《安全环境-环保技术》之水泥窑尾烟气SCR脱硝技术
水泥窑脱硝技术

水泥窑脱硝技术水泥窑脱硝技术是一种用于减少水泥生产过程中氮氧化物(NOx)排放的方法。
随着环境保护意识的增强和环境法规的加强,水泥企业对于减少污染物排放的要求也越来越高。
水泥窑脱硝技术应运而生,成为一种有效的减排手段。
水泥生产过程中产生的NOx主要来自燃烧过程中的高温氧化反应。
NOx是一种有害气体,对大气环境和人体健康都有一定的危害。
因此,减少NOx的排放对于保护环境和改善空气质量至关重要。
水泥窑脱硝技术的基本原理是通过在水泥窑燃烧区域注入脱硝剂,将NOx转化为无害的氮气和水。
常用的脱硝剂包括氨水、尿素等。
脱硝剂与燃烧产生的NOx发生反应,生成氮气和水,从而达到减少NOx排放的目的。
水泥窑脱硝技术具有以下几个优点。
首先,它可以高效地降低NOx 排放浓度,达到环保要求。
其次,该技术对水泥生产过程的影响较小,不会对产品质量产生明显影响。
此外,水泥窑脱硝技术还可以与其他污染物治理技术相结合,形成综合治理,进一步提高治理效果。
然而,水泥窑脱硝技术也存在一些挑战和限制。
首先,脱硝剂的选择和投加量需要根据具体情况进行优化,以确保脱硝效果和经济性的平衡。
其次,脱硝剂的投加和混合需要精确控制,以避免对水泥生产过程的干扰。
此外,脱硝剂的储存和处理也需要注意安全性和环保性。
为了实现水泥窑脱硝技术的有效应用,水泥企业需要加强技术研发和设备更新,提高脱硝效率和稳定性。
同时,加强监测和管理,确保脱硝系统的正常运行和排放达标。
此外,政府和相关部门也应加强监管和支持,推动水泥企业采用脱硝技术,促进水泥行业的可持续发展。
水泥窑脱硝技术是一种有效的减少水泥生产过程中NOx排放的方法。
通过合理选择脱硝剂和优化投加量,水泥企业可以实现环境保护和经济效益的双赢。
水泥行业应积极采用水泥窑脱硝技术,为改善环境质量和可持续发展做出贡献。
水泥厂scr脱硝工艺流程
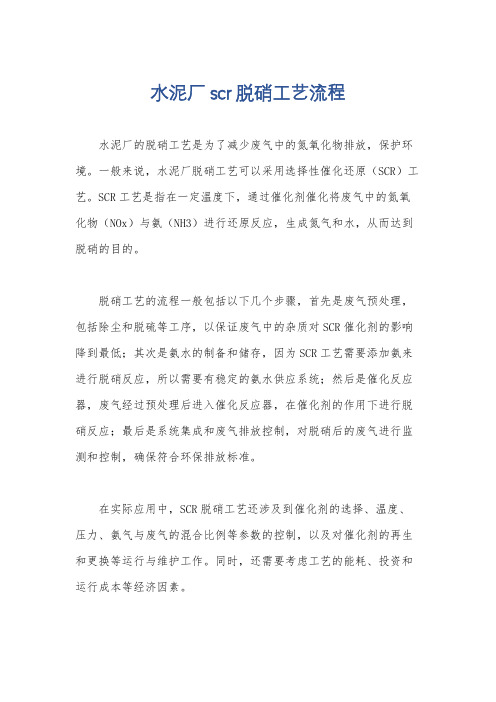
水泥厂scr脱硝工艺流程
水泥厂的脱硝工艺是为了减少废气中的氮氧化物排放,保护环境。
一般来说,水泥厂脱硝工艺可以采用选择性催化还原(SCR)工艺。
SCR工艺是指在一定温度下,通过催化剂催化将废气中的氮氧化物(NOx)与氨(NH3)进行还原反应,生成氮气和水,从而达到脱硝的目的。
脱硝工艺的流程一般包括以下几个步骤,首先是废气预处理,包括除尘和脱硫等工序,以保证废气中的杂质对SCR催化剂的影响降到最低;其次是氨水的制备和储存,因为SCR工艺需要添加氨来进行脱硝反应,所以需要有稳定的氨水供应系统;然后是催化反应器,废气经过预处理后进入催化反应器,在催化剂的作用下进行脱硝反应;最后是系统集成和废气排放控制,对脱硝后的废气进行监测和控制,确保符合环保排放标准。
在实际应用中,SCR脱硝工艺还涉及到催化剂的选择、温度、压力、氨气与废气的混合比例等参数的控制,以及对催化剂的再生和更换等运行与维护工作。
同时,还需要考虑工艺的能耗、投资和运行成本等经济因素。
总的来说,水泥厂的SCR脱硝工艺流程是一个复杂的系统工程,需要综合考虑环保、经济和工程实际情况,以达到高效、稳定地减
少氮氧化物排放的目的。
水泥窑炉烟气SCR脱硝技术的现状分析
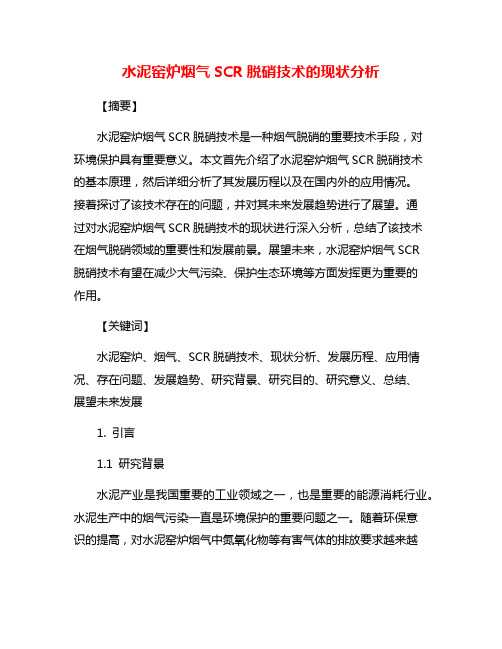
水泥窑炉烟气SCR脱硝技术的现状分析【摘要】水泥窑炉烟气SCR脱硝技术是一种烟气脱硝的重要技术手段,对环境保护具有重要意义。
本文首先介绍了水泥窑炉烟气SCR脱硝技术的基本原理,然后详细分析了其发展历程以及在国内外的应用情况。
接着探讨了该技术存在的问题,并对其未来发展趋势进行了展望。
通过对水泥窑炉烟气SCR脱硝技术的现状进行深入分析,总结了该技术在烟气脱硝领域的重要性和发展前景。
展望未来,水泥窑炉烟气SCR脱硝技术有望在减少大气污染、保护生态环境等方面发挥更为重要的作用。
【关键词】水泥窑炉、烟气、SCR脱硝技术、现状分析、发展历程、应用情况、存在问题、发展趋势、研究背景、研究目的、研究意义、总结、展望未来发展1. 引言1.1 研究背景水泥产业是我国重要的工业领域之一,也是重要的能源消耗行业。
水泥生产中的烟气污染一直是环境保护的重要问题之一。
随着环保意识的提高,对水泥窑炉烟气中氮氧化物等有害气体的排放要求越来越严格。
研究和应用SCR脱硝技术成为解决水泥窑炉烟气污染的重要途径。
SCR脱硝技术是一种通过氨选择性催化还原(SCR)来降低烟气中氮氧化物排放的先进技术。
通过在烟气中引入适量氨气,然后经过催化剂的作用,将氮氧化物转化为氮气和水蒸气,从而达到脱硝的目的。
这种技术在减少氮氧化物排放还能提高水泥熟料的质量和降低燃料消耗。
随着SCR脱硝技术的不断发展和完善,其在水泥窑炉烟气处理中的应用越来越广泛。
在实际应用过程中仍然存在一些问题,如催化剂的选择、运行成本的控制等,需要进一步研究解决。
对水泥窑炉烟气SCR脱硝技术的现状进行分析,对于进一步推动该技术的发展具有重要意义。
1.2 研究目的研究目的是为了深入了解水泥窑炉烟气SCR脱硝技术的现状,探讨其在环境保护和资源利用方面的作用和意义。
通过对该技术的基本原理、发展历程、国内外应用情况、存在的问题及发展趋势进行分析,从而为相关研究和实践提供参考和借鉴,推动该技术在水泥工业中的更广泛应用,提高燃烧效率,减少污染物排放,推动工业可持续发展。
水泥炉窑选择性催化还原脱硝技术

水泥炉窑选择性催化还原脱硝技术随着我国工业的发展,不可避免地伴随着大量的二氧化氮排放。
水泥炉窑是排放二氧化氮较大的工业生产设备之一。
为了减少排放,保护环境,保证人民健康,水泥炉窑选择性催化还原脱硝技术得到了广泛应用和推广。
一、水泥炉窑选择性催化还原脱硝技术简介水泥炉窑选择性催化还原脱硝技术(Selective Catalytic Reduction,SCR)是一种利用催化剂促进氮氧化物中的NOx转化成水和氮的技术。
该技术早在20世纪70年代就开始应用,但直到近几年,随着环保要求的提高以及SCR技术的不断进步,才得到了更广泛的应用。
二、技术原理SCR技术是一种催化反应,需要使用钝化层较薄、具有较高比表面积的氧化物作为催化剂。
SCR催化剂在一定温度范围内,可以将NOx与氨气发生化学反应,将其转化为无害的氮气(N2)和水(H2O)。
因此,SCR技术需要在氧化物催化剂的存在下,将氨气喷入含有NOx的烟气中,以使其进行化学反应。
三、应用现状SCR技术作为一种成熟、安全、可靠的脱硝技术,已经在我国的电力、钢铁、化工、水泥等多个行业得到了广泛应用。
根据不同排放标准的要求,在水泥行业中,部分地区和企业已经对水泥炉窑进行了SCR设备的投资建设和运行。
四、技术特点1、高效性SCR脱硝技术的脱除率可达到90%以上,这与其他技术相比更为高效。
2、稳定性SCR脱硝技术的稳定性较高,可以经受流量和质量波动较大的排放气体。
3、环保性水泥炉窑选择性催化还原脱硝技术能够很好地消除氮氧化物的排放,降低对环境的污染。
4、可靠性SCR系统采用自动化控制,可以实现自动清灰和自动检测功能,降低了系统的运行风险。
五、不足之处1、催化剂故障SCR技术是一种依靠催化剂催化作用来实现NOx转化的技术,因此催化剂的寿命问题是现实生产中需要考虑的问题。
2、氨泄漏氨是SCR脱硝技术中必不可少的物质,但其对人体有刺激性和腐蚀性,一旦氨泄漏将对人体和设备带来严重危害,同时还会污染环境。
水泥窑炉烟气SCR脱硝技术的现状分析

水泥窑炉烟气SCR脱硝技术的现状分析随着环境保护法的实施和环境意识的增强,烟气脱硝技术在水泥窑炉中的应用越来越广泛。
本文将对水泥窑炉烟气SCR脱硝技术的现状进行分析。
烟气脱硝技术是指通过添加适量的还原剂,将烟气中的氮氧化物(NOx)转化为无害物质氮气和水,从而降低烟气中的污染物含量。
SCR(Selective Catalytic Reduction)脱硝技术是目前应用最广泛的烟气脱硝技术,其原理是利用催化剂将NOx与氨气(NH3)或尿素(NH2CONH2)反应生成氮气和水。
水泥窑炉烟气的氮氧化物含量较高。
由于水泥生产过程中燃烧温度高、氧气浓度低,烟气中的NOx生成量较大。
水泥窑炉烟气SCR脱硝技术需要具备高效的脱硝能力,以满足严格的排放标准。
水泥窑炉烟气中存在复杂的成分。
除了NOx,烟气中还含有大量的粉尘、SOx、CO等有害物质。
这些有害物质对SCR催化剂的稳定性和活性有一定的影响。
需要通过合理的催化剂选择和催化剂保护技术,提高SCR系统的稳定性和耐受性。
水泥窑炉烟气的工况条件复杂多变。
水泥窑炉的运行状态受到原料成分、窑温、窑速等因素的影响,导致烟气组成和排放浓度存在较大变化。
水泥窑炉烟气SCR系统需要具备较强的自适应能力,能够根据烟气组成和浓度的变化调整脱硝效率。
水泥窑炉烟气SCR系统的投资和运行成本较高。
SCR系统需要投入大量的资金建设和维护,催化剂的选择和更换也需要耗费一定的成本。
SCR系统需要消耗氨气或尿素作为还原剂,这也需要一定的运营成本。
如何降低SCR系统的投资和运行成本,是当前水泥窑炉烟气SCR脱硝技术研究的重要问题。
水泥窑炉烟气SCR脱硝技术在应用中面临诸多挑战,包括高效的脱硝能力、复杂的烟气成分、复杂多变的工况条件以及较高的投资和运行成本等。
未来,应加强催化剂设计和催化剂保护技术的研究,提高SCR系统的稳定性和耐受性;加强对烟气组成和浓度的监测和控制,提高SCR系统的自适应能力;加强工程实践和经济性分析,寻找降低SCR系统投资和运行成本的有效途径。
SCR烟气脱硝技术ppt课件
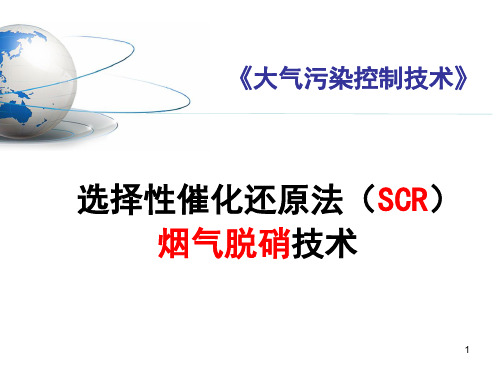
烟气中NOX来源
烟气中NOX特征 NOX净化技术方向 SCR烟气脱硝原理 SCR烟气脱硝工艺 SCR工艺运行要点
5
2. 烟气中NOX特征
NO、NO2
烟气一次污染物中NO 占NOX的90~95%
酸性
可被碱液吸收
浓度低
1000ppm左右
氧化性
可被还原为N2 实现无害化
6
11
2
主要 内容 3
4
5 6
烟气中NOX来源
《大气污染控制技术》
选择性催化还原法(SCR) 烟气脱硝技术
1
11
2
主要 内容 3
4
5 6
烟气中NOX来源
烟气中NOX特征 NOX净化技术方向 SCR烟气脱硝原理 SCR烟气脱硝工艺 SCR工艺运行要点
2
1.1 烟气中NOX --来源
热力型 空气中 N2+O2=NOX
燃料型 燃料中N+O2=NOX
措施:
催化剂中加入MoO3,与催化剂表面的 V2O5复合型氧化物,降低As的毒化。
25
6.2 SCR-运行维护
(5) 失效催化剂的处理
在SCR脱硝过程中,由于烟气中存在灰分和其它的杂 质和有毒的化学成份等因素,从而降低催化剂的活性。
再生:水洗再生、热还原再生、SO2酸化热再生
及酸、碱液处理再生。
更换:活性降低到一定的程度,不能满足脱硝性
9
4. 选择性催化还原法(SCR)--思路
催化剂
NOX + 还原剂
N2 + 无害物质
具有选择性 产物无害化 条件易实现
NH3
10
选择性催化还原法(SCR)--原理
6NO + 4NH3 = 5N2 + 6H20 6NO2 + 8NH3 = 7N2 + 12H20
水泥窑炉烟气SCR脱硝技术的现状分析
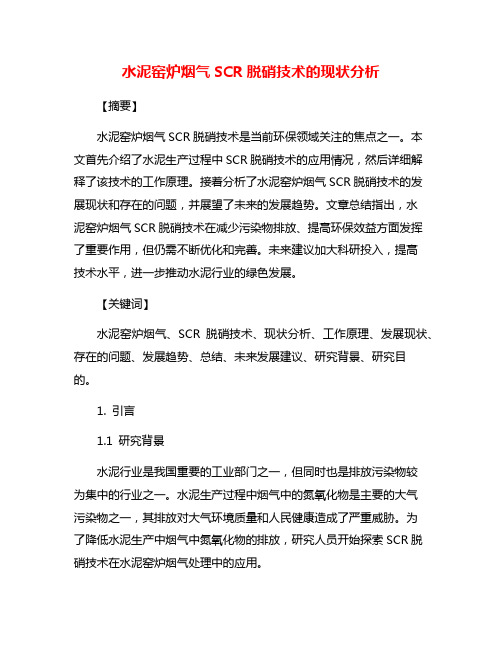
水泥窑炉烟气SCR脱硝技术的现状分析【摘要】水泥窑炉烟气SCR脱硝技术是当前环保领域关注的焦点之一。
本文首先介绍了水泥生产过程中SCR脱硝技术的应用情况,然后详细解释了该技术的工作原理。
接着分析了水泥窑炉烟气SCR脱硝技术的发展现状和存在的问题,并展望了未来的发展趋势。
文章总结指出,水泥窑炉烟气SCR脱硝技术在减少污染物排放、提高环保效益方面发挥了重要作用,但仍需不断优化和完善。
未来建议加大科研投入,提高技术水平,进一步推动水泥行业的绿色发展。
【关键词】水泥窑炉烟气、SCR脱硝技术、现状分析、工作原理、发展现状、存在的问题、发展趋势、总结、未来发展建议、研究背景、研究目的。
1. 引言1.1 研究背景水泥行业是我国重要的工业部门之一,但同时也是排放污染物较为集中的行业之一。
水泥生产过程中烟气中的氮氧化物是主要的大气污染物之一,其排放对大气环境质量和人民健康造成了严重威胁。
为了降低水泥生产中烟气中氮氧化物的排放,研究人员开始探索SCR脱硝技术在水泥窑炉烟气处理中的应用。
水泥生产过程中的SCR脱硝技术应用情况主要包括对SCR脱硝催化剂的选择和SCR反应器的设计。
不同的水泥生产工艺和排放特点需求不同的SCR脱硝技术方案,在实际应用中需要充分考虑水泥窑炉烟气的温度、氧含量、尘埃含量等参数,选择合适的SCR脱硝催化剂及设计适合的SCR反应器才能确保SCR脱硝系统的有效运行。
通过对水泥窑炉烟气SCR脱硝技术的工作原理及发展现状进行深入研究,可以为我国水泥行业的大气污染治理提供有效的技术支撑和科学依据。
1.2 研究目的1. 分析水泥窑炉烟气SCR脱硝技术在水泥生产过程中的应用情况,探讨其优势和局限性,为进一步研究提供基础和参考。
2. 探究水泥窑炉烟气SCR脱硝技术的工作原理,深入了解其运行机理,为优化脱硝效果和降低成本提供理论依据。
4. 研究水泥窑炉烟气SCR脱硝技术存在的问题,探讨其在实际应用中可能遇到的挑战和障碍,为解决问题提出对策和建议。
水泥窑炉烟气SCR脱硝技术行业应用情况简述
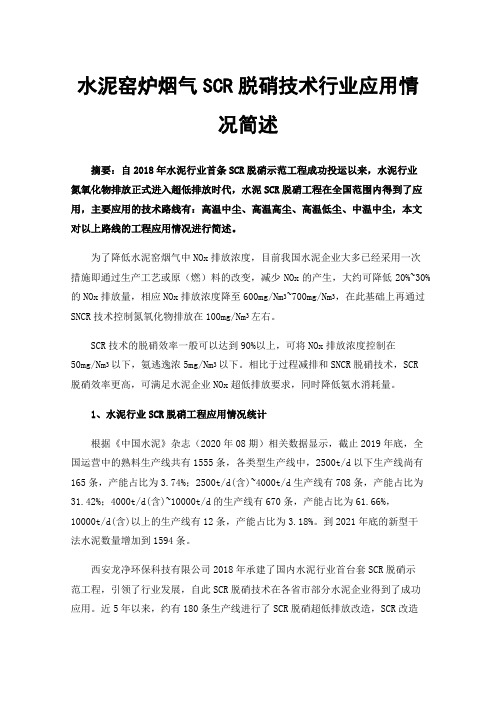
水泥窑炉烟气SCR脱硝技术行业应用情况简述摘要:自2018年水泥行业首条SCR脱硝示范工程成功投运以来,水泥行业氮氧化物排放正式进入超低排放时代,水泥SCR脱硝工程在全国范围内得到了应用,主要应用的技术路线有:高温中尘、高温高尘、高温低尘、中温中尘,本文对以上路线的工程应用情况进行简述。
为了降低水泥窑烟气中NOx排放浓度,目前我国水泥企业大多已经采用一次措施即通过生产工艺或原(燃)料的改变,减少NOx的产生,大约可降低20%~30%的NOx排放量,相应NOx排放浓度降至600mg/Nm3~700mg/Nm3,在此基础上再通过SNCR技术控制氮氧化物排放在100mg/Nm3左右。
SCR技术的脱硝效率一般可以达到90%以上,可将NOx排放浓度控制在50mg/Nm3以下,氨逃逸浓5mg/Nm3以下。
相比于过程减排和SNCR脱硝技术,SCR脱硝效率更高,可满足水泥企业NOx超低排放要求,同时降低氨水消耗量。
1、水泥行业SCR脱硝工程应用情况统计根据《中国水泥》杂志(2020年08期)相关数据显示,截止2019年底,全国运营中的熟料生产线共有1555条,各类型生产线中,2500t/d以下生产线尚有165条,产能占比为3.74%;2500t/d(含)~4000t/d生产线有708条,产能占比为31.42%;4000t/d(含)~10000t/d的生产线有670条,产能占比为61.66%,10000t/d(含)以上的生产线有12条,产能占比为3.18%。
到2021年底的新型干法水泥数量增加到1594条。
西安龙净环保科技有限公司2018年承建了国内水泥行业首台套SCR脱硝示范工程,引领了行业发展,自此SCR脱硝技术在各省市部分水泥企业得到了成功应用。
近5年以来,约有180条生产线进行了SCR脱硝超低排放改造,SCR改造占比约11.3%。
水泥行业已实施和在实施的SCR脱硝工程项目所在区域如表1所示。
表1水泥行业已实施和在实施的SCR脱硝工程项目所在区域2、水泥SCR脱硝技术业绩应用情况及代表单位根据水泥SCR脱硝的设计温度与除尘器形式的不同,技术路线分为高温中尘、高温高尘、高温低尘、中温中尘,水泥SCR脱硝的技术路线及代表单位简介详见下表:2.1高温中尘技术路线西安龙净环保科技有限公司是最早开展水泥行业SCR脱硝研究和应用的环保企业,西安龙净自主研发的高温中尘即“高温电除尘器+SCR脱硝一体化技术”已在国内多个水泥生产线成功应用,该技术具有成熟可靠、投资适中等优点,近年来西安龙净通过对水泥脱硝技术的多次升级与创新,在不设旁路烟道的前提下,实现了众多水泥SCR脱硝系统的长期稳定、高效经济运行,业绩在行业内遥遥领先。
- 1、下载文档前请自行甄别文档内容的完整性,平台不提供额外的编辑、内容补充、找答案等附加服务。
- 2、"仅部分预览"的文档,不可在线预览部分如存在完整性等问题,可反馈申请退款(可完整预览的文档不适用该条件!)。
- 3、如文档侵犯您的权益,请联系客服反馈,我们会尽快为您处理(人工客服工作时间:9:00-18:30)。
水泥窑尾烟气SCR脱硝技术一前言2015年全国氮氧化物排放量1851.9万吨,其中,水泥排放氮氧化物约占全国排放总量的10%,仅次于火电和机动车行业,位居第三。
2016年年底,国务院印发《“十三五”节能减排综合工作方案》,提出到2020年氮氧化物排放总量比2015年下降15%以上的主要目标。
《水泥工业大气污染物排放标准》(GB 4915-2013)要求氮氧化物排放限值400 mg/Nm3,重点地区320 mg/Nm3;在氮氧化物排放要求日趋严格背景下,2017年5月,江苏省环保厅《关于开展全省非电行业氮氧化物深度减排的通知》要求,水泥行业2019年6月1日前氮氧化物排放不高于100 mg/Nm3;2018年9月,《唐山市生态环境深度整治攻坚月行动方案》提出氮氧化物排放浓度不高于50 mg/Nm3。
现行的脱硝技术大体分为氧化法脱硝和催化还原法脱硝。
氧化法脱硝采用强氧化剂,如臭氧、亚氯酸钠等强氧化剂,把NOx氧化成高价氮氧化物,然后通过水或者碱液体进行吸收,但是存在耗电高、二次污染物废水排放问题。
催化还原法,一般指SCR法,因其无二次污染排放问题,脱硝效率高,可以实现超净排放,运行可靠稳定、适应负荷波动等优点,广泛的应用在各个工矿企业中。
SCR脱硝技术作为全世界应用最广泛高效的氮氧化物脱除技术,符合水泥行业日趋严格的氮氧化物排放要求,是一种理想的水泥窑脱硝技术。
研究高效水泥窑SCR脱硝技术,具有现实意义。
二水泥窑尾烟气特点(1)NOx含量高,为300~1300mg/Nm3。
(2)湿度大,水含量8~16%;水蒸气露点一般为45~55℃。
(3)粉尘含量高,烟尘浓度达60~120 g/Nm3,并含有碱土金属氧化物等腐蚀性成分。
(4)粉尘粒径小(小于10μm的颗粒约占75~90%)、比电阻高,除尘难度大。
(5)粉尘中碱金属氧化物含量高。
以上这些烟气特点均增加了脱硝的难度和投资成本。
表1某水泥窑尾飞灰与燃煤锅炉飞灰主要成分对比三水泥窑尾烟气SCR脱硝难点目前,国外有一些水泥生产线 SCR运行案例,但未见其长期稳定运行且各项指标满意、完全可推广的技术案例报导,其主要原因是,水泥生产工艺的高效脱硝技术路线尚达不到电厂燃煤锅炉脱硝技术的成熟度和可靠度。
自2018年起,国内有几个水泥窑SCR脱硝工程陆续开始建设,但到目前为止还没有长期稳定运行的报导,几个项目中投运时间较长的已经暴露出催化剂堵塞问题。
水泥窑尾预热器出来的烟气中粉尘含量高达60~120 g/Nm3,且存在大量的碱土金属CaO,通过催化剂时,有堵塞催化剂的风险,易加快催化剂的磨损,同时催化剂在含高钙飞灰的烟气中长期运行会逐渐失活,这是水泥窑尾烟气SCR脱硝必须要解决的难点。
造成催化剂失活的几种可能原因是:(1)氧化钙造成微孔的堵塞水泥窑尾飞灰中CaO含量高,粘性大;且飞灰粒径小,大部分在10μm以下。
飞灰与催化剂接触时极易吸附在催化剂表面堵塞催化剂微孔,造成催化剂活性下降。
但是CaO在飞灰中相对其他成分与催化剂组分的亲和性不是特别突出,并不是特别容易扩散进入催化剂中的组分。
此外,相对化学作用,物理作用一般是可逆的。
通过周期性的吹灰可以将沉积在催化剂表面的飞灰及时去除,故CaO对催化剂微孔的堵塞一般不是活性下降的主要原因。
(2)氧化钙的碱性造成催化剂酸性下降由于CaO自身是含有碱性的物质,而目前使用的V2O5基催化剂中的活性位是酸性的,沉积在催化剂表面的 CaO会中和催化剂表面的酸位,阻断催化反应的发生。
水泥窑尾飞灰浓度高、飞灰中含钙量高, CaO的碱性对催化剂的影响应引起重视。
(3)生成的CaSO4引起活性下降由于沉积在催化剂表面的CaO与烟气中的SO3反应生成的 CaSO4,而造成催化剂微孔的堵塞是催化剂性能下降的主要原因。
CaO中毒机理包括四个步骤。
步骤 1 – CaO附着到催化剂表面上的宏观孔中。
步骤 2 – SO3渗漏CaO颗粒周围的气膜。
步骤 3 – SO3扩散到CaO颗粒中。
步骤 4 –随着SO3向CaO颗粒中扩散到,它与CaO反应,生成CaSO4。
在CaO中毒过程中,CaO首先在催化剂表面沉积,沉积速度相对较慢。
沉积在催化剂表面的CaO与烟气中SO3的反应属于气固反应,由于在催化剂表面有活性物质催化氧化SO2生成SO3,SO3浓度相对较高,反应速度为快速反应。
快速反应生成的CaSO4的体积会膨胀14%左右,会遮蔽反应活性位,堵塞催化剂表面,影响反应物在催化剂微孔结构内的扩散。
在 CaO 中毒机理中,其中CaO的沉积速度相对较慢,是控制关键,降低CaO在催化剂表面的沉积量是减缓催化剂中毒的有效手段。
四水泥窑尾烟气SCR脱硝技术路线针对水泥窑尾烟气可进行的SCR脱硝的三个位置如下图所示,分别是预热器出口的310~450℃的中高温烟气,余热锅炉出口的200~210℃的中低温烟气和窑尾除尘器出口的70~120℃低温排放尾气。
图1水泥窑烟气SCR脱硝位置示意图4.1中温脱硝技术路线310~450℃温度区间脱硝,脱硝活性高,催化剂用量少,无需加热再生设备,运行成本低,可实现长期稳定可靠运行。
水泥窑炉的窑尾出口烟气温度约310~450℃,是最佳SCR脱硝温度反应区,但是该处粉尘含量高、碱金属含量高,会导致催化剂碱中毒和堵塞,影响中高温SCR脱硝剂的使用寿命,因此需要将烟气除尘后再送入SCR反应器。
“高温除尘+中温SCR 脱硝”的工艺路线无需额外补能就可以实现长期稳定运行,使水泥生产中的除尘脱硝工艺具备高效减排、节能节材的明显优势。
4.2中低温脱硝技术路线200~210℃温度段脱硝,催化剂活性较低,用量较大,且这个温度段是硫铵生成的最佳温度段。
烟气中SO3与NH3反应生成硫铵副产物,易糊堵催化剂,引起催化剂失活,且硫铵粘性大,难以使用吹灰器吹掉。
因此,需要采用增设加热再生装置的方式,不定期将烟气加热到350℃来缓解硫铵对催化剂的影响。
但是这样增加了系统的复杂性,且对后续风机及设备提出了新的要求。
4.3低温脱硝技术路线70~120℃的脱硝催化剂国内外报道的应用很少,成功应用案例也很少,目前国内的低温催化剂起活温度一般≥150℃。
在70~120℃温度区间,催化剂活性很低,催化剂使用量大,价格昂贵,工程造价高。
在此温度下烟气成分对活性有很大影响,需要烟气几乎无尘,SO2含量小于10mg/Nm3,水含量也很少。
目前水泥行业烟气中的水含量较高,达到8~16%,低温下水对催化剂活性影响非常大,H2O会和反应物NH3抢夺催化剂表面的活性位,导致催化剂迅速失活,尤其当水含量>10%,尤为明显。
同时烟气中也有少量硫和碱金属,运行中长期累积在催化剂表面,极易导致催化剂失活。
在70~120℃温度段和200~210℃温度段进行脱硝,如果采用“热风炉+GGH”的工艺,将烟气加热到250~280℃,再进行SCR脱硝,虽然脱硝效率可以得到保证,但是水泥窑烟气量大,不仅设备的投资费用很高,而且加热烟气所消耗的燃料量也相当巨大,运行成本也非常高。
五华电光大水泥烟气脱硝用催化剂北京华电光大环境股份有限公司依托华北电力大学,组建了自己的研发生产团队,脱硝催化剂具有完全自主知识产权。
在对水泥窑尾烟气脱硝技术充分论证、广泛调研的基础上,结合自身技术优势,华电光大研发出适用于水泥窑尾烟气的脱硝催化剂。
该催化剂主要有以下特点:5.1抗堵灰能力强华电光大水泥烟气脱硝用催化剂为板式催化剂。
板式催化剂的源初设计就是为了满足高灰的烟气的脱硝而诞生和发展起来的。
板式催化剂相对于蜂窝催化剂具有节距大,孔道角落少,不易形成低流速区等特点,能有效避免飞灰的堆积、堵塞催化剂孔道。
同时,板式脱硝催化剂以金属钢网为基材,具有柔性结构,烟气流过板式催化剂时,催化剂单板在烟气中不停振动,使飞灰难以附着于催化剂表面。
此外,华电光大充分发挥自主产权优势,通过以下方式优化提高了脱硝催化剂的抗堵灰能力,具体如下:图2华电光大板式脱硝催化剂(1)根据设计条件合理选择催化剂。
水泥窑尾灰分粒径小,而且碱土金属含量高,导致灰分有粘性,催化剂孔道容易积灰,因此在催化剂选型时采用的是间距>6mm,开孔率不低于88%的板式催化剂,并在催化剂模块的顶部加装滤灰网板,避免烟气的大颗粒(爆米花)飞灰进入催化剂通道内造成催化剂的堵塞。
(2)华电光大所用不锈钢网板全部为自己设计生产,经过反复实验,有效降低了不锈钢网板的原始厚度,可在不减少涂敷的物料厚度的同时有效控制产品厚度。
因为催化剂壁厚相对减薄,催化剂的柔韧度提升,烟气在通过催化剂孔道时,会强化催化剂自抖动能力,从而避免了飞灰在催化剂表面的沉积和堵塞催化剂的问题。
(3)华电光大生产的催化剂采用辊面特殊处理工艺增加辊压力,大幅提高泥料在不锈钢网板上的粘附性能,提高催化剂的致密度。
同时通过调整涂覆工艺,控制催化剂表面光滑度,减少摩擦系数,可以使飞灰不易附着在催化剂表面。
(4)由于催化剂堵塞和磨损经常同时发生,华电光大根据客户灰分情况调整优化生产工艺,增强其耐磨性能。
我公司的板式脱硝催化剂经过西安热工院的检测,剥落率仅为0.26%,磨损率为0.016%/kg。
催化剂已经过多个项目的验证,耐磨损性能极强。
另外,板式催化剂与常见的蜂窝催化剂相比,比表面积偏小,所用体积量偏大10%-20%。
但在水泥行业却不存在这样的问题。
目前,水泥行业普遍采用几何比表面积303m2/m3的13×13孔蜂窝催化剂(开孔率87.5%),而华电光大水泥烟气脱硝用催化剂的几何比表面积有283m2/m3(开孔率89.9%)、300m2/m3(开孔率89.0%)、333m2/m3(开孔率88.0%)三种规格,与蜂窝催化剂相近;蜂窝催化剂不再有体积量方面的优势。
5.2抗碱金属中毒能力强针对水泥窑尾烟气特点,华电光大在常规催化剂的基础上做了性能改进:开发了具有高效抗碱金属的脱硝催化剂,在高碱金属含量飞灰烟气中具有优异的活性以及长的使用寿命。
通过对催化剂进行理论分析、性能评价和表征,分析催化剂中各元素赋存形态与催化剂性能之间的关系,深入了解催化剂中毒原理,并从减缓催化剂化学中毒和物理中毒方面切入,成功开发了抗碱金属中毒SCR脱硝催化剂。
(1)增加催化剂表面酸性碱金属、碱土金属对催化剂中毒,主要是与活性中心(V)的酸位发生反应,占据酸位导致氨无法吸附在酸位上,造成催化剂活性降低。
在此基础上,ⅥB,ⅠB,Ⅷ副族过度金属元素,以及稀土金属可提高催化剂的酸位。
通过筛选复配,以及加工方式的优化,比例调整等一系列工作,成功选取了合适的助催化剂,提高了脱硝催化剂整体酸位,增加了氨的吸附位点和碱金属抗性。
从而提高了碱金属的容量。
(2)添加抗碱金属助剂碱金属、碱土金属与催化剂的活性中心酸位作用,为了避免催化剂失活或者降低催化剂失活速率,要降低碱金属、碱土金属与活性中心酸位的接触,也就是保护催化剂活性中心。