车螺纹
车螺纹进刀深度计算公式

车螺纹进刀深度计算公式车螺纹是一种常见的机械连接元件,广泛应用于汽车、机械设备等领域。
在车螺纹加工过程中,进刀深度的计算是十分重要的,它直接影响到车螺纹的质量和工作性能。
本文将介绍车螺纹进刀深度的计算公式及其相关知识。
一、车螺纹进刀深度的定义车螺纹进刀深度是指车刀相对于螺纹轴线的进刀距离,也就是车刀在车削过程中与工件表面的接触深度。
进刀深度的选择要根据螺纹的形状、尺寸、材料等因素进行合理的计算和确定,以确保螺纹的加工质量。
二、车螺纹进刀深度计算公式车螺纹进刀深度的计算公式可以根据螺纹的类型和标准进行选择。
下面以常见的ISO标准螺纹为例,介绍车螺纹进刀深度的计算公式。
1. 内螺纹进刀深度计算公式:对于内螺纹,其进刀深度计算公式为:进刀深度= (0.5 × P) + C其中,P为螺距,C为余量。
螺距是指螺纹的一个周期所包含的螺纹数量,它是螺纹的一个重要参数。
余量是为了确保内螺纹的质量和配合要求而设置的,一般为正值。
2. 外螺纹进刀深度计算公式:对于外螺纹,其进刀深度计算公式为:进刀深度= (0.5 × P) + C其中,P和C的含义同上。
三、车螺纹进刀深度计算实例下面以M12×1.5的内螺纹为例,介绍车螺纹进刀深度的具体计算过程。
1. 计算螺距:根据M12×1.5的规格,可知其螺距为1.5mm。
2. 计算余量:根据螺纹的配合要求和加工经验,假设余量为0.1mm。
3. 计算进刀深度:根据内螺纹进刀深度计算公式,可知进刀深度= (0.5 × 1.5) + 0.1= 0.85mm。
因此,M12×1.5的内螺纹进刀深度为0.85mm。
四、进刀深度的影响因素车螺纹的进刀深度不仅与螺纹的规格有关,还受到以下因素的影响:1. 工件材料:不同材料的工件对进刀深度有不同的要求,如硬度大的材料要求进刀深度小。
2. 切削刃形状:车刀的切削刃形状也会对进刀深度产生影响,不同刃形的车刀对进刀深度的要求不同。
车螺纹注意事项

车螺纹注意事项车螺纹是车辆在轮胎和轮辋之间使用的紧固装置。
它们扮演着关键的角色,可以确保轮胎牢固地固定在车辆上,提供安全而平稳的行驶。
使用车螺纹时需要注意以下几点。
首先,要正确选择合适的螺纹尺寸和类型,以确保它们与车辆的轮胎和轮辋相匹配。
不同的车辆可能需要不同规格的螺纹,所以在购买之前最好查阅车辆制造商的规格指南。
选用适当的螺纹尺寸和类型可以确保其与轮辋匹配度完美,避免出现螺纹松动或不牢固的情况。
其次,要确保螺纹的紧固力达到适当的标准。
过紧的螺纹可能会导致螺纹变形,而过松的螺纹则可能导致松动和脱落。
一般来说,可以使用扭矩扳手来正确安装和拆卸螺纹。
扭矩扳手可以帮助控制施加在螺纹上的力度,确保达到正确的紧固力。
如果没有扭矩扳手,可以使用正确尺寸的扳手手动紧固,但要小心不要过分用力,以免损坏螺纹或其他相关零件。
另外,需要定期检查和维护螺纹。
车辆行驶过程中,一些外界的因素,如颠簸的路面、振动和长时间使用等,都可能引起螺纹松动。
因此,应定期检查并拧紧螺纹,确保其保持良好的紧固状态。
此外,还需要及时更换磨损严重的螺纹,以免影响其紧固效果。
注意,为了保证最佳的安全性能,应将车螺纹的更换工作交给专业技术人员进行。
此外,在使用车螺纹时,还需要注意以下几点。
首先,要保持螺纹清洁。
尽量避免在螺纹上积聚泥土、灰尘和其他杂物,这可能会导致螺纹更难拧紧,甚至损坏螺纹。
可以使用刷子或气压装置清除螺纹上的杂物。
其次,要避免过度使用螺纹。
频繁的安装和拆卸可能会损伤螺纹,导致它们失去紧固性。
因此,在不需要更换轮胎或进行其他维护工作时,尽量避免拆卸螺纹。
最后,当使用车螺纹时,还需要保持其在正确的位置上。
当螺纹松动时,应立即拧紧。
如果螺纹损坏或失效,应立即更换。
不要试图自行修复或继续使用损坏的螺纹,这可能会导致危险的驾驶条件。
如果出现无法拧紧螺纹或其他与螺纹相关的问题,应尽快咨询专业技术人员寻求帮助。
总之,车螺纹的使用需要谨慎,并且需要定期检查和维护。
普通车床车螺纹的步骤
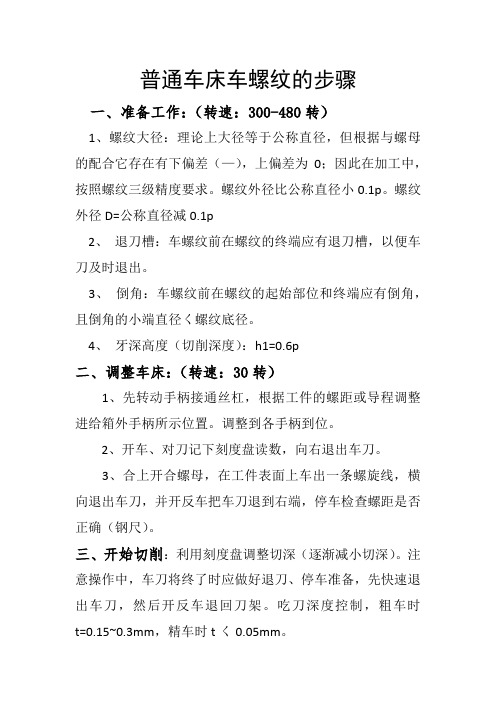
3、倒角:车螺纹前在螺纹的起始部位和终端应有倒角,且倒角的小端直径く螺纹底径。
4、牙深高度(切削深度):h1=0.6p
二、调整车床:(转速:30转)
1、先转动手柄接通丝杠,根据工件的螺距或导程调整进给箱外手柄所示位置。调整到各手柄到位。
2、开车、对刀记下刻度盘读数,向右退出车刀。
3、合上开合螺母,在工件表面上车出一条螺旋线,横向退出车刀,并开反车把车刀退到右端,停车检查螺距是否正确工作:(转速:300-480转)
1、螺纹大径:理论上大径等于公称直径,但根据与螺母的配合它存在有下偏差(—),上偏差为0;因此在加工中,按照螺纹三级精度要求。螺纹外径比公称直径小0.1p。螺纹外径D=公称直径减0.1p
2、退刀槽:车螺纹前在螺纹的终端应有退刀槽,以便车刀及时退出。
普通车床车螺纹教程

普通车床车螺纹教程
车螺纹是车床加工中常见的操作之一,下面将详细介绍普通车床车螺纹的操作步骤。
1. 准备工作:选择合适的车刀、切削液和螺纹规格。
根据需要,选择合适的螺距和螺纹类型。
2. 将工件固定在车床的夹持装置上。
确保工件稳固,并根据需要进行适当的夹紧和支撑。
3. 调整车床的转速和进给速度。
根据工件材料和螺纹规格,选择合适的车削参数。
4. 使用车刀将工件端面削平,确保车削开始时刀具与工件的接触面积充分。
5. 将车刀切削边缘与工件端面垂直对齐。
开始车削前,注意刀具的朝向和位置。
6. 缓慢向工件表面进给车刀,保持适当的切削深度。
同时,使用适量的切削液进行冷却和润滑。
7. 轻轻地转动手轮,同时保持车刀沿着工件轮廓移动,形成螺纹的切削。
8. 控制进给速度,使车床给进床移动的距离等于螺纹螺距。
一圈结束后,及时调整车床床的位置,开始下一圈的车削。
9. 继续进行车削,直到螺纹的长度满足要求。
10. 完成车削后,停止车床的运转。
使用刷子清除工件表面的切削屑,并进行必要的修整和磨光。
11. 检查车削的螺纹是否符合规格要求,可以使用螺纹量规进行测量。
12. 若需要进行下一步工序,及时清洁工件和车床。
若不需要继续加工,可以拆卸工件,并妥善保管。
以上是普通车床车螺纹的简要步骤,希望对您有所帮助。
车螺纹注意事项
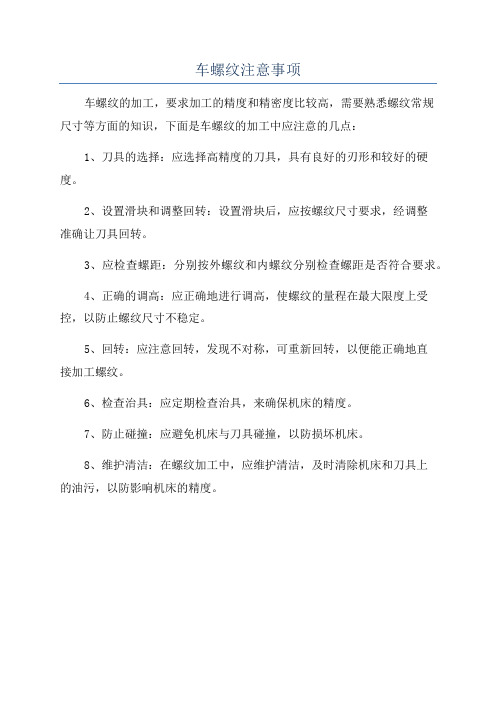
车螺纹注意事项
车螺纹的加工,要求加工的精度和精密度比较高,需要熟悉螺纹常规
尺寸等方面的知识,下面是车螺纹的加工中应注意的几点:
1、刀具的选择:应选择高精度的刀具,具有良好的刃形和较好的硬度。
2、设置滑块和调整回转:设置滑块后,应按螺纹尺寸要求,经调整
准确让刀具回转。
3、应检查螺距:分别按外螺纹和内螺纹分别检查螺距是否符合要求。
4、正确的调高:应正确地进行调高,使螺纹的量程在最大限度上受控,以防止螺纹尺寸不稳定。
5、回转:应注意回转,发现不对称,可重新回转,以便能正确地直
接加工螺纹。
6、检查治具:应定期检查治具,来确保机床的精度。
7、防止碰撞:应避免机床与刀具碰撞,以防损坏机床。
8、维护清洁:在螺纹加工中,应维护清洁,及时清除机床和刀具上
的油污,以防影响机床的精度。
普车螺纹操作方法
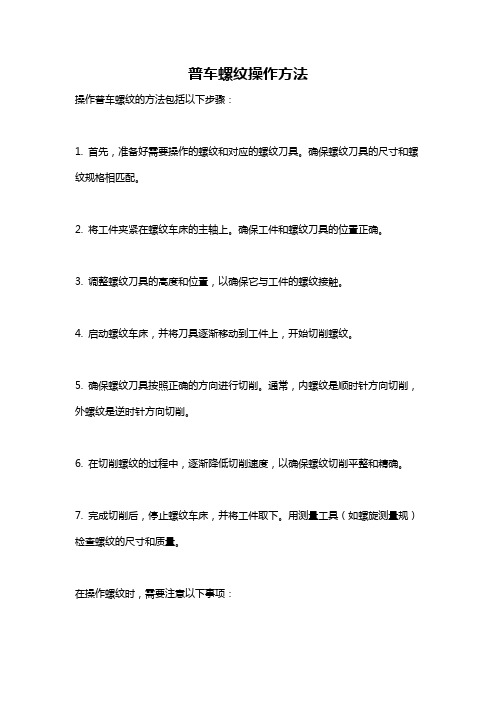
普车螺纹操作方法
操作普车螺纹的方法包括以下步骤:
1. 首先,准备好需要操作的螺纹和对应的螺纹刀具。
确保螺纹刀具的尺寸和螺纹规格相匹配。
2. 将工件夹紧在螺纹车床的主轴上。
确保工件和螺纹刀具的位置正确。
3. 调整螺纹刀具的高度和位置,以确保它与工件的螺纹接触。
4. 启动螺纹车床,并将刀具逐渐移动到工件上,开始切削螺纹。
5. 确保螺纹刀具按照正确的方向进行切削。
通常,内螺纹是顺时针方向切削,外螺纹是逆时针方向切削。
6. 在切削螺纹的过程中,逐渐降低切削速度,以确保螺纹切削平整和精确。
7. 完成切削后,停止螺纹车床,并将工件取下。
用测量工具(如螺旋测量规)检查螺纹的尺寸和质量。
在操作螺纹时,需要注意以下事项:
1. 确保使用合适的刀具和工件夹具,以防止刀具断裂或工件脱离夹具。
2. 切削过程中,保持螺纹刀具和工件之间的冷却润滑,以提高切削效率和延长刀具寿命。
3. 调整螺纹刀具的位置和切削力,以确保切削过程平稳和均匀。
4. 定期检查螺纹刀具的磨损情况,及时更换磨损严重的刀具。
5. 在操作过程中,遵循安全规范,保持工作环境整洁有序,以确保操作人员的安全。
车螺纹方法
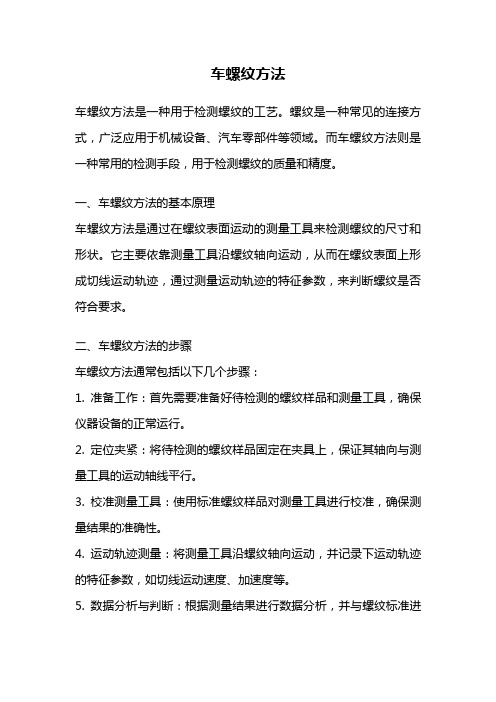
车螺纹方法车螺纹方法是一种用于检测螺纹的工艺。
螺纹是一种常见的连接方式,广泛应用于机械设备、汽车零部件等领域。
而车螺纹方法则是一种常用的检测手段,用于检测螺纹的质量和精度。
一、车螺纹方法的基本原理车螺纹方法是通过在螺纹表面运动的测量工具来检测螺纹的尺寸和形状。
它主要依靠测量工具沿螺纹轴向运动,从而在螺纹表面上形成切线运动轨迹,通过测量运动轨迹的特征参数,来判断螺纹是否符合要求。
二、车螺纹方法的步骤车螺纹方法通常包括以下几个步骤:1. 准备工作:首先需要准备好待检测的螺纹样品和测量工具,确保仪器设备的正常运行。
2. 定位夹紧:将待检测的螺纹样品固定在夹具上,保证其轴向与测量工具的运动轴线平行。
3. 校准测量工具:使用标准螺纹样品对测量工具进行校准,确保测量结果的准确性。
4. 运动轨迹测量:将测量工具沿螺纹轴向运动,并记录下运动轨迹的特征参数,如切线运动速度、加速度等。
5. 数据分析与判断:根据测量结果进行数据分析,并与螺纹标准进行比较,判断螺纹是否符合要求。
6. 结果记录:将测量结果记录下来,包括测量数据、判断结果等。
三、车螺纹方法的应用领域车螺纹方法广泛应用于机械制造、汽车零部件等领域。
在机械制造中,螺纹是一种重要的连接方式,螺纹的质量和精度直接影响到机械设备的性能和可靠性。
因此,通过车螺纹方法对螺纹进行检测,可以确保产品质量,提高生产效率。
在汽车零部件制造中,车螺纹方法也扮演着重要的角色,用于检测发动机、底盘、传动系统等零部件的螺纹质量。
四、车螺纹方法的优势和局限性车螺纹方法具有以下优势:1. 非接触式测量:车螺纹方法采用非接触式测量,不会对螺纹表面造成损伤。
2. 高精度测量:车螺纹方法可以实现对螺纹尺寸和形状的高精度测量,确保产品质量。
3. 高效率:车螺纹方法可以实现对大批量产品的快速检测,提高生产效率。
然而,车螺纹方法也存在一定的局限性:1. 对设备要求高:车螺纹方法需要使用专门的测量设备,对设备的要求较高。
车螺纹
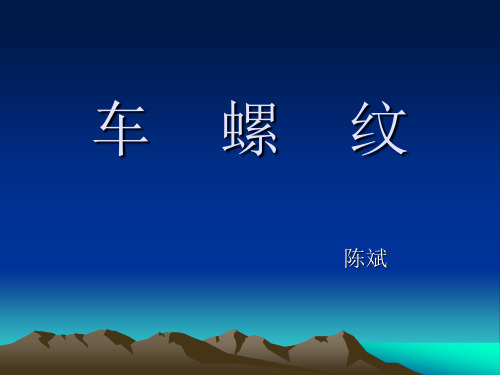
3、车端面时应注意以下几点: (1)车刀的刀尖应对准工件的回转中心否则会在端 面中心留下凸台。 (2)工件中心处的线速度较低,为获得整个端面上 较好的表面质量,车端面的转速比车外圆的转速 高一些。 (3)直径较大的端面车削时应将床鞍锁紧在床身上, 以防有床鞍让刀引起的端面外凸或内凹。此时用 小滑板调整背吃刀量 (4)保持车刀锋利。中、小拖板的镶条不应太松, 车刀刀架应压紧,防止让刀而产生凸面。 (5)精度要求高的端面,亦应分粗、精加工。
外圆车削的步骤和方法
切削用量三要素是指切削速度、进给量和切削深度三者的总称, 切屑的类型主要包括带状切屑、节状切屑 、粒状切屑和崩碎切屑
一、车削端面和台阶 1、车刀的选择 车削端面和台阶,通常使用90度偏刀和45度刀,安装时应特别强调刀 尖要严格对准工件中心,否则会使工件端面中心留有凸台,甚至出现 刀尖崩刃。 用45度刀车端面,可采用较大背吃刀量,切削顺利,表面光滑,大小 平面均可车削,应用较多; 用90度左偏刀从外向中心进给车端面,适合车削尺寸较小的端面或一 般的台阶面;用90度右偏刀从中心向外进给车端面,适合车削中心带 孔的端面或一般的台阶端面;用左偏刀车端面,刀头强度较好,适宣 车削较大端面,尤其是铸、锻件的大端面。
螺纹车刀
螺纹车刀属切削刀具的一种,是用来在车削加工机床 上进行螺纹的切削加工的一种刀具。 螺纹车刀分为内螺纹车刀和外螺纹车刀两大类,从机 械制造初期使用的需要手工磨的焊接刀头的螺纹车刀、高 速钢材料磨成的螺纹车刀、高速钢梳刀片式的螺纹车刀及 机夹式螺纹车刀等,机夹式螺纹车刀是目前被广泛使用的 机夹式螺纹车刀,机夹式螺纹车刀分为刀杆和刀片两部分, 刀杆上装有刀垫,用螺钉压紧,刀片安装在刀垫上,刀片 又分为硬质合金未涂层刀片(用来加工有色金属的刀片, 如:铝、铝合金、铜、铜合金等材料),硬质合金涂层刀 片(用来加工钢材、铸铁、不锈钢、合金材料等)。
- 1、下载文档前请自行甄别文档内容的完整性,平台不提供额外的编辑、内容补充、找答案等附加服务。
- 2、"仅部分预览"的文档,不可在线预览部分如存在完整性等问题,可反馈申请退款(可完整预览的文档不适用该条件!)。
- 3、如文档侵犯您的权益,请联系客服反馈,我们会尽快为您处理(人工客服工作时间:9:00-18:30)。
例:
T0202;(退刀槽加工) S400; G00 X22.0 Z-19.0; G75 R0.5; G75 X16.0 Z-20.0 P1000 Q1000
F20.0; G00 X100.0 Z50.0; T0303;(螺纹加工) G00 X22.0 Z2.0; G76 P020060 Q100 R300; G76 X16.75 Z-18.0 P1624 Q500 F2.5; G00 X100.0 Z50.0; T0202;(工件切断) S200; G00 X40.0 Z-53.0; G01 X2.0 F20.0; X40.0; G00 X100.0 Z50.0; M05; M30;
Z-30; N20 X35; G70 P10 Q20; G00 G40 X100 Z50;
T0202 S300;(退刀槽加工) G00 X35 Z-30; G01 X26 F30; G04 X4; G01 X35; G00 X100 Z50;
T0303; M03 S400; G00 X29.1 Z5 ; G32 Z-28 F2; G00 X31;
试用G32指令编写螺纹加工程序。
2、螺纹切削循环 G92
格式:
G92 X(U)_Z(W)_R_F_;
锥螺纹起点半径与 终点半径的差值
用G92进行圆柱螺纹加工
45°
X
Z
W
4(R)
3(F) 2(F)
R
1(R)
O
XU 22
R<0
Z
用G92进行圆锥螺纹加工
例:
T0303; M03 S400; G00 X29.1 Z5 ; G32 Z-28 F2; G00 X31;
公制螺纹 2.0
1.299 0.9 0.6 0.6
2.5 1.624
1.0 0.7 0.6
3.0 1.949
1.2 0.7 0.6
3.5 2.273
1.5 0.7 0.6
4.0 2.598
1.5 0.8 0.6
0.16
0.4
0.4
0.4
0.6
0.6
0.1
0.4
0.4
0.4
0.4
0.15
0.4
0.4
0.4
(3)背吃刀量 当螺纹牙型较深、螺距较大 时,通常分几次进行切削。每次进给的背吃 刀量用螺纹深度减精加工背吃刀量所得的差 按递减规律分配
螺距 牙深(半径值)
1次 2次 3次
4次
切削
次数
5次
及对
应背
吃刀
6次
量
直径值
(㎜) 7次
1.0 0.649
0.7 0.4 0.2
1.5 0.974
0.8 0.6 0.4
T0303; M03 S400;
G00 X35 Z5; G92 X29.1 Z-28 F2;
X28.5; X27.9; X27.5; X27.4;
G00 X100; Z50;
M05; M30;
4.编程举例(6)
T0303; M03 S600; G00 X22 Z2; G92 X19.2 Z-24 F1.5;
3、螺纹切削复合循环 G73
格式:
G76 P(m)(r)(a) Q(△d min)R(d); G76 X(u) Z(W) R(i) P(k) Q(Δd ) F(L) ;
X(U) Z(W):终点坐标。
锥螺纹起点半径与 终点半径的差值
3、螺纹切削复合循环 G73
格式:
G76 P(m)(r)(a) Q(△d min)R(d); G76 X(u) Z(W) R(i) P(k) Q(Δd ) F(L) ;
X18.6; X18.376; G00 X100 Z50; M05; M30;
3、螺纹切削复合循环 G76
格式:
G76 P(m)(r)(a) Q(△d min)R(d); G76 X(u) Z(W) R(i) P(k) Q(Δd ) F(L) ;
m :精加工重复次数,必须用2位数表示。 r :螺纹末端倒角量。必须用2位数表示, 如r=12,则倒角量=12×0.1×导程。 a :刀尖角度。可以选择80°,60°,55°, 30°,29°和0°六种中的一种。 m,r和a用地址P同时指定。
3、螺纹切削复合循环 G73
格式:
G76 P(m)(r)(a) Q(△d min)R(d); G76 X(u) Z(W) R(i) P(k) Q(Δd ) F(L) ;
Δdmin :最小背吃刀量(用半径值指定),此数值 不可用小数点方式表示。如Δdmin=0.01时,需写 成Q10。 d :精加工余量。
i :车削锥螺纹时螺纹部分半径差,即螺纹切削 起始点与切削终点的半径差。 加工圆柱螺纹时时,I为负,反之为正。
3、螺纹切削复合循环 G73
格式:
G76 P(m)(r)(a) Q(△d min)R(d); G76 X(u) Z(W) R(i) P(k) Q(Δd ) F(L) ;
Z5; X28.5 ; G32 Z-28 F2; G00 X31; Z5; X 27.9; G32 Z-28 F2; G00 X31; Z5;
X27.5 ; G32 Z-28 F2; G00 X31;
Z5; X27.4 ; G32 Z-28 F2; G00 X100; Z50; M05; M30;
练习:
=29.8mm ②计算螺纹小径 d´=d-1.3P=(30-1.3×2)mm
=27.4mm ③确定背吃刀量
0.9mm 0.6mm 0.6mm 0.4mm 0.1mm
④主轴转速 n≤1200/P-80=520r/min 取n=400r/min ⑤加工程序
O2028 T0101;(外圆表面加工) G98 M03 S800; G00 X35 Z2; G71 U1 R0.5; G71 P10 Q20 U0.5 W0.1 F80; N10 G00 X21.8; G01 G42 X29.8 Z-2 F40;
G76 P020060 Q0.1 R0.1;
(精车2次,60°螺纹刀,最小切削量 0.1mm,精车余量0.1mm)
G76 X31 Z-28 R0 P1.3 Q0.8F2;
(直螺纹,牙高1.3mm,第一刀切深0.8mm, 导程2mm)
G00 X100; Z50;
M05; M30;
GSK980TDA:
k : 螺纹牙型的高度 (X轴方向的半径值)。 此数值不可用小数点方式表示。 如k=1.3时,需写成P1300。 Δd :第一刀背吃刀量(用半径值指定)。此数 值不可用小数点方式表示。 如Δd=0.5时,需写成Q500。
3、螺纹切削复合循环 G73
格式:
G76 P(m)(r)(a) Q(△d min)R(d); G76 X(u) Z(W) R(i) P(k) Q(Δd ) F(L) ;
0.2
0.2
0.4
8次
0.15
0.3
9次
0.2
4.车螺纹前圆柱面及螺纹实际小径的
确定
车螺纹之前加
螺纹加工经验公式 工外圆对应的
尺寸
螺纹大径=公称直径-0.1XP
螺纹小径=公称直径-1.3XP
P为螺纹的螺距
车螺纹指令中指 定最后一次循环 时的X直径值
5.螺纹车削刀具切入与切出行程的确定
在数控车床上加工螺纹时,会在螺纹起始段 和停止段发生螺距不规则现象,所以实际 加工螺纹的长度W应包括切入和切出的空 行程量,如图所示。L1为切入空刀行程量, 一般取3~5mm;L2为切出空刀行程量, 一般取2~3mm,一般选在螺纹退刀槽的 终点处或螺纹收尾处。
例:
G76 P030860 Q0.1 R0.2;
(精车3次,倒角量为0.8导程,60°螺纹刀,最小切削量 0.1mm,精车余量0.2mm)
G76 X35 Z40 R0 P2.5 Q1 F4;
(直螺纹,牙高2.5mm,第一刀切深1mm,导程4mm)
1.指令格式(1)
例:
T0303; M03 S400; G00 X33 Z5 ;
L :螺纹导程。
3、螺纹切削复合循环 G73
格式:
精加工重复次数倒角量刀尖角 最小切入量 精加工余量
G76 P(m)(r)(a) Q(△d min)R(d); G76 X(u) Z(W) R(i) P(k) Q(Δd ) F(L) ;
终点坐标
螺牙高度 第一次切入量 螺纹导程
锥螺纹起点半径与终 点半径的差值
Z5; X28.5 ; G32 Z-28 F2; G00 X31; Z5; X 27.9; G32 Z-28 F2; G00 X31; Z5;
X27.5 ; G32 Z-28 F2; G00 X31;
Z5; X27.4 ; G32 Z-28 F2; G00 X100; Z50; M05; M30;
例:
单位是0.001mm
单位是0.001mm
GSK980TDA:
T0303; M03 S400; G00 X33 Z5 ; G76 P020060 Q100 R100;
(精车2次,60°螺纹刀,最小切削量 0.1mm,精车余量0.1mm)
G76 X31 Z-28 R0 P1300 Q800 F2;
(直螺纹,牙高1.3mm,第一刀切深0.8mm, 导程2mm)
P—工件螺距 K—保险系数,一般取80 如果数控系统能够支持高速螺纹加工,则可 采用高档螺纹加工刀具,主轴转速按照线速 度200m/min选取;而经济性数控车床如果 采用高主轴转速加工螺纹则会出现乱牙现象。
(2)进给速度 螺纹加工时数控车床主轴转 速和工作台纵向进给量存在严格数量关系, 即主轴旋转1转,工作台移动一个待加工工 件螺纹导程距离。因此在加工程序中只要给 出主轴转速和螺纹导程,数控系统会自动运 算并控制工作台纵向移动速度。