装载机论文中英文对照资料外文翻译文献
装载机中英文翻译
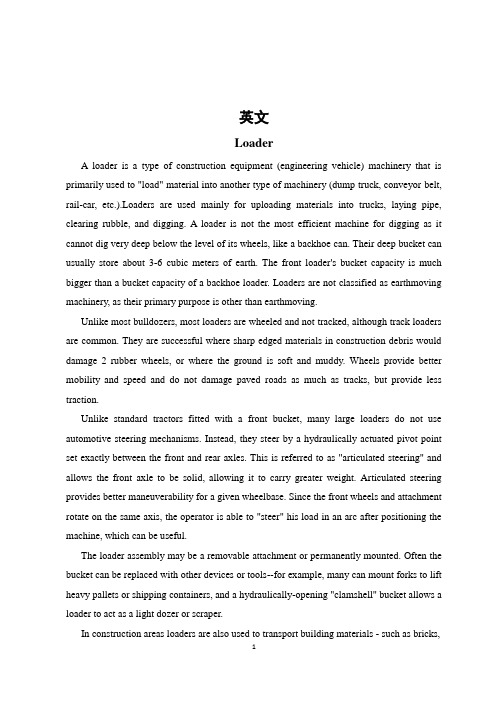
英文LoaderA loader is a type of construction equipment (engineering vehicle) machinery that is primarily used to "load" material into another type of machinery (dump truck, conveyor belt, rail-car, etc.).Loaders are used mainly for uploading materials into trucks, laying pipe, clearing rubble, and digging. A loader is not the most efficient machine for digging as it cannot dig very deep below the level of its wheels, like a backhoe can. Their deep bucket can usually store about 3-6 cubic meters of earth. The front loader's bucket capacity is much bigger than a bucket capacity of a backhoe loader. Loaders are not classified as earthmoving machinery, as their primary purpose is other than earthmoving.Unlike most bulldozers, most loaders are wheeled and not tracked, although track loaders are common. They are successful where sharp edged materials in construction debris would damage 2 rubber wheels, or where the ground is soft and muddy. Wheels provide better mobility and speed and do not damage paved roads as much as tracks, but provide less traction.Unlike standard tractors fitted with a front bucket, many large loaders do not use automotive steering mechanisms. Instead, they steer by a hydraulically actuated pivot point set exactly between the front and rear axles. This is referred to as "articulated steering" and allows the front axle to be solid, allowing it to carry greater weight. Articulated steering provides better maneuverability for a given wheelbase. Since the front wheels and attachment rotate on the same axis, the operator is able to "steer" his load in an arc after positioning the machine, which can be useful.The loader assembly may be a removable attachment or permanently mounted. Often the bucket can be replaced with other devices or tools--for example, many can mount forks to lift heavy pallets or shipping containers, and a hydraulically-opening "clamshell" bucket allows a loader to act as a light dozer or scraper.In construction areas loaders are also used to transport building materials - such as bricks,pipe, metal bars, and digging tools - over short distances.Loaders are also used for snow removal, using their bucket or a snowbasket, but usually using a snowplow attachment. They clear snow from streets, highways and parking lots. They sometimes load snow into dump trucks for transport.Front loaders gained popularity during the last two decades, especially in urban engineering projects and small earthmoving works. Many engineering vehicle manufacturers offer a wide range of loaders, the most notable are those of John Deere, Caterpillar, Case, V olvo, Komatsu and Liebherr.The following we will introduce Carter 938G Series II Wheel Loader.EngineThe 938G II provides more power, excellent fuel economy, and reduced maintenance. Turbocharged, ATAAC. Turbocharging packs dense air into the cylinders for more complete combustion and lower emissions. Air-to-air aftercooling (ATAAC) provides a separate cooling system for intake manifold air. The ATAAC system reduces smoke and emissions by providing cooler inlet air for more efficient combustion.Constant Net Horsepower. The 938G II’s electronic engine is integrated with an on-demand cooling fan. The engine compensates for varying fan loads and provides constant net horsepower, regardless of operating conditions. A consistent level of “working” horsepower is provided and fuel consumption is reduced.Oil Change Intervals. The engine oil change interval is increased to500 hours (with CH-4 oil), reducing costs and downtimePowerful Performance. The 3126B ATAAC engine delivers net power of 119 kW (160 hp), and meets EPA Tier 2 emissions standards. Its advanced system keeps fuel at low pressure in the fuel lines until it is injected into the cylinder. Fuel pressure is created hydraulically in response to a signal from the ADEM III™ Electronic Control Module.Electronic Control Module. The Advanced Diesel Engine Module (ADEM III) fuel system isa proprietary electronic control module, which provides improved engine response and fuel efficiency,plus advanced diagnostics and reduced emissions. Altitude capability is increased to 3050 meters (10,000 feet) without derating. ADEM III allows full electronic integration of the engine and transmission for maximum power train efficiency.Power TrainAdvanced Caterpillar power train is reliable and fuel efficient.Electronic Power Shift Transmission.The electronic power shift transmission with automatic shift capability is a countershaft design built by Caterpillar. It is electronically controlled and allows full power shifts and directional changes. Fully modulated gear shifts contribute to operator comfort and increase component life.Electronic Clutch Pressure Control (ECPC). Senses input from both the transmission and the operator controls in the cab to modulate each individual clutch through a proportional electro-hydraulic valve. This results in smoother gear changes and improved shift quality. Energy is modulated into the clutches, resulting in longer clutch life.Integrated Braking System. New for G Series II, IBS integrates downshifting and transmission neutralization into the left-hand brake pedal. IBS provides smooth, optimized transmission neutralizer performance with a greater range of adjustability. The Integrated Braking System also lowers owning and operating costs by reducing axle oil temperatures, which can extend service brake life.Easy Service. Daily transmission oil level check is done from the ground through a well-protected sight gauge.An oil sampling valve allows quick,clean access to the transmission for S•O•SSM oil analysis.Cooling SystemNew G Series II cooling package reduces radiator plugging and improves fuel efficiency. Reverse Flow. Air enters through the rear grill and exits out the top opening and side hood doors. Rear air flow picks up less debris from the ground, reducing plugging.Improved System Access. The 938G II adds a swing-out grill, hydraulic oil cooler and air conditioner condenser for easier cleaning. Side panels open to allow access to both sides of all cores for cleaning. A heavy duty Airborne Debris Grill, with 4 mm perforations is available as an attachment.On-Demand Fan. Electronically controlled, variable speed on-demand fan adjusts to meet the varying cooling requirements of the machine. Fan speed is determined by oil, coolant and inletmanifold temperatures. In cooler operating conditions, average fan speed is reduced, resulting in less fuel consumption, lower noise levels and less radiator plugging.Unit Core Radiator. New unit core radiator with square wave shaped fins.Lower fin density (6 fins per inch) allows debris to pass through more easily.Environmental FeaturesCaterpillar cares about the environment and continues to develop innovative solutions.Low Exhaust Emissions. The Cat 3126B ATAAC engine used in the 938G Series II is a low emission engine designed to meet Tier 2 emission regulations. It is electronically controlled, with air-to-air aftercooling for more efficient combustion and cleaner emissions.Reduced Sound. The electronic on-demand fan automaticallyregulates fan speed depending on cooling requirements. The fan draws less horsepower in cooler ambient temperatures, which reduces fuel consumption. Sound levels are also reduced when the fan slows down.There is additional insulation around the engine to reduce sound levels.Environmental Fluids. Extended Life Coolant/Antifreeze with anti-foaming and anti-corrosion properties provide extended service intervals (up to 6000 hours) and requires less frequent fluid changes and disposals. Air conditioning refrigerant is CFC-free. Operator StationThe ultimate in wheel loader operator comfort and efficiency.1 Steering. Low effort hand metering unit steering. Tilt steering column helps fit the wheel to the operator. Load sensing steering directs power through the steering system only when needed. When not steering, more engine power is available to generate rimpull, breakout and lift forces.2 Excellent Visibility. The front window provides remarkable forward and peripheral viewing, including the machine wheels and bucket corners. Bonded glass in the windshield eliminates frame obstructions.The sloping hood provides excellent visibility to the rear of the machine.3 Finger Tip Controls. New pilot-assisted hydraulic implement controls deliver comfortable, low-effort operation. Single lever joystick and lift lever F-N-R switch are available as attachments.4 New Instrument Cluster. Gauges, status indicators and alert indicators are now centrally located. 3-level warning system monitors key functions. The system alerts the operator of immediate or impending problems with engine oil pressure, parking brake, fuel pressure,electrical system, brake oil pressure,hydraulic oil temperature, transmission filter bypass, engine inlet manifold temperature, primary steering oil pressure and the air inlet heater. LED warning indicators with no bulbs to replace.5 Cab Access. Left and right side doors swing open 180 degrees and latch for optimal ventilation, visibility and communication to ground level. Left and right side sliding windows are available as an attachment. Full service platforms are provided on both sides of the machine for safety and easy maintenance access.6 Floor Mounted Pedals. All pedals including the new electronic governor,are floor mounted for greater operator comfort. Left pedal incorporates the new Integrated Braking System that combines service brake, transmission neutralizer and downshift functions.7 Generous Storage partments for lunchbox, coolersand cups.8 Seat Options. The standard cloth and vinyl seat adjusts 6 ways. A new Caterpillar Contourair suspension seat (attachment) provides increased operator comfort with 6-way adjustment and automotive-style lumbar support.9 Electronic Autoshift Control. Set for manual or one of two fully automatic shifting modes.10 Ride Control System Switch.Attachment that reduces fore and aft pitch for a smoother, more comfortable ride. Allows the selection of three different modes: Off –always off service. On – always in service.Auto – the system is automatically actuated when the machine travels at a speed greater than 9 km (6 mph).11 Transmission Neutralizer Lockout Switch. Rocker switch that locks out the neutralizer. Defaults back to neutralizer “on” upon machine start up.译文装载机装载机是一种主要用于向另一种机械(自卸车、输送皮带、铁路运输车辆等)“装载”物料的建设机械(工程车辆)设备。
机械毕业设计外文翻译装载机进展概况

装载机进展概况AbstractThis paper have discussed s.s. ZL-50 type fork-lift truck mainly overall fictitious prototype design as well as some kinds of typical schoolwork operating modes imitate and emulate , include equipment and the overall parts needed build mould. In this design course, have applied ADAMS software and the software of PRO/ENGINEER. ADAMS software is used in the emulation of some kinds of schoolwork operating modes, and the software of PRO/ENGINEER is used to build mould mainly. Through the simulated emulation for some kinds of overall schoolwork operating modes, can see relatively distinctly the overall possible condition in actual schoolwork course that met , can in time modify , have reduced actual design time , have raised production efficiency.The innovation of this design Zhi is in in, imitate and have emulated fork-lift truck the 3 kinds of typical schoolwork operating mode in actual schoolwork, is effect again have imitated in actual schoolwork the hydraulic impact of use, so when being helpful to solve actual loading, the actual problem of meeting the stock that is hard to uninstall can so raise production efficiency.Key words: Fork-lift truck 、fictitious prototype , build mould, emulation, optimization、production efficiencyLoader DevelopmentChina's modern 20 wheel loaders began in the mid-1960s of the Z435. The aircraft as a whole rack, rear axle steering. After years of hard work, the attraction was the world's most advanced technology wheel loader on the basis of the successful development of the power of 162 KW of shovel-fit wheel loaders, stereotypes for Z450 (later ZL50), and in 1971 December 18, formally appraised by experts. Thus the birth of China's first articulated wheel loader, thus creating our industry loader formation and development history.Z450-type loader with hydraulic mechanical transmission, power shift, Shuangqiaoshan drive, hydraulic manipulation, articulated power steering, gas oil Afterburner brake wheel loaders, and other modern, the basic structure of the world's advanced level for the time . Basically represent the first generation of wheeled loading the basic structure. The aircraft in the overall performance of dynamic, and insertion force a rise of power and flexibility, manipulation of light, the higher operating efficiency of a series of advantages.1978, Heavenly Creations by the Department in accordance with the requirements of machinery, worked out to LIUGONG Z450-based type of wheel loaders series of standards. The development of standards, with reservations Zrepresentatives loaders, L replaced by "4" on behalf of wheel, for ZL50 to Z450, it is so developed a LIUGONG ZL50-based China ZL-wheel loaders series of standards, this is Wong loader on the development of China's a major turning point. The standard was worked out by the industry after the division of labor, LIUGONG Xiamen ZL40 the manufacture of the large and medium wheel loaders, as workers, to the following small and medium-sized manufacturing ZL30 wheel loaders, and gradually formed a LIUGONG Xiamen workers, and 10% for workers at the loader to four backbone enterprises. To the late 1970s, early 1980s loader manufacturing enterprises in China has increased to more than 20, China has initially formed the loader industry. So far, China has developed wheel loader to the third generation, but the basic structure is still the Z450 (ZL50) evolved from. Change is not a very large second generation, third generation of some larger changes. 2001 China loader industry-wide total sales have exceeded 30,000 Taiwan, the world loader in the forefront of the market. Therefore, at present, China has become the world's loader marketing power.Prospect of small loaderFor a long time, small loader always been neglected in the status of a government department, not to regulate the management of the industry, well-known businesses loader products is dismissive. However, these did not affect small loader (hereinafter referred to small equipment) rapid development, and now with a small market despite its huge market demand has attracted such as the Long renowned engineering machinery enterprises to participate in the competition, the main battlefield in the rural areas with the small size of the market, sales have already reached 4 ~ 5 million, more than 200 brands to participate in market competition. But small market can be said to be installed speed expansion disorderly competition coexist. How to achieve industrial upgrading is placed in front of the small equipment industry must resolve a problem.Lack industry attributionCompared with large and medium-sized industries loaders, small with the development of the industry can use "plan" to describe, not only government departments related to the absence of industrial policies or development plans, and to date, industry has not completely clear attribution, the reality of the small equipment industries across engineering machinery, agricultural machinery and construction machinery, the three industries of grey areas. Despite the small market with a flourishing, but all small equipment manufacturers and dealers can dodge exists in the industry before the many obstacles to development.Small installed mainly refers to the rated load between 0.3 ~ 0.9 T products, also known as micro-loader. As industry ownership is not clear, with small products has been no unified national technology and quality standards, the overwhelming majority of products are installed in the small-wheeled tractor developed on the basis of the. In addition small installed the product is currently used by the main component partsfrom tractors and light truck, not by the needs of small equipment for low-speed heavy-duty bridge, special bins key component parts, including even small projects with special tires. As a low technical content, resulting in a very low threshold of industry and become the de facto "open" industry, any person, business can be very easily installed into small industries.Small enterprises have installed a number of "fans", according to Construction Machinery Association Scraper Branch Secretary-General Chen Kai Yun, a conservative estimate at more than 200. More concentrated in Shandong Laizhou, Taian, Weifang, in Luoyang, Henan Province, Quanzhou, Fujian Province, and other places, annual sales of more than 2,000 Taiwan enterprises with a small handful, the majority of small businesses with annual sales in 3200 by the following, with the production of small enterprises , the same easy to set up and close down.It is precisely because the strength of small enterprises with very limited products without high technology content, in the vast majority of enterprises to participate in market competition are in the process of basically a single means to price competition to sell products for the purpose, without taking into account future market things. In the common with the credit industry, services, brand competition means small industry basically not installed, in addition to differences in the strength of enterprises and product differentiation, marketing and management philosophy that is thedeep-seated causes.Because users of the products of small equipment to mainly rural users, and users can only cover rural farm machinery sales networks, construction machinery and construction machinery sales are only part of the network coverage in rural areas. And the sale of equipment similar, with small products also requires agents or distributors can take the initiative to sell products to users and to users with standard and thoughtful service, and farm machinery dealers more customary sit shop operator, has no sales force, There is no specialized service teams, more difficult to expect the market planning, customer management. Construction machinery dealers and farm machinery dealers also have a lot of similarities, and engineering machinery dealers not accustomed to deal with rural users. Therefore, the small market is not mature with the sales network, to a large extent affected the market maturation process can not be achieved on the one hand, the user guide, on the other hand, can not be achieved on the manufacturers facilitating role. Operating environment and the use of the different habits, resulting in a lack of support for non-small pieces of installed products can hardly meet the actual needs of users, increasing the cost of services at the same time, improve customer satisfaction become almost impossible task.Increased market differentiationUnlike the preceding two years, with no small on the future of the market is basically no doubts. However, when the small rural installed by the new face of thebuilding the vast potential market demand, whether it is the product itself, or the level of industrial development is clearly not satisfied., And because of the double impact of external factors, with small market differentiation is an inexorable trend.Relying solely on price competition means does not make the small favorably with industry development. In fact, it is due to excessive price competition, leading to small enterprises with low profitability, sales, and the prosperity of the entire industry can not hide the crisis of survival. Anticipate with a few small companies have started the "innovation" in the product upgrades at the same time, learn from the equipment industry and other related industries experience, to establish their own marketing team and distribution network and market competition tends to differentiation.In the high-end users with the needs of small change, directly contributing to small enterprises with the differentiation, with the concept of progress and consumer financial strength of the expansion, some of the rural users (particularly in the industrialized operation of agriculture users) product performance and after-sales service and put forward higher requirements. Liaoning Anshan Haihong such as production of high-end products not only with small to have their own patented technology (use of mechanical devices greatly enhance the performance of its products, avoid using electric control, hydraulic devices, such as product performance after upgrading to the use of rural users increased maintenance costs ), and introduced the "non-controversial" services.Especially in big enterprises with increased involvement of small enterprises with pressure, the end of 2006, the Dragon Holdings acquired Henan Baiyun electrical and mechanical equipment involved in the production of small fields.Small with a huge potential market demand, but only to meet user needs, and guide the user needs, small equipment will have lasting vitality. Existing small enterprises with well-known loaders already facing small enterprises involved with the production sectors and small users to buy equipment or equipment, such as small excavators alternative products twin crises, with the production of small enterprises can take the initiative to upgrade their win more more time and greater market space.Any industries are indispensable for the development of market competition and government regulations two factors. With the status quo on small industries, market competition and excessive government regulation missing, the entire industry in a very low level of operation development, and a lack of development of the industry often staying power will gradually shrink, or even disappear.First to be addressed is the issue of trade with small, small equipment products really have their own products "definition", a special product standards. Although at this stage with small user groups mainly concentrated in the rural market, but themarket coverage of the future is certainly both urban and rural areas, this is because small equipment can be widely used for municipal maintenance, landscape construction, building and construction, underground loading and unloading areas.Second, improve industry access threshold is a feasible solution. Small equipment industry can learn from the industry's largest equipment manufacturers licensing system, in terms of production quality suitable restrictions and improve the industry's manufacturing standards.In recent years loader well-known enterprises in recent years have involved with the production of small areas, such as the Dragon, XCMG, and the mountains, but not really most of the production of one ton of small equipment products, the main reason is hindering their high-end products in the market inadequate capacity. However, this also means that for the small enterprises with not too much time, if not in the relatively short period of time upgrading of enterprises and products, from business philosophy, product marketing idea to the concept of all-round self-improvement,self-transformed into a long-term development objectives and marketcompetition-conscious modern manufacturing enterprises, and a larger-scale sales, in the future and well-known enterprises loader win in the competition may be very small.Mechanical Engineering Society of China was founded in 1936, China was set up earlier, the largest one of the Institute of Engineering. The existing 33 professional chapters, 180,000 members, of whom there are more than 3,000 senior members, more than 500 members of Hong Kong, Macao and overseas, there are more than 4,000 corporate members.Academic exchange is the Institute's basic functions, the Institute is held annually hundreds, and colorful academic conferences. Special is an annual Chinese Mechanical Engineering Society annual meeting, the topic is the integration activities of the various large-scale comprehensive meeting. , The main thrust of the report will include the General Assembly, the topic of academic, scientific and technological progress releases, forums, lectures, display, a number of activities such as presentation, rich in content, as well as inside and outside the country in the industry has had a tremendous impact.Editing, publishing and academic meetings and academic exchanges wings. Over the years, the organization has prepared a "China Materials Engineering ceremony," and "machine repair manual," such as hundreds of large-scale tool, science and technology books and related materials. Academic journals published by the "Journal of mechanical engineering", "Chinese Mechanical Engineering", more than 60 species, and for promoting the development of academic disciplines has played an important role.Member Society is the mainstay of the Institute and the basis for the existence of the necessary conditions for achieving democracy Office will learn organizational guarantee. Member services is the Institute for the work of the main tasks of Institute staff is a sacred duty. Has been the establishment of a wide range of multi-levelstructure and membership of the service system, and conducting appropriate Member activities, and actively explore characteristics of the times with the Member services. Institute of years of development experience has shown that membership is a source of vitality Institute.Continuing education and professional certification is the Institute's an effective way to serve the community. Over the years, have carried out fruitful work. 1983 founded the mechanical engineer degree (now Beijing mechanical engineer OLI), is the first in China to establish a "mechatronics" and the "Industrial Engineering" two professional, and entrusted Quanguokaowei for higher education self-study examination. To welding and nondestructive testing for the representatives of accredited professionals work focused on quality, service-oriented economy, and widely alleged members and the industry peer Road. In recent years, actively promote the international mutual recognition of qualifications engineers.Chinese Mechanical Engineering Society of China's machinery industry is a very important external communication channels, to the industry and the large number of government departments entrusted task of the international exchange and cooperation. Chinese Mechanical Engineering Society of China's accession to the representatives of 11 international organizations, 23 countries and 38 first-class academic institutions and professional organizations has signed bilateral cooperation agreements with more than 60 countries and regions, including more than 1,000 scientific research, teaching, design, manufacturing, consulting, intermediary and social welfare institutions established a good working relationship.I will stick to science and technology and economic integration as the key link, and always bring the Institute for Scientific and Technological Advice as to promote economic development and work closely with the main battlefield, active structures for economic development platform. I will rely on his close "in Beijing Teng-day certification Advisory Center," galaxy of talent and give full play to the advantages of network, enterprises actively carry out technical advice, enterprise certification advisory and development strategy consulting. Not only to learn activities closer to the corporate and service industries, and effectively speed up the Institute's own capabilities and the enhancement of overall strength.International Exhibition is I will carry out international exchanges and cooperation forms an important one. The exhibition platform, organizations Chinese and foreign entrepreneurs, technology sector between the exchanges and cooperation and promote economic and trade development and industrialization of technological progress. As Chinese Mechanical Engineering Society masterpiece in the field of exhibitions, Beijing Essen Welding and Cutting Fair has become first in Asia and second in the world in the welding professional exhibitions.I will set up a "Chinese Mechanical Engineering Society Science and Technology Award", and China Machinery Industry Federation and jointly set up the "China Machinery Industry, Science and Technology Award." Over the years, the China Association for Science and Technology, Chinese Academy of Sciences, Chinese Academy of Engineering, recommending talents, and actively promote respect for independent innovation, and abide by scientific ethics, and the pursuit of harmony andprogress of scientific thought, effectively mobilize the broad masses of scientific and technological workers initiative and creativity.I will also attach great importance to their work, procedures, scientific management and democratic management, and in 2004 took the lead in the national Institute adopted the ISO9001: 2000 quality management system certification. It is not only that I will work more scientific and standardized At the same time, the community has also been the recognition and praise.翻译:本文要紧论述了ZL-50轮式装载机整机虚拟样机设计和几种典型作业工况的模拟和仿真,包括工作装置和整机所需要部件的建模。
挖掘装载机论文中英文对照资料外文翻译文献
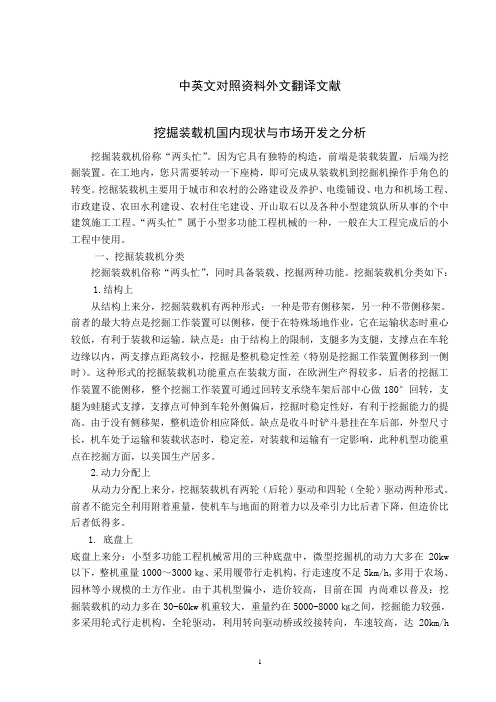
中英文对照资料外文翻译文献挖掘装载机国内现状与市场开发之分析挖掘装载机俗称“两头忙”。
因为它具有独特的构造,前端是装载装置,后端为挖掘装置。
在工地内,您只需要转动一下座椅,即可完成从装载机到挖掘机操作手角色的转变。
挖掘装载机主要用于城市和农村的公路建设及养护、电缆铺设、电力和机场工程、市政建设、农田水利建设、农村住宅建设、开山取石以及各种小型建筑队所从事的个中建筑施工工程。
“两头忙”属于小型多功能工程机械的一种,一般在大工程完成后的小工程中使用。
一、挖掘装载机分类挖掘装载机俗称“两头忙”,同时具备装载、挖掘两种功能。
挖掘装载机分类如下:1.结构上从结构上来分,挖掘装载机有两种形式:一种是带有侧移架,另一种不带侧移架。
前者的最大特点是挖掘工作装置可以侧移,便于在特殊场地作业,它在运输状态时重心较低,有利于装载和运输。
缺点是:由于结构上的限制,支腿多为支腿,支撑点在车轮边缘以内,两支撑点距离较小,挖掘是整机稳定性差(特别是挖掘工作装置侧移到一侧时)。
这种形式的挖掘装载机功能重点在装载方面,在欧洲生产得较多,后者的挖掘工作装置不能侧移,整个挖掘工作装置可通过回转支承绕车架后部中心做180°回转,支腿为蛙腿式支撑,支撑点可伸到车轮外侧偏后,挖掘时稳定性好,有利于挖掘能力的提高。
由于没有侧移架,整机造价相应降低。
缺点是收斗时铲斗悬挂在车后部,外型尺寸长,机车处于运输和装载状态时,稳定差,对装载和运输有一定影响,此种机型功能重点在挖掘方面,以美国生产居多。
2.动力分配上从动力分配上来分,挖掘装载机有两轮(后轮)驱动和四轮(全轮)驱动两种形式。
前者不能完全利用附着重量,使机车与地面的附着力以及牵引力比后者下降,但造价比后者低得多。
1.底盘上底盘上来分:小型多功能工程机械常用的三种底盘中,微型挖掘机的动力大多在20kw 以下,整机重量1000~3000㎏、采用履带行走机构,行走速度不足5km/h,多用于农场、园林等小规模的土方作业。
机械类外文文献及翻译
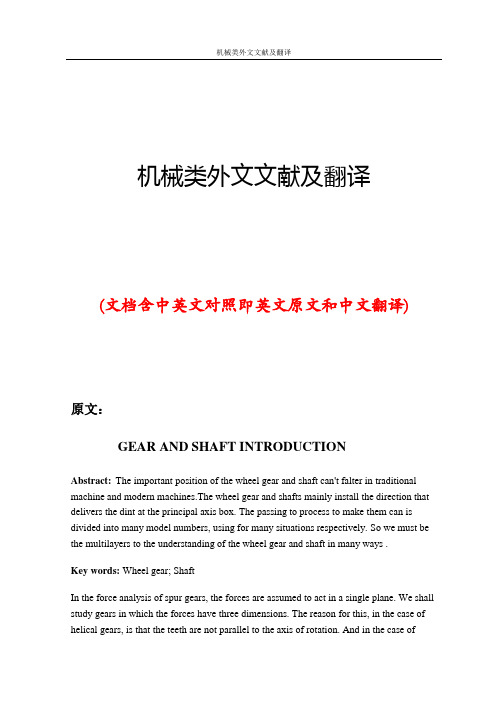
机械类外文文献及翻译(文档含中英文对照即英文原文和中文翻译)原文:GEAR AND SHAFT INTRODUCTIONAbstract:The important position of the wheel gear and shaft can't falter in traditional machine and modern machines.The wheel gear and shafts mainly install the direction that delivers the dint at the principal axis box. The passing to process to make them can is divided into many model numbers, using for many situations respectively. So we must be the multilayers to the understanding of the wheel gear and shaft in many ways .Key words: Wheel gear; ShaftIn the force analysis of spur gears, the forces are assumed to act in a single plane. We shall study gears in which the forces have three dimensions. The reason for this, in the case of helical gears, is that the teeth are not parallel to the axis of rotation. And in the case ofbevel gears, the rotational axes are not parallel to each other. There are also other reasons, as we shall learn.Helical gears are used to transmit motion between parallel shafts. The helix angle is the same on each gear, but one gear must have a right-hand helix and the other a left-hand helix. The shape of the tooth is an involute helicoid. If a piece of paper cut in the shape of a parallelogram is wrapped around a cylinder, the angular edge of the paper becomes a helix. If we unwind this paper, each point on the angular edge generates an involute curve. The surface obtained when every point on the edge generates an involute is called an involute helicoid.The initial contact of spur-gear teeth is a line extending all the way across the face of the tooth. The initial contact of helical gear teeth is a point, which changes into a line as the teeth come into more engagement. In spur gears the line of contact is parallel to the axis of the rotation; in helical gears, the line is diagonal across the face of the tooth. It is this gradual of the teeth and the smooth transfer of load from one tooth to another, which give helical gears the ability to transmit heavy loads at high speeds. Helical gears subject the shaft bearings to both radial and thrust loads. When the thrust loads become high or are objectionable for other reasons, it may be desirable to use double helical gears. A double helical gear (herringbone) is equivalent to two helical gears of opposite hand, mounted side by side on the same shaft. They develop opposite thrust reactions and thus cancel out the thrust load. When two or more single helical gears are mounted on the same shaft, the hand of the gears should be selected so as to produce the minimum thrust load.Crossed-helical, or spiral, gears are those in which the shaft centerlines are neither parallel nor intersecting. The teeth of crossed-helical fears have point contact with each other, which changes to line contact as the gears wear in. For this reason they will carry out very small loads and are mainly for instrumental applications, and are definitely not recommended for use in the transmission of power. There is on difference between a crossed heli : cal gear and a helical gear until they are mounted in mesh with each other. They are manufactured in the same way. A pair of meshed crossed helical gears usually have the same hand; that is ,a right-hand driver goes with a right-hand driven. In the design of crossed-helical gears, the minimum sliding velocity is obtained when the helix angle areequal. However, when the helix angle are not equal, the gear with the larger helix angle should be used as the driver if both gears have the same hand.Worm gears are similar to crossed helical gears. The pinion or worm has a small number of teeth, usually one to four, and since they completely wrap around the pitch cylinder they are called threads. Its mating gear is called a worm gear, which is not a true helical gear. A worm and worm gear are used to provide a high angular-velocity reduction between nonintersecting shafts which are usually at right angle. The worm gear is not a helical gear because its face is made concave to fit the curvature of the worm in order to provide line contact instead of point contact. However, a disadvantage of worm gearing is the high sliding velocities across the teeth, the same as with crossed helical gears.Worm gearing are either single or double enveloping. A single-enveloping gearing is onein which the gear wraps around or partially encloses the worm.. A gearing in which each element partially encloses the other is, of course, a double-enveloping worm gearing. The important difference between the two is that area contact exists between the teeth of double-enveloping gears while only line contact between those of single-enveloping gears. The worm and worm gear of a set have the same hand of helix as for crossed helical gears, but the helix angles are usually quite different. The helix angle on the worm is generally quite large, and that on the gear very small. Because of this, it is usual to specify the lead angle on the worm, which is the complement of the worm helix angle, and the helix angle on the gear; the two angles are equal for a 0-deg. Shaft angle.When gears are to be used to transmit motion between intersecting shaft, some of bevel gear is required. Although bevel gear are usually made for a shaft angle of 0 deg. They may be produced for almost any shaft angle. The teeth may be cast, milled, or generated. Only the generated teeth may be classed as accurate. In a typical bevel gear mounting, one of the gear is often mounted outboard of the bearing. This means that shaft deflection can be more pronounced and have a greater effect on the contact of teeth. Another difficulty, which occurs in predicting the stress in bevel-gear teeth, is the fact the teeth are tapered.Straight bevel gears are easy to design and simple to manufacture and give very good results in service if they are mounted accurately and positively. As in the case of squr gears, however, they become noisy at higher values of the pitch-line velocity. In these cases it is often go : od design practice to go to the spiral bevel gear, which is the bevel counterpart of thehelical gear. As in the case of helical gears, spiral bevel gears give a much smoother tooth action than straight bevel gears, and hence are useful where high speed are encountered.It is frequently desirable, as in the case of automotive differential applications, to have gearing similar to bevel gears but with the shaft offset. Such gears are called hypoid gears because their pitch surfaces are hyperboloids of revolution. The tooth action between such gears is a combination of rolling and sliding along a straight line and has much in common with that of worm gears.A shaft is a rotating or stationary member, usually of circular cross section, having mounted upon it such elementsas gears, pulleys, flywheels, cranks, sprockets, and other power-transmission elements. Shaft may be subjected to bending, tension, compression, or torsional loads, acting singly or in combination with one another. When they are combined, one may expect to find both static and fatigue strength to be important design considerations, since a single shaft may be subjected to static stresses, completely reversed, and repeated stresses, all acting at the same time.The word “shaft” covers numerous v ariations, such as axles and spindles. Anaxle is a shaft, wither stationary or rotating, nor subjected to torsion load. A shirt rotating shaft is often called a spindle.When either the lateral or the torsional deflection of a shaft must be held to close limits, the shaft must be sized on the basis of deflection before analyzing the stresses. The reason for this is that, if the shaft is made stiff enough so that the deflection is not too large, it is probable that the resulting stresses will be safe. But by no means should the designer assume that they are safe; it is almost always necessary to calculate them so that he knows they are within acceptable limits. Whenever possible, the power-transmission elements, such as gears or pullets, should be located close to the supporting bearings, This reduces the bending moment, and hence the deflection and bending stress.Although the von Mises-Hencky-Goodman method is difficult to use in design of shaft, it probably comes closest to predicting actual failure. Thus it is a good way of checking a shaft that has already been designed or of discovering why a particular shaft has failed in service. Furthermore, there are a considerable number of shaft-design problems in which the dimension are pretty well limited by other considerations, such as rigidity, and it is only necessary for the designer to discover something about the fillet sizes, heat-treatment,and surface finish and whether or not shot peening is necessary in order to achieve the required life and reliability.Because of the similarity of their functions, clutches and brakes are treated together. In a simplified dynamic representation of a friction clutch, or brake, two in : ertias I and I traveling at the respective angular velocities W and W, one of which may be zero in the case of brake, are to be brought to the same speed by engaging the clutch or brake. Slippage occurs because the two elements are running at different speeds and energy is dissipated during actuation, resulting in a temperature rise. In analyzing the performance of these devices we shall be interested in the actuating force, the torque transmitted, the energy loss and the temperature rise. The torque transmitted is related to the actuating force, the coefficient of friction, and the geometry of the clutch or brake. This is problem in static, which will have to be studied separately for eath geometric configuration. However, temperature rise is related to energy loss and can be studied without regard to the type of brake or clutch because the geometry of interest is the heat-dissipating surfaces. The various types of clutches and brakes may be classified as fllows:. Rim type with internally expanding shoes. Rim type with externally contracting shoes. Band type. Disk or axial type. Cone type. Miscellaneous typeThe analysis of all type of friction clutches and brakes use the same general procedure. The following step are necessary:. Assume or determine the distribution of pressure on the frictional surfaces.. Find a relation between the maximum pressure and the pressure at any point. Apply the condition of statical equilibrium to find (a) the actuating force, (b) the torque, and (c) the support reactions.Miscellaneous clutches include several types, such as the positive-contact clutches, overload-release clutches, overrunning clutches, magnetic fluid clutches, and others.A positive-contact clutch consists of a shift lever and two jaws. The greatest differences between the various types of positive clutches are concerned with the design of the jaws. To provide a longer period of time for shift action during engagement, the jaws may be ratchet-shaped, or gear-tooth-shaped. Sometimes a great many teeth or jaws are used, and they may be cut either circumferentially, so that they engage by cylindrical mating, or on the faces of the mating elements.Although positive clutches are not used to the extent of the frictional-contact type, they do have important applications where synchronous operation is required.Devices such as linear drives or motor-operated screw drivers must run to definite limit and then come to a stop. An overload-release type of clutch is required for these applications. These clutches are usually spring-loaded so as to release at a predetermined toque. The clicking sound which is heard when the overload point is reached is considered to be a desirable signal.An overrunning clutch or coupling permits the driven member of a machine to “freewheel” or “overrun” bec ause the driver is stopped or because another source of power increase the speed of the driven. This : type of clutch usually uses rollers or balls mounted between an outer sleeve and an inner member having flats machined around the periphery. Driving action is obtained by wedging the rollers between the sleeve and the flats. The clutch is therefore equivalent to a pawl and ratchet with an infinite number of teeth.Magnetic fluid clutch or brake is a relatively new development which has two parallel magnetic plates. Between these plates is a lubricated magnetic powder mixture. An electromagnetic coil is inserted somewhere in the magnetic circuit. By varying the excitation to this coil, the shearing strength of the magnetic fluid mixture may be accurately controlled. Thus any condition from a full slip to a frozen lockup may be obtained.齿轮和轴的介绍摘要:在传统机械和现代机械中齿轮和轴的重要地位是不可动摇的。
关于轮式装载机的英文及翻译
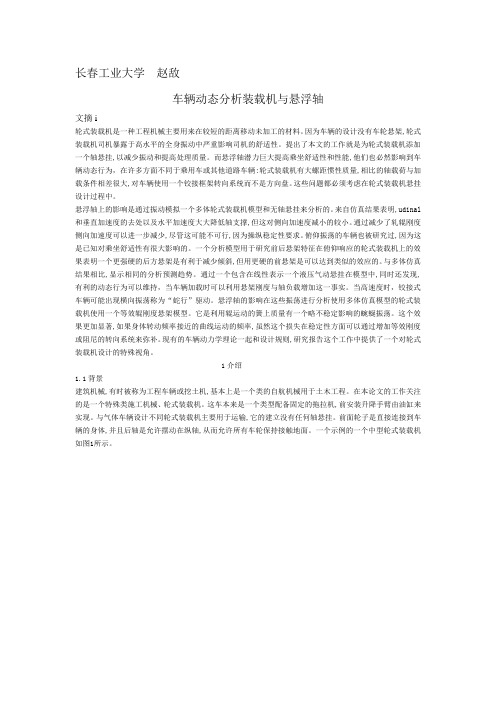
长春工业大学赵敌车辆动态分析装载机与悬浮轴文摘i轮式装载机是一种工程机械主要用来在较短的距离移动未加工的材料。
因为车辆的设计没有车轮悬架,轮式装载机司机暴露于高水平的全身振动中严重影响司机的舒适性。
提出了本文的工作就是为轮式装载机添加一个轴悬挂,以减少振动和提高处理质量。
而悬浮轴潜力巨大提高乘坐舒适性和性能,他们也必然影响到车辆动态行为,在许多方面不同于乘用车或其他道路车辆:轮式装载机有大螺距惯性质量,相比的轴载荷与加载条件相差很大,对车辆使用一个铰接框架转向系统而不是方向盘。
这些问题都必须考虑在轮式装载机悬挂设计过程中。
悬浮轴上的影响是通过振动模拟一个多体轮式装载机模型和无轴悬挂来分析的。
来自仿真结果表明,udinal 和垂直加速度的去处以及水平加速度大大降低轴支撑,但这对侧向加速度减小的较小。
通过减少了轧辊刚度侧向加速度可以进一步减少,尽管这可能不可行,因为操纵稳定性要求。
俯仰振荡的车辆也被研究过,因为这是已知对乘坐舒适性有很大影响的。
一个分析模型用于研究前后悬架特征在俯仰响应的轮式装载机上的效果表明一个更强硬的后方悬架是有利于减少倾斜,但用更硬的前悬架是可以达到类似的效应的。
与多体仿真结果相比,显示相同的分析预测趋势。
通过一个包含在线性表示一个液压气动悬挂在模型中,同时还发现,有利的动态行为可以维持,当车辆加载时可以利用悬架刚度与轴负载增加这一事实。
当高速度时,铰接式车辆可能出现横向振荡称为“蛇行”驱动。
悬浮轴的影响在这些振荡进行分析使用多体仿真模型的轮式装载机使用一个等效辊刚度悬架模型。
它是利用辊运动的簧上质量有一个略不稳定影响的蜿蜒振荡。
这个效果更加显著,如果身体转动频率接近的曲线运动的频率,虽然这个损失在稳定性方面可以通过增加等效刚度或阻尼的转向系统来弥补。
现有的车辆动力学理论一起和设计规则,研究报告这个工作中提供了一个对轮式装载机设计的特殊视角。
1介绍1.1背景建筑机械,有时被称为工程车辆或挖土机,基本上是一个类的自航机械用于土木工程。
(完整版)机械类外文文献翻译
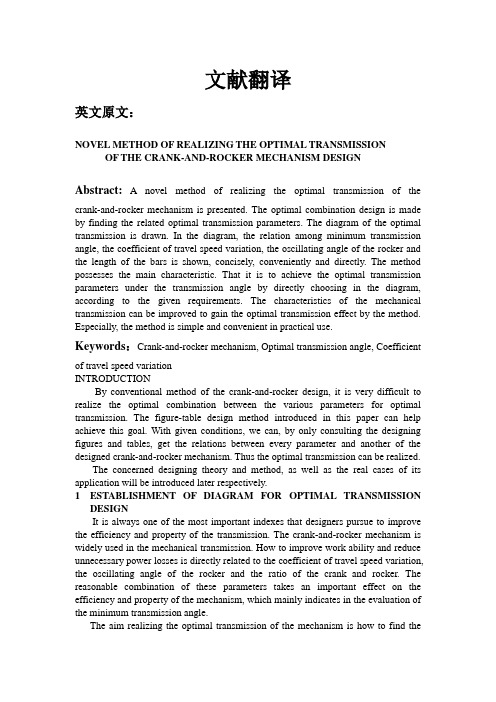
文献翻译英文原文:NOVEL METHOD OF REALIZING THE OPTIMAL TRANSMISSION OF THE CRANK-AND-ROCKER MECHANISM DESIGN Abstract: A novel method of realizing the optimal transmission of the crank-and-rocker mechanism is presented. The optimal combination design is made by finding the related optimal transmission parameters. The diagram of the optimal transmission is drawn. In the diagram, the relation among minimum transmission angle, the coefficient of travel speed variation, the oscillating angle of the rocker and the length of the bars is shown, concisely, conveniently and directly. The method possesses the main characteristic. That it is to achieve the optimal transmission parameters under the transmission angle by directly choosing in the diagram, according to the given requirements. The characteristics of the mechanical transmission can be improved to gain the optimal transmission effect by the method. Especially, the method is simple and convenient in practical use.Keywords:Crank-and-rocker mechanism, Optimal transmission angle, Coefficient of travel speed variationINTRODUCTIONBy conventional method of the crank-and-rocker design, it is very difficult to realize the optimal combination between the various parameters for optimal transmission. The figure-table design method introduced in this paper can help achieve this goal. With given conditions, we can, by only consulting the designing figures and tables, get the relations between every parameter and another of the designed crank-and-rocker mechanism. Thus the optimal transmission can be realized.The concerned designing theory and method, as well as the real cases of its application will be introduced later respectively.1ESTABLISHMENT OF DIAGRAM FOR OPTIMAL TRANSMISSION DESIGNIt is always one of the most important indexes that designers pursue to improve the efficiency and property of the transmission. The crank-and-rocker mechanism is widely used in the mechanical transmission. How to improve work ability and reduce unnecessary power losses is directly related to the coefficient of travel speed variation, the oscillating angle of the rocker and the ratio of the crank and rocker. The reasonable combination of these parameters takes an important effect on the efficiency and property of the mechanism, which mainly indicates in the evaluation of the minimum transmission angle.The aim realizing the optimal transmission of the mechanism is how to find themaximum of the minimum transmission angle. The design parameters are reasonably combined by the method of lessening constraints gradually and optimizing separately. Consequently, the complete constraint field realizing the optimal transmission is established.The following steps are taken in the usual design method. Firstly, the initial values of the length of rocker 3l and the oscillating angle of rocker ϕ are given. Then the value of the coefficient of travel speed variation K is chosen in the permitted range. Meanwhile, the coordinate of the fixed hinge of crank A possibly realized is calculated corresponding to value K .1.1 Length of bars of crank and rocker mechanismAs shown in Fig.1, left arc G C 2 is the permitted field of point A . Thecoordinates of point A are chosen by small step from point 2C to point G .The coordinates of point A are 02h y y c A -= (1)22A A y R x -= (2)where 0h , the step, is increased by small increment within range(0,H ). If the smaller the chosen step is, the higher the computational precision will be. R is the radius of the design circle. d is the distance from 2C to G .2cos )2cos(22cos 33ϕθϕϕ⎥⎦⎤⎢⎣⎡--+=l R l d (3) Calculating the length of arc 1AC and 2AC , the length of the bars of themechanism corresponding to point A is obtained [1,2].1.2 Minimum transmission angle min γMinimum transmission angle min γ(see Fig.2) is determined by the equations [3]322142322min 2)(cos l l l l l l --+=γ (4) 322142322max 2)(cos l l l l l l +-+=γ (5) max min180γγ-︒=' (6) where 1l ——Length of crank(mm)2l ——Length of connecting bar(mm)3l ——Length of rocker(mm)4l ——Length of machine frame(mm)Firstly, we choose minimum comparing min γ with minγ'. And then we record all values of min γ greater than or equal to ︒40 and choose the maximum of them.Secondly, we find the maximum of min γ corresponding to any oscillating angle ϕ which is chosen by small step in the permitted range (maximum of min γ is different oscillating angle ϕ and the coefficient of travel speed variation K ).Finally, we change the length of rockerl by small step similarly. Thus we3γcorresponding to the different length of bars, may obtain the maximum ofmindifferent oscillating angle ϕand the coefficient of travel speed variation K.Fig.3 is accomplished from Table for the purpose of diagram design.It is worth pointing out that whatever the length of rocker 3l is evaluated, the location that the maximum of min γ arises is only related to the ratio of the length of rocker and the length of machine frame 3l /4l , while independent of 3l .2 DESIGN METHOD2.1 Realizing the optimal transmission design given the coefficient of travelspeed variation and the maximum oscillating angle of the rockerThe design procedure is as follows.(1) According to given K and ϕ, taken account to the formula the extreme included angle θ is found. The corresponding ratio of the length of bars 3l /4l is obtained consulting Fig.3.︒⨯+-=18011K K θ (7) (2) Choose the length of rocker 3l according to the work requirement, the length of the machine frame is obtained from the ratio 3l /4l .(3) Choose the centre of fixed hinge D as the vertex arbitrarily, and plot an isosceles triangle, the side of which is equal to the length of rocker 3l (see Fig.4), andϕ=∠21DC C . Then plot 212C C M C ⊥, draw N C 1, and make angleθ-︒=∠9012N C C . Thus the point of intersection of M C 2 and N C 1 is gained. Finally, draw the circumcircle of triangle 21C PC ∆.(4) Plot an arc with point D as the centre of the circle, 4l as the radius. The arc intersections arc G C 2 at point A . Point A is just the centre of the fixed hinge of the crank.Therefore, from the length of the crank2/)(211AC AC l -= (8)and the length of the connecting bar112l AC l -= (9)we will obtain the crank and rocker mechanism consisted of 1l , 2l , 3l , and 4l .Thus the optimal transmission property is realized under given conditions.2.2 Realizing the optimal transmission design given the length of the rocker (or the length of the machine frame) and the coefficient of travel speed variationWe take the following steps.(1) The appropriate ratio of the bars 3l /4l can be chosen according to given K . Furthermore, we find the length of machine frame 4l (the length of rocker 3l ).(2) The corresponding oscillating angle of the rocker can be obtained consulting Fig.3. And we calculate the extreme included angle θ.Then repeat (3) and (4) in section 2.13 DESIGN EXAMPLEThe known conditions are that the coefficient of travel speed variation1818.1=K and maximum oscillating angle ︒=40ϕ. The crankandrockermechanism realizing the optimal transmission is designed by the diagram solution method presented above.First, with Eq.(7), we can calculate the extreme included angle ︒=15θ. Then, we find 93.0/43=l l consulting Fig.3 according to the values of θ and ϕ.If evaluate 503=l mm, then we will obtain 76.5393.0/504==l mm. Next, draw sketch(omitted).As result, the length of bars is 161=l mm,462=l mm,503=l mm,76.534=l mm.The minimum transmission angle is︒=--+=3698.462)(arccos 322142322min l l l l l l γ The results obtained by computer are 2227.161=l mm, 5093.442=l mm, 0000.503=l mm, 8986.534=l mm.Provided that the figure design is carried under the condition of the Auto CAD circumstances, very precise design results can be achieved.4 CONCLUSIONSA novel approach of diagram solution can realize the optimal transmission of the crank-and-rocker mechanism. The method is simple and convenient in the practical use. In conventional design of mechanism, taking 0.1 mm as the value of effective the precision of the component sizes will be enough.译文:认识曲柄摇臂机构设计的最优传动方法摘要:一种曲柄摇臂机构设计的最优传动的方法被提出。
挖掘机中英文对照外文翻译文献

(文档含英文原文和中文翻译)中英文翻译外文文献A Summary of Small-size Excavators Home and Abroad I. The brief introduction of hydraulic excavatorParts such as the hydraulic excavator is by engine, hydraulic system and works device and walks device and electric control etc are formed. The hydraulic system is formed by hydraulic pump, control valve, hydraulic cylinder, hydraulic pressure motor, pipe route and fuel tank etc. The electric control system includes supervision dish, motor control system, pump brain and various kinds of sensor and solenoid valves etc. The hydraulic excavator is general by the work device and turns round the device and walks device three is mostly formed. According to his construction and use, we can differentiate : many kinds of typespressure, turns round entirely, not turns round entirely, utility version, mould for a special purpose, the joining with a hinge type and arm type stretched out and drawn back etc.The work device is directly accomplishing the device that excavates the assignment. It has been joined with a hinge by moves the arm, fights the pole and shovels the fill etc three parts. Moving that the arm rises and falls and the pole fought stretches out and draws back and shoveling fighting moves all with moving back and forth type two effect hydraulic cylinders control. In order to suit the needs of various difference construction school assignments, the hydraulic pressure excavator can be joined in marriage loading many kinds of work devices, if excavating and many kinds of school assignment machines and tools such as lifting job, loading, leveling, clamp and pushes soil and shock hammer etc.Turning round and walks the device is the organism of hydraulic pressure excavator, upper setting up power-on device and transmission system of turntable. The engine is the power supply of hydraulic pressure excavator, and adopts diesel oil will also can modify the electromotor in the convenient place mostly.The hydraulic drive system by way of the hydraulic pump with the engine the motive force transmission to hydraulic pressure motor and hydraulic cylinder etc actuator, the promotion work device moves, thus accomplishes the various school assignments. Take more PV-200's mould hydraulic pressure excavators of use in building site as the example. This machine adopts the type the opening center load of advanced version to be passed feeling system (OLSS). This system is with oblique of control type oblique the method of angle (export volume of flow ) variable plunger pump, and reduced the power delivery of engine, thus reduces the oil consumption burnt, and is one kind of saving energy mould system. The characteristic of this kind of hydraulic system is: the fixed torque is controlled, and it is unchangeable to keep the hydraulic pump drive torque, and year absolutely control can reduce the off-loading loss of school assignment time; Oil capacity is controlled, and the export volume of flow of hydraulic pump in the time of can reducing neutral gear and fine control reduces the power loss.The history of the first hand excavator was published up to now to have more than 130 years, and went through from the steam drive fill to turn round that the machinery turns round the developing the course step by step of the complete automatic hydraulic pressure excavator of excavator and application mechanical and electrical liquid integration technology to power drive and the internal-combustion engine drive in the time. Thehydraulic pressure to anti- the type hanging which shoveled machinery in the 1940’s, and developing out the pulling type at the initial stage of in the 1950’s with middle period in succession, to turn round the full hydraulic pressure of hydraulic pressure excavator and caterpillar tread type entirely mechanical. Initial stage the trial hydraulic pressure excavator is the hydraulic technique that adopts plane and machine tool, lacking the hydraulic pressure component that is suitable in the mechanical various operating modes, it is stable inadequately to make the quality, and necessary is not completely yet. From in the 1960’s, the hydraulic pressure excavator is entered the popularization and in vigorous development stage, and mechanical manufacturing plant and the breed of each country increases very fast, and the output is rapidly increased. 83% of the mechanical gross output was occupied to hydraulic pressure excavator output, and is close to 100% at present 1968-1970 certain period.ⅡSmall excavator development and its tendency20th century 80 ~ 90's small mechanical device in construction and soon in municipal engineering, transportation, pipeline has displayed abigger superiority and can rapidly develop. The small excavator forsaved the manpower, the physical resource in these projects makes thesmall excavator mainly to use in the city the constructionconstruction and generally left a bigger contribution,gradually became in the city construct ionto have the representative construction machinery.The small excavator development mainly relies on the urbanconstruction development, because city transformation, constructionconstruction more, the request construction time short, theconstruction machinery affects small, safe, the low pollution, theradius of gyration to the environment is small, is advantageous fortransports as well as has with the city scenery appearancecoordination outward appearance, the small excavator has satisfied thecity each kind of work request, can maximum limit display itsproductivity in the city narrow working space, therefore has theunique superiority.1. The development of small excavatorsThe small excavator mainly uses in the city the constructionconstruction and the general housing repairs and maintains and so onthe work, the request has the good operating performance and therotation performance.Initial small excavator by tire type primarily, because the tire typewalks the natural in the soft ground and the passing difference,afterwards gradually by the marching substitution, and in moved thearm strut organization place toorganism tocarry on swings, completed the trench sidewall excavation renovationwork behind, but this kind of small excavator excavation scope wassmall, cannot realize the material. Hereafter, the small excavator increased upside has rotated theorganization, has solved behind themetial and so on the problem, enhancedthe excavator operating performance, formed the small excavator thebasic structure. Afterwards, the small excavator in the radius ofgyration, behind the field of vision, moved aspect and so on armelevation angle, machine capability has the further improvement,develops for the present standard type.2.Technical progressesSmall excavator working conditions majority of in city, in order toprevent walks when damages the road surface, starts from the 80's touse the rubber caterpillar band, and gradually obtains thepopularization. A rubber caterpillar band heavy wheel is when theinternal iron circuit board the movement, the hard circuit board jointplace and the heavy wheel contact falls to the ground, becomes walksthe destruction road surface main reason. Before uses the width shapeiron circuit board, a rubber caterpillar band heavy wheel diameter isbigger, therefore when approaches the ground, this slit changes in abig way, creates the caterpillar band to the road surface destruction.The super small excavator use and the before same heavy wheel, onlywas the hard circuit board which in the caterpillar band used changesnarrowly, therefore when contacted the ground the slit changesslightly, reduced to the damage of ground.Rear area the small rotation excavator rotation rear part size isextremely small, in order to guarantee the excavator work thestability, must have the enough counterweight, and in does notincrease the mechanical weight under the premise, uses increases thecaterpillar band length and widens the chassis and so on the effectivemethod.But, the chassis width is transported the truck width the limit, forsolves this problem, has used ViCTAS in the super small excavator (Vio- Crawler Technology by Advanced Stability) the technology.fortablenessThe small excavator majority of seals cab, has not rained when thechair frequently drips wet by the rain seeps. In order to solve thisproblem, the use surface and the interior gather a peaceful fat rubberbody to manufacture has not sewn the seam the chair, cannot againfrom sew the seam place destruction, the durability also can enhance,becomes the complete waterproofing chair.Impels the small excavator market fast development the factor:mobile is flexible, extremely is suitable for work andso on cities each kind of pipelining, foundation construction, publicutilities as well as house service. The small excavator compactvolume, the special design enable its to carry on the work in theenvironment which the large-scale excavator is unable to construct.(2) The small excavator has the multi-purpose small excavator truemerit is it has multi-purpose. The small excavator can install manyauxiliary works machines and tools, like the installment brokenhammer, the hydraulic pressure pliers use in the lightweightdemolision work, installs a clamp to use in to eliminate the work,installs the drum, the plate uses in the trench to fill in buriesthe compaction, the installment turns on lathe digs drills uses in thedrill hole, the lift hook uses in to hoist up heavy item and so on.(3)The small excavator is advantageous for the transportation and oneof shift work location small hydraulic pressure excavator market rapidexpansion reasons should belong to its size and the weight. The smallexcavation function conveniently shifts in each job location, thesmall excavator does not need the large-scale trailer perhaps theheavy-duty truck carries on the transportation, the small transportmeans may deliver. Like this not only can facilitate thetransportation, but also may greatly reduce the machine the cartageexpense.(4) Small excavator bright work characteristic: The rear part radiusof turn for the zero design, causes the small excavator not to need inthe work space limited environment mean industry time excavatoroperator to consider the job location is, whether thus enable theoperator to have the obstacle to hinder the excavator the rotation tosuffice wholly absorbed to the scoop operation, this has alsoprevented around the job location the building as well as theexcavator own damage.(5) Invests the repayment rate to be high, the cost recycles quicklyThe small excavator price is cheap, the cost recycles quickly.Slightly digs take the 6t level as the example, American, the Europeandate brand machine price about 400,000 Yuan, South Korea's machineprice about 320,000 Yuan, the domestically produced machine price is30 ~ 320,000 Yuan some brands is lower; But the 20t level center digsthe price in 70 ~ 1 million Yuan. The higher investment repayment ratecauses the small excavator deeply the general center small earthworkconstruction to contract owner's welcome.4 Small excavators technological development tendenciesThe small excavator technological development complied with the globaldiversification job location the demand, has experienced more than 30years history successional variationtechnicalperformance, job function, work efficiency, security, environmentalprotection, energy conservation and maintenance maintenance had thelarge scale enhancement, has formed the quite consistent technicalstandard and the work standard. Mainly manifests in following severalaspects:(1) The tailless rotation and moves the arm deflection technology totake slightly digs the basic concept to move the arm deflection andthe tailless rotation function later period promotes in the 1990s facethe world market. Moves the arm deflection in the organism front part,but does not have the organization to be able to realize is locatednearby the lower part of wall the direct excavation work to havefrequently to move the fuselage. The tailless rotation structureapplication, causes it when the neck of land work does not need toworry the rear part the collision. The tailless rotation structuraldesign difficulty lies in rotates in the platform the generalarrangement, the dynamic system thermal equilibrium solution as wellas the entire machine stable solution. But moves the arm deflectionorganization the design difficulty to lie in an articulation positionthe determination and the hinge body manufacture technology.(2) New hydraulic control technologyThe new hydraulic control technology should have the work efficiencyhigh, the serviceability is good, has the good efficiency, may carryon the high efficiency, the powerful work. The new fluid environmentcompatibility presses the system not to shoulder the size theinfluence, completely needs the oil of the hydraulic pressure system, the current capacity accordingto the control handle scope distribution point, definitely may deferto operator's intention with ease to complete the work. At the sametime, because the engine load is small may avoid the current capacitythe senseless loss, can realize slightly moves the operation and thecompound operation. The new hydraulic control technology applicationalso can increase the dynamic output, enhances the work speed, reducesthe fuel consumption.(3)Security performanceHas the strict legal rule in the European market and the North Americamarket to the security, the equipment security performance can givethe operator to provide the relieved work the environment, enhancesoperator's security. The small excavator security performance mainlymanifests in the cab ROPS/FOPS design below, should satisfy theperformance requirement in the cab experiment:①May satisfy must energy absorption;② May satisfy must anti- load;(4) Environmental protection technologyMainly manifests in the power, the low oil consumption, cleanlydischarges the engine in the application. The new engine shouldsatisfy the American EPATier2 standard and the European EU standard,will cause the environmental pollution the compound to discharge thecontrol in the threshold. The new engine simultaneously reduced thevibration and the noise, is beneficial to the environmental protectionand operator's health.(5) Man-machine project technologyThe cab conforms to the man-machine engineering principle,internal spacious, field of vision open, modelling artistic, the easeof operation, reduces effort the measuring appliance demonstrationdirect-viewing, is accurate, can provide one kind of comfortableoperating environment to the pilot, fully reduces pilot's weariness.(6) Services the maintenance technologyMaintains from the current maintenance to the regular inspectionservice, the simplification operation is extremely essential, canenhance the machine the reliability, makes the machine throughout tomaintain the good condition. Must cause the daily inspection side, the realization not to need withthe aid of the tool as soon as to touch the type operation.Maintenance repair then quickly dnd simplely, but fast carries on theinternal spare part and the system inspection and the service. Moreover, in the design must fully consider prevents the machine theaccident damage.Such as the cowling, the guard plateguards against the collision structural design;Moves the arm hydraulic cylinder guard plate design; Fuel oil tank draw-offvalve; The independence bulldozes the board hydraulic pressure hosedesign; Waterproofing electric system design; In the work installmenthose sets at the design; X frame and halfway up the mountainsidecaterpillar band design; The engine machine oil filter elementreplacement time lengthens; Has forerunner system which the pipelinefilters; Dual spatially filters structure design and so on.5 ConclusionsSociety's development has a more tremendous influence to the smallexcavator, at present the overseas small excavator had the suitable development, like Carter other forces, company and so on Hitachi,small pine, Mitsubishi, the small excavator product has formed theseries, and in unceasingly carries on the development, the expandeduse, the increase appendix type. The domestic small excavatordevelopment has also obtained the certain result,中文译文国内外小型挖掘机发展综述一、液压挖掘机简介液压挖掘机是由发动机、液压系统、工作装置、行走装置和电气控制等部分组成。
装载机中英文对照外文翻译文献

中英文资料外文翻译文献(文档含英文原文和中文翻译)英文原文Reality-driven virtual wheel loader operationAbstract: Virtual prototyping (VP) tools enable us to investigate, explore, and communicate the performance and behavior of an evolving product and thus reduce the number of physical prototypes needed. Finite element (FE) and multibody simulation (MBS) tools are frequently used for virtual prototyping in mechanical engineering today.These tools can effectively support the process of problem identification, concept verification, and detailed optimization.The industrial use of VP tools can be enhanced by developing methods that support situated modeling,efficient simulation, and visualization based on virtual reality (VR) technology. In this paper we have concentrated on the development of methods for inverse modeling and VR animation.The method presented is illustrated by a simulation and visualization of internal dynamic forces in a wheel loader when excavating granulated material such as gravel or seed.Key words: Virtual prototyping, inverse modeling, FE,MBS, visualization1- IntroductionVirtual reality (VR) tools offer new possibilities for product development, including simulation, skills training,and communication with distributed colleagues [1]. Virtual prototyping (VP) uses VR technology to investigate and explore a product before it is manufactured. The aim of VP is to reduce the number of physical prototypes needed and thus save both time and money. Finite element (FE) and multibody simulation (MBS) tools are commonly used for virtual prototyping in mechanical engineering today. These tools can provide effective support for the process of verifying formulated requirements. For example, they can be used to evaluate and select alternative solutions or as a final check or optimization of a solution concept. The use of VP tools is even more effective if they are supported by an information framework for handling the information created during the verification process. Effective use of VP tools requires integration of methods and models. Integration can be achieved by using various types of frameworks, such as product lifecycle management (PLM) systems or extended PLM systems, in which some models can share data or beassociated with each other, as in CAD-FE models. An approach to such a research framework is described in the MOSAIC project (e.g. [2]) and [3]) which has been further developed in the VISP project (e.g., [4], [5] and [6]). One interesting research area that these frameworks also address is how to capture not only the data but also the knowledge that is generated during a development project so that it can be re-used in another project or used to explain changes in an existing product. This research area also deals with traceability (i.e., how to find information created earlier); design rationale (i.e., the reason for a certain design shape or design decision); and decision support (i.e., the use of one or more methods to draw a conclusion based on the stored structure of information – i.e., formal knowledge – that is presented to the user).2 - ResearchThe research presented in this paper was undertaken in collaboration with V olvo Construction Equipment (V olvoCE), which supplied the industrial problem and environment. V olvo CE also contributed models and realistic data about working conditions. All other research was performed at KTH in the Department of Machine Design.2.1- V olvo Construction Equipment (V olvo CE)V olvo CE is one of the world’s leading producers of construction machines, with a product range that includes wheel loaders, excavators, articulated haulers, and motor graders. The V olvo wheel loaders are designed and manufactured on four continents. The new range of V olvo wheel loaders uses modern technology, such as loadsensing hydraulics, service accessibility, TP-linkage, the Care Cab, automatic power shift, and high-performance and low-emission engines to combine increased performance with improved operator comfort and reduced environmental impact.Figure 1: A wheel loader from Volvo CE [7]Because wheel loaders are heavily loaded during normal operation, accurate prediction of strength and fatigue is a high priority. Moreover, because machines canbe customized for specific operations, the required performance and behavior of each customized loader is unique. Consequently, the behavior of the complete system must be considered when studying the strength and reliability of the components, and the behavior of the components constrains the performance and reliability of the system.2.2 - Research focusAt V olvo CE a highly systematic procedure based on physical and virtual testing is used to predict the strength and fatigue life of individual components. However, it is considered strategically important to improve the ability to study the virtual behavior of a system of components or subsystems, or in other words, the behavior of more complete vehicles. A first step in that direction is to expand and integrate the use of existing MBS and FE tools.One interesting research challenge is to develop a methodology that supports modeling of components and subsystems and enables reuse of models for different analyses. In considering this problem, we will concentrate on the use of FE and MBS models. Another important issue is how to assemble MBS system models that need to have elastic components (which we can import from FE models) in order to enable high-quality simulations of complete vehicle dynamics behavior, as well as operator comfort related to noise and vibration.The development of complex products requires simultaneous consideration of several aspects and draws on a multitude of competencies. It is thus important that any methodology developed should also include suitable ways to present and communicate simulation results. We believe that animation of motion geometry and property graphs as well as scaled force and torque arrows can be an important complement to more traditional means of communication.2.3 - Research realizationThe research reported here focuses on the evaluation and verification of design concepts that takes place continuously and iteratively during the design process. Our approach to this research topic has been to treat it as part of the design process. The evaluation process can be characterized as an exploratory process that is built around questions and answers until all principal uncertainty about a concept has been revealed (i.e., the complexity is managed).The modeling approach that has been chosen is a systems approach, in which parts are treated as subsystems that can be connected at specific connection points. The configuration of the system models to be simulated is then a part of the evaluation process. The work presented here centered on an industrial application, namely a wheel loader from V olvo CE performing a digging operation in a pile of granulated material. This application has been used to guide the research as we have sought to develop a methodology for simulation-assisted decision-making in the design process and enabling areas. Thus we have examined•methods for architecting modular system models and configuring reusable and modular simulation models.•methods for integrating measurements with simulation model experimentation in general and inverse modeling in particular.•methods for presenting and communicating the results of simulations.3 - Decision-makingA general though rough description of a design process is the stage-gate model, in which the process is divided into a number of predefined phases with gates between them. Decisions are taken continuously during the design work, but major decisions are concentrated at the predefined gates between major design activities or phases. The activities between the gates are focused on detailing and resolving uncertainties about the actual concept, that is, on gaining knowledge about the concept. These activities are triggered by the specifications that define the target values for the properties of the proposed product.The activities can all be seen as part of a verification process that iteratively evaluates all critical requirements, either by simulating behavior or by using other sources ofinformation, including colleagues and old designs. In this paper we are focusing on the use of simulation and simulation models as a tool to make this evaluation process more efficient.In figure 2, we have illustrated the concept verification process taking place between two gates in the development process. The main activity in this process is “investigate problem”, w here the problem is whatever is unknown about a requirement and needs to be further investigated.The database symbols indicate that for each step in this process there are a number of predefined models that maybe candidates for use in solving an actual problem.3.1- Model Architecting and ConfigurationAn important part of the verification process is the ability to configure system models, each adapted to perform a specific task, and each consisting of models of componentsand subsystems. To be able to analyze this system, there must also be a feasible level of detail and a feasible simulation tool.To achieve this goal, the product concept being studied must be divided into components and subsystems that can be modeled separately. Models of components and subsystems are both referred to as subsystem models in what follows.We also need to define a way to configure system models from these subsystems models. Our approach is based on identifying and representing the connections between subsystem models (see [8]). In discussing these connections, we refer to the connection point at the subsystem as the mating feature, and the physical connection as the interface feature. Figure 3 shows a system model of a lifting unit comprising subsystem models that are connected by interface features at the specified mating positions. A mating feature may be a discrete point or a set of points representing one (or several) surface(s) on the component. An interface featuremay be a set of constraint equations or a more complex model, as is indicated for one of the joints in figure 3.Figure 3: A lifting unit in a wheel loader composed o submodels conne fcted by interface featuresFigure 4: Models of a wheel loader lifting frame with different levels of detailThis modeling approach has great potential, but to take full advantage of it we need to define more than one variant, and preferably two or three, of most subsystems. These variants may have different levels of detail and may be targeted for different software tools. These variants are the main precondition for setting up a system model that is suited to exploring the question (formulated as a problem) of how behavior will be affected by a property of a product concept. Figure 4 shows some wheel loader lifting frame models and their mating features with different levels of detail.The exploratory nature of the verification process outlined in figure 2 results in corollary problems arising from the problem initially stated. The sequence of problem tasks and questions places demands on the modeling environment to make it easy to configure new or partly new configurations of system models. A typical problem sequence starts with a defined problem, which requires a rather rough model of the overall behavior of the concept, (e.g. a complete vehicle). A corollary problem will then involve either more focused analysis of a portion of the entire system, or a more detailed analysis of the total system. Both these corollary problems require new system models to be configured. For example, if a more focused analysis is called for, attention would focus only on the lifting unit, and some of the subsystem models would probably be replaced with more detailed models. The calculated forces in theinitial system model would be the boundary conditions for this analysis. If it is the total system that needs to be examined, as would be the case if we wanted a more detailed study of the behavior of a subsystem working within the total system or the impact of one component on the behavior of the total system, then some subsystem models would need to be replaced with more detailed models.The modeling approach presented in this paper makes it possible to reuse some of the subsystem models when tackling both these corollary problems.3.2 - Inverse modelingIn many cases, not all the parameters of a system model are known or can be obtained directly from measurements. If measurements are used to infer the values of parameters on which the measurements themselves depend, we have an inverse measurement problem, which from now on will be referred to as an inverse problem. The estimation of these parameters or functions requires both a model and measurements [9]. This technique has been widely applied in the environmental sciences (e.g., [10]). The size of real industrial problems and the disparate scales involved, as well as the nonlinear and often poorly formulated nature of inverse problems, mean that inverse modeling is among the fundamental challenges facing computer-aided engineering. Any solution will require the joint effort of computer scientists and engineers. However, this issue falls outside the scope of the present paper, which focuses on methodological issues.Inverse modeling, or parameter assessment, may be seen as an optimization problem in which the error between measured and simulated data is the objective function S that is to be minimized. If the standard statistical assumptions given in [11] are valid, then an ordinary least Squares objective function is appropriate [9]:where Yi denotes a measured quantity, and i Y a calculated model value at a time, location, or other space indicated by i. It is also possible for i to denote a given measurement in time or space. The collections of all measured andcalculated values are denoted Y and Y , respectively.In modeling dynamic behavior, a dependent variable such as the frequency of the first bending mode of the vehicle can be measured at one or more positions. However, some basic parameter, such as the bending stiffness of the front and rear frame and of the joints that connect the two frames, may not be known. If the frequency and the mass distribution are known, this parameter can be determined with a model that accurately represents the fundamental dynamic properties of the individual components.Simulation models may also suffer from a lack of accurate descriptions of the surrounding external interactions with the model. When testing a prototype, some of the important and critical loads may be very hard or even impossible to measure. Inverse modeling offers one solution to this dilemma by allowing us to combine measurements from experimental tests and simulation models. The measurements are used as driving conditions that control the simulation model, with which the requestedinternal properties can be calculated.A first approach to describing a method for inverse modeling involves the following steps:•Decide whether inverse modeling is necessary or whether traditional experimental testing or a simulation approach will be adequate for the task inhand.•If inverse modeling is necessary, identify the interior object states and changes of state that cannot be measured in experimental tests.•Configure a system model based on subsystem models that are connected at predefined positions (mating features) by connecting elements (interface features).•Identify the boundary conditions that need to be measured in order to drive or control the simulation model.•Develop expressions or models for external interaction forces that cannot be measured.•Perform the analysis and calculate the interior loads. This approach fits very well in the verification loop in figure 2. A closer view of the activity “investigate problem” is given in figure 5.Figure 5: The activity “investigate problem”The proposed method applies to activities two (create behavior system) and three (simulate behavior) in figure 5. After simulating the behavior, it is critical to interpret the results and verify that the simulation gives a correct and sufficiently accurate reflection of the studied properties.Consequently when we are planning experimental studies,we should also consider what properties we should measure in order to be able to verify the results obtained using the simulation.The remaining activity in the verification task in figure 5 is to formulate an answer to the initial problem. As indicated in the figure, this answer can also be based on answers from earlier analyses.3.3 - Presentation of simulation resultsBoth when interpreting results and when formulating answers, it is important to select the most appropriate way to present the simulation results. This is a strategically important issue for successful communication and collaboration inteam-based development of complex products.During simulation, a lot of results are created and saved in special results files. A common way to analyze simulation results has been to plot graphs of selected properties at interesting (critical) positions in the product. This approach has been applied in simulations since the late 1960s when we started to use these types of computer tools. However, developments in hardware and software now provide far more powerful ways to present simulation results. We can now, for example, show an animation of a work cycle of a robot or of the eigenmodes of a component.The ability to animate product behavior and to identify critical states during operation brings a new dimension to presenting results. The animation can include many other components besides motion geometry and property graphs,including scaled force and torque arrows to indicate component and interacting loadsduring a work task.Such animations permit more team-centered discussion ofwhat is actually happening in the conceptual design during the simulated operation and give a common understanding among the team members. They can also shorten the iteration loop and development time because this type of qualitative evaluation demands very little preparation before the team discussion.We suggest that animation should be used to present and obtain an immediate response before the answer is formulated. When it comes to formulating the answer, we also think that animation of internal interactions as well as of global systems behavior play an important role as a complement to more traditional documentation with text and graphs.4 - Case Study: A wheel loader digging sequenceIn order to illustrate the work approach outlined in this paper, we have studied a digging sequence of a wheel loader. The problem is to calculate loads in three bearings of the lifting unit during digging in a pile of granulated material and loading it on a truck.This is the initial problem statement – a formulation that is based on the stated requirements, actual design concept, and previously defined and solved problems that can be examined and compared to existing conditions. In this case, the design concept is not unknown since the task relates to improvement of an existing product.Next we have to decide how to solve the problem and to come up with an answer. At this stage, we need to find out whether we need to use inverse modeling as described earlier. The components of interest are bearings G, D, and F (see figure 6).Figure 6: The location of bearing G, D and FThese component loads cannot be measured during an experimental study. It is also hard to derive them solely from simulation models, which would require an accurate description of external conditions in order to achieve acceptable simulation results. Thus we do need to use inverse modeling.4.1 - Modeling approachWe have chosen to study a model of a complete vehicle and to use the inverse modeling approach combining measured properties and numerical simulation tools. The vehicle has been modeled in the ADAMS modeling environment. The model is based solely on rigid bodies connected by kinematic joints and force elements [12]. The first bending mode of the vehicle is represented by an elastic interface feature connecting the front and rear frames of the vehicle. This elastic interface feature is modeled using force elements. The parameters of the interface feature representationare assessed using the inverse modeling technique described earlier. The systems model comprises a total of 50 rigid bodies. The surrounding environment gives the external interaction conditions, which in this case are•the wheel contact against the ground, and•the contact with the pile of granulated material.The wheel contact is handled by using an available tire model in the chosen modeling environment (ADAMS).The parameter values of the tire model are also obtained with inverse modeling of the measured fundamentalvertical eigenfrequencies of the vehicle. Eriksson and Slättengren [13] have developed a separate subroutine for describing the interaction between the bucket and the pile of granulated material. This routine has been implemented in ADAMS as a general force subroutine (GFOSUB), which calculates all six generalized component forces.In order to drive the simulation model, we need to measure the lift and tilt angle of the lifting unit as well as the steering angle and propelling velocity on the drive shaft. With these measured values, we can control the motion and turning (propelling velocity and steering angle) of the vehicle as well as the digging (lift and tilt angle). In addition we need to measure some properties to use for validation and verification of the simulation model. Here we choose to measure forces in the lift and tilt cylinders and the torque on the drive shaft. Figure 7 shows a wheel loader in the experimental test case and the corresponding ADAMS model.4.2 - Preprocessing of measurementsRecording the measurements with a sampling frequency of 500 Hz generates too much data to be practically handled by a simulation tool. It also includes a frequency spectrum containing higher frequencies (>30 Hz) than we are interested in for this study. Consequently we have to perform some presimulation processing of the measured signals by applying a low-pass filter and resampling the signals to 50 Hz. This processing adapts the signals to fit the ADAMS modeling environment in general and this vehicle model in particular.Furthermore, angular measures of steering lift and tilt need to be translated into corresponding cylinder lengths for the actuators that are generating this movement. This can be done by performing a kinematic analysis of the ADAMS models using the angular measurements to control the angle of the actual rotational joint. During this simulation the length of the actuators is calculated (i.e. Inverse modeled) and saved so that this data can be used as input to the inverse simulation of the vehicle.A first direct response of the simulation is of course given the engineer performing the simulation. A second responsecan easily be obtained from the project team if an animation of reaction forces during the simulation is prepared and used as a base for a qualitative evaluation. Figure 8 shows a snapshot of the animation of the vehicle at a point when the bucket is entering the pile. It clearly shows that the reaction force in bearing D is the largest of those three being studied. It also shows that the size is almost double that of the force in bearing G and three times that in bearing F. An animation will also illustrate how these forces vary during the simulated work cycleFigure 8: A snapshot during animation of reaction forces inG, D, and F bearingsThis qualitative approach to the reaction forces is presented in quantitative terms in figures 9 to 11.The final ta sk in the outlined activity “investigate problem” in figure 5 is to use these findings to formulate an answer to the question about the loads in bearings G, D,and F. The content of this answer is preferably an aggregation of animation(s) of the bearing loads, as shown in figure 8, the force history graphs in figures 9 to 11, anda short discussion of the interpretation of these results.4.4- Validation and verification of simulation modelBefore formulating the answer, we have to verify (is the model right?) and validate (is this the right model?) our simulation model so that we can conclude whether or not our results and conclusions are correct and accurate enough. The required accuracy is context dependent, and sometimes a qualitative result is sufficient. In other cases,a detailed result is sought.During the experimental study we prepared for the verification phase by measuring additional properties to those needed solely to drive the simulation. Of these measurements, we will use output torque on the propelling shaft and cylinder forces in the lift and tilt cylinders to validate the simulation model and verify our simulation results.A comparison of the measured values and the corresponding simulated values is shown in figures 12 to 14.For the lift and tilt cylinders, we can see that we have goodcorrelation for the phase from five to seven seconds andacceptable correlation for the rest of the work cycle for the lift cylinder. For the tilt cylinder, however, we find a significant deviation during the phase from ten to eighteen seconds. After ten seconds, the bucket is tilted against its end stop and the cylinder valve is closed. This is why the cylinder force is almost constant during this period – the slightly decreasing force is probably due to a small leakage in the hydraulic system. Since the hydraulics are not represented in the simulation model, this is a plausible explanation of the relatively low correlation during this phase.5- DiscussionA decision support system is intended to reduce uncertainty about a concept and its behavior. The natural way to do this is to formulate questions about what we do not know. These questions may concern specific properties as well as overall behavior. To handle such questions, we need a model architecture that enables easy configuration of a simulation model that is targeted at the formulated question. To enhance model performance, a system simulation model is preferably a mixed-fidelity model [8]. The correctness of simulation results must always be judged in relation to the purpose for conducting the simulation, that is, the actual question that has beenformulated. With its modular model architecture, the simulation model used in the presented case study can easily be made more detailed by, for example, including a submodel of the hydraulic system, and by exchanging one or several of the rigid bodies with elastic submodels imported from FE software such as ANSYS [14] that has capabilities for dynamic condensation, e.g. the Craig- Bampton approach [15] which is interoperable with ADAMS. Model-based design reasoning and simulation-assisted decision-making require situated modeling [16]. In other words, the model must be easy to reconfigure and optimize for a new purpose (i.e. the model must be adapted to the present situation in the development process). Assume,for example, that a question relating to operator comfort is raised after the digging simulation presented above has been performed, communicated, and discussed. A modular model architecture allows the simplified subsystem model of the cab and its connection to the front frame to be replaced with more detailed model variants of the cab andof the interface features of the vibration isolators. Animations (and otherVR-related techniques) that simulate behavior significantly help the simulation engineer to interpret and understand the simulated behavior and the different phases of that behavior. Consequently, communication and team-based design reasoning and model verification and validation benefit from VR animations.6- ConclusionsThis paper presents a model of decision support that systematically utilizes VP in the decision process. The methods underpinning this model have been developed and together they provide a basis for a methodology for a simulation-assisted decision process. This methodology comprises methods for•architecting modular system models and configuring reusable and modular simulation models•integrating measurements with simulation model experimentation in general and inverse modeling in particular•presenting and communicating simulation resultsA modular model architecture is a main precondition for easy configuration of a simulation model for each question that arisesIntegrating measurements and simulation modeling is very valuable for some simulation tasks where inverse modeling and inverse simulation offer significant advantages. This is often the case when modeling complex systems and behaviors, where some properties cannot easily be measured and others are difficult to define a priori.Animation of a product’s behavior can be a powerful tool for presenting simulation results, for example by using scaled force and torque arrows to indicate component and interacting loads during a work task. Such animations promote a qualitative evaluation of simulation results that is preferable in team-centered discussion and also give a faster indication of the correctness and feasibility of the model.This methodology has been applied in an industrial test case involving the dynamic behavior of a wheel loader from V olvo CE. The results so far are promising but tentative. We plan to further test and develop the methodology in upcoming projects. 7- AcknowledgementsThe authors wish to thank Allan Ericsson at V olvo CE for assisting with the simulations as well as for measurements on the wheel loader.。
- 1、下载文档前请自行甄别文档内容的完整性,平台不提供额外的编辑、内容补充、找答案等附加服务。
- 2、"仅部分预览"的文档,不可在线预览部分如存在完整性等问题,可反馈申请退款(可完整预览的文档不适用该条件!)。
- 3、如文档侵犯您的权益,请联系客服反馈,我们会尽快为您处理(人工客服工作时间:9:00-18:30)。
中英文对照资料外文翻译文献附录一中文翻译轮式装载机的典型20 世纪 20 年代,小型农用拖拉机都配备的轻质材料 re-handling 装载机铲斗。
这难以置信担任现代轮式装载机的最早的原型。
轮式装载机的最早版本是旋转桶和电梯武器装载上农场型拖拉机。
一桶装上拖拉机离合器的绞盘,通过使用金属丝绳,然后甩重力了通过旅行释放机制。
20 世纪 30 年代,多家厂家正在发展小型轮式装载机的紧固水桶到拖拉机上。
科技公司在英国曼彻斯特,桶装的拖拉机的他们缪尔山加载程序的第一次录制制造商之一,28 马力拖拉机装入 0.5 立方码 (0.4 m3) 电缆控制斗。
刚性框架轮式装载机1939 年,来自芝加哥的一位工程师弗兰克 G.霍夫的名称,开发第一个自包含、两轮驱动、橡胶累了、装载机称为 Hough 模型 HS。
这台机器了斗容量的 1/3 立方码(0.25 m3)。
桶重力通过闩锁机制被甩了。
其他制造商开始生产综合四轮驱动轮式装载机。
许多第一次的轮式装载机的有刚架。
虽然这些机器被集成在一起,他们刚架有限导致要转大圆圈损在严密的地方经营的机的操纵性能。
由毛毛虫,开发的第三个轮式装载机,例如了刚架。
其他制造商喜欢欧几里得 / 特雷克斯轮式装载机市场中输入 1957 年较晚,与小刚架轮式装载机单元称为L-7。
古河 FL35I 4 x 4 铰接式装载机也许在轮式装载机的演变中的最重要里程碑之一是铰接架的介绍。
厂商在俄勒冈州波特兰首创这一技术在 1953 年模型 LD-5,在 1944 年,霍夫接着液压与第一个生产装载机驱动斗倾斜。
这给了机器控制倾倒的能力,操作员可以接近低齿轮的一家银行和通过装载期间回倾斜桶铲充分的斗。
1947 年,霍夫将推进轮式装载机发展再一次当公司开发了世界上第一个四轮驱动液压轮式装载机 HM 模型。
模型仍被视为现代轮式装载机的先行者。
制造可以引进与液压马达时它开发模型 H 轮式装载机在 1952 年的第一个轮式装载机和模型 HP 轮式装载机在 1957 年贷记。
这些装载机了单一的集中装入的斗臂。
公司,创办的,是另一家公司向美国市场介绍液压轮式装载机。
这涉及紧固液压轮机制与液压动力向斗人群。
这一发展转型挖坑机几乎从机轮式装载机。
前臂由于轮式装载机增加在上世纪 50 年代的大小,关切的安全的问题,特别是在装载机臂支点的定位。
定位该运算符的背后,加载程序的武器,向上和向下,移动了接近的操作员。
这所带来的问题。
第一,动胳膊提出了只等待发生意外。
第二,移动部件有限的营办商侧的可见性,尤其是在增高的位置。
在上世纪 50 年代末,美国轮式装载机生产厂家的数目正在重新定位臂支点是操作员的前面,而不是后面的国家安全局与协作。
霍夫是第一次来新的、更安全的设计,与他们的模型何轮式装载机生产厂商之一。
其他制造商迅速跟进在通过包括卡特彼勒于 1958 年,案件于 1959 年,阿利斯-查默斯在1961 年和 1962 年密歇根的前已装入数据透视。
大型轮式装载机到 60 年代,轮式装载机生产趋势集中在较大的机器上更大的有效载荷能力。
卡特彼勒推出其六立方院子后 (4.6 m3) 模型 998 1963 年,多项行业调查透露装载机要远远大于标准尺寸的五到六立方码(3.8 至 4.6 m3)的需要。
市场苛刻的从加载工具更坚固耐用的移动性和大型轮式装载机被当作解决方案。
制造商开始把防洪与大型大中型的轮式装载机市场。
国际联合收割机 Hough 司建 H 400,与 10 立方码 (7.6 m3) 斗轮式装载机。
其他厂商的反应包括卡特彼勒 992, 1200 和密歇根州的 475 10 立方码(7.6 m3) 斗生产装载机。
多年来,该行业继续的有效载荷能力的极限。
上世纪 70 年代,轮式装载机的一些展示了在 1975年工程机械博览会与增加有效载荷能力,否则不包括霍夫的 21 立方码(16-m3) 580 业内见过和克拉克密歇根大规模 675 轮式装载机 24 立方码 (18.3 m3) 能力。
[] 151986 年,有效载荷能力中的记录坏了当川崎重工有限公司为煤技术研究协会开发规模最大的轮式装载机,与日本的表面采矿设备 25 立方码(19 m3)的能力。
最终,包括卡特彼勒、小松和莱图尔诺其他制造商会深入研究制作装载机 20 立方码(15.3 m3)的能力。
的遗产1988 小松 WA600 1 L 轮是生产商的破纪录的重型装备建设的声誉。
公司开发,并仍在世界中,L-2350年最大的轮式装载机的制造商。
这个加载器主要用于表面采矿和拥有 2300 马力机和 80 吨、 53 立方码 (40.5 m3) 容量岩桶和漏钢的 266,000 磅力。
高度、驾驶室及充分提高,斗的顶部是惊人 43 英尺 9 英寸 (13.23 m)。
这台机器被为了加载 300-400 吨加挖掘的卡车在四、五刀路。
勒图诺轮式装载机功能柴油电动传动的直流电动马达的每个车轮,由莱图尔诺自己开发的概念。
20 世纪 60 年代,该公司开始生产齿条和驱动器通过传输的提升机和桶倾斜的权力很大电动装载机。
首先,这些巨大的齿条和马达非常商业上的成功由于没有铰接式转向的优势加载器的工业力量减弱。
结果,很少有人真正建成。
这样一个模型的是绰号的怪物和测量 52 英尺(16 米)长的 SL 40 模式。
莱图尔诺轮式装载机的现今线被从 1968 年首次生产电驱动模型的 L 700 系列。
L-700 是一系列的成功到今天大量生产的装载机先行的。
机器已离开齿条和电机,但仍保留电驱动车轮。
虽然和齿条电机轮式装载机凡不大卖,他们确实努力工作,已超过 20 年的生命周期。
新进展今天,电气装载机存在的市场和函数具有相同的容量和多功能性为柴油发动机或汽油引擎轮式装载机。
轮式装载机也有了一系列的摊子、叉、和扩大其任务,包括轻拆除和隧道的不同大小的桶等附件。
[21] 一些轮式装载机来配备骑控件,它允许更大的工作速度,在崎岖不平的表面上的。
政府现正进行新的突破,在采用混合动力技术,减少燃料传输。
2008 年 3 月沃尔沃亮相工程机械博览会生产前其 L220F 混合轮式装载机的原型。
加载程序将提供燃料消耗减少 10%。
技术沃尔沃集团内已经产生,并保持机密,并受专利。
定于 2009 年底生产,L220F 将是该行业的第一个商用混合轮式装载机。
沃尔沃还提出了名为的装载机的设计理念。
这是关于未来愿景的轮式装载机可外观到 2020 年。
有一个柴油混合动力汽车和电动马达。
替换标准变速器、动力传动系统可和车轴,将功能电动马达,它将使每个车轮内的运行更安静,比当前的模型。
的出租车也是玻璃的独特的完全由将为经营者提供更大范围的所有边可见性。
装载机是怎么工作的轮式装载机今天是组成的透视的框架,通常铰接式,与引擎安装上的后轮,和驾驶室或冠层停留的前端或后端框架。
枢纽布置的机器是在给予轮式装载机的机动和小型车削圈工作能力的关键。
1974 W14 轮装载机市场按其马力在分节。
紧凑型轮式装载机装载机 80 马力或更少,并分类然后坏了相应地从 80 到 150 匹马力、 150 到 200 马力和 200 到 250 马力。
供电从通过液力变矩器和动力转向齿轮,齿轮驱动车轮的柴油机。
大多数轮式装载机,现要求所有车轮都是相同大小的但太可在两轮驱动操作机器的四轮驱动。
虽然前轮驱动使良好的牵引,执行完整的斗时,后轮驱动增强了机器的挖掘性能。
说明书在设备行业一套规范标准用于衡量轮式装载机性能容量和处理某些构建应用程序的效用。
这些包括斗功能包括桶和切削刃或牙齿、废轮胎、提供牵引能力的大小、水松负载和配重、速度和掘起力。
掘起力是轮式装载机大部分引述规范,并提供轮式装载机挖能力的指示。
历史一般服务和车间设施工程与制造分裂中期 1950 年代以来运作歌赋歌赋科技哈迈尔。
自 1960 年代以来,1989 年,高达工程工作主要由歌赋歌赋科技哈迈尔制造司,其专门的希斯特和履带机器装配在进行。
在八十年代作用已扩大到包括在房屋钢制作的希斯特和卡特彼勒机的帧。
这包括生产,从切割板加工的所有方面。
这一工作成为可能的创新焊接固定装置由,以后建立了系统设计和规划的计算机化生产管理系统。
机械装配在这段期间包括希斯特电动升降机卡车,H40XL 到 H275H 的机器。
卡特彼勒机名称下建介乎 910 至 966 轮式装载机、 518 日志 Skidders 和 120 G/130 G 平地机。
在 1988 年哈迈歌赋歌赋科技尔的基督城分公司被聘请条例草案管理生产的混凝土搅拌机。
歌赋歌赋和哈迈尔现在占 70%的新西兰市场地下混凝土搅拌机。
在大约这个时候,希斯特和履带机器能够导入到新西兰完全建立起来。
哈迈歌赋歌赋科技尔的接近此铅制造司和工程资源,然后在通过传递到哈迈歌赋歌赋科技尔的基督城分支。
制造司的主要工作人员被转移到基督城分公司,和一些新的工作人员被聘请具有专门知识的范围。
新的工作人员包括查理·格雷特巴奇、歌赋工程工程经理和尼尔,机械加工车间领班。
在 1990 年歌赋歌赋科技哈迈尔添加测井叉由设计的产品,其范围,以及大量的其他自定义设计的产品。
在 1994 年歌赋工程被成立的哈迈歌赋、歌赋科技尔专门设计的业务单位和水桶和日志叉、混凝土搅拌机、混凝土批植物等现有歌赋歌赋科技哈迈尔产品的生产。
自己设计的产品,作为歌赋工程还确立建设输送机、回收箱和螺旋输送机项目钢加工商。
在 1995 年歌赋工程包括资源和固体建模的 3D CAD 程序于 1998 年。
Cad 技术的引进改善歌赋工程产品设计的灵活性和不断增加的范围的产品,如自动配料的植物,导致水泥筒仓、轮式装载机和挖掘机斗,以及自定义设计和生成项目。
1996 年歌赋工程设立一个站点在奥克兰,其中迅速扩大,并需于 2000 年建成的新厂房。
在 1999 年歌赋工程安装削减其不断增加的产品范围的南港岛最大数控铣刀。
成果歌赋歌赋和哈迈尔五十多年建立了广泛的土方工程机械、加工和建设行业品牌产品。
从七十年代初到 1989 年歌赋歌赋科技哈默斯制造司装配履带机器与制造大量进口法规要求对轮式机械组件。
在此期间成为同义卡特彼勒性能和质量。
在八十年代初期制造部开始内部钢制作的日志辋、轮式装载机、平地机的帧。
进口规定而丢弃名称被应用到水桶、日志叉和当前生产的歌赋工程的附件。
我们所知道的最古老的产品是沼泽犁序列号 GH5000/5 位于附近布伦海姆布雷谢历史公园。
我们仍有蓝色打印的副本应你需要一个。
犁制造 1950 和是状况良好,无疑将会继续下去。
布雷谢历史公园是值得一看的机械爱好者,因为集合包括所有的引擎类型大多数工作秩序。
如:裂具和刀片式服务器首先制造于 1966 年,随后在 1972 年与950A 和 966 C 轮式装载机的程序集。