间二硝基苯生产工艺规程
苯硝化生产硝基苯工艺过程与防范对策

苯硝化生产硝基苯工艺过程与防范对策摘要本文对硝基苯的生产工艺进行了简要阐述,分析了生产工艺危险性,并列举案例分析,最后针对硝基苯的安全生产,提出了安全预防措施,这对硝基苯的生产能长期、稳定、安全运行具有重要意义。
关键词:硝基苯工艺危险性预防措施引言硝基苯是一种重要的化工原料和中间体,用于生产苯胺、联苯胺、二硝基苯等多种医药和染料行业,也可用作于农药、炸药及橡胶硫化促进剂的原料,其中主要用途是制取苯胺和聚氨酯泡沫塑料,目前,90%以上的硝基苯用于生产苯胺[1-3]。
工业上硝基苯生产工艺过程主要包括苯硝化反应、硝基苯洗涤、硝基苯精馏等单元过程,生产过程中使用了大量易燃易爆、有毒有害、强腐蚀、强氧化的化学危险品。
由于苯硝化反应中副反应生成的杂质(主要是硝基酚盐类)爆炸危险性很高,而且极易积累在精馏塔釜等受热部位,监测和处理不及时就容易发生爆炸,使其生产过程中安全事故具有突发性、灾害性的特点。
因此对苯硝化生产硝基苯工艺过程进行危险性定量分析及对爆炸事故的安全研究,并提出具体的预防措施意义重大。
1 硝基苯生产工艺1.1硝基苯简介硝基苯,有机化合物,又名密斑油、苦杏仁油,无色或微黄色具有苦杏仁味的油状液体[4]。
化学式为C6H5NO2,难溶于水,密度比水大,相对密度1.205,熔点6℃,沸点210~211℃,闪点为87.8℃,爆炸下限为1.8%(93.3℃)。
易溶于乙醇、乙醚、苯和油。
遇明火、高热会燃烧、爆炸。
与硝酸反应剧烈。
低毒,半数致死量(大鼠,经口640mg/kg),硝基苯由苯经硝酸和硫酸混合硝化而得。
实验室制硝基苯由于溶有硝酸分解产生的二氧化氮而有颜色,除杂方式:加氢氧化钠溶液,分液。
1.2硝基苯的应用硝基苯是重要的基本有机化工原料,用于生产染料、香料、炸药等有机合成工业,经催化加氢或铁粉还原可得苯胺,这是硝基苯的最主要用途,由苯胺进而生产各种有机中间体,广泛应用于合成皮革(MDI)、橡胶、医药、农药、军事及其他工业[5-10]。
对二硝基苯的合成路线

对二硝基苯的合成路线1.引言1.1 概述二硝基苯是一种常见的有机化合物,具有广泛的应用领域,特别是在染料、炸药和药物合成等方面。
本文主要介绍了二硝基苯的合成路线。
二硝基苯的合成方法有多种,可以通过不同的反应途径得到。
其中最常见的方法是通过硝基化反应获得。
硝化反应是一种将有机物中的氢原子替换为硝基基团的反应,采用硝酸和底物进行反应。
本文将重点介绍两种常用的二硝基苯的合成方法。
第一种方法是将苯基聚合物与硝酸反应,在酸催化下发生硝基化反应,得到二硝基苯。
第二种方法是通过对硝基甲苯的还原反应得到二硝基苯。
这两种方法各有优劣,根据具体需求可以选择适合的合成路线。
在本文的后续内容中,将详细介绍这两种合成方法的具体步骤、反应条件和实验操作,以及反应机理的解析。
同时,我们还将对这两种方法进行对比分析,讨论它们的优劣势和适用范围,为读者提供更全面的了解。
通过对二硝基苯的合成方法进行研究和探讨,可以为相关领域的科学研究和工业生产提供重要的参考和指导。
同时,也有助于扩展我们对有机合成反应的认识和理解,提高我们在有机化学领域的研究水平。
文章的后续部分将详细介绍二硝基苯的合成方法,同时总结并展望相关研究的发展方向。
通过本文的阅读,读者将对二硝基苯的合成有更深入的了解,并可以运用这些合成方法开展自己的研究工作。
让我们一起深入探索二硝基苯的合成路线,为有机化学领域的发展做出贡献。
1.2 文章结构文章结构部分的内容可以描述整篇文章的组织结构和各个部分的内容安排。
具体可以按照以下内容编写:文章结构部分:本文将按照以下结构进行论述:引言、正文和结论。
引言部分将首先对二硝基苯的概念进行概述,介绍其重要性和应用领域。
接着,将阐明本文的目的和意义,以及为什么选择这个主题进行研究。
正文部分将分为两个主要部分:二硝基苯的合成方法1和合成方法2。
其中,合成方法1将介绍某一种具体的合成路线,包括所需的原料、反应条件和步骤等。
合成方法2将介绍另一种不同的合成途径,对比分析两种合成方法的优缺点,并提供相关的实验数据和反应机理说明。
硝基苯工艺规程

3、酸性硝基苯的中和、水洗
液碱的配制:液碱由液碱泵打碱到配碱罐循环,同时 打开软水稀释,其加软水量和液碱加料量为2:1,使碱 浓度在10%左右,当配碱罐(V517)液位达80%停止配 碱,再用液碱泵将稀碱送到稀碱高位槽备用。
自硝化分离器分离后的酸性硝基苯溢流至中和锅, 10%液碱从稀碱高位槽底部经流量计流入混合器中,同 时回收软水从软水高位槽(V519)经流量计流入混合器 中与稀碱混合,经混合稀释至3-5%浓度的稀碱流入中和 锅(F506),控制其出口PH在9-10,使酸性硝基苯得以 中和,中和后的硝基苯与废水由溢流管流出,沿切线方 向进入中和分离器(V521)中部,分离后上层废水去废 水捕集器(V534),下层硝基苯去一水洗锅(F507), 一水洗锅(F507)所用洗水系从二水洗锅(F508)水洗 后回收水,从一水洗锅(F507)中溢流出的硝基苯沿切 线方向进入一水洗分中部,分离后下层粗硝基苯流入二 水洗锅(F508),上层废水去废水捕集器(V534)。
4、产品用途:
硝基苯是重要的有机化工原料之一,用 于生产多种医药和染料中间体,例如用硝 基苯经磺化可生产硝基苯磺酸。也可直接 还原重排生产对氨基酚还可以进一步硝化 制得一系列中间体等。
硝基苯最大用途是用作生产苯胺。
二、原料规格
三、生产原理及主要化学反应
1、苯的硝化 主反应:
反应机理:HONO2++H2SO4→NO2++H2O+HSO4-
冀衡集团蓝天化工有限公司
硝基苯 工艺流程
主讲:冯世华
2011-04-09
主要内容:
产品说明 原料规格 生产原理及主要化学反应 工艺过程的叙述(附流程示意图) 不正常现象及其原因和处理办法 生产操作
间苯规程(间羟基苯甲酸车间工艺操作规程)
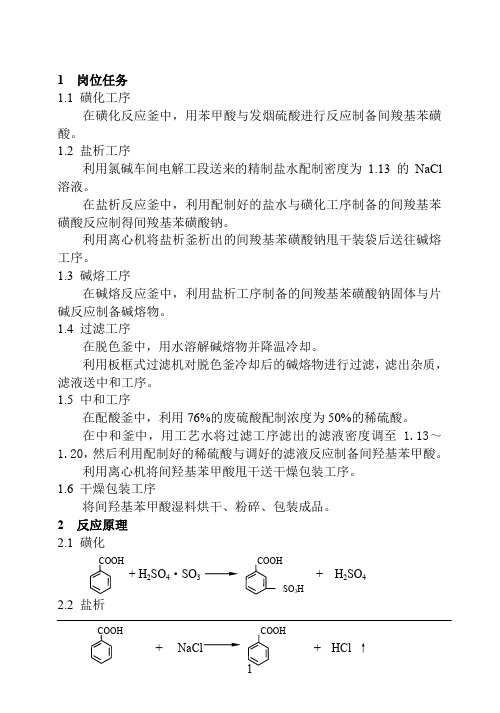
1 岗位任务1.1 磺化工序在磺化反应釜中,用苯甲酸与发烟硫酸进行反应制备间羧基苯磺酸。
1.2 盐析工序利用氯碱车间电解工段送来的精制盐水配制密度为1.13的NaCl 溶液。
在盐析反应釜中,利用配制好的盐水与磺化工序制备的间羧基苯磺酸反应制得间羧基苯磺酸钠。
利用离心机将盐析釜析出的间羧基苯磺酸钠甩干装袋后送往碱熔工序。
1.3 碱熔工序在碱熔反应釜中,利用盐析工序制备的间羧基苯磺酸钠固体与片碱反应制备碱熔物。
1.4 过滤工序在脱色釜中,用水溶解碱熔物并降温冷却。
利用板框式过滤机对脱色釜冷却后的碱熔物进行过滤,滤出杂质,滤液送中和工序。
1.5 中和工序在配酸釜中,利用76%的废硫酸配制浓度为50%的稀硫酸。
在中和釜中,用工艺水将过滤工序滤出的滤液密度调至 1.13~1.20,然后利用配制好的稀硫酸与调好的滤液反应制备间羟基苯甲酸。
利用离心机将间羟基苯甲酸甩干送干燥包装工序。
1.6 干燥包装工序将间羟基苯甲酸湿料烘干、粉碎、包装成品。
2 反应原理2.1 磺化+ H2SO4·SO3+ H2SO4SO3H2.2 盐析+NaCl+ HCl ↑SO 3H SO 3Na副反应:H 2SO 4(浓) + NaCl Na 2SO 4 + HCl ↑2.3 碱熔+ NaOH + Na 2SO 3 + H 2OSO 3Na ONa2.4 中和+ H 2SO 4 + Na 2SO 4OH3 工艺流程叙述将苯甲酸与发烟硫酸投入磺化釜中进行反应制得间羧基苯磺酸;之后过料至盐析釜中与在盐水配水槽中配制好的饱和盐水进行反应制得间羧基苯磺酸钠;将制得的间羧基苯磺酸钠打入离心机中甩干、装袋后投入碱熔釜中,与片碱进行反应制得碱熔料;再将碱熔料投入脱色釜中,溶解、降温,在板框式压滤机中过滤,滤液用滤液泵打入中和釜中与在配酸釜中配制好的硫酸进行反应制得粗品间羟基苯甲酸;将粗品放料到离心机中甩干送干燥包装工段进行烘干、粉碎、包装,制得成品间羟基苯甲酸。
硝基苯基本工艺介绍

硝基苯生产工艺技术方案硝基苯生产历史:硝基苯自一八三四年家由英国科学家米尔斯琪第一次有苯硝化制取,并于一八五六年在英国实现工业化生产,迄今已有一百近年历史。
作为最早发展起来化学工业原料之一,硝基苯在有机化工原料工业中始终占有重要地位。
硝基苯是生产苯胺老式原料,其产量95%用来做苯胺,还可以作染料中间体、用做溶剂等,五十年代后期随着橡胶橡胶助剂和聚氨基泡沫塑料工业发展和应用,苯胺需求量也越来越大,对其硝基苯需求猛增。
近年来,由于以美国ArCO化学公司一种由硝基苯直接制MDI新工艺推广应用再很大限度上增进了硝基苯生产发展。
当前硝基苯生产办法重要有两种:直接硝化法和绝热硝化法。
1、直接硝化法是将苯用混酸直接硝化生产硝基苯。
该办法又有不同生产工艺路线。
a、锅式间歇式持续硝化工艺b、环式硝化器持续硝化工艺c、锅环混用持续硝化工艺d、泵式持续硝化工艺这四种工艺共用长处是工艺技术成熟,操作易掌握,设备材料较普通,常压低温,重要缺陷是设备腐蚀严重,副产稀硫酸浓缩回收需耗大量能源。
当前各生产厂家以其技术优势和能源优势不同而各自采用适合自己状况不同工艺。
2、绝热硝化法:绝热硝化法是由美国氰胺公司和加拿大工业公司联合开发,并在美国罗比康公司和第一化学公司建成了工业化生产装置。
该法是将过量苯和硝酸与硫酸混合物加至一组反映器中,与135度和0.5Mpa压力下进行持续硝化反映,将反映物与稀硫酸分离,反映产物经中和、水洗和精制得到成品硝基苯,稀硫酸在真空下闪蒸出水后浓缩至70---75%循环使用。
该工艺突出长处在于反映热被稀硫酸吸取,硝化反映器内不需设立复杂冷却系统,节约了浓缩所需大量能耗。
该工艺还不能在国内普遍推广,重要障碍是对设备材料苛刻规定及昂贵工程造价。
国内硝基苯生产技术重要有锅式串联持续生产工艺和环式串联持续生产工艺。
使用锅式串联持续生产工艺厂家重要有南化工业公司等7家,采用环式串联持续生产工艺厂家有烟台合成革厂和河南化工厂两家,而两家工艺和设备又有所部同,砚台合成革厂为两器串联,河南化工厂为三器一锅串联。
年产12000吨二硝基苯工艺设计书

年产12000吨二硝基苯工艺设计书1.1设计的目的,意义及要求设计的目的及意义化工课程设计是高等工业学校各专业教学计划的重要组成部分,是学生在毕业前进行的、全面运用所学的专业知识的综合训练,是培养学生综合素质和解决工程实际问题能力的一个重要的实践性教学环节。
该过程是学生在校期间所学知识、理论及各种能力的综合应用与升华,是创新潜能得到激发的过程,是对各专业教学目标、教学过程、教学管理和教学效果的全面检验。
化工课程设计教学环节的教学目的是对学生从事科学研究的基本训练,是在教师指导下,通过毕业论文的教学过程,培养学生探求未知、探求真理的科学精神,以及优良的科学品质与科学素养,培养学生开展科学研究的方法。
使学生了解本学科的发展动态和最新科学技术,检验学生综合运用基础理论、基本知识和基本技能,解决科学与技术领域有关问题的能力,检验科研基本训练的实际效果。
工程设计是工程师工作实践中最富创造性的内容。
设计能力不同于理论分析能力、表达能力和动手能力,它是一种如何将思维形式的知识转化为客观上尚未存在而可以实现的物质实体的创造能力,即不仅是认识客观、表现客观而且是创造客观的能力。
因此设计能力的培养对工科学生尤为重要。
具体来讲化工课程设计有如下目的、意义:(1)通过课程设计的训练,使学生进一步巩固加深所学的基础理论、基本技能和专业知识,使之系统化、综合化。
(2)在课程设计中着重培养学生独立工作、独立思考并运用已学的知识解决实际工程技术问题的能力,结合课题的需要更应注意培养学生独立的获取新知识的能力。
(3)通过化工课程设计加强对学生计算、绘图、实验方法、数据处理、编辑设计文件、使用规范化手册等最基本的工作实践能力的培养。
(4)通过化工课程设计的训练,使学生树立起具有符合国情和生产实际的正确的设计思想和观点;树立起严谨、负责、实事求是、刻苦钻研、勇于探索并具有创新意识及与他人合作的工作作风。
设计的要求化工生产具有连续化、自动化程度高,且生产过程具有易燃、易爆、易腐蚀、能耗大、对环境有污染等特点。
二硝基苯生产过程中硝基酚生成原因及控制
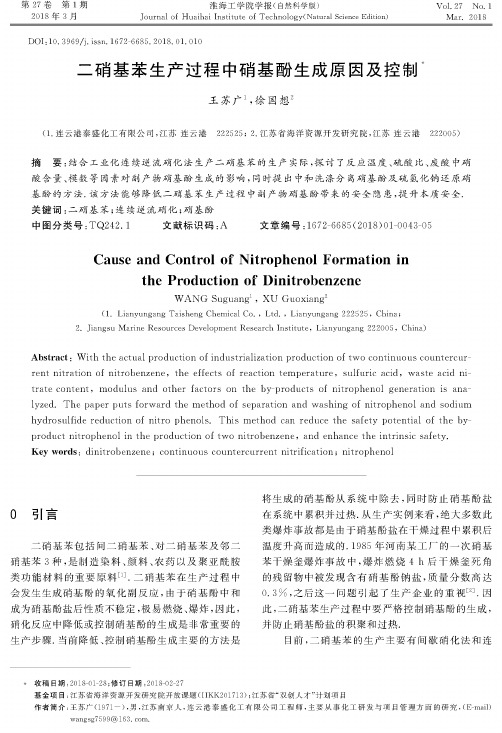
第27卷第1期2018年3月淮海工学院学报(自然科学版)Journal of Huaihai Institute of TechnologyCNatural Science Edition)Vol.27 No. 1Mar.2018D O I:10. 3969/j. issn. 1672-6685. 2018. 01. 010二硝基苯生产过程中硝基酚生成原因及控制^王苏广\徐国想2(1.连云港泰盛化工有限公司,江苏连云港222525; 2.江苏省海洋资源开发研究院,江苏连云港222005)摘要:结合工业化连续逆流硝化法生产二硝基苯的生产实际,探讨了反应温度、硫酸比、废酸中硝 酸含量、模数等因素对副产物硝基酚生成的影响,同时提出中和洗涤分离硝基酚及硫氢化钠还原硝基酚的方法.该方法能够降低二硝基苯生产过程中副产物硝基酚带来的安全隐患,提升本质安全.关键词:二硝基苯;连续逆流硝化;硝基酚中图分类号:T Q242. 1 文献标识码:A文章编号:1672-6685(2018)01-0043-05Cause and Control of Nitrophenol Formation inthe Production of DinitrobenzeneW A NG Suguang1 ,XU Guoxiang2(1. Lianyungang Taisheng Chemical Co. , Ltd. , Lianyungang 222525, China;2. Jiangsu Marine Resources Development Research Institute, Lianyungang 222005, China)Abstract:With the actual production of industrialization production of two continuous countercurrent nitration of nitrobenzene,the e ffects of reaction temperature,sulfuric acid,waste acid nitrate content,modulus and other factors on the by-products of nitrophenol generation is analyzed.The paper puts forward the method of separation and washing of nitrophenol and sodium hydrosulfide reduction of nitro phenols.This method can reduce the safety potential of the byproduct nitrophenol in the production of two nitrobenzene,and enhance the intrinsic safety. Keywords:dinitrobenzene;continuouscountercurrentnitriiication;nitrophenol0引言二硝基苯包括间二硝基苯、对二硝基苯及邻二硝基苯3种,是制造染料、颜料、农药以及聚亚酰胺类功能材料的重要原料[1].二硝基苯在生产过程中会发生生成硝基酚的氧化副反应,由于硝基酚中和成为硝基酚盐后性质不稳定,极易燃烧、爆炸,因此,硝化反应中降低或控制硝基酚的生成是非常重要的生产步骤.当前降低、控制硝基酚生成主要的方法是*将生成的硝基酚从系统中除去,同时防止硝基酚盐在系统中累积并过热.从生产实例来看,绝大多数此类爆炸事故都是由于硝基酚盐在干燥过程中累积后温度升高而造成的.1985年河南某工厂的一次硝基苯干燥釜爆炸事故中,爆炸燃烧4h后干燥釜死角的残留物中被发现含有硝基酚钠盐,质量分数高达0.3%,之后这一问题引起了生产企业的重视[2].因 此,二硝基苯生产过程中要严格控制硝基酚的生成,并防止硝基酚盐的积聚和过热.目前,二硝基苯的生产主要有间歇硝化法和连*收稿日期:2018-01-28;修订日期:2018-02-27基金项目:江苏省海洋资源开发研究院开放课题(HKK201713);江苏省“双创人才”计划项目作者筒介:王苏广(1971 —),男,江苏南京人,连云港泰盛化工有限公司工程师,主要从事化工研发与项目管理方面的研究,(E-mail) wangsg7599@163. com .44淮海工学院学报(自然科学版)2018年3月洗涤水续逆流硝化法两种.与间歇硝化法相比,连续逆流硝 化法的优点较 :①、、反应物浓度等工 定,不随时间的变化而变化,故反在较为有利的条件下,有利于提高并稳定产品的 ;②工艺条件变化小,工人操作方便,有利于,且易于实现自动化控制.相而言,连续逆流硝化法更便于运用自动控制 :科学的成果, 消除事故 的主要因素a、、反应物浓度等不稳定因素)如果企业暂时不能达 样的要求,则可采取两个个以上的 措施,形成最合 :系,取得最大程度的 能.合工业化连续逆流硝化法生产二硝基苯的实例,影响 硝基酚的因素,提出二硝基苯中硝基酚的分离及处理方法.1硝化反应机理二硝基苯生产中的硝化反应机理为:首先硝酸与硫酸反应,生成硝酸合氢离子与负硫酸氢根;硝酸 合氢离子分解 与硝酰 ;肖酰 再与硝基苯络合物;而后 络合物分解,得硝化物与氢;氢与硫酸氢合为.h 2so 4 + h n o 3 幑幐h 2n o 3 + + h so 4 一,H2N03十幑幐 H20+N02+,n o 2N 〇2N 〇2+n o 2HN 〇2Hn o 2帨 J +HS 〇4 一 —--I I ;|+H2SO4x n o 2n o 2同时硝化过程中发生氧化副 硝基酚[3],n o 2n o 2帨J十N 〇2Hn o 2NO2^H、0N0n o 2NO2h 2o + hso 4+n o 2+ h n o 2 + h 2so 4,OHn o 2+ hso 4HOHno 2HN02OHno 2no 2+ h 2so 4.OH+H S 04no 2o h2生产流程连续逆流硝化法生产二硝基苯主要包含硝化、预洗、中和、洗涤等工序,工艺流程 1 .硝化装置由4台硝化机、2台预洗机、2台中和机、2台洗涤机串联而成.连续硝化用的硝化机由釜体、、提升器、换热盘管、导流筒、分 、H 、进出等;页洗机、中和机及洗涤机J相同,由釜体、、提升器、换热夹套、导流筒、分、、进出等.十预洗废水预冼废水二硝基苯图1二硝基苯连续逆流硝化流程Fig . 1 D initrobenzene continuous countercurrent nitrification p r o c e j>s第1期王苏广等:二硝基苯生产过程中硝基酚生成原因及控制452. 1硝化硝基苯从1#硝化机加人,硫酸由4#硝化机加人,硝酸补加到2#,3#,4#硝化机,预洗废水加到1 #硝化机,各硝化机之间相互串联.硝化物与废酸逆流,废酸逐台流到1 #硝化机并从分离器流出,废 酸浓缩后循环套用;酸性二硝基苯逐台流到4#硝 化机并从分离器流出.2.2预洗酸性二硝基苯从4 #硝化机流人1#预洗机,预 洗水由2 #预洗机加人,两台预洗机之间相互串联.硝化物与洗废流,洗废台流 1#洗机,再流到1 #硝化机,回收废水中的硝酸、硫酸,酸性二硝基苯逐台流到2 #预洗机.预洗的作用是用水洗去硝化物中的酸与水溶性杂质,减少中和过程中氢氧化钠用量.2.3 中和酸性二硝基苯从2 #预洗机流人1#中和机,氢 氧化钠溶液连同洗涤废水由2#中和机加人,两台 中和机之间相互串联.二硝基苯与废水逆流进行中和反应,废水逐台流到1#中和机,并从1#中和机 流出,二硝基苯从2#中和机流出.中和的目的是中和酸,更主要的是将硝基酚与氢氧化钠作用生成硝基酚钠盐,而后溶于水,与硝化物分离.2.4洗涤二硝基苯从2#中和机流人1#洗涤机,洗涤水由2#洗涤机加人,两台洗涤机之间相互串联.硝化物与洗涤水逆流进行充分洗涤,废水逐台流到1 #洗涤机,并从1#洗涤机流至2#中和机,洗涤合格的二硝基苯从2 #洗涤机流人成品槽.中和后洗涤的目的是洗去二硝基苯中残留的氢氧化钠、硫酸钠、硝酸钠与硝基酚钠盐等杂质.2.5废水预处理从1#中和机流出的废水和经过计量的硫氢化钠连续流人1#废水还原釜,然后依次流人2#,#废水还原釜进行还原反应.废水预处理的目的是将废水中的硝基酚钠转化为氨基酚钠,消除废水处理过程中的安全隐患.3影响硝基酚生成的因素二硝基苯的硝化反应与生成硝基酚的氧化副反应是平行反应.结合连续逆流硝化法生产数据发现,反应温度、硫酸比(指投人的原料硫酸与硝基苯的体积比)、废酸中硝酸含量、模数(又称相比,指废酸和有机相的体积比)是影响硝基酚生成的主要因素. 3.1反应温度对硝基酚生成的影响反应温度会对硝化反应和氧化副反应的速度产生影响,具体为:反应温度提高10'c,硝化反应速度提高2. 2倍,氧化副反应速度提高4倍[4].因此可通过降低反应温度来降低两个反应的速度.在降低温度的过程中,硝化反应速度降低得慢,氧化副反应速度降低得快.反应温度对硝基酚生成的影响如表1所示.表1反应温度对硝基酚生成的影响Table 1Effect of reaction temperature on the formationof nitrophenol序号反应温度/C硝基酚质量分数/%12107. 59860. 162 0387 20.081 348510.081 0582 50. 079 6680 60. 079 2由表1可以看出,随着反应温度的降低,硝基酚生成量逐渐下降;当反应温度降至87. 2 时,硝基酚生成量不再明显下降.二硝基苯是间、邻、对二硝苯的混合物,由于该混合物在80〜82 C开始结晶,因此反应温度不应过低,控制在(85±2)C为宜.3.2硫酸比对硝基酚生成的影响硝硫混酸硝化中,硫酸是活化剂,它使硝酸离解成硝酰阳离子N〇2 + .硫酸比(指投人的原料硫酸与硝基苯的体积比)小,硫酸有效浓度低,硝酰阳离子N〇2+含量就低,则硝化反应程度低,氧化副反应程高,而 的硝基酚 .比硝基酚的2.表2硫酸比对硝基酚生成的影响Table 2 Effect of sulfuric acid ratio on the formationof nitrophenol序号硫酸比硝基酚质量分数/ %10. 850. 080 520. 800. 080 930. 750. 081 040. 650. 081 850. 600. 109 260. 550. 128 0由表2可以看出,硝基酚的生成量随着硫酸比降低而升高.提高硫酸比可以减少氧化副反应,控制46淮海工学院学报(自然科学版)2018年3月硝基酚的生成,但硫酸比过大,硫酸有效浓度升高,不仅会增加硫酸的消耗,而且会使硝化物在废酸中的溶解度增大,导致废酸和硝化物分离不清.试验数据表明,1 000 L质量分数为94. 8%的硫酸能溶解400 k g二硝基苯.因此硫酸比控制在0. 65〜0. 75较为合适.3.3废酸中硝酸含量对硝基酚生成的影响根据反应原理,废酸中硝酸含量升高,硝酰阳离子浓度升高,则氧化副反应速度降低,硝化反应速度升高.废酸中硝酸含量对硝基酚生成的影响如表3所示.表3硝酸含量对硝基酚生成的影响Table3Effect of the content of nitric acid on th eformation of nitrophenol序号硝酸体积分数/%硝基酚质量分数/%1 21. 0150. 116 20.102 03200.081 24250.081 65300.081 86350.081 7从表3可以看出,硝酸体积分数在低于2. 0%时,随着体积分数的升高,硝基酚生成量不断下降; 硝酸体积分数升高到2. 0%以后,硝基酚的生成量趋于稳定;如果再提高废酸中硝酸的体积分数,随废 酸流失的硝酸就会增多,使硝酸的消耗升高.综合考虑认为,硝酸体积分数控制在2%〜3%较为适宜. 3.4模数对硝基酚生成的影响硝化反应过程中,模数(废酸与有机相的体积比)增大,硝化反应速度升高,氧化副反应相对减少[5].因硝酸在废酸、有机相中的分配系数不同,故 其在废酸、有机相中的数量差别很大.废酸中的硝酸用于硝化反应,而硝化物中的硝酸则用于氧化反应,硝化机内废酸增多,有机相就会减少,生成的硝基酚量也减少.模数对硝基酚生成的影响如表4所示.表4模数对硝基酚生成的影响T able4 Effect of m odulus on the formation of nitrophenol序号模数硝基酚质量分数/%12. 00.142 02250.113 53300.081 64350.081 45400.081 66450.081 5从表4可以看出,模数增大,氧化副反应减少,硝基酚生成量下降;当模数增大到3.0时,硝基酚生成量不再下降,若继续增大模数,势必造成产能降低.综合考虑,适宜模数控制在3〜4之间.4中和洗涤分离硝基酚硝基酚呈弱酸性,可与氢氧化钠发生中和反应,生成硝基酚钠盐.硝基酚钠溶于水,利用该性质先用8%(质量分数)氢氧化钠水溶液将二硝基苯中的硝基酚中和成硝基酚钠盐,然后加水洗涤分离.生产实 践发现,洗涤水用量对硝基酚钠盐含量具有一定影,5表5洗涤水量对硝基酚钠盐含量的影响 T able5 Influence of w ashing w ater on the content ofsodium salt of nitrophenol序号V(水):V(二硝基苯)预洗前硝基酚质量分数/%中洗涤后硝基酚质量分数/%10. 5:10. 081 600035321. 0:10. 081 8000182315:10. 081 5000029420:10. 081 6000028525:10. 081 0000026630:10. 081 2000028注:硝基酚质量分数用紫外分光光度法测定,中和洗涤后的硝基 酚钠盐折算为硝基酚计.从表5数据可以看出,随着洗涤用水的增加,二 硝基苯中硝基酚钠盐质量分数逐渐降低,当洗涤水与二硝基苯的体积比达到1. 5:1时,二硝基苯中硝基酚钠盐质量分数不再下降.综合考虑废水处理成本及安全因素,将洗涤水与二硝基苯的体积比控制在1. 5:1至2.0:1之间较为适宜.5硫氢化钠还原硝基酚二硝基苯中和洗涤废水呈碱性,p H值在8〜9, 中含有 的氢氧化钠氢化钠与氢氧化钠应生成还原能力更强的硫化钠,硫氢化钠与硫化钠均属于硫化碱,可用于还原硝基.硫化碱还原具有反应条件温和、可使多硝基化合物中的硝基分步还原等优点[6].本工艺采用硫氢化钠还原废水中的硝基酚钠盐,将其转化为安全稳定的氨基酚钠盐.表6为 随机抽取不同批次二硝基苯洗涤废水处理前后硝基酚含 的第1期王苏广等:二硝基苯生产过程中硝基酚生成原因及控制47表6处理前后硝基酚的含量对照T able6 Control table of nitrophenol content b e fo re andafter treatm ent in w ashing w astew ater序号处理前洗涤废水中硝基酚质量分数/%处理后洗涤废水中硝基酚质量分数/%10.062 80. 000 2320.063 10. 000 1830.064 50. 000 2640.061 20. 000 2250.062 30. 000 1860.063 50. 000 19注:硝基酚质量分数用紫外分光光度法测定,废水中的硝基酚钠 盐折算为硝基酚计.由表6可见,使用硫氢化钠可以有效地将二硝基苯中和洗涤废水中的硝基酚转化为氨基酚钠盐,确保废水后处理安全.6结论在二硝基苯的生产过程中,氧化副反应生成硝基酚不可避免,但采用连续逆流硝化法,通过改进设备,优化工艺条件,综合运用源头控制与末端治理相结合的技术方案,可有效降低副产物硝基酚带来的安全隐患,提升本质安全.对生产中的相关数据进行总结分析可以看出,通过降低反应温度、提高硫酸比、增加废酸中硝酸的含量、增大模数等措施,可降低氧化副反应的发生,减少硝基酚的生成;采用连续逆流中和洗涤工艺可以将硝基酚转化为硝基酚钠,有效实现二硝基苯与硝基酚的分离;废水中的硝基酚钠采用硫氢化钠还原,将其转换成氨基酚钠类物质,使生产的危险等级明显降低.参考文献:[1]盂明.年产12000吨二硝基苯工艺设计研究[D].上海:华东理工大学,2012.[]翁绍琳.防止硝基化合物生产中的爆炸事故[J].染料工业,1996,33(5) :19-22.[]杨师棣,李宽芳,张前进.硝基苯制备中副产物的分析[].张掖师专学报(综合版),1996,13(1) :115-118.[]尹世英,张金鹏.控制TNT生产中氧化副反应的方法[].兵工学报,1994(1)22-25.[]董云.MNT废酸用甲苯萃取工艺的探讨[J].染料工业,2001,38(2)47-48,33.[]陈永红.对硫化碱还原历程写法的探讨[J].阜阳师范学院学报(自然科学版),1997(3): 6263.(责任编辑:秦海明)声明为适应我国信息化建设发展的需要,有力地促进科研学术信息的交流和信息资源的开发利用,扩展广大作者的学术交流渠道和促使科研成果的迅速转化,本刊已先后加人了《中国学术期刊(光 盘版)》《中国期刊网》、由国家科技部组织实施的原中国科技信息研究所万方数据网络中心具体负责运作的“万方数据网”、由科学技术部西南信息中心所创办的大型综合性《中文科技期刊数据库》,并成为上述《中国学术期刊(光盘版)》《中国期刊网》《中国学术期刊综合评价数据库》《中国核心期刊(遴选)数据库》以及“万方数据—数字化期刊群”《中文科技期刊数据库》全文收录期刊,它们将 以网络和光盘等不同的方式向社会提供文献信息服务.凡向本刊所投稿件,均视为愿意进人上述各文献数据库,其作者著作权使用费已包含在本刊一次性所付稿酬中,不再另付.如有不同意者,请另 投它刊或特别声明需另作处理.淮海工学院学术期刊社。
硝基苯的生产
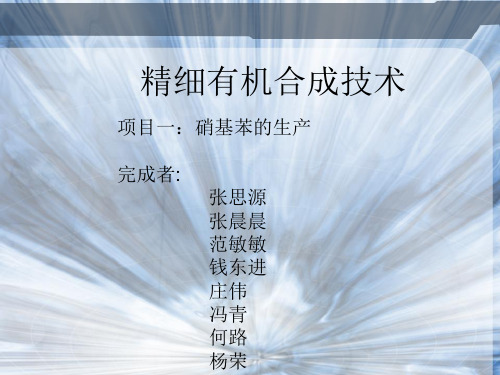
损害。急性中毒:有头痛、头晕、乏力、皮肤粘膜紫绀、 手指麻木等症状;严重时可出现胸闷、呼吸困难、心悸, 甚至心律紊乱、昏迷、抽搐、呼吸麻痹。有时中毒后出现 溶血性贫血、黄疸、中毒性肝炎。慢性中毒:可有神经衰 弱综合征;慢性溶血时,可出现贫血、黄疸;还可引起中 毒性肝炎。 环境危害:对环境有危害,对水体可造成污染。 燃爆危险:本品可燃,有毒。
苯绝热硝化的优点:
最后反应温度高,硝化速率快;国外已建成 年产19万吨的生产装置,硝化过程不需冷却 水;利用反应热浓缩废酸,能耗低,可降低 生产成本。但此法为防止苯的挥发,损失热 量,防止空气氧化,需在压力下密闭操作, 闪蒸设备需要特殊材料钽。国内尚未采用绝 热硝化法,仅致力于常压冷却连续硝化法的 工艺改进
640
0.0058
515
0.0018
3.3
0.0006
8
0.0024
• 工业成本
(2.9×2×640+0.9×2×515+0.3×2×3.3+1.2×2×8)
=4660.18元
硝基苯:
• 急性毒性:LD50:489 mg/kg(大鼠经口);2100 mg/kg(大 鼠经皮) LC50:无资料亚急性和慢性毒性:刺激性:家兔经眼: 500mg/24小时,轻度刺激。家兔经皮: 500mg/24 小时, 轻度刺激。
通过洗涤器除去。
• 防护措施:
• 呼吸系统防护:可能接触其蒸气时,佩戴过滤式防毒面具 (半面罩)。紧急事态抢救或撤离时,佩戴自给式呼吸器。 眼睛防护:戴安全防护眼镜。身体防护:穿透气型防毒服。 手防护:戴橡胶耐油手套。其他防护:工作现场禁止吸烟、 进食和饮水。及时换洗工作服。工作前后不饮酒,用温水 洗澡。注意检测毒物。实行就业前和定期的体检。
- 1、下载文档前请自行甄别文档内容的完整性,平台不提供额外的编辑、内容补充、找答案等附加服务。
- 2、"仅部分预览"的文档,不可在线预览部分如存在完整性等问题,可反馈申请退款(可完整预览的文档不适用该条件!)。
- 3、如文档侵犯您的权益,请联系客服反馈,我们会尽快为您处理(人工客服工作时间:9:00-18:30)。
NO 24-HNO 3=O 2N —<(C ==?S-^O 2 +H 2O3.3酸性二硝基苯的中和精制,酸性二硝基苯中含有酸(主要为硝酸)和副反应生成的邻、对二硝基苯,用氢氧化钠中和酸性硝基苯 中的硝酸,利用亚硫酸钠磺化取代反应,生成不溶于水的邻、对硝 基苯磺酸钠,以达到精制的目的。
3.4精制锅的间二硝基苯的水洗。
用水洗去除中和精制后产生的少 量的碱和邻、对硝基苯磺酸钠,从而制得高纯度的间二硝基苯。
有关反应如下:NO 2 SO 3Na<<=>>-^NO 2 +Na 2SO 4 ------------ ►Ch +H 2O NO 2 +Na 2SO 4 NO 2 -<(S^>-SO 3Na +NaNO 23.5硝化反应的抽取。
用硝基苯萃取硝化废酸中的二硝基苯,同行 斯硝基苯同硝化废酸中的剩余硝酸反应生成二硝基苯。
抽取后的废主反应: NO, +HoO 副反应:Z VNO 2+ HNO 3 =酸送浓酸岗位提炼后循环使用或外售。
硝基苯抽取后成为酸性硝基苯,作为硝化的原料。
有关反应如下:HNO3+NaOH=NaNO3+H2O四、工艺过程的叙述4.1各种原料的接受4.1.1粗硝基苯从硝基苯车间粗硝基苯储罐由输送泵送到木工段硝基苯计量槽(V102)中。
4.1.2硫酸从废酸回收工段浓缩岗位槽自流到木工段硫酸计量槽(V105)中。
4.1.3 .98%硝酸从硝基苯工段硝酸储罐经泵送至木工段硝酸计量槽(V104)中4.1.4.30%的液碱从硝基苯工段液碱储罐经泵送至木工段液碱计量槽(V106)中。
4.1.5亚硫酸钠经提升机(LS101)送至三楼,供亚硫酸钠配制罐(104AB)使用。
4.2硝基苯的硝化421硝化开车前的检查和准备1)检查硝化锅各部位是否正常,水压、汽压、电压是否稳定,温度计,真空表,报警装置是否好用。
2)硝化锅的数字显示仪和记录仪,两表温差不能超过2度,并记录好两表的同步温度水温差。
3)领取操作记录表,做好记录。
422.硝化工序正常停车1)反应达到终点,确认合格,放料完毕后,即可停搅拌,继续通冷却水,直至室温(或<40度)可停冷却水。
2)当全而停下来后,应在现场对整个情况进行核对。
以防止漏停或错停,即此才认为停车完毕,关闭硝化系统的记录仪表。
填写操作记录。
3)如属长时间停车,必须用空压打净蛇管及夹套内的水,以防止冻坏。
4.硝化过程的叙述:酸性硝基苯从萃取锅经酸性苯泵(P102AB)打入酸性硝基苯计量槽(V101AB),向硝化锅(R102AB)中先从硫酸计量槽(V105)加入规定的硫酸,打开硝化锅(R102AB)的搅拌装置,再从硝酸计量槽(V102AB)加入规定量的浓硝酸,同时开硝化锅蛇管及夹套的冷却水,冷却降温,硝酸加完后,冷却到锅温到30度,开始滴加酸性硝基苯计量槽(V101AB)中的酸性硝基苯,调节加料速度,加料时间半小时。
硝化温度不能超过80度,硝基苯加完后,缓慢升温到90度,继续保温35min,取样分析粗间二硝基苯的凝固点,以及废酸中硝酸的含量,合格后,降温至70-72 度,在20min内加入精流量计计量的水进行稀释,稀释温度控制在85-90度静止约30min,分离后下层废酸放入抽取锅(RIOla、b)中,用硝基苯萃取废酸中的硝酸和间二硝基苯,上层间二硝基苯放入精制釜(R103a、b)中。
4.2.3硝化工序正常停车1)反应达到终点,确认合格,放料完毕后,即可停搅拌,继续通冷却水,直至室温(或<40度)可停冷却水。
2)当全面停下来后,应在现场对整个情况进行核对。
以防止漏停或错停,即此才认为停车完毕,关闭硝化系统的记录仪表。
填写操作记录。
3)如属长时间停车,必须用空压打净蛇管及夹套内的水,以防止冻坏。
4.3精制反应及造粒包装4.3.1精制、造粒、包装开车前的检查和准备1)检查精制锅各部位是否正常,水压、气压、电压是否稳定,温度计,真空表是否良好,计量装置是否准确。
2)准备好包装袋。
3)领取操作记录表,做好记录。
4.3.2精制的工艺叙述:首先向精制釜中加入计量的清水,开启精制釜搅拌升温至70摄氏度,将硝化釜内的粗二硝基苯放入精制釜内,然后从碱计量槽(V106)加入30%的液碱到精制釜中,调整溶液PH值为7时,开始降温至79度以下,向精制釜内,加亚硫酸钠溶液亚硫酸钠的配制在亚硫酸钠配制锅(R104a、b)中加入规定量的水,然后加入亚硫酸钠,配制成11-17%的溶液,供精制使用。
精制釜精致温度控制在68-75度,精致时间90-110min,取样分析间二硝基苯的凝固点,合格后,降温到90度,静置30min分离后, 上层废水流入集液罐(VI 10a、b)中。
升温至95度,保温30min后,加酸调节PH值5-6 ,开喷淋水降温至75度,75度以下用夹套水冷却至60度。
造粒样品分析合格后,物料流入以铺好抽滤布的抽滤槽(V109a、b、c、d)中。
开真空泵(P103a、b),集液罐及各阀门处于正常位置,开始放料, 抽净后,用喷淋水洗料1-2次,洗涤合格后,经真空泵抽滤水后分析,分析合格后,进行包装,最终的间二硝基苯成品。
集液罐的废水放入废水池外排。
4.3.3精制、造粒、包装的正常停车1)反应达到终点后,确认和狗,放料完毕后,即可停搅拌。
2)当全面停下来以后,应对整个情况进行核对,以防止漏停和错停,确认后,即可停车完毕。
关闭记录系统,填写记录表。
3)如属长时间停车,必须用空压打净系统,以防止冻坏。
4.4萃取4.4.1萃取开车前的检查和准备1)检查萃取锅各部位是否正常,水压、电压、汽压是否稳定。
温度计是否良好。
2)记录表是否完全。
4.4.2萃取的工艺叙述:硝化锅下层的废酸通过管道流入萃取锅(R101A、B)中,开启搅拌,慢慢从硝基苯计量槽加入其中粗硝基苯,加完后搅拌30min,静置3小时,分离下层废酸去浓缩岗位。
经提浓后循环使用。
上层酸性硝基苯用酸性硝基苯泵(PllOa、b)送往酸性硝基苯计量槽,功硝化使用。
4.4.3萃取正常停车1)反应到达终点,确认合格后,放料完毕后,即可停搅拌。
2)当全面停下来以后,应在现场整个情况进行核对,以防止漏停和错停,确认后即可停车完毕,填写操作记录表。
3)如属长时间停车,必须用空压打净系统,以防止冻坏。
4.5工艺流程简图五、不正常现象的原因及处理方法5.1硝化工序5.1」硝化工序可能发生的不正常现象及处理方法5.1.2紧急情况的处理1)如遇停水、停电,应立即停止加料,继续加水冷却,并及时与负责生产指挥的领导部门联系。
2)用手盘车搅拌,注意锅内温度。
3)如果超过115度,紧急放料与事故池。
4)一旦管路阀门堵塞,用低压蒸汽吹扫,严禁用铁器敲打。
5)操作人员中毒立即撤离现场,送医救治。
6)发生火灾时应立即组织扑救,按事预案进行,并打报警电话119o 7)硝化锅维修时,要彻底洗净内残存物,管线加盲板,电源切断后,方可进行维修。
5.2精制、造粒、包装工序。
5.2.1可能发生的不正常现象5.2.2紧急情况的处理1)如遇停水停电,应立即停止搅拌,并及时与负责指导的有关部门联系。
2)一旦管线堵塞,用低压蒸气吹扫,严禁用铁器敲打。
3)操作人员中毒后,立即脱离现场,送医院观察治疗。
4)发生火灾时立即组织扑救,按时雇员进行,并打报警电话119。
5)设备维修时,要彻底洗净设备内残余物管线加盲板,电源切断后,方可进行维修。
5.3萃取工序5.3.1可能发生的不正常现象5.3.2紧急情况的处理1)如遇停水停电,应立即停止搅拌,并及时与负责指导的有关部门联系。
2) 2)一旦管线堵塞,用低压蒸气吹扫,严禁用铁器敲打。
3)操作人员中毒后,立即脱离现场,送医院观察治疗。
4)发生火灾时立即组织扑救,按时雇员进行,并打报警电话1195)设备维修时,要彻底洗净设备内残余物管线加盲板,电源切断后,方可进行维修。
六、操作条件一览表6.1硝化工序条件a.投硫酸量(L/批):1680b.投硝酸量(L/批):634c.投硝基苯量(L/ftt) : 1500e.硝基苯加料速度(L/h) : 220f.硝化温度(摄氏度):30-80g•硝化时间(h) :6h.保温时间(h) :0.5i.保温温度(摄氏度):90±2j.加稀释水量(L): 480-545k.稀释水温度(摄氏度):80-95l.预警温度(摄氏度):100m.报警温度(摄氏度):1156.2精制工艺条件6.2.1中和工艺条件a.加碱量(L) : 545-682b.中和温度(摄氏度):80c中和时间(min) : 30d中和PH值:6-76.2.2精制工艺条件a.加亚硫酸钠量(L) : 1910-1977b.加亚硫酸钠的温度(摄氏度):80c.精制温度(摄氏度):70-75d.精制时间(min) : 90-110e.静止时间(min) : 30f.放母液温度(摄氏度):90-856.2.3造粒工艺条件a.造粒温度(摄氏度):95-78b.造粒时间(min) : 20-30c.放料温度(摄氏度):W606.3萃取工艺条件a.加废酸量(L/批):硝化废酸b.加硝基苯量(L/批):1500c.加料速度(L/h):400d.萃取温度(摄氏度):95-78e.萃取时间(h) : 4f.保温时间(h) : 0.5g.保温温度(摄氏度):40 ±0.5h.静止时间(h) : 16.4抽滤a.抽滤时间(min) : 60-90b.真空度(mpa):W-0.04七、三废排放八、每吨成品的消耗定彳三废名称组成排放量一级排放标准处理方法1.3t/t排放母液废水邻、对硝基苯,磺酸钠、硫酸钠硝烟NO-N2O3混合物10kg/t水吸收排放硝化废酸H2SO465-70% 1.67t/t浓缩回收序号原料名称规格消耗定额理论实际1苯99.9%584.32硫酸98%1962.83硝酸98%965.64碱30%1505亚硫酸钠96%2596副产硫酸副产硫酸68 2.608.2动力序号名称单位消耗定额备注1水t/t成品10P^0.2mpa2电Kwh/t成品1803汽t/t成品 2.8D0.4mpa4汽水t/t成品30九、安全生产的基本守则9.1所有与生产有关的人员必选掌握工艺规程,技术安全防火通则, 经岗位培训考试合格后,方能上岗工作。
9.2上岗前,按岗位规程穿戴好劳保护具。
9.3原料硝基苯,产品间二硝基苯均属易燃、易爆、有毒物质,操作者班前班后6小时内,严禁饮酒,否则易产生中毒现象。
9.4管道阀门堵塞时,应用低压蒸汽吹扫干净,严禁用钝器敲击堵塞部位。
9.5操作者必须坚持岗位,操作中执行巡回检查制度,由不安全隐患及时处理及时汇报。
9.6发生着火时,必须立即组织扑救,并打火警电话:1199.7工房内严格控制硝基苯浓度5mg/m3,二硝基苯浓度小于lmg/m\9.8生产的产品必须及时运到指定地点储存,车间最多存量3吨。