高温蠕变与疲劳(课堂PPT)
合集下载
蠕变 PPT课件

继续进行。需更大切应力作用才能使位错重新运动和增殖。 在高温下,位错可借助外界提供的热激活能和空位扩散来克
服某些短程障碍,从而使变形不断产生。
位错热激活方式有多种,高温下热激活主要是刃位错的攀移。
28
蠕变第一阶段:由于蠕变变形逐渐产生应变硬化,使位错源 开动的阻力及位错滑移阻力增大,使蠕变速率不断降低。
线)可得到十万小时的持久强度极限值。 如:12Cr1MoV钢在580℃、100000h的持久强度极限为89MPa。
26
27
10.3 蠕变变形与蠕变断裂机理
一、蠕变变形机理 金属蠕变变形主要是通过位错滑移、原子扩散及晶界滑
动等机理进行的,且随温度及应力的变化而有所不同。
(一)位错滑移蠕变 在蠕变过程中,位错滑移仍然是一种重要的变形机理。 在常温下,若滑移面上位错运动受阻产生塞积,滑移便不能
在耐热合金中晶界上形成的空洞照片,如图。
36
以上两种形成裂纹方式,都有空洞萌生过程。
可见,晶界空洞对材料在高温使用温度范围和寿命是至关重 要的。裂纹形成后,进一步依靠晶界滑动、空位扩散和空洞 连接而扩展,最终导致沿晶断裂。
由于蠕变断裂主要在晶界上产生,因此,晶界的形态、晶界 上的析出物和杂质偏聚、晶粒大小及晶粒度的均匀性等对蠕 变断裂均会产生很大影响。
这就是说:要提高金属材料的高温力学性能,应控制晶内和 晶界的原子扩散过程。
这种扩散过程主要取决于:合金的化学成分、冶炼工艺、热 处理工艺等因素。
41
(一)合金化学成分的影响 位错越过障碍所需的激活能(蠕变激活能)越高的金属,越
难产生蠕变变形。 实验表明:纯金属蠕变激活能大体与其自扩散激活能相近。 因此,耐热钢及合金的基体材料一般选用熔点高、自扩散激活 能大或层错能低的金属及合金。
服某些短程障碍,从而使变形不断产生。
位错热激活方式有多种,高温下热激活主要是刃位错的攀移。
28
蠕变第一阶段:由于蠕变变形逐渐产生应变硬化,使位错源 开动的阻力及位错滑移阻力增大,使蠕变速率不断降低。
线)可得到十万小时的持久强度极限值。 如:12Cr1MoV钢在580℃、100000h的持久强度极限为89MPa。
26
27
10.3 蠕变变形与蠕变断裂机理
一、蠕变变形机理 金属蠕变变形主要是通过位错滑移、原子扩散及晶界滑
动等机理进行的,且随温度及应力的变化而有所不同。
(一)位错滑移蠕变 在蠕变过程中,位错滑移仍然是一种重要的变形机理。 在常温下,若滑移面上位错运动受阻产生塞积,滑移便不能
在耐热合金中晶界上形成的空洞照片,如图。
36
以上两种形成裂纹方式,都有空洞萌生过程。
可见,晶界空洞对材料在高温使用温度范围和寿命是至关重 要的。裂纹形成后,进一步依靠晶界滑动、空位扩散和空洞 连接而扩展,最终导致沿晶断裂。
由于蠕变断裂主要在晶界上产生,因此,晶界的形态、晶界 上的析出物和杂质偏聚、晶粒大小及晶粒度的均匀性等对蠕 变断裂均会产生很大影响。
这就是说:要提高金属材料的高温力学性能,应控制晶内和 晶界的原子扩散过程。
这种扩散过程主要取决于:合金的化学成分、冶炼工艺、热 处理工艺等因素。
41
(一)合金化学成分的影响 位错越过障碍所需的激活能(蠕变激活能)越高的金属,越
难产生蠕变变形。 实验表明:纯金属蠕变激活能大体与其自扩散激活能相近。 因此,耐热钢及合金的基体材料一般选用熔点高、自扩散激活 能大或层错能低的金属及合金。
第四章 材料的疲劳ppt课件

对青铜:
σ-1 =0.21 σb
疲劳极限与材料强度近似成正比,所以合金化、
细化晶粒和组织等强化方法可以提高材料的疲劳
极限。
.
(2)非对称应力循环下的疲劳极限
大多数机械零件所承受载荷属于非对称循 环应力。 ——考虑平均应力、应力幅、应力比
应力比提高, 疲劳极限和 疲劳寿命增 长!
.
平均应力提高,疲劳极限和疲劳寿命减小!
不适用于循环频率较高的试验,故也称低频疲劳或应变疲劳。
.
观察试件在这一阶段的破坏断口,可见到材料已
发生塑性变形的特征。所以低周疲劳性能常用应 变-寿命曲线表征。一般的疲劳曲线特指N>104范
围内的应力-寿命曲线。
有些机械零件,例如一次性使用的火箭发动机的某些零件、 导弹壳体等,在整个使用寿命期间应力变化次数只有几百到 几千次,故其疲劳属于低周疲劳。但对绝大多数通用零件来 说,当其承受变应力作用时,其应力循环次数总是大于 10000的。所以大部分是高周疲劳。
.
例题
疲劳试验的平均应力是50MPa,应力变化 幅度是30MPa。试计算:1、最大应力;2、 最小应力;3、应力比。
解:平均应力σm= (σmax+σmin)/2=50 应力变化Δσ=2σa= (σmax-σmin)=30 σmax=65MPa;σmin=35MPa;r=0.54
.
1.2 疲劳破坏
德国人Wohler针对火车车轴疲劳进行研究, 得到了循环应力(S)与疲劳循环寿命(N) 之间的关系。——疲劳曲线(S-N曲线)
.
旋转弯曲疲劳试验
试样旋转并承受一弯矩。 产生弯矩的力恒定不变且 不转动。试样可装成悬臂, 在一点或两点加力;或装 成横梁,在四点加力。试 验一直进行到试样失效或 超过预定应力循环次数。
第八章材料的蠕变 ppt课件

29
8.3 蠕变变形和蠕变断裂机制
8.3.1 蠕变变形机理 材料在高温下加载后,要伴生一定量的瞬时变形,其中包括
弹性变形和塑性变形。在机理上,瞬时变形与常温的弹、塑性变形 相似,弹性变形由正应力作用产生,塑性变形主要由切应力作用产 生。随后产生的蠕变变形取决于温度和应力的共同作用,与常温塑 性变形有所不同。
减速蠕变
恒速蠕变
加速蠕变
蠕变 断裂
瞬时应变
蠕变速率
恒温、恒应力条件
10
❖ 第 I 阶段:AB段,减速蠕变阶段(过渡蠕变 阶段)。开始的蠕变速率很大,随着时间的 延长,蠕变速率逐渐减小,到B点,蠕变速 率达到最小值;
❖ 第Ⅱ阶段:BC段,恒速蠕变阶段(稳态蠕变 阶段)。特点是蠕变速率几乎不变。一般可 以表示为材料的蠕变速率。
2)在常温下晶界变形极不明显,可忽略不计。但在高温蠕变条 件下,由于晶界强度降低,其变形量很大,有时甚至占总蠕变变形 量的一半,这是蠕变变形的重要特点之一。
30
鉴于蠕变变形是涉及晶体内位错运动、 晶界变形、原子扩散等多种复杂的过程,下 面分别阐述相应过程的蠕变变形机制。
(1) 位错滑移蠕变机理 在高温下,由于温度升高,给原子和
材料的持久强度是实验测定的,持久 强度实验时间通常比蠕变极限实验要长得 多,根据设计要求,持久强度实验最长可 达几万 ~ 几十万小时。
26
由于实际高温构件所要求的持久强度一般要求几 千到几万小时,较长者可达几万至几十万小时。 实际上持久强度是不宜直接测定的,一般要通过 内插或外推方法确定。所以,在多数情况下,实 际的持久强度值是利用短时寿命(如几十或几百, 最多是几千小时)数据的外推来估计的。 实验表明:金属材料在给定温度下,持久应力和 断裂时间(断裂寿命)t 可用下列经验公式表示:
8.3 蠕变变形和蠕变断裂机制
8.3.1 蠕变变形机理 材料在高温下加载后,要伴生一定量的瞬时变形,其中包括
弹性变形和塑性变形。在机理上,瞬时变形与常温的弹、塑性变形 相似,弹性变形由正应力作用产生,塑性变形主要由切应力作用产 生。随后产生的蠕变变形取决于温度和应力的共同作用,与常温塑 性变形有所不同。
减速蠕变
恒速蠕变
加速蠕变
蠕变 断裂
瞬时应变
蠕变速率
恒温、恒应力条件
10
❖ 第 I 阶段:AB段,减速蠕变阶段(过渡蠕变 阶段)。开始的蠕变速率很大,随着时间的 延长,蠕变速率逐渐减小,到B点,蠕变速 率达到最小值;
❖ 第Ⅱ阶段:BC段,恒速蠕变阶段(稳态蠕变 阶段)。特点是蠕变速率几乎不变。一般可 以表示为材料的蠕变速率。
2)在常温下晶界变形极不明显,可忽略不计。但在高温蠕变条 件下,由于晶界强度降低,其变形量很大,有时甚至占总蠕变变形 量的一半,这是蠕变变形的重要特点之一。
30
鉴于蠕变变形是涉及晶体内位错运动、 晶界变形、原子扩散等多种复杂的过程,下 面分别阐述相应过程的蠕变变形机制。
(1) 位错滑移蠕变机理 在高温下,由于温度升高,给原子和
材料的持久强度是实验测定的,持久 强度实验时间通常比蠕变极限实验要长得 多,根据设计要求,持久强度实验最长可 达几万 ~ 几十万小时。
26
由于实际高温构件所要求的持久强度一般要求几 千到几万小时,较长者可达几万至几十万小时。 实际上持久强度是不宜直接测定的,一般要通过 内插或外推方法确定。所以,在多数情况下,实 际的持久强度值是利用短时寿命(如几十或几百, 最多是几千小时)数据的外推来估计的。 实验表明:金属材料在给定温度下,持久应力和 断裂时间(断裂寿命)t 可用下列经验公式表示:
高温及环境下的材料力学性能概述(PPT 49张)
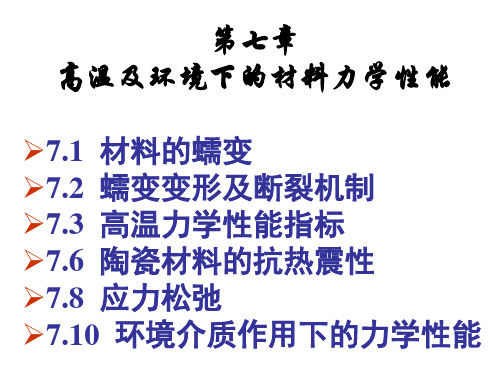
在使用上,选用哪种表示方法应视蠕变速率与服役时间而定。
(2)持久强度极限
持久强度极限定义:材料在高温长时载荷作用下的断裂 强度。 蠕变极限表征的是蠕变变形抗力,持久强度极限表征断 裂抗力,是两种不同的性能指标。
持久强度极限表示方法:
t
--在规定温度(t)晶界滑动蠕变机制
晶界在外力的作用下,会发生相对滑动变形: 在常温下,可以忽略不计;
但在高温时,晶界的相对滑动可以引起明 显的塑性变形,产生蠕变。
二、蠕变损伤与断裂机制
蠕变断裂多数为沿晶断裂,由此可见蠕变造成的损伤主要发 生在晶界上。
变形速率提 高,等强温 度提高。
等强温度
等强温度以上工作的材料,晶粒不可过细。
一、抗热震断裂
对急剧受热或冷却的陶瓷材料,若温差ΔTc引起热应力达到 陶瓷材料断裂强度σf,则发生热震断裂,抗热震参数R为:
(E,v,a分别为弹性模量、泊松比、热膨胀系数。)
高温下的位错热激活主要是刃型位错的攀移,模型见下图:
(2)扩散蠕变
认为蠕变是高温下大量原子
与空位定向移动造成的:
承受拉应力(A、B晶界)的晶界, 空位浓度增加; 承受压应力(C、D晶界)的晶界, 空位浓度减小。 晶体内空位从受拉晶界向受压晶 界迁移,原子朝相反方向运动, 使得晶体伸长--扩散蠕变。
同一材料的蠕变曲线随应力大小、温度高低有不同:
应力较小、温度较低时:蠕变的恒速蠕变阶段持 续时间长,甚至不出现加速蠕变阶段; 应力较大、温度较高时:蠕变恒速蠕变阶段持续 时间短,甚至消失,试样在短时间内断裂,主要 为加速蠕变。
7.2、蠕变变形及断裂机制
一、蠕变变形机制: 位错滑移蠕变、扩散蠕变、晶界滑动蠕变 (1)位错滑移蠕变 位错滑移仍是蠕变变形一种重要的变形机制。高温下会 出现新的滑移系。 常温下,如果滑移面上的位错运动受阻产生塞积,滑移 不能进行,只有在更大的切应力作用下位移重新运动和 增殖(硬化)。 但在高温下,位错可借助于外界提供的热激活能和空位 扩散克服某些短程障碍,从而产生变形(软化)。
材料物理课件3.2 高温蠕变

3.2.1 典型的蠕变曲线 1. 各阶段的特点
8
延 6 伸 率 4 × 10-2
2
第三阶段蠕变 第二阶段蠕变 第一阶段蠕变 弹性伸长 时间(小时) 时间(小时)
200 300 400 500 600
0
0
100
(1) 弹性形变阶段 ) 起始段,在外力作用下,发生瞬时弹性形变, 起始段,在外力作用下,发生瞬时弹性形变,即 应力和应变同步。 应力和应变同步。 (2)第一阶段蠕变(蠕变减速阶段或过渡阶段) )第一阶段蠕变(蠕变减速阶段或过渡阶段) 其特点是应变速率随时间递减,持续时间较短, 其特点是应变速率随时间递减,持续时间较短, 应变速率有如下关系: 应变速率有如下关系: U=dε/dt=At-n ε 低温时n=1,得:ε=Blnt , 低温时 高温时n=2/3,得: ε=Bt-2/3 , 高温时 此阶段类似于可逆滞弹性形变。 此阶段类似于可逆滞弹性形变。
(1)气孔:气孔率增加,蠕变率增加。 )气孔:气孔率增加,蠕变率增加。 原因:气孔减少抵抗蠕变的有效截面积。 原因:气孔减少抵抗蠕变的有效截面积。 (2)晶粒:晶粒越小,蠕变率越大。 )晶粒:晶粒越小,蠕变率越大。 原因:晶界的比例随晶粒的减小而大大增加, 原因:晶界的比例随晶粒的减小而大大增加,晶界扩 散及晶界流动加强。 散及晶界流动加强。 (3) 玻璃相:玻璃相粘度越小,蠕变率增加。 ) 玻璃相:玻璃相粘度越小,蠕变率增加。 原因:温度升高,玻璃的粘度降低,变形速率增大, 原因:温度升高,玻璃的粘度降低,变形速率增大, 蠕变率增大。 蠕变率增大。 说明粘性流动对材料致密化的影响: 说明粘性流动对材料致密化的影响:材料在高温烧结 晶界粘性流动,气孔容纳晶粒滑动时发生的形变, 时,晶界粘性流动,气孔容纳晶粒滑动时发生的形变, 即实现材料致密化。 即实现材料致密化。
高温蠕变与疲劳

C % / h
(MPa)表示。
蠕变极限适用于失效方式为过量变形的那些高温零部件。
持久强度是材料抵抗蠕变断裂的能力。它是在
一定温度下,规定时间内使材料断裂的最大应力值,
以
表t C示。
对于锅炉、管道等构件。其主要破坏方式是断
裂而不是变形,设计这类构件就要采用持久强度指 标。
持久塑性是材料承受蠕变变形能力的大小,用 蠕变断裂时的相对伸长率和相对断面收缩率表示。
4、蠕变断裂机制图 晶间断裂是蠕变断裂的普遍形式,高温
低应力下情况更是如此。
晶间断裂有两种模型:一种是晶界滑动 和应力集中模型,另一种是空位聚集模型。
第一种模型:
图12.18 晶界滑动在三晶粒交界处形成楔形空间
第二种模型 :
图12.20 空位聚集形成空洞
断裂机制图 :
影响蠕变断裂机制的最重要因素是应力、 温度和加载速率,因此,断裂机制图的纵坐
标通常为规范化流变应力fl/E,横坐标为断
裂时间tf或相对温度T/Tm。
图12.21 Nimonic 80A合金断裂机制图
图12.22断裂机制图示意图
二、高温疲劳
高温疲劳涉及疲劳、蠕变和环境影响等几个与 时间有关的过程的交互作用,这些过程在高温疲劳 损伤中的相对作用随具体材料而异。
材料在高温下的疲劳行为,除了与循环应力有 关,还与材料的化学成分、显微组织和环境等因素 有很大关系。
金属材料的典型蠕变曲线如图12.16所示。
图12.16 典型蠕变曲线
oa线段是施加外载荷后试样的瞬时应变0,不 属于蠕变;
曲线abcd表明应变是随时间增长逐渐产生的, 称为蠕变;蠕变曲线上任一点的斜率表示该点的蠕
变速率,用 表示。
高温及环境下的材料力学性能概述(PPT 49张)
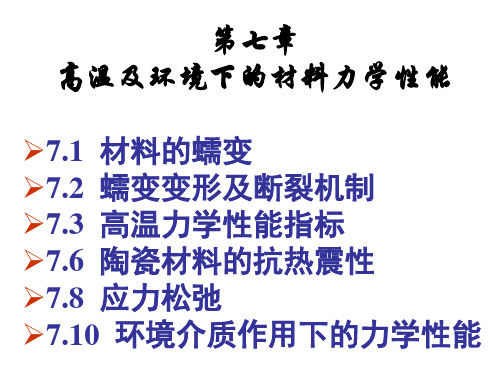
在使用上,选用哪种表示方法应视蠕变速率与服役时间而定。
(2)持久强度极限
持久强度极限定义:材料在高温长时载荷作用下的断裂 强度。 蠕变极限表征的是蠕变变形抗力,持久强度极限表征断 裂抗力,是两种不同的性能指标。
持久强度极限表示方法:
t
--在规定温度(t)下,达到规定的持续时间τ抵抗断裂 的最大应力。
各种耐热钢及高温合金对冶炼工艺的要求较高, 钢中的夹杂物和某些冶金缺陷会使材料的持久强 度极限降低。 高温合金对杂质元素及气体含量要求很严格,即 使含量只有十万分之一,当其在晶界偏聚后,会 导致晶界的严重弱化,使热弹性降低。
(3)热处理工艺的影响
如:珠光体耐热钢一般采用正火加高温回火工 艺,正火温度较高,以促使C化物充分溶于奥 氏体中,回火温度高于使用温度100-150℃, 以提高使用温度下的组织稳定性。
蠕变速度:
d d
按蠕变速率的变化,蠕变
过程分成三个阶段:
金属、陶瓷的典型蠕变曲线
第一阶段(ab):蠕变速率随时间减小--减速蠕变或过渡蠕 变阶段。
第二阶段(bc):蠕变速率Βιβλιοθήκη 变且最小--稳态蠕变或恒速蠕 变阶段。
第三阶段(cd):时间延长,蠕变速度逐渐增大,直至d点产生 蠕变断裂--加速蠕变阶段。
延滞断裂 静载疲劳
一、应力腐蚀
应力腐蚀(Stress Corrosion Cracking, SCC)--金属在拉应 力和特定的化学介质共同作用下,经过一段时间后所产生的低 应力脆断现象。 应力腐蚀的危险性在于它常发生在相当缓和的介质和不大的 应力状态下,往往事先没有明显的预兆,故常造成灾难性的事 故。
要降低蠕变速度提高蠕变极限,必须控制位错 攀移的速度; 要提高断裂抗力,即提高持久强度,必须抑制 晶界的滑动。
《高温蠕变机制》课件

பைடு நூலகம்
金属材料加工领域的应用
要点一
金属冶炼
高温蠕变机制在金属冶炼过程中能够指导冶炼工艺的优化 ,提高金属材料的性能。
要点二
金属成型
高温蠕变机制的研究有助于开发更为可靠的金属成型工艺 ,提高产品的质量和稳定性。
其他领域的应用与展望
汽车工业
高温蠕变机制在汽车工业中具有广泛的应用前景,能 够提高汽车发动机和传动系统的性能和可靠性。
VS
应力集中促进蠕变
应力集中的区域,如材料中的裂纹、孔洞 等,会成为蠕变的起点,加速蠕变过程。
微观结构的影响
晶粒尺寸影响蠕变速率
晶粒尺寸越小,材料的抗蠕变性能越好。这是因为晶粒越小,晶界数量越多,阻碍位错运动的能力越强。
第二相强化作用
材料中的第二相粒子可以阻碍位错运动,提高材料的抗蠕变性能。
环境因素的影响
优化提供理论指导。
研究高温蠕变过程中的应力松弛 和损伤累积机制,提出有效的控 制策略,降低蠕变变形和损伤的
风险。
高温蠕变与损伤的预测与评估
1
发展高温蠕变与损伤的预测模型,通过引入材料 的微观结构和宏观性能参数,实现对蠕变行为的 定量描述和预测。
2
开展高温蠕变损伤评估研究,建立损伤评估标准 和方法,实现对材料在高温环境下服役寿命的预 测和评估。
气氛环境影响
某些气氛,如氧气、水蒸气等,可以与材料 发生化学反应,改变材料内部结构,从而影 响蠕变速率。
腐蚀介质影响
在腐蚀介质中,材料表面的保护膜可能被破 坏,暴露出新鲜的表面,从而加速蠕变。
04
高温蠕变实验与测试技术
蠕变速率的测定
蠕变速率
01
指材料在恒温、恒应力的条件下,变形随时间逐渐增加的速度
金属材料加工领域的应用
要点一
金属冶炼
高温蠕变机制在金属冶炼过程中能够指导冶炼工艺的优化 ,提高金属材料的性能。
要点二
金属成型
高温蠕变机制的研究有助于开发更为可靠的金属成型工艺 ,提高产品的质量和稳定性。
其他领域的应用与展望
汽车工业
高温蠕变机制在汽车工业中具有广泛的应用前景,能 够提高汽车发动机和传动系统的性能和可靠性。
VS
应力集中促进蠕变
应力集中的区域,如材料中的裂纹、孔洞 等,会成为蠕变的起点,加速蠕变过程。
微观结构的影响
晶粒尺寸影响蠕变速率
晶粒尺寸越小,材料的抗蠕变性能越好。这是因为晶粒越小,晶界数量越多,阻碍位错运动的能力越强。
第二相强化作用
材料中的第二相粒子可以阻碍位错运动,提高材料的抗蠕变性能。
环境因素的影响
优化提供理论指导。
研究高温蠕变过程中的应力松弛 和损伤累积机制,提出有效的控 制策略,降低蠕变变形和损伤的
风险。
高温蠕变与损伤的预测与评估
1
发展高温蠕变与损伤的预测模型,通过引入材料 的微观结构和宏观性能参数,实现对蠕变行为的 定量描述和预测。
2
开展高温蠕变损伤评估研究,建立损伤评估标准 和方法,实现对材料在高温环境下服役寿命的预 测和评估。
气氛环境影响
某些气氛,如氧气、水蒸气等,可以与材料 发生化学反应,改变材料内部结构,从而影 响蠕变速率。
腐蚀介质影响
在腐蚀介质中,材料表面的保护膜可能被破 坏,暴露出新鲜的表面,从而加速蠕变。
04
高温蠕变实验与测试技术
蠕变速率的测定
蠕变速率
01
指材料在恒温、恒应力的条件下,变形随时间逐渐增加的速度
- 1、下载文档前请自行甄别文档内容的完整性,平台不提供额外的编辑、内容补充、找答案等附加服务。
- 2、"仅部分预览"的文档,不可在线预览部分如存在完整性等问题,可反馈申请退款(可完整预览的文档不适用该条件!)。
- 3、如文档侵犯您的权益,请联系客服反馈,我们会尽快为您处理(人工客服工作时间:9:00-18:30)。
二、高温疲劳
2
一、高温蠕变
1、蠕变现象和蠕变曲线 当温度T≥(0.3~0.5)Tm(Tm为熔点,单位为K)时,金属材
料在恒载荷的持续作用下,发生与时间相关的塑性变形,称 为蠕变。
相应的应变与时间关系曲线称为蠕变曲线。
金属材料的典型蠕变曲线如图12.16所示。
3
图12.16 典型蠕变曲线
4
oa线段是施加外载荷后试样的瞬时应变0,不 属于蠕变;
蠕变第三阶段(cd段)的蠕变速率随时间延长急 剧增大直至断裂,称为加速蠕变阶段。
6
蠕变曲线各阶段持续时间的长短随材料 和试验条件而变化。如图12.17所示 :
图12.17 应力和温度对蠕变曲线影响示意图
a)等温曲线(σ4>σ3>σ2>σ1)
b)等压力曲线(T4>T3>T2>T1) 7
2、蠕变极限和持久强度
温度和加载速率,因此,断裂机制图的纵坐
标通常为规范化流变应力fl/E,横坐标为断
裂时间tf或相对温度T/Tm。
16
图12.21 Nimonic 80A合金断裂机制图
17
图12.22断裂机制图示意图
18
二、高温疲劳
高温疲劳涉及疲劳、蠕变和环境影响等几个与 时间有关的过程的交互作用,这些过程在高温疲劳 损伤中的相对作用随具体材料而异。
12
4、蠕变断裂机制图 晶间断裂是蠕变断裂的普遍形式,高温
低应力下情况更是如此。
晶间断裂有两种模型:一种是晶界滑动 和应力集中模型,另一种是空位聚集模型。
13
第一种模型:
图12.18 晶界滑动在三晶粒交界处形成楔形空间
14
第二种模型 :
图12.20 空位聚集形成空洞
15
断裂机制图 : 影响蠕变断裂机制的最重要因素是应力、
缺口构件的开裂时间(裂纹扩展孕育期)ti
与缺口根部截面的初始应力0和绝对温度T间
有如下关系 :
1 ti
Ai0C
exp(Qi ) RT
11
式中:Ai、C是与温度有关的材料常数;Qi是开 裂激活能。
裂纹体的蠕变开裂时间可用应力强度因子KI描 述:
ti Ai'KI C'
式中:Ai′、C′是与温度有关的材料常数。
12.3 高温蠕变与疲劳
很多构件长期在高温条件下运转。例如,航空 发动机叶片的使用温度高达1000℃,用Cr-Mo-V钢 制造的汽轮机转子使用温度约为550℃等。
高温对金属材料的力学性能影响很大。
温度和时间还影响金属材料的断裂形式。
1
一、高温蠕变
1、蠕变现象和蠕变曲线 2、蠕变极限和持久强度 3、蠕变断裂 4、蠕变断裂机制图
曲线abcd表明应变是随时间增长逐渐产生的, 称为蠕变;蠕变曲线上任一点的斜率表示该点的蠕
变速率,用 表示。
根据蠕变速率的变化情况可以将蠕变过程分为 三个阶段:
5
ab段为蠕变第一阶段,其蠕变速率随时间而逐 渐减小,故又称为减速蠕变阶段;
bc段为蠕变第二阶段,又称恒速蠕变或稳态蠕 变阶段,即其蠕变速率保持恒定;
材料在高温下的疲劳行为,除了与循环应力有 关,还与材料的化学成分、显微组织和环境等因素 有很大关系。
19
8
持久强度是材料抵抗蠕变断裂的能力。它是在
一定温度下,规定时间内使材料其主要破坏方式是断
裂而不是变形,设计这类构件就要采用持久强度指 标。
持久塑性是材料承受蠕变变形能力的大小,用 蠕变断裂时的相对伸长率和相对断面收缩率表示。
9
3、蠕变断裂 对于不含裂纹的构件或试样,其稳态蠕变速率与蠕变断
裂时间或加速蠕变阶段开始时间tf之间存在以下经验关系:
stf Cf
式中:和Cf为材料常数。
实际意义:在早期稳态蠕变阶段得到后,再通过较高应
力即和可较由高t温f 度的C短f 期/蠕s变预试测验。获得Cf,则长期蠕变断裂寿命
10
对于含有裂纹或类似裂纹缺陷的构件,
其蠕变断裂是在裂纹或缺陷尖端再萌生蠕变 裂纹,即裂纹开裂、主裂纹扩展和断裂的过 程。
蠕变极限是高温长时期载荷下材料对变形的抗力指标,是高温强度
设计的重要依据。它有两种表示方法。
一种是在给定温度下,规定时间内产生一定蠕变总量的应力值,以
C (MPa)表示。 % /t 另一种是在一定温度下,产生规定的稳态蠕变速率的应力值,以
C % / h
(MPa)表示。
蠕变极限适用于失效方式为过量变形的那些高温零部件。
2
一、高温蠕变
1、蠕变现象和蠕变曲线 当温度T≥(0.3~0.5)Tm(Tm为熔点,单位为K)时,金属材
料在恒载荷的持续作用下,发生与时间相关的塑性变形,称 为蠕变。
相应的应变与时间关系曲线称为蠕变曲线。
金属材料的典型蠕变曲线如图12.16所示。
3
图12.16 典型蠕变曲线
4
oa线段是施加外载荷后试样的瞬时应变0,不 属于蠕变;
蠕变第三阶段(cd段)的蠕变速率随时间延长急 剧增大直至断裂,称为加速蠕变阶段。
6
蠕变曲线各阶段持续时间的长短随材料 和试验条件而变化。如图12.17所示 :
图12.17 应力和温度对蠕变曲线影响示意图
a)等温曲线(σ4>σ3>σ2>σ1)
b)等压力曲线(T4>T3>T2>T1) 7
2、蠕变极限和持久强度
温度和加载速率,因此,断裂机制图的纵坐
标通常为规范化流变应力fl/E,横坐标为断
裂时间tf或相对温度T/Tm。
16
图12.21 Nimonic 80A合金断裂机制图
17
图12.22断裂机制图示意图
18
二、高温疲劳
高温疲劳涉及疲劳、蠕变和环境影响等几个与 时间有关的过程的交互作用,这些过程在高温疲劳 损伤中的相对作用随具体材料而异。
12
4、蠕变断裂机制图 晶间断裂是蠕变断裂的普遍形式,高温
低应力下情况更是如此。
晶间断裂有两种模型:一种是晶界滑动 和应力集中模型,另一种是空位聚集模型。
13
第一种模型:
图12.18 晶界滑动在三晶粒交界处形成楔形空间
14
第二种模型 :
图12.20 空位聚集形成空洞
15
断裂机制图 : 影响蠕变断裂机制的最重要因素是应力、
缺口构件的开裂时间(裂纹扩展孕育期)ti
与缺口根部截面的初始应力0和绝对温度T间
有如下关系 :
1 ti
Ai0C
exp(Qi ) RT
11
式中:Ai、C是与温度有关的材料常数;Qi是开 裂激活能。
裂纹体的蠕变开裂时间可用应力强度因子KI描 述:
ti Ai'KI C'
式中:Ai′、C′是与温度有关的材料常数。
12.3 高温蠕变与疲劳
很多构件长期在高温条件下运转。例如,航空 发动机叶片的使用温度高达1000℃,用Cr-Mo-V钢 制造的汽轮机转子使用温度约为550℃等。
高温对金属材料的力学性能影响很大。
温度和时间还影响金属材料的断裂形式。
1
一、高温蠕变
1、蠕变现象和蠕变曲线 2、蠕变极限和持久强度 3、蠕变断裂 4、蠕变断裂机制图
曲线abcd表明应变是随时间增长逐渐产生的, 称为蠕变;蠕变曲线上任一点的斜率表示该点的蠕
变速率,用 表示。
根据蠕变速率的变化情况可以将蠕变过程分为 三个阶段:
5
ab段为蠕变第一阶段,其蠕变速率随时间而逐 渐减小,故又称为减速蠕变阶段;
bc段为蠕变第二阶段,又称恒速蠕变或稳态蠕 变阶段,即其蠕变速率保持恒定;
材料在高温下的疲劳行为,除了与循环应力有 关,还与材料的化学成分、显微组织和环境等因素 有很大关系。
19
8
持久强度是材料抵抗蠕变断裂的能力。它是在
一定温度下,规定时间内使材料其主要破坏方式是断
裂而不是变形,设计这类构件就要采用持久强度指 标。
持久塑性是材料承受蠕变变形能力的大小,用 蠕变断裂时的相对伸长率和相对断面收缩率表示。
9
3、蠕变断裂 对于不含裂纹的构件或试样,其稳态蠕变速率与蠕变断
裂时间或加速蠕变阶段开始时间tf之间存在以下经验关系:
stf Cf
式中:和Cf为材料常数。
实际意义:在早期稳态蠕变阶段得到后,再通过较高应
力即和可较由高t温f 度的C短f 期/蠕s变预试测验。获得Cf,则长期蠕变断裂寿命
10
对于含有裂纹或类似裂纹缺陷的构件,
其蠕变断裂是在裂纹或缺陷尖端再萌生蠕变 裂纹,即裂纹开裂、主裂纹扩展和断裂的过 程。
蠕变极限是高温长时期载荷下材料对变形的抗力指标,是高温强度
设计的重要依据。它有两种表示方法。
一种是在给定温度下,规定时间内产生一定蠕变总量的应力值,以
C (MPa)表示。 % /t 另一种是在一定温度下,产生规定的稳态蠕变速率的应力值,以
C % / h
(MPa)表示。
蠕变极限适用于失效方式为过量变形的那些高温零部件。