汽车用电镀层和化学处理层
QC 汽车用涂镀层和化学处理层

QC/T 625—1999前言本标准是对JB 2864—1981 和ZB T 04004—1988 修订版。
本标准自生效之日起,同时代替JB 2864—1981 和ZB T O4004—1988。
本标准由国家机械工业局提出。
本标准由全国汽车标准化技术委员会归口。
本标准由基础分标准分技术委员会组织修订。
本标准主要起草单位:第一汽车集团公司工艺处。
本标准主要起草人:魏晓川、向际新。
中华人民共和国汽车行业标准QC/T 625—1999代替 JB 2864—81ZB T04 004—88汽车用涂镀层和化学处理层1 适用范围本标准规定了汽车及其附件等产品的涂镀层和化学处理层的主要技术指标、检验方法和适用条件。
本标准适用于设计师在进行汽车产品设计时使用,也适用于表面处理工作者在进行工艺设计时使用。
本标准不包括油漆类涂层。
2 引用标准下列标准所包含的条文,通过在本标准中引用而构成为本标准的条文。
在本标准出版时,所示版本均为有效。
所有标准都会被修订,使用本标准的各方应探讨使用下列标准最新版本的可能性。
GB/T 4342—1991 金属显微维氏硬度试验方法GB/T 4955-1997 金属覆盖层厚度测量阳极溶解库仑法GB/T 4956—1985 磁性金属机体上非磁性覆盖层厚度测量磁性方法GB/T 4957—1985 非磁性金属机体上非导电覆盖层厚度测量涡流方法GB/T 5267—1985 螺纹紧固件的电镀层GB/T 5270—1985 金属基体上的金属覆盖层(电沉积层和化学沉积层)附着强度试验方法GB/T 6461—1986 金属覆盖层对底材为阴极的覆盖层腐蚀试验后的电镀试样的评级GB/T 8013—1987 铝及铝合金阳极氧化阳极氧化膜的总规范GB/T 8014—1987 铝及铝合金阳极氧化阳极氧化膜厚度的定义和有关测量厚度的规定GB/T 9797—1997 金属覆盖层镍+铬和铜+镍+铬电镀层GB/T 9798—1997 金属覆盖层镍电镀层GB/T 9799—1997 金属覆盖层钢铁上的锌电镀层GB/T 9800—1988 电镀锌和电镀镉层的铬酸盐转化膜GB/T 10125—1997 人造气氛腐蚀试验盐雾试验GB/T 11250.1—1989 复合金属覆盖层厚度的测定—金相法CB/T 11376—1997 金属的磷酸盐转化膜GB/T 11379—1989 金属覆盖层工程用铬电镀层GB/T 12333—1990 金属覆盖层工程用铜电镀层GB/T 12599—1990 金属覆盖层锡电镀层GB/T 12600—1990 金属覆盖层塑料上铜+镍+铬电镀层GB/T 12967.3—1991 铝及铝合金阳极氧化膜氧化膜的铜加速醋酸盐雾试验(CASS 试验)G B/T 13346—1992 金属覆盖层钢铁上的镉电镀层 GB/T 13911—1992 金属镀覆和化学处理表示方法GB/T 13912—1992 金属覆盖层钢铁制品的热镀锌层技术要求GB/T 15519—1995 钢铁的化学氧化膜SJ/T 11110—1996 金属覆盖层工程用银和银合金电镀层3 汽车用涂镀层和化学处理层的表示方法汽车用涂镀层和化学处理层的表示方法按GB/T 13911 规定。
汽车零件电镀层及化学处理层质量标准

电镀层及化学处理层1 主题内容与适用范围本标准规定了汽车零(部)件的电镀层和化学处理层的技术规范及膜层的质量要求。
本标准适用于汽车零(部)件的电镀层及化学处理层的质量控制和验收。
2 引用标准GB4956-85 磁性金属基体上非磁性覆盖层厚度测量-磁性方法GB5270-85 金属基体上金属覆盖层-附着强度试验方法GB6458-86 金属覆盖层-中性盐雾试验(NSS试验)GB6460-86 金属覆盖层-铜加速醋酸盐雾试验(CASS试验)GB6461-86 金属覆盖层-对底材为阴极的覆盖层腐蚀试验后的电镀试样的评级GB6462-86 金属和氧化物覆盖层-横断面厚度显微镜测量方法GB9792-88 金属材料上的转化膜-单位面积上膜层质量的测定-重量法GB/T12610-90 塑料上电镀层-热循环试验3 术语3.1 主要表面在工件的某些表面上,其镀层或化学处理层对制件的外观和(或)使用性能起着重要作用。
3.2 厚度工件的主要表面上,凡是能与直径为20mm的球体相接触的部位上的厚度的最小值。
4 镀覆及化学处理的表示方法4.1 电镀表示方法基体材料/镀覆方法·镀覆名称·镀覆层厚度·镀复层特征·后处理4.2 化学处理表示方法基体材料/处理方法·处理特征·后处理(颜色)4.3 基体材料为钢铁材料时,其符号允许省略。
4.4 如果镀层或化学处理层的特征、厚度、颜色及后处理无具体要求时,其符号允许省略。
4.5 表示符号4.5.1 基体材料表示符号:金属材料用化学元素符号表示,合金材料用其主要成分的化学元素符号表示,非金属材料用国际通用缩写字母表示,如铜用Cu表示,塑料用PL表示。
4.5.2 镀覆方法和处理方法的表示符号见表1。
表1方法名称符号备注镀覆方法电镀化学镀机械镀锌铬膜EPCPMPJZnCr化学处理方法化学氧化阳极氧化锰盐磷化锌盐磷化铬酸盐处理(白色)铬酸盐处理(彩色)铬酸盐处理(绿色)铬酸盐处理(黑色)铜及合金钝化COAOMnPhZnPhBCGHP钢铁化学氧化又称发兰包括镀铬阳极松孔磷化无特定要求时只标注Ph磷化无特定要求时只标注Ph简称白钝化简称彩色钝化简称绿钝化简称黑钝化也用于银层钝化表示4.5.3 镀层厚度用阿拉伯数字表示,单位为μm。
汽车用起动继电器技术条件

汽车用起动继电器技术条件1.范围本标准规定了汽车用系列起动继电器的产品分类、技术要求、试验方法、检验规则和标志、包装运输及贮存。
本标准适用于汽车用起动继电器(以下简称继电器)。
2.引用标准以下标准所包含的条文,通过在本标准中引用而构成为本标准的条文。
本标准出版时,所有版本均为有效。
所有标准会被修订,使用本标准的各方应探讨使用下列标准最新版本的可能性。
JB 2864—1981 汽车用电镀层和化学处理层ZB T35001—1987 汽车电气设备基本技术条件GB/T 2828—1987 逐批检查记数抽样程序及抽样表(适用于连续批的检查)GB 191--1990 包装储存图示标志3.产品分类继电器按其标称电压分为:DC12V和DC24V。
继电器的型号按其标称电压和配套车型分为JDxx和JDxxx。
4.技术要求继电器应符合本标准的要求,并应按照经规定程序批准的图样及设计文件制造。
工作环境条件继电器应在下列条件下正常工作:a)温度-40℃~55℃b)相对湿度≤95%c)大气压力86kPa~106 kPa4.3外观4.3.1继电器零部件表面应光洁,保护层应均匀、无锈蚀、脱落等缺陷,冲印字迹应清晰、完整。
4.3.2 继电器电镀层和化学处理层应符合JB 2864标准要求。
4.4 外形及安装尺寸继电器的外形及安装尺寸应符合产品图样规定。
4.5 继电器为短时工作制,定额时间为12s。
4.6 基本性能4.6.1 闭合电压性能继电器在环境温度为23±5℃时,其闭合电压应符合表1中的规定,且其触点应可能地一次闭合,不允许有跳动合接触不良等情况。
表1 基本性能要求4.6.2断开电压性能4.6.3闭合与断开电压差性能继电器在环境温度为23±5℃时,其闭合与断开电压差应符合表1中的规定.4.7 过电流性能继电器应能承受120A负载电流历时30s的过流试验,试验后触头不得有损伤,其基本性能应符合本标准第4.6条的规定。
QC-T-218-1996汽车用转向管柱上组合开关技术条件
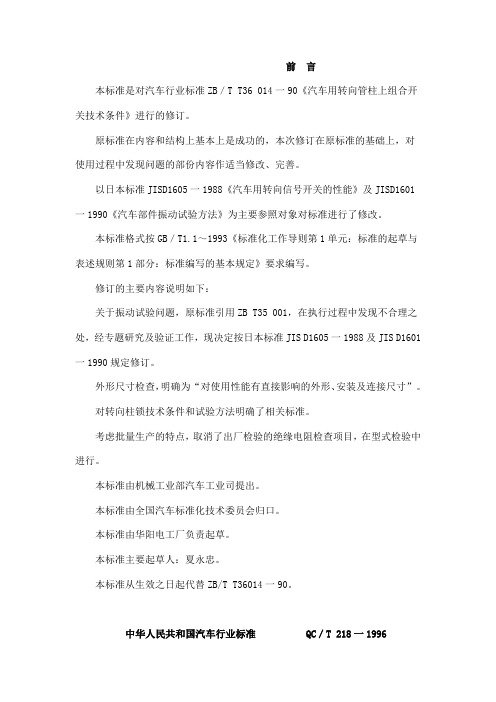
前言本标准是对汽车行业标准ZB/T T36 014一90《汽车用转向管柱上组合开关技术条件》进行的修订。
原标准在内容和结构上基本上是成功的,本次修订在原标准的基础上,对使用过程中发现问题的部份内容作适当修改、完善。
以日本标准JISD1605一1988《汽车用转向信号开关的性能》及JISD1601 一1990《汽车部件振动试验方法》为主要参照对象对标准进行了修改。
本标准格式按GB/T1.1~1993《标准化工作导则第1单元:标准的起草与表述规则第1部分:标准编写的基本规定》要求编写。
修订的主要内容说明如下:关于振动试验问题,原标准引用ZB T35 001,在执行过程中发现不合理之处,经专题研究及验证工作,现决定按日本标准JIS D1605一1988及JIS D1601 一1990规定修订。
外形尺寸检查,明确为“对使用性能有直接影响的外形、安装及连接尺寸”。
对转向柱锁技术条件和试验方法明确了相关标准。
考虑批量生产的特点,取消了出厂检验的绝缘电阻检查项目,在型式检验中进行。
本标准由机械工业部汽车工业司提出。
本标准由全国汽车标准化技术委员会归口。
本标准由华阳电工厂负责起草。
本标准主要起草人:夏永忠。
本标准从生效之日起代替ZB/T T36014一90。
中华人民共和国汽车行业标准QC/T 218一1996汽车用转向管柱上组合开关技术条件代替ZB/T T36 014 一901 范围本标准规定了汽车用转向管柱上组合开关的技术要求、检验规则和试验方法等。
本标准适用于安装在汽车转向管柱上的组合开关(以下简称“组合开关”)。
2 引用标准下列标准包含的条文,通过在本标准中引用而构成为本标准的条文。
在标准出版时,所示版本为有效。
所有标准都会被修订,使用本标准的各方应探讨使用下列标准最新版本的可能性。
GB2423.4一81电工电子产品基本环境试验规程试验Db:交变湿热试验方法GB 2423.17一81电工电子产品基本环境试验规程试验ka:盐雾试验方法GB 2828一87逐批检查计数抽样程序及抽样表(适用于连续批的检查)GB 4094—94汽车操纵件指示器和信号装置的标志JB 2864—81汽车用电镀层和化学处理层ZB T36 009一89汽车电器接线柱标记QC/T 29028一91汽车用带点火开关的转向柱锁性能试验方法QC/T 29029一91汽车用带点火开关的转向柱锁技术条件3 定义本标准采用下列定义:3.1 转向管柱上组合开关安装在汽车转向管柱上,由两个以上用以控制汽车的灯光、信号、操纵电器等部件的开关组成的装置。
汽车用电镀层和化学转化膜_CACJR-5-94

3 术语
主要表面 镀层对于工件的外观和使用性能起主要作用的表面。与ψ20mm 球面接触不上的凹面 和镀后进行涂装的表面,不作为主要表面。
4 有关说明
4.1 产品图上所标注的零件尺寸均为镀前加工尺寸,如果要求镀后保证图纸上所标注的尺
寸,必须在尺寸后加注“镀后”字样。如“
Φ10
0 −0.015
镀后”。
中国第一汽车集团公司 1994—04—08 批准
上的锌电镀层、钢铁上非防护装饰性用途的锌电镀层。 2 引用标准
GB 9799 金属覆盖层 钢铁上的锌电镀层 GB 9800 电镀锌和电镀镉层的铬酸盐转化膜 GB 4955 金属覆盖层厚度测量 阳极溶解库仑方法 GB 4956 磁性金属基体上非磁性覆盖层厚度测量 磁性方法 GB 5270 金属基体上金属覆盖层(电沉积层和化学沉积层)附着强度试验方法 3 术语 3.1 主要表面 指工件上电镀前和电镀后的某此表面。该表面上的镀层对于工件的外观和使用性能 是起主要作用的。 3.2 局部厚度 在工件的主要表面上选定的一面积内,做规定次数的厚度测量,所得测量结果的算 术平均值。 3.3 最小局部厚度 在某工件的主要表面上测到的局部厚度的最低值。 4 基体金属 本标准未规定镀锌之前基体金属的表面状态,电镀生产方和需方应对电镀前基体的 表面状态作出规定或协商认可。由于基体金属表面质量太差而使镀锌层达不到令人满意的 外观和使用性能的要求时,不能认为电镀生产质量不合要求。 5 产品设计文件应明确下列技术要求 a 镀层级别(见第 6 章); b 注明主要表面,例如用图纸或提供有适当标记的样品说明; c 基体金属的性质、表面状态或表面粗糙度; d 对镀层外观要求的必要说明; e 电镀前后的热处理要求; f 转化膜的类型; g 抽样和检验的要求; h 镀前准备、电镀和镀后处理过程中的任何特殊要求或限制。 6 镀层厚度和镀层级别
CAYT-4.16-2008 锌铝涂层
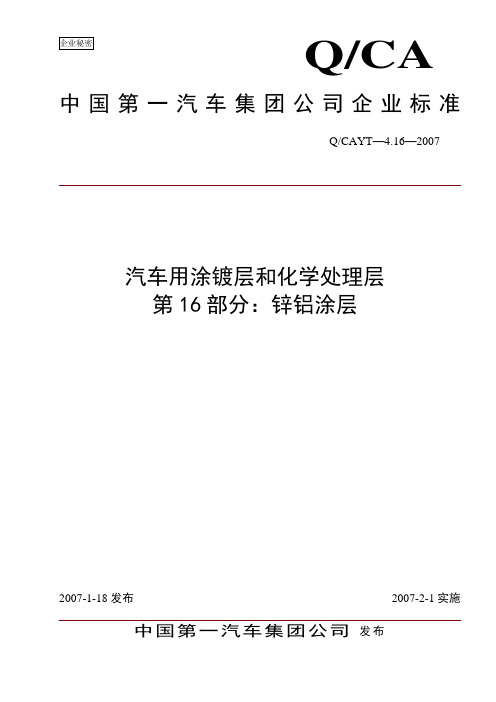
注:“M”表示基体材料,如Fe、Al等。
5 性能要求
汽车用锌铝涂层的性能要求见表2。
1
Q/CAYT—4.16—2007
表2 汽车用锌铝涂层的性能要求
序 项目
号 1 外观 2 附着性
技术指标
M/Zn-Al·A
M/Zn-Al·B M/Zn-Al·C M/Zn-Al·D
①涂层呈银灰色,不允许漏涂、起泡、流挂、堆积、变色、划
经1h-120℃ 热冲击后,按GB/T 10125的规定进行中性盐雾试验.无热存放或180℃*96h,减少盐雾 试验时间。
7 运输、包装、贮存
按供需双方协议规定执行。
2
3 术语和定义
下列术语适用于本部分。 锌铝涂层 zinc-aluminum coating 由非电解的微细鳞片状锌、铝薄片及不含铬的金属盐和有机成分组成。在高温烧结作用下形成表面 保护涂层。具有高耐蚀、耐高温、无氢脆、无污染的特点。
4 图纸标记及适用范围
图纸标记及适用范围见表1。 表1 汽车用锌铝涂层图纸标记及适用范围
图样标记
适用范围
M/Zn-Al·A 应用于中等腐蚀环境,如汽车内部或装在白车身上的零件。
M/Zn-Al·B
应用于严酷腐蚀环境或承担温度负荷腐蚀环境,如:汽车外部和底盘 区域、发动机区域零件。
汽车车标电镀工艺

汽车车标电镀工艺汽车车标电镀工艺简介•汽车车标电镀工艺是一项重要的表面处理技术,用于增强车标的美观和耐用性。
•通过电化学方法,在车标表面镀上一层金属或合金,以提升表面硬度和防腐性能。
过程1.首先,准备车标的基材,通常是铝合金或塑料材质。
2.清洗车标基材,去除表面的油污和杂质。
3.化学处理,例如酸洗或酸蚀,以增加基材表面的粗糙度,提升附着力。
4.涂层处理,在基材表面涂上一层金属溶胶或液体,用于导电和促进电镀过程。
5.电镀过程中,将车标放入电解槽中,与金属阳极相连,通过电流将金属离子沉积在基材表面,形成金属膜。
6.精整,对电镀后的车标进行表面抛光、打磨或其他工艺处理,以获得光滑且均匀的金属表面。
7.清洗,将精整后的车标进行彻底清洗,去除残留的化学物质和杂质。
8.检测,对电镀后的车标进行质量检测,确保其符合规定的标准和要求。
9.包装,将完成的车标包装好,以保护其表面不受损坏。
优点•提升外观:电镀后的车标表面光滑、亮丽,增加车辆的整体美观度。
•增加耐用性:通过电镀,车标的表面硬度和耐腐蚀性能得到提高,更加耐磨损和氧化。
•多样性选择:电镀工艺可以采用不同的金属材料,如镍、铬、铜和金等,以实现不同的装饰效果。
应用领域•汽车制造行业:车标是汽车品牌的重要标识,电镀工艺广泛应用于汽车制造过程中。
•其他工业:电镀工艺也可以应用于其他产品,如家电、电子设备、装饰品等,以提升其外观和耐用性。
结论•汽车车标电镀工艺是一项重要的表面处理技术,可为车标提供美观和耐用性。
•通过电镀工艺,车标表面形成金属膜,增加硬度和耐腐蚀性能。
•电镀工艺的广泛应用,使得不同行业的产品都能受益于其优点。
•未来随着技术的发展,电镀工艺将进一步改进和创新,以满足不断变化的市场需求。
持续创新与环保•随着社会对环保的日益关注,汽车车标电镀工艺也在不断推动着技术创新。
•现在已经有一些新型的环保电镀技术被广泛应用,比如无铬电镀技术。
•无铬电镀技术通过使用无铬镀液替代传统的六价铬酸盐镀液,达到了环保的目的。
汽车用电镀层和化学转化膜

汽车用电镀层和化学转化膜1 主题内容和适用范围本标准规定了汽车电镀及转化膜零件表面处理在图样上的标注使用条件分级本标准适用于各种类型汽车的电镀层和化学转化膜本标准金属镀层和化学处理表示方法参照GB/T139112 引用标准GB/T13911 金属镀覆和化学处理表示方法GB197 普通螺纹公差与配合GB6458 金属覆盖层中性盐雾试验(NSS试验)GB6460 金属覆盖层铜加醋酸盐雾试验(CASS试验)GB6461 对底材为阴极的覆盖层腐蚀试验后的电镀试样的评级3 术语主要表面镀层对于工件的外观和使用性能起主要作用的表面,与¢29mm地球接触不上的凹面和镀后进行涂装的表面,不作为主要表面。
4 有关表面4.1产品图上所标注的零件尺寸均为镀前加工尺寸,如果要求镀后保证图纸上所标注的尺寸,必须在图纸后加注“镀后”字样。
如“¢100-0。
015镀后”。
4.2 产品图所表注的表面粗糙度均指镀前加工的表面的表面粗糙度。
如果要求镀后保证图纸上所表注的表面粗糙度,必须在表面粗糙度代号后加注“镀后”字样。
4.3需要镀保护层普通螺纹零件,图上所表注螺纹公差带均为镀后螺纹公差带,内螺纹镀前不留镀层余量,镀后仅对螺纹零件的主要表面检查其镀层厚度。
外螺纹镀前必须留镀层余量,镀前螺纹公差带根据镀层厚度要求按GB197确定。
如有特殊需要,在外螺纹上不留或少留镀层余量时,应在图上明确规定。
5 使用条件分级按汽车电镀产品使用环境的恶劣程度使用条件分四级(见表1)汽车电镀产品使用条件分级6 表面处理在图样上的标注表面处理的标注见表27 其他7.1 各种镀层的技术要求,详见每种镀层标准。
7.2 中性盐雾试验标准(NSS试验)按照GB6458标准进行。
对于镀锌层,NSS试验仅用于检查钝化膜的质量。
7.3 铜加速醋酸盐雾试验(CASS试验)应按GB6460进行。
- 1、下载文档前请自行甄别文档内容的完整性,平台不提供额外的编辑、内容补充、找答案等附加服务。
- 2、"仅部分预览"的文档,不可在线预览部分如存在完整性等问题,可反馈申请退款(可完整预览的文档不适用该条件!)。
- 3、如文档侵犯您的权益,请联系客服反馈,我们会尽快为您处理(人工客服工作时间:9:00-18:30)。
中华人民共和国第一机械工业部部标准
JB 2864—81
汽车用电镀层和化学处理层
本标准适用于汽车及其附件等产品的电镀层和化学处理层。
1 本标准包括电镀层和化学处理层的厚度、硬度和耐蚀性等。
电镀层厚度和化学处理层厚度是指零件的主要表面上的最小值。
主要表面是
指装配后零件在产品中使用时容易受到腐蚀的、磨损的或其他工作表面。
对通常条件下不容易达到规定厚度的表面,如深孔内部、深凹处等,一般不
作为主要表面。
如有特殊厚度要求时,应在技术文件上注明。
一、镀锌层
2 镀锌层的厚度及耐蚀性要求应符合表1规定。
3 镀锌层镀后均应经彩虹色钝化处理。
二、镀镉层
4 镀镉层的厚度及耐蚀性要求应符合表2规定。
注:除特殊需要外,原则上不采用镀镉层。
5 镀镜层镀后均应经彩虹色钝化处理。
三、镀锡层
6 镀锡层的厚度及耐蚀性要求应符合表3规定。
7 稳定接触电阻钢件镀锡时,必须镀以5微米铜层为底层。
8 接触镀锡(H·Sn)不规定镀层厚度。
9 熟浸镀锡(J·Sn)不规定镀层厚度。
四、镀银层
10 镀银层的厚度及耐蚀性要求应符合表4规定。
11 镀后必须进行抗暗处理。
五、镀铅层
12 镀铅层的厚度及耐蚀性要求应符合表5规定。
13 钢件镀铅时,必须镀铜作为底层。
六、镀铜层
14 镀铜层的厚度要求应符合表6规定。
15 防止渗碳镀铜部位的表面光洁度不低于△6,如其光洁度低于▽6时,则应适当增加镀层厚度,以保证防止渗碳的质量。
16 接触镀铜(H·Cu)不规定镀层厚度。
七、镀镍层
17 镀镍层的厚度及耐蚀性要求应符合表7规定。
八、镀硬铬层
18 镀硬铬层的厚度和硬度要求应符合表8规定。
九、镀松孔铬层
19 镀松孔铬层的厚度。
松孔层深度及硬度要求应符合表9规定。
注:镀层厚度和松孔层深度不包括磨削量。
20 镀后必须去氢。
十、防护装饰性镀铬层
21 防护装饰性镀铬层的镀层等级应符合表10规定。
22 防护装饰性镀铬层的厚度及耐蚀性要求应符合表11规定。
23 允许选用不同镀层组合和厚度,但耐蚀性能必须符合该等级规定的指标。
24 评定等级应以3~5件的平均值计算。
十一、镀铅锡合金层
25 镀铅锡合金层的厚度要求应符合表12规定。
26 镀层中锡含量为6~9%,其余为铅。
十二、铝及铝合金电化学氧化处理
27 铝及铝合金电化学氧化处理的厚度、硬度及耐蚀性要求应符合表13规定。
28 装饰件的装饰氧化(D·Y·Z)后着色,其颜色标记按
GB 1238—76《金属镀层及化学处理表示方法》标注。
十三、化学镀镍层
29 化学镀镍层的厚度及耐蚀性要求应符合表14规定。
30 钢基体金属化学镀镍时,其镀层厚度为6微米;必须镀以5微米铜层为底层。
十四、钢铁件的化学处理
31 钢铁件的化学处理的标记及使用条件应符合表15规定。
32 氧化和防蚀磷化零件的腐蚀试验及其评定方法应符合下列规定:
(1)在室温(18~25℃)下,把未经涂油的氧化零件浸入3%(重量比)
的CuSO
4·5H
2
0(化学纯)溶液中,经30秒钟后,如不出现置换铜,即为合格
(棱角除外)。
(2)在室温(18~25℃)下,把未经涂油的防蚀磷化零件浸入3%(重量
比)的NaCl(化学纯)溶液中,静置2小时,如不出现锈点,即为合格(棱角除外)。
33 氧化及防蚀磷化后均应防锈处理。
十五、锌合金钝化处理
34 锌合金钝化处理的耐蚀性要求应符合表16规定。
35 镀锌、镀镉或镀银的弹性零件和镀硬铬零件镀后必须驱氢以消除氢脆者,应在技术文件上注明。
十六、试验方法及验收规则
36镀层厚度的测定应符合JB 2114—77《金属覆盖层厚度检验方法显微镜法》、
JB 2115—77《金属覆盖层厚度检验方法计时液流法》、JB 2116—77《金属覆盖层厚度检验方法薄铬镀层点滴法》、JB 2118—77《金属覆盖层厚度检验方法阴极溶解法》和JB 2119一77《金属覆盖层厚度检验方法磁性法》的规定。
37 中性试雾试验应符合JB1606—75《电工产品盐雾试验方法》的规定。
对于镀锌层和镀镉层,中性盐雾试验仅用于检验其钝化膜的质量。
38 铜加速醋酸盐雾试验应符合JB 2109—77《醋酸盐雾试验方法》的规定。
39 腐蚀试验结果的检查与评级应符合JB 2108—77《阴极性金属镀层腐蚀试验结果的保护性评价方法》的规定。