双色模具的设计及注塑成型
双色模具设计原理
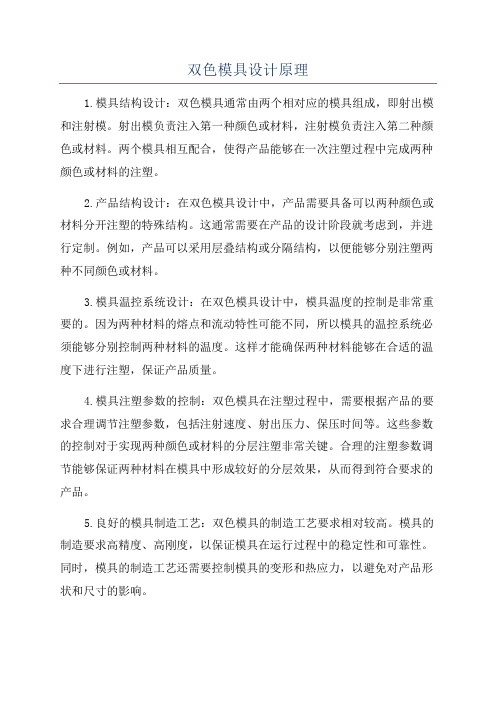
双色模具设计原理1.模具结构设计:双色模具通常由两个相对应的模具组成,即射出模和注射模。
射出模负责注入第一种颜色或材料,注射模负责注入第二种颜色或材料。
两个模具相互配合,使得产品能够在一次注塑过程中完成两种颜色或材料的注塑。
2.产品结构设计:在双色模具设计中,产品需要具备可以两种颜色或材料分开注塑的特殊结构。
这通常需要在产品的设计阶段就考虑到,并进行定制。
例如,产品可以采用层叠结构或分隔结构,以便能够分别注塑两种不同颜色或材料。
3.模具温控系统设计:在双色模具设计中,模具温度的控制是非常重要的。
因为两种材料的熔点和流动特性可能不同,所以模具的温控系统必须能够分别控制两种材料的温度。
这样才能确保两种材料能够在合适的温度下进行注塑,保证产品质量。
4.模具注塑参数的控制:双色模具在注塑过程中,需要根据产品的要求合理调节注塑参数,包括注射速度、射出压力、保压时间等。
这些参数的控制对于实现两种颜色或材料的分层注塑非常关键。
合理的注塑参数调节能够保证两种材料在模具中形成较好的分层效果,从而得到符合要求的产品。
5.良好的模具制造工艺:双色模具的制造工艺要求相对较高。
模具的制造要求高精度、高刚度,以保证模具在运行过程中的稳定性和可靠性。
同时,模具的制造工艺还需要控制模具的变形和热应力,以避免对产品形状和尺寸的影响。
总结起来,双色模具设计原理包括模具结构设计、产品结构设计、模具温控系统设计、模具注塑参数的控制以及良好的模具制造工艺。
只有在这些方面都能够做到合理设计和工艺控制,才能够实现高质量的双色产品的生产。
双色模具设计的原理是非常复杂的,需要设计师和工程师在实践中不断摸索和总结经验,以满足市场对双色产品的需求。
双色模具设计及注塑时要注意的事项

双色模具设计及注塑时要注意的事项双色模具就是两种塑胶材料在同一台注塑机上注塑,分两次成型,通常由两套模具组成,后模要旋转180度,而前模不动,但是产品只出模一次的模具。
一般这种模塑工艺也叫双料注塑,且需要专门的双色注塑机。
双色模具设计及注塑时要注意的事项有:1、两型腔和型芯的运水布置尽量充分,并且均衡、一样。
2、模具的前模以中心旋转180º后,必须与后模吻合。
设计时必须注意这一点。
3、99%的情况是先注塑产品的硬胶部分,再注塑产品的软胶部分。
因为软胶易变形。
先成型成型温度高的塑胶原材料,再成型温度低的。
4、三板模的水口最好能设计成可以自动脱模动作。
特别要注意软胶水口的脱模动作是否可靠。
5、在设计时,请仔细查看双色模具注塑机的参数数据,如,最大容模厚度、最小容模厚度、顶棍孔距离等。
6、注塑时,第一次注塑成型的产品尺寸可以略大,以使它在第二次成型时能与另一个型腔压得更紧,以达到封胶的作用。
7、前模的两个形状是不同的,分别成型1种产品。
而后模的两个形状完全一样。
(注意:如有不一样,要做前模滑块来保证后模一致)8、注意在第二次注塑时,塑胶的流动是否会冲动第一次已经成型好的产品,使其胶位变形?如果有这个可能,一定要想办法改善。
9、为了使两种塑胶“粘”得更紧,要考虑材料之间的“粘性”以及模具表面的粗糙度。
双色模具注塑有专门的TPU;而模具表面越光滑,它们“粘‘得更紧。
10、在设计第二次注塑的型腔时,为了避免型腔插(或擦)伤第一次已经成型好的产品胶位,可以设计一部分避空。
但是必须慎重考虑每一处封胶位的强度,即:在双色模具注塑中,是否会有在大的注塑压力下,塑胶发生变形,导致第二次注塑可能会有批锋产生的可能。
双色模具设计及双色注塑成型的36条经验
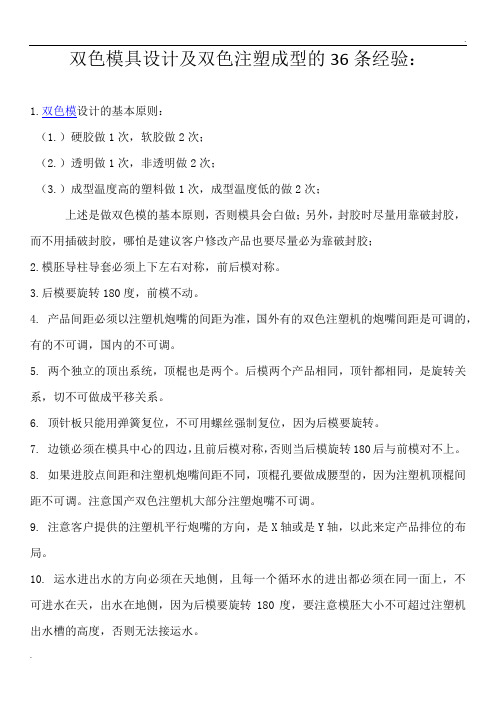
双色模具设计及双色注塑成型的36条经验:1.双色模设计的基本原则:(1.)硬胶做1次,软胶做2次;(2.)透明做1次,非透明做2次;(3.)成型温度高的塑料做1次,成型温度低的做2次;上述是做双色模的基本原则,否则模具会白做;另外,封胶时尽量用靠破封胶,而不用插破封胶,哪怕是建议客户修改产品也要尽量必为靠破封胶;2.模胚导柱导套必须上下左右对称,前后模对称。
3.后模要旋转180度,前模不动。
4. 产品间距必须以注塑机炮嘴的间距为准,国外有的双色注塑机的炮嘴间距是可调的,有的不可调,国内的不可调。
5. 两个独立的顶出系统,顶棍也是两个。
后模两个产品相同,顶针都相同,是旋转关系,切不可做成平移关系。
6. 顶针板只能用弹簧复位,不可用螺丝强制复位,因为后模要旋转。
7. 边锁必须在模具中心的四边,且前后模对称,否则当后模旋转180后与前模对不上。
8. 如果进胶点间距和注塑机炮嘴间距不同,顶棍孔要做成腰型的,因为注塑机顶棍间距不可调。
注意国产双色注塑机大部分注塑炮嘴不可调。
9. 注意客户提供的注塑机平行炮嘴的方向,是X轴或是Y轴,以此来定产品排位的布局。
10. 运水进出水的方向必须在天地侧,且每一个循环水的进出都必须在同一面上,不可进水在天,出水在地侧,因为后模要旋转180度,要注意模胚大小不可超过注塑机出水槽的高度,否则无法接运水。
11. 第一次注塑的产品要放在非操作侧,因为第一次注塑后产品要旋转180度进行第二次注塑,正好转到操作侧,方便取产品。
12. 出口模的码模位要在操作侧和非操作侧,不可在天地侧,因为他们的产品要全自动。
13. 分型面的注意事项:后模分型面要将两个产品合并后取得的分型面为后模的;前模分型面要取单个产品的即可,不可取合并后的产品分型面。
14. 前后法兰的公差为负0.05mm,两法兰间距公差为正负0.02mm,顶棍与顶棍孔的间隙单边为 0.1mm,前后模导套导柱的中心距公差为正负0.01,模框四边和深度都要加公差,否则当后模旋转180度后,因高低不一致而产生批锋。
双色模介绍及设计规范——【注塑模具】
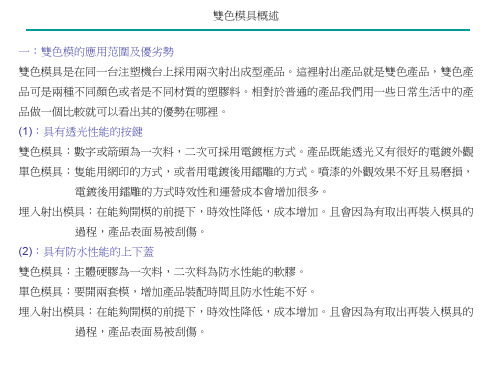
頂出板可為一組
一二次的公模入 子不一樣,就可 以成型普通雙色 模很難做的產品
雙色模具概述 10:後記 綜上所述,我們對於雙色模具就會有一個簡單的了解。對於以後所設計的模具要學會靈活運 用,才能更好將模具設計的合理化。
我們所接觸到的射出機台多為臥式轉盤,當然機台也有立式轉盤,也還有很多機台兩個射嘴並 不是平行的,有可能是垂直又或是成一定角度的。這可以根據實際需求來定做成型機台。
相對於公模側,母模側的 出水就自由的多,理論上 四個方向都可以出水,但 考慮到成型和架模等等的 因素在一起的話,建議將 水路做於天地側,再次一 級便是做於機台的外側, 晝量不要將水路出在機台 的中心側,很多時候在中 心側是無法接水。
雙色模具概述
8:雙色模之滑塊篇 之所以會將滑塊單獨從機構中提出來介紹,最主要的原因還是雙色模的一二次公模要為相同(轉 中板方式除外),那麼滑塊很多時候滑塊不得不做在母模側來完成機構要求。如下圖:
可做模仁避空
一次模具
二次模具
二次射出封膠時晝量要以靠破一次塑膠的方式,哪怕隻有0.1~0.2的膠位靠破。在沒有辦法的情
況下才可採用插破一次塑膠封膠,插破角度最小應取3度。如下圖:
一次膠
二次膠
插破封膠不好,角度 應做大,3度以上
雙色模具概述
7:雙色模之水路簡介 雙色模由於射出機台的特殊性,其公母模側接水的方式也會有所不同。如下圖:
電鍍後用鐳雕的方式時效性和運營成本會增加很多。 埋入射出模具:在能夠開模的前提下,時效性降低,成本增加。且會因為有取出再裝入模具的
過程,產品表面易被刮傷。 (2):具有防水性能的上下蓋 雙色模具:主體硬膠為一次料,二次料為防水性能的軟膠。 單色模具:要開兩套模,增加產品裝配時間且防水性能不好。 埋入射出模具:在能夠開模的前提下,時效性降低,成本增加。且會因為有取出再裝入模具的
双色注塑模具设计及双色注塑成型注意事项与经验 共三十六条

双色注塑模具设计及双色注塑成型注意事项与经验共三十六条1.双色注塑模具设计的基本原则:(1.)硬胶做1次,软胶做2次;(2.)透明做1次,非透明做2次;(3.)注塑成型温度高的塑料做1次,成型温度低的做2次;上述是做双色注塑模具的基本原则,否则注塑模具会白做;另外,封胶时尽量用靠破封胶,而不用插破封胶,哪怕是建议客户修改产品也要尽量必为靠破封胶;2.模胚导柱导套必须上下左右对称,前后模对称。
3.后模要旋转180度,前模不动。
4. 产品间距必须以注塑机炮嘴的间距为准,国外有的双色注塑机的炮嘴间距是可调的,有的不可调,国内的不可调。
5. 两个独立的顶出系统,顶棍也是两个。
后模两个产品相同,顶针都相同,是旋转关系,切不可做成平移关系。
6. 顶针板只能用弹簧复位,不可用螺丝强制复位,因为后模要旋转。
7. 边锁必须在模具中心的四边,且前后模对称,否则当后模旋转180后与前模对不上。
8. 如果进胶点间距和注塑机炮嘴间距不同,顶棍孔要做成腰型的,因为注塑机顶棍间距不可调。
注意国产双色注塑机大部分注塑炮嘴不可调。
9. 注意客户提供的注塑机平行炮嘴的方向,是X轴或是Y轴,以此来定产品排位的布局。
10. 运水进出水的方向必须在天地侧,且每一个循环水的进出都必须在同一面上,不可进水在天,出水在地侧,因为后模要旋转180度,要注意模胚大小不可超过注塑机出水槽的高度,否则无法接运水。
11. 第一次注塑的产品要放在非操作侧,因为第一次注塑后产品要旋转180度进行第二次注塑,正好转到操作侧,方便取产品。
12. 出口模的码模位要在操作侧和非操作侧,不可在天地侧,因为他们的产品要全自动。
13. 分型面的注意事项:后模分型面要将两个产品合并后取得的分型面为后模的;前模分型面要取单个产品的即可,不可取合并后的产品分型面。
14. 前后法兰的公差为负0.05mm,两法兰间距公差为正负0.02mm,顶棍与顶棍孔的间隙单边为0.1mm,前后模导套导柱的中心距公差为正负0.01,模框四边和深度都要加公差,否则当后模旋转180度后,因高低不一致而产生批锋。
双色模具的设计及注塑成型
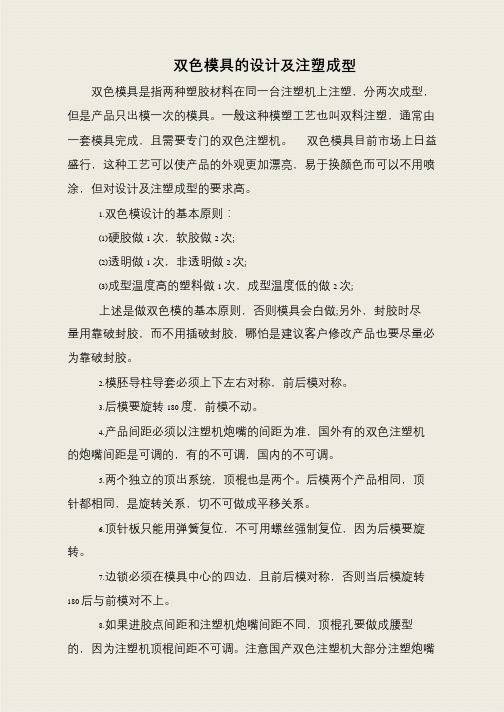
双色模具的设计及注塑成型
双色模具是指两种塑胶材料在同一台注塑机上注塑,分两次成型,但是产品只出模一次的模具。
一般这种模塑工艺也叫双料注塑,通常由一套模具完成,且需要专门的双色注塑机。
双色模具目前市场上日益盛行,这种工艺可以使产品的外观更加漂亮,易于换颜色而可以不用喷涂,但对设计及注塑成型的要求高。
1.双色模设计的基本原则:
(1)硬胶做1 次,软胶做2 次;
(2)透明做1 次,非透明做2 次;
(3)成型温度高的塑料做1 次,成型温度低的做2 次;
上述是做双色模的基本原则,否则模具会白做;另外,封胶时尽
量用靠破封胶,而不用插破封胶,哪怕是建议客户修改产品也要尽量必为靠破封胶。
2.模胚导柱导套必须上下左右对称,前后模对称。
3.后模要旋转180 度,前模不动。
4.产品间距必须以注塑机炮嘴的间距为准,国外有的双色注塑机的炮嘴间距是可调的,有的不可调,国内的不可调。
5.两个独立的顶出系统,顶棍也是两个。
后模两个产品相同,顶针都相同,是旋转关系,切不可做成平移关系。
6.顶针板只能用弹簧复位,不可用螺丝强制复位,因为后模要旋转。
7.边锁必须在模具中心的四边,且前后模对称,否则当后模旋转180 后与前模对不上。
8.如果进胶点间距和注塑机炮嘴间距不同,顶棍孔要做成腰型的,因为注塑机顶棍间距不可调。
注意国产双色注塑机大部分注塑炮嘴。
双色模具注塑原理
双色模具注塑原理
双色模具注塑是一种先进的注塑技术,它可以使产品在注塑成型时同时具有两种不同的颜色或材料。
这种技术在塑料制品生产中得到了广泛的应用,可以生产出更加美观和功能性更强的产品。
双色模具注塑的原理是利用一台注塑机和两个或多个注射装置,通过交替注射不同颜色或材料的塑料,使得产品在成型过程中可以同时具有两种不同的颜色或材料。
这种技术需要精密的模具设计和注射控制,以确保两种塑料能够准确地注射到模具中,并且能够完美地结合在一起。
在双色模具注塑中,首先需要设计好产品的结构和颜色分布,然后制作出相应的双色模具。
在注塑成型过程中,注射装置会交替注射不同颜色或材料的塑料,模具会根据设计要求将两种塑料结合在一起,最终形成具有两种颜色或材料的产品。
双色模具注塑技术可以生产出各种类型的产品,例如汽车零部件、家用电器配件、日用品等。
这种技术不仅可以提高产品的美观度,还可以增加产品的功能性,例如在产品的外壳上使用不同颜色的塑料来标识不同的功能区域,或者在产品的表面上使用不同材料的塑料来增加产品的抗磨损性能。
总的来说,双色模具注塑技术是一种先进的注塑技术,它可以生产出更加美观和功能性更强的产品。
随着注塑技术的不断发展,相信双色模具注塑技术在未来会得到更广泛的应用,为塑料制品行业带来更多的创新和发展。
双色注塑模工艺分析及模具设计
双色注塑模工艺分析及模具设计
1.工艺分析
a.产品结构和尺寸:双色注塑产品的结构和尺寸对注塑工艺有很大的
影响。
需要分析产品的复杂程度、壁厚分布、缩水率等因素,确定是否适
合双色注塑工艺。
b.材料特性:双色注塑产品通常由两种不同的材料组成,需要对两种
材料的熔融温度、熔融指数、流动性等进行分析,确保两种材料能够良好
地结合在一起。
c.注塑工艺参数:包括注射压力、注射速度、模具温度、冷却时间等。
需要通过试验和仿真模拟,确定合适的注塑工艺参数,避免产品缺陷如翘曲、留痕等。
2.模具设计
a.模具结构设计:双色注塑模具通常由注塑模芯、注塑模腔、移位机构、分色机构等部分组成。
需要根据产品的结构和成型要求设计合理的模
具结构,确保双色注塑成型的准确性和可靠性。
b.分色机构设计:双色注塑需要通过分色机构实现两种不同颜色材料
的注入和分离。
需要考虑分色机构的类型(旋转式、滑动式等)、分色位
置和过渡区域的设计,确保双色注塑产品的色彩和图案能够完美呈现。
c.冷却系统设计:双色注塑需要通过冷却系统来散热降温,快速固化
成型。
需要设计合理的冷却水路,保证模具表面温度均匀分布,避免产品
变形和缺陷。
d.模具材料选择:双色注塑模具通常由优质的工具钢制成,需要根据
产品的批量和质量要求,选择合适的模具材料,以确保模具寿命和成型效果。
以上就是双色注塑模工艺分析及模具设计的简要介绍。
在实际生产中,还需要通过试制和改进不断优化工艺和模具设计,提高双色注塑产品的质
量和产能。
双色模具注塑成型及设计,你了解多少?
双色模具注塑成型及设计,你了解多少?随着技术和工艺的不断更新,注塑工艺也有了很大的发展,其中双色模具注塑成型技术已经得到广泛的应用。
在本篇文档中,我们将对双色模具注塑成型技术进行详细介绍,并探讨一些设计上的考虑。
双色注塑成型技术的简介双色注塑成型技术是一种将两种不同的材料注塑在同一模具中的技术。
它可以在同一件制品上实现两种颜色、两种软硬度、两种材料的结合。
这种技术可以大大的降低产品的成本,加速了产品的开发与生产速度,同时也提高了产品的质量和美观度。
双色注塑成型技术的应用场景双色注塑成型技术的应用场景非常广泛,如手机外壳、电器外壳、玩具、医疗器械、汽车内饰等领域。
其中,手机外壳是最常见的应用场景之一。
这种技术可以实现手机外壳的多种颜色,同时提高了手机外壳的品质,增强了手机外壳的耐用性。
双色注塑成型技术的优点双色注塑成型技术相比于传统注塑工艺有以下优点:•可以通过一个模具制作出多种颜色、硬度、材料的产品,从而降低了成本;•可以大大提高产品的美观度和质量,满足消费者的个性化需求;•节约了生产时间,大大提高了生产效率;•双色注塑成型技术可以大大缩减生产时的所需工艺,降低了生产成本,提高了生产效率。
双色注塑成型技术的设计考虑在使用双色注塑成型技术时,设计者需要注意以下事项:1.材质选择:在双色注塑成型技术中,使用的材料需要具备良好的相容性,同时还需要考虑材料的硬度、强度、耐热性以及高温和低温的性能。
因此,材料的选择非常重要。
2.模具设计:双色注塑成型技术需要一个特殊的模具,这种模具有两个型腔分别注塑两种不同颜色的材料。
模具设计需要考虑模具的材料、尺寸、射出口、挂件等因素。
3.工艺控制:双色注塑成型技术需要精确定位两个型腔,保证注塑的多种材料能够精准的覆盖到所需的位置,这需要高超的工艺控制水平。
双色注塑成型技术的未来双色注塑成型技术在未来将继续得到广泛的应用,随着工艺和技术的不断推进,它可以用于更多的领域,从而提高产品的质量和美观度,满足消费者的个性化需求,同时也可以大大缩减生产周期,降低生产成本。
双色模具设计及双色注塑成型的36条经验
双色模具设计及双色注塑成型的36条经验1.双色模具设计要考虑产品的结构和使用功能,合理设计产品的内外形状,确保产品在注塑成型时能够顺利分离并达到预期效果。
2.双色模具设计中要注意两种颜色的材料流动和混色问题,避免颜色交叉污染。
3.在双色注塑过程中,要控制两种颜色的注射压力和速度,以避免色块儿不均匀或颜色混合不好的问题。
4.双色模具设计要合理设置副模和主模的开关位置和开关顺序,确保两种颜色的注塑成型能够同时进行。
5.在双色注塑过程中,需要合理设置两种颜色的熔体温度和熔体流率,以确保两种颜色能够顺利融合。
6.双色模具设计中要考虑产品的尺寸收缩和变形问题,确保产品的尺寸和外观质量。
7.双色注塑时要注意注塑机的射胶量和压力,以确保两种颜色注塑料能够充满整个模具腔体。
8.双色模具设计要考虑产品的冷却和固化时间,以避免产品变形和缩水的问题。
9.双色注塑时要注意两种颜色注塑料的开合模时间和速度,以确保产品分离顺利。
10.双色模具设计中要考虑产品的镂空和细节处理,确保产品的复杂结构能够正确注塑。
11.双色注塑时要注意产品的填充速度和压力,以避免产品出现短充或气泡等缺陷。
12.双色模具设计要考虑模具的损耗问题,合理选择模具材料和加工工艺,延长模具的使用寿命。
13.双色注塑时要注意熔体温度的控制,避免产品出现烧焦和热分解等问题。
14.双色模具设计要考虑产品的注塑料和色母的选择,确保颜色稳定和耐磨性能。
15.双色注塑时要注意产品的射胶位置和射胶方式,以确保两种颜色注塑料能够充分融合。
16.双色模具设计中要考虑产品的模胚和射胶道的设计,确保产品的流畅性和充满性。
17.双色注塑时要注意注塑成型周期和循环时间,以提高生产效率和降低成本。
18.双色模具设计要考虑产品的特殊要求和辅助工艺,如压纹、喷漆等,提高产品的附加值。
19.双色注塑时要注意产品的表面光洁度和质量要求,以满足消费者对产品外观的要求。
20.双色模具设计要考虑产品的组装和拆卸问题,以方便产品的维修和更换。
- 1、下载文档前请自行甄别文档内容的完整性,平台不提供额外的编辑、内容补充、找答案等附加服务。
- 2、"仅部分预览"的文档,不可在线预览部分如存在完整性等问题,可反馈申请退款(可完整预览的文档不适用该条件!)。
- 3、如文档侵犯您的权益,请联系客服反馈,我们会尽快为您处理(人工客服工作时间:9:00-18:30)。
双色模具的设计及注塑成型
双色模具的设计及注塑成型
双色模具是指两种塑胶材料在同一台注塑机上注塑,分两次成型,但是产品只出模一次的模具。
一般这种模塑工艺也叫双料注塑,通常由一套模具完成,且需要专门的双色注塑机。
双色模具目前市场上日益盛行,这种工艺可以使产品的外观更加漂亮,易于换颜色而可以不用喷涂,但对设计及注塑成型的要求高。
1.双色模设计的基本原则:
(1)硬胶做1次,软胶做2次;
(2)透明做1次,非透明做2次;
(3)成型温度高的塑料做1次,成型温度低的做2次;
上述是做双色模的基本原则,否则模具会白做;另外,封胶时尽量用靠破封胶,而不用插破封胶,哪怕是建议客户修改产品也要尽量必为靠破封胶。
2.模胚导柱导套必须上下左右对称,前后模对称。
3.后模要旋转180度,前模不动。
4.产品间距必须以注塑机炮嘴的间距为准,国外有的双色注塑机的炮嘴间距是可调的,有的不可调,国内的不可调。
5.两个独立的顶出系统,顶棍也是两个。
后模两个产品相同,顶针都相同,是旋转关系,切不可做成平移关系。
6.顶针板只能用弹簧复位,不可用螺丝强制复位,因为后模要旋转。
7.边锁必须在模具中心的四边,且前后模对称,否则当后模旋转180后与前模对不上。
8.如果进胶点间距和注塑机炮嘴间距不同,顶棍孔要做成腰型的,因为注塑机顶棍间距不可调。
注意国产双色注塑机大部分注塑炮嘴不可调。
9.注意客户提供的注塑机平行炮嘴的方向,是X轴或是Y轴,以此来定产品排位的布局。
10.运水进出水的方向必须在天地侧,且每一个循环水的进出都必须在同一面上,不可进水在天,出水在地侧,因为后模要旋转180度,要注意模胚大小不可超过注塑机出水槽的高度,否则无法接运水。
11.第一次注塑的产品要放在非操作侧,因为第一次注塑后产品要旋转180度进行第二次注塑,正好转到操作侧,方便取产品。
12.出口模的码模位要在操作侧和非操作侧,不可在天地侧,因为他们的产品要全自动。
13.分型面的注意事项:后模分型面要将两个产品合并后取得的分型面为后模的;前模分型面要取单个产品的即可,不可取合并后的产品分型面。
14.前后法兰的公差为负0.05mm,两法兰间距公差为正负0.02mm,顶棍与顶棍孔的间隙单边为0.1mm,前后模导套导柱的中心距公差为正负0.01mm,模框四边和深度都要加公差,否则当后模旋转180度后,因高低不一致而产生批锋。
框深公差为负0.02mm。
15.如果在模胚厂已经将模胚加工完,本厂要加工唧嘴和顶棍孔时,要以4个导柱导套孔的间距中心为基准取数,否则偏差太多,容易卡死模。
订模胚时要注明是双色模胚,四个导柱导套和框对称,后模旋转180度后能与前模匹配。
16.如果是后模旋转的双色话就简单多了..两个前模芯一样...一边注塑好硬胶后.旋转180度(注意产品转的时候不能掉落,浇口可以自动分离) , 转到另外一边后再注塑软胶...注塑硬胶无需布置顶针...只需布置在软胶这边模芯即可...另外缩水要注意...如果软胶完全把硬胶缠住..则只需放硬胶的缩水...如果是轮廓相接则硬胶软胶都要放缩水。
17.如果是一套模具的双色模具的话,那就是一个直炮筒,一个90度的炮筒射胶,不需要旋转,只需一个模芯,软胶与硬胶的分离方法靠行位封胶。
18.Cavity的两个外形是不同的,分别成型1种产品。
而Core的两个外形完好一样。
19.模具的前、后模以中心旋转180°后,必需吻合。
设计时必需做这个检查动作。
20.留意顶针孔的位置,最小间隔210mm。
大的模具须恰当增加顶棍孔的数量。
并且,由于注塑机本身附带的顶针不够长,所以我们的模具中必需设计加长顶针,顶针长出模胚底板150mm左右。
21.后模底板上必需设计2个定位圈。
22.前模面板加A板的总厚度不能少于170mm。
请认真查看这种型号的注塑机的其它参考数据,比方,最大容模厚度、最小容模厚度、顶棍孔间隔等。
23.前侧SPRUE的深度不要超越65mm。
上侧(大水口)SPRUE的顶部到模胚中心的间隔不小于150mm。
24.在设计第二次注塑的CAVITY时,为了防止CAVITY插(或擦)伤第一次曾经成型好的产品胶位,可以设计一局部避空。
但是必需慎重思索每一处封胶位的强度,即:在注塑中,能否会有在大的注塑压力下,塑胶发作变形,招致第二次注塑可能会有批锋产生的可能。
25.注塑时,第一次注塑成型的产品尺寸可以略大,以使它在第二次成型时能与另一个CAVITY压得更紧,以到达封胶的作用。
26.在A、B板合模前,要留意前模Slider或Lifter能否会先复位而压坏产品?如此,必需想方法使在A、B板先合模,之后前模的SLIDER或LIFET才干复位。
27. 两CAVITY和CORE 的运水布置尽量充分,并且平衡、一样。
28.99%的`情况是先注塑产品的硬胶局部,再注塑产品的软胶局部。
由于软胶易变形。
29.留意在第二次注塑时,塑胶的活动能否会冲动第一次曾经成型好的产品,使其胶位变形?假设有这个可能,一定要想方法改善。
30.双色模具一定要谨慎选择浇口位置。
一次产品最好选择潜伏式进胶,这样产品和流道可以自动切断。
当无法采用潜伏式进胶时,可以考虑三板模或者热流道模具。
一次料如果是点浇口,要做波仔,避免因一次进点残留而碰穿二次料。
31.双色注塑模具常采用旋转注塑模。
旋转注塑模两个位置上的凸模/凹模要求尺寸、精度一致,且与凹模/凸模配合良好。
当无法利用双色注塑机上的顶出脱模机构时,回转台上必须要设置液压顶出脱模机构。
32.双色模具注塑成型通常选用不同颜色的同一种塑料,也可以是两种不同的塑料原料,这个时候就要考虑两种材料的界面作用、收缩率差异、加工工艺参数等方面了。
双色注塑制品一般以ABS、PC等硬塑料配合TPE软塑料为主,由于成本或应用的关系,要充分考虑采用的两种物料之间可能没有良好的粘合性和融合性,两种料之间结合处的模具处理(一般都会有压花纹路的现象或者需要做封模槽)还有料厚的厚度等很多问题!为了使两种塑胶“粘”得更紧,要思索材料之间的“粘性”以及模具外表的粗糙度。
双色注塑有专用的TPU材料;而模具外表越光滑,它们“粘得越紧。
33.一般来说,双色模具的缩水率取决于一次材料。
因为一次材料已经把塑料制品的轮廓撑住了,二次材料不会收缩更多。
至于如何确定一次材料和二次材料,这有许多要考虑到的因素,比如原料流动性,塑料制品形状等等。
34.留意前后模的定位;一切插穿、靠破面的斜度落差尽量大些,要0.1mm以上。
35.ABS/PC,ABS/PC+ABS,ABS/PMMA双色注塑时,需要先注塑温度较高的PC,PC+ABS 或者PMMA。
如果是透明面壳模具时大部分采用倒装模具结构。
36.透明的大的双色注塑对于结构设计而言是需要注意的地方:
A. 浇口位置的预留,必须和模具厂预先达成一致;
B. 材料厚度推荐使用透明的0.8mm以上,非透明的0.7mm以上,非透明的尽量采用浅色,有LED灯时候注意遮光;
C. 透明件分模面和孔的地方宽度一致,宽度推荐0.5mm,曲面接顺,避免侧面看,能
透过很远,不美观,尽量减少孔;
D. 非透明件的厚度有限,上面筋条等结构尽量是在0.5-0.6mm之间,避免缩水;
E. 就目前而言不推荐做带主镜片的双色注塑,模具和产品成本太高,对模具厂家的设备和技术水平有相当的要求,做的话,需要对方给出整个一个流程的解决详细方案供评估,针对中间的环节都需要审查;
F. 对于大面积的双色注塑件,两个关键的测试是跌落和冷热冲击,在这两个测试里面,透明件和非透明件容易脱开。
冷热冲击-40 -65,时间48小时。
G. 双色件上结构尽量简化,复杂的做到配合件上面,非透明件的筋条宽度尽量在
0.5-0.6mm,避免缩水。