表面强化技术 PPT
合集下载
表面形变强化技术

奥赫弗尔特理论
• 奥赫弗尔特认为,喷丸的残余应力的产生 取决于两个方面的机制: • 一方面由于大量弹丸压人产生的切应力造 成了表面塑性延伸; • 另一方面,由于弹丸的冲击产生的表面法 向力引起了赫芝压应力与亚表面应力的结 合。 • 在大多数材料中这两种机制并存。
喷丸产生的残余压应力
• 经喷丸和滚压 后,金属表面产生 的残余压应力的大 小,不但与强化方 法、工艺参数有关, 还与材料的晶体类 型、强度水平以及 材料在单调拉伸时 的硬化率有关。
• 这种表面形貌和表层组织结构产生的变化,有效 地提高了金属表面强度、耐应力腐蚀性能和疲劳 强度。
二、表面形变强化的主要方法及应用
• (一)表面形变强化的 主要方法 • 1.滚压 • 目前,滚压强化用的滚 轮、滚压力大小等尚无 标准。 • 对于圆角、沟槽等可通 过滚压获得表层形变强 化,并能在表面产生约 5mm深的残余压应力, 其分布如图所示。
残余压应力
• 具有高硬化率的面心立方晶体的镍基或铁 基奥氏体热强合金,表面产生的压应力高, 可达材料自身屈服点的2-4倍。
• 材料的硬化率越高,产生的残余压应力越 大。
表面强化方法
有效地提高了金属表面强度、耐应力腐蚀性能和疲劳强度。
• 表面强化方法还可消除切削加工留下的刀痕; • 表面形变强化手段还可能使表面粗糙度略有增 加,但却使切削加工的尖锐刀痕圆滑,因此可减 轻由切削加工留下的尖锐刀痕的不利影响。
喷丸强度
• 当弧高度f达到饱和值,试片表面达到全覆 盖率时,以此弧高度f定义为喷九强度。 • 喷丸强度的表示方法是0.25C或fc=0.25, 字母或脚码代表试片种类,数字表示弧高 度值(单位为mm)。
(2)表面覆盖率试验
• 喷丸强化后表面弹丸坑占有的面积与总面 积的比值称为表面覆盖率。 • 一般认为,喷丸强化零件要求表面覆盖率 达到表面积的100%即全面覆盖时,才能有 效地改善疲劳性能和抗应力腐蚀性能。
第七章 表面形变强化技术

渗碳钢经喷丸后的残余压应力
• 常用的渗碳钢经喷丸后,表层的残留奥 氏体有相当大的一部分将转变成马氏体, 因相变时体积膨胀而产生压应力,从而 使得表层残余应力场向着更大的压应力 方向变化。
• 在相同喷丸压力下: • 大直径弹丸喷丸后的压应力较低,压应 力层较深; • 小直径弹丸喷丸后表面压应力较高,压 应力层较浅,且压应力值随深度下降很 快。 • 对于表面有凹坑、凸台。划痕等缺陷或 表面脱碳的工件,通常选用较大的弹丸, 以获得较深的压应力层,使表面缺陷造 成的应力集中减小到最低程度。
喷丸产生的残余压应力
• 经喷丸和滚压 后,金属表面产生 的残余压应力的大 小,不但与强化方 法、工艺参数有关, 还与材料的晶体类 型、强度水平以及 材料在单调拉伸时 的硬化率有关。
残余压应力
• 具有高硬化率的面心立方晶体的镍基或铁 基奥氏体热强合金,表面产生的压应力高, 可达材料自身屈服点的2-4倍。
喷丸强度
• 当弧高度f达到饱和值,试片表面达到全覆 盖率时,以此弧高度f定义为喷九强度。 • 喷丸强度的表示方法是0.25C或fc=0.25, 字母或脚码代表试片种类,数字表示弧高 度值(单位为mm)。
(2)表面覆盖率试验
• 喷丸强化后表面弹丸坑占有的面积与总面 积的比值称为表面覆盖率。 • 一般认为,喷丸强化零件要求表面覆盖率 达到表面积的100%即全面覆盖时,才能有 效地改善疲劳性能和抗应力腐蚀性能。
(4)玻璃弹丸
• 近十几年发展起来的新型喷丸材料, 已在国防工业和飞机制造业中获得广泛应 用。 • 脆性较大 。
(5)陶瓷弹丸
• 弹丸硬度很高,但脆性较大。喷丸后表层 可获得较高的残余应力。
(6)聚合塑料弹丸
• 是一种新型的喷丸介质,以聚合碳酸酯为 原料,颗粒硬而耐磨,无粉尘,不污染环 境,可连续使用,成本低,而且即使有棱 边的新丸也不会损伤工件表面。
钢的表面强化技术
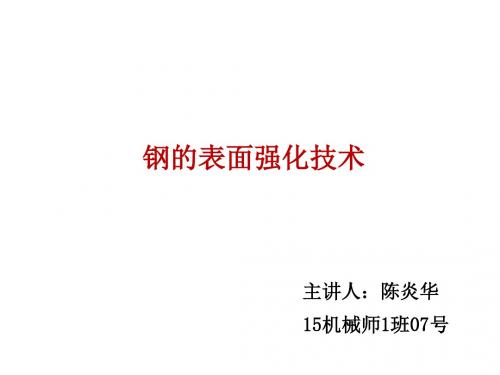
冲裁模的强化部位
1—凸模
2—凹模
电火花强化
• 强化层的性能决定于基体和电极材料,通常所 用的电极材料有TiC、WC、ZrC、NbC、 Cr3C2、硬质合金等,基体材料包括碳钢、合 金钢、铸铁、铸钢等所有的导电体。 • 电火花表面强化因电极材料的沉积发生有规律 地胀大,除此之外工件没有其它变形,工件心 部的组织与性能也不发生变化,因此十分适用 模具的表面处理。
(二)、电火 花表面强化
电火花表面强 化是利用工具 电极与工件间 在气体中产生 的火花放电作 用,把作为电 极的导电材料 溶渗进工件表 层形成合金化 的表面强化层 或对磨损部位 沉积堆焊(修 复)。
电火化表面强化过程示意图
1—工具电极
2—工件
电火花表面强化的设备
• 直流电以每隔10-3~10-1秒的 周期,在10-6~10-5秒的极短 时间内放电,电极材料与工件 的接触部被加热到8000~ 25000℃,并且在等离子冶金 状态下转移到工件表面及形成 合金(Alloying)和堆积 (Deposition),同时向工 件表面扩散(Diffusion)和 渗透(Penetration)从而高 强度密切结合。
• (1)提高钢表面的硬度、耐磨性、耐蚀性和抗高温氧化性能, 大幅度提高模具的使用寿命。
• (2)提高钢表面抗擦伤能力,提高生产率。 • (3)采用碳素工具钢或低合金钢,经表面涂层或合金化处理 后,可达到或超过高合金化材料甚至硬质合金的性能指标, 不仅可大幅度降低材料成本,而且可以简化零件制造的加工 工艺和热处理工艺,降低生产成本。
电火花强化的应用
• 用YG8作电极,对3Cr2W8V钢制模具进行 电火花强化处理后,在各类酸碱中的耐蚀 性提高4~15倍; • 对Cr12钢制定子双槽模刃口部位经电火花 表面强化后,每次刃磨的平均使用寿命由5 万次提高到20万次
表面强化ppt

材料的表面强化
surface strengthening
组员:安
研究目的
材料的失效,如,疲劳、磨 损、腐蚀、氧化、烧损以 及辐射损伤等,一般都是 从表面开始的,表面的局 部损坏又很快造成整个零 件失效,最终导致设备停 产。
表面强化
改善机械零件和构件表面性能、提高疲劳强度 和耐磨性能,提高耐腐蚀性能的工艺方法,又 叫表面处理。
表面机械处理
原理:通过机械手段在金属表面产生压缩变形,使表面形成形变
硬化层,微观是晶粒间产生位错,晶粒变形或破碎——细晶强化。
方法:喷丸,表面锤击,表面滚压,
内挤压,超声冲击。
应用:1.使模具表面产生冷作硬化
磨损性能,从而提高模具使用寿命。
2. 改善模具表面粗糙度 3.提高模具疲劳强度,抗冲击,
• 表面强化的优势
表面,形成表面合金层的工艺。
种类:渗碳,渗氮,碳氮共渗,渗硼,渗金属
越王勾践剑历经2500年未生锈,且吹可断发,原因是什么?
越王勾践剑的主要成分是铜、锡以 及少量的铝、铁、镍、硫组成的青 铜合金。 通过对菱形花纹的成分、结构等进 行分析测试,剑身菱形花纹处含硫 高,推测采用化学方法——硫化 工艺,硫化铜可以防止锈蚀,以保 持花纹的艳丽,千年不锈。
中国在战国时代已经 开始对钢进行淬火。 利用大豆中分解出来 的 N ,C 元素富化烧红的 铁剑表面,以增强其强度 和韧性。 飞机 在飞行, 停飞 中,遇到空气摩擦升温 到200°C,因而飞机蒙 皮的表面涂上高聚物涂 料使其免受环境介质腐 蚀,减少阻力。
表面热处理
• 表面淬火 • 感应加热热处理
• 渗碳、渗氮 表面化学处理 • 渗金属 • 喷丸 表面机械处理 • 和滚压等
• 根据需要,改善材料的表面性能,会有效地延长使用寿命。 • 节约资源,提高生产力,减少环境污染。 • 最大优势是能制备出优于本体材料性能的 表面功能薄层, 其厚度 一般为几微米到几毫米,却使零件具有了更高的耐面技术正在蓬勃发展,
surface strengthening
组员:安
研究目的
材料的失效,如,疲劳、磨 损、腐蚀、氧化、烧损以 及辐射损伤等,一般都是 从表面开始的,表面的局 部损坏又很快造成整个零 件失效,最终导致设备停 产。
表面强化
改善机械零件和构件表面性能、提高疲劳强度 和耐磨性能,提高耐腐蚀性能的工艺方法,又 叫表面处理。
表面机械处理
原理:通过机械手段在金属表面产生压缩变形,使表面形成形变
硬化层,微观是晶粒间产生位错,晶粒变形或破碎——细晶强化。
方法:喷丸,表面锤击,表面滚压,
内挤压,超声冲击。
应用:1.使模具表面产生冷作硬化
磨损性能,从而提高模具使用寿命。
2. 改善模具表面粗糙度 3.提高模具疲劳强度,抗冲击,
• 表面强化的优势
表面,形成表面合金层的工艺。
种类:渗碳,渗氮,碳氮共渗,渗硼,渗金属
越王勾践剑历经2500年未生锈,且吹可断发,原因是什么?
越王勾践剑的主要成分是铜、锡以 及少量的铝、铁、镍、硫组成的青 铜合金。 通过对菱形花纹的成分、结构等进 行分析测试,剑身菱形花纹处含硫 高,推测采用化学方法——硫化 工艺,硫化铜可以防止锈蚀,以保 持花纹的艳丽,千年不锈。
中国在战国时代已经 开始对钢进行淬火。 利用大豆中分解出来 的 N ,C 元素富化烧红的 铁剑表面,以增强其强度 和韧性。 飞机 在飞行, 停飞 中,遇到空气摩擦升温 到200°C,因而飞机蒙 皮的表面涂上高聚物涂 料使其免受环境介质腐 蚀,减少阻力。
表面热处理
• 表面淬火 • 感应加热热处理
• 渗碳、渗氮 表面化学处理 • 渗金属 • 喷丸 表面机械处理 • 和滚压等
• 根据需要,改善材料的表面性能,会有效地延长使用寿命。 • 节约资源,提高生产力,减少环境污染。 • 最大优势是能制备出优于本体材料性能的 表面功能薄层, 其厚度 一般为几微米到几毫米,却使零件具有了更高的耐面技术正在蓬勃发展,
表面强化技术
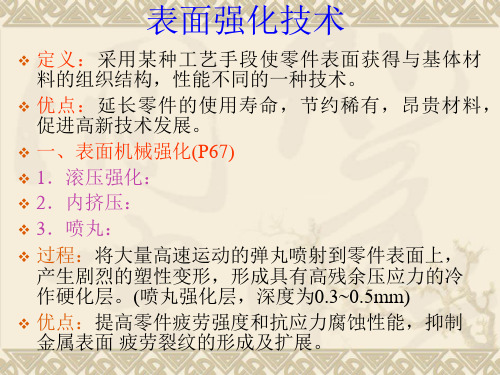
2.激光表面处理原理:激光束向金属表面层进行热传递,金 属表层和其所吸引的激光进行光热转换。由于光子能穿过金属 的能力极低,仅能使金属表面的一薄层温度升高,加之金属导 带电子的平均自由时间只有10-3s左右,因此,这种交换和热平 衡的建立是非常迅速的。从理论上分析,在激光加热过程中, 金属表面极薄层的温度在微秒(10-6s)级,甚至纳秒(10-9s)级或皮 秒(10-12s)级内就能达到相变或熔化温度。 3.激光表面处理设备: 4.激光表面处理技术: (1)激光表面强化 (2)激光表面涂敷 (3)激光表面非晶态处理 (4)激光表面合金化 (5)激光气相沉积
二、表面热处理强化 和表面化学热处理强化
1、表面热处理: 定义:通过对零件表层加热,冷却,表层发生相变,从而改 变表层组织和性能而不改变成分的一种技术,它是最基本、应 用最广泛的表面强化技术之一。 原理:当零件表面层快速加热时,零件截面上的温度分布是 不均匀的,表层温度高而且由表及里逐渐降低。当表面的温度 超过相变点以上达到奥氏体状态时,随后的快冷使表面获得马 氏体组织,而零件的心部仍保留原组织状态,表面得到硬化层, 这样就达到强化零件表面的目的。 常用方法:高频和中频感应加热表面淬火,火焰加热表面淬 火,接触电阻加热表面淬火,浴炉(高温盐浴炉)加热表面淬火 等。以上除接触电阻加热表面淬火外,其它均为常规的热处子束表面相变强化 (2)电子束表面重熔 (3)电子束表面合金化 (4)电子束表面非晶态处理 3.电子束表面处理设备
三、电火花强化P68
定义:通过电火花的放电作用把一种导电材料涂敷熔渗 到另一种导电材料的表面,从而改变后者表面的性能。 (如把硬质合金材料涂到用碳素钢制成的各类刀具、量具 及零件表面,可大幅提高其表面硬度(硬度可达70~74HRC)、 增加耐磨性、耐腐蚀性,提高使用寿命1~2倍。) 适用范围:上述各类零件的表面强化和磨损部位的修补。 原理:在电极与工件之间接直流或交流电,振动器使电 极与工件之间的放电间隙频繁发生变化并不断产生火花放 电,经多次放电并相应移动电极的位置,就使电极材料熔 结覆盖在工件表面上,从而形成强化层。
第十章-模具表面强化技术

(4) 渗氮处理后,工件的变形很小,适合精密模具的表面强化。
*
表面化学热处理技术
二、渗氮(氮化)
(一)气体渗氮
表2 部分模具钢的气体渗氮工艺规范
牌号
处理 方法
渗氮工艺规范
渗氮层 深度/mm
表面硬度
阶段
渗氮温度/℃
时间/h
氨分解率/%
30CrMnSiA
一段
—
500±5
25~30
20~30
0.2~0.3
(一)气体渗氮
(1) 经过渗氮后钢表面形成一层极硬的合金氮化物,渗氮层的硬度一般可达到68~72HRC,不需要再经过淬火便具有很高的表面硬度和耐磨层,而且还可以保持到600~650℃而不明显下降。
(2) 渗氮后钢的疲劳极限可提高15%~35%。这是由于渗氮层的体积增大,使工件表面产生了残余压应力。
(3) 渗氮后的钢具有很高的抗腐蚀能力。
>58HRC
Cr12MoV
760~800HV
*
表面化学热处理技术
二、渗氮(氮化)
(二)离子渗氮
离子渗氮有如下特点:
(1) 渗氮速度快,生产周期短。
(2) 渗氮层质量高。
(3) 工件的变形小。
(4) 对材料的适应性强。
氮碳共渗
提高硬度、耐磨性、抗粘附性、抗蚀性、耐热疲劳性
冷挤模、拉深模、挤压模穿孔针
渗硼
具有极好的表面硬度、耐磨性、抗粘附性、抗氧化性、热硬性、良好的抗蚀性
挤压模、拉深模
碳氮硼三元共渗
提高硬度、强度、耐磨性、耐疲劳性、抗蚀性
挤压模、冲头针尖
盐浴覆层 (TD处理)
提高硬度、耐磨性、耐热疲劳性、抗蚀性、抗粘附性、抗氧化性
*
表面化学热处理技术
二、渗氮(氮化)
(一)气体渗氮
表2 部分模具钢的气体渗氮工艺规范
牌号
处理 方法
渗氮工艺规范
渗氮层 深度/mm
表面硬度
阶段
渗氮温度/℃
时间/h
氨分解率/%
30CrMnSiA
一段
—
500±5
25~30
20~30
0.2~0.3
(一)气体渗氮
(1) 经过渗氮后钢表面形成一层极硬的合金氮化物,渗氮层的硬度一般可达到68~72HRC,不需要再经过淬火便具有很高的表面硬度和耐磨层,而且还可以保持到600~650℃而不明显下降。
(2) 渗氮后钢的疲劳极限可提高15%~35%。这是由于渗氮层的体积增大,使工件表面产生了残余压应力。
(3) 渗氮后的钢具有很高的抗腐蚀能力。
>58HRC
Cr12MoV
760~800HV
*
表面化学热处理技术
二、渗氮(氮化)
(二)离子渗氮
离子渗氮有如下特点:
(1) 渗氮速度快,生产周期短。
(2) 渗氮层质量高。
(3) 工件的变形小。
(4) 对材料的适应性强。
氮碳共渗
提高硬度、耐磨性、抗粘附性、抗蚀性、耐热疲劳性
冷挤模、拉深模、挤压模穿孔针
渗硼
具有极好的表面硬度、耐磨性、抗粘附性、抗氧化性、热硬性、良好的抗蚀性
挤压模、拉深模
碳氮硼三元共渗
提高硬度、强度、耐磨性、耐疲劳性、抗蚀性
挤压模、冲头针尖
盐浴覆层 (TD处理)
提高硬度、耐磨性、耐热疲劳性、抗蚀性、抗粘附性、抗氧化性
表面强化技术

• 2.机理: 加工硬化机理。即随变形量的增 加,金属强度硬度升高,塑性韧性下降。
• 2.机理: 加工硬化机理。即随变形量的 增加,金属强度硬度升高,塑性韧性下 降。
• 原因:a、位错密度随变形量增加而增加, 从而变形抗力增加;b、随变形量增加, 亚结构细化,亚晶界对位错运动有阻碍; c、随变形量增加,空位密度增加;d、 几何硬化。
件、轴类零件和沟槽类零件等,对形状
复杂的零件表面就无法应用了。
四、孔挤压强化
• 1.定义:利用特定的工模具(棒、衬套、 开合模具等)对工件的孔壁或周边进行 连续、缓慢、均匀的挤压,使其形成一 定厚度的塑性变形层,达到提高表面疲 劳强度和抗应力腐蚀能力的一种表面强 化工艺。
• 2.工艺方法:棒挤压、套挤压、压印模挤 压、旋压挤压。
HRC=20+60(2C-1.3C2)
• (4)加热温度的确定
• (5)感应加热淬火设备参数确定
• 包括感应电源、感应圈、喷火装置。
• 感应电源的输出频率主要有高频(100~ 500KHz)、超音频(20~100KHz)、中频 (0.5~10KHz)、和工频(50Hz)。频率是根 据零件的尺寸和硬化层深度确定的。
(4)需很大的设备投入,所以单件小批量生产时 生产成本高。大型的工件淬火,它无法完成。 设备无法移动,因此灵活性相对较差。
• 3、工艺流程和技术要点
预先调质 处理
确定加热温 度与加热方式
根据工件要 求选择功率
制定回火 工艺参数
确定冷却方 式与冷却介质
设计感应 加热器
• (1)前期的预先处理
中高碳钢经过调质处理后,心部可以获得强度和
成本低、应用范围广的零件表面强化技术。它 的强化效果主要表现在延长承受交变负荷的零 件使用寿命。这个效果特别明显,也特别立竿 见影,是其它强化方法难以比拟的。
• 2.机理: 加工硬化机理。即随变形量的 增加,金属强度硬度升高,塑性韧性下 降。
• 原因:a、位错密度随变形量增加而增加, 从而变形抗力增加;b、随变形量增加, 亚结构细化,亚晶界对位错运动有阻碍; c、随变形量增加,空位密度增加;d、 几何硬化。
件、轴类零件和沟槽类零件等,对形状
复杂的零件表面就无法应用了。
四、孔挤压强化
• 1.定义:利用特定的工模具(棒、衬套、 开合模具等)对工件的孔壁或周边进行 连续、缓慢、均匀的挤压,使其形成一 定厚度的塑性变形层,达到提高表面疲 劳强度和抗应力腐蚀能力的一种表面强 化工艺。
• 2.工艺方法:棒挤压、套挤压、压印模挤 压、旋压挤压。
HRC=20+60(2C-1.3C2)
• (4)加热温度的确定
• (5)感应加热淬火设备参数确定
• 包括感应电源、感应圈、喷火装置。
• 感应电源的输出频率主要有高频(100~ 500KHz)、超音频(20~100KHz)、中频 (0.5~10KHz)、和工频(50Hz)。频率是根 据零件的尺寸和硬化层深度确定的。
(4)需很大的设备投入,所以单件小批量生产时 生产成本高。大型的工件淬火,它无法完成。 设备无法移动,因此灵活性相对较差。
• 3、工艺流程和技术要点
预先调质 处理
确定加热温 度与加热方式
根据工件要 求选择功率
制定回火 工艺参数
确定冷却方 式与冷却介质
设计感应 加热器
• (1)前期的预先处理
中高碳钢经过调质处理后,心部可以获得强度和
成本低、应用范围广的零件表面强化技术。它 的强化效果主要表现在延长承受交变负荷的零 件使用寿命。这个效果特别明显,也特别立竿 见影,是其它强化方法难以比拟的。
表面处理ppt课件

1-5铬的后处理 镀锌是电镀之后,容易变色,用手碰的时候很容易沾上指纹。特别是空 气湿润时候,容易生成白色斑点。不使用优秀的光泽漆的话,很难做到 表面有光亮的镀金层。为了克服这个问题,开发了一种新的铬处理。 做铬处理,腐蚀性也大大增加,有色彩,表面光亮。
6
最新课件
达克罗表面处理
2-1概要 达克罗表面处理是利用金属锌的粉末,和氧化金属结合的耐蚀性能,极 高的银白色表面处理。铬酸与乙醇水溶液中加上细微的锌薄片混合在一 起,在金属表面涂抹,形成一层薄膜(6 - 10㎛),通过热处理(300℃)获得 它的皮膜层。达克罗处理是,利用粉刷的形式处理皮膜,达克罗原料的 构成是,特殊的锌粉末,金属氧化物,还原剂等。
6.皮膜密度:3.2-4.0 g/㎠
2-3 达克罗处理特点
1.防锈能力强,适合用在中-高,腐蚀性部位。
2.耐热性防锈能力好。
3.不需去氢处理。
4.绿色工程(经整个工程,没有有害物质排除。)
5.什么样的金属他都可以处理。
6.对铝的接触,有着很好的防锈能力。
8
最新课件
磷酸盐皮膜
3-1磷酸盐皮膜性质 磷酸锌与磷酸锰的皮膜是结晶,它们的形状个不同。色彩是磷酸锌是灰 色,磷酸锰是灰黑色。磷酸铁的皮膜是非晶体,表面色彩是由促进剂, 处理之前铁的表面情况来判断她的颜色由金色到紫色,根据条件种类也 不同。皮膜的耐蚀性是一般越薄的话会越弱。特别是磷酸铁的皮膜很 薄,所以耐蚀性很弱。
材及其设备。
特点:操作简单,使用方便、经济实用,同时添加了高效缓蚀剂、抑雾剂,防止金属出现
过腐蚀和氢脆现象、抑制酸雾的产生。特别适用于小型复杂工件。
15
最新课件
脱脂是除去基体表面油污的过程。
16
最新课件
6
最新课件
达克罗表面处理
2-1概要 达克罗表面处理是利用金属锌的粉末,和氧化金属结合的耐蚀性能,极 高的银白色表面处理。铬酸与乙醇水溶液中加上细微的锌薄片混合在一 起,在金属表面涂抹,形成一层薄膜(6 - 10㎛),通过热处理(300℃)获得 它的皮膜层。达克罗处理是,利用粉刷的形式处理皮膜,达克罗原料的 构成是,特殊的锌粉末,金属氧化物,还原剂等。
6.皮膜密度:3.2-4.0 g/㎠
2-3 达克罗处理特点
1.防锈能力强,适合用在中-高,腐蚀性部位。
2.耐热性防锈能力好。
3.不需去氢处理。
4.绿色工程(经整个工程,没有有害物质排除。)
5.什么样的金属他都可以处理。
6.对铝的接触,有着很好的防锈能力。
8
最新课件
磷酸盐皮膜
3-1磷酸盐皮膜性质 磷酸锌与磷酸锰的皮膜是结晶,它们的形状个不同。色彩是磷酸锌是灰 色,磷酸锰是灰黑色。磷酸铁的皮膜是非晶体,表面色彩是由促进剂, 处理之前铁的表面情况来判断她的颜色由金色到紫色,根据条件种类也 不同。皮膜的耐蚀性是一般越薄的话会越弱。特别是磷酸铁的皮膜很 薄,所以耐蚀性很弱。
材及其设备。
特点:操作简单,使用方便、经济实用,同时添加了高效缓蚀剂、抑雾剂,防止金属出现
过腐蚀和氢脆现象、抑制酸雾的产生。特别适用于小型复杂工件。
15
最新课件
脱脂是除去基体表面油污的过程。
16
最新课件
- 1、下载文档前请自行甄别文档内容的完整性,平台不提供额外的编辑、内容补充、找答案等附加服务。
- 2、"仅部分预览"的文档,不可在线预览部分如存在完整性等问题,可反馈申请退款(可完整预览的文档不适用该条件!)。
- 3、如文档侵犯您的权益,请联系客服反馈,我们会尽快为您处理(人工客服工作时间:9:00-18:30)。
第13讲 表面强化技术
目
1 2 3
录
表面强化技术的定义及分类 金属表面形变强化 表面淬火 热扩渗技术 等离子体扩渗技术 激光表面强化技术 电子束表面强化技术
2018/5/22
4
5 6 7
目
8 9 10
录
电镀和化学镀 气相沉积技术 热喷涂、堆焊和热喷焊 离子注入和电火花表面强化
11
2018/5/22
表2-1 喷丸对模具寿命的影响
模具名称 电动机定、转 子模 定子单模冲模 一字槽光冲模 活扳手热精压 模 模具材料 喷丸介质d/mm 铸钢丸0.5 玻璃丸0.25~0.35 玻璃丸0.25~0.35 铸钢丸0.5 玻璃丸0.25~0.35 一次刃磨使用寿命/万次 喷丸前 1.2~3.2 52 0.96~1.35 0.175 0.388 喷完后 11.49 70 2.0~2.3 0.263 0.517
1.2 表面强化技术定义
定义:采用某种工艺手段使零件表面获得与基体材料 的组织结构,性能不同的一种技术。 优点:延长零件的使用寿命,节约稀有、昂贵材料, 促进高新技术发展。
2018/5/22
1 表面强化技术的定义及分类
1.3 表面强化技术分类
金属表面形变强化 电子束表面强化技术
表面淬火
电镀和化学镀
2018/5/22
2 金属表面形变强化
2.2.2 喷丸材料
1 钢丝线切割丸 2
铸钢丸
铸钢丸
常用钢丝直径d=0.4~1.2mm,硬度为45~50 HRC 为最佳,组织最好好回火M或者B。
弹丸尺寸为0.2~1.5mm,退火处理,硬度为 30~57 HRC,易碎,耗量大,但价格便宜 一般来说,黑色金属制件可用铸铁丸、钢铸丸、 铸钢丸的品质与含碳量有关,一般含碳量在 钢丝线切割丸、玻璃丸和陶瓷丸。有色金属如 0.85%~1.2% ,锰含量在0.65%~1.2% 铝合金、镁合金、钛合金和不锈钢则采用不锈 含质量分数为60%的SiO2,硬度46~50HRC, 钢丸、玻璃丸和陶瓷丸。 脆性大,适用于零件硬度低于弹丸的硬度的场 合。 弹丸硬度高,但脆性大,喷丸后可或得较高的 残余压应力。 包括SiO2颗粒和Al2O3颗粒。喷丸时用水混合 SiO2颗粒,利用压缩空气
5 陶瓷弹丸
6 液态喷丸介质
2 金属表面形变强化
2.3 表面强化在模具表面强化工艺中的影响
表面形变强化可以使模具表面产生冷作硬化,改善模具表面 的粗糙度,有效去除电火花加工产生的表面变质层,提高模具的 疲劳强度,抗冲击磨损性能,从而达到提高零件使用寿命的目的 。喷丸强化后模具使用寿命的提高见表2-1。
表面锤击 表面滚压 内挤压 用小锤(手工或机械)锤击金属表面,使其内部加工硬化 通过滚轮对金属零件表面进行滚压强化 使孔的内表面形成形变强化的工艺措施,效果明显 国内外广泛应用于弹簧、齿轮链条、轴、叶片、火车轮等 新兴起的,设备体积小,应用方便,效率高
喷丸
超声冲击
2018/5/22
2 金属表面形变强化
1 表面强化技术的定义及分类
表面强化是经表面欲处理后,通过表面涂覆、表面改 性或表面复合处理,改变固体金属表面或非金属表面 的化学成分、组织结构、形态和应力状态等,以获得 所需要表面性能的系统工程。它是近代技术与经典表 面工艺相结合而繁衍、发展起来的,有着坚实的科学 基础,具有明显的交叉、边缘学科的性质和极强的实 用性。
2018/5/22
2 金属表面形变强化
1.叶轮 2.叶轮转向 3.接触叶片前的弹丸
6
机械离心式喷丸机
4.弹丸输送管 5.漏斗
6.压缩空气 7.喷射管 8.90°弯曲喷管 9.弹丸
2018/5/22
2 金属表面形变强化
气动式喷丸机
1.零件 2.阀门 4.管道 5.喷嘴 7.储丸箱 8.排尘管
3.空气过滤器 6.导丸管 9.转换口
热扩渗技术
表面 强化技术
气相沉积技术
等离子体扩渗技术
热喷涂和热喷焊 离子注入和电火花 表面强化
激光表面强化技术
2018/5/22
2 金属表面形变强化
2.1 金属表面形变强化的机理及主要方法
原理:通过机械手段(滚压、喷丸等)在金属表面产生压缩 变形,使表面形成形变硬化层,此形变硬化层深度可达 0.15~1.5mm。在此形变硬化层中产生两种变化: (1)在组织结构上,亚晶粒极大地细化,位错密度增加,晶 格畸变度变大; (2)形成了高的宏观残余应力。 表面形变强化的主要方法
1 表面强化技术的定义及分类
1.1 表面强化技术概述
表面工程是一个既古老又新颖 的学科,人们使用表面工程技 术已有悠久的历史。追溯到几 千年前,我国早在春秋战国时 期就已经开始应用钢的淬火、 铜器热镀锡、鎏金及油漆等古 老技术。但是,表面工程的迅 速发展还是从19世纪工业革命 开始,20世纪80年代成为世界 上10大关键技术,进入20世纪 90年代发展势头出现工程研究 的热潮,几乎涉及了工业的各 个领域,表面工程技术仍是将 是主导21世纪的关键技术之一 。 2018/5/22
Cr12 Cr12 60Si2Mn 3CrW8V
2018/5/22
3 表面淬火
3.1 表面淬火的原理及特点
利用快速加热将钢件表面加热到相变温度以上转变为奥氏 体,然后快冷,形成马氏体组织的硬化层,而心部仍保持其 原始组织—珠光体、索氏体,且硬化层与基体之间具有不完 全淬火的过渡层。 适用材料 — 中、高碳钢,普通灰铸铁、球墨铸铁、可锻铸 铁、合金铸铁。
塑形形变层 (a)弹丸撞击表面
位错 晶界 亚晶界 (b)喷弹丸后组织结构
图2-1 喷丸表面的塑形变形
图2-2 表面滚压示意图
2018/5/22
2 金属表面形变强化
2.2 喷丸强化 2.2.1 喷丸强化的设备
喷丸采用的设备按驱动弹丸的方式可分为机械离心喷丸 机和气动喷丸机两大类。喷丸机又有干喷和湿喷之分。干喷 式工作条件差,湿喷式是将弹丸混合在也太重成悬浮状,然 后喷出弹丸,因此工作条件有所改善。 (1)机械式离心喷丸机 弹丸由高速旋转的叶片和叶轮离 心力加速抛出。喷丸功率小,制造成本高,主要用于喷丸强 度高、品种少、批量大、形状简单、尺寸较大的工件。 (2)气动离心喷丸机 以压缩空气驱动弹丸达到高速后撞 击工件的受喷表面。可通过控制气压来控制喷丸强度,操作 灵活,一台机器可喷多个零件,适用于喷丸强度低、品种多 、批量小、形状复杂、尺寸较小的零部件,但功耗大、生产 效率低。
目
1 2 3
录
表面强化技术的定义及分类 金属表面形变强化 表面淬火 热扩渗技术 等离子体扩渗技术 激光表面强化技术 电子束表面强化技术
2018/5/22
4
5 6 7
目
8 9 10
录
电镀和化学镀 气相沉积技术 热喷涂、堆焊和热喷焊 离子注入和电火花表面强化
11
2018/5/22
表2-1 喷丸对模具寿命的影响
模具名称 电动机定、转 子模 定子单模冲模 一字槽光冲模 活扳手热精压 模 模具材料 喷丸介质d/mm 铸钢丸0.5 玻璃丸0.25~0.35 玻璃丸0.25~0.35 铸钢丸0.5 玻璃丸0.25~0.35 一次刃磨使用寿命/万次 喷丸前 1.2~3.2 52 0.96~1.35 0.175 0.388 喷完后 11.49 70 2.0~2.3 0.263 0.517
1.2 表面强化技术定义
定义:采用某种工艺手段使零件表面获得与基体材料 的组织结构,性能不同的一种技术。 优点:延长零件的使用寿命,节约稀有、昂贵材料, 促进高新技术发展。
2018/5/22
1 表面强化技术的定义及分类
1.3 表面强化技术分类
金属表面形变强化 电子束表面强化技术
表面淬火
电镀和化学镀
2018/5/22
2 金属表面形变强化
2.2.2 喷丸材料
1 钢丝线切割丸 2
铸钢丸
铸钢丸
常用钢丝直径d=0.4~1.2mm,硬度为45~50 HRC 为最佳,组织最好好回火M或者B。
弹丸尺寸为0.2~1.5mm,退火处理,硬度为 30~57 HRC,易碎,耗量大,但价格便宜 一般来说,黑色金属制件可用铸铁丸、钢铸丸、 铸钢丸的品质与含碳量有关,一般含碳量在 钢丝线切割丸、玻璃丸和陶瓷丸。有色金属如 0.85%~1.2% ,锰含量在0.65%~1.2% 铝合金、镁合金、钛合金和不锈钢则采用不锈 含质量分数为60%的SiO2,硬度46~50HRC, 钢丸、玻璃丸和陶瓷丸。 脆性大,适用于零件硬度低于弹丸的硬度的场 合。 弹丸硬度高,但脆性大,喷丸后可或得较高的 残余压应力。 包括SiO2颗粒和Al2O3颗粒。喷丸时用水混合 SiO2颗粒,利用压缩空气
5 陶瓷弹丸
6 液态喷丸介质
2 金属表面形变强化
2.3 表面强化在模具表面强化工艺中的影响
表面形变强化可以使模具表面产生冷作硬化,改善模具表面 的粗糙度,有效去除电火花加工产生的表面变质层,提高模具的 疲劳强度,抗冲击磨损性能,从而达到提高零件使用寿命的目的 。喷丸强化后模具使用寿命的提高见表2-1。
表面锤击 表面滚压 内挤压 用小锤(手工或机械)锤击金属表面,使其内部加工硬化 通过滚轮对金属零件表面进行滚压强化 使孔的内表面形成形变强化的工艺措施,效果明显 国内外广泛应用于弹簧、齿轮链条、轴、叶片、火车轮等 新兴起的,设备体积小,应用方便,效率高
喷丸
超声冲击
2018/5/22
2 金属表面形变强化
1 表面强化技术的定义及分类
表面强化是经表面欲处理后,通过表面涂覆、表面改 性或表面复合处理,改变固体金属表面或非金属表面 的化学成分、组织结构、形态和应力状态等,以获得 所需要表面性能的系统工程。它是近代技术与经典表 面工艺相结合而繁衍、发展起来的,有着坚实的科学 基础,具有明显的交叉、边缘学科的性质和极强的实 用性。
2018/5/22
2 金属表面形变强化
1.叶轮 2.叶轮转向 3.接触叶片前的弹丸
6
机械离心式喷丸机
4.弹丸输送管 5.漏斗
6.压缩空气 7.喷射管 8.90°弯曲喷管 9.弹丸
2018/5/22
2 金属表面形变强化
气动式喷丸机
1.零件 2.阀门 4.管道 5.喷嘴 7.储丸箱 8.排尘管
3.空气过滤器 6.导丸管 9.转换口
热扩渗技术
表面 强化技术
气相沉积技术
等离子体扩渗技术
热喷涂和热喷焊 离子注入和电火花 表面强化
激光表面强化技术
2018/5/22
2 金属表面形变强化
2.1 金属表面形变强化的机理及主要方法
原理:通过机械手段(滚压、喷丸等)在金属表面产生压缩 变形,使表面形成形变硬化层,此形变硬化层深度可达 0.15~1.5mm。在此形变硬化层中产生两种变化: (1)在组织结构上,亚晶粒极大地细化,位错密度增加,晶 格畸变度变大; (2)形成了高的宏观残余应力。 表面形变强化的主要方法
1 表面强化技术的定义及分类
1.1 表面强化技术概述
表面工程是一个既古老又新颖 的学科,人们使用表面工程技 术已有悠久的历史。追溯到几 千年前,我国早在春秋战国时 期就已经开始应用钢的淬火、 铜器热镀锡、鎏金及油漆等古 老技术。但是,表面工程的迅 速发展还是从19世纪工业革命 开始,20世纪80年代成为世界 上10大关键技术,进入20世纪 90年代发展势头出现工程研究 的热潮,几乎涉及了工业的各 个领域,表面工程技术仍是将 是主导21世纪的关键技术之一 。 2018/5/22
Cr12 Cr12 60Si2Mn 3CrW8V
2018/5/22
3 表面淬火
3.1 表面淬火的原理及特点
利用快速加热将钢件表面加热到相变温度以上转变为奥氏 体,然后快冷,形成马氏体组织的硬化层,而心部仍保持其 原始组织—珠光体、索氏体,且硬化层与基体之间具有不完 全淬火的过渡层。 适用材料 — 中、高碳钢,普通灰铸铁、球墨铸铁、可锻铸 铁、合金铸铁。
塑形形变层 (a)弹丸撞击表面
位错 晶界 亚晶界 (b)喷弹丸后组织结构
图2-1 喷丸表面的塑形变形
图2-2 表面滚压示意图
2018/5/22
2 金属表面形变强化
2.2 喷丸强化 2.2.1 喷丸强化的设备
喷丸采用的设备按驱动弹丸的方式可分为机械离心喷丸 机和气动喷丸机两大类。喷丸机又有干喷和湿喷之分。干喷 式工作条件差,湿喷式是将弹丸混合在也太重成悬浮状,然 后喷出弹丸,因此工作条件有所改善。 (1)机械式离心喷丸机 弹丸由高速旋转的叶片和叶轮离 心力加速抛出。喷丸功率小,制造成本高,主要用于喷丸强 度高、品种少、批量大、形状简单、尺寸较大的工件。 (2)气动离心喷丸机 以压缩空气驱动弹丸达到高速后撞 击工件的受喷表面。可通过控制气压来控制喷丸强度,操作 灵活,一台机器可喷多个零件,适用于喷丸强度低、品种多 、批量小、形状复杂、尺寸较小的零部件,但功耗大、生产 效率低。