第二章 金属切削过程及其物理现象PPT课件
合集下载
第2章 金属切削过程的基本规律-PPT课件

图2-6 积屑瘤、切屑及加工表面硬度
3.控制积屑瘤产生的措施
(1)避开容易产生积屑瘤的切削速度范围 当工件材料一定时 ,切削速度是影响积屑瘤的主要因素。 (2)降低材料塑性 工件材料塑性越大,刀具与切屑之间的平 均摩擦因数增加,越容易生成积屑瘤。 (3)合理使用切削液 使用切削液可降低切削温度,减少摩擦 ,因此,可抑制积屑瘤的产生。 (4)增大刀具前角、提高刀具刃磨质量 刀具前角的增大,可 以减少切屑变形和切削力,降低切削温度,因此,增大前角能 抑制积屑瘤的产生。
2.切削用量的影响
(1)背吃刀量和进给量 背吃刀量ap或进给量f加大,均使切削 力增大,但两者的影响程度不同。 (2)切削速度 加工塑性金属时,在中速和高速下,切削力一 般随着vc的增大而减小。
3.刀具几何参数的影响
(1)前角 前角γ0加大,使切屑变形减小,因此切削力下降。 (2)负倒棱 在锋利的切削刃上磨出负倒棱,可以提高刃区的 强度,从而提高刀具使用寿命,但使切削变形加大,切削力增 加。 (3)主偏角 主偏角κr对主切削力影响较小,主要影响切削力的 作用方向,即影响Fp与Ff的比值。 (4)刃倾角 刃倾角对主切削力Fc的影响甚微;对Fp的影响较 大。 (5)刀尖圆弧半径 刀尖圆弧半径rε对Fp、Ff的影响较大,对Fc 的影响较小。
2.1.1 切屑的形成过程及变形区的划分
变形的主要特征:
• 剪切滑移变形
• 加工硬化
图2-1 第一变形区金属的滑移
2.1.1 切屑的形成过程及变形区的划分
切屑沿前刀面排出时进 一步受到前刀面的挤压和摩
擦,使靠近前刀面Βιβλιοθήκη 金属纤 维化,基本与前刀面平行。图2-3 加工表面的形成和变形
2.1.2 变形系数
3 P F 10 c c c
第一篇-第二章 金属切削过程15页
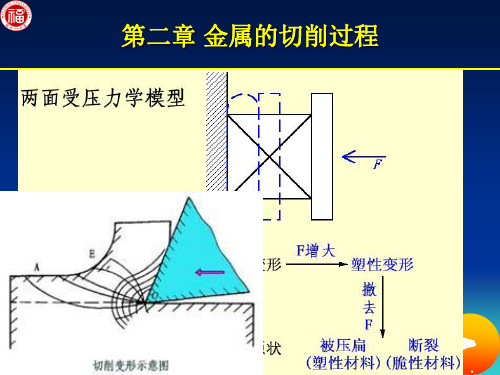
该区域对工件表面的残余应力以
第及一后变刀形面区的磨损有很大的影响。
第二变形区
第三变形区
剪切角Φ :剪切面与切削速 度方向间的夹角称为剪切角。 当 切 削 速 度 增 大 时 , OA 与 OM会慢慢靠近, Φ减小。
三、切削的变形及影响因素
1. 变形系数:
厚度变形系数:
h
h ch hD
长度变形系数:
3. 剪切角Ф :
0
4
4
0
2. 影响切削变形的因素:
① 工件材料:
工件塑性↗
② 刀具角度:
γ O↗
Ф↗
③ 切削速度:
vc ↗
④ 摩擦系数:
μ↗
β↗
延伸率δ ↗
ξ↗
ξ↙
ξ↙
Φ↙
ξ↗
四、切屑的类型 切屑的形成
1. 带状切屑:
产形形特成生状点原条:因件::
切连切速削绵高塑不过,性断 程切材呈 变削料带 形层、未状 小及切,充削切 速小屑呈分切破削工变面坏度、毛底力表形上值高前茸面小面即的,、 角 状很 且粗变应因切 大 。光 稳糙为力此削 。滑 定度切还只厚屑未有而 ;低,达塑度背 已。剪到性较面 加对 滑生移产而安无全断有裂危;害前角。大,
3. 对切削过程的影响:
① 积屑瘤代替刀刃进行切削,保护
12了. 特产刀点生刃,:条增件大:了前角。
② 积屑瘤使切削厚度增大。
③①积硬切屑削度瘤塑形是状性工不材件规料则材。,料频繁的生长脱 故②:落粗2刀和切,加~具界影削工3.响时5切面区倍尺可削状的寸人,。况温精为可符度度控以合、和制表代在压积面屑刀力替质瘤量的。生
第及一后变刀形面区的磨损有很大的影响。
第二变形区
第三变形区
剪切角Φ :剪切面与切削速 度方向间的夹角称为剪切角。 当 切 削 速 度 增 大 时 , OA 与 OM会慢慢靠近, Φ减小。
三、切削的变形及影响因素
1. 变形系数:
厚度变形系数:
h
h ch hD
长度变形系数:
3. 剪切角Ф :
0
4
4
0
2. 影响切削变形的因素:
① 工件材料:
工件塑性↗
② 刀具角度:
γ O↗
Ф↗
③ 切削速度:
vc ↗
④ 摩擦系数:
μ↗
β↗
延伸率δ ↗
ξ↗
ξ↙
ξ↙
Φ↙
ξ↗
四、切屑的类型 切屑的形成
1. 带状切屑:
产形形特成生状点原条:因件::
切连切速削绵高塑不过,性断 程切材呈 变削料带 形层、未状 小及切,充削切 速小屑呈分切破削工变面坏度、毛底力表形上值高前茸面小面即的,、 角 状很 且粗变应因切 大 。光 稳糙为力此削 。滑 定度切还只厚屑未有而 ;低,达塑度背 已。剪到性较面 加对 滑生移产而安无全断有裂危;害前角。大,
3. 对切削过程的影响:
① 积屑瘤代替刀刃进行切削,保护
12了. 特产刀点生刃,:条增件大:了前角。
② 积屑瘤使切削厚度增大。
③①积硬切屑削度瘤塑形是状性工不材件规料则材。,料频繁的生长脱 故②:落粗2刀和切,加~具界影削工3.响时5切面区倍尺可削状的寸人,。况温精为可符度度控以合、和制表代在压积面屑刀力替质瘤量的。生
第二章金属切削过程的物理现象

切削力。
◆切削力影响刀具的磨损和使用寿命。 ◆切削力影响加工精度。 ◆是计算切削功率、设计和选用机床刀具夹具的必要依据。
二、切削力的产生
1、来自工件的切削力:工件材 料被切过程中所发生的弹性变 形和塑性变形的抗力。
2、来自切屑的切削力:切屑对 刀具前刀面的摩擦力和加工表 面对刀具后刀面的摩擦力。
三.切削力的分解和切削功率
简言之,被切削的金属层在前刀面的挤压作用下,通过 剪切滑移变形便形成了切削。
金属切削过程中的三个变形区
第Ⅰ变形区 近切削刃处切削层 内产生的塑性变形区;
第Ⅱ变形区 与前刀面接触的 切屑层内产生的变形区;
第Ⅲ变形区 近切削刃处已加 工表层内产生的变形区 (后刀 面与工件的接触区域)
1、第一变形区 (剪切滑移区)
Ⅱ区:形成带状切屑,冷焊条件逐 渐形成,随着切削速度的提高积屑 瘤也增大。
Ⅲ区:积屑瘤随切削速度的 提高而减小,当达到Ⅲ区右 边界时,积屑瘤消失。
Ⅳ区:切削速度进一步提高,由 于切削温度较高而冷焊消失,此 时积屑瘤不再存在了。但切屑底 部的纤维化依然存在,切屑的滞 留倾向也依然存在。
4)刀具的前角
2)切削温度
切削温度也是形成积屑瘤的重要条件。切削 温度过低,粘结现象不易发生;切削温 度过高, 加工硬化现象有削弱作用,因而积屑瘤也不易产 生。
对于碳钢,300ºC~ 350ºC范围内最容易产 生积屑瘤, 500ºC以上趋于消失。
3)积屑瘤与切削速度的关系
Ⅰ区:切削速度很低,形成粒状 或节状切屑,没有积屑瘤生成。
进给抗力Ff:切削合力F在进给运动方向的合力,车外圆 时,Ff与工件的轴线相平行,因此又称轴向分力。Ff作用 在机床的进给机构上,它是设计进给机构必须的数据。
◆切削力影响刀具的磨损和使用寿命。 ◆切削力影响加工精度。 ◆是计算切削功率、设计和选用机床刀具夹具的必要依据。
二、切削力的产生
1、来自工件的切削力:工件材 料被切过程中所发生的弹性变 形和塑性变形的抗力。
2、来自切屑的切削力:切屑对 刀具前刀面的摩擦力和加工表 面对刀具后刀面的摩擦力。
三.切削力的分解和切削功率
简言之,被切削的金属层在前刀面的挤压作用下,通过 剪切滑移变形便形成了切削。
金属切削过程中的三个变形区
第Ⅰ变形区 近切削刃处切削层 内产生的塑性变形区;
第Ⅱ变形区 与前刀面接触的 切屑层内产生的变形区;
第Ⅲ变形区 近切削刃处已加 工表层内产生的变形区 (后刀 面与工件的接触区域)
1、第一变形区 (剪切滑移区)
Ⅱ区:形成带状切屑,冷焊条件逐 渐形成,随着切削速度的提高积屑 瘤也增大。
Ⅲ区:积屑瘤随切削速度的 提高而减小,当达到Ⅲ区右 边界时,积屑瘤消失。
Ⅳ区:切削速度进一步提高,由 于切削温度较高而冷焊消失,此 时积屑瘤不再存在了。但切屑底 部的纤维化依然存在,切屑的滞 留倾向也依然存在。
4)刀具的前角
2)切削温度
切削温度也是形成积屑瘤的重要条件。切削 温度过低,粘结现象不易发生;切削温 度过高, 加工硬化现象有削弱作用,因而积屑瘤也不易产 生。
对于碳钢,300ºC~ 350ºC范围内最容易产 生积屑瘤, 500ºC以上趋于消失。
3)积屑瘤与切削速度的关系
Ⅰ区:切削速度很低,形成粒状 或节状切屑,没有积屑瘤生成。
进给抗力Ff:切削合力F在进给运动方向的合力,车外圆 时,Ff与工件的轴线相平行,因此又称轴向分力。Ff作用 在机床的进给机构上,它是设计进给机构必须的数据。
第二章 金属切削原理机械制造技术A ppt课件
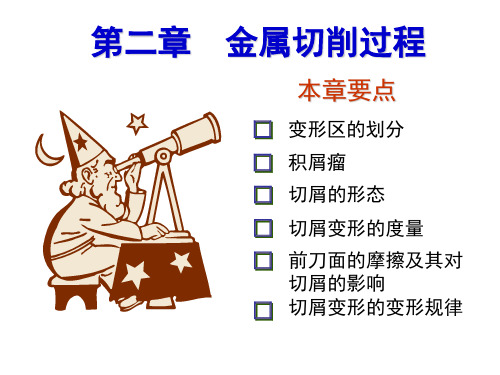
第二章
金属切削过程
本章要点
变形区的划分 积屑瘤 切屑的形态 切屑变形的度量 前刀面的摩擦及其对 切屑的影响 切屑变形的变形规律
2.1 金属切削过程概述
切屑的形成
45° M
A
F
B
O
a)正挤压
45° M A F
切削层
M
BO
O F
b)偏挤压
c)切削
刀具
精品资料
• 你怎么称呼老师?
• 如果老师最后没有总结一节课的重点的难点,你 是否会认为老师的教学方法需要改进?
0
Fr
Ff
Fn
• 切削层的截面积Ac
Ac acaw • 剪切面的截面积As
As
Ac
sin
剪切力:Fs
As
Ac
sin
总切削力: F rco F s s (0)F ss F irc c no o A c s s ( (0 0 ))
F zF rcos(0)
FyFrsin (0)
Fy Fz
Ⅱ Ⅰ
Ⅲ
热的主要来源。 ➢ 第Ⅱ变形区:靠近前刀面的
切削部位三个变形区
切屑底层,切屑排出时受前刀
面挤压与摩擦。是造成前刀面磨损和产生积屑瘤的主要原因。
➢ 第Ⅲ变形区:已加工面受到后刀面挤压与摩擦,产生变 形。是造成后刀面磨损、已加工表面的质量(表面粗糙度 、加工硬化和残余应力)的主要原因。
2.1 金属切削过程概述
2.2 积屑瘤
积屑瘤的利弊
粗加工时:保护刀具、增大前角。(利)
精加工时:严重影响加工表面的尺寸精度和 粗糙度。(弊)
2.2 积屑瘤
积屑瘤的控制 :(切削速度影响积屑瘤的主要
因素)
金属切削过程
本章要点
变形区的划分 积屑瘤 切屑的形态 切屑变形的度量 前刀面的摩擦及其对 切屑的影响 切屑变形的变形规律
2.1 金属切削过程概述
切屑的形成
45° M
A
F
B
O
a)正挤压
45° M A F
切削层
M
BO
O F
b)偏挤压
c)切削
刀具
精品资料
• 你怎么称呼老师?
• 如果老师最后没有总结一节课的重点的难点,你 是否会认为老师的教学方法需要改进?
0
Fr
Ff
Fn
• 切削层的截面积Ac
Ac acaw • 剪切面的截面积As
As
Ac
sin
剪切力:Fs
As
Ac
sin
总切削力: F rco F s s (0)F ss F irc c no o A c s s ( (0 0 ))
F zF rcos(0)
FyFrsin (0)
Fy Fz
Ⅱ Ⅰ
Ⅲ
热的主要来源。 ➢ 第Ⅱ变形区:靠近前刀面的
切削部位三个变形区
切屑底层,切屑排出时受前刀
面挤压与摩擦。是造成前刀面磨损和产生积屑瘤的主要原因。
➢ 第Ⅲ变形区:已加工面受到后刀面挤压与摩擦,产生变 形。是造成后刀面磨损、已加工表面的质量(表面粗糙度 、加工硬化和残余应力)的主要原因。
2.1 金属切削过程概述
2.2 积屑瘤
积屑瘤的利弊
粗加工时:保护刀具、增大前角。(利)
精加工时:严重影响加工表面的尺寸精度和 粗糙度。(弊)
2.2 积屑瘤
积屑瘤的控制 :(切削速度影响积屑瘤的主要
因素)
金属切削过程ppt课件

滑移,其间的摩擦属于内摩擦。
➢ 滑动区:切屑在脱离前刀面之前 ,与前刀面只在一些突出点接触, 切屑与前刀面之间的摩擦属于外摩 擦。
lf1
lf2
切屑与前刀面的摩擦
20
三 刀—屑接触区的变形与摩擦
前刀面变形区的特点
切屑流动速度不均匀:
v屑
表层流速大,底层流速小。
当 max s 时,v屑 0
滞留现象
a
ach ac
◆ 长度变形系数
l
lc lch
由于沿切屑宽度方向基本没有变形, 根据体积不变原理:
变形系数: a l
一般: 1 14
变形程度的表示
• 剪切角
• 剪切角越大,ach 越小
( ac 不变), 越小。
• 前角增大,剪切角增 大,变形减小。
15
变形程度的表示
剪应变
既然切削过程中金属变形的主要形式是剪切滑移,当然就可以用相对 滑移,来衡量切削过程的变形程度
2)由于出发点与实际差别较大(切削变形以剪切为主),故不精确。有 时等于1,甚至小于1(切削耐热合金,如钛合金时)。
17
变形程度的表示
几种表示变形程度的参数的比较 •剪应变:建立在纯剪切的观点上,最接近实际情况,是比较合理、精确的近似 (忽略了挤压)。
特点:
1)在 0 10 ~ 30, 5 ~ 35 , 增加, 下降
刀具 O
切屑根部金相照片
8
二、切削层金属的变形
1 三个变形区
➢ 第Ⅰ变形区:即剪切变形区,金属剪切滑移, 成为切屑。金属切削过程的塑性变形主要集中于 此区域。
Ⅱ Ⅰ
Ⅲ
特征:剪切滑移,晶粒拉长
➢ 第Ⅱ变形区:靠近前刀面处,切屑排出时受前 刀面挤压与摩擦,使靠近前刀面的的晶粒进一步剪 切滑移。
金属切削基本原理机械制造技术基础幻灯片PPT

第Ⅱ变形区的影响。
)
➢剪 切 角 越 小 、 前 角 越
小,剪切变形量越大
φ
G
OH
γ0 相对滑移系数
Φ-0
φ
90-φ φ
7 .
2.1.1 切屑的形成与切削变形
特
点 在高温高压作用下,切屑底层与前刀面发生沾接,切屑
与前刀面之间既有外摩擦,也有内摩擦。
➢ 粘结区:高温高压使切屑底 层软化,粘嵌在前刀面高低不
力力
种 类 及
◆ 残余张应力: 易使加工表面产生裂纹,降低零件疲劳强度
影 ◆ 残余压应力:
响
有利于提高零件疲劳强度
◆ 残余应力分布不均:
会使工件发生变形,影响形状和尺寸精度
9 .
2.1.1 切屑的形成与切削变形
23
残 余 应 力
◆ 热塑变形效应:表层张应力,里层压应力
◆ 里层金属弹性恢复:若里层金属产生拉伸变形,则弹性 恢复后表层得到压应力,里层为张应力
刀 具
➢前角增大,刀具容易切入工件,剪切角增大,切削力减小。 加工塑性大的材料时,增大前角则总切削力明显减小;而加工
几 脆性材料时,增大前角对减小总切削力的作用不显著。
何 ➢负倒棱提高了正前角刀具的刃口强度,但同时也增加了负倒 角 棱前角(负前角)参加切削的比例,负前角的绝对值越大,切削 度 变形程度越大,所以切削力越大。
平的凹坑中,形成长度为lfi的
粘接区。切屑的粘接层与上层 金属之间产生相对滑移,其间 的摩擦属于内摩擦。
➢ 滑动区:切屑在脱离前刀面 之前,与前刀面只在一些突出 点接触,切屑与前刀面之间的 摩擦属于外摩擦。
lfi
lfo
切屑与前刀面的摩擦
8积 .屑
2.1.1 切屑的形成与切削变形
)
➢剪 切 角 越 小 、 前 角 越
小,剪切变形量越大
φ
G
OH
γ0 相对滑移系数
Φ-0
φ
90-φ φ
7 .
2.1.1 切屑的形成与切削变形
特
点 在高温高压作用下,切屑底层与前刀面发生沾接,切屑
与前刀面之间既有外摩擦,也有内摩擦。
➢ 粘结区:高温高压使切屑底 层软化,粘嵌在前刀面高低不
力力
种 类 及
◆ 残余张应力: 易使加工表面产生裂纹,降低零件疲劳强度
影 ◆ 残余压应力:
响
有利于提高零件疲劳强度
◆ 残余应力分布不均:
会使工件发生变形,影响形状和尺寸精度
9 .
2.1.1 切屑的形成与切削变形
23
残 余 应 力
◆ 热塑变形效应:表层张应力,里层压应力
◆ 里层金属弹性恢复:若里层金属产生拉伸变形,则弹性 恢复后表层得到压应力,里层为张应力
刀 具
➢前角增大,刀具容易切入工件,剪切角增大,切削力减小。 加工塑性大的材料时,增大前角则总切削力明显减小;而加工
几 脆性材料时,增大前角对减小总切削力的作用不显著。
何 ➢负倒棱提高了正前角刀具的刃口强度,但同时也增加了负倒 角 棱前角(负前角)参加切削的比例,负前角的绝对值越大,切削 度 变形程度越大,所以切削力越大。
平的凹坑中,形成长度为lfi的
粘接区。切屑的粘接层与上层 金属之间产生相对滑移,其间 的摩擦属于内摩擦。
➢ 滑动区:切屑在脱离前刀面 之前,与前刀面只在一些突出 点接触,切屑与前刀面之间的 摩擦属于外摩擦。
lfi
lfo
切屑与前刀面的摩擦
8积 .屑
2.1.1 切屑的形成与切削变形
第2章 金属切削过程
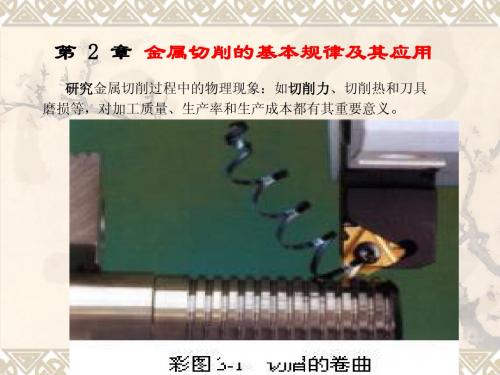
⑶主偏角 主偏角κ r 对主切削力影响不大,对吃刀抗力和进给抗 力影响显著( κr ↑—— Fp↓,Ff↑)
切削力/ N
2200
1800
1400 1000
κr - Fc
κr – Ff κr – Fp
FC—— 切削力(Fz) Ff—— 进给力(Fx) FP—— 背向力(Fy)
600 200 30 45 60
进给力Fx (Ff)
也称轴向分力,用Fx表示—总切削力在进给方 向的分力,是设计机床进给机构不可缺少的参数。 背向力 Fy(Fp) 也称径向分力,用Fy表示 —总切削力在垂直于
工作平面方向的分力,是进行加工精度分析、计算
系统刚度,分析工艺系统振动所必须的参数。
三个分力FC、Ff、FP与合力F 合力F =
2、切削温度的分布
★ 切削塑性材料 :
前刀面靠近刀尖处温度最高。
★ 切削脆性材料: 后刀面靠近刀尖处温度最高
750 ℃
刀 具
2.3.3 影响切削温度的主要因素
1.切削用量对刀具温度的影响
切削温度与切削用量的关系式为:
θ = Cθ VcZθ fyθ apxθ 三个影响指数 zθ >yθ >xθ ,说明切削速度对切削 温度的影响最大,背吃刀量对切削温度的影响最小。
C区是刀尖区,由于散热差,强度低,磨损 严重,磨损带最大宽度用VC表示 B区处于磨损带中间,磨损均匀,最大磨损 量VBmax;
3.边界磨损
N区处于切削刃与待加工表面的相交处,磨 损严重,磨损量以VN表示,此区域的 磨损也叫边界磨损
2.4.2 刀具磨损的主要原因
1. 硬质点磨损
工件材料中含有硬质点杂质,在加工过程中会将刀具表面划伤, 造成机械磨损。低速刀具磨损的主要原因是硬质点磨损。
《金属切削原理》课件
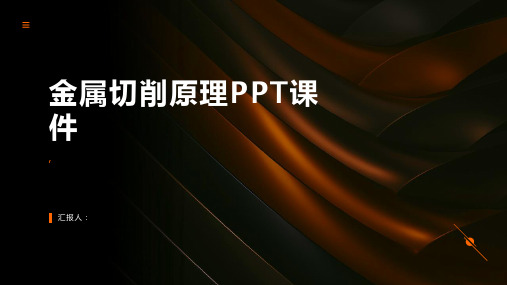
金属切削在机械制造中的应用
加工精度:金属切削可以精确地加工出各种形状和尺寸的零件 加工效率:金属切削可以提高生产效率,缩短生产周期 加工范围:金属切削可以加工各种金属材料,包括钢、铝、铜等 加工质量:金属切削可以保证加工质量,提高产品的可靠性和耐用性
金属切削在航空航天领域的应用
飞机制造:金属 切削用于制造飞 机机身、机翼、 发动机等部件
新材料硬度 高,耐磨性 好,对刀具 寿命和加工 效率产生影 响
新材料热导 率低,切削 过程中热量 难以散发, 对刀具和工 件产生影响
新材料化学 活性强,易 与刀具材料 发生化学反 应,影响刀 具寿命和加 工质量
新材料加工 难度大,对 刀具材料和 加工工艺提 出更高要求
新材料加工 过程中产生 的废料处理 问题,对环 保和资源利 用提出挑战
切削热的ห้องสมุดไป่ตู้生与散失
切削热的产生:刀具与工件之间的摩擦和剪切作用 切削热的散失:通过刀具、工件和切屑的传导、对流和辐射等方式 切削热的影响:影响刀具寿命、工件加工精度和表面质量 切削热的控制:通过优化刀具材料、切削参数和冷却方式等手段
切削表面的形成与变化
切削过程:刀具与工件之间的相对运动 切削力:刀具与工件之间的相互作用力 切削温度:刀具与工件之间的摩擦热 切削表面:刀具与工件之间的接触面
火箭制造:金属 切削用于制造火 箭发动机、燃料 箱、控制系统等 部件
卫星制造:金属 切削用于制造卫 星外壳、太阳能 电池板、天线等 部件
空间站制造:金 属切削用于制造 空间站外壳、太 阳能电池板、生 命支持系统等部 件
金属切削在汽车工业领域的应用
汽车零部件制造:金属切削用于生产汽车发动机、变速箱、底盘等零部件 汽车车身制造:金属切削用于生产汽车车身、车门、车窗等车身部件 汽车模具制造:金属切削用于生产汽车模具,如冲压模具、注塑模具等 汽车维修与保养:金属切削用于汽车维修与保养,如更换损坏的零部件、修复车身损伤等
- 1、下载文档前请自行甄别文档内容的完整性,平台不提供额外的编辑、内容补充、找答案等附加服务。
- 2、"仅部分预览"的文档,不可在线预览部分如存在完整性等问题,可反馈申请退款(可完整预览的文档不适用该条件!)。
- 3、如文档侵犯您的权益,请联系客服反馈,我们会尽快为您处理(人工客服工作时间:9:00-18:30)。
第二章 金属切削过程物理现象
本章主要内容: 刀具的结构、材料 切削过程的基本现象 切削用量的选择
第一节 切削变形与切屑的形成
金属切削过程是指在刀具和切削力的 作用下形成切屑的过程,在这一过程中, 始终存在着刀具切削工件和工件材料抵抗 切削的矛盾,产生许多物理现象,如切削 力、切削热、积屑瘤、刀具磨损和加工硬 化等。
第一节 切削变形与切屑的形成
➢通过分析积屑瘤产生原因可以得出防止积屑瘤 的主要方法:
1)降低切削速度,使温度较低,粘结现象不易 发 生;
2)采用高速切削,使切削温度高于积屑瘤消失的 相应温度;
3)采用润滑性能好的切削液,减小摩擦; 4)增大刀具前角,以减小切屑于前刀面接触区的
压力; 5)适当提高工件材料硬度,减小加工硬化倾向。
切削力↑
四、影响切削力的因素
标准切削试验:刀具材料P10,工件材料45钢
σb = 650 Mpa,车刀几何参数为go =10°、 r = 45°、ls =0°。
Fz CFzaP1. 0 f0. 7KF 5z
即,ap增大一倍,Fz也增大一倍;而f 增大一倍, Fz只能增大68%~80%。
四、影响切削力的因素
沿滑移线的剪切变形以及随之产生的加工硬化。 (2)第二变形区II:切屑与前刀面磨擦的区域,
切屑底层靠近前刀面处纤维化,流动速度减缓, 切屑弯曲,切削与刀具接触温度升高。 (3)第三变形区III:工件已加工表面与后刀面接 触的区域,存在纤维化与 加工硬化,变形较密集。
第一节 切削变形与切屑的形成
2.切屑的类型及切屑控制(图a∽c为切削塑性材料,图d为切削脆性材料)
加工一般钢料或其它塑性材料时,常常在前刀 面处粘着一块剖面有时呈三角状的硬块。它的 硬度很高,通常是工件材料的2—3倍,在处于 比较稳定的状态时,能够代替 刀刃进行切削。这块冷焊在前 刀面上的金属称为积屑瘤或刀 瘤。(积屑瘤的形成过程: )
第一节 切削变形与切屑的形成
➢切屑瘤对切削过程的影响: 1)实际前角增大 2)增大切削厚度,可能引起振动 3)是加工表面粗糙度增大 4)对刀具寿命有影响
• “可接受”的切屑标准:不妨碍正常的加 工;不影响操作者的安全;易于清理、存 放和搬运。
• 切削控制的措施:在前刀面上磨制出断屑 槽或使用压块式断屑器。
第一节 切削变形与切屑的形成
断屑槽的基本形式:
L:切屑在前刀面上的接触长度 R:卷屑槽半径
第一节 切削变形与切屑的形成
3.积屑瘤现象 ➢ 在切削速度不高而又能形成连续切屑的情况下,
第一节 切削变形与切屑的形成
➢切屑控制: • “不可接受”的切屑:切削条件恶劣导致。
影响主要有拉伤工件的已加工表面;划伤 机床;造成刀具的早期破损;影响操作者 的安全。
• 切屑控制:在切削加工中采取适当的措施 来控制切屑的卷曲、流出与折断,使形成 “可接受”的良好屑形。
第一节 切削变形与切屑的形成
Fc——切削力,单位:N; vc——切削速度,单位:m/s。
三、切削功率的计算
(2)切削功率
Pc Fcvc
1000
单位:kw
PE
Pe
——机床传动效率,一般,取 = 0.75~0.85。
四、影响切削力的因素
总切削力的来源有两个方面: 一是克服被加工材料对弹性变形和塑性 变形的抗力; 二是克服切屑对刀具前面的摩擦阻力和 工件表面对刀具后面的摩擦阻力。
第二节 切削力和切削功率
一、切削力的来源与分解 (1)总切削力的分解
1)切削力Fc (Fz) 2)背向力Fp (Fy) 3)进给力Ff (Fx)
一、切削力的来源与分解
(1)总切削力的分解
F F z2F x2y F z2F x2F y2
F y F xy cors
F xF xs y in r
Fy (0.15~0.7)Fz Fx (0.1~00.6F)z
二、切削的经验公式
2. 切削力的经验公式
切削力 F zCFzaPX FzfyFzK Fz
二、切削的经验公式
切削力 背向力 进给力
F zCFzaPXFzfyFzKFz
FyCFyaPXFyfyFyKFy
FxCFxaPXFxfyFxKFx
三、切削ห้องสมุดไป่ตู้率的计算
(2)切削功率
Pe Fcvc
1000
单位:kw
由此可见,从减小切削力和节省动力消 耗的观点出发,在切除相同余量的条件
四、影响切削力的因素
1)工件材料的性能对切削力有显著的影响。 工件材料的硬度或强度愈高,材料的
剪切屈服强度也愈高,发生剪切变形的抗 力也愈大,故切削力也愈大。
四、影响切削力的因素
2)切削用量对切削力的影响。
a)背吃刀量ap 和进给量f 对切削力的影响;
↑ 背吃刀量ap ↑
进给量f↑
AD ↑
变形抗力 摩擦力
• 随着刀具的连续移动,原来处于始滑移面 上的金属不断向刀具靠拢,应力和变形也 逐渐加大。在终滑移面OE上,应力和变形 达到最大值。
• 越过OE面,切削层金属将脱离工件基体, 沿着前刀面流出而形成切屑。
第一节 切削变形与切屑的形成
➢ 三个变形区: (1)第一变形区I:从OA线到OE线内的区域,伴随
第一节 切削变形与切屑的形成
一.切削过程及切屑种类
1.切屑形成过程:对塑性金属进行切削时, 切屑的形成过程就是切削层金属的变形过 程。 •当工件受到刀具的挤压以后,切削层金属 在始滑移面OA以左发生弹性变形。在OA面 上,应力达到材 料的屈服强度,则 发生塑性变形,产 生滑移现象。
第一节 切削变形与切屑的形成
第一节 切削变形与切屑的形成
➢积屑瘤产生原因分析: 积屑瘤的产生以及它的积聚高度与金属材料
的硬化性质有关,也与刃前区的温度和压力分布 有关。一般说来,塑性材料的加工硬化倾向愈强, 愈易产生积屑瘤;温度与压力太低,不会产生积 屑瘤;反之,温度太高,产生弱化作用,也不会 产生积屑瘤。走刀量保持一定时,积屑瘤高度与 切削速度有密切关系。
切削类型
切削条件
特
征
a)带状切屑 b)挤裂切屑 c)单元切屑 d)崩碎切屑
切削厚度较小,切削速 度较高,刀具前角较大
切削速度较低,切削厚 度较大,刀具前角较小
相比b)进一步减小刀具 前角,减低切削速度
加工硬脆材料时切削厚 度较大时产生
内表面光滑,外表面毛茸 内表面有裂纹,外表面呈锯齿形 整个单元被切离 形状是不规则的,表面是凸凹不平的
本章主要内容: 刀具的结构、材料 切削过程的基本现象 切削用量的选择
第一节 切削变形与切屑的形成
金属切削过程是指在刀具和切削力的 作用下形成切屑的过程,在这一过程中, 始终存在着刀具切削工件和工件材料抵抗 切削的矛盾,产生许多物理现象,如切削 力、切削热、积屑瘤、刀具磨损和加工硬 化等。
第一节 切削变形与切屑的形成
➢通过分析积屑瘤产生原因可以得出防止积屑瘤 的主要方法:
1)降低切削速度,使温度较低,粘结现象不易 发 生;
2)采用高速切削,使切削温度高于积屑瘤消失的 相应温度;
3)采用润滑性能好的切削液,减小摩擦; 4)增大刀具前角,以减小切屑于前刀面接触区的
压力; 5)适当提高工件材料硬度,减小加工硬化倾向。
切削力↑
四、影响切削力的因素
标准切削试验:刀具材料P10,工件材料45钢
σb = 650 Mpa,车刀几何参数为go =10°、 r = 45°、ls =0°。
Fz CFzaP1. 0 f0. 7KF 5z
即,ap增大一倍,Fz也增大一倍;而f 增大一倍, Fz只能增大68%~80%。
四、影响切削力的因素
沿滑移线的剪切变形以及随之产生的加工硬化。 (2)第二变形区II:切屑与前刀面磨擦的区域,
切屑底层靠近前刀面处纤维化,流动速度减缓, 切屑弯曲,切削与刀具接触温度升高。 (3)第三变形区III:工件已加工表面与后刀面接 触的区域,存在纤维化与 加工硬化,变形较密集。
第一节 切削变形与切屑的形成
2.切屑的类型及切屑控制(图a∽c为切削塑性材料,图d为切削脆性材料)
加工一般钢料或其它塑性材料时,常常在前刀 面处粘着一块剖面有时呈三角状的硬块。它的 硬度很高,通常是工件材料的2—3倍,在处于 比较稳定的状态时,能够代替 刀刃进行切削。这块冷焊在前 刀面上的金属称为积屑瘤或刀 瘤。(积屑瘤的形成过程: )
第一节 切削变形与切屑的形成
➢切屑瘤对切削过程的影响: 1)实际前角增大 2)增大切削厚度,可能引起振动 3)是加工表面粗糙度增大 4)对刀具寿命有影响
• “可接受”的切屑标准:不妨碍正常的加 工;不影响操作者的安全;易于清理、存 放和搬运。
• 切削控制的措施:在前刀面上磨制出断屑 槽或使用压块式断屑器。
第一节 切削变形与切屑的形成
断屑槽的基本形式:
L:切屑在前刀面上的接触长度 R:卷屑槽半径
第一节 切削变形与切屑的形成
3.积屑瘤现象 ➢ 在切削速度不高而又能形成连续切屑的情况下,
第一节 切削变形与切屑的形成
➢切屑控制: • “不可接受”的切屑:切削条件恶劣导致。
影响主要有拉伤工件的已加工表面;划伤 机床;造成刀具的早期破损;影响操作者 的安全。
• 切屑控制:在切削加工中采取适当的措施 来控制切屑的卷曲、流出与折断,使形成 “可接受”的良好屑形。
第一节 切削变形与切屑的形成
Fc——切削力,单位:N; vc——切削速度,单位:m/s。
三、切削功率的计算
(2)切削功率
Pc Fcvc
1000
单位:kw
PE
Pe
——机床传动效率,一般,取 = 0.75~0.85。
四、影响切削力的因素
总切削力的来源有两个方面: 一是克服被加工材料对弹性变形和塑性 变形的抗力; 二是克服切屑对刀具前面的摩擦阻力和 工件表面对刀具后面的摩擦阻力。
第二节 切削力和切削功率
一、切削力的来源与分解 (1)总切削力的分解
1)切削力Fc (Fz) 2)背向力Fp (Fy) 3)进给力Ff (Fx)
一、切削力的来源与分解
(1)总切削力的分解
F F z2F x2y F z2F x2F y2
F y F xy cors
F xF xs y in r
Fy (0.15~0.7)Fz Fx (0.1~00.6F)z
二、切削的经验公式
2. 切削力的经验公式
切削力 F zCFzaPX FzfyFzK Fz
二、切削的经验公式
切削力 背向力 进给力
F zCFzaPXFzfyFzKFz
FyCFyaPXFyfyFyKFy
FxCFxaPXFxfyFxKFx
三、切削ห้องสมุดไป่ตู้率的计算
(2)切削功率
Pe Fcvc
1000
单位:kw
由此可见,从减小切削力和节省动力消 耗的观点出发,在切除相同余量的条件
四、影响切削力的因素
1)工件材料的性能对切削力有显著的影响。 工件材料的硬度或强度愈高,材料的
剪切屈服强度也愈高,发生剪切变形的抗 力也愈大,故切削力也愈大。
四、影响切削力的因素
2)切削用量对切削力的影响。
a)背吃刀量ap 和进给量f 对切削力的影响;
↑ 背吃刀量ap ↑
进给量f↑
AD ↑
变形抗力 摩擦力
• 随着刀具的连续移动,原来处于始滑移面 上的金属不断向刀具靠拢,应力和变形也 逐渐加大。在终滑移面OE上,应力和变形 达到最大值。
• 越过OE面,切削层金属将脱离工件基体, 沿着前刀面流出而形成切屑。
第一节 切削变形与切屑的形成
➢ 三个变形区: (1)第一变形区I:从OA线到OE线内的区域,伴随
第一节 切削变形与切屑的形成
一.切削过程及切屑种类
1.切屑形成过程:对塑性金属进行切削时, 切屑的形成过程就是切削层金属的变形过 程。 •当工件受到刀具的挤压以后,切削层金属 在始滑移面OA以左发生弹性变形。在OA面 上,应力达到材 料的屈服强度,则 发生塑性变形,产 生滑移现象。
第一节 切削变形与切屑的形成
第一节 切削变形与切屑的形成
➢积屑瘤产生原因分析: 积屑瘤的产生以及它的积聚高度与金属材料
的硬化性质有关,也与刃前区的温度和压力分布 有关。一般说来,塑性材料的加工硬化倾向愈强, 愈易产生积屑瘤;温度与压力太低,不会产生积 屑瘤;反之,温度太高,产生弱化作用,也不会 产生积屑瘤。走刀量保持一定时,积屑瘤高度与 切削速度有密切关系。
切削类型
切削条件
特
征
a)带状切屑 b)挤裂切屑 c)单元切屑 d)崩碎切屑
切削厚度较小,切削速 度较高,刀具前角较大
切削速度较低,切削厚 度较大,刀具前角较小
相比b)进一步减小刀具 前角,减低切削速度
加工硬脆材料时切削厚 度较大时产生
内表面光滑,外表面毛茸 内表面有裂纹,外表面呈锯齿形 整个单元被切离 形状是不规则的,表面是凸凹不平的