微细加工技术概述及其应用
电子束微细加工技术的发展及其应用

电子束微细加工技术的发展及其应用电子束微细加工技术随着科学技术的发展而逐渐成熟,其在加工工业领域有着广泛的应用。
本文将重点探讨电子束微细加工技术的发展历程,技术特点以及在各个领域的应用。
一、电子束微细加工技术的发展历程电子束微细加工技术可以追溯到二十世纪中期,当时美国贝尔实验室的研究人员首次将电子束用于微细加工。
当时,电子束微细加工技术还处于探索阶段,局限于单层薄膜的微细加工。
随着科学技术的发展,电子束微细加工技术经历了从单层薄膜加工到多层薄膜、集成电路、光学器件以及生物医学等领域的拓展过程。
二、电子束微细加工技术的技术特点1.高精度电子束微细加工技术的加工精度可以达到亚微米级别。
由于电子束的微小直径,因此加工精度高。
同时,电子束微细加工技术无需接触到工件表面,因此可以避免因为接触而导致的破坏。
2.高速度电子束微细加工技术的加工速度比传统机械加工技术快得多。
电子束可以在微小的空间内加工,从而提高加工效率。
3.可控性强电子束微细加工技术可以通过调整电子束的加速电压和电子束的聚焦来实现不同的加工效果。
同时,电子束微细加工技术还具有可调的深度控制功能。
三、电子束微细加工技术在各个领域的应用1.集成电路在集成电路制造领域,电子束微细加工技术可以实现极小尺寸的电路设计。
利用电子束微细加工技术可以制造出亚微米级别的电路,这对于集成电路的制造具有重要的作用。
2.生物医学电子束微细加工技术在生物医学领域的应用主要集中在生物芯片制造方面。
利用电子束微细加工技术可以制造出超薄的微处理芯片,这些芯片可以被用于感应、检测和诊断。
3.光学器件利用电子束微细加工技术可以制造出高精度的光学器件,如光纤、光阻、光学芯片等等,这些光学器件可以被应用于通讯、光电子学、测量、材料加工等领域。
4.微纳机械电子束微细加工技术在微纳机械领域具有广泛的应用。
可以利用电子束微细加工技术制造出微米级别的光学器件、电子器件和机械器件等。
在微纳机械领域,电子束微细加工技术在制造微机械设备时具有独特的优势。
微细加工技术概述

1、电子束微细加工技术
电子束加工的原理
电子束加工是在真空条件下, 利用聚焦后能量密度极高(106~ 109W/cm2)的电子束,以极高的 速度冲击到工件表面极小的面 积上,在很短的时间(几分之一 微秒)内,其能量的大部分转变 为热能,使被冲击部分的工件 材料达到几千摄氏度以上的高 温,从而引起材料的局部熔化 和气化,被真空系统抽走。
微细加工的特点
微细加工作为精密加工领域中的一个极重要的关键技术, 目前有如下的几个特点: 1. 微细加工和超微细加工是多学科的制造系统工程; 2. 微细加工和超微细加工是多学科的综合高新技术; 3. 平面工艺是微细加工的工艺基础; 4. 微细加工技术和精密加工技术互补; 5. 微细加工和超微细加工与自动化技术联系紧密; 6.微细加工检测一体化。
所谓微细加工技术就是指能够制造微小尺寸零件 的加工技术的总称。 • 广义地讲,微细加工技术包含了各种传统精密加 工方法和与其原理截然不同的新方法,如微细切削 磨料加工、微细特种加工、半导体工艺等; • 狭义地讲,微细加工技术是在半导体集成电路制 造技术的基础上发展起来的,微细加工技术主要是 指半导体集成电路的微细制造技术,如气相沉积、 热氧化、光刻、离子束溅射、真空蒸镀等。
电子束切割
利用电子束在磁场中偏转的原理,使电子束在工 件内部偏转,还可以利用电子束加工弯孔和曲面。
电子束微细焊接
电子束焊接是利用电子束作为热源的一种焊接工艺,在 焊接不同的金属和高熔点金属方面显示了很大的优越性, 已成为工业生产中的重要特种工艺之一。 电子束焊接具有以下的工艺特点: (1)焊接深宽比高。 (2)焊接速度高,易于实现高速自动化。 (3)热变形小。 (4)焊缝物理性能好。 (5)工艺适应性强。 (6)焊接材料范围广。
微细加工技术概述及其应用

2011 年春季学期研究生课程考核(读书报告、研究报告)考核科目:微细超精密机械加工技术原理及系统设计学生所在院(系):机电工程学院学生所在学科:机械设计及理论学生姓名:杨嘉学号:10S008214学生类别:学术型考核结果阅卷人微细加工技术概述及其应用摘要微细加工原指加工尺度约在微米级范围的加工方法,现代微细加工技术已经不仅仅局限于纯机械加工方面,电、磁、声等多种手段已经被广泛应用于微细加工,从微细加工的发展来看,美国和德国在世界处于领先的地位,日本发展最快,中国有很大差距。
本文从用电火花加工方法加工微凹坑和用微铣削方法加工微小零件两方面描述了微细加工技术的实际应用。
关键词:微细加工;电火花;微铣削1微细加工技术简介及国内外研究成果1.1微细加工技术的概念微细加工原指加工尺度约在微米级范围的加工方法。
在微机械研究领域中,从尺寸角度,微机械可分为1mm~10mm的微小机械,1μm~1mm的微机械,1nm~1μm的纳米机械,微细加工则是微米级精细加工、亚微米级微细加工、纳米级微细加工的通称。
广义上的微细加工,其方式十分丰富,几乎涉及现代特种加工、微型精密切削加工等多种方式,微机械制造过程又往往是多种加工方法的组合。
从基本加工类型看,微细加工可大致分为四类:分离加工——将材料的某一部分分离出去的加工方式,如分解、蒸发、溅射、切削、破碎等;接合加工——同种或不同材料的附和加工或相互结合加工方式,如蒸镀、淀积、生长等;变形加工——使材料形状发生改变的加工方式,如塑性变形加工、流体变形加工等;材料处理或改性和热处理或表面改性等。
微细加工技术曾广泛用于大规模集成电路的加工制作,正是借助于微细加工技术才使得众多的微电子器件及相关技术和产业蓬勃兴起。
目前,微细加工技术已逐渐被赋予更广泛的内容和更高的要求,已在特种新型器件、电子零件和电子装置、机械零件和装置、表面分析、材料改性等方面发挥日益重要的作用,特别是微机械研究和制作方面,微细加工技术已成为必不可少的基本环节。
微细加工技术在微电子器件制备中的应用研究

微细加工技术在微电子器件制备中的应用研究微电子器件制备是当今电子技术领域的热点研究方向之一。
微电子器件制备的核心就是微细加工技术,该技术主要以光刻、薄膜沉积、化学加工、离子注入、蚀刻等为基础。
这些微细加工技术在微电子制备中发挥着不可替代的作用,是现代信息和通信技术、计算机技术、医学和生物技术等方面的关键技术。
下面我们将从几个方面来探讨微细加工技术在微电子器件制备中的应用研究。
一、微电子器件制备的重要性微电子器件制备一直是电子技术领域的研究热点,已广泛应用于计算机、手机、数字化电视等高科技领域。
目前,在自动化控制、靶向治疗、生物芯片、智能传感等领域都有了广泛应用。
国家也将微电子产业作为发展战略,积极发展集成电路、显示器、微处理器等产业。
因此,微电子器件制备将在未来的高科技发展中扮演着越来越重要的角色。
二、微细加工技术的分类及应用1. 光刻技术:光刻技术是微细加工技术中的重要一环。
它的原理是将光照射到光刻胶上,形成图案,再通过蚀刻或其他化学反应形成图案,用于制作晶体管、太阳能电池、光子晶体器件等。
2. 薄膜沉积技术:薄膜沉积技术也是微电子器件制备中应用广泛的技术。
它主要包括化学气相沉积、物理气相沉积、电化学沉积等技术。
薄膜沉积技术的主要应用领域是微电子器件中的互连线的分离层等。
3. 化学加工技术:化学加工技术是用化学方法对微电子材料进行处理,以制备出微电子器件。
在化学加工技术中,蚀刻技术是最为常见的一种技术。
蚀刻技术主要是通过酸、碱等化学物质对材料进行腐蚀、溶解或者氧化等,然后按要求形成器件。
4. 离子注入技术:离子注入技术主要是将离子注入到半导体材料中去,以改变其电学性质和物理特性,进而形成微电子器件。
三、微细加工技术的研究方向1. 多维度控制技术在微电子器件制备中,需要对于个别的材料可实现严格的调控,比如要求薄膜良率高、晶圆表面平整度高等等。
因此,为提高整个加工过程的可控性,就要求多维度控制技术的发展,实现对于加工过程中每一环节的精细控制,比如对于温度、光照强度、反应时间等方面的控制。
微细加工工艺技术

微细加工工艺技术微细加工工艺技术是一种应用于微电子、光学、纳米学等领域的高精度加工技术,该技术能够实现对微细结构的精密加工。
在微细加工工艺技术中,常常采用的加工方法有激光刻蚀、化学蚀刻、光刻以及微电子束等。
激光刻蚀是一种应用激光照射,通过激光束的高能量将材料表面局部蚀刻的加工方法。
与传统的机械刻蚀相比,激光刻蚀具有高精度、高效率的优点。
在激光刻蚀中,光束的聚焦度和光斑直径是影响加工精度的重要参数。
化学蚀刻是一种利用特定的化学反应,在材料表面选择性地产生化学蚀刻产物,并将其去除的加工方法。
化学蚀刻通常需要制备特定的蚀刻溶液,通过控制溶液的浓度和温度,来影响化学反应的速率和选择性。
化学蚀刻可以实现微细结构的高精度加工,并被广泛应用于光学元件和微流控芯片等领域。
光刻是一种基于光化学反应的加工方法,通过光阻的选择性暴露和去除,来形成所需的图案结构。
在光刻过程中,首先在材料表面涂敷一层光刻胶,然后利用光刻机的紫外光照射和显影等步骤,实现图案的转移。
光刻具有高精度、高分辨率和高重复性的优点,是微细加工中不可或缺的工艺之一。
微电子束也是一种实现微细结构加工的重要方法。
微电子束利用高能电子束在材料表面定向照射,经过准直、聚焦和偏转等步骤,将电子束的能量转化为对材料的加工作用。
通过控制电子束的参数,如能量、聚焦度和扫描速度等,可以实现对微细结构的精密加工。
微电子束在高精度加工领域具有很大的应用潜力,尤其在微电子器件、光电器件以及半导体器件等方面,具有广阔的发展前景。
总的来说,微细加工工艺技术是一种实现高精度加工的重要方法,包括激光刻蚀、化学蚀刻、光刻和微电子束等。
这些加工方法在微电子、光学、纳米学等领域发挥着重要作用,推动了相关技术的进步和应用的发展。
未来随着科学技术的不断进步,微细加工工艺技术将继续发展壮大,为人类社会带来更多的科技成果和应用产品。
微细加工技术的研究与应用
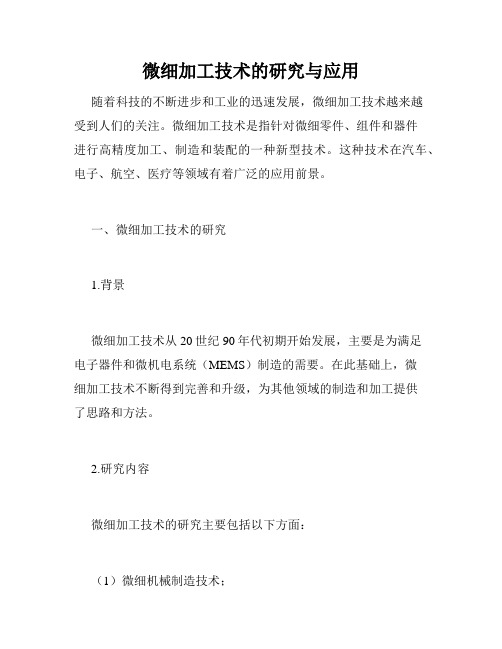
微细加工技术的研究与应用随着科技的不断进步和工业的迅速发展,微细加工技术越来越受到人们的关注。
微细加工技术是指针对微细零件、组件和器件进行高精度加工、制造和装配的一种新型技术。
这种技术在汽车、电子、航空、医疗等领域有着广泛的应用前景。
一、微细加工技术的研究1.背景微细加工技术从20世纪90年代初期开始发展,主要是为满足电子器件和微机电系统(MEMS)制造的需要。
在此基础上,微细加工技术不断得到完善和升级,为其他领域的制造和加工提供了思路和方法。
2.研究内容微细加工技术的研究主要包括以下方面:(1)微细机械制造技术;(2)微细电子制造技术;(3)微细光学制造技术;(4)微细生物制造技术。
其中,微细机械制造技术是应用最为广泛的一项技术,主要针对微型零部件、机械组件和器件等进行加工和制造。
3.研究难点微细加工技术的研究面临着许多难点,其中最主要的难点是如何实现高精度加工。
微细零部件的尺寸通常都在数微米至数百微米之间,而传统加工技术所能达到的精度却远远不够。
因此,如何在微小尺度下进行高精度加工,是微细加工技术研究的核心问题。
二、微细加工技术的应用1.汽车制造领域汽车制造领域是微细加工技术应用的主要领域之一。
在汽车制造中,许多零部件的尺寸都很小,而且对加工精度要求很高。
例如,发动机的火花塞、气门、燃油喷嘴等部件;车身的紧固件、密封件和缝合件等,都需要采用微细加工技术进行加工和制造。
2.电子制造领域电子制造领域也是微细加工技术应用的重要领域之一。
在电子制造中,许多IC芯片、闪存和存储器等器件的结构都非常微小,需要采用微细加工技术进行精密加工和制造。
同时,电子制造领域还需要采用微细加工技术进行导电薄膜的制造、微型电极的加工等工作。
3.医疗领域医疗领域也是微细加工技术应用的一个新兴领域。
在医疗领域中,微细加工技术可以用于制造微型手术器械、医用传感器、微型分析芯片等器件,从而为医疗诊断和治疗提供了新的手段和方法。
微细加工技术

微细加工概念 微细加工机理 微细加工方法 LIGA技术及准LIGA技术
微细加工技术应用 生物加工技术
6.1 微细加工技术概述
6.1.1 微细加工的概念
微细加工技术是指加工微小尺寸零件的生产加工技术。 从广义的角度来讲,微细加工包括各种传统精密加工方法和 与传统精密加工方法完全不同的方法,如切削加工,磨料加 工,电火花加工等。从狭义的角度来讲,微细加工主要是指 半导体集成电路制造技术。
6.2 微细加工机理
(4)晶界、空隙、裂纹(102 ~1)mm 它们的破坏是以缺陷 面为基础的晶粒破坏。 (5)缺口(1 mm 以上) 缺口空间的破坏是由于应力集中而 引起的破坏。
在微细切削去除 时,当应力作用的区 域在某个缺陷空间范 围内,则将以与该区 域相应的破坏方式而 破坏。图 6-1 为材料 微观缺陷分布情况。
较大,允许的切削深度 ap 较大。微细加工时,从强度和刚 度都不允许大的切削深度 ap,因此切屑很小。
6.1 微细加工技术概述
3. 加工特征 一般加工时,多以尺寸、形状、位置精度为加工特征。
精密和超精密加工也是如此,所用加工方法偏重于能够形成 工件的一定形状和尺寸。微细加工和超微细加工却以分离或 结合原子、分子为加工对象,以电子束、激光束、离子束为 加工基础,采用沉积、刻蚀、溅射、蒸镀等手段进行各种处 理。这是因为它们各自所加工的对象不同而造成的。
2021/8/21
2
6.1 微细加工技术概述
微小尺寸加工与一般尺寸加工的不同点: 1. 精度的表示方法
在微小尺寸加工时,由于加工尺寸很小,精度就必须用 尺寸的绝对值来表示,即用去除的一块材料的大小表示,从 而引入加工单位尺寸的概念。加工单位就是去除的一块材料 的尺寸。 2. 微观机理
微细加工综述
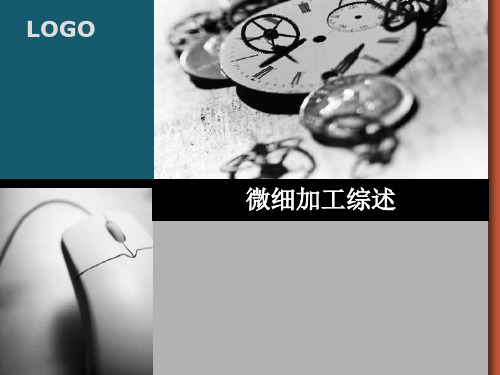
www.themegallery.co m
微细加工技术综述
1.3.3 微细线切割加工:
微细电火花线切割加工的基本原理是利用移动的 微细金属导线作电极, 对工件进行脉冲火花放电、切割 成形。 微细电火花线切割几乎可加工具有任何硬度的导 电金属材料, 且加工过程中不受宏观力的作用, 从而可 保证较好的加工精度与表面质量。广泛应用于微小齿 轮、微小花键、微小异形孔、以及半导体模具、钟表 模具等具有复杂形状的微小零件的加工。 台湾的Yunn - Shiuan Liao等开发了桌面式高精度多 功能微细电火花线切割机床, 用来加工复杂的三维微零 件。机床能够达到1μm的尺寸精度和Rmax=0.64μm的表 面粗糙度。
1986年原苏联基辅工学院用工业激光器在硬质合 金毛坯上打中心孔,孔径为0.6一1.omm,深度为 6mm; 英 国 学 者 Mark Heaten 采 用 受 激 准 分 子 激 光 在 PMMA 材料上加工出微小涡轮盘, 叶片数为31 。
激光束微细加工发展现状
2001年,德国学者Peter Heyl 研制了用于加工三维 结构的高精度激光加工机, 研究了陶瓷和硬金属的激 光加工工艺, 在WC/Co 材料上加工出微三维结构。平 均表面粗糙度达到Ra =0.16μm, 最大表面粗粗度可达 Rz=0.7μm, 所加工工件的表面粗糙度达到了高精度电 火花铣削的表面粗糙度。 瑞士某公司利用固体激光器给飞机涡轮叶片进行打 孔,可以加工直径从20腼到80腼的微孔,并且其直径 与深度之比可达1:80; 日本在厚1mm的氮化硅板上打出孔径0.Zmm的孔, 在0.05mm的陶瓷薄膜上加工出孔径 0.02mm的孔,而 在钦、白金、钨、钥等难以加工的材料上也进行了 有效的激光加工。
二、高能束流微细特种加工技术
- 1、下载文档前请自行甄别文档内容的完整性,平台不提供额外的编辑、内容补充、找答案等附加服务。
- 2、"仅部分预览"的文档,不可在线预览部分如存在完整性等问题,可反馈申请退款(可完整预览的文档不适用该条件!)。
- 3、如文档侵犯您的权益,请联系客服反馈,我们会尽快为您处理(人工客服工作时间:9:00-18:30)。
武汉工程职业技术学院毕业论文课题名称机加工细微加工技术概述及其应用学生姓名陈凯 .学号1104180317专业模具设计与制造班级 2011级模具三班指导教师秦丽萍年月日目录摘要 (3)引言 (4)第一章微细加工技术简介及国内外 (5)1.1 (5)1.2 (9)第二章微细加工技术应用实例 (11)2.1 (11)2.2 (13)总结 (15)参考文献 (16)3 微细加工技术概述及其应用摘要:微细加工原指加工尺度约在微米级范围的加工方法,现代微细加工技术已经不仅仅局限于纯机械加工方面,电、磁、声等多种手段已经被广泛应用于微细加工,从微细加工的发展来看,美国和德国在世界处于领先的地位,日本发展最快,中国有很大差距。
本文从用电火花加工方法加工微凹坑和用微铣削方法加工微小零件两方面描述了微细加工技术的实际应用。
关键词:微细加工;电火花;微铣削引言:随着科学技术的发展,近年来在IT 、医疗器械以及通讯领域,人们对微小型零件(如:微型传感器、微型加速度计、微透镜阵列等)的需求日益增加。
这种需求的增加促进了微细加工技术的发展。
在目前的多种微细加工技术中,微机电系统(MicroElectroMechanicalSystem ,MEMS)一直是主流技术之一。
由于MEMS 技术衍生于微电子技术,它的主要加工对象被限制在硅基材料上,并且工件的几何形状基本上是简单的二维形状,因而只有在大规模集成电路的批量制造等方面才是经济的。
微细切削加工技术,特别是微细铣削作为MEMS 技术的补充,由于其几乎不受加工对象材料和几何形状的限制而受到研究人员的重视,正在成为微细加工技术中的新生力量。
近年来,采用传统的机械加工方法而进行微细制造的研究越来越受到人们的重视,针对特征尺寸在410~10m 所谓中间尺度微小机械零件的微细切削制造成为一大研究热点,其原因是机加工具有几大优势:1加工精度高;2生产效率高、灵活;3能加工任意三维特征的零件;4能加工包括钢在内的多种材料;5 1微细加工技术简介及国内外研究成果1.1微细加工技术的概念微细加工原指加工尺度约在微米级范围的加工方法。
在微机械研究领域中,从尺寸角度,微机械可分为1mm~10mm的微小机械,1μm~1mm的微机械,1nm~1μm的纳米机械,微细加工则是微米级精细加工、亚微米级微细加工、纳米级微细加工的通称。
广义上的微细加工,其方式十分丰富,几乎涉及现代特种加工、微型精密切削加工等多种方式,微机械制造过程又往往是多种加工方法的组合。
从基本加工类型看,微细加工可大致分为四类:分离加工——将材料的某一部分分离出去的加工方式,如分解、蒸发、溅射、切削、破碎等;接合加工——同种或不同材料的附和加工或相互结合加工方式,如蒸镀、淀积、生长等;变形加工——使材料形状发生改变的加工方式,如塑性变形加工、流体变形加工等;材料处理或改性和热处理或表面改性等。
微细加工技术曾广泛用于大规模集成电路的加工制作,正是借助于微细加工技术才使得众多的微电子器件及相关技术和产业蓬勃兴起。
目前,微细加工技术已逐渐被赋予更广泛的内容和更高的要求,已在特种新型器件、电子零件和电子装置、机械零件和装置、表面分析、材料改性等方面发挥日益重要的作用,特别是微机械研究和制作方面,微细加工技术已成为必不可少的基本环节。
现代微细加工技术已经不仅仅局限于纯机械加工方面,电、磁、声等多种手段已经被广泛应用于微细加工,微细超精密加工的主要方法如下:微细电火花加工技术的研究起步于20世纪60年代末,是在绝缘的工作液中通过工具电极和工件间脉冲火花放电产生的瞬时、局部高温来熔化和汽化蚀除金属的一种加工技术。
由于其在微细轴孔加工及微三维结构制作方面存在的巨大潜力和应用背景,得到了高度重视。
实现微细电火花加工的关键在于微小电极的制作、微小能量放电电源、工具电极的微量伺服进给、加工状态检测、系统控制及加工工艺方法等。
微细切削技术是一种由传统切削技术衍生出来的微细切削加工方法,主要包括微细车削、微细铣削、微细钻削、微细磨削、微冲压等。
微细车削是加工微小型回转类零件的主要手段,与宏观加工类似,也需要微细车床以及相应的检测与控制系统,但其对主轴的精度、刀具的硬度和微型化有很高的要求。
图1.1为用单晶金刚石刀头加工的微型丝杠。
微细钻削的关键是微细钻头的制备,目前借助于电火花线电极磨削可以稳定地制成直径为10um的钻头,最小的可达6.5um。
微细铣削可以实现任意形状微三维结构的加工,生产效率高,便于扩展功能,对于微机械的实用化开发很有价值.图1.1微细磨削是在小型精密磨削装置上进行的,能够从事外圆以及内孔的加工。
已制备的微细磨削装置,工件转速可达2 000 r/min,砂轮转速为3 500r/min,磨削采用手动走刀方式。
为防止工件变形或损坏,用显微镜和电视显示屏监视着砂轮与工件的接触状态。
微细磨削加工的微型齿轮轴,材料为硬质合金,轮齿表面粗糙度可达到Ra0.049 um。
微机械元件的加工很多情况下要完成三维形体的微细加工,需要采用不同的蚀刻技术。
蚀刻的基本原理是在被加工零件的表面贴上一定形状的掩膜,经蚀刻剂的淋洒并去除反应产物后,工件的裸露部分逐步被刻除,从而达到设计的形状和尺寸。
根据沿晶向的蚀刻速度分为等向蚀刻与异向蚀刻。
若工件被蚀刻的速度沿各个方向相等则为等向蚀刻,它可以用来制造任意横向几何形状的微型结构,高度一般仅为几微米。
所谓微细电解加工是指在微细加工范围内(1~l 000 nm),利用金属阳极电化学溶解去除材料的制造技术,其中材料的去除是以离子溶解的形式进行的,在电解加工中通过控制电流的大小和电流通过的时间,控制工件的去除速度和去除量,从而得到高精度、微小尺寸零件的加工方法。
加工间隙的大小直接影响微细电解加工的成形精度与加工效果,通过降低加工电压、提高脉冲频率和降低电解液浓度,电解微细加工间隙可控制在10um以下。
图1.2是用幅值为2 V、脉宽为3S、频率为33 MHz的脉冲电源在镍片上加工深为5um的螺旋槽,使用的电解液为0.2 mol/L的HCL溶液,其加工间隙为600nm,表粗糙度度100 nm。
图1.21.1.1什么是微切削加工技术7 微切削是一种快速且低成本的微小零件机械加工方式,而且不受材料的限制[1],使CNC加工中心可实现2D、215D 简单特征到复杂3D曲面零件的微加工,通过使用此法加工出的微小模具可达到批量生产的目的。
1.1.2微切削的加工范畴(1) 微切削指加工尺寸在1mm以下、精度为0.01—0.001mm零件的切削加工。
(2) T.MasuzaWa定义微切削为切削厚度小于999um的切削过程[2]。
试验中他把切削厚度选择在1—200um。
(3) 国际生产工程协会CIRP物理化学科学制造过程会议把加工尺度定义在1—500um。
(4) A. Simoneau认为微切削定义应从切削特点上真正反映微切削与宏观切削的分别,尺度效应的出现。
(5) Subbiah.S认为微切削是以下三种情况下的微量材料去除过程:一是微小产品及部件的加工过程;二是制造大型工件上的微小、复杂结构;三是在大型工件上制造精密的光滑表面。
因此微切削并不完全需要微小尺寸的刀具,用宏观切削中的刀具也可以做到微切削[5]。
1.1.3.微切削影响因素(1) 尺寸效应与宏观切削不同,对于微细切削来讲,切削力与切削能量都会随着材料的去处量的减少而减少,中外很多者都对此进行了大量的实验验证,此外当微切削进给量减少到微米级别时, 切削力会出现急剧增大的现象, 此类现象归结为微纳尺度切削中的尺寸效应。
与常规尺度切削相比, 微细切削时, 刀具前刀面参与切削的面积减小, 刀刃附近区域将承担主要的材料去除工作, 此时刀具刃口半径对于切削变形和材料去除的影响不容忽视; V ogler与K i m等人[12-13]通过实验验证了最小切削厚度对切削厚度堆积的影响,他们发现在微细加工中,当进给量小于切削厚度时, 刀具经过工件, 工件表面仅发生弹性变形, 而不是常规的切削, 随着切削进给量的增加,当刀具刀刃半径与切削进给量大小相当时刀具在工件表面产生耕切现象, 此时工件产生弹塑性变形;当进给量增大到远大于刀具刀刃半径时, 此时刀具在切削中可视为锋利。
(2) 切削速度很多学者都在微细切削实验中采用高速钢、硬质合金或者金刚石材料刀具对工件进行切削,硬质合金刀具硬度高, 切削力较小,但成本较高速钢高出很多,较前两者来说金刚石刀具切削最为锋利。
除去切削液消除积屑瘤对微细切削的影响, 这几种刀具在不同切削速度下反应出切削力的规律也是不一样的。
G. Bissacco等人[14]通过大量实验发现由于前刀面的切削区域的变形及摩擦在整个切削中所占的比例较小,导致硬质合金刀具与高速钢刀具在切削时,切削速度对切削力影响并不明显; 同时由于两种材料的刀具刀刃半径较金刚石刀具大, 刃口圆弧部分对加工面所产生的挤压所占的比例较大, 从而使得切削速度对切削力的影响更小, 所以高速钢与硬质合金刀具用于微细切削时,切削速度对切削力的影响并不明显。
金刚石刀具刀刃半径较硬质合金和高速钢刀具小很多, S . S . Joshi等人[15]通过实验发现金刚石刀具随着切削速度的增加切削力下降, 且切削速度对于切削力的影响取决于最小切削厚度与刀具刀刃半径的比值。
(3) 主轴转速微细加工中,主轴转速对于微切削的影响也是不可忽视的。
Ya zhou Sun , Qing xin , Meng等人通过大量实验,发现在微细切削中主轴转速对于切削力的影响是有一定规律的。
91.2微细加工技术的研究现状从国际上微细加工技术的研究与发展看,主要形成了以美国为代表的硅基MEMS 制造技术,以德国为代表的LIGA 制造技术和以日本为代表的传统加工方法的微细化等主要流派。
他们的研究与应用情况基本上代表了国际微细加工的水平和方向。
在美国,以Moore公司和Precitech公司为代表,专门从事超精密加工技术研究和装备生产;在欧洲,英国Cranfield大学的超精密工程中心(CUPE)是世界著名的超精密加工技术研究单位之一;日本对超精密加工技术的研究相对美、英、德来说起步较晚,却是当今世界发展最快的国家。
日本通产省工业技术院机械工程实验室(MEL)于1996 年开发了世界上第一台微型化的机床-微型车床[3],长32mm、宽25mm、高30.5mm,重量为100g,主轴电机额定功率为1.5W,转速10000r/min。
用该机床切削黄铜,沿进给方向的表面粗糙度值为Rz1.5μm,加工工件的圆度为2.5μm,最小外圆直径为60μm。
切削试验中的功率消耗仅为普通车床的1/500。
MEL 开发的微细铣床,长170mm、宽170mm、高102mm,主轴用功率为36W 的无刷直流伺服电机,转速约为15600r/min。