调速器调试试验
调速器试验项目

调速器试验项目
一、调速器油压装置调试:
1、上电检查试验;
2、模拟量、开关量的检查试验;
3、油泵手动启、停试验;
4、油泵自动启、停试验;
5、自动补气装置检查试验。
二、调速器无水试验:
1、上电检查试验;
2、测频回路(PT测频和齿盘测频)检查试验;
3、液压系统油管路漏检;
4、导叶、主配位移传感器调整试验;
5、手动开、停机试验;
6、模拟自动开、停机及紧急停机试验;
7、模拟一次调频试验;
8、模拟各通道切换试验;
9、电源消失试验;
10、模拟事故、故障试验;
11、导叶分段关闭调整试验;
12、调速器静态特性试验。
三、调速器有水试验:
1、手动开、停机试验;
2、自动开、停机试验;
3、空载频率摆动试验;
4、空载扰动试验;
5、机组过速(电气过速和机械过速)试验;
6、一次调频试验;
7、负荷下调速器试验;
8、机组甩负荷试验;
9、负载扰动试验(调速器参数建模试验);
10、事故低油压试验。
[汇总]调速器故障处理与调试
![[汇总]调速器故障处理与调试](https://img.taocdn.com/s3/m/d106a139dc36a32d7375a417866fb84ae45cc380.png)
调速器故障处理与调试1油泵、压油罐及导水机构最低操作油压试验待油压装置及调速器装配完毕后,安全阀调整螺栓松出,用手盘动油泵与电动机的联轴器,转动应均匀,且压油罐的供油阀,排气、排油阀均开启,主接力器处于全关锁定位置。
此时启动油泵电动机,启动应平稳无杂音,使油泵在空载状况下进行1小时试运转,(压油罐排气阀有油冒出时,即行关闭),以检查油泵转动部分是否发热,油泵运转情况是否良好。
油温应低于50℃,油泵轴承、外壳、及电动机轴承温度应低于60℃,外壳振动幅值小于0.05mm。
待油泵运转正常后,就可关闭排油、气阀,调整安全阀,使压油罐油压保持额定油压的16%或稍低。
打开供油总阀,操作接力器,此时导水机构应能在无水状态下作全行程的移动。
关闭供排油阀,调节安全阀,依次按额定油压值的25%、50%、75%、100%(为了安全,必须先排尽油罐顶部的空气)进行升压试验,各连续运20分钟,同时仔细检查补气阀,中间油罐,压油罐附件、接头,以及所有焊缝处的渗漏情况。
在无压时作相应处理,无油时作焊补处理。
上述试验合格后,再调整安全阀,使压油罐内的油压达1.25倍的额定油压保持30分钟。
检查压油罐各部位有无渗漏现象,压力表读数有无明显下降。
然后降至额定油压,用0.5kg的小锤沿焊缝周围70mm处轻轻锤击焊缝处应无渗漏现象。
然后打开排油阀排油,至压力为零。
关闭排油与排气阀,由排油阀口充入干净的压缩空气后,关闭排油阀,启动油泵供油至油面计上部刚能看出一点空气时止。
按此时的压力整定好电接点压力表的上限值,再降低0.1MPa~0.2MPa后整定好下限值,同时将集油槽内的补气阀吸气管调至集油槽油面以上(待油气比及油压合格后,再将管口调至油面下),再慢慢调整压油罐排油阀至合适的开度。
压油罐经过不断排油——补气——供油后,罐上部空气逐渐增加,在相同油压的情况下,油面就渐渐下降。
待油下降到油面计上稍能看清油面时,即应将电接点压力表的上、下限指示值向上移一相同数值,使油泵停止时,从油面计上部刚能看到空气即可。
6RA80调速器调试方法

6RA80调速器调试方法调速器是一种用于调节电机转速的设备,它可以根据需求改变电机的转速,实现转速控制。
在使用调速器之前,需要进行调试,确保其正常工作。
下面将介绍一种常用的6RA80调速器调试方法。
1.调试前准备在进行调试之前,需要先了解6RA80调速器的基本原理和功能,并对调速器进行全面检查,确保其电气连接正确、机械部分无故障。
2.参数设置调速器的工作需要根据具体的工况来设置相关参数,包括电压、频率、转速等。
根据实际情况,设置电压和频率参数,并将转速设定为初始值。
3.连接测试设备将调速器与电机连接,确保电机与调速器之间的接线正确无误。
同时,连接调试仪表,如测速仪、电压表、电流表等。
4.调试步骤(1)开机将电源接通,开启电源开关,调速器和电机开始工作。
(2)参数调整根据实际需求,逐步调整各参数,如电压、频率等。
可以通过观察测速仪表的读数来判断转速是否达到预期。
(3)检测电流通过电流表观察电机的电流情况,确保电流在正常范围内。
如果电流过大或过小,需要进行相应的调整。
(4)检测电压通过电压表观察电机的电压情况,确保电压在正常范围内。
如果电压过高或过低,需要进行相应的调整。
(5)稳定运行调整各参数后,观察电机的稳定运行情况,确保转速稳定在预期范围内。
如果转速不稳定,可能需要调整PID参数或其他相关参数。
(6)故障排除如果在调试过程中出现故障,如电机不能启动、转速异常等,需要根据具体情况进行故障排除,检查电路连接、传感器等部分。
5.调试记录在调试过程中,需要记录各参数的调整情况、电流、电压等数据,以备后续参考和分析。
6.安全注意事项在进行调试时,需要注意安全事项,如佩戴绝缘手套、避免触碰高压电源等。
同时,遵循调试步骤,逐步调整参数,确保调试过程安全和有效。
以上是一种常用的6RA80调速器调试方法。
调试过程中需要根据具体情况进行调整和判断,确保调速器正常工作,实现对电机转速的精确控制。
直流调速器(590C)的简单调试方法

5. 粗调完成后,要对调速器进行细调,既对调速器的输出进行校准。校准参数也是在设定参数的菜单内。按E键,直至液晶屏上行显示:DIGITAL DCDRIVE;下行显示:MENU LEVEL。按一下M键,液晶屏上行显示:MENU LEVEL;下行显示DIAGNOSTICS。按一下↓键,液晶屏下行显示变为SETUP PARAMETERS,按一下M键,液晶屏上行显示:SETUP PARAMETERS,下行显示:RAMPS;按数下↓键,直至液晶屏下行显示:CALIBRATION(校准)。按一下M键,液晶屏上行显示:CALIBRATION;下行显示:ARMATUREV CAL(电枢电压校准),再按一下M键,液晶屏上行显示:ARMATUREV CAL;下行显示:1.0000(校准值);此时可启动电机运行,并用万用表监测电枢电压,将设定值调到最大,待电机转速到达设定值后,用↑键和↓键调整修整值,将电枢电压输出调整到电机名牌额定电压值;再用万用表测量测速发电机的实际反馈电压值和极性。停止电机运行,待主回路接触器跳开后,将测速小板子上的测速反馈校正到实际的反馈电压值,如测速反馈极性不对,将两根测速线对换一下即可。再将反馈模式由电枢电压反馈切换到测速发电机反馈。操作方法如下:按E键,直至液晶屏上行显示:SETUP PARAMETERS,下行显示:CALIBRATION。按3下↓键,直至液晶屏下行显示:SPEED LOOP。按一下M键,液晶屏上行显示:SPEED LOOP(速度环);下行显示:PROP GAIN(速度环比例增益)。按4下↓键,直至液晶屏下行显示:SPEED FBK SELECT(速度反馈选择);按一下M键,液晶屏上行显示:SPEED FBK SELECT;下行显示:ARM VOLTS FBK(电枢电压反馈)。按一下↑键,将下行显示由ARM VOLTS FBK改为ANALOG
调速器的调试
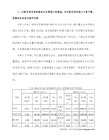
1)单机空载稳定性观测
①手动空载摆动值测试。检查机组各部分均已具备启动条件后,手动操作调速器使导叶慢慢开启至空载开度附近。当机组转速升至80%后,慢慢调整导叶开度使机组频率稳定在50Hz附近;停止操作导叶接力器,待稳定一段时间后用频率计测量机组频率,并记录连续3min机组频率摆动值的最大值fmax和最小值fmin则频率摆动范围为△f=fmax-fmin。如以相对量表示,则为△x=2(fmax-fmin)%。此时的频率波动,一般均系水力不平衡或机组本身问题所致,与调速器无关。
【摘要】调速器是水轮发电机组自动控制、调节系统的核心部件之一,其性能、工况直接关系水电站输出的电能质量和供电可靠性。介绍小型水电站调速器的主要调整试验及日常维护内容;常见故障的类别、现象和原因;分析查找故障的基本方法。
【关键词】小Biblioteka 水电站调速器调试试验故障判别 1概述
水轮机调速器是水轮机调节系统的核心,也是小型水电站总体自动化系统的关键部件之一。调速器对水轮机的控制,是自动控制原理在水轮发电机组控制上的具体应用,它除了具有一般自动控制装置的特征外,还有以下特点。
3.4常见的内因及故障现象
3.4.1运行不稳定
1)参数选配不当,如微分系数、比例系数过大都会引起空载的不稳定。
2)机械性卡阻,如伺服电机卡阻、引导阀活塞不活,或杠杆间的连接销钉松动,存在过大的运动间隙等。
3)主配压阀及接力器漏油。主配压阀或接力器漏油往往是不对称的,致使接力器在没有信号作用的情况下向开或向关的方向缓慢移动,移过一定距离时引起反馈机构动作,接力器又较快地移回原位置。因此,由漏油引起的摆动往往是不等速的,也可能是不等幅的周期性摆动。
2)空载扰动试验
机组需在各种工况下运行,欲使水轮机调节系统获得良好的性能,必须合理选择系统中的有关参数。空载扰动试验方法如下:通过突变频率给定值来进行频率扰动试验。扰动量一般为±(8-10%)fn,扰动试验需记录频率扰动的超调量和过渡过程时间、调节次数等有关数据。通过若干组有关数据的比较,就可确定系统的最佳参数。国标对该试验无考核要求。
浅谈水轮机调速器调试维护

浅谈水轮机调速器调试维护张仕俭(广西水利供水有限责任公司,广西南宁530023)应用科技脯要】水轮发电机的最重要的核心部件之一的调速器,在整个水轮发电机运行过程中直接关系到电能质量和供电持续的可靠性。
本文介绍了调速器基本功能,重点阐述调速器的调整t糙与维护,并给出诊断调速器的故障的技术,以达到良好的维护的效果,可供渗孝。
饫j禽§卸调速器;调试;维护水轮机调速器是水轮机调节系统的核心,也是小型水电站总体自动化系统的关键部件之一。
调速器对水轮机的控制,是自动控制原理在水轮发电机组控制上的具体应用。
1调速器的功能调速器的设计,根据用电用户小和水电运行环境的特殊要求,将针对常规调速器的不足之处,使得调速器具有更完善的功能和独特的性能。
并网功能:调速器能根据指令(机旁操作或遥控系统作)自动开机,采用闭环控制方式启动,机组转速上升迅速平稳,自动达到空载开度。
当机组到达空载开度后,自动准同期控制系统即能精确调控机组频率跟踪网频,并具有相角控制达到每分钟至少可提供6次以上过周期并网点的机会,使机组并网更迅速、平稳。
调节有功功率:我国大多数中小水电机组都是并入电网,长期带固定负荷运行的。
机组并网后,转速已被电网拖人同步状态,故不需继续调频,其主要操作是调节有功功率。
调速器具有开环调功及闭环调功两种方式,所用的执行机构又是数控电液随动系统,具有定位精度高,带自锁装置不溜负荷等特点,从而使整个调节有功功率的过程达到迅速、平稳、精确的:r Y,-,T-。
自动调频功能:中小型水轮发电机组在农村小电网中,经常因电网解列而被迫甩负荷停机。
调速器有性能优越的自动辨识系统,一旦电网解列,自动辨识系统立即将调速器由并网带基荷运行状态改为带小网调频运行状态。
快速的状态辨识及调控,能使装备有滑速器的地方电网在电网籀列后迎速自救,不会造成电网解列后,地方小电网全网崩溃的严重后果,保障了发电、供电、用电的安全。
2调速器的调整试验与维护21调速器的调试静态试验(充水前试验)。
调速器空载开机试验

调速器空载开机试验
一、试验依据
(一)空载扰动
转速摆动值和超调量最小、波动次数少、稳定快。
(二)空载摆动
任意3min内的机组转速摆动相对值不超过±0.15%。
二、试验准备
调试笔记本、万用表、调速器配线表
三、试验方法
(一)调速器空载扰动试验(以A套为例)
1.调速器在“现地”“自动”方式下;
2.选择进入“系统有水试验”窗口;
3.选择“空载扰动试验”,进入“空载扰动试验”界面;
4.在“调节参数”中输入PID调节参数;
5.在“频率给定”中输入给定频率(一般频率阶跃扰动信号在±2-±4Hz
内);
6.在调试笔记本的B&R软件内录取变量:导叶开度、频率给定、频率的波
形图;
7.观察调速器导叶动作调节过程、转速超调情况;
8.根据试验情况修改PID参数再次进行试验;
9.从中选取调节最优参数最为空载PID参数
(二)调速器空载摆动试验
1.在空载扰动试验完成后,选取空载扰动最优PID参数;
2.在空载工况下,录取转速3min内的摆动值
3.重复测定3次。
电子调速器调试教程

电子调速器调试教程1.确认电子调速器的基本参数:在调试电子调速器之前,首先要确认电子调速器的基本参数,如输入电压、输出电压、额定电流等。
这些参数将影响电子调速器的工作效果和稳定性。
2.确定电机的工作要求:在开始调试之前,需要明确电机的工作要求,比如最大速度、最小速度、加速时间、减速时间等。
这些要求将作为调试的依据,以确保电机可以按照要求进行工作。
3.连接电子调速器和电机:将电子调速器正确连接到电机上。
一般来说,电子调速器有输入端和输出端,输入端连接供电和控制信号,输出端连接电机。
确保连接无误,并且使用可靠的接线方法,以防止接触不良或短路等问题。
4.调整PID参数:大多数电子调速器都采用了PID控制算法来实现精确调速。
调试过程中,首先需要调整PID参数,以便使电机的转速能够快速、平稳地达到设定值。
PID参数一般包括比例系数、积分系数和微分系数。
通过逐步调整这些参数,可以找到最佳的PID参数配置,以实现较好的调速效果。
5.设定和调整速度曲线:当PID参数调整完成后,需要设定和调整速度曲线,即根据电机的工作要求设定电机的速度变化规律。
常见的速度曲线包括线性加速、S型加速等。
通过调整速度曲线,可以使电机的加速和减速更加平滑,从而提高电机的运行效果。
6.测试和监测:调试完毕后,需要进行测试和监测,以验证电子调速器的工作效果。
可以通过观察电机的运行状态、测量电机的转速、耗电功率等参数,来评估电子调速器的性能。
如果发现任何异常或不满意的地方,需要及时调整和修改相关参数,直到达到预期的效果。
7.定期维护和检查:电子调速器是一个复杂的装置,需要定期维护和检查,以保证其长期稳定运行。
维护和检查的内容包括清洁设备、检查接线、更换零部件等。
定期维护和检查可以延长电子调速器的使用寿命,并且减少故障的发生。
总结:电子调速器的调试是一个复杂而重要的过程,需要有一定的专业知识和经验。
通过正确调试,可以保证电子调速器的正常工作,提高电机的运行效率和稳定性。
- 1、下载文档前请自行甄别文档内容的完整性,平台不提供额外的编辑、内容补充、找答案等附加服务。
- 2、"仅部分预览"的文档,不可在线预览部分如存在完整性等问题,可反馈申请退款(可完整预览的文档不适用该条件!)。
- 3、如文档侵犯您的权益,请联系客服反馈,我们会尽快为您处理(人工客服工作时间:9:00-18:30)。
调速器调试试验文件管理序列号:[K8UY-K9IO69-O6M243-OL889-F88688][键入文档标题][键入作者姓名]2013/10/15目录1实验目的为了检验调速器性能的优劣,在正式投入运行前必须进行一系列调整实验,合理的选择整定调速器的各种调节参数,使其具有良好的静、动态特性,从而保证水轮发电机组安全可靠运行。
2静态实验(无水实验)2.1 试验前的检查2.1.1 电气柜、机械柜安装电气柜安装于电站屏柜布置层,不得与大电流、大功率设备,如励磁系统安装在一起。
柜体安装牢固,采用螺钉(或焊接方式)固定与基础板上,柜体包括柜体活动部分(前后门)必须可靠接地。
2.1.2 线路检查安装单位电缆接线已经结束,安装检查工作已经结束。
调速器交、直流220V输入电源线由独立电缆线输入,进入指定接线端子。
核实LCU输入调速器的离散量接点(开机令、停机令、增减负荷令、紧急停机令)、来自锁锭位置的接点和机组出口断路器接点必须为无源接点。
调速器信号输入屏蔽线按照要求接入,电缆屏蔽线应单边接入调速器接地端子,并且不得与动力线同用一根电缆。
2.1.3 安全检查发电机开关跳开、闸刀已拉开。
工作门全关、闸门落下(或蝴蝶阀已经全关),压力钢管处于无水状态。
水车室、转轮室内不得有人工作。
调速器静态试验工作票已开。
有关人员确认调试人员可以开始工作。
油压装置处于正常自动运行状态2.1.4 上电检查上电前,断开调速器柜内主设备电源输入端(位移传感器电源、接近开关电源等)。
通入交直流220V电压,测量上一步骤中断开各端电源电压是否正确,并记录当前工作电源的电压值。
在开度传感器侧测量与传感器接线电缆电源值(与设计传感器电源相同)。
检查完毕,断开电源,恢复线路。
上电后,观察10分钟,无明显烧焦、异味、放电声等。
2.2 接力器电气反馈传感器调整试验调速器处于机手动状态。
导叶(桨叶)开度传感器行程反馈的调整:A、精密电阻型传感器手动将导叶(桨叶)关到全关位置,稳定之后,旋开可变电阻的固定螺丝(共有2个),调整传感器电位器,使其输出电压值为0.15V±0.02,锁紧固定螺丝。
手动将导叶(桨叶)开到全开位置,稳定之后,调整印制板上的可调电阻,使其输出电压值为9.88V±0.02。
调整结束后,来回开启和关闭接力器,反复校核调整值。
B、直线位移传感器和拉线式位移传感器手动将导叶(桨叶)关到全关位置(传感器伸出本体为开启方向),稳定之后,再开到全开位置,保证导叶(桨叶)全行程在传感器的正常工作行程之内。
记录全关、全开位置稳定时程序监视到的反馈数据,通过程序调整使导叶(桨叶)全关、全开位置对应开度数值为0~100%,全关范围0~0.50%,全开范围99.00%~100%之内。
C、角位移传感器角位移传感器装有变程轮,其作用为将接力器直线行程转换为120度的角度位移。
导叶和桨叶开关机时间整定,分段关闭时间的整定。
注意事项:调速器发生误动作,相当一部分问题由直线位移传感器安装未校平,不牢固引起,因此,建议安装或检修时,将传感器本体校水平。
出现误动作的主要现象有:误开机、误发机频故障、显示屏显示错误值等等诸多问题。
2.3 远方信号校验试验远方开机令、停机令、增减有功指令、紧急停机命令、急停复归命令等开入量,触摸屏显示正确,与设计功能点对应。
(与监控设备单位配合)断路器接点从发电机出口断路器辅助接点直接引入,不得从继电器转接获得此接点。
锁锭投入、拔除信号可以直接从锁锭的位置行程开关处接线,也可以从监控开出扩展得到此信号。
2.4 测频回路试验做测频回路试验时,将接力器开启至大于6%的开度位置,调速器置手动,断路器处于“分”位置。
2.4.1 机频测量试验机频测量试验即网频端不施加频率信号。
断开外部机组PT信号线,使用信号发生器发出模拟机频信号,将信号发生器频率信号接入单相调压器输入端,调节输出端电压为0.3V接入调速器机频端子,依次改变机频在10Hz−95Hz间发频。
2.4.2 网频测量试验断开外部电网PT信号线,使用信号发生器发出模拟网频信号,将信号发生器频率信号接入单相调压器输入端,调节输出端电压为0.3V接入调速器网频端子,依次改变“网频”在48Hz−52Hz间发频。
以上测量发频值与收频值最大偏差不得大于0.02Hz。
2.4.3 模拟实际机端电压频率测量试验模拟实际机端电压频率测量试验即拆除上述1、2项试验接线,将市电接入调压器输入端,将输出端电压调节至120V,接入机频和网频输入端,观察10分钟,记录机频与网频变化最大值与最小值。
2.5 齿盘测频试验从用户得到机组额定转速(锦东机组额定转速166.7r/min)以及齿盘齿数(1、2号机72齿,3、4号机36齿),经换算得出相当于齿盘旋转时的模拟频率值。
用频率发生器模拟齿盘信号,观察频率测量是否正确。
采用频率发生器接入电压整形板后接入调速器齿盘测频开关输入端子。
2.6 模拟动作试验2.6.1 机械开限增减试验(带机械开限调速器)动作机械开限电磁阀,观察机械开限开关方向是否正确。
开限范围是否正确,开限刻度读数是否正确。
2.6.2 紧急停机实验将导叶开启到30%,按下“紧急停机”按钮,导叶应快速关至全关;按“急停复归”按钮,紧急停机电磁阀应复归,导叶能自由开启。
将导叶开启到全开位置,按下“紧急停机”按钮,导叶至全关,测量纪录导叶两段关闭时间,同时测量开机时间,如果不符合要求,需机械调整,记录最终的调整时间。
2.6.3 手自动切换试验将机械开限开启至80%。
模拟开机至空载状态,模拟合断路器,此时为开度模式。
操作按钮,切换导叶“自动”、“手动”,观察切换前后导叶的实际开度,同时观察指示灯显示、继电器动作情况。
切换前后,导叶开度无明显扰动(导叶变化应小于1%),指示灯显示、继电器动作应正确。
2.6.4 模拟动作试验机械开限全开,调速器切到自动方式,由信号发生器发出模拟机频,网频PT接入。
由中控室(或LCU)向调速器发出“开机”、“合断路器”、“停机”、“增加”、“减少”等命令,观察调速器在各种工况下工作状态,并记录波形,分析实际数据。
2.7 插值运算参数校核试验2.7.1 起动开度校核试验从电厂处获得确切的不同水头对应的开机空载开度曲线。
据此,确定第一开机度和第二开机度接点值。
输入不同水头,自动开机至空载状态。
观察纪录不同水头下的起动开度ⅠYKJ1、起动开度ⅡYKJ2是否符合曲线要求。
2.7.2 最大出力限制线校核试验从电厂处获得确切的不同水头对应的最大出力限制曲线。
模拟合上油开关,让调速器进入模拟负载状态。
输入不同水头,在不同的水头下操作,操作导叶增/减开关,模拟增加负荷至最大值,检查是否与曲线符合。
2.7.3 电气协联关系试验(轴流式双调机组)从用户获得确切的导叶和桨叶的协联关系曲线,检查并核定程序中的协联表格值。
调速器处于“自动”工况,开限L=100%,功率给定P G=0%,机频信号f j=50.00H Z。
导叶在不同开度位置下,调整不同水头值,记录桨叶开度,检查是否与曲线符合。
2.8 调节模式切换试验调速器工作在模拟负载状态下。
操作调速器触摸屏上模式切换按键,手动进行模式切换,观察导叶开度变化,检查是否有扰动。
手动模式切换使调速器工作在开度或功率模式下。
机频超出50±0.5H Z时,观察调速器是否自动切换至频率模式。
在功率模式下,模拟功率故障,观察调速器是否自动切换至开度模式。
2.9 电源消失试验调速器工作在模拟负载状态。
(断路器合,机频50Hz)先后切除直流、交流电源,观察接力器变化情况,检查是否有明显扰动。
先后接通交流、直流电源,观察接力器变化情况,检查是否有明显扰动。
2.10 故障、事故试验调速器工作于模拟负载状态,自动工况。
分别断开网频信号、功率反馈、故障灯应闪烁,发出故障报警。
断开机频信号线,调速器维持原位,同时发出报警信号。
断开导叶反馈信号,桨叶反馈信号(双调机组),调速器自动切至机手动,同时发出报警信号。
PLC程序内置PLC故障位,模拟PLC故障,调速器自动切至机手动,同时发出报警信号2.11 静特性试验1、调速器处于“自动”工况,负载状态,参数设置为:永态转差率bp=4%,PID系数kp=10、ki=10、kd=0,开限= 100%,YG=50%,f j=50.00H Z,PG=0,FG=50.00H Z。
2、将机频f j从50.00开始,以0.001Hz递增或递减,每间隔0.20Hz记录一次,使接力器行程单调上升或单调下降一个来回,录波并记录机频f Z和相应导叶行程值。
3、根据记录数据采用一次线性回归法计算调速器转速死区是否符合标准。
实验结果:转速死区要求小于2%%。
快速工程计算方法:记录同一发频值的最大接力器开关位置偏差为△ymax ,接力器的全行程为ymax,则试验最大转速死区为ix=(△ymax/ymax)×bp。
2.12 模拟甩负荷试验调速器置自动运行、断路器合、增加导叶开度,使接力器位于电气出力限制位置(判断是否能够限制住),断开断路器信号,观察导叶变化规律。
(要求超过稳定转速3%额定值以上的波峰不得超过2次,转速调整时间小于40S)2.13 通讯试验连接好通讯电缆(选用专用计算机通讯电缆),按监控系统要求设定站号、波特率、数据位、停止位、奇偶校验位、工作模式等。
保证通讯上行、下行量的正确性和可靠性。
3动态实验(充水后实验)3.1 手动开、停机试验3.1.1 试验前检查充水试验已经完成,确认可以进行开停机试验调速器处于纯机械手动方式,机械开限在全关位置,事故电磁阀已经复归,手动指示灯亮。
动态试验工作票已开。
3.1.2 试验过程根据实际水头设置水头参数,打开机械开限,拔出锁锭,准备手动开机。
缓慢操作手柄,使导叶缓缓开启,机组转速逐渐升高。
如未发现异常,应调整机组至空载运行状态,观察空载开度、水头和机组频率等参数是否正常。
注意事项:若机频、网频在30分钟内测量无异常,则切入自动运行工况。
记录当前水头值、空载开度。
机组自动稳定运行30分钟后,如无异常,切换至机械手动将导叶关闭,手动停机。
根据当前水头和空载开度调整第一和第二开机度,以0.5%开度递增和递减,将开机曲线表输入至文件寄存器。
(混流式机组第一开机度=1.6倍当前空载开度;第二开机度=1.1倍当前空载开度、贯流式机组相应减小)。
3.2 自动开停机试验3.2.1 试验前检查手动开机试验已经完成,试验过程无异常现象。
调速器处于停机备用状态,网频信号正常,“急停复归”指示灯、“自动”指示灯亮。
3.2.2 自动开机试验过程bp、bt、Td、Tn置运行参数,水头值为当前实际值。
锁锭拔出,机械开限开启至30%开度,准备自动开停机试验。
由中控室(LCU)发“开机令”,导叶先开到起动开度Ⅰ,经数秒钟后,当fj〉45HZ时导叶开度应关到起动开度Ⅱ,机组到空载状态。