数控铣床编程概述
数控铣床基础编程
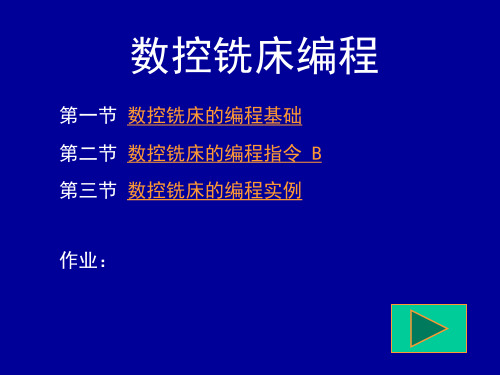
2.用φ10mm的刀具铣如图所示的槽,刀心轨迹为虚线,槽深
2mm,刀具位置如图,试编程。
3.用φ6刀具铣图示三个字母,刀心轨迹为虚线、深2mm
4.精铣题图所示的侧面,刀具直径φ10mm,采用刀 具半径补偿指令编程。
举例:型腔类零件加工 材料:铝合金 分析:槽宽14mm
刀具直径8mm 精度:粗、精加工一次 加工:精加工使用刀补 路线:粗加工
13.暂停指令G04 指令格式为:G04 P_ 钻孔、镗孔时,加工终了时,在刀具继续旋
转的同时停止刀具进给一段时间。 例:G04 P1 进给运动暂停1秒。
某些数控系统的设定单位为毫秒(mS)!
举例
第三节 编程举例: 1.如题图所示,刀心起点为工件零点O,按“O→A→B→C→D
→E”顺序运动,写出A、B、C、D、E各点的绝对、增量坐标值 (所有的点均在XOY平面内)。
精加工
粗加工轨迹
精加工轨迹
6.请根据以下程序推出刀具所走的路线,并划出路
线图 N10 G90 G92 X0 Y0 Z0 M03 S300 N20 G17 G02 X30 Y0 I15 J0 F300 N30 G01 X0 Y-40 N40 X-30 Y0 N50 G02 X0 Y0 I15 J0 N60 M05
现场加工(2)
编程加工如下零件,提交加工程序。
P239: 8 11 12
作业
夹具
铣刀
长度补偿
点位
轮廓
半径补偿
镜像
Y
30
-20 -10 0 -10
3 -20
-30
10 20 30 X 4
循环
工 件4
工 件6 工件24
工件
G01的功能下才可以生效。 操作时以刀具的实际长度值进行补偿。
数控铣床编程
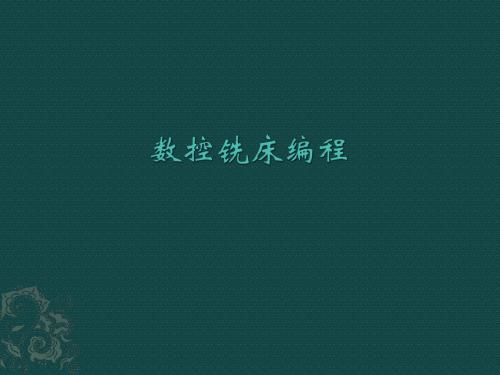
2)绝对值/增量值方式G90/G91 格式:G90/G91 X Y Z 3)尺寸单位选择G20/G21 G20:英制 G21 G21:公制 4)G00快速点定位 格式:G00 X Y Z X Y Z为目标点坐标值
5)G01直线插补 6)G02/G03圆弧插补 7)G04暂停 使刀具做无进给短暂的光整加工,一般用于 镗平面、锪孔等场合。 8)G27/G28/G29自动返回参考点 9)刀具补偿
2、加工工艺范围 1)平面类:一般只需两轴联动 2)变斜角类:最好用四轴或五轴控制 3)曲面类:一般采用三坐标联动
三、基本编程方法 1、坐标选择 1)机床坐标系 2)工件坐标系 选择原则: 选在零件的尺寸基准上 选在精度较高的工件表面 对称零件一般设在对称中心 一般零件,设在零件轮廓的某一角上 Z轴方向上的零点一般设ห้องสมุดไป่ตู้工件表面 应将刀具起点和程序原点设在同一位置
2、常用功能指令 (1)准备功能指令 1)工件坐标系设定指令G92 格式:G92 X Y Z(X Y Z为坐标原点到刀具起点 的有向距离) 通过设定刀具起点相对于坐标原点的位置建立工 件坐标系。 G92并不驱使机床刀具或工作台运动,只是通过 该指令确定刀具当前机床坐标位置相对于加工原 点(编程起点)的距离关系以建立工件坐标系。
1、数控铣床的用途和组成 分为立式和卧式 主要用于各类较复杂的平面、曲面和壳体类 零件的加工,特别适合于加工各种具有复杂 曲线轮廓及截面的零件,如模具等。 一般由数控系统、主传动系统、进给伺服系 统、冷却润滑系统等组成。
二、数控铣床编程基础 1、数控铣床的主要功能 1)点位控制 2)连续轮廓控制 3)半径补偿 4)长度补偿 5)比例及镜像加工 6)数据输入输出及DNC功能 7)数据采集功能 8)自诊断功能
数控铣床编程

三.螺旋线进给指令格式
X Y I_J _Z_;XY平面圆弧,G17可省略
G02 G18 G19 G03 X Z I_K _Y_;ZX平面圆弧 Y_Z_J_K_X_ ;YZ平面圆弧 Z Z_ Y_ X_ :为⊥圆弧面坐标轴的进给量。 例:G90 G17 G03 X30 Y30 I-30 J0 Z30 F100 O
R3=R R2 R1
X
例:见图32所示的刀具半径补偿程序。设加工开始时刀具距离工件表面 50mm,切削深度为10mm。
Y 50
A
b
B
N4 40 a 30 N6 20 d N7 10 与 D01 对应的补偿量 N2 O 10 20 30 40 50 X C N3 N5 c
图 32
刀补动作
按增量方式编程
小结
数控铣床加工范围; 数控铣床常用指令;
2. G00指令刀具相对于工件从当前位置以各轴预先设定的快移进给速度移
动到程序段所指定的下一个定位点。
G00指令中的快进速度由机床参数对各轴分别设定,不能用程序规定。由 于各轴以各自速度移动,不能保证各轴同时到达终点,因而联动直线轴 的合成轨迹并不总是直线。 快移速度可由面板上的进给修调旋钮修正。
数控铣床编程实例:轮廓加工
一、数控铣床常用指令
1 、 快速定位(G00)和直线加工(G01)
(1)快速定位指令格式: G00 X Y Z 。 以机床自身设定的最大移动速度沿直线或折线移动, 移动中不加工。 X Y Z 为终点坐标。 (2)直线加工指令格式: G01 X Y Z F 。 以给定的切削速度F 沿直线进给到X Y Z 指定点。 注:1. G00,G01为模态指令 2. F为模态代码,指定切削速度:在G00或新的F指令出 现以前,一直有效。
数控铣床编程讲解
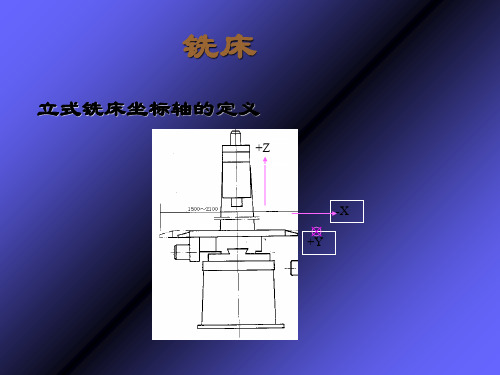
➢ 格式:
G17
G18
G19
该指令选择一个平面,在此平面中进行圆弧插补和刀
具半径补偿。
G17选择XY平面,G18选择ZX平面,G19选择YZ平面。
移动指令与平面选择无关。例如在规定了G17 Z_时,
Z轴照样会移动。
G17、G18、G19为模态功能,可相互注销,G17为缺省
值。
一、数控铣床常用编程指令
铣床
立式铣床坐标轴的定义
+Z
-X +Y
数控机床编程指令
一、数控铣床编程基本指令 二、数控铣床简化编程指令
一、数控铣床常用编程指令
5-1、M指令(或辅助功能)
表 3-2 指令 M03 M04 M05 M06 M08 M09 M19 M20 M30 M98 M99
功能 主轴正转 主轴反转 主轴停 换刀 切削液开 切削液关
O 20 40 60
N6 M30
%0002 N1 G91G01X20 Y15 N2 X20 Y30 N3 X20 Y-20 N4 X-60 Y-25 N5 M30
图8 两种指令方式
一、数控铣床常用编程指令
2、坐标系设定G92(此坐标最好不要动,要是动 了关机在开机就可消除)
格式:G92 X_ Y_ Z_
二、有关单位的设定
1、尺寸单位选择G20,G21,G22(一般我们会 使用的是G21公制,G20英制是外国人用的单位)
➢格式: G20 G21 G22
本系统采用3种尺寸输入制式:英制由G20指定,公制 由G21指定,脉冲当量由G22指定,缺省时采用公制。 3种制式下线性轴、旋转轴的尺寸单位如表4所示。
➢要取消刀具长度补偿时用指令G49或H00。 ➢G43、G44、G49都是模态代码,可相互注销。
数控铣床编程及加工

4、顺铣和逆铣对加工的影响
在铣削加工中,采用顺铣还是逆铣方式是影响加工表面 粗糙度的重要因素之一。铣削方式的选择应视零件图样 的加工要求,工件材料的性质、特点以及机床、刀具等 条件综合考虑。通常,由于数控机床传动采用滚珠丝杠 结构,其进给传动间隙很小,顺铣的工艺性就优于逆铣。 在铣削加工零件轮廓时应尽量采用顺铣加工方式;同时, 为了降低表面粗糙度值,提高刀具耐用度,对于铝镁合 金、钛合金和耐热合金等材料,尽量采用顺铣加工;但 如果零件毛坯为黑色金属锻件或铸件,表皮硬而且余量 一般较大,这时采用逆铣较为合理。
有些零件需要在不同的位置上重复加工同样的轮廓形 状,将这一轮廓形状的加工程序作为子程序,在需要的位 置上重复调用,就可以完成对该零件的加工。 8. 宏程序功能
该功能可用一个总指令代表实现某一功能的一系列指 令,并能对变量进行运算,使程序更具灵活性和方便性。
五、数控铣床所用刀具及其工艺特点
数控铣床和加工中心上使用的刀具主要有 铣削用刀具和孔加工用刀具两大类。
专用铣削夹具。
常用数控 铣削夹具
多工位夹具。适用于中批量生产。
气动或液压夹具。适用于生产批量较 大、不宜采用其他夹具的工件。
也经常采用平口虎钳、分度头和三爪 自定心卡盘等通用夹具。
通用夹具 (1)机用虎钳
(2) 三爪卡盘
1、夹具的刚度和夹紧力都要满足大切 削力的要求。
2、夹具结构不要妨碍刀具对工件各部 位的多面加工。
三、 数控铣床编程时应注意的问题
*了解数控系统的功能及规格。不同的数控系统在编写数 控加工程序时,在格式及指令上是不完全相同的。
*熟悉零件的加工工艺。 *合理选择刀具、夹具及切削用量、切削液。 *编程尽量使用子程序。 *程序零点的选择要使数据计算的简单。
数控铣床的操作与编程
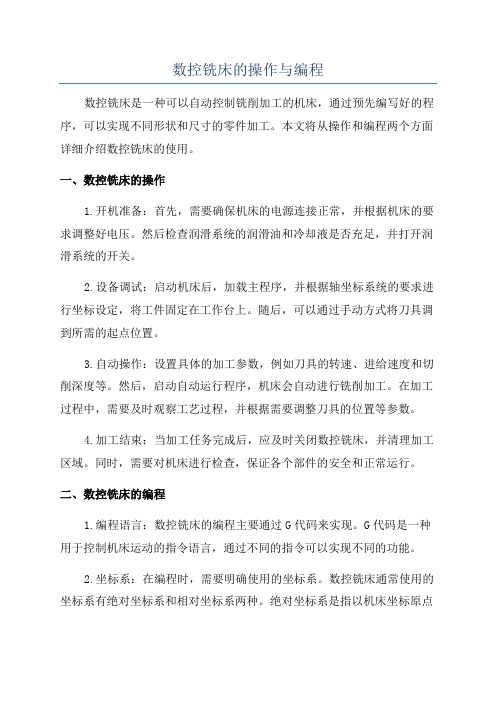
数控铣床的操作与编程数控铣床是一种可以自动控制铣削加工的机床,通过预先编写好的程序,可以实现不同形状和尺寸的零件加工。
本文将从操作和编程两个方面详细介绍数控铣床的使用。
一、数控铣床的操作1.开机准备:首先,需要确保机床的电源连接正常,并根据机床的要求调整好电压。
然后检查润滑系统的润滑油和冷却液是否充足,并打开润滑系统的开关。
2.设备调试:启动机床后,加载主程序,并根据轴坐标系统的要求进行坐标设定,将工件固定在工作台上。
随后,可以通过手动方式将刀具调到所需的起点位置。
3.自动操作:设置具体的加工参数,例如刀具的转速、进给速度和切削深度等。
然后,启动自动运行程序,机床会自动进行铣削加工。
在加工过程中,需要及时观察工艺过程,并根据需要调整刀具的位置等参数。
4.加工结束:当加工任务完成后,应及时关闭数控铣床,并清理加工区域。
同时,需要对机床进行检查,保证各个部件的安全和正常运行。
二、数控铣床的编程1.编程语言:数控铣床的编程主要通过G代码来实现。
G代码是一种用于控制机床运动的指令语言,通过不同的指令可以实现不同的功能。
2.坐标系:在编程时,需要明确使用的坐标系。
数控铣床通常使用的坐标系有绝对坐标系和相对坐标系两种。
绝对坐标系是指以机床坐标原点为零点,以工件上其中一固定点为基准进行编程;相对坐标系是以刀具当前位置为零点,以刀具的运动方向为基准进行编程。
3.几何指令:使用G代码可以实现不同的几何功能,如直线、圆弧、孤立点等。
在编程时,需要确定刀具的起点和终点坐标,以及刀具的路径和切削深度等参数。
4.速度指令:使用F代码可以设置刀具的进给速度,单位通常为毫米/分钟。
在编程时,需要根据具体的加工情况,选择合适的进给速度,以确保加工质量和效率。
5.刀具补偿:有时候,由于刀具的直径和轨迹的误差等原因,需要进行刀具补偿来纠正加工误差。
在编程时,可以使用H代码来设置刀具补偿的值,以调整刀具的路径和位置。
6.循环指令:在编程中,可以使用循环指令来实现重复的加工操作。
数控铣床编程与操作(机类)
数控铣床编程与操作
数控铣床编程与操作
机床原点
机床原点是指机床坐标系的原点, 即X=0, Y=0, Z=0的点,对某一具体的 机床来说,机床原点是固定的,是机床 制造商设置在机床上的一个物理位置。
数控铣床编程与操作
♫ 工件坐标系和工件零点
工件坐标系 工件坐标系是编程人员在编程时使用的,
程
校
Y
序 校
核检
和
试
N切
N
检
完成
验Y
手工编程过程的框图
数控铣床编程与操作
计算机自动编程 自动编程是指在编程过程中,除了
分析零件图样和制定工艺方案由人工进 行外,其余工作均由计算机辅助完成。
数控铣床编程与操作
♫ 数控加工工序的划分原则:
先面后孔的原则 刀具集中的原则 粗、精分开的原则 按部位分序的原则
M02和M30 程序结束,M02结束在程序末尾, M30结束后又返回程序头
M03、M04和M05 主轴正转、反转和停转 M06——换刀(常用于加工中心,刀库换刀) M08、M09 冷却液开、冷却液关
数控铣床编程与操作
M98和M99
M98主程序调用子程序 M99子程序返回主程序 在程序中含有某些固定顺序或重复出现的区域时,作为 子程序存入贮存器以简化程序编程
转任意角度来执行。
♫ 子程序调用功能 有些零件需要在不同的位置上重复加工同样
的轮廓形状,将这一轮廓形状的加工程序作为子 程序,在需要的位置上重复调用,就可以完成对 该零件的加工。
♫ 宏程序功能 该功能可用一个总指令代表实现某一功能的
一系列指令,并能对变量进行运算,使程序更具 灵活性和方便性。
数控铣床编程与操作 2.6 数控铣床主要加工对象
数控铣床简答及编程
数控铣床简答及编程数控铣床是一种高精度加工设备,它可以通过数控程序来控制工作台的移动和切削刀具的运动,完成各种复杂形状的零件加工。
与传统的手工铣床相比,数控铣床具有高效、高精度、低误差等优势,被广泛应用于航空、航天、汽车、造船、模具、机械等领域。
一、数控铣床的基本结构数控铣床的基本结构包括机床主体、进给系统、主轴系统、数控系统等。
其中,机床主体是数控铣床的主体部分,包括床身、工作台、横梁等。
进给系统是用来控制工作台在三维方向上的运动,包括直线进给和旋转进给两种方式。
主轴系统是用来控制切削刀具的转速和进给速度,以便完成不同加工要求的零件加工。
数控系统则是数控铣床的核心部件,它能够根据预先编写好的数控程序来指导机床进行零件加工。
二、数控铣床的编程方式数控铣床的编程方式分为手工编程和CAM编程两种,下面分别介绍:1、手工编程手工编程是指程序员根据加工工艺要求和加工图纸,手动写出数控程序的过程。
这种编程方式需要程序员具备较强的数学和加工知识,熟悉加工工艺和刀具选择等方面的知识。
手工编程的优点是程序的灵活性高,能够满足各种特殊加工要求,但缺点是编程效率较低,容易出错,需要较高的编程技能和经验。
手工编程的基本编程指令包括以下几种:G指令:是数控程序的基本控制指令,用来描述工作台和刀具的运动轨迹、速度和加速度等信息;M指令:用来控制机床的辅助功能,如冷却系统、加热系统、气动系统等;F指令:用来控制工具的进给速度,通常用于控制铣削刀具的进给速度;S指令:用来控制主轴的转速和方向。
2、CAM编程CAM(计算机辅助制造)编程是指运用CAM软件自动生成数控程序的过程。
它不需要程序员手写代码,而是通过输入加工图纸和加工参数等信息,由计算机自动生成加工程序。
CAM 编程具有编程效率高、编程精度高、易于操作等特点,较大程度上提高了数控铣床的生产效率。
CAM编程的主要步骤包括以下几个方面:1)导入CAD模型:CAM软件通过导入CAD模型,将三维模型转换成与机床控制器兼容的G代码或M代码;2)设置加工参数:CAM软件可以设置各种加工参数,如工具直径、切削速度、加工深度等;3)生成刀路:CAM软件通过自动选择刀具路径,生成数控程序,并对其进行模拟、分析和优化;4)输出NC文件:CAM软件将数控程序输出到NC文件中,供机床控制器进行控制和加工。
第一章数控铣床概述
图1-1 数控铣床
图1-2 加工中心
第一节 数控铣床(加工中心)的组成和工作原理 一 、数控铣床(加工中心)的 数控铣床(加工中心)大体由输入装臵、数 控装臵、伺服系统、检测及其辅助装臵和机床本 体等组成。 1、输入装臵 数控程序编制后需要存储在一定的介质上, 按目前的控制介质大致分为纸介质和电磁介质, 相应地通过不同方法输入到数控装臵中去。纸带 输入方法,即在专用的纸带上穿孔,用不同孔的 位臵组成数控代码,再通过纸带阅读机将代表不 同含义的信息读入。手动输入是将数控程序通过 数控机床上的键盘输入,程序内容将存储在数控 系统的存储器内,使用时可以随时调用。
伺服系统接收数控装臵输出的各种信号,经 过分配、放大、转换等功能,驱动各运动部件, 完成零件的切削加工。 4、检测装臵 位臵检测、速度反馈装臵根据系统要求不断 测定运动部件的位臵或速度,转换成电信号传 输到数控装臵中,与目标信号进行比较、运算, 进行控制。 5、运动部件 由包括床身、主轴箱、工作台、进给机构等 组成的机械部件,伺服电机驱动运动部件运动, 完成工件与刀具之间的相对运动。
基础篇 数控铣床(加工中心)的编程 第一章 数控铣床(加工中心)概述
数控铣床是主要采用铣削方式加工零件的 数控机床,它能够进行外形轮廓铣削、平面 或曲面型腔铣削及三维复杂型面的铣削,如 凸轮、模具、叶片等,另外数控铣床还具有 孔加工的功能,通过特定的功能指令可进行 一系列孔的加工,如钻孔、扩孔、铰孔、镗 孔和攻丝等,如图1-1所示。
第二节 数控铣床(加工中心)的分类和特点 数控机床加工与普通机床有着一定的区别: 1)工序集中 数控机床一般带有可以自动换 刀的刀架、刀库,换刀过程由程序控制自动进行 ,因此,工序比较集中,减少机床占地面积,节 约厂房,同时减少或没有中间环节(如半成品的 中间检测、暂存搬运等),既省时间又省人力。 2)自动化程度高 数控机床加工时,不需人 工控制刀具,自动化程度高,对操作工人的要求 降低。数控操作工在数控机床上加工出的零件比 普通工在传统机床上加工出的零件精度高,而且 省时、省力,降低了工人的劳动强度。
数控铣床基本编程指令-与简单程序编写
说明
G92 X X2 Y Y2 Z Z2 则将工件原点设定到距刀具起始点距离为X= -X2,Y= -Y2 ,Z= -Z2 的位置上。
G92 设置加工坐标系
(3)、工件坐标系选择 G54-G59
G54~G59是系统预置的六个坐标系,可根据需要选用。
该指令执行后,所有坐标值指定的坐标尺寸都是选定的工件加工坐标系中的位置。1~6号工件加工坐标系是通过CRT/MDI方式设置的。
X
Y
Z
G17
G18
G19
01
格式: G28 X _ Y _ Z _
02
其中,X、Y、Z 为指定的中间点位置。
(1)、自动返回参考点 G28
三、参考点控制指令
说明:
执行G28指令时,各轴先以G00的速度快移到程序指 令的中间点位置,然后自动返回参考点。
在使用上经常将XY和Z分开来用。先用G28 Z...提刀并回Z轴参考点位置,然后再用G28 X...Y...回到XY方向的参考点。
O
X
Y
A
R30
G90 G03 X30 Y0 I-40 J0 F80 G91 G03 X0 Y0 I-40 J0 F80
(5)G02/ G03 实现空间螺旋线进给 格式:G17 G02(G03) X... Y... R... Z... F... 或 G18 G02(G03) X... Z... R... Y... F... G19 G02(G03) Y... Z... R... X... F...
1
2
(3)编程算法
或 G91G02 X(xb-xa)Y(yb-ya)I(x1-xa)J(y1-ya)F f ;
或 G17G90 G02 X xb Y yb I(x1-xa) J (y1-ya) F f ;
- 1、下载文档前请自行甄别文档内容的完整性,平台不提供额外的编辑、内容补充、找答案等附加服务。
- 2、"仅部分预览"的文档,不可在线预览部分如存在完整性等问题,可反馈申请退款(可完整预览的文档不适用该条件!)。
- 3、如文档侵犯您的权益,请联系客服反馈,我们会尽快为您处理(人工客服工作时间:9:00-18:30)。
数控铣床编程概述一、教学要求1、了解数控铣床的编程特点;2、掌握数控铣床编程的内容与步骤;3、掌握数控铣床编程的基础知识;二、教学内容5.1.1数控编程的定义为了使数控机床能根据零件加工的要求进行动作,必须将这些要求以机床数控系统能识别的指令形式告知数控系统,这种数控系统可以识别的指令称为程度,制作程序的过程称为数控编程。
数控编程的过程不仅仅指编写数控加工指令代码的过程,它还包括从零件分析到编写加工指令代码,再到制成控制介质以及程序校核的全过程。
在编程前首先要进行零件的加工工艺分析,确定加工艺路线、工艺参数、刀具的运动轨迹、位移量、切削参数(切削速度、进给量、背吃刀量)以及各项辅助功能(换刀、主轴正反转、切削液开关等);接着根据数控机床规定的指令代码及程序格式编写加工程序单;再把这一程序单中的内容记录在控制介质上(如软盘、移动存储器、硬盘等),检查正确无误后采用手工输人方式或计算机传输方式输入数控机床的数控装置中,从而指挥机床加工零件。
5.2.1数控编程的内容与步骤数控编程步骤如图5-1所示,主要有以下几个方面的内容:图5-1 数控编程步骤(a)分析图样包括零件轮廓分析,零件尺寸精度、形位精度、表面粗糙度、技术要求的分析,零件材料、热处理等要求的分析。
(b)确定加工艺包括选择加工方案,确定加工路线,选择定位与夹紧方式,选择刀具,选择各项切削参数,选择对刀点、换刀点。
(c)数值计算选择编程原点,对零件图形各基点进行正确的数学计算,为编写程序单做好准备。
(d)编写程序单根据数控机床规定的指令代码及程序格式编写加工程序单。
(e)制作控制介质简单的数控程序直接采用手工输入机床,当程序自动输入机床时,必须制作控制介质。
现在大多数程序采用软盘、移动存储器、硬盘作为存储介质,采用计算机传输来输入机床。
目前,除了少数老式的数控机床仍在采用穿孔纸带外,现代数控机床均不再采用此种控制介质了。
(f)程序校验程序必须经过校验正确后才能使用。
一般采用机床空运行的方式进行校验,有图形显示卡的机床可直接在CRT显示屏上进行校验,现在有很多学校还采用计算机数控模拟进行校验。
以上方式只能进行数控程序、机床动作的校验,如果要校验加工精度,则要进行首件试切校验。
5.3数控编程的分类数控编程可分为手工编程和自动编程两种。
5.3.1.手工编程手工编程是指所有编制加工程序的全过程,即图样分析、工艺处理、数值计算、编写程序单、制作控制介质、程序校验都是由手工来完成。
手工编程不需要计算机、编程器、编程软件等辅助设备,只需要有合格的编程人员即可完成。
手工编程具有编程快速及时的优点,其缺点是不能进行复杂曲面的编程。
手工编程比较适合批量较大、形状简单、计算方便、轮廓由直线或圆弧组成的零件的加工。
对于形状复杂的零件,特别是具有非圆曲线、列表曲线及曲面的零件,采用手工编程则比较困难,最好采用自动编程的方法进行编程。
5.3.2.自动编程自动编程是指用计算机编制数控加工程序的过程。
自动编程的优点是效率高,正确性好。
自动编程由计算机代替人完成复杂的坐标计算和书写程序单的工作,它可以解决许多手工编制无法完成的复杂零件编程难题,但其缺点是必须具备自动编程系统或自动编程软件。
自动编程较适合形状复杂零件的加工程序编制,如:模具加工、多轴联动加工等场合。
实现自动编程的方法主要有语言式自动编程和图形交互式自动编程两种。
前者通过高级语言的形式表示出全部加工内容;计算机运行时采用批处理方式,一次性处理、输出加工程序。
后者是采用人机对话的处理方式,利用CAD/CAM 功能生成加工程序。
CAD/CAM软件编程加工过程为:图样分析、零件分析、三维造型、生成加工刀具轨迹;后置处理生成加工程序、程序校验、程序传输并进行加工。
5.4常用CAD/CAM软件介绍5.4.1.UG(Unigraphics)UG起源于麦道飞机制造公司,是由EDS公司开发的集成化CAD/CAE/CAM系统,是当前国际、国内最为流行的工业设计平台。
其庞大的模块群为企业提供了从产品设计、产品分析、加工装配、检验,到过程管理、虚拟动作等全系列的支持,其主要模块有数控造型、数控加工、产品装配等通用模块和计算机辅助工业设计、钣金设计加工、模具设计加工、管路设计布局等专用模块。
该软件的容量较大,对计算机的硬件配置要求也较高,所以早期版本在我国使用不很广泛,但随着计算机配置的不断升级,该软件在国际、国内的CAD/CAE/CAM市场上已占有了很大的份额。
5.4.2.Pro/EngineerPro/Engineer是由美国PTC(参数科技公司)于1989年开发的,它开创了三维CAD/CAM参数化的先河,采用单一数据库的设计,是基于特征、全参数、全相关性的CAD/CAE /CAM系统。
它包含零件造型、产品装配、数控加:工、模具开发、钣金件设计、外形设计、逆向工程、机构模拟、应力分析等功能模块,因而广泛应用于机械、汽车、模具、工业设计、航天、家电、玩具等行业,在国内外尤其是制造业发达的地区有着庞大的用户群。
5.4.3SolidWorksSolidWorks是一个在微机平台上运行的通用设计的CAD 软件,它具有高效方便的计算机辅助该软件有极强的图形格式转换功能,几乎所有的CAD/CAE/CAM软件都可以与SolidWorks软件进行数据转换,美中不足的是其数控加工功能不够强大而且操作也比较烦琐,所以该软件常作为数控自动化编程中的造型软件,再将造型完成的三维实体通过数据转换到UG、Masteream、Cimatron软件中进行自动化编程。
5.4.4MastercamMastercam是由美国CNCSoftware公司推出的基于PC平台,集二维绘图、三维曲面设计、体素拼合、数控编程、刀具路径模拟及真实感模拟为一身的CAD/CAM软件,该软件尤其对于复杂曲面的生成与加工具有独到的优势,但其对零件的设计、模具的设计功能不强。
由于该软件对运行环境要求较低、操作灵活易掌握、价格便宜,所以受到我国中小数控企业的欢迎。
5.4.5CimatronCimatron系统是源于以色列为了设计开发喷气式战斗机所发展出来的软件。
它由以色列的Cimatron公司提供的一套集成CAD/CAE/CAM的专业软件,它具有模具设计、三维造型、生成工程图、数控加工等功能。
该软件在我国得到了广泛的使用,特别是在数控加工方面更是占有很大的比重。
5.4.6CAXA制造工程师CAXA制造工程师是我国北航海尔软件有限公司研制开发的全中文、面向数控铣床与加工中心的三维CAD/CAM软件,它既具有线框造型、曲面造型和实体造型的设计功能,又具有生成二至五轴的加工代码的数控加工功能,可用于加工具有复杂三维曲面的零件。
由于该软件是我国自行研制的数控软件,采用了全中文的操作界面,学习与操作都很方便,而且价格也较低,所以该软件近几年在国内得到了较大程度的推广。
另外,CAXA系列软件中的“CAXA线切割”也是一种方便实用的线切割自动编程软件。
5.5 数控铣床编程的基础知识5.5.1程序的结构与格式每一种数控系统,根据系统本身的特点与编程的需要,都有一定的程序格式。
对于不同的机床,其程序格式也不同,因此,编程人员必须严格按照机床说明书的格式进行编程。
但程序的常规格式却是相同的。
a、程序的组成一个完整的程序由程序号、程序内容和程序结束三部分组成:%0001 零件程序号(%1~4294967295)N10 G90 G80 G40 G49 G17 程序内容N20 G00 G54 X0 Y0 Z50 F300 程序段N30 M03 S500。
N260 M05N270 M30 程序结束(1)程序号每一个储存在零件存储器中的程序都需要指定一个程序号来加以区别,这种用于区别零件加工程序代号称为程序号,同一机床的程序号不能重复。
程序号写在程序的最前面,必须单独占用一行。
(2)程序内容程序内容是整个程序的核心,它由许多程序段组成,每个程序段由一个或多个指令构成,它表示数控机床的全部动作。
在数控铣床的程序中,子程序的调用也作为主程序内容的一部分,主程序中只完成换刀、调转速、工件定位等动作,其余加工动作都由子程序来完成。
(3)程序结束程序结束通过M代码来实现,它必须写在程序的最后。
可以作为程序结束标记的M代码有M02和M30,它们代表零件加工主程序的结束。
为了保证最后程序段的正常执行,通常要求M02(M30)也必须单独占一行。
此外,子程序结束有专用的结束标记,HNC—21M系统中用M99来表示子程序结束后返回主程序。
5.5.2.程序段的组成(1)程序段基本格式程序段是程序的基本组成部分,每个程序段由若干个数据字构成,而数据字又由表示地址的英文字母、特殊文字和数字构成。
如X30、G90等。
程序段格式是指一个程序段中字、字符、数据的排列、书写方式和顺序。
通常情况下,程序段格式有字—地址程序段格式、使用分隔符的程序段格式、固定程序段格式三种。
字—地址程序段格式如下:N50 C01 X30 Y30 Z30 F100 S800 TO1 M03;(2)程序段号与程序段结束程序段由程序段号NXX开头,以程序段结束标记CR(或IJ)结束,实际使用时,常用符号“;”或“*”表示CR(或LP)。
程庄段的中间部分是程序段的内容,主要包括准备功能字、尺寸功能字、进给功能字、主轴功能字、刀具功能字、辅助功能字等,但并不是所有程序段都必须包含所有功能字,有时一个程序段内可仅包含其中一个或几个功能字,如下列程序段都是正确的程序段。
N10 C01 X100 F100;N10 M05;NXX为程序段号,由地址N和后面的若干位数字表示。
在大部分系统中,程序段号仅作为“跳转”或“程序检索”的目标位置指示,因此,它的大小顺序可以颠倒,也可以省略,程序段在存储器内以输入的先后顺序排列,而程序的执行是严格按信息在存储器内的先后顺序一段一段地执行,也就是说执行的先后次序与程序段号无关。
但是,当程序段号省略时,该程序段将不能作为“跳转”或“程序检索”的目标程序段。
程序段号也可以由数控系统自动生成,程序段号的递增量可以通过“机床参数”进行设置,一般可设定增量值为10。
(3)程序的斜杠跳跃有时,在程序段的前面有“/”符号,该符号称为斜杠跳跃符号,该程序段称为可跳跃程序段。
如下列程序段:/N10 G00 X100;这样的程序段,可以由操作者对程序段和执行情况进行控制。
若操作机床使系统的“跳过程序段”信号生效,程序执行时将跳过这些程序段;若“跳过程序段”信号无效,程序段照常执行,该程序段和不加“/”符号的程序段相同。
(4)程序段注释为了方便检查、阅读数控程序,在许多数控系统中允许对程序进行注释,注释可以作为对操作者的提示显示在屏幕上,但注释对机床动作没有丝毫影响。