压铸件常见缺陷及解决办法手册-1
压铸件的常见缺陷和解决的对策
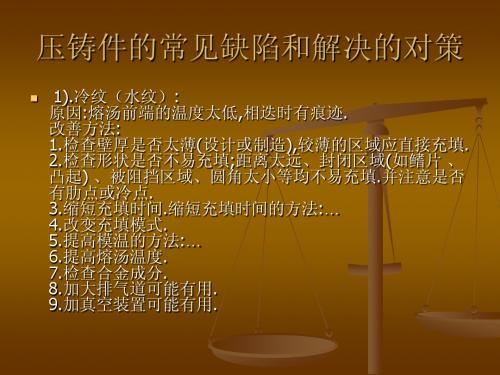
1).冷纹(水纹): 1).冷纹(水纹): 原因:熔汤前端的温度太低,相迭时有痕迹. 原因:熔汤前端的温度太低,相迭时有痕迹. 改善方法: 改善方法: 1.检查壁厚是否太薄(设计或制造),较薄的区域应直接充填. 1.检查壁厚是否太薄(设计或制造),较薄的区域应直接充填. 2.检查形状是否不易充填;距离太远、封闭区域(如鳍片 、 2.检查形状是否不易充填;距离太远、封闭区域( 凸起) 、被阻挡区域、圆角太小等均不易充填. 凸起) 、被阻挡区域、圆角太小等均不易充填.并注意是否 有肋点或冷点. 有肋点或冷点. 3.缩短充填时间.缩短充填时间的方法:… 3.缩短充填时间.缩短充填时间的方法: 4.改变充填模式. 4.改变充填模式. 5.提高模温的方法:… 5.提高模温的方法: 6.提高熔汤温度. 6.提高熔汤温度. 7.检查合金成分. 7.检查合金成分. 8.加大排气道可能有用. 8.加大排气道可能有用. 9.加真空装置可能有用. 9.加真空装置可能有用.
压铸件的常见缺陷和解决的对策
3).气孔(砂孔): 3).气孔(砂孔): 1.空气夹杂在熔汤中. 1.空气夹杂在熔汤中. 2.气体的来源:熔解时、在料管中、在模具中、离型剂. 2.气体的来源:熔解时、在料管中、在模具中、离型剂. 3.压射力不足,材质疏松。 3.压射力不足,材质疏松。 4.模具温度过高,热收缩。 4.模具温度过高,热收缩。 改善方法: 改善方法: 1.适当的慢速. 1.适当的慢速. 2.检查流道转弯是否圆滑,截面积是否渐减. 2.检查流道转弯是否圆滑,截面积是否渐减. 3.检查逃气道面积是否够大,是否有被阻塞,位置是否位于最后充填的 3.检查逃气道面积是否够大,是否有被阻塞, 地方. 地方. 4.检查离型剂是否喷太多,模温是否太低或太高. 4.检查离型剂是否喷太多,模温是否太低或太高. 5.使用真空. 5.使用真空. 6.调整射料压力。 6.调整射料压力。
常见压铸件缺陷解决方法
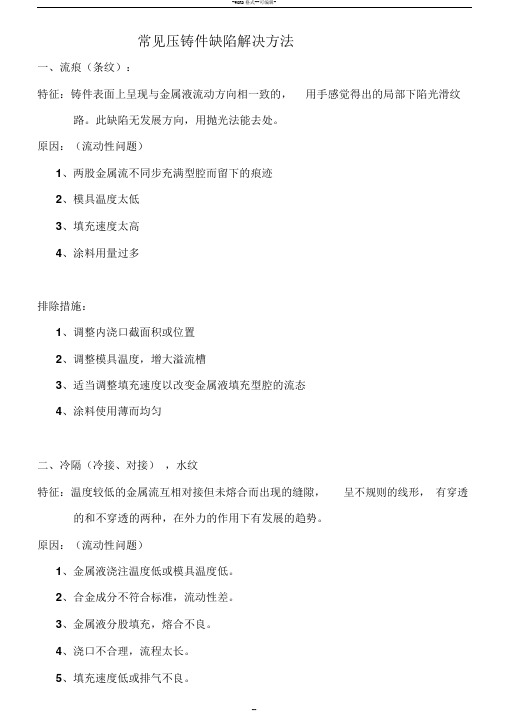
-WORD格式--可编辑-常见压铸件缺陷解决方法一、流痕(条纹):特征:铸件表面上呈现与金属液流动方向相一致的,用手感觉得出的局部下陷光滑纹路。
此缺陷无发展方向,用抛光法能去处。
原因:(流动性问题)1、两股金属流不同步充满型腔而留下的痕迹2、模具温度太低3、填充速度太高4、涂料用量过多排除措施:1、调整内浇口截面积或位置2、调整模具温度,增大溢流槽3、适当调整填充速度以改变金属液填充型腔的流态4、涂料使用薄而均匀二、冷隔(冷接、对接),水纹特征:温度较低的金属流互相对接但未熔合而出现的缝隙,呈不规则的线形,有穿透的和不穿透的两种,在外力的作用下有发展的趋势。
原因:(流动性问题)1、金属液浇注温度低或模具温度低。
2、合金成分不符合标准,流动性差。
3、金属液分股填充,熔合不良。
4、浇口不合理,流程太长。
5、填充速度低或排气不良。
6、比压偏低。
排除措施:1、适当提高浇注温度和模具温度。
2、改变合金成分,提高流动性。
3、改进浇注系统,加大内浇口速度,改善填充条件。
4、改善排溢条件,增大溢流量。
5、提高压射速度,改善排气条件。
6、提高比压三、擦伤(粘模伤痕)特征:顺着脱模方向,由于金属粘附,模具制造斜度太小而造成铸件表面的拉伤痕迹,严重时成为拉伤面。
产生原因:(粘着现象)1、型芯、型壁的铸造斜度太小或出现倒斜度。
2、型芯、型壁有压伤痕。
3、合金粘附模具。
4、铸件顶出偏斜,或型芯轴线偏斜。
5、型壁表面粗糙。
6、涂料常喷涂不到。
7、铝合金中含铁量低于0.6% 。
排除措施:1、修正模具,保证制造斜度。
2、打光压痕。
-WORD格式--可编辑-3、合理设计浇注系统,避免金属流对冲型芯、型壁,适当降低填充速度。
4、修正模具结构。
5、打光表面。
6、涂料用量薄而均匀,不能漏喷涂料。
7、适当增加含铁量至0.6~0.8%。
四、凹陷(缩陷、塌边)特征:铸件平滑表面上出现的凹瘪的部分,其表面呈自然冷却状态。
产生原因:(模具设计、环境问题)1、铸件结构设计不合理,有局部厚实部位,产生热节。
压铸件常见缺陷及解决办法手册
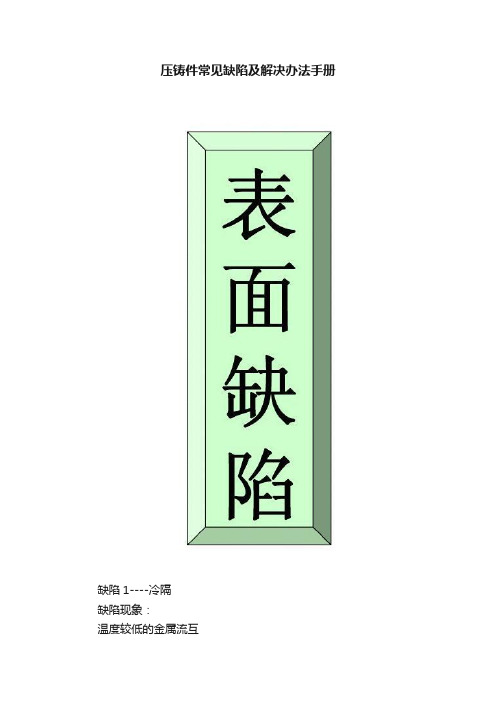
压铸件常见缺陷及解决办法手册缺陷1----冷隔缺陷现象:温度较低的金属流互相对接但未熔合而出现的缝隙,呈不规则的线形,有穿透的和不穿透的两种,在外力的作用下有发展的趋势。
1、产品发黑,伴有流痕。
适当提高浇注温度和模具温度;2、改变合金成分,提高流动性;3、烫模件看铝液流向,金属液碰撞产生冷隔出现一般为涡旋状,伴有流痕。
改进浇注系统,改善内浇口的填充方向。
另外可在铸件边缘开设集渣包以改善填充条件;4、伴有远端压不实。
更改浇口位置和截面积,改善排溢条件,增大溢流量;5、产品发暗,经常伴有表面气泡。
提高压射速度,6、铸件整体压不实。
提高比压(尽量不采用)。
1、金属液浇注温度低或模具温度低;2、合金成分不符合标准,流动性差;3、金属液分股填充,熔合不良;4、浇口不合理,流程太长;5、填充速度低或排气不良;6、压射比压偏低。
分析判断及解决办法产生原因其他名称:冷接(对接)缺陷2----擦伤缺陷现象:顺着脱模方向,由于金属粘附,模具制造斜度太小而造成铸件表面的拉伤痕迹,严重时成为拉伤面甚至产生裂纹。
其他名称:拉伤、拉痕、粘模伤痕缺陷3----欠铸缺陷现象:金属液未充满型腔,铸件上出现填充不完整的部位。
多出现在铸件末端或狭窄深腔处。
其他名称:浇不足、轮廓不清、边角残缺缺陷4----气泡其他名称:鼓泡缺陷现象:铸件表皮下,聚集气体鼓胀所形成的泡,有时会崩裂,存在贯通和非贯通两种。
缺陷5----流痕缺陷现象:首先进入型腔的金属液形成一个极薄而又不完全的金属层后,被后来的金属液所弥补而留下的痕迹。
铸件表面上呈现与金属液流动方向相一致,用手感觉得出局部下陷。
此缺陷无发展方向,用抛光法能去处。
1、涂黑油烫模,能看出金属流的流向和填充顺序。
调整内浇口截面积、位置或填充方向,以达到同步填充的目的;2、用模具测温枪测量模具温度。
调整模具温度至工艺要求范围内;3、产品表面,内浇口处的金属流会出现特亮的部位。
适当调整填充速度以改变金属液填充型腔的流态;4、产品表面发黑,局部会出现涂料堆积现象。
压铸件常见缺陷及改善对策
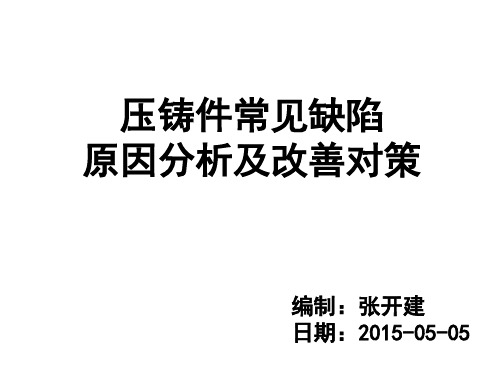
粘模(拉模)-预防措施: 1、修复模具表面损伤部位,修正脱模斜度,提高 模具硬度(HRC45°~48°),提高模具光洁度。 2、调整顶杆,使顶出平衡。 3、更换脱模效果好的脱模剂。 4、调整合金含铁量。 5、降低浇注温度,控制模具温度平稳、平衡。 6、调整内浇口方向,避免金属液直冲型芯、型壁。
龟裂-预防措施: 1、正确选用模具材料及热处理工艺。 2、浇注温度不宜过高,尤其是高熔点的合金。在 能满足生产需求条件下,尽可能选用较低的浇注温度。
3、模具预热要充分和均匀。 4、模具生产到一定模次后进行退火,消除内应力。 5、浇道和型腔表面不定期抛光处理,确保表面光 洁度。
6、合理选择模具冷却方法,确保模具热平衡。
三、气泡图片
缺陷名称:气泡 英文名称: blisters
三、气泡
特征及检验方法:铸件表面有大小不等的隆起, 或有皮下形成空洞。目视可以识别。
产生原因: 1、金属液在压射室充满度过低(控制在45%~70%), 易产生卷气,初压射速度过高。 2、模具浇注系统不合理,排气不良。 3、熔炼温度过高,含气量高,熔液未除气。 4、模具温度过高,留模时间不够,金属凝固时间 不足,强度不够过早开模,受压气体膨胀起来。 5、脱模剂、注射头油用量过多。 6、喷涂后吹气时间过短,模具表面水未吹干。
产生原因: 1、首先进入型腔的金属液形成一个极薄的而又不 完全的金属层后,被后来的金属液所弥补而留下的痕 迹。 2、模具温度过低。 3、内浇口截面积过小及位置不当产生喷溅。 4、作用于金属液上的压力不足。 5、花纹:涂料和注射油用量过多。
压铸件的常见缺陷及预防和解决

第一章压铸件的缺陷特征,产生原因,防止方法名称流痕及花纹网状毛翅脆性裂纹缩孔缩松特征及检查方法外观检查:铸件表面上有与金属液流动方向一致的条纹,有明显可见的与金属基体颜色不一样无方向性的纹路,无发展趋势。
外观检查:压铸件表面上有网状发丝一样凸起或凹陷的痕迹,随压铸次数增加而不断扩大和延伸外观检查或金相检查:合金晶粒粗大或极小,使铸件易断裂或碰碎外观检查:将铸件放在碱性溶液中,裂纹处呈暗灰色金属基体的破坏与裂开呈直线或波浪形,纹路狭小而长,在外力作用下有发展趋向裂纹有穿透和不穿透两种解剖外观检查或探伤检查;缩孔表面呈暗色并不光滑,形状不规则的孔洞,大而集中的为缩孔,小而分散的为缩松产生原因1,首先进入型腔的金属液形成一个极薄的而又不完全的金属层后,被后来的金属液所弥补而留下的痕迹。
2,模温过低3,内浇道截面积过小及位置不当产生喷溅。
4,作用于金属液上的压力不足花纹:涂料用量过多。
1,压铸模型腔表面龟裂2,压铸模材质不当或热处理工艺不正确3,压铸模冷热温差变化太大4,浇注温度过高5,压铸模预热不足6,型腔表面粗糙7,压铸模壁薄或有尖角1,合金过热太大或保温时间过长2,激烈过冷,结晶过细3,铝合金含有锌铁等杂质太多4,铝合金中含铜超出规定范围在铸件上由于应力或外力而产生的裂纹1,锌合金铸件的裂纹(1)锌合金中有害杂质铅,锡,铁和镉的含量超过了规定范围(2)铸件从压铸模中取出过迟(3)型芯的抽出或推出受力不均(4)铸件的厚薄相接处转变剧烈(5)熔炼温度过高2,铝合金铸件的裂纹(1)合金中铁含量过高或硅含量过低(2)合金中有害杂质的含量过高,降低了合金的的可塑性(3)铝硅合金:铝硅铜合金含锌或含铜量过高;铝镁合金中含镁量过多(4)模具,特别是型芯温度太低(5)铸件壁厚有剧烈变化之处(6)留模时间过长(7)顶出时受力不均3,镁合金铸件的裂纹(1)合金中铝硅含量高(2)模具温度低(3)铸件壁厚薄变化剧裂(4)顶出和抽芯受力不均匀4,铜合金铸件的裂纹(1)黄铜中锌的含量过高(冷裂)或过低(热裂)(2)硅黄铜中硅的含量高(3)开模时间晚,特别是型芯多的铸件缩孔是压铸件在冷凝过程中,内部补偿不足而造成的孔穴1,浇注温度过高2,压射比压低3,铸件在结构上有金属积聚的部位和截面变化剧烈4,内浇道较小防止方法1,提高模温2,调整内浇道截面积或位置3,调整内浇道速度及压力4,适当地选用涂料及调整用量1,正确选用压铸模材料及热处理工艺2,浇注温度不宜过高尤其是高熔点合金3,模具预热要充分4,压铸模要定期或压铸一定次数后退火,打磨成型部分表面1,合金不宜过热2,提高模具温度,降低浇注温度3,严格控制合金成分在允许的范围内1,合金材料的配比要注意杂质含量不要超过起点要求2,调整好开模时间3,要使推杆受力均匀4,改变壁厚不均匀性1,正确控制合金成分,在某些情况下:可在合金中加纯铝锭以降低合金中含镁量;或在合金中加铝硅中间合金以提高硅含量2,提高模具温度3,改变铸件结构4,调整抽芯机构或使推杆受力均匀1,合金中加纯镁以降低铝硅含量2,模具温度要控制在要求的范围内3,改进铸件结构消除厚薄变化较大的截面4,调整好型芯和推,杆使之受力均衡1,保证合金的化学成分合金元素取其下限:硅黄铜在配制时,硅和锌的含量不能同时取上限2,提高模具温度3,适当控制调整开模时间1,改变铸件结构消除金属积聚及截面变化大处2,在可能条件下降低浇注温度3,提高压射比压4,适当改善浇注系统,使压力更好的传递第二章铸造铝合金缺陷及分析[size=3]一氧化夹渣缺陷特征:氧化夹渣多分布在铸件的上表面,在铸型不通气的转角部位。
压铸常见不良改善方法

冷纹
铸件表面有明显的不规则的下陷线形纹路(有穿透与不穿透两种)形状细小而狭长,有时交接边缘光滑,在外力作用下有可能断开的可能.
1.两股金属流互相对接,但未完全熔合而又无夹杂期间,两股金属结合力薄弱.
2.浇道口位置不正确,流路太长
3.内浇口速度太低.
4.溢流槽位与金属汇聚处不吻合或容量不够.
3.镶块及滑块磨损.
4.分模面上杂物未清理干净.
5.投影面积计算不正确,超过锁模力.
6.压铸模强度不够造成变形.
1.检查合模力及增压情况.
2.调整增压机构,使增压锋值降低.
3.检查压铸模强度和闭锁原件.
4.检查压铸模损坏情况并修理.
5.清理分模面防止有杂物.
多料
铸件上存在不规则凸起部分
1压铸模热处理不当,产生崩缺.
7.填充速度太高.
1.降低浇注温度.
2.模具温度控制在工艺范围内.
3.消除型腔粗糙的表面.
4.检查离模剂用量是否适当.
5.调整内浇注防止金属液正面冲击.
6.适当降低填充速度.
7.检查模具材料及热处理工艺和硬度.
气泡
铸件接近表面有气体聚集,有时看到铸件表面鼓炮.
1.由卷入气体引起:
1.1型腔气体没有排出被包在铸件中.
1.首先进入型腔的金属液形成一个极薄而不完整的金属层,被后来的金属所覆盖而留下痕迹.
2.模温太低.
3.内截面浇道过小,当位置不当时产生喷溅.
4.作用于金属面上压力不足.
花纹):离模剂用量过多.
1.调整内浇道截面积和位置.
2.调整内浇道速度和压力.
3.提高模温.
4.适当喷涂离模剂.
网状毛翅
铸件表而有网状发丝样凸起或凹陷的痕迹,随压铸之次数增加而不断扩大和延伸.
常见压铸件缺陷解决方法

常见压铸件缺陷解决方法常见压铸件缺陷解决方法苏州金澄精密铸造有限公司是一家压铸制造和精密加工企业,公司专业从事通讯、汽车零部件的压铸、精密加工项目。
并且金澄是苏州市压铸协会理事单位,拥有行业内领先的技术研发中心。
下面金澄为你讲解压铸件的常见缺陷和解决方法。
1、冷纹(水纹):原因:熔汤前端的温度太低,相迭时有痕迹。
改善方法:(1)、检查壁厚是否太薄(设计或制造)较薄的区域应直接充填;(2)、检查形状是否不易填充;距离太远、封闭区域(如鳍片、凸起);(3)、缩短填充时间(4)、改变填充模式2、裂痕(裂纹)原因:(1)、收缩应力;(2)、顶出或整缘时受力裂开;(3)、模具表面裂开。
改善方式:(1)、加大圆角;(2)、检查是否有热点;(3)、增压时间改变(冷室机);(4)、增加或缩短合模时间;3、气孔(砂孔)原因:(1)、空气夹杂在熔汤中;(2)、气体的来源:溶解时、在料管中、在模具中、离型剂;(3)、压射力不足,材质疏松;改善方法:(1)、适当的慢速;(2)、气体的`来源:溶解时、在料管中、在模具中、离型剂;(3)、检查逃气道面积是否有被阻塞,位置是否位于最后填充的地方。
4、波纹(流痕)原因:第一层熔汤在表面急遽冷却,第二层熔汤流过未能将第一层熔解,却又有足够的融合,造成组织不同。
改善方法:(1)、改善填充模式;(2)、缩短填充时间;5、毛边原因:(1)、锁模力不足;(2)、模具合模不良;(3)、模具强度不足;改善方法:(1)、同改善缩孔的方法;(2)、局部冷却;(3)、加热另一边;6、积碳:原因:离型剂或其它杂质积附在模具上.改善方法:(1)、减小离型剂喷洒量.;(2)、升高模温;(3)、选择适合的离型剂.;(4)、使用软水稀释离型剂.7、起泡:原因:气体卷在铸件的表面下面.改善方式: (1)、减少卷气(同气孔).;(2)、冷却或防低模温;8、黏膜:原因:(1)、锌,铝,镁积附在模具表面;(2)、熔汤冲击模具,造成模面损坏.改善方法:(1)、降低模具温度;(2)、降低划面粗糙度.;(3)、加大拔模角.;(4)、镀膜.;(5)、改变充填模式.;(6)、降低浇口速度;压铸件最常见的缺陷2017-03-22 08:54 | #2楼压铸件目前广泛应用于各种装饰方面,如家具配件、建筑装饰、浴室配件、灯饰零件、玩具、领带夹、皮带扣、各种金属饰扣等,因此对铸件表面质量要求较高,同时要求有良好的表面处理性能。
压铸产品铸造缺陷产生原因及处理办法(1)
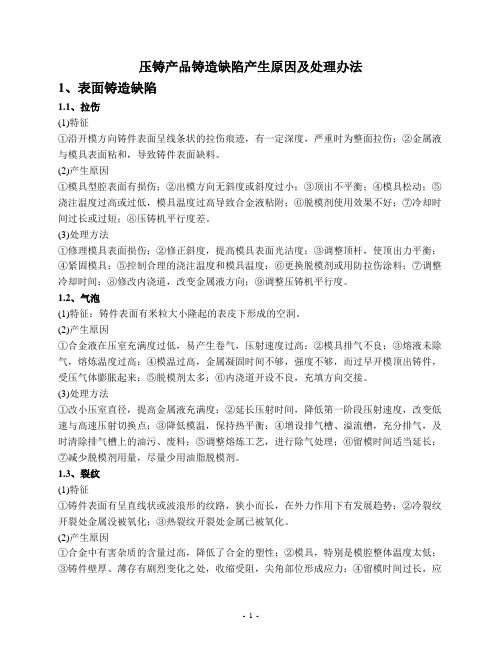
压铸产品铸造缺陷产生原因及处理办法1、表面铸造缺陷1.1、拉伤(1)特征①沿开模方向铸件表面呈线条状的拉伤痕迹,有一定深度,严重时为整面拉伤;②金属液与模具表面粘和,导致铸件表面缺料。
(2)产生原因①模具型腔表面有损伤;②出模方向无斜度或斜度过小;③顶出不平衡;④模具松动;⑤浇注温度过高或过低,模具温度过高导致合金液粘附;⑥脱模剂使用效果不好;⑦冷却时间过长或过短;⑧压铸机平行度差。
(3)处理方法①修理模具表面损伤;②修正斜度,提高模具表面光洁度;③调整顶杆,使顶出力平衡;④紧固模具;⑤控制合理的浇注温度和模具温度;⑥更换脱模剂或用防拉伤涂料;⑦调整冷却时间;⑧修改内浇道,改变金属液方向;⑨调整压铸机平行度。
1.2、气泡(1)特征:铸件表面有米粒大小隆起的表皮下形成的空洞。
(2)产生原因①合金液在压室充满度过低,易产生卷气,压射速度过高;②模具排气不良;③熔液未除气,熔炼温度过高;④模温过高,金属凝固时间不够,强度不够,而过早开模顶出铸件,受压气体膨胀起来;⑤脱模剂太多;⑥内浇道开设不良,充填方向交接。
(3)处理方法①改小压室直径,提高金属液充满度;②延长压射时间,降低第一阶段压射速度,改变低速与高速压射切换点;③降低模温,保持热平衡;④增设排气槽、溢流槽,充分排气,及时清除排气槽上的油污、废料;⑤调整熔炼工艺,进行除气处理;⑥留模时间适当延长;⑦减少脱模剂用量,尽量少用油脂脱模剂。
1.3、裂纹(1)特征①铸件表面有呈直线状或波浪形的纹路,狭小而长,在外力作用下有发展趋势;②冷裂纹开裂处金属没被氧化;③热裂纹开裂处金属已被氧化。
(2)产生原因①合金中有害杂质的含量过高,降低了合金的塑性;②模具,特别是模腔整体温度太低;③铸件壁厚、薄存有剧烈变化之处,收缩受阻,尖角部位形成应力;④留模时间过长,应力大;⑤顶出时受力不均匀。
(3)处理方法:①正确控制合金成分,②改变铸件结构,加大圆角,改变出模斜度,减少壁厚差;③变更或增加顶出位置,使顶出受力均匀;④缩短开模及抽芯时间;⑤提高模温,保持模具热平衡。