天然气转化合成甲醇的工艺
甲醇合成的工艺方法介绍
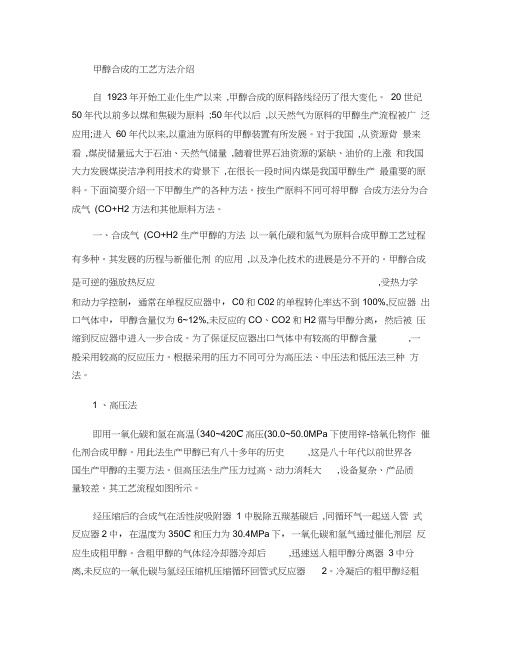
甲醇合成的工艺方法介绍自1923年开始工业化生产以来,甲醇合成的原料路线经历了很大变化。
20 世纪50年代以前多以煤和焦碳为原料;50年代以后,以天然气为原料的甲醇生产流程被广泛应用;进入60 年代以来,以重油为原料的甲醇装置有所发展。
对于我国,从资源背景来看,煤炭储量远大于石油、天然气储量,随着世界石油资源的紧缺、油价的上涨和我国大力发展煤炭洁净利用技术的背景下,在很长一段时间内煤是我国甲醇生产最重要的原料。
下面简要介绍一下甲醇生产的各种方法。
按生产原料不同可将甲醇合成方法分为合成气(CO+H2 方法和其他原料方法。
一、合成气(CO+H2 生产甲醇的方法以一氧化碳和氢气为原料合成甲醇工艺过程有多种。
其发展的历程与新催化剂的应用,以及净化技术的进展是分不开的。
甲醇合成是可逆的强放热反应,受热力学和动力学控制,通常在单程反应器中,C0和C02的单程转化率达不到100%,反应器出口气体中,甲醇含量仅为6~12%,未反应的CO、CO2和H2需与甲醇分离,然后被压缩到反应器中进入一步合成。
为了保证反应器出口气体中有较高的甲醇含量,一般采用较高的反应压力。
根据采用的压力不同可分为高压法、中压法和低压法三种方法。
1 、高压法即用一氧化碳和氢在高温(340~420C高压(30.0~50.0MPa下使用锌-铬氧化物作催化剂合成甲醇。
用此法生产甲醇已有八十多年的历史,这是八十年代以前世界各国生产甲醇的主要方法。
但高压法生产压力过高、动力消耗大,设备复杂、产品质量较差。
其工艺流程如图所示。
经压缩后的合成气在活性炭吸附器 1 中脱除五羰基碳后,同循环气一起送入管式反应器2中,在温度为350C和压力为30.4MPa下,一氧化碳和氢气通过催化剂层反应生成粗甲醇。
含粗甲醇的气体经冷却器冷却后,迅速送入粗甲醇分离器3中分离,未反应的一氧化碳与氢经压缩机压缩循环回管式反应器2。
冷凝后的粗甲醇经粗甲醇储槽 4 进入精馏工序,在粗分离塔5顶部分离出二甲醚和甲酸甲酯及其他低沸点不凝物,重组分则在精分离塔 6 中除去水和杂醇,得到精制的甲醇。
甲醇工业生产工艺
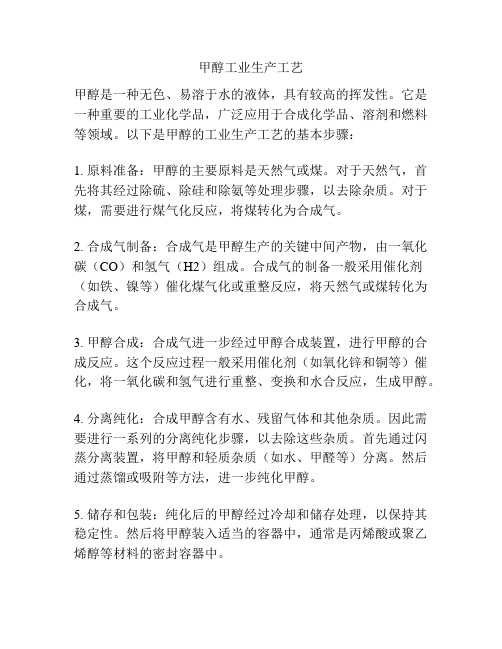
甲醇工业生产工艺
甲醇是一种无色、易溶于水的液体,具有较高的挥发性。
它是一种重要的工业化学品,广泛应用于合成化学品、溶剂和燃料等领域。
以下是甲醇的工业生产工艺的基本步骤:
1. 原料准备:甲醇的主要原料是天然气或煤。
对于天然气,首先将其经过除硫、除硅和除氨等处理步骤,以去除杂质。
对于煤,需要进行煤气化反应,将煤转化为合成气。
2. 合成气制备:合成气是甲醇生产的关键中间产物,由一氧化碳(CO)和氢气(H2)组成。
合成气的制备一般采用催化剂(如铁、镍等)催化煤气化或重整反应,将天然气或煤转化为合成气。
3. 甲醇合成:合成气进一步经过甲醇合成装置,进行甲醇的合成反应。
这个反应过程一般采用催化剂(如氧化锌和铜等)催化,将一氧化碳和氢气进行重整、变换和水合反应,生成甲醇。
4. 分离纯化:合成甲醇含有水、残留气体和其他杂质。
因此需要进行一系列的分离纯化步骤,以去除这些杂质。
首先通过闪蒸分离装置,将甲醇和轻质杂质(如水、甲醛等)分离。
然后通过蒸馏或吸附等方法,进一步纯化甲醇。
5. 储存和包装:纯化后的甲醇经过冷却和储存处理,以保持其稳定性。
然后将甲醇装入适当的容器中,通常是丙烯酸或聚乙烯醇等材料的密封容器中。
以上是甲醇工业生产的基本步骤。
甲醇的工业生产工艺在不同的厂家和地区可能会有所差异,但总体流程是大致相同的。
随着技术的发展,一些新型生产工艺,如生物质转化法和光电催化法等,也在逐渐应用于甲醇的生产过程中,以提高生产效率和降低环境影响。
甲醇生产工艺流程图
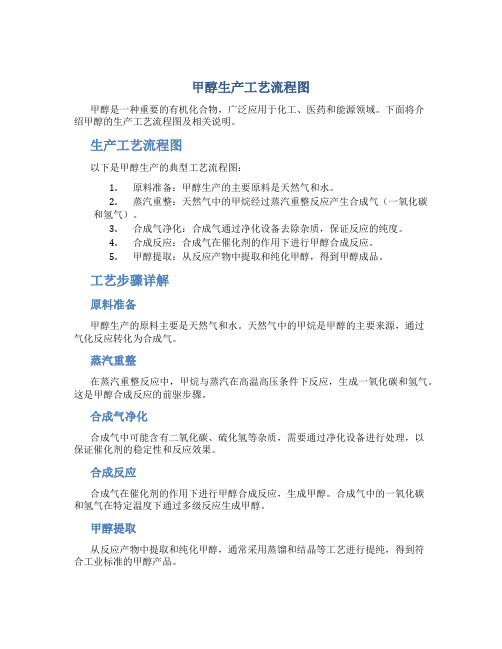
甲醇生产工艺流程图甲醇是一种重要的有机化合物,广泛应用于化工、医药和能源领域。
下面将介绍甲醇的生产工艺流程图及相关说明。
生产工艺流程图以下是甲醇生产的典型工艺流程图:1.原料准备:甲醇生产的主要原料是天然气和水。
2.蒸汽重整:天然气中的甲烷经过蒸汽重整反应产生合成气(一氧化碳和氢气)。
3.合成气净化:合成气通过净化设备去除杂质,保证反应的纯度。
4.合成反应:合成气在催化剂的作用下进行甲醇合成反应。
5.甲醇提取:从反应产物中提取和纯化甲醇,得到甲醇成品。
工艺步骤详解原料准备甲醇生产的原料主要是天然气和水。
天然气中的甲烷是甲醇的主要来源,通过气化反应转化为合成气。
蒸汽重整在蒸汽重整反应中,甲烷与蒸汽在高温高压条件下反应,生成一氧化碳和氢气。
这是甲醇合成反应的前驱步骤。
合成气净化合成气中可能含有二氧化碳、硫化氢等杂质,需要通过净化设备进行处理,以保证催化剂的稳定性和反应效果。
合成反应合成气在催化剂的作用下进行甲醇合成反应,生成甲醇。
合成气中的一氧化碳和氢气在特定温度下通过多级反应生成甲醇。
甲醇提取从反应产物中提取和纯化甲醇,通常采用蒸馏和结晶等工艺进行提纯,得到符合工业标准的甲醇产品。
结论甲醇生产工艺是一个复杂的过程,需要经过多个步骤的精心设计和操作才能获得高质量的产品。
通过合理控制反应条件、提高催化剂的活性和选择合适的分离工艺,可以提高甲醇生产效率和产品质量,满足不同需求。
以上是关于甲醇生产工艺流程图的介绍,希望能给您带来一些帮助和启发。
天然气制甲醇工艺流程
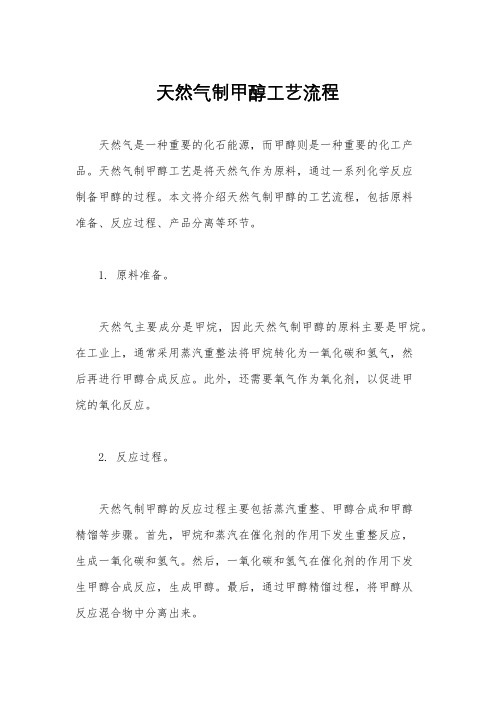
天然气制甲醇工艺流程天然气是一种重要的化石能源,而甲醇则是一种重要的化工产品。
天然气制甲醇工艺是将天然气作为原料,通过一系列化学反应制备甲醇的过程。
本文将介绍天然气制甲醇的工艺流程,包括原料准备、反应过程、产品分离等环节。
1. 原料准备。
天然气主要成分是甲烷,因此天然气制甲醇的原料主要是甲烷。
在工业上,通常采用蒸汽重整法将甲烷转化为一氧化碳和氢气,然后再进行甲醇合成反应。
此外,还需要氧气作为氧化剂,以促进甲烷的氧化反应。
2. 反应过程。
天然气制甲醇的反应过程主要包括蒸汽重整、甲醇合成和甲醇精馏等步骤。
首先,甲烷和蒸汽在催化剂的作用下发生重整反应,生成一氧化碳和氢气。
然后,一氧化碳和氢气在催化剂的作用下发生甲醇合成反应,生成甲醇。
最后,通过甲醇精馏过程,将甲醇从反应混合物中分离出来。
3. 产品分离。
甲醇合成反应产生的混合物中除了甲醇外,还包含未反应的气体和其他杂质。
因此,需要进行产品分离,将甲醇从混合物中提取出来。
通常采用蒸馏、吸附、结晶等方法进行产品分离,得到纯度较高的甲醇产品。
4. 工艺优化。
天然气制甲醇的工艺流程需要根据原料性质、反应条件等因素进行优化。
例如,在蒸汽重整反应中,催化剂的选择、反应温度和压力的控制等都会影响反应的效果。
在甲醇合成反应中,催化剂的活性和选择性对甲醇的产率和纯度有重要影响。
因此,工艺优化是提高天然气制甲醇效率和产品质量的关键。
总之,天然气制甲醇工艺流程包括原料准备、反应过程、产品分离和工艺优化等环节。
通过合理的工艺设计和操作,可以实现天然气向甲醇的高效转化,为化工行业提供了重要的甲醇资源。
甲醇合成的工艺流程和设备

甲醇合成的工艺流程和设备工艺流程:1. 一氧化碳和氢气的制备:首先,通过煤炭气化或天然气重整等方法制备一氧化碳和氢气,然后进行净化和分离处理,得到高纯度的一氧化碳和氢气。
2. 催化反应:将一氧化碳和氢气送入反应器中,在一定的温度和压力条件下,通过催化剂的作用发生一系列反应,将一氧化碳和氢气转化为甲醇。
3. 分离纯化:将反应产物中的甲醇、水蒸汽和未反应的一氧化碳、氢气等组分进行分离和纯化处理,得到高纯度的甲醇产品。
设备:1. 一氧化碳和氢气制备装置:包括气化炉、重整炉、净化器、分离塔等设备。
2. 催化反应器:通常采用固定床反应器,内部填充有高效催化剂,能够保证反应物的充分接触和反应。
3. 分离纯化装置:包括精馏塔、萃取塔、膜分离装置等,用于将反应产物中的各种组分进行分离和纯化处理。
以上是甲醇气相合成的工艺流程和设备,通过精心设计和优化,可以实现甲醇的高效生产,满足不同行业的需求。
甲醇气相合成是一种复杂的化学工艺过程,涉及到高温高压、催化剂选择、反应器设计等多个方面的技术问题。
在甲醇的生产过程中,存在一系列的技术挑战,包括反应的选择性和产率问题、催化剂的稳定性和寿命等。
针对这些挑战,科学家和工程师们提出了许多解决方案,并对工艺流程和设备进行了深入的研究和优化。
在工艺流程方面,甲醇气相合成主要包括气体净化、气体反应和产物分离三个阶段。
首先,气体净化要求将一氧化碳和氢气分离、净化并去除其它杂质;然后在反应阶段,一氧化碳和氢气在一定的温度、压力和催化剂存在下发生反应,生成甲醇;最后在产物分离阶段,需要对反应产物中的甲醇、水蒸汽、未反应的一氧化碳、氢气等组分进行分离、纯化和回收。
这些工艺环节都需要设计合适的设备和优化的操作条件,以保证甲醇高效产出且质量优良。
对于设备的选择和设计,首先需要考虑气体净化部分的设备选型,包括气化炉、重整炉、净化器和分离塔等。
这些设备需要具备耐高温、高压、耐腐蚀等特性,同时还要保证反应物料的净化和分离效果。
甲醇合成的工艺流程和设备

甲醇合成的工艺流程和设备甲醇是一种重要的化工原料,广泛应用于化工、医药、食品等领域。
甲醇的合成工艺流程主要包括天然气制甲醇和煤制甲醇两种。
以下将以天然气制甲醇为例,介绍甲醇的合成工艺流程和设备。
1. 甲醇合成工艺流程甲醇的合成主要通过气相合成法进行,该方法通过一系列复杂的催化反应将一氧化碳和氢气合成甲醇。
具体的工艺流程如下:- 天然气→天然气净化→变化转换反应→合成气→合成气净化→合成气改质→甲醇合成→甲醇回收2. 甲醇合成设备甲醇合成设备主要包括催化反应器、冷凝器、分离塔等:- 催化反应器:将一氧化碳和氢气催化反应生成甲醇,需要具有较高的反应活性和选择性。
- 冷凝器:用于冷却和凝结合成气中的甲醇,使其形成液体甲醇。
- 分离塔:用于将液体甲醇从残余的气相中分离出来,保证甲醇的纯度和回收率。
3. 甲醇生产过程甲醇生产过程主要包括天然气的催化转变、合成气的制备、甲醇的合成和甲醇的回收等环节。
整个过程需要耗费大量的热能和电能,因此需要具备较为完备的能源设施和配套设备。
总的来说,甲醇的合成工艺流程较为复杂,需要涉及多个催化反应和分离过程,所需要的设备也比较繁杂。
企业在进行甲醇合成生产时,需要充分考虑到工艺流程和设备配置,确保生产过程的高效稳定。
甲醇是一种重要的化学品,其合成工艺的复杂性和对能源的依赖性使得甲醇工业在全球范围内备受关注。
天然气制甲醇是目前全球最为主流的甲醇生产工艺。
下面将详细介绍甲醇的合成工艺流程和设备,以及在甲醇生产过程中可能出现的关键技术和挑战。
4. 甲醇合成过程甲醇的合成工艺主要涉及以下几个过程:4.1 天然气制备合成气首先,天然气需要在天然气净化设备中进行净化处理,去除其中的硫化氢、二氧化碳和水等杂质。
通过石灰石和干燥剂的吸附、脱硫等处理,可使天然气达到合成气制备的要求。
然后,经催化转化反应,天然气中的甲烷和水蒸气进行高温反应,生成一氧化碳和氢气,形成合成气。
4.2 合成气的制备合成气是由一氧化碳和氢气所组成的气体混合物,它是甲醇合成的重要中间产物。
天然气制甲醇

天然气制甲醇一、产品介绍:1.1物化性质:纯甲醇为无色透明略带酒精气味的易挥发液体,甲醇分子式:ch4o,分子量32.04,沸点64.5℃,熔点-97.8℃,和水相对密度0.7915(20/4℃),闪点12.22℃,自燃点463.89℃。
甲醇能和水以任意比相溶,但不形成共沸物,能和多数常用的有机溶剂(乙醇、乙醚、丙酮、苯等)混溶,并形成恒沸点混合物。
甲醇能和一些盐如cacl2、mgcl2等形成结晶化合物,称为结晶醇如cacl2〃ch3oh、mgcl2〃6ch3oh,和盐的结晶水合物类似,甲醇遇热、明火或氧化剂易着火。
遇明火会爆炸,蒸汽与空气混合物爆炸下限6%~36.5%(体积)。
燃烧时无烟,火焰呈蓝色。
甲醇具有脂肪族伯醇的一般性质,连有羟基的碳原子上的三个氢原子均可被一一氧化,或脱氢生成甲醛,再氧化成甲酸,甲酸氧化的最终产物是二氧化碳和水。
试剂甲醇常密封保存在棕色瓶中臵于较冷处。
1.2用途:甲醇是一种重要的有机化工原料,主要用于生产甲醛,消耗量要占到甲酵总产量的一半。
目前用甲醇合成二甲醚、乙二醇、乙醛、乙醇也日益受到重视。
甲醇是一种重要的有机溶剂,其溶解性能优于乙醇,可用于调制油漆。
一些无机盐如碘化钠、氯化钙、硝酸铵、硫酸铜、硝酸银、氯化铵、氯化钠都或多或少地能溶于甲醇。
作为一种良好的萃取剂,甲醇在分析化学中可用于一些物质的分离,还用于检验和测定硼。
甲醇还可以做防冻剂。
甲醇经微生物发酵可生产甲醇蛋白,富含维生素和蛋白质,具有营养价值高而成本低的优点,是颇有发展前景的饲料添加剂,能广泛用于牲畜、家禽、鱼类的饲养。
甲醇是一种优良燃料可作能源,甲醇和汽油(柴油)或其它物质可混合成各种不同用途的工业用或民用的新型燃料,甲醇和汽油混合可作为燃料用于运输业。
二、甲醇行业介绍:2.1世界甲醇行业新特点:1)装臵大型化全球已有12套百万吨级的甲醇装臵,更有3套产能超过170万吨的装臵。
2)装臵原料地化装臵由以美湾为主的消费地向以天然气产地为主的原料地集中。
甲醇生产工艺 生产甲醇的工艺
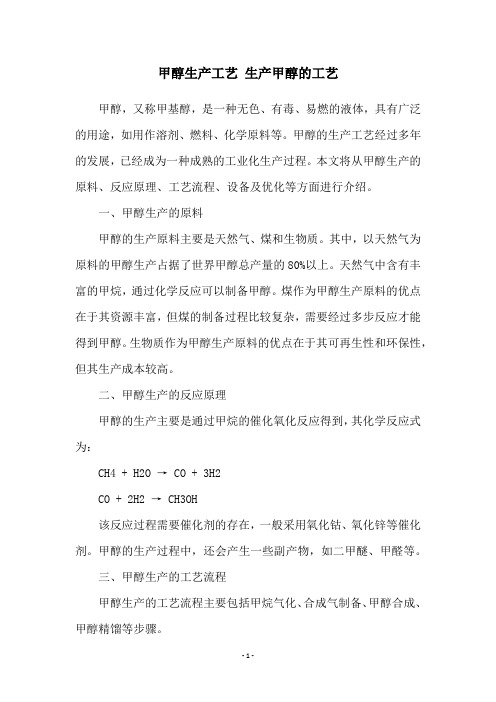
甲醇生产工艺生产甲醇的工艺甲醇,又称甲基醇,是一种无色、有毒、易燃的液体,具有广泛的用途,如用作溶剂、燃料、化学原料等。
甲醇的生产工艺经过多年的发展,已经成为一种成熟的工业化生产过程。
本文将从甲醇生产的原料、反应原理、工艺流程、设备及优化等方面进行介绍。
一、甲醇生产的原料甲醇的生产原料主要是天然气、煤和生物质。
其中,以天然气为原料的甲醇生产占据了世界甲醇总产量的80%以上。
天然气中含有丰富的甲烷,通过化学反应可以制备甲醇。
煤作为甲醇生产原料的优点在于其资源丰富,但煤的制备过程比较复杂,需要经过多步反应才能得到甲醇。
生物质作为甲醇生产原料的优点在于其可再生性和环保性,但其生产成本较高。
二、甲醇生产的反应原理甲醇的生产主要是通过甲烷的催化氧化反应得到,其化学反应式为:CH4 + H2O → CO + 3H2CO + 2H2 → CH3OH该反应过程需要催化剂的存在,一般采用氧化钴、氧化锌等催化剂。
甲醇的生产过程中,还会产生一些副产物,如二甲醚、甲醛等。
三、甲醇生产的工艺流程甲醇生产的工艺流程主要包括甲烷气化、合成气制备、甲醇合成、甲醇精馏等步骤。
1.甲烷气化:将甲烷与氧气进行反应,生成一氧化碳和氢气。
2.合成气制备:将一氧化碳和氢气按一定比例混合,生成合成气。
3.甲醇合成:将合成气和催化剂一起进入甲醇合成反应器进行反应,生成甲醇和一些副产物。
4.甲醇精馏:将反应产生的混合物进行精馏,分离出甲醇和其他有害物质。
四、甲醇生产的设备甲醇生产的设备主要包括气化炉、合成气制备设备、甲醇合成反应器、甲醇精馏塔等。
气化炉是甲烷气化的关键设备,其主要作用是将甲烷和氧气进行反应,生成一氧化碳和氢气。
合成气制备设备是将一氧化碳和氢气按一定比例混合的设备。
甲醇合成反应器是将合成气和催化剂一起进入进行反应的设备。
甲醇精馏塔是将反应产生的混合物进行精馏的设备。
五、甲醇生产的优化甲醇生产的优化主要包括催化剂的改进、反应条件的优化、设备的改进等方面。
- 1、下载文档前请自行甄别文档内容的完整性,平台不提供额外的编辑、内容补充、找答案等附加服务。
- 2、"仅部分预览"的文档,不可在线预览部分如存在完整性等问题,可反馈申请退款(可完整预览的文档不适用该条件!)。
- 3、如文档侵犯您的权益,请联系客服反馈,我们会尽快为您处理(人工客服工作时间:9:00-18:30)。
天然气转化合成甲醇的工艺综述2015-6-24专业:化工12-3班学号:学生姓名:劳慧指导教师:刘峥一.前言 (1)二.主体部分 (2)1. 天然气合成甲醇的原理 (2)2. 高压法合成甲醇的原理及工艺流程 (2)3. 低压法合成甲醇的原理及工艺流程 (3)4. 中压法合成甲醇的原理及流程 (4)5. 三者的比较 (4)6. 以天然气合成甲醇的优势和现状 (6)7. 其他原料合成甲醇与天然气合成甲醇的比较 (6)三.结论部分 (8)1. 对天然气合成甲醇的认识和了解 (8)2. 对天然气转化合成甲醇提出我的观点和见解 (8)四.参考文献 (8)天然气转化合成甲醇的工艺一.前言20世纪60年代,石油和天然气作为一次能源与煤炭一起成为主要能源。
与此同时,以石油和天然气为原料的化学工业也迅猛发展起来。
与石油不同的是,天然气的成分主要是低分子量的烷烃。
因此,天然气化工在发展中逐步成为一个体系。
天然气是储量十分丰富的资源和能源,同时也是主要的温室气体之一,合理地利用天然气不仅关系到未来的资源配置和能源利用,而且也是可持续发展的重要战略发展方向之一。
天然气可以合成多种化工原料产品,比如生产合成氨还有甲醇,其中甲醇是最重要的。
甲醇是一种重要的基础化工产品和化工原料,主要用于生产甲醛。
醋酸、甲苯胺、氯甲烷、乙二醇及各种酸的酯类和维尼纶等,并在很多工业部门中广泛用作溶剂。
甲醇在气田开发中用作防冻剂,添在汽油中可提高汽油的辛烷值,甲醇还可直接用作燃料用于发动机。
目前工业上几乎都是采用一氧化碳、二氧化碳加压催化氢化法合成甲醇。
典型的流程包括原料气制造、原料气净化、甲醇合成、粗甲醇精馏等工序。
天然气、石脑油、重油、煤及其加工产品(焦炭、焦炉煤气)、乙炔尾气等均可作为生产甲醇合成气的原料。
天然气与石脑油的蒸气转化需在结构复杂造价很高的转化炉中进行。
由天然气制合成气进而合成甲醇是制甲醇产品一条重要的工艺路线。
二.主体部分1.天然气合成甲醇的原理天然气转化合成气中的CO 或2CO 与2H 在一定温度、压力和催化剂作用下反应生成甲醇。
其主反应为:OH CH H CO 322⇔+ (1)O H OH CH H CO 23223+⇔+ (2)主要副反应有:O H OCH CH H CO 233242+⇔+ (3)O H CH H CO 2423+⇔+ (4)O H OH H C H CO 2942384+⇔+ (5)O H CO H CO 222+⇔+ (8)甲醇的合成反应是减分子放热反应,由化学热力学原理可知,增加压力、降低温度、减少反应气流中的惰性气体浓度均有利于甲醇的生成。
反应物中的氢气与一氧化碳的摩尔比对甲醇平衡质量分数也有影响。
2.高压法合成甲醇的原理及工艺流程(1)原理:经压缩后的合成气的CO 或2CO 与2H 在300-400C ,30a MP 和氧化锌/氧化铬催化剂的共同作用下反应生成甲醇。
(2)流程方法:经压缩后的合成气在活性炭吸附器中脱除五羰基碳后,同循环气一起送入管式反应器中,在350C 和30MPa 压力下,一氧化碳和氢气通过催化剂层,发生反应生成粗甲醇。
含粗甲醇的气体从反应器出来后,经换热、冷却后迅速送入粗甲醇分离器中,使粗甲醇从气相中冷凝出来,未反应的一氧化碳和氢气循环返回反应器。
冷凝出的粗甲醇送入精馏装置,在第一分馏塔中分出二甲醚和甲酸甲酯及其他低沸点不纯物,在第二分馏塔中除去水和杂醇,得到精甲醇。
甲醇的质量分数:99.85%-99.95%。
3.低压法合成甲醇的原理及工艺流程(1)原理:经压缩后的合成气的CO或者CO与2H在温度200-300C ,2压力4-5MPa和铜基催化剂的作用下反应生成甲醇。
(2)流程方法:合成气经压缩机压缩至4-5MPa后,送入合成塔,经铜基催化剂催化合成甲醇。
合成反应的反应热用热回收装置产生高压蒸汽用作透平压缩机动力。
合成塔出来的含甲醇的产物气体经换热器与混合气换热后,用空气或冷却水换热冷却,使甲醇冷凝并在分离器中分离得到粗甲醇。
粗甲醇经闪蒸罐闪蒸后送去精馏装置精制。
精制中,先用初馏塔除去二甲醚、甲酸甲酯等低沸点杂质。
塔底物进第一精馏塔。
在第一精馏塔中,50%的甲醇由塔顶出来,其热量作为第二精馏塔再沸器加热的热源,塔底物进第二精馏塔。
第二精馏塔塔顶馏出物经冷凝得精甲醇,部分回流后,其余为精甲醇产品,质量分数为99.9%。
该工艺除纯甲醇产品外,第一精馏塔顶部馏出的50%甲醇经换热和部分回流后,可冷凝得到50%-60%的甲醇溶液。
4.中压法合成甲醇的原理及流程(1)原理:经压缩后的合成气在压力为8-15MPa,温度为230-280C和三元铜系催化剂的作用下生成甲醇。
(2)流程方法:合成气压缩至8MPa,与循环气一起送入合成塔,入塔温度220C 左右。
合成塔为冷激型,回收的合成反应热产生中压蒸汽可供转化使用。
合成塔出塔气经换热器预热合成气后,冷却,在冷凝器中将粗甲醇冷凝分离出来,不凝气大部分循环使用,少部分驰放作为转化炉燃料。
粗甲醇在拔顶塔和精制塔中,经蒸馏除去二甲醚、甲酸甲酯及杂醇油等杂质后,即得精甲醇产品,纯度99.9%5.三者的比较高压法、低压法、中压法三种方法合成甲醇,三者在生产设备和生产方法上有各自的特点,各有不同,各有优势。
甲醇合成塔是甲醇生产的关键设备,目前应用的主要塔型有冷管型、多段绝热段间冷型合成塔以及副产蒸汽的等温型合成塔。
粗甲醇的精馏有两种流程,即二塔流程和三塔流程。
A.冷管型:适合于低压合成的冷管型合成塔有ICI的冷管型塔。
我国中、高压法合成普遍采用冷管型塔,有多重冷管结构型式。
B.多段绝热段间冷型合成塔:第一种型式为多段绝热段间冷激式,第二种型式为段间换热器型。
C.副产蒸汽的等温型合成塔:最具代表性、工业化应用最早的是德国鲁奇等温管壳型甲醇合成塔。
我国在消化吸收的基础上自己设计制造了20多个大小不同的鲁奇型等温合成塔,是目前国内甲醇装置中应用最多、效果最好的塔型。
(1)生产方法和设备:高压法合成甲醇目前广泛使用UKW法;低压法合成甲醇使用德国鲁奇法,使用的合成塔为德国鲁奇等温管壳型合成塔,该合成塔具有:1.无需设置开工加热炉,开工时直接将蒸汽送入甲醇合成塔壳程使催化剂加热升温。
2.合成塔既是反应器又是废锅,合成反应热由管外的沸水移走,管外沸水与废锅汽包组成自然循环,只要控制沸水的蒸汽压力,沸水温度也就恒定,故操作时管内催化床的反应温度比较平稳。
3.管壳型合成塔反应温度易于控制,而且由于换热良好,催化床的温度分布也均匀,有利于抑制副反应和延长催化剂的寿命。
4.单程转化率较冷激型塔高,出口甲醇浓度在5-10MPa 下可达5%-10%,在同等条件下几乎为常用冷激塔的一倍,因此气体的循环量也小,随之而来可获得两点好处,一是可以选用较小尺寸的设备和管道,二是可以降低运动中的动力消耗。
5.鱿鱼催化床的反应温度易于保持恒定,故允许含CO比较高的补充气送入合成塔,获得的粗甲醇不仅浓度高,而且质量好。
6.副产蒸汽过热后课用于驱动补充气和循环气压缩机的蒸汽透平,而蒸汽透平用过的乏气又能继续用于甲醇蒸馏,所以系统的热利用度很高;中压法合成甲醇主要是在低压法的基础上改进而成的。
(2)三者的特点:高压法的特点是催化剂耐硫,抗热性较好,对含硫合成气比较适应,一般性过热对催化剂不致造成严重失活。
但该催化剂的选择性较差,导致副产物较多,因而影响收率。
高温高压操作对设备材质要求严,使设备投资费用较高,对技术经济效果有负面影响;低压合成法所用的铜基催化剂比高压合成法所用的锌铬催化剂活性高,选择性好所得粗甲醇中甲醇的质量分数高,因而使收率提高,生产成本下降。
但由于反应压力低,使生产设备体积庞大,不利于大规模生产,仅适用于中小规模的生产。
此外,催化剂耐硫性不如高压合成法,因此生产合成气的天然气中,硫的质量分数必须降至6*1.010以下;中压法合成甲醇兼有高压法和低压法的优点,是近年来采用较多的工艺。
6.以天然气合成甲醇的优势和现状目前,随着石油资源的日益衰竭和石油价格的持续上涨,以天然气合成甲醇等重要化工产品显得十分重要。
以天然气合成甲醇的优势突出在原料上的优势,与石油资源的缺乏相比,天然气储量丰富。
与石油价格相比,天然气价格低廉。
与煤、石油原料相比,天然气是一中清洁能源。
另一面的优势在合成甲醇的工艺上,合成气制甲醇有多种工艺并且也相应投产而且转化率和产率都很高,甲醇的纯度也相当的高。
后续的研究开发可以在已有工艺上进行优化操作。
所以,综上所述以天然气转化合成甲醇在化工生产中占着一定的重要地位,并且是生产甲醇的主要工艺。
7.其他原料合成甲醇与天然气合成甲醇的比较(1)光催化二氧化碳和水合成甲醇基于绿色环保和节约能源两方面看,光催化二氧化碳和水制甲醇是目前较为有前景的合成方法。
光催化二氧化碳和水合成甲醇的催化剂,即铜基催化剂和非铜基催化剂,其中铜基催化剂占主导地位。
光催化二氧化碳和水合成甲醇具有很重要的研究意义。
但目前采用的一些体系催化效率普遍不高,远未达到高效催化能力,且对光催化还原二氧化碳的催化机理的研究报道不多,没有工业化生产。
(2)生物质转化合成甲醇利用生物质合成甲醇主要是通过裂解生物质制合成气,进而利用合成气制甲醇。
生物质主要来源于农业中的废弃物如玉米秸秆、稻壳等,来源丰富、价格低廉而且有利于环境保护,属可再生能源。
但是生物质制合成气的过程十分困难,其中分解焦油过程需较高温度分解,温度可达1000C 以上,而在此温度下催化剂容易烧结和失活,而且很容易造成积碳。
(3)煤转化合成甲醇我国是个缺油少气、煤炭资源丰富的国家,因而煤制甲醇工艺仍是国内中、长期新建项目的首选。
由煤制甲醇生产技术成熟、成本低,对我国能源结构调整、缓解石油供需矛盾具有重要意义。
煤制甲醇工艺主要包括造气、压缩、合成和粗甲醇精制等4个工序。
造气采用鲁奇高压气化炉,使用纯氧气化剂,煤气经冷却脱出焦油、脱硫和二氧化碳制得组成为氢气和一氧化碳的合成气。
煤气化制合成气的好处是可以脱除气态硫等污染物,是煤洁净利用的关键所在。
然而在煤炭生产、使用和运输的过程中也给环境带来了诸多危害。
先如今是环境友好的社会,所以煤制甲醇工艺仍需处理环境的危害问题。
三.结论部分1.对天然气合成甲醇的认识和了解目前,全球天然气经由合成气间接制取甲醇的产量占甲醇产量的90%。
天然气是制甲醇的主要原料,其主要成分是甲烷,还含有少量其他烷烃、烯烃和氮气。
以天然气生产甲醇原料气有蒸汽转化、催化部分氧化、非催化部分氧化等方法。
其中蒸汽转化应用得最广泛。
天然气进入蒸汽转化炉前需进行净化处理消除有害物质,转化后的气体经压缩合成工段合成甲醇,具体工艺见主体部分。
2.对天然气转化合成甲醇提出我的观点和见解制取甲醇有多种工艺方法,天然气转化合成、各种煤转化合成、液化石油气合成、光催化二氧化碳和水合成和生物质转化合成。