机床设计主传动系设计解析
精密机床主传动变速系统的设计
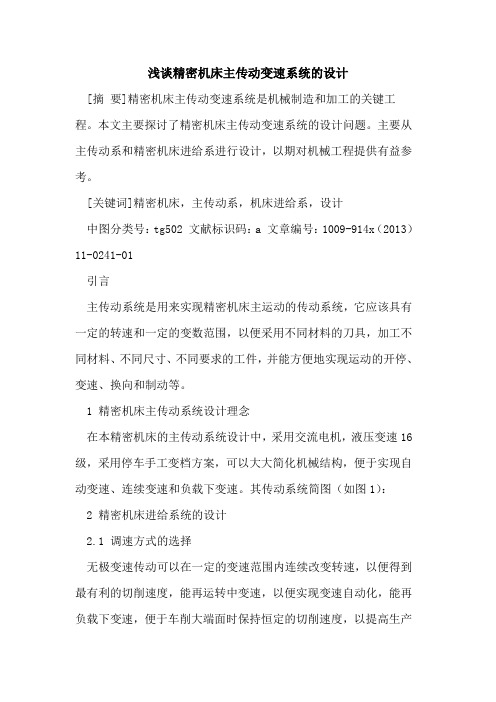
浅谈精密机床主传动变速系统的设计[摘要]精密机床主传动变速系统是机械制造和加工的关键工程。
本文主要探讨了精密机床主传动变速系统的设计问题。
主要从主传动系和精密机床进给系进行设计,以期对机械工程提供有益参考。
[关键词]精密机床,主传动系,机床进给系,设计中图分类号:tg502 文献标识码:a 文章编号:1009-914x(2013)11-0241-01引言主传动系统是用来实现精密机床主运动的传动系统,它应该具有一定的转速和一定的变数范围,以便采用不同材料的刀具,加工不同材料、不同尺寸、不同要求的工件,并能方便地实现运动的开停、变速、换向和制动等。
1 精密机床主传动系统设计理念在本精密机床的主传动系统设计中,采用交流电机,液压变速16级,采用停车手工变档方案,可以大大简化机械结构,便于实现自动变速、连续变速和负载下变速。
其传动系统简图(如图1):2 精密机床进给系统的设计2.1 调速方式的选择无极变速传动可以在一定的变速范围内连续改变转速,以便得到最有利的切削速度,能再运转中变速,以便实现变速自动化,能再负载下变速,便于车削大端面时保持恒定的切削速度,以提高生产效率和加工质量。
精密机床上常用的无级变速机构为直流或交流调速电动机。
交流电机体积小,转动惯量小,动态响应快,没有电刷,磨损和故障少,在中,小功率领域应用广泛。
直流调速在控制力度和精度上比交流变频调速要好,在大功率和低速工作场合,调速性能更稳定,考虑到此次改造为大功率,大扭矩加工精密机床,常在低速下运行,故此次选择直流无级调速。
2.2 伺服进给系统设计数控精密机床的伺服进给系统由伺服驱动电路,伺服驱动装置,机械传动机构及执行部件组成。
它的作用是接受数控系统发出的进给速度和位移指令信号,由伺服驱动电路做转换和放大后,经伺服驱动装置(直流、交流伺服电机,功率步进电机,电液脉冲马达等)和机械传动机构,驱动精密机床的工作台等执行部件实现工作进给和快速运动。
机床设计-传动系统

转速图的绘制
主传动系统的传动路线表达式:
36
1
主电机 440r / min
φ126 φ256
I
3306 4224
II
42
4222 62
III
60
1380 72
IV(主
轴)
48
主轴的转速计算:
126
n主轴
=
n电机
× 256
×uI-II
×uII-III
×uIII-IV
a
126
n主轴max
=
n电机
× 256
×uI
-II
max
×uII -III max
×uIII-IVmax
126
n主轴min
=
n电机
× 256
×uI
-II
min
×uII -III min
×uIII-IVmin
直接标出转速值 。 注意: 转速格线间距大小并不代表公比ф的
数值大小。
转速图一点三线 转速点——传动轴上的圆点,表示该轴具有的转速。
如轴Ⅳ(主轴)上有12个圆点,表示具有12级转速。
传动线——相邻两轴的相关两个 转速点之间的连线。
传传动比大于1其对数值为正,传 动线向右上倾斜;
应用: 普通机床应用最为广泛的一种变速方式。
变速方式的选择
主传动系统的变速方式分为无级变速和有级变速两种。
(1)有级变速 变速机构——是指在输入轴转速不变的条件下,使输出轴获得不 同转速的传动装置。 有级(或分级)变速机构
➢滑移齿轮变速机构 ➢交换齿轮变速机构 ➢多速电动机 ➢离合器变速机构 ➢摆移变速机构
数控车床的主传动系统设计PPT

在进行动态特性分析时,需要考虑主轴的转速、转矩和刚度等参数,以及传动系统的固有频率和阻尼比等特性。 通过分析这些参数,可以评估主传动系统在加工过程中的稳定性,预测可能出现的振动和噪声问题,并采取相应 的措施进行优化设计。
强度与刚度分析
总结词
强度与刚度分析是评估主传动系统在承受外力和变形时的性能表现,以确保系统的可靠性和稳定性。
总结词:传统设计
详细描述:该实例介绍了一种传统的数控车床主传动系统设计,主要采用齿轮传 动和链传动组合的方式,具有结构简单、可靠性高的优点,但效率较低,适用于 一般加工需求。
实例二:主传动系统的改进设计
总结词:优化设计
详细描述:该实例针对传统主传动系统的不足,进行了优化改进。采用新型轴承和材料,提高了传动效率和稳定性,减少了 维护成本,适用于高精度、高效率的加工需求。
设计目的和意义
设计目的
设计出高效、稳定、可靠的数控车床主传动系统,满足加工精度和效率的要求, 提高生产效率和产品质量。
意义
主传动系统设计的优劣直接影响到数控车床的性能和加工精度,进而影响到整个 机械制造行业的生产水平和产品质量。因此,对数控车床主传动系统进行合理设 计,对于提高机械制造行业的整体水平具有重要意义。
要点二
详细描述
在进行热特性分析时,需要考虑主轴的转速、切削力和材 料导热系数等参数。通过建立热传导模型,可以预测主传 动系统在不同工况下的温度变化和热变形情况。根据分析 结果,可以采取相应的散热措施和热补偿技术,提高系统 的热稳定性和加工精度。
06 主传动系统实例分析
实例一:某型号数控车床主传动系统设计
高耐磨材料
选用高耐磨材料,如陶瓷和硬质 合金,以提高主传动系统的使用 寿命和可靠性,减少维护成本。
机床主传动系统设计

机床主传动系统设计机床主传动系统是机床的核心组成部分,它直接影响着机床的性能和加工质量。
主传动系统主要由电机、速度变换机构、主轴、传动装置等部分组成。
本文将从设计电机、速度变换机构、主轴和传动装置四个方面,对机床主传动系统的设计进行详细阐述。
首先是电机的设计。
电机作为机床主传动系统的动力源,其选型需考虑到机床加工的要求以及传动系统的性能要求。
一般情况下,机床加工精度要求高,所以应选择具有较高功率和较小扭矩波动的交流伺服电机。
考虑到机床的节能要求,可选择带有高效能力推力轴承和电子换向器的永磁同步电机。
其次是速度变换机构的设计。
速度变换机构主要用于实现不同速度的转换,使得机床能够适应不同加工工艺的要求。
常见的速度变换机构有齿轮传动、带式传动和链条传动等。
在实际设计中,应根据机床的加工要求和工艺特点选择合适的速度变换机构,并根据机械原理进行优化设计。
第三是主轴的设计。
主轴作为机床主传动系统的核心部件,其设计要考虑到机床的加工精度、刚性和动平衡等要求。
一般情况下,主轴采用高精度两端支撑方式,以保证主轴的刚性和稳定性。
在主轴的设计中,还应注意对主轴进行合理的冷却和润滑方式设计,以提高主轴的使用寿命和可靠性。
最后是传动装置的设计。
传动装置作为主传动系统的连接组件,其设计应满足机床的传动效率、刚性和减振要求。
常见的传动装置有皮带传动、齿轮传动和液压传动等。
对于机床主传动系统设计,可以根据机床的加工特点和需求,选用合适的传动装置进行设计,并通过结构优化和改进,提高传动效率和减少传动误差。
综上所述,机床主传动系统的设计需要综合考虑电机、速度变换机构、主轴和传动装置等多个方面因素。
在设计过程中,应根据机床的加工要求和工艺特点,选择合适的组件和参数,并进行优化设计,以提高机床的性能和加工质量。
只有设计出合理、可靠的主传动系统,机床才能够发挥其最大的潜力,达到高精度、高效率的加工效果。
机床主传动设计
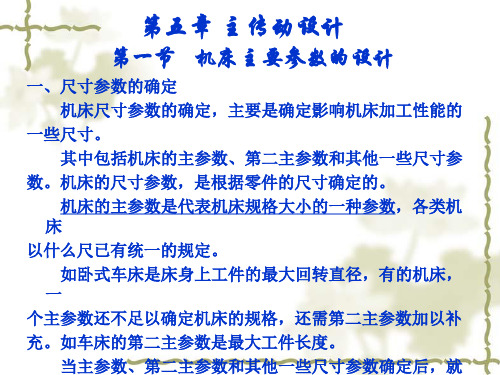
通用机床是为适应多种零件加工而设计制造的,主轴需 要变速。因此需确定它的变速范围,即最低与最高转速。
1).主轴最低(nmin)和最高转速(nmax)的确定
根据公式有:
nm in
1000 vm in
d m ax
nm ax
1000 vmax
2 、主电动机和传动机构须能供给和传递足够的功率和扭 矩,并具有较高的传动效率。
3、执行件(如主轴组件)须有足够的精度、刚度、抗振 性和小于许可限度的热变形和温升。
4 、噪声应在允许的范围内。 5、 操纵要轻便灵活、迅速、安全可靠,并须便于调整和 维修。 6 、结构简单、润滑与密封良好,便于加工和装配,成本 低。
此表不仅可用于转速、双行程数和进给量数列,而且也可用于机床 尺寸和功率参数等数列。表中的数列应优先选用。
图 7 1
3、公比的选用 a.对于通用机床,为使转速损失不过大,机床结构又不过于
复杂,一般取Ф=1.26或1.41。
b.对于大批量生产用的专用机床,自动化机床公比应取小些, 这些机床的生产率高,转速损失的影响显著,一般取 Ф=1.12或1.26
dm in
nmax和nmin的比值是变速范围Rn:
Rn nm ax nm in
注意:dmax和dmin不是机床上可能加工的最大和最小直径, 而是经济加工的最大和最小直径 (即不是理论上的最大和 最小直径),通常可取dmax= KD ; dmin=Rd dmax
最大加工直径dmax =( 0.5-0.6)D 最小加工直径dmin=(0.2-0.25)dmax
例:
以Ø 400mm普通车床为例,计算其主轴的极限转速。 (1)计算主轴最高转速nmax:
机床主传动设计第八讲
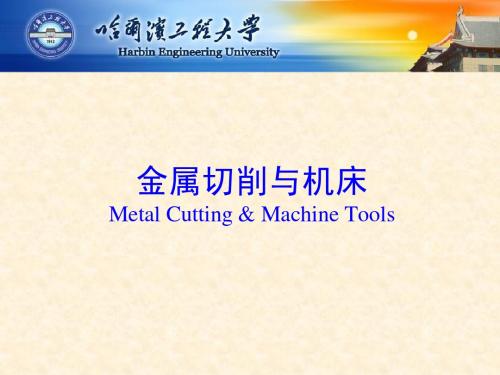
2. 滑移齿轮变速机构
优点:变速范围大,变速级数也较多;在较大的变速范 围内可传递较大的功率和扭矩;因而空载功率损失较小等。 缺点:变速箱的构造复杂,不能在运转中变速,为使滑 移齿轮容易进入啮合,多用直齿圆柱齿轮传动,传动平稳性 不如斜齿轮传动等。
Metal Cutting & Machine Tools
Metal Cutting & Machine Tools
切削机床主传动方案选择
二、变速方式选择 3. 离合器变速机构
安排离合器的位臵应注意以下几个方面: 1)尽量减小离合器的尺寸;
2)避免出现超速现象;
3)要考虑到结构上的因素; 4)各种变速机构的组合;
Metal Cutting & Machine Tools
Metal Cutting & Machine Tools
切削机床主传动方案选择
四、制动方式选择
2. 机械制动
1)闸带式制动器 结构简单,轴向尺寸小,操纵杠杆应作用于闸带的松边 ,使操纵力小且制动平稳。但制动时闸轮受到较大的单侧压力 ,对所在传动轴有不良影响,故用于中小型机床。
Metal Cutting & Machine Tools
nmin
1000 vmin d max
nmax
1000 vmax d min
nmax和nmin的比值是变速范围Rn:
nmax Rn nmin
Metal Cutting & Machine Tools
切削机床主传动参数拟定
2) 主轴转速数列 目前,在机床中应用最广泛的还是有级变速,极限转速 确定后,还需确定中间转速。 如某机床的分级变速机构共有Z 级,其中n1=nmin,nz=nmax ,Z 级转速分别为:n1,n2,n3,……, nj, nj+1,……,nz. 如果加工某一工件所需要的最有利的切削速度为v ,则相 应的转速位n。通常,分级变速机构不能恰好得到这个转速, 而是处于某两极转速 nj与nj+1之间:
第3章数控机床主传动系统设计

3.3无级变速传动链的设计
数控机床的主运动广泛采用无级变速 。 无级变速优势: 在一定范围内,转速(或速度)能连续地变 换,从而获取最有利的切削速度。 数控机床一般都采用由直流或调速电动 机作为驱动源的电气无级调速。
(2)主要设计内容:
拟定结构式或结构网; 拟定转速图, 拟定各传动副的传动比; 确定带轮直径、齿轮齿数; 布置、排列齿轮,绘制传动系统图。
3. 2 分级变速主传动系统设计
3. 2. 1转速图的概念
转速图由“三线一点”组成,即传动轴线、转速 线、传动线和转速点。
3. 2 分级变速主传动系统设计
由Z, φ, n1可知主轴的各级转速应为: 31.5, 45, 63, 90, 125, 180, 250,500、710、 1000、1400。
2)变速组和传动副数的确定 :
变速组和传动副数可能的方案有: 12=4×3 12=3×4 12=3×2×2 12=2×3×2 12=2×2×3
3. 2 分级变速主传动系统设计
②绘制转速图: A、 本例所选定的结构式共有三个变速 组,变速机构共需4根轴,加上电动机轴 共5根轴,(电动机到I轴为定比带传动)故 转速图需5条竖线。主轴共12级转速,电 动机轴转速与主轴最高转速相近,故需 12条横线。然后,标注主轴的各级转速 及电动机轴的转速。
3. 1 主传动系统设计概述
(2)按传动装置类型 可分为机械传动装置 液压传动装置 电气传动装置 以及它们的组合
3. 1 主传动系统设计概述
(3)按变速的连续性 可以分为分级变速传动和无级变速传动。 分级变速传动是在一定的变速范围内均 匀、离散地分布着有限级数的转速,变 速级数一般不超过20~30级。 分级变速传动方式有滑移齿轮变速、交 换齿轮变速和离合器(如摩擦片式、牙嵌 式、齿轮式离合器)变速。
机械制造装备设计课程设计-机床主传动系统设计
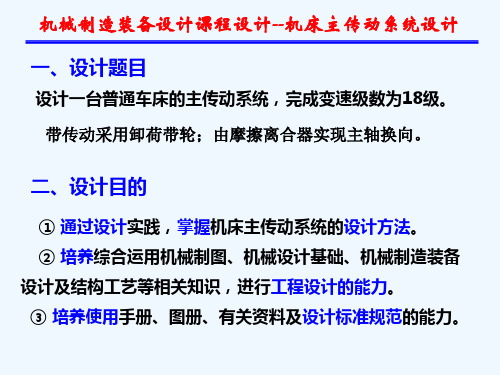
nm in
nj
n nmax
机械制造装备设计课程设计--机床主传动系统设计
计算转速的确定 (1)等比传动,中型通用机床(C6132、C6140)
z 1
nj nmin 3
(2)等比传动,大型通用机床
z
nj nmin 3
总级数
机床类
9
中型
n3
大型
n4
12
16
18 20
n4
n5
n6
n7
n5
机床 C6140 C6132
功率(KW)
7.5 3.0
机床 Z3040 Z3063
功率(KW) 机床
3.0
X62、63
5.5
X63W
功率(KW) 7.5 10.0
机械制造装备设计课程设计--机床主传动系统设计
2. 主轴的估算
在设计之初,由于确定的仅仅是一个设计方案,具体构造尚 未确定,因此,只能根据统计资料,初步确定出主轴的直径。
4、编写设计计算说明书 主要包括: 1)运动设计和动力计算的计算过程和分析; 2)结构设计说明(包括主要结构的分析以及其他需要说明 或论证的问题); 3)参考文献
机械制造装备设计课程设计--机床主传动系统设计
四、课程设计的步骤和注意事项
1、准备工作 2、运动设计
① 传动方案设计(集中传动或分离式传动); ② 结构式; ③ 绘制转速图; ④ 确定齿轮齿数; ⑤ 绘制传动系统图; ⑥ 带和带轮的设计计算;
lg
Rn :变速范围
Rn
n max n min
例:已知 n45~20r0p0m 1.41
z lR g n 1 lg 2( 0 4 0 ) 5 1 0 1.9 0 8 1 1.9 1 8 12
- 1、下载文档前请自行甄别文档内容的完整性,平台不提供额外的编辑、内容补充、找答案等附加服务。
- 2、"仅部分预览"的文档,不可在线预览部分如存在完整性等问题,可反馈申请退款(可完整预览的文档不适用该条件!)。
- 3、如文档侵犯您的权益,请联系客服反馈,我们会尽快为您处理(人工客服工作时间:9:00-18:30)。
2.3.2 主传动系分类和传动方式 (一)主传动系分类:可按不同特征分类
1.按驱动主运动的电动机类型: 交流电动机、直流电动机;
2.按传动装置类型:机械传动装置、液压传动 装置、电气传动装置及其组合;
3.按变速的连续性:★ 无级变速传动、有级(分级)变速传动
(1)无级变速传动: 在一定速度(或转速)范围内能连续、任意改变 速度 (或转速)。
(1)确定变速组的个数和传动副数 可采用双联、三联、或四联滑移齿轮变速组。
(2)确定传动顺序方案:各变速组在传动链中先后顺序。 一般根据传动副“前多后少”原则; 结构或使用上特殊要求可采用其它传动顺序方案。
(3)确定扩大顺序方案: 各变速组的级比指数由小到大的排列顺序。 一般根据变速组的“扩大顺序与传动顺序相一致” 原则; 采用其它扩大顺序方案,应进行分析比较。
22
62
X1 P0 3
P1 2
60
R2
uc1 uc2
301.416 X2(P21)
18
72
X2P0P16
P2 2
R n R 0 R 1 R 2 R j 1 .42 1 1 .43 1 1 .46 1 n n m m a i1 n 3 x.5 4 1 4 05 0
2.齿轮变速组传动比和变速范围限制
③电气无级变速器 采用直流或交流调速电动机来实现变速。主要用于数控机床、精密和大型机床。可 以与机械分级变速装置串联使用。
◆直流调速电动机——采用调压和调磁方式来得到主轴所需要的转速: 恒功率调速段——额定转速到最高转速之间是用调节磁场的方式实现调速; 恒转矩调速段——最低转速到额定转速之间是用调节电枢电压的方式实现调速。
◆交流调速电动机——通常采用变频调速方式进行调速。调速性能好、效率高,调速范围 宽,结构上无电刷和换向器。
(2)有级变速传动通用机床 在若干固定速度(或转速)级内不连续变速。
①传递功率大; ②变速范围大; ③传动比准确,工作可靠; ④有速度损失,传动平稳性↓。
◆实现有级变速的装置或机构 ①滑移齿轮变速:多采用双联和三联滑移齿轮 。
③多速电动机变速: 双速或三速交流异步电动机实现变速。
◆能在运转中变速; ◆变速箱结构简单; ◆在高、低速时输出功率不同,按低速小功率选用电动机,高速大功率不能完全发挥能力; ◆体积大,价格高。
④离合器变速: ◆牙嵌式离合器或齿轮式离合器
变速机构为斜齿、人字型圆柱齿轮或重型机床的传动齿轮大而重用。 ◇结构简单,轴向尺寸小; ◇不打滑,传动比准确; ◇能传递较大转矩; ◇不能在运转中变速。
Z ( P a ) X a ( P b ) X b ( P c ) X c ( P i) X i
结构式与转速图的区别: ① 转速图表达变速特性更具体、完整,转
速和传动比是绝对值; ② 结构式表达变速特性较简单、直观,转
速和传动比是相对数值;
(二)变速组变速范围和极限传动比 1.变速组的变速范围: 变速组中最大传动比与最小传动比的比值,
※级比指数规律:→基型变速系统变速规律
◇基本组的级比指数
(且必须为1);
◇任一扩大组的级比指数
, X 0, 1
且
Xi 1
i 1,2
Xi P0P 1P2..P i.1
2.结构式 用数学表达式表示传动系统的传动关系。
◆ 作用: 主轴转速级数;各变速组的传动副数; 各变速组级比指数;传动顺序。
◆ 一般表达式:
分离传动主变速传动系统图
2.3.3 有级(分级)变速主传动系的设计 拟定结构式、转速图
确定各传动副的传动比 确定带轮直径、齿轮齿数 布置、排列齿轮——绘制传动系统图
(一)拟定转速图和结构式 1.转速图(三线一点图)
分析和设计分级主传动系统的工具。 ◆作用: 传动轴数目及传动轴之间的传递关系; 主轴的各级转速值及其传动路线; 各传动轴的转速分级和转速值; 各传动副的传动比。
◇对传动比限制
☆降速传动:
→避免从动齿轮过大,增加箱体径向尺寸;
u 14 ☆升速传动:
min
直齿轮→避免扩大传动误差,减少振动和噪声;
斜齿轮→避免扩大传动误差,减少振动和噪声。
umax 2 umax2.5
◇ 对变速组变速范围限制 →最后扩大组的变速范围
Rj
R jX j(p j 1 )p 0 p 1 p 2 p j 1 (p j 1 ) 2 0 ~ .2 2 .5 5 8 ~ 10
◆片式摩擦离合器:用于自动或半自动机床。 ◇可实现运转中变速,接合平稳,冲击小; ◇结构较复杂,摩擦片间有相对滑动,发热较大。
(二)主传动系的传动方式 1.集中传动方式 主传动系的全部传动和变速机构集中装在同一个主轴箱内。→普通精度的通用机床 ☆结构紧凑,便于实现集中操作; ☆箱体数量少,安装、调整方便; ☆传动件的振动和发热直接影响主轴的工作精 度,↓加工质量。
(三)主变速传动系设计的一般原则 →减小传动件结构尺寸
主传传 递动功系率属一T 于定恒时 功,9 率↑传传动动5 件。转n P 5 速c, 0↓传9递转5矩, 5 ↓结P n 构E 0 c件尺(寸N 。m )
1.变速组传动副“前多后少” 原则 主变速系统从电机→主轴总趋势为降速传动,传动链前面的转速较高,当传递功率一
12312326
12322126
二种12级转速的转速图
3.变速组的降速要“前慢后快”的原则
u u u ◇保证中间轴有适当高的转速,当传递功率一 a min b min c min 定, T↓,↓传动件的尺寸;
◇中间轴最高转速≤电机转速, →振动、发热、噪声。
(四)结构式与转速图拟定 1.结构式拟定
ua3
24 1 1
48 1.412 2
② 一个主动转速点引出的传动线数目表示该变速 组不同传动比的传动副数。
③ 两条传动轴格线间相互平行的传动线表示同一 传动副的传动比。
◆变速规律(级比指数规律) ☆基型变速系统(常规变速传动系统): 以单速电动机驱动,由若干个变速组串联起来的、 使主轴得到既不重复又排列均匀的等比数列的变速 系统。 ☆变速组的级比: 变速组中相邻两传动比比值(大于1); ☆级比指数: 级比值的指数,即组内相邻两传动线拉开格数。
(4)检验最后扩大组的变速范围
(5)写出结构式
R 8~ 10 X j(p j 1 )
p 0p 1p 2 (p j 1 )
j
2.转速图拟定 ◇确定V带传动∶Ⅰ轴转速不能过低(结构尺寸);
Ⅰ轴转速不能过高(振动、噪声)。 ◇画转速图格线∶传动轴格线、转速格线、转速点。 ◇分配传动比∶
①传动线的高差表明传动比的数值。 ■传动线的倾斜程度反映传动比的大小:
水平传动线─等速传动,1; 向下方倾斜的传动线─降速传动,u<1; 向上方倾斜的传动线─升速传动,u>1。
■ 传动比数值用传动线的高差来表示(从动转速点与 主动转速点相差格数):
36 1
ua1 3610
30 1 1
ua2
42 1.41
定时,↑传动件转速 ,↓传递转矩,↓结构件尺寸。
p a p b p c p j
2.传动顺序与扩大顺序相一致原则 →变速组传动线“前紧后松”或“前密后疏” 传动顺序依次为基本组、第一扩大组、第二 扩大组、……,↑中间轴转速。
例如:
图(a)
图(b)
传递同转矩X ,0( b)X 结1 构 尺寸X 大2 。 X j
X1 3
第一扩大组:
在基本组基础上,该变速组起到第一次扩大变速作用。
□第一扩大变速特性:
级比指数等于基本组传动副 数 动副数。
,相邻两条传动线拉开的格数,等于基本组的传
X1 P0
③第二扩大组的变速特性
变速组c 级比
级比指数
uc1
6022
30
uc2
18 72
(二)组成
动力源 定比传动机构
变速装置 主轴部件 开停装置 制动装置 换向装置 操纵机构 润滑和密封装置
箱体
齿轮变速机构
多速电动机变 速 、离合器变速
机械无极变速 液压无极变速
滑移齿轮 交换齿轮
(三)主传动系设计的基本要求 1.使用性能要求 2.传递动力要求 3.工作性能要求 4.经济性的要求 5.调整维修方便;结构简单紧凑;便于加工和装配。
机床设计主传动系设计解析
1
2.3 机床主传动系设计
2.3.1 主传动系统功用、组成及设计要求 2.3.2 主传动系分类和传动方式 2.3.3 有级变速主传动系的设计 2.3.4 无级变速主传动系的设计
2.3.1 主传动系统功用、组成及设计要求 (一)功用 实现机床主运动,属于外联系传动链。
1.动力源→执行件(主轴、工作台); 2.保证执行件具有一定的转速或速度和足够的转速范围; 3.实现主运动的开停、变速、换向和制动。
如图所示:将传动系统中的三个变速组,按 运动顺序分别称为变速组a、b、c: ①基本组变速特性 变速组a:三个传动比是公比为 的等比数列,即
ua1
361 36
1
0
30 1 1
ua2
42 1.41
ua3
24 1 1
48 1.412 2
使Ⅱ轴得到三级转速(355、500、710)均相差一格,
在其它变速组不改变传动比的条件下,使主轴得到三级
特点: ◆变速范围大,变速级数多; ◆变速方便又节省时间; ◆在较大的变速范围内可传递较大功率和转矩; ◆不工作的齿轮不啮合,空载功率损失较小; ◆变速结构较复杂; ◆采用直齿圆柱齿轮,承载能力、传动平稳性差; ◆不能在运转中变速。
②交换齿轮变速 ◆结构简单,不用操纵机构; ◆轴向尺寸小,变速箱结构紧凑; ◆主动、被动齿轮对调使用,齿轮数量少; ◆更换齿轮费时费力; ◆装于悬臂轴端、箱体外,刚性差,润滑困难。