产品测试控制程序
产品检验控制程序

1 目的为验证原材料、半成品、成品的质量特性是否符合规定要求,确保经查验合格的原材料、半成品、成品投入使用。
2 适用范围适用于进料、制程及最终成品的查验。
3 职责3.1仓库负责原材料、半成品、成品的入库及储存,并负责对来料送检以及储存时间超过3个月的半成品、成品出货前进行送检。
3.2 出产部负责在成品的出产控制、查验,出产的半成品/成品的送检。
3.3 品质部负责进料、制程、成品查验,品质稽核及品质查验尺度的制订。
3.4 技术部负责制订原材料、在成品、半成品/成品接收尺度,查验过程中的技术撑持和协助。
3.5 采购负责原材料不良时与供应商的联络与处置。
4 名词术语4.1 查验:通过不雅察和判断,适当时结合测量、试验所进行的符合性评价。
4.2 进料查验:对采购的原材料、配套件和委外加工件入厂时的查验。
4.3 制程查验:指为防止不合格品流入下道工序,而对各道工序加工的产物及影响产物质量的主要工序所进行的查验。
4.4 最终查验:是指在出产全部工序结束后,对其出产的半成品或成品的查验。
4.5 特采:质量不完全符合尺度的原材料或器件,其缺陷不合错误最终产物质量发生决定性影响,经技术部和相关部分评估风险后,或征得客户定见,同意采用选别、让步接收等方法进行处置。
4.6 原材料:指出产过程所需要的原料,包罗主要材料、辅助材料、外购半成品、委外加工半成品、补缀用备件、包装材料等。
4.7 在成品:从一个出产工序转给另一个出产工序继续加工的便宜半成品以及不克不及单独计算成本的便宜半成品。
4.8 半成品:指颠末必然出产过程并已查验合格,但尚未制造完工成为成品,仍需进一步加工的中间产物。
4.9 成品:指已完成全部出产过程,按规定尺度查验合格,可供发卖的产物。
4.10 紧急放行:出产急需来不及验证就发放出产部使用。
5 作业程序5.1 进料点收、送检:委外/供应厂商交货时仓管直接带供应商将货交至“暂收区〞,并需随货附送货单,仓库依本公司物料需求单之规格、数量点收,查对无误后在供应商送货单上盖本公司“暂收专用章〞交还送货供应商做暂收动作,填写来料送检单转品质部查验。
XP-QP-15 产品检验控制程序
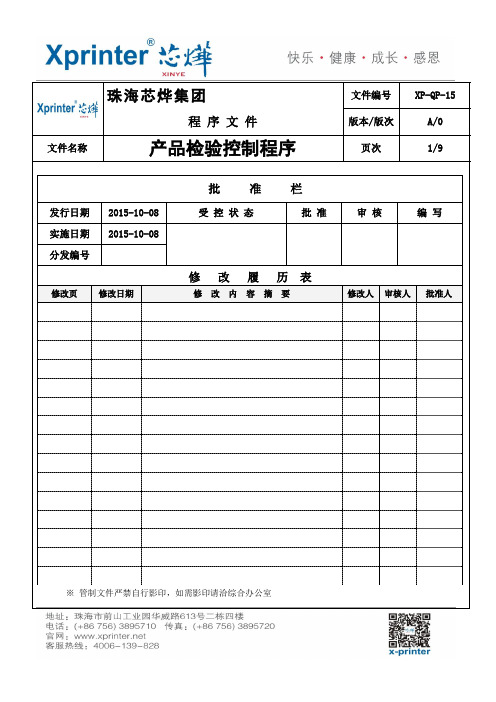
※ 管制文件严禁自行影印,如需影印请洽综合办公室珠海芯烨集团程 序 文 件文件编号 XP-QP-15 版本/版次 A/0 文件名称产品检验控制程序页次1/9批 准 栏发行日期 2015-10-08 受 控 状 态批 准 审 核 编 写 实施日期 2015-10-08分发编号修 改 履 历 表修改页修改日期修 改 内 容 摘 要修改人 审核人批准人一、目的:对外购产品、半成品、成品进行规定的检验和试验,防止未经检验和试验的外购产品、半成品、成品投入使用、入库和出货。
二、适用范围:凡本公司产品所用的原材料、辅助材料、包装材料、半成品(外协品)、成品均属之。
三、定义:3.1标准样品:公司生产、品质确定之标准样品或客户确认样品。
3.2不合格品:未满足要求的产品。
产品的要求一般通过质量特性来规定。
成品、半成品、原材料、外购件和外包件对照产品图样、工艺文件、技术标准进行检验和试验,被判定为一个或多个质量特性不符合(未满足)规定要求,统称为不合格品。
3.3产品质量特性:包括但不限于以下方面:a) 安全性;b) 使用要求。
一般指使用功能(含装配功能,功能性外观)、性能指标; c) 非功能性外观。
3.4不合格的严重性分类。
A 类:致命不合格(致命缺陷,英文缩写CR )。
是指产品的关键特性不符合规定要求。
1) 安全特性不合格。
必然造成产品存在安全隐患,如裸露部分有锐利的边缘;安全测试不合格。
2) 关键使用要求不合格。
必然造成产品不能使用,如关键安装孔缺失。
B 类:严重不合格(严重缺陷,英文缩写MA )。
产品的普通使用要求不符合规定要求、或非功能性外观不符合规定要求。
1) 必然造成产品生产困难。
如安装孔错位;安装件严重歪斜。
2) 必然造成产品使用不正常。
如元器件虚焊;电路板短路;外观肮脏或划痕;功能丝印错误。
3) 非功能性外观、涂层或工艺严重不合格。
如外观变形严重;涂层颜色明显同其他部件不匹配;涂层有明显的划痕;非功能性丝印错误。
产品质量控制程序

产品质量控制程序引言概述:在现代制造业中,产品质量是企业生存和发展的基石。
为了确保产品的质量,企业需要建立一套完善的质量控制程序。
本文将介绍产品质量控制程序的五个部分,包括供应商评估、原材料检验、生产过程控制、成品检验和售后服务。
一、供应商评估:1.1 供应商资质审核:企业应对供应商进行资质审核,包括对其生产能力、质量管理体系、技术实力等方面进行评估,确保供应商具备满足产品质量要求的能力。
1.2 供应商质量管理:企业应与供应商建立长期稳定的合作关系,并要求供应商建立质量管理体系,确保其产品符合质量标准。
1.3 供应商绩效评估:企业应定期对供应商进行绩效评估,包括对其产品质量、交货准时性、售后服务等方面进行评估,以便及时调整供应链管理。
二、原材料检验:2.1 来料检验:对进货的原材料进行检验,包括外观、尺寸、化学成分等方面的检测,确保原材料符合质量要求。
2.2 抽样检验:采用抽样检验的方式对原材料进行检验,确保原材料的质量稳定。
2.3 记录和追溯:对原材料进行记录和追溯,确保原材料的质量可追溯,便于后期质量问题的排查和处理。
三、生产过程控制:3.1 工艺控制:制定标准化的工艺流程,对生产过程进行控制,确保产品的质量稳定。
3.2 过程监测:通过设备监控和数据采集,对生产过程进行实时监测,及时发现异常情况并进行调整。
3.3 人员培训:对生产人员进行培训,提高其质量意识和操作技能,确保生产过程的质量可控。
四、成品检验:4.1 外观检验:对成品进行外观检验,包括表面光洁度、尺寸精度等方面的检测,确保成品符合外观要求。
4.2 功能检验:对成品进行功能性能测试,确保成品的功能正常。
4.3 可靠性检验:对成品进行可靠性测试,包括耐久性、可靠性等方面的检测,确保成品的质量可靠。
五、售后服务:5.1 售后反馈:建立售后服务反馈机制,及时收集和处理客户的质量问题反馈。
5.2 售后追踪:对售后服务进行追踪和评估,对质量问题进行分析和改进,提高产品质量和售后服务质量。
产品功能试验控制程序

1.0目的:1.1确保品质性能,依照产品的各种不同规格,制定相应试验与要求,测试产品的品质,提供改进方向等可靠度资料,作为设计改进的参考。
1.2通过化学检测,发现可能不合格产品的缺陷及症结所在,提供设制程改进的参考,使产品可靠度水准能符合品质系统及产品规格要求。
2.0范围:2.1新品开发时的验证:试作品完成时需对其进行杂质含量的确定。
2.2功能性试验:新硅石投入必须对抽取相对应的硅石样本、金属硅样本、磨粉之后的硅粉、酸洗之后的硅粉、成品多晶硅样本进行元素外委的功能性测试。
3.0定义:3.1周期性检测:周期性检测样品的抽取按照相应的控制计划执行。
4.0职责:无。
5.0流程:流程 权责单位 相关说明表单品保部委托单位 ⑴新产品由品保部提出委托试验 ⑵各单位须送外委之样品按实际需求填外部委托申请表(3)研发部之实验样品由研发部送样人员提请相关的检测委托申请表[实验检测委托申请表] [外部检测委托申请表]实验员[实验检测委托申请表] [外部检测委托申请表]实验员 确认有样品的标识、数量实验员 委托单位 [外部检测委托申请单]外委测试管理人员 由外委测试管理人员将外委测试值传递给委托者。
[外部检测委托申请单]实验员相关试验记录表实验员 将测试数据填入[实验检测委托申请表]。
[实验检测委托申请表]实验员 委托单位将测试数值传递给委托者;实验员 文管中心《记录控制程序》6.0内容:6.1试验委托:依据[实验检测委托申请单]和[外部检测委托申请单]进行内委或者外委试验申请。
6.1.1资料查证:实验员依《产品功能试验控制程序》对测试品进行资料的查证,以决定委外测试或内部测试。
6.2测试品确认:样品接收人员依委托内容做测试品确认,如外观不良则判定不合格,并重新知会委托人重试 验 委 托资料查证重新取样NY试验报告委外试验试验结果通知内部试验记录保存测试品确认新取样。
6.3委外试验:6.3.1委外试验的抽样送样单位为供应中心、生产中心、技术中心,其余部门若有送样的必要,则统一经由相应部门完成取样并填写[外部检测委托申请单]。
产品检验控制程序

5.2电缸模组检验规范QS-QCD-02
5.3气缸检验规范QS-QCD-03
6.0相关记录:
6.1产品制程检查表QR-QCD-003
6.2组立检验记录表(首-巡-终)QR-QCD-004
6.3线上检查表QR-QCD-002
6.4来料检测记录表QR-QCD-013
进料检验项目如下:
类别
内容
检验项目
检验频率
检验方式
抽检比率
原材料
铝制品
铁制品
压铸件
尺寸
外观
厂家检验报告
每批
抽检
2%
辅料
橡胶制品
标准件
尺寸
外观
每批
抽检
0.2%
包装辅材
PE袋
气泡膜
纸箱
尺寸
外观
每批
抽检
0.2%
4.2过程检验
4.2.1首检
各组长在批量生产前,须按照图纸要求制作首件,并对首件检查合格后,交生产主管确认OK后,交质检部进行首检。质检部按照图纸对首件检验合格后,在首件签名确认:
4.4:出货时,仓库依据业务的“发货通知单”上规定交期,应提前备料,交送货员带给客户验收。
4.5进料、过程、最终检验过程中应严格按相关要求对产品的性能进行相关测试及试验,并做好相应的检验记录,交品管部主管审核保存。
4.6品管部负责每月对各工序产品质量按工厂有关规定进行统计分析,并负责保存有关记录。
5.0相关文件
4.2.3巡检
4.2.3.1零配件
质检部不定时对各工序进行巡检(每次巡检时间间隔不得大于2小时),并将巡检结果记录于“产品制程检查表QR-QCD-003”中。发现不合格时,检验员立即通知生产单位进行改善,生产的不合格品按《不合格品控制程序QS-QCD-01》处理。
公司质量管理过程和产品的监视和测量控制程序

公司质量管理过程和产品的监视和测量控制程序1. 目的通过对产品实现的必需过程进行监视和测量,以确保满足顾客的要求,对产品特性进行监视和测量,以验证产品符合规定要求。
2.适用范围适用于本公司产品实现过程持续满足预定目标的能力和用于生产的产品进行监视和测量的控制。
3.职责综合部负责对质量管理体系各过程进行监控。
生产部负责产品特性的监控和测量。
4.工作程序4.1过程的监视和测量过程的监视和测量包含对质量管理体系过程活动的监视和测量及对产品实现过程的监视和测量。
4.1.1对质量管理体系过程活动的监视、测量,可采用调查、了解、分析的方法,每年进行一次。
4.1.2对产品实现各过程的监视、测量,根据本公司的实际情况,确定为“焊接、组装、调试”过程进行重点监视和测量。
质检部负责制定焊接、组装、调试的技术规范、测试指标及数据记录等。
4.1.3生产过程的测量和监视a) 生产部门负责使用控制图,对质量形成的关键过程进行测量,对图形数据分布进行趋势分析,明确过程质量和过程实际能力之间的关系,以确定需要采取纠正或预防措施的时机。
b) 当过程产品合格率接近或低于控制下限时,生产部门应及时发出《纠正预防措施实施单》,定出责任部门,对其从人、机、料、法、环等方面分析原因、制定和实施4.2 产品的监视与测量4.2.1综合部编制检验指导书,明确检验点、控制频率、抽样方案、控制项目、监测方法、使用的计量器具设备等。
4.2.2进货验证对购进的材料,仓库管理员核对送货单,确认财产品名、规格数量等无误后,置于待检区或挂上“待检品”牌予以标识和区分。
并填写《送检单》交有关部门检验,具体内容见《采购控制程序》。
4.2.3半成品的监视和测量4.2.3.1对于生产和组装线上的产品,按规定要求设置质量控制点,按规定间隔依检验规程对产品进行监视和测量。
进行检验,经检验合格,在产品上贴上工号标签,对关键过程由检验员进行检验,在产品上贴上检验员工号标签,方可转入下道工序,如不合格则执行《不合格品控制程序》。
产品质量检测控制程序
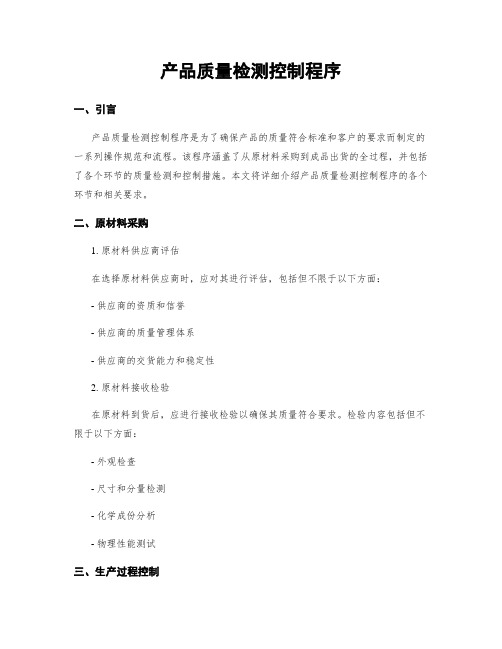
产品质量检测控制程序一、引言产品质量检测控制程序是为了确保产品的质量符合标准和客户的要求而制定的一系列操作规范和流程。
该程序涵盖了从原材料采购到成品出货的全过程,并包括了各个环节的质量检测和控制措施。
本文将详细介绍产品质量检测控制程序的各个环节和相关要求。
二、原材料采购1. 原材料供应商评估在选择原材料供应商时,应对其进行评估,包括但不限于以下方面:- 供应商的资质和信誉- 供应商的质量管理体系- 供应商的交货能力和稳定性2. 原材料接收检验在原材料到货后,应进行接收检验以确保其质量符合要求。
检验内容包括但不限于以下方面:- 外观检查- 尺寸和分量检测- 化学成份分析- 物理性能测试三、生产过程控制1. 设备校验和维护生产设备应定期进行校验和维护,以确保其正常工作和准确性。
2. 生产过程监控生产过程中应进行实时监控,以确保产品符合质量标准。
监控内容包括但不限于以下方面:- 温度和湿度监测- 生产速度和压力监测- 原材料投入量和混合比例监测3. 抽样检验在生产过程中,应定期进行抽样检验,以验证产品的质量。
抽样检验的频率和标准应根据产品的特性和客户的要求确定。
四、成品检验1. 成品外观检查成品应进行外观检查,以确保其外观符合标准和客户的要求。
2. 功能性能测试成品应进行功能性能测试,以确保其满足产品设计和客户的要求。
3. 包装检验成品的包装应进行检验,以确保包装的完整性和符合标准要求。
五、记录和报告1. 质量记录所有的质量检测结果和相关数据应进行记录,包括但不限于以下方面:- 原材料检验记录- 生产过程监控记录- 成品检验记录2. 不合格品处理对于不合格的产品,应制定相应的处理措施,包括但不限于以下方面:- 进行再加工或者修复- 进行退货或者报废- 进行供应商追责3. 质量报告定期向相关部门和管理层提交质量报告,包括但不限于以下方面:- 质量检测结果统计- 不合格品处理情况- 改进措施的实施情况六、培训和改进1. 培训对相关人员进行质量检测和控制方面的培训,以提高其质量意识和技能水平。
GJB9001产品检验和试验控制程序
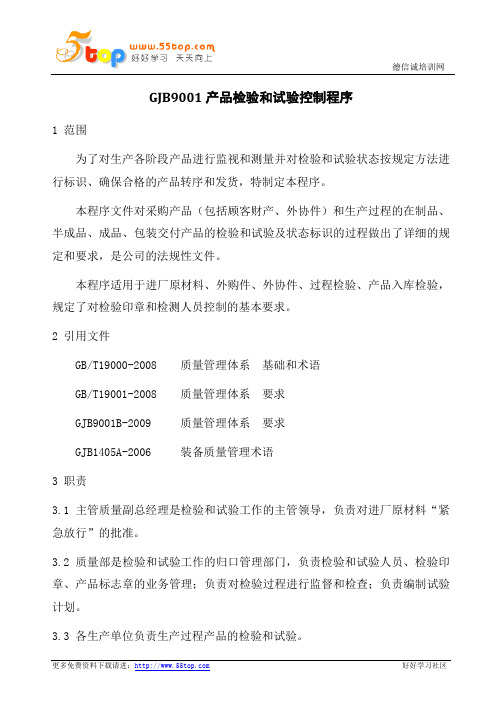
GJB9001产品检验和试验控制程序1 范围为了对生产各阶段产品进行监视和测量并对检验和试验状态按规定方法进行标识、确保合格的产品转序和发货,特制定本程序。
本程序文件对采购产品(包括顾客财产、外协件)和生产过程的在制品、半成品、成品、包装交付产品的检验和试验及状态标识的过程做出了详细的规定和要求,是公司的法规性文件。
本程序适用于进厂原材料、外购件、外协件、过程检验、产品入库检验,规定了对检验印章和检测人员控制的基本要求。
2 引用文件GB/T19000-2008 质量管理体系基础和术语GB/T19001-2008 质量管理体系要求GJB9001B-2009 质量管理体系要求GJB1405A-2006 装备质量管理术语3 职责3.1 主管质量副总经理是检验和试验工作的主管领导,负责对进厂原材料“紧急放行”的批准。
3.2 质量部是检验和试验工作的归口管理部门,负责检验和试验人员、检验印章、产品标志章的业务管理;负责对检验过程进行监督和检查;负责编制试验计划。
3.3 各生产单位负责生产过程产品的检验和试验。
3.4 人力资源部负责对检验和试验人员的培训。
3.5 检验员负责对原材料、外购件、外协件及半成品、成品进行检验,做出判定结论并办理质量证明文件。
当出现重大检验、试验质量事故时检验员有权越级上报主管领导。
3.6 测试人员、理化分析人员负责对原材料、外协件、外购件及生产过程的半成品、成品进行测试、理化分析,做出判定结论并办理质量证明文件。
3.7 检验技术员负责对检验员有争议的判定或误判进行确认或重新判定;负责重大质量问题上报有关领导。
4 控制要求4.1 工作流程4.2 控制要求4.2.1 检验人员、测试人员、理化分析人员,必须经过培训后持证上岗。
4.2.2 检验和试验使用的设备应处于受控状态。
详见《监视和测量设备控制程序》。
4.2.3 生产用的原材料、外协件、外购件、半成品及成品,未经检验或检验不合格不得投入使用(4.5.1.7除外)、转下道工序或交付顾客。
- 1、下载文档前请自行甄别文档内容的完整性,平台不提供额外的编辑、内容补充、找答案等附加服务。
- 2、"仅部分预览"的文档,不可在线预览部分如存在完整性等问题,可反馈申请退款(可完整预览的文档不适用该条件!)。
- 3、如文档侵犯您的权益,请联系客服反馈,我们会尽快为您处理(人工客服工作时间:9:00-18:30)。
产品实现和测试程序
1 目的
对产品及开发的测试实现过程进行规范,保证产品的设计质量。
2 适用范围
适用于公司内所有产品,包括开发任务的下达、软件编码、硬件设计、自测、软硬件联调和试生产活动。
3 职责
3.1 项目负责人
◆按开发计划制定并下达项目任务书。
◆组织项目组成员进行软、硬件设计、自测。
◆提交测试部进行整体测试。
.
3.2 项目组成员进行软、硬件设计、自测,保证完成任务书规定的要求。
3.3 测试部编写测试计划、测试用例,执行联调测试,编写《整体测试报告》、《项目测
试分析报告》。
3.4 当产品包含硬件设计或硬件改动时,总工办负责组织产品试生产、生产工具的测试。
总工办负责提供测试部测试所需的硬件产品。
生产管理部执行产品试生产活动。
4 工作流程
5 工作程序
5.1 项目负责人为每个项目开发人员下达“项目任务书”,规定项目的进度和每个开发人员
的任务进度等,任务书以文件的形式下达。
5.2 编写测试计划和测试用例
测试人员根据产品规范,系统分析报告编写测试计划和测试用例,如果有其他能帮助编写测试计划和测试用例的文档或工具,也应该提供。
5.3 测试计划和测试用例的评审
测试人员编写完测试计划和测试用例后,由评审组人员进行评审,如果评审通过,并且测试所需的其他资源已经准备好,进入联调测试;如果评审没有通过,测试人员修改测试计划和测试用例,直至评审通过。
5.4 软件程序编码、自测
◆软件开发工程师按任务书的要求实现各模块,并编写“开发者指南”、“文件列
表”。
◆“开发者指南”——记录程序开发的环境、模块(部件)号、开发中的难点、
应该注意的问题、模块中已知的缺陷等,这些信息是为后续开发者或维护者
提供方便,所以编写者应从这个角度进行编写。
◆自测——开发人员根据测试部提供的测试用例,编写测试程序,测试程序提
交给项目负责人测试同意后(留下同意记录),开发人员利用测试程序进行
自测;自测发现的BUG开发人员进行修改,修改达到目的后,编写自测报
告,提交给测试部进行联调测试。
◆“文件列表”——是模块的源代码清单,为配置管理员检查源代码是否完整提
供依据。
◆项目负责人应组织编写用户使用说明。
对于在测试过程中使用到的测试程序,由测试部进行确认,填写《测试程序确认报告》,确认通过后,才能用来进行测试。
5.5 硬件设计、自测
当产品涉及硬件设计时,由硬件工程师绘制电路原理图,绘制PCB图,测试、选型元器件,外协加工少量样品后,联合调试驱动、硬件电路,对产品硬件进行测试,发现的bug通过bug追踪系统来进行管理。
硬件工程师负责为软件模块编程人员提供测试通过的硬件样品。
5.6 生产工具的测试
当开发产品中包含硬件时,项目负责人组织编写生产工具。
当编写完生产工具后,项目负责人填写《生产工具测试申请表》连同生产工具及生产工具安装、使用指导(readme文件)提交给总工办,由总工办测试,并留下测试记录,测试通过后,提供给相关部门使用。
5.7 联调测试
◆在测试人员进行测试之前,由测试部检查开发部进行自测的情况,只有自测达
到要求以后,测试部才开始进行联调测试。
◆由项目负责人在管理系统中提交测试申请,由测试人员进行整体测试,及时发
现并修改样品或软件模块中的问题。
发现的bug提交到bug追踪系统中进行
追踪管理。
◆软件和软件联调测试,确保软件和硬件之间的正常通讯及软硬件之间的协调工
作。
◆系统间联调测试,如城管管理系统,bill计费系统和用户端系统之间的联调测
试。
5.8 编写《整体测试报告》、《项目测试分析报告》
测试通过以后,测试人员编写《整体测试报告》、《项目测试分析报告》,评审并提交存档。
5.9 当产品发生较大改动时,及时和相关负责人进行沟通协调,在测试过程中,按照产
品设计对产品提出有益性意见,并对评审后的相关文件及时修改存档。
负责跟踪、记录测试样件测试软件及硬件在测试过程中发生的问题,并形成产品测试分析报告。
5.10 阶段性组织召开产品测试总结会议。
6 相关文件
1) 《产品需求和系统设计控制程序》
2) 《产品开发策划和监控程序》
3) 《配置管理程序》
7 相关质量记录
1) “项目任务书”
2) “开发者指南”
3) “测试计划”
4) “文件列表”
5) “PCB图”
6) “配套明细表”
7) “整体测试报告”
8) “项目测试分析报告”
9) “测试用例”
10) “试生产单”
11) “测试程序确认报告”
12) “评审报告”
13) 出厂检验不合格记录表。