甲醇合成的工艺流程和设备
甲醇合成的工艺流程
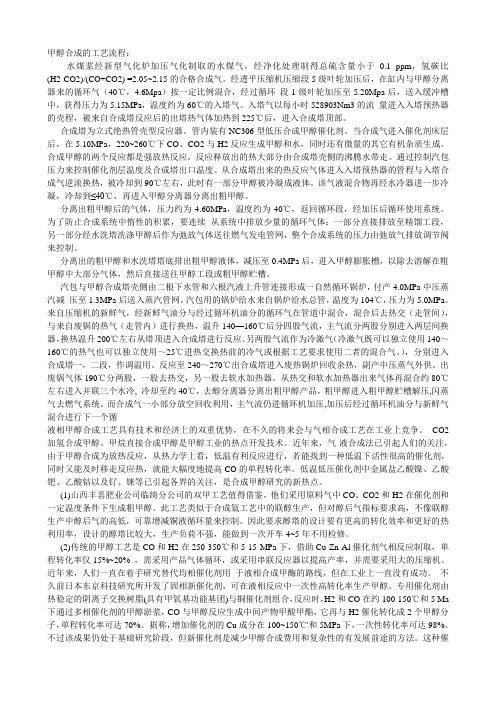
甲醇合成的工艺流程:水煤浆经新型气化炉加压气化制取的水煤气,经净化处理制得总硫含量小于0.1 ppm,氢碳比(H2-CO2)/(CO+CO2) =2.05~2.15的合格合成气。
经透平压缩机压缩段5级叶轮加压后,在缸内与甲醇分离器来的循环气(40℃,4.6Mpa)按一定比例混合,经过循环段1级叶轮加压至5.20Mpa后,送入缓冲槽中,获得压力为5.15MPa,温度约为60℃的入塔气。
入塔气以每小时528903Nm3的流量进入入塔预热器的壳程,被来自合成塔反应后的出塔热气体加热到225℃后,进入合成塔顶部。
合成塔为立式绝热管壳型反应器。
管内装有NC306型低压合成甲醇催化剂。
当合成气进入催化剂床层后,在5.10MPa,220~260℃下CO、CO2与H2反应生成甲醇和水,同时还有微量的其它有机杂质生成。
合成甲醇的两个反应都是强放热反应,反应释放出的热大部分由合成塔壳侧的沸腾水带走。
通过控制汽包压力来控制催化剂层温度及合成塔出口温度。
从合成塔出来的热反应气体进入入塔预热器的管程与入塔合成气逆流换热,被冷却到90℃左右,此时有一部分甲醇被冷凝成液体。
该气液混合物再经水冷器进一步冷凝,冷却到≤40℃,再进入甲醇分离器分离出粗甲醇。
分离出粗甲醇后的气体,压力约为4.60MPa,温度约为40℃,返回循环段,经加压后循环使用系统。
为了防止合成系统中惰性的积累,要连续从系统中排放少量的循环气体:一部分直接排放至精馏工段,另一部分经水洗塔洗涤甲醇后作为弛放气体送往燃气发电管网,整个合成系统的压力由弛放气排放调节阀来控制。
分离出的粗甲醇和水洗塔塔底排出粗甲醇液体,减压至0.4MPa后,进入甲醇膨胀槽,以除去溶解在粗甲醇中大部分气体,然后直接送往甲醇工段或粗甲醇贮槽。
汽包与甲醇合成塔壳侧由二根下水管和六根汽液上升管连接形成一自然循环锅炉,付产4.0MPa中压蒸汽减压至1.3MPa后送入蒸汽管网。
汽包用的锅炉给水来自锅炉给水总管,温度为104℃,压力为5.0MPa。
甲醇合成的工艺流程和设备
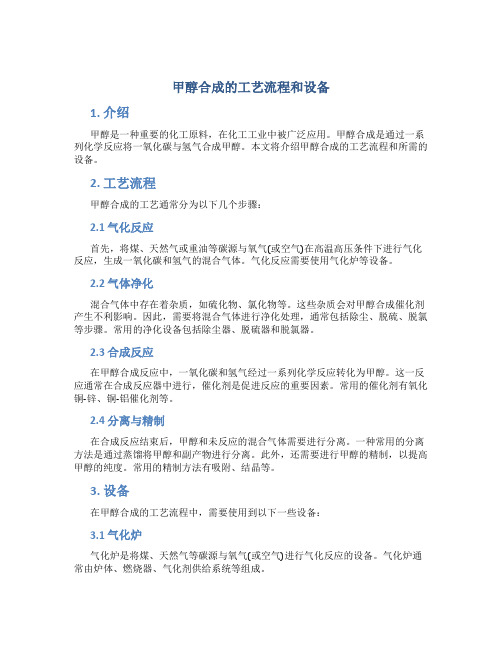
甲醇合成的工艺流程和设备1. 介绍甲醇是一种重要的化工原料,在化工工业中被广泛应用。
甲醇合成是通过一系列化学反应将一氧化碳与氢气合成甲醇。
本文将介绍甲醇合成的工艺流程和所需的设备。
2. 工艺流程甲醇合成的工艺通常分为以下几个步骤:2.1 气化反应首先,将煤、天然气或重油等碳源与氧气(或空气)在高温高压条件下进行气化反应,生成一氧化碳和氢气的混合气体。
气化反应需要使用气化炉等设备。
2.2 气体净化混合气体中存在着杂质,如硫化物、氯化物等。
这些杂质会对甲醇合成催化剂产生不利影响。
因此,需要将混合气体进行净化处理,通常包括除尘、脱硫、脱氯等步骤。
常用的净化设备包括除尘器、脱硫器和脱氯器。
2.3 合成反应在甲醇合成反应中,一氧化碳和氢气经过一系列化学反应转化为甲醇。
这一反应通常在合成反应器中进行,催化剂是促进反应的重要因素。
常用的催化剂有氧化铜-锌、铜-铝催化剂等。
2.4 分离与精制在合成反应结束后,甲醇和未反应的混合气体需要进行分离。
一种常用的分离方法是通过蒸馏将甲醇和副产物进行分离。
此外,还需要进行甲醇的精制,以提高甲醇的纯度。
常用的精制方法有吸附、结晶等。
3. 设备在甲醇合成的工艺流程中,需要使用到以下一些设备:3.1 气化炉气化炉是将煤、天然气等碳源与氧气(或空气)进行气化反应的设备。
气化炉通常由炉体、燃烧器、气化剂供给系统等组成。
3.2 除尘器除尘器用于去除混合气体中的固体颗粒物,以保证合成反应的正常进行。
除尘器可以采用重力沉淀、过滤等原理进行操作。
3.3 脱硫器脱硫器主要用于去除混合气体中的硫化物。
常用的脱硫方法有化学吸收脱硫、物理吸附脱硫等。
3.4 脱氯器脱氯器用于去除混合气体中的氯化物。
脱氯通常采用物理吸附或化学吸收的方式进行。
3.5 合成反应器合成反应器是进行甲醇合成反应的设备。
合成反应器通常由反应罐体、催化剂床层等组成。
3.6 分离设备分离设备主要用于将合成反应产物中的甲醇和副产物进行分离。
甲醇合成的工艺流程和设备

甲醇合成的工艺流程和设备甲醇合成是一种重要的工业化学反应,它是通过一系列的工艺流程和设备来完成的。
下面将详细介绍甲醇合成的工艺流程和设备。
第一步是气体净化。
原料气体主要是天然气或煤气,其中含有一些杂质,如硫化氢、二氧化碳、氨等。
这些杂质会对后续的合成反应产生不利影响,因此需要通过气体净化来去除。
气体净化主要包括硫化氢去除、二氧化碳去除和氨去除等步骤。
硫化氢可以通过催化氧化反应转化为硫,二氧化碳可以通过碱性溶液吸收,氨可以通过酸性溶液吸收。
第二步是合成气的制备。
合成气是甲醇合成的重要原料,它是一种混合气体,主要由一氧化碳和氢气组成。
合成气的制备一般采用催化剂转化法或气化法。
催化剂转化法是将天然气或煤气与蒸汽在催化剂的作用下反应生成合成气。
气化法是将煤、石油等碳质原料在高温、高压条件下气化生成合成气。
第三步是甲醇的合成。
合成气进入甲醇合成反应器后,经过一系列的反应生成甲醇。
甲醇合成一般采用低温高压条件下的催化反应。
常用的催化剂有铜-锌氧化物、铜-铝氧化物等。
甲醇合成反应的主要反应是一氧化碳和氢气生成甲醇。
反应温度一般在200-300摄氏度,压力一般在10-30兆帕。
甲醇的合成反应是一个平衡反应,需要通过适当的操作控制反应条件和催化剂的选择来提高甲醇的产率和选择性。
气体净化装置主要包括硫化氢去除器、二氧化碳去除器和氨去除器等。
硫化氢去除器通常采用催化氧化法,其中含有催化剂床层。
二氧化碳去除器采用碱性溶液吸收法,溶液中加入碱性物质,如钠碱。
氨去除器采用酸性溶液吸收法,溶液中加入酸性物质,如硫酸。
合成气制备装置主要包括催化转化装置和气化装置。
催化转化装置中含有催化剂床层,通过催化反应将天然气或煤气转化为合成气。
气化装置一般采用煤气化炉或石油气化炉,通过高温、高压条件下将煤或石油气化生成合成气。
甲醇合成反应器是甲醇合成的核心设备。
反应器一般采用垂直的压力容器,内部装有催化剂床层。
合成气经过加热后进入反应器,与催化剂发生反应生成甲醇。
合成气制甲醇工艺流程设计与设备选型
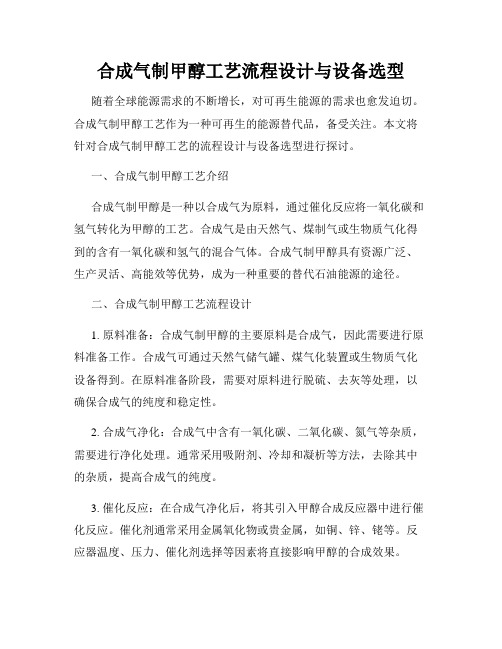
合成气制甲醇工艺流程设计与设备选型随着全球能源需求的不断增长,对可再生能源的需求也愈发迫切。
合成气制甲醇工艺作为一种可再生的能源替代品,备受关注。
本文将针对合成气制甲醇工艺的流程设计与设备选型进行探讨。
一、合成气制甲醇工艺介绍合成气制甲醇是一种以合成气为原料,通过催化反应将一氧化碳和氢气转化为甲醇的工艺。
合成气是由天然气、煤制气或生物质气化得到的含有一氧化碳和氢气的混合气体。
合成气制甲醇具有资源广泛、生产灵活、高能效等优势,成为一种重要的替代石油能源的途径。
二、合成气制甲醇工艺流程设计1. 原料准备:合成气制甲醇的主要原料是合成气,因此需要进行原料准备工作。
合成气可通过天然气储气罐、煤气化装置或生物质气化设备得到。
在原料准备阶段,需要对原料进行脱硫、去灰等处理,以确保合成气的纯度和稳定性。
2. 合成气净化:合成气中含有一氧化碳、二氧化碳、氮气等杂质,需要进行净化处理。
通常采用吸附剂、冷却和凝析等方法,去除其中的杂质,提高合成气的纯度。
3. 催化反应:在合成气净化后,将其引入甲醇合成反应器中进行催化反应。
催化剂通常采用金属氧化物或贵金属,如铜、锌、铑等。
反应器温度、压力、催化剂选择等因素将直接影响甲醇的合成效果。
4. 分离提纯:在甲醇合成反应后,需要进行甲醇的分离和提纯。
通常采用蒸馏、回流和精馏等技术,将甲醇与未反应的气体或杂质分离,得到高纯度的甲醇产品。
三、合成气制甲醇设备选型合成气制甲醇的设备选型是确保工艺顺利进行的重要环节。
在选择设备时,需要考虑以下几个方面:1. 反应器选择:反应器是催化反应的核心设备,对反应效果有着直接影响。
在选择反应器时,需要考虑反应物的流动性、催化剂的服用性和反应温度的控制性等因素。
常见的反应器类型包括固定床反应器、流化床反应器和管式反应器等。
2. 分离设备选择:分离设备是将甲醇与未反应的气体或杂质进行分离的关键设备。
根据甲醇和原料气体的性质和比例,可以选择蒸馏塔、萃取塔和吸附塔等设备。
甲醇合成原理方法与工艺

甲醇合成原理方法与工艺图1煤制甲醇流程示意图煤气经过脱硫、变换,酸性气体脱除等工序后,原料气中的硫化物含量小于0.1mg/m3。
进入合成气压缩机,经压缩后的工艺气体进入合成塔,在催化剂作用下合成粗甲醇,并利用其反应热副产3.9MPa中压蒸汽,降温减压后饱和蒸汽送入低压蒸汽管网,同时将粗甲醇送至精馏系统。
一、甲醇合成反应机理自CO加氢合成甲醇工业化以来,有关合成反应机理一直在不断探索和研究之中。
早期认为合成甲醇是通过CO在催化剂表面吸附生成中间产物而合成的,即CO是合成甲醇的原料。
但20世纪70年代以后,通过同位素示踪研究,证实合成甲醇中的原子来源于CO2,所以认为CO2是合成甲醇的起始原料。
为此,分别提出了CO和CO2合成甲醇的机理反应。
但时至今日,有关合成机理尚无定论,有待进一步研究。
为了阐明甲醇合成反应的模式,1987年朱炳辰等对我国C301型铜基催化剂,分别对仅含有CO或CO2或同时含有CO和CO2三种原料气进行了甲醇合成动力学实验测定,三种情况下均可生成甲醇,试验说明:在一定条件下,CO和CO2均可在铜基催化剂表面加氢生成甲醇。
因此基于化学吸附的CO连续加氢而生成甲醇的反应机理被人们普遍接受。
对甲醇合成而言,无论是锌铬催化剂还是铜基催化剂,其多相(非匀相)催化过程均按下列过程进行:①扩散——气体自气相扩散到气体一催化剂界面;②吸附——各种气体组分在催化剂活性表面上进行化学吸附;③表面吸附——化学吸附的气体,按照不同的动力学假说进行反应形成产物;④解析——反应产物的脱附;⑤扩散——反应产物自气体一催化剂界面扩散到气相中去。
甲醇合成反应的速率,是上述五个过程中的每一个过程进行速率的总和,但全过程的速率取决于最慢步骤的完成速率。
研究证实,过程①与⑤进行得非常迅速,过程②与④的进行速率较快,而过程③分子在催化剂活性界面的反应速率最慢,因此,整个反应过程的速率取决于表面反应的进行速率。
提高压力、升高温度均可使甲醇合成反应速率加快,但从热力学角度分析,由于CO、C02和H2合成甲醇的反应是强放热的体积缩小反应,提高压力、降低温度有利于化学平衡向生成甲醇的方向移动,同时也有利于抑制副反应的进行。
甲醇生产—甲醇生产工艺流程
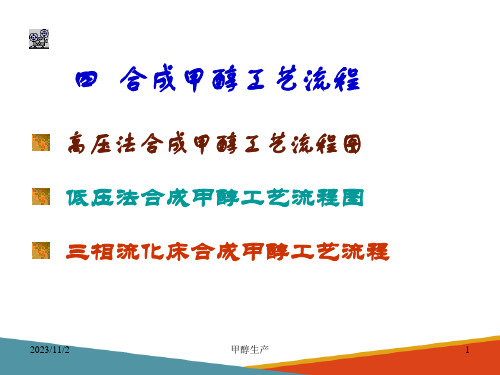
再见 反应器,冷激气在段间经喷嘴喷入,喷嘴分布于反应器的整
个截面上,以便冷激气与反应气混合均匀。混合的温度正好 是反应温度低限,混合气进入下一段床层进行反应。段中进 行的反应为绝热反应,释放的反应热使反应气体温度升高, 但未超过反应温度高限,于下一段间再与冷激气混合降温后 进入下段床层进行反应。冷激式绝热反应器在反应过程中流 量不断增大,各段反应条件略有差异,气体的组成和空速都 不同。
水
3
乙炔尾气
99..99%甲 醇
杂醇油
➢低压法合成甲醇工艺流程图
2023/11/2
甲醇生产
4
2 三相流化床合成甲醇工艺流程
工艺流程(图) 优点:单程转化率高,出口甲醇1520%(V);循环气量少;动力消耗低;反 应器结构简单;温度均匀易于控制。 缺点:三相互相夹带不易分离。
2023/11/2
甲醇生产
2023/11/2
甲醇生产
2
1.低压法合成甲醇流程示意图
O2 水汽
乙炔尾气
400
加热炉
2023/11/2
220000
KK2C2COO3 3
转转 化化 器器
脱脱硫硫塔塔 CCOO2空空 放空
99.85%
分分
脱脱
精甲醇
离离
烃烃 精
器器
塔塔
馏 塔 杂醇油
粗粗甲甲醇醇槽槽
(2) 列管式等温反应器 该类反应器类似于列管式换热器, 其结构示意如图5-10所示。 催化剂装填于列管中,壳程走冷却水(锅炉给水)。反应热 由管外锅炉给水带走,同时产生高压蒸汽。通过对蒸汽压力
合成甲醇工艺流程图
合成甲醇工艺流程图二、预处理700 mmH 2O 30℃二、气柜2、物料平衡表三、焦炉气压缩1、系统图0.3172Mpa 140℃40℃2、物料平衡表注意:停车时造成煤气放散30000Nm3/h2、物料平衡表原材料消耗定额及消耗量表(生产甲醇耗煤气Nm3/吨)催化剂、化学品消耗定额及消耗量表三废排放量表四、转化在转化炉中焦炉气发生如下反应:2H2+O2=H2O+115.48kcal (1) 2CH4+O2=2CO+4H2+17.0kcal (2) CH4+H2O=CO+3H2-49.3kcal (3) CH4+CO2=2CO+2H2-59.1kcal (4) CO+H2O=CO2+H2+9.8kcal (5) 反应最终按(5)达到平衡。
2、物料平衡表(2)危险物料特性装置危险性物料主要物性表(3)催化剂技术规格催化剂技术规格(4)物料消耗(消耗定额以吨甲醇产品计)主要节能措施:燃料气使用甲醇合成工段的弛放气,合理利用了废气。
利用转化气副产中压蒸汽,可回收热量13.85x103kw,并利用转化气预热锅炉给水和脱盐水,可回收热量12.1x103kw,充分回收了反应热。
五、合成气压缩2、物料平衡(1)本装置(630#)为10万吨/年甲醇合成装置的合成气压缩机组,处理新鲜气量46951Nm3/h(干),循环气量259592Nm3/h,合成气出口压力为6.0MPa(A)。
除部分接管外,整个装置由压缩机厂成套供应。
合成气压缩机为离心式二合一机组,由汽轮机驱动,汽轮机为抽汽凝汽式。
正常操作时无三废排放,压缩机运转产生的噪声经消音、隔离处理后可降至85dBA以下。
(2)装置危险性物料主要物性表动力消耗主要节能措施:1、压缩机采用汽轮机驱动,减少了电力消耗。
2、二级射汽抽气器用凝汽器冷凝下来的冷凝液作冷却介质,节省了循环水用量。
合成塔中进行的反应是在催化剂的作用下进行甲醇合成反应CO+2H2=CH3OH+Q CO2+3H2=CH3OH+H2O+Q 副反应: 4CO+8H2=C4H9OH+3H2O 8CO+17H2=C8H18+8H2O 等2、物料平衡(1)原材料技术规格(2)产品技术规格(3)催化剂、吸附剂、化学品技术规格(4)装置危险性物料主要物性(5)消耗A 原材料消耗定额及消耗量B 动力(水、电、汽、气)消耗定额及消耗量C 催化剂、吸附剂和化学品消耗定额及消耗量D 三废排放量E 主要节能措施利用反应热副产蒸汽,回收高位热能5.6x106kcal/h.利用洗醇塔回收弛放气中的甲醇,减少产品损失,每年可回收甲醇874吨。
甲醇合成的生产工艺流程及主要设备
第一节 幼儿生病特征观察
米,摸时是平的或略凹,无紧张感。倘若安静时,发现前囟 凸起,饱满,有紧张感或凹得很深,均属不正常现象,务必 及时就诊。
4.皮肤 正常新生儿皮肤红润细腻,似有绒毛感。新生儿皮肤对外
界细菌、毒素侵入的屏障功能很差,故擦洗抚摸动作宜轻柔, 应洗净手再接触。因为新生儿皮肤表面似良好的培养基,任 何致病或不致病的细菌附着都可能很快地得到滋养而繁殖, 尤其是腋下、臀沟、骶尾骨部更甚。
上一页 下一页 返回
第一节 幼儿生病特征观察
二、病情判断与治疗
妈妈和自己的宝宝朝夕相处,应掌握一定的医学卫生知识, 对宝宝机体出现的变化能做出初步判断,做到心中有数,免 得急中出错。
婴幼儿患病不会用语言表示,但只耍你仔细观察,就能看 出一些异常迹象,如:
情绪不佳 生性好动的小孩,如不像平时那样好说、好
病有轻重缓急,轻病家庭里就可以自己解决,重病能做到 不延误治疗时机。急缓是指发病过程,急病不一定是重病, 缓病也不一定是轻病。如感冒发热,孩子往往起病急,可先 用点消炎退热片、在家观察一下,不必晚卜着急卜医院,特 别在冬天深夜里,天还下着雨雪,狂风怒吼,这样外出反易 加重病情。如有喘憋明显、声音嘶哑, 即使不发热,也要立
上一页 下一页 返回
任务2 甲醇合成的工艺流程
由此可知,合成工序主要由两部分组成,包括甲醇的合成与甲醇的分离, 前者在合成塔中进行,后者由一系列传热设备和气液分离设备来完成。
由于平衡和速率的限制,CO、CO2和H2的单程转化率低,为了充分 利用未反应原料气,较好的措施是分离出甲醇后把未反应的气体返回合 成塔重新反应,这就构成了循环流程。
上一页 下一页 返回
第一节 幼儿生病特征观察
甲醇合成的工艺流程和设备
甲醇合成的工艺流程和设备工艺流程:1. 一氧化碳和氢气的制备:首先,通过煤炭气化或天然气重整等方法制备一氧化碳和氢气,然后进行净化和分离处理,得到高纯度的一氧化碳和氢气。
2. 催化反应:将一氧化碳和氢气送入反应器中,在一定的温度和压力条件下,通过催化剂的作用发生一系列反应,将一氧化碳和氢气转化为甲醇。
3. 分离纯化:将反应产物中的甲醇、水蒸汽和未反应的一氧化碳、氢气等组分进行分离和纯化处理,得到高纯度的甲醇产品。
设备:1. 一氧化碳和氢气制备装置:包括气化炉、重整炉、净化器、分离塔等设备。
2. 催化反应器:通常采用固定床反应器,内部填充有高效催化剂,能够保证反应物的充分接触和反应。
3. 分离纯化装置:包括精馏塔、萃取塔、膜分离装置等,用于将反应产物中的各种组分进行分离和纯化处理。
以上是甲醇气相合成的工艺流程和设备,通过精心设计和优化,可以实现甲醇的高效生产,满足不同行业的需求。
甲醇气相合成是一种复杂的化学工艺过程,涉及到高温高压、催化剂选择、反应器设计等多个方面的技术问题。
在甲醇的生产过程中,存在一系列的技术挑战,包括反应的选择性和产率问题、催化剂的稳定性和寿命等。
针对这些挑战,科学家和工程师们提出了许多解决方案,并对工艺流程和设备进行了深入的研究和优化。
在工艺流程方面,甲醇气相合成主要包括气体净化、气体反应和产物分离三个阶段。
首先,气体净化要求将一氧化碳和氢气分离、净化并去除其它杂质;然后在反应阶段,一氧化碳和氢气在一定的温度、压力和催化剂存在下发生反应,生成甲醇;最后在产物分离阶段,需要对反应产物中的甲醇、水蒸汽、未反应的一氧化碳、氢气等组分进行分离、纯化和回收。
这些工艺环节都需要设计合适的设备和优化的操作条件,以保证甲醇高效产出且质量优良。
对于设备的选择和设计,首先需要考虑气体净化部分的设备选型,包括气化炉、重整炉、净化器和分离塔等。
这些设备需要具备耐高温、高压、耐腐蚀等特性,同时还要保证反应物料的净化和分离效果。
甲醇合成的工艺流程和设备
甲醇合成的工艺流程和设备甲醇是一种重要的化工原料,广泛应用于化工、医药、食品等领域。
甲醇的合成工艺流程主要包括天然气制甲醇和煤制甲醇两种。
以下将以天然气制甲醇为例,介绍甲醇的合成工艺流程和设备。
1. 甲醇合成工艺流程甲醇的合成主要通过气相合成法进行,该方法通过一系列复杂的催化反应将一氧化碳和氢气合成甲醇。
具体的工艺流程如下:- 天然气→天然气净化→变化转换反应→合成气→合成气净化→合成气改质→甲醇合成→甲醇回收2. 甲醇合成设备甲醇合成设备主要包括催化反应器、冷凝器、分离塔等:- 催化反应器:将一氧化碳和氢气催化反应生成甲醇,需要具有较高的反应活性和选择性。
- 冷凝器:用于冷却和凝结合成气中的甲醇,使其形成液体甲醇。
- 分离塔:用于将液体甲醇从残余的气相中分离出来,保证甲醇的纯度和回收率。
3. 甲醇生产过程甲醇生产过程主要包括天然气的催化转变、合成气的制备、甲醇的合成和甲醇的回收等环节。
整个过程需要耗费大量的热能和电能,因此需要具备较为完备的能源设施和配套设备。
总的来说,甲醇的合成工艺流程较为复杂,需要涉及多个催化反应和分离过程,所需要的设备也比较繁杂。
企业在进行甲醇合成生产时,需要充分考虑到工艺流程和设备配置,确保生产过程的高效稳定。
甲醇是一种重要的化学品,其合成工艺的复杂性和对能源的依赖性使得甲醇工业在全球范围内备受关注。
天然气制甲醇是目前全球最为主流的甲醇生产工艺。
下面将详细介绍甲醇的合成工艺流程和设备,以及在甲醇生产过程中可能出现的关键技术和挑战。
4. 甲醇合成过程甲醇的合成工艺主要涉及以下几个过程:4.1 天然气制备合成气首先,天然气需要在天然气净化设备中进行净化处理,去除其中的硫化氢、二氧化碳和水等杂质。
通过石灰石和干燥剂的吸附、脱硫等处理,可使天然气达到合成气制备的要求。
然后,经催化转化反应,天然气中的甲烷和水蒸气进行高温反应,生成一氧化碳和氢气,形成合成气。
4.2 合成气的制备合成气是由一氧化碳和氢气所组成的气体混合物,它是甲醇合成的重要中间产物。
- 1、下载文档前请自行甄别文档内容的完整性,平台不提供额外的编辑、内容补充、找答案等附加服务。
- 2、"仅部分预览"的文档,不可在线预览部分如存在完整性等问题,可反馈申请退款(可完整预览的文档不适用该条件!)。
- 3、如文档侵犯您的权益,请联系客服反馈,我们会尽快为您处理(人工客服工作时间:9:00-18:30)。
项目 压力 温度
高压法 30.0MPa 340~380℃
中压法
低压法
10.0~15.0MPa 5.0~10.0MPa
270℃左右
210~260℃
催化剂 Zn-Cr
Cu-Zn-Cr Cu-Zn-Al
与高压法工艺相比,中、低压法工艺在投资和综合技
术经济指标方面都具有显著优势。以天然气为原料的甲 醇厂,高压法能耗达64.8GJ/t甲醇,而大型低压法装置为 29.5~31.5GJ/t甲醇。1970年代后国外新建的大中型甲 醇装置全部采用低压法,超大型装置(大于50万吨/年) 采用中压法,高压法渐趋淘汰。
从目前国内外甲醇工业发展情况来看,预计以副产蒸 汽、等温合成为特征的中低压合成工艺将是今后相当长 一段时期内甲醇合成的主流工艺
甲醇合成基本步骤
甲醇合成流程虽有多种,但是许多基本步骤是共同具备的
压缩
预热
合成
冷却
分离
循环
惰性气体排放
基本流程
高压工艺流程
高压流程是使用锌铬催化剂,在300~400℃, 30MPa的高温高压下合成甲醇。
低压工艺流程
采用铜系低温高活性催化剂,可在低压5MPa下进行合成 。 冷激型流程,因其结构简单,目前广泛采用,但反应器
出口甲醇含量低。
第二节 甲醇合成塔
第三节 冷却分离设备
甲醇合成的工艺流程和 设备
2020年4月29日星期三
甲醇合成流程种类
高压法
锌铬催化剂
30MPa,400℃
投资及生产成本高
中压法
铜基催化剂
10MPa ,200~300℃
设备紧凑
低压法
铜基催化剂
4~5MPa ,2催化剂 12MPa ,240~280℃
与中小型合成氨联合
高、中、低压法甲醇生产主要操作条件