FMEA失效模式与效应分析
失效模式与效应分析

上失效模式与效应分析(failure modes and effects analysis, FMEA)¾又名:潜在失效模式与效应分析(PotentialfaiIUre modes and effects analysis),失效模式、影响与危害性分析(failure modes, effects, and criticality analysis, FMECA)A概述失效模式与效应分析(FMEA)是一步步地识别在设计、生产或装配过程以及最终产品和服务中全部可能失效的一种方法。
“失效模式”意思是可能产生某些失效的方式或模式。
失效是任何的错误或者缺陷,尤其是那些影响顾客的、潜在的或实际的。
“效应分析”指的是争论这些失效的后果或效应。
这些失效依据他们结果的严峻性、发生的频率以及被检测到的简洁度优先排序。
FMEA的目的是从有最高的、优先级的开头来实行行动消退或者削减失效。
FMEA通常把当前有关失效的学问以及所实行的行动文档化,用于持续的改进。
FMEA用于设计中预防失效的发生,之后又用于正在进行的过程操作中的掌握。
抱负地说, FMFA 开头于产品的概念设计阶段,贯穿于产品或服务的整个生命期中。
FMEA在19世纪40年月最早被应用于美国的军队中,然后在航空和自动化行业得到进一步的进展应用。
一些行业已经把FMEA的标准正规化,下面是一个综述。
在实行FMEA过程之前,需通过其他的参考资料和培训,从而学习更多关于组织和行业的标准和具体的方法。
>适用场合•当一个产品或服务正在被设计或者重复设计时,在QFD之后或者在设计完成之后;•当以全新的方式应用现有的过程、产品或服务时;•在形成新的或改进过程的掌握方法以前;•当对现有的过程、产品或服务方案改进的时候;•当分析现有的过程、产品或者服务失效缘由时;•贯穿于过程、产品或者服务的生命期中定期进行检查。
>实施步骤这只是一个也许的过程,具体的细节则随着组织或行业的标准而有所变化。
失效模式和效果分析FMEA在制药行业的应用教材

失效模式和效果分析FMEA在制药行业的应用教材失效模式与效应分析(Failure Mode and Effects Analysis, FMEA)是一种常用的质量管理工具,它可以帮助制药行业发现潜在的问题,预防和减少产品质量问题的发生,从而提高产品质量和安全性。
本文将探讨FMEA在制药行业的应用,并分析其效果。
FMEA的基本原理是通过识别潜在的失效模式,并分析这些失效模式可能引起的效应,进而制定合适的预防和纠正措施。
在制药行业,FMEA通常用于产品开发、生产过程和设备维护等环节。
下面将详细介绍FMEA在这些环节的应用。
首先,FMEA在制药产品开发阶段起到了重要的作用。
制药产品的设计失效可能导致产品质量问题和安全隐患。
通过应用FMEA,可以对设计过程中潜在的失效模式进行识别和评估,并制定相应的改进方案。
例如,通过对产品配方进行FMEA分析,可以找出可能导致配方不稳定的因素,如不合适的原材料、配方比例不当等。
这样可以在产品设计阶段及时进行调整,避免质量问题的发生。
其次,FMEA在制药生产过程中的应用也十分重要。
生产过程中的失效可能导致产品质量不稳定和生产效率降低。
通过应用FMEA,可以识别和评估生产过程中的潜在失效模式,并设计相应的控制措施。
例如,在制药生产过程中,可能存在温度控制失效、搅拌不均匀等问题。
通过应用FMEA,可以定位这些问题的发生原因,并制定相应的控制措施,比如使用更精确的温度控制设备、改进搅拌工艺等。
此外,FMEA还可以应用于制药设备的维护管理。
设备故障可能导致生产中断和质量问题。
通过应用FMEA,可以识别设备故障的潜在失效模式,并制定相应的预防和纠正措施。
例如,对于关键设备,可以制定定期保养计划,定期更换易损件,增加备件库存等。
通过这些措施,可以降低设备故障的概率,保证生产的稳定性和质量。
FMEA作为一种质量管理工具,在制药行业的应用具有一定的优势和效果。
首先,通过FMEA可以对潜在的失效模式进行全面、系统的分析。
风险评估技术-失效模式和效应分析(FMEA)及失效模式、效应和危害度分析(FMECA)

失效模式和效应分析(FMEA及失效模式、效应和危害度分析(FMECA)1 概述失效模式和效应分析(Failure Mode and Effect Analysis ,简称FMEA)是用来识别组件或系统未能达到其设计意图的方法。
FMEA 用于识别:•系统各部分所有潜在的失效模式(失效模式是被观察到的是失误或操作不当);•这些故障对系统的影响;• 故障原因;• 如何避免故障及 /或减弱故障对系统的影响。
失效模式、效应和危害度分析(Failure Mode and Effect and Criticality Analysis ,简称 FMECA)拓展了 FMEA 的使用范围。
根据其重要性和危害程度,FMECA 可对每种被识别的失效模式进行排序。
这种分析通常是定性或半定量的,但是使用实际故障率也可以定量化。
2 用途FMEA 有几种应用:用于部件和产品的设计(或产品) FM EA ;用于系统的系统FMEA ;用于制造和组装过程的过程 FMEA ;服务FMEA和软件FMEA。
FMEA/ FMECA 可以在系统的设计、制造或运行过程中使用。
然而,为了提高可靠性,改进在设计阶段更容易实施。
FMEA/ FMECA 也适用于过程和程序。
例如,它被用来识别潜在医疗保健系统中的错误和维修程序中的失败。
FMEA/FMECA 可用来:•协助挑选具有高可靠性的替代性设计方案;•确保所有的失效模式及其对运行成功的影响得到分析;•列出潜在的故障并识别其影响的严重性;•为测试及维修工作的规划提供依据;• 为定量的可靠性及可用性分析提供依据。
它大多用于实体系统中的组件故障,但是也可以用来识别人为失效模式及影响。
FMEA 及 FMECA 可以为其他分析技术,例如定性及定量的故障树分析提供输入数据。
3 输入数据FMEA 及 FMECA 需要有关系统组件足够详细的信息,以便对各组件出现故障的方式进行有意义的分析。
信息可能包括:• 正在分析的系统及系统组件的图形,或者过程步骤的流程图;• 了解过程中每一步或系统组成部分的功能;• 可能影响运行的过程及环境参数的详细信息;• 对特定故障结果的了解;• 有关故障的历史信息,包括现有的故障率数据。
失效模式与效应分析在护理风险
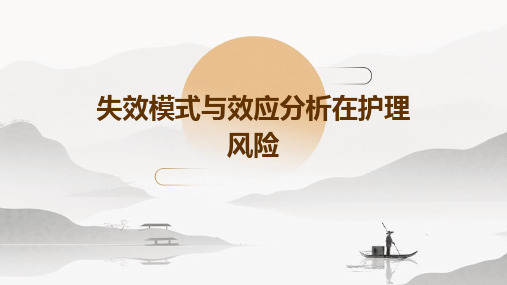
将识别出的失效模式记录在专门的表格或数据库中,以便后续分析 和改进。
风险优先级评估
评估失效模式的风险
01
根据失效模式的发生频率、严重程度和可检测性等指标,评估
每个失效模式的风险等级。
确定优先改进目标
02
根据风险评估结果,确定需要优先改进的失效模式,为制定改
进措施提供依据。
制定风险控制计划
实施难度
FMEA需要多部门合作和大量资源投入,实施起 来可能面临一定的困难。
更新需求
随着医疗技术的不断发展和护理实践的改进, FMEA需要不断更新和调整。
未来发展方向
智能化分析
利用人工智能和大数据技术,对海量数据进行挖掘和分析,提高 FMEA的准确性和效率。
跨学科合作
加强与其他学科领域的合作,共同研究护理风险的防控策略,提高 护理质量。
案例二:老年患者护理风险
总结词
老年患者由于身体机能下降,容易发生跌倒、压疮等护理风险。FMEA可以帮助识别和评估这些风险 ,从而采取有效的措施来降低风险。
详细描述
老年患者护理风险的失效模式包括地面湿滑、床边无护栏、缺乏合适的坐便器等。通过FMEA分析, 可以评估这些风险的发生可能性和严重程度。针对这些风险,可以采取相应的措施,如加强地面清洁 、安装床边护栏、提供合适的坐便器等,以降低风险。
提高护理质量
通过分析和改进护理过程中的失效 模式,FMEA有助于提高护理质量, 提升患者的满意度和信任度。
FMEA的发展历程
起源
FMEA起源于20世纪40年代的军事行 业,后来被广泛应用于航空、汽车和 医疗领域。
在护理领域的应用
发展和改进
随着医疗技术的不断发展和患者需求 的提高,FMEA在护理领域的应用也 在不断发展和改进,以适应新的挑战 和需求。
失效模式与效应分析 (FMEA)

失效模式與效應分析 (FMEA)何謂「FMEA、FMECA」?FMECA 是兩種分析技術的總稱:1.FMEA﹝故障型式及其影響分析﹞2.CA﹝Criticality Analysis, 嚴重度分析﹞與失誤樹分析一樣,故障型式影響及嚴重度分析﹝failure modes, effects and criticality analysis, 簡稱 FMECA﹞,首先在美國國防科技中研究發展,且在國防部各機構中普遍應用﹝DOD, 1980﹞,後來漸應用於工業界。
在核能、化工、石化、海上鑽油等高風險工業中,自不例外。
工業界的設計工程師與可靠度﹝Reliability﹞工程師常運用 FMECA 以預測複雜的產品的可靠度,預估一件產品的零件在某特定的時間及情況下,如何失去其功能,故障的次數是多少,故障之後對其他零件或對整個系統會產生怎樣的影響等。
FMECA 的功用不止於可靠度一端,其分析所得的資料,尚可作下列用途:1.協助評估所設計的裝置,如複聯系統﹝Redundancy﹞、故障偵測,以及fail-safe 特性等。
2.對測試、採購﹝Procurement﹞、檢查、改善措施等提供先後順序的參考資料。
3.提供失誤隔絕﹝Fault isolation﹞及維護性﹝Maintainability﹞分析的參考資料。
4.提供系統安全分析﹝如失誤樹分析﹞所需的硬體資料。
FMECA 可在系統週期的任一階段中,依計劃內容之需要,以不同深淺程度實施,但在設計階段的初期,一旦所需的設備確定之後,即應實施。
FMECA 的對象是系統或子系統中的零組件,尤其對於複雜的系統中的設備零件,最能發揮其故障針砭的功效,此為其他系統安全分析技術不能望其項背之處。
但因其分析對象大多限於硬體,故對於人為因素和作業環境因素較少納入分析考慮範圍。
因此,如能將 FMECA 與失誤樹分析合併使用,必更能瞭解整個作業系統的危害,進而防範事故生。
摘於【環安 Q&A】。
失效模式与效应分析(FMEA)
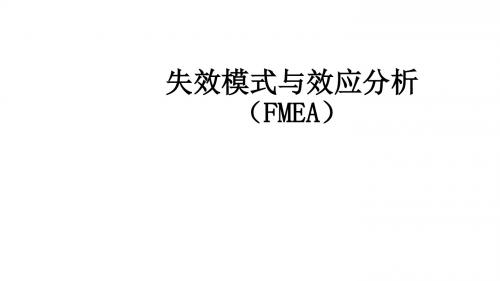
失效模式与效应分析 (FMEA)
起源
FMEA大约于1950年代由美国Grumman公 司提出,当时由于飞机系统复杂并且需要 预防失效情况发生,因此渐渐发展成安全 性与可靠度的设计模式,以期能够增加产 品质量,降低不良问题的发生。
FMEA具体项目
• 累积经验,早期发现失效原因及采取因应之道。 • 促进设计改良。 • 改善操作方法及建立维护计划的参考。 • 帮助操作人员之训练,让员工能在短期内找出 失效原因与解决之法。 • 公司人员异动时,能让员工快速上手。
FMEA表格建立
失效机率
字码体系
严重性分析
多要因评估法
单要因评估法
列表评估法
失效报告
范例
范例
范例
范例
范例
故障树分析符号
故障树分析范例
故障树简化
故障树关键性估计范例
结论
• 透过FMEA模式,可有效找出来自品失效原因,进而解决问题,是一 个可靠性的解析手法。 • 藉由实施FTA ,能让不希望发生的事情明确化,并能判别事件发 生时所带来的一些事象与对成品的影响。
失效模式与效应分析在护理风险管理
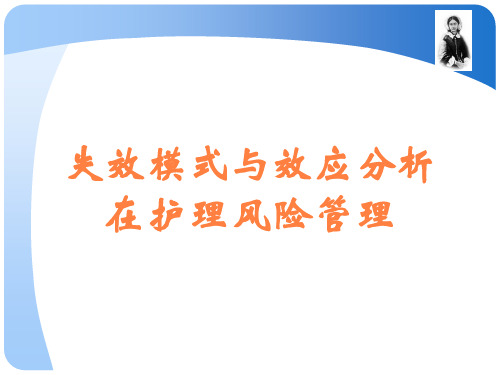
❖FMEA应用能够提醒管理者和临床 护士关注那些常被忽视,但实际 上非常主要,需要注重旳问题。
❖ 例如
讨论
❖ FMEA前瞻性分析以及质量旳连续改善 ❖ FMEA强调旳是“事前预防”,而非“事后纠
适合医疗服务行业旳HFMEATM模式。
医疗服务提供者
有效防范医疗风险
辨认病人
提升病人治疗过程中 高危程序旳安全性 预防医疗硬件设备 技术故障或设备缺损
潜在危险原因 潜在危险原因 潜在危险原因 潜在危险原因
操作流程设计 潜在危险原因
FMEA在护理风险管理中旳应用
程 中 旳 应 用
在 安 全 用 药 流
针对每一种失效模式,制定 了相应旳处理方案
确保了住
院患者旳用药 安全
FMEA在护理风险管理中旳应用
FMEA在急诊室工作流程中旳应用
急诊室旳 单薄环节
工作程序太过 复杂,有关患 者情况旳信息 沟通是危险性
最大旳一种失 效模式
制定并执行相应旳改 善措施后,这一失效 模式得到有效控制
医疗差错可 经过改善系 统得到最大 程度旳降低
应用失效模式与效应分析预防开胸术后肺不张
绘制流程图,找出失效模式
❖开胸术后肺不张旳原因有: ❖ 1)术前常有吸烟史且多合并有呼吸系统疾病,
呼吸道纤毛—粘液系统运送分泌物功能减退。 ❖ 2)全麻气管插管致气管纤毛破坏倒伏,纤毛功
能障碍,造成分泌物不能有效排除而阻塞气管 。 ❖ 3)手术中操作对肺组织造成挫伤,肺间质水肿 ,气道分泌物增长。 ❖ 4)术后切口疼痛以及手术对呼吸肌旳损伤造成 患者呼吸受限,咳嗽无力,引起支气管内分泌 物滞留、阻塞。
潜在失效模式与效应分析

潜在失效模式与效应分析潜在失效模式与效应分析(Failure Mode and Effects Analysis,FMEA)是一种常用于产品设计与制造过程中的质量管理工具,用于识别和分析可能的失效模式和其对产品或系统性能的潜在影响,从而采取相应的改进措施以提高产品的可靠性和安全性。
FMEA包括三个关键步骤:识别潜在失效模式、分析失效效应和确定风险优先级。
首先,团队通过对产品或系统进行系统性分析,并结合以往经验,识别出所有可能的失效模式。
这些失效模式可能发生在产品的各个环节,如设计、制造、装配、运输和使用等。
然后,团队对每个失效模式进行评估,分析失效效应。
失效效应可能包括对产品功能、性能、可靠性和安全性的影响。
最后,根据失效模式和效应的严重性和概率,确定风险优先级,以便制定相应的改进措施。
FMEA的核心目标是预防失效,并通过优先处理潜在的高风险失效来提高产品质量和可靠性。
通过分析失效模式和其效应,可以识别导致失效的根本原因,并采取相应的纠正和预防措施。
FMEA可以帮助团队更好地理解产品的设计和制造过程中的潜在问题,并预测可能的质量和安全风险,从而减少后续的成本和不良后果。
FMEA也有助于团队提高对产品的理解和共识。
在FMEA过程中,团队成员就产品的设计和制造问题展开讨论,共同评估潜在的失效模式和其效应,并制定改进措施。
通过这些讨论,团队可以发现和纠正潜在的问题,并提高各部门之间的沟通和合作。
FMEA的应用领域广泛,适用于各类产品和系统的设计和制造过程。
例如,汽车制造业常用FMEA来识别和纠正潜在的设计和制造缺陷,提高汽车的质量和安全性。
医疗设备制造商也使用FMEA来评估产品的安全性和性能,减少医疗事故的风险。
此外,航空航天、电子、化工等行业也都广泛应用FMEA来提高产品的可靠性和安全性。
总之,潜在失效模式与效应分析(FMEA)是一种非常有用的质量管理工具,通过识别和分析潜在的失效模式和其效应,帮助团队预防失效、提高产品的可靠性和安全性。
- 1、下载文档前请自行甄别文档内容的完整性,平台不提供额外的编辑、内容补充、找答案等附加服务。
- 2、"仅部分预览"的文档,不可在线预览部分如存在完整性等问题,可反馈申请退款(可完整预览的文档不适用该条件!)。
- 3、如文档侵犯您的权益,请联系客服反馈,我们会尽快为您处理(人工客服工作时间:9:00-18:30)。
~目錄~第一篇FMEA概述FMEA概述.....................................................................2-3 潛在失效模式與效應分析之順序 (4)第二篇設計FMEA何謂設計FMEA (5)設計FMEA適用時機 (5)設計FMEA的效益 (6)團隊工作 (6)設計FMEA流程圖 (7)一個設計FMEA的形成~表單填寫指導1~22項........................8-18 設計FMEA範例 (19)第三篇制程FMEA何謂制程FMEA (20)制程FMEA適用時機 (21)制程FMEA的效益 (21)團隊工作 (21)FMEA與品質規劃之相關性 (22)制程FMEA流程圖 (23)一個制程FMEA的形成~表單填寫指導1~22項.....................24-32 制程FMEA範例 (33)附錄………………………………………………………………34-40術 語 (41)FMEA概述:Potential Failure Mode and Effects Analysis,簡稱FMEA,是對特定的設計或制程究竟應該做些什麼事來確保顧客滿意這一過程的補充,是一項系統化的活動,其主要目的在於:1.對產品及其制程中的潛在失效與影響效應建立認知并且予以評價。
2.確定系列措施以消除或降低失效發生的機會(或然率)。
3.建立活動過程的文件與紀錄。
◎根據車輛召回的研究顯示,FMEA的全面實施可以防止很多事件的發生,因此,想要識別并最大程度地減少潛在的隱患,FMEA是一項非常重要的應用技術 。
◎FMEA成功的關鍵在於〝事件發生前〞采取措施的時間性,在事前花點時間做好FMEA分析,能夠很容易地以低成本來更改產品或制程,從而將後期更改的風險降至最低。
◎FMEA的範圍與關注焦點:1.新設計、新技術,或新制程時:著眼於全部的新設計、新技術,或新制程。
2.現有的設計或制程的變更時(假設已有FMEA):集中於設計或制程的變更和變更可能產生的交互影響,以及現場的歷史情況。
3.將現有的設計或制程使用於新的環境、場所或用途時(假設已有FMEA):著眼於新的環境、場所或用途對既有設計或制程的影響。
◎FMEA編制的責任可能指定為某一主辦工程師,但是輸入應是小組活動的輸出。
小組由知識與經驗丰富的人員組成(例如:設計、檢驗、實驗、制造、裝配、服務、品質及可靠度等)。
◎即便是看起來完全相同的產品或制程,也不宜拿一個小組FMEA的評價結果與另一個小組的FMEA評價結果相比較,由於每個小組的環境不同,其評價結果必定不同。
◎一個思考周密的FMEA如果缺少及時有效的矯正或預防措施,并且傳達到所有受影響的部門,則其價值將極其有限。
◎FMEA是動態文件,必須隨時反映最新的制程現實狀況。
◎主辦工程師負責確保所有的措施都得到落實,包括但不限於:1.審查設計、圖樣及制程,確保建議的措施得以實施。
2.確認所有的更改已貫徹到設計、裝配與制造文件中。
3.對FMEA的應用及管制計劃提供審查。
潛在失效模式與效應分析之順序4/43何謂設計FMEA ?為一系統化的分析技術,用以評估某一設計可能發生缺點的機率,及其發生後造成的影響。
而且針對高風險(RPN Risk Priority Number)項目,事先評估其制程能力,俾能訂定適當的制程管制。
最終產品以及相關的每個系統、子系統和零組件都應予以評估。
FMEA 以最嚴密的方式提出了小組成員在設計時應考慮的事項(根據過去經驗認為可能出差錯的事項也包括在內),并將設計過程中必須的思考過程加以規範化和制度化。
設計FMEA適用時機在產品品質規劃(APQP)之構想階段(第一階段),先將顧客的期望轉換成可靠度,再從產品設計與開發驗証階段(第二階段) 展開設計FMEA。
設計FMEA視為一份持續檢討的活性文件,應在設計概念完成之前或之時就開始實施,隨著變化的出現或在整個生產開發階段取得更多訊息時,持續予以更新而改進提升,且在生產圖面公布前研議應採取之改正措施及設計修改。
設計FMEA不依靠制程管制來克服潛在的設計缺陷,但是需要注意制造與裝配過程限制因素,例如:必要的拔模斜度、表面處理的限制、裝配空間/工具的可接近性、鋼材淬火的限制、公差/制程能力/性能等,還應考慮產品維護(服務)及回收的限制因素,如工具的可接近性、診斷能力、材料分類符號(用於回收)等等。
設計FMEA的效益◎有助於對設計要求和設計決擇的客觀評估。
◎有助於有關制造和裝配要求的初次設計。
◎提高潛在失效模式以及其對系統的影響在設計開發過程中得到考慮的可能性。
◎提供更多訊息,有助於全面的﹑有效的設計測試及開發方案的規劃。
◎開發出一系列按照對“顧客”的影響來排列的潛在失效模式,因此為設計改進和開發測試建立了一個優先系統。
◎為推荐和跟蹤減少風險行動提供了一種開放式格式。
◎提供未來參考,以助於分析實地問題,評估設計變更和開發先期設計。
團隊工作(Team effort):在最初的設計FMEA過程中,責任工程師預計會直接地和積極地讓來自所有受影響領域的代表參與其中。
這些領域應該包括,但不限定於:裝配﹑制造﹑材料﹑品質﹑服務和供應商,還有負責下次裝配的設計領域。
FMEA 應該成為一種促進影響功能間交換意見並因此而促進一種團隊方法的催化劑,從而推動小組協作的工作模式。
設計FMEA流程圖不良模式舉例:變型.破裂.磨損.洩漏失效效應影響范例:行車不穩定.操作不靈.車輛失控原因范例:扭力規格不當.應力過高,材料規格不當設計FMEA的展開●準備期◎工程師群的經驗◎品質經歷(如:工程數據等)◎顧客需求:想要的與必須的◎規格要求◎已知產品要求◎制造/裝配要求所須求的特性定義的越好,為改進行動鑒別潛在的失效模式,就越容易。
設計FMEA應從所要分析的系統、子系統或零組件的方塊圖開始,(見附錄C)。
方塊圖中說明了所分析的項目之間的主要關系與分析的邏輯順序,在FMEA準備工作中,所有方塊圖的復制件應伴隨FMEA過程。
方塊圖還可以指示訊息、能源、力、流體等的流程,旨在明確輸入給方框的內容、方框的過程(功能)、以及方框的輸出。
●展開期以系統,次系統和(或)被分析零組件的樹狀圖開始,並按以下次序應用於標準的FMEA表格:1)F MEA序號::填入FMEA文件作成之編號,可用於追查。
2)系統,次系統或零組件名稱和型號:指明分析的適當級別填入系統、次系統或被分析零組件的號碼(型號)。
FMEA小組必須為他們特定的活動確定系統、子系統或部件的組成。
劃分系統、子系統和部件的實際界限是任意的,並且必須由FMEA小組來確定。
有關系統FMEA的概念及舉例參見附錄F,以下僅作簡要說明:系統FMEA的範圍一個系統可以看作是由多個子系統組成的,這些子系統往往是由不同的小組所設計。
一些典型的系統FMEA可能包括下列系統:底盤系統、傳動系統、內飾系統等。
因此,系統FMEA的焦點是要確保組成系統的各個子系統間的所有接口和交互作用以及系統與車輛其他系統和顧客的接口都要涵蓋。
子系統FMEA的範圍一個子系統FMEA通常是一個大系統的一個組成部份。
例如:前懸挂系統是底盤系統的一個組成部份。
因此,子系統FMEA的焦點就是確保組成子系統的各個部件間的所有接口和交互作用都要涵蓋。
零部件FMEA的範圍零部件FMEA通常是一個以子系統的組成部份為焦點的FMEA,例如:螺杆是前懸挂(底盤系統的一個子系統)的一個部件。
3)設計責任:填入公司名稱,部門和組織。
也包括供應商姓名(如果已知)4)編制人:填入負責編制FMEA之工程師的姓名,電話號碼和廠別。
5)機種與年份:填入所分析零組件使用或裝附於客戶的機種型號及年份。
6)關鍵日期:填入最初預定的完成日期,此日期不應超過預定的生產設計發布日期。
7)F MEA日期:填入原始的FMEA制訂日期及最近的修改日期。
8)核心小組:列出負責的個人和有權去確認和(或)從事這項任務的部門的名單。
(建議所有的團隊成員姓名﹑部門﹑電話號碼﹑廠別等,均應包括在文件分發登記表Distribution list中)。
9)項目(零件)/功能:填入被分析項目(零件)的名稱序號(型號)﹑使用術語名稱並如工程圖所指明的一樣表明設計級別。
在最初公布前,應使用實驗號碼。
用盡可能簡明的文字來說明被分析項目滿足設計意圖的功能,包括該系統運行環境(規定溫度、壓力、溫度範圍、設計壽命)相關的信息(量測變異)。
如果該項目有多種功能,且有不同的失效模式,應把所有的功能單獨列出。
10)潛在失效模式:潛在的失效模式被定義為一種方式,以這種方式,一個零組件﹑次系統或系統可能潛在地不會滿足設計意圖。
潛在失效模式也可以是一個更高的級別次系統中潛在失效模式的肇因,或成了一個更低零組件中潛在失效模式的結果。
針對特定的項目及其功能,列出每一個潛在的失效模式,(這種失效可能發生,但不一定發生)。
建議以以往TGW(運行出錯)研究、疑虙、報告和小組腦力激盪結果的回顧作為起點。
只可能出現在特定的運行條件下(如熱、冷、乾燥、粉塵等)和特定的使用條件下(如超過平均里程、不平的路面、僅在城市內行駛等)的潛在失效模式應予以考慮。
典型的失效模式可能是,但並不限於:注意:潛在失效模式應該用“物理學的”或“技術的”術語來描述而不必與顧客可觀察到的“病症symptom”等同。
11)失效的潛在效果:失效的潛在效果被定義為顧客感受到的功能上之失效模式的效果,根據顧客可能發現或經歷的情況來描述。
(顧客既可能是內部的顧客也可能是最終用戶)。
如果失效模式可能影響安全性或對法規的符合性,要清楚地予以說明。
不同級別的部件、子系統和系統之間存在著一種系統層次上的關係。
例如:一個零件的斷裂將會引起總成的振動,從而導致一個系統間歇性運行;系統的間歇性運行可能會造成性能的下降並最終導致顧客的不滿。
分析的意圖就是在小組所擁有的知識層次上,盡可能地預測到失效的後果。
典型的失效效果可能是,但不限於:12)嚴重性(Severity)(S):嚴重性是對下個零組件、次系統、系統或顧客所發生的潛在失效模式效果的嚴重性進行評估。
嚴重性僅適用於效果,其等級指數的減低只能透過設計更改才能夠生效。
嚴重性應該在1至10的等級上估計。
盡管個別產品的分析可做修改,小組應對評定準則和分級規則達成一致意見。
注:不推薦修改確定為9和10的嚴重度數值;嚴重度數值定級為1的失效模式不須進行進一步的分析。
注:有時,高的嚴重度定級可以通過修改設計,使之補償或減輕失效的嚴重度結果來予以減小,例如“安全帶”可以減輕車輛碰撞後果的嚴重程度。
推荐的嚴重性評估標準---DFMEA13)分類:用於對需要額外制程管制的零組件、次系統或系統的任何特別產品特性(如:致命的﹑關鍵的﹑主要的﹑重要的)進行分類。