射出成型机の知识
射出成型简介

射出成型简介1 射出成形之基本知识。
1.1 射出成形的特征以及组成。
射出成形是将溶融的成形材料以高压的方式填充到封闭的模具内,射出成形的模腔内承受的压力约400KGF/CM2,大约为400个大气压,以这样高的压力来制作产品是它的特征,这是它的优点也是它的缺点。
也就是说模具必须制作得相当坚固,因而模具价格也相当昂贵,因此必须大量生产以便与高价的模具费用互相扣抵,例如每批之生产量必须10000PCS以上才合理,换句话说;射出成形的工作必须以大量生产才行。
成型过程所说几个步骤:1.1.1关门安全门上才开始成型。
1.1.2 锁模将移动侧的移动板前进,使得模具关闭,模具关闭以后确实地把模具锁紧。
1.1.3 射出(包括保压)螺杆快速地往前推进,把熔融之成形材料注入模腔内填充成形,填充之后压力要必须继续保持,这个动作特别取名为“保压”。
在刚充填时模具承受的压力,一般叫做射出压或者叫做“一次压”。
1.1.4 冷却(以及下个动作的可塑化工程)模腔内之成形材料等待冷却凝固之过程叫“冷却”。
在这时候射出装置也准备下次工作,这个过程叫做“可塑化过程”。
放在料斗里的成形材料,流入加热的料管内加热,是依据螺杆旋转把原料变成熔融状态,螺杆像拨取螺丝的原理一样,一面转一面后退,螺杆前端会储存熔融之成形材料,螺杆旋转时,抵抗螺杆向后退的压力称之为螺杆的“背压”。
1.1.5 打开模具将移动侧的移动板向后退,模具跟着打开。
1.1.6 打开安全门安全门打开,这时成形机处于待机中之状能。
1.1.7 取件将成品取出,然后检视确认模具内未残留任何对象再关门.以上整个成形作业叫做一个CYCLE成型。
成品是由模具的形状成形出来。
模具是由母模及公模块合成,公母模模仁之间留有空隙,材料在此流入压缩形成产品。
成型材料要流入公母模之前的通路有主流道(SPRUE)流道(RUNNER)闸门(GATE)等。
1.2 射出成形机射出成形机以较大项目来区分,可分为两项,锁模装置和射出装置。
精密射出成型

精密射出成型乃是传统射出成型但是要求产品之高精密度。
一、射出成型各阶段之基本原理与物理现象:﹝1﹞射出成型以模具的机械动作可分为锁模阶段、充填阶段、保压阶段、冷却阶段及开模顶出五个阶段,如图1-1所示;但以熔胶在模具的流动至开模为止,则可分为充填、保压及冷却三个过程。
图1-1模具机械动作阶段图﹝2﹞在充填过程中时射出成形机的螺杆向前运动将熔胶经由浇口,流道压入模穴内。
由于熔融树脂具有高度黏性,为,同时熔胶也必须维持有压力梯度。
熔胶的黏度随时间、剪变率而改变,因此在模腔内各点的压力随着时间位置在变化。
在整个过程中,模穴壁上的压力随时间的变化大致如图1-2所示。
图1-2模穴压力在射出成周期的变化。
﹝1﹞充填阶段﹝2﹞压料(packing) ﹝3﹞冷却阶段在充填阶段﹝1﹞压力主要是来克服熔胶在模穴内流动的阻力,当模穴充填完后由于熔胶的可压缩性以及其后冷却的收缩,为了补偿这个收缩效应,在保压阶段﹝2﹞保压压力将熔胶继续压挤入模穴直浇口凝固。
尔后熔胶一直冷却至表面固化到某一程度成品才被顶出。
充填阶段时,当熔胶流入模穴时与冷的腔壁接触,会形成薄的凝层,靠近壁上的熔胶温度会降低,在熔胶流动的峰前,由于喷流效应( Fountain Flow Effect ) 熔胶从中心往两模腔壁流动造成等速的熔胶流动,同时热熔胶从中心带至前缘及两边模腔壁。
在熔峰后端之熔胶则是层状流动,在中心的流动速度最大,而凝固层边的流速为零。
如图1-3所示。
图1-3充填过程中熔胶流动方向剖面流速分布图。
熔胶流峰显示喷流效应(Fountain FlowEffect)同理靠近模穴处温度较低而肉厚中央熔胶仍然保持高温,有时由于黏度生热﹝Viscous Heating﹞的效应﹝与射速有关﹞在较近模穴的地方会产生高温,这种现象在浇口尤其显着( 图1-4 )。
由于熔胶是非牛顿流体,黏度呈现剪薄(Shear Thinning ﹞效应随着温度、剪切率而改变,因此在充填过程中,压力、速度、温度,以及扮随的黏度、剪切率在流动方向以及肉厚方向均有很大的变化,对于成型及成品品质会有很大的影响。
射出机介绍

18
六.射出機規格表
t ¨ Î ² O § µ ¶ Ø ¥ ê Â Ò ¼ O ¤ unit ³ Á Û ± ì ± ½ ª | ® mm ù ¬  û ® g ¥ X À £ ¤ O kg/cm2 | ¬ ¥ û ® g ¥ X À £ ¤ O kg/cm2 z ½ ² × ® g ¥ X ® e ¿ n cm3 g g ® X ¥ « q ¶ oz ù  û ¬ g ® X ¥ v ² cm3/sec | ¬ ¥ û ® g ¥ X ² v cm3/sec i ¶ ¥ ì ¤ Æ ¯ à ¤ O kg/hr ³ ± Á Û ± ì ° j Â à ¼ Æ rpm } ¼ ¶ Ò ¦ æ µ { mm W ¤ ¬ º ¶ ¡ ¹ j (H*V) mm Ò ª ¼ O ¤ Ø o ¤ mm Ò « ¼ p d ½ ³ ò mm o £ ª À ¦ « ¼ Ò ¦ æ µ { mm ¹ ® q ð ° ¨ ¹ F (À ° ® ú ) hp q ¼ ¹ ö ® e ¶ q kw ° ® À ú ³ Ì ° ª ¨ Ï ¥ Î À £ ¤ O kg/cm2 ÷ ± ¾ ñ ¤ Ø ¤ o m ÷ ± ¾ ñ « ¶ q ton Ë ½ ¸ c ¤ Ø ¤ o m Ë ½ ¸ c « ¶ q ton HC-250 250
要研究成形技術及其管理,如不能對所謂成形三要素的--原科、成 形及模具加以一番的探討,必難一登殿堂 15
五.射出工程條件控制
影響射出成型品質的射出工程可分為3階段 A.填充:將原料射出/擠壓到模穴內,將之填充。 B.保壓:為彌補模穴內原料冷卻固化(反應固化)所 導致的體積收縮,而保持的壓力。
C.冷卻:模穴內原料進一步冷卻,固化到成型工 件可從模具內取出。
射出成型的介绍(一)

一、射出成型机的认识介绍
第一章
一、射出成型的特征: 射出成型是把成型材料以主压方式充填到模具腔内,射出
成型的模具腔内承受之压力约400KG.F/CM2大约为400个大气压。 以这样高的压力来制作产品,是射出成型的特征,这是它
的优点,也是它的缺点,也就是部模具必须制作得相当坚固,困而 模具价格也相当昂贵,因此必须多量生产,以便于高价之模具费用, 互相扣抵,换句话说,射出成型之工作,必须大量生产才行。 二、射出成型的过程(一个CYCLE循环)
OFF,ON—OFF……7~8次,听到马达转换为Y之声音后,启动马达之动作,便完成。 12、启动后,让PUMP(泵)空转约3~5分钟后再浪各油路动作。 13、启动后,马达的声需费1小时的时间),成型机才能达
到安定的状态,生产出来的产品品质才会稳定。
整个射出成型的循环中时间内容可分为三大部分: 1、射出时间 2、静止时间 3、开关模时间
第二章 一、塑胶射出成型机的分类:
1、依射出量来区分 2、依锁模力来区分 3、依锁模方式来区分 二、塑胶射出成型机旬部的构造分为: 1、锁模装置单元 2、射出装置单元 3、机座装置单元 三、塑胶射出成型机各部位名称及功能:
1、操作控制箱 功能:是各种开启开关及操作开关。如:装模手动、半自动、全自动、顶
出、射出座前、退油压中子,等开关。 2、成型条件调整控制盘 功能:是调整压力、速度行程、料量、时间等射出成型条件。 3、侦(监)测器 功能:可以由侦监测器查出机器的异常点及高定时间功能。 4、温度高定控制器 功能:是调整料管温度,控制料管温度、各段料管温度、灌嘴(NOZZLE)
温度分开单独设定,调整、控制。
5、锁模单元: 功能: 将模具关闭、打开的作用。 6、顶出油压单元 功能: 系模具打开后,将产品由模具内顶出来,以利人手去取拿,或自行落下,
注塑培训射出成型机於高分子加工简介.ppt

經換算為射出時間最好在1秒以內。
EX: D=40mm, L=0.6*S=2.4D=96mm, t=1sec,
螺桿速度多段控制的影響—波前速度
螺桿等速度
螺桿速度多段控制
滯流區
螺桿速度多段控制的影響—壓力
螺桿等速度(87.8MPa) 螺桿速度多段控制(57.9MPa)
充填速度適當的調控,將可有效降低射出壓力
螺桿速度多段控制的影響—合模力
88ton
62ton
螺桿等速度
螺桿速度多段控制
充填速度適當的調控,將可有效降低合模力
(2)合模裝置的構造區主要區分為肘節式及直壓式
頂出機構
二、射出成形步驟原理
加熱熔化 加壓流動 壓縮及續壓
塑料
熔膠
成形
冷卻固化 開模頂出 成品
螺桿轉速 料缸溫度 噴嘴溫度 螺桿背壓
充填速度 充填壓力上限 充填時間 進料位置、 充填/保壓轉換位置 殘留量 保壓壓力(二段壓) 保壓時間
模具溫度 冷卻時間 開關模速度 頂出速度 頂出量
各塑膠ρ值、μ值
塑膠名稱 PS PE PP ABS AS
NYLON PC
PMMA H.PVC NORYL PBT POM
ρ值 0.98 0.73 0.75 0.92 0.99 1.01 1.06 1.06 1.00 0.9 1.02 1.17
μ值 92% 95% 95% 88% 90% 90% 85% 86% 83% 85% 90% 88%
较全面塑胶模具成型射出基础知识

塑胶射出基础知识一、射出成型原理中有几个要先注意且重要的观念。
二、射出成型机参数的意义。
三、成型条件设定的程序。
四、你有一个新模子,怎样选择适合的成型机?五、你怎样观察生产中的条件是否稳定?六、补充资料1一.射出成型原理中有几个特别注意且重要的观念。
➢材料在模具中流动的●像岩浆一样的流动●硬化层●越小越薄的通道越难进入●射出机压力与模内压力分开思考2二.射出成型的参数意义1.射出压:又称“一次压”,指成品充填时所需之压力,操作时是指开始射出到产品的充填至95%时所用之压力。
2.保压:又称“二次压”,指充填完毕后,持续之压力。
操作上是指成品最后5%~10%充填完毕后一直维持到浇口凝固后所需之压力。
3.充填时间(一次压时间):开始射出到切换保压间的时间。
位置切换设定时,压力、速度、材料流动性、模具构造等所匹配自然产生的时间,一般可从射出机查出。
也可以直接设定。
4.保压时间(二次压时间):依材料凝固速度、成品、浇口大小、冷却速3率而决定,由操作者输入。
理论上可用浇口凝固测量(GATE SEAL)得知,但一般都用经验值。
5.最大射出压力:射出机在射胶时泵可出之最大压力。
6.理论射出容量:一次最多可射出之容积。
7.可塑化能力:单位时间内可熔融多少材料的能力。
8.射出率:单位时间内最多可射出容积的能力。
9.背压:射出机螺杆计量时,油压缸对应于螺杆自动后退的阻力,当背压愈大时,塑料密度愈高,不容易有气泡,但太大则螺杆不能后退,无法完成计量程序。
反之,螺杆后退快,但塑料密度松,易产生气泡。
4三.成形条件的设定程序1了解材料之限制条件(料温、流动性、压力、速度之需求…)2了解模具之限制条件(作动、耐压强度…)3了解成品之限制条件(不饱模是否会黏模、重量大小…)4确认材料干燥条件(温度、时间)是否达到。
5预估成品料量、设定计量。
6依材料特性及模具成品的状况,设定一次压、速度。
7保压设定为零(或极低值)。
8开始射出、观察充填状况。
射出成型机操作知识
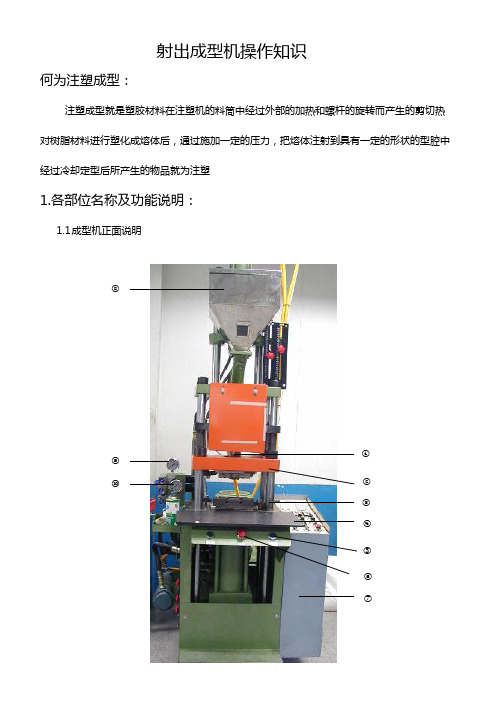
射出成型机操作知识何为注塑成型:注塑成型就是塑胶材料在注塑机的料筒中经过外部的加热和螺杆的旋转而产生的剪切热对树脂材料进行塑化成熔体后,通过施加一定的压力,把熔体注射到具有一定的形状的型腔中经过冷却定型后所产生的物品就为注塑1.各部位名称及功能说明:1.1成型机正面说明料管 上模板●立柱❍工作台⏹自动☐紧急回升☐电箱❑料斗❒油压表♦压力表1.2电控板说明:a.成型计数b.料嘴温度c.射退计时d.松退计时e.电热开关f.开模/关模 g.手动/自动 h.马达激活 i.马达停止 j. 射退/射出k.洗料/螺旋 l.顶针使用 m.松退使用 n.顶针开关 o.电源开关p.冷却计时 q.上节温度表2.模具安装:2.1打开电源,电热开关,调整内模或外模在作业规范中所设定的温度。
2.2待达升至所设定的温度后,按动马达,将总压力调至用手动能开模,关模为合适。
2.3把模具放至机台,用手动关模,射料,检查机器料管射料口是否对正模具进料口。
2.4手动关模,锁紧上下模板。
2.5装模完成。
2.6待机器调整程序完成后方可自动作业。
注意:在安装模具时要特别注意安全,非熟练装模人员或技术人员不得擅自安装。
3.调整机器3.1模具装好后,不能立即转自动操作,须调整机器的各个控制动作开关。
3.2调整总压,一次压,二次压设定适当的压力。
3.3调整开模慢速控制轮,强力锁模控制轮,开模停止控制轮。
特别注意,开模慢速控制一定要调至适当的位置,如关模无慢速,自动操作时易把模具压裂。
3.4根据内、外模穴的大小,调整加料停止控制轮与射二次压控制轮。
3.5调整射出速度与背压至合适为止。
3.6以上工序完成后,进入操作阶段。
注意:调整机器由专业技术人员调整,其它不熟练的人员不得自行调整,操作员若发现有不良现象立即停机,请专业人员调整之。
4.操作方法:4.1将手动/自动开关转为手动,开始旋料(加料)至自动停止为止。
4.2再把开关转为自动,进行试模。
4.3试机二,三模后,准备作业。
射出成形基础(1)

塑料的流动黏度
有一个理论说塑料的黏度决定 于分子链的纠缠程度,纠缠的 程度越少,黏度就越低,反之 亦然;而塑料本身的分子量大 小,分子结构以及外在的加工 温度,流动切断力(使分子链 配向)和受压缩的程度等都会 影响它的纠缠,此既影响塑料 黏度之因素。
充填三阶段: 1.射出相→熔融的塑料 被快速射入模腔,刚
是自注道至成形品之通路,通常设在合模线两侧,浇道的剖面通常是圆形。多模 穴模具的成形品与浇道配置很重要,应使流进各模穴的成形材料同步而均匀。
冷料井(cold slug well)
射出成形机的喷嘴前端在射出后仍有少量熔融材料残留,此残留材料在下次射 出前凝固,若直接进入成形品中会造成制品外观不良,为了防止如此设计冷料井, 使射出 材料前端的凝块积滞此处。
射出成形之重点
工 流 重 点 §心层不会立即冷却,模具的每一角落都有高压力。 射出 §需要保压,成形品的尺寸和凹塌决定于这时段。 后期 §射出压、保压是关键(瞬间施高压,立即降压保 (填充 持)。 及 §模具温度很重要(应高一点)。 保压) §模具内树脂压力的实际变化很重要(需测定)。 §为使心层冷却固化,要冷却模具。 冷 §对模具高速循环冷却水。 §关键是冷却水、速度、温度。 却 §模具温度偏差应尽量少(需测定)。 §由树脂来的热移动很重要。 程
7
开关模
5
向后松退,避免塑料从喷嘴漏出。 塑件冷却定形,同时注射螺杆完成射料
6
6 冷却时间
准备。
滑动模板后退,两半边模打开。退件机 构将塑件顶出。
5 4
7
清除塑件,喷脱模剂,安装嵌件、插针
等。模具重新闭合,下一循环开始。
8
结晶性材料 成型收缩率 较大 。
非结晶性材 料成型收缩 率较小。
- 1、下载文档前请自行甄别文档内容的完整性,平台不提供额外的编辑、内容补充、找答案等附加服务。
- 2、"仅部分预览"的文档,不可在线预览部分如存在完整性等问题,可反馈申请退款(可完整预览的文档不适用该条件!)。
- 3、如文档侵犯您的权益,请联系客服反馈,我们会尽快为您处理(人工客服工作时间:9:00-18:30)。
1.射出成形とは射出成形(Injection Molding)とは、加熱溶融させた材料を金型内に射出注入し、冷却・固化させる事によって、成形品を得る方法です。
複雑な形状の製品を大量に生産するのに適し、成形加工の一大分野をなしています。
射出成形の工程は大きく分けて、6つあります。
1.型締め(合模)2.射出3.保圧4.冷却5.型開き(开模)6.製品の取出しの順序で行われ、このサイクルの繰り返しで、製品を連続的に生産できます。
2.射出成形機射出成形機は型締ユニットと射出ユニットに分かれています。
型締ユニットは金型の開閉、突き出し(エジェクター)を行い、図のようなトグル式(连杆式)と、油圧シリンダー(机筒)で直接金型を開閉する直圧式とがあります。
射出ユニットは樹脂を加熱溶融させ、金型内へ射出します。
スクリュー(螺杆)を回転させ、図のようにホッパー(料斗)から投入した樹脂を、スクリュー前部へ溜め(計量と呼びます)、必要樹脂量に相当するストローク(击打)溜めた後、射出します。
樹脂が金型内を流動している時は、スクリューの移動速度(射出速度)を制御し、樹脂が充填された後は圧力(保圧力)で制御します。
速度制御から圧力制御への切換えは、一定のスクリュー位置や一定の射出圧力に達した時に切換わるよう設定します。
タイバー拉杆クロスヘッド直角解套エジェクター脱模机构シリンダー(机筒)ホッパー(料斗)スクリュー(螺杆)実際の動きを観てみたい場合はここをクリックしてください⇒3.金型金型(Mold)とは、材料樹脂をある決まった形状にするため、樹脂を射出注入する金属製の型です。
図には記していませんが、実際には幾つかの孔が空いており、温水や油、ヒーター等で温度管理されています。
溶融した材料はスプルー(注射塑模内主流道)から金型内に入り、ランナー(分流道)・ゲート(浇口)を経てキャビティ(前模)内に充填されます。
その後、冷却工程を経て、金型が開き成形機のエジェクタロッド(顶出杆)に金型のエジェクタプレート(顶板)が押されて成形品が突き出されます。
エジェクターピン(顶针)キャビティ(前模,模腔)エジェクタロッド(喷射器杆)エジェクタプレート(顶板)スプルー(注射塑模内主流道)ランナー(分流道)・ゲート(阀门)実際の動きを観てみたい場合はここをクリックしてください⇒4.成形品成形品は、溶融樹脂が流れ込むスプルー、キャビティ(模腔)へ導くランナーと製品部分から成っています。
1回の成形で製品が1つしか得られないのは効率が悪いので、複数のキャビティがランナーで結ばれ、通常複数個が同時に成形できるようになっています。
その時、各キャビティでランナーの長さが異なると、樹脂が同時に充填されず、キャビティ間で寸法や外観、物性が異なることが多くあるため、通常同じ長さのランナーに設計します。
5.再生材(回料)の使用成形品のうちスプルーとランナーは、製品ではありません。
この部分は、廃棄される場合もありますし、細かく砕かれて再び成形用の材料として再利用される事もあります。
これを一般に再生材と呼んでいます。
再生材は、単独で成形用の材料として使用される訳ではなく、通常のペレット(新料)に配合して使用されます。
これは、一度成形の工程を経ているため、樹脂の様々な特性が変化している可能性があるためです。
再生材の配合割合は30%程度が上限です。
あまり配合割合が高いと、樹脂本来の性質が損なわれてしまう可能性があるためです。
再生材を使用した場合の、特性は樹脂データベースの再生特性をご覧ください。
ジュラコンの再生特性を見る⇒6.成形条件成形条件とは、必要とする成形品を得るために設定する成形機のシリンダー(料筒)温度や射出速度、金型温度などのことで、その組合わせは無数にあります。
その条件によっては得られる成形品の外観や寸法、機械的物性等が変化するため、最適な成形条件を出すのには習熟した技術と経験が必要です。
当社材料の標準的な成形条件をご紹介します。
下の樹脂名をクリックしてください成形機用語:(あ行)圧縮成形アニーリング(退火)アフタキュア(后固化,后硫化)アンダカット(下切,咬边)インジェクション(注射)ブロ-成形インフレーション法(吹塑法) ウェルドマーク(焊接痕) 押出機(か行)ガイドピン(定位销)ガイドブッシュ(导环)型締時間型締力型内圧力型開き力可動盤金型加熱シリンダ(加热机筒)キャビティ(模腔)強化プラスチックき裂(龟裂)ゲート(浇口)硬化硬化剤合成樹脂固化固定盤コールドスラグ(冷块)コンパウンド(复合物)(さ行)射出圧力射出成形射出成形機射出速度収縮充てん剤条こんショットシリコーンゴムスクリュスプルスプルブッシュ成形成形圧力成形温度成形サイクル積層成形(た行)ダイタイバタイバ間隔ダイプレート多数個取り金型突き出しデイライトトグル式型締機構トランスファ成形(な行)ノズルノズルタッチ熱可塑性エラストマー(は行)背圧発泡成形パーティングラインバリピンホールBMCフェノール樹脂ブッシュプランジャブロー成形ベント式(ら行)リブLIM射出成形不良発生時の対策ガイド不良現象原因対策シルバーストリークス成型品表面に樹脂の流動方向に沿って生成する銀条痕で、これは成型品表面をガスが走った跡である成形条件シリンダー温度が高いノズル温度が高い射出速度が速い可塑化工程で空気の巻き込みがある成形サイクルが長く、シリンダー内での樹脂の滞留が長いシリンダー温度を下げるノズル温度を下げる射出速度をおそくするスクリュー回転数を下げる背圧をかける(10_20Kgf/c_-G)ホッパー側のシリンダー温度を高くする可能な限りシリンダー温度を下げる容量の小さい射出成形機で成形する金型金型のガス抜きが不充分金型にガス抜きをつける製品設計ゲートが小さいため摩擦発熱があるゲートを大きくする樹脂材料の粒形が小さい材料中の水分率が高い粒状の小さな材料(特に粉砕品)を混入しない材料の予備乾燥を充分に行う(0.1%以下にする)フローマークゲートを中心に発生する細かい円弧状の波紋成形条件金型温度が低い成形温度が低い射出速度がおそい金型温度を高くするシリンダー温度を高くする射出速度をはやくする製品設計ゲート数が少ないゲートが小さいランナーが小さいゲート数を増やすゲートを大きくするランナーを大きくする樹脂流動性が足りない流動性の良いグレードを使用す(グレード選定の不適切)るヒケキャビティに充填された樹脂が冷却の不均一により体積の収縮差を生じ、表面がくぼんだ状態となる成形条件成形温度が高い金型温度の高すぎ又は低すぎ射出・保持圧力が低い射出・保持時間が短い冷却時間が不足しているクッションがないシリンダー温度を下げる金型温度を適正にする射出・保持圧力を上げる射出・保持時間を長くする冷却時間を充分とるクッションを5mm_10mmとる製品設計ランナー、ゲートが小さいゲート位置の不良ランナー、ゲートを大きくする内厚に変化のある成型品の場合、ゲートを肉厚部につける成形機逆流防止がなされていない逆流防止機構をつけるそり平板状成型品に見られる凸状変形、凹状変形またはねじれ変形。
箱状製品で壁がコア側に張り出してくる変形。
充填された樹脂の不均一収縮による成形機射出圧力が低く、射出速度がおそい射出・保圧時間が短い冷却時間が短い矯正治具を用いていないコア、キャビティの金型温度格差が大射出圧力を高く、射出速度を早くする射出・保圧時間を長くする冷却時間を長くする射出成形後、治具を用いて変形を防止する金型温調機で、コア、キャビティを別個に制御する金型成型品の突き出しがアンバランスノックアウトピンの面積が小さい離型が悪い突き出しのバランスをとるノックアウトピンの面積を大きくするテーパーを充分とる。
離型剤を塗布する。
製品設計ゲート位置の不良成型品の肉厚変動が大きい広い成形面積にゲートが1ケしかないゲート位置を変更成型品の肉厚が均一になるように設計変更する多点ゲートを設けるショートショット金型内への樹脂の充填不足状態、成型品末端部にあらわれる成形条件成形温度が低い金型温度が低い射出速度がおそいシリンダー温度を上げる金型温度を上げる射出速度を速くするさざ波状のしわもショートショットの一種である射出圧力が低いクッションがゼロ(樹脂供給が不足)射出圧力を上げるクッションをとる(5_10mm)製品設計スプルー、ランナー、ゲートの断面積が小さいスプルー、ランナー、ゲートの断面積を大きくする樹脂樹脂の流動性不足(グレード選定の不適切)良流動性のグレードに変えるクレーズまたはクラック成型品の表面に発生する細い線状のひびまたは割れ成形条件金型温度が低い射出速度がはやい射出・保持圧力が高い型締圧力が不足冷却時間が短い樹脂のオーバーパッキング金型温度を上げる射出速度をおそくする射出・保持圧力を下げる型締圧力を充分とる冷却時間を長くするオーバーパッキングしない金型離型不良テーパーを充分とる。
離型剤を塗布する。
ばり金型の接合部に樹脂がはみ出して固化する現象成形条件シリンダー温度が高い射出速度がはやい射出、保持圧力が高い型締圧力が不足樹脂のフィード量が多いシリンダー温度を下げる射出速度をおそくする射出、保持圧力を下げる型締圧力を上げるフィード量を適正にする(クッション量5mm程度にする)金型金型の合わせ面が平滑でない金型を修正する樹脂樹脂の流動性が良すぎる樹脂グレードを変更する(流動性の良さを下げる適切なグレードの選定)色調不良本来の無色透明性を失い、成型品が黄色化または黒色化する現象成形条件シリンダー温度が高いスクリュー回転数が大きい背圧をかけていない樹脂のシリンダー滞留時間が長いシリンダー温度を下げるスクリュー回転数を下げる背圧をかける(10_20Kgf/c_-G)できる限り滞留時間を短くしシリンダー温度を下げる成形機シリンダー、またはノズルに樹脂が滞留する部分がある滞留のない構造にする管理樹脂ペレットを乾燥する際、乾燥空気によって汚染されている乾燥機の空気吸込口にフィルターを設ける(フィルターとしては例えばガーゼ、発泡ウレタンなどがよい)光沢不良成形条件成形温度が低い金型温度が低いガスの発生射出速度がおそい射出、保持圧力が低い樹脂の充量不足シリンダー温度を上げる金型温度を上げるシリンダー温度を下げる。
背圧をかける(10_20Kgf/c_-G)射出速度をはやくする射出、圧力を上げる樹脂の充填量を調節する金型金型のガス抜きが悪い金型のガス抜きを充分とる管理金型キャビティ面へのオイル類の付着金型キャビティ面に錆がついたり傷がついたりしているキャビティ面をクリーニングするキャビティ面を磨き、メッキをかける黒条・焼け成型品の一部が過熱により変色する現象で、これは空気が高温で急圧縮されるために樹脂が焼けるものである成形条件シリンダー温度が高い可塑化工程でのエアの巻き込み射出圧力・射出速度が大きい滞留時間が長いシリンダー温度を下げるスクリュー回転数を下げる背圧をかける(10_20Kgf/c_-G)射出圧力・射出速度を小さくするまたは、ゲートを大きくするシリンダー温度を下げる成形サイクルを短くする容量の小さな射出成形機で成形する金型金型のガス抜きが悪い金型にガス抜きをつける製品設計ゲート位置が不良ゲートが小さいため摩擦発熱があるゲート位置を変更する(ウェルドがパーティングの方に集まるように)ゲートサイズを大きくする成形機シリンダーまたはノズルに樹脂が滞留する部分がある滞留のない構造にする気泡 成型品厚肉部にみられる真空泡、あるいは残存モノマー、水、空気の膨張による気泡 成形条件 成形温度が高い 金型温度が低い(成型品の厚肉中心部の冷却に伴う体積収縮) 可塑化工程での空気の巻き込み 射出・保圧時間が短い 射出・保持圧力が低い クッションがないシリンダー温度を下げる 金型温度を上げるスクリュー回転数を下げる 背圧をかける(10_20Kgf/c_-G ) ホッパー側のシリンダー温度を高くする射出・保圧時間は少なくともゲートシール時間以上とる射出・保持圧力を高くするクッションをゲートシール時で5_10mm に設定する製品設計 ランナー、ゲートが小さい(体積収縮に見合う樹脂が充填されない)ランナー、ゲートを大きくする成形機 逆流防止がされていないノズル径が小さい。