煤制油
煤制油

直 接 液 化 技 术
煤
热裂解
自由基碎片∑R
供氢
∑R· + H→∑RH
初级加氢产物∑RH 脱氧反应 脱硫反应 脱氮反应
化 学 反 应
液体燃料
煤 加 氢 液炭, 焦炭
原料煤性质 气氛 工艺参数 煤液化溶剂
干燥无灰基原料液体油收率高 热溶解煤 氢气在液化中的作用 反应温度 溶解氢气 反应压力 煤转换化为低分子产物的速率,即转化的 难易度 CO+H2O反应剂在液化中的作用 供氢和传递氢的作用 反应时间
一 次 性 能 源
天然气:采储比61
煤:采储比227
分布均匀 价格稳定
一吨油
3~4吨煤
45美元 /桶
80美元/桶
2010年
利比亚日均产油160万桶左右,占全球日 产量的2%。自利比亚国内动荡以来,其原 油产量已经减少一半,能源出口几近停顿
原油价格再创新高
147.94美元/桶,甚至 150美元/桶
氢气有力于煤的溶解和加氢液化转化率的提高 容易使褐煤液化,低煤化程度的煤更易反应
煤 加 氢 液 化 影 响 因 素
de
溶剂直接与煤剂反应 氢耗量
优点
热效率高 液体产品收率高
直 接 液 化 优 缺 点
de
缺点
煤浆加氢工艺过程的总 体操作条件相对苛刻
费托(Fischer-Tropsch)工艺
摩比尔(Mobil)工艺
王家岭矿难救援现场
我好纠结, 好纠结!
※我国煤液化技术取得重大突破
※大型煤制油项目已经启动
神华集团煤直接制油项目位于煤炭资源丰富 的内蒙古伊金霍洛旗,于2005年5月开工, 工程规划总规模为500万吨 。
仅试产成功的首条示范生产线,投产后每年即 可转化约350万吨煤,生产柴油、石脑油等产品 108万吨
煤制油技术总结
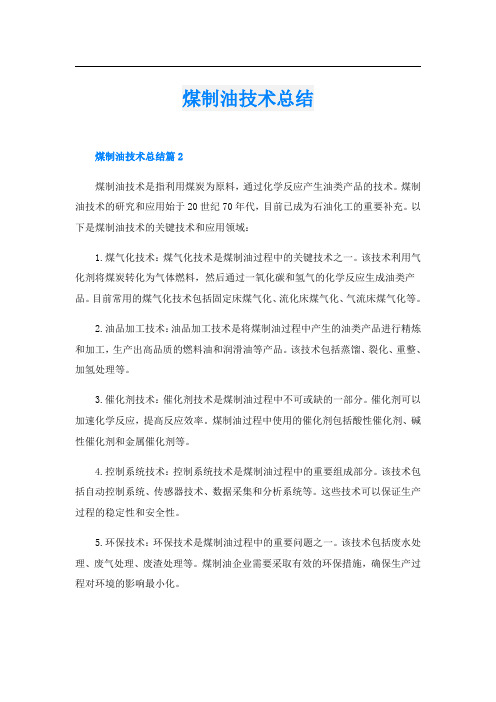
煤制油技术总结煤制油技术总结篇2煤制油技术是指利用煤炭为原料,通过化学反应产生油类产品的技术。
煤制油技术的研究和应用始于20世纪70年代,目前已成为石油化工的重要补充。
以下是煤制油技术的关键技术和应用领域:1.煤气化技术:煤气化技术是煤制油过程中的关键技术之一。
该技术利用气化剂将煤炭转化为气体燃料,然后通过一氧化碳和氢气的化学反应生成油类产品。
目前常用的煤气化技术包括固定床煤气化、流化床煤气化、气流床煤气化等。
2.油品加工技术:油品加工技术是将煤制油过程中产生的油类产品进行精炼和加工,生产出高品质的燃料油和润滑油等产品。
该技术包括蒸馏、裂化、重整、加氢处理等。
3.催化剂技术:催化剂技术是煤制油过程中不可或缺的一部分。
催化剂可以加速化学反应,提高反应效率。
煤制油过程中使用的催化剂包括酸性催化剂、碱性催化剂和金属催化剂等。
4.控制系统技术:控制系统技术是煤制油过程中的重要组成部分。
该技术包括自动控制系统、传感器技术、数据采集和分析系统等。
这些技术可以保证生产过程的稳定性和安全性。
5.环保技术:环保技术是煤制油过程中的重要问题之一。
该技术包括废水处理、废气处理、废渣处理等。
煤制油企业需要采取有效的环保措施,确保生产过程对环境的影响最小化。
煤制油技术的应用领域非常广泛,包括石油化工、能源、航空航天、交通运输、军事等领域。
随着全球能源结构的转变和环境保护政策的加强,煤制油技术将面临着更多的机遇和挑战。
煤制油技术总结篇3煤制油技术是指利用煤炭生产出燃料油和化工原料的技术,是目前全球煤炭深加工的重要方向之一。
煤制油技术主要包括气化、催化裂化、蒸馏和分离等几个主要环节,以下是煤制油技术的详细总结。
1.气化气化是指将煤炭在高温下与水蒸气反应,生成一氧化碳、氢气、甲烷等可燃气体,同时还会产生二氧化碳、氮气等副产物。
气化技术是煤制油过程中重要的环节之一,它可以有效地将煤炭中的碳转化为可燃气体,从而提高了燃料油的产率。
煤制油调研报告

煤制油调研报告一、背景介绍煤制油是指利用煤炭作为原料,通过化学反应将煤转化成油品的过程。
由于煤炭资源丰富,煤制油成为解决能源问题和碳排放问题的重要途径之一。
本调研报告旨在了解煤制油的发展现状、技术路线以及对环境和经济的影响。
二、煤制油技术路线煤制油的技术路线主要包括间接液化和直接液化两种方法。
1. 间接液化技术间接液化技术是指先将煤转化为合成气,再将合成气转化为液体燃料的过程。
这一技术路线采用多段反应器,包括气化、合成气制备、催化合成等步骤。
间接液化技术的优点是生产工艺成熟、设备稳定可靠,但是对煤质要求高,生产成本较高。
2. 直接液化技术直接液化技术是指将煤直接转化为液体燃料的过程。
这一技术路线主要包括溶剂解煤和兰斯曼气化两种方法。
直接液化技术的优点是对煤种适应性强,能够有效利用低质煤,但是生产工艺较复杂,设备投资较大。
三、煤制油发展现状目前,煤制油技术已经在中国取得了较大的发展。
我国拥有世界上最大的煤炭储量,因此发展煤制油具有优势。
中国采用的主要技术路线是间接液化技术,已经建设了多个煤制油基地,如山西阳煤化工公司的山西财团煤制油项目和内蒙古中国能源集团的内蒙古煤制油项目等。
这些项目不仅提高了能源供应的稳定性,还有利于优化煤炭结构,促进能源结构的升级。
四、煤制油的影响煤制油对环境和经济有着深远的影响。
1. 环境影响煤制油是一种高碳排放过程,会对大气环境造成污染。
煤制油过程中产生的二氧化碳等温室气体会加剧全球变暖的问题。
此外,煤制油会产生大量的固体废弃物和废水,对土壤和水源造成污染。
因此,在推进煤制油的发展过程中,必须加强环保措施,减少污染物排放,提高资源利用率。
2. 经济影响煤制油的发展对经济有着积极的影响。
煤制油能够提高我国的能源供应安全,减少对进口石油的依赖,降低能源价格波动对经济的冲击。
同时,煤制油也能够带动相关产业的发展,创造就业机会,促进经济增长。
五、发展煤制油的建议为了更好地发展煤制油,以下是一些建议:1. 加强环境保护意识,采取有效的污染治理措施,减少煤制油对环境的影响。
煤制油原理
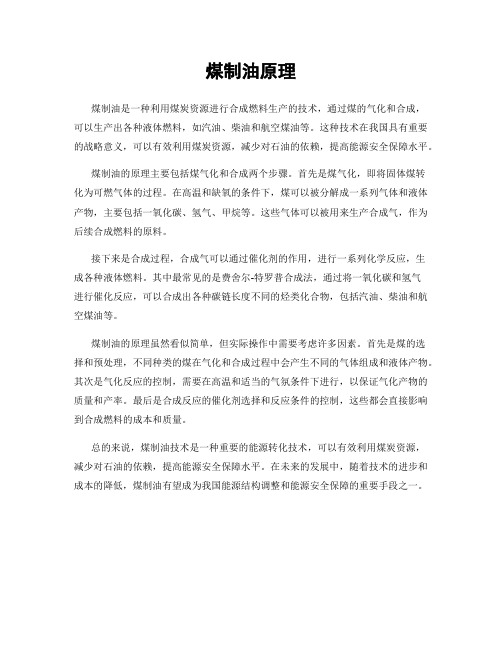
煤制油原理
煤制油是一种利用煤炭资源进行合成燃料生产的技术,通过煤的气化和合成,
可以生产出各种液体燃料,如汽油、柴油和航空煤油等。
这种技术在我国具有重要的战略意义,可以有效利用煤炭资源,减少对石油的依赖,提高能源安全保障水平。
煤制油的原理主要包括煤气化和合成两个步骤。
首先是煤气化,即将固体煤转
化为可燃气体的过程。
在高温和缺氧的条件下,煤可以被分解成一系列气体和液体产物,主要包括一氧化碳、氢气、甲烷等。
这些气体可以被用来生产合成气,作为后续合成燃料的原料。
接下来是合成过程,合成气可以通过催化剂的作用,进行一系列化学反应,生
成各种液体燃料。
其中最常见的是费舍尔-特罗普合成法,通过将一氧化碳和氢气
进行催化反应,可以合成出各种碳链长度不同的烃类化合物,包括汽油、柴油和航空煤油等。
煤制油的原理虽然看似简单,但实际操作中需要考虑许多因素。
首先是煤的选
择和预处理,不同种类的煤在气化和合成过程中会产生不同的气体组成和液体产物。
其次是气化反应的控制,需要在高温和适当的气氛条件下进行,以保证气化产物的质量和产率。
最后是合成反应的催化剂选择和反应条件的控制,这些都会直接影响到合成燃料的成本和质量。
总的来说,煤制油技术是一种重要的能源转化技术,可以有效利用煤炭资源,
减少对石油的依赖,提高能源安全保障水平。
在未来的发展中,随着技术的进步和成本的降低,煤制油有望成为我国能源结构调整和能源安全保障的重要手段之一。
煤制油的工作原理
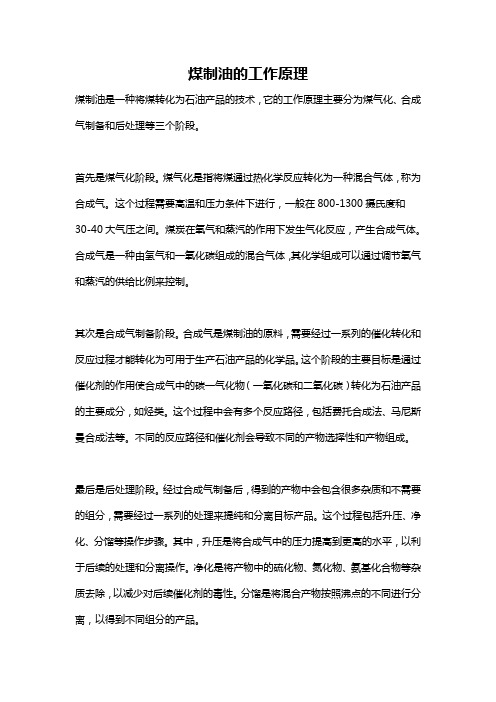
煤制油的工作原理煤制油是一种将煤转化为石油产品的技术,它的工作原理主要分为煤气化、合成气制备和后处理等三个阶段。
首先是煤气化阶段。
煤气化是指将煤通过热化学反应转化为一种混合气体,称为合成气。
这个过程需要高温和压力条件下进行,一般在800-1300摄氏度和30-40大气压之间。
煤炭在氧气和蒸汽的作用下发生气化反应,产生合成气体。
合成气是一种由氢气和一氧化碳组成的混合气体,其化学组成可以通过调节氧气和蒸汽的供给比例来控制。
其次是合成气制备阶段。
合成气是煤制油的原料,需要经过一系列的催化转化和反应过程才能转化为可用于生产石油产品的化学品。
这个阶段的主要目标是通过催化剂的作用使合成气中的碳一气化物(一氧化碳和二氧化碳)转化为石油产品的主要成分,如烃类。
这个过程中会有多个反应路径,包括费托合成法、马尼斯曼合成法等。
不同的反应路径和催化剂会导致不同的产物选择性和产物组成。
最后是后处理阶段。
经过合成气制备后,得到的产物中会包含很多杂质和不需要的组分,需要经过一系列的处理来提纯和分离目标产品。
这个过程包括升压、净化、分馏等操作步骤。
其中,升压是将合成气中的压力提高到更高的水平,以利于后续的处理和分离操作。
净化是将产物中的硫化物、氮化物、氨基化合物等杂质去除,以减少对后续催化剂的毒性。
分馏是将混合产物按照沸点的不同进行分离,以得到不同组分的产品。
总的来说,煤制油的工作原理是先将煤进行气化,得到合成气,然后经过催化反应将合成气转化为石油产品的主要成分,最后通过后处理步骤来提纯和分离产品。
这个过程不仅可以利用煤炭这种丰富的资源,还有利于减少对传统石油资源的依赖,同时也可以减少煤炭的燃烧排放对环境的影响,具有重要的经济和环境效益。
然而,煤制油技术仍然面临着工艺复杂、投资大、能耗高等挑战,需要进一步的研发和优化,以提高效率和经济性。
煤制油技术总结
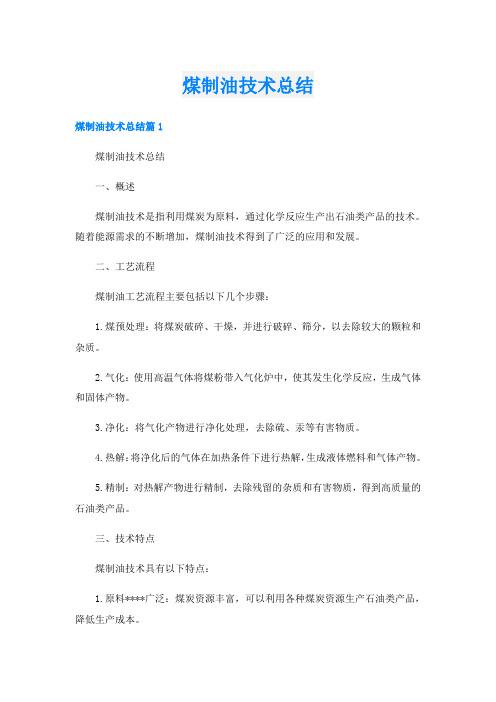
煤制油技术总结煤制油技术总结篇1煤制油技术总结一、概述煤制油技术是指利用煤炭为原料,通过化学反应生产出石油类产品的技术。
随着能源需求的不断增加,煤制油技术得到了广泛的应用和发展。
二、工艺流程煤制油工艺流程主要包括以下几个步骤:1.煤预处理:将煤炭破碎、干燥,并进行破碎、筛分,以去除较大的颗粒和杂质。
2.气化:使用高温气体将煤粉带入气化炉中,使其发生化学反应,生成气体和固体产物。
3.净化:将气化产物进行净化处理,去除硫、汞等有害物质。
4.热解:将净化后的气体在加热条件下进行热解,生成液体燃料和气体产物。
5.精制:对热解产物进行精制,去除残留的杂质和有害物质,得到高质量的石油类产品。
三、技术特点煤制油技术具有以下特点:1.原料****广泛:煤炭资源丰富,可以利用各种煤炭资源生产石油类产品,降低生产成本。
2.生产效率高:通过气化、热解和精制等步骤,可以实现高效生产,提高生产效率。
3.污染排放低:净化处理后,气化产物中的有害物质较少,热解产物经过精制处理后,可以得到高质量的石油类产品,减少对环境的污染。
4.能源利用率高:煤制油技术中使用的能源主要是热能,热能利用率高,可以减少能源浪费。
四、应用前景随着能源需求的不断增加,煤制油技术将有更广泛的应用前景。
同时,随着技术的不断进步和环保要求的提高,煤制油技术也将得到进一步的发展和提高,为能源行业的发展做出更大的贡献。
煤制油技术总结篇2煤制油技术总结1.引言煤制油技术是指利用煤炭为原料,通过一系列化学反应过程生产出油品的技术。
近年来,随着能源需求的不断增加,煤制油技术得到了广泛的应用和快速发展。
*旨在对煤制油技术进行全面的总结和分析,探讨其技术特点、应用现状及未来发展趋势。
2.煤制油技术概述煤制油技术主要包括煤气化技术、油煤浆技术、煤直接液化技术以及煤制油加氢技术等。
这些技术各有特点,应用领域也各不相同。
其中,煤气化技术是煤制油过程中最基本的环节之一,其目的是将煤炭转化为可燃气体的混合物;油煤浆技术则是将煤炭与水、添加剂等混合制成煤浆,便于输送和加工;煤直接液化技术则是将煤炭直接转化为液体燃料;最后,煤制油加氢技术则是将煤气化得到的气体通过加氢处理,得到高辛烷值的汽油和柴油等燃料。
煤制油技术
谢谢指导
风险挑战
技术风险 资源问题 投资风险
煤制油有直接液化和 间接液化两种技术路 线,在全球范围内, 大规模工业化生产的 只有南非萨索尔公司 的间接液化技术,美 国、德国、日本均号 称拥有成熟的直接液 化技术,但均未有大 批量工业化生产的例 子。
资源要素主要包括煤 炭资源和水资源。煤 直接液化法生产一吨 油品需要煤炭3~4吨, 煤间接液化法生产一 吨油品需要煤炭5~7 吨。煤制油工艺需要 消耗大量的水,煤直 接液化法生产一吨油 品需要消耗8吨至9吨 水,Sasol公司所采 用的间接液化方式, 耗水量更是直接液化 法的1.5倍。
资源储备
中国2003-2012能源消费结构
中国各种一次能源消费的百分率 (%)
中国总的能源特征是“富煤、少油、有气”,与之对应的是煤炭在能源消费结 构中占主导,然而煤炭的燃烧引起了严重的环境污染,对煤炭的进一步加工处理使 用已迫在眉睫。
中国能源 元化消费的最佳选择。2
神华鄂尔多斯百万吨煤制油项目工艺流程
技术发展
国内发展
中国中科院山西煤化所从20世纪80年代开始进行铁基、 钴基两大类催化剂费-托合成油煤炭间接液化技术研究及 工程开发,完成了2000吨/年规模的煤基合成油工业实验, 5吨煤炭可合成1吨成品油。目前世界上可以通过”煤制 油”技术合成高品质柴油的只有南非等少数国家。山西 煤化所优质清洁柴油的问世,标志着我国已具备了开发 和提供先进成套产业化自主技术的能力,并成为世界上 少数几个拥有可将煤变为高清洁柴油全套技术的国家之 一。
无论是Sasol公司或 者Shell公司技术, 最大优点是成熟可靠, 而缺点是引进费用高, 使项目总体造价可能 大幅度上升(估计 ﹥15%);相反,采用 国内自主研发技术最 大缺点是,工程放大 存在一定风险,放大 倍数越大,风险也越 大,好处是项目总体 造价可以大幅降低。
煤制油技术总结
煤制油技术总结引言煤制油技术是一种将煤炭转化为液体燃料和化工产品的方法。
随着石油资源的减少和能源需求的增加,煤制油技术在能源领域受到了广泛关注和研究。
本文将对煤制油技术的原理、工艺和发展进行总结和分析。
一、煤制油技术的原理煤制油技术的原理是利用煤炭中的有机物质,在高温、高压和催化剂的作用下,通过热解、裂解和氢化等反应,将煤转化为液体燃料和化工产品。
煤制油技术可以分为间接煤液化和直接煤液化两种方法。
1.间接煤液化:间接煤液化是将煤转化为合成气(由CO和H2组成的气体),然后再通过合成气的催化反应,将其转化为石油产品。
间接煤液化的主要步骤包括煤气化、合成气的净化、合成气的催化反应和产品分离等。
2.直接煤液化:直接煤液化是将煤直接转化为液体燃料和化工产品,不经过合成气的步骤。
直接煤液化的主要反应种类有热解、裂解、氢化和重聚等。
二、煤制油技术的工艺流程煤制油技术的工艺流程主要包括原料预处理、煤气化、合成气的净化、合成反应、产品分离和废水处理等环节。
1.原料预处理:将煤炭进行粉碎和筛分,去除杂质和含硫等有害物质。
2.煤气化:将预处理后的煤炭在高温下与氧气或蒸汽进行反应,产生合成气。
煤气化可以采用固定床、流化床或床浆等反应器。
3.合成气的净化:对合成气中的灰尘、硫化物、苯等有害物质进行净化和除尘处理。
4.合成反应:将净化后的合成气经过催化剂的作用,进行一系列的热解、裂解、氢化和重聚等反应,将其转化为液体燃料和化工产品。
5.产品分离:将合成反应产生的产品进行分离和提纯,得到液体燃料和化工产品。
6.废水处理:处理工艺中产生的废水,通过物理、化学等方法进行处理,达到环保要求后排放或回用。
三、煤制油技术的发展现状煤制油技术作为一种可替代石油资源的方法,已经在世界范围内得到广泛应用和研发。
以下是煤制油技术的一些发展现状:1.国际发展现状:美国、南非、中国等国家在煤制油技术研究和应用方面处于领先地位。
美国的CTL(Coal-to-Liquid)技术已经商业化应用,并取得了良好的经济和环境效益。
国内外煤制油技术
政策支持与市场前景
政策支持:政府对 煤制油技术的研发 和推广给予大力支 持
01
市场需求:随着能 源需求的不断增长, 煤制油技术具有广 阔的市场前景
02
04
环保要求:煤制油 技术需要满足环保 要求和可持续发展 目标
03
技术挑战:煤制油 技术面临技术难题 和成本压力
谢谢
20世纪初,美国、德国等国家 开始研究煤制油技术
20世纪50年代,美国、日本等 国家开始大规模研究煤制油技术
21世纪初,中国开始研究并建 设煤制油工厂
煤制油技术的应用领域
交通燃料:煤制油技术可以生产出清洁、高效的交通 燃料,如汽油、柴油等。
化工原料:煤制油技术可以生产出各种化工原料,如烯 烃、芳烃等,用于生产塑料、橡胶、涂料等化工产品。
03
国际先进水平,但在一些关键技术上仍有差距
发展趋势:国内外煤制油技术都在不断改进和创
04新,以提ຫໍສະໝຸດ 技术水平和降低成本生产规模
国内煤制油技术: 生产规模较小, 主要集中在小型 煤制油企业
国外煤制油技术: 生产规模较大, 技术水平相对较 高
国外煤制油技术: 生产规模较大, 主要集中在大型 煤制油企业
国内煤制油技术: 生产规模较小, 成本较高
国内煤制油技术: 生产规模较小, 技术水平相对较 低
国外煤制油技术: 生产规模较大, 成本较低
成本效益
01
国内煤制油技术:成本
较低,但效益相对较低
02
国外煤制油技术:成本
较高,但效益相对较高
03
技术成熟度:国内技术
相对成熟,国外技术相
对先进
04
环保性能:国内技术环
电力行业:煤制油技术可以生产出高质量的电力,用 于发电、供热等。
煤制油技术总结(优秀5篇)
煤制油技术总结(优秀5篇)煤制油技术总结(优秀5篇)煤制油技术总结要怎么写,才更标准规范?根据多年的文秘写作经验,参考优秀的煤制油技术总结样本能让你事半功倍,下面分享【煤制油技术总结(优秀5篇)】相关方法经验,供你参考借鉴。
煤制油技术总结篇1煤制油技术是一种利用煤炭生产燃油的新技术,其主要包括煤气化、催化裂化、重油加工等过程。
本文将对该技术进行详细介绍,并分析其应用现状及发展趋势。
煤制油技术的基本原理是将煤炭通过气化、催化裂化、重油加工等过程,转化为燃油。
具体来说,首先将煤炭气化生成一氧化碳和氢气,然后通过催化裂化将一氧化碳转化为可燃性气体,最后将可燃性气体与重油进行加工,生成燃油。
该技术的应用现状主要体现在以下几个方面:首先,煤炭气化技术是煤制油技术的核心,目前主要采用水煤浆气化技术,该技术具有较高的转化率和生产效率;其次,催化裂化技术是煤制油技术的关键,目前主要采用择形催化裂化技术,该技术能够将一氧化碳转化为可燃性气体,具有较高的选择性;最后,重油加工技术是煤制油技术的难点,目前主要采用超临界重油加工技术,该技术能够将重油转化为高浓度的燃油,具有较高的生产效率和环保性。
煤制油技术的发展趋势主要体现在以下几个方面:首先,煤制油技术将向着更高的转化率和生产效率方向发展,以提高燃油的产量和生产效率;其次,煤制油技术将向着更加环保的方向发展,采用更加环保的催化剂和加工技术,减少环境污染;最后,煤制油技术将向着智能化和自动化的方向发展,以提高生产效率和产品质量。
总之,煤制油技术是一种具有广阔应用前景的新技术,其不仅能够提高燃油的产量和生产效率,还能够降低环境污染,是未来能源发展的重要方向之一。
煤制油技术总结篇2煤制油技术总结一、概述煤制油技术是指利用煤炭为原料,通过化学反应生产出油品和化工产品的技术。
煤制油技术具有原料丰富、工艺流程简单、生产效率高、成本低等优点,是当前世界上最先进的石油替代品之一。
二、技术原理煤制油技术主要分为煤气化技术、油煤液化技术和费-托合成技术。
- 1、下载文档前请自行甄别文档内容的完整性,平台不提供额外的编辑、内容补充、找答案等附加服务。
- 2、"仅部分预览"的文档,不可在线预览部分如存在完整性等问题,可反馈申请退款(可完整预览的文档不适用该条件!)。
- 3、如文档侵犯您的权益,请联系客服反馈,我们会尽快为您处理(人工客服工作时间:9:00-18:30)。
煤制油、煤制烯烃项目汇报材料提纲一、煤制油项目1、煤制油简介:煤制油也称煤液化,是以煤炭为原料生产液体燃料和化工原料的煤化工技术的简称。
通常有两种技术路线,直接液化和间接液化。
2、直接液化:煤直接液化是煤在适当的温度和压力条件下,直接催化加氢裂化,使其降解和加氢转化为液体油品的工艺过程,煤直接液化也称加氢液化。
煤直接液化技术国内外都进行了大量的技术研究,并建设了许多中试装置,但是目前世界上并没有正在商业运行中的工业化装置。
位于内蒙古鄂尔多斯的神华百万吨级直接液化煤制油示范装置2010年5月投产,预计将成为世界上第一个百万吨级的直接液化煤制油商业示范装置。
但去年实地考察了解到,该装置现在只能生产30万吨/年成品油,主要靠煤焦油加氢来生产,技术还是不成熟。
国外煤直接液化技术二战期间德国建设了大量煤直接液化和间接液化装置,煤制油成为其油品的主要来源之一。
第二次世界大战结束,美国、日本、法国、意大利及前苏联等国相继开展了煤直接液化技术研究。
目前不少国家已经完成了中间放大试验,为建立商业化示范厂奠定了基础。
典型的煤直接液化工艺主要包括德国IGOR工艺(装置规模200吨/天)、美国HTI工艺(装置规模600吨/天)及日本NEDOL工艺(装置规模150吨/天)。
国内煤直接液化技术我国从20世纪70年代开始开展煤炭直接液化技术研究。
20多年来,北京煤化学研究所对我国上百个煤种进行了直接液化试验研究,并开发出高活性煤直接液化催化剂,同时也进行了煤液化油品的提质加工研究。
1997-2000年,煤炭科学研究总院分别与美国、德国、日本等有关机构合作,完成了神华煤、云南先锋煤和黑龙江依兰煤直接液化示范工厂的初步可行性研究。
2004年1月,以煤直接液化中试为首要研究任务的“神华煤制油研究中心有限公司”正式成立,2004年9月,研究中心第一期工程,占地150亩的煤直接液化中试装置(PDU)正式建成。
2004-2006年:6吨/天的PDU装置进行了3次试验。
神华煤直接液化技术采用强制内循环的悬浮床反应器,采用成熟的减压蒸馏固液分离技术,溶剂加氢采用T-Star工艺。
3、间接液化:煤的间接液化以煤为原料先经气化制合成气(CO+H2),再在催化剂的作用下,经F-T合成生成烃类产品和化学品的过程。
工艺流程图如下:国外间接液化技术:国外间接液化已有70多年历史,二战时期德国已经在进行间接液化生产,1956年沙索在南非形成了规模化工业生产,是成熟可靠的煤液化技术。
至今,沙索在南非已建成了3个大厂,年耗原煤近5000万吨,生产油品和化学品700多万吨,其中油品近500万吨。
SASOL已成为世界煤化工装置的典范。
国内煤间接液化技术(1)、中科合成油公司是以中科院山西煤炭化学研究所的浆态床合成液体燃料技术研发团队和设施为基础,联合内蒙古伊泰集团、神华集团、山西潞安集团、徐州矿务集团等共同组建的技术型企业,目前已将发展到拥有研发中心(太原)、工程公司(北京)、催化剂公司(安徽/内蒙/山西),并参股特种设备制造(内蒙)、精细化学品生产(内蒙)的综合性技术研发和应用企业。
2009年3月20日,采用中科合成油公司技术的伊泰16万吨/年煤间接液化项目正式产油成功。
该项目采用的浆态床反应器、费托合成催化剂、油品精制和系统集成全部由我国自主研制。
(2)、2002年12月,兖矿集团在上海组建上海兖矿能源科技研发有限公司,开始开展煤间接液化技术的研究和开发工作。
2004年3月,位于山东鲁南化肥厂的5000吨级低温费托合成、100吨/年催化剂中试装置建成,并实现一次投料试车成功。
2006年4月又开始建设高温费托合成中试装置和100吨/年高温费托合成催化剂中试装置,2007年初高温费托合成催化剂中试装置生产出高温Ⅱ型催化剂,2007年6月高温费托合成中试装置一次投料开车成功,生产出合格产品。
(3)、中石化石科院于2004年开始进行费托合成的相关研究工作,开展了F-T合成的催化剂、反应工程、系统工程等方面的研究工作,开发出了第一代高性能的固定床F-T合成催化剂—RFT-1。
2006年初RFT-1催化剂通过中石化集团公司组织的中试评议。
2006年6月在镇海炼化建设的中石化第一套3000吨/年GTL中试装置中交。
截止2007年8月21日,该装置运行240天,产油550t。
2008年中石化宁波工程公司已完成编制70万吨/年煤制油固定床工业化装置工艺包。
(4)、2004年开始,金巢集团与南非金山大学合作研发费托合成技术,于2005年开始在陕西宝鸡建设中试厂,2007年12月底中试装置建设完成。
该中试厂投资1亿元人民币,于08年1月开车试运行;2008年4月正式开始运行,并已生产出符合要求的产品。
2008年10月金巢集团在陕西宝鸡举行金巢清洁燃料油工程技术专家鉴定会。
金巢开发的该技术目前致力于焦炉煤气制合成油的原料路线。
4、直接液化和间接液化技术对比煤直接液化和间接液化技术各有长短,下面分别对比其对煤质的要求、工艺过程和工艺特点。
直接液化对煤质的要求(1)煤的灰分要低,一般小于5%。
因此,原煤要进行洗选,生产出精煤后再进行液化。
(2)煤的可磨性要好。
煤的直接液化要先把煤磨成200筛目(粒径0.074mm)左右的煤粉,才适合配制成油煤浆。
(3)煤中的氢含量越高越好,氧的含量越低越好,它可以减少加氢的供气量,也可以减少废水生成。
(4)煤中的硫和氮等杂原子含量越低越好,以降低油品加工费用。
因此,能用于直接液化的煤,一般是褐煤、长焰煤等年青煤种,而且这些牌号的煤也不是都能直接液化的。
神华集团的不粘煤、长焰煤和云南先锋矿的褐煤都是较好的直接液化煤种。
间接液化对煤质的要求(1)煤的灰分要求比直接液化相对不严格。
(2)煤的可磨性也要。
(3)对于用水煤浆制气的工艺,要求煤的成浆性能要好。
水煤浆的固体质量分数应在60%以上。
(4)煤的灰融点也有一定要求,一般要求煤的灰融点温度小于1300℃。
间接液化对煤的适应性广,原则上所有煤都能气化成合成气。
当然,不同的煤要选择不同的气化方法。
另外,还有个最佳经济性的问题。
所以,对不同的煤选择不同的气化方法。
煤直接和间接液化工艺过程比较煤直接液化和间接液化工艺特点比较直接液化间接液化5、成本分析:伊泰16万吨煤制油成本、消耗见附件一煤制油\工程相关资料.zip。
120万吨煤制油成本及盈利能力测算见附件二。
煤制油\煤制油分析Book1.xls。
6、中国煤制油产品需求分析从 2001 年到 2010 年我国原油产量逐年上升,但远不能满足消费需求,因此我国原油进量迅速上升,原油进口依存度相应升高。
详细数据请看下表。
2001年16493 6026 755 217642002年16720 6941 721 229402003年16956 9113 813 252552004年17450 12282 549 291832005年18084 12708 807 299862006年18368 14518 634 322522007年18666 16318 383 346002008年18973 17889 373 364892009年18940 20379 207 391122010年20301 23931 304 439282011年进口原油 2.54亿吨(54%) 2012年进口原油 2.71亿吨(59%) 在国内原油产量不断上升的情况下,我国的原油进口依存度仍然从2001年的24.22%上升到了2010年的53.79%,如下图。
面对如此大的原油进口量,开展多种路线的煤制油工业示范,掌握商业化煤制油装置的技术和经验,就体现出其必要性。
在我国的原油消费中,柴油和汽油仍然占据着最大的比重,2010年柴油和汽油加起来达到原油总消费量的53%。
我国的汽油产量和消费量近10年来呈现逐年上升的趋势,在大量进口原油的前提下,由于炼油能力充足,我国汽油进口量较少,并维持了一定数量的出口。
2001年-2010年中国汽油产销数据如下表。
年份国内产量进口量出口量表观消费量2001年4154.66 0.02 577.17 3577.512002年4319.87 0.01 612.20 3707.682003年4770.18 0.00 754.24 4015.942004年5145.20 0.10 533.80 4611.502005年5214.80 0.60 563.80 4651.602006年5374.80 6.80 369.30 5012.302007年5994.00 22.70 464.22 5552.482008年6347.54 198.70 203.55 6342.692009年7194.80 4.41 494.31 6704.902010年7675.30 0.00 517.10 7158.20 值得注意的是,我国汽油消费量的增长幅度远小于乘用车的销量增长幅度,其中一个重要原因是甲醇掺混汽油的影响。
据不完全统计,2009年我国约有500万吨的甲醇被掺混于汽油中出售。
大量甲醇的掺混使汽油生产出现了过剩,我国2009年的实际汽油需求量可能在7200万吨左右,与产量相当。
在新的成品油定价机制下,国际油价对国内汽油市场将有极大的影响,可以预期国内汽油价格将长期处于高位。
而随着汽车消费量快速增长带来的汽油消费量的新的增长空间,煤基甲醇制汽油将在我国的汽油供应体系中赢得一席之地。
2001年-2010年中国柴油产销数据如下表所示。
年份国内产量进口量出口量表观消费量2001年7485.66 27.47 25.65 7487.482002年7669.23 48.08 125.70 7591.612003年8512.90 84.75 224.06 8373.592004年10162.10 274.94 63.65 10373.392005年10824.10 48.10 139.50 10732.702006年11352.90 56.80 79.20 11330.502007年12370.20 162.24 66.03 12466.412008年13323.60 624.75 62.86 13885.492009年14126.80 183.64 450.70 13859.742010年15887.40 179.90 467.30 15600.0目前中国计划建设的间接液化煤制油项目基本都采用低温费托合成技术(LTFT),产品80%左右为费托合成柴油,主要有以下特点。
费托合成柴油的主要组分是碳原子数在9到12之间的直链饱和烷烃,烯烃含量较少,硫含量极少,NOx排放低,十六烷值高,是一种高质量的柴油。
费托合成柴油密度比柴油小,但低热值比柴油高,在使用时柴油机的供油系统不必作更多改动。