
4
载荷分配校核
汽车安装电池包后,校核汽车的质心分布是否合理。