冲压模的研究现状及发展方向
我国冲压模具技术的现状与发展

我国冲压模具技术的现状与发展冲压模具是现代制造业中不可或缺的重要工艺装备,广泛应用于汽车、电子、家电等众多领域。
随着我国制造业的快速发展,冲压模具技术也取得了显著的进步,但同时也面临着一些挑战。
我国冲压模具技术的现状可以从以下几个方面来描述。
在模具设计方面,计算机辅助设计(CAD)和计算机辅助工程(CAE)技术得到了广泛应用。
通过这些技术,模具设计师能够更加高效、准确地完成模具结构的设计和优化。
同时,三维设计软件的普及使得模具设计更加直观,有助于提前发现和解决潜在的问题。
在模具制造方面,数控加工技术的应用日益广泛。
数控机床的高精度、高效率加工能力,大大提高了模具零件的加工精度和生产效率。
电火花加工、线切割加工等特种加工技术也在模具制造中发挥着重要作用,满足了复杂形状和高精度模具零件的加工需求。
模具材料方面,我国已经能够生产出多种高性能的模具钢,如冷作模具钢、热作模具钢和塑料模具钢等。
这些材料的性能不断提升,为制造高质量的冲压模具提供了有力保障。
在模具表面处理技术上,诸如渗氮、渗碳、镀硬铬等工艺得到了进一步的改进和优化,提高了模具的表面硬度、耐磨性和耐腐蚀性,延长了模具的使用寿命。
然而,我国冲压模具技术仍存在一些不足之处。
与国际先进水平相比,我国在高端模具的研发和制造方面仍有一定差距。
例如,在一些大型、精密、复杂的冲压模具领域,还依赖进口。
模具的标准化程度有待提高。
标准化程度低会导致模具制造周期长、成本高,影响整个行业的发展效率。
模具行业的专业人才相对短缺。
尤其是既懂模具技术又熟悉市场需求的复合型人才不足,制约了行业的创新和发展。
在模具寿命和可靠性方面,仍需要进一步提升。
一些模具在使用过程中容易出现磨损、变形等问题,影响生产效率和产品质量。
展望未来,我国冲压模具技术有着广阔的发展前景。
随着智能制造技术的不断发展,冲压模具将朝着智能化、数字化的方向迈进。
通过引入工业互联网、大数据等技术,实现模具设计、制造和使用过程的智能化监控和管理,提高生产效率和质量。
冲压行业现状及未来行业发展趋势

一、冲压行业现状随着工业化的快速发展,冲压行业作为制造业的一个重要组成部分,扮演着至关重要的角色。
冲压是利用模具和冲压机械对金属材料进行塑性变形加工的一种工艺,广泛应用于汽车、电子、家电、航空航天等领域。
目前,冲压行业在我国占据着相当大的市场份额,是国民经济的支柱产业之一。
1.1 冲压行业的规模根据统计数据显示,我国冲压行业的总产值和出口额均居世界领先地位。
特别是汽车、家电等领域的快速发展,带动了冲压行业的迅速增长。
冲压行业在国民经济中占据着举足轻重的地位,为整个制造业的稳定发展做出了巨大贡献。
1.2 冲压行业的发展瓶颈然而,随着市场竞争的加剧和外部环境的变化,冲压行业也面临着一些困难和挑战。
技术更新换代缓慢,产品同质化严重,成本压力大等问题成为了冲压行业发展的瓶颈。
能源消耗、环境污染等问题也限制了冲压行业的可持续发展。
1.3 冲压行业的市场需求尽管如此,冲压行业仍然拥有广阔的市场需求。
随着汽车、电子、家电等行业的不断发展,冲压件的需求量将会持续增加。
随着智能制造的推动和国家政策的扶持,冲压行业将迎来更多的发展机遇。
二、冲压行业未来发展趋势2.1 技术升级和智能制造为了应对市场竞争和环境压力,冲压行业将加快技术更新换代,推进智能制造。
通过引进先进的设备和技术,提高生产效率和产品质量,降低能源消耗和环境污染,从而实现可持续发展。
2.2 专业化和定制化随着市场需求的多样化,冲压行业将朝着专业化和定制化方向发展。
不再满足于传统的大批量生产模式,而是更加注重个性化产品和服务,提高市场竞争力。
2.3 国际化合作和市场拓展为了开拓更大的市场空间,冲压行业将积极开展国际合作,加强与国外企业的交流与合作,拓展国际市场,提高品牌影响力。
2.4 绿色制造和节能减排作为传统制造业,冲压行业将更加注重绿色制造和节能减排。
通过技术创新和管理优化,实现资源的有效利用,减少能源消耗和环境污染,实现可持续发展。
2.5 人才培养和团队建设冲压行业将加大人才培养和团队建设力度,提高员工的技术水平和创新能力,培养一批具有国际竞争力的专业人才,为行业的发展注入新的活力。
冲压模具技术的现状和发展趋势
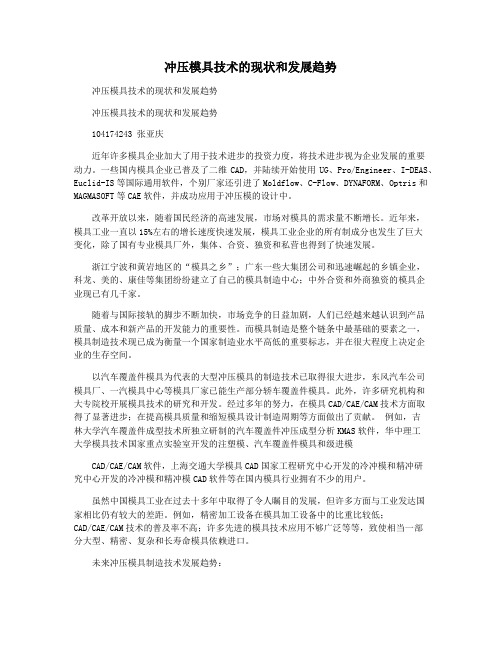
冲压模具技术的现状和发展趋势冲压模具技术的现状和发展趋势冲压模具技术的现状和发展趋势104174243 张亚庆近年许多模具企业加大了用于技术进步的投资力度,将技术进步视为企业发展的重要动力。
一些国内模具企业已普及了二维CAD,并陆续开始使用UG、Pro/Engineer、I-DEAS、Euclid-IS等国际通用软件,个别厂家还引进了Moldflow、C-Flow、DYNAFORM、Optris和MAGMASOFT等CAE软件,并成功应用于冲压模的设计中。
改革开放以来,随着国民经济的高速发展,市场对模具的需求量不断增长。
近年来,模具工业一直以15%左右的增长速度快速发展,模具工业企业的所有制成分也发生了巨大变化,除了国有专业模具厂外,集体、合资、独资和私营也得到了快速发展。
浙江宁波和黄岩地区的“模具之乡”;广东一些大集团公司和迅速崛起的乡镇企业,科龙、美的、康佳等集团纷纷建立了自己的模具制造中心;中外合资和外商独资的模具企业现已有几千家。
随着与国际接轨的脚步不断加快,市场竞争的日益加剧,人们已经越来越认识到产品质量、成本和新产品的开发能力的重要性。
而模具制造是整个链条中最基础的要素之一,模具制造技术现已成为衡量一个国家制造业水平高低的重要标志,并在很大程度上决定企业的生存空间。
以汽车覆盖件模具为代表的大型冲压模具的制造技术已取得很大进步,东风汽车公司模具厂、一汽模具中心等模具厂家已能生产部分轿车覆盖件模具。
此外,许多研究机构和大专院校开展模具技术的研究和开发。
经过多年的努力,在模具CAD/CAE/CAM技术方面取得了显著进步;在提高模具质量和缩短模具设计制造周期等方面做出了贡献。
例如,吉林大学汽车覆盖件成型技术所独立研制的汽车覆盖件冲压成型分析KMAS软件,华中理工大学模具技术国家重点实验室开发的注塑模、汽车覆盖件模具和级进模CAD/CAE/CAM软件,上海交通大学模具CAD国家工程研究中心开发的冷冲模和精冲研究中心开发的冷冲模和精冲模CAD软件等在国内模具行业拥有不少的用户。
冲压模具的现状与发展
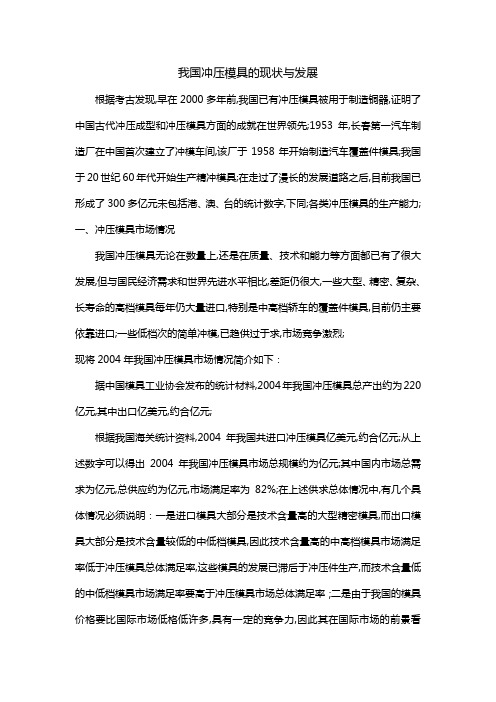
我国冲压模具的现状与发展根据考古发现,早在2000多年前,我国已有冲压模具被用于制造铜器,证明了中国古代冲压成型和冲压模具方面的成就在世界领先;1953年,长春第一汽车制造厂在中国首次建立了冲模车间,该厂于1958年开始制造汽车覆盖件模具;我国于20世纪60年代开始生产精冲模具;在走过了漫长的发展道路之后,目前我国已形成了300多亿元未包括港、澳、台的统计数字,下同;各类冲压模具的生产能力;一、冲压模具市场情况我国冲压模具无论在数量上,还是在质量、技术和能力等方面都已有了很大发展,但与国民经济需求和世界先进水平相比,差距仍很大,一些大型、精密、复杂、长寿命的高档模具每年仍大量进口,特别是中高档轿车的覆盖件模具,目前仍主要依靠进口;一些低档次的简单冲模,已趋供过于求,市场竞争激烈;现将2004年我国冲压模具市场情况简介如下:据中国模具工业协会发布的统计材料,2004年我国冲压模具总产出约为220亿元,其中出口亿美元,约合亿元;根据我国海关统计资料,2004年我国共进口冲压模具亿美元,约合亿元;从上述数字可以得出2004年我国冲压模具市场总规模约为亿元;其中国内市场总需求为亿元,总供应约为亿元,市场满足率为82%;在上述供求总体情况中,有几个具体情况必须说明:一是进口模具大部分是技术含量高的大型精密模具,而出口模具大部分是技术含量较低的中低档模具,因此技术含量高的中高档模具市场满足率低于冲压模具总体满足率,这些模具的发展已滞后于冲压件生产,而技术含量低的中低档模具市场满足率要高于冲压模具市场总体满足率;二是由于我国的模具价格要比国际市场低格低许多,具有一定的竞争力,因此其在国际市场的前景看好,2005年冲压模具出口达到亿美元,比2004年增长%就可说明这一点;三是近年来港资、台资、外资企业在我国发展迅速,这些企业中大量的自产自用的冲压模具无确切的统计资料,因此未能计入上述数字之中;二、冲压模具水平状况近年来,我国冲压模具水平已有很大提高;大型冲压模具已能生产单套重量达50多吨的模具;为中档轿车配套的覆盖件模具国内也能生产了;精度达到1~2μm,寿命2亿次左右的多工位级进模国内已有多家企业能够生产;表面粗糙度达到Ra≦μm的精冲模,大尺寸Φ≧300mm精冲模及中厚板精冲模国内也已达到相当高的水平;1. 模具CAD/CAM技术状况我国模具CAD/CAM技术的发展已有20多年历史;由原华中工学院和武汉733厂于1984年共同完成的精冲模CAD/CAM系统是我国第一个自行开发的模具CAD/CAM系统;由华中工学院和北京模具厂等于1986年共同完成的冷冲模CAD/CAM系统是我国自行开发的第一个冲裁模CAD/CAM系统;上海交通大学开发的冷冲模CAD/CAM系统也于同年完成;20世纪90年代以来,国内汽车行业的模具设计制造中开始采用CAD/CAM技术;国家科委863计划将东风汽车公司作为CIMS应用示范工厂,由华中理工大学作为技术依托单位,开发的汽车车身与覆盖件模具CAD/CAPP/CAM集成系统于1996年初通过鉴定;在此期间,一汽和成飞汽车模具中心引进了工作站和CAD/CAM软件系统,并在模具设计制造中实际应用,取得了显着效益;1997年一汽引进了板料成型过程计算机模拟CAE软件并开始用于生产;21世纪开始CAD/CAM技术逐渐普及,现在具有一定生产能力的冲压模具企业基本都有了CAD/CAM技术;其中部分骨干重点企业还具备各CAE能力;模具CAD/CAM技术能显着缩短模具设计与制造周期,降低生产成本,提高产品质量,已成为人们的共识;在“八五”、“九五”期间,已有一大批模具企业推广普及了计算机绘图技术,数控加工的使用率也越来越高,并陆续引进了相当数量的CAD/CAM系统;如美国EDS的UG,美国Parametric Technology公司的Pro/Engineer,美国CV公司的CADS5,英国DELCAM公司的DOCT5,日本HZS 公司的网址:CRADE及space-E,以色列公司的Cimatron,还引进了AutoCAD、CATIA 等软件及法国Marta-Daravision公司用于汽车及覆盖件模具的Euclid-IS等专用软件;国内汽车覆盖件模具生产企业普遍采用了CAD/CAM技术;DL图的设计和模具结构图的设计均已实现二维CAD,多数企业已经向三维过渡,总图生产逐步代替零件图生产;且模具的参数化设计也开始走向少数模具厂家技术开发的领域;在冲压成型CAE软件方面,除了引进的软件外,华中科技大学、吉林大学、湖南大学等都已研发了较高水平的具有自主知识产权的软件,并已在生产实践中得到成功应用,产生了良好的效益;快速原型RP与传统的快速经济模具相结合,快速制造大型汽车覆盖件模具,解决了原来低熔点合金模具靠样件浇铸模具,模具精度低、制件精度低,样件制作难等问题,实现了以三维CAD模型作为制模依据的快速模具制造,并且保证了制件的精度,为汽车行业新车型的开发、车身快速试制提供了覆盖件制作的保证,它标志着RPM应用于汽车车身大型覆盖件试制模具已取得了成功;围绕着汽车车身试制、大型覆盖件模具的快速制造,近年来也涌现出一些新的快速成型方法,例如目前已开始在生产中应用的无模多点成型及激光冲击和电磁成型等技术;它们都表现出了降低成本、提高效率等优点;2. 模具设计与制造能力状况在国家产业政策的正确引导下,经过几十年努力,现在我国冲压模具的设计与制造能力已达到较高水平,包括信息工程和虚拟技术等许多现代设计制造技术已在很多模具企业得到应用;虽然如此,我国的冲压模具设计制造能力与市场需要和国际先进水平相比仍有较大差距;这些主要表现在高档轿车和大中型汽车覆盖件模具及高精度冲模方面,无论在设计还是加工工艺和能力方面,都有较大差距;轿车覆盖件模具,具有设计和制造难度大,质量和精度要求高的特点,可代表覆盖件模具的水平;虽然在设计制造方法和手段方面已基本达到了国际水平,模具结构功能方面也接近国际水平,在轿车模具国产化进程中前进了一大步,但在制造质量、精度、制造周期等方面,与国外相比还存在一定的差距;标志冲模技术先进水平的多工位级进模和多功能模具,是我国重点发展的精密模具品种;有代表性的是集机电一体化的铁芯精密自动阀片多功能模具,已基本达到国际水平;但总体上和国外多工位级进模相比,在制造精度、使用寿命、模具结构和功能上,仍存在一定差距;汽车覆盖件模具制造技术正在不断地提高和完善,高精度、高效益加工设备的使用越来越广泛;高性能的五轴高速铣床和三轴的高速铣床的应用已越来越多;NC、DNC技术的应用越来越成熟,可以进行倾角加工和超精加工;这些都提高了模具型面加工精度,提高了模具的质量,缩短了模具的制造周期;模具表面强化技术也得到广泛应用;工艺成熟、无污染、成本适中的离子渗氮技术越来越被认可,碳化物被覆处理TD处理及许多镀涂层技术在冲压模具上的应用日益增多;真空处理技术、实型铸造技术、刃口堆焊技术等日趋成熟;激光切割和激光焊接技术也得到了应用;3. 专业化程度及分布状况我国模具行业专业化程度还比较低,模具自产自配比例过高;国外模具自产自配比例一般为30%,我国冲压模具自产自配比例为60%;这就对专业化产生了很多不利影响;现在,技术要求高、投入大的模具,其专业化程度较高,例如覆盖件模具、多工位级进模和精冲模等;而一般冲模专业化程度就较低;由于自配比例高,所以冲压模具生产能力的分布基本上跟随冲压件生产能力的分布;但是专业化程度较高的汽车覆盖件模具和多工位、多功能精密冲模的专业生产企业的分布有不少并不跟随冲压件能力分布而分布,而往往取决于主要投资者的决策;例如四川有较大的汽车覆盖件模具的能力,江苏有较强的精密冲模的能力,而模具的用户大都不在本地;三、冲压模具的发展重点与展望发展重点的选取应根据市场需求、发展趋势和目前状况来确定;可按产品重点、技术重点和其他重点分别叙述;1、冲压模具产品发展重点;冲压模具共有7小类,并有一些按其服务对象来称呼的一些种类;目前急需发展的是汽车覆盖件模具,多功能、多工位级进模和精冲模;这些模具现在产需矛盾大,发展前景好;汽车覆盖件模具中发展重点是技术要求高的中高档轿车大中型覆盖件模具,尤其是外覆盖件模具;高强度板和不等厚板的冲压模具及大型多工位级进模、连续模今后将会有较快的发展;多功能、多工位级进模中发展重点是高精度、高效率和大型、高寿命的级进模;精冲模中发展重点是厚板精冲模大型精冲模,并不断提高其精度;2、冲压模具技术发展重点;模具技术未来发展趋势主要是朝信息化、高速化生产与高精度化发展;因此从设计技术来说,发展重点在于大力推广CAD/CAE/CAM技术的应用,并持续提高效率,特别是板材成型过程的计算机模拟分析技术;模具CAD、CAM技术应向宜人化、集成化、智能化和网络化方向发展,并提高模具CAD、CAM系统专用化程度;为了提高CAD、CAE、CAM技术的应用水平,建立完整的模具资料库及开发专家系统和提高软件的实用性十分重要;从加工技术来说,发展重点在于高速加工和高精度加工;高速加工目前主要是发展高速铣削、高速研抛和高速电加工及快速制模技术;高精度加工目前主要是发展模具零件精度1μm以下和表面粗糙度Ra≦μm的各种精密加工;提高模具标准化程度,搞好模具标准件生产供应也是冲压模具技术发展重点之一;为了提高冲压模具的寿命,模具表面的各种强化超硬处理等技术也是发展重点; 对于模具数字化制造、系统集成、逆向工程、快速原型/模具制造及计算机辅助应用技术等方面形成全方位解决方案,提供模具开发与工程服务,全面提高企业水平和模具质量,这更是冲压模具技术发展的重点;3、其他发展重点及展望;其他发展重点及展望的内涵十分丰富,这里只就管理、专业化与标准化及行业调整三个方面作一些分析;企业管理是一个系统工程,是一门学问,是科学技术;与工业发达国家模具企业相比,在某种意义上说,我们的管理落后更甚于技术落后;因此改进管理十分重要,且任务繁重,目前模具企业的管理有许多形式,各有其适应对象,但搞好信息化建设,逐步实现信息化管理已成为发展方向,行业也对此有共识;由于历史和体制上的原因,我国模具专业化和标准化水平一直很低,其中冲压模具的专业化比塑料模和压铸模更低;这在一定程度上妨碍了冲压模具的发展,根据国内外模具专业化情况来看,专业化可以有多层意思:1模具生产独立于其他产品生产,专业生产模具外供;2按模具种类划分,专门从事某一类模具如冲压模具生产;3在某一类模具中,按其服务对象或模具工艺及尺寸大小,选取该类模具中的某种模具例如汽车覆盖件模具、多工位级进模具、精冲模具等等进行专业化生产;4专业生产模具中的某一些零件如模架、冲头、弹性元件等供给模具生产企业;5按工序开展专业化协作;例如目前社会上专门从事模具设计的公司、专门进行型腔加工或电加工协作的企业、专门接受测量或热处理委托业务的企业及专业从事抛光业务的企业等等,这种多层次的专业化促进了模具行业的发展;但专业化的路途仍旧遥远,必须加快进程才能适应形势;因此,这也是发展重点;行业调整是一个十分繁重的任务,模具行业更是如此;模具行业面临的调整任务主要有:1 模具企业组织结构的调整;使模具分厂车间独立出来,成为面向社会、自负盈亏的独立法人是调整的方向;模具企业按小而精、小而专、小而特的方向发展,并且在条件成熟情况下企业之间进行联合,以及发展产、学、研和科、工、贸相结合的联合体,也是调整的方向;规模效应也引起大家的重视;2 模具产品结构的调整;随着汽车工业、电子信息工业和家电工业的发展,冲压模具市场结构正在发生很大变化;与此相适应,冲压模具产品结构必须进行相应的调整;例如汽车覆盖件模具、汽车零件精冲模具、高精度高难度的引线框架冲模、接插件多工位级进模、各种电机定转子级进冲模等,其产品种类和产量必将有很大发展,有关企业必须根据市场需求来调整其产品结构;总体来看,应不断提高技术含量的大型、精密、复杂、长寿命模具的比例;3 模具技术结构的调整;21世纪已进入信息时代,信息时代的发展日新月异,模具行业和企业要发展必须把握时代脉搏,自觉主动地调整自已的技术结构;传统的模具设计制造技术必须用先进适用的高新技术进行改造,模具的技术含量必将逐步而快速地提高,现代化工业企业管理技术也必将逐步替代作坊式的管理模式;模具行业和模具企业,只有不断进行技术结构的调整,才能在瞬息万变的市场经济中立于不败之地;4 模具进出口结构的调整;2005年,我国冲压模具进口亿美元,出口亿美元,进出口相抵后净进口亿美元,进出口之比:1;我国的冲压模具出口量只占生产量的5%;这样的结构明显不合理;模具工业发达国家,模具产出中一般都有30%左右的出口,出口模具大大多于进口模具;我们虽然不可能在短时间内达到模具工业发达国家一样的进出口结构,但努力扩大出口,逐步改善结构,经过若干年努力,尽量做到进出口基本平衡,则应该是我们调整的目标;在信息化带动工业化发展的今天,在经济全球化趋向日渐加速的情况下,我国冲压模具必须尽快提高水平;通过改革与发展,采取各种有效措施,在冲压模具行业全体职工的共同努力奋斗之下,我国冲压模具也一定会不断提高水平,逐渐缩小与世界先进水平的差距;“十一五”期间,在科学发展观指导下,不断提高自主开发能力、重视创新、坚持改革开放、走新型工业化道路,将速度效益型的增长模式逐步转变到质量和水平效益型轨道上来,我国的冲压模具的水平也必然会更上一层楼;。
冲压模具技术的现状和发展趋势
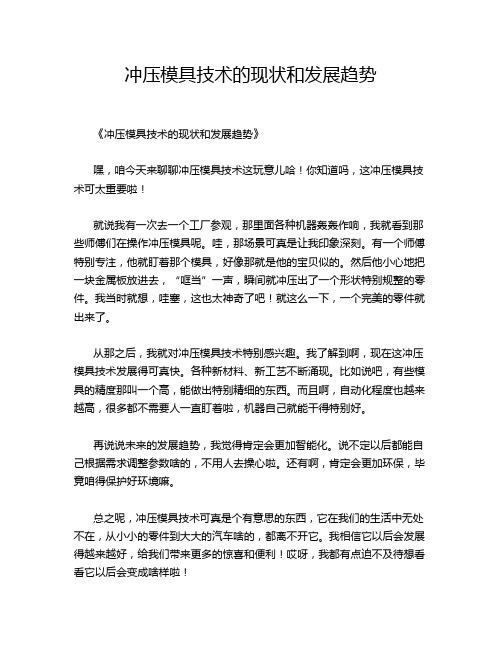
冲压模具技术的现状和发展趋势《冲压模具技术的现状和发展趋势》
嘿,咱今天来聊聊冲压模具技术这玩意儿哈!你知道吗,这冲压模具技术可太重要啦!
就说我有一次去一个工厂参观,那里面各种机器轰轰作响,我就看到那些师傅们在操作冲压模具呢。
哇,那场景可真是让我印象深刻。
有一个师傅特别专注,他就盯着那个模具,好像那就是他的宝贝似的。
然后他小心地把一块金属板放进去,“哐当”一声,瞬间就冲压出了一个形状特别规整的零件。
我当时就想,哇塞,这也太神奇了吧!就这么一下,一个完美的零件就出来了。
从那之后,我就对冲压模具技术特别感兴趣。
我了解到啊,现在这冲压模具技术发展得可真快。
各种新材料、新工艺不断涌现。
比如说吧,有些模具的精度那叫一个高,能做出特别精细的东西。
而且啊,自动化程度也越来越高,很多都不需要人一直盯着啦,机器自己就能干得特别好。
再说说未来的发展趋势,我觉得肯定会更加智能化。
说不定以后都能自己根据需求调整参数啥的,不用人去操心啦。
还有啊,肯定会更加环保,毕竟咱得保护好环境嘛。
总之呢,冲压模具技术可真是个有意思的东西,它在我们的生活中无处不在,从小小的零件到大大的汽车啥的,都离不开它。
我相信它以后会发展得越来越好,给我们带来更多的惊喜和便利!哎呀,我都有点迫不及待想看看它以后会变成啥样啦!。
冲压模具课题研究报告
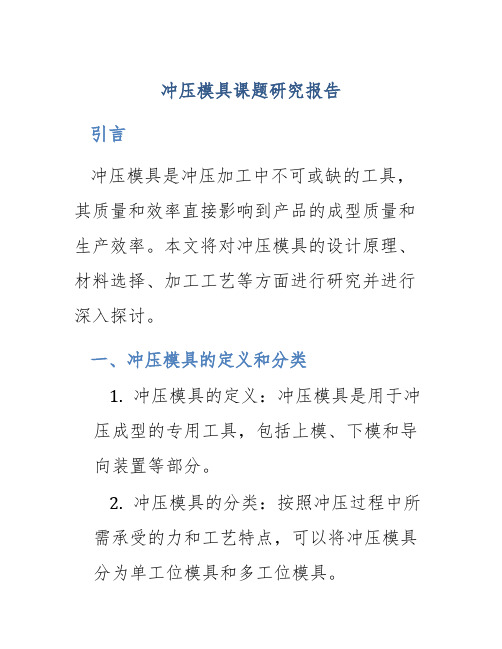
冲压模具课题研究报告引言冲压模具是冲压加工中不可或缺的工具,其质量和效率直接影响到产品的成型质量和生产效率。
本文将对冲压模具的设计原理、材料选择、加工工艺等方面进行研究并进行深入探讨。
一、冲压模具的定义和分类1.冲压模具的定义:冲压模具是用于冲压成型的专用工具,包括上模、下模和导向装置等部分。
2.冲压模具的分类:按照冲压过程中所需承受的力和工艺特点,可以将冲压模具分为单工位模具和多工位模具。
二、冲压模具的设计原理冲压模具设计的核心原理是根据产品的形状和尺寸要求,合理确定上模、下模、导向装置等的结构形式,并确保冲压过程中工艺参数的控制。
1.冲压模具的结构形式:冲压模具一般由上模、下模和导向装置组成,其中上模和下模分别负责产品的凸出和凹陷形状,导向装置确保模具的定位和导向精度。
2.冲压模具的工艺参数控制:冲压模具的设计中需要考虑冲床的能力、冲压工艺参数的选定以及模具的寿命等因素。
三、冲压模具材料的选择冲压模具的材料选择直接影响到模具的质量和使用寿命。
常用的冲压模具材料包括工具钢、硬质合金、高速钢等。
1.工具钢:工具钢具有较高的硬度、耐磨和耐热性能,适用于大多数冲压工作。
2.硬质合金:硬质合金具有较高的硬度和耐磨性能,适用于冲压工作中的耐磨部位。
3.高速钢:高速钢具有较高的硬度和耐热性能,适用于高速冲压工作。
四、冲压模具的加工工艺冲压模具的加工工艺包括数控机床加工、表面处理和热处理等过程。
1.数控机床加工:数控机床加工是冲压模具制造中的重要环节,通过数控机床可以实现模具的高精度加工。
2.表面处理:表面处理是为了提高模具表面的硬度和耐磨性,常见的表面处理方法有硬化、镀铬和涂覆等。
3.热处理:热处理可以改变模具的材料组织结构和力学性能,常见的热处理方法有淬火、回火、正火等。
五、冲压模具的应用领域和发展趋势冲压模具广泛应用于汽车、电子、家电等行业,随着工艺和技术的不断发展,冲压模具的设计、制造和应用也得到了进一步的提升。
冲压模发展现状及未来趋势分析

冲压模发展现状及未来趋势分析摘要:冲压模作为现代制造业中的重要工具,对产品的制造质量和生产效率有着重要影响。
本文分析了冲压模的发展现状,并探讨了未来冲压模技术的趋势和发展方向。
引言:随着制造业的不断发展,冲压成型技术在各个领域中得到了广泛应用。
而冲压模作为冲压工艺的核心,其设计、制造和应用对提高产品质量和生产效率至关重要。
本文将对冲压模的发展现状进行分析,并探讨未来冲压模技术的发展趋势。
一、冲压模的发展现状1. 传统冲压模的应用广泛传统冲压模主要由冲头、模座、导柱、模柄等构成,广泛应用于汽车、电子、通信等领域。
随着这些行业的增长,传统冲压模依然是主要的冲压加工工具。
2. 数字化技术的应用随着计算机技术的发展,数字化技术在冲压模设计和制造中的应用越来越广泛。
CAD/CAM技术的引入使得冲压模的设计更加精确和高效,大大提高了产品质量和生产效率。
3. 模具材料的革新传统的冲压模主要使用高速钢和合金钢材料制造,但随着材料科学的进步,新型材料如硬质合金、粉末冶金材料等开始被广泛应用于冲压模制造中。
这些材料具有高耐磨性、高硬度和高强度等特点,有望进一步提高冲压模的寿命和效率。
二、未来冲压模技术的趋势1. 智能化和自动化未来的冲压模将趋向于智能化和自动化。
通过引入现代传感技术和自动化控制系统,冲压模可以实现自动加载和卸载功能,提高生产效率和降低劳动强度。
同时,智能化的冲压模还可以通过数据采集和分析实现实时监控和故障诊断,提高设备的可靠性和可维护性。
2. 快速工具变更和柔性制造随着市场需求的不断变化,制造企业需要更快地进行产品改型和工具调整。
未来的冲压模将更加注重快速工具变更和柔性制造能力,使厂商能够更加快速地响应市场需求。
3. 制造工艺的改进随着先进制造技术的不断发展,冲压模的制造工艺也在不断改进。
例如,光刻和激光焊接技术的应用将使得冲压模的制造更加精确和高效。
4. 三维打印技术的应用三维打印技术作为一种新兴的制造技术,正在逐渐应用于冲压模的制造过程中。
(完整)冲压模的研究现状及发展方向

冲压模的研究现状及发展方向1 冲压模的研究现状模具制造技术现代化是模具工业发展的基础.计算机技术、信息技术、自动化技术等先进技术正在不断向传统制造技术渗透、交叉、融合形成了现代模具制造技术。
其中高速铣削加工、电火花铣削加工、慢走丝切割加工、精密磨削及抛光技术、数控测量等代表了现代冲模制造的技术水平[1]。
高速铣削加工不但具有加工速度高以及良好的加工精度和表面质量(主轴转速一般为1500040000r/min),加工精度一般可达10微米,最好的表面粗糙度Ra≤1微米),而且与传统切削加工相比具有温升低(工件只升高3摄氏度)、切削力小,因而可加工热敏材料和刚性差的零件,合理选择刀具和切削用量还可实现硬材料(60HRC)加工;电火花铣削加工(又称电火花创成加工)是以高速旋转的简单管状电极作三维或二维轮廓加工(像数控铣一样),因此不再需要制造昂贵的成形电极[2],如日本三菱公司生产的EDSCAN8E电火花铣削加工机床,配置有电极损耗自动补偿系统、CAD/CAM集成系统、在线自动测量系统和动态仿真系统,体现了当今电火花加工机床的技术水平;慢走丝线切割技术的发展水平已相当高,功能也相当完善,自动化程度已达到无人看管运行的程度,目前切割速度已达到300mm /min,加工精度可达±1.5微米,表面粗糙度达Ra=01~0.2微米;精度磨削及抛光已开始使用数控成形磨床、数控光学曲线磨床、数控连续轨迹坐标磨床及自动抛光等先进设备和技术;模具加工过程中的检测技术也取得了很大的发展,现在三坐标测量机除了能高精度地测量复杂曲面的数据外,其良好的温度补偿装置、可靠的抗振保护能力、严密的除尘措施及简单操作步骤,使得现场自动化检测成为可能[3]。
此外,激光快速成形技术(RPM)与树脂浇注技术在快速经济制模技术中得到了成功的应用。
利用RPM 技术快速成形三维原型后,通过陶瓷精铸、电弧涂喷、消失模、熔模等技术可快速制造各种成形模。
- 1、下载文档前请自行甄别文档内容的完整性,平台不提供额外的编辑、内容补充、找答案等附加服务。
- 2、"仅部分预览"的文档,不可在线预览部分如存在完整性等问题,可反馈申请退款(可完整预览的文档不适用该条件!)。
- 3、如文档侵犯您的权益,请联系客服反馈,我们会尽快为您处理(人工客服工作时间:9:00-18:30)。
冲压模的研究现状及发展方向1 冲压模的研究现状模具制造技术现代化是模具工业发展的基础。
计算机技术、信息技术、自动化技术等先进技术正在不断向传统制造技术渗透、交叉、融合形成了现代模具制造技术。
其中高速铣削加工、电火花铣削加工、慢走丝切割加工、精密磨削及抛光技术、数控测量等代表了现代冲模制造的技术水平[1]。
高速铣削加工不但具有加工速度高以及良好的加工精度和表面质量(主轴转速一般为),加工精度一般可达10微米,最好的表面粗糙度Ra≤1微米),而且与传统切削加工相比具有温升低(工件只升高3摄氏度)、切削力小,因而可加工热敏材料和刚性差的零件,合理选择刀具和切削用量还可实现硬材料(60HRC)加工;电火花铣削加工(又称电火花创成加工)是以高速旋转的简单管状电极作三维或二维轮廓加工(像数控铣一样),因此不再需要制造昂贵的成形电极[2],如日本三菱公司生产的EDSCAN8E电火花铣削加工机床,配置有电极损耗自动补偿系统、CAD/CAM集成系统、在线自动测量系统和动态仿真系统,体现了当今电火花加工机床的技术水平;慢走丝线切割技术的发展水平已相当高,功能也相当完善,自动化程度已达到无人看管运行的程度,目前切割速度已达到300mm /min,加工精度可达±微米,表面粗糙度达Ra=01~微米;精度磨削及抛光已开始使用数控成形磨床、数控光学曲线磨床、数控连续轨迹坐标磨床及自动抛光等先进设备和技术;模具加工过程中的检测技术也取得了很大的发展,现在三坐标测量机除了能高精度地测量复杂曲面的数据外,其良好的温度补偿装置、可靠的抗振保护能力、严密的除尘措施及简单操作步骤,使得现场自动化检测成为可能[3]。
此外,激光快速成形技术(RPM)与树脂浇注技术在快速经济制模技术中得到了成功的应用。
利用RPM技术快速成形三维原型后,通过陶瓷精铸、电弧涂喷、消失模、熔模等技术可快速制造各种成形模。
如清华大学开发研制的“M-RPMS-Ⅱ型多功能快速原型制造系统”是我国自主知识产权的世界惟一拥有两种快速成形工艺(分层实体制造SSM和熔融挤压成形7MEM)的系统,它基于“模块化技术集成”之概念而设计和制造,具有较好的价格性能比[4]。
一汽模具制造公司在以CAD/CAM加工的主模型为基础,采用瑞士汽巴精化的高强度树脂浇注成形的树脂冲模应用在国产轿车试制和小批量生产开辟了新的途径[5]。
2 发展方向在冲模的设计制造上,目前正朝着以下两方面发展:一方面,为了适应高速、自动、精密、安全等大批量现代生产的需要,冲模正向高效率、高精度、高寿命及多工位、多功能方向发展,与此相比适应的新型模具材料及其热处理技术,各种高效、精密、数控自动化的模具加工机床和检测设备以及模具CAD/CAM技术也在迅速发展;另一方面,为了适应产品更新换代和试制或小批量生产的需要,锌基合金冲模、聚氨酯橡胶冲模、薄板冲模、钢带冲模、组合冲模等各种简易冲模及其制造技术也得到了迅速发展。
冲压成形理论及冲压工艺方面冲压成形理论的研究是提高冲压技术的基础。
目前,国内外对冲压成形理论的研究非常重视,在材料冲压性能研究、冲压成形过程应力应变分析、板料变形规律研究及坯料与模具之间的相互作用研究等方面均取得了较大的进展。
特别是随着计算机技术的飞跃发展和塑性变形理论的进一步完善,近年来国内外已开始应用塑性成形过程的计算机模拟技术,即利用有限元(FEM)等有值分析方法模拟金属的塑性成形过程,根据分析结果,设计人员可预测某一工艺方案成形的可行性及可能出现的质量问题,并通过在计算机上选择修改相关参数,可实现工艺及模具的优化设计。
这样既节省了昂贵的试模费用,也缩短了制模具周期[6]。
研究推广能提高生产率及产品质量、降低成本和扩大冲压工艺应用范围的各种压新工艺,也是冲压技术的发展方向之一。
目前,国内外相继涌现出精密冲压工艺、软模成形工艺、高能高速成形工艺及无模多点成形工艺等精密、高效、经济的冲压新工艺。
其中,精密冲裁是提高冲裁件质量的有效方法,它扩大了冲压加工范围,目前精密冲裁加工零件的厚度可达25mm,精度可达IT16~17 级[7];用液体、橡胶、聚氨酯等作柔性凸模或凹模的软模成形工艺,能加工出用普通加工方法难以加工的材料和复杂形状的零件,在特定生产条件下具有明显的经济效果;采用爆炸等高能效成形方法对于加工各种尺寸在、形状复杂、批量小、强度高和精度要求较高的板料零件,具有很重要的实用意义[8];利用金属材料的超塑性进行超塑成形,可以用一次成形代替多道普通的冲压成形工序,这对于加工形状复杂和大型板料零件具有突出的优越性;无模多点成形工序是用高度可调的凸模群体代替传统模具进行板料曲面成形的一种先进技术,我国已自主设计制造了具有国际领先水平的无模多点成形设备,解决了多点压机成形法,从而可随意改变变形路径与受力状态,提高了材料的成形极限,同时利用反复成形技术可消除材料内残余应力,实现无回弹成形[9]。
无模多点成形系统以CAD/CAM/CAE 技术为主要手段,能快速经济地实现三维曲面的自动化成形。
冲压设备和冲压生产自动化方面性能良好的冲压设备是提高冲压生产技术水平的基本条件,高精度、高寿命、高效率的冲模需要高精度、高自动化的冲压设备相匹配。
为了满足大批量高速生产的需要,目前冲压设备也由单工位、单功能、低速压力机朝着多工位、多功能、高速和数控方向发展,加之机械乃至机器人的大量使用,使冲压生产效率得到大幅度提高,各式各样的冲压自动线和高速自动压力机纷纷投入使用[10]。
如在数控四边折弯机中送入板料毛坯后,在计算机程序控制下便可依次完成四边弯曲,从而大幅度提高精度和生产率;在高速自动压力机上冲压电机定转子冲片时,一分钟可冲几百片,并能自动叠成定、转子铁芯,生产效率比普通压力机提高几十倍,材料利用率高达97%;公称压力为250KN 的高速压力机的滑块行程次数已达2000次/min 以上[11]。
在多功能压力机方面,日本田公司生产的2000KN“冲压中心”采用CNC 控制,只需5min 时间就可完成自动换模、换料和调整工艺参数等工作;美国惠特尼公司生产的CNC 金属板材加工中心,在相同的时间内,加工冲压件的数量为普通压力机的4~10 倍,并能进行冲孔、分段冲裁、弯曲和拉深等多种作业[12]。
近年来,为了适应市场的激烈竞争,对产品质量的要求越来越高,且其更新换代的周期大为缩短。
冲压生产为适应这一新的要求,开发了多种适合不同批量生产的工艺、设备和模具。
其中,无需设计专用模具、性能先进的转塔数控多工位压力机、激光切割和成形机、CNC 万能折弯机等新设备已投入使用。
特别是近几年来在国外已经发展起来、国内亦开始使用的冲压柔性制造单元(FMC)和冲压柔性制造系统(FMS)代表了冲压生产新的发展趋势。
FMS 系统以数控冲压设备为主体,包括板料、模具、冲压件分类存放系统、自动上料与下料系统,生产过程完全由计算机控制,车间实现24 小时无人控制生产。
同时,根据不同使用要求,可以完成各种冲压工序,甚至焊接、装配等工序,更换新产品方便迅速,冲压件精度也高[13]。
冲压标准化及专业化生产方面模具的标准化及专业化生产,已得到模具行业和广泛重视。
因为冲模属单件小批量生产,冲模零件既具的一定的复杂性和精密性,又具有一定的结构典型性。
因此,只有实现了冲模的标准化,才能使冲模和冲模零件的生产实现专业化、商品化,从而降低模具的成本,提高模具的质量和缩短制造周期[14]。
目前,国外先进工业国家模具标准化生产程度已达70%~80%,模具厂只需设计制造工作零件,大部分模具零件均从标准件厂购买,使生产率大幅度提高。
模具制造厂专业化程度越不定期越高,分工越来越细,如目前有模架厂、顶杆厂、热处理厂等,甚至某些模具厂仅专业化制造某类产品的冲裁模或弯曲模,这样更有利于制造水平的提高和制造周期的缩短[15]。
我国冲模标准化与专业化生产近年来也有较大发展,除反映在标准件专业化生产厂家有较多增加外,标准件品种也有扩展,精度亦有提高。
但总体情况还满足不了模具工业发展的要求,主要体现在标准化程度还不高(一般在40%以下),标准件的品种和规格较少,大多数标准件厂家未形成规模化生产,标准件质量也还存在较多问题[16]。
另外,标准件生产的销售、供货、服务等都还有待于进一步提高。
3 总结目前我国模具工业的发展步伐日益加快,但在整个模具设计制造水平和标准化程度上,与德国、美国、日本的发达国家相比还存在相当大的差距。
存在的问题和差距主要表现在下列5个方面:(1)总量供不应求。
(2)企业组织结构、产品结构、技术结构和进出口结构都不合理。
(3)模具产品水平低很多,生产周期长。
(4)开发能力较差,经济效益较差。
(5)与国际水平相比,模具企业的管理落后。
根据国际生产技术学会提供的资料显示,机械零件粗加工的75%和精加工的50%都将由模具成形来完成。
因此模具被誉为“金属加工中的帝王”,是“进入富裕社会的原动力”、“模具就是黄金”。
在信息化带动工业化发展的今天,在经济全球化趋向日渐加速的情况下,我国冲压模具必须尽快提高水平。
通过改革与发展,采取各种有效措施,在冲压模具行业全体职工的共同努力奋斗之下,我国冲压模具也一定会不断提高水平,逐渐缩小与世界先进水平的差距。
“十一五”期间,在科学发展观指导下,不断提高自主开发能力、重视创新、坚持改革开放、走新型工业化道路,将速度效益型的增长模式逐步转变到质量和水平效益型轨道上来,我国的冲压模具的水平也必然会更上一层楼。
参考文献[1] 张毅. 现代冲压技术[M]. 北京: 国防工业出版社, 1994,21-26.[2] 陈炎嗣, 郭景仪. 冲压模具设计与制造技术[M]. 北京: 北京出版社, 1991,45-50.[3] 陈孝康, 陈炎嗣, 周兴隆. 实用模具技术手册[M]. 北京: 中国轻工业出版社,2001,32-36.[4] 许发樾. 实用模具设计与制造手册[M]. 北京: 机械工业出版社, 2001,76-80.[5] “模具实用技术丛书”编委会. 冲模设计应用实例[M]. 北京: 机械工业出版社,1999,46-48.[6] 周大隽, 等. 冲模结构设计要领与范例[M]. 北京: 机械工业出版社,2006,56-58.[7] 赵昌盛. 实用模具材料应用手册[M]. 北京: 机械工业出版社, 2005,47-51.[8]Zone-Ching Lin , Chun-Yao Hsu . An Investigation of an Expert System for Shearing CutProgressive Die Design . Taiwan: National Taiwan Institute of Technology,,87-92.[9] 李焕芳. 冷冲压模具发展现状[J]. 中国高新技术企业, 2010, 27(9): 26-30.[10][11] 余银柱, 赵跃文. 冲压工艺与模具设计[M]. 北京: 北京大学出版社, 2005,35-41.[12] 薛啓翔. 冷冲压实用技术[M]. 北京: 机械工业出版社, 2006,91-95.[13] 陈炎嗣. 冲压模具设计与制造技术[M]. 北京: 北京出版社, 1994,48-53.[14] 曹立文, 王冬, 丁海娟, 郭世清. 新编实用冲压模具设计手册[M]. 人民邮电出版社, 2007,33-37.[15] 张春水. 高效精密冲模设计与制造[M]. 西安: 电子科技大学出版社, 1989,41-46.[16] 余最康, 陆子茹. 冷冲压模具设计与制造[M]. 南京: 江苏科学技术出版社,1983,58-66.。