PVD和CVD涂层方法
PVD与CVD涂层工艺比较
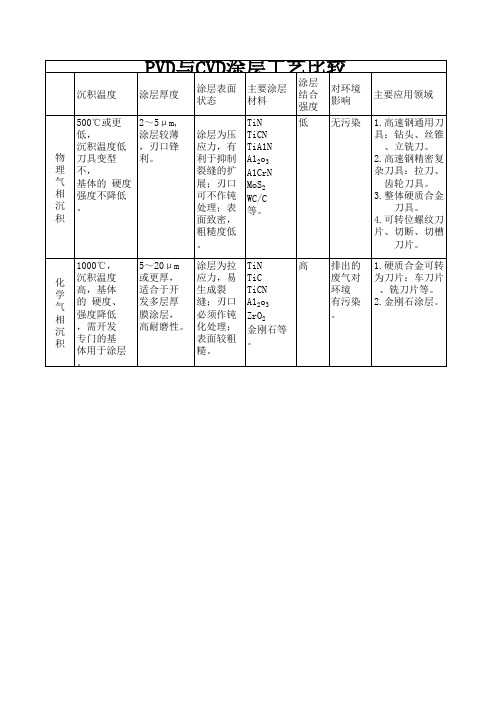
物 理 气 相 沉 积
化 学 气 相 沉 积
1000℃, 沉积温度 高,基体 的 硬度~20μ m 或更厚, 适合于开 发多层厚 膜涂层, 高耐磨性。
TiN TiC TiCN A12o3 ZrO2 金刚石等 。
高
排出的 废气对 环境 有污染 。
PVD与CVD涂层工艺比较
沉积温度 500℃或更 低, 沉积温度低 刀具变型 不, 基体的 硬度 强度不降低 。 涂层厚度 2~5μ m, 涂层较薄 ,刃口锋 利。 涂层表面 状态 涂层为压 应力,有 利于抑制 裂缝的扩 展;刃口 可不作钝 处理;表 面致密, 粗糙度低 。 涂层为拉 应力,易 生成裂 缝;刃口 必须作钝 化处理; 表面较粗 糙。 主要涂层 材料 TiN TiCN TiA1N A12o3 A1CrN MoS2 WC/C 等。 涂层 结合 强度 低 对环境 影响 无污染 主要应用领域 1.高速钢通用刀 具:钻头、丝锥 、立铣刀。 2.高速钢精密复 杂刀具:拉刀、 齿轮刀具。 3.整体硬质合金 刀具。 4.可转位螺纹刀 片、切断、切槽 刀片。 1.硬质合金可转 为刀片:车刀片 、铣刀片等。 2.金刚石涂层。
PVD和CVD
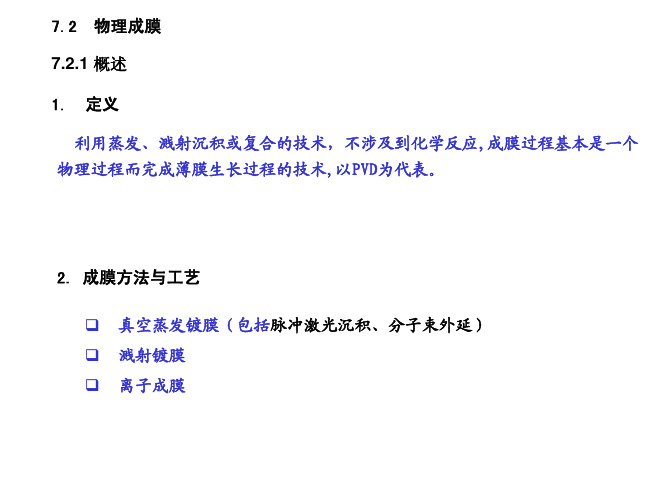
其特点是: 1) 2) 辉光放电空间产生的电子,获得足够的能量,足以产生碰撞电离,减少 对二次电子的依赖,降低击穿电压 射频电压能够通过任何类型的阻抗耦合进去,所以,电极无需是导体, 可以溅射任何材料
(3)电磁场中的气体放电 在放电电场空间加上磁场,放电空间中的电子就要围绕磁力线作回旋运 动,其回旋半径为eB/mv,磁场对放电的影响效果,因电场与磁场的相互位置 不同而有很大的差别。
(2)射频溅射镀膜 射频是无线电波发射范围的频率,为避免干扰电台工作,溅射专用频率规定 为13.56MHz。
适用于导体、半导体、绝 缘体
缺点 大功率射频电源造价昂贵 具有人身防护问题 不适宜工业生产应用
(3)磁控溅射镀膜 与直流溅射相似,不同之处在于阴极靶的后面设置磁场,磁场在靶材表面 形成闭合的环形磁场,与电场正交。
应变能释放出现刃位错
The strained film said: “We are all tired enough, please give us a break!” Oh, it is more comfortable now, although a few of our colleagues are still suffering the pressure.
缺点: 速度太慢,不适宜镀制工件,工业上应用很难
3)高频感应加热 高频线圈通以高频电流后,产生涡流电流,致内置材料升温,熔化成膜。
4)电弧加热 高真空下,被蒸发材料作阴极、内接铜杆作阳极,通电压,移动阳电极尖端 与阴极接触,阴极局部熔化发射热电子,再分开电极,产生弧光放电,使阴极 材料蒸发成膜。
5)激光加热 非接触加热。用激光作热源,使被蒸发材料汽化成膜。常用CO2、Ar、YAG钕 玻璃,红宝石等大功率激光器。
薄膜技术中PVD和CVD的区别详解

Page 24
Page 14
溅射法
直流溅射沉积装置
真空系统中,靶材
是需要溅射的材料, 它作为阴极。相对于 作为阳极的衬底加有 数千伏的电压。在对 系统预抽真空以后, 充入适当压力的惰性 气体。
Page 15
溅射法
溅射法分类
(1)直流溅射; (2)高频溅射; (3)磁控溅射; (4)反应溅射; (5)离子镀。
Page 16
Page 10
真空蒸镀
蒸发源分类
(一)电阻加热蒸发 (二)电子束加热蒸发 (三)电弧加热蒸发 (四)激光加热蒸发
Page 11
真空蒸镀
真空蒸发的影响因素
1.物质的蒸发速度 2.元素的蒸汽压 3.薄膜沉积的均匀性 4.薄膜沉积的纯度
Page 12
真空蒸镀
薄膜沉积的纯度
蒸发源的纯度; 加热装置、坩埚可能造成的污染; 真空系统中的残留气体。
物理气相沉积(PVD)
物理气相沉积法过程的三个阶段: 1,从原材料中发射出粒子; 2,粒子运输到基片; 3,粒子在基片上凝结、成核、长大、成膜。
Page 6
物理气相沉积(PVD)
PVD
物理气相沉积技术中最为基本的两种方法就 是蒸发法和溅射法,另外还有离子束和离子助等 等方法。
蒸发法相对溅射法具有一些明显的优点,包 括较高的沉积速度,相对较高的真空度,以及由 此导致的较高的薄膜质址等。
薄膜制备
张洋洋
薄膜制备工艺包括:薄膜制备方法的 选择,基体材料的选择及表面处理, 薄膜制备条件的选择和薄膜结构、性 能与工艺参数的关系等。
Page 2
薄
膜
物理气相沉积(PVD)
制
化学气相沉积 ( CVD)
CVD和PVD工艺比较

VII. 最后一个比较因素是操作运行安全问题 操作运行安全问题。PVD 操作运行安全问题 是一种完全没有污染的工序,有人称它为“绿色工 程”。而CVD的反应气体、反应尾气都可能具有一 定的腐蚀性,可燃性及毒性,反应尾气中还可能有 粉末状以及碎片状的物质,因此对设备、环境、操 作人员都必须采取一定的措施加以防范。
V. 在CVD工艺过程中,要严格控制工艺条件 控制工艺条件,否 控制工艺条件 则,系统中的反应气体或反应产物的腐蚀作用会使 基体脆化。 VI. 比较CVD和PVD这两种工艺的成本 成本比较困难, 成本 有人认为最初的设备投资PVD是CVD的3一4倍,而 PVD工艺的生产周期是CVD的1/10。在CVD的一个 操作循环中,可以对各式各样的工件进行处理,而 PVD就受到很大限制。综合比较可以看出,在两种 工艺都可用的范围内,采用PVD要比CVD代价高。
厚度上的区别正好可以弥补 PVD阶梯覆盖性能的不足 阶梯覆盖性能的不足
III. CVD镀层往往比各种PVD镀层略厚一些,前者厚 厚 度在7.5µm左右,后者通常不到2.5µm厚。CVD镀层的 表面略比基体的表面粗糙些。相反,PVD镀膜如实地 反映材料的表面,不用研磨就具有很好的金属光泽, 这在装饰镀膜方面十分重要。
I. 工艺温度高低 CVD 和 PVD 之间的主要区别。 工艺温度高低是 温度对于高速钢镀膜具有重大意义。 CVD 法的工艺 温度超过了高速钢的回火温度,用 CVD 法镀制的高 速钢工件,必须进行镀膜后的真空热处理,以恢复硬 度。镀后热处理会产生不容许的变形。 II. CVD 工艺对进人反应器工件的清洁 要求 PVD 清洁要求 清洁 要求比 工艺低一些,因为工件表面的一些脏东西很容易在高 温下烧掉。此外,高温下得到的镀层结合强度要更好 些。
PVD和CVD涂层方法
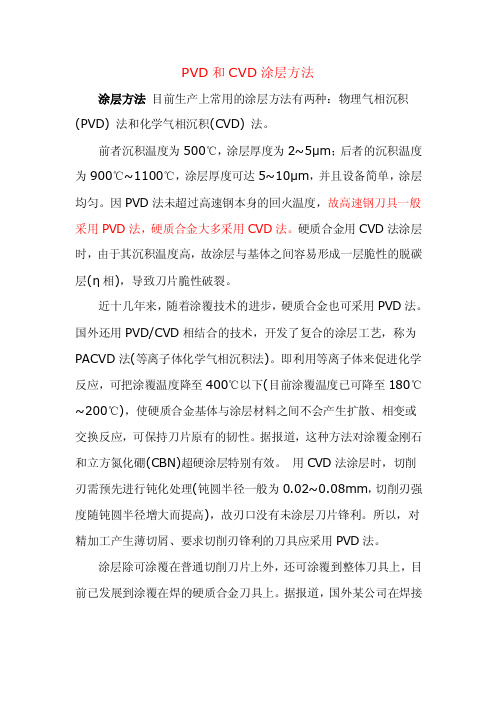
PVD和CVD涂层方法涂层方法目前生产上常用的涂层方法有两种:物理气相沉积(PVD) 法和化学气相沉积(CVD) 法。
前者沉积温度为500℃,涂层厚度为2~5µm;后者的沉积温度为900℃~1100℃,涂层厚度可达5~10µm,并且设备简单,涂层均匀。
因PVD法未超过高速钢本身的回火温度,故高速钢刀具一般采用PVD法,硬质合金大多采用CVD法。
硬质合金用CVD法涂层时,由于其沉积温度高,故涂层与基体之间容易形成一层脆性的脱碳层(η相),导致刀片脆性破裂。
近十几年来,随着涂覆技术的进步,硬质合金也可采用PVD法。
国外还用PVD/CVD相结合的技术,开发了复合的涂层工艺,称为PACVD法(等离子体化学气相沉积法)。
即利用等离子体来促进化学反应,可把涂覆温度降至400℃以下(目前涂覆温度已可降至180℃~200℃),使硬质合金基体与涂层材料之间不会产生扩散、相变或交换反应,可保持刀片原有的韧性。
据报道,这种方法对涂覆金刚石和立方氮化硼(CBN)超硬涂层特别有效。
用CVD法涂层时,切削刃需预先进行钝化处理(钝圆半径一般为0.02~0.08mm,切削刃强度随钝圆半径增大而提高),故刃口没有未涂层刀片锋利。
所以,对精加工产生薄切屑、要求切削刃锋利的刀具应采用PVD法。
涂层除可涂覆在普通切削刀片上外,还可涂覆到整体刀具上,目前已发展到涂覆在焊的硬质合金刀具上。
据报道,国外某公司在焊接式的硬质合金钻头上采用了PCVD法,结果使加工钢料时的钻头寿命比高速钢钻头长10倍,效率提高5倍。
涂层成份又有哪些呢?各自的区别在哪里,应用面怎样。
通常使用的涂层有:TiC、TiN、Ti(C.N)、Gr7O3、Al2O3等。
以上几种CVD的硬质涂层基本具备低的滑动摩擦系数,高的抗磨能力,高的抗接触疲劳能力,高的表面强度,保证表面具有足够的尺寸稳定性与基体之间有高的粘附强度。
PVD与CVD涂层工艺比较PVD与CVD涂层工艺比较沉积温度涂层厚度涂层表面状态主要涂层材料涂层结合强度对环境影响主要应用领域物理气相沉积500℃或更低,沉积温度低刀具变型不,基体的硬度强度不降低。
玻璃工艺中的表面改性与涂层技术
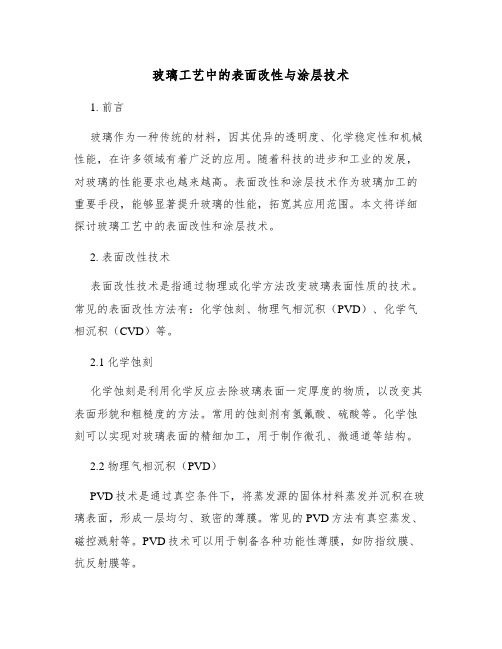
玻璃工艺中的表面改性与涂层技术1. 前言玻璃作为一种传统的材料,因其优异的透明度、化学稳定性和机械性能,在许多领域有着广泛的应用。
随着科技的进步和工业的发展,对玻璃的性能要求也越来越高。
表面改性和涂层技术作为玻璃加工的重要手段,能够显著提升玻璃的性能,拓宽其应用范围。
本文将详细探讨玻璃工艺中的表面改性和涂层技术。
2. 表面改性技术表面改性技术是指通过物理或化学方法改变玻璃表面性质的技术。
常见的表面改性方法有:化学蚀刻、物理气相沉积(PVD)、化学气相沉积(CVD)等。
2.1 化学蚀刻化学蚀刻是利用化学反应去除玻璃表面一定厚度的物质,以改变其表面形貌和粗糙度的方法。
常用的蚀刻剂有氢氟酸、硫酸等。
化学蚀刻可以实现对玻璃表面的精细加工,用于制作微孔、微通道等结构。
2.2 物理气相沉积(PVD)PVD技术是通过真空条件下,将蒸发源的固体材料蒸发并沉积在玻璃表面,形成一层均匀、致密的薄膜。
常见的PVD方法有真空蒸发、磁控溅射等。
PVD技术可以用于制备各种功能性薄膜,如防指纹膜、抗反射膜等。
2.3 化学气相沉积(CVD)CVD技术是通过在真空条件下,将气体前驱体在加热或光照的条件下分解,在玻璃表面沉积一层薄膜。
CVD技术可以实现对玻璃表面进行纳米级加工,用于制备纳米结构薄膜。
3. 涂层技术涂层技术是在玻璃表面涂覆一层或多层涂层,以改善玻璃的性能和增加其功能。
常见的涂层方法有溶胶-凝胶法、喷涂法、 roll-to-roll 涂层等。
3.1 溶胶-凝胶法溶胶-凝胶法是通过溶液中的金属盐或氧化物与醇或酸反应,形成溶胶,随后溶胶凝胶化形成涂层。
该方法可以实现对玻璃表面进行精细调控,制备出具有特定性能的涂层,如光学涂层、抗菌涂层等。
3.2 喷涂法喷涂法是将涂料通过喷枪喷涂在玻璃表面,形成均匀的涂层。
喷涂法适用于大面积涂层制备,效率高,成本低。
常见的喷涂方法有空气喷涂、高压喷涂等。
3.3 roll-to-roll 涂层roll-to-roll 涂层是一种连续涂层制备技术,通过滚轴将涂料均匀涂覆在玻璃表面。
涂层刀具的涂层材料、涂层方法及发展方向
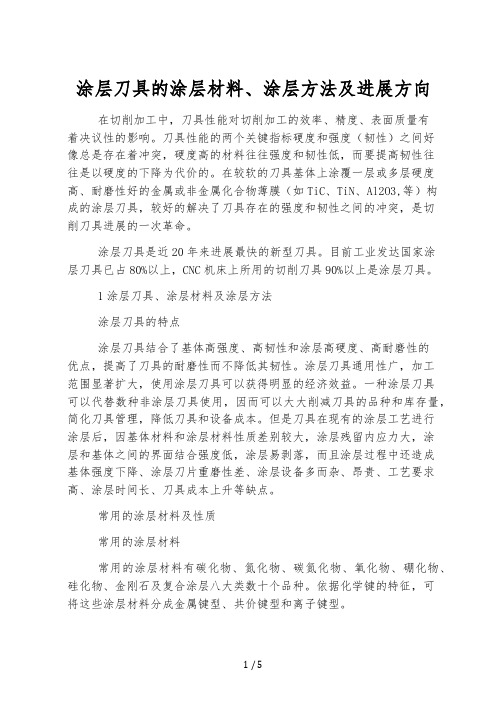
涂层刀具的涂层材料、涂层方法及进展方向在切削加工中,刀具性能对切削加工的效率、精度、表面质量有着决议性的影响。
刀具性能的两个关键指标硬度和强度(韧性)之间好像总是存在着冲突,硬度高的材料往往强度和韧性低,而要提高韧性往往是以硬度的下降为代价的。
在较软的刀具基体上涂覆一层或多层硬度高、耐磨性好的金属或非金属化合物薄膜(如TiC、TiN、Al2O3,等)构成的涂层刀具,较好的解决了刀具存在的强度和韧性之间的冲突,是切削刀具进展的一次革命。
涂层刀具是近20年来进展最快的新型刀具。
目前工业发达国家涂层刀具已占80%以上,CNC机床上所用的切削刀具90%以上是涂层刀具。
1涂层刀具、涂层材料及涂层方法涂层刀具的特点涂层刀具结合了基体高强度、高韧性和涂层高硬度、高耐磨性的优点,提高了刀具的耐磨性而不降低其韧性。
涂层刀具通用性广,加工范围显著扩大,使用涂层刀具可以获得明显的经济效益。
一种涂层刀具可以代替数种非涂层刀具使用,因而可以大大削减刀具的品种和库存量,简化刀具管理,降低刀具和设备成本。
但是刀具在现有的涂层工艺进行涂层后,因基体材料和涂层材料性质差别较大,涂层残留内应力大,涂层和基体之间的界面结合强度低,涂层易剥落,而且涂层过程中还造成基体强度下降、涂层刀片重磨性差、涂层设备多而杂、昂贵、工艺要求高、涂层时间长、刀具成本上升等缺点。
常用的涂层材料及性质常用的涂层材料常用的涂层材料有碳化物、氮化物、碳氮化物、氧化物、硼化物、硅化物、金刚石及复合涂层八大类数十个品种。
依据化学键的特征,可将这些涂层材料分成金属键型、共价键型和离子键型。
涂层材料的性质金属键型涂层材料(如TiB2、TiC、TiN、VC、WC等)熔点高、脆性低、界面结合强度高、交互作用趋势强、多层匹配性好,具有良好的综合性能,是最一般的涂层材料。
共价键型涂层材料(如B4C、SiC、BN、金刚石等)硬度高、热胀系数低、与基体界面结合强度差、稳定性和多层匹配性差。
第6章PVD与CVD

一些金属的蒸发温度
由上表可见大多数金属的蒸发温度都在1000 度到2000度之间,而钨、钼的熔点都高于2000度, 因此加热的金属材料一般都选钨、钼。 电阻法的缺点是膜材料与加热材料之间产生扩 散或反应,使加热材料本身的熔点和蒸发点降低, 以致造成镀得的膜层含有杂质。大多数膜材料在熔 化后将于加热材料浸润。表面扩张,附着在加热器 上形成面蒸发源,蒸发效果比较好。反之,若膜材 料与加热材料不侵润,膜材料将融为一个液球,成 为点蒸发源,如果加热器的形状不合适液球将从加 热器上脱落下来,使蒸镀失败。因此蒸镀时要根据 膜材料的性质,注意选择加热器的形状。
6.3.2 EMI溅射镀膜特点 价格低(国内拥有自主知识产权的话)。 真空溅射加工的金属薄膜厚度只有0.5~2µm,绝对不影响装配。 真空溅射是彻底的环保制程,绝对环保无污染。 欲溅射材料无限制, 任何常温固态导电金属及有机材料、绝缘材料皆可 使用(例:铜、铬、银、金、不锈钢、铝、氧化矽SiO2等)。 被溅射基材几无限制(ABS、PC、PP、PS、玻璃、陶瓷、epoxy resin 等)。 膜质致密均匀、膜厚容易控制。 附着力强(ASTM3599方法测试4B)。 可同时搭配多种不同溅射材料之多层膜。并且,可随客户指定变换镀 层次序。
6.2真空蒸镀 真空蒸镀
6.2.1 原理 在真空中将蒸镀材料加热蒸发产生蒸气,使其附着在基板 上凝聚成薄膜。真空蒸镀属于物理气相沉积法。 1.蒸发过程 1)汽化热 2)蒸气压 3)蒸发温度 4)蒸发速率
6.2.2 真空蒸镀的关键部件
1.蒸发器
蒸发器的加热温度要达到膜材料熔化的温度,其加 热方式通常为电阻法、电子束法等。 电阻法是用高熔点金属做成适当的形状的加热器, 并将膜材料放在上面加热,利用电流的热效应使加 热器温度达到材料蒸发的温度,膜材料蒸发并淀积 在基板上。
- 1、下载文档前请自行甄别文档内容的完整性,平台不提供额外的编辑、内容补充、找答案等附加服务。
- 2、"仅部分预览"的文档,不可在线预览部分如存在完整性等问题,可反馈申请退款(可完整预览的文档不适用该条件!)。
- 3、如文档侵犯您的权益,请联系客服反馈,我们会尽快为您处理(人工客服工作时间:9:00-18:30)。
.
PVD和CVD涂层方法
涂层方法目前生产上常用的涂层方法有两种:物理气相沉积(PVD) 法和化学气相沉积(CVD) 法。
前者沉积温度为500℃,涂层厚度为2~5μm;后者的沉积温度为900℃~1100℃,涂层厚度可达5~10μm,并且设备简单,涂层均匀。
因PVD法未超过高速钢本身的回火温度,故高速钢刀具一般采用PVD法,硬质合金大多采用CVD法。
硬质合金用CVD法涂层时,由于其沉积温度高,故涂层与基体之间容易形成一层脆性的脱碳层(η相),导致刀片脆性破裂。
近十几年来,随着涂覆技术的进步,硬质合金也可采用PVD法。
国外还用PVD/CVD相结合的技术,开发了复合的涂层工艺,称为PACVD法(等离子体化学气相沉积法)。
即利用等离子体来促进化学反应,可把涂覆温度降至400℃以下(目前涂覆温度已可降至180℃~200℃),使硬质合金基体与涂层材料之间不会产生扩散、相变或交换反应,可保持刀片原有的韧性。
据报道,这种方法对涂覆金刚石和立方氮化硼(CBN)超硬涂层特别有效。
用CVD法涂层时,切削刃需预先进行钝化处理(钝圆半径一般为0.02~0.08mm,切削刃强度随钝圆半径增大而提高),故刃口没有未涂层刀片锋利。
所以,对精加工产生薄切屑、要求切削刃锋利的刀具应采用PVD法。
涂层除可涂覆在普通切削刀片上外,还可涂覆到整体刀具上,目前已
发展到涂覆在焊的硬质合金刀具上。
据报道,国外某公司在焊接;.
.
式的硬质合金钻头上采用了PCVD法,结果使加工钢料时的钻头寿命比高速钢钻头长10倍,效率提高5倍。
涂层成份又有哪些呢?各自的区别在哪里,应用面怎样。
通常使用的涂层有:TiC、TiN、Ti(C.N)、Gr7O3、Al2O3等。
以上几种CVD的硬质涂层基本具备低的滑动摩擦系数,高的抗磨能力,高的抗接触疲劳能力,高的表面强度,保证表面具有足够的尺寸稳定性与基体之间有高的粘附强度。
PVD与CVD涂层工艺比较
;.
.
PVD与CVD涂层工艺比较
涂层
涂层表面主要涂层对环境
主要应用领域结合强沉积温度涂层厚度
状态材料影响
度
1.高速钢通用刀具:TiN
钻头、丝锥、物立铣刀。
涂层为压应TiCN
℃或更低,500刀理2.~25μm, 力,有利于抑高速钢精密复杂TiA1N
沉积温度低气刀具。
齿轮涂层较薄具:拉刀、制裂缝的扩A1o32刀具变型不,低无污染刀相,刃口锋 3.展;刃口可不整体硬质合金A1CrN
基体的硬度沉利。
具作钝处理;表。
MoS2强度不降低。
可转位螺纹刀片、积4.面致密,粗糙WC/C 等。
度低。
切断、切槽刀片。
1000℃,520μm沉积温度~TiN
涂层为拉应化学硬质合金可转为刀或更厚, 1. 高,基体TiC
排出的废气力,易生成裂气片:车刀片、铣刀片适合于开硬度、的TiCN
缝;刃口必须相高对环境等。
发多层厚强度降低A1o32作钝化处理;沉有污染。
膜涂层,金刚石2.涂层。
,需开发ZrO2积表面较粗糙。
专门的基高耐磨性。
等。
金刚石
体用于涂层。
;.。